service ISUZU TF SERIES 2004 Workshop Manual
[x] Cancel search | Manufacturer: ISUZU, Model Year: 2004, Model line: TF SERIES, Model: ISUZU TF SERIES 2004Pages: 4264, PDF Size: 72.63 MB
Page 1784 of 4264
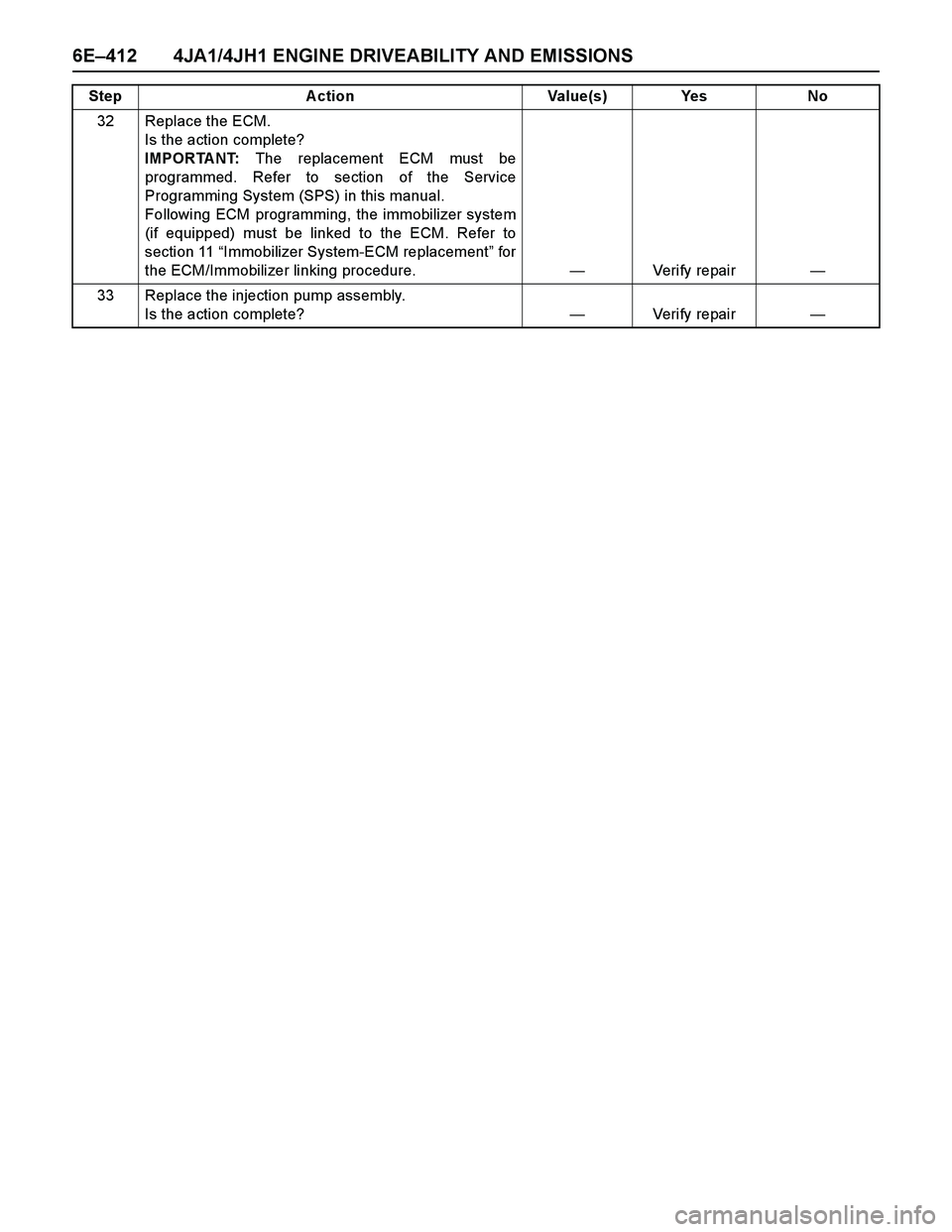
6E–412 4JA1/4JH1 ENGINE DRIVEABILITY AND EMISSIONS
32 Replace the ECM.
Is the action complete?
IMPORTANT: The replacement ECM must be
programmed. Refer to section of the Service
Programming System (SPS) in this manual.
Following ECM programming, the immobilizer system
(if equipped) must be linked to the ECM. Refer to
section 11 “Immobilizer System-ECM replacement” for
the ECM/Immobilizer linking procedure.—Veri fy repai r—
33 Replace the injection pump assembly.
Is the action complete?—Veri fy repai r— Step Action Value(s) Yes No
Page 1789 of 4264
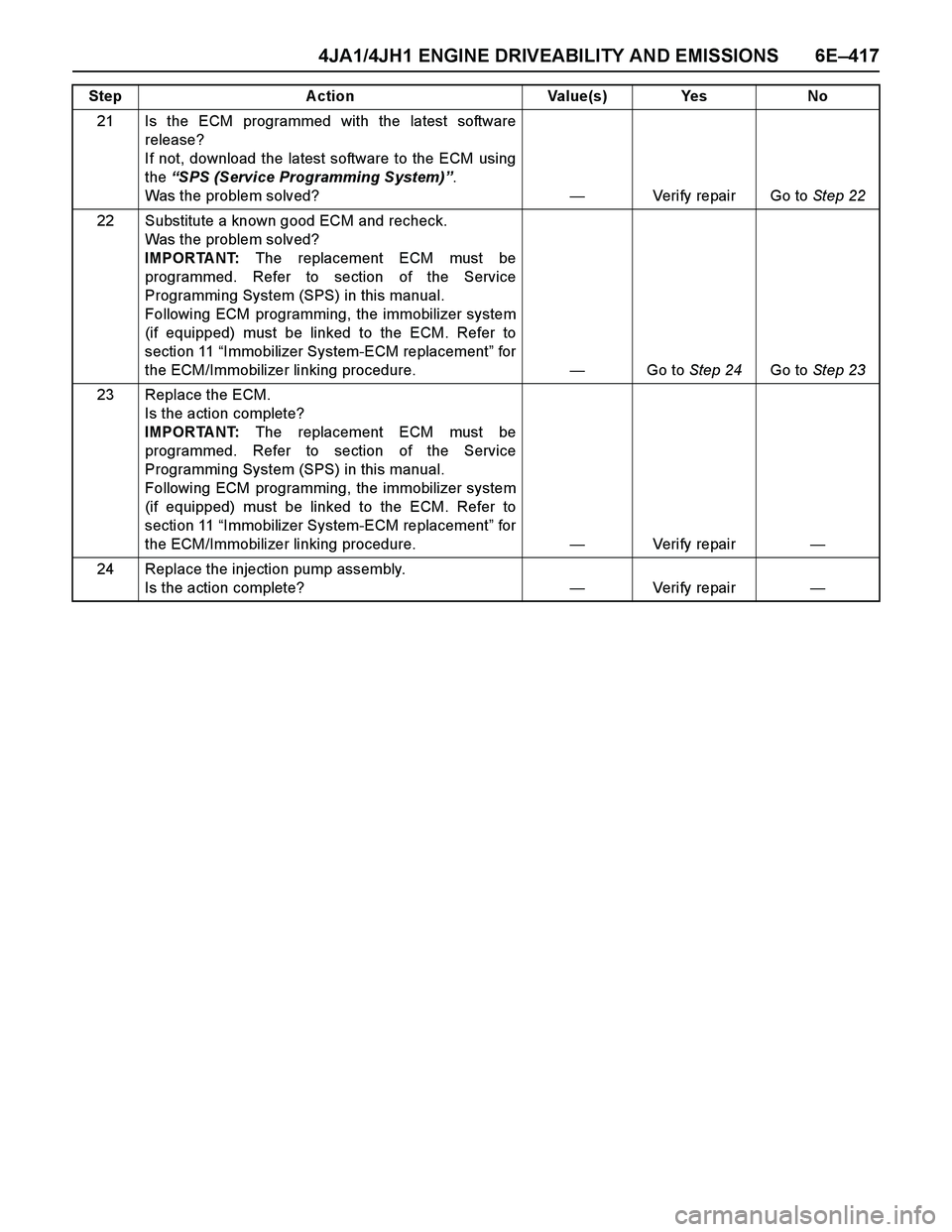
4JA1/4JH1 ENGINE DRIVEABILITY AND EMISSIONS 6E–417
21 Is the ECM programmed with the latest software
release?
If not, download the latest software to the ECM using
the “SPS (Service Programming System)”.
Was the problem solved?—Verify repair Go to Step 22
22 Substitute a known good ECM and recheck.
Was the problem solved?
IMPORTANT: The replacement ECM must be
programmed. Refer to section of the Service
Programming System (SPS) in this manual.
Following ECM programming, the immobilizer system
(if equipped) must be linked to the ECM. Refer to
section 11 “Immobilizer System-ECM replacement” for
the ECM/Immobilizer linking procedure. —Go to Step 24Go to Step 23
23 Replace the ECM.
Is the action complete?
IMPORTANT: The replacement ECM must be
programmed. Refer to section of the Service
Programming System (SPS) in this manual.
Following ECM programming, the immobilizer system
(if equipped) must be linked to the ECM. Refer to
section 11 “Immobilizer System-ECM replacement” for
the ECM/Immobilizer linking procedure.—Veri fy repai r—
24 Replace the injection pump assembly.
Is the action complete?—Veri fy repai r— Step Action Value(s) Yes No
Page 1790 of 4264
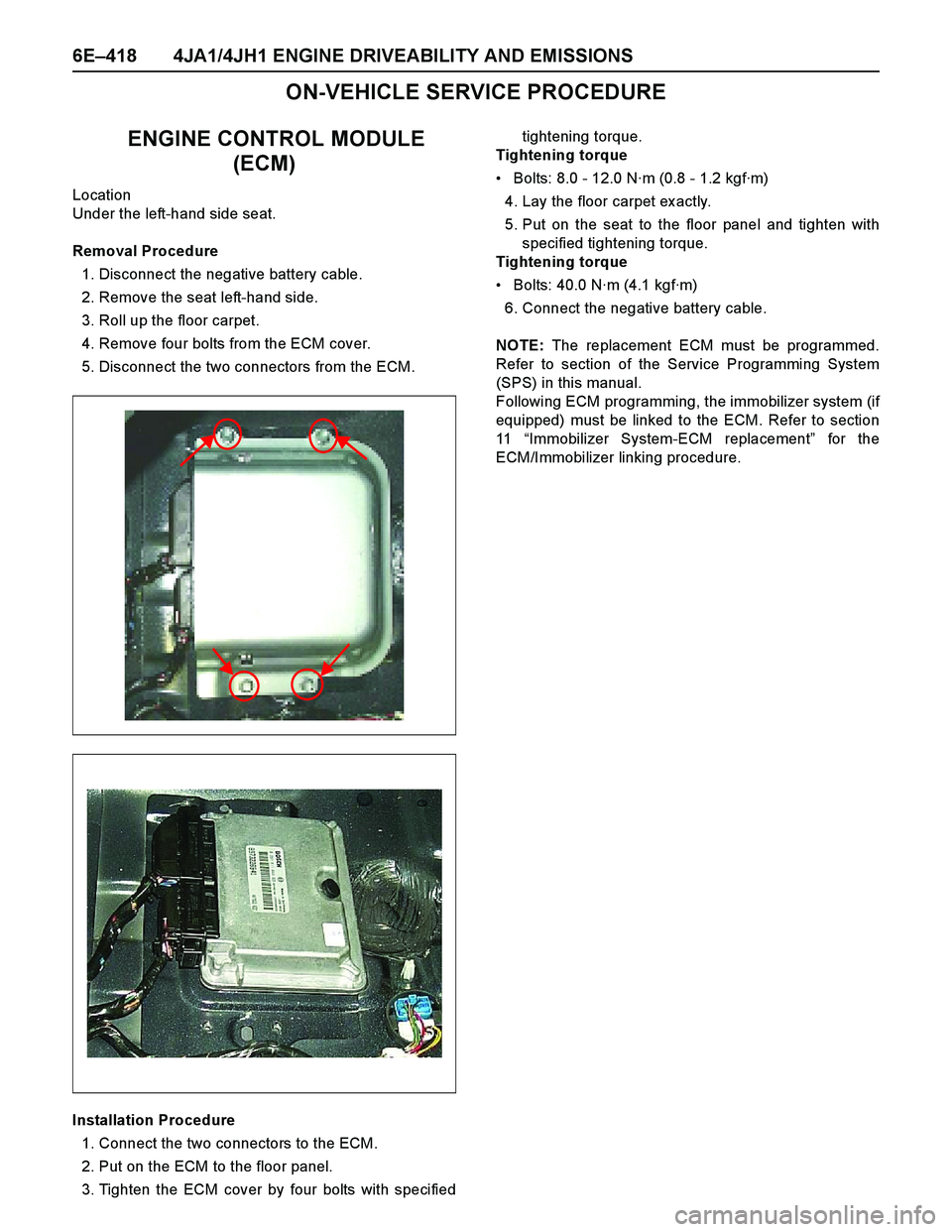
6E–418 4JA1/4JH1 ENGINE DRIVEABILITY AND EMISSIONS
ON-VEHICLE SERVICE PROCEDURE
ENGINE CONTROL MODULE
(ECM)
Location
Under the left-hand side seat.
Removal Procedure
1. Disconnect the negative battery cable.
2. Remove the seat left-hand side.
3. Roll up the floor carpet.
4. Remove four bolts from the ECM cover.
5. Disconnect the two connectors from the ECM.
Installation Procedure
1. Connect the two connectors to the ECM.
2. Put on the ECM to the floor panel.
3. Tighten the ECM cover by four bolts with specifiedtightening torque.
Tightening torque
Bolts: 8.0 - 12.0 N·m (0.8 - 1.2 kgf·m)
4. Lay the floor carpet ex actly.
5. Put on the seat to the floor panel and tighten with
specified tightening torque.
Tightening torque
Bolts: 40.0 N·m (4.1 kgf·m)
6. Connect the negative battery cable.
NOTE: The replacement ECM must be programmed.
Refer to section of the Service Programming System
(SPS) in this manual.
Following ECM programming, the immobilizer system (if
equipped) must be linked to the ECM. Refer to section
11 “Immobilizer System-ECM replacement” for the
ECM/Immobilizer linking procedure.
Page 1794 of 4264
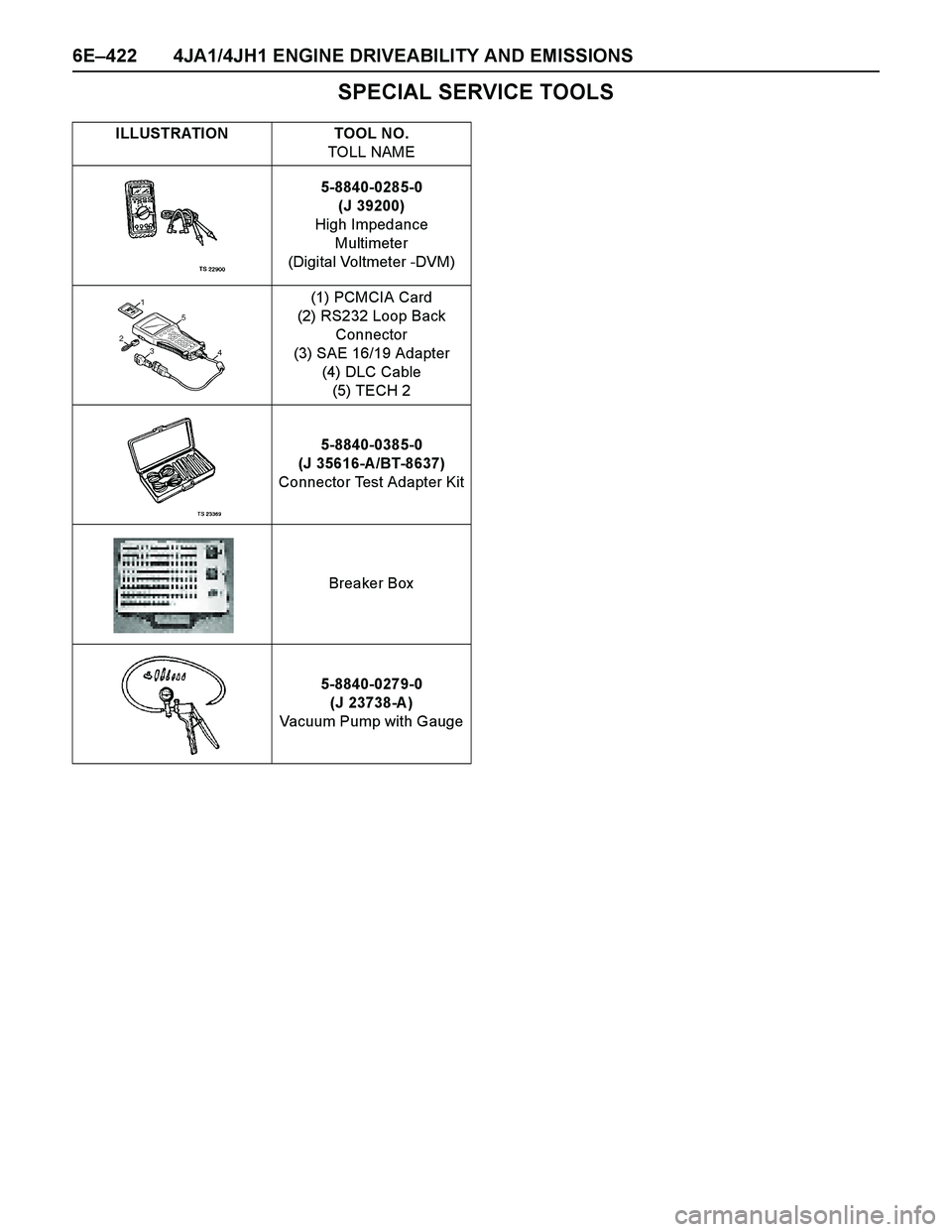
6E–422 4JA1/4JH1 ENGINE DRIVEABILITY AND EMISSIONS
SPECIAL SERVICE TOOLS
ILLUSTRATION TOOL NO.
TOLL NAME
5-8840-0285-0
(J 39200)
High Impedance
Multimeter
(Digital Voltmeter -DVM)
(1) PCMCIA Card
(2) RS232 Loop Back
Connector
(3) SAE 16/19 Adapter
(4) DLC Cable
(5) TECH 2
5-8840-0385-0
(J 35616-A /BT-8637)
Connector Test Adapter Kit
Breaker Box
5-8840-0279-0
(J 23738-A )
Vacuum Pump with Gauge
Page 1795 of 4264
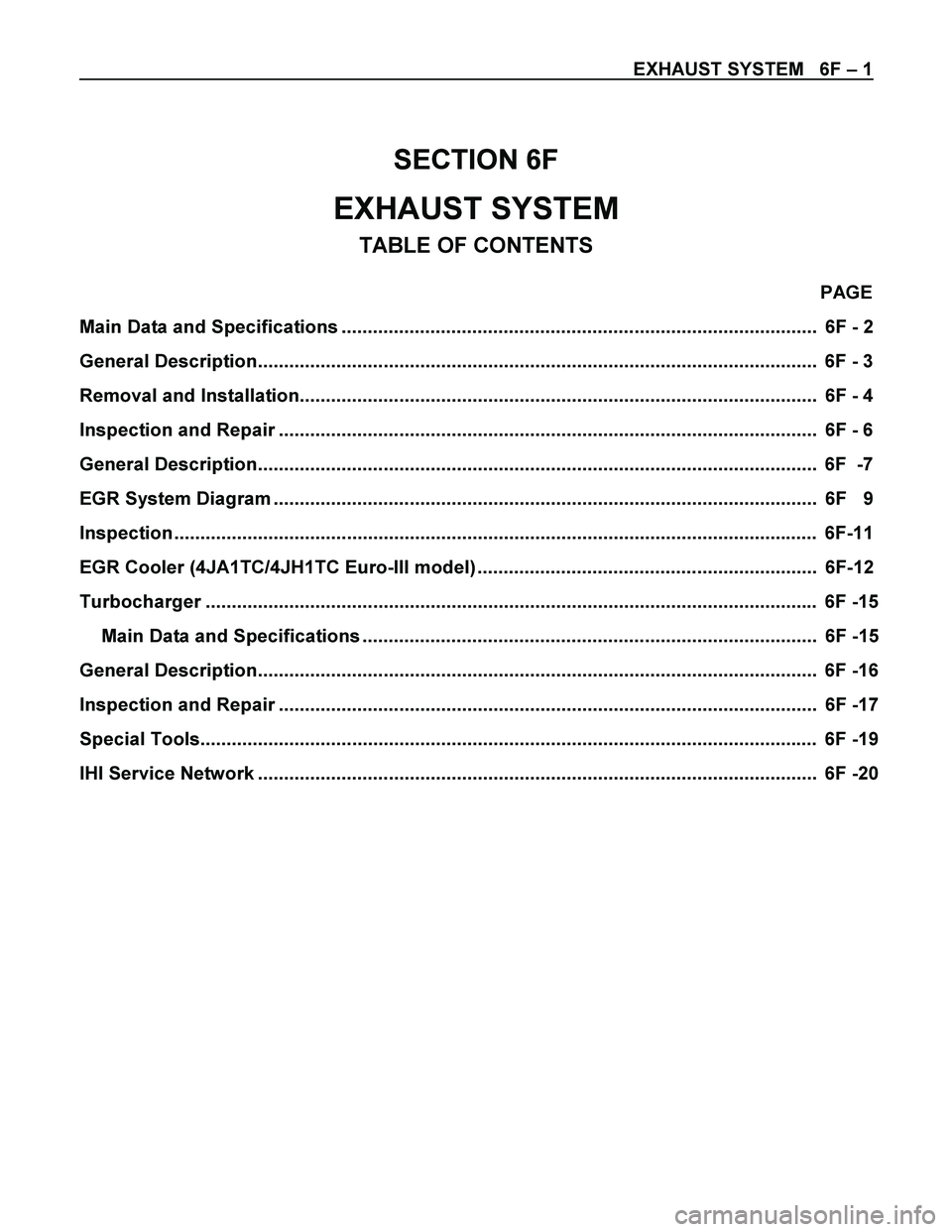
EXHAUST SYSTEM 6F – 1
SECTION 6F
EXHAUST SYSTEM
TABLE OF CONTENTS
PAGE
Main Data and Specifications ........................................................................................... 6F - 2
General Description........................................................................................................... 6F - 3
Removal and Installation................................................................................................... 6F - 4
Inspection and Repair ....................................................................................................... 6F - 6
General Description........................................................................................................... 6F -7
EGR System Diagram ........................................................................................................ 6F 9
Inspection ........................................................................................................................... 6F-11
EGR Cooler (4JA1TC/4JH1TC Euro-III model) ................................................................. 6F-12
Turbocharger ..................................................................................................................... 6F -15
Main Data and Specifications ....................................................................................... 6F -15
General Description........................................................................................................... 6F -16
Inspection and Repair ....................................................................................................... 6F -17
Special Tools...................................................................................................................... 6F -19
IHI Service Network ........................................................................................................... 6F -20
Page 1811 of 4264
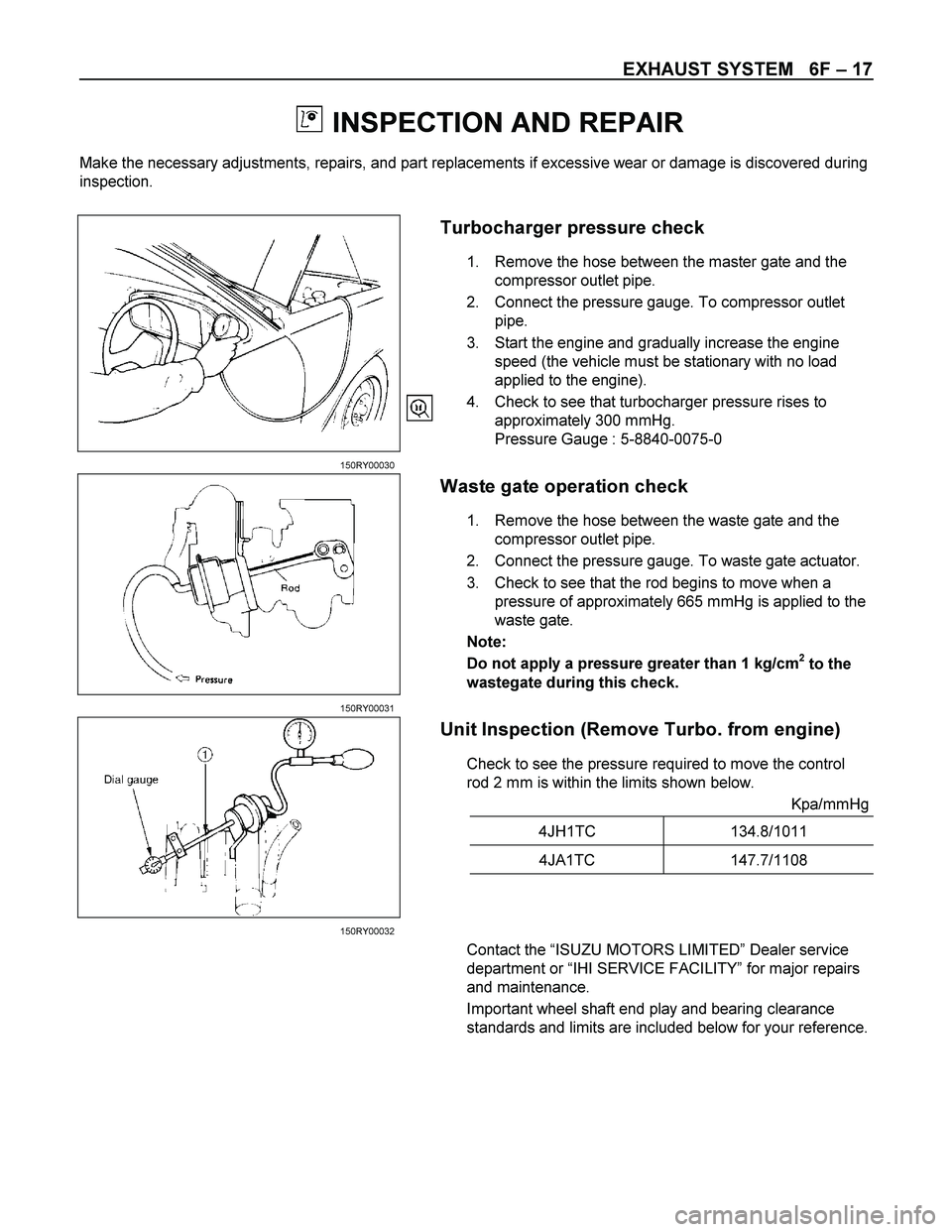
EXHAUST SYSTEM 6F – 17
INSPECTION AND REPAIR
Make the necessary adjustments, repairs, and part replacements if excessive wear or damage is discovered during
inspection.
Turbocharger pressure check
1. Remove the hose between the master gate and the
compressor outlet pipe.
2. Connect the pressure gauge. To compressor outlet
pipe.
3. Start the engine and gradually increase the engine
speed (the vehicle must be stationary with no load
applied to the engine).
4. Check to see that turbocharger pressure rises to
approximately 300 mmHg.
Pressure Gauge : 5-8840-0075-0
150RY00030
Waste gate operation check
1. Remove the hose between the waste gate and the
compressor outlet pipe.
2. Connect the pressure gauge. To waste gate actuator.
3. Check to see that the rod begins to move when a
pressure of approximately 665 mmHg is applied to the
waste gate.
Note:
Do not apply a pressure greater than 1 kg/cm
2 to the
wastegate during this check.
150RY00031
Unit Inspection (Remove Turbo. from engine)
Check to see the pressure required to move the control
rod 2 mm is within the limits shown below.
Kpa/mmHg
4JH1TC 134.8/1011
4JA1TC 147.7/1108
150RY00032
Contact the “ISUZU MOTORS LIMITED” Dealer service
department or “IHI SERVICE FACILITY” for major repairs
and maintenance.
Important wheel shaft end play and bearing clearance
standards and limits are included below for your reference.
Page 1814 of 4264
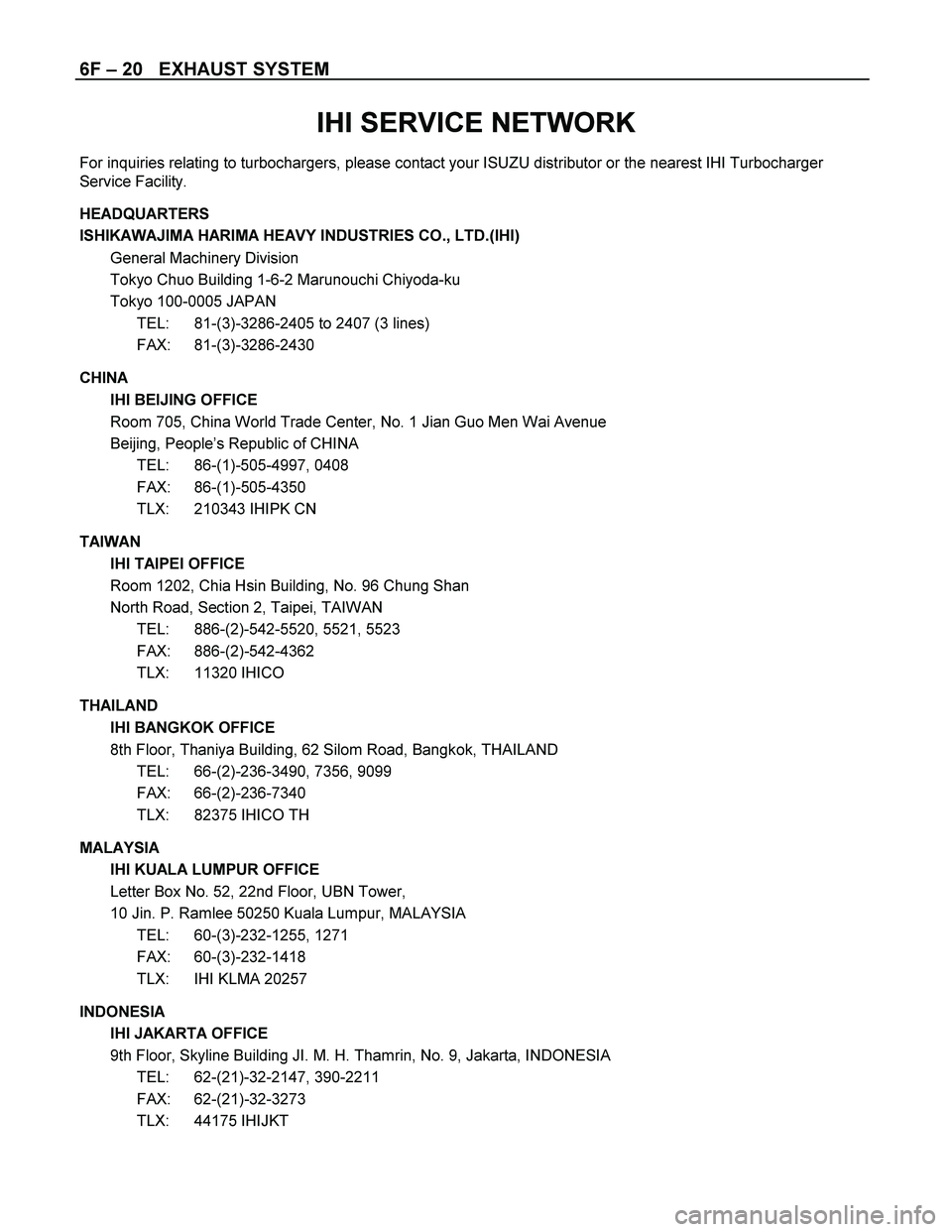
6F – 20 EXHAUST SYSTEM
IHI SERVICE NETWORK
For inquiries relating to turbochargers, please contact your ISUZU distributor or the nearest IHI Turbocharger
Service Facility.
HEADQUARTERS
ISHIKAWAJIMA HARIMA HEAVY INDUSTRIES CO., LTD.(IHI)
General Machinery Division
Tokyo Chuo Building 1-6-2 Marunouchi Chiyoda-ku
Tokyo 100-0005 JAPAN
TEL: 81-(3)-3286-2405 to 2407 (3 lines)
FAX: 81-(3)-3286-2430
CHINA
IHI BEIJING OFFICE
Room 705, China World Trade Center, No. 1 Jian Guo Men Wai Avenue
Beijing, People’s Republic of CHINA
TEL: 86-(1)-505-4997, 0408
FAX: 86-(1)-505-4350
TLX: 210343 IHIPK CN
TAIWAN
IHI TAIPEI OFFICE
Room 1202, Chia Hsin Building, No. 96 Chung Shan
North Road, Section 2, Taipei, TAIWAN
TEL: 886-(2)-542-5520, 5521, 5523
FAX: 886-(2)-542-4362
TLX: 11320 IHICO
THAILAND
IHI BANGKOK OFFICE
8th Floor, Thaniya Building, 62 Silom Road, Bangkok, THAILAND
TEL: 66-(2)-236-3490, 7356, 9099
FAX: 66-(2)-236-7340
TLX: 82375 IHICO TH
MALAYSIA
IHI KUALA LUMPUR OFFICE
Letter Box No. 52, 22nd Floor, UBN Tower,
10 Jin. P. Ramlee 50250 Kuala Lumpur, MALAYSIA
TEL: 60-(3)-232-1255, 1271
FAX: 60-(3)-232-1418
TLX: IHI KLMA 20257
INDONESIA
IHI JAKARTA OFFICE
9th Floor, Skyline Building JI. M. H. Thamrin, No. 9, Jakarta, INDONESIA
TEL: 62-(21)-32-2147, 390-2211
FAX: 62-(21)-32-3273
TLX: 44175 IHIJKT
Page 1825 of 4264
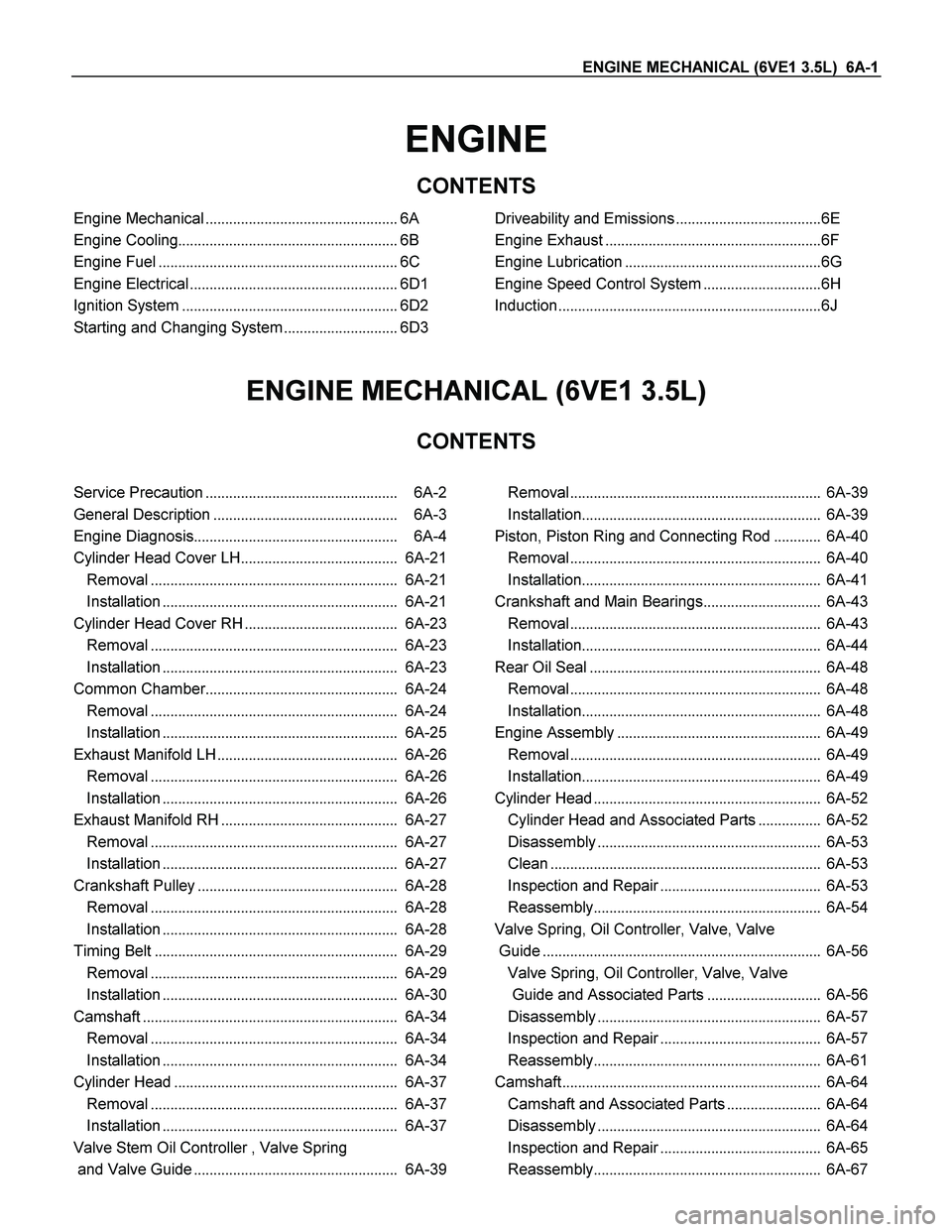
ENGINE MECHANICAL (6VE1 3.5L) 6A-1
ENGINE
CONTENTS
Engine Mechanical.................................................6A
Engine Cooling........................................................6B
Engine Fuel.............................................................6C
Engine Electrical.....................................................6D1
Ignition System.......................................................6D2
Starting and Changing System.............................6D3 Driveability and Emissions.....................................6E
Engine Exhaust.......................................................6F
Engine Lubrication..................................................6G
Engine Speed Control System..............................6H
Induction...................................................................6J
ENGINE MECHANICAL (6VE1 3.5L)
CONTENTS
Service Precaution................................................. 6A-2
General Description............................................... 6A-3
Engine Diagnosis.................................................... 6A-4
Cylinder Head Cover LH........................................ 6A-21
Removal............................................................... 6A-21
Installation............................................................ 6A-21
Cylinder Head Cover RH....................................... 6A-23
Removal............................................................... 6A-23
Installation............................................................ 6A-23
Common Chamber................................................. 6A-24
Removal............................................................... 6A-24
Installation............................................................ 6A-25
Exhaust Manifold LH.............................................. 6A-26
Removal............................................................... 6A-26
Installation............................................................ 6A-26
Exhaust Manifold RH............................................. 6A-27
Removal............................................................... 6A-27
Installation............................................................ 6A-27
Crankshaft Pulley................................................... 6A-28
Removal............................................................... 6A-28
Installation............................................................ 6A-28
Timing Belt.............................................................. 6A-29
Removal............................................................... 6A-29
Installation............................................................ 6A-30
Camshaft................................................................. 6A-34
Removal............................................................... 6A-34
Installation............................................................ 6A-34
Cylinder Head......................................................... 6A-37
Removal............................................................... 6A-37
Installation............................................................ 6A-37
Valve Stem Oil Controller , Valve Spring
and Valve Guide.................................................... 6A-39
Removal................................................................ 6A-39
Installation............................................................. 6A-39
Piston, Piston Ring and Connecting Rod............ 6A-40
Removal................................................................ 6A-40
Installation............................................................. 6A-41
Crankshaft and Main Bearings.............................. 6A-43
Removal................................................................ 6A-43
Installation............................................................. 6A-44
Rear Oil Seal........................................................... 6A-48
Removal................................................................ 6A-48
Installation............................................................. 6A-48
Engine Assembly.................................................... 6A-49
Removal................................................................ 6A-49
Installation............................................................. 6A-49
Cylinder Head.......................................................... 6A-52
Cylinder Head and Associated Parts................ 6A-52
Disassembly......................................................... 6A-53
Clean..................................................................... 6A-53
Inspection and Repair......................................... 6A-53
Reassembly.......................................................... 6A-54
Valve Spring, Oil Controller, Valve, Valve
Guide....................................................................... 6A-56
Valve Spring, Oil Controller, Valve, Valve
Guide and Associated Parts............................. 6A-56
Disassembly......................................................... 6A-57
Inspection and Repair......................................... 6A-57
Reassembly.......................................................... 6A-61
Camshaft.................................................................. 6A-64
Camshaft and Associated Parts........................ 6A-64
Disassembly......................................................... 6A-64
Inspection and Repair......................................... 6A-65
Reassembly.......................................................... 6A-67
Page 1826 of 4264
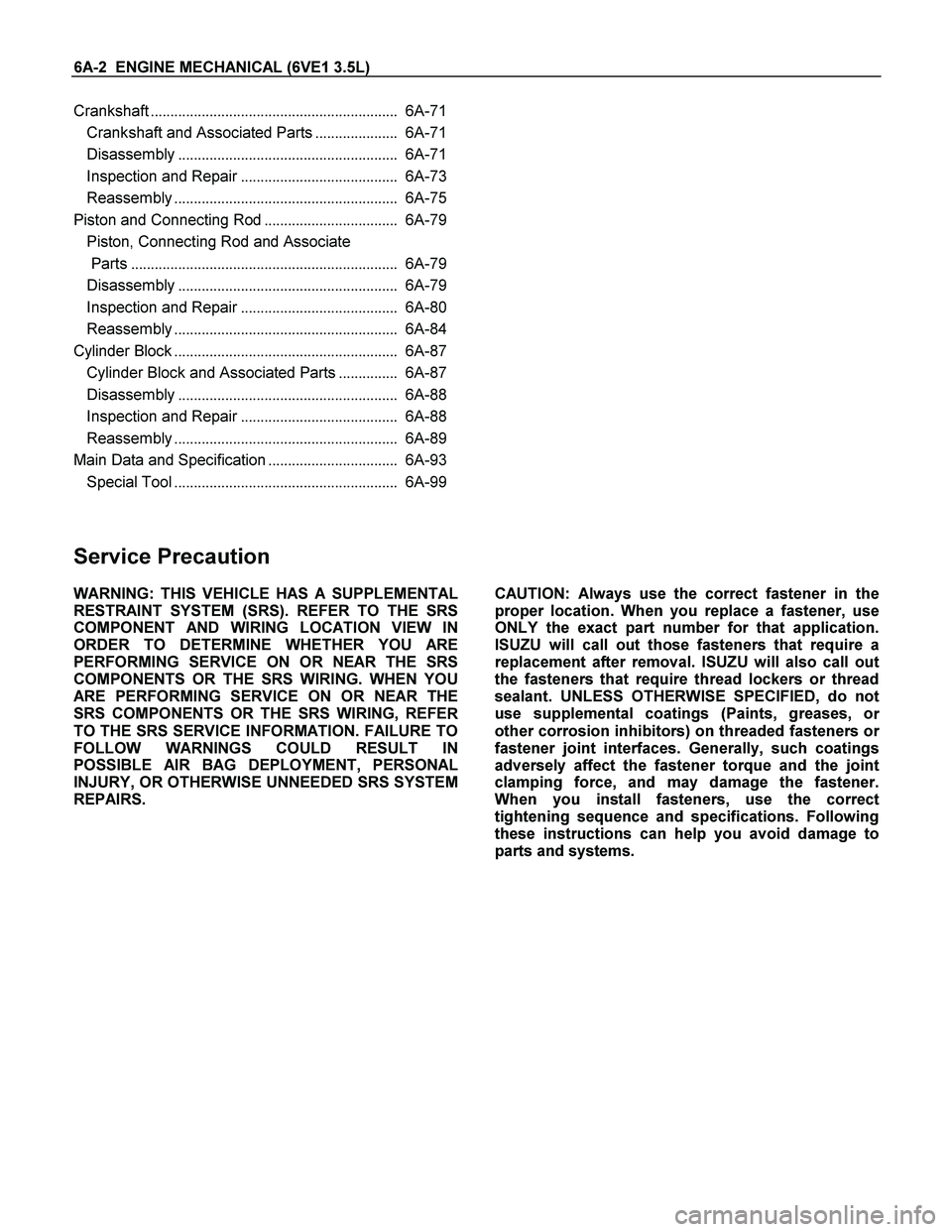
6A-2 ENGINE MECHANICAL (6VE1 3.5L)
Crankshaft............................................................... 6A-71
Crankshaft and Associated Parts..................... 6A-71
Disassembly........................................................ 6A-71
Inspection and Repair........................................ 6A-73
Reassembly......................................................... 6A-75
Piston and Connecting Rod.................................. 6A-79
Piston, Connecting Rod and Associate
Parts.................................................................... 6A-79
Disassembly........................................................ 6A-79
Inspection and Repair........................................ 6A-80
Reassembly......................................................... 6A-84
Cylinder Block......................................................... 6A-87
Cylinder Block and Associated Parts............... 6A-87
Disassembly........................................................ 6A-88
Inspection and Repair........................................ 6A-88
Reassembly......................................................... 6A-89
Main Data and Specification................................. 6A-93
Special Tool......................................................... 6A-99
Service Precaution
WARNING: THIS VEHICLE HAS A SUPPLEMENTAL
RESTRAINT SYSTEM (SRS). REFER TO THE SRS
COMPONENT AND WIRING LOCATION VIEW IN
ORDER TO DETERMINE WHETHER YOU ARE
PERFORMING SERVICE ON OR NEAR THE SRS
COMPONENTS OR THE SRS WIRING. WHEN YOU
ARE PERFORMING SERVICE ON OR NEAR THE
SRS COMPONENTS OR THE SRS WIRING, REFE
R
TO THE SRS SERVICE INFORMATION. FAILURE TO
FOLLOW WARNINGS COULD RESULT IN
POSSIBLE AIR BAG DEPLOYMENT, PERSONAL
INJURY, OR OTHERWISE UNNEEDED SRS SYSTEM
REPAIRS.
CAUTION: Always use the correct fastener in the
proper location. When you replace a fastener, use
ONLY the exact part number for that application.
ISUZU will call out those fasteners that require a
replacement after removal. ISUZU will also call out
the fasteners that require thread lockers or thread
sealant. UNLESS OTHERWISE SPECIFIED, do not
use supplemental coatings (Paints, greases, o
r
other corrosion inhibitors) on threaded fasteners o
r
fastener joint interfaces. Generally, such coatings
adversely affect the fastener torque and the joint
clamping force, and may damage the fastener.
When you install fasteners, use the correct
tightening sequence and specifications. Following
these instructions can help you avoid damage to
parts and systems.
Page 1827 of 4264
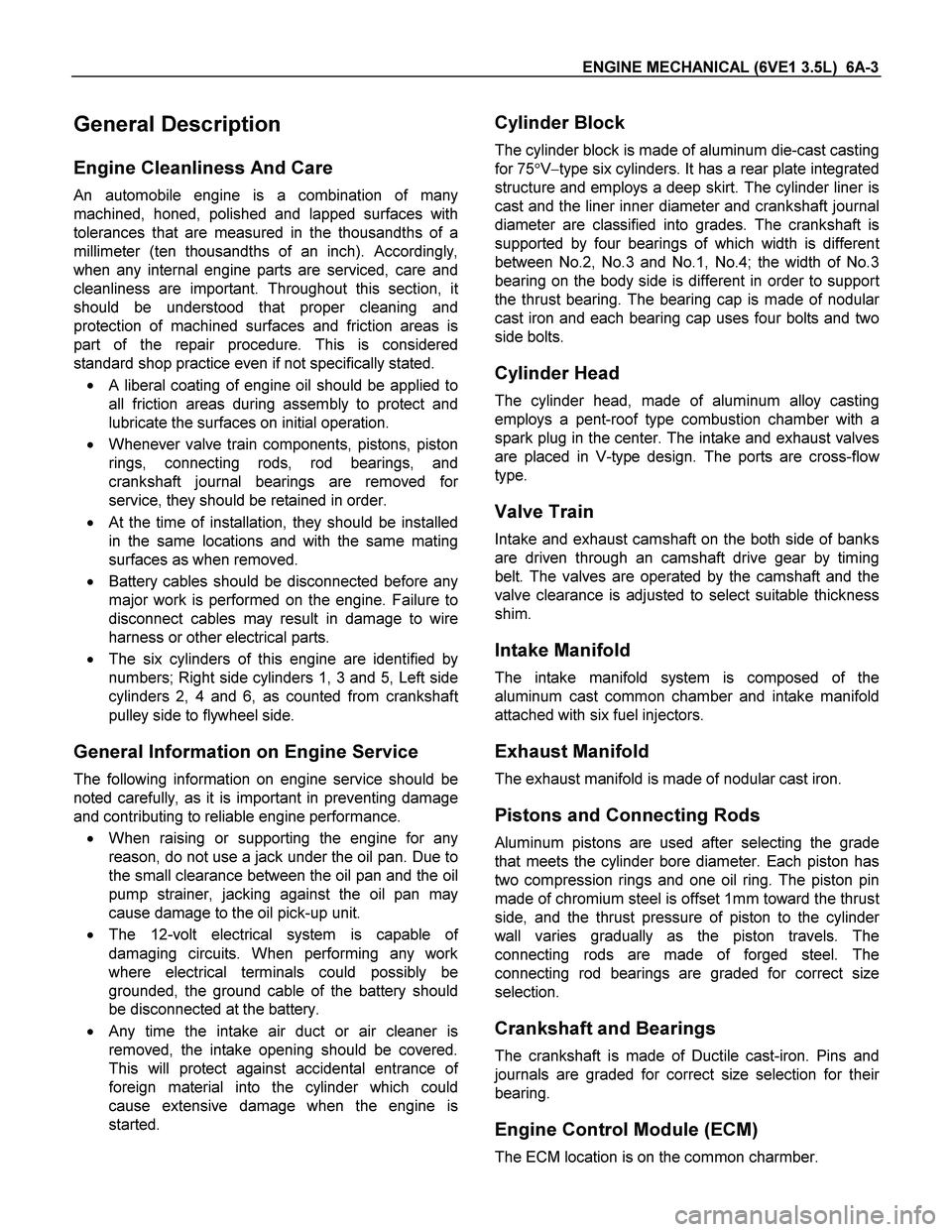
ENGINE MECHANICAL (6VE1 3.5L) 6A-3
General Description
Engine Cleanliness And Care
An automobile engine is a combination of many
machined, honed, polished and lapped surfaces with
tolerances that are measured in the thousandths of a
millimeter (ten thousandths of an inch). Accordingly,
when any internal engine parts are serviced, care and
cleanliness are important. Throughout this section, i
t
should be understood that proper cleaning and
protection of machined surfaces and friction areas is
part of the repair procedure. This is considered
standard shop practice even if not specifically stated.
A liberal coating of engine oil should be applied to
all friction areas during assembly to protect and
lubricate the surfaces on initial operation.
Whenever valve train components, pistons, piston
rings, connecting rods, rod bearings, and
crankshaft journal bearings are removed fo
r
service, they should be retained in order.
At the time of installation, they should be installed
in the same locations and with the same mating
surfaces as when removed.
Battery cables should be disconnected before any
major work is performed on the engine. Failure to
disconnect cables may result in damage to wire
harness or other electrical parts.
The six cylinders of this engine are identified by
numbers; Right side cylinders 1, 3 and 5, Left side
cylinders 2, 4 and 6, as counted from crankshaf
t
pulley side to flywheel side.
General Information on Engine Service
The following information on engine service should be
noted carefully, as it is important in preventing damage
and contributing to reliable engine performance.
When raising or supporting the engine for any
reason, do not use a jack under the oil pan. Due to
the small clearance between the oil pan and the oil
pump strainer, jacking against the oil pan may
cause damage to the oil pick-up unit.
The 12-volt electrical system is capable o
f
damaging circuits. When performing any work
where electrical terminals could possibly be
grounded, the ground cable of the battery should
be disconnected at the battery.
Any time the intake air duct or air cleaner is
removed, the intake opening should be covered.
This will protect against accidental entrance o
f
foreign material into the cylinder which could
cause extensive damage when the engine is
started.
Cylinder Block
The cylinder block is made of aluminum die-cast casting
for 75Vtype six cylinders. It has a rear plate integrated
structure and employs a deep skirt. The cylinder liner is
cast and the liner inner diameter and crankshaft journal
diameter are classified into grades. The crankshaft is
supported by four bearings of which width is differen
t
between No.2, No.3 and No.1, No.4; the width of No.3
bearing on the body side is different in order to suppor
t
the thrust bearing. The bearing cap is made of nodular
cast iron and each bearing cap uses four bolts and two
side bolts.
Cylinder Head
The cylinder head, made of aluminum alloy casting
employs a pent-roof type combustion chamber with a
spark plug in the center. The intake and exhaust valves
are placed in V-type design. The ports are cross-flo
w
type.
Valve Train
Intake and exhaust camshaft on the both side of banks
are driven through an camshaft drive gear by timing
belt. The valves are operated by the camshaft and the
valve clearance is adjusted to select suitable thickness
shim.
Intake Manifold
The intake manifold system is composed of the
aluminum cast common chamber and intake manifold
attached with six fuel injectors.
Exhaust Manifold
The exhaust manifold is made of nodular cast iron.
Pistons and Connecting Rods
Aluminum pistons are used after selecting the grade
that meets the cylinder bore diameter. Each piston has
two compression rings and one oil ring. The piston pin
made of chromium steel is offset 1mm toward the thrus
t
side, and the thrust pressure of piston to the cylinder
wall varies gradually as the piston travels. The
connecting rods are made of forged steel. The
connecting rod bearings are graded for correct size
selection.
Crankshaft and Bearings
The crankshaft is made of Ductile cast-iron. Pins and
journals are graded for correct size selection for thei
r
bearing.
Engine Control Module (ECM)
The ECM location is on the common charmber.