battery replacement ISUZU TF SERIES 2004 User Guide
[x] Cancel search | Manufacturer: ISUZU, Model Year: 2004, Model line: TF SERIES, Model: ISUZU TF SERIES 2004Pages: 4264, PDF Size: 72.63 MB
Page 1791 of 4264
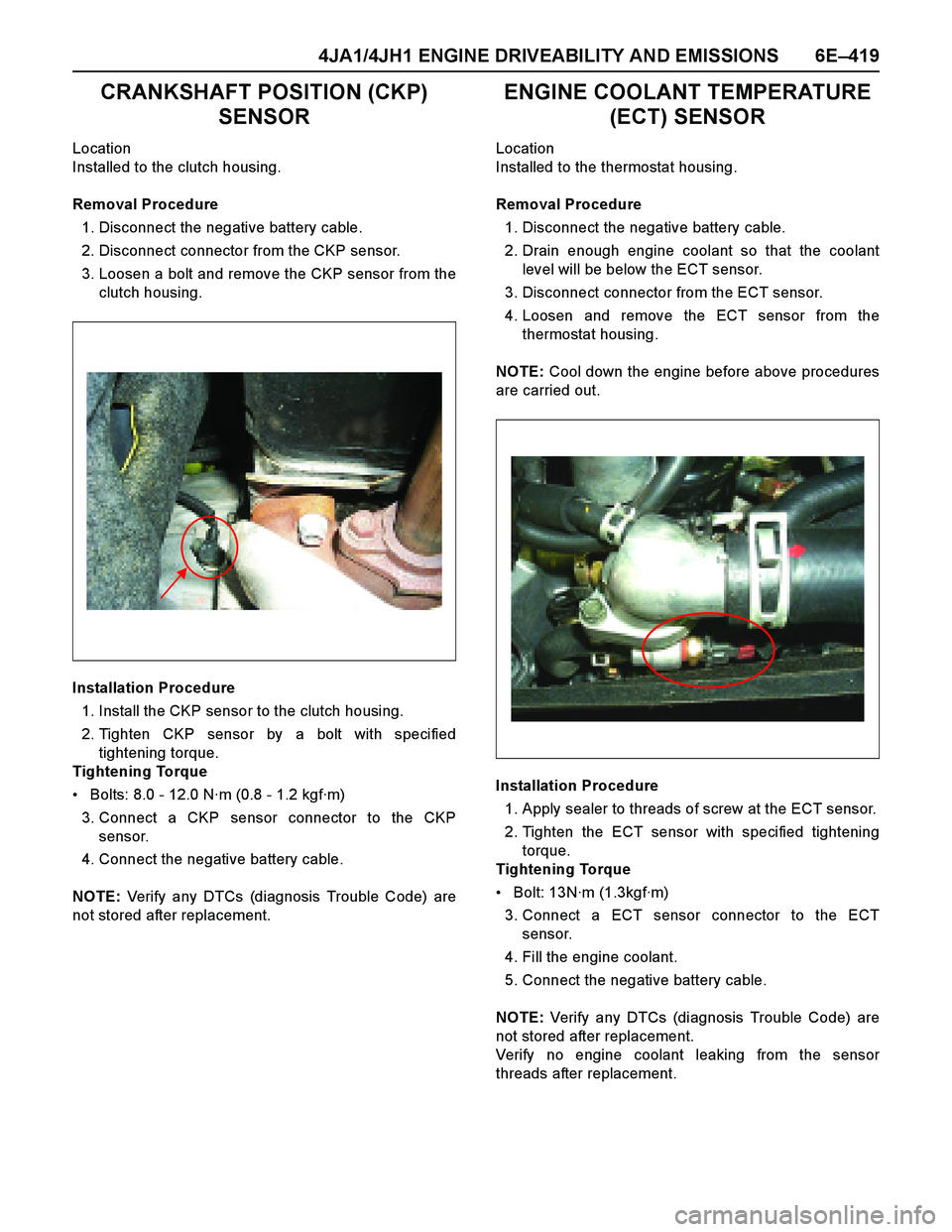
4JA1/4JH1 ENGINE DRIVEABILITY AND EMISSIONS 6E–419
CRANKSHAFT POSITION (CKP)
SENSOR
Location
Installed to the clutch housing.
Removal Procedure
1. Disconnect the negative battery cable.
2. Disconnect connector from the CKP sensor.
3. Loosen a bolt and remove the CKP sensor from the
clutch housing.
Installation Procedure
1. Install the CKP sensor to the clutch housing.
2. Tighten CKP sensor by a bolt with specified
tightening torque.
Tightening Torque
Bolts: 8.0 - 12.0 N·m (0.8 - 1.2 kgf·m)
3. Connect a CKP sensor connector to the CKP
sensor.
4. Connect the negative battery cable.
NOTE: Verify any DTCs (diagnosis Trouble Code) are
not stored after replacement.
ENGINE COOLANT TEMPERATURE
(ECT) SENSOR
Location
Installed to the thermostat housing.
Removal Procedure
1. Disconnect the negative battery cable.
2. Drain enough engine coolant so that the coolant
level will be below the ECT sensor.
3. Disconnect connector from the ECT sensor.
4. Loosen and remove the ECT sensor from the
thermostat housing.
NOTE: Cool down the engine before above procedures
are carried out.
Installation Procedure
1. Apply sealer to threads of screw at the ECT sensor.
2. Tighten the ECT sensor with specified tightening
torque.
Tightening Torque
Bolt: 13N·m (1.3kgf·m)
3. Connect a ECT sensor connector to the ECT
sensor.
4. Fill the engine coolant.
5. Connect the negative battery cable.
NOTE: Verify any DTCs (diagnosis Trouble Code) are
not stored after replacement.
Verify no engine coolant leaking from the sensor
threads after replacement.
Page 1792 of 4264

6E–420 4JA1/4JH1 ENGINE DRIVEABILITY AND EMISSIONS
MASS AIR FLOW (MAF) & INTAKE
AIR TEMPERATURE (IAT) SENSOR
Location
Installed to the intake duct housing.
Removal Procedure
1. Disconnect the negative battery cable.
2. Disconnect a MAF & IAT sensor connector from the
MAF & IAT sensor assembly.
3. Loosen the clips and remove the MAF & IAT sensor
assembly from the intake duct housing.
Installation Procedure
1. Install the MAF & IAT sensor assembly into intake
air duct.
2. Tighten the clips.
3. Connect a MAF & IAT sensor connector to the MAF
& IAT sensor assembly.
4. Connect the negative battery cable.
NOTE: Verify any DTCs (diagnosis Trouble Code) are
not stored after replacement.
THROTTLE POSITION SENSOR
(TPS)
Location
Installed on the throttle body.
Removal Procedure
1. Disconnect the negative battery cable.
2. Disconnect the TPS connector.
3. Loosen two screws and remove TPS from the
throttle body.
Installation Procedure
1. Temporary tighten the TPS by two screws.
2. Connect a TPS connectors to the TPS.
3. Connect the Tech2 to the vehicle.
4. Connect the negative battery cable.
5. Select “Data Display” with the Tech2.
6. Check the throttle position data and adjust the TPS
position.
7. Tighten two screws.
NOTE: Verify any DTCs (diagnosis Trouble Code) are
not stored after replacement.
Page 1793 of 4264
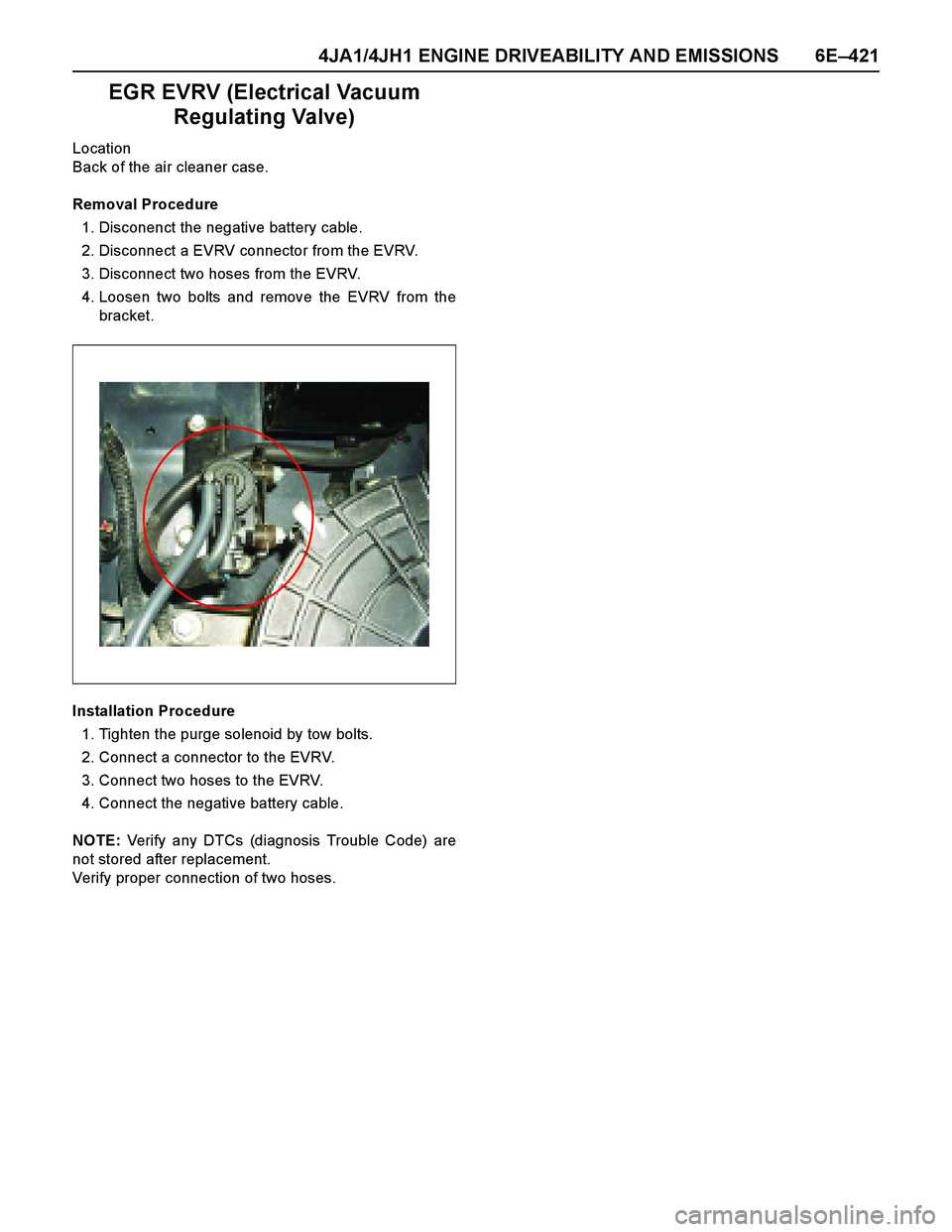
4JA1/4JH1 ENGINE DRIVEABILITY AND EMISSIONS 6E–421
EGR EVRV (Electrical Vacuum
Regulating Valve)
Location
Back of the air cleaner case.
Removal Procedure
1. Disconenct the negative battery cable.
2. Disconnect a EVRV connector from the EVRV.
3. Disconnect two hoses from the EVRV.
4. Loosen two bolts and remove the EVRV from the
bracket.
Installation Procedure
1. Tighten the purge solenoid by tow bolts.
2. Connect a connector to the EVRV.
3. Connect two hoses to the EVRV.
4. Connect the negative battery cable.
NOTE: Verify any DTCs (diagnosis Trouble Code) are
not stored after replacement.
Verify proper connection of two hoses.
Page 1931 of 4264
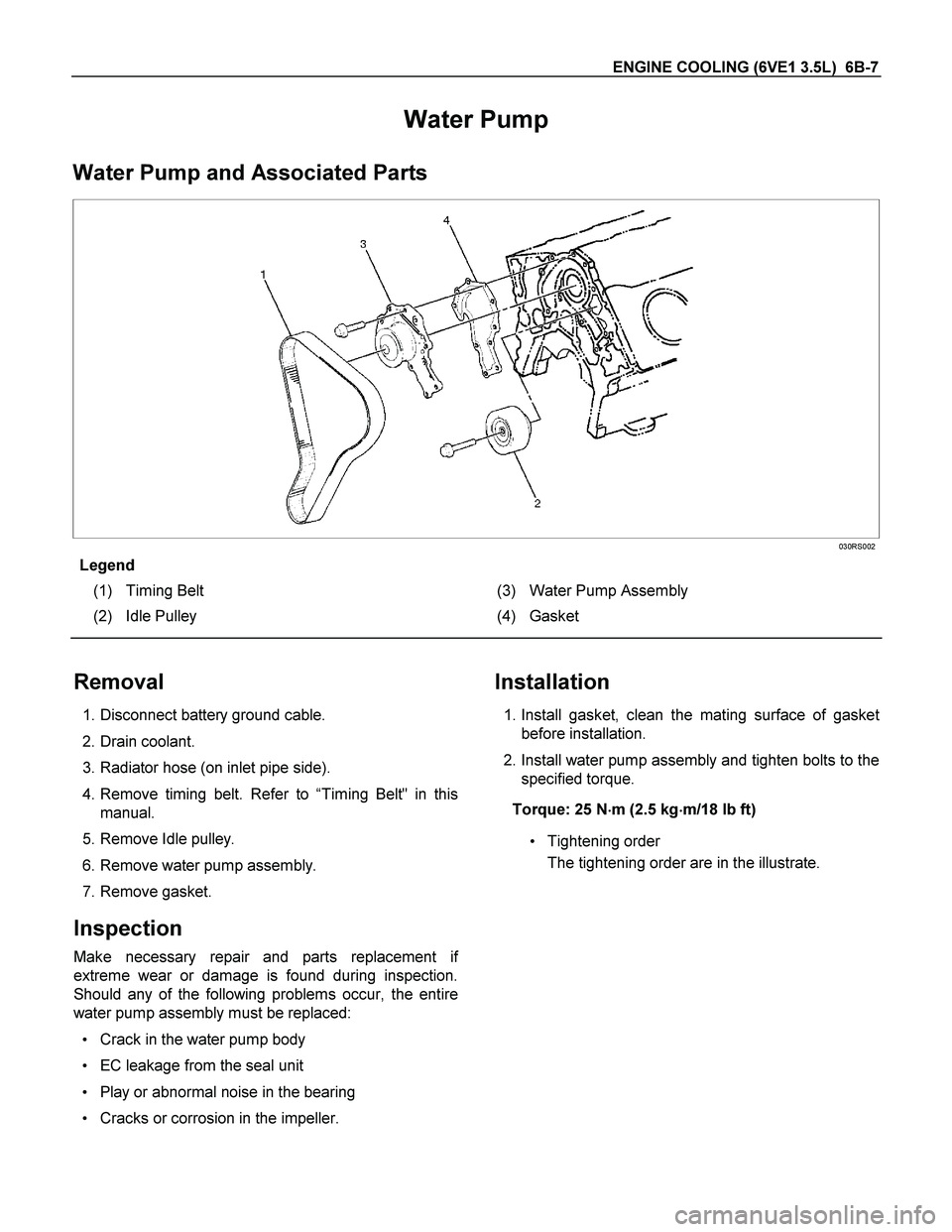
ENGINE COOLING (6VE1 3.5L) 6B-7
Water Pump
Water Pump and Associated Parts
030RS002
Legend
(1) Timing Belt (3) Water Pump Assembly
(2) Idle Pulley (4) Gasket
Removal
1. Disconnect battery ground cable.
2. Drain coolant.
3. Radiator hose (on inlet pipe side).
4. Remove timing belt. Refer to “Timing Belt" in this
manual.
5. Remove Idle pulley.
6. Remove water pump assembly.
7. Remove gasket.
Inspection
Make necessary repair and parts replacement if
extreme wear or damage is found during inspection.
Should any of the following problems occur, the entire
water pump assembly must be replaced:
Crack in the water pump body
EC leakage from the seal unit
Play or abnormal noise in the bearing
Cracks or corrosion in the impeller.
Installation
1. Install gasket, clean the mating surface of gasket
before installation.
2. Install water pump assembly and tighten bolts to the
specified torque.
Torque: 25 N
m (2.5 kg
m/18 lb ft)
Tightening order
The tightening order are in the illustrate.
Page 1933 of 4264
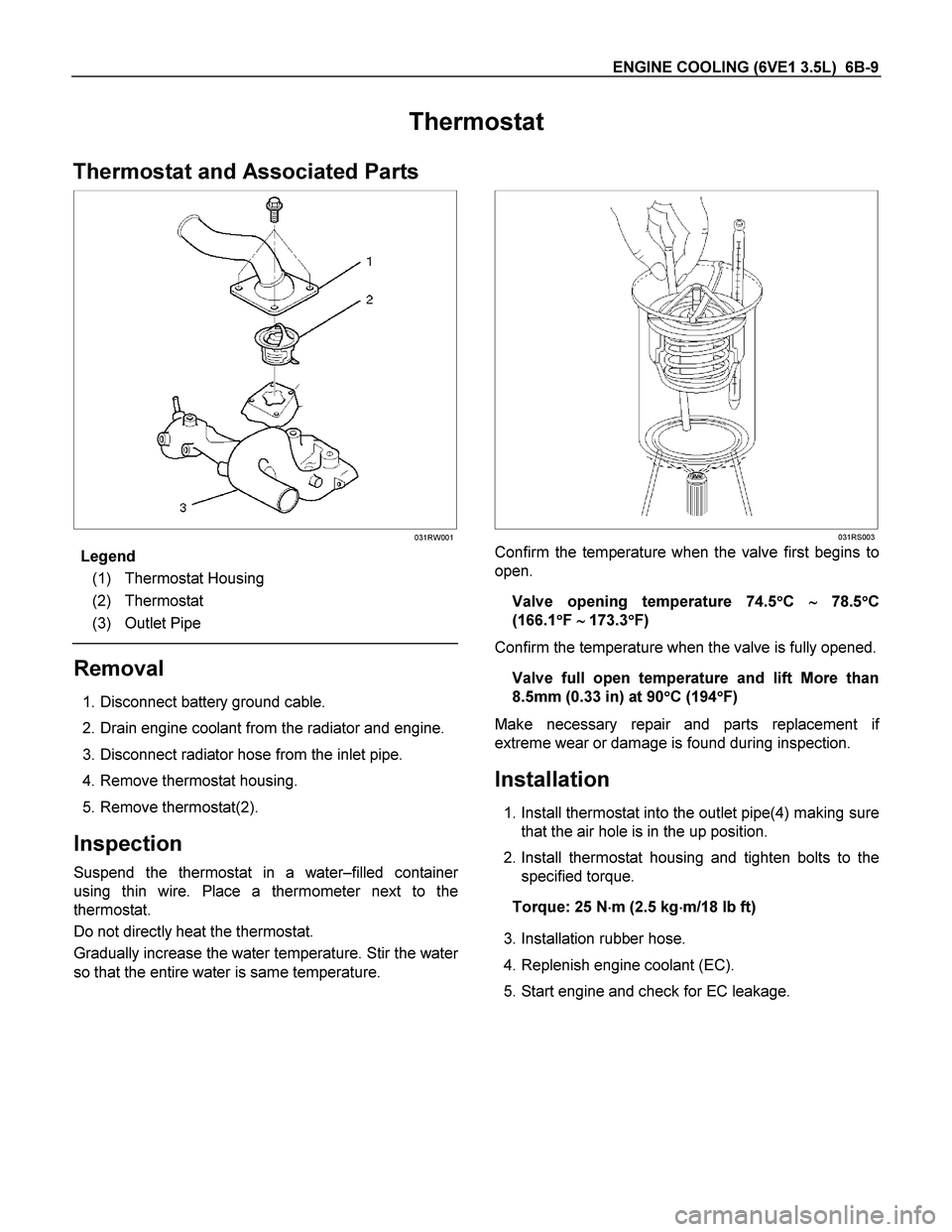
ENGINE COOLING (6VE1 3.5L) 6B-9
Thermostat
Thermostat and Associated Parts
031RW001
Legend
(1) Thermostat Housing
(2) Thermostat
(3) Outlet Pipe
Removal
1. Disconnect battery ground cable.
2. Drain engine coolant from the radiator and engine.
3. Disconnect radiator hose from the inlet pipe.
4. Remove thermostat housing.
5. Remove thermostat(2).
Inspection
Suspend the thermostat in a water–filled container
using thin wire. Place a thermometer next to the
thermostat.
Do not directly heat the thermostat.
Gradually increase the water temperature. Stir the wate
r
so that the entire water is same temperature.
031RS003
Confirm the temperature when the valve first begins to
open.
Valve opening temperature 74.5
C
78.5
C
(166.1
F
173.3
F)
Confirm the temperature when the valve is fully opened.
Valve full open temperature and lift More than
8.5mm (0.33 in) at 90
C (194
F)
Make necessary repair and parts replacement i
f
extreme wear or damage is found during inspection.
Installation
1. Install thermostat into the outlet pipe(4) making sure
that the air hole is in the up position.
2. Install thermostat housing and tighten bolts to the
specified torque.
Torque: 25 N
m (2.5 kg
m/18 lb ft)
3. Installation rubber hose.
4. Replenish engine coolant (EC).
5. Start engine and check for EC leakage.
Page 1959 of 4264
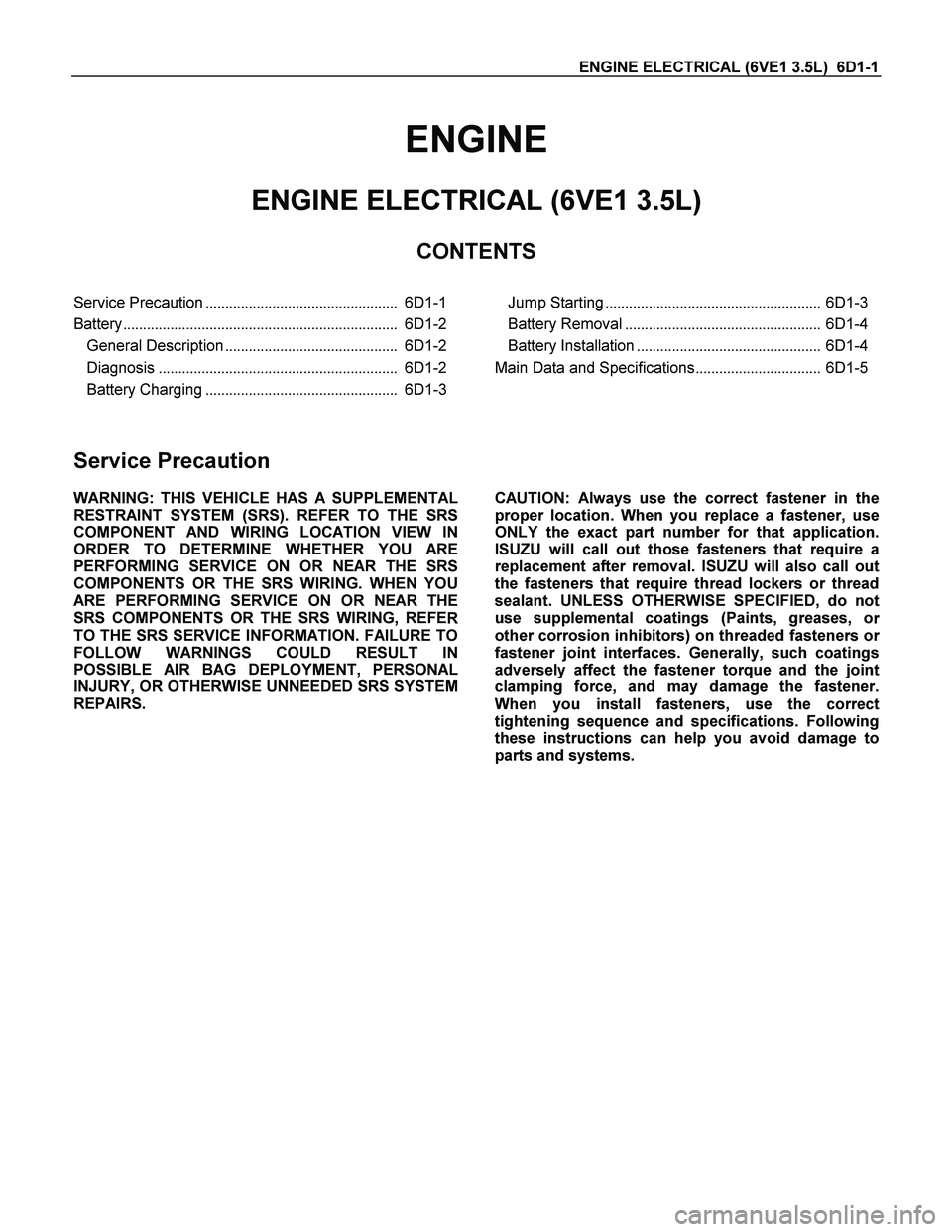
ENGINE ELECTRICAL (6VE1 3.5L) 6D1-1
ENGINE
ENGINE ELECTRICAL (6VE1 3.5L)
CONTENTS
Service Precaution................................................. 6D1-1
Battery...................................................................... 6D1-2
General Description............................................ 6D1-2
Diagnosis............................................................. 6D1-2
Battery Charging................................................. 6D1-3
Jump Starting....................................................... 6D1-3
Battery Removal.................................................. 6D1-4
Battery Installation............................................... 6D1-4
Main Data and Specifications................................ 6D1-5
Service Precaution
WARNING: THIS VEHICLE HAS A SUPPLEMENTAL
RESTRAINT SYSTEM (SRS). REFER TO THE SRS
COMPONENT AND WIRING LOCATION VIEW IN
ORDER TO DETERMINE WHETHER YOU ARE
PERFORMING SERVICE ON OR NEAR THE SRS
COMPONENTS OR THE SRS WIRING. WHEN YOU
ARE PERFORMING SERVICE ON OR NEAR THE
SRS COMPONENTS OR THE SRS WIRING, REFE
R
TO THE SRS SERVICE INFORMATION. FAILURE TO
FOLLOW WARNINGS COULD RESULT IN
POSSIBLE AIR BAG DEPLOYMENT, PERSONAL
INJURY, OR OTHERWISE UNNEEDED SRS SYSTEM
REPAIRS.
CAUTION: Always use the correct fastener in the
proper location. When you replace a fastener, use
ONLY the exact part number for that application.
ISUZU will call out those fasteners that require a
replacement after removal. ISUZU will also call out
the fasteners that require thread lockers or thread
sealant. UNLESS OTHERWISE SPECIFIED, do not
use supplemental coatings (Paints, greases, o
r
other corrosion inhibitors) on threaded fasteners or
fastener joint interfaces. Generally, such coatings
adversely affect the fastener torque and the joint
clamping force, and may damage the fastener.
When you install fasteners, use the correct
tightening sequence and specifications. Following
these instructions can help you avoid damage to
parts and systems.
Page 2054 of 4264
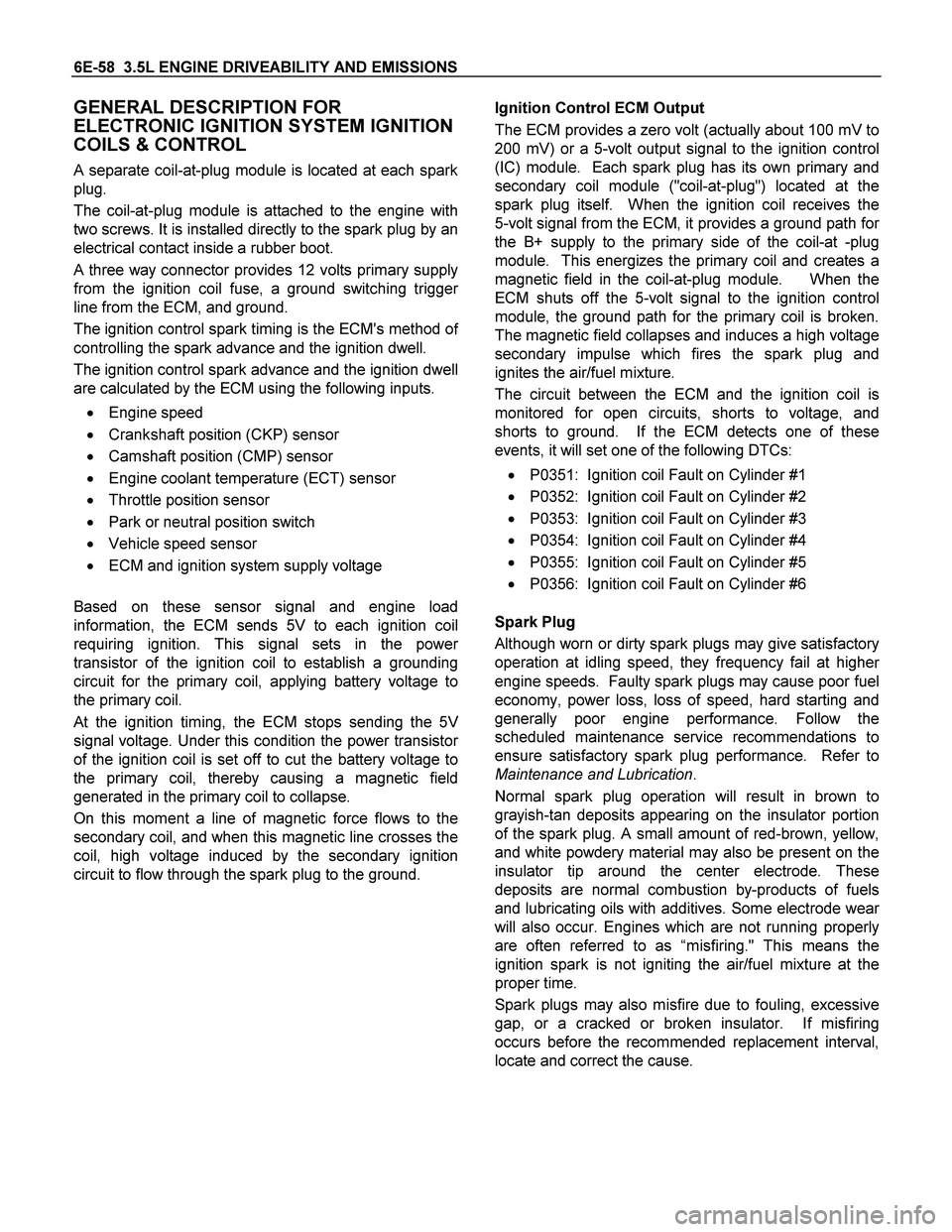
6E-58 3.5L ENGINE DRIVEABILITY AND EMISSIONS
GENERAL DESCRIPTION FOR
ELECTRONIC IGNITION SYSTEM IGNITION
COILS & CONTROL
A separate coil-at-plug module is located at each spark
plug.
The coil-at-plug module is attached to the engine with
two screws. It is installed directly to the spark plug by an
electrical contact inside a rubber boot.
A three way connector provides 12 volts primary supply
from the ignition coil fuse, a ground switching trigge
r
line from the ECM, and ground.
The ignition control spark timing is the ECM's method o
f
controlling the spark advance and the ignition dwell.
The ignition control spark advance and the ignition dwell
are calculated by the ECM using the following inputs.
Engine speed
Crankshaft position (CKP) sensor
Camshaft position (CMP) sensor
Engine coolant temperature (ECT) sensor
Throttle position sensor
Park or neutral position switch
Vehicle speed sensor
ECM and ignition system supply voltage
Based on these sensor signal and engine load
information, the ECM sends 5V to each ignition coil
requiring ignition. This signal sets in the powe
r
transistor of the ignition coil to establish a grounding
circuit for the primary coil, applying battery voltage to
the primary coil.
At the ignition timing, the ECM stops sending the 5V
signal voltage. Under this condition the power transistor
of the ignition coil is set off to cut the battery voltage to
the primary coil, thereby causing a magnetic field
generated in the primary coil to collapse.
On this moment a line of magnetic force flows to the
secondary coil, and when this magnetic line crosses the
coil, high voltage induced by the secondary ignition
circuit to flow through the spark plug to the ground.
Ignition Control ECM Output
The ECM provides a zero volt (actually about 100 mV to
200 mV) or a 5-volt output signal to the ignition control
(IC) module. Each spark plug has its own primary and
secondary coil module ("coil-at-plug") located at the
spark plug itself. When the ignition coil receives the
5-volt signal from the ECM, it provides a ground path fo
r
the B+ supply to the primary side of the coil-at -plug
module. This energizes the primary coil and creates a
magnetic field in the coil-at-plug module. When the
ECM shuts off the 5-volt signal to the ignition control
module, the ground path for the primary coil is broken.
The magnetic field collapses and induces a high voltage
secondary impulse which fires the spark plug and
ignites the air/fuel mixture.
The circuit between the ECM and the ignition coil is
monitored for open circuits, shorts to voltage, and
shorts to ground. If the ECM detects one of these
events, it will set one of the following DTCs:
P0351: Ignition coil Fault on Cylinder #1
P0352: Ignition coil Fault on Cylinder #2
P0353: Ignition coil Fault on Cylinder #3
P0354: Ignition coil Fault on Cylinder #4
P0355: Ignition coil Fault on Cylinder #5
P0356: Ignition coil Fault on Cylinder #6
Spark Plug
Although worn or dirty spark plugs may give satisfactory
operation at idling speed, they frequency fail at highe
r
engine speeds. Faulty spark plugs may cause poor fuel
economy, power loss, loss of speed, hard starting and
generally poor engine performance. Follow the
scheduled maintenance service recommendations to
ensure satisfactory spark plug performance. Refer to
Maintenance and Lubrication.
Normal spark plug operation will result in brown to
grayish-tan deposits appearing on the insulator portion
of the spark plug. A small amount of red-brown, yellow,
and white powdery material may also be present on the
insulator tip around the center electrode. These
deposits are normal combustion by-products of fuels
and lubricating oils with additives. Some electrode wea
r
will also occur. Engines which are not running properly
are often referred to as “misfiring." This means the
ignition spark is not igniting the air/fuel mixture at the
proper time.
Spark plugs may also misfire due to fouling, excessive
gap, or a cracked or broken insulator. If misfiring
occurs before the recommended replacement interval,
locate and correct the cause.
Page 2065 of 4264
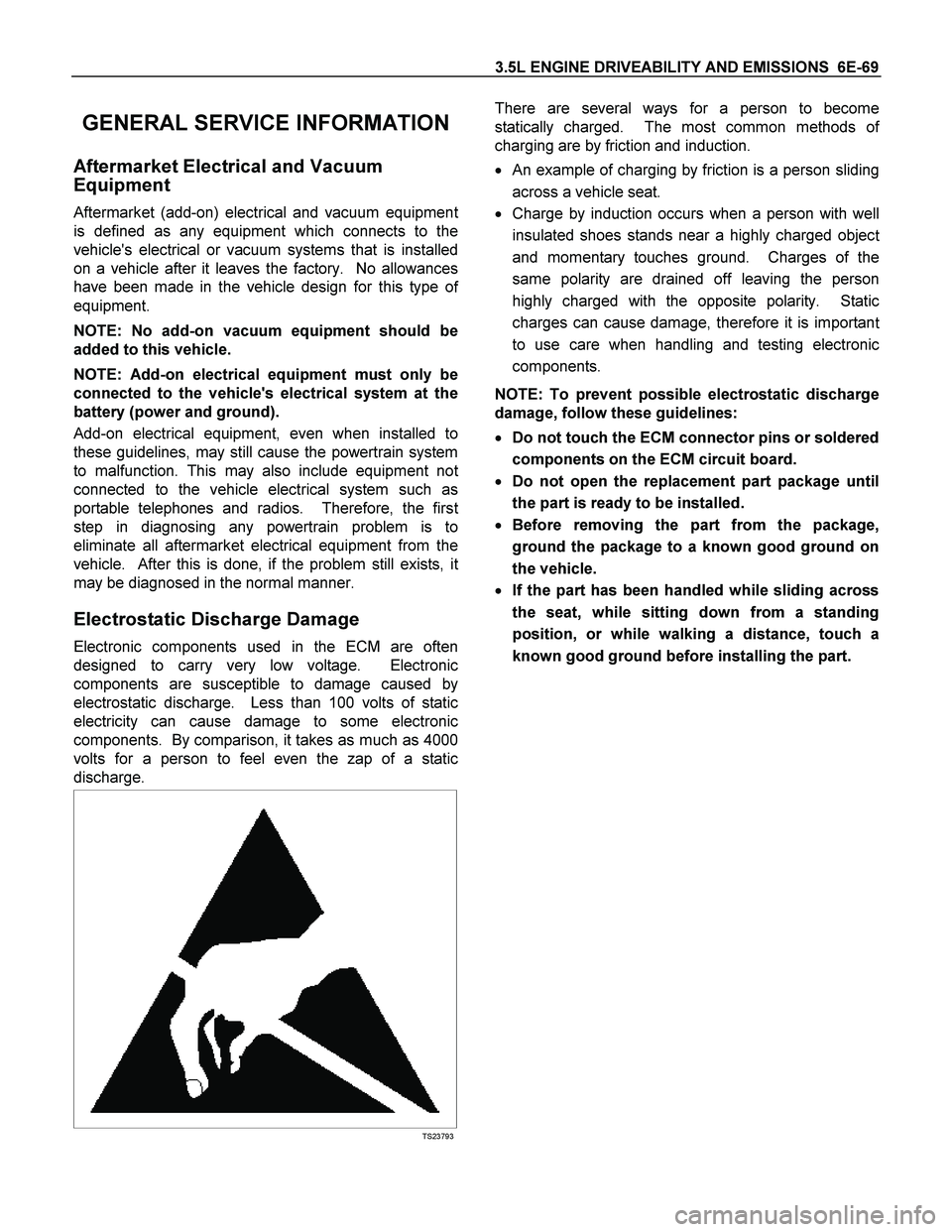
3.5L ENGINE DRIVEABILITY AND EMISSIONS 6E-69
GENERAL SERVICE INFORMATION
Aftermarket Electrical and Vacuum
Equipment
Aftermarket (add-on) electrical and vacuum equipment
is defined as any equipment which connects to the
vehicle's electrical or vacuum systems that is installed
on a vehicle after it leaves the factory. No allowances
have been made in the vehicle design for this type o
f
equipment.
NOTE: No add-on vacuum equipment should be
added to this vehicle.
NOTE: Add-on electrical equipment must only be
connected to the vehicle's electrical system at the
battery (power and ground).
Add-on electrical equipment, even when installed to
these guidelines, may still cause the powertrain system
to malfunction. This may also include equipment no
t
connected to the vehicle electrical system such as
portable telephones and radios. Therefore, the firs
t
step in diagnosing any powertrain problem is to
eliminate all aftermarket electrical equipment from the
vehicle. After this is done, if the problem still exists, i
t
may be diagnosed in the normal manner.
Electrostatic Discharge Damage
Electronic components used in the ECM are often
designed to carry very low voltage. Electronic
components are susceptible to damage caused by
electrostatic discharge. Less than 100 volts of static
electricity can cause damage to some electronic
components. By comparison, it takes as much as 4000
volts for a person to feel even the zap of a static
discharge.
TS23793
There are several ways for a person to become
statically charged. The most common methods o
f
charging are by friction and induction.
An example of charging by friction is a person sliding
across a vehicle seat.
Charge by induction occurs when a person with well
insulated shoes stands near a highly charged objec
t
and momentary touches ground. Charges of the
same polarity are drained off leaving the person
highly charged with the opposite polarity. Static
charges can cause damage, therefore it is importan
t
to use care when handling and testing electronic
components.
NOTE: To prevent possible electrostatic discharge
damage, follow these guidelines:
Do not touch the ECM connector pins or soldered
components on the ECM circuit board.
Do not open the replacement part package until
the part is ready to be installed.
Before removing the part from the package,
ground the package to a known good ground on
the vehicle.
If the part has been handled while sliding across
the seat, while sitting down from a standing
position, or while walking a distance, touch a
known good ground before installing the part.
Page 2087 of 4264
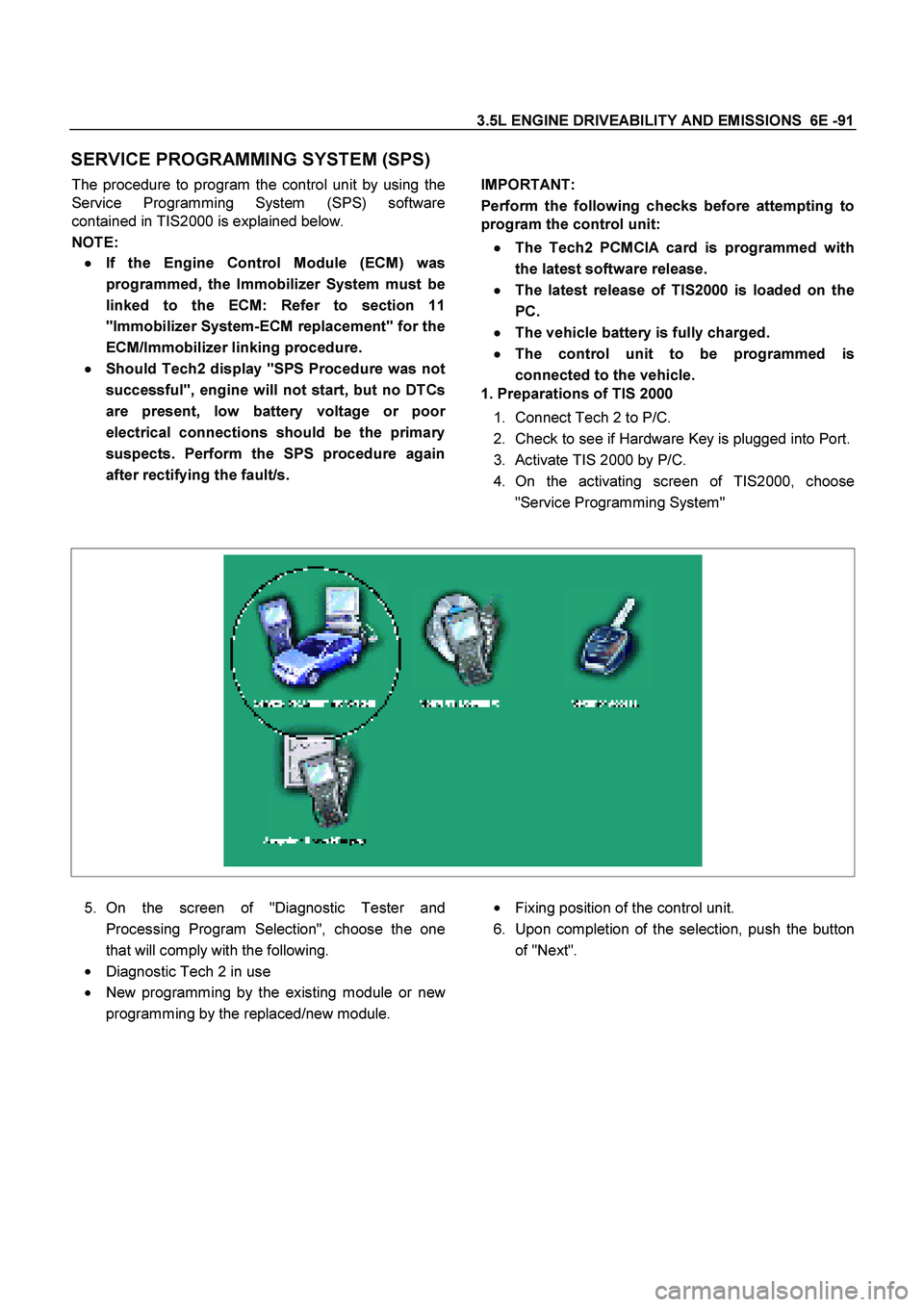
3.5L ENGINE DRIVEABILITY AND EMISSIONS 6E -91
SERVICE PROGRAMMING SYSTEM (SPS)
The procedure to program the control unit by using the
Service Programming System (SPS) software
contained in TIS2000 is explained below.
NOTE:
If the Engine Control Module (ECM) was
programmed, the Immobilizer System must be
linked to the ECM: Refer to section 11
"Immobilizer System-ECM replacement" for the
ECM/Immobilizer linking procedure.
Should Tech2 display "SPS Procedure was not
successful", engine will not start, but no DTCs
are present, low battery voltage or poo
r
electrical connections should be the primary
suspects. Perform the SPS procedure again
after rectifying the fault/s.
IMPORTANT:
Perform the following checks before attempting to
program the control unit:
The Tech2 PCMCIA card is programmed with
the latest software release.
The latest release of TIS2000 is loaded on the
PC.
The vehicle battery is fully charged.
The control unit to be programmed is
connected to the vehicle.
1. Preparations of TIS 2000
1.
Connect Tech 2 to P/C.
2.
Check to see if Hardware Key is plugged into Port.
3.
Activate TIS 2000 by P/C.
4.
On the activating screen of TIS2000, choose
"Service Programming System"
5.
On the screen of "Diagnostic Tester and
Processing Program Selection", choose the one
that will comply with the following.
Diagnostic Tech 2 in use
New programming by the existing module or new
programming by the replaced/new module.
Fixing position of the control unit.
6.
Upon completion of the selection, push the button
of "Next".
Page 2229 of 4264
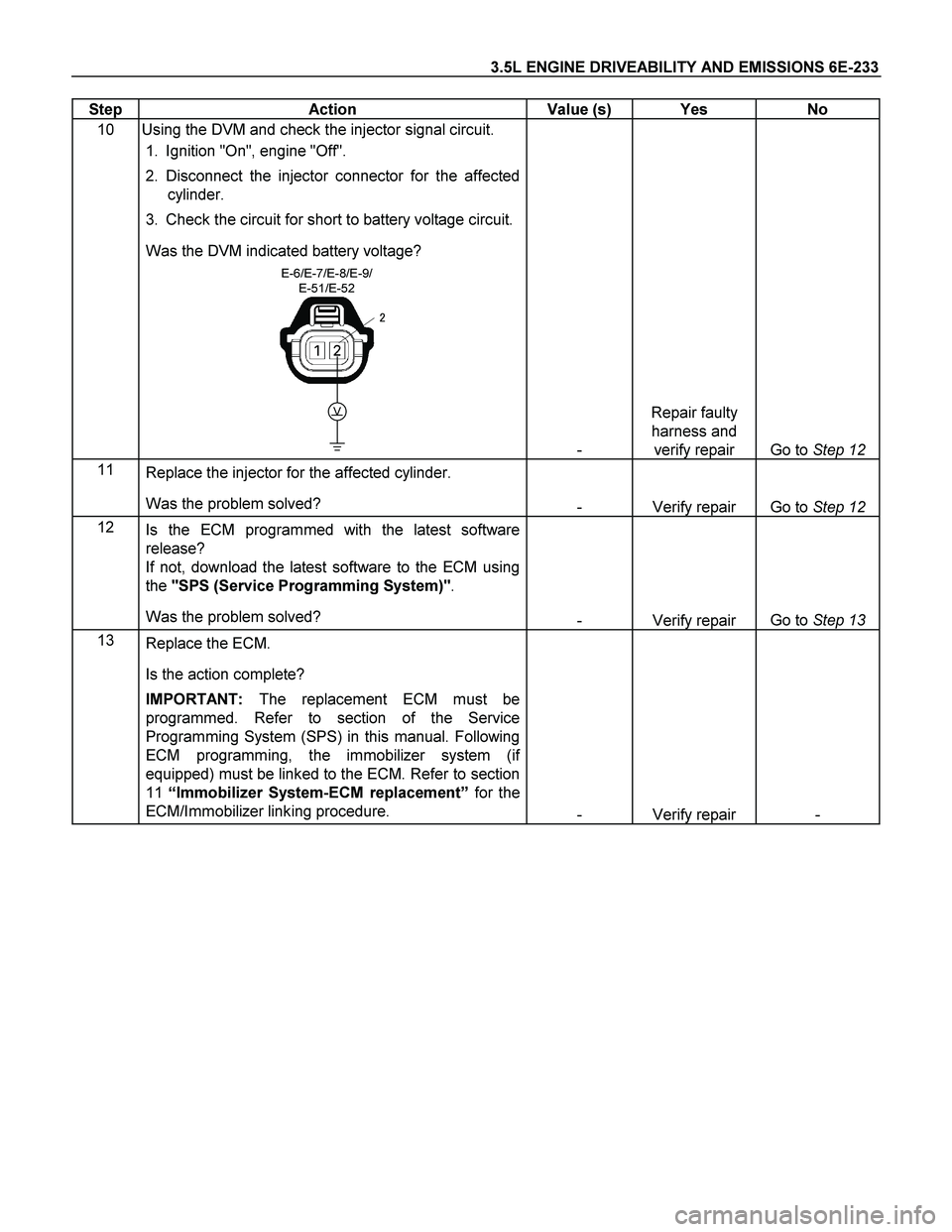
3.5L ENGINE DRIVEABILITY AND EMISSIONS 6E-233
Step Action Value (s) Yes No
10 Using the DVM and check the injector signal circuit.
1. Ignition "On", engine "Off".
2. Disconnect the injector connector for the affected
cylinder.
3. Check the circuit for short to battery voltage circuit.
Was the DVM indicated battery voltage?
E-6/E-7/E-8/E-9/
E-51/E-52
V
- Repair faulty
harness and
verify repair Go to Step 12
11
Replace the injector for the affected cylinder.
Was the problem solved?
- Verify repair Go to Step 12
12
Is the ECM programmed with the latest software
release?
If not, download the latest software to the ECM using
the "SPS (Service Programming System)".
Was the problem solved?
- Verify repair Go to Step 13
13
Replace the ECM.
Is the action complete?
IMPORTANT: The replacement ECM must be
programmed. Refer to section of the Service
Programming System (SPS) in this manual. Following
ECM programming, the immobilizer system (if
equipped) must be linked to the ECM. Refer to section
11 “Immobilizer System-ECM replacement” for the
ECM/Immobilizer linking procedure.
- Verify repair -