check engine ISUZU TF SERIES 2004 Workshop Manual
[x] Cancel search | Manufacturer: ISUZU, Model Year: 2004, Model line: TF SERIES, Model: ISUZU TF SERIES 2004Pages: 4264, PDF Size: 72.63 MB
Page 2838 of 4264
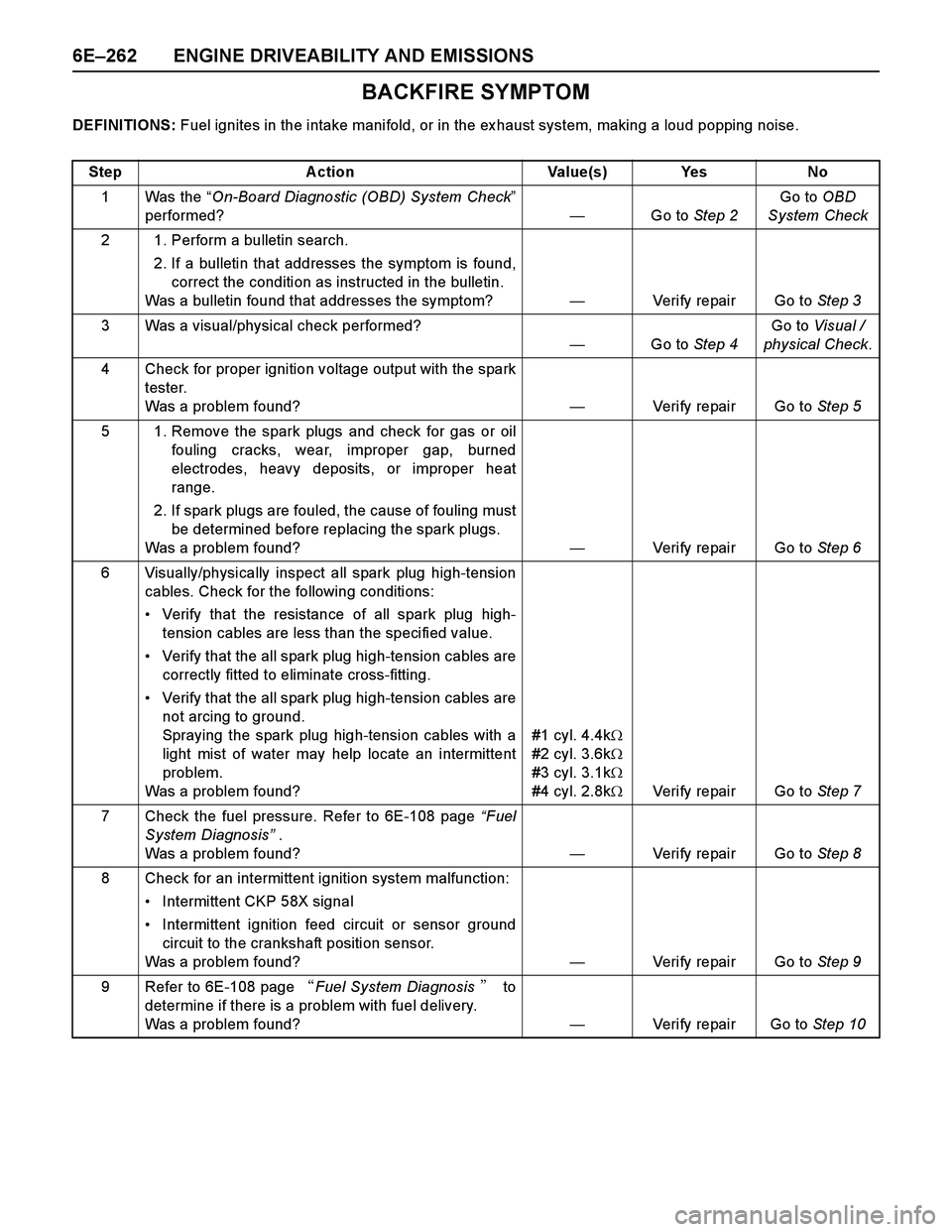
6E–262 ENGINE DRIVEABILITY AND EMISSIONS
BACKFIRE SYMPTOM
DEFINITIONS: Fuel ignites in the intake manifold, or in the ex haust system, making a loud popping noise.
Step Action Value(s) Yes No
1Was the “On-Board Diagnostic (OBD) System Check”
performed?—Go to Step 2Go to OBD
System Check
2 1. Perform a bulletin search.
2. If a bulletin that addresses the symptom is found,
correct the condition as instructed in the bulletin.
Was a bulletin found that addresses the symptom?—Verify repair Go to Step 3
3 Was a visual/physical check performed?
—Go to Step 4Go to Visual /
physical Check.
4 Check for proper ignition voltage output with the spark
tester.
Was a problem found?—Verify repair Go to Step 5
5 1. Remove the spark plugs and check for gas or oil
fouling cracks, wear, improper gap, burned
electrodes, heavy deposits, or improper heat
range.
2. If spark plugs are fouled, the cause of fouling must
be determined before replacing the spark plugs.
Was a problem found?—Verify repair Go to Step 6
6 Visually/physically inspect all spark plug high-tension
cables. Check for the following conditions:
Verify that the resistance of all spark plug high-
tension cables are less than the specified value.
Verify that the all spark plug high-tension cables are
correctly fitted to eliminate cross-fitting.
Verify that the all spark plug high-tension cables are
not arcing to ground.
Spraying the spark plug high-tension cables with a
light mist of water may help locate an intermittent
problem.
Was a problem found?#1 cyl. 4.4k
#2 cyl. 3.6k
#3 cyl. 3.1k
#4 cyl. 2.8kVerify repair Go to Step 7
7 Check the fuel pressure. Refer to 6E-108 page “Fuel
System Diagnosis” .
Was a problem found?—Verify repair Go to Step 8
8 Check for an intermittent ignition system malfunction:
Intermittent CKP 58X signal
Intermittent ignition feed circuit or sensor ground
circuit to the crankshaft position sensor.
Was a problem found?—Verify repair Go to Step 9
9 Refer to 6E-108 page Fuel System Diagnosis to
determine if there is a problem with fuel delivery.
Was a problem found?—Verify repair Go to Step 10
Page 2839 of 4264
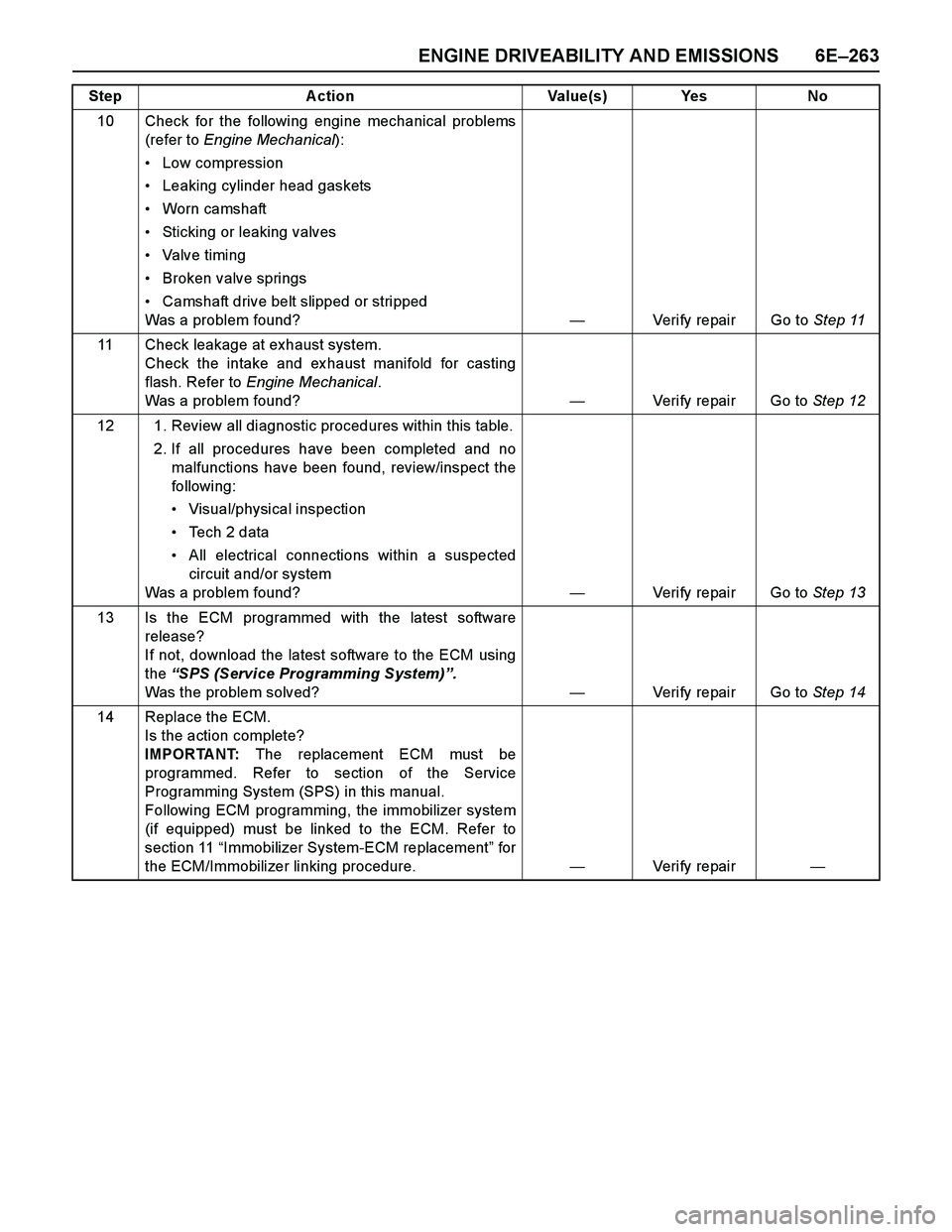
ENGINE DRIVEABILITY AND EMISSIONS 6E–263
10 Check for the following engine mechanical problems
(refer to Engine Mechanical):
Low compression
Leaking cylinder head gaskets
Worn camshaft
Sticking or leaking valves
Valve timing
Broken valve springs
Camshaft drive belt slipped or stripped
Was a problem found?—Verify repair Go to Step 11
11 Check leakage at exhaust system.
Check the intake and ex haust manifold for casting
flash. Refer to Engine Mechanical.
Was a problem found?—Verify repair Go to Step 12
12 1. Review all diagnostic procedures within this table.
2. If all procedures have been completed and no
malfunctions have been found, review/inspect the
followi ng:
Visual/physical inspection
Te c h 2 d a t a
All electrical connections within a suspected
circuit and/or system
Was a problem found?—Verify repair Go to Step 13
13 Is the ECM programmed with the latest software
release?
If not, download the latest software to the ECM using
the “SPS (Service Programming System)”.
Was the problem solved?—Verify repair Go to Step 14
14 Replace the ECM.
Is the action complete?
IMPORTANT: The replacement ECM must be
programmed. Refer to section of the Service
Programming System (SPS) in this manual.
Following ECM programming, the immobilizer system
(if equipped) must be linked to the ECM. Refer to
section 11 “Immobilizer System-ECM replacement” for
the ECM/Immobilizer linking procedure.—Veri fy repai r— Step Action Value(s) Yes No
Page 2842 of 4264
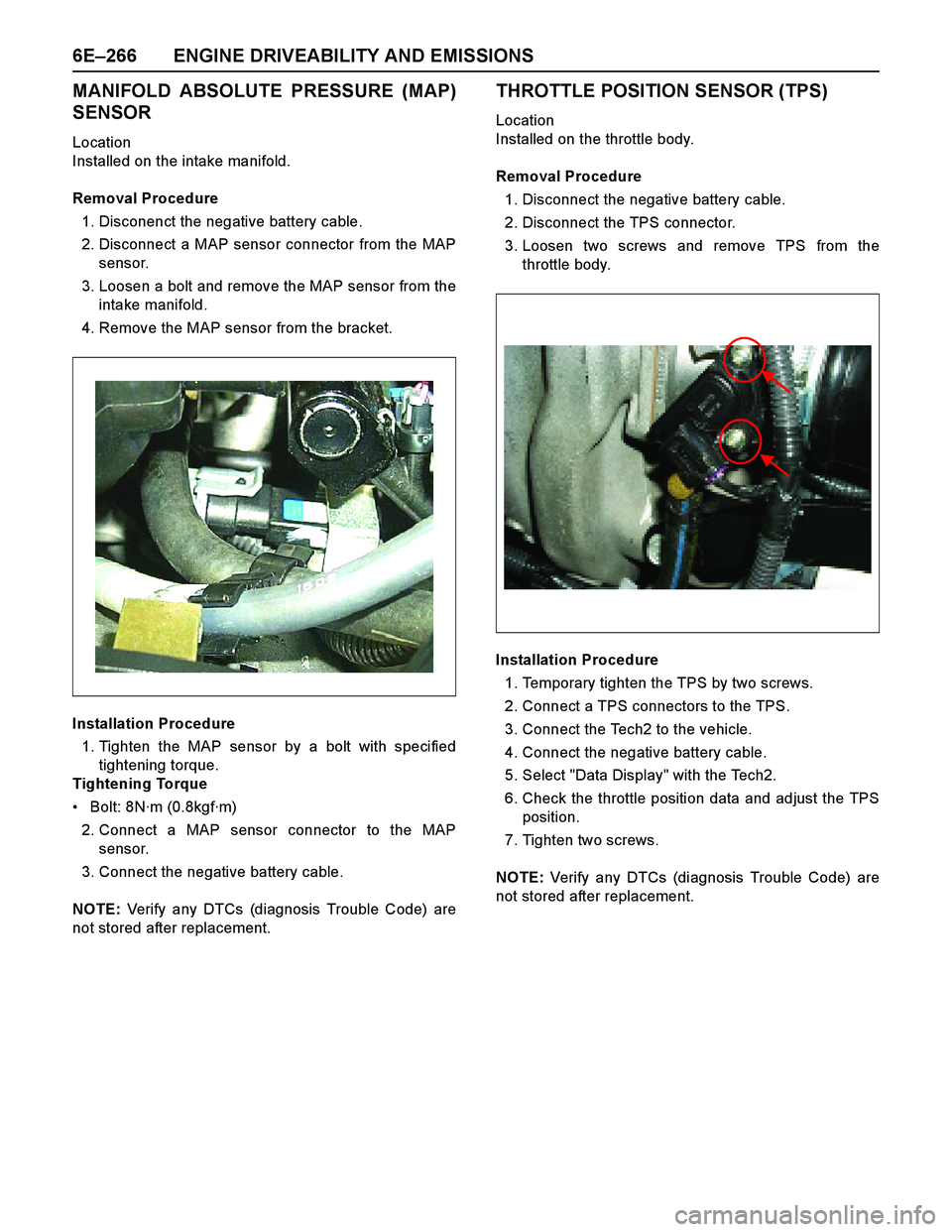
6E–266 ENGINE DRIVEABILITY AND EMISSIONS
MANIFOLD ABSOLUTE PRESSURE (MAP)
SENSOR
Location
Installed on the intake manifold.
Removal Procedure
1. Disconenct the negative battery cable.
2. Disconnect a MAP sensor connector from the MAP
sensor.
3. Loosen a bolt and remove the MAP sensor from the
intake manifold.
4. Remove the MAP sensor from the bracket.
Installation Procedure
1. Tighten the MAP sensor by a bolt with specified
tightening torque.
Tightening Torque
Bolt: 8N·m (0.8kgf·m)
2. Connect a MAP sensor connector to the MAP
sensor.
3. Connect the negative battery cable.
NOTE: Verify any DTCs (diagnosis Trouble Code) are
not stored after replacement.
THROTTLE POSITION SENSOR (TPS)
Location
Installed on the throttle body.
Removal Procedure
1. Disconnect the negative battery cable.
2. Disconnect the TPS connector.
3. Loosen two screws and remove TPS from the
throttle body.
Installation Procedure
1. Temporary tighten the TPS by two screws.
2. Connect a TPS connectors to the TPS.
3. Connect the Tech2 to the vehicle.
4. Connect the negative battery cable.
5. Select "Data Display" with the Tech2.
6. Check the throttle position data and adjust the TPS
position.
7. Tighten two screws.
NOTE: Verify any DTCs (diagnosis Trouble Code) are
not stored after replacement.
Page 2847 of 4264
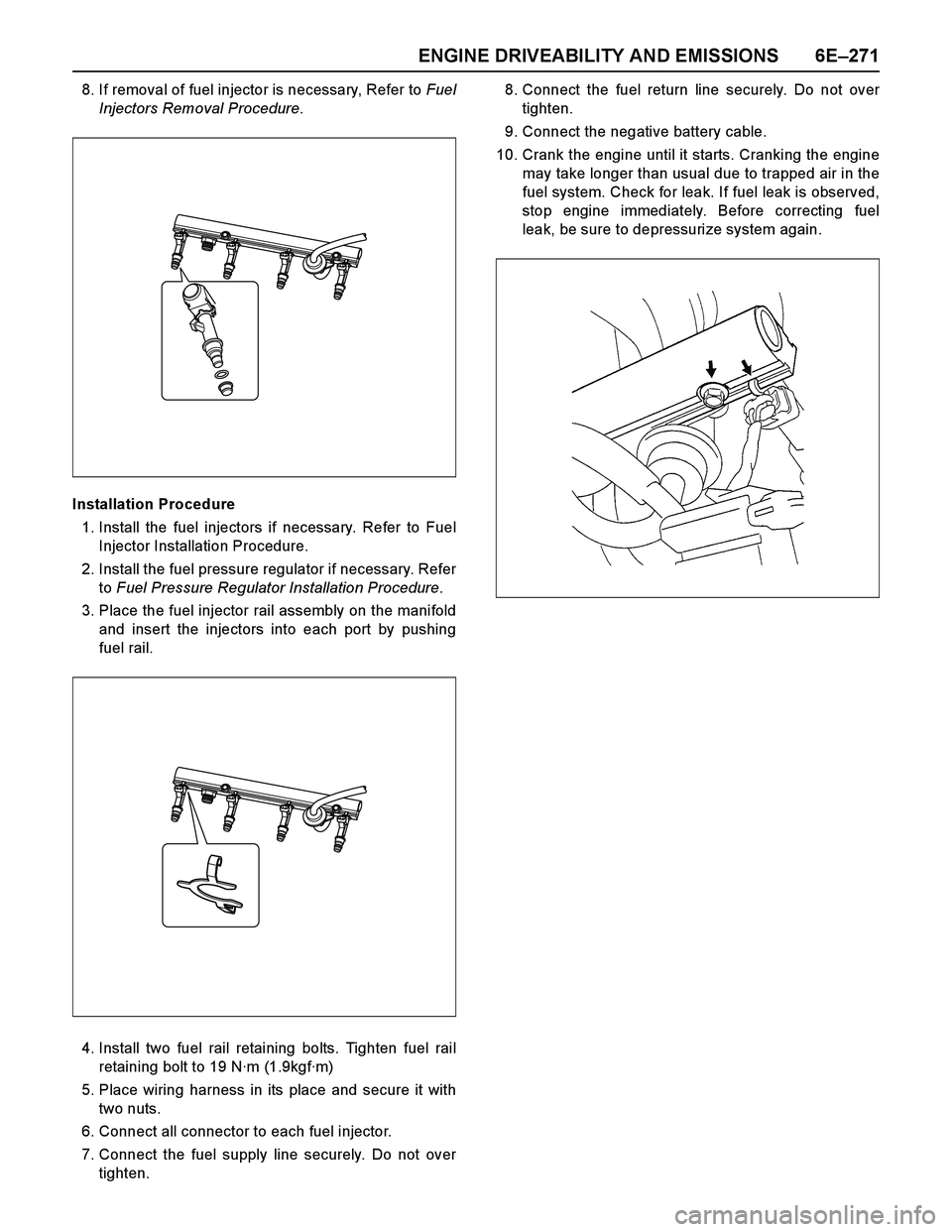
ENGINE DRIVEABILITY AND EMISSIONS 6E–271
8. If removal of fuel injector is necessary, Refer to Fuel
Injectors Removal Procedure.
Installation Procedure
1. Install the fuel injectors if necessary. Refer to Fuel
Injector Installation Procedure.
2. Install the fuel pressure regulator if necessary. Refer
to Fuel Pressure Regulator Installation Procedure.
3. Place the fuel injector rail assembly on the manifold
and insert the injectors into each port by pushing
fuel rail.
4. Install two fuel rail retaining bolts. Tighten fuel rail
retaining bolt to 19 N·m (1.9kgf·m)
5. Place wiring harness in its place and secure it with
two nuts.
6. Connect all connector to each fuel injector.
7. Connect the fuel supply line securely. Do not over
tighten.8. Connect the fuel return line securely. Do not over
tighten.
9. Connect the negative battery cable.
10. Crank the engine until it starts. Cranking the engine
may take longer than usual due to trapped air in the
fuel system. Check for leak. If fuel leak is observed,
stop engine immediately. Before correcting fuel
leak, be sure to depressurize system again.
Page 2848 of 4264
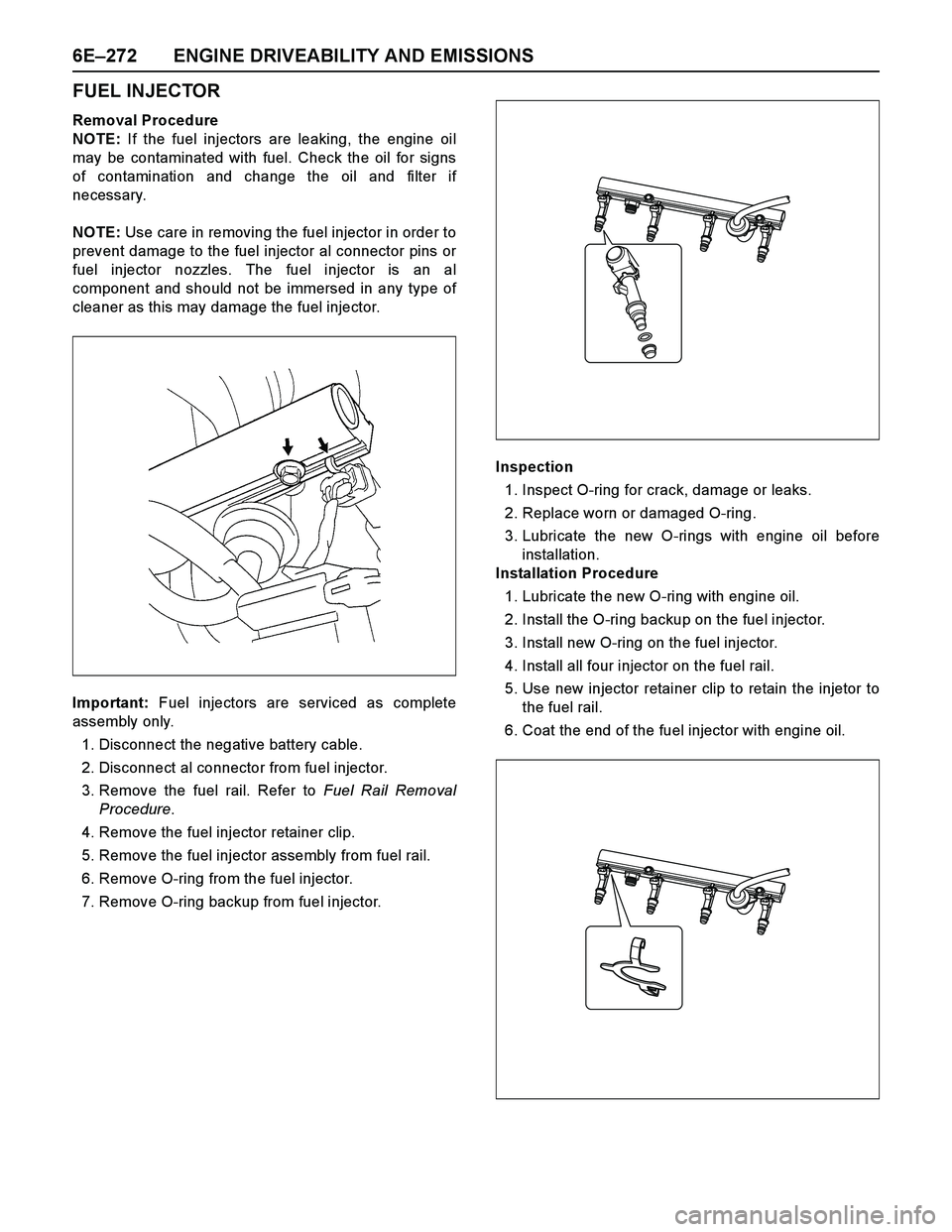
6E–272 ENGINE DRIVEABILITY AND EMISSIONS
FUEL INJECTOR
Removal Procedure
NOTE: If the fuel injectors are leaking, the engine oil
may be contaminated with fuel. Check the oil for signs
of contamination and change the oil and filter if
necessary.
NOTE: Use care in removing the fuel injector in order to
prevent damage to the fuel injector al connector pins or
fuel injector nozzles. The fuel injector is an al
component and should not be immersed in any type of
cleaner as this may damage the fuel injector.
Important: Fuel injectors are serviced as complete
assembly only.
1. Disconnect the negative battery cable.
2. Disconnect al connector from fuel injector.
3. Remove the fuel rail. Refer to Fuel Rail Removal
Procedure.
4. Remove the fuel injector retainer clip.
5. Remove the fuel injector assembly from fuel rail.
6. Remove O-ring from the fuel injector.
7. Remove O-ring backup from fuel injector.Inspection
1. Inspect O-ring for crack, damage or leaks.
2. Replace worn or damaged O-ring.
3. Lubricate the new O-rings with engine oil before
installation.
Installation Procedure
1. Lubricate the new O-ring with engine oil.
2. Install the O-ring backup on the fuel injector.
3. Install new O-ring on the fuel injector.
4. Install all four injector on the fuel rail.
5. Use new injector retainer clip to retain the injetor to
the fuel rail.
6. Coat the end of the fuel injector with engine oil.
Page 2851 of 4264
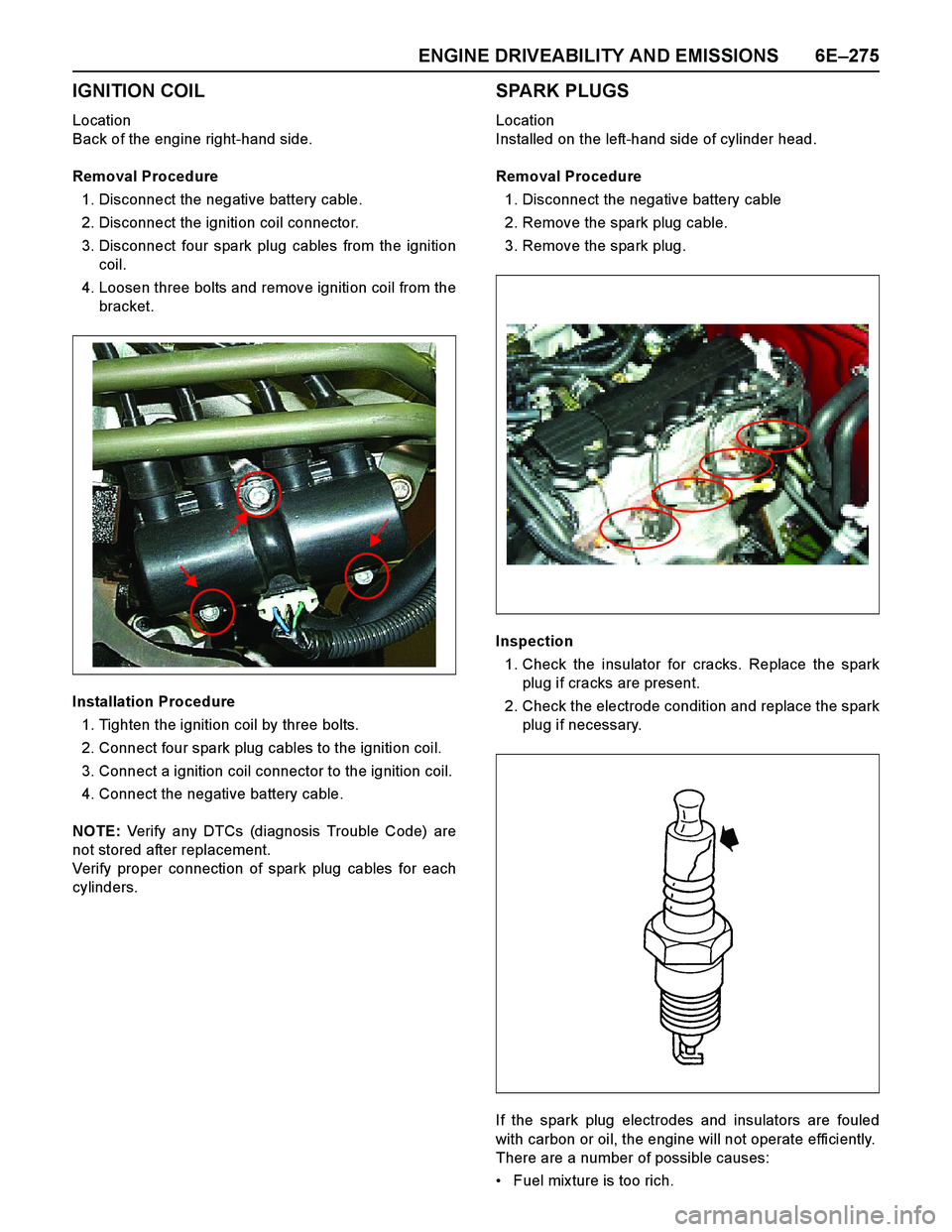
ENGINE DRIVEABILITY AND EMISSIONS 6E–275
IGNITION COIL
Location
Back of the engine right-hand side.
Removal Procedure
1. Disconnect the negative battery cable.
2. Disconnect the ignition coil connector.
3. Disconnect four spark plug cables from the ignition
coil.
4. Loosen three bolts and remove ignition coil from the
bracket.
Installation Procedure
1. Tighten the ignition coil by three bolts.
2. Connect four spark plug cables to the ignition coil.
3. Connect a ignition coil connector to the ignition coil.
4. Connect the negative battery cable.
NOTE: Verify any DTCs (diagnosis Trouble Code) are
not stored after replacement.
Verify proper connection of spark plug cables for each
cylinders.
SPARK PLUGS
Location
Installed on the left-hand side of cylinder head.
Removal Procedure
1. Disconnect the negative battery cable
2. Remove the spark plug cable.
3. Remove the spark plug.
Inspection
1. Check the insulator for cracks. Replace the spark
plug if cracks are present.
2. Check the electrode condition and replace the spark
plug if necessary.
If the spark plug electrodes and insulators are fouled
with carbon or oil, the engine will not operate efficiently.
There are a number of possible causes:
Fuel mix ture is too rich.
Page 2852 of 4264
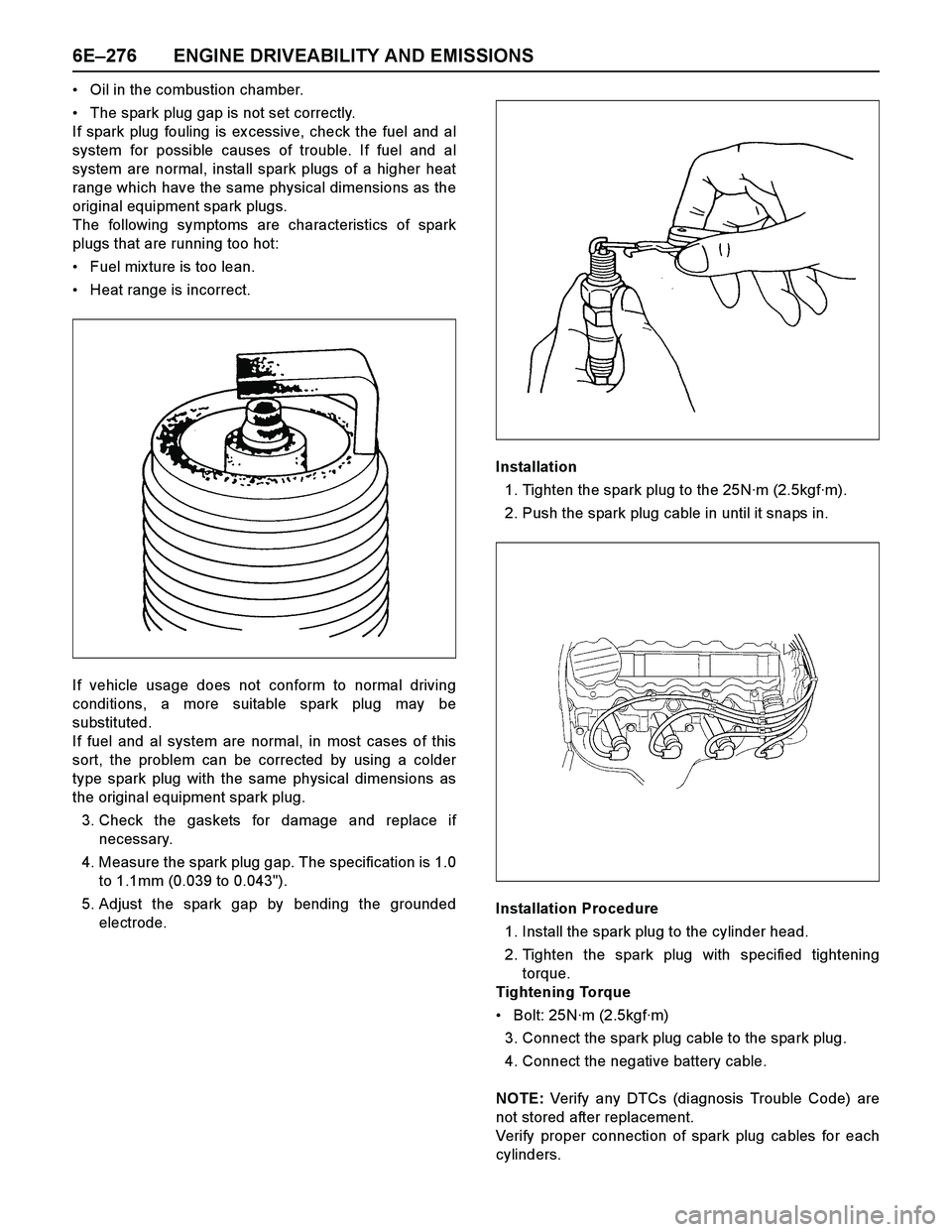
6E–276 ENGINE DRIVEABILITY AND EMISSIONS
Oil in the combustion chamber.
The spark plug gap is not set correctly.
If spark plug fouling is ex cessive, check the fuel and al
system for possible causes of trouble. If fuel and al
system are normal, install spark plugs of a higher heat
range which have the same physical dimensions as the
original equipment spark plugs.
The following symptoms are characteristics of spark
plugs that are running too hot:
Fuel mixture is too lean.
Heat range is incorrect.
If vehicle usage does not conform to normal driving
conditions, a more suitable spark plug may be
substituted.
If fuel and al system are normal, in most cases of this
sort, the problem can be corrected by using a colder
type spark plug with the same physical dimensions as
the original equipment spark plug.
3. Check the gaskets for damage and replace if
necessary.
4. Measure the spark plug gap. The specification is 1.0
to 1.1mm (0.039 to 0.043").
5. Adjust the spark gap by bending the grounded
electrode.Installation
1. Tighten the spark plug to the 25N·m (2.5kgf·m).
2. Push the spark plug cable in until it snaps in.
Installation Procedure
1. Install the spark plug to the cylinder head.
2. Tighten the spark plug with specified tightening
torque.
Tightening Torque
Bolt: 25N·m (2.5kgf·m)
3. Connect the spark plug cable to the spark plug.
4. Connect the negative battery cable.
NOTE: Verify any DTCs (diagnosis Trouble Code) are
not stored after replacement.
Verify proper connection of spark plug cables for each
cylinders.
Page 2853 of 4264
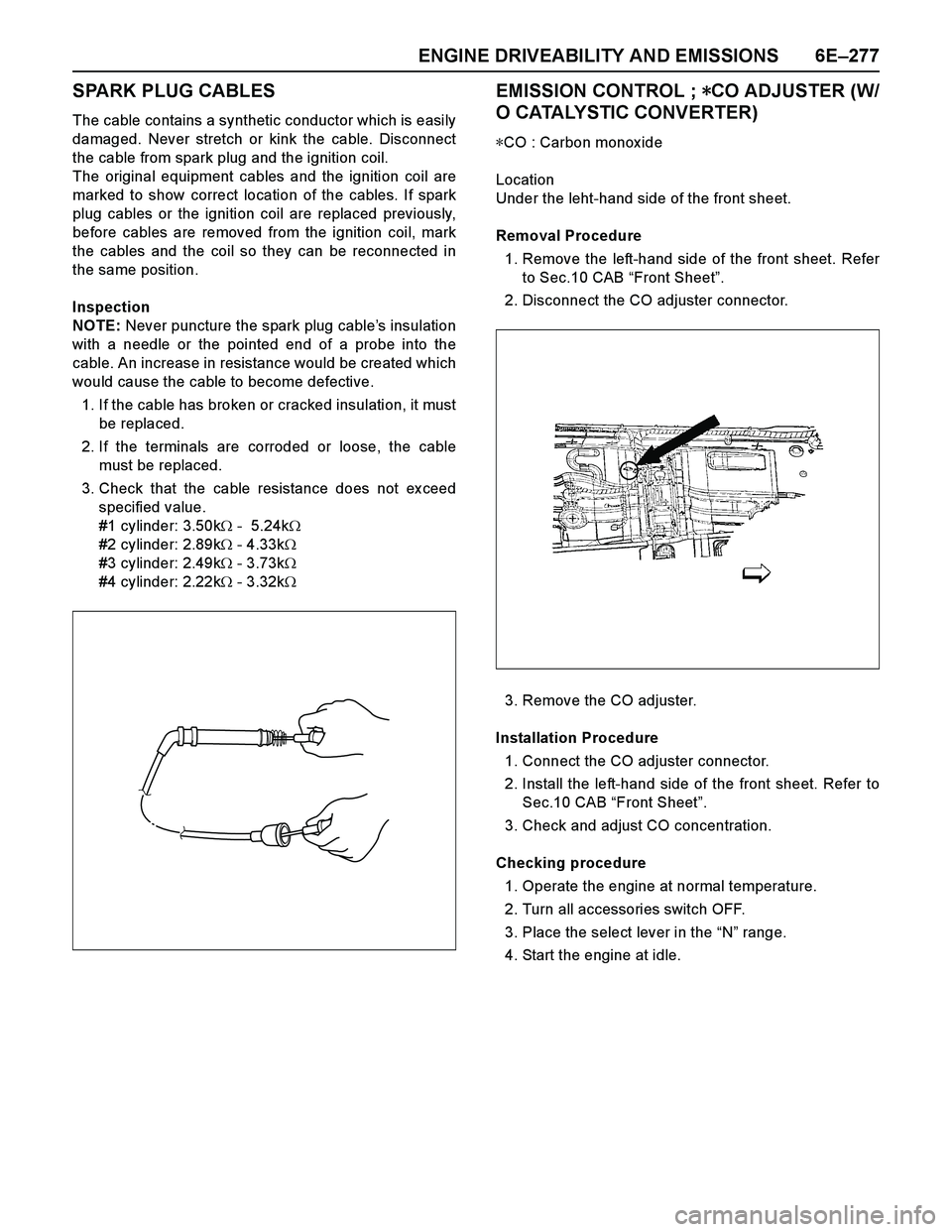
ENGINE DRIVEABILITY AND EMISSIONS 6E–277
SPARK PLUG CABLES
The cable contains a synthetic conductor which is easily
damaged. Never stretch or kink the cable. Disconnect
the cable from spark plug and the ignition coil.
The original equipment cables and the ignition coil are
marked to show correct location of the cables. If spark
plug cables or the ignition coil are replaced previously,
before cables are removed from the ignition coil, mark
the cables and the coil so they can be reconnected in
the same position.
Inspection
NOTE: Never puncture the spark plug cable’s insulation
with a needle or the pointed end of a probe into the
cable. An increase in resistance would be created which
would cause the cable to become defective.
1. If the cable has broken or cracked insulation, it must
be replaced.
2. If the terminals are corroded or loose, the cable
must be replaced.
3. Check that the cable resistance does not ex ceed
specified value.
#1 cylinder: 3.50k - 5.24k
#2 cylinder: 2.89k - 4.33k
#3 cylinder: 2.49k - 3.73k
#4 cylinder: 2.22k - 3.32k
EMISSION CONTROL ;
CO ADJUSTER (W/
O CATALYSTIC CONVERTER)
CO : Carbon monox ide
Location
Under the leht-hand side of the front sheet.
Removal Procedure
1. Remove the left-hand side of the front sheet. Refer
to Sec.10 CAB “Front Sheet”.
2. Disconnect the CO adjuster connector.
3. Remove the CO adjuster.
Installation Procedure
1. Connect the CO adjuster connector.
2. Install the left-hand side of the front sheet. Refer to
Sec.10 CAB “Front Sheet”.
3. Check and adjust CO concentration.
Checking procedure
1. Operate the engine at normal temperature.
2. Turn all accessories switch OFF.
3. Place the select lever in the “N” range.
4. Start the engine at idle.
Page 2854 of 4264
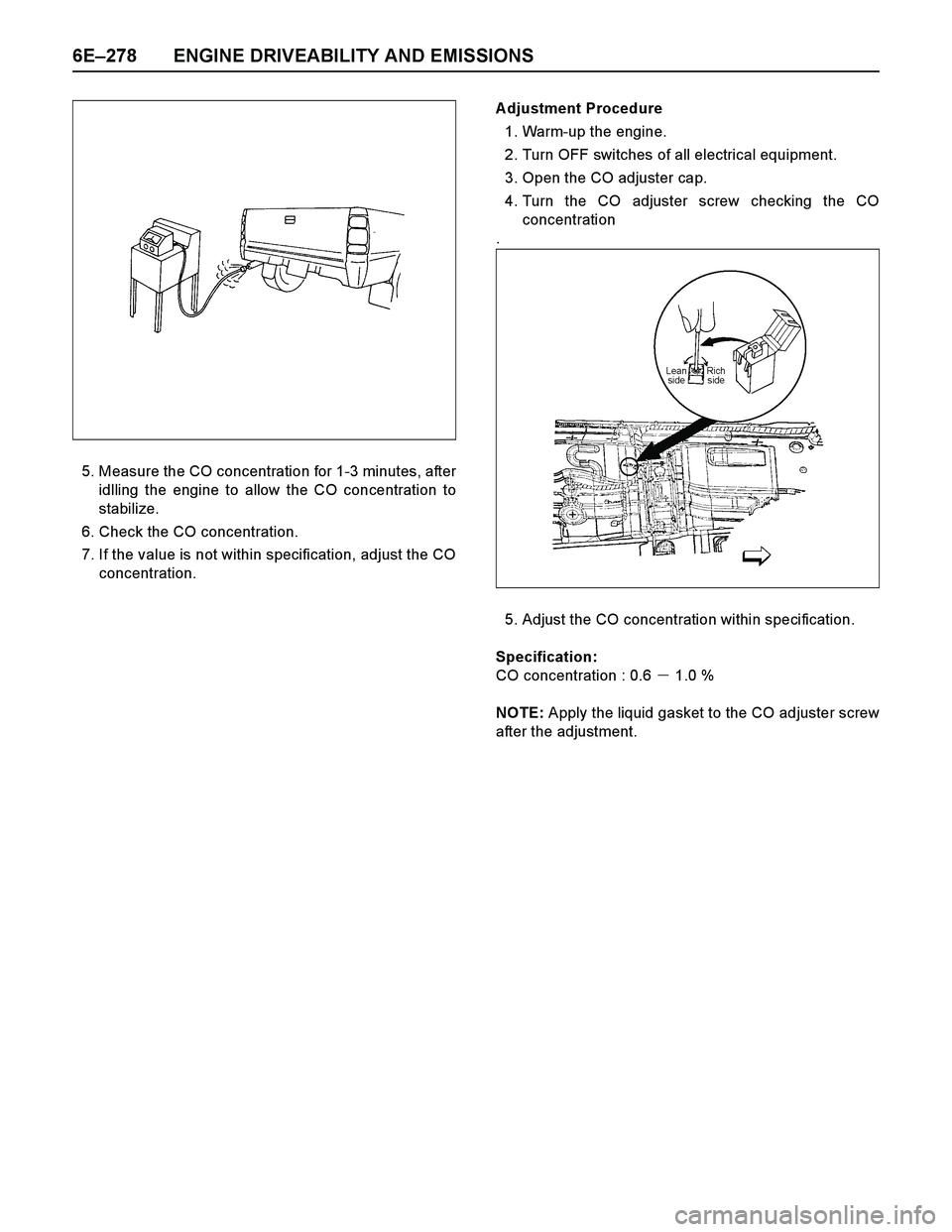
6E–278 ENGINE DRIVEABILITY AND EMISSIONS
5. Measure the CO concentration for 1-3 minutes, after
idlling the engine to allow the CO concentration to
stabilize.
6. Check the CO concentration.
7. If the value is not within specification, adjust the CO
concentration.A djustment Procedure
1. Warm-up the engine.
2. Turn OFF switches of all electrical equipment.
3. Open the CO adjuster cap.
4. Turn the CO adjuster screw checking the CO
concentration
.
5. Adjust the CO concentration within specification.
Specification:
CO concentration : 0.6 1.0 %
NOTE: Apply the liquid gasket to the CO adjuster screw
after the adjustment.
Page 2859 of 4264
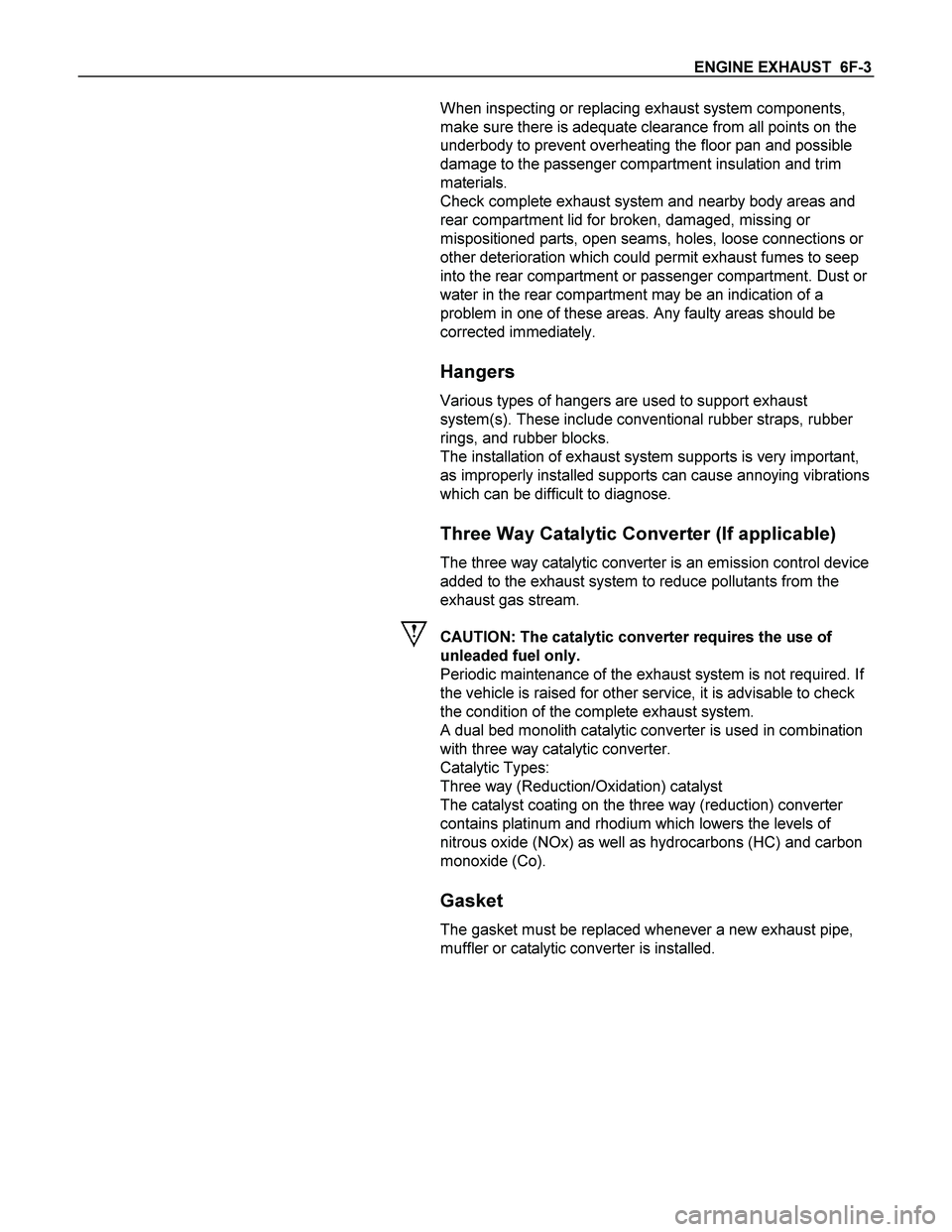
ENGINE EXHAUST 6F-3
When inspecting or replacing exhaust system components,
make sure there is adequate clearance from all points on the
underbody to prevent overheating the floor pan and possible
damage to the passenger compartment insulation and trim
materials.
Check complete exhaust system and nearby body areas and
rear compartment lid for broken, damaged, missing or
mispositioned parts, open seams, holes, loose connections or
other deterioration which could permit exhaust fumes to seep
into the rear compartment or passenger compartment. Dust or
water in the rear compartment may be an indication of a
problem in one of these areas. Any faulty areas should be
corrected immediately.
Hangers
Various types of hangers are used to support exhaust
system(s). These include conventional rubber straps, rubber
rings, and rubber blocks.
The installation of exhaust system supports is very important,
as improperly installed supports can cause annoying vibrations
which can be difficult to diagnose.
Three Way Catalytic Converter (If applicable)
The three way catalytic converter is an emission control device
added to the exhaust system to reduce pollutants from the
exhaust gas stream.
CAUTION: The catalytic converter requires the use of
unleaded fuel only.
Periodic maintenance of the exhaust system is not required. If
the vehicle is raised for other service, it is advisable to check
the condition of the complete exhaust system.
A dual bed monolith catalytic converter is used in combination
with three way catalytic converter.
Catalytic Types:
Three way (Reduction/Oxidation) catalyst
The catalyst coating on the three way (reduction) converter
contains platinum and rhodium which lowers the levels of
nitrous oxide (NOx) as well as hydrocarbons (HC) and carbon
monoxide (Co).
Gasket
The gasket must be replaced whenever a new exhaust pipe,
muffler or catalytic converter is installed.