fuel pressure ISUZU TF SERIES 2004 Manual Online
[x] Cancel search | Manufacturer: ISUZU, Model Year: 2004, Model line: TF SERIES, Model: ISUZU TF SERIES 2004Pages: 4264, PDF Size: 72.63 MB
Page 2023 of 4264
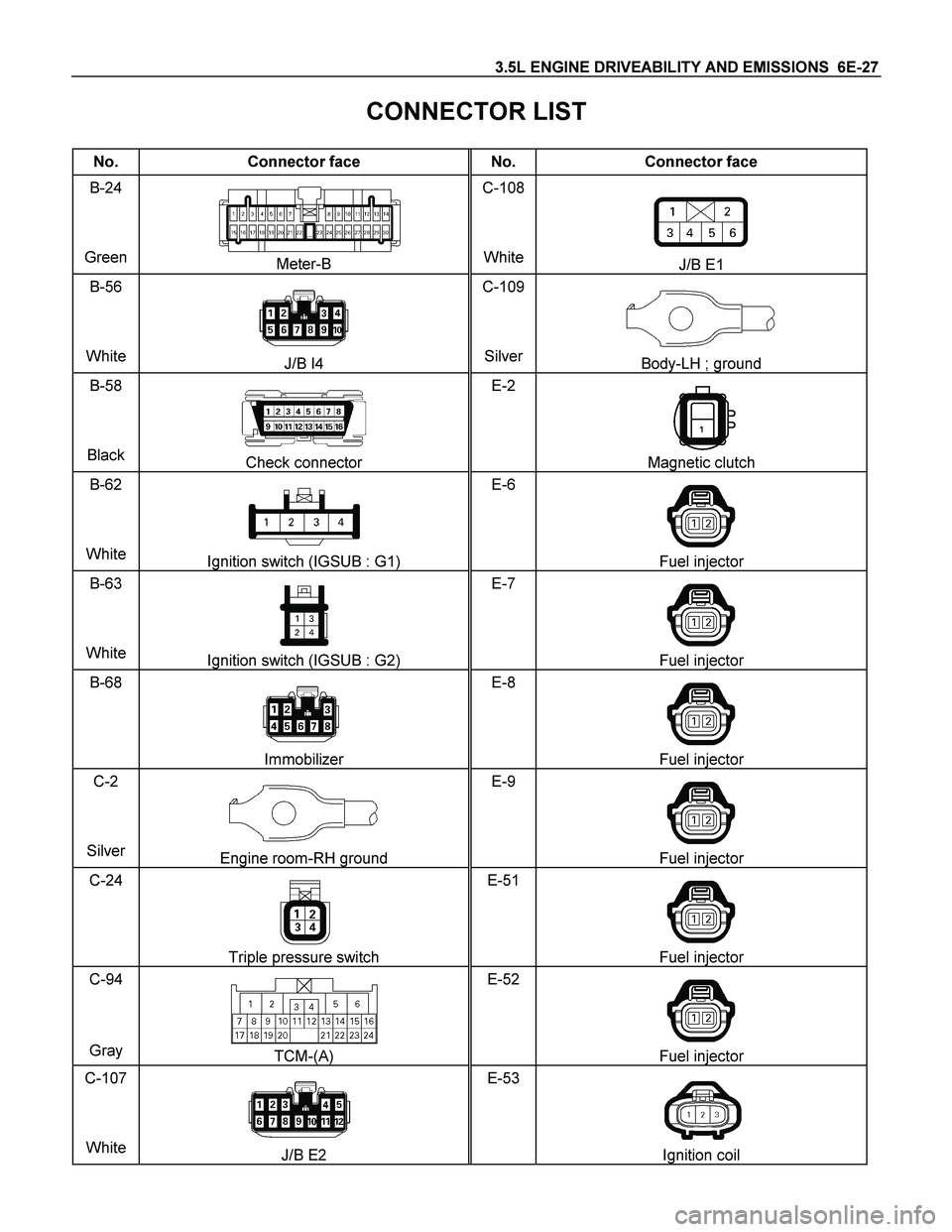
3.5L ENGINE DRIVEABILITY AND EMISSIONS 6E-27
CONNECTOR LIST
No. Connector face No. Connector face
B-24
Green
Meter-B C-108
WhiteJ/B E1
B-56
White
J/B I4 C-109
SilverBody-LH ; ground
B-58
Black
Check connector E-2
Magnetic clutch
B-62
White
Ignition switch (IGSUB : G1) E-6
Fuel injector
B-63
White
Ignition switch (IGSUB : G2) E-7
Fuel injector
B-68
Immobilizer E-8
Fuel injector
C-2
Silver
Engine room-RH ground E-9
Fuel injector
C-24
Triple pressure switch E-51
Fuel injector
C-94
Gray TCM-(A) E-52
Fuel injector
C-107
White
J/B E2 E-53
Ignition coil
Page 2043 of 4264
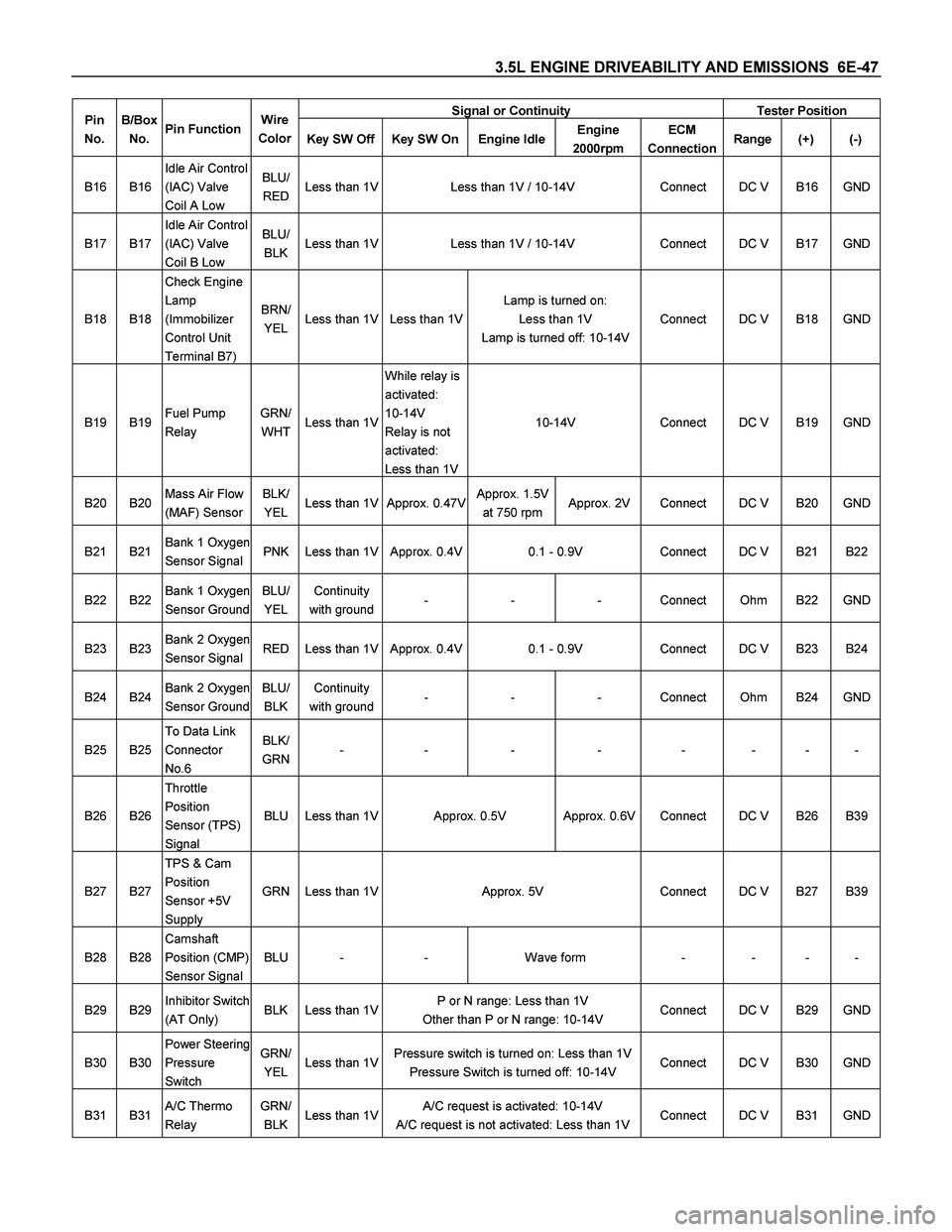
3.5L ENGINE DRIVEABILITY AND EMISSIONS 6E-47
Signal or Continuity Tester Position Pin
No. B/Box
No. Pin Function Wire
Color
Key SW Off Key SW On Engine IdleEngine
2000rpm ECM
Connection Range (+) (-)
B16 B16 Idle Air Control
(IAC) Valve
Coil A Low BLU/
RED Less than 1V Less than 1V / 10-14V Connect DC V B16 GND
B17 B17 Idle Air Control
(IAC) Valve
Coil B Low BLU/
BLKLess than 1V Less than 1V / 10-14V Connect DC V B17 GND
B18 B18 Check Engine
Lamp
(Immobilizer
Control Unit
Terminal B7) BRN/
YELLess than 1V Less than 1VLamp is turned on:
Less than 1V
Lamp is turned off: 10-14VConnect DC V B18 GND
B19 B19 Fuel Pump
Relay GRN/
WHT Less than 1V While relay is
activated:
10-14V
Relay is not
activated:
Less than 1V10-14V Connect DC V B19 GND
B20 B20 Mass Air Flow
(MAF) Sensor BLK/
YELLess than 1V Approx. 0.47VApprox. 1.5V
at 750 rpmApprox. 2V Connect DC V B20 GND
B21 B21 Bank 1 Oxygen
Sensor Signal PNK Less than 1V Approx. 0.4V 0.1 - 0.9V Connect DC V B21 B22
B22 B22 Bank 1 Oxygen
Sensor Ground BLU/
YELContinuity
with ground - - - Connect Ohm B22 GND
B23 B23 Bank 2 Oxygen
Sensor Signal RED Less than 1V Approx. 0.4V 0.1 - 0.9V Connect DC V B23 B24
B24 B24 Bank 2 Oxygen
Sensor Ground BLU/
BLKContinuity
with ground - - - Connect Ohm B24 GND
B25 B25 To Data Link
Connector
No.6 BLK/
GRN - - - - - - - -
B26 B26 Throttle
Position
Sensor (TPS)
Signal BLU Less than 1V Approx. 0.5V Approx. 0.6V Connect DC V B26 B39
B27 B27 TPS & Cam
Position
Sensor +5V
Supply GRN Less than 1V Approx. 5V Connect DC V B27 B39
B28 B28 Camshaft
Position (CMP)
Sensor Signal BLU - - Wave form - - - -
B29 B29 Inhibitor Switch
(AT Only) BLK Less than 1V P or N range: Less than 1V
Other than P or N range: 10-14V Connect DC V B29 GND
B30 B30 Power Steering
Pressure
Switch GRN/
YELLess than 1V Pressure switch is turned on: Less than 1V
Pressure Switch is turned off: 10-14V Connect DC V B30 GND
B31 B31 A/C Thermo
Relay GRN/
BLKLess than 1V A/C request is activated: 10-14V
A/C request is not activated: Less than 1VConnect DC V B31 GND
Page 2047 of 4264
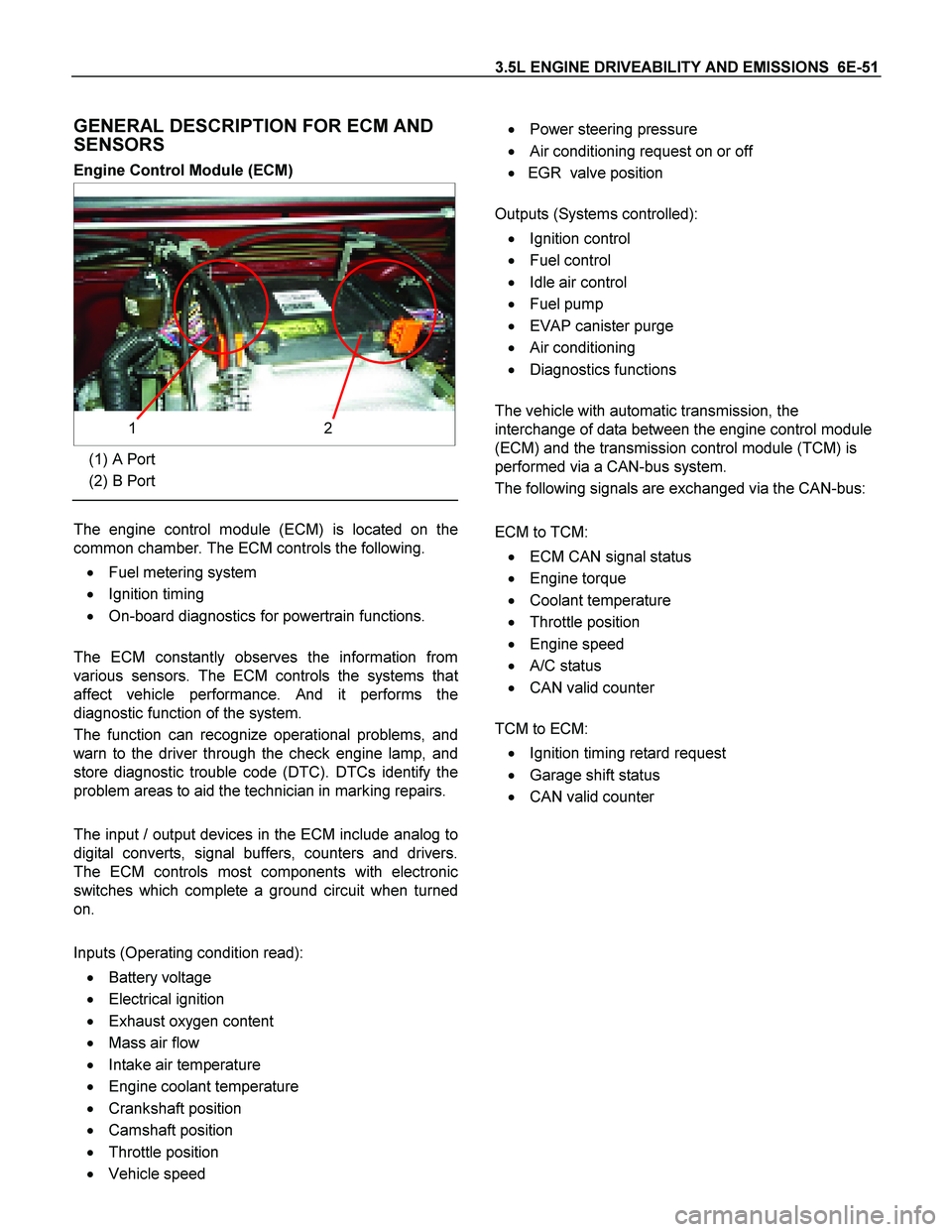
3.5L ENGINE DRIVEABILITY AND EMISSIONS 6E-51
GENERAL DESCRIPTION FOR ECM AND
SENSORS
Engine Control Module (ECM)
1 2
(1) A Port
(2) B Port
The engine control module (ECM) is located on the
common chamber. The ECM controls the following.
Fuel metering system
Ignition timing
On-board diagnostics for powertrain functions.
The ECM constantly observes the information from
various sensors. The ECM controls the systems tha
t
affect vehicle performance. And it performs the
diagnostic function of the system.
The function can recognize operational problems, and
warn to the driver through the check engine lamp, and
store diagnostic trouble code (DTC). DTCs identify the
problem areas to aid the technician in marking repairs.
The input / output devices in the ECM include analog to
digital converts, signal buffers, counters and drivers.
The ECM controls most components with electronic
switches which complete a ground circuit when turned
on.
Inputs (Operating condition read):
Battery voltage
Electrical ignition
Exhaust oxygen content
Mass air flow
Intake air temperature
Engine coolant temperature
Crankshaft position
Camshaft position
Throttle position
Vehicle speed
Power steering pressure
Air conditioning request on or off
EGR valve position
Outputs (Systems controlled):
Ignition control
Fuel control
Idle air control
Fuel pump
EVAP canister purge
Air conditioning
Diagnostics functions
The vehicle with automatic transmission, the
interchange of data between the engine control module
(ECM) and the transmission control module (TCM) is
performed via a CAN-bus system.
The following signals are exchanged via the CAN-bus:
ECM to TCM:
ECM CAN signal status
Engine torque
Coolant temperature
Throttle position
Engine speed
A/C status
CAN valid counter
TCM to ECM:
Ignition timing retard request
Garage shift status
CAN valid counter
Page 2052 of 4264
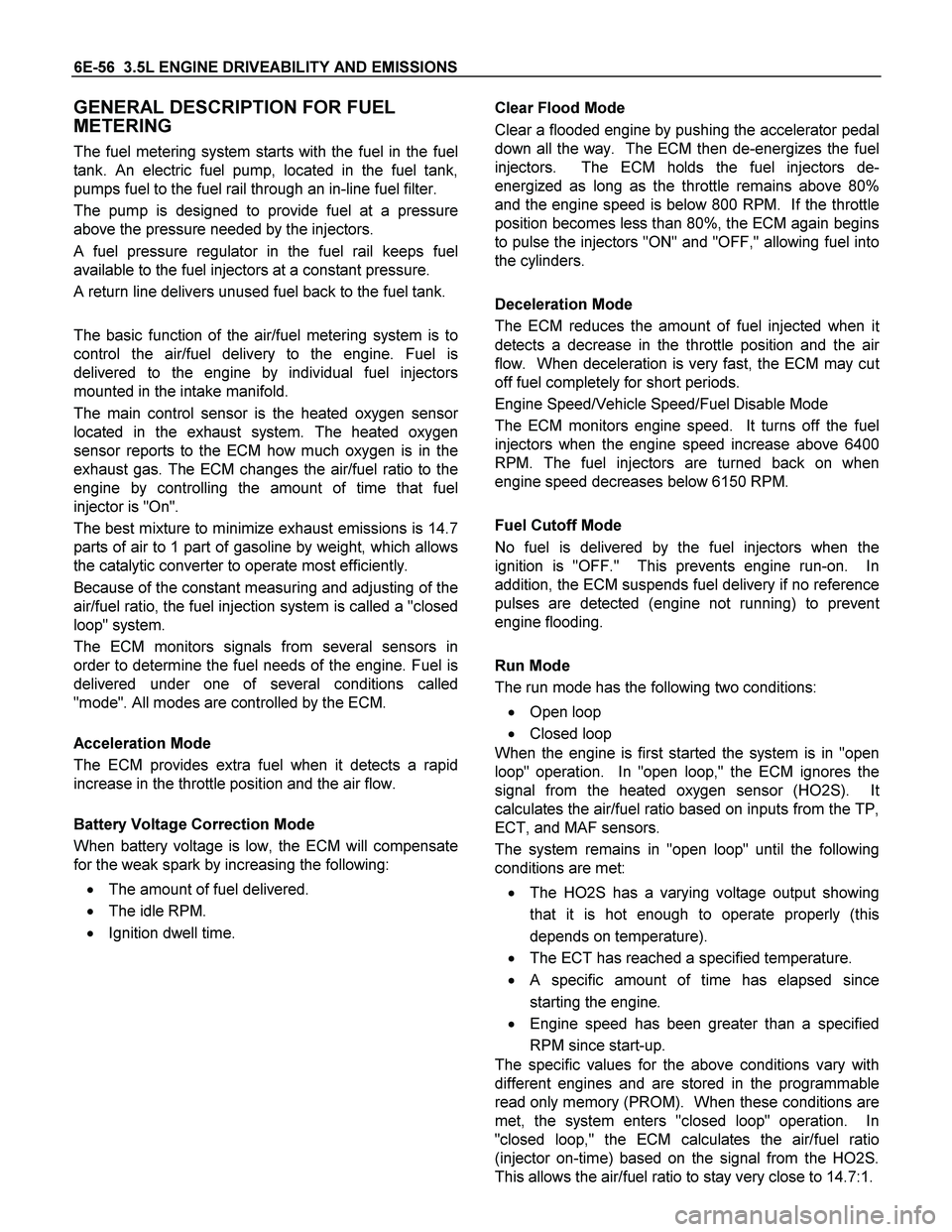
6E-56 3.5L ENGINE DRIVEABILITY AND EMISSIONS
GENERAL DESCRIPTION FOR FUEL
METERING
The fuel metering system starts with the fuel in the fuel
tank. An electric fuel pump, located in the fuel tank,
pumps fuel to the fuel rail through an in-line fuel filter.
The pump is designed to provide fuel at a pressure
above the pressure needed by the injectors.
A fuel pressure regulator in the fuel rail keeps fuel
available to the fuel injectors at a constant pressure.
A return line delivers unused fuel back to the fuel tank.
The basic function of the air/fuel metering system is to
control the air/fuel delivery to the engine. Fuel is
delivered to the engine by individual fuel injectors
mounted in the intake manifold.
The main control sensor is the heated oxygen senso
r
located in the exhaust system. The heated oxygen
sensor reports to the ECM how much oxygen is in the
exhaust gas. The ECM changes the air/fuel ratio to the
engine by controlling the amount of time that fuel
injector is "On".
The best mixture to minimize exhaust emissions is 14.7
parts of air to 1 part of gasoline by weight, which allows
the catalytic converter to operate most efficiently.
Because of the constant measuring and adjusting of the
air/fuel ratio, the fuel injection system is called a "closed
loop" system.
The ECM monitors signals from several sensors in
order to determine the fuel needs of the engine. Fuel is
delivered under one of several conditions called
"mode". All modes are controlled by the ECM.
Acceleration Mode
The ECM provides extra fuel when it detects a rapid
increase in the throttle position and the air flow.
Battery Voltage Correction Mode
When battery voltage is low, the ECM will compensate
for the weak spark by increasing the following:
The amount of fuel delivered.
The idle RPM.
Ignition dwell time.
Clear Flood Mode
Clear a flooded engine by pushing the accelerator pedal
down all the way. The ECM then de-energizes the fuel
injectors. The ECM holds the fuel injectors de-
energized as long as the throttle remains above 80%
and the engine speed is below 800 RPM. If the throttle
position becomes less than 80%, the ECM again begins
to pulse the injectors "ON" and "OFF," allowing fuel into
the cylinders.
Deceleration Mode
The ECM reduces the amount of fuel injected when i
t
detects a decrease in the throttle position and the air
flow. When deceleration is very fast, the ECM may cu
t
off fuel completely for short periods.
Engine Speed/Vehicle Speed/Fuel Disable Mode
The ECM monitors engine speed. It turns off the fuel
injectors when the engine speed increase above 6400
RPM. The fuel injectors are turned back on when
engine speed decreases below 6150 RPM.
Fuel Cutoff Mode
No fuel is delivered by the fuel injectors when the
ignition is "OFF." This prevents engine run-on. In
addition, the ECM suspends fuel delivery if no reference
pulses are detected (engine not running) to preven
t
engine flooding.
Run Mode
The run mode has the following two conditions:
Open loop
Closed loop
When the engine is first started the system is in "open
loop" operation. In "open loop," the ECM ignores the
signal from the heated oxygen sensor (HO2S). I
t
calculates the air/fuel ratio based on inputs from the TP,
ECT, and MAF sensors.
The system remains in "open loop" until the following
conditions are met:
The HO2S has a varying voltage output showing
that it is hot enough to operate properly (this
depends on temperature).
The ECT has reached a specified temperature.
A specific amount of time has elapsed since
starting the engine.
Engine speed has been greater than a specified
RPM since start-up.
The specific values for the above conditions vary with
different engines and are stored in the programmable
read only memory (PROM). When these conditions are
met, the system enters "closed loop" operation. In
"closed loop," the ECM calculates the air/fuel ratio
(injector on-time) based on the signal from the HO2S.
This allows the air/fuel ratio to stay very close to 14.7:1.
Page 2053 of 4264
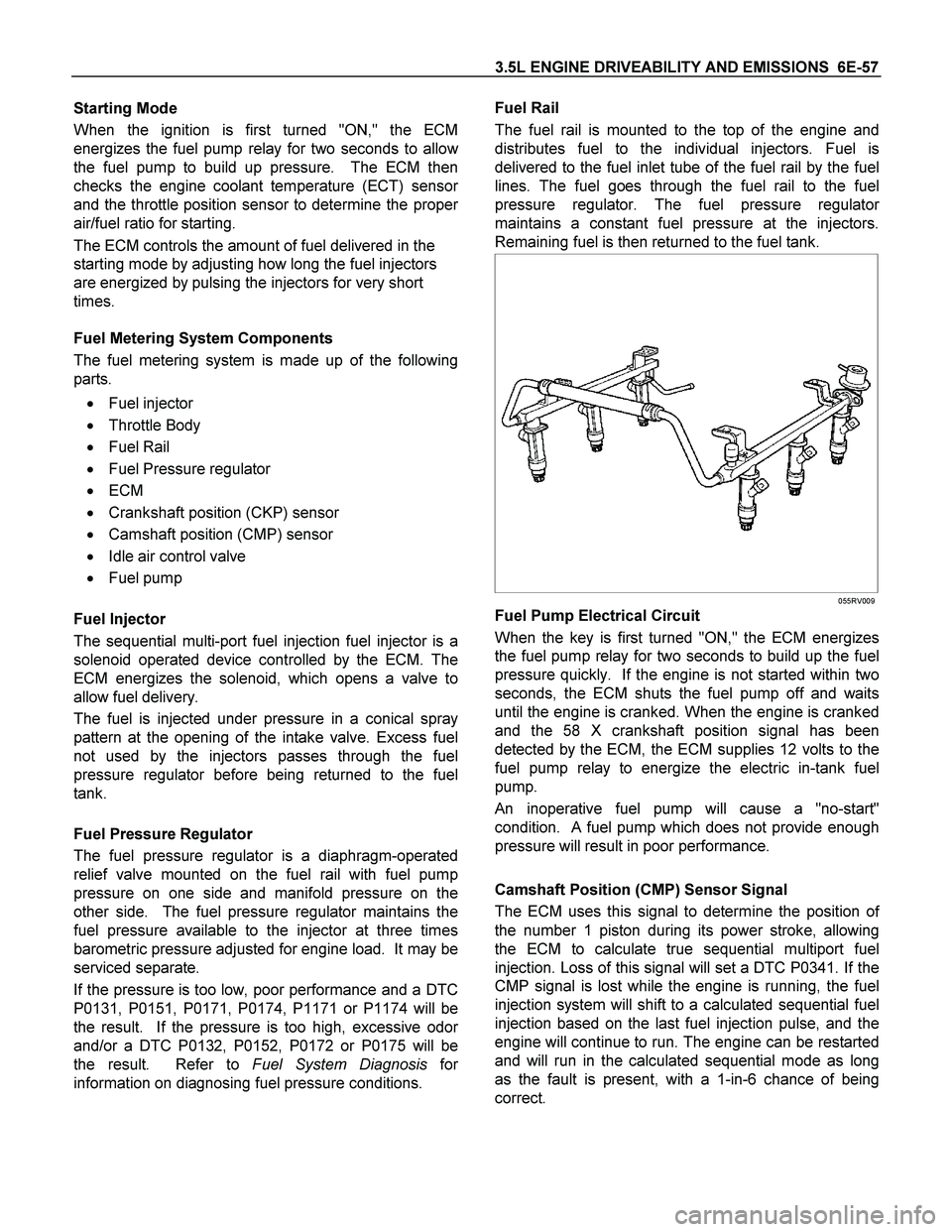
3.5L ENGINE DRIVEABILITY AND EMISSIONS 6E-57
Starting Mode
When the ignition is first turned "ON," the ECM
energizes the fuel pump relay for two seconds to allo
w
the fuel pump to build up pressure. The ECM then
checks the engine coolant temperature (ECT) senso
r
and the throttle position sensor to determine the proper
air/fuel ratio for starting.
The ECM controls the amount of fuel delivered in the
starting mode by adjusting how long the fuel injectors
are energized by pulsing the injectors for very short
times.
Fuel Metering System Components
The fuel metering system is made up of the following
parts.
Fuel injector
Throttle Body
Fuel Rail
Fuel Pressure regulator
ECM
Crankshaft position (CKP) sensor
Camshaft position (CMP) sensor
Idle air control valve
Fuel pump
Fuel Injector
The sequential multi-port fuel injection fuel injector is a
solenoid operated device controlled by the ECM. The
ECM energizes the solenoid, which opens a valve to
allow fuel delivery.
The fuel is injected under pressure in a conical spray
pattern at the opening of the intake valve. Excess fuel
not used by the injectors passes through the fuel
pressure regulator before being returned to the fuel
tank.
Fuel Pressure Regulator
The fuel pressure regulator is a diaphragm-operated
relief valve mounted on the fuel rail with fuel pump
pressure on one side and manifold pressure on the
other side. The fuel pressure regulator maintains the
fuel pressure available to the injector at three times
barometric pressure adjusted for engine load. It may be
serviced separate.
If the pressure is too low, poor performance and a DTC
P0131, P0151, P0171, P0174, P1171 or P1174 will be
the result. If the pressure is too high, excessive odo
r
and/or a DTC P0132, P0152, P0172 or P0175 will be
the result. Refer to Fuel System Diagnosisfo
r
information on diagnosing fuel pressure conditions.
Fuel Rail
The fuel rail is mounted to the top of the engine and
distributes fuel to the individual injectors. Fuel is
delivered to the fuel inlet tube of the fuel rail by the fuel
lines. The fuel goes through the fuel rail to the fuel
pressure regulator. The fuel pressure regulato
r
maintains a constant fuel pressure at the injectors.
Remaining fuel is then returned to the fuel tank.
055RV009
Fuel Pump Electrical Circuit
When the key is first turned "ON," the ECM energizes
the fuel pump relay for two seconds to build up the fuel
pressure quickly. If the engine is not started within two
seconds, the ECM shuts the fuel pump off and waits
until the engine is cranked. When the engine is cranked
and the 58 X crankshaft position signal has been
detected by the ECM, the ECM supplies 12 volts to the
fuel pump relay to energize the electric in-tank fuel
pump.
An inoperative fuel pump will cause a "no-start"
condition. A fuel pump which does not provide enough
pressure will result in poor performance.
Camshaft Position (CMP) Sensor Signal
The ECM uses this signal to determine the position o
f
the number 1 piston during its power stroke, allowing
the ECM to calculate true sequential multiport fuel
injection. Loss of this signal will set a DTC P0341. If the
CMP signal is lost while the engine is running, the fuel
injection system will shift to a calculated sequential fuel
injection based on the last fuel injection pulse, and the
engine will continue to run. The engine can be restarted
and will run in the calculated sequential mode as long
as the fault is present, with a 1-in-6 chance of being
correct.
Page 2066 of 4264
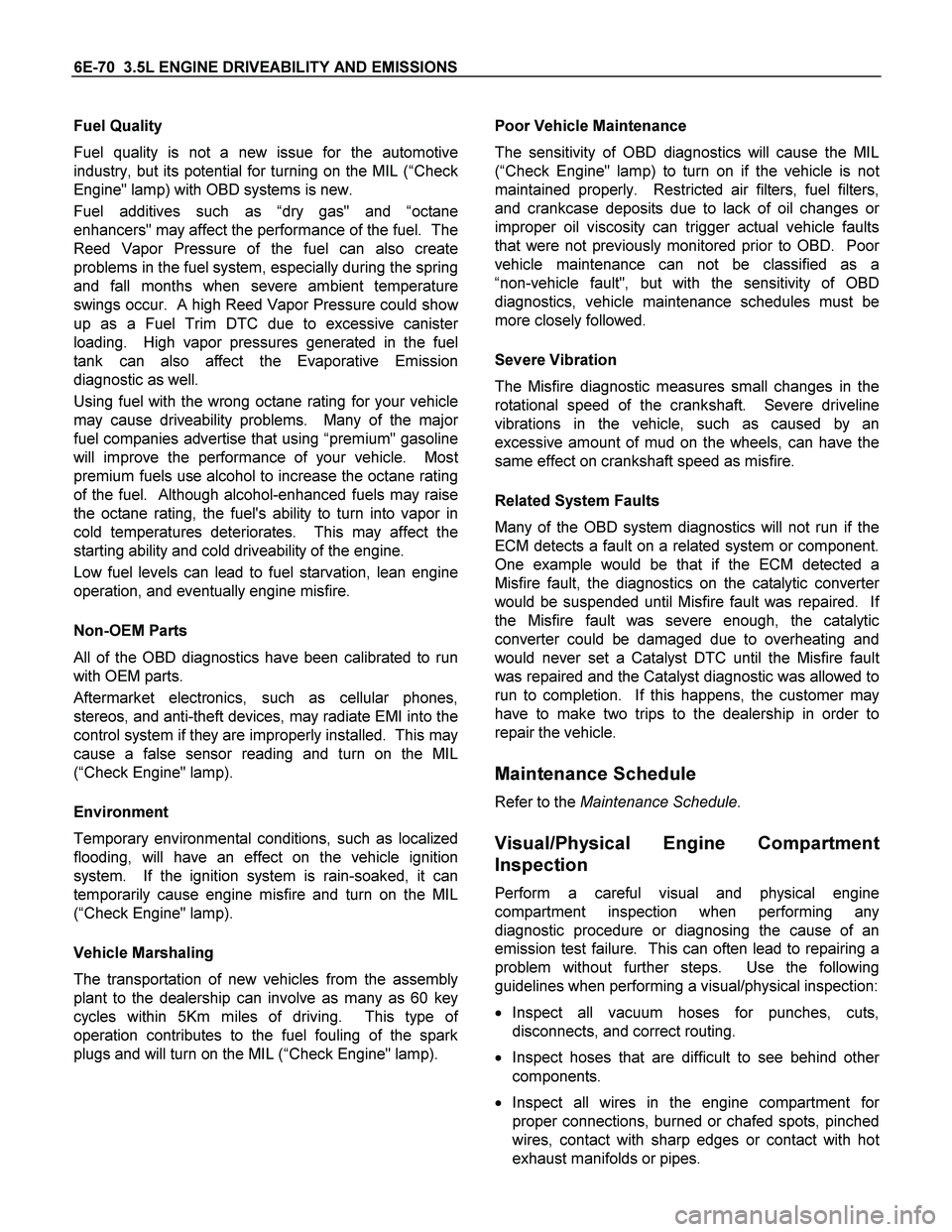
6E-70 3.5L ENGINE DRIVEABILITY AND EMISSIONS
Fuel Quality
Fuel quality is not a new issue for the automotive
industry, but its potential for turning on the MIL (“Check
Engine" lamp) with OBD systems is new.
Fuel additives such as “dry gas" and “octane
enhancers" may affect the performance of the fuel. The
Reed Vapor Pressure of the fuel can also create
problems in the fuel system, especially during the spring
and fall months when severe ambient temperature
swings occur. A high Reed Vapor Pressure could sho
w
up as a Fuel Trim DTC due to excessive canister
loading. High vapor pressures generated in the fuel
tank can also affect the Evaporative Emission
diagnostic as well.
Using fuel with the wrong octane rating for your vehicle
may cause driveability problems. Many of the majo
r
fuel companies advertise that using “premium" gasoline
will improve the performance of your vehicle. Mos
t
premium fuels use alcohol to increase the octane rating
of the fuel. Although alcohol-enhanced fuels may raise
the octane rating, the fuel's ability to turn into vapor in
cold temperatures deteriorates. This may affect the
starting ability and cold driveability of the engine.
Low fuel levels can lead to fuel starvation, lean engine
operation, and eventually engine misfire.
Non-OEM Parts
All of the OBD diagnostics have been calibrated to run
with OEM parts.
Aftermarket electronics, such as cellular phones,
stereos, and anti-theft devices, may radiate EMI into the
control system if they are improperly installed. This may
cause a false sensor reading and turn on the MIL
(“Check Engine" lamp).
Environment
Temporary environmental conditions, such as localized
flooding, will have an effect on the vehicle ignition
system. If the ignition system is rain-soaked, it can
temporarily cause engine misfire and turn on the MIL
(“Check Engine" lamp).
Vehicle Marshaling
The transportation of new vehicles from the assembly
plant to the dealership can involve as many as 60 key
cycles within 5Km miles of driving. This type o
f
operation contributes to the fuel fouling of the spark
plugs and will turn on the MIL (“Check Engine" lamp).
Poor Vehicle Maintenance
The sensitivity of OBD diagnostics will cause the MIL
(“Check Engine" lamp) to turn on if the vehicle is no
t
maintained properly. Restricted air filters, fuel filters,
and crankcase deposits due to lack of oil changes o
r
improper oil viscosity can trigger actual vehicle faults
that were not previously monitored prior to OBD. Poo
r
vehicle maintenance can not be classified as a
“non-vehicle fault", but with the sensitivity of OBD
diagnostics, vehicle maintenance schedules must be
more closely followed.
Severe Vibration
The Misfire diagnostic measures small changes in the
rotational speed of the crankshaft. Severe driveline
vibrations in the vehicle, such as caused by an
excessive amount of mud on the wheels, can have the
same effect on crankshaft speed as misfire.
Related System Faults
Many of the OBD system diagnostics will not run if the
ECM detects a fault on a related system or component.
One example would be that if the ECM detected a
Misfire fault, the diagnostics on the catalytic converte
r
would be suspended until Misfire fault was repaired. If
the Misfire fault was severe enough, the catalytic
converter could be damaged due to overheating and
would never set a Catalyst DTC until the Misfire faul
t
was repaired and the Catalyst diagnostic was allowed to
run to completion. If this happens, the customer may
have to make two trips to the dealership in order to
repair the vehicle.
Maintenance Schedule
Refer to the Maintenance Schedule.
Visual/Physical Engine Compartment
Inspection
Perform a careful visual and physical engine
compartment inspection when performing any
diagnostic procedure or diagnosing the cause of an
emission test failure. This can often lead to repairing a
problem without further steps. Use the following
guidelines when performing a visual/physical inspection:
Inspect all vacuum hoses for punches, cuts,
disconnects, and correct routing.
Inspect hoses that are difficult to see behind othe
r
components.
Inspect all wires in the engine compartment fo
r
proper connections, burned or chafed spots, pinched
wires, contact with sharp edges or contact with ho
t
exhaust manifolds or pipes.
Page 2076 of 4264
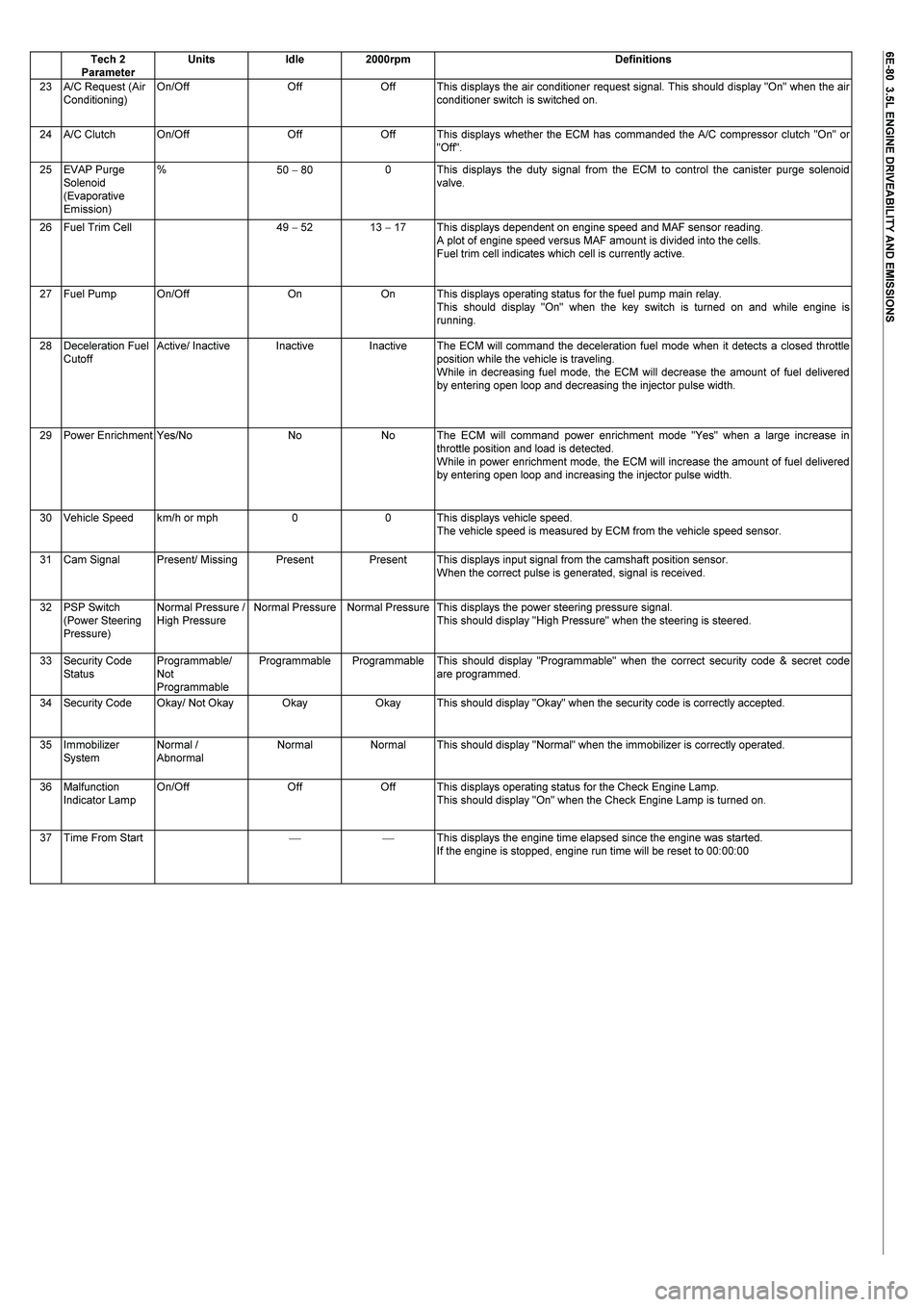
6E-80 3.5L ENGINE DRIVEABILITY AND EMISSIONS
Tech 2
Parameter
Units Idle 2000rpm Definitions
23 A/C Request (Air
Conditioning) On/Off Off Off This displays the air conditioner request signal. This should display "On" when the air
conditioner switch is switched on.
24 A/C Clutch On/Off Off Off This displays whether the ECM has commanded the A/C compressor clutch "On" or
"Off".
25 EVAP Purge
Solenoid
(Evaporative
Emission) % 50 80 0 This displays the duty signal from the ECM to control the canister purge solenoid
valve.
26 Fuel Trim Cell 49 52 13 17 This displays dependent on engine speed and MAF sensor reading.
A plot of engine speed versus MAF amount is divided into the cells.
Fuel trim cell indicates which cell is currently active.
27 Fuel Pump On/Off On On This displays operating status for the fuel pump main relay.
This should display "On" when the key switch is turned on and while engine is
running.
28 Deceleration Fuel
Cutoff Active/ Inactive Inactive Inactive The ECM will command the deceleration fuel mode when it detects a closed throttle
position while the vehicle is traveling.
While in decreasing fuel mode, the ECM will decrease the amount of fuel delivered
by entering open loop and decreasing the injector pulse width.
29 Power Enrichment Yes/No No No The ECM will command power enrichment mode "Yes" when a large increase in
throttle position and load is detected.
While in power enrichment mode, the ECM will increase the amount of fuel delivered
by entering open loop and increasing the injector pulse width.
30 Vehicle Speed km/h or mph 0 0 This displays vehicle speed.
The vehicle speed is measured by ECM from the vehicle speed sensor.
31 Cam Signal Present/ Missing Present Present This displays input signal from the camshaft position sensor.
When the correct pulse is generated, signal is received.
32 PSP Switch
(Power Steering
Pressure) Normal Pressure /
High Pressure Normal PressureNormal PressureThis displays the power steering pressure signal.
This should display "High Pressure" when the steering is steered.
33 Security Code
Status Programmable/
Not
Programmable Programmable Programmable This should display "Programmable" when the correct security code & secret code
are programmed.
34 Security Code Okay/ Not Okay Okay Okay This should display "Okay" when the security code is correctly accepted.
35 Immobilizer
System Normal /
Abnormal Normal Normal This should display "Normal" when the immobilizer is correctly operated.
36 Malfunction
Indicator Lamp On/Off Off Off This displays operating status for the Check Engine Lamp.
This should display "On" when the Check Engine Lamp is turned on.
37 Time From Start This displays the engine time elapsed since the engine was started.
If the engine is stopped, engine run time will be reset to 00:00:00
Page 2102 of 4264
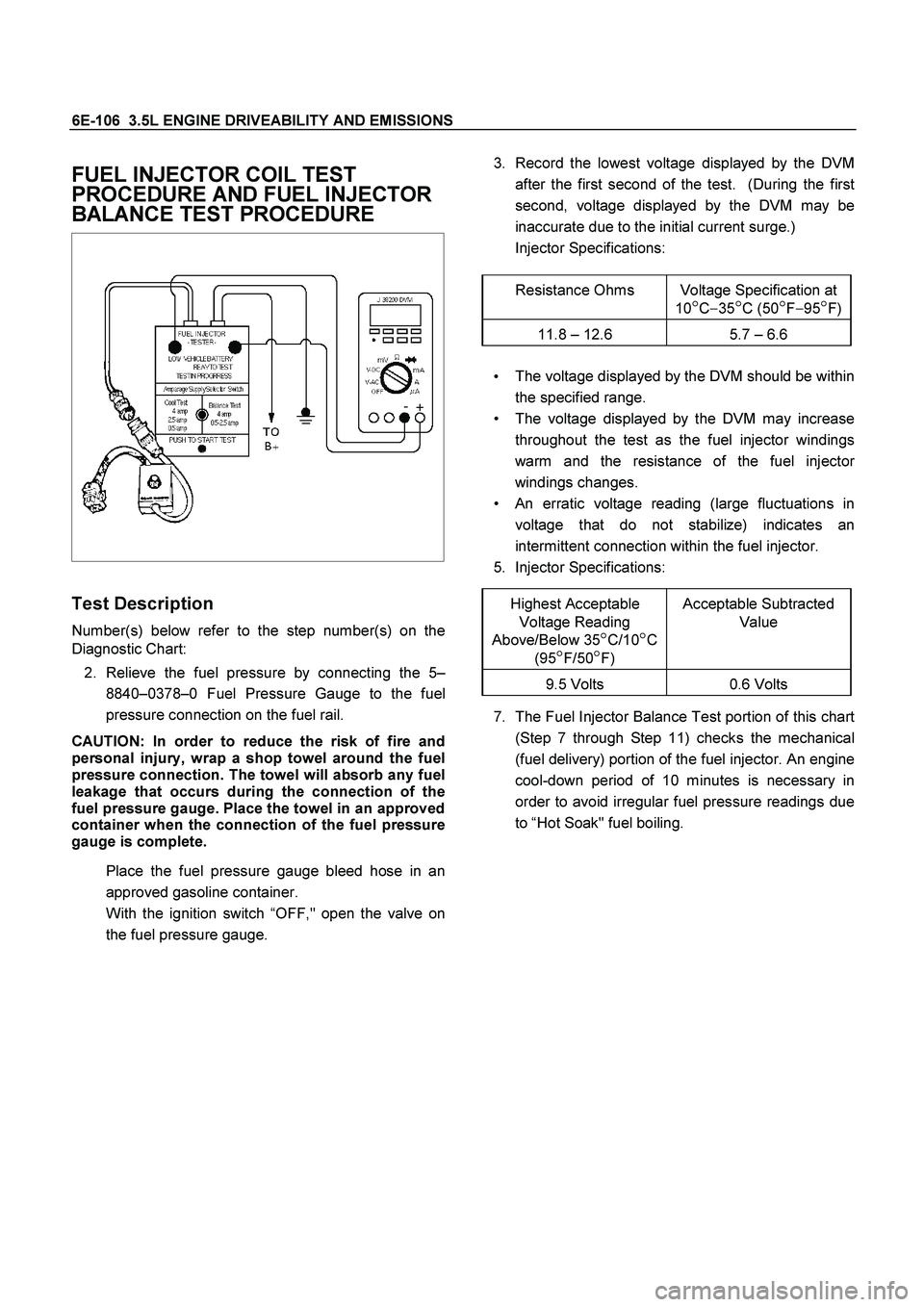
6E-106 3.5L ENGINE DRIVEABILITY AND EMISSIONS
FUEL INJECTOR COIL TEST
PROCEDURE AND FUEL INJECTOR
BALANCE TEST PROCEDURE
Test Description
Number(s) below refer to the step number(s) on the
Diagnostic Chart:
2.
Relieve the fuel pressure by connecting the 5–
8840–0378–0 Fuel Pressure Gauge to the fuel
pressure connection on the fuel rail.
CAUTION: In order to reduce the risk of fire and
personal injury, wrap a shop towel around the fuel
pressure connection. The towel will absorb any fuel
leakage that occurs during the connection of the
fuel pressure gauge. Place the towel in an approved
container when the connection of the fuel pressure
gauge is complete.
Place the fuel pressure gauge bleed hose in an
approved gasoline container.
With the ignition switch “OFF," open the valve on
the fuel pressure gauge.
3.
Record the lowest voltage displayed by the DVM
after the first second of the test. (During the first
second, voltage displayed by the DVM may be
inaccurate due to the initial current surge.)
Injector Specifications:
Resistance Ohms Voltage Specification at
10
C
35C (50F
95F)
11.8 – 12.6 5.7 – 6.6
The voltage displayed by the DVM should be within
the specified range.
The voltage displayed by the DVM may increase
throughout the test as the fuel injector windings
warm and the resistance of the fuel injecto
r
windings changes.
An erratic voltage reading (large fluctuations in
voltage that do not stabilize) indicates an
intermittent connection within the fuel injector.
5.
Injector Specifications:
Highest Acceptable
Voltage Reading
Above/Below 35
C/10C
(95
F/50F) Acceptable Subtracted
Value
9.5 Volts 0.6 Volts
7.
The Fuel Injector Balance Test portion of this chart
(Step 7 through Step 11) checks the mechanical
(fuel delivery) portion of the fuel injector. An engine
cool-down period of 10 minutes is necessary in
order to avoid irregular fuel pressure readings due
to “Hot Soak" fuel boiling.
Page 2104 of 4264
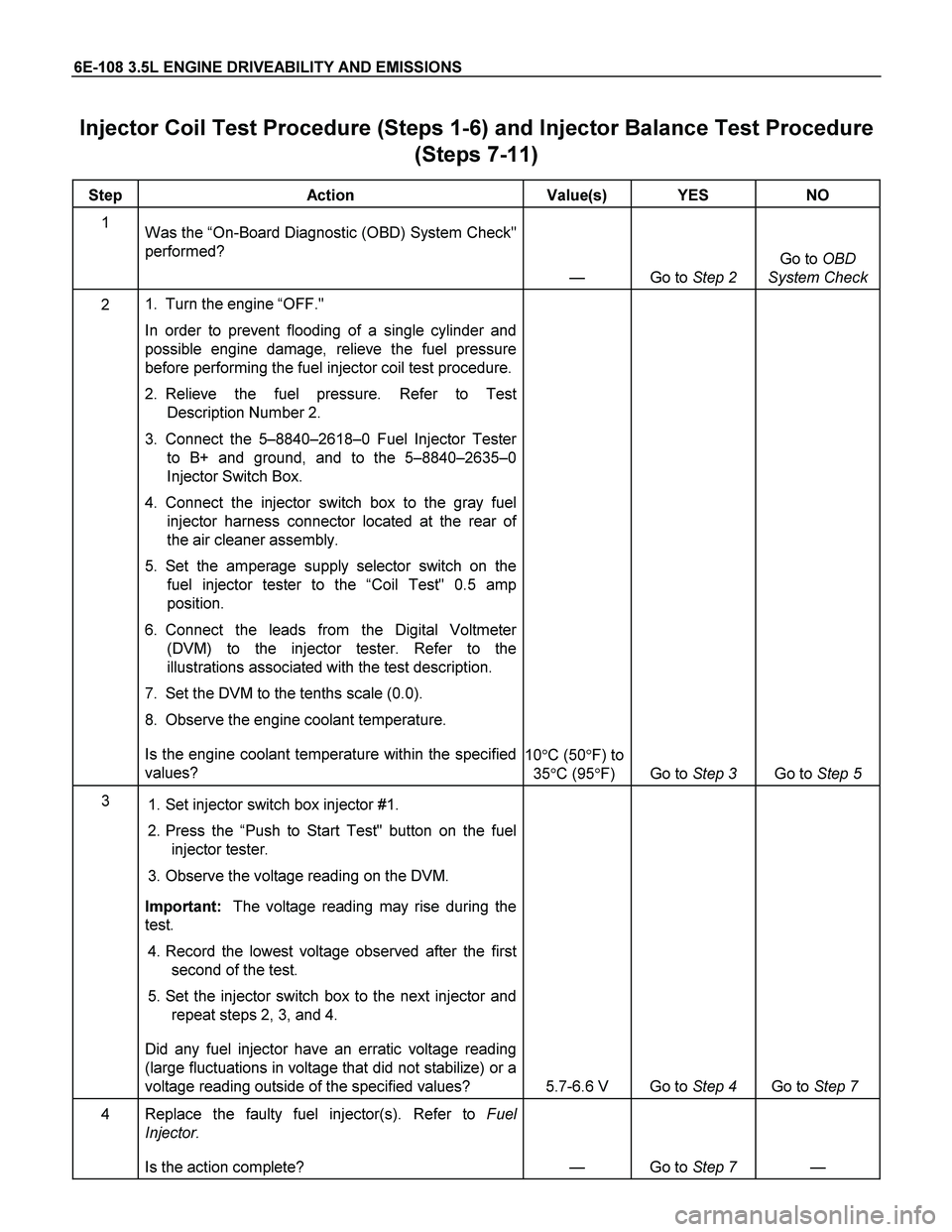
6E-108 3.5L ENGINE DRIVEABILITY AND EMISSIONS
Injector Coil Test Procedure (Steps 1-6) and Injector Balance Test Procedure
(Steps 7-11)
Step Action Value(s) YES NO
1
Was the “On-Board Diagnostic (OBD) System Check"
performed?
— Go to Step 2 Go to OBD
System Check
2 1. Turn the engine “OFF."
In order to prevent flooding of a single cylinder and
possible engine damage, relieve the fuel pressure
before performing the fuel injector coil test procedure.
2. Relieve the fuel pressure. Refer to Test
Description Number 2.
3. Connect the 5–8840–2618–0 Fuel Injector Tester
to B+ and ground, and to the 5–8840–2635–0
Injector Switch Box.
4. Connect the injector switch box to the gray fuel
injector harness connector located at the rear of
the air cleaner assembly.
5. Set the amperage supply selector switch on the
fuel injector tester to the “Coil Test" 0.5 amp
position.
6. Connect the leads from the Digital Voltmeter
(DVM) to the injector tester. Refer to the
illustrations associated with the test description.
7. Set the DVM to the tenths scale (0.0).
8. Observe the engine coolant temperature.
Is the engine coolant temperature within the specified
values? 10C (50F) to
35C (95F) Go to Step 3 Go to Step 5
3
1. Set injector switch box injector #1.
2. Press the “Push to Start Test" button on the fuel
injector tester.
3. Observe the voltage reading on the DVM.
Important: The voltage reading may rise during the
test.
4. Record the lowest voltage observed after the first
second of the test.
5. Set the injector switch box to the next injector and
repeat steps 2, 3, and 4.
Did any fuel injector have an erratic voltage reading
(large fluctuations in voltage that did not stabilize) or a
voltage reading outside of the specified values? 5.7-6.6 V Go to Step 4 Go to Step 7
4 Replace the faulty fuel injector(s). Refer to Fuel
Injector.
Is the action complete? — Go to Step 7 —
Page 2105 of 4264
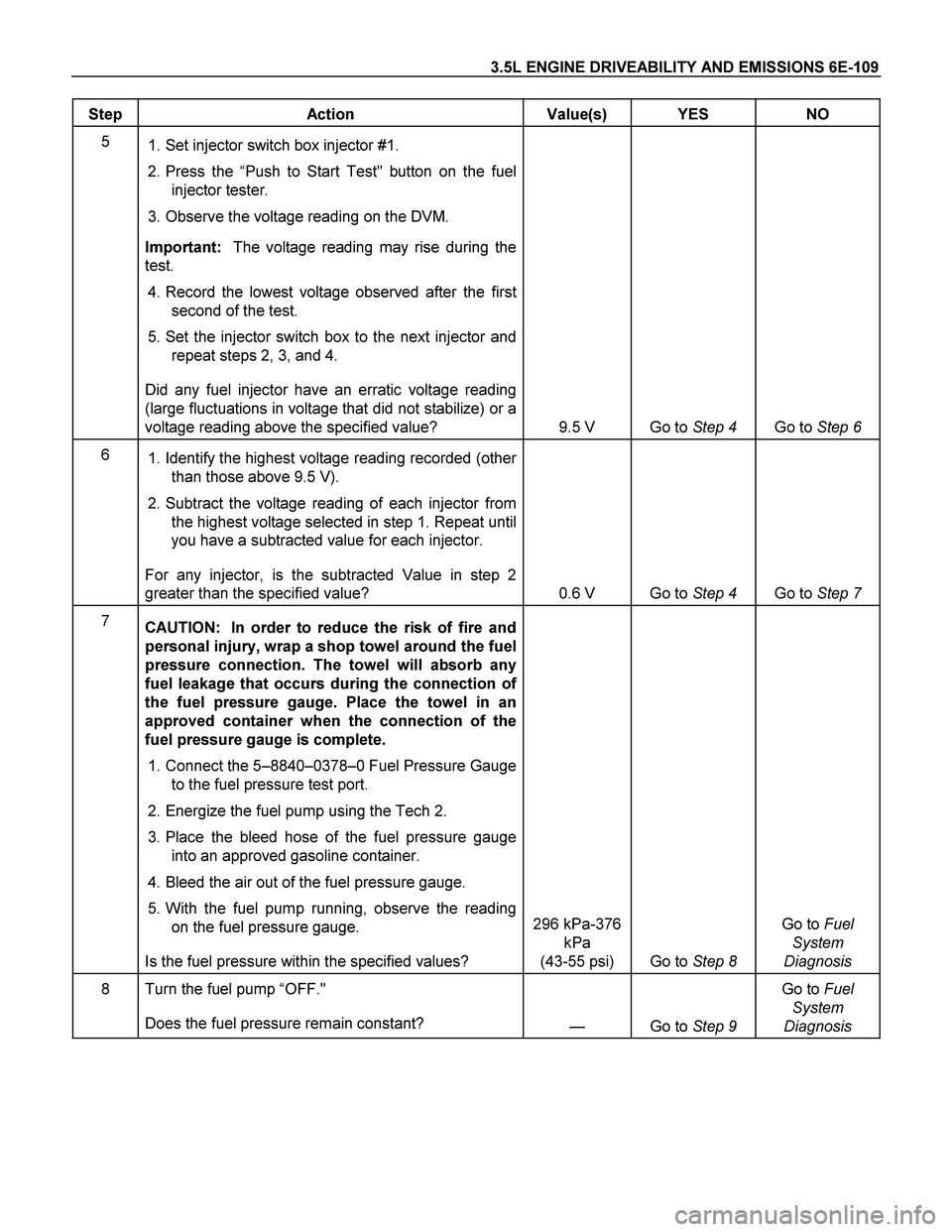
3.5L ENGINE DRIVEABILITY AND EMISSIONS 6E-109
Step Action Value(s) YES NO
5
1. Set injector switch box injector #1.
2. Press the “Push to Start Test" button on the fuel
injector tester.
3. Observe the voltage reading on the DVM.
Important: The voltage reading may rise during the
test.
4. Record the lowest voltage observed after the first
second of the test.
5. Set the injector switch box to the next injector and
repeat steps 2, 3, and 4.
Did any fuel injector have an erratic voltage reading
(large fluctuations in voltage that did not stabilize) or a
voltage reading above the specified value? 9.5 V Go to Step 4 Go to Step 6
6
1. Identify the highest voltage reading recorded (other
than those above 9.5 V).
2. Subtract the voltage reading of each injector from
the highest voltage selected in step 1. Repeat until
you have a subtracted value for each injector.
For any injector, is the subtracted Value in step 2
greater than the specified value? 0.6 V Go to Step 4 Go to Step 7
7
CAUTION: In order to reduce the risk of fire and
personal injury, wrap a shop towel around the fuel
pressure connection. The towel will absorb any
fuel leakage that occurs during the connection of
the fuel pressure gauge. Place the towel in an
approved container when the connection of the
fuel pressure gauge is complete.
1. Connect the 5–8840–0378–0 Fuel Pressure Gauge
to the fuel pressure test port.
2. Energize the fuel pump using the Tech 2.
3. Place the bleed hose of the fuel pressure gauge
into an approved gasoline container.
4. Bleed the air out of the fuel pressure gauge.
5. With the fuel pump running, observe the reading
on the fuel pressure gauge.
Is the fuel pressure within the specified values? 296 kPa-376
kPa
(43-55 psi) Go to Step 8 Go to Fuel
System
Diagnosis
8 Turn the fuel pump “OFF."
Does the fuel pressure remain constant?
— Go to Step 9 Go to Fuel
System
Diagnosis