fuel pressure ISUZU TF SERIES 2004 Workshop Manual
[x] Cancel search | Manufacturer: ISUZU, Model Year: 2004, Model line: TF SERIES, Model: ISUZU TF SERIES 2004Pages: 4264, PDF Size: 72.63 MB
Page 2362 of 4264
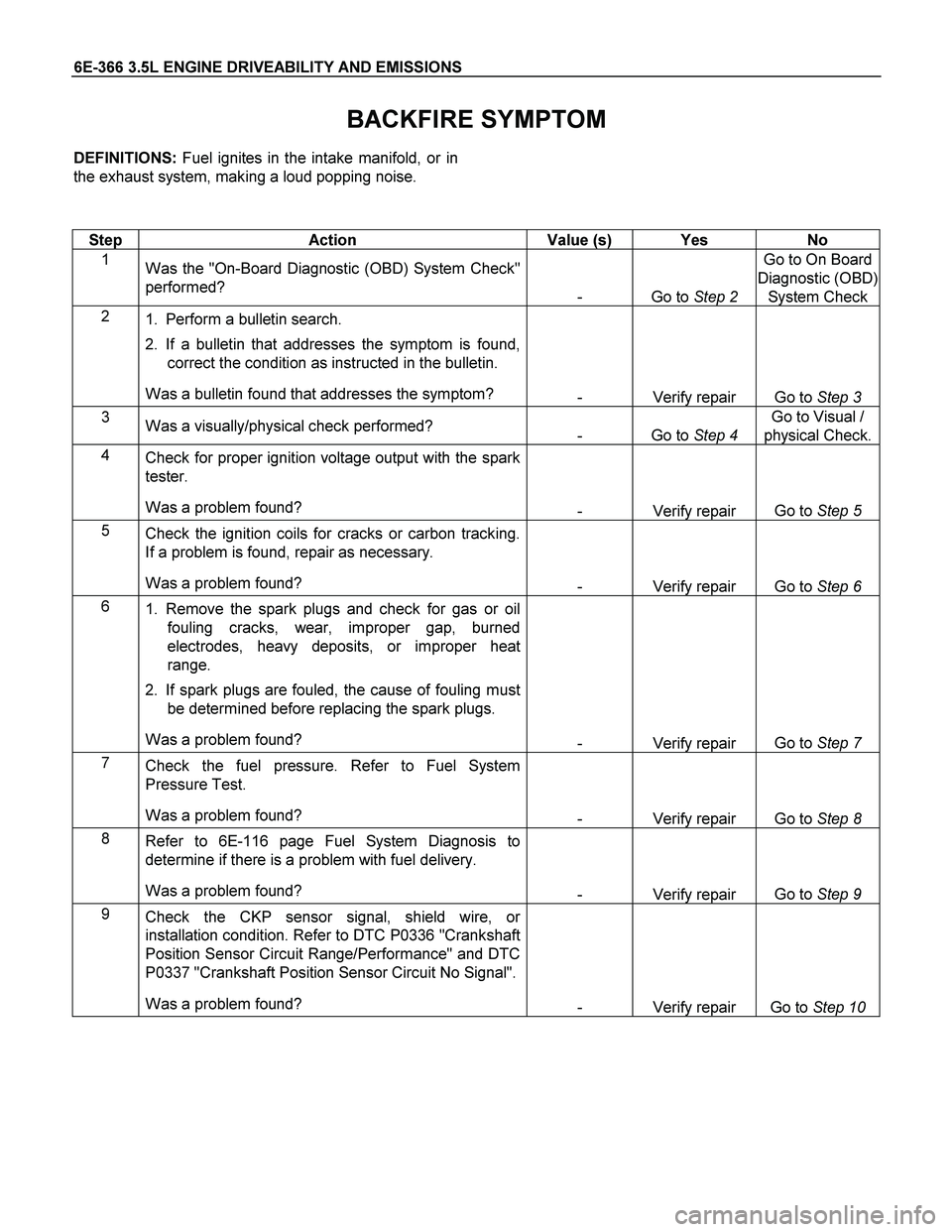
6E-366 3.5L ENGINE DRIVEABILITY AND EMISSIONS
BACKFIRE SYMPTOM
DEFINITIONS: Fuel ignites in the intake manifold, or in
the exhaust system, making a loud popping noise.
Step Action Value (s) Yes No
1
Was the "On-Board Diagnostic (OBD) System Check"
performed?
- Go to Step 2 Go to On Board
Diagnostic (OBD)
System Check
2
1. Perform a bulletin search.
2. If a bulletin that addresses the symptom is found,
correct the condition as instructed in the bulletin.
Was a bulletin found that addresses the symptom?
- Verify repair Go to Step 3
3
Was a visually/physical check performed?
- Go to Step 4 Go to Visual /
physical Check.
4
Check for proper ignition voltage output with the spark
tester.
Was a problem found?
- Verify repair Go to Step 5
5
Check the ignition coils for cracks or carbon tracking.
If a problem is found, repair as necessary.
Was a problem found?
- Verify repair Go to Step 6
6
1. Remove the spark plugs and check for gas or oil
fouling cracks, wear, improper gap, burned
electrodes, heavy deposits, or improper heat
range.
2. If spark plugs are fouled, the cause of fouling must
be determined before replacing the spark plugs.
Was a problem found?
- Verify repair Go to Step 7
7
Check the fuel pressure. Refer to Fuel System
Pressure Test.
Was a problem found?
- Verify repair Go to Step 8
8
Refer to 6E-116 page Fuel System Diagnosis to
determine if there is a problem with fuel delivery.
Was a problem found?
- Verify repair Go to Step 9
9
Check the CKP sensor signal, shield wire, or
installation condition. Refer to DTC P0336 "Crankshaft
Position Sensor Circuit Range/Performance" and DTC
P0337 "Crankshaft Position Sensor Circuit No Signal".
Was a problem found?
- Verify repair Go to Step 10
Page 2370 of 4264
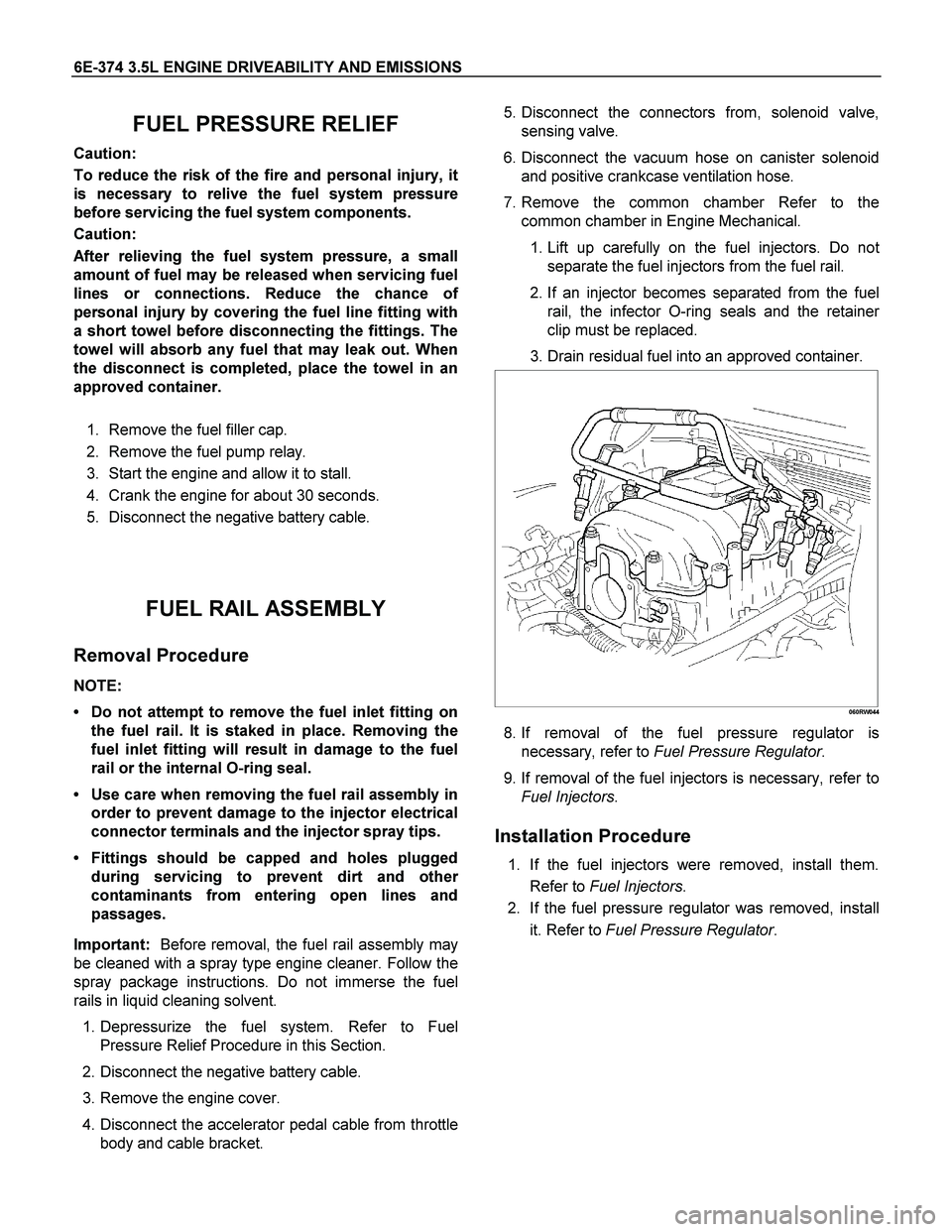
6E-374 3.5L ENGINE DRIVEABILITY AND EMISSIONS
FUEL PRESSURE RELIEF
Caution:
To reduce the risk of the fire and personal injury, it
is necessary to relive the fuel system pressure
before servicing the fuel system components.
Caution:
After relieving the fuel system pressure, a small
amount of fuel may be released when servicing fuel
lines or connections. Reduce the chance o
f
personal injury by covering the fuel line fitting with
a short towel before disconnecting the fittings. The
towel will absorb any fuel that may leak out. When
the disconnect is completed, place the towel in an
approved container.
1. Remove the fuel filler cap.
2. Remove the fuel pump relay.
3. Start the engine and allow it to stall.
4. Crank the engine for about 30 seconds.
5. Disconnect the negative battery cable.
FUEL RAIL ASSEMBLY
Removal Procedure
NOTE:
Do not attempt to remove the fuel inlet fitting on
the fuel rail. It is staked in place. Removing the
fuel inlet fitting will result in damage to the fuel
rail or the internal O-ring seal.
Use care when removing the fuel rail assembly in
order to prevent damage to the injector electrical
connector terminals and the injector spray tips.
Fittings should be capped and holes plugged
during servicing to prevent dirt and othe
r
contaminants from entering open lines and
passages.
Important: Before removal, the fuel rail assembly may
be cleaned with a spray type engine cleaner. Follow the
spray package instructions. Do not immerse the fuel
rails in liquid cleaning solvent.
1. Depressurize the fuel system. Refer to Fuel
Pressure Relief Procedure in this Section.
2. Disconnect the negative battery cable.
3. Remove the engine cover.
4. Disconnect the accelerator pedal cable from throttle
body and cable bracket.
5. Disconnect the connectors from, solenoid valve,
sensing valve.
6. Disconnect the vacuum hose on canister solenoid
and positive crankcase ventilation hose.
7. Remove the common chamber Refer to the
common chamber in Engine Mechanical.
1. Lift up carefully on the fuel injectors. Do no
t
separate the fuel injectors from the fuel rail.
2. If an injector becomes separated from the fuel
rail, the infector O-ring seals and the retaine
r
clip must be replaced.
3. Drain residual fuel into an approved container.
060RW044
8. If removal of the fuel pressure regulator is
necessary, refer to Fuel Pressure Regulator.
9. If removal of the fuel injectors is necessary, refer to
Fuel Injectors.
Installation Procedure
1. If the fuel injectors were removed, install them.
Refer to Fuel Injectors.
2. If the fuel pressure regulator was removed, install
it. Refer to Fuel Pressure Regulator.
Page 2373 of 4264
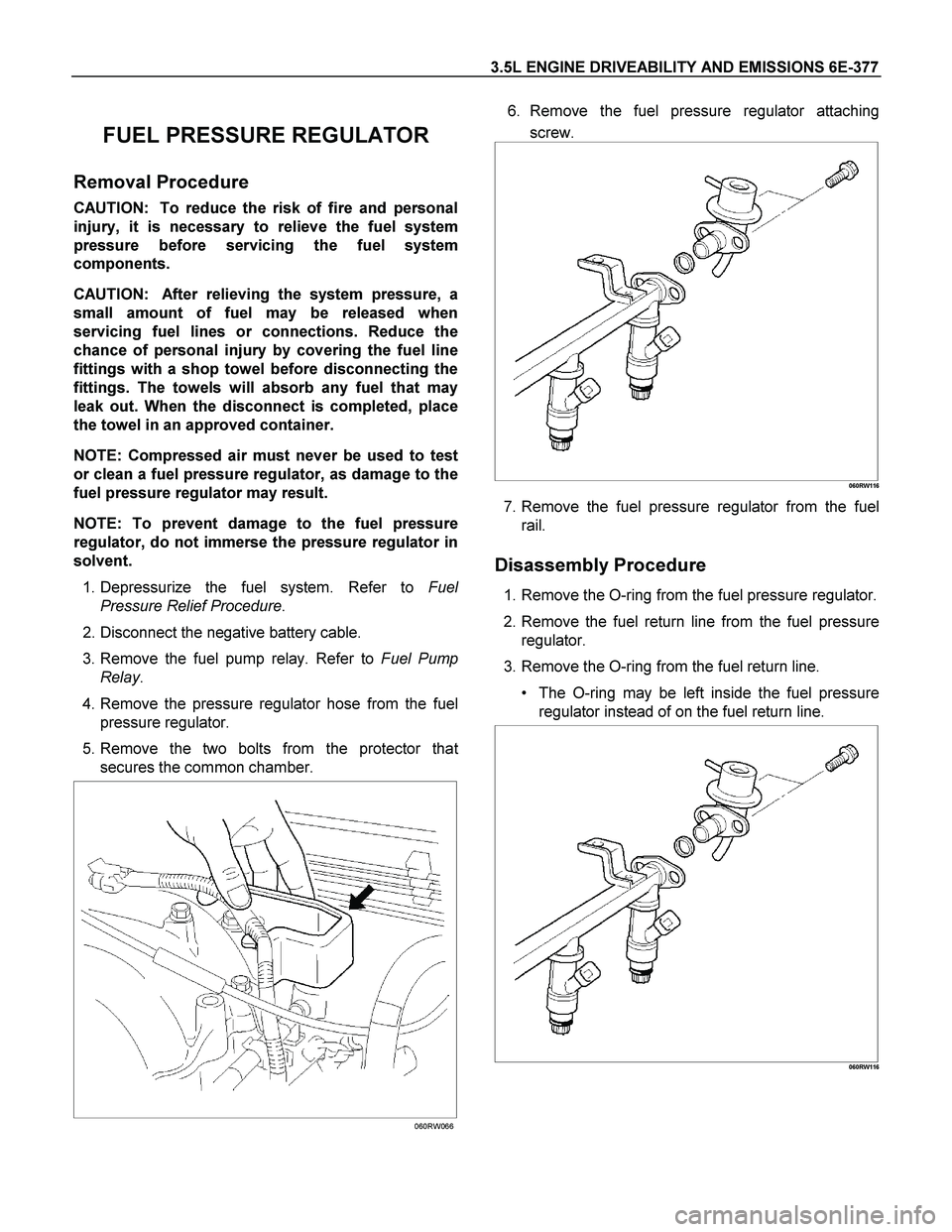
3.5L ENGINE DRIVEABILITY AND EMISSIONS 6E-377
FUEL PRESSURE REGULATOR
Removal Procedure
CAUTION: To reduce the risk of fire and personal
injury, it is necessary to relieve the fuel system
pressure before servicing the fuel system
components.
CAUTION: After relieving the system pressure, a
small amount of fuel may be released when
servicing fuel lines or connections. Reduce the
chance of personal injury by covering the fuel line
fittings with a shop towel before disconnecting the
fittings. The towels will absorb any fuel that may
leak out. When the disconnect is completed, place
the towel in an approved container.
NOTE: Compressed air must never be used to test
or clean a fuel pressure regulator, as damage to the
fuel pressure regulator may result.
NOTE: To prevent damage to the fuel pressure
regulator, do not immerse the pressure regulator in
solvent.
1. Depressurize the fuel system. Refer to Fue
l
Pressure Relief Procedure.
2. Disconnect the negative battery cable.
3. Remove the fuel pump relay. Refer to Fuel Pump
Relay.
4. Remove the pressure regulator hose from the fuel
pressure regulator.
5. Remove the two bolts from the protector tha
t
secures the common chamber.
060RW066
6. Remove the fuel pressure regulator attaching
screw.
060RW116
7. Remove the fuel pressure regulator from the fuel
rail.
Disassembly Procedure
1. Remove the O-ring from the fuel pressure regulator.
2. Remove the fuel return line from the fuel pressure
regulator.
3. Remove the O-ring from the fuel return line.
The O-ring may be left inside the fuel pressure
regulator instead of on the fuel return line.
060RW116
Page 2374 of 4264
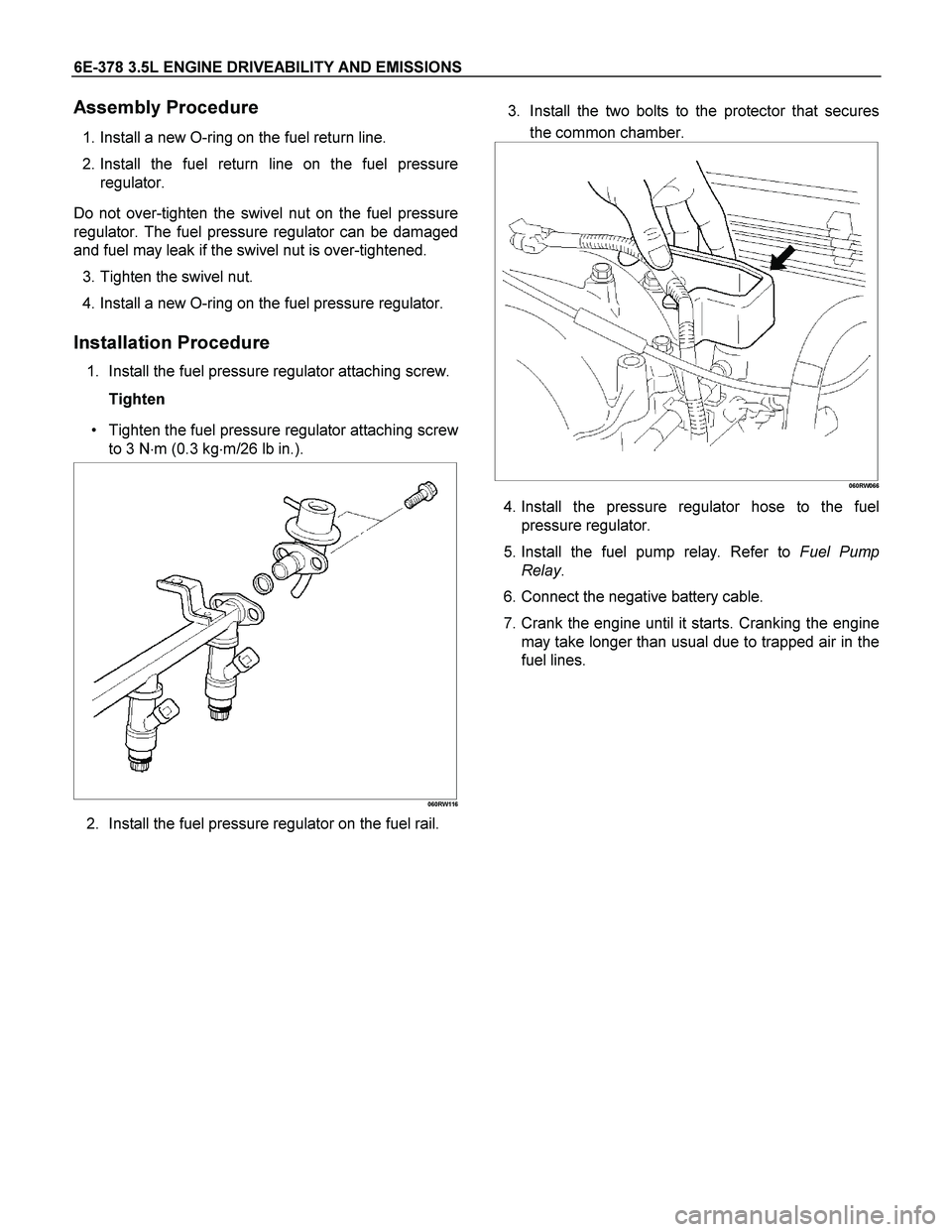
6E-378 3.5L ENGINE DRIVEABILITY AND EMISSIONS
Assembly Procedure
1. Install a new O-ring on the fuel return line.
2. Install the fuel return line on the fuel pressure
regulator.
Do not over-tighten the swivel nut on the fuel pressure
regulator. The fuel pressure regulator can be damaged
and fuel may leak if the swivel nut is over-tightened.
3. Tighten the swivel nut.
4. Install a new O-ring on the fuel pressure regulator.
Installation Procedure
1. Install the fuel pressure regulator attaching screw.
Tighten
Tighten the fuel pressure regulator attaching scre
w
to 3 Nm (0.3 kgm/26 lb in.).
060RW116
2. Install the fuel pressure regulator on the fuel rail.
3. Install the two bolts to the protector that secures
the common chamber.
060RW066
4. Install the pressure regulator hose to the fuel
pressure regulator.
5. Install the fuel pump relay. Refer to Fuel Pump
Relay.
6. Connect the negative battery cable.
7. Crank the engine until it starts. Cranking the engine
may take longer than usual due to trapped air in the
fuel lines.
Page 2407 of 4264
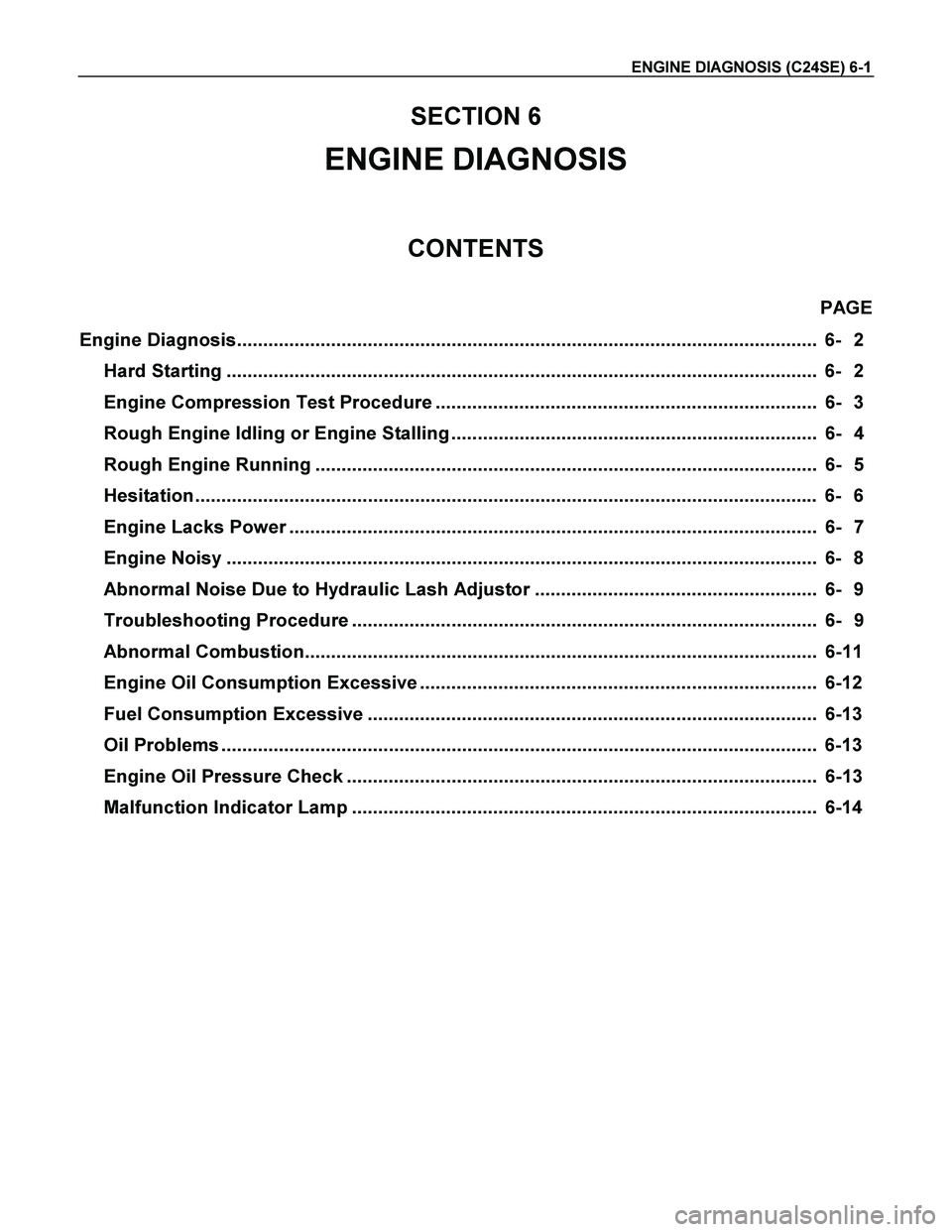
ENGINE DIAGNOSIS (C24SE) 6-1
SECTION 6
ENGINE DIAGNOSIS
CONTENTS
PAGE
Engine Diagnosis............................................................................................................... 6- 2
Hard Starting ................................................................................................................. 6- 2
Engine Compression Test Procedure ......................................................................... 6- 3
Rough Engine Idling or Engine Stalling ...................................................................... 6- 4
Rough Engine Running ................................................................................................ 6- 5
Hesitation....................................................................................................................... 6- 6
Engine Lacks Power ..................................................................................................... 6- 7
Engine Noisy ................................................................................................................. 6- 8
Abnormal Noise Due to Hydraulic Lash Adjustor ...................................................... 6- 9
Troubleshooting Procedure ......................................................................................... 6- 9
Abnormal Combustion.................................................................................................. 6-11
Engine Oil Consumption Excessive ............................................................................ 6-12
Fuel Consumption Excessive ...................................................................................... 6-13
Oil Problems .................................................................................................................. 6-13
Engine Oil Pressure Check .......................................................................................... 6-13
Malfunction Indicator Lamp ......................................................................................... 6-14
Page 2409 of 4264
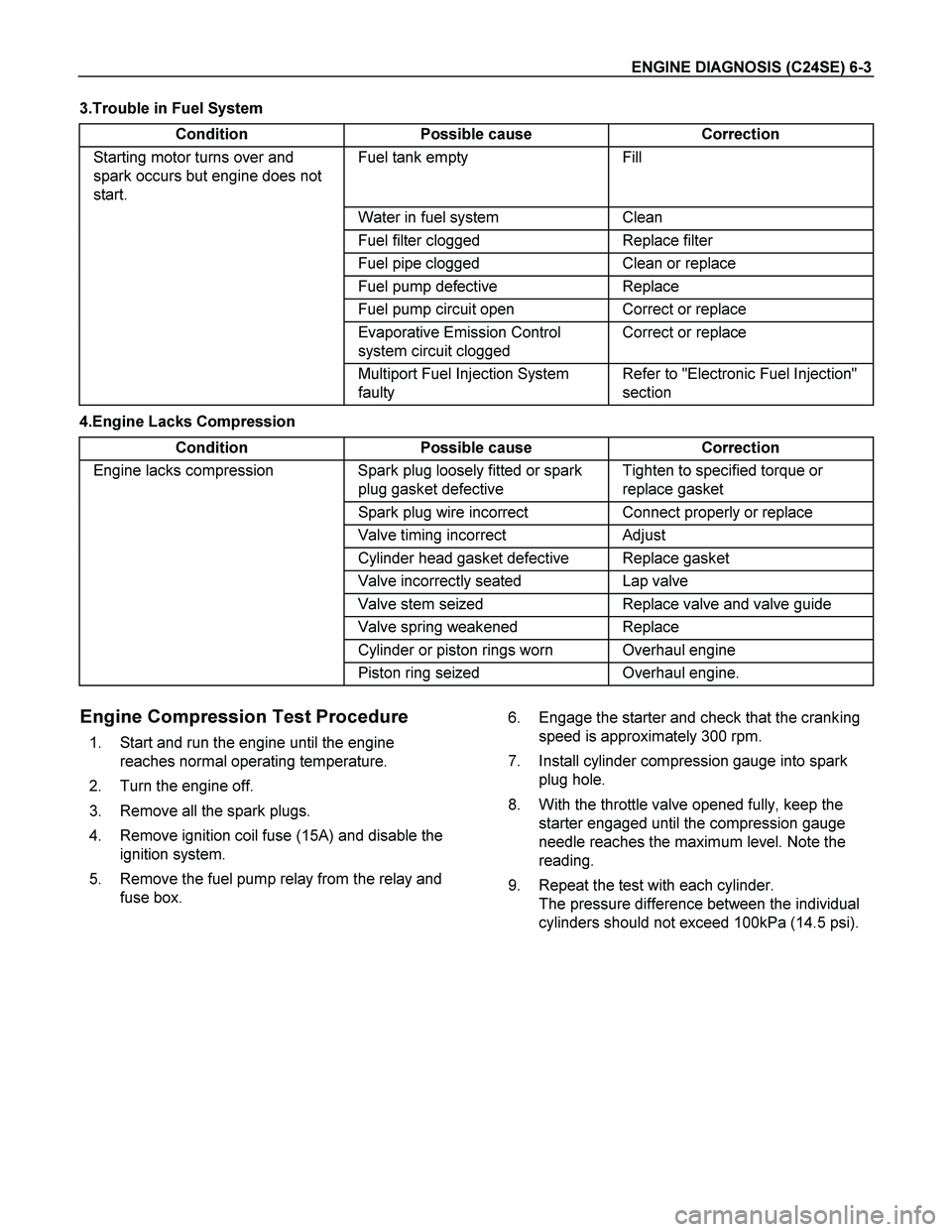
ENGINE DIAGNOSIS (C24SE) 6-3
3.Trouble in Fuel System
Condition Possible cause Correction
Starting motor turns over and
spark occurs but engine does not
start. Fuel tank empty Fill
Water in fuel system Clean
Fuel filter clogged Replace filter
Fuel pipe clogged Clean or replace
Fuel pump defective Replace
Fuel pump circuit open Correct or replace
Evaporative Emission Control
system circuit clogged Correct or replace
Multiport Fuel Injection System
faulty Refer to "Electronic Fuel Injection"
section
4.Engine Lacks Compression
Condition Possible cause Correction
Engine lacks compression Spark plug loosely fitted or spark
plug gasket defective Tighten to specified torque or
replace gasket
Spark plug wire incorrect Connect properly or replace
Valve timing incorrect Adjust
Cylinder head gasket defective Replace gasket
Valve incorrectly seated Lap valve
Valve stem seized Replace valve and valve guide
Valve spring weakened Replace
Cylinder or piston rings worn Overhaul engine
Piston ring seized Overhaul engine.
Engine Compression Test Procedure
1. Start and run the engine until the engine
reaches normal operating temperature.
2. Turn the engine off.
3. Remove all the spark plugs.
4. Remove ignition coil fuse (15A) and disable the
ignition system.
5. Remove the fuel pump relay from the relay and
fuse box. 6. Engage the starter and check that the cranking
speed is approximately 300 rpm.
7. Install cylinder compression gauge into spark
plug hole.
8. With the throttle valve opened fully, keep the
starter engaged until the compression gauge
needle reaches the maximum level. Note the
reading.
9. Repeat the test with each cylinder.
The pressure difference between the individual
cylinders should not exceed 100kPa (14.5 psi).
Page 2410 of 4264
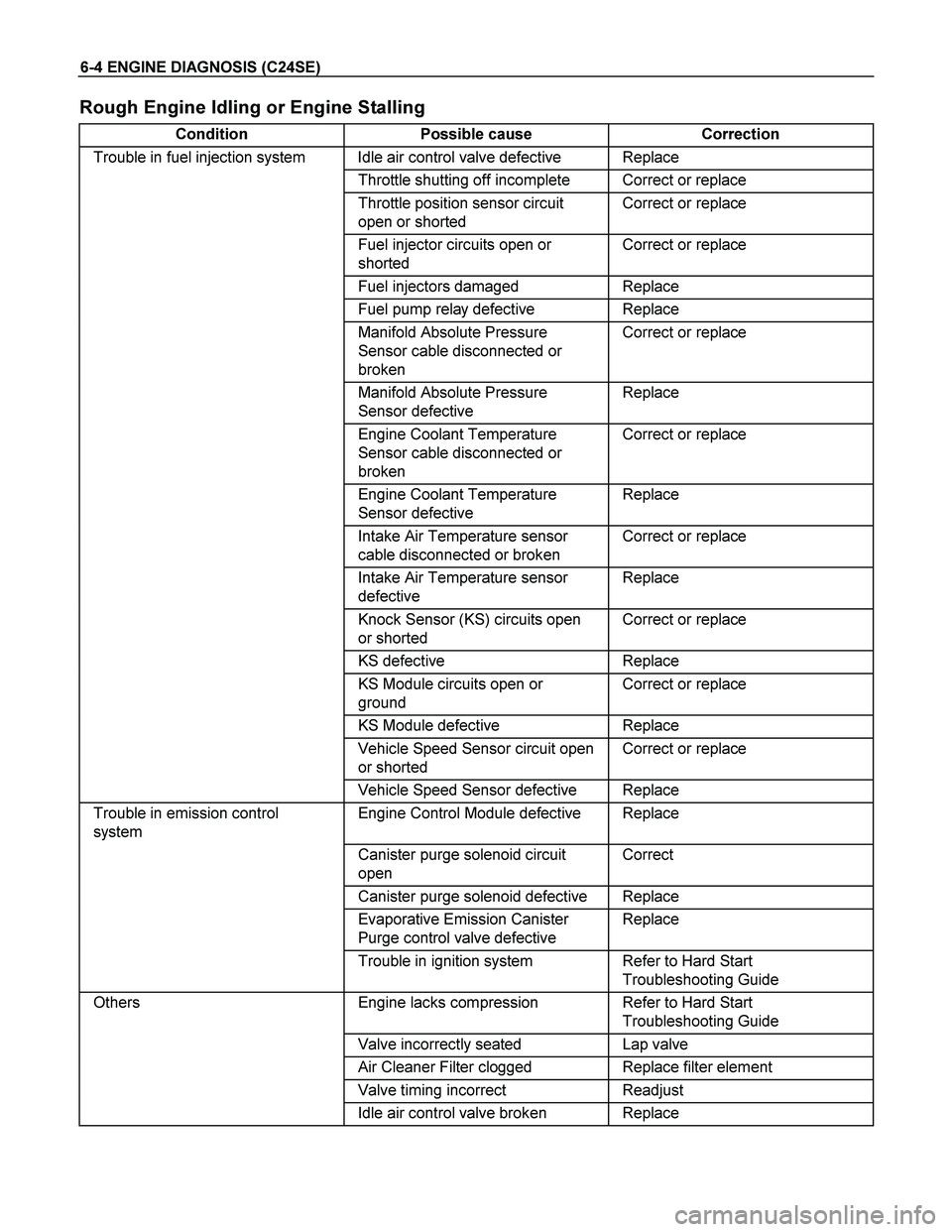
6-4 ENGINE DIAGNOSIS (C24SE)
Rough Engine Idling or Engine Stalling
Condition Possible cause Correction
Trouble in fuel injection system Idle air control valve defective Replace
Throttle shutting off incomplete Correct or replace
Throttle position sensor circuit
open or shorted Correct or replace
Fuel injector circuits open or
shorted Correct or replace
Fuel injectors damaged Replace
Fuel pump relay defective Replace
Manifold Absolute Pressure
Sensor cable disconnected or
broken Correct or replace
Manifold Absolute Pressure
Sensor defective Replace
Engine Coolant Temperature
Sensor cable disconnected or
broken Correct or replace
Engine Coolant Temperature
Sensor defective Replace
Intake Air Temperature sensor
cable disconnected or broken Correct or replace
Intake Air Temperature sensor
defective Replace
Knock Sensor (KS) circuits open
or shorted Correct or replace
KS defective Replace
KS Module circuits open or
ground Correct or replace
KS Module defective Replace
Vehicle Speed Sensor circuit open
or shorted Correct or replace
Vehicle Speed Sensor defective Replace
Trouble in emission control
system Engine Control Module defective Replace
Canister purge solenoid circuit
open Correct
Canister purge solenoid defective Replace
Evaporative Emission Canister
Purge control valve defective Replace
Trouble in ignition system Refer to Hard Start
Troubleshooting Guide
Others Engine lacks compression Refer to Hard Start
Troubleshooting Guide
Valve incorrectly seated Lap valve
Air Cleaner Filter clogged Replace filter element
Valve timing incorrect Readjust
Idle air control valve broken Replace
Page 2411 of 4264
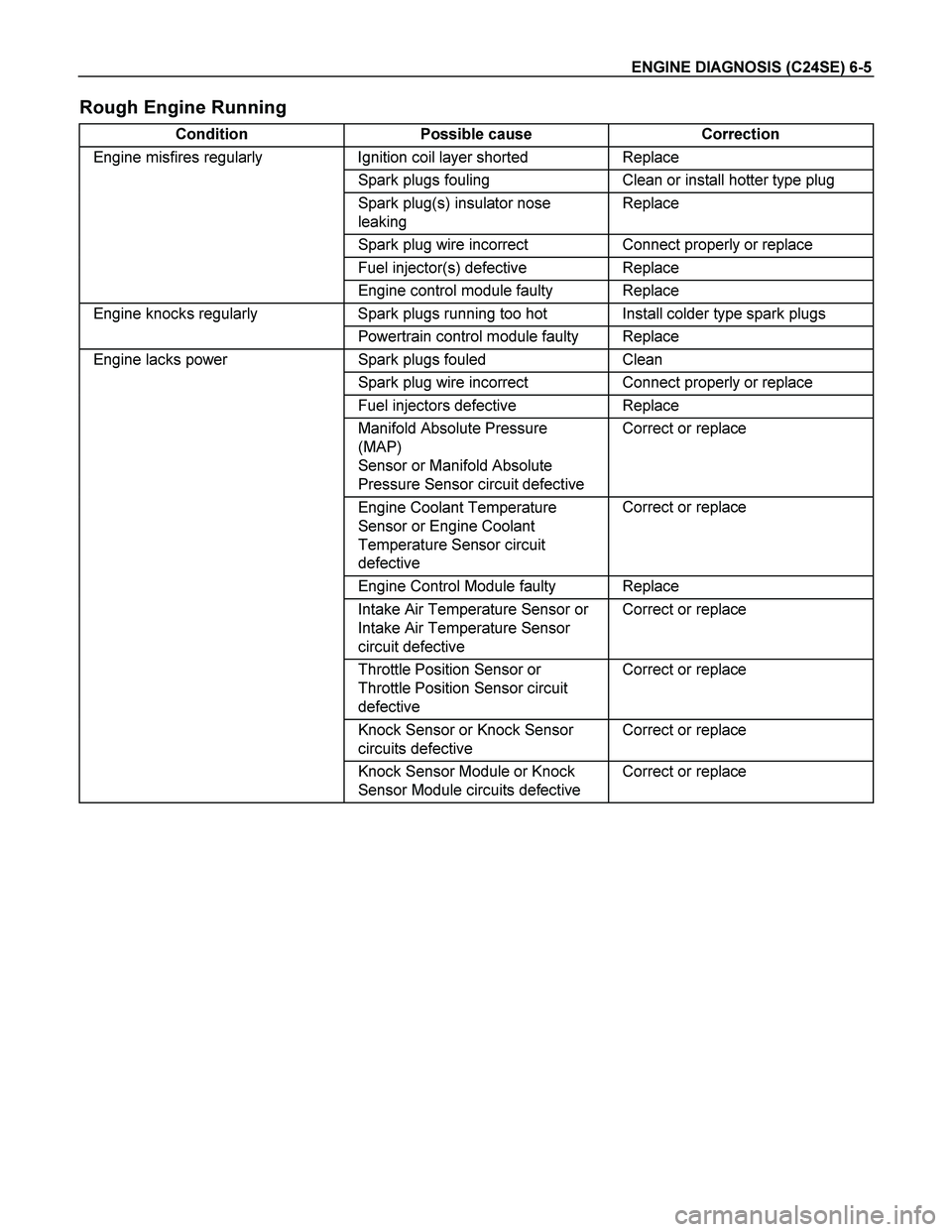
ENGINE DIAGNOSIS (C24SE) 6-5
Rough Engine Running
Condition Possible cause Correction
Engine misfires regularly Ignition coil layer shorted Replace
Spark plugs fouling Clean or install hotter type plug
Spark plug(s) insulator nose
leaking Replace
Spark plug wire incorrect Connect properly or replace
Fuel injector(s) defective Replace
Engine control module faulty Replace
Engine knocks regularly Spark plugs running too hot Install colder type spark plugs
Powertrain control module faulty Replace
Engine lacks power Spark plugs fouled Clean
Spark plug wire incorrect Connect properly or replace
Fuel injectors defective Replace
Manifold Absolute Pressure
(MAP)
Sensor or Manifold Absolute
Pressure Sensor circuit defective Correct or replace
Engine Coolant Temperature
Sensor or Engine Coolant
Temperature Sensor circuit
defective Correct or replace
Engine Control Module faulty Replace
Intake Air Temperature Sensor or
Intake Air Temperature Sensor
circuit defective Correct or replace
Throttle Position Sensor or
Throttle Position Sensor circuit
defective Correct or replace
Knock Sensor or Knock Sensor
circuits defective Correct or replace
Knock Sensor Module or Knock
Sensor Module circuits defective Correct or replace
Page 2412 of 4264
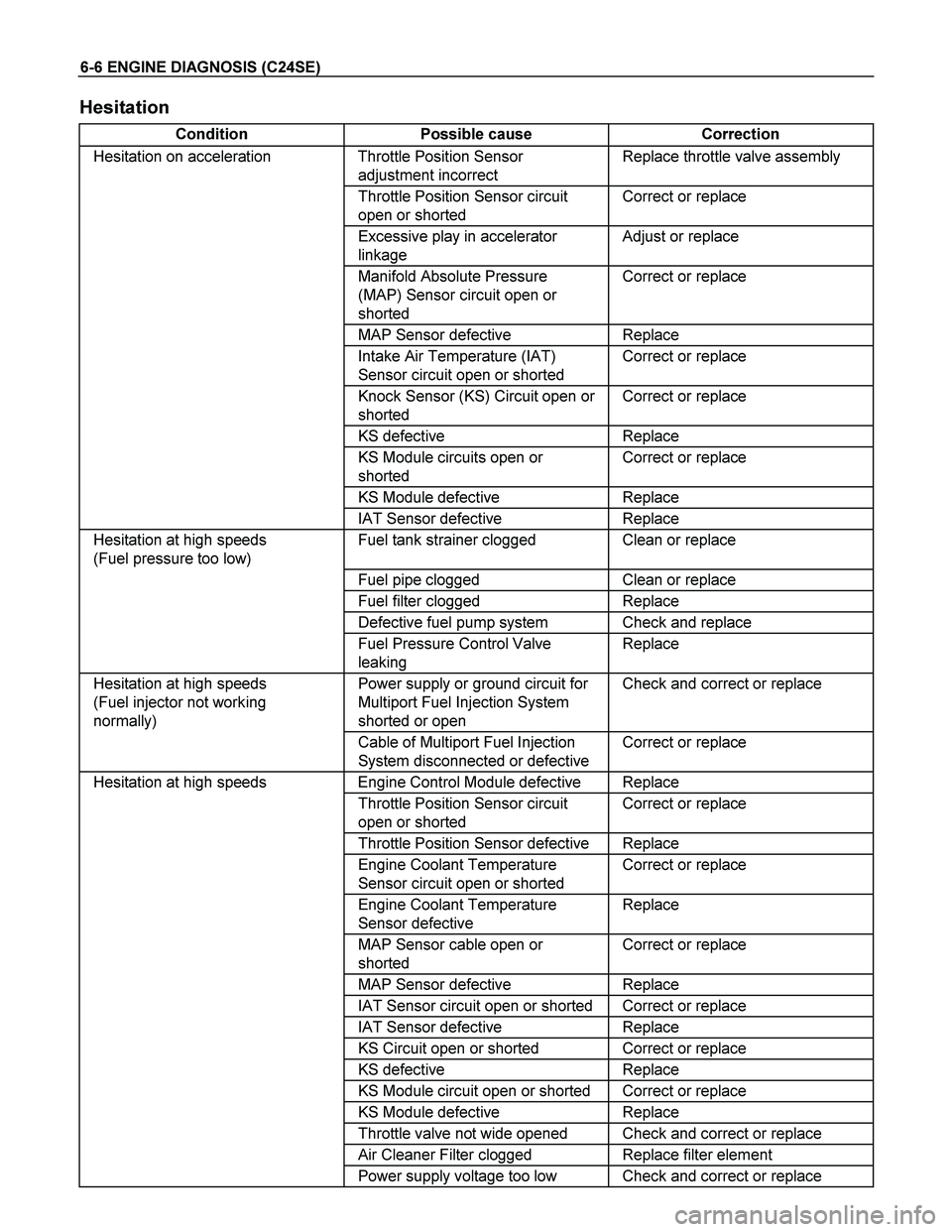
6-6 ENGINE DIAGNOSIS (C24SE)
Hesitation
Condition Possible cause Correction
Hesitation on acceleration Throttle Position Sensor
adjustment incorrect Replace throttle valve assembly
Throttle Position Sensor circuit
open or shorted Correct or replace
Excessive play in accelerator
linkage Adjust or replace
Manifold Absolute Pressure
(MAP) Sensor circuit open or
shorted Correct or replace
MAP Sensor defective Replace
Intake Air Temperature (IAT)
Sensor circuit open or shorted Correct or replace
Knock Sensor (KS) Circuit open or
shorted Correct or replace
KS defective Replace
KS Module circuits open or
shorted Correct or replace
KS Module defective Replace
IAT Sensor defective Replace
Hesitation at high speeds
(Fuel pressure too low) Fuel tank strainer clogged Clean or replace
Fuel pipe clogged Clean or replace
Fuel filter clogged Replace
Defective fuel pump system Check and replace
Fuel Pressure Control Valve
leaking Replace
Hesitation at high speeds
(Fuel injector not working
normally) Power supply or ground circuit for
Multiport Fuel Injection System
shorted or open Check and correct or replace
Cable of Multiport Fuel Injection
System disconnected or defective Correct or replace
Hesitation at high speeds Engine Control Module defective Replace
Throttle Position Sensor circuit
open or shorted Correct or replace
Throttle Position Sensor defective Replace
Engine Coolant Temperature
Sensor circuit open or shorted Correct or replace
Engine Coolant Temperature
Sensor defective Replace
MAP Sensor cable open or
shorted Correct or replace
MAP Sensor defective Replace
IAT Sensor circuit open or shorted Correct or replace
IAT Sensor defective Replace
KS Circuit open or shorted Correct or replace
KS defective Replace
KS Module circuit open or shorted Correct or replace
KS Module defective Replace
Throttle valve not wide opened Check and correct or replace
Air Cleaner Filter clogged Replace filter element
Power supply voltage too low Check and correct or replace
Page 2413 of 4264
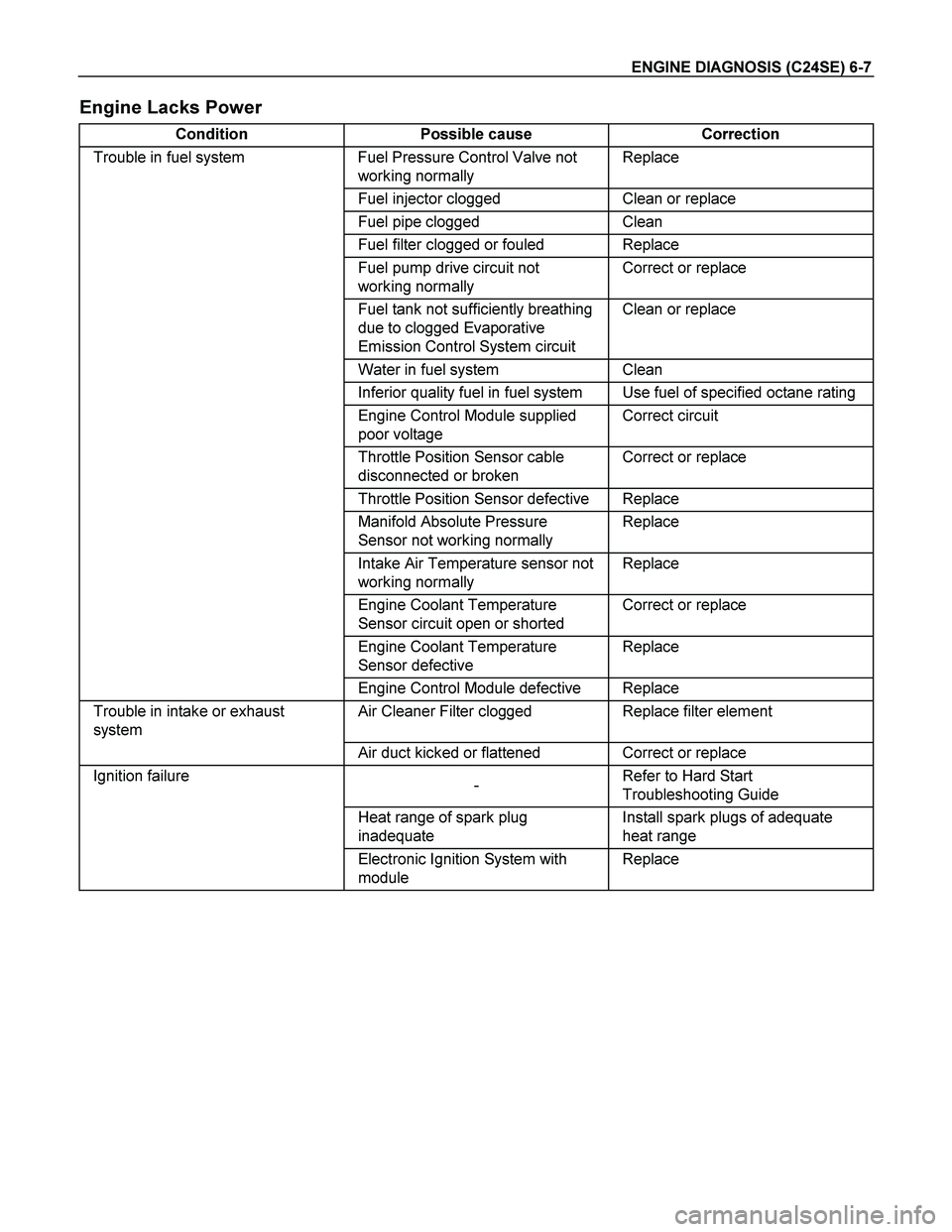
ENGINE DIAGNOSIS (C24SE) 6-7
Engine Lacks Power
Condition Possible cause Correction
Trouble in fuel system Fuel Pressure Control Valve not
working normally Replace
Fuel injector clogged Clean or replace
Fuel pipe clogged Clean
Fuel filter clogged or fouled Replace
Fuel pump drive circuit not
working normally Correct or replace
Fuel tank not sufficiently breathing
due to clogged Evaporative
Emission Control System circuit Clean or replace
Water in fuel system Clean
Inferior quality fuel in fuel system Use fuel of specified octane rating
Engine Control Module supplied
poor voltage Correct circuit
Throttle Position Sensor cable
disconnected or broken Correct or replace
Throttle Position Sensor defective Replace
Manifold Absolute Pressure
Sensor not working normally Replace
Intake Air Temperature sensor not
working normally Replace
Engine Coolant Temperature
Sensor circuit open or shorted Correct or replace
Engine Coolant Temperature
Sensor defective Replace
Engine Control Module defective Replace
Trouble in intake or exhaust
system Air Cleaner Filter clogged Replace filter element
Air duct kicked or flattened Correct or replace
Ignition failure
- Refer to Hard Start
Troubleshooting Guide
Heat range of spark plug
inadequate Install spark plugs of adequate
heat range
Electronic Ignition System with
module Replace