check engine ISUZU TF SERIES 2004 Workshop Manual
[x] Cancel search | Manufacturer: ISUZU, Model Year: 2004, Model line: TF SERIES, Model: ISUZU TF SERIES 2004Pages: 4264, PDF Size: 72.63 MB
Page 30 of 4264
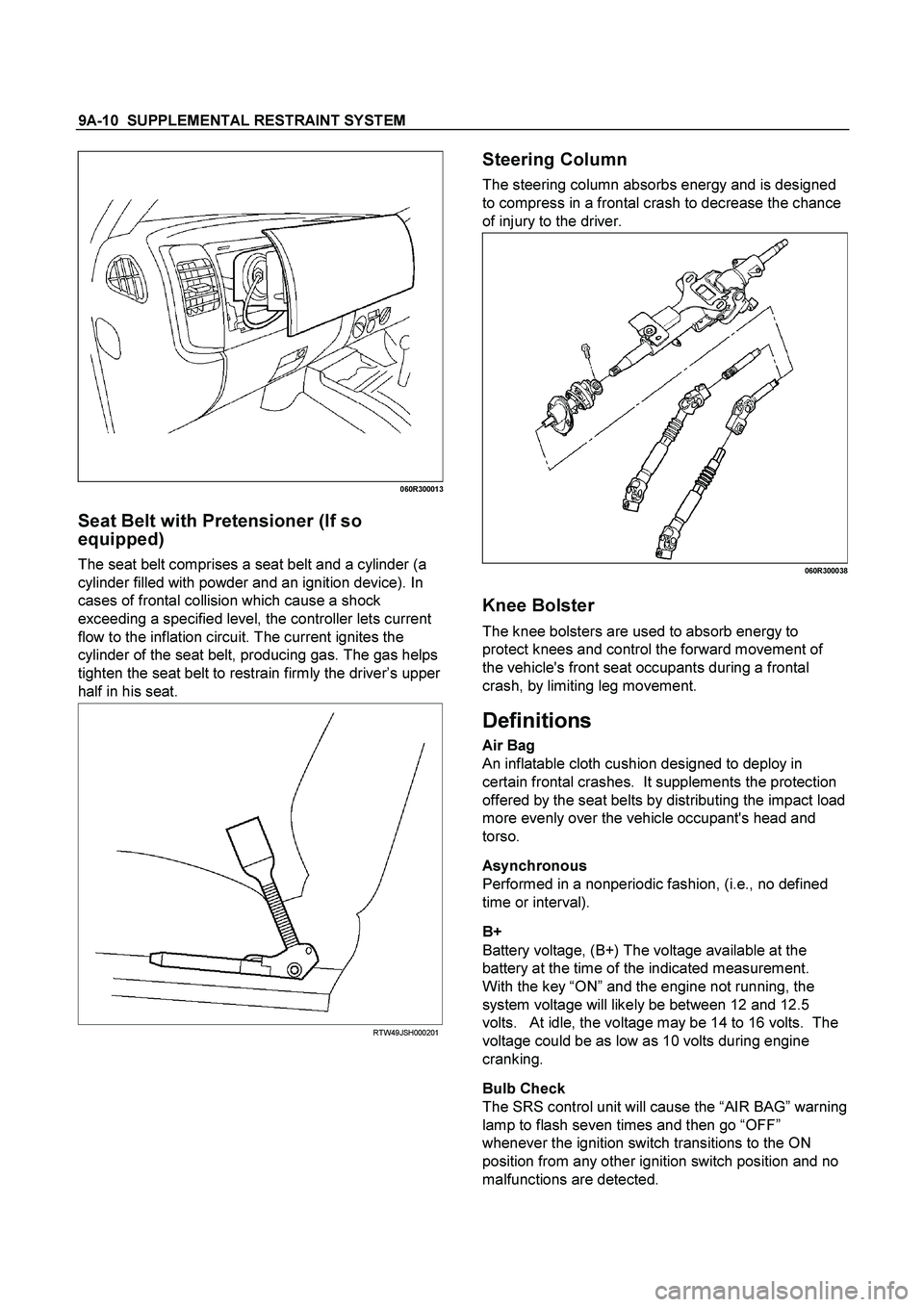
9A-10 SUPPLEMENTAL RESTRAINT SYSTEM
060R300013
Seat Belt with Pretensioner (If so
equipped)
The seat belt comprises a seat belt and a cylinder (a
cylinder filled with powder and an ignition device). In
cases of frontal collision which cause a shock
exceeding a specified level, the controller lets current
flow to the inflation circuit. The current ignites the
cylinder of the seat belt, producing gas. The gas helps
tighten the seat belt to restrain firmly the driver’s upper
half in his seat.
RTW49JSH000201
Steering Column
The steering column absorbs energy and is designed
to compress in a frontal crash to decrease the chance
of injury to the driver.
060R300038
Knee Bolster
The knee bolsters are used to absorb energy to
protect knees and control the forward movement of
the vehicle's front seat occupants during a frontal
crash, by limiting leg movement.
Definitions
Air Bag
An inflatable cloth cushion designed to deploy in
certain frontal crashes. It supplements the protection
offered by the seat belts by distributing the impact load
more evenly over the vehicle occupant's head and
torso.
Asynchronous
Performed in a nonperiodic fashion, (i.e., no defined
time or interval).
B+
Battery voltage, (B+) The voltage available at the
battery at the time of the indicated measurement.
With the key “ON” and the engine not running, the
system voltage will likely be between 12 and 12.5
volts. At idle, the voltage may be 14 to 16 volts. The
voltage could be as low as 10 volts during engine
cranking.
Bulb Check
The SRS control unit will cause the “AIR BAG” warning
lamp to flash seven times and then go “OFF”
whenever the ignition switch transitions to the ON
position from any other ignition switch position and no
malfunctions are detected.
Page 207 of 4264
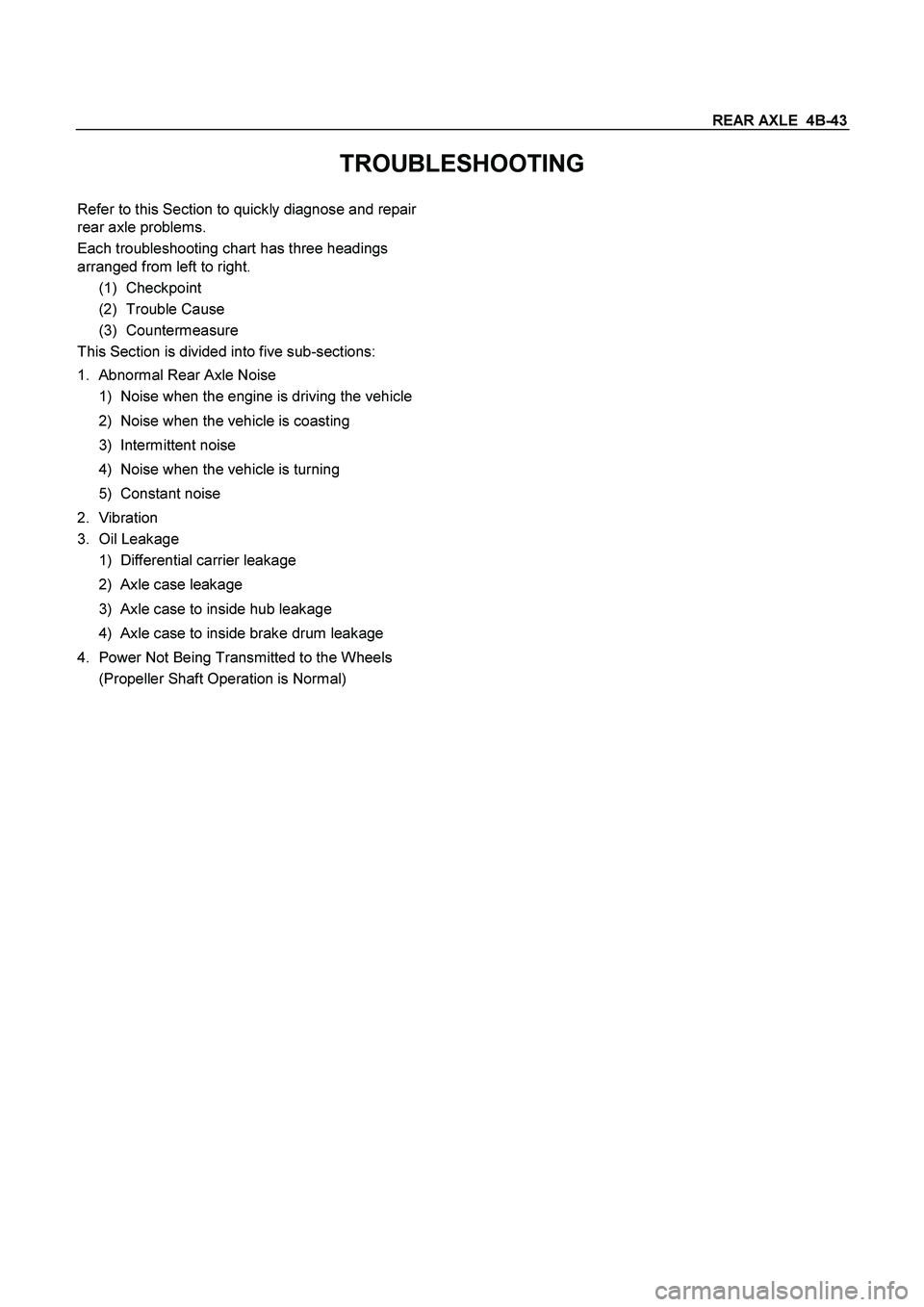
REAR AXLE 4B-43
TROUBLESHOOTING
Refer to this Section to quickly diagnose and repair
rear axle problems.
Each troubleshooting chart has three headings
arranged from left to right.
(1) Checkpoint
(2) Trouble Cause
(3) Countermeasure
This Section is divided into five sub-sections:
1. Abnormal Rear Axle Noise
1) Noise when the engine is driving the vehicle
2) Noise when the vehicle is coasting
3) Intermittent noise
4) Noise when the vehicle is turning
5) Constant noise
2. Vibration
3. Oil Leakage
1) Differential carrier leakage
2) Axle case leakage
3) Axle case to inside hub leakage
4) Axle case to inside brake drum leakage
4. Power Not Being Transmitted to the Wheels
(Propeller Shaft Operation is Normal)
Page 208 of 4264
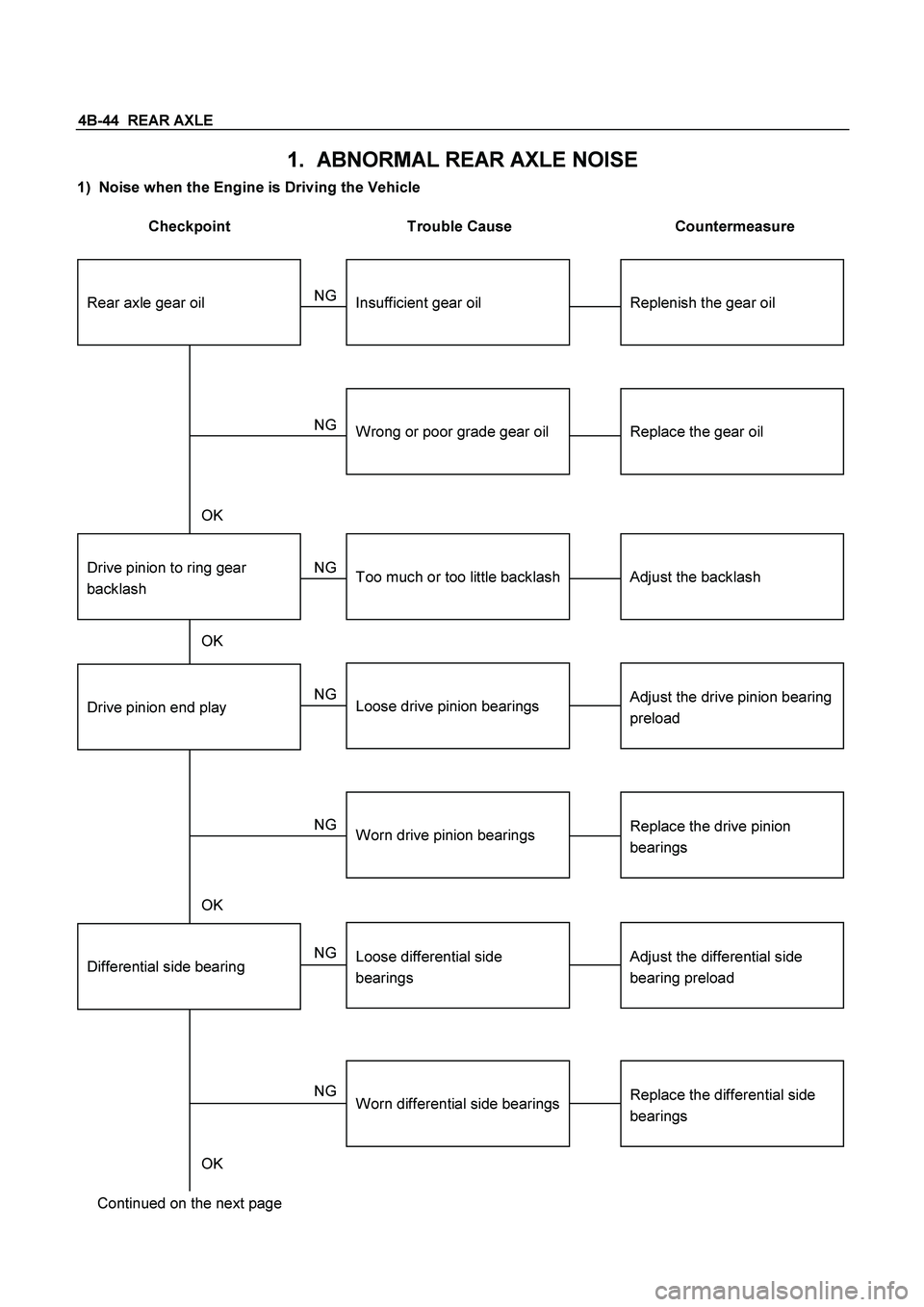
4B-44 REAR AXLE
1. ABNORMAL REAR AXLE NOISE
1) Noise when the Engine is Driving the Vehicle
Checkpoint Trouble Cause Countermeasure
Replenish the gear oilInsufficient gear oil NG
Differential side bearingAdjust the differential side
bearing preload
Replace the drive pinion
bearings
Adjust the drive pinion bearing
preload
Replace the gear oil
Loose differential side
bearings
Worn drive pinion bearings
Loose drive pinion bearings
Wrong or poor grade gear oil
Drive pinion to ring gear
backlash
Drive pinion end play
Adjust the backlashToo much or too little backlash
Continued on the next pageOK OK
NG NG NG NG NG
OK
OK
Rear axle gear oil
Replace the differential side
bearingsWorn differential side bearings NG
Page 337 of 4264
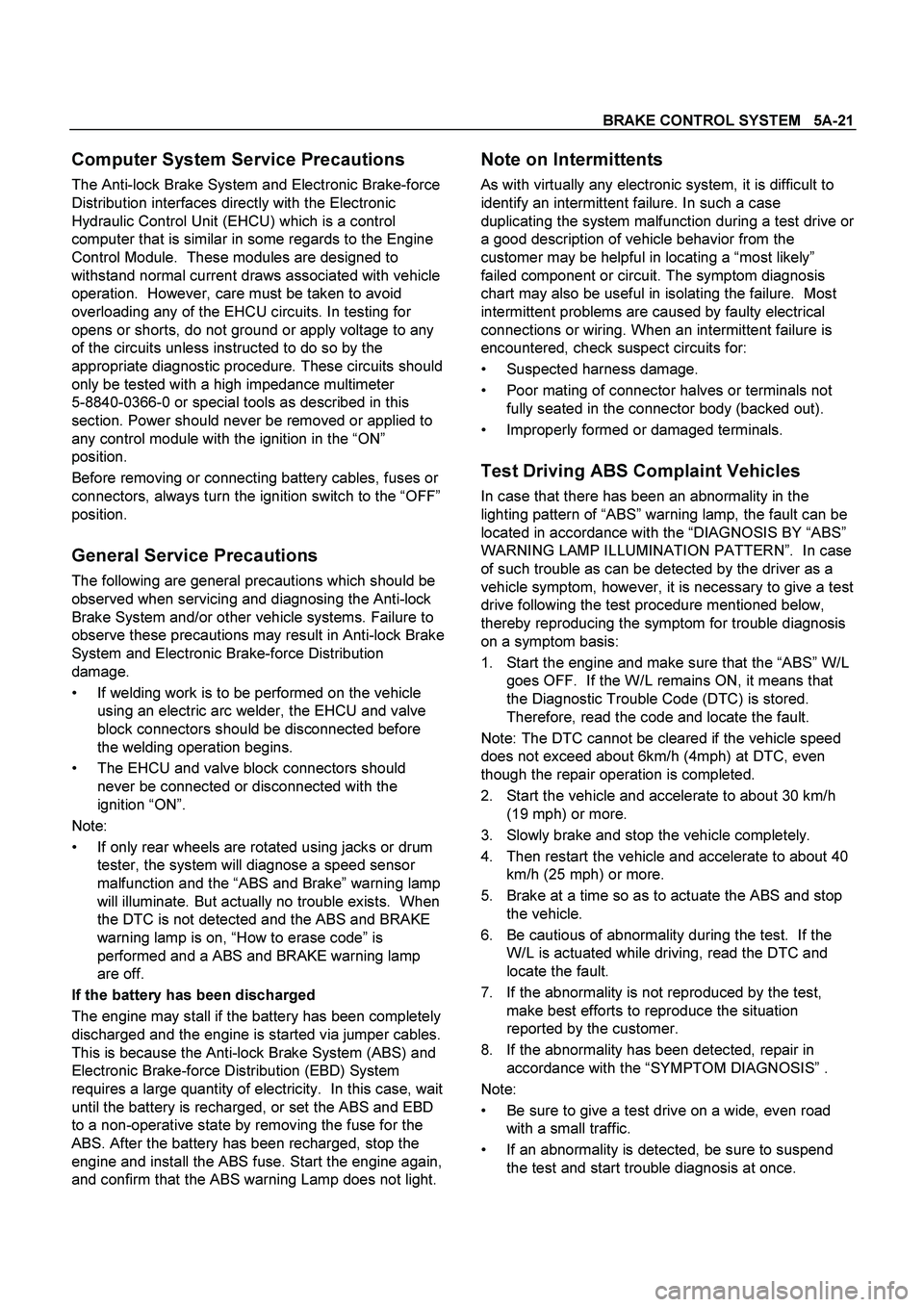
BRAKE CONTROL SYSTEM 5A-21
Computer System Service Precautions
The Anti-lock Brake System and Electronic Brake-force
Distribution interfaces directly with the Electronic
Hydraulic Control Unit (EHCU) which is a control
computer that is similar in some regards to the Engine
Control Module. These modules are designed to
withstand normal current draws associated with vehicle
operation. However, care must be taken to avoid
overloading any of the EHCU circuits. In testing for
opens or shorts, do not ground or apply voltage to any
of the circuits unless instructed to do so by the
appropriate diagnostic procedure. These circuits should
only be tested with a high impedance multimeter
5-8840-0366-0 or special tools as described in this
section. Power should never be removed or applied to
any control module with the ignition in the “ON”
position.
Before removing or connecting battery cables, fuses or
connectors, always turn the ignition switch to the “OFF”
position.
General Service Precautions
The following are general precautions which should be
observed when servicing and diagnosing the Anti-lock
Brake System and/or other vehicle systems. Failure to
observe these precautions may result in Anti-lock Brake
System and Electronic Brake-force Distribution
damage.
If welding work is to be performed on the vehicle
using an electric arc welder, the EHCU and valve
block connectors should be disconnected before
the welding operation begins.
The EHCU and valve block connectors should
never be connected or disconnected with the
ignition “ON”.
Note:
If only rear wheels are rotated using jacks or drum
tester, the system will diagnose a speed sensor
malfunction and the “ABS and Brake” warning lamp
will illuminate. But actually no trouble exists. When
the DTC is not detected and the ABS and BRAKE
warning lamp is on, “How to erase code” is
performed and a ABS and BRAKE warning lamp
are off.
If the battery has been discharged
The engine may stall if the battery has been completely
discharged and the engine is started via jumper cables.
This is because the Anti-lock Brake System (ABS) and
Electronic Brake-force Distribution (EBD) System
requires a large quantity of electricity. In this case, wait
until the battery is recharged, or set the ABS and EBD
to a non-operative state by removing the fuse for the
ABS. After the battery has been recharged, stop the
engine and install the ABS fuse. Start the engine again,
and confirm that the ABS warning Lamp does not light.
Note on Intermittents
As with virtually any electronic system, it is difficult to
identify an intermittent failure. In such a case
duplicating the system malfunction during a test drive or
a good description of vehicle behavior from the
customer may be helpful in locating a “most likely”
failed component or circuit. The symptom diagnosis
chart may also be useful in isolating the failure. Most
intermittent problems are caused by faulty electrical
connections or wiring. When an intermittent failure is
encountered, check suspect circuits for:
Suspected harness damage.
Poor mating of connector halves or terminals not
fully seated in the connector body (backed out).
Improperly formed or damaged terminals.
Test Driving ABS Complaint Vehicles
In case that there has been an abnormality in the
lighting pattern of “ABS” warning lamp, the fault can be
located in accordance with the “DIAGNOSIS BY “ABS”
WARNING LAMP ILLUMINATION PATTERN”. In case
of such trouble as can be detected by the driver as a
vehicle symptom, however, it is necessary to give a test
drive following the test procedure mentioned below,
thereby reproducing the symptom for trouble diagnosis
on a symptom basis:
1.
Start the engine and make sure that the “ABS” W/L
goes OFF. If the W/L remains ON, it means that
the Diagnostic Trouble Code (DTC) is stored.
Therefore, read the code and locate the fault.
Note: The DTC cannot be cleared if the vehicle speed
does not exceed about 6km/h (4mph) at DTC, even
though the repair operation is completed.
2. Start the vehicle and accelerate to about 30 km/h
(19 mph) or more.
3. Slowly brake and stop the vehicle completely.
4. Then restart the vehicle and accelerate to about 40
km/h (25 mph) or more.
5. Brake at a time so as to actuate the ABS and stop
the vehicle.
6. Be cautious of abnormality during the test. If the
W/L is actuated while driving, read the DTC and
locate the fault.
7. If the abnormality is not reproduced by the test,
make best efforts to reproduce the situation
reported by the customer.
8. If the abnormality has been detected, repair in
accordance with the “SYMPTOM DIAGNOSIS” .
Note:
Be sure to give a test drive on a wide, even road
with a small traffic.
If an abnormality is detected, be sure to suspend
the test and start trouble diagnosis at once.
Page 338 of 4264
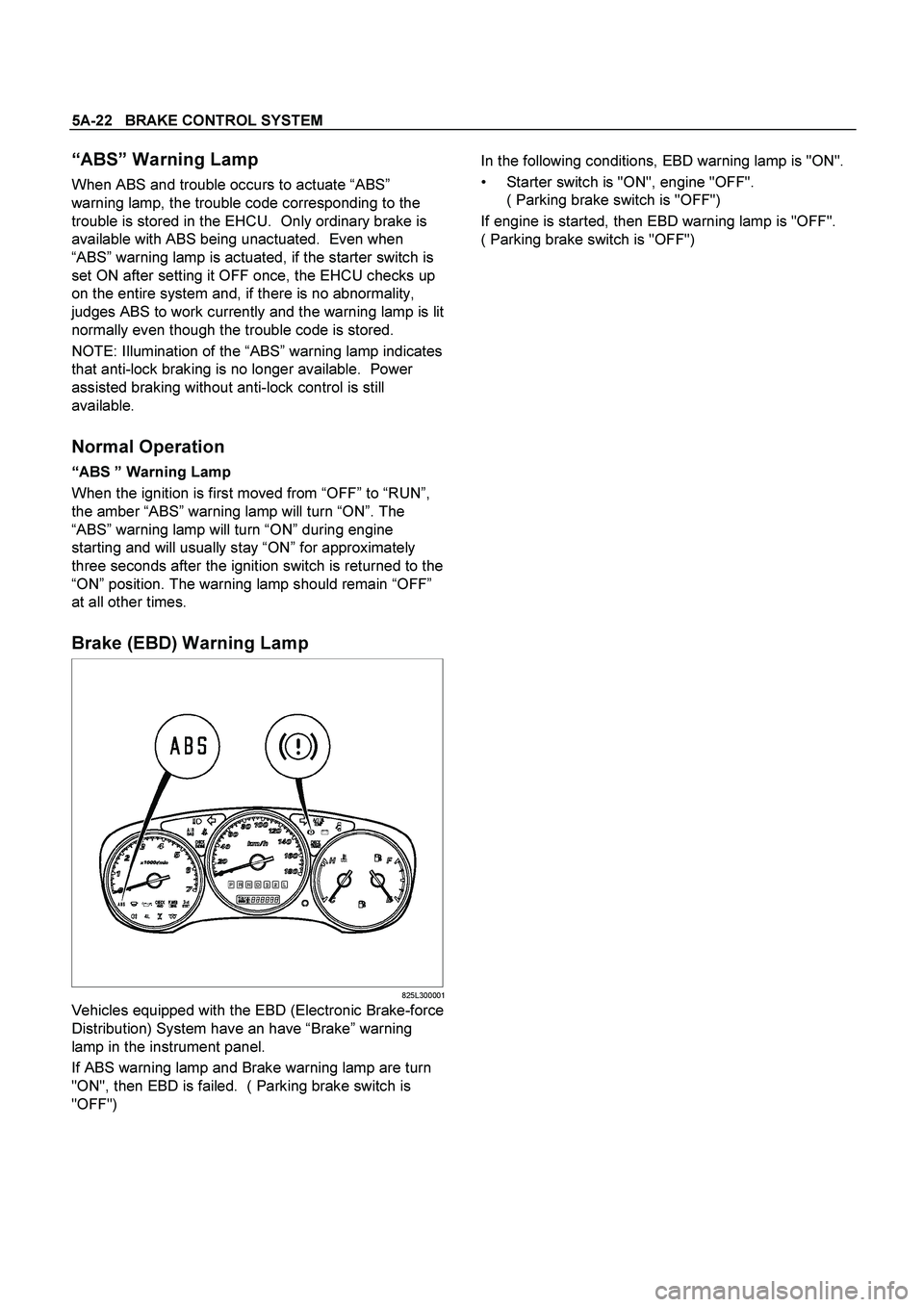
5A-22 BRAKE CONTROL SYSTEM
“ABS” Warning Lamp
When ABS and trouble occurs to actuate “ABS”
warning lamp, the trouble code corresponding to the
trouble is stored in the EHCU. Only ordinary brake is
available with ABS being unactuated. Even when
“ABS” warning lamp is actuated, if the starter switch is
set ON after setting it OFF once, the EHCU checks up
on the entire system and, if there is no abnormality,
judges ABS to work currently and the warning lamp is lit
normally even though the trouble code is stored.
NOTE: Illumination of the “ABS” warning lamp indicates
that anti-lock braking is no longer available. Power
assisted braking without anti-lock control is still
available.
Normal Operation
“ABS ” Warning Lamp
When the ignition is first moved from “OFF” to “RUN”,
the amber “ABS” warning lamp will turn “ON”. The
“ABS” warning lamp will turn “ON” during engine
starting and will usually stay “ON” for approximately
three seconds after the ignition switch is returned to the
“ON” position. The warning lamp should remain “OFF”
at all other times.
Brake (EBD) Warning Lamp
825L300001
Vehicles equipped with the EBD (Electronic Brake-force
Distribution) System have an have “Brake” warning
lamp in the instrument panel.
If ABS warning lamp and Brake warning lamp are turn
"ON", then EBD is failed. ( Parking brake switch is
"OFF")
In the following conditions, EBD warning lamp is "ON".
Starter switch is "ON", engine "OFF".
( Parking brake switch is "OFF")
If engine is started, then EBD warning lamp is "OFF".
( Parking brake switch is "OFF")
Page 343 of 4264
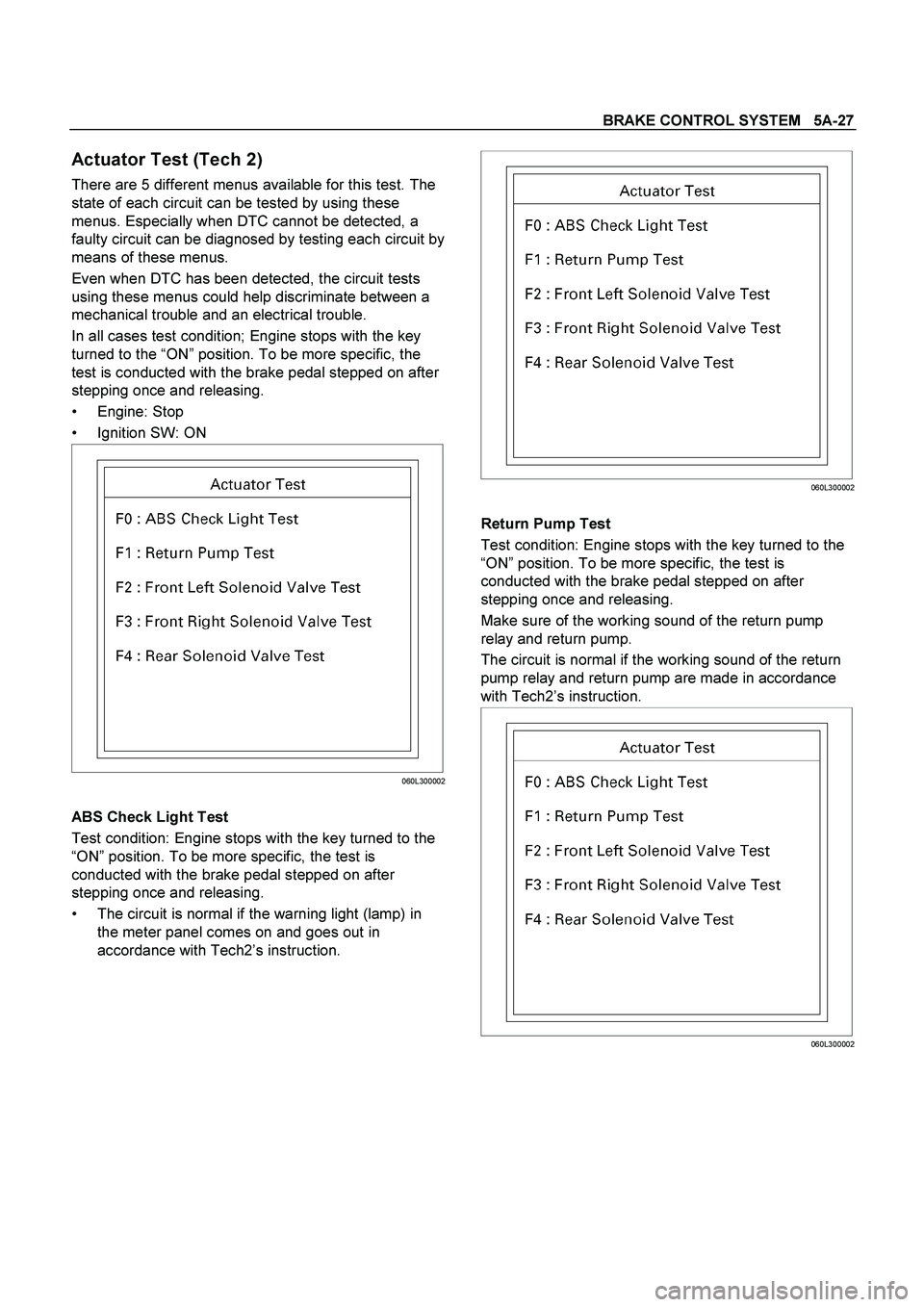
BRAKE CONTROL SYSTEM 5A-27
Actuator Test (Tech 2)
There are 5 different menus available for this test. The
state of each circuit can be tested by using these
menus. Especially when DTC cannot be detected, a
faulty circuit can be diagnosed by testing each circuit by
means of these menus.
Even when DTC has been detected, the circuit tests
using these menus could help discriminate between a
mechanical trouble and an electrical trouble.
In all cases test condition; Engine stops with the key
turned to the “ON” position. To be more specific, the
test is conducted with the brake pedal stepped on after
stepping once and releasing.
Engine: Stop
Ignition SW: ON
060L300002
ABS Check Light Test
Test condition: Engine stops with the key turned to the
“ON” position. To be more specific, the test is
conducted with the brake pedal stepped on after
stepping once and releasing.
The circuit is normal if the warning light (lamp) in
the meter panel comes on and goes out in
accordance with Tech2’s instruction.
060L300002
Return Pump Test
Test condition: Engine stops with the key turned to the
“ON” position. To be more specific, the test is
conducted with the brake pedal stepped on after
stepping once and releasing.
Make sure of the working sound of the return pump
relay and return pump.
The circuit is normal if the working sound of the return
pump relay and return pump are made in accordance
with Tech2’s instruction.
060L300002
Page 344 of 4264
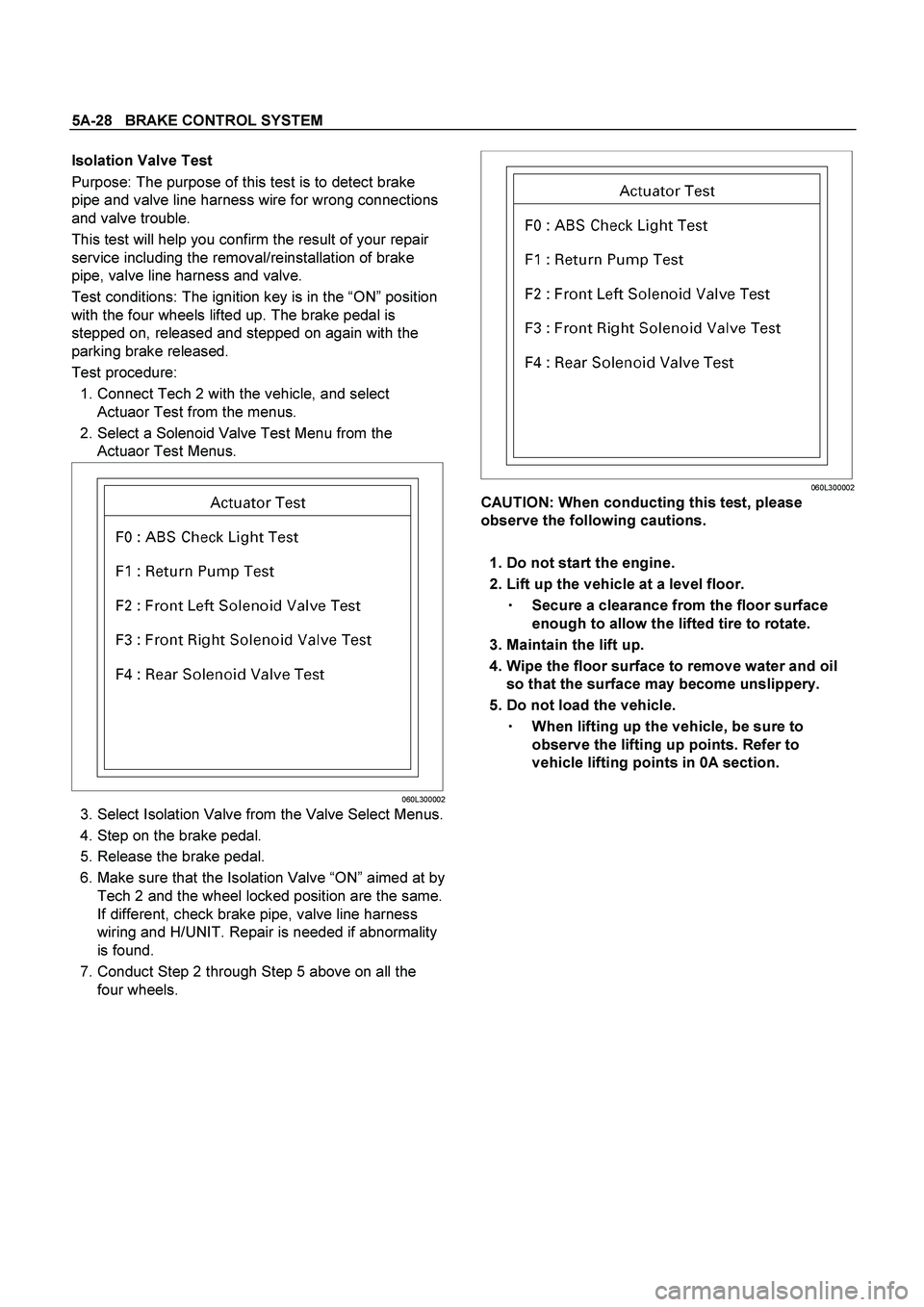
5A-28 BRAKE CONTROL SYSTEM
Isolation Valve Test
Purpose: The purpose of this test is to detect brake
pipe and valve line harness wire for wrong connections
and valve trouble.
This test will help you confirm the result of your repair
service including the removal/reinstallation of brake
pipe, valve line harness and valve.
Test conditions: The ignition key is in the “ON” position
with the four wheels lifted up. The brake pedal is
stepped on, released and stepped on again with the
parking brake released.
Test procedure:
1. Connect Tech 2 with the vehicle, and select
Actuaor Test from the menus.
2. Select a Solenoid Valve Test Menu from the
Actuaor Test Menus.
060L300002
3. Select Isolation Valve from the Valve Select Menus.
4. Step on the brake pedal.
5. Release the brake pedal.
6. Make sure that the Isolation Valve “ON” aimed at by
Tech 2 and the wheel locked position are the same.
If different, check brake pipe, valve line harness
wiring and H/UNIT. Repair is needed if abnormality
is found.
7. Conduct Step 2 through Step 5 above on all the
four wheels.
060L300002
CAUTION: When conducting this test, please
observe the following cautions.
1. Do not start the engine.
2. Lift up the vehicle at a level floor.
Secure a clearance from the floor surface
enough to allow the lifted tire to rotate.
3. Maintain the lift up.
4. Wipe the floor surface to remove water and oil
so that the surface may become unslippery.
5. Do not load the vehicle.
When lifting up the vehicle, be sure to
observe the lifting up points. Refer to
vehicle lifting points in 0A section.
Page 345 of 4264
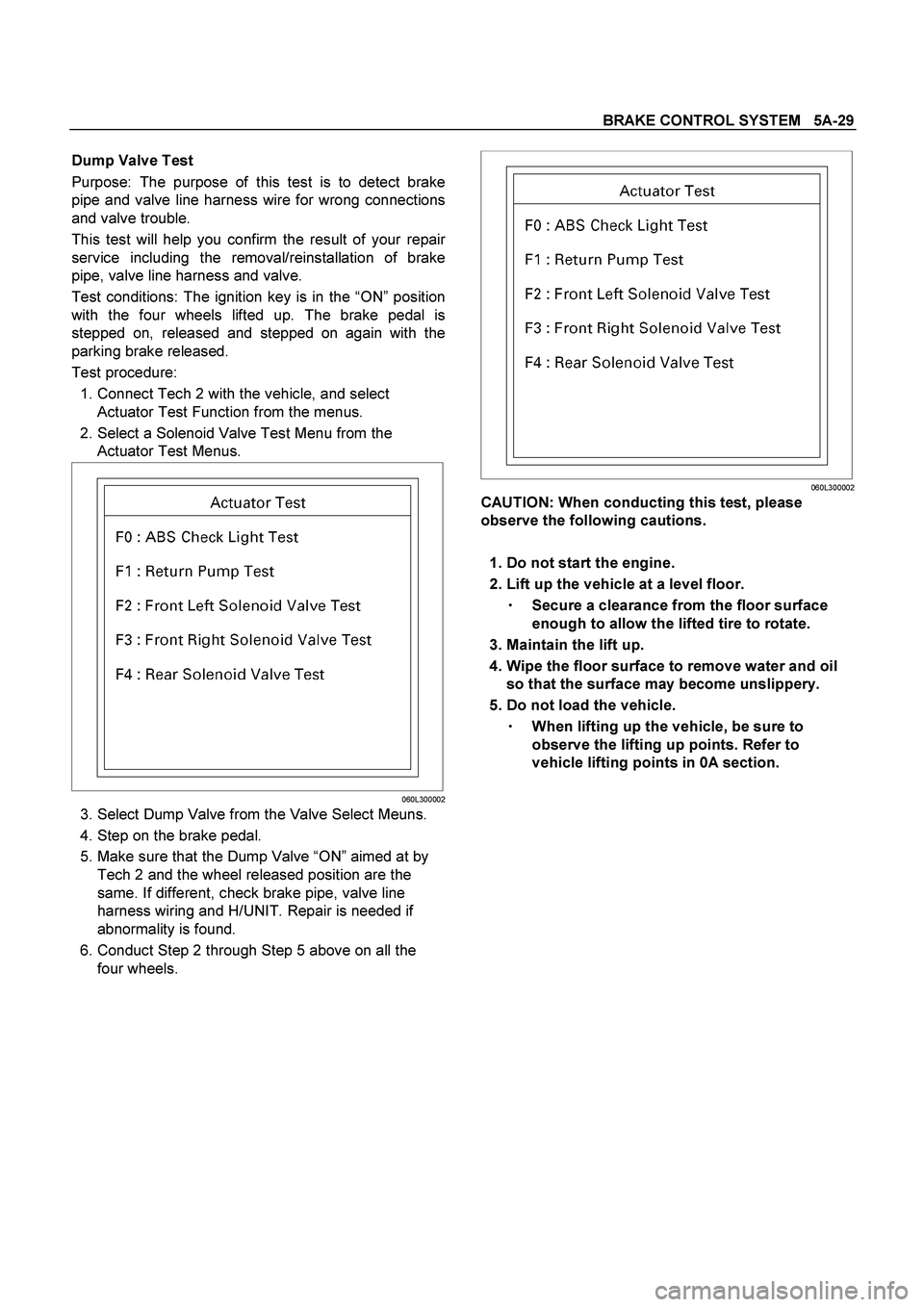
BRAKE CONTROL SYSTEM 5A-29
Dump Valve Test
Purpose: The purpose of this test is to detect brake
pipe and valve line harness wire for wrong connections
and valve trouble.
This test will help you confirm the result of your repai
r
service including the removal/reinstallation of brake
pipe, valve line harness and valve.
Test conditions: The ignition key is in the “ON” position
with the four wheels lifted up. The brake pedal is
stepped on, released and stepped on again with the
parking brake released.
Test procedure:
1. Connect Tech 2 with the vehicle, and select
Actuator Test Function from the menus.
2. Select a Solenoid Valve Test Menu from the
Actuator Test Menus.
060L300002
3. Select Dump Valve from the Valve Select Meuns.
4. Step on the brake pedal.
5. Make sure that the Dump Valve “ON” aimed at by
Tech 2 and the wheel released position are the
same. If different, check brake pipe, valve line
harness wiring and H/UNIT. Repair is needed if
abnormality is found.
6. Conduct Step 2 through Step 5 above on all the
four wheels.
060L300002
CAUTION: When conducting this test, please
observe the following cautions.
1. Do not start the engine.
2. Lift up the vehicle at a level floor.
Secure a clearance from the floor surface
enough to allow the lifted tire to rotate.
3. Maintain the lift up.
4. Wipe the floor surface to remove water and oil
so that the surface may become unslippery.
5. Do not load the vehicle.
When lifting up the vehicle, be sure to
observe the lifting up points. Refer to
vehicle lifting points in 0A section.
Page 351 of 4264
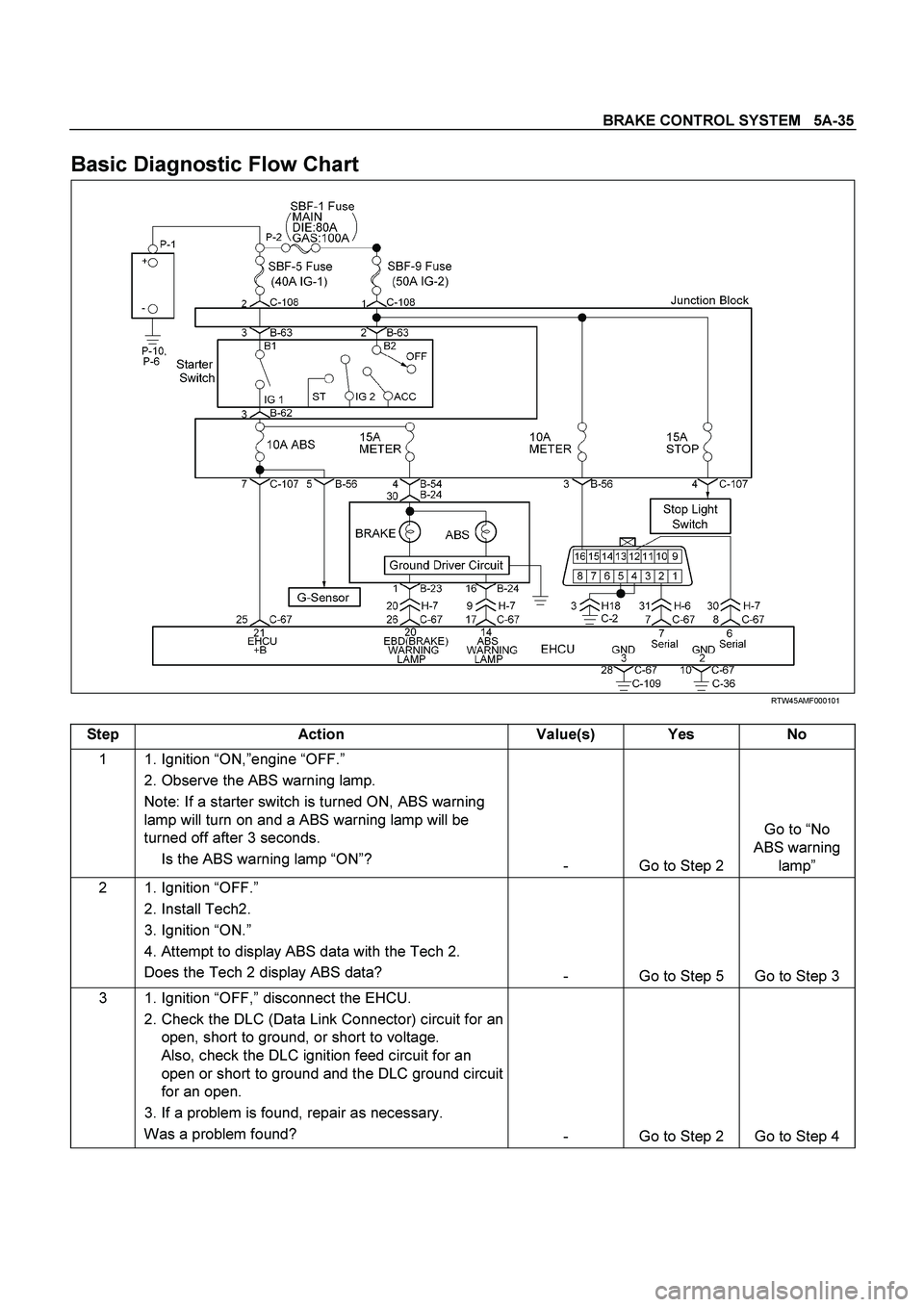
BRAKE CONTROL SYSTEM 5A-35
Basic Diagnostic Flow Chart
RTW45AMF000101
Step Action Value(s) Yes No
1 1. Ignition “ON,”engine “OFF.”
2. Observe the ABS warning lamp.
Note: If a starter switch is turned ON, ABS warning
lamp will turn on and a ABS warning lamp will be
turned off after 3 seconds.
Is the ABS warning lamp “ON”?
- Go to Step 2 Go to “No
ABS warning
lamp”
2 1. Ignition “OFF.”
2. Install Tech2.
3. Ignition “ON.”
4. Attempt to display ABS data with the Tech 2.
Does the Tech 2 display ABS data?
- Go to Step 5 Go to Step 3
3 1. Ignition “OFF,” disconnect the EHCU.
2. Check the DLC (Data Link Connector) circuit for an
open, short to ground, or short to voltage.
Also, check the DLC ignition feed circuit for an
open or short to ground and the DLC ground circuit
for an open.
3. If a problem is found, repair as necessary.
Was a problem found?
- Go to Step 2 Go to Step 4
Page 358 of 4264
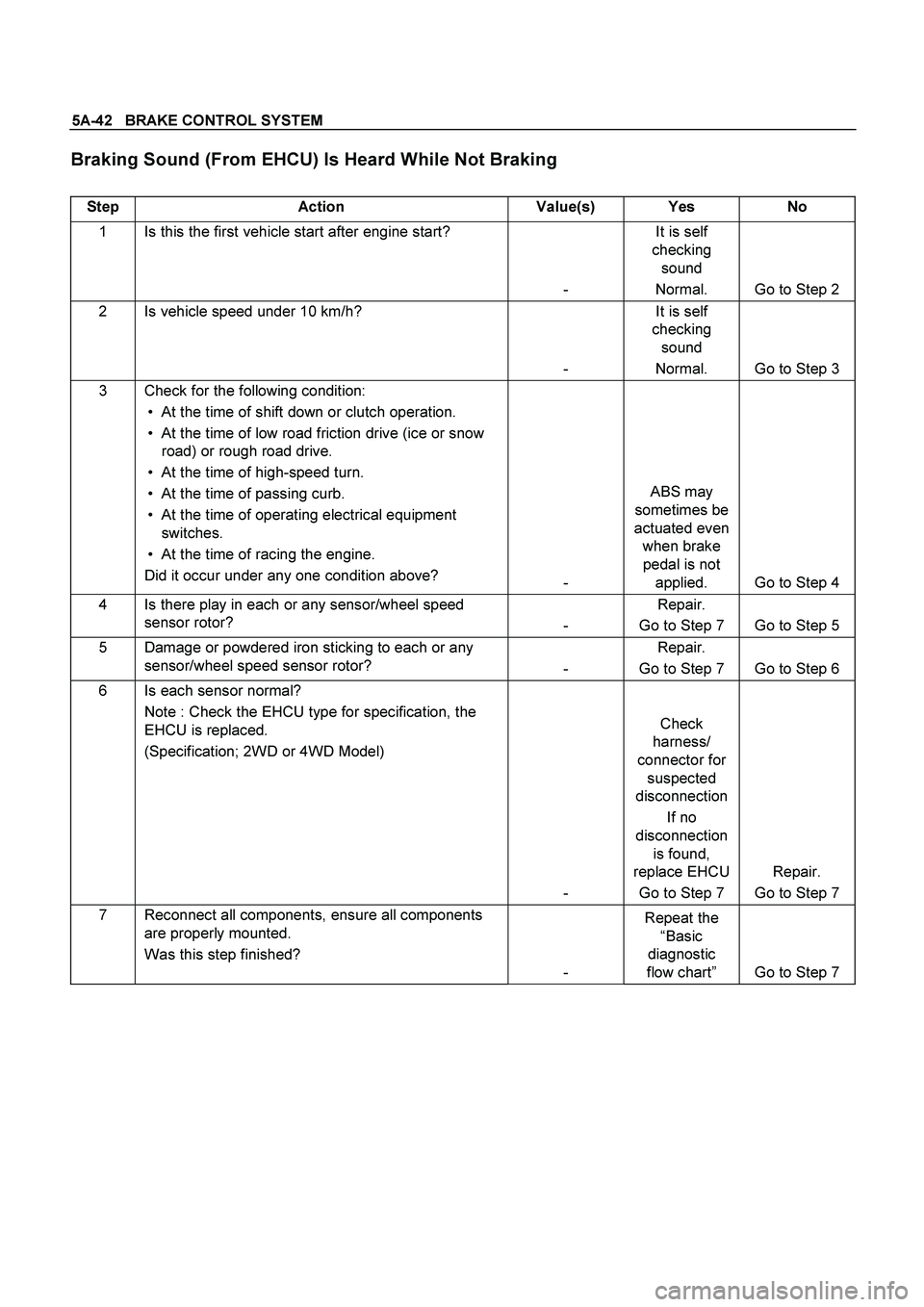
5A-42 BRAKE CONTROL SYSTEM
Braking Sound (From EHCU) Is Heard While Not Braking
Step Action Value(s) Yes No
1 Is this the first vehicle start after engine start?
- It is self
checking
sound
Normal. Go to Step 2
2 Is vehicle speed under 10 km/h?
- It is self
checking
sound
Normal. Go to Step 3
3 Check for the following condition:
At the time of shift down or clutch operation.
At the time of low road friction drive (ice or snow
road) or rough road drive.
At the time of high-speed turn.
At the time of passing curb.
At the time of operating electrical equipment
switches.
At the time of racing the engine.
Did it occur under any one condition above?
- ABS may
sometimes be
actuated even
when brake
pedal is not
applied. Go to Step 4
4 Is there play in each or any sensor/wheel speed
sensor rotor?
- Repair.
Go to Step 7 Go to Step 5
5 Damage or powdered iron sticking to each or any
sensor/wheel speed sensor rotor?
- Repair.
Go to Step 7 Go to Step 6
6 Is each sensor normal?
Note : Check the EHCU type for specification, the
EHCU is replaced.
(Specification; 2WD or 4WD Model)
- Check
harness/
connector for
suspected
disconnection
If no
disconnection
is found,
replace EHCU
Go to Step 7 Repair.
Go to Step 7
7 Reconnect all components, ensure all components
are properly mounted.
Was this step finished?
- Repeat the
“Basic
diagnostic
flow chart” Go to Step 7