check transmission fluid ISUZU TF SERIES 2004 Workshop Manual
[x] Cancel search | Manufacturer: ISUZU, Model Year: 2004, Model line: TF SERIES, Model: ISUZU TF SERIES 2004Pages: 4264, PDF Size: 72.63 MB
Page 1451 of 4264
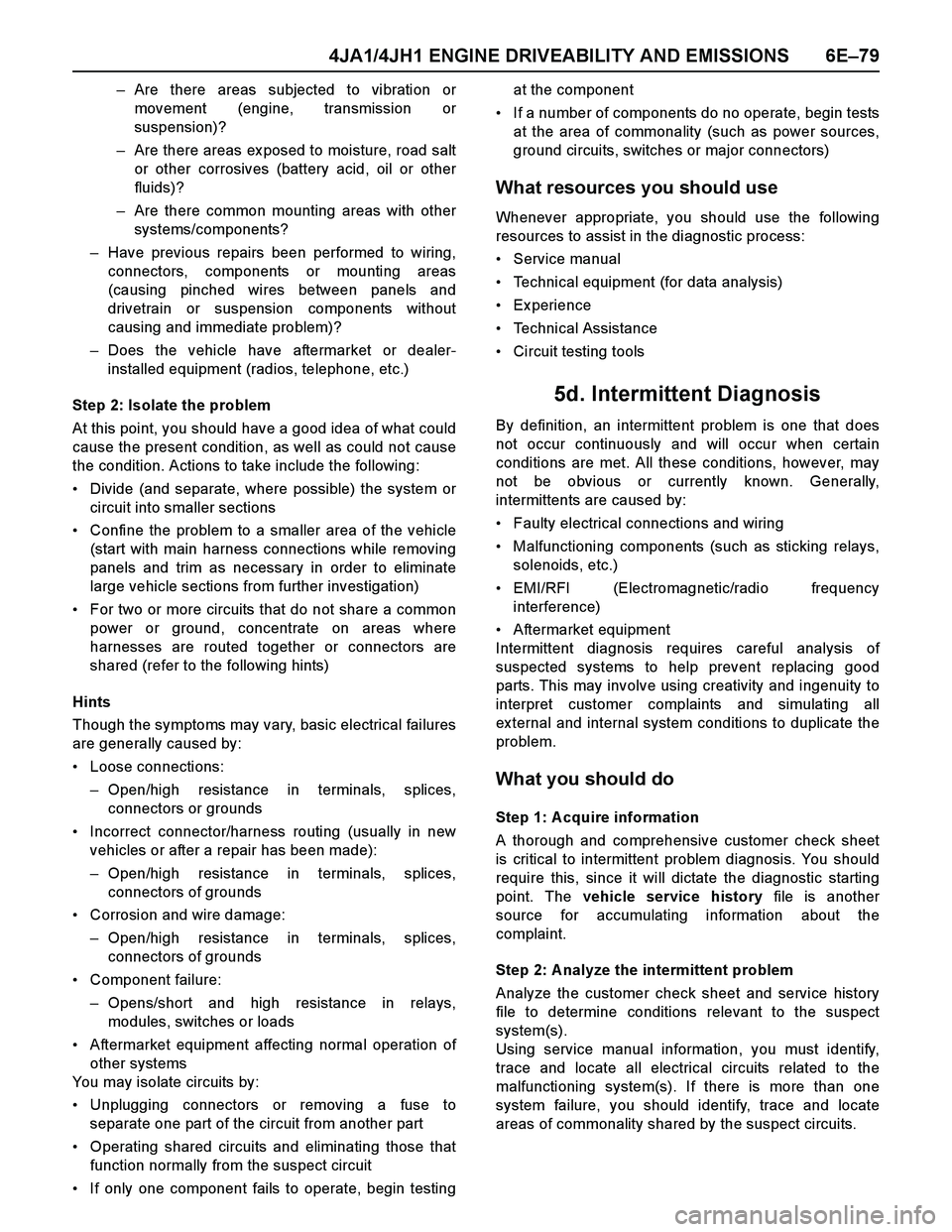
4JA1/4JH1 ENGINE DRIVEABILITY AND EMISSIONS 6E–79
–Are there areas subjected to vibration or
movement (engine, transmission or
suspension)?
–Are there areas ex posed to moisture, road salt
or other corrosives (battery acid, oil or other
fluids)?
–Are there common mounting areas with other
systems/components?
–Have previous repairs been performed to wiring,
connectors, components or mounting areas
(causing pinched wires between panels and
drivetrain or suspension components without
causing and immediate problem)?
–Does the vehicle have aftermarket or dealer-
installed equipment (radios, telephone, etc.)
Step 2: Isolate the problem
At this point, you should have a good idea of what could
cause the present condition, as well as could not cause
the condition. Actions to take include the following:
Divide (and separate, where possible) the system or
circuit into smaller sections
Confine the problem to a smaller area of the vehicle
(start with main harness connections while removing
panels and trim as necessary in order to eliminate
large vehicle sections from further investigation)
For two or more circuits that do not share a common
power or ground, concentrate on areas where
harnesses are routed together or connectors are
shared (refer to the following hints)
Hints
Though the symptoms may vary, basic electrical failures
are generally caused by:
Loose connections:
–Open/high resistance in terminals, splices,
connectors or grounds
Incorrect connector/harness routing (usually in new
vehicles or after a repair has been made):
–Open/high resistance in terminals, splices,
connectors of grounds
Corrosion and wire damage:
–Open/high resistance in terminals, splices,
connectors of grounds
Component failure:
–Opens/short and high resistance in relays,
modules, switches or loads
Aftermarket equipment affecting normal operation of
other systems
You may isolate circuits by:
Unplugging connectors or removing a fuse to
separate one part of the circuit from another part
Operating shared circuits and eliminating those that
function normally from the suspect circuit
If only one component fails to operate, begin testingat the component
If a number of components do no operate, begin tests
at the area of commonality (such as power sources,
ground circuits, switches or major connectors)
What resources you should use
Whenever appropriate, you should use the following
resources to assist in the diagnostic process:
Service manual
Technical equipment (for data analysis)
Ex perience
Technical Assistance
Circuit testing tools
5d. Intermittent Diagnosis
By definition, an intermittent problem is one that does
not occur continuously and will occur when certain
conditions are met. All these conditions, however, may
not be obvious or currently known. Generally,
intermittents are caused by:
Faulty electrical connections and wiring
Malfunctioning components (such as sticking relays,
solenoids, etc.)
EMI/RFI (Electromagnetic/radio frequency
interference)
Aftermarket equipment
Intermittent diagnosis requires careful analysis of
suspected systems to help prevent replacing good
parts. This may involve using creativity and ingenuity to
interpret customer complaints and simulating all
ex ternal and internal system conditions to duplicate the
problem.
What you should do
Step 1: A cquire information
A thorough and comprehensive customer check sheet
is critical to intermittent problem diagnosis. You should
require this, since it will dictate the diagnostic starting
point. The vehicle service history file is another
source for accumulating information about the
complaint.
Step 2: A nalyze the intermittent problem
Analyze the customer check sheet and service history
file to determine conditions relevant to the suspect
system(s).
Using service manual information, you must identify,
trace and locate all electrical circuits related to the
malfunctioning system(s). If there is more than one
system failure, you should identify, trace and locate
areas of commonality shared by the suspect circuits.
Page 2516 of 4264
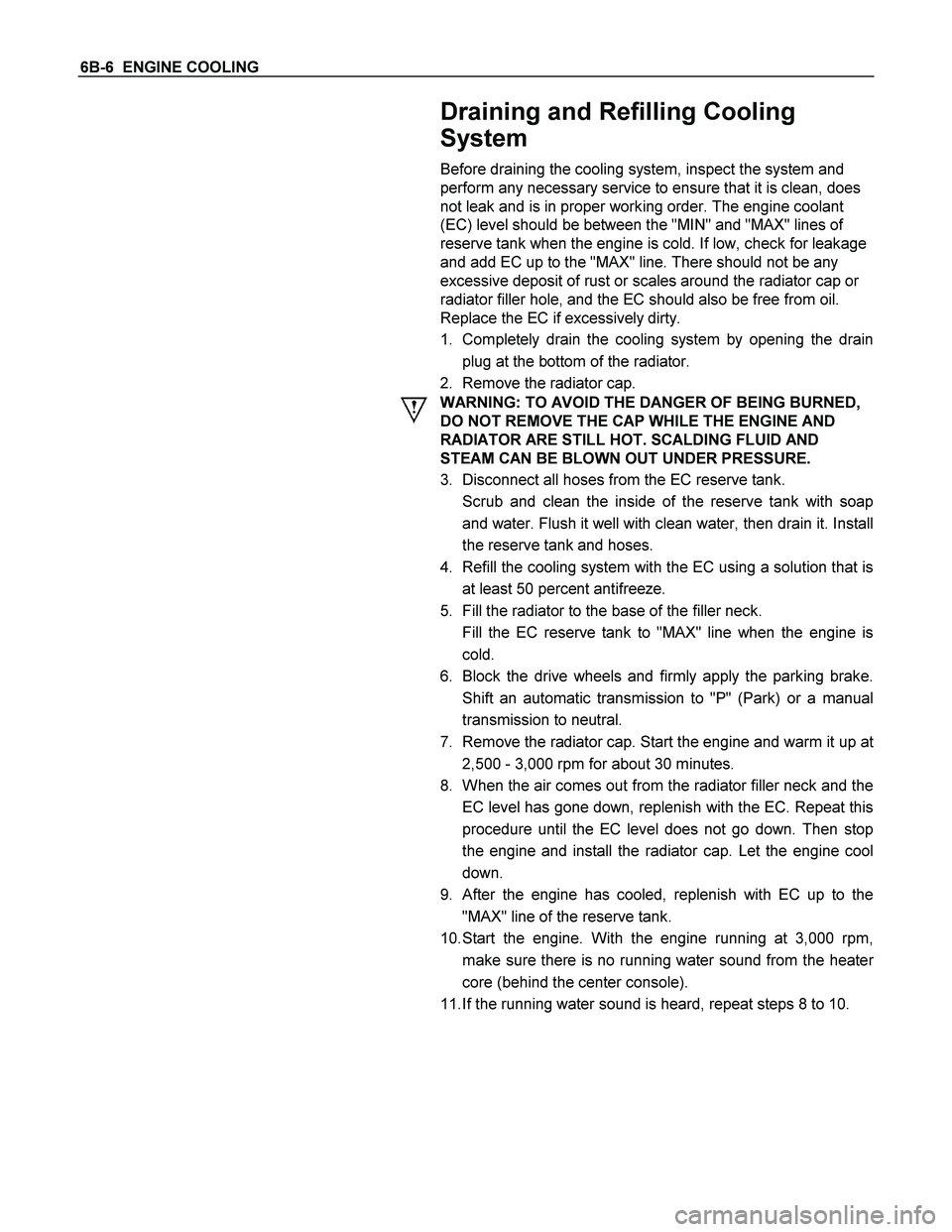
6B-6 ENGINE COOLING
Draining and Refilling Cooling
System
Before draining the cooling system, inspect the system and
perform any necessary service to ensure that it is clean, does
not leak and is in proper working order. The engine coolant
(EC) level should be between the "MIN" and "MAX" lines of
reserve tank when the engine is cold. If low, check for leakage
and add EC up to the "MAX" line. There should not be any
excessive deposit of rust or scales around the radiator cap or
radiator filler hole, and the EC should also be free from oil.
Replace the EC if excessively dirty.
1. Completely drain the cooling system by opening the drain
plug at the bottom of the radiator.
2. Remove the radiator cap.
WARNING: TO AVOID THE DANGER OF BEING BURNED,
DO NOT REMOVE THE CAP WHILE THE ENGINE AND
RADIATOR ARE STILL HOT. SCALDING FLUID AND
STEAM CAN BE BLOWN OUT UNDER PRESSURE.
3. Disconnect all hoses from the EC reserve tank.
Scrub and clean the inside of the reserve tank with soap
and water. Flush it well with clean water, then drain it. Install
the reserve tank and hoses.
4. Refill the cooling system with the EC using a solution that is
at least 50 percent antifreeze.
5. Fill the radiator to the base of the filler neck.
Fill the EC reserve tank to "MAX" line when the engine is
cold.
6. Block the drive wheels and firmly apply the parking brake.
Shift an automatic transmission to "P" (Park) or a manual
transmission to neutral.
7. Remove the radiator cap. Start the engine and warm it up a
t
2,500 - 3,000 rpm for about 30 minutes.
8. When the air comes out from the radiator filler neck and the
EC level has gone down, replenish with the EC. Repeat this
procedure until the EC level does not go down. Then stop
the engine and install the radiator cap. Let the engine cool
down.
9. After the engine has cooled, replenish with EC up to the
"MAX" line of the reserve tank.
10. Start the engine. With the engine running at 3,000 rpm,
make sure there is no running water sound from the heate
r
core (behind the center console).
11. If the running water sound is heard, repeat steps 8 to 10.
Page 2640 of 4264

6E–64 ENGINE DRIVEABILITY AND EMISSIONS
–Are there areas subjected to vibration or
movement (engine, transmission or
suspension)?
–Are there areas ex posed to moisture, road salt
or other corrosives (battery acid, oil or other
fluids)?
–Are there common mounting areas with other
systems/components?
–Have previous repairs been performed to wiring,
connectors, components or mounting areas
(causing pinched wires between panels and
drivetrain or suspension components without
causing and immediate problem)?
–Does the vehicle have aftermarket or dealer-
installed equipment (radios, telephone, etc.)
Step 2: Isolate the problem
At this point, you should have a good idea of what could
cause the present condition, as well as could not cause
the condition. Actions to take include the following:
Divide (and separate, where possible) the system or
circuit into smaller sections
Confine the problem to a smaller area of the vehicle
(start with main harness connections while removing
panels and trim as necessary in order to eliminate
large vehicle sections from further investigation)
For two or more circuits that do not share a common
power or ground, concentrate on areas where
harnesses are routed together or connectors are
shared (refer to the following hints)
Hints
Though the symptoms may vary, basic electrical failures
are generally caused by:
Loose connections:
–Open/high resistance in terminals, splices,
connectors or grounds
Incorrect connector/harness routing (usually in new
vehicles or after a repair has been made):
–Open/high resistance in terminals, splices,
connectors of grounds
Corrosion and wire damage:
–Open/high resistance in terminals, splices,
connectors of grounds
Component failure:
–Opens/short and high resistance in relays,
modules, switches or loads
Aftermarket equipment affecting normal operation of
other systems
You may isolate circuits by:
Unplugging connectors or removing a fuse to
separate one part of the circuit from another part
Operating shared circuits and eliminating those that
function normally from the suspect circuit
If only one component fails to operate, begin testingat the component
If a number of components do no operate, begin tests
at the area of commonality (such as power sources,
ground circuits, switches or major connectors)
What resources you should use
Whenever appropriate, you should use the following
resources to assist in the diagnostic process:
Service manual
Technical equipment (for data analysis)
Ex perience
Technical Assistance
Circuit testing tools
5d. Intermittent Diagnosis
By definition, an intermittent problem is one that does
not occur continuously and will occur when certain
conditions are met. All these conditions, however, may
not be obvious or currently known. Generally,
intermittents are caused by:
Faulty electrical connections and wiring
Malfunctioning components (such as sticking relays,
solenoids, etc.)
EMI/RFI (Electromagnetic/radio frequency
interference)
Aftermarket equipment
Intermittent diagnosis requires careful analysis of
suspected systems to help prevent replacing good
parts. This may involve using creativity and ingenuity to
interpret customer complaints and simulating all
ex ternal and internal system conditions to duplicate the
problem.
What you should do
Step 1: A cquire information
A thorough and comprehensive customer check sheet
is critical to intermittent problem diagnosis. You should
require this, since it will dictate the diagnostic starting
point. The vehicle service history file is another
source for accumulating information about the
complaint.
Step 2: A nalyze the intermittent problem
Analyze the customer check sheet and service history
file to determine conditions relevant to the suspect
system(s).
Using service manual information, you must identify,
trace and locate all electrical circuits related to the
malfunctioning system(s). If there is more than one
system failure, you should identify, trace and locate
areas of commonality shared by the suspect circuits.
Page 3170 of 4264

7B1-6 MANUAL TRANSMISSION
Torque : 63 N·m (6.4 kg·m/46 lb·ft)
4. Install center bearing on crossmember.
Torque : 69 N·m (7.0 kg·m/51 lb·ft)
5. Check transmission fluid level.
6. Lower vehicle.
Page 3595 of 4264
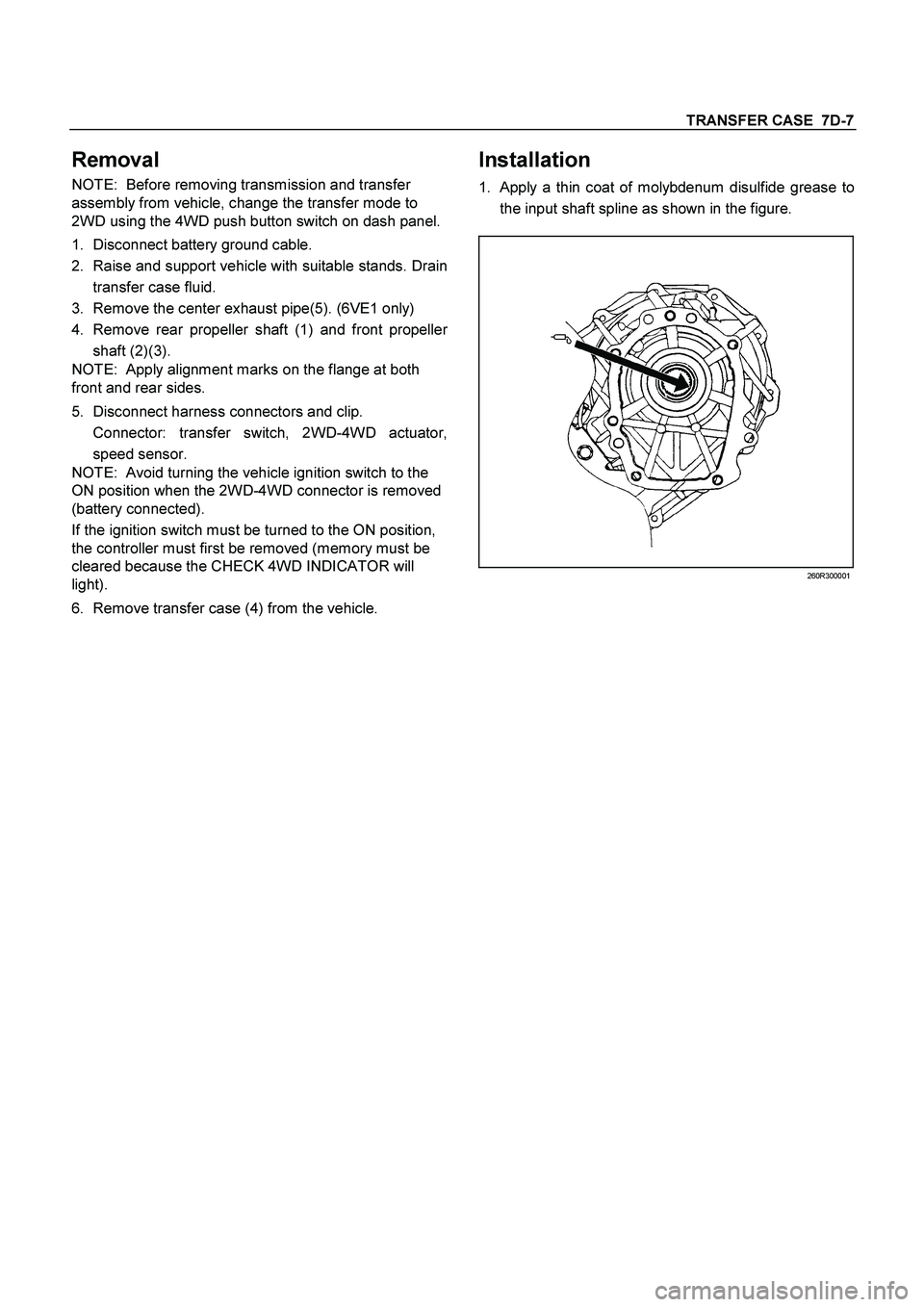
TRANSFER CASE 7D-7
Removal
NOTE: Before removing transmission and transfer
assembly from vehicle, change the transfer mode to
2WD using the 4WD push button switch on dash panel.
1.
Disconnect battery ground cable.
2.
Raise and support vehicle with suitable stands. Drain
transfer case fluid.
3. Remove the center exhaust pipe(5). (6VE1 only)
4.
Remove rear propeller shaft (1) and front propelle
r
shaft (2)(3).
NOTE: Apply alignment marks on the flange at both
front and rear sides.
5.
Disconnect harness connectors and clip.
Connector: transfer switch, 2WD-4WD actuator,
speed sensor.
NOTE: Avoid turning the vehicle ignition switch to the
ON position when the 2WD-4WD connector is removed
(battery connected).
If the ignition switch must be turned to the ON position,
the controller must first be removed (memory must be
cleared because the CHECK 4WD INDICATOR will
light).
6.
Remove transfer case (4) from the vehicle.
Installation
1.
Apply a thin coat of molybdenum disulfide grease to
the input shaft spline as shown in the figure.
260R300001
Page 3724 of 4264
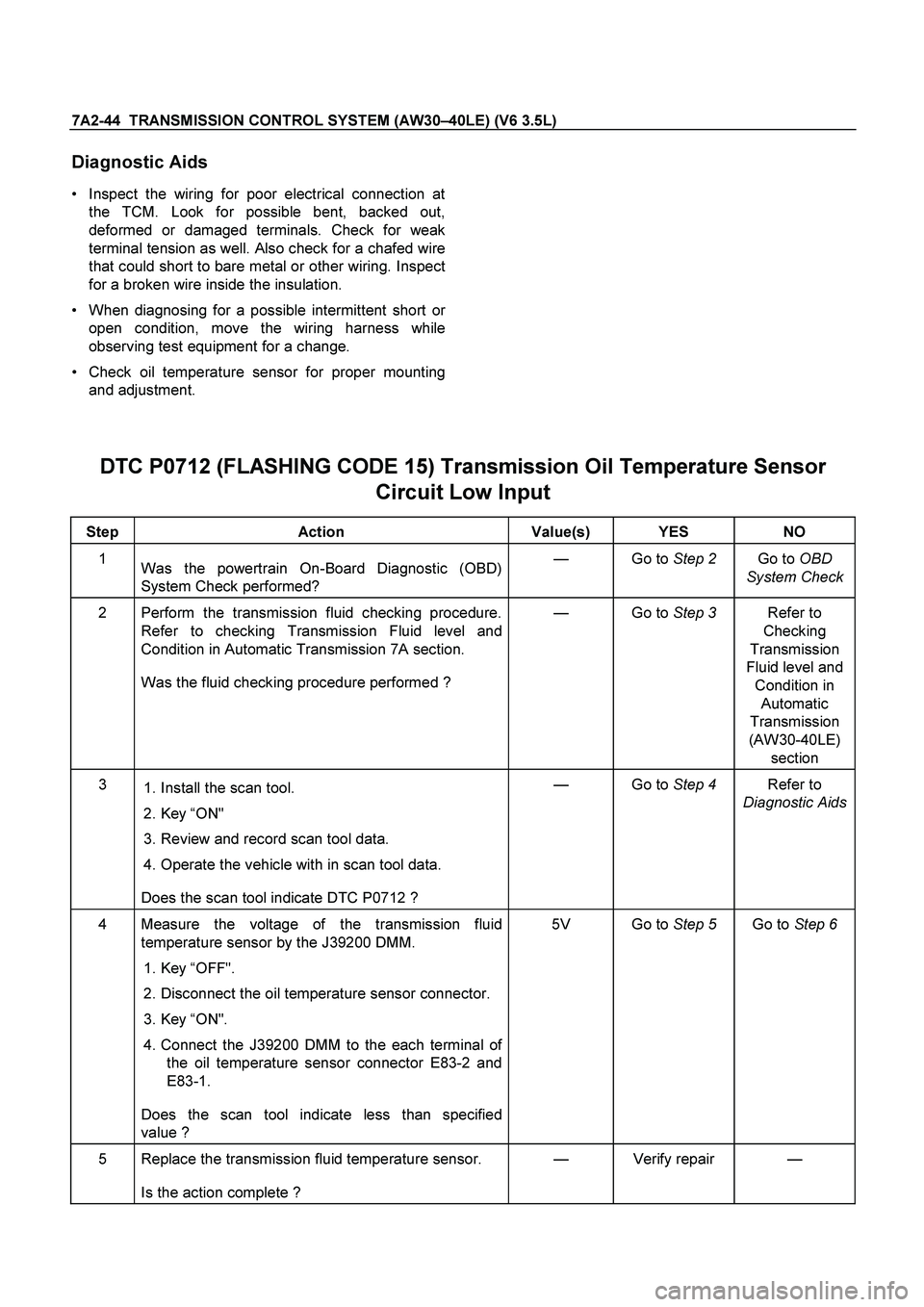
7A2-44 TRANSMISSION CONTROL SYSTEM (AW30–40LE) (V6 3.5L)
Diagnostic Aids
Inspect the wiring for poor electrical connection at
the TCM. Look for possible bent, backed out,
deformed or damaged terminals. Check for weak
terminal tension as well. Also check for a chafed wire
that could short to bare metal or other wiring. Inspect
for a broken wire inside the insulation.
When diagnosing for a possible intermittent short o
r
open condition, move the wiring harness while
observing test equipment for a change.
Check oil temperature sensor for proper mounting
and adjustment.
DTC P0712 (FLASHING CODE 15) Transmission Oil Temperature Sensor
Circuit Low Input
Step Action Value(s) YES NO
1
Was the powertrain On-Board Diagnostic (OBD)
System Check performed? — Go to Step 2 Go to OBD
System Check
2 Perform the transmission fluid checking procedure.
Refer to checking Transmission Fluid level and
Condition in Automatic Transmission 7A section.
Was the fluid checking procedure performed ? — Go to Step 3 Refer to
Checking
Transmission
Fluid level and
Condition in
Automatic
Transmission
(AW30-40LE)
section
3
1. Install the scan tool.
2. Key “ON"
3. Review and record scan tool data.
4. Operate the vehicle with in scan tool data.
Does the scan tool indicate DTC P0712 ? — Go to Step 4 Refer to
Diagnostic Aids
4 Measure the voltage of the transmission fluid
temperature sensor by the J39200 DMM.
1. Key “OFF".
2. Disconnect the oil temperature sensor connector.
3. Key “ON".
4. Connect the J39200 DMM to the each terminal of
the oil temperature sensor connector E83-2 and
E83-1.
Does the scan tool indicate less than specified
value ? 5V Go to Step 5 Go to Step 6
5 Replace the transmission fluid temperature sensor.
Is the action complete ? — Verify repair —
Page 3727 of 4264
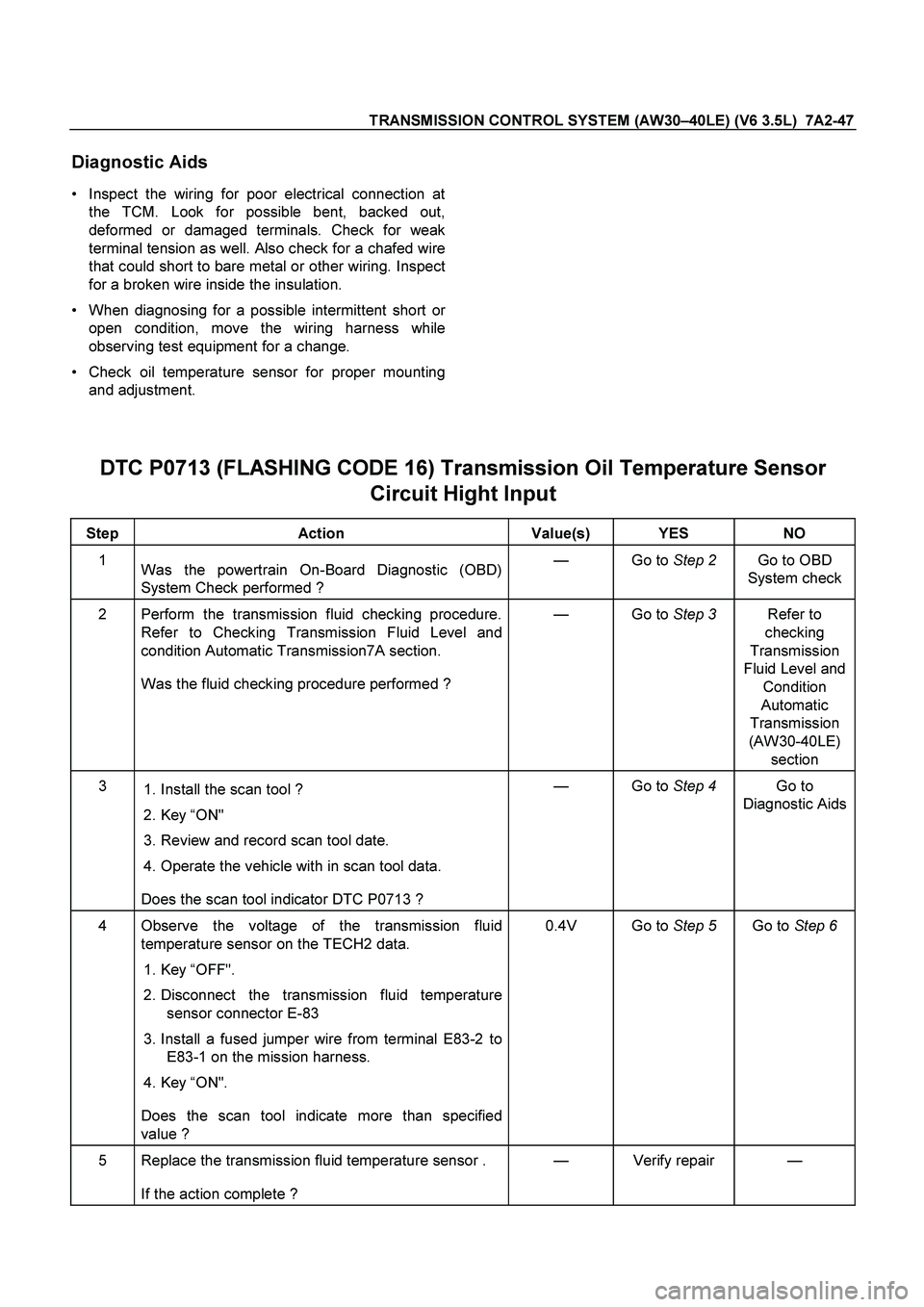
TRANSMISSION CONTROL SYSTEM (AW30–40LE) (V6 3.5L) 7A2-47
Diagnostic Aids
Inspect the wiring for poor electrical connection at
the TCM. Look for possible bent, backed out,
deformed or damaged terminals. Check for weak
terminal tension as well. Also check for a chafed wire
that could short to bare metal or other wiring. Inspect
for a broken wire inside the insulation.
When diagnosing for a possible intermittent short o
r
open condition, move the wiring harness while
observing test equipment for a change.
Check oil temperature sensor for proper mounting
and adjustment.
DTC P0713 (FLASHING CODE 16) Transmission Oil Temperature Sensor
Circuit Hight Input
Step Action Value(s) YES NO
1
Was the powertrain On-Board Diagnostic (OBD)
System Check performed ? — Go to Step 2 Go to OBD
System check
2 Perform the transmission fluid checking procedure.
Refer to Checking Transmission Fluid Level and
condition Automatic Transmission7A section.
Was the fluid checking procedure performed ? — Go to Step 3 Refer to
checking
Transmission
Fluid Level and
Condition
Automatic
Transmission
(AW30-40LE)
section
3
1. Install the scan tool ?
2. Key “ON"
3. Review and record scan tool date.
4. Operate the vehicle with in scan tool data.
Does the scan tool indicator DTC P0713 ? — Go to Step 4 Go to
Diagnostic Aids
4 Observe the voltage of the transmission fluid
temperature sensor on the TECH2 data.
1. Key “OFF".
2. Disconnect the transmission fluid temperature
sensor connector E-83
3. Install a fused jumper wire from terminal E83-2 to
E83-1 on the mission harness.
4. Key “ON".
Does the scan tool indicate more than specified
value ? 0.4V Go to Step 5 Go to Step 6
5 Replace the transmission fluid temperature sensor .
If the action complete ? — Verify repair —
Page 3739 of 4264
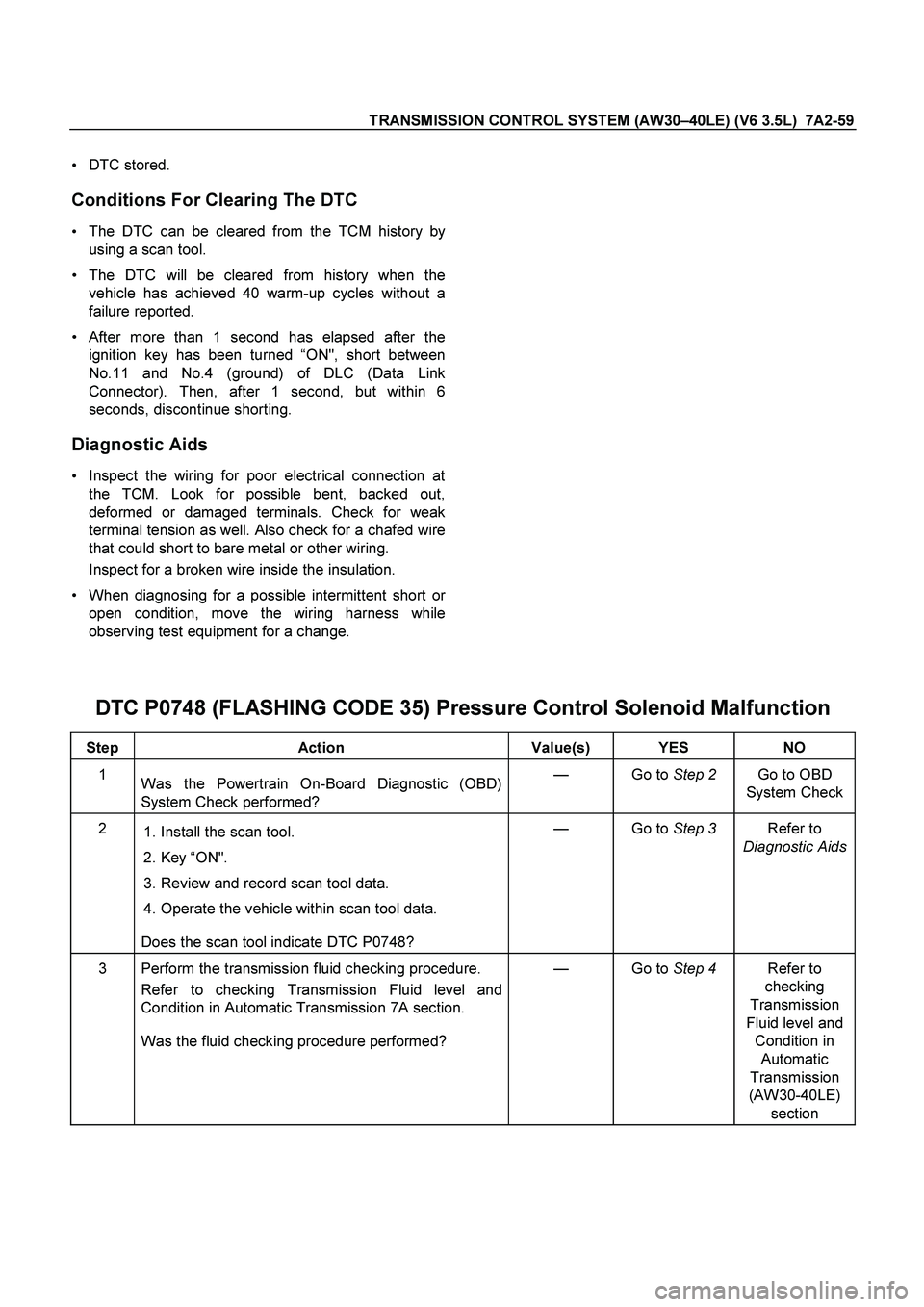
TRANSMISSION CONTROL SYSTEM (AW30–40LE) (V6 3.5L) 7A2-59
DTC stored.
Conditions For Clearing The DTC
The DTC can be cleared from the TCM history by
using a scan tool.
The DTC will be cleared from history when the
vehicle has achieved 40 warm-up cycles without a
failure reported.
After more than 1 second has elapsed after the
ignition key has been turned “ON", short between
No.11 and No.4 (ground) of DLC (Data Link
Connector). Then, after 1 second, but within 6
seconds, discontinue shorting.
Diagnostic Aids
Inspect the wiring for poor electrical connection at
the TCM. Look for possible bent, backed out,
deformed or damaged terminals. Check for weak
terminal tension as well. Also check for a chafed wire
that could short to bare metal or other wiring.
Inspect for a broken wire inside the insulation.
When diagnosing for a possible intermittent short o
r
open condition, move the wiring harness while
observing test equipment for a change.
DTC P0748 (FLASHING CODE 35) Pressure Control Solenoid Malfunction
Step Action Value(s) YES NO
1
Was the Powertrain On-Board Diagnostic (OBD)
System Check performed? — Go to Step 2 Go to OBD
System Check
2
1. Install the scan tool.
2. Key “ON".
3. Review and record scan tool data.
4. Operate the vehicle within scan tool data.
Does the scan tool indicate DTC P0748? — Go to Step 3 Refer to
Diagnostic Aids
3 Perform the transmission fluid checking procedure.
Refer to checking Transmission Fluid level and
Condition in Automatic Transmission 7A section.
Was the fluid checking procedure performed? — Go to Step 4 Refer to
checking
Transmission
Fluid level and
Condition in
Automatic
Transmission
(AW30-40LE)
section
Page 3768 of 4264
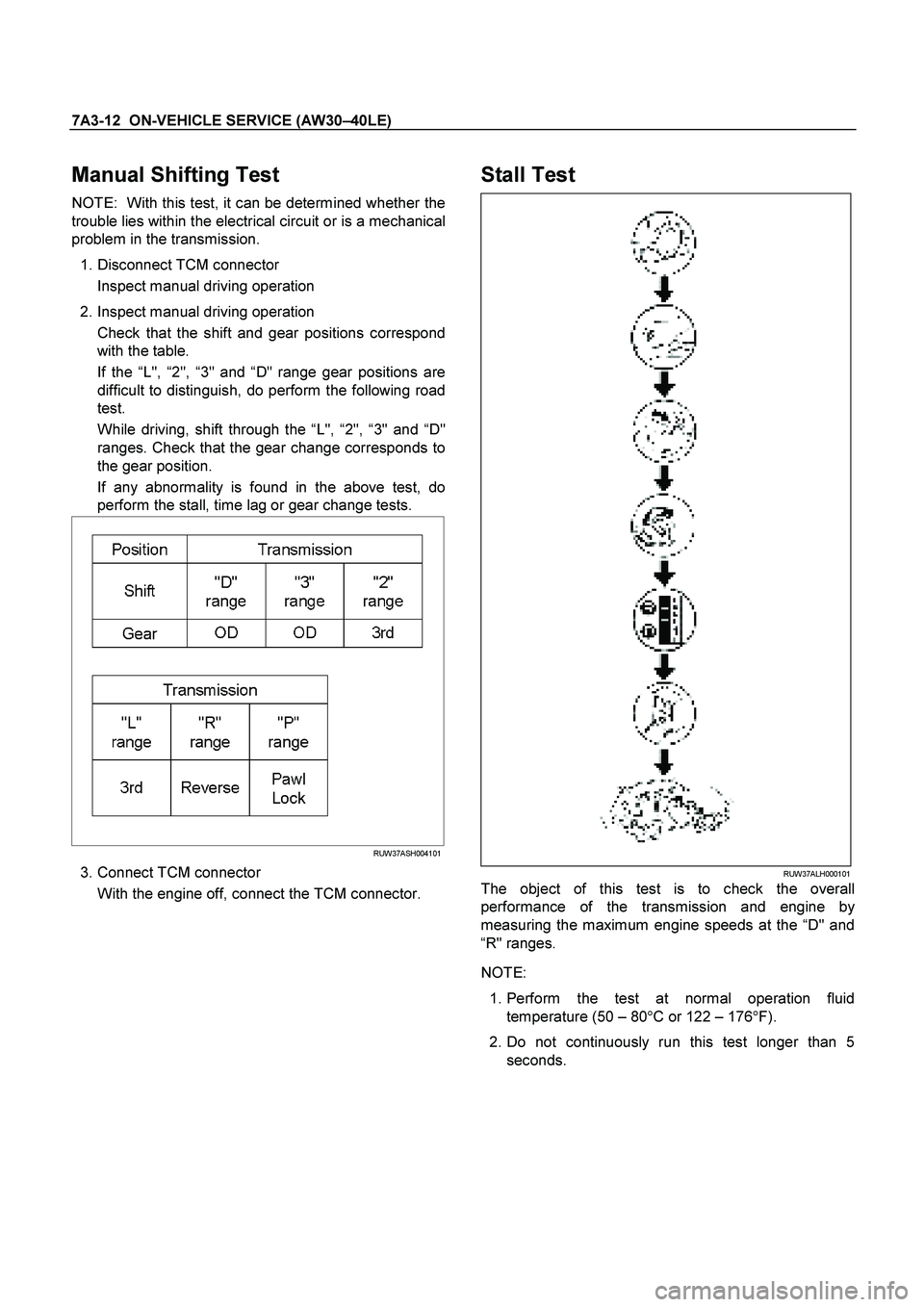
7A3-12 ON-VEHICLE SERVICE (AW30 –40LE)
Manual Shifting Test
NOTE: With this test, it can be determined whether the
trouble lies within the electrical circuit or is a mechanical
problem in the transmission.
1. Disconnect TCM connector
Inspect manual driving operation
2. Inspect manual driving operation
Check that the shift and gear positions correspond
with the table.
If the “L", “2", “3" and “D" range gear positions are
difficult to distinguish, do perform the following road
test.
While driving, shift through the “L", “2", “3" and “D"
ranges. Check that the gear change corresponds to
the gear position.
If any abnormality is found in the above test, do
perform the stall, time lag or gear change tests.
RUW37ASH004101
3. Connect TCM connector
With the engine off, connect the TCM connector.
Stall Test
RUW37ALH000101
The object of this test is to check the overall
performance of the transmission and engine b
y
measuring the maximum engine speeds at the “D" and
“ R" ranges.
NOTE:
1. Perform the test at normal operation fluid
temperature (50 – 80
C or 122 – 176
F).
2. Do not continuously run this test longer than 5 seconds.
Page 3770 of 4264
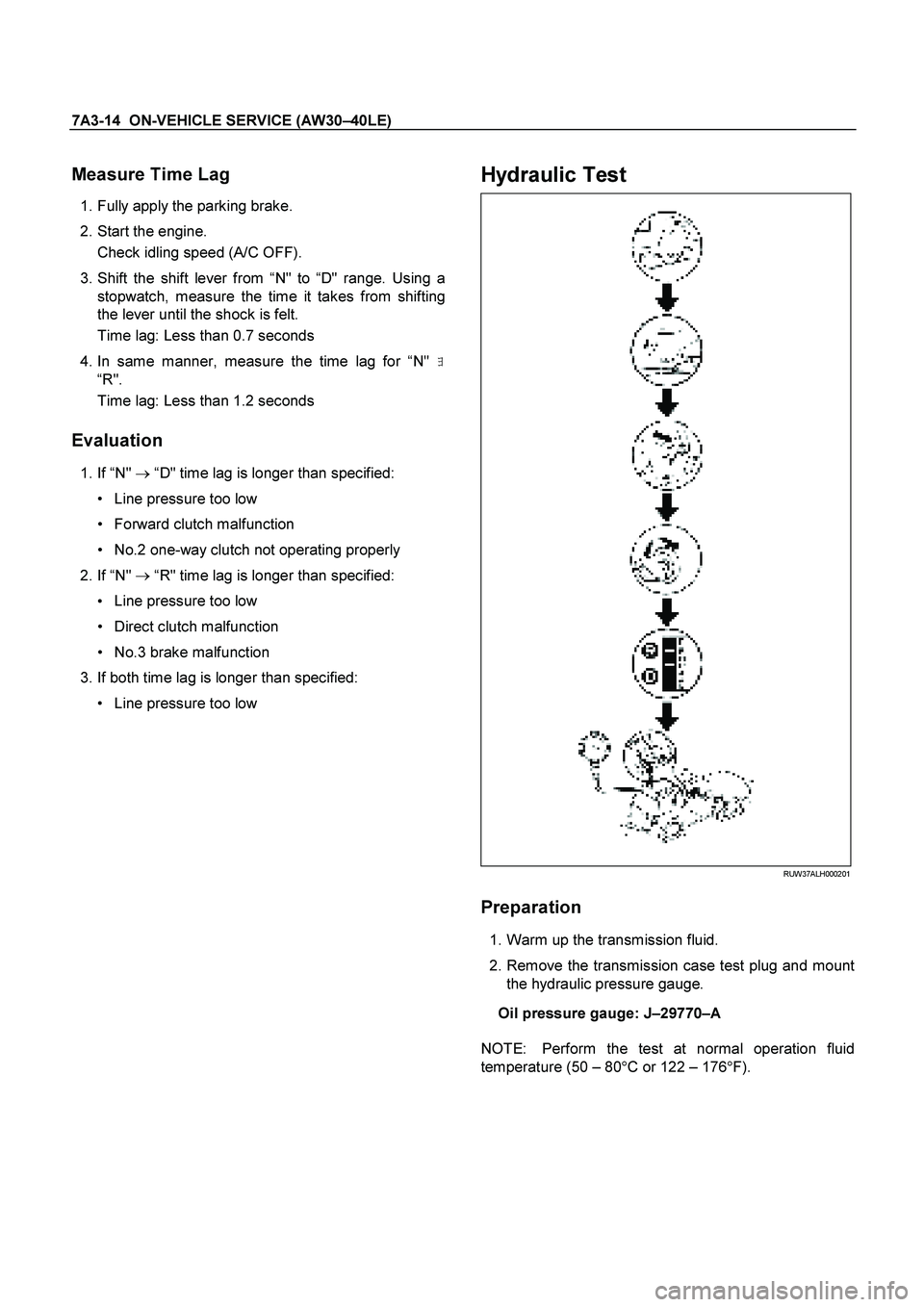
7A3-14 ON-VEHICLE SERVICE (AW30 –40LE)
Measure Time Lag
1. Fully apply the parking brake.
2. Start the engine. Check idling speed (A/C OFF).
3. Shift the shift lever from “N" to “D" range. Using a
stopwatch, measure the time it takes from shifting
the lever until the shock is felt.
Time lag: Less than 0.7 seconds
4. In same manner, measure the time lag for “N"
“R".
Time lag: Less than 1.2 seconds
Evaluation
1. If “N"
“ D" time lag is longer than specified:
Line pressure too low
Forward clutch malfunction
No.2 one-way clutch not operating properly
2. If “N"
“ R" time lag is longer than specified:
Line pressure too low
Direct clutch malfunction
No.3 brake malfunction
3. If both time lag is longer than specified:
Line pressure too low
Hydraulic Test
RUW37ALH000201
Preparation
1. Warm up the transmission fluid.
2. Remove the transmission case test plug and mount the hydraulic pressure gauge.
Oil pressure gauge: J –29770 –A
NOTE: Perform the test at normal operation fluid
temperature (50 – 80
C or 122 – 176
F).