Transmission control module JEEP GRAND CHEROKEE 2002 WJ / 2.G Workshop Manual
[x] Cancel search | Manufacturer: JEEP, Model Year: 2002, Model line: GRAND CHEROKEE, Model: JEEP GRAND CHEROKEE 2002 WJ / 2.GPages: 2199, PDF Size: 76.01 MB
Page 251 of 2199
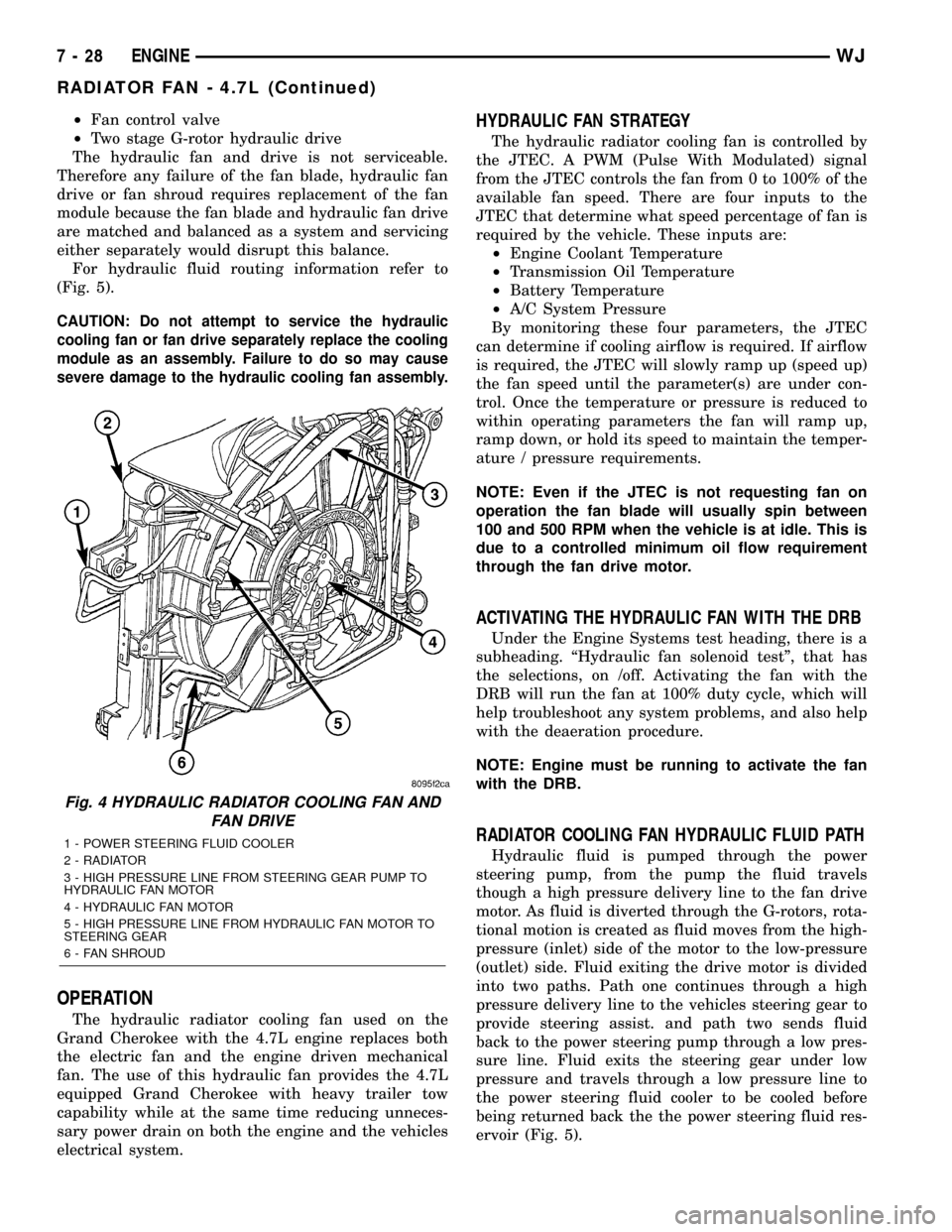
²Fan control valve
²Two stage G-rotor hydraulic drive
The hydraulic fan and drive is not serviceable.
Therefore any failure of the fan blade, hydraulic fan
drive or fan shroud requires replacement of the fan
module because the fan blade and hydraulic fan drive
are matched and balanced as a system and servicing
either separately would disrupt this balance.
For hydraulic fluid routing information refer to
(Fig. 5).
CAUTION: Do not attempt to service the hydraulic
cooling fan or fan drive separately replace the cooling
module as an assembly. Failure to do so may cause
severe damage to the hydraulic cooling fan assembly.
OPERATION
The hydraulic radiator cooling fan used on the
Grand Cherokee with the 4.7L engine replaces both
the electric fan and the engine driven mechanical
fan. The use of this hydraulic fan provides the 4.7L
equipped Grand Cherokee with heavy trailer tow
capability while at the same time reducing unneces-
sary power drain on both the engine and the vehicles
electrical system.
HYDRAULIC FAN STRATEGY
The hydraulic radiator cooling fan is controlled by
the JTEC. A PWM (Pulse With Modulated) signal
from the JTEC controls the fan from 0 to 100% of the
available fan speed. There are four inputs to the
JTEC that determine what speed percentage of fan is
required by the vehicle. These inputs are:
²Engine Coolant Temperature
²Transmission Oil Temperature
²Battery Temperature
²A/C System Pressure
By monitoring these four parameters, the JTEC
can determine if cooling airflow is required. If airflow
is required, the JTEC will slowly ramp up (speed up)
the fan speed until the parameter(s) are under con-
trol. Once the temperature or pressure is reduced to
within operating parameters the fan will ramp up,
ramp down, or hold its speed to maintain the temper-
ature / pressure requirements.
NOTE: Even if the JTEC is not requesting fan on
operation the fan blade will usually spin between
100 and 500 RPM when the vehicle is at idle. This is
due to a controlled minimum oil flow requirement
through the fan drive motor.
ACTIVATING THE HYDRAULIC FAN WITH THE DRB
Under the Engine Systems test heading, there is a
subheading. ªHydraulic fan solenoid testº, that has
the selections, on /off. Activating the fan with the
DRB will run the fan at 100% duty cycle, which will
help troubleshoot any system problems, and also help
with the deaeration procedure.
NOTE: Engine must be running to activate the fan
with the DRB.
RADIATOR COOLING FAN HYDRAULIC FLUID PATH
Hydraulic fluid is pumped through the power
steering pump, from the pump the fluid travels
though a high pressure delivery line to the fan drive
motor. As fluid is diverted through the G-rotors, rota-
tional motion is created as fluid moves from the high-
pressure (inlet) side of the motor to the low-pressure
(outlet) side. Fluid exiting the drive motor is divided
into two paths. Path one continues through a high
pressure delivery line to the vehicles steering gear to
provide steering assist. and path two sends fluid
back to the power steering pump through a low pres-
sure line. Fluid exits the steering gear under low
pressure and travels through a low pressure line to
the power steering fluid cooler to be cooled before
being returned back the the power steering fluid res-
ervoir (Fig. 5).
Fig. 4 HYDRAULIC RADIATOR COOLING FAN AND
FAN DRIVE
1 - POWER STEERING FLUID COOLER
2 - RADIATOR
3 - HIGH PRESSURE LINE FROM STEERING GEAR PUMP TO
HYDRAULIC FAN MOTOR
4 - HYDRAULIC FAN MOTOR
5 - HIGH PRESSURE LINE FROM HYDRAULIC FAN MOTOR TO
STEERING GEAR
6 - FAN SHROUD
7 - 28 ENGINEWJ
RADIATOR FAN - 4.7L (Continued)
Page 264 of 2199
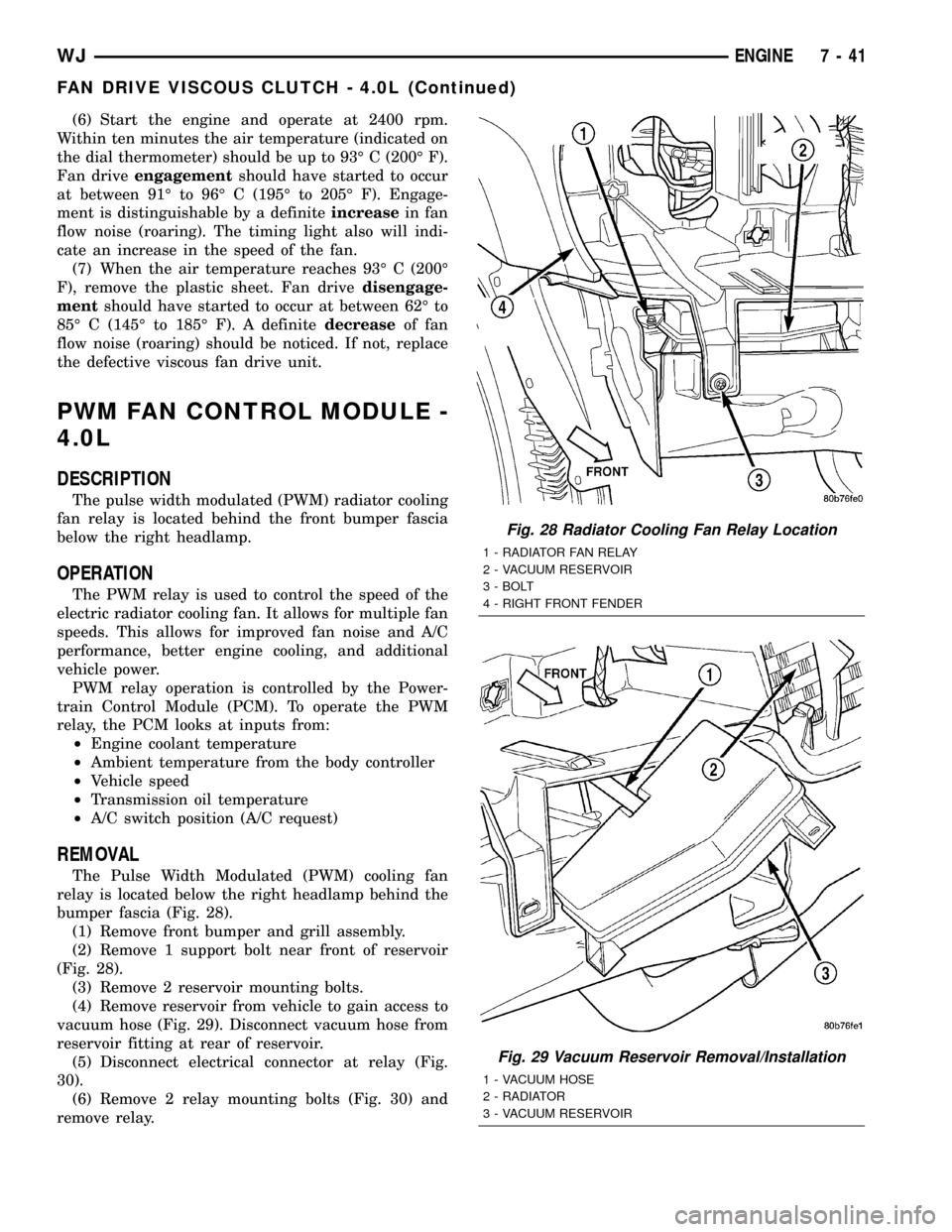
(6) Start the engine and operate at 2400 rpm.
Within ten minutes the air temperature (indicated on
the dial thermometer) should be up to 93É C (200É F).
Fan driveengagementshould have started to occur
at between 91É to 96É C (195É to 205É F). Engage-
ment is distinguishable by a definiteincreasein fan
flow noise (roaring). The timing light also will indi-
cate an increase in the speed of the fan.
(7) When the air temperature reaches 93É C (200É
F), remove the plastic sheet. Fan drivedisengage-
mentshould have started to occur at between 62É to
85É C (145É to 185É F). A definitedecreaseof fan
flow noise (roaring) should be noticed. If not, replace
the defective viscous fan drive unit.
PWM FAN CONTROL MODULE -
4.0L
DESCRIPTION
The pulse width modulated (PWM) radiator cooling
fan relay is located behind the front bumper fascia
below the right headlamp.
OPERATION
The PWM relay is used to control the speed of the
electric radiator cooling fan. It allows for multiple fan
speeds. This allows for improved fan noise and A/C
performance, better engine cooling, and additional
vehicle power.
PWM relay operation is controlled by the Power-
train Control Module (PCM). To operate the PWM
relay, the PCM looks at inputs from:
²Engine coolant temperature
²Ambient temperature from the body controller
²Vehicle speed
²Transmission oil temperature
²A/C switch position (A/C request)
REMOVAL
The Pulse Width Modulated (PWM) cooling fan
relay is located below the right headlamp behind the
bumper fascia (Fig. 28).
(1) Remove front bumper and grill assembly.
(2) Remove 1 support bolt near front of reservoir
(Fig. 28).
(3) Remove 2 reservoir mounting bolts.
(4) Remove reservoir from vehicle to gain access to
vacuum hose (Fig. 29). Disconnect vacuum hose from
reservoir fitting at rear of reservoir.
(5) Disconnect electrical connector at relay (Fig.
30).
(6) Remove 2 relay mounting bolts (Fig. 30) and
remove relay.
Fig. 28 Radiator Cooling Fan Relay Location
1 - RADIATOR FAN RELAY
2 - VACUUM RESERVOIR
3 - BOLT
4 - RIGHT FRONT FENDER
Fig. 29 Vacuum Reservoir Removal/Installation
1 - VACUUM HOSE
2 - RADIATOR
3 - VACUUM RESERVOIR
WJENGINE 7 - 41
FAN DRIVE VISCOUS CLUTCH - 4.0L (Continued)
Page 270 of 2199
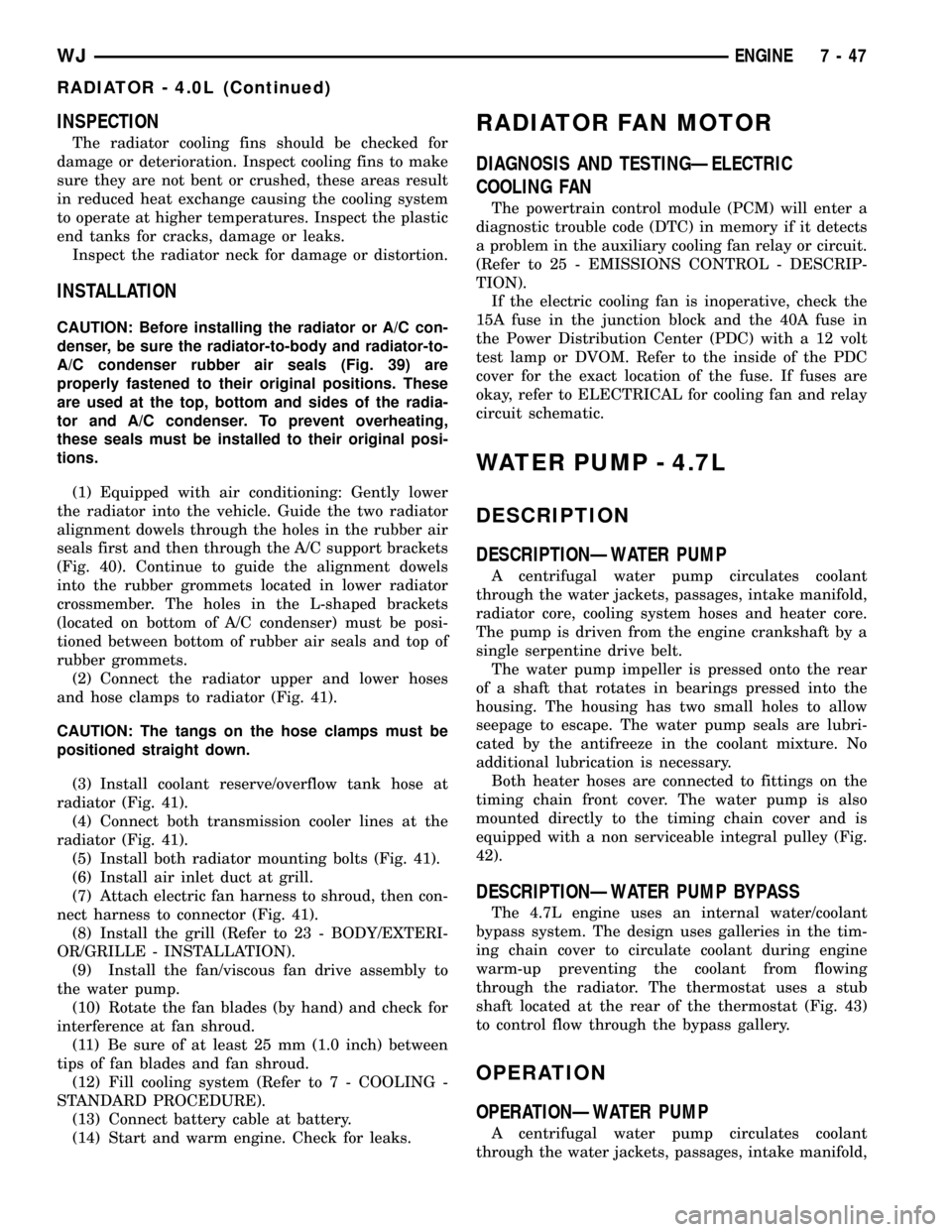
INSPECTION
The radiator cooling fins should be checked for
damage or deterioration. Inspect cooling fins to make
sure they are not bent or crushed, these areas result
in reduced heat exchange causing the cooling system
to operate at higher temperatures. Inspect the plastic
end tanks for cracks, damage or leaks.
Inspect the radiator neck for damage or distortion.
INSTALLATION
CAUTION: Before installing the radiator or A/C con-
denser, be sure the radiator-to-body and radiator-to-
A/C condenser rubber air seals (Fig. 39) are
properly fastened to their original positions. These
are used at the top, bottom and sides of the radia-
tor and A/C condenser. To prevent overheating,
these seals must be installed to their original posi-
tions.
(1) Equipped with air conditioning: Gently lower
the radiator into the vehicle. Guide the two radiator
alignment dowels through the holes in the rubber air
seals first and then through the A/C support brackets
(Fig. 40). Continue to guide the alignment dowels
into the rubber grommets located in lower radiator
crossmember. The holes in the L-shaped brackets
(located on bottom of A/C condenser) must be posi-
tioned between bottom of rubber air seals and top of
rubber grommets.
(2) Connect the radiator upper and lower hoses
and hose clamps to radiator (Fig. 41).
CAUTION: The tangs on the hose clamps must be
positioned straight down.
(3) Install coolant reserve/overflow tank hose at
radiator (Fig. 41).
(4) Connect both transmission cooler lines at the
radiator (Fig. 41).
(5) Install both radiator mounting bolts (Fig. 41).
(6) Install air inlet duct at grill.
(7) Attach electric fan harness to shroud, then con-
nect harness to connector (Fig. 41).
(8) Install the grill (Refer to 23 - BODY/EXTERI-
OR/GRILLE - INSTALLATION).
(9) Install the fan/viscous fan drive assembly to
the water pump.
(10) Rotate the fan blades (by hand) and check for
interference at fan shroud.
(11) Be sure of at least 25 mm (1.0 inch) between
tips of fan blades and fan shroud.
(12) Fill cooling system (Refer to 7 - COOLING -
STANDARD PROCEDURE).
(13) Connect battery cable at battery.
(14) Start and warm engine. Check for leaks.
RADIATOR FAN MOTOR
DIAGNOSIS AND TESTINGÐELECTRIC
COOLING FAN
The powertrain control module (PCM) will enter a
diagnostic trouble code (DTC) in memory if it detects
a problem in the auxiliary cooling fan relay or circuit.
(Refer to 25 - EMISSIONS CONTROL - DESCRIP-
TION).
If the electric cooling fan is inoperative, check the
15A fuse in the junction block and the 40A fuse in
the Power Distribution Center (PDC) with a 12 volt
test lamp or DVOM. Refer to the inside of the PDC
cover for the exact location of the fuse. If fuses are
okay, refer to ELECTRICAL for cooling fan and relay
circuit schematic.
WATER PUMP - 4.7L
DESCRIPTION
DESCRIPTIONÐWATER PUMP
A centrifugal water pump circulates coolant
through the water jackets, passages, intake manifold,
radiator core, cooling system hoses and heater core.
The pump is driven from the engine crankshaft by a
single serpentine drive belt.
The water pump impeller is pressed onto the rear
of a shaft that rotates in bearings pressed into the
housing. The housing has two small holes to allow
seepage to escape. The water pump seals are lubri-
cated by the antifreeze in the coolant mixture. No
additional lubrication is necessary.
Both heater hoses are connected to fittings on the
timing chain front cover. The water pump is also
mounted directly to the timing chain cover and is
equipped with a non serviceable integral pulley (Fig.
42).
DESCRIPTIONÐWATER PUMP BYPASS
The 4.7L engine uses an internal water/coolant
bypass system. The design uses galleries in the tim-
ing chain cover to circulate coolant during engine
warm-up preventing the coolant from flowing
through the radiator. The thermostat uses a stub
shaft located at the rear of the thermostat (Fig. 43)
to control flow through the bypass gallery.
OPERATION
OPERATIONÐWATER PUMP
A centrifugal water pump circulates coolant
through the water jackets, passages, intake manifold,
WJENGINE 7 - 47
RADIATOR - 4.0L (Continued)
Page 310 of 2199
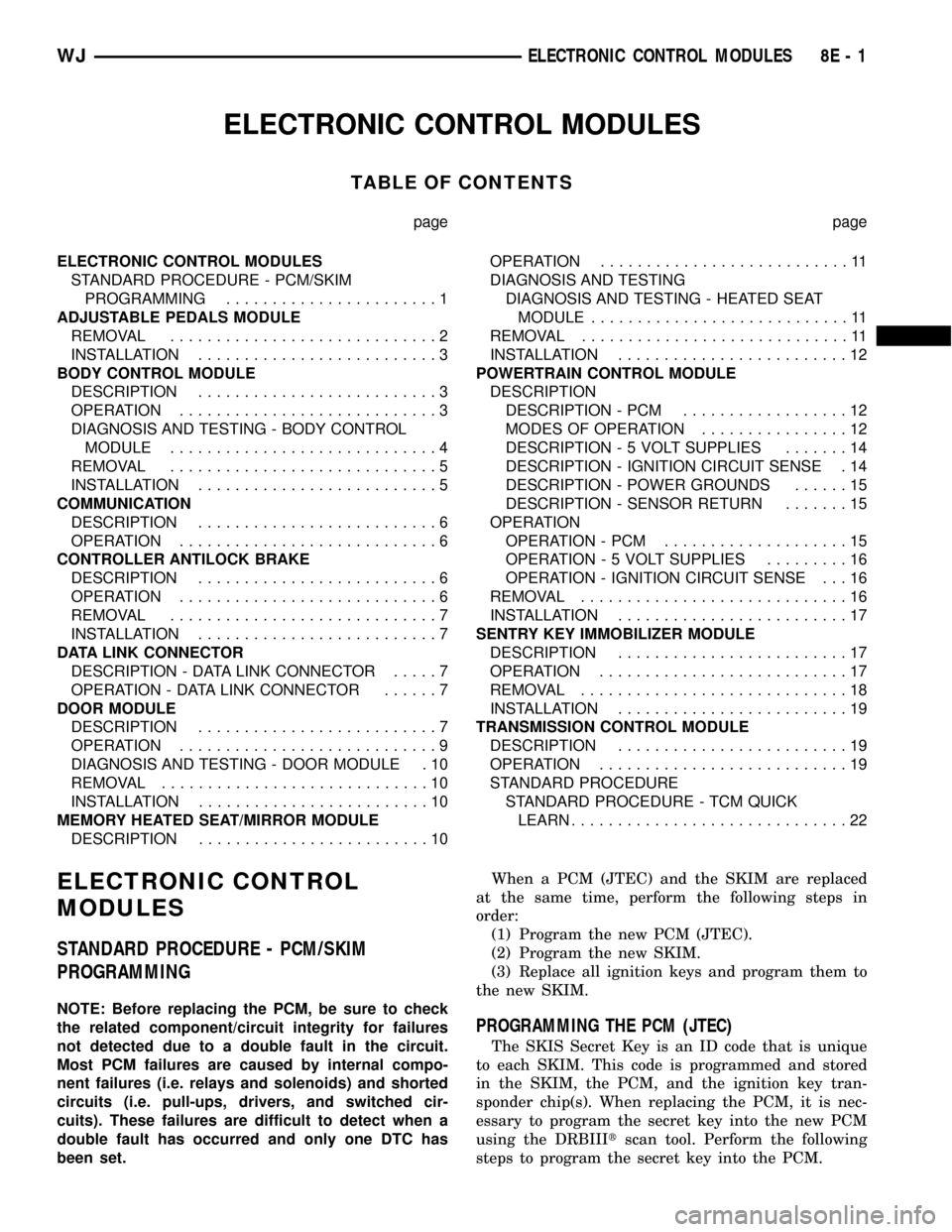
ELECTRONIC CONTROL MODULES
TABLE OF CONTENTS
page page
ELECTRONIC CONTROL MODULES
STANDARD PROCEDURE - PCM/SKIM
PROGRAMMING.......................1
ADJUSTABLE PEDALS MODULE
REMOVAL.............................2
INSTALLATION..........................3
BODY CONTROL MODULE
DESCRIPTION..........................3
OPERATION............................3
DIAGNOSIS AND TESTING - BODY CONTROL
MODULE.............................4
REMOVAL.............................5
INSTALLATION..........................5
COMMUNICATION
DESCRIPTION..........................6
OPERATION............................6
CONTROLLER ANTILOCK BRAKE
DESCRIPTION..........................6
OPERATION............................6
REMOVAL.............................7
INSTALLATION..........................7
DATA LINK CONNECTOR
DESCRIPTION - DATA LINK CONNECTOR.....7
OPERATION - DATA LINK CONNECTOR......7
DOOR MODULE
DESCRIPTION..........................7
OPERATION............................9
DIAGNOSIS AND TESTING - DOOR MODULE . 10
REMOVAL.............................10
INSTALLATION.........................10
MEMORY HEATED SEAT/MIRROR MODULE
DESCRIPTION.........................10OPERATION...........................11
DIAGNOSIS AND TESTING
DIAGNOSIS AND TESTING - HEATED SEAT
MODULE............................11
REMOVAL.............................11
INSTALLATION.........................12
POWERTRAIN CONTROL MODULE
DESCRIPTION
DESCRIPTION - PCM..................12
MODES OF OPERATION................12
DESCRIPTION - 5 VOLT SUPPLIES.......14
DESCRIPTION - IGNITION CIRCUIT SENSE . 14
DESCRIPTION - POWER GROUNDS......15
DESCRIPTION - SENSOR RETURN.......15
OPERATION
OPERATION - PCM....................15
OPERATION - 5 VOLT SUPPLIES.........16
OPERATION - IGNITION CIRCUIT SENSE . . . 16
REMOVAL.............................16
INSTALLATION.........................17
SENTRY KEY IMMOBILIZER MODULE
DESCRIPTION.........................17
OPERATION...........................17
REMOVAL.............................18
INSTALLATION.........................19
TRANSMISSION CONTROL MODULE
DESCRIPTION.........................19
OPERATION...........................19
STANDARD PROCEDURE
STANDARD PROCEDURE - TCM QUICK
LEARN..............................22
ELECTRONIC CONTROL
MODULES
STANDARD PROCEDURE - PCM/SKIM
PROGRAMMING
NOTE: Before replacing the PCM, be sure to check
the related component/circuit integrity for failures
not detected due to a double fault in the circuit.
Most PCM failures are caused by internal compo-
nent failures (i.e. relays and solenoids) and shorted
circuits (i.e. pull-ups, drivers, and switched cir-
cuits). These failures are difficult to detect when a
double fault has occurred and only one DTC has
been set.When a PCM (JTEC) and the SKIM are replaced
at the same time, perform the following steps in
order:
(1) Program the new PCM (JTEC).
(2) Program the new SKIM.
(3) Replace all ignition keys and program them to
the new SKIM.
PROGRAMMING THE PCM (JTEC)
The SKIS Secret Key is an ID code that is unique
to each SKIM. This code is programmed and stored
in the SKIM, the PCM, and the ignition key tran-
sponder chip(s). When replacing the PCM, it is nec-
essary to program the secret key into the new PCM
using the DRBIIItscan tool. Perform the following
steps to program the secret key into the PCM.
WJELECTRONIC CONTROL MODULES 8E - 1
Page 311 of 2199
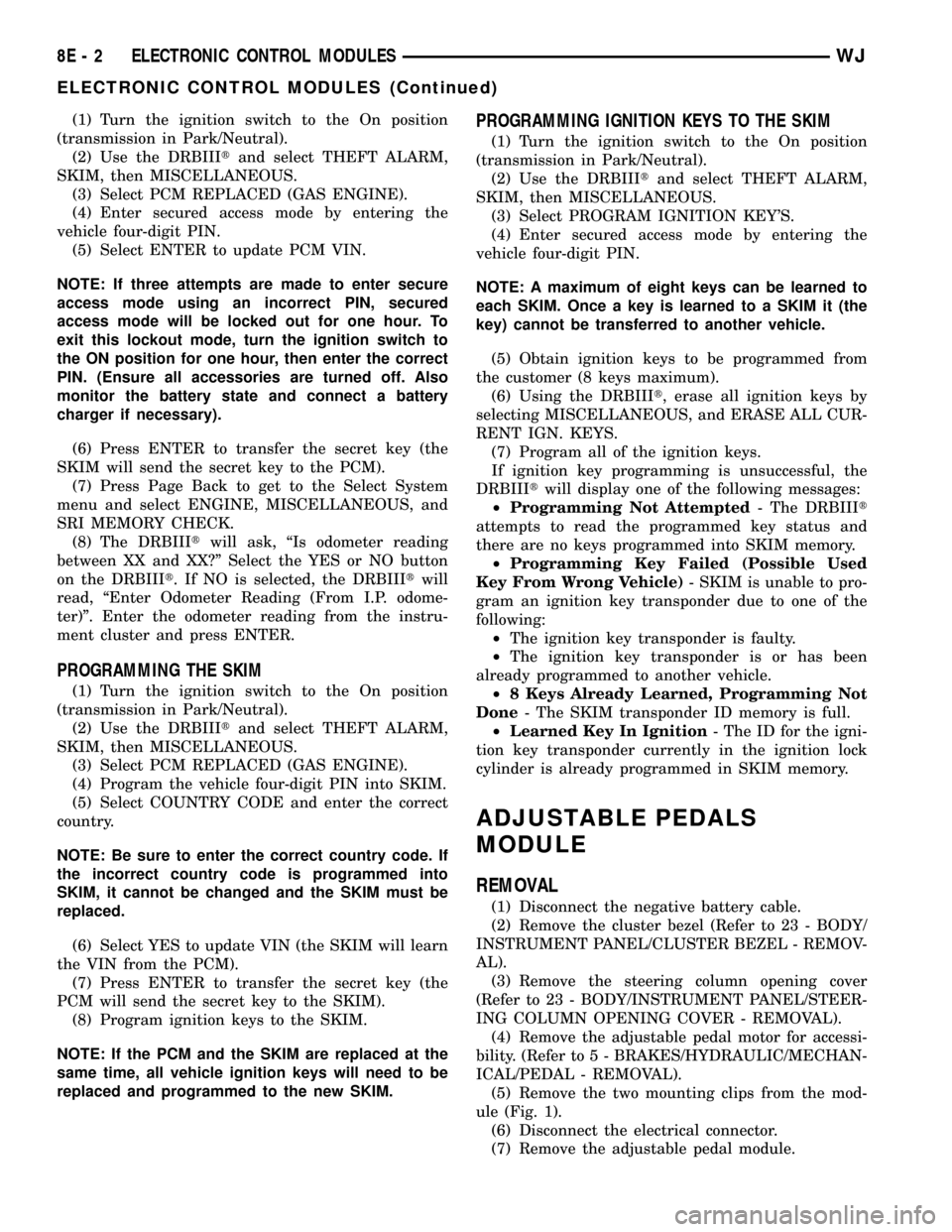
(1) Turn the ignition switch to the On position
(transmission in Park/Neutral).
(2) Use the DRBIIItand select THEFT ALARM,
SKIM, then MISCELLANEOUS.
(3) Select PCM REPLACED (GAS ENGINE).
(4) Enter secured access mode by entering the
vehicle four-digit PIN.
(5) Select ENTER to update PCM VIN.
NOTE: If three attempts are made to enter secure
access mode using an incorrect PIN, secured
access mode will be locked out for one hour. To
exit this lockout mode, turn the ignition switch to
the ON position for one hour, then enter the correct
PIN. (Ensure all accessories are turned off. Also
monitor the battery state and connect a battery
charger if necessary).
(6) Press ENTER to transfer the secret key (the
SKIM will send the secret key to the PCM).
(7) Press Page Back to get to the Select System
menu and select ENGINE, MISCELLANEOUS, and
SRI MEMORY CHECK.
(8) The DRBIIItwill ask, ªIs odometer reading
between XX and XX?º Select the YES or NO button
on the DRBIIIt. If NO is selected, the DRBIIItwill
read, ªEnter Odometer Reading (From I.P. odome-
ter)º. Enter the odometer reading from the instru-
ment cluster and press ENTER.
PROGRAMMING THE SKIM
(1) Turn the ignition switch to the On position
(transmission in Park/Neutral).
(2) Use the DRBIIItand select THEFT ALARM,
SKIM, then MISCELLANEOUS.
(3) Select PCM REPLACED (GAS ENGINE).
(4) Program the vehicle four-digit PIN into SKIM.
(5) Select COUNTRY CODE and enter the correct
country.
NOTE: Be sure to enter the correct country code. If
the incorrect country code is programmed into
SKIM, it cannot be changed and the SKIM must be
replaced.
(6) Select YES to update VIN (the SKIM will learn
the VIN from the PCM).
(7) Press ENTER to transfer the secret key (the
PCM will send the secret key to the SKIM).
(8) Program ignition keys to the SKIM.
NOTE: If the PCM and the SKIM are replaced at the
same time, all vehicle ignition keys will need to be
replaced and programmed to the new SKIM.
PROGRAMMING IGNITION KEYS TO THE SKIM
(1) Turn the ignition switch to the On position
(transmission in Park/Neutral).
(2) Use the DRBIIItand select THEFT ALARM,
SKIM, then MISCELLANEOUS.
(3) Select PROGRAM IGNITION KEY'S.
(4) Enter secured access mode by entering the
vehicle four-digit PIN.
NOTE: A maximum of eight keys can be learned to
each SKIM. Once a key is learned to a SKIM it (the
key) cannot be transferred to another vehicle.
(5) Obtain ignition keys to be programmed from
the customer (8 keys maximum).
(6) Using the DRBIIIt, erase all ignition keys by
selecting MISCELLANEOUS, and ERASE ALL CUR-
RENT IGN. KEYS.
(7) Program all of the ignition keys.
If ignition key programming is unsuccessful, the
DRBIIItwill display one of the following messages:
²Programming Not Attempted- The DRBIIIt
attempts to read the programmed key status and
there are no keys programmed into SKIM memory.
²Programming Key Failed (Possible Used
Key From Wrong Vehicle)- SKIM is unable to pro-
gram an ignition key transponder due to one of the
following:
²The ignition key transponder is faulty.
²The ignition key transponder is or has been
already programmed to another vehicle.
²8 Keys Already Learned, Programming Not
Done- The SKIM transponder ID memory is full.
²Learned Key In Ignition- The ID for the igni-
tion key transponder currently in the ignition lock
cylinder is already programmed in SKIM memory.
ADJUSTABLE PEDALS
MODULE
REMOVAL
(1) Disconnect the negative battery cable.
(2) Remove the cluster bezel (Refer to 23 - BODY/
INSTRUMENT PANEL/CLUSTER BEZEL - REMOV-
AL).
(3) Remove the steering column opening cover
(Refer to 23 - BODY/INSTRUMENT PANEL/STEER-
ING COLUMN OPENING COVER - REMOVAL).
(4) Remove the adjustable pedal motor for accessi-
bility. (Refer to 5 - BRAKES/HYDRAULIC/MECHAN-
ICAL/PEDAL - REMOVAL).
(5) Remove the two mounting clips from the mod-
ule (Fig. 1).
(6) Disconnect the electrical connector.
(7) Remove the adjustable pedal module.
8E - 2 ELECTRONIC CONTROL MODULESWJ
ELECTRONIC CONTROL MODULES (Continued)
Page 315 of 2199
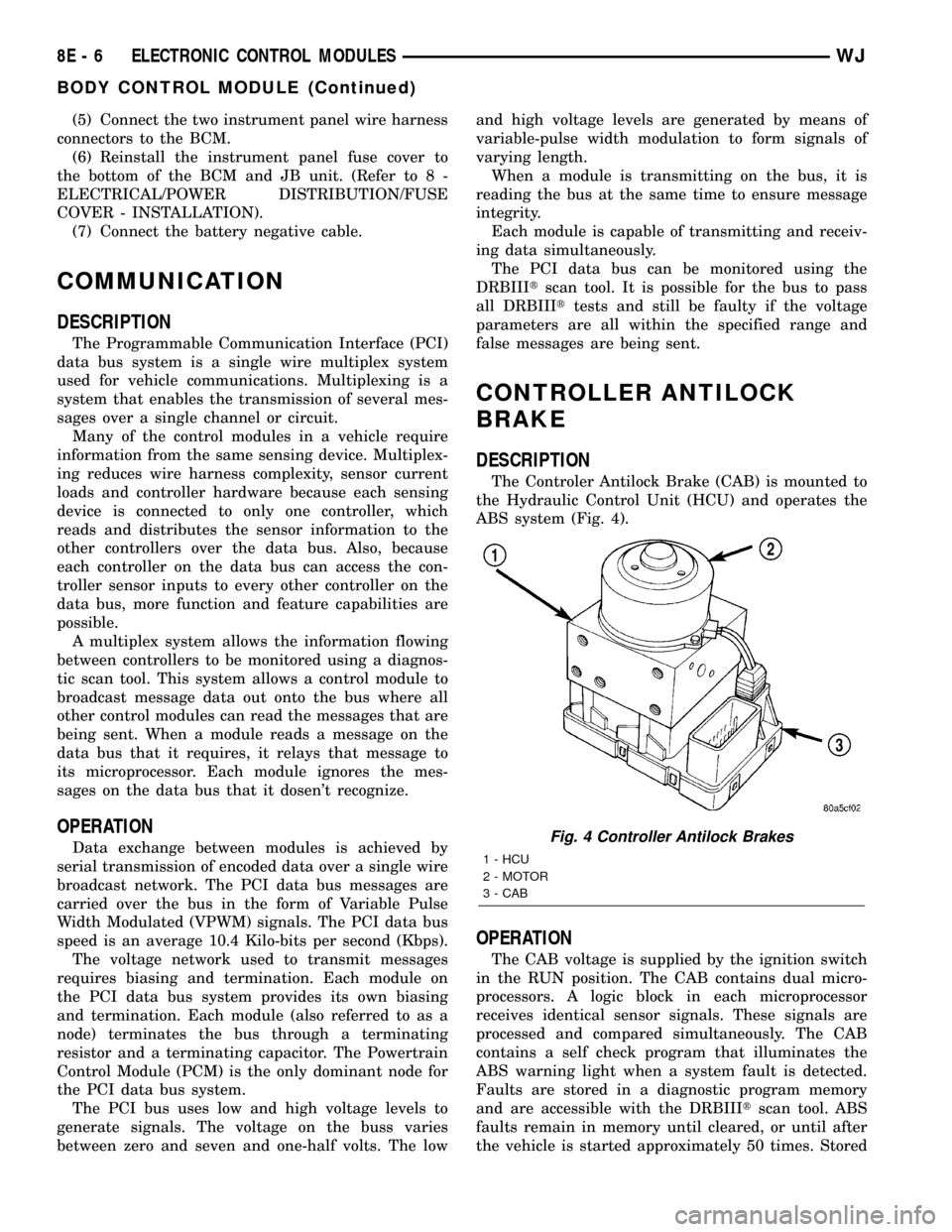
(5) Connect the two instrument panel wire harness
connectors to the BCM.
(6) Reinstall the instrument panel fuse cover to
the bottom of the BCM and JB unit. (Refer to 8 -
ELECTRICAL/POWER DISTRIBUTION/FUSE
COVER - INSTALLATION).
(7) Connect the battery negative cable.
COMMUNICATION
DESCRIPTION
The Programmable Communication Interface (PCI)
data bus system is a single wire multiplex system
used for vehicle communications. Multiplexing is a
system that enables the transmission of several mes-
sages over a single channel or circuit.
Many of the control modules in a vehicle require
information from the same sensing device. Multiplex-
ing reduces wire harness complexity, sensor current
loads and controller hardware because each sensing
device is connected to only one controller, which
reads and distributes the sensor information to the
other controllers over the data bus. Also, because
each controller on the data bus can access the con-
troller sensor inputs to every other controller on the
data bus, more function and feature capabilities are
possible.
A multiplex system allows the information flowing
between controllers to be monitored using a diagnos-
tic scan tool. This system allows a control module to
broadcast message data out onto the bus where all
other control modules can read the messages that are
being sent. When a module reads a message on the
data bus that it requires, it relays that message to
its microprocessor. Each module ignores the mes-
sages on the data bus that it dosen't recognize.
OPERATION
Data exchange between modules is achieved by
serial transmission of encoded data over a single wire
broadcast network. The PCI data bus messages are
carried over the bus in the form of Variable Pulse
Width Modulated (VPWM) signals. The PCI data bus
speed is an average 10.4 Kilo-bits per second (Kbps).
The voltage network used to transmit messages
requires biasing and termination. Each module on
the PCI data bus system provides its own biasing
and termination. Each module (also referred to as a
node) terminates the bus through a terminating
resistor and a terminating capacitor. The Powertrain
Control Module (PCM) is the only dominant node for
the PCI data bus system.
The PCI bus uses low and high voltage levels to
generate signals. The voltage on the buss varies
between zero and seven and one-half volts. The lowand high voltage levels are generated by means of
variable-pulse width modulation to form signals of
varying length.
When a module is transmitting on the bus, it is
reading the bus at the same time to ensure message
integrity.
Each module is capable of transmitting and receiv-
ing data simultaneously.
The PCI data bus can be monitored using the
DRBIIItscan tool. It is possible for the bus to pass
all DRBIIIttests and still be faulty if the voltage
parameters are all within the specified range and
false messages are being sent.
CONTROLLER ANTILOCK
BRAKE
DESCRIPTION
The Controler Antilock Brake (CAB) is mounted to
the Hydraulic Control Unit (HCU) and operates the
ABS system (Fig. 4).
OPERATION
The CAB voltage is supplied by the ignition switch
in the RUN position. The CAB contains dual micro-
processors. A logic block in each microprocessor
receives identical sensor signals. These signals are
processed and compared simultaneously. The CAB
contains a self check program that illuminates the
ABS warning light when a system fault is detected.
Faults are stored in a diagnostic program memory
and are accessible with the DRBIIItscan tool. ABS
faults remain in memory until cleared, or until after
the vehicle is started approximately 50 times. Stored
Fig. 4 Controller Antilock Brakes
1 - HCU
2 - MOTOR
3 - CAB
8E - 6 ELECTRONIC CONTROL MODULESWJ
BODY CONTROL MODULE (Continued)
Page 320 of 2199
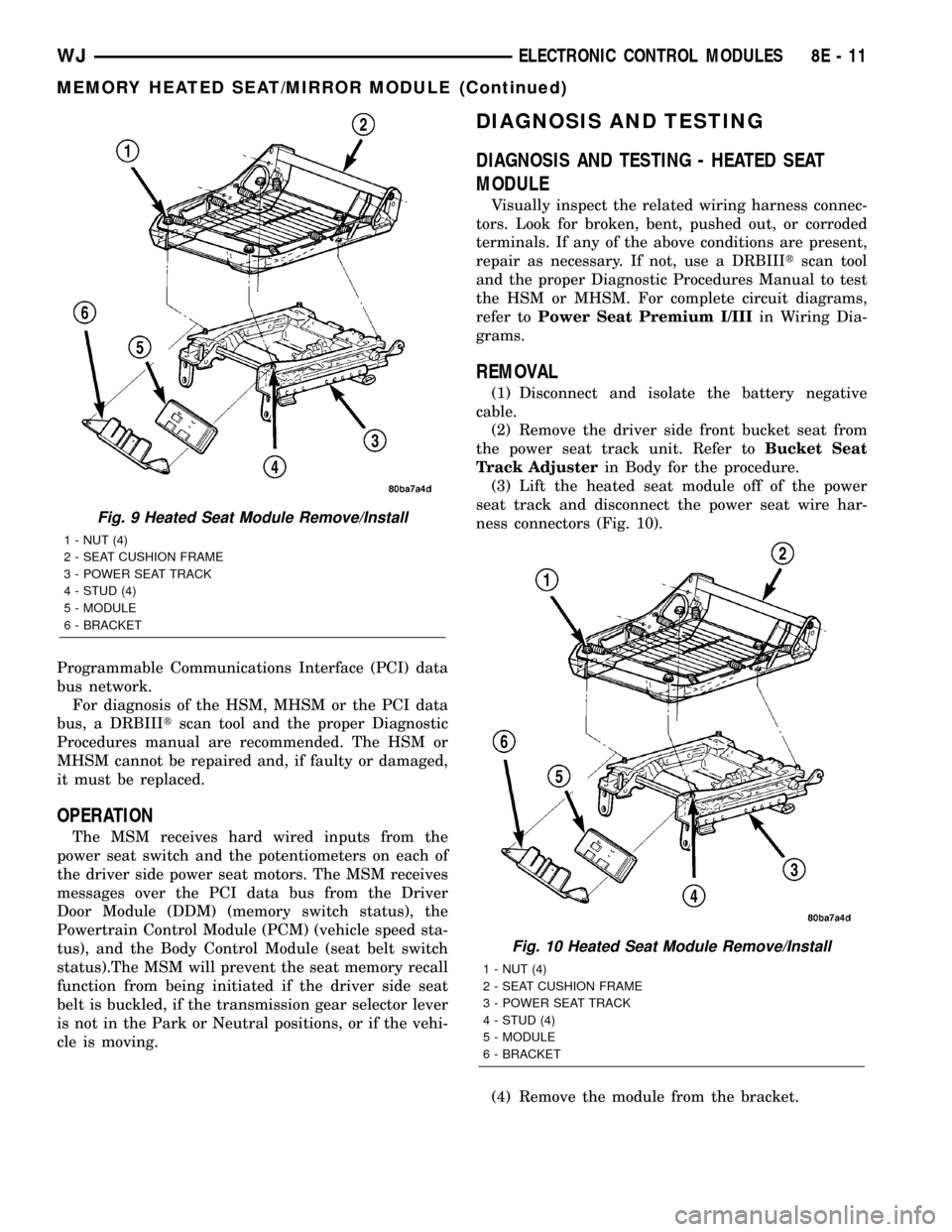
Programmable Communications Interface (PCI) data
bus network.
For diagnosis of the HSM, MHSM or the PCI data
bus, a DRBIIItscan tool and the proper Diagnostic
Procedures manual are recommended. The HSM or
MHSM cannot be repaired and, if faulty or damaged,
it must be replaced.
OPERATION
The MSM receives hard wired inputs from the
power seat switch and the potentiometers on each of
the driver side power seat motors. The MSM receives
messages over the PCI data bus from the Driver
Door Module (DDM) (memory switch status), the
Powertrain Control Module (PCM) (vehicle speed sta-
tus), and the Body Control Module (seat belt switch
status).The MSM will prevent the seat memory recall
function from being initiated if the driver side seat
belt is buckled, if the transmission gear selector lever
is not in the Park or Neutral positions, or if the vehi-
cle is moving.
DIAGNOSIS AND TESTING
DIAGNOSIS AND TESTING - HEATED SEAT
MODULE
Visually inspect the related wiring harness connec-
tors. Look for broken, bent, pushed out, or corroded
terminals. If any of the above conditions are present,
repair as necessary. If not, use a DRBIIItscan tool
and the proper Diagnostic Procedures Manual to test
the HSM or MHSM. For complete circuit diagrams,
refer toPower Seat Premium I/IIIin Wiring Dia-
grams.
REMOVAL
(1) Disconnect and isolate the battery negative
cable.
(2) Remove the driver side front bucket seat from
the power seat track unit. Refer toBucket Seat
Track Adjusterin Body for the procedure.
(3) Lift the heated seat module off of the power
seat track and disconnect the power seat wire har-
ness connectors (Fig. 10).
(4) Remove the module from the bracket.
Fig. 9 Heated Seat Module Remove/Install
1 - NUT (4)
2 - SEAT CUSHION FRAME
3 - POWER SEAT TRACK
4 - STUD (4)
5 - MODULE
6 - BRACKET
Fig. 10 Heated Seat Module Remove/Install
1 - NUT (4)
2 - SEAT CUSHION FRAME
3 - POWER SEAT TRACK
4 - STUD (4)
5 - MODULE
6 - BRACKET
WJELECTRONIC CONTROL MODULES 8E - 11
MEMORY HEATED SEAT/MIRROR MODULE (Continued)
Page 324 of 2199
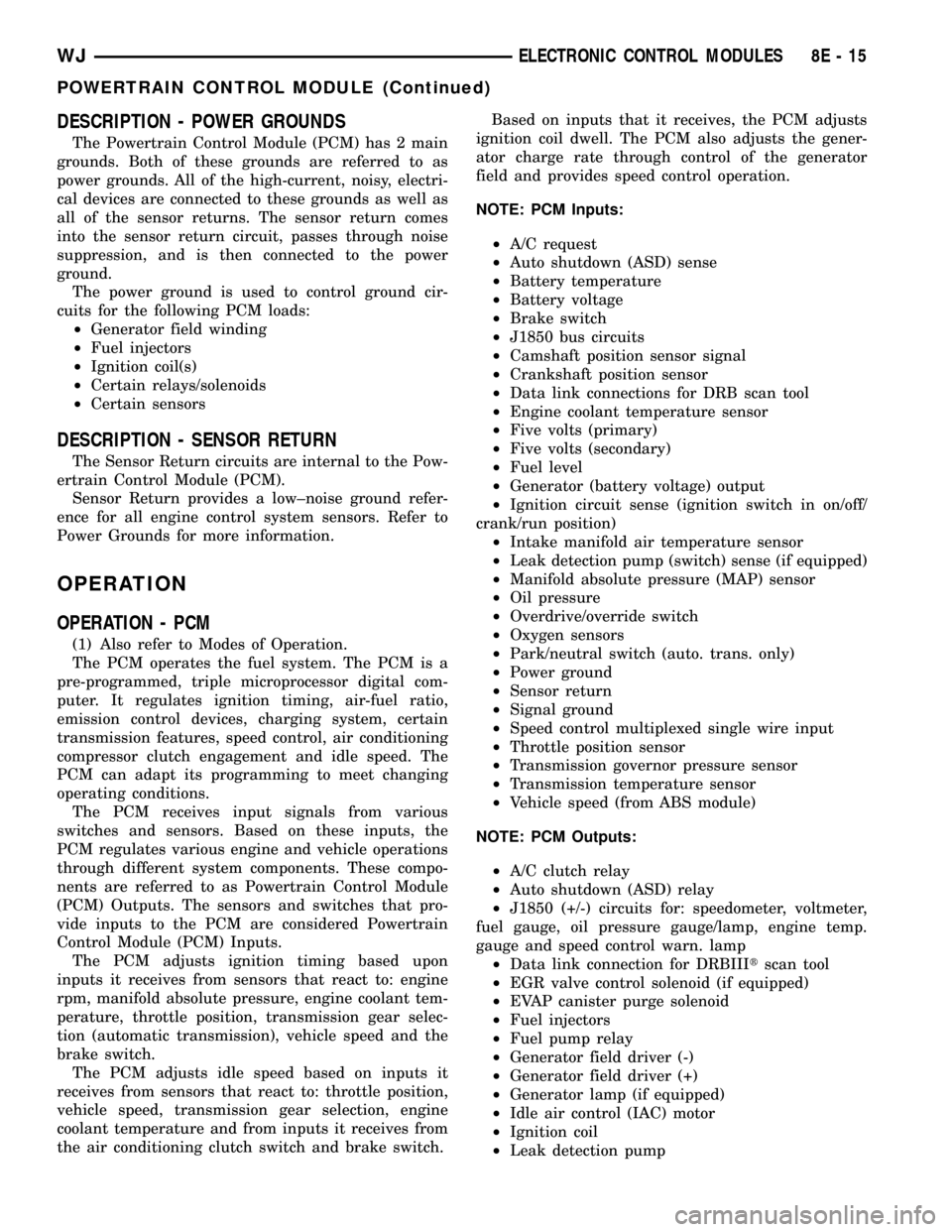
DESCRIPTION - POWER GROUNDS
The Powertrain Control Module (PCM) has 2 main
grounds. Both of these grounds are referred to as
power grounds. All of the high-current, noisy, electri-
cal devices are connected to these grounds as well as
all of the sensor returns. The sensor return comes
into the sensor return circuit, passes through noise
suppression, and is then connected to the power
ground.
The power ground is used to control ground cir-
cuits for the following PCM loads:
²Generator field winding
²Fuel injectors
²Ignition coil(s)
²Certain relays/solenoids
²Certain sensors
DESCRIPTION - SENSOR RETURN
The Sensor Return circuits are internal to the Pow-
ertrain Control Module (PCM).
Sensor Return provides a low±noise ground refer-
ence for all engine control system sensors. Refer to
Power Grounds for more information.
OPERATION
OPERATION - PCM
(1) Also refer to Modes of Operation.
The PCM operates the fuel system. The PCM is a
pre-programmed, triple microprocessor digital com-
puter. It regulates ignition timing, air-fuel ratio,
emission control devices, charging system, certain
transmission features, speed control, air conditioning
compressor clutch engagement and idle speed. The
PCM can adapt its programming to meet changing
operating conditions.
The PCM receives input signals from various
switches and sensors. Based on these inputs, the
PCM regulates various engine and vehicle operations
through different system components. These compo-
nents are referred to as Powertrain Control Module
(PCM) Outputs. The sensors and switches that pro-
vide inputs to the PCM are considered Powertrain
Control Module (PCM) Inputs.
The PCM adjusts ignition timing based upon
inputs it receives from sensors that react to: engine
rpm, manifold absolute pressure, engine coolant tem-
perature, throttle position, transmission gear selec-
tion (automatic transmission), vehicle speed and the
brake switch.
The PCM adjusts idle speed based on inputs it
receives from sensors that react to: throttle position,
vehicle speed, transmission gear selection, engine
coolant temperature and from inputs it receives from
the air conditioning clutch switch and brake switch.Based on inputs that it receives, the PCM adjusts
ignition coil dwell. The PCM also adjusts the gener-
ator charge rate through control of the generator
field and provides speed control operation.
NOTE: PCM Inputs:
²A/C request
²Auto shutdown (ASD) sense
²Battery temperature
²Battery voltage
²Brake switch
²J1850 bus circuits
²Camshaft position sensor signal
²Crankshaft position sensor
²Data link connections for DRB scan tool
²Engine coolant temperature sensor
²Five volts (primary)
²Five volts (secondary)
²Fuel level
²Generator (battery voltage) output
²Ignition circuit sense (ignition switch in on/off/
crank/run position)
²Intake manifold air temperature sensor
²Leak detection pump (switch) sense (if equipped)
²Manifold absolute pressure (MAP) sensor
²Oil pressure
²Overdrive/override switch
²Oxygen sensors
²Park/neutral switch (auto. trans. only)
²Power ground
²Sensor return
²Signal ground
²Speed control multiplexed single wire input
²Throttle position sensor
²Transmission governor pressure sensor
²Transmission temperature sensor
²Vehicle speed (from ABS module)
NOTE: PCM Outputs:
²A/C clutch relay
²Auto shutdown (ASD) relay
²J1850 (+/-) circuits for: speedometer, voltmeter,
fuel gauge, oil pressure gauge/lamp, engine temp.
gauge and speed control warn. lamp
²Data link connection for DRBIIItscan tool
²EGR valve control solenoid (if equipped)
²EVAP canister purge solenoid
²Fuel injectors
²Fuel pump relay
²Generator field driver (-)
²Generator field driver (+)
²Generator lamp (if equipped)
²Idle air control (IAC) motor
²Ignition coil
²Leak detection pump
WJELECTRONIC CONTROL MODULES 8E - 15
POWERTRAIN CONTROL MODULE (Continued)
Page 325 of 2199
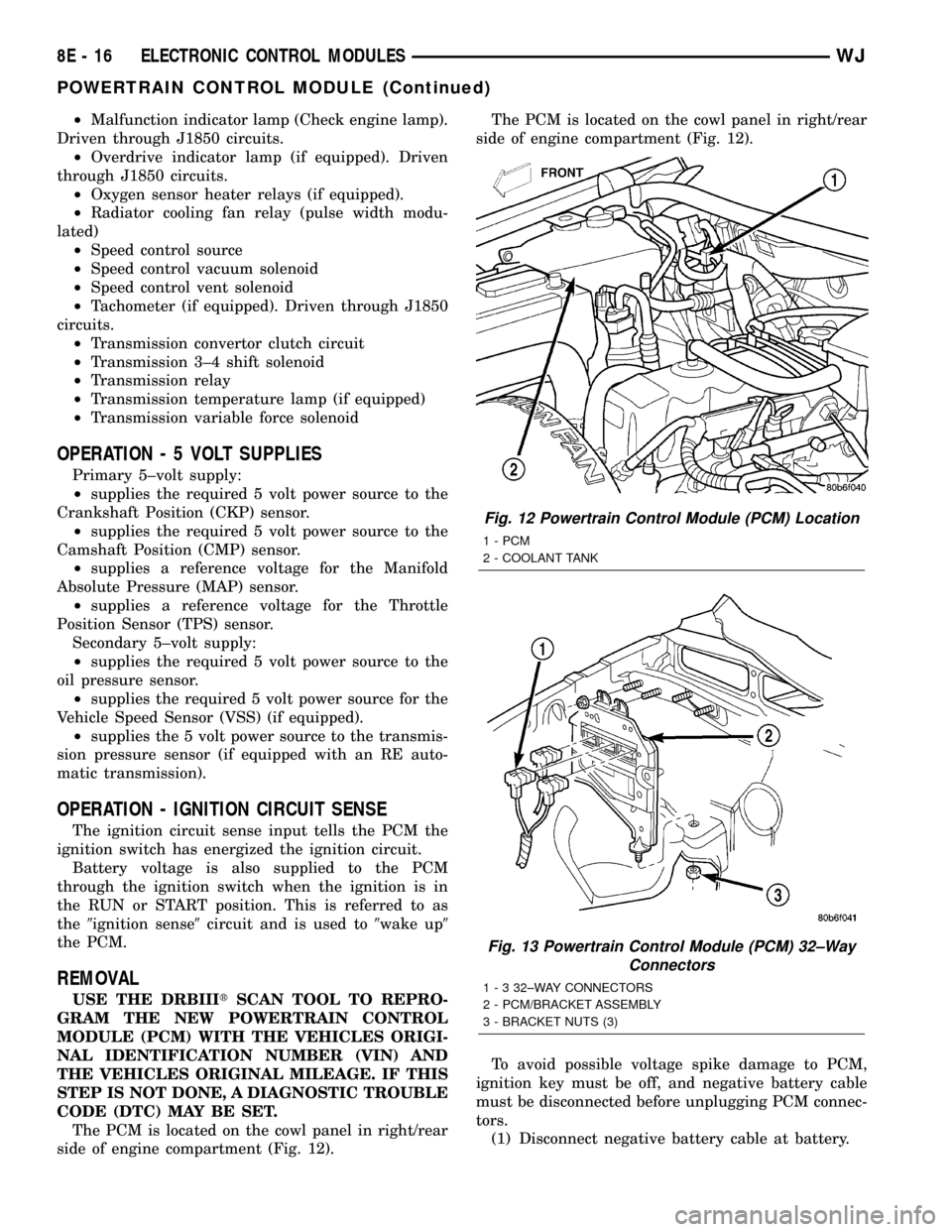
²Malfunction indicator lamp (Check engine lamp).
Driven through J1850 circuits.
²Overdrive indicator lamp (if equipped). Driven
through J1850 circuits.
²Oxygen sensor heater relays (if equipped).
²Radiator cooling fan relay (pulse width modu-
lated)
²Speed control source
²Speed control vacuum solenoid
²Speed control vent solenoid
²Tachometer (if equipped). Driven through J1850
circuits.
²Transmission convertor clutch circuit
²Transmission 3±4 shift solenoid
²Transmission relay
²Transmission temperature lamp (if equipped)
²Transmission variable force solenoid
OPERATION - 5 VOLT SUPPLIES
Primary 5±volt supply:
²supplies the required 5 volt power source to the
Crankshaft Position (CKP) sensor.
²supplies the required 5 volt power source to the
Camshaft Position (CMP) sensor.
²supplies a reference voltage for the Manifold
Absolute Pressure (MAP) sensor.
²supplies a reference voltage for the Throttle
Position Sensor (TPS) sensor.
Secondary 5±volt supply:
²supplies the required 5 volt power source to the
oil pressure sensor.
²supplies the required 5 volt power source for the
Vehicle Speed Sensor (VSS) (if equipped).
²supplies the 5 volt power source to the transmis-
sion pressure sensor (if equipped with an RE auto-
matic transmission).
OPERATION - IGNITION CIRCUIT SENSE
The ignition circuit sense input tells the PCM the
ignition switch has energized the ignition circuit.
Battery voltage is also supplied to the PCM
through the ignition switch when the ignition is in
the RUN or START position. This is referred to as
the9ignition sense9circuit and is used to9wake up9
the PCM.
REMOVAL
USE THE DRBIIItSCAN TOOL TO REPRO-
GRAM THE NEW POWERTRAIN CONTROL
MODULE (PCM) WITH THE VEHICLES ORIGI-
NAL IDENTIFICATION NUMBER (VIN) AND
THE VEHICLES ORIGINAL MILEAGE. IF THIS
STEP IS NOT DONE, A DIAGNOSTIC TROUBLE
CODE (DTC) MAY BE SET.
The PCM is located on the cowl panel in right/rear
side of engine compartment (Fig. 12).The PCM is located on the cowl panel in right/rear
side of engine compartment (Fig. 12).
To avoid possible voltage spike damage to PCM,
ignition key must be off, and negative battery cable
must be disconnected before unplugging PCM connec-
tors.
(1) Disconnect negative battery cable at battery.
Fig. 12 Powertrain Control Module (PCM) Location
1 - PCM
2 - COOLANT TANK
Fig. 13 Powertrain Control Module (PCM) 32±Way
Connectors
1 - 3 32±WAY CONNECTORS
2 - PCM/BRACKET ASSEMBLY
3 - BRACKET NUTS (3)
8E - 16 ELECTRONIC CONTROL MODULESWJ
POWERTRAIN CONTROL MODULE (Continued)
Page 326 of 2199
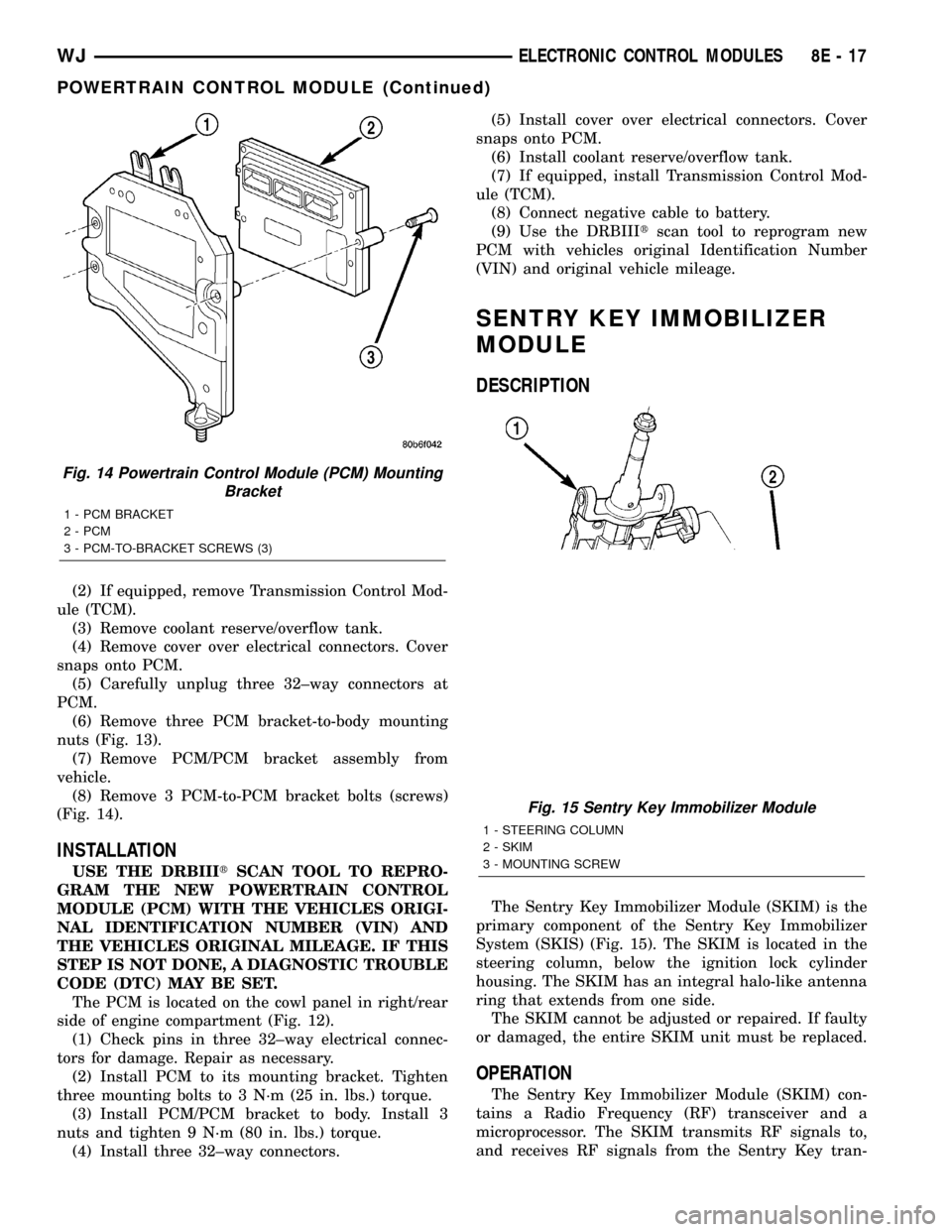
(2) If equipped, remove Transmission Control Mod-
ule (TCM).
(3) Remove coolant reserve/overflow tank.
(4) Remove cover over electrical connectors. Cover
snaps onto PCM.
(5) Carefully unplug three 32±way connectors at
PCM.
(6) Remove three PCM bracket-to-body mounting
nuts (Fig. 13).
(7) Remove PCM/PCM bracket assembly from
vehicle.
(8) Remove 3 PCM-to-PCM bracket bolts (screws)
(Fig. 14).
INSTALLATION
USE THE DRBIIItSCAN TOOL TO REPRO-
GRAM THE NEW POWERTRAIN CONTROL
MODULE (PCM) WITH THE VEHICLES ORIGI-
NAL IDENTIFICATION NUMBER (VIN) AND
THE VEHICLES ORIGINAL MILEAGE. IF THIS
STEP IS NOT DONE, A DIAGNOSTIC TROUBLE
CODE (DTC) MAY BE SET.
The PCM is located on the cowl panel in right/rear
side of engine compartment (Fig. 12).
(1) Check pins in three 32±way electrical connec-
tors for damage. Repair as necessary.
(2) Install PCM to its mounting bracket. Tighten
three mounting bolts to 3 N´m (25 in. lbs.) torque.
(3) Install PCM/PCM bracket to body. Install 3
nuts and tighten 9 N´m (80 in. lbs.) torque.
(4) Install three 32±way connectors.(5) Install cover over electrical connectors. Cover
snaps onto PCM.
(6) Install coolant reserve/overflow tank.
(7) If equipped, install Transmission Control Mod-
ule (TCM).
(8) Connect negative cable to battery.
(9) Use the DRBIIItscan tool to reprogram new
PCM with vehicles original Identification Number
(VIN) and original vehicle mileage.
SENTRY KEY IMMOBILIZER
MODULE
DESCRIPTION
The Sentry Key Immobilizer Module (SKIM) is the
primary component of the Sentry Key Immobilizer
System (SKIS) (Fig. 15). The SKIM is located in the
steering column, below the ignition lock cylinder
housing. The SKIM has an integral halo-like antenna
ring that extends from one side.
The SKIM cannot be adjusted or repaired. If faulty
or damaged, the entire SKIM unit must be replaced.
OPERATION
The Sentry Key Immobilizer Module (SKIM) con-
tains a Radio Frequency (RF) transceiver and a
microprocessor. The SKIM transmits RF signals to,
and receives RF signals from the Sentry Key tran-
Fig. 14 Powertrain Control Module (PCM) Mounting
Bracket
1 - PCM BRACKET
2 - PCM
3 - PCM-TO-BRACKET SCREWS (3)
Fig. 15 Sentry Key Immobilizer Module
1 - STEERING COLUMN
2 - SKIM
3 - MOUNTING SCREW
WJELECTRONIC CONTROL MODULES 8E - 17
POWERTRAIN CONTROL MODULE (Continued)