Transmission control module JEEP GRAND CHEROKEE 2002 WJ / 2.G Owner's Manual
[x] Cancel search | Manufacturer: JEEP, Model Year: 2002, Model line: GRAND CHEROKEE, Model: JEEP GRAND CHEROKEE 2002 WJ / 2.GPages: 2199, PDF Size: 76.01 MB
Page 442 of 2199

pletely controlled by the instrument cluster logic cir-
cuit, and that logic will only allow this indicator to
operate when the instrument cluster receives a bat-
tery current input on the fused ignition switch out-
put (run-start) circuit. Therefore, the indicator will
always be off when the ignition switch is in any posi-
tion except On or Start. The bulb only illuminates
when it is provided a path to ground by the instru-
ment cluster transistor. The instrument cluster will
turn on the overdrive off indicator for the following
reasons:
²Bulb Test- Each time the ignition switch is
turned to the On position the overdrive off indicator
is illuminated for about three seconds as a bulb test.
²Overdrive Off Indicator Lamp-On Message-
Each time the cluster receives an overdrive off indi-
cator lamp-on message from the PCM or TCM indi-
cating that the Off position of the overdrive off
switch has been selected, the overdrive off indicator
will be illuminated. The indicator remains illumi-
nated until the cluster receives an overdrive off indi-
cator lamp-off message from the PCM or TCM, or
until the ignition switch is turned to the Off position,
whichever occurs first.
²Actuator Test- Each time the cluster is put
through the actuator test, the overdrive off indicator
will be turned on for the duration of the test to con-
firm the functionality of the bulb and the cluster con-
trol circuitry.
The PCM or TCM continually monitors the over-
drive off switch to determine the proper outputs to
the automatic transmission. The PCM or TCM then
sends the proper overdrive off indicator lamp-on or
lamp-off messages to the instrument cluster. If the
overdrive off indicator fails to light during the bulb
test, replace the bulb with a known good unit. For
further diagnosis of the overdrive off indicator or the
instrument cluster circuitry that controls the indica-
tor, (Refer to 8 - ELECTRICAL/INSTRUMENT
CLUSTER - DIAGNOSIS AND TESTING). For
proper diagnosis of the overdrive control system, the
PCM, the TCM, the PCI data bus, or the electronic
message inputs to the instrument cluster that control
the overdrive off indicator, a DRBIIItscan tool is
required. Refer to the appropriate diagnostic infor-
mation.
REAR FOG LAMP INDICATOR
DESCRIPTION
A rear fog lamp indicator is standard equipment on
all instrument clusters, but is only functional on
vehicles equipped with optional rear fog lamps,
which are available only in certain international
markets where they are required. The rear fog lampindicator is located on the left edge of the instrument
cluster, to the left of the tachometer. The rear fog
lamp indicator consists of an International Control
and Display Symbol icon for ªRear Fog Lightº
imprinted on an amber lens. The lens is located
behind a cutout in the opaque layer of the instru-
ment cluster overlay. The dark outer layer of the
overlay prevents the indicator from being clearly vis-
ible when it is not illuminated. The icon appears sil-
houetted against an amber field through the
translucent outer layer of the overlay when the indi-
cator is illuminated from behind by a replaceable
incandescent bulb and bulb holder unit located on
the instrument cluster electronic circuit board. When
the exterior lighting is turned On, the illumination
intensity of the rear fog lamp indicator is dimmable,
which is adjusted using the panel lamps dimmer con-
trol ring on the control stalk of the left multi-func-
tion switch. The rear fog lamp indicator lens is
serviced as a unit with the instrument cluster lens,
hood and mask unit.
OPERATION
The rear fog lamp indicator gives an indication to
the vehicle operator whenever the rear fog lamps are
illuminated. This indicator is controlled by a transis-
tor on the instrument cluster electronic circuit board
based upon cluster programming and electronic mes-
sages received by the cluster from the Body Control
Module (BCM) over the Programmable Communica-
tions Interface (PCI) data bus. The rear fog lamp
indicator bulb is completely controlled by the instru-
ment cluster logic circuit, and that logic will allow
this indicator to operate whenever the instrument
cluster receives a battery current input on the fused
B(+) circuit. Therefore, the indicator can be illumi-
nated regardless of the ignition switch position. The
bulb only illuminates when it is provided a path to
ground by the instrument cluster transistor. The
instrument cluster will turn on the rear fog lamp
indicator for the following reasons:
²Rear Fog Lamp Indicator Lamp-On Mes-
sage- Each time the cluster receives a rear fog lamp
indicator lamp-on message from the BCM indicating
that the rear fog lamps are turned On, the rear fog
lamp indicator will be illuminated. The indicator
remains illuminated until the cluster receives a rear
fog lamp indicator lamp-off message from the BCM.
²Actuator Test- Each time the cluster is put
through the actuator test, the rear fog lamp indicator
will be turned on for the duration of the test to con-
firm the functionality of the bulb and the cluster con-
trol circuitry.
The BCM continually monitors the exterior light-
ing (left multi-function) switch to determine the
proper outputs to the rear fog lamp relay. The BCM
WJINSTRUMENT CLUSTER 8J - 27
OVERDRIVE OFF INDICATOR (Continued)
Page 447 of 2199
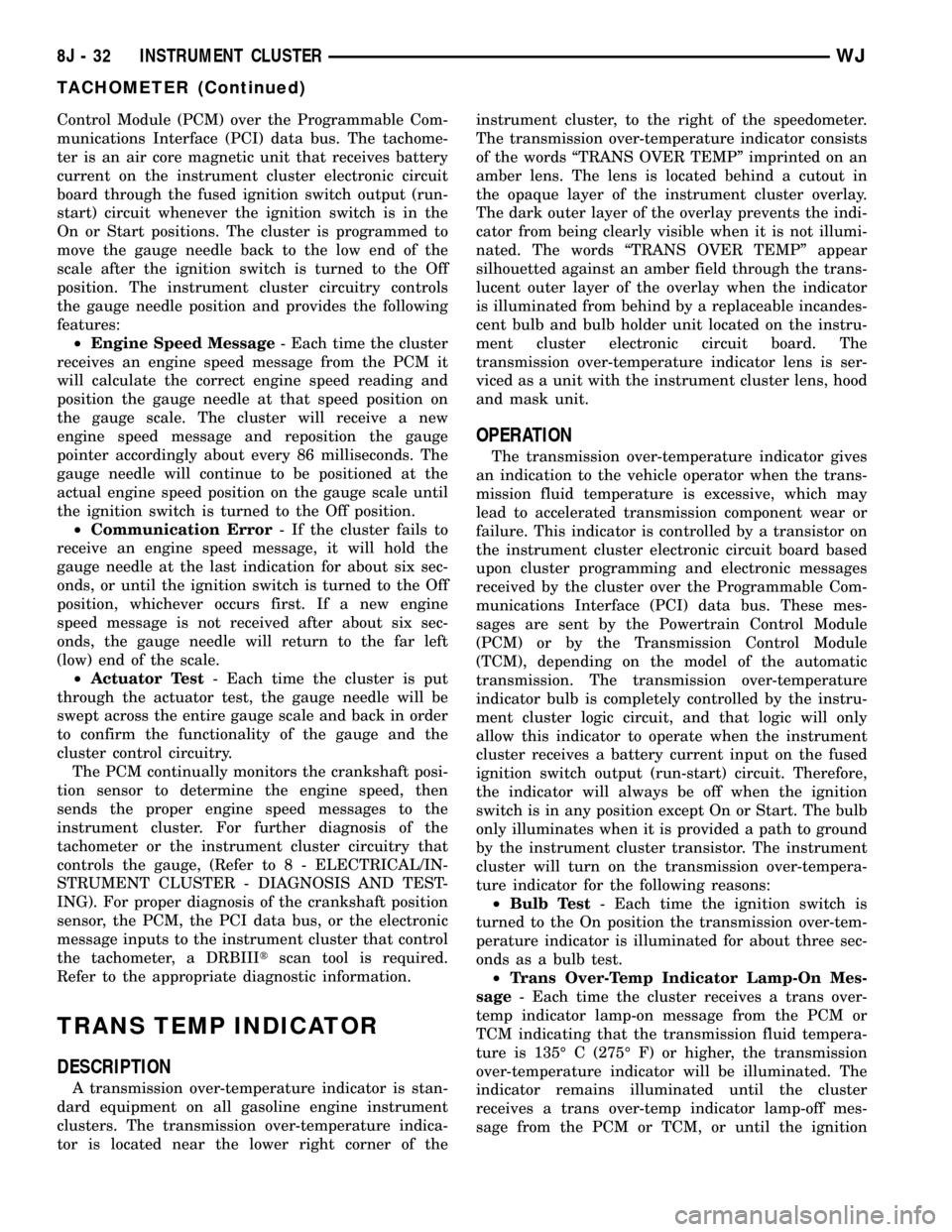
Control Module (PCM) over the Programmable Com-
munications Interface (PCI) data bus. The tachome-
ter is an air core magnetic unit that receives battery
current on the instrument cluster electronic circuit
board through the fused ignition switch output (run-
start) circuit whenever the ignition switch is in the
On or Start positions. The cluster is programmed to
move the gauge needle back to the low end of the
scale after the ignition switch is turned to the Off
position. The instrument cluster circuitry controls
the gauge needle position and provides the following
features:
²Engine Speed Message- Each time the cluster
receives an engine speed message from the PCM it
will calculate the correct engine speed reading and
position the gauge needle at that speed position on
the gauge scale. The cluster will receive a new
engine speed message and reposition the gauge
pointer accordingly about every 86 milliseconds. The
gauge needle will continue to be positioned at the
actual engine speed position on the gauge scale until
the ignition switch is turned to the Off position.
²Communication Error- If the cluster fails to
receive an engine speed message, it will hold the
gauge needle at the last indication for about six sec-
onds, or until the ignition switch is turned to the Off
position, whichever occurs first. If a new engine
speed message is not received after about six sec-
onds, the gauge needle will return to the far left
(low) end of the scale.
²Actuator Test- Each time the cluster is put
through the actuator test, the gauge needle will be
swept across the entire gauge scale and back in order
to confirm the functionality of the gauge and the
cluster control circuitry.
The PCM continually monitors the crankshaft posi-
tion sensor to determine the engine speed, then
sends the proper engine speed messages to the
instrument cluster. For further diagnosis of the
tachometer or the instrument cluster circuitry that
controls the gauge, (Refer to 8 - ELECTRICAL/IN-
STRUMENT CLUSTER - DIAGNOSIS AND TEST-
ING). For proper diagnosis of the crankshaft position
sensor, the PCM, the PCI data bus, or the electronic
message inputs to the instrument cluster that control
the tachometer, a DRBIIItscan tool is required.
Refer to the appropriate diagnostic information.
TRANS TEMP INDICATOR
DESCRIPTION
A transmission over-temperature indicator is stan-
dard equipment on all gasoline engine instrument
clusters. The transmission over-temperature indica-
tor is located near the lower right corner of theinstrument cluster, to the right of the speedometer.
The transmission over-temperature indicator consists
of the words ªTRANS OVER TEMPº imprinted on an
amber lens. The lens is located behind a cutout in
the opaque layer of the instrument cluster overlay.
The dark outer layer of the overlay prevents the indi-
cator from being clearly visible when it is not illumi-
nated. The words ªTRANS OVER TEMPº appear
silhouetted against an amber field through the trans-
lucent outer layer of the overlay when the indicator
is illuminated from behind by a replaceable incandes-
cent bulb and bulb holder unit located on the instru-
ment cluster electronic circuit board. The
transmission over-temperature indicator lens is ser-
viced as a unit with the instrument cluster lens, hood
and mask unit.
OPERATION
The transmission over-temperature indicator gives
an indication to the vehicle operator when the trans-
mission fluid temperature is excessive, which may
lead to accelerated transmission component wear or
failure. This indicator is controlled by a transistor on
the instrument cluster electronic circuit board based
upon cluster programming and electronic messages
received by the cluster over the Programmable Com-
munications Interface (PCI) data bus. These mes-
sages are sent by the Powertrain Control Module
(PCM) or by the Transmission Control Module
(TCM), depending on the model of the automatic
transmission. The transmission over-temperature
indicator bulb is completely controlled by the instru-
ment cluster logic circuit, and that logic will only
allow this indicator to operate when the instrument
cluster receives a battery current input on the fused
ignition switch output (run-start) circuit. Therefore,
the indicator will always be off when the ignition
switch is in any position except On or Start. The bulb
only illuminates when it is provided a path to ground
by the instrument cluster transistor. The instrument
cluster will turn on the transmission over-tempera-
ture indicator for the following reasons:
²Bulb Test- Each time the ignition switch is
turned to the On position the transmission over-tem-
perature indicator is illuminated for about three sec-
onds as a bulb test.
²Trans Over-Temp Indicator Lamp-On Mes-
sage- Each time the cluster receives a trans over-
temp indicator lamp-on message from the PCM or
TCM indicating that the transmission fluid tempera-
ture is 135É C (275É F) or higher, the transmission
over-temperature indicator will be illuminated. The
indicator remains illuminated until the cluster
receives a trans over-temp indicator lamp-off mes-
sage from the PCM or TCM, or until the ignition
8J - 32 INSTRUMENT CLUSTERWJ
TACHOMETER (Continued)
Page 490 of 2199
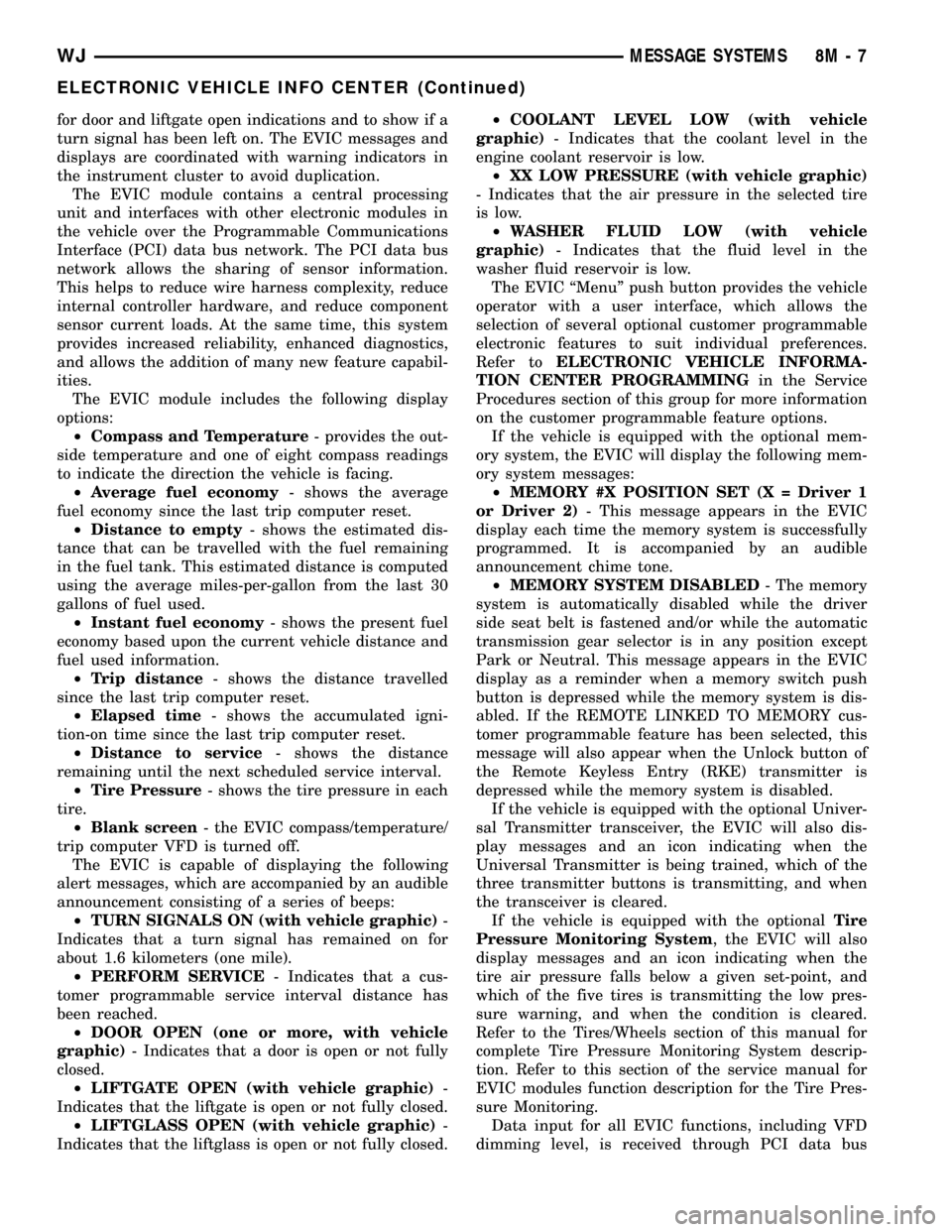
for door and liftgate open indications and to show if a
turn signal has been left on. The EVIC messages and
displays are coordinated with warning indicators in
the instrument cluster to avoid duplication.
The EVIC module contains a central processing
unit and interfaces with other electronic modules in
the vehicle over the Programmable Communications
Interface (PCI) data bus network. The PCI data bus
network allows the sharing of sensor information.
This helps to reduce wire harness complexity, reduce
internal controller hardware, and reduce component
sensor current loads. At the same time, this system
provides increased reliability, enhanced diagnostics,
and allows the addition of many new feature capabil-
ities.
The EVIC module includes the following display
options:
²Compass and Temperature- provides the out-
side temperature and one of eight compass readings
to indicate the direction the vehicle is facing.
²Average fuel economy- shows the average
fuel economy since the last trip computer reset.
²Distance to empty- shows the estimated dis-
tance that can be travelled with the fuel remaining
in the fuel tank. This estimated distance is computed
using the average miles-per-gallon from the last 30
gallons of fuel used.
²Instant fuel economy- shows the present fuel
economy based upon the current vehicle distance and
fuel used information.
²Trip distance- shows the distance travelled
since the last trip computer reset.
²Elapsed time- shows the accumulated igni-
tion-on time since the last trip computer reset.
²Distance to service- shows the distance
remaining until the next scheduled service interval.
²Tire Pressure- shows the tire pressure in each
tire.
²Blank screen- the EVIC compass/temperature/
trip computer VFD is turned off.
The EVIC is capable of displaying the following
alert messages, which are accompanied by an audible
announcement consisting of a series of beeps:
²TURN SIGNALS ON (with vehicle graphic)-
Indicates that a turn signal has remained on for
about 1.6 kilometers (one mile).
²PERFORM SERVICE- Indicates that a cus-
tomer programmable service interval distance has
been reached.
²DOOR OPEN (one or more, with vehicle
graphic)- Indicates that a door is open or not fully
closed.
²LIFTGATE OPEN (with vehicle graphic)-
Indicates that the liftgate is open or not fully closed.
²LIFTGLASS OPEN (with vehicle graphic)-
Indicates that the liftglass is open or not fully closed.²COOLANT LEVEL LOW (with vehicle
graphic)- Indicates that the coolant level in the
engine coolant reservoir is low.
²XX LOW PRESSURE (with vehicle graphic)
- Indicates that the air pressure in the selected tire
is low.
²WASHER FLUID LOW (with vehicle
graphic)- Indicates that the fluid level in the
washer fluid reservoir is low.
The EVIC ªMenuº push button provides the vehicle
operator with a user interface, which allows the
selection of several optional customer programmable
electronic features to suit individual preferences.
Refer toELECTRONIC VEHICLE INFORMA-
TION CENTER PROGRAMMINGin the Service
Procedures section of this group for more information
on the customer programmable feature options.
If the vehicle is equipped with the optional mem-
ory system, the EVIC will display the following mem-
ory system messages:
²MEMORY #X POSITION SET (X = Driver 1
or Driver 2)- This message appears in the EVIC
display each time the memory system is successfully
programmed. It is accompanied by an audible
announcement chime tone.
²MEMORY SYSTEM DISABLED- The memory
system is automatically disabled while the driver
side seat belt is fastened and/or while the automatic
transmission gear selector is in any position except
Park or Neutral. This message appears in the EVIC
display as a reminder when a memory switch push
button is depressed while the memory system is dis-
abled. If the REMOTE LINKED TO MEMORY cus-
tomer programmable feature has been selected, this
message will also appear when the Unlock button of
the Remote Keyless Entry (RKE) transmitter is
depressed while the memory system is disabled.
If the vehicle is equipped with the optional Univer-
sal Transmitter transceiver, the EVIC will also dis-
play messages and an icon indicating when the
Universal Transmitter is being trained, which of the
three transmitter buttons is transmitting, and when
the transceiver is cleared.
If the vehicle is equipped with the optionalTire
Pressure Monitoring System, the EVIC will also
display messages and an icon indicating when the
tire air pressure falls below a given set-point, and
which of the five tires is transmitting the low pres-
sure warning, and when the condition is cleared.
Refer to the Tires/Wheels section of this manual for
complete Tire Pressure Monitoring System descrip-
tion. Refer to this section of the service manual for
EVIC modules function description for the Tire Pres-
sure Monitoring.
Data input for all EVIC functions, including VFD
dimming level, is received through PCI data bus
WJMESSAGE SYSTEMS 8M - 7
ELECTRONIC VEHICLE INFO CENTER (Continued)
Page 499 of 2199
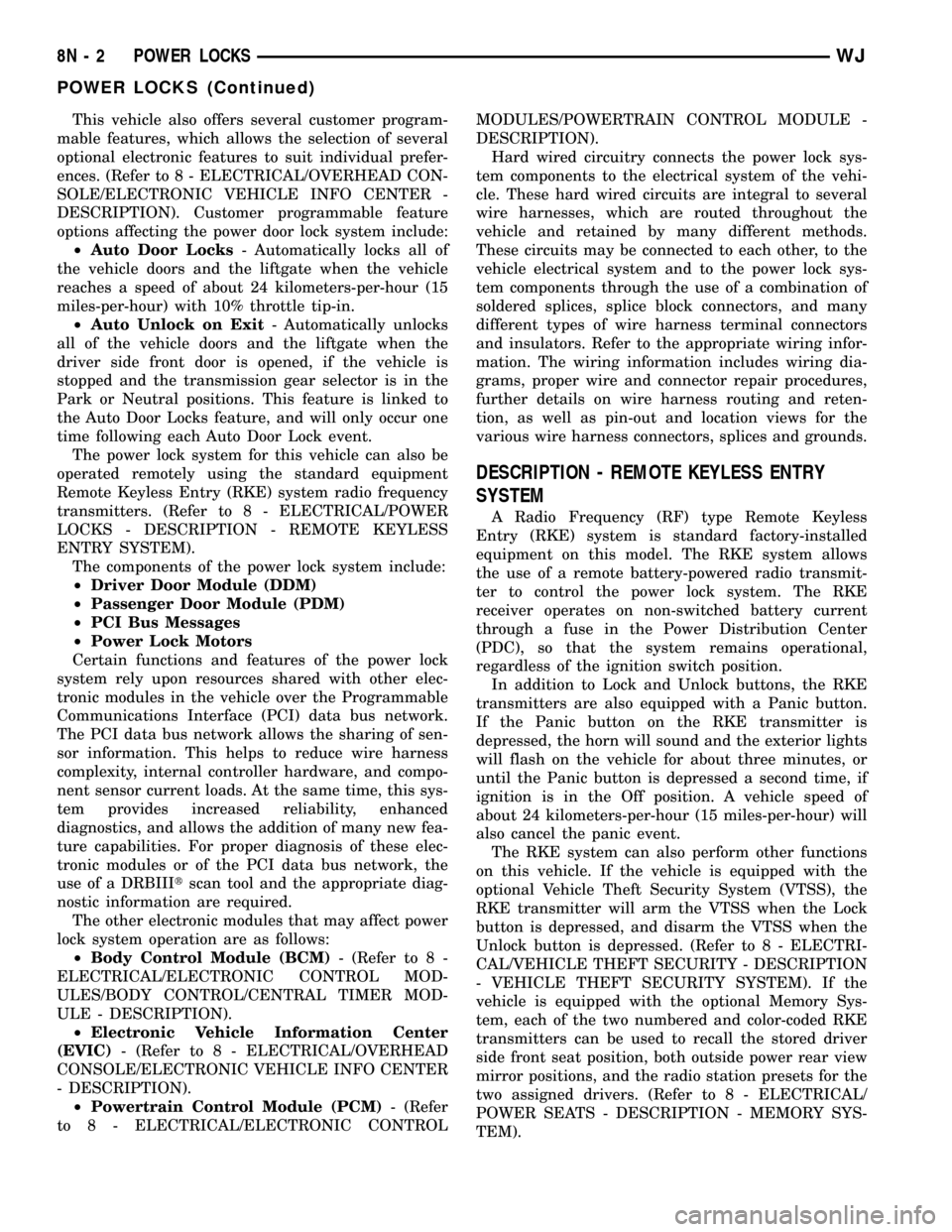
This vehicle also offers several customer program-
mable features, which allows the selection of several
optional electronic features to suit individual prefer-
ences. (Refer to 8 - ELECTRICAL/OVERHEAD CON-
SOLE/ELECTRONIC VEHICLE INFO CENTER -
DESCRIPTION). Customer programmable feature
options affecting the power door lock system include:
²Auto Door Locks- Automatically locks all of
the vehicle doors and the liftgate when the vehicle
reaches a speed of about 24 kilometers-per-hour (15
miles-per-hour) with 10% throttle tip-in.
²Auto Unlock on Exit- Automatically unlocks
all of the vehicle doors and the liftgate when the
driver side front door is opened, if the vehicle is
stopped and the transmission gear selector is in the
Park or Neutral positions. This feature is linked to
the Auto Door Locks feature, and will only occur one
time following each Auto Door Lock event.
The power lock system for this vehicle can also be
operated remotely using the standard equipment
Remote Keyless Entry (RKE) system radio frequency
transmitters. (Refer to 8 - ELECTRICAL/POWER
LOCKS - DESCRIPTION - REMOTE KEYLESS
ENTRY SYSTEM).
The components of the power lock system include:
²Driver Door Module (DDM)
²Passenger Door Module (PDM)
²PCI Bus Messages
²Power Lock Motors
Certain functions and features of the power lock
system rely upon resources shared with other elec-
tronic modules in the vehicle over the Programmable
Communications Interface (PCI) data bus network.
The PCI data bus network allows the sharing of sen-
sor information. This helps to reduce wire harness
complexity, internal controller hardware, and compo-
nent sensor current loads. At the same time, this sys-
tem provides increased reliability, enhanced
diagnostics, and allows the addition of many new fea-
ture capabilities. For proper diagnosis of these elec-
tronic modules or of the PCI data bus network, the
use of a DRBIIItscan tool and the appropriate diag-
nostic information are required.
The other electronic modules that may affect power
lock system operation are as follows:
²Body Control Module (BCM)- (Refer to 8 -
ELECTRICAL/ELECTRONIC CONTROL MOD-
ULES/BODY CONTROL/CENTRAL TIMER MOD-
ULE - DESCRIPTION).
²Electronic Vehicle Information Center
(EVIC)- (Refer to 8 - ELECTRICAL/OVERHEAD
CONSOLE/ELECTRONIC VEHICLE INFO CENTER
- DESCRIPTION).
²Powertrain Control Module (PCM)- (Refer
to 8 - ELECTRICAL/ELECTRONIC CONTROLMODULES/POWERTRAIN CONTROL MODULE -
DESCRIPTION).
Hard wired circuitry connects the power lock sys-
tem components to the electrical system of the vehi-
cle. These hard wired circuits are integral to several
wire harnesses, which are routed throughout the
vehicle and retained by many different methods.
These circuits may be connected to each other, to the
vehicle electrical system and to the power lock sys-
tem components through the use of a combination of
soldered splices, splice block connectors, and many
different types of wire harness terminal connectors
and insulators. Refer to the appropriate wiring infor-
mation. The wiring information includes wiring dia-
grams, proper wire and connector repair procedures,
further details on wire harness routing and reten-
tion, as well as pin-out and location views for the
various wire harness connectors, splices and grounds.
DESCRIPTION - REMOTE KEYLESS ENTRY
SYSTEM
A Radio Frequency (RF) type Remote Keyless
Entry (RKE) system is standard factory-installed
equipment on this model. The RKE system allows
the use of a remote battery-powered radio transmit-
ter to control the power lock system. The RKE
receiver operates on non-switched battery current
through a fuse in the Power Distribution Center
(PDC), so that the system remains operational,
regardless of the ignition switch position.
In addition to Lock and Unlock buttons, the RKE
transmitters are also equipped with a Panic button.
If the Panic button on the RKE transmitter is
depressed, the horn will sound and the exterior lights
will flash on the vehicle for about three minutes, or
until the Panic button is depressed a second time, if
ignition is in the Off position. A vehicle speed of
about 24 kilometers-per-hour (15 miles-per-hour) will
also cancel the panic event.
The RKE system can also perform other functions
on this vehicle. If the vehicle is equipped with the
optional Vehicle Theft Security System (VTSS), the
RKE transmitter will arm the VTSS when the Lock
button is depressed, and disarm the VTSS when the
Unlock button is depressed. (Refer to 8 - ELECTRI-
CAL/VEHICLE THEFT SECURITY - DESCRIPTION
- VEHICLE THEFT SECURITY SYSTEM). If the
vehicle is equipped with the optional Memory Sys-
tem, each of the two numbered and color-coded RKE
transmitters can be used to recall the stored driver
side front seat position, both outside power rear view
mirror positions, and the radio station presets for the
two assigned drivers. (Refer to 8 - ELECTRICAL/
POWER SEATS - DESCRIPTION - MEMORY SYS-
TEM).
8N - 2 POWER LOCKSWJ
POWER LOCKS (Continued)
Page 501 of 2199
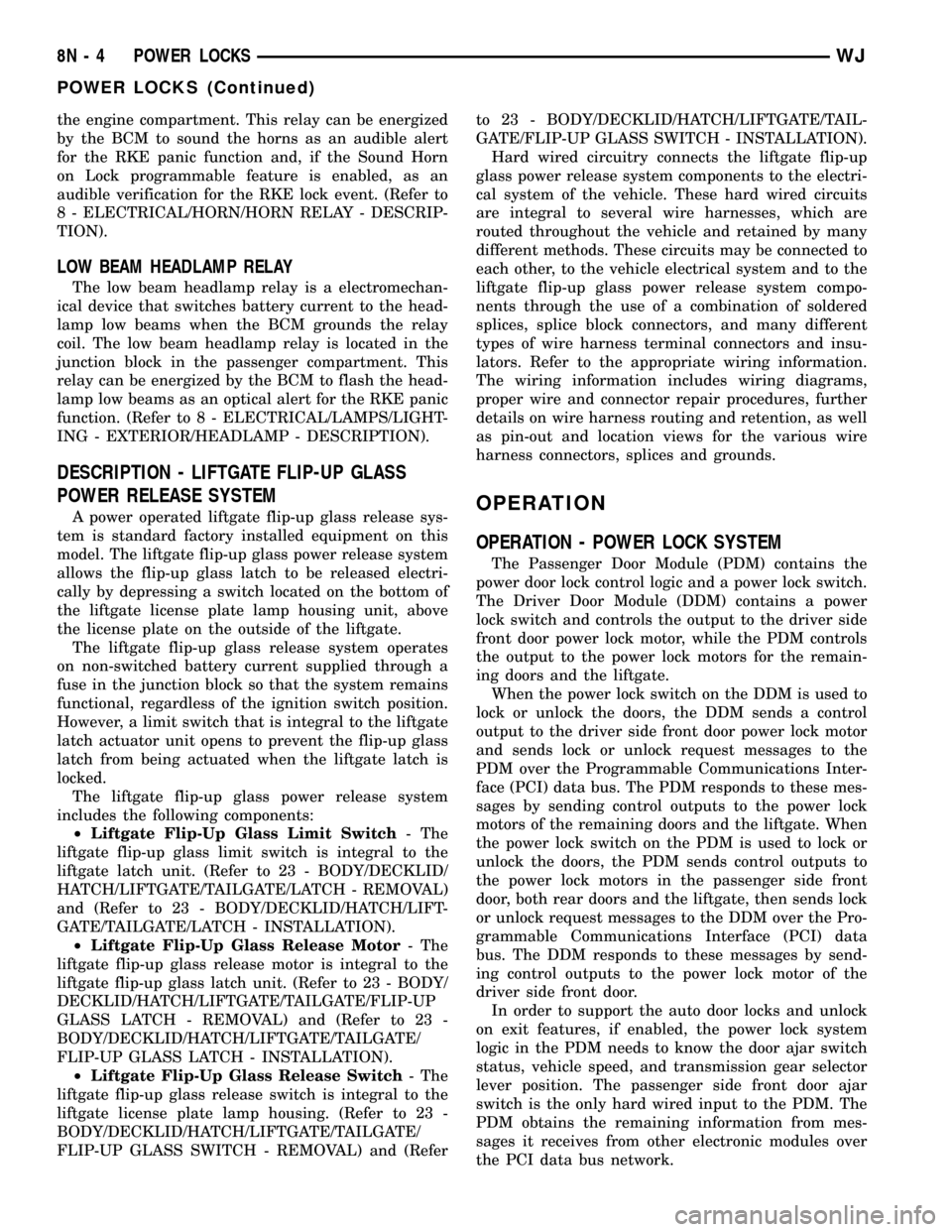
the engine compartment. This relay can be energized
by the BCM to sound the horns as an audible alert
for the RKE panic function and, if the Sound Horn
on Lock programmable feature is enabled, as an
audible verification for the RKE lock event. (Refer to
8 - ELECTRICAL/HORN/HORN RELAY - DESCRIP-
TION).
LOW BEAM HEADLAMP RELAY
The low beam headlamp relay is a electromechan-
ical device that switches battery current to the head-
lamp low beams when the BCM grounds the relay
coil. The low beam headlamp relay is located in the
junction block in the passenger compartment. This
relay can be energized by the BCM to flash the head-
lamp low beams as an optical alert for the RKE panic
function. (Refer to 8 - ELECTRICAL/LAMPS/LIGHT-
ING - EXTERIOR/HEADLAMP - DESCRIPTION).
DESCRIPTION - LIFTGATE FLIP-UP GLASS
POWER RELEASE SYSTEM
A power operated liftgate flip-up glass release sys-
tem is standard factory installed equipment on this
model. The liftgate flip-up glass power release system
allows the flip-up glass latch to be released electri-
cally by depressing a switch located on the bottom of
the liftgate license plate lamp housing unit, above
the license plate on the outside of the liftgate.
The liftgate flip-up glass release system operates
on non-switched battery current supplied through a
fuse in the junction block so that the system remains
functional, regardless of the ignition switch position.
However, a limit switch that is integral to the liftgate
latch actuator unit opens to prevent the flip-up glass
latch from being actuated when the liftgate latch is
locked.
The liftgate flip-up glass power release system
includes the following components:
²Liftgate Flip-Up Glass Limit Switch- The
liftgate flip-up glass limit switch is integral to the
liftgate latch unit. (Refer to 23 - BODY/DECKLID/
HATCH/LIFTGATE/TAILGATE/LATCH - REMOVAL)
and (Refer to 23 - BODY/DECKLID/HATCH/LIFT-
GATE/TAILGATE/LATCH - INSTALLATION).
²Liftgate Flip-Up Glass Release Motor- The
liftgate flip-up glass release motor is integral to the
liftgate flip-up glass latch unit. (Refer to 23 - BODY/
DECKLID/HATCH/LIFTGATE/TAILGATE/FLIP-UP
GLASS LATCH - REMOVAL) and (Refer to 23 -
BODY/DECKLID/HATCH/LIFTGATE/TAILGATE/
FLIP-UP GLASS LATCH - INSTALLATION).
²Liftgate Flip-Up Glass Release Switch- The
liftgate flip-up glass release switch is integral to the
liftgate license plate lamp housing. (Refer to 23 -
BODY/DECKLID/HATCH/LIFTGATE/TAILGATE/
FLIP-UP GLASS SWITCH - REMOVAL) and (Referto 23 - BODY/DECKLID/HATCH/LIFTGATE/TAIL-
GATE/FLIP-UP GLASS SWITCH - INSTALLATION).
Hard wired circuitry connects the liftgate flip-up
glass power release system components to the electri-
cal system of the vehicle. These hard wired circuits
are integral to several wire harnesses, which are
routed throughout the vehicle and retained by many
different methods. These circuits may be connected to
each other, to the vehicle electrical system and to the
liftgate flip-up glass power release system compo-
nents through the use of a combination of soldered
splices, splice block connectors, and many different
types of wire harness terminal connectors and insu-
lators. Refer to the appropriate wiring information.
The wiring information includes wiring diagrams,
proper wire and connector repair procedures, further
details on wire harness routing and retention, as well
as pin-out and location views for the various wire
harness connectors, splices and grounds.OPERATION
OPERATION - POWER LOCK SYSTEM
The Passenger Door Module (PDM) contains the
power door lock control logic and a power lock switch.
The Driver Door Module (DDM) contains a power
lock switch and controls the output to the driver side
front door power lock motor, while the PDM controls
the output to the power lock motors for the remain-
ing doors and the liftgate.
When the power lock switch on the DDM is used to
lock or unlock the doors, the DDM sends a control
output to the driver side front door power lock motor
and sends lock or unlock request messages to the
PDM over the Programmable Communications Inter-
face (PCI) data bus. The PDM responds to these mes-
sages by sending control outputs to the power lock
motors of the remaining doors and the liftgate. When
the power lock switch on the PDM is used to lock or
unlock the doors, the PDM sends control outputs to
the power lock motors in the passenger side front
door, both rear doors and the liftgate, then sends lock
or unlock request messages to the DDM over the Pro-
grammable Communications Interface (PCI) data
bus. The DDM responds to these messages by send-
ing control outputs to the power lock motor of the
driver side front door.
In order to support the auto door locks and unlock
on exit features, if enabled, the power lock system
logic in the PDM needs to know the door ajar switch
status, vehicle speed, and transmission gear selector
lever position. The passenger side front door ajar
switch is the only hard wired input to the PDM. The
PDM obtains the remaining information from mes-
sages it receives from other electronic modules over
the PCI data bus network.
8N - 4 POWER LOCKSWJ
POWER LOCKS (Continued)
Page 540 of 2199
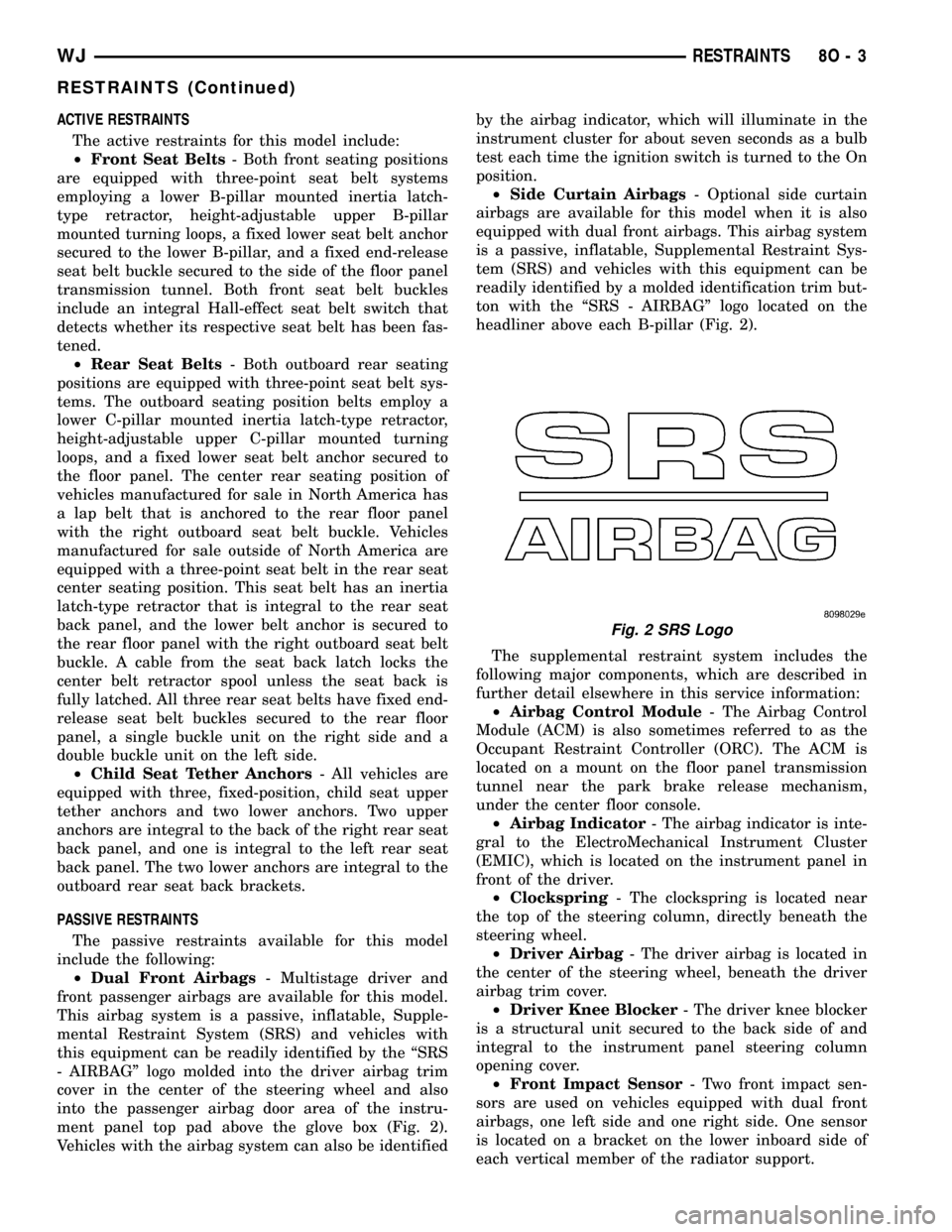
ACTIVE RESTRAINTS
The active restraints for this model include:
²Front Seat Belts- Both front seating positions
are equipped with three-point seat belt systems
employing a lower B-pillar mounted inertia latch-
type retractor, height-adjustable upper B-pillar
mounted turning loops, a fixed lower seat belt anchor
secured to the lower B-pillar, and a fixed end-release
seat belt buckle secured to the side of the floor panel
transmission tunnel. Both front seat belt buckles
include an integral Hall-effect seat belt switch that
detects whether its respective seat belt has been fas-
tened.
²Rear Seat Belts- Both outboard rear seating
positions are equipped with three-point seat belt sys-
tems. The outboard seating position belts employ a
lower C-pillar mounted inertia latch-type retractor,
height-adjustable upper C-pillar mounted turning
loops, and a fixed lower seat belt anchor secured to
the floor panel. The center rear seating position of
vehicles manufactured for sale in North America has
a lap belt that is anchored to the rear floor panel
with the right outboard seat belt buckle. Vehicles
manufactured for sale outside of North America are
equipped with a three-point seat belt in the rear seat
center seating position. This seat belt has an inertia
latch-type retractor that is integral to the rear seat
back panel, and the lower belt anchor is secured to
the rear floor panel with the right outboard seat belt
buckle. A cable from the seat back latch locks the
center belt retractor spool unless the seat back is
fully latched. All three rear seat belts have fixed end-
release seat belt buckles secured to the rear floor
panel, a single buckle unit on the right side and a
double buckle unit on the left side.
²Child Seat Tether Anchors- All vehicles are
equipped with three, fixed-position, child seat upper
tether anchors and two lower anchors. Two upper
anchors are integral to the back of the right rear seat
back panel, and one is integral to the left rear seat
back panel. The two lower anchors are integral to the
outboard rear seat back brackets.
PASSIVE RESTRAINTS
The passive restraints available for this model
include the following:
²Dual Front Airbags- Multistage driver and
front passenger airbags are available for this model.
This airbag system is a passive, inflatable, Supple-
mental Restraint System (SRS) and vehicles with
this equipment can be readily identified by the ªSRS
- AIRBAGº logo molded into the driver airbag trim
cover in the center of the steering wheel and also
into the passenger airbag door area of the instru-
ment panel top pad above the glove box (Fig. 2).
Vehicles with the airbag system can also be identifiedby the airbag indicator, which will illuminate in the
instrument cluster for about seven seconds as a bulb
test each time the ignition switch is turned to the On
position.
²Side Curtain Airbags- Optional side curtain
airbags are available for this model when it is also
equipped with dual front airbags. This airbag system
is a passive, inflatable, Supplemental Restraint Sys-
tem (SRS) and vehicles with this equipment can be
readily identified by a molded identification trim but-
ton with the ªSRS - AIRBAGº logo located on the
headliner above each B-pillar (Fig. 2).
The supplemental restraint system includes the
following major components, which are described in
further detail elsewhere in this service information:
²Airbag Control Module- The Airbag Control
Module (ACM) is also sometimes referred to as the
Occupant Restraint Controller (ORC). The ACM is
located on a mount on the floor panel transmission
tunnel near the park brake release mechanism,
under the center floor console.
²Airbag Indicator- The airbag indicator is inte-
gral to the ElectroMechanical Instrument Cluster
(EMIC), which is located on the instrument panel in
front of the driver.
²Clockspring- The clockspring is located near
the top of the steering column, directly beneath the
steering wheel.
²Driver Airbag- The driver airbag is located in
the center of the steering wheel, beneath the driver
airbag trim cover.
²Driver Knee Blocker- The driver knee blocker
is a structural unit secured to the back side of and
integral to the instrument panel steering column
opening cover.
²Front Impact Sensor- Two front impact sen-
sors are used on vehicles equipped with dual front
airbags, one left side and one right side. One sensor
is located on a bracket on the lower inboard side of
each vertical member of the radiator support.
Fig. 2 SRS Logo
WJRESTRAINTS 8O - 3
RESTRAINTS (Continued)
Page 546 of 2199
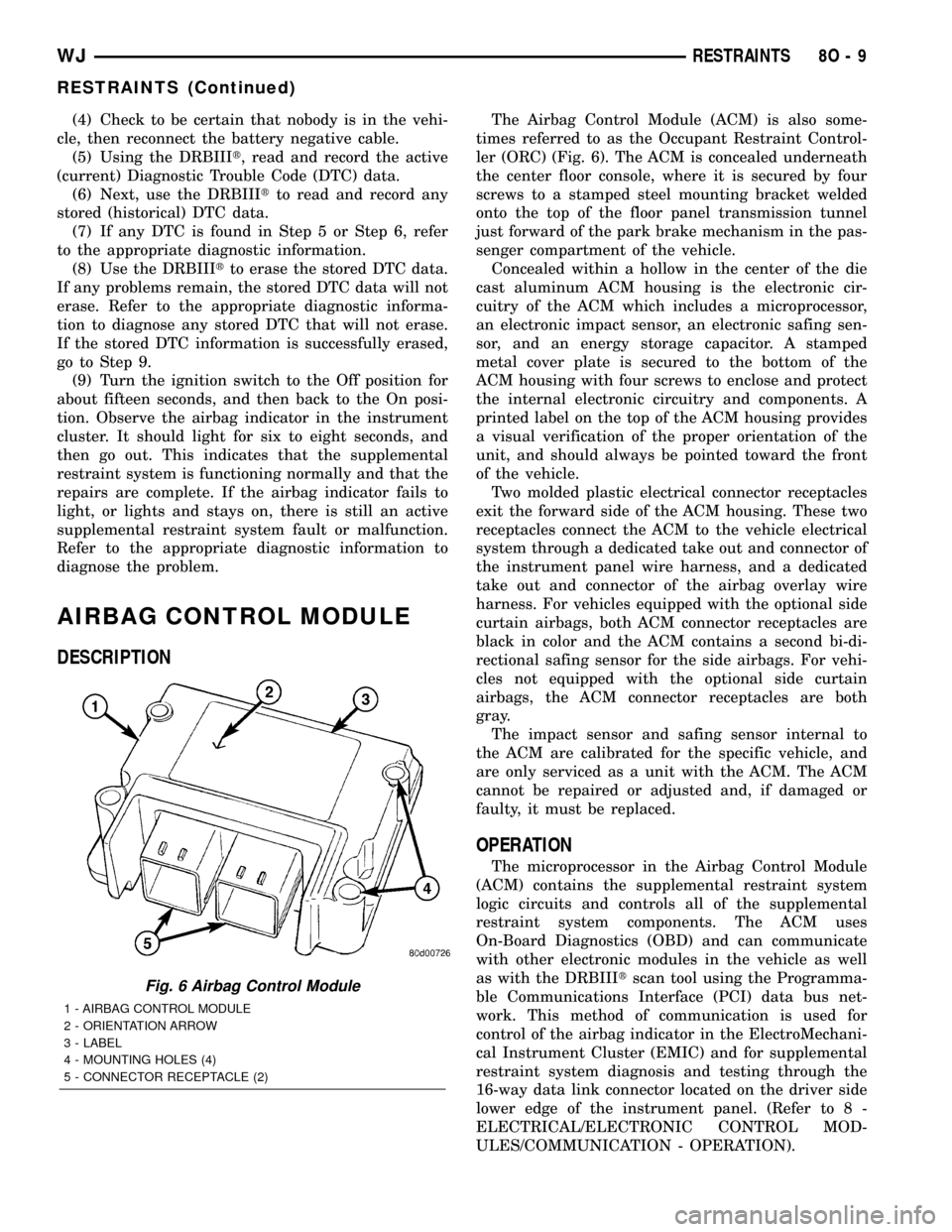
(4) Check to be certain that nobody is in the vehi-
cle, then reconnect the battery negative cable.
(5) Using the DRBIIIt, read and record the active
(current) Diagnostic Trouble Code (DTC) data.
(6) Next, use the DRBIIItto read and record any
stored (historical) DTC data.
(7) If any DTC is found in Step 5 or Step 6, refer
to the appropriate diagnostic information.
(8) Use the DRBIIItto erase the stored DTC data.
If any problems remain, the stored DTC data will not
erase. Refer to the appropriate diagnostic informa-
tion to diagnose any stored DTC that will not erase.
If the stored DTC information is successfully erased,
go to Step 9.
(9) Turn the ignition switch to the Off position for
about fifteen seconds, and then back to the On posi-
tion. Observe the airbag indicator in the instrument
cluster. It should light for six to eight seconds, and
then go out. This indicates that the supplemental
restraint system is functioning normally and that the
repairs are complete. If the airbag indicator fails to
light, or lights and stays on, there is still an active
supplemental restraint system fault or malfunction.
Refer to the appropriate diagnostic information to
diagnose the problem.
AIRBAG CONTROL MODULE
DESCRIPTION
The Airbag Control Module (ACM) is also some-
times referred to as the Occupant Restraint Control-
ler (ORC) (Fig. 6). The ACM is concealed underneath
the center floor console, where it is secured by four
screws to a stamped steel mounting bracket welded
onto the top of the floor panel transmission tunnel
just forward of the park brake mechanism in the pas-
senger compartment of the vehicle.
Concealed within a hollow in the center of the die
cast aluminum ACM housing is the electronic cir-
cuitry of the ACM which includes a microprocessor,
an electronic impact sensor, an electronic safing sen-
sor, and an energy storage capacitor. A stamped
metal cover plate is secured to the bottom of the
ACM housing with four screws to enclose and protect
the internal electronic circuitry and components. A
printed label on the top of the ACM housing provides
a visual verification of the proper orientation of the
unit, and should always be pointed toward the front
of the vehicle.
Two molded plastic electrical connector receptacles
exit the forward side of the ACM housing. These two
receptacles connect the ACM to the vehicle electrical
system through a dedicated take out and connector of
the instrument panel wire harness, and a dedicated
take out and connector of the airbag overlay wire
harness. For vehicles equipped with the optional side
curtain airbags, both ACM connector receptacles are
black in color and the ACM contains a second bi-di-
rectional safing sensor for the side airbags. For vehi-
cles not equipped with the optional side curtain
airbags, the ACM connector receptacles are both
gray.
The impact sensor and safing sensor internal to
the ACM are calibrated for the specific vehicle, and
are only serviced as a unit with the ACM. The ACM
cannot be repaired or adjusted and, if damaged or
faulty, it must be replaced.
OPERATION
The microprocessor in the Airbag Control Module
(ACM) contains the supplemental restraint system
logic circuits and controls all of the supplemental
restraint system components. The ACM uses
On-Board Diagnostics (OBD) and can communicate
with other electronic modules in the vehicle as well
as with the DRBIIItscan tool using the Programma-
ble Communications Interface (PCI) data bus net-
work. This method of communication is used for
control of the airbag indicator in the ElectroMechani-
cal Instrument Cluster (EMIC) and for supplemental
restraint system diagnosis and testing through the
16-way data link connector located on the driver side
lower edge of the instrument panel. (Refer to 8 -
ELECTRICAL/ELECTRONIC CONTROL MOD-
ULES/COMMUNICATION - OPERATION).
Fig. 6 Airbag Control Module
1 - AIRBAG CONTROL MODULE
2 - ORIENTATION ARROW
3 - LABEL
4 - MOUNTING HOLES (4)
5 - CONNECTOR RECEPTACLE (2)
WJRESTRAINTS 8O - 9
RESTRAINTS (Continued)
Page 547 of 2199
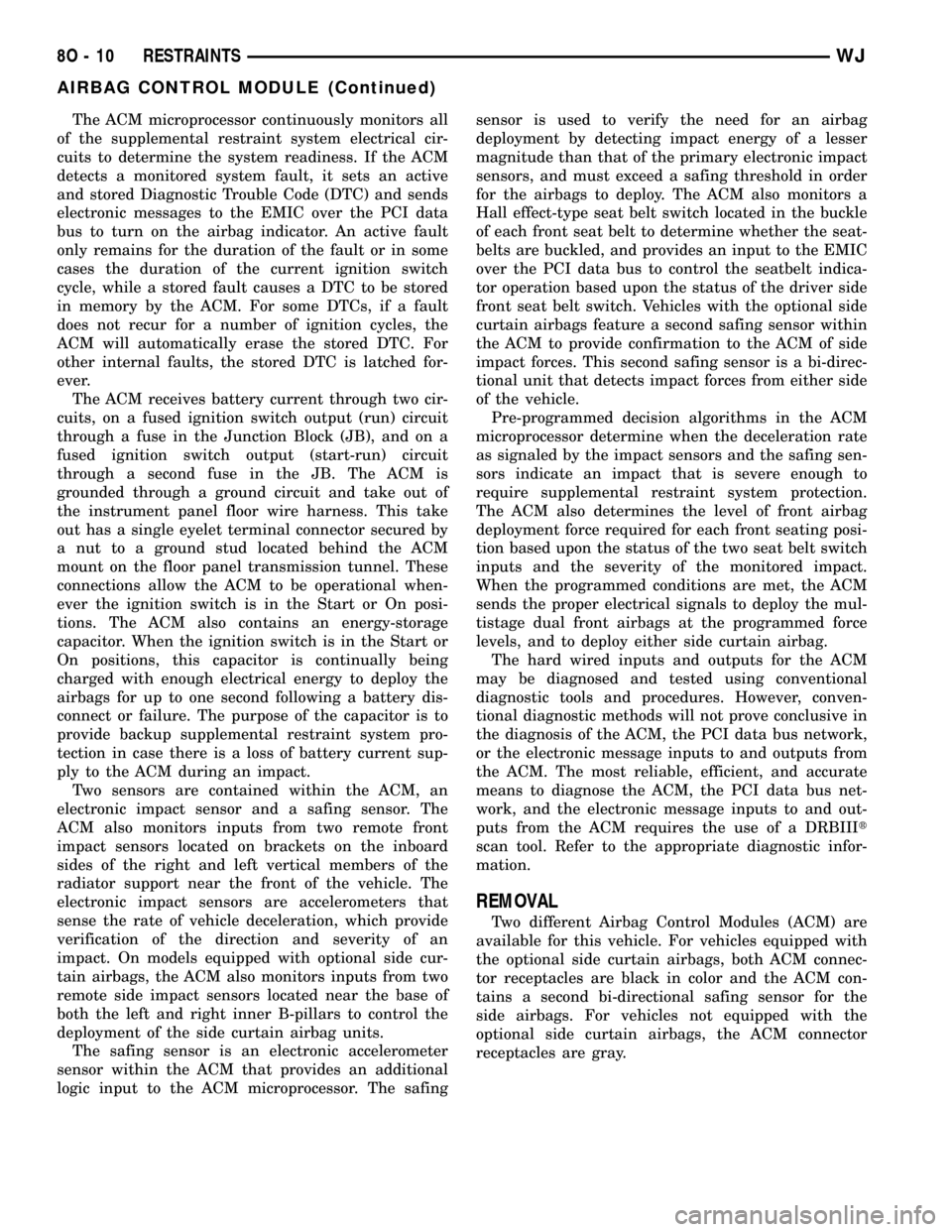
The ACM microprocessor continuously monitors all
of the supplemental restraint system electrical cir-
cuits to determine the system readiness. If the ACM
detects a monitored system fault, it sets an active
and stored Diagnostic Trouble Code (DTC) and sends
electronic messages to the EMIC over the PCI data
bus to turn on the airbag indicator. An active fault
only remains for the duration of the fault or in some
cases the duration of the current ignition switch
cycle, while a stored fault causes a DTC to be stored
in memory by the ACM. For some DTCs, if a fault
does not recur for a number of ignition cycles, the
ACM will automatically erase the stored DTC. For
other internal faults, the stored DTC is latched for-
ever.
The ACM receives battery current through two cir-
cuits, on a fused ignition switch output (run) circuit
through a fuse in the Junction Block (JB), and on a
fused ignition switch output (start-run) circuit
through a second fuse in the JB. The ACM is
grounded through a ground circuit and take out of
the instrument panel floor wire harness. This take
out has a single eyelet terminal connector secured by
a nut to a ground stud located behind the ACM
mount on the floor panel transmission tunnel. These
connections allow the ACM to be operational when-
ever the ignition switch is in the Start or On posi-
tions. The ACM also contains an energy-storage
capacitor. When the ignition switch is in the Start or
On positions, this capacitor is continually being
charged with enough electrical energy to deploy the
airbags for up to one second following a battery dis-
connect or failure. The purpose of the capacitor is to
provide backup supplemental restraint system pro-
tection in case there is a loss of battery current sup-
ply to the ACM during an impact.
Two sensors are contained within the ACM, an
electronic impact sensor and a safing sensor. The
ACM also monitors inputs from two remote front
impact sensors located on brackets on the inboard
sides of the right and left vertical members of the
radiator support near the front of the vehicle. The
electronic impact sensors are accelerometers that
sense the rate of vehicle deceleration, which provide
verification of the direction and severity of an
impact. On models equipped with optional side cur-
tain airbags, the ACM also monitors inputs from two
remote side impact sensors located near the base of
both the left and right inner B-pillars to control the
deployment of the side curtain airbag units.
The safing sensor is an electronic accelerometer
sensor within the ACM that provides an additional
logic input to the ACM microprocessor. The safingsensor is used to verify the need for an airbag
deployment by detecting impact energy of a lesser
magnitude than that of the primary electronic impact
sensors, and must exceed a safing threshold in order
for the airbags to deploy. The ACM also monitors a
Hall effect-type seat belt switch located in the buckle
of each front seat belt to determine whether the seat-
belts are buckled, and provides an input to the EMIC
over the PCI data bus to control the seatbelt indica-
tor operation based upon the status of the driver side
front seat belt switch. Vehicles with the optional side
curtain airbags feature a second safing sensor within
the ACM to provide confirmation to the ACM of side
impact forces. This second safing sensor is a bi-direc-
tional unit that detects impact forces from either side
of the vehicle.
Pre-programmed decision algorithms in the ACM
microprocessor determine when the deceleration rate
as signaled by the impact sensors and the safing sen-
sors indicate an impact that is severe enough to
require supplemental restraint system protection.
The ACM also determines the level of front airbag
deployment force required for each front seating posi-
tion based upon the status of the two seat belt switch
inputs and the severity of the monitored impact.
When the programmed conditions are met, the ACM
sends the proper electrical signals to deploy the mul-
tistage dual front airbags at the programmed force
levels, and to deploy either side curtain airbag.
The hard wired inputs and outputs for the ACM
may be diagnosed and tested using conventional
diagnostic tools and procedures. However, conven-
tional diagnostic methods will not prove conclusive in
the diagnosis of the ACM, the PCI data bus network,
or the electronic message inputs to and outputs from
the ACM. The most reliable, efficient, and accurate
means to diagnose the ACM, the PCI data bus net-
work, and the electronic message inputs to and out-
puts from the ACM requires the use of a DRBIIIt
scan tool. Refer to the appropriate diagnostic infor-
mation.
REMOVAL
Two different Airbag Control Modules (ACM) are
available for this vehicle. For vehicles equipped with
the optional side curtain airbags, both ACM connec-
tor receptacles are black in color and the ACM con-
tains a second bi-directional safing sensor for the
side airbags. For vehicles not equipped with the
optional side curtain airbags, the ACM connector
receptacles are gray.
8O - 10 RESTRAINTSWJ
AIRBAG CONTROL MODULE (Continued)
Page 548 of 2199
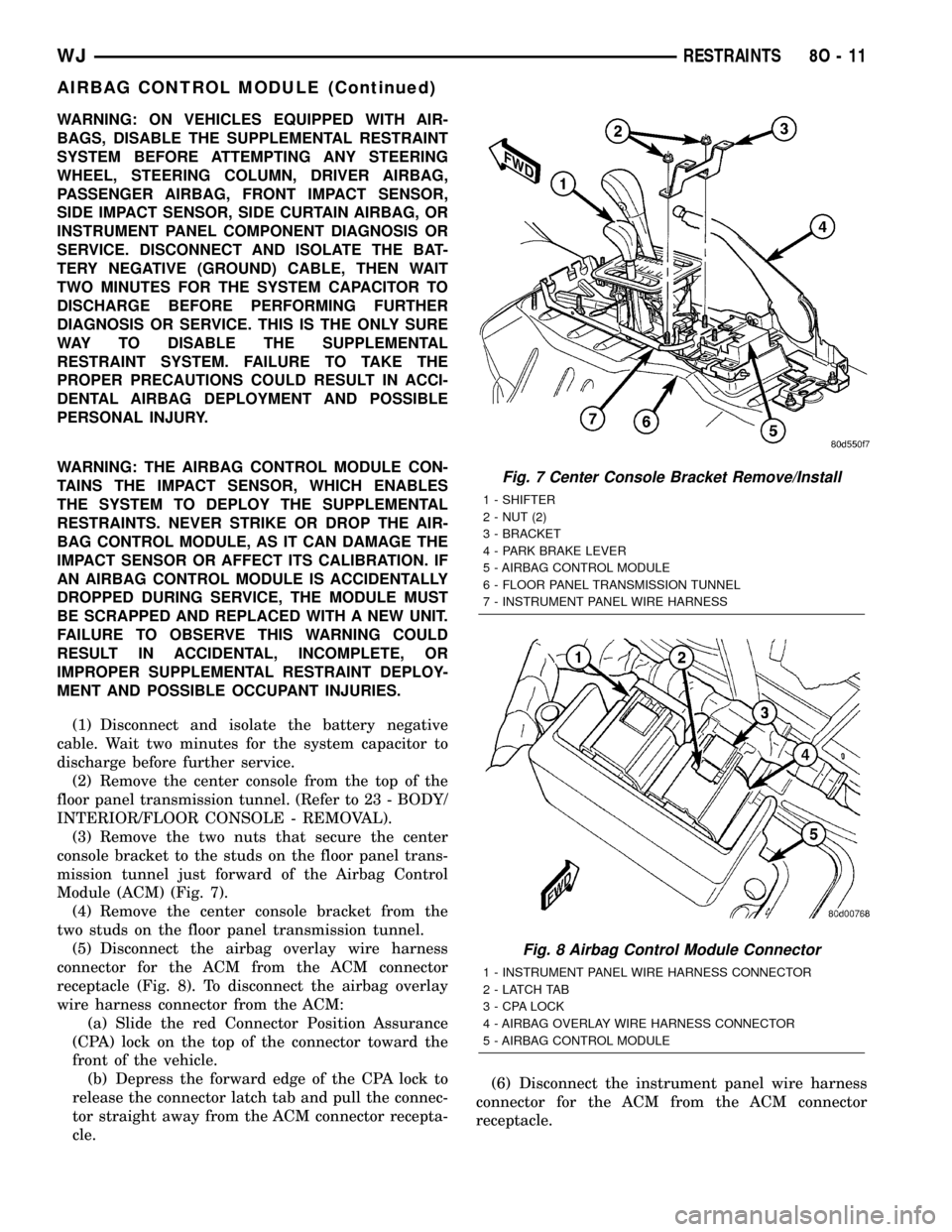
WARNING: ON VEHICLES EQUIPPED WITH AIR-
BAGS, DISABLE THE SUPPLEMENTAL RESTRAINT
SYSTEM BEFORE ATTEMPTING ANY STEERING
WHEEL, STEERING COLUMN, DRIVER AIRBAG,
PASSENGER AIRBAG, FRONT IMPACT SENSOR,
SIDE IMPACT SENSOR, SIDE CURTAIN AIRBAG, OR
INSTRUMENT PANEL COMPONENT DIAGNOSIS OR
SERVICE. DISCONNECT AND ISOLATE THE BAT-
TERY NEGATIVE (GROUND) CABLE, THEN WAIT
TWO MINUTES FOR THE SYSTEM CAPACITOR TO
DISCHARGE BEFORE PERFORMING FURTHER
DIAGNOSIS OR SERVICE. THIS IS THE ONLY SURE
WAY TO DISABLE THE SUPPLEMENTAL
RESTRAINT SYSTEM. FAILURE TO TAKE THE
PROPER PRECAUTIONS COULD RESULT IN ACCI-
DENTAL AIRBAG DEPLOYMENT AND POSSIBLE
PERSONAL INJURY.
WARNING: THE AIRBAG CONTROL MODULE CON-
TAINS THE IMPACT SENSOR, WHICH ENABLES
THE SYSTEM TO DEPLOY THE SUPPLEMENTAL
RESTRAINTS. NEVER STRIKE OR DROP THE AIR-
BAG CONTROL MODULE, AS IT CAN DAMAGE THE
IMPACT SENSOR OR AFFECT ITS CALIBRATION. IF
AN AIRBAG CONTROL MODULE IS ACCIDENTALLY
DROPPED DURING SERVICE, THE MODULE MUST
BE SCRAPPED AND REPLACED WITH A NEW UNIT.
FAILURE TO OBSERVE THIS WARNING COULD
RESULT IN ACCIDENTAL, INCOMPLETE, OR
IMPROPER SUPPLEMENTAL RESTRAINT DEPLOY-
MENT AND POSSIBLE OCCUPANT INJURIES.
(1) Disconnect and isolate the battery negative
cable. Wait two minutes for the system capacitor to
discharge before further service.
(2) Remove the center console from the top of the
floor panel transmission tunnel. (Refer to 23 - BODY/
INTERIOR/FLOOR CONSOLE - REMOVAL).
(3) Remove the two nuts that secure the center
console bracket to the studs on the floor panel trans-
mission tunnel just forward of the Airbag Control
Module (ACM) (Fig. 7).
(4) Remove the center console bracket from the
two studs on the floor panel transmission tunnel.
(5) Disconnect the airbag overlay wire harness
connector for the ACM from the ACM connector
receptacle (Fig. 8). To disconnect the airbag overlay
wire harness connector from the ACM:
(a) Slide the red Connector Position Assurance
(CPA) lock on the top of the connector toward the
front of the vehicle.
(b) Depress the forward edge of the CPA lock to
release the connector latch tab and pull the connec-
tor straight away from the ACM connector recepta-
cle.(6) Disconnect the instrument panel wire harness
connector for the ACM from the ACM connector
receptacle.
Fig. 7 Center Console Bracket Remove/Install
1 - SHIFTER
2 - NUT (2)
3 - BRACKET
4 - PARK BRAKE LEVER
5 - AIRBAG CONTROL MODULE
6 - FLOOR PANEL TRANSMISSION TUNNEL
7 - INSTRUMENT PANEL WIRE HARNESS
Fig. 8 Airbag Control Module Connector
1 - INSTRUMENT PANEL WIRE HARNESS CONNECTOR
2 - LATCH TAB
3 - CPA LOCK
4 - AIRBAG OVERLAY WIRE HARNESS CONNECTOR
5 - AIRBAG CONTROL MODULE
WJRESTRAINTS 8O - 11
AIRBAG CONTROL MODULE (Continued)
Page 549 of 2199
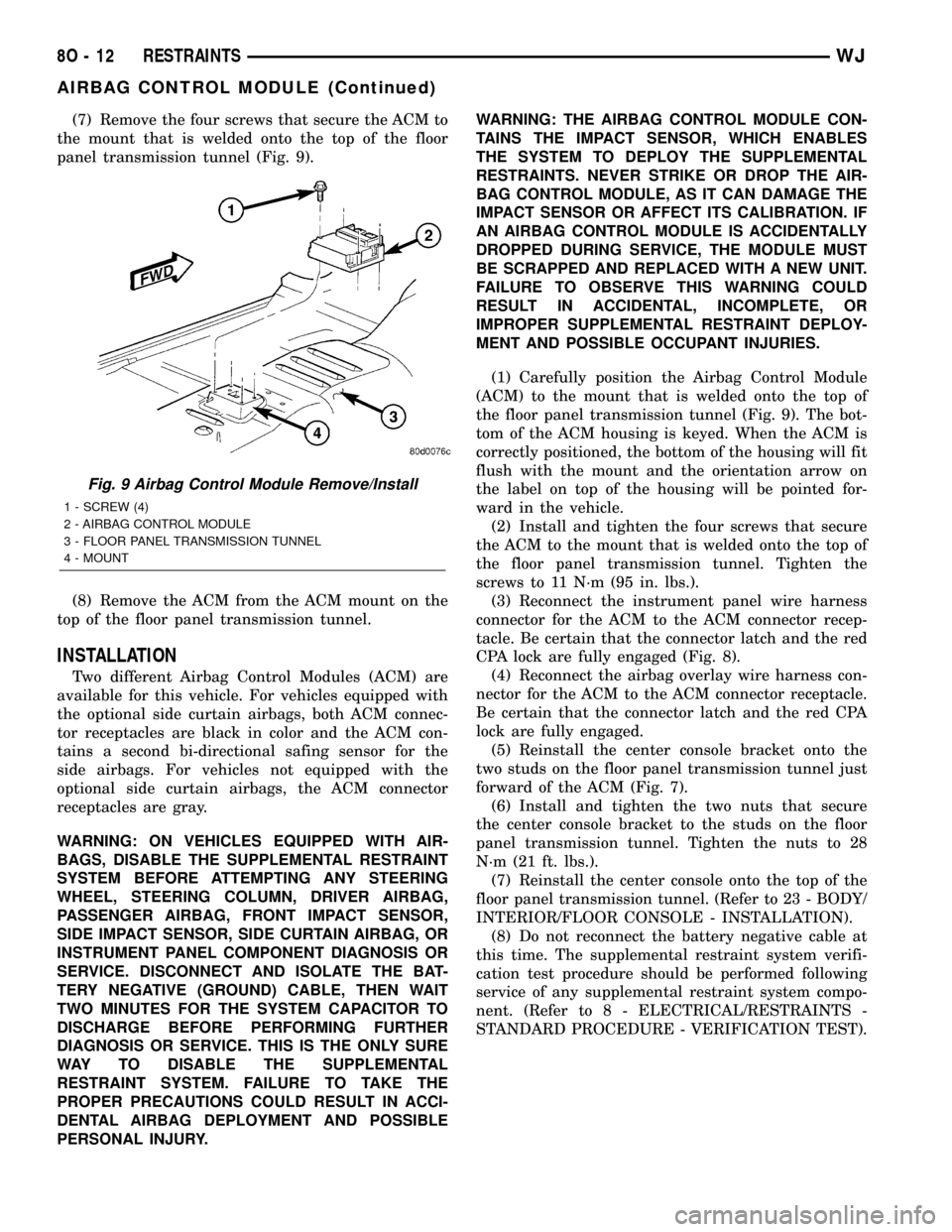
(7) Remove the four screws that secure the ACM to
the mount that is welded onto the top of the floor
panel transmission tunnel (Fig. 9).
(8) Remove the ACM from the ACM mount on the
top of the floor panel transmission tunnel.
INSTALLATION
Two different Airbag Control Modules (ACM) are
available for this vehicle. For vehicles equipped with
the optional side curtain airbags, both ACM connec-
tor receptacles are black in color and the ACM con-
tains a second bi-directional safing sensor for the
side airbags. For vehicles not equipped with the
optional side curtain airbags, the ACM connector
receptacles are gray.
WARNING: ON VEHICLES EQUIPPED WITH AIR-
BAGS, DISABLE THE SUPPLEMENTAL RESTRAINT
SYSTEM BEFORE ATTEMPTING ANY STEERING
WHEEL, STEERING COLUMN, DRIVER AIRBAG,
PASSENGER AIRBAG, FRONT IMPACT SENSOR,
SIDE IMPACT SENSOR, SIDE CURTAIN AIRBAG, OR
INSTRUMENT PANEL COMPONENT DIAGNOSIS OR
SERVICE. DISCONNECT AND ISOLATE THE BAT-
TERY NEGATIVE (GROUND) CABLE, THEN WAIT
TWO MINUTES FOR THE SYSTEM CAPACITOR TO
DISCHARGE BEFORE PERFORMING FURTHER
DIAGNOSIS OR SERVICE. THIS IS THE ONLY SURE
WAY TO DISABLE THE SUPPLEMENTAL
RESTRAINT SYSTEM. FAILURE TO TAKE THE
PROPER PRECAUTIONS COULD RESULT IN ACCI-
DENTAL AIRBAG DEPLOYMENT AND POSSIBLE
PERSONAL INJURY.WARNING: THE AIRBAG CONTROL MODULE CON-
TAINS THE IMPACT SENSOR, WHICH ENABLES
THE SYSTEM TO DEPLOY THE SUPPLEMENTAL
RESTRAINTS. NEVER STRIKE OR DROP THE AIR-
BAG CONTROL MODULE, AS IT CAN DAMAGE THE
IMPACT SENSOR OR AFFECT ITS CALIBRATION. IF
AN AIRBAG CONTROL MODULE IS ACCIDENTALLY
DROPPED DURING SERVICE, THE MODULE MUST
BE SCRAPPED AND REPLACED WITH A NEW UNIT.
FAILURE TO OBSERVE THIS WARNING COULD
RESULT IN ACCIDENTAL, INCOMPLETE, OR
IMPROPER SUPPLEMENTAL RESTRAINT DEPLOY-
MENT AND POSSIBLE OCCUPANT INJURIES.
(1) Carefully position the Airbag Control Module
(ACM) to the mount that is welded onto the top of
the floor panel transmission tunnel (Fig. 9). The bot-
tom of the ACM housing is keyed. When the ACM is
correctly positioned, the bottom of the housing will fit
flush with the mount and the orientation arrow on
the label on top of the housing will be pointed for-
ward in the vehicle.
(2) Install and tighten the four screws that secure
the ACM to the mount that is welded onto the top of
the floor panel transmission tunnel. Tighten the
screws to 11 N´m (95 in. lbs.).
(3) Reconnect the instrument panel wire harness
connector for the ACM to the ACM connector recep-
tacle. Be certain that the connector latch and the red
CPA lock are fully engaged (Fig. 8).
(4) Reconnect the airbag overlay wire harness con-
nector for the ACM to the ACM connector receptacle.
Be certain that the connector latch and the red CPA
lock are fully engaged.
(5) Reinstall the center console bracket onto the
two studs on the floor panel transmission tunnel just
forward of the ACM (Fig. 7).
(6) Install and tighten the two nuts that secure
the center console bracket to the studs on the floor
panel transmission tunnel. Tighten the nuts to 28
N´m (21 ft. lbs.).
(7) Reinstall the center console onto the top of the
floor panel transmission tunnel. (Refer to 23 - BODY/
INTERIOR/FLOOR CONSOLE - INSTALLATION).
(8) Do not reconnect the battery negative cable at
this time. The supplemental restraint system verifi-
cation test procedure should be performed following
service of any supplemental restraint system compo-
nent. (Refer to 8 - ELECTRICAL/RESTRAINTS -
STANDARD PROCEDURE - VERIFICATION TEST).
Fig. 9 Airbag Control Module Remove/Install
1 - SCREW (4)
2 - AIRBAG CONTROL MODULE
3 - FLOOR PANEL TRANSMISSION TUNNEL
4 - MOUNT
8O - 12 RESTRAINTSWJ
AIRBAG CONTROL MODULE (Continued)