headlamp JEEP GRAND CHEROKEE 2002 WJ / 2.G Workshop Manual
[x] Cancel search | Manufacturer: JEEP, Model Year: 2002, Model line: GRAND CHEROKEE, Model: JEEP GRAND CHEROKEE 2002 WJ / 2.GPages: 2199, PDF Size: 76.01 MB
Page 1898 of 2199
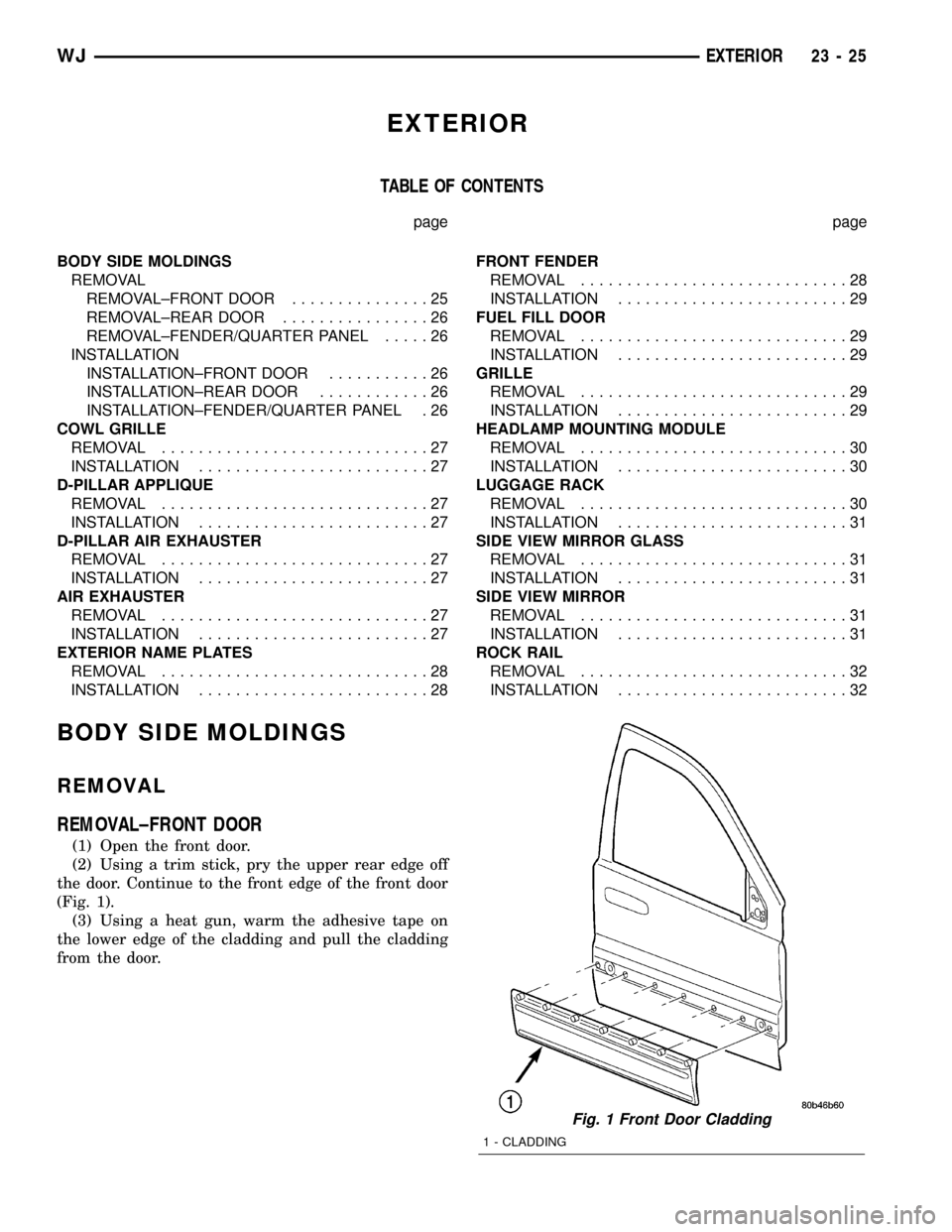
EXTERIOR
TABLE OF CONTENTS
page page
BODY SIDE MOLDINGS
REMOVAL
REMOVAL±FRONT DOOR...............25
REMOVAL±REAR DOOR................26
REMOVAL±FENDER/QUARTER PANEL.....26
INSTALLATION
INSTALLATION±FRONT DOOR...........26
INSTALLATION±REAR DOOR............26
INSTALLATION±FENDER/QUARTER PANEL . 26
COWL GRILLE
REMOVAL.............................27
INSTALLATION.........................27
D-PILLAR APPLIQUE
REMOVAL.............................27
INSTALLATION.........................27
D-PILLAR AIR EXHAUSTER
REMOVAL.............................27
INSTALLATION.........................27
AIR EXHAUSTER
REMOVAL.............................27
INSTALLATION.........................27
EXTERIOR NAME PLATES
REMOVAL.............................28
INSTALLATION.........................28FRONT FENDER
REMOVAL.............................28
INSTALLATION.........................29
FUEL FILL DOOR
REMOVAL.............................29
INSTALLATION.........................29
GRILLE
REMOVAL.............................29
INSTALLATION.........................29
HEADLAMP MOUNTING MODULE
REMOVAL.............................30
INSTALLATION.........................30
LUGGAGE RACK
REMOVAL.............................30
INSTALLATION.........................31
SIDE VIEW MIRROR GLASS
REMOVAL.............................31
INSTALLATION.........................31
SIDE VIEW MIRROR
REMOVAL.............................31
INSTALLATION.........................31
ROCK RAIL
REMOVAL.............................32
INSTALLATION.........................32
BODY SIDE MOLDINGS
REMOVAL
REMOVAL±FRONT DOOR
(1) Open the front door.
(2) Using a trim stick, pry the upper rear edge off
the door. Continue to the front edge of the front door
(Fig. 1).
(3) Using a heat gun, warm the adhesive tape on
the lower edge of the cladding and pull the cladding
from the door.
Fig. 1 Front Door Cladding
1 - CLADDING
WJEXTERIOR 23 - 25
Page 1903 of 2199
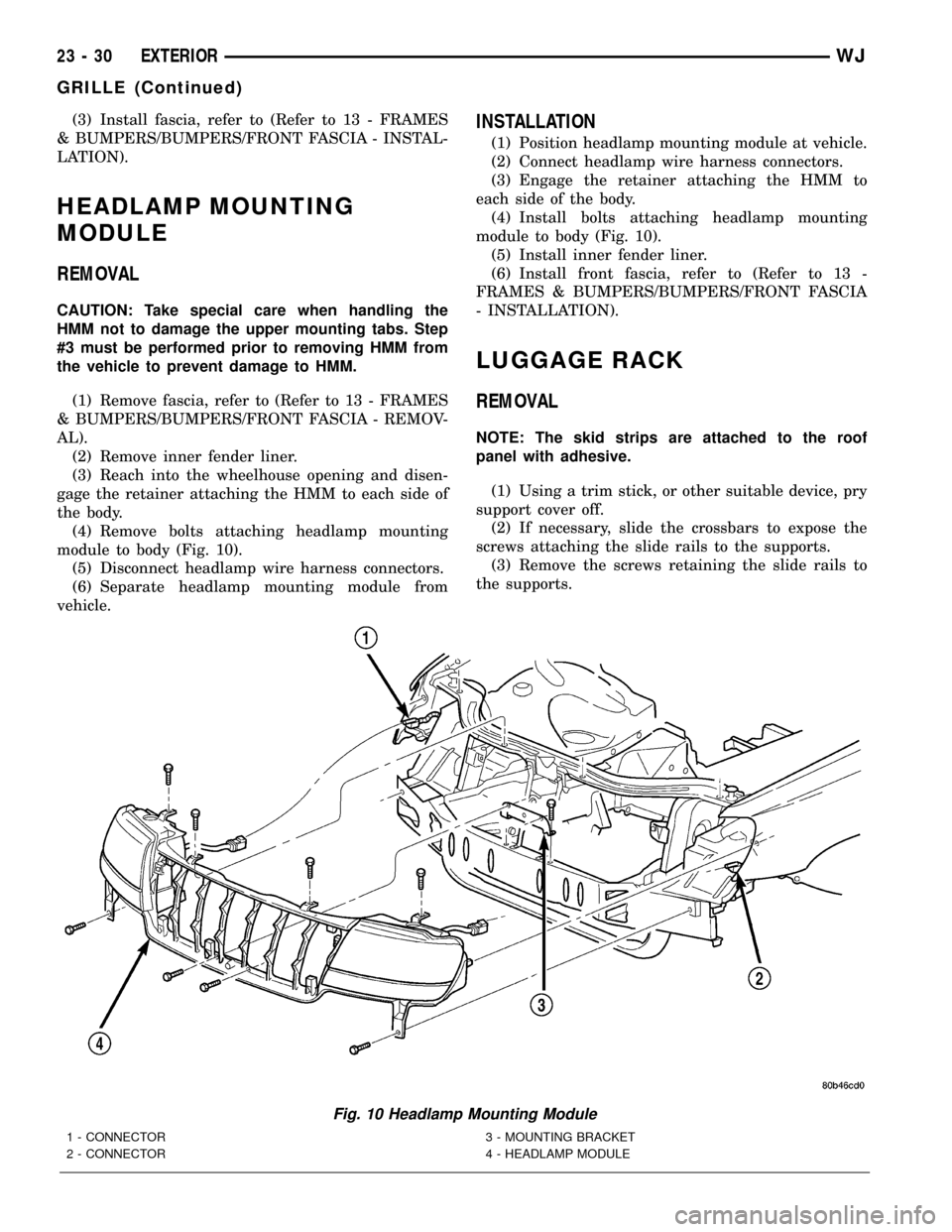
(3) Install fascia, refer to (Refer to 13 - FRAMES
& BUMPERS/BUMPERS/FRONT FASCIA - INSTAL-
LATION).
HEADLAMP MOUNTING
MODULE
REMOVAL
CAUTION: Take special care when handling the
HMM not to damage the upper mounting tabs. Step
#3 must be performed prior to removing HMM from
the vehicle to prevent damage to HMM.
(1) Remove fascia, refer to (Refer to 13 - FRAMES
& BUMPERS/BUMPERS/FRONT FASCIA - REMOV-
AL).
(2) Remove inner fender liner.
(3) Reach into the wheelhouse opening and disen-
gage the retainer attaching the HMM to each side of
the body.
(4) Remove bolts attaching headlamp mounting
module to body (Fig. 10).
(5) Disconnect headlamp wire harness connectors.
(6) Separate headlamp mounting module from
vehicle.
INSTALLATION
(1) Position headlamp mounting module at vehicle.
(2) Connect headlamp wire harness connectors.
(3) Engage the retainer attaching the HMM to
each side of the body.
(4) Install bolts attaching headlamp mounting
module to body (Fig. 10).
(5) Install inner fender liner.
(6) Install front fascia, refer to (Refer to 13 -
FRAMES & BUMPERS/BUMPERS/FRONT FASCIA
- INSTALLATION).
LUGGAGE RACK
REMOVAL
NOTE: The skid strips are attached to the roof
panel with adhesive.
(1) Using a trim stick, or other suitable device, pry
support cover off.
(2) If necessary, slide the crossbars to expose the
screws attaching the slide rails to the supports.
(3) Remove the screws retaining the slide rails to
the supports.
Fig. 10 Headlamp Mounting Module
1 - CONNECTOR
2 - CONNECTOR3 - MOUNTING BRACKET
4 - HEADLAMP MODULE
23 - 30 EXTERIORWJ
GRILLE (Continued)
Page 1918 of 2199
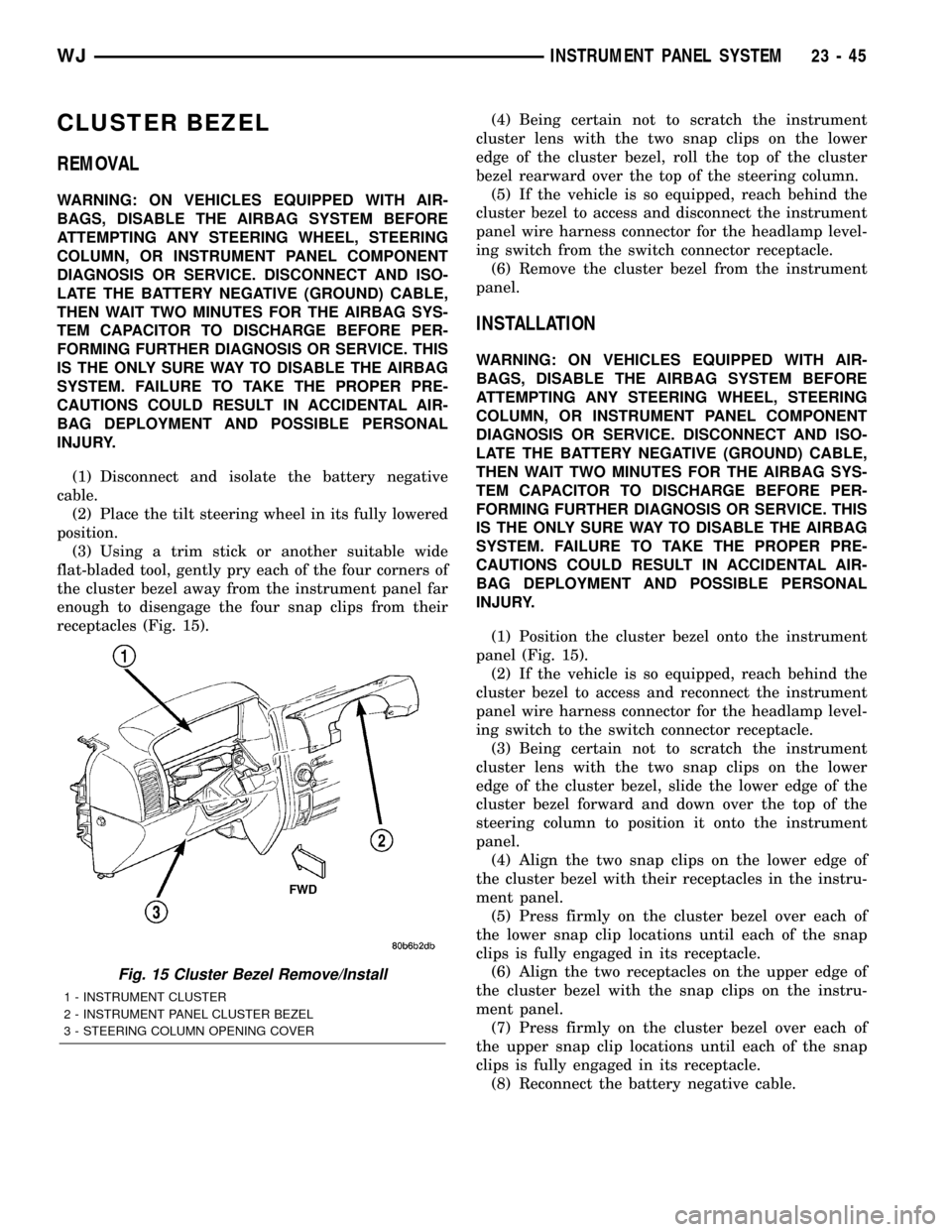
CLUSTER BEZEL
REMOVAL
WARNING: ON VEHICLES EQUIPPED WITH AIR-
BAGS, DISABLE THE AIRBAG SYSTEM BEFORE
ATTEMPTING ANY STEERING WHEEL, STEERING
COLUMN, OR INSTRUMENT PANEL COMPONENT
DIAGNOSIS OR SERVICE. DISCONNECT AND ISO-
LATE THE BATTERY NEGATIVE (GROUND) CABLE,
THEN WAIT TWO MINUTES FOR THE AIRBAG SYS-
TEM CAPACITOR TO DISCHARGE BEFORE PER-
FORMING FURTHER DIAGNOSIS OR SERVICE. THIS
IS THE ONLY SURE WAY TO DISABLE THE AIRBAG
SYSTEM. FAILURE TO TAKE THE PROPER PRE-
CAUTIONS COULD RESULT IN ACCIDENTAL AIR-
BAG DEPLOYMENT AND POSSIBLE PERSONAL
INJURY.
(1) Disconnect and isolate the battery negative
cable.
(2) Place the tilt steering wheel in its fully lowered
position.
(3) Using a trim stick or another suitable wide
flat-bladed tool, gently pry each of the four corners of
the cluster bezel away from the instrument panel far
enough to disengage the four snap clips from their
receptacles (Fig. 15).(4) Being certain not to scratch the instrument
cluster lens with the two snap clips on the lower
edge of the cluster bezel, roll the top of the cluster
bezel rearward over the top of the steering column.
(5) If the vehicle is so equipped, reach behind the
cluster bezel to access and disconnect the instrument
panel wire harness connector for the headlamp level-
ing switch from the switch connector receptacle.
(6) Remove the cluster bezel from the instrument
panel.
INSTALLATION
WARNING: ON VEHICLES EQUIPPED WITH AIR-
BAGS, DISABLE THE AIRBAG SYSTEM BEFORE
ATTEMPTING ANY STEERING WHEEL, STEERING
COLUMN, OR INSTRUMENT PANEL COMPONENT
DIAGNOSIS OR SERVICE. DISCONNECT AND ISO-
LATE THE BATTERY NEGATIVE (GROUND) CABLE,
THEN WAIT TWO MINUTES FOR THE AIRBAG SYS-
TEM CAPACITOR TO DISCHARGE BEFORE PER-
FORMING FURTHER DIAGNOSIS OR SERVICE. THIS
IS THE ONLY SURE WAY TO DISABLE THE AIRBAG
SYSTEM. FAILURE TO TAKE THE PROPER PRE-
CAUTIONS COULD RESULT IN ACCIDENTAL AIR-
BAG DEPLOYMENT AND POSSIBLE PERSONAL
INJURY.
(1) Position the cluster bezel onto the instrument
panel (Fig. 15).
(2) If the vehicle is so equipped, reach behind the
cluster bezel to access and reconnect the instrument
panel wire harness connector for the headlamp level-
ing switch to the switch connector receptacle.
(3) Being certain not to scratch the instrument
cluster lens with the two snap clips on the lower
edge of the cluster bezel, slide the lower edge of the
cluster bezel forward and down over the top of the
steering column to position it onto the instrument
panel.
(4) Align the two snap clips on the lower edge of
the cluster bezel with their receptacles in the instru-
ment panel.
(5) Press firmly on the cluster bezel over each of
the lower snap clip locations until each of the snap
clips is fully engaged in its receptacle.
(6) Align the two receptacles on the upper edge of
the cluster bezel with the snap clips on the instru-
ment panel.
(7) Press firmly on the cluster bezel over each of
the upper snap clip locations until each of the snap
clips is fully engaged in its receptacle.
(8) Reconnect the battery negative cable.
Fig. 15 Cluster Bezel Remove/Install
1 - INSTRUMENT CLUSTER
2 - INSTRUMENT PANEL CLUSTER BEZEL
3 - STEERING COLUMN OPENING COVER
WJINSTRUMENT PANEL SYSTEM 23 - 45
Page 1925 of 2199
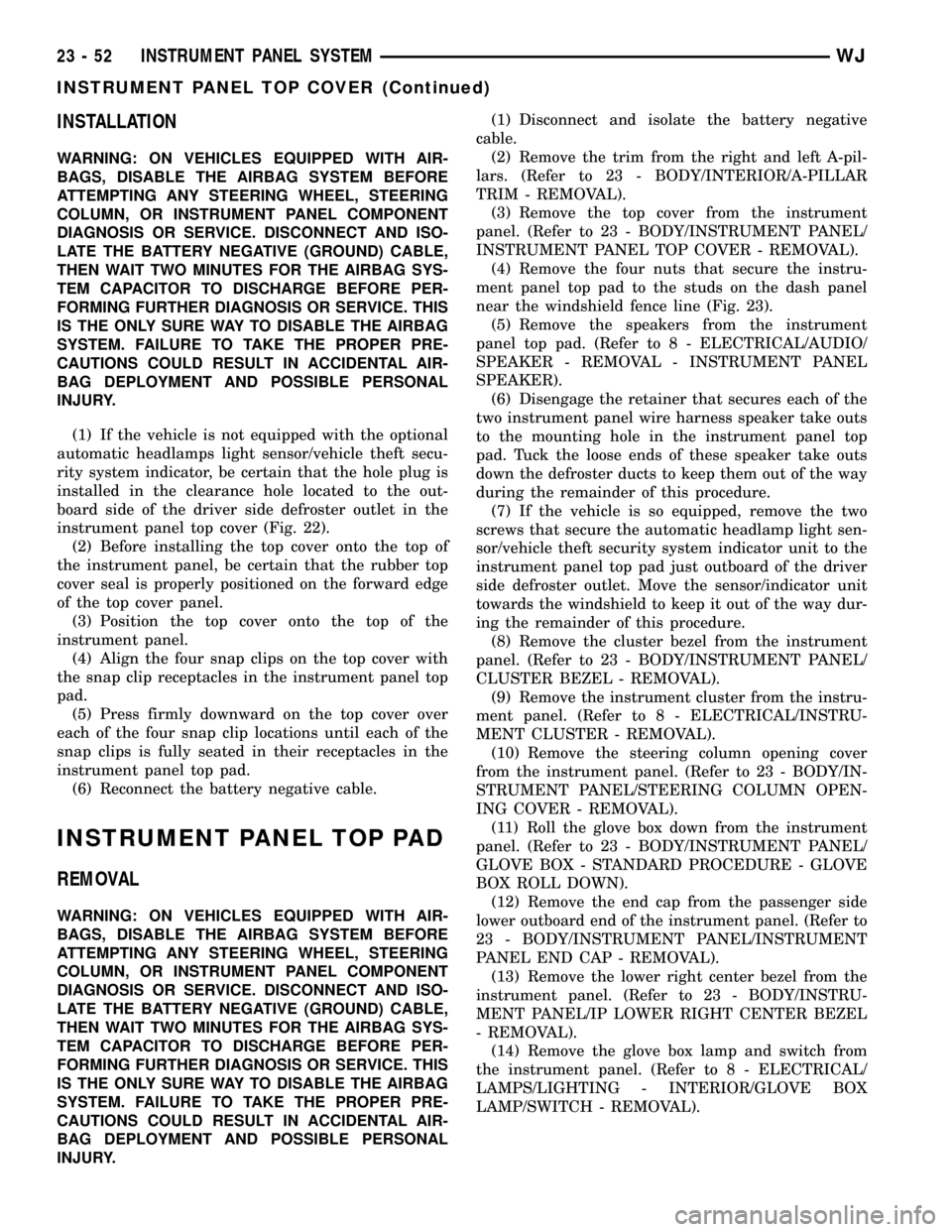
INSTALLATION
WARNING: ON VEHICLES EQUIPPED WITH AIR-
BAGS, DISABLE THE AIRBAG SYSTEM BEFORE
ATTEMPTING ANY STEERING WHEEL, STEERING
COLUMN, OR INSTRUMENT PANEL COMPONENT
DIAGNOSIS OR SERVICE. DISCONNECT AND ISO-
LATE THE BATTERY NEGATIVE (GROUND) CABLE,
THEN WAIT TWO MINUTES FOR THE AIRBAG SYS-
TEM CAPACITOR TO DISCHARGE BEFORE PER-
FORMING FURTHER DIAGNOSIS OR SERVICE. THIS
IS THE ONLY SURE WAY TO DISABLE THE AIRBAG
SYSTEM. FAILURE TO TAKE THE PROPER PRE-
CAUTIONS COULD RESULT IN ACCIDENTAL AIR-
BAG DEPLOYMENT AND POSSIBLE PERSONAL
INJURY.
(1) If the vehicle is not equipped with the optional
automatic headlamps light sensor/vehicle theft secu-
rity system indicator, be certain that the hole plug is
installed in the clearance hole located to the out-
board side of the driver side defroster outlet in the
instrument panel top cover (Fig. 22).
(2) Before installing the top cover onto the top of
the instrument panel, be certain that the rubber top
cover seal is properly positioned on the forward edge
of the top cover panel.
(3) Position the top cover onto the top of the
instrument panel.
(4) Align the four snap clips on the top cover with
the snap clip receptacles in the instrument panel top
pad.
(5) Press firmly downward on the top cover over
each of the four snap clip locations until each of the
snap clips is fully seated in their receptacles in the
instrument panel top pad.
(6) Reconnect the battery negative cable.
INSTRUMENT PANEL TOP PAD
REMOVAL
WARNING: ON VEHICLES EQUIPPED WITH AIR-
BAGS, DISABLE THE AIRBAG SYSTEM BEFORE
ATTEMPTING ANY STEERING WHEEL, STEERING
COLUMN, OR INSTRUMENT PANEL COMPONENT
DIAGNOSIS OR SERVICE. DISCONNECT AND ISO-
LATE THE BATTERY NEGATIVE (GROUND) CABLE,
THEN WAIT TWO MINUTES FOR THE AIRBAG SYS-
TEM CAPACITOR TO DISCHARGE BEFORE PER-
FORMING FURTHER DIAGNOSIS OR SERVICE. THIS
IS THE ONLY SURE WAY TO DISABLE THE AIRBAG
SYSTEM. FAILURE TO TAKE THE PROPER PRE-
CAUTIONS COULD RESULT IN ACCIDENTAL AIR-
BAG DEPLOYMENT AND POSSIBLE PERSONAL
INJURY.(1) Disconnect and isolate the battery negative
cable.
(2) Remove the trim from the right and left A-pil-
lars. (Refer to 23 - BODY/INTERIOR/A-PILLAR
TRIM - REMOVAL).
(3) Remove the top cover from the instrument
panel. (Refer to 23 - BODY/INSTRUMENT PANEL/
INSTRUMENT PANEL TOP COVER - REMOVAL).
(4) Remove the four nuts that secure the instru-
ment panel top pad to the studs on the dash panel
near the windshield fence line (Fig. 23).
(5) Remove the speakers from the instrument
panel top pad. (Refer to 8 - ELECTRICAL/AUDIO/
SPEAKER - REMOVAL - INSTRUMENT PANEL
SPEAKER).
(6) Disengage the retainer that secures each of the
two instrument panel wire harness speaker take outs
to the mounting hole in the instrument panel top
pad. Tuck the loose ends of these speaker take outs
down the defroster ducts to keep them out of the way
during the remainder of this procedure.
(7) If the vehicle is so equipped, remove the two
screws that secure the automatic headlamp light sen-
sor/vehicle theft security system indicator unit to the
instrument panel top pad just outboard of the driver
side defroster outlet. Move the sensor/indicator unit
towards the windshield to keep it out of the way dur-
ing the remainder of this procedure.
(8) Remove the cluster bezel from the instrument
panel. (Refer to 23 - BODY/INSTRUMENT PANEL/
CLUSTER BEZEL - REMOVAL).
(9) Remove the instrument cluster from the instru-
ment panel. (Refer to 8 - ELECTRICAL/INSTRU-
MENT CLUSTER - REMOVAL).
(10) Remove the steering column opening cover
from the instrument panel. (Refer to 23 - BODY/IN-
STRUMENT PANEL/STEERING COLUMN OPEN-
ING COVER - REMOVAL).
(11) Roll the glove box down from the instrument
panel. (Refer to 23 - BODY/INSTRUMENT PANEL/
GLOVE BOX - STANDARD PROCEDURE - GLOVE
BOX ROLL DOWN).
(12) Remove the end cap from the passenger side
lower outboard end of the instrument panel. (Refer to
23 - BODY/INSTRUMENT PANEL/INSTRUMENT
PANEL END CAP - REMOVAL).
(13) Remove the lower right center bezel from the
instrument panel. (Refer to 23 - BODY/INSTRU-
MENT PANEL/IP LOWER RIGHT CENTER BEZEL
- REMOVAL).
(14) Remove the glove box lamp and switch from
the instrument panel. (Refer to 8 - ELECTRICAL/
LAMPS/LIGHTING - INTERIOR/GLOVE BOX
LAMP/SWITCH - REMOVAL).
23 - 52 INSTRUMENT PANEL SYSTEMWJ
INSTRUMENT PANEL TOP COVER (Continued)
Page 1928 of 2199
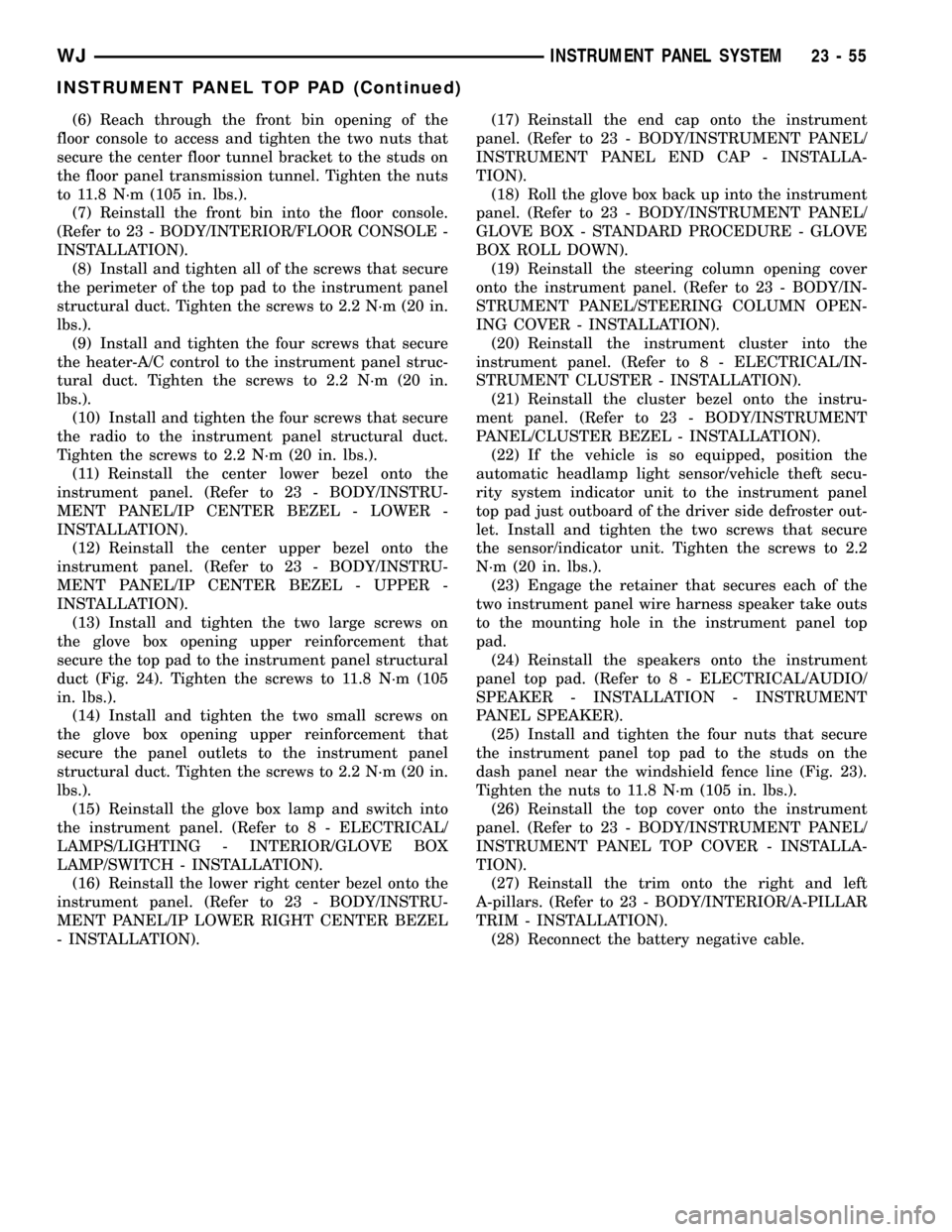
(6) Reach through the front bin opening of the
floor console to access and tighten the two nuts that
secure the center floor tunnel bracket to the studs on
the floor panel transmission tunnel. Tighten the nuts
to 11.8 N´m (105 in. lbs.).
(7) Reinstall the front bin into the floor console.
(Refer to 23 - BODY/INTERIOR/FLOOR CONSOLE -
INSTALLATION).
(8) Install and tighten all of the screws that secure
the perimeter of the top pad to the instrument panel
structural duct. Tighten the screws to 2.2 N´m (20 in.
lbs.).
(9) Install and tighten the four screws that secure
the heater-A/C control to the instrument panel struc-
tural duct. Tighten the screws to 2.2 N´m (20 in.
lbs.).
(10) Install and tighten the four screws that secure
the radio to the instrument panel structural duct.
Tighten the screws to 2.2 N´m (20 in. lbs.).
(11) Reinstall the center lower bezel onto the
instrument panel. (Refer to 23 - BODY/INSTRU-
MENT PANEL/IP CENTER BEZEL - LOWER -
INSTALLATION).
(12) Reinstall the center upper bezel onto the
instrument panel. (Refer to 23 - BODY/INSTRU-
MENT PANEL/IP CENTER BEZEL - UPPER -
INSTALLATION).
(13) Install and tighten the two large screws on
the glove box opening upper reinforcement that
secure the top pad to the instrument panel structural
duct (Fig. 24). Tighten the screws to 11.8 N´m (105
in. lbs.).
(14) Install and tighten the two small screws on
the glove box opening upper reinforcement that
secure the panel outlets to the instrument panel
structural duct. Tighten the screws to 2.2 N´m (20 in.
lbs.).
(15) Reinstall the glove box lamp and switch into
the instrument panel. (Refer to 8 - ELECTRICAL/
LAMPS/LIGHTING - INTERIOR/GLOVE BOX
LAMP/SWITCH - INSTALLATION).
(16) Reinstall the lower right center bezel onto the
instrument panel. (Refer to 23 - BODY/INSTRU-
MENT PANEL/IP LOWER RIGHT CENTER BEZEL
- INSTALLATION).(17) Reinstall the end cap onto the instrument
panel. (Refer to 23 - BODY/INSTRUMENT PANEL/
INSTRUMENT PANEL END CAP - INSTALLA-
TION).
(18) Roll the glove box back up into the instrument
panel. (Refer to 23 - BODY/INSTRUMENT PANEL/
GLOVE BOX - STANDARD PROCEDURE - GLOVE
BOX ROLL DOWN).
(19) Reinstall the steering column opening cover
onto the instrument panel. (Refer to 23 - BODY/IN-
STRUMENT PANEL/STEERING COLUMN OPEN-
ING COVER - INSTALLATION).
(20) Reinstall the instrument cluster into the
instrument panel. (Refer to 8 - ELECTRICAL/IN-
STRUMENT CLUSTER - INSTALLATION).
(21) Reinstall the cluster bezel onto the instru-
ment panel. (Refer to 23 - BODY/INSTRUMENT
PANEL/CLUSTER BEZEL - INSTALLATION).
(22) If the vehicle is so equipped, position the
automatic headlamp light sensor/vehicle theft secu-
rity system indicator unit to the instrument panel
top pad just outboard of the driver side defroster out-
let. Install and tighten the two screws that secure
the sensor/indicator unit. Tighten the screws to 2.2
N´m (20 in. lbs.).
(23) Engage the retainer that secures each of the
two instrument panel wire harness speaker take outs
to the mounting hole in the instrument panel top
pad.
(24) Reinstall the speakers onto the instrument
panel top pad. (Refer to 8 - ELECTRICAL/AUDIO/
SPEAKER - INSTALLATION - INSTRUMENT
PANEL SPEAKER).
(25) Install and tighten the four nuts that secure
the instrument panel top pad to the studs on the
dash panel near the windshield fence line (Fig. 23).
Tighten the nuts to 11.8 N´m (105 in. lbs.).
(26) Reinstall the top cover onto the instrument
panel. (Refer to 23 - BODY/INSTRUMENT PANEL/
INSTRUMENT PANEL TOP COVER - INSTALLA-
TION).
(27) Reinstall the trim onto the right and left
A-pillars. (Refer to 23 - BODY/INTERIOR/A-PILLAR
TRIM - INSTALLATION).
(28) Reconnect the battery negative cable.
WJINSTRUMENT PANEL SYSTEM 23 - 55
INSTRUMENT PANEL TOP PAD (Continued)
Page 1985 of 2199
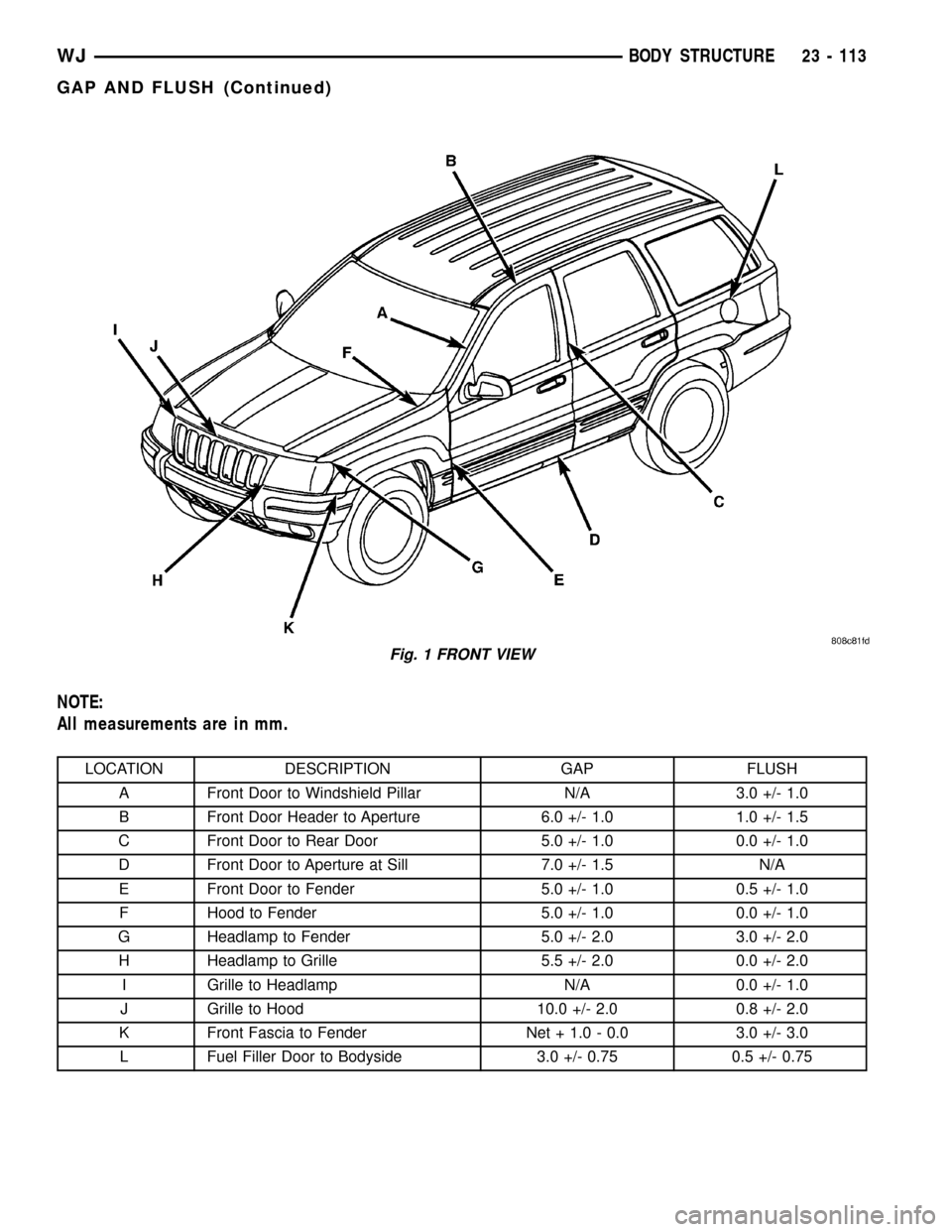
NOTE:
All measurements are in mm.
LOCATION DESCRIPTION GAP FLUSH
A Front Door to Windshield Pillar N/A 3.0 +/- 1.0
B Front Door Header to Aperture 6.0 +/- 1.0 1.0 +/- 1.5
C Front Door to Rear Door 5.0 +/- 1.0 0.0 +/- 1.0
D Front Door to Aperture at Sill 7.0 +/- 1.5 N/A
E Front Door to Fender 5.0 +/- 1.0 0.5 +/- 1.0
F Hood to Fender 5.0 +/- 1.0 0.0 +/- 1.0
G Headlamp to Fender 5.0 +/- 2.0 3.0 +/- 2.0
H Headlamp to Grille 5.5 +/- 2.0 0.0 +/- 2.0
I Grille to Headlamp N/A 0.0 +/- 1.0
J Grille to Hood 10.0 +/- 2.0 0.8 +/- 2.0
K Front Fascia to Fender Net + 1.0 - 0.0 3.0 +/- 3.0
L Fuel Filler Door to Bodyside 3.0 +/- 0.75 0.5 +/- 0.75
Fig. 1 FRONT VIEW
WJBODY STRUCTURE 23 - 113
GAP AND FLUSH (Continued)
Page 2103 of 2199
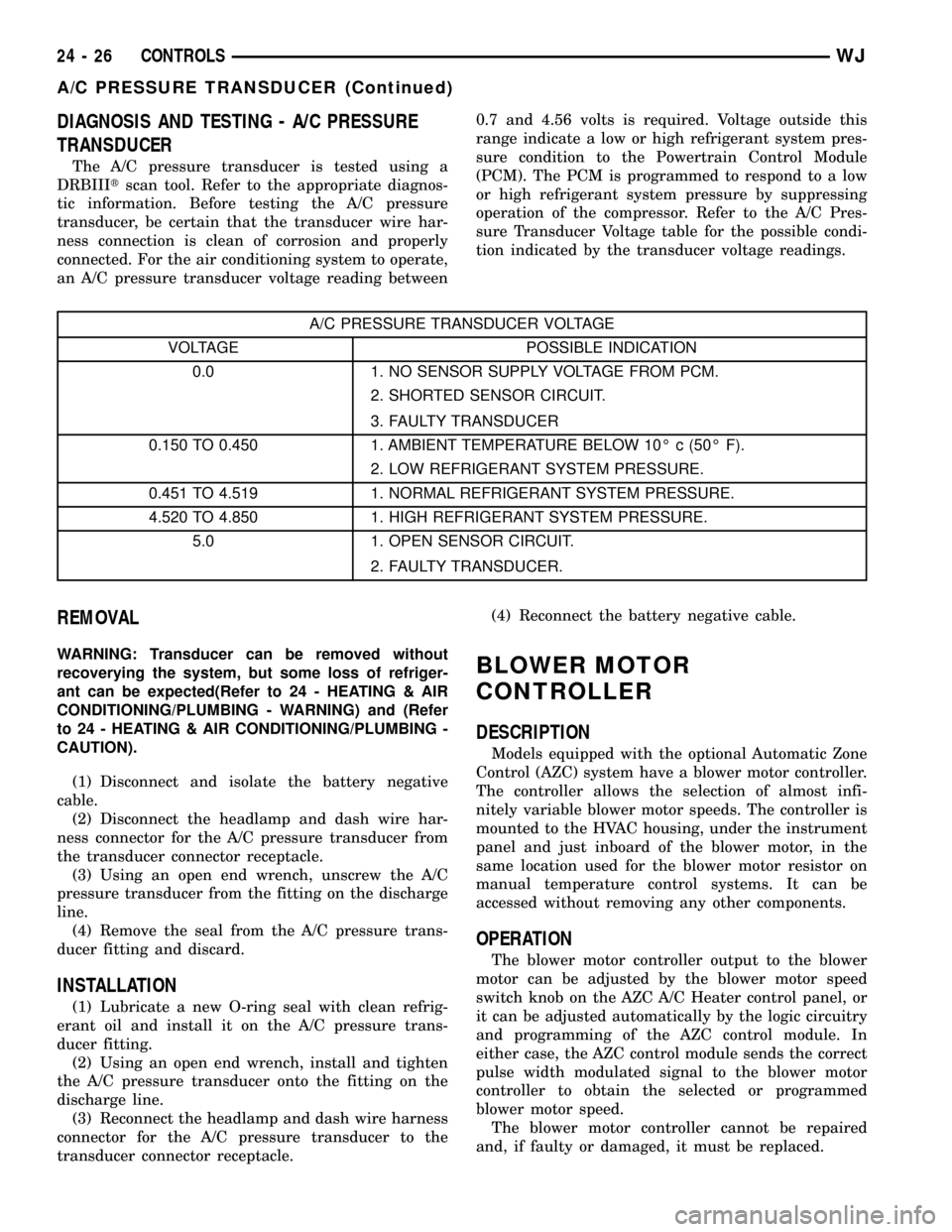
DIAGNOSIS AND TESTING - A/C PRESSURE
TRANSDUCER
The A/C pressure transducer is tested using a
DRBIIItscan tool. Refer to the appropriate diagnos-
tic information. Before testing the A/C pressure
transducer, be certain that the transducer wire har-
ness connection is clean of corrosion and properly
connected. For the air conditioning system to operate,
an A/C pressure transducer voltage reading between0.7 and 4.56 volts is required. Voltage outside this
range indicate a low or high refrigerant system pres-
sure condition to the Powertrain Control Module
(PCM). The PCM is programmed to respond to a low
or high refrigerant system pressure by suppressing
operation of the compressor. Refer to the A/C Pres-
sure Transducer Voltage table for the possible condi-
tion indicated by the transducer voltage readings.
A/C PRESSURE TRANSDUCER VOLTAGE
VOLTAGE POSSIBLE INDICATION
0.0 1. NO SENSOR SUPPLY VOLTAGE FROM PCM.
2. SHORTED SENSOR CIRCUIT.
3. FAULTY TRANSDUCER
0.150 TO 0.450 1. AMBIENT TEMPERATURE BELOW 10É c (50É F).
2. LOW REFRIGERANT SYSTEM PRESSURE.
0.451 TO 4.519 1. NORMAL REFRIGERANT SYSTEM PRESSURE.
4.520 TO 4.850 1. HIGH REFRIGERANT SYSTEM PRESSURE.
5.0 1. OPEN SENSOR CIRCUIT.
2. FAULTY TRANSDUCER.
REMOVAL
WARNING: Transducer can be removed without
recoverying the system, but some loss of refriger-
ant can be expected(Refer to 24 - HEATING & AIR
CONDITIONING/PLUMBING - WARNING) and (Refer
to 24 - HEATING & AIR CONDITIONING/PLUMBING -
CAUTION).
(1) Disconnect and isolate the battery negative
cable.
(2) Disconnect the headlamp and dash wire har-
ness connector for the A/C pressure transducer from
the transducer connector receptacle.
(3) Using an open end wrench, unscrew the A/C
pressure transducer from the fitting on the discharge
line.
(4) Remove the seal from the A/C pressure trans-
ducer fitting and discard.
INSTALLATION
(1) Lubricate a new O-ring seal with clean refrig-
erant oil and install it on the A/C pressure trans-
ducer fitting.
(2) Using an open end wrench, install and tighten
the A/C pressure transducer onto the fitting on the
discharge line.
(3) Reconnect the headlamp and dash wire harness
connector for the A/C pressure transducer to the
transducer connector receptacle.(4) Reconnect the battery negative cable.
BLOWER MOTOR
CONTROLLER
DESCRIPTION
Models equipped with the optional Automatic Zone
Control (AZC) system have a blower motor controller.
The controller allows the selection of almost infi-
nitely variable blower motor speeds. The controller is
mounted to the HVAC housing, under the instrument
panel and just inboard of the blower motor, in the
same location used for the blower motor resistor on
manual temperature control systems. It can be
accessed without removing any other components.
OPERATION
The blower motor controller output to the blower
motor can be adjusted by the blower motor speed
switch knob on the AZC A/C Heater control panel, or
it can be adjusted automatically by the logic circuitry
and programming of the AZC control module. In
either case, the AZC control module sends the correct
pulse width modulated signal to the blower motor
controller to obtain the selected or programmed
blower motor speed.
The blower motor controller cannot be repaired
and, if faulty or damaged, it must be replaced.
24 - 26 CONTROLSWJ
A/C PRESSURE TRANSDUCER (Continued)
Page 2111 of 2199

INSTALLATION
INSTALLATION - RECIRCULATION DOOR
VACUUM ACTUATOR
(1) Install the recirculation door vacuum actuator
on the HVAC housing and tighten the mounting
screws to 2.2 N´m (20 in. lbs.).
(2) Engage the recirculation door actuating rod
with the recirculation door lever.
(3) Engage the recirculation door pivot connection
with the door pivot pin.
(4) Plug in the vacuum harness connector to the
recirculation door vacuum actuator.
(5) Install the instrument panel in the vehicle.
Refer to Instrument Panel System for the procedures.
INSTALLATION - RECIRCULATION DOOR
ELECTRIC ACTUATOR
(1) Install the recirculation door actuator on the
recirculation door housing and tighten the mounting
screws to 2.2 N´m (20 in. lbs.).
(2) Install the recirculation door housing on the
HVAC unit and tighten the mounting screws to 2.2
N´m (20 in. lbs.).
(3) Plug in the wire harness connector to the recir-
culation door actuator.
(4) Install the instrument panel in the vehicle.
Refer to Instrument Panel System for the procedures.
VACUUM CHECK VALVE
DESCRIPTION
Two vacuum check valves (non AZC only) are
installed on the vacuum supply system. One is on the
accessory vacuum supply line in the engine compart-
ment, near the vacuum tap on the engine intake
manifold. A second vacuum check valve is located on
the bottom of the HVAC unit behind the passenger
front floor duct on the black vacuum line. The vac-
uum check valves are designed to allow vacuum to
flow in only one direction through the accessory vac-
uum supply circuits.
OPERATION
The use of a vacuum check valve helps to maintain
the system vacuum needed to retain the selected A/C
Heater mode settings. The check valve will prevent
the engine from bleeding down system vacuum
through the intake manifold during extended heavy
engine load (low engine vacuum) operation.
The vacuum check valve cannot be repaired and, if
faulty or damaged, it must be replaced.
REMOVAL
(1) Unplug the HVAC vacuum supply line connec-
tor at the vacuum check valve near the engine intake
manifold vacuum adapter fitting.
(2) Note the orientation of the check valve in the
vacuum supply line for correct installation.
(3) Unplug the vacuum check valve from the vac-
uum supply line fittings.
INSTALLATION
(1) Plug in the vacuum check valve at the vacuum
supply line fittings, noting the orientation of the
check valve in the vacuum supply line for correct
installation.
(2) Plug in the HVAC vacuum supply line connec-
tor at the vacuum check valve near the engine intake
manifold vacuum adapter fitting.
VACUUM RESERVOIR
DESCRIPTION
The vacuum reservoir is mounted in the right front
of the vehicle behind the headlamp mounting module
(Fig. 22). The headlamp mounting module and head-
lamp assembly must be removed from the vehicle to
access the vacuum reservoir for service. Refer to
Lamps/Lighting for the procedures.
OPERATION
Engine vacuum is stored in the vacuum reservoir.
The stored vacuum is used to operate the vacuum-
Fig. 21 RECIRCULATION DOOR HOUSING
1 - RECIRCULATION DOOR HOUSING
2 - ATTACHING SCREWS
24 - 34 CONTROLSWJ
RECIRCULATION DOOR ACTUATOR (Continued)
Page 2112 of 2199

controlled vehicle accessories during periods of low
engine vacuum such as when the vehicle is climbing
a steep grade, or under other high engine load oper-
ating conditions.
The vacuum reservoir cannot be repaired and, if
faulty or damaged, it must be replaced.
REMOVAL
(1) Remove the right side headlamp mounting
module and headlamp assembly. Refer to Lamps/
Lighting for the procedures.
(2) Remove the two screws that secure the vacuum
reservoir to the base of the radiator closure panel.
(3) Remove the vacuum reservoir.
INSTALLATION
(1) Install the vacuum reservoir in the vehicle and
tighten the two screws to 3.4 N´m (30 in. lbs.).
(2) Install the right side headlamp mounting mod-
ule and headlamp assembly. Refer to Lamps/Lighting
for the procedures.
EVAPORATOR TEMPERATURE
SENSOR
DESCRIPTION
The evaporator probe is a 2 wire temperature sens-
ing element located at the coldest point on the face of
the evaporator. The switch is attached to the evapo-
rator coil fins. The evaporator temperature probe
prevents condensate water on the evaporator coil
from freezing and obstructing A/C system air flow.
OPERATION
The probe is used to switch the clutch OFF before
evaporator freeze-up occurs. Output from the probe is
sampled by the Body Control Module (BCM). The
clutch is switched OFF when the probe temperature
reaches 1.1É C (34É F). It is allowed to switch ON
when the probe temperature reaches 2.2É C (36É F).
REMOVAL
(1) Disconnect and isolate the battery negative
cable.
(2) Remove the HVAC housing from the vehi-
cle(Refer to 24 - HEATING & AIR CONDITIONING/
DISTRIBUTION/HVAC HOUSING - REMOVAL).
(3) Disassemble the HVAC housing(Refer to 24 -
HEATING & AIR CONDITIONING/DISTRIBUTION/
HVAC HOUSING - DISASSEMBLY).
(4) Carefully pull the probe out of the evaporator
core.
INSTALLATION
(1) Install the new probe into the evaporator.
NOTE: The new probe must not go into the same
hole (in the evaporator core) that the old probe was
removed from.
(2) Reassemble the HVAC housing(Refer to 24 -
HEATING & AIR CONDITIONING/DISTRIBUTION/
HVAC HOUSING - ASSEMBLY).
(3) Reinstall the HVAC assembly in the vehicle(Re-
fer to 24 - HEATING & AIR CONDITIONING/DIS-
TRIBUTION/HVAC HOUSING - INSTALLATION).
(4) Reconnect the battery negative cable.
Fig. 22 VACUUM RESERVOIR
1 - FAN RELAY
2 - SPEED CONTROL SERVO
3 - VACUUM RESERVOIR
WJCONTROLS 24 - 35
VACUUM RESERVOIR (Continued)
Page 2139 of 2199
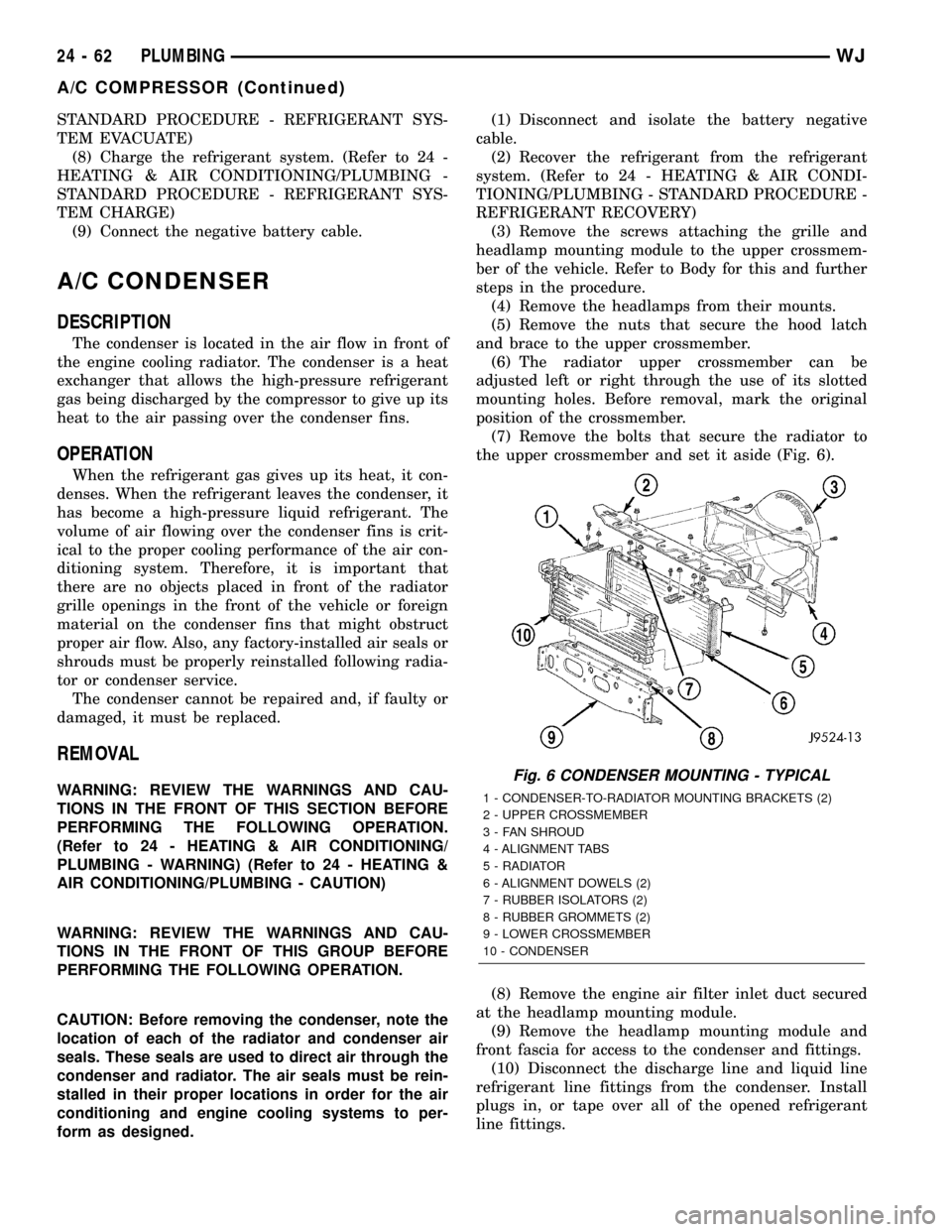
STANDARD PROCEDURE - REFRIGERANT SYS-
TEM EVACUATE)
(8) Charge the refrigerant system. (Refer to 24 -
HEATING & AIR CONDITIONING/PLUMBING -
STANDARD PROCEDURE - REFRIGERANT SYS-
TEM CHARGE)
(9) Connect the negative battery cable.
A/C CONDENSER
DESCRIPTION
The condenser is located in the air flow in front of
the engine cooling radiator. The condenser is a heat
exchanger that allows the high-pressure refrigerant
gas being discharged by the compressor to give up its
heat to the air passing over the condenser fins.
OPERATION
When the refrigerant gas gives up its heat, it con-
denses. When the refrigerant leaves the condenser, it
has become a high-pressure liquid refrigerant. The
volume of air flowing over the condenser fins is crit-
ical to the proper cooling performance of the air con-
ditioning system. Therefore, it is important that
there are no objects placed in front of the radiator
grille openings in the front of the vehicle or foreign
material on the condenser fins that might obstruct
proper air flow. Also, any factory-installed air seals or
shrouds must be properly reinstalled following radia-
tor or condenser service.
The condenser cannot be repaired and, if faulty or
damaged, it must be replaced.
REMOVAL
WARNING: REVIEW THE WARNINGS AND CAU-
TIONS IN THE FRONT OF THIS SECTION BEFORE
PERFORMING THE FOLLOWING OPERATION.
(Refer to 24 - HEATING & AIR CONDITIONING/
PLUMBING - WARNING) (Refer to 24 - HEATING &
AIR CONDITIONING/PLUMBING - CAUTION)
WARNING: REVIEW THE WARNINGS AND CAU-
TIONS IN THE FRONT OF THIS GROUP BEFORE
PERFORMING THE FOLLOWING OPERATION.
CAUTION: Before removing the condenser, note the
location of each of the radiator and condenser air
seals. These seals are used to direct air through the
condenser and radiator. The air seals must be rein-
stalled in their proper locations in order for the air
conditioning and engine cooling systems to per-
form as designed.(1) Disconnect and isolate the battery negative
cable.
(2) Recover the refrigerant from the refrigerant
system. (Refer to 24 - HEATING & AIR CONDI-
TIONING/PLUMBING - STANDARD PROCEDURE -
REFRIGERANT RECOVERY)
(3) Remove the screws attaching the grille and
headlamp mounting module to the upper crossmem-
ber of the vehicle. Refer to Body for this and further
steps in the procedure.
(4) Remove the headlamps from their mounts.
(5) Remove the nuts that secure the hood latch
and brace to the upper crossmember.
(6) The radiator upper crossmember can be
adjusted left or right through the use of its slotted
mounting holes. Before removal, mark the original
position of the crossmember.
(7) Remove the bolts that secure the radiator to
the upper crossmember and set it aside (Fig. 6).
(8) Remove the engine air filter inlet duct secured
at the headlamp mounting module.
(9) Remove the headlamp mounting module and
front fascia for access to the condenser and fittings.
(10) Disconnect the discharge line and liquid line
refrigerant line fittings from the condenser. Install
plugs in, or tape over all of the opened refrigerant
line fittings.Fig. 6 CONDENSER MOUNTING - TYPICAL
1 - CONDENSER-TO-RADIATOR MOUNTING BRACKETS (2)
2 - UPPER CROSSMEMBER
3 - FAN SHROUD
4 - ALIGNMENT TABS
5 - RADIATOR
6 - ALIGNMENT DOWELS (2)
7 - RUBBER ISOLATORS (2)
8 - RUBBER GROMMETS (2)
9 - LOWER CROSSMEMBER
10 - CONDENSER
24 - 62 PLUMBINGWJ
A/C COMPRESSOR (Continued)