Step button JEEP GRAND CHEROKEE 2002 WJ / 2.G User Guide
[x] Cancel search | Manufacturer: JEEP, Model Year: 2002, Model line: GRAND CHEROKEE, Model: JEEP GRAND CHEROKEE 2002 WJ / 2.GPages: 2199, PDF Size: 76.01 MB
Page 493 of 2199
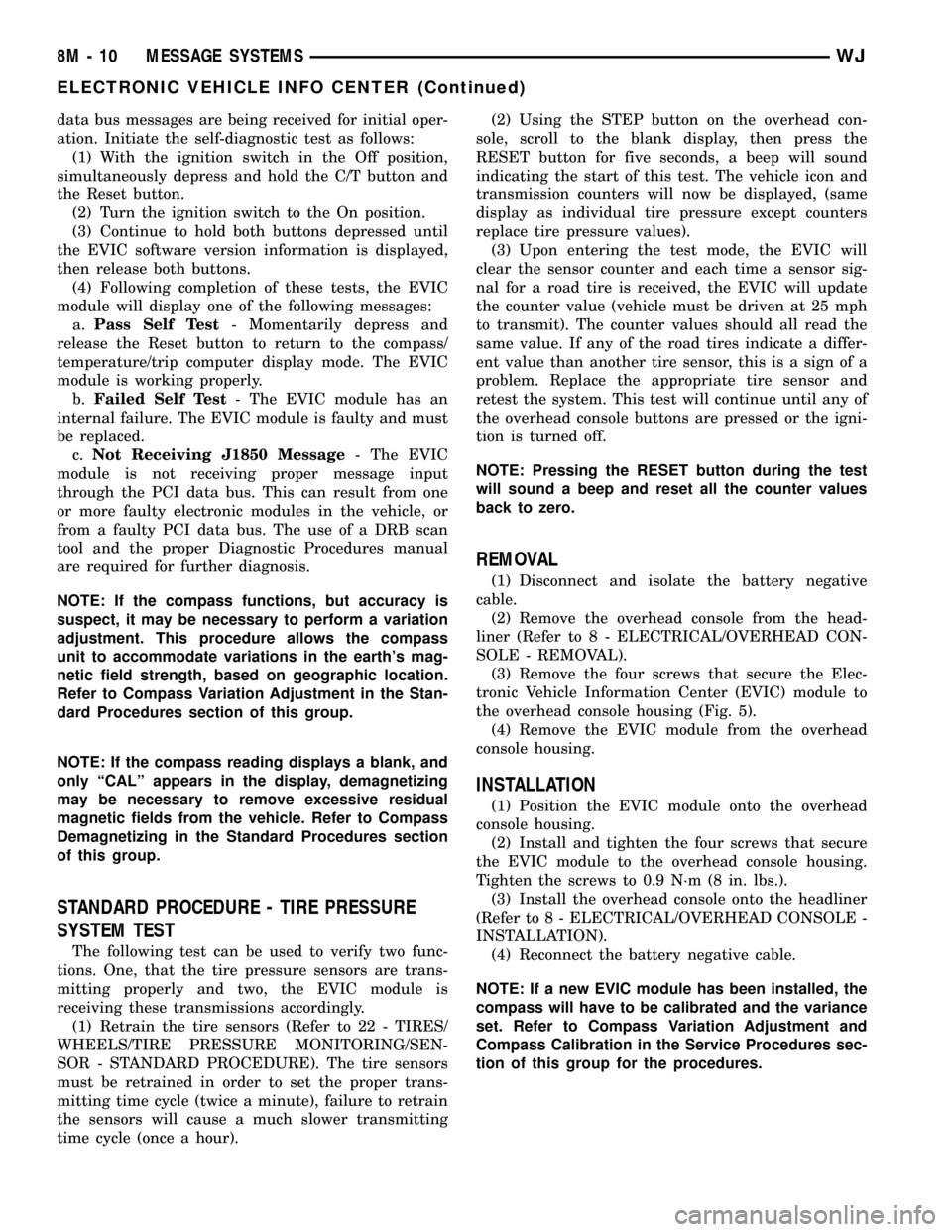
data bus messages are being received for initial oper-
ation. Initiate the self-diagnostic test as follows:
(1) With the ignition switch in the Off position,
simultaneously depress and hold the C/T button and
the Reset button.
(2) Turn the ignition switch to the On position.
(3) Continue to hold both buttons depressed until
the EVIC software version information is displayed,
then release both buttons.
(4) Following completion of these tests, the EVIC
module will display one of the following messages:
a.Pass Self Test- Momentarily depress and
release the Reset button to return to the compass/
temperature/trip computer display mode. The EVIC
module is working properly.
b.Failed Self Test- The EVIC module has an
internal failure. The EVIC module is faulty and must
be replaced.
c.Not Receiving J1850 Message- The EVIC
module is not receiving proper message input
through the PCI data bus. This can result from one
or more faulty electronic modules in the vehicle, or
from a faulty PCI data bus. The use of a DRB scan
tool and the proper Diagnostic Procedures manual
are required for further diagnosis.
NOTE: If the compass functions, but accuracy is
suspect, it may be necessary to perform a variation
adjustment. This procedure allows the compass
unit to accommodate variations in the earth's mag-
netic field strength, based on geographic location.
Refer to Compass Variation Adjustment in the Stan-
dard Procedures section of this group.
NOTE: If the compass reading displays a blank, and
only ªCALº appears in the display, demagnetizing
may be necessary to remove excessive residual
magnetic fields from the vehicle. Refer to Compass
Demagnetizing in the Standard Procedures section
of this group.
STANDARD PROCEDURE - TIRE PRESSURE
SYSTEM TEST
The following test can be used to verify two func-
tions. One, that the tire pressure sensors are trans-
mitting properly and two, the EVIC module is
receiving these transmissions accordingly.
(1) Retrain the tire sensors (Refer to 22 - TIRES/
WHEELS/TIRE PRESSURE MONITORING/SEN-
SOR - STANDARD PROCEDURE). The tire sensors
must be retrained in order to set the proper trans-
mitting time cycle (twice a minute), failure to retrain
the sensors will cause a much slower transmitting
time cycle (once a hour).(2) Using the STEP button on the overhead con-
sole, scroll to the blank display, then press the
RESET button for five seconds, a beep will sound
indicating the start of this test. The vehicle icon and
transmission counters will now be displayed, (same
display as individual tire pressure except counters
replace tire pressure values).
(3) Upon entering the test mode, the EVIC will
clear the sensor counter and each time a sensor sig-
nal for a road tire is received, the EVIC will update
the counter value (vehicle must be driven at 25 mph
to transmit). The counter values should all read the
same value. If any of the road tires indicate a differ-
ent value than another tire sensor, this is a sign of a
problem. Replace the appropriate tire sensor and
retest the system. This test will continue until any of
the overhead console buttons are pressed or the igni-
tion is turned off.
NOTE: Pressing the RESET button during the test
will sound a beep and reset all the counter values
back to zero.
REMOVAL
(1) Disconnect and isolate the battery negative
cable.
(2) Remove the overhead console from the head-
liner (Refer to 8 - ELECTRICAL/OVERHEAD CON-
SOLE - REMOVAL).
(3) Remove the four screws that secure the Elec-
tronic Vehicle Information Center (EVIC) module to
the overhead console housing (Fig. 5).
(4) Remove the EVIC module from the overhead
console housing.
INSTALLATION
(1) Position the EVIC module onto the overhead
console housing.
(2) Install and tighten the four screws that secure
the EVIC module to the overhead console housing.
Tighten the screws to 0.9 N´m (8 in. lbs.).
(3) Install the overhead console onto the headliner
(Refer to 8 - ELECTRICAL/OVERHEAD CONSOLE -
INSTALLATION).
(4) Reconnect the battery negative cable.
NOTE: If a new EVIC module has been installed, the
compass will have to be calibrated and the variance
set. Refer to Compass Variation Adjustment and
Compass Calibration in the Service Procedures sec-
tion of this group for the procedures.
8M - 10 MESSAGE SYSTEMSWJ
ELECTRONIC VEHICLE INFO CENTER (Continued)
Page 506 of 2199
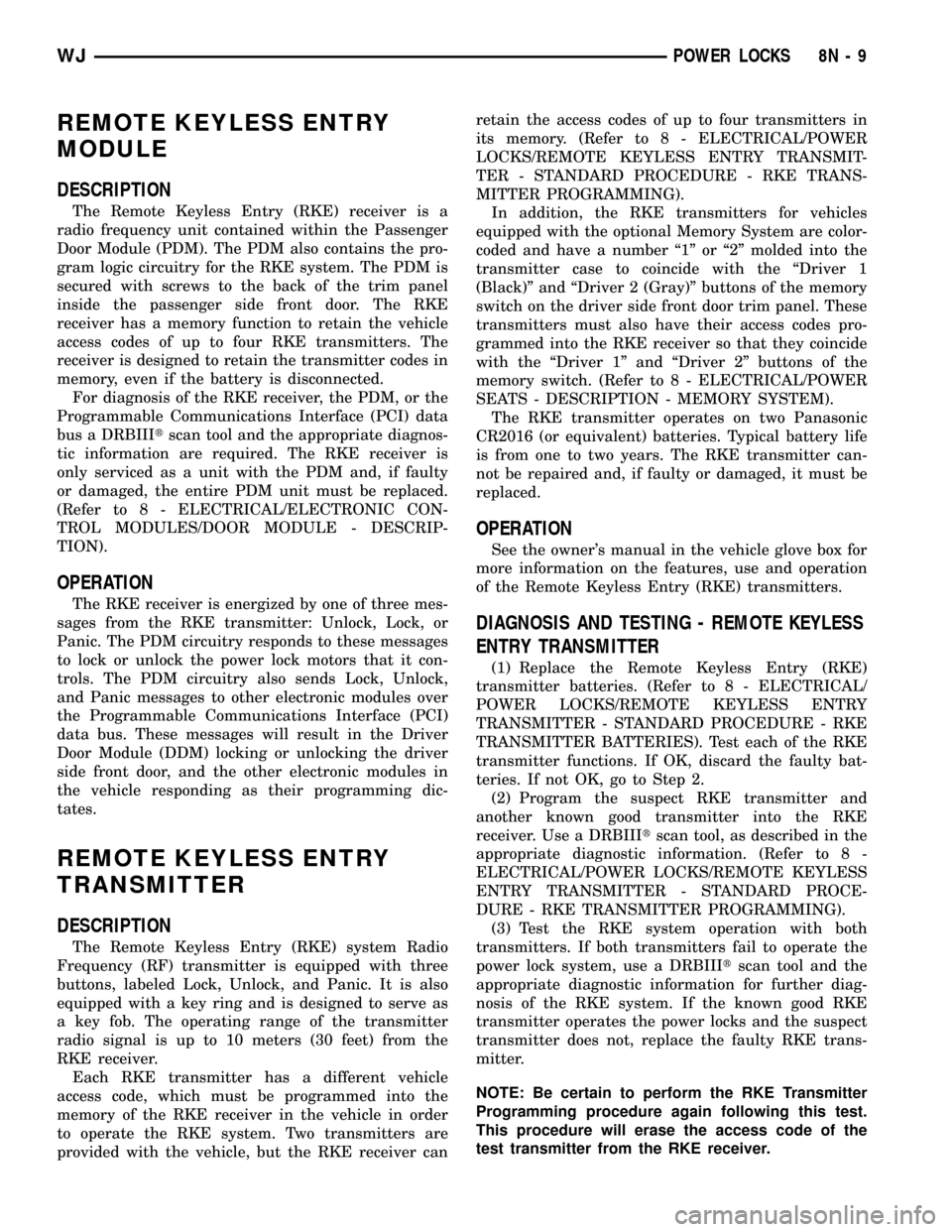
REMOTE KEYLESS ENTRY
MODULE
DESCRIPTION
The Remote Keyless Entry (RKE) receiver is a
radio frequency unit contained within the Passenger
Door Module (PDM). The PDM also contains the pro-
gram logic circuitry for the RKE system. The PDM is
secured with screws to the back of the trim panel
inside the passenger side front door. The RKE
receiver has a memory function to retain the vehicle
access codes of up to four RKE transmitters. The
receiver is designed to retain the transmitter codes in
memory, even if the battery is disconnected.
For diagnosis of the RKE receiver, the PDM, or the
Programmable Communications Interface (PCI) data
bus a DRBIIItscan tool and the appropriate diagnos-
tic information are required. The RKE receiver is
only serviced as a unit with the PDM and, if faulty
or damaged, the entire PDM unit must be replaced.
(Refer to 8 - ELECTRICAL/ELECTRONIC CON-
TROL MODULES/DOOR MODULE - DESCRIP-
TION).
OPERATION
The RKE receiver is energized by one of three mes-
sages from the RKE transmitter: Unlock, Lock, or
Panic. The PDM circuitry responds to these messages
to lock or unlock the power lock motors that it con-
trols. The PDM circuitry also sends Lock, Unlock,
and Panic messages to other electronic modules over
the Programmable Communications Interface (PCI)
data bus. These messages will result in the Driver
Door Module (DDM) locking or unlocking the driver
side front door, and the other electronic modules in
the vehicle responding as their programming dic-
tates.
REMOTE KEYLESS ENTRY
TRANSMITTER
DESCRIPTION
The Remote Keyless Entry (RKE) system Radio
Frequency (RF) transmitter is equipped with three
buttons, labeled Lock, Unlock, and Panic. It is also
equipped with a key ring and is designed to serve as
a key fob. The operating range of the transmitter
radio signal is up to 10 meters (30 feet) from the
RKE receiver.
Each RKE transmitter has a different vehicle
access code, which must be programmed into the
memory of the RKE receiver in the vehicle in order
to operate the RKE system. Two transmitters are
provided with the vehicle, but the RKE receiver canretain the access codes of up to four transmitters in
its memory. (Refer to 8 - ELECTRICAL/POWER
LOCKS/REMOTE KEYLESS ENTRY TRANSMIT-
TER - STANDARD PROCEDURE - RKE TRANS-
MITTER PROGRAMMING).
In addition, the RKE transmitters for vehicles
equipped with the optional Memory System are color-
coded and have a number ª1º or ª2º molded into the
transmitter case to coincide with the ªDriver 1
(Black)º and ªDriver 2 (Gray)º buttons of the memory
switch on the driver side front door trim panel. These
transmitters must also have their access codes pro-
grammed into the RKE receiver so that they coincide
with the ªDriver 1º and ªDriver 2º buttons of the
memory switch. (Refer to 8 - ELECTRICAL/POWER
SEATS - DESCRIPTION - MEMORY SYSTEM).
The RKE transmitter operates on two Panasonic
CR2016 (or equivalent) batteries. Typical battery life
is from one to two years. The RKE transmitter can-
not be repaired and, if faulty or damaged, it must be
replaced.
OPERATION
See the owner's manual in the vehicle glove box for
more information on the features, use and operation
of the Remote Keyless Entry (RKE) transmitters.
DIAGNOSIS AND TESTING - REMOTE KEYLESS
ENTRY TRANSMITTER
(1) Replace the Remote Keyless Entry (RKE)
transmitter batteries. (Refer to 8 - ELECTRICAL/
POWER LOCKS/REMOTE KEYLESS ENTRY
TRANSMITTER - STANDARD PROCEDURE - RKE
TRANSMITTER BATTERIES). Test each of the RKE
transmitter functions. If OK, discard the faulty bat-
teries. If not OK, go to Step 2.
(2) Program the suspect RKE transmitter and
another known good transmitter into the RKE
receiver. Use a DRBIIItscan tool, as described in the
appropriate diagnostic information. (Refer to 8 -
ELECTRICAL/POWER LOCKS/REMOTE KEYLESS
ENTRY TRANSMITTER - STANDARD PROCE-
DURE - RKE TRANSMITTER PROGRAMMING).
(3) Test the RKE system operation with both
transmitters. If both transmitters fail to operate the
power lock system, use a DRBIIItscan tool and the
appropriate diagnostic information for further diag-
nosis of the RKE system. If the known good RKE
transmitter operates the power locks and the suspect
transmitter does not, replace the faulty RKE trans-
mitter.
NOTE: Be certain to perform the RKE Transmitter
Programming procedure again following this test.
This procedure will erase the access code of the
test transmitter from the RKE receiver.
WJPOWER LOCKS 8N - 9
Page 523 of 2199
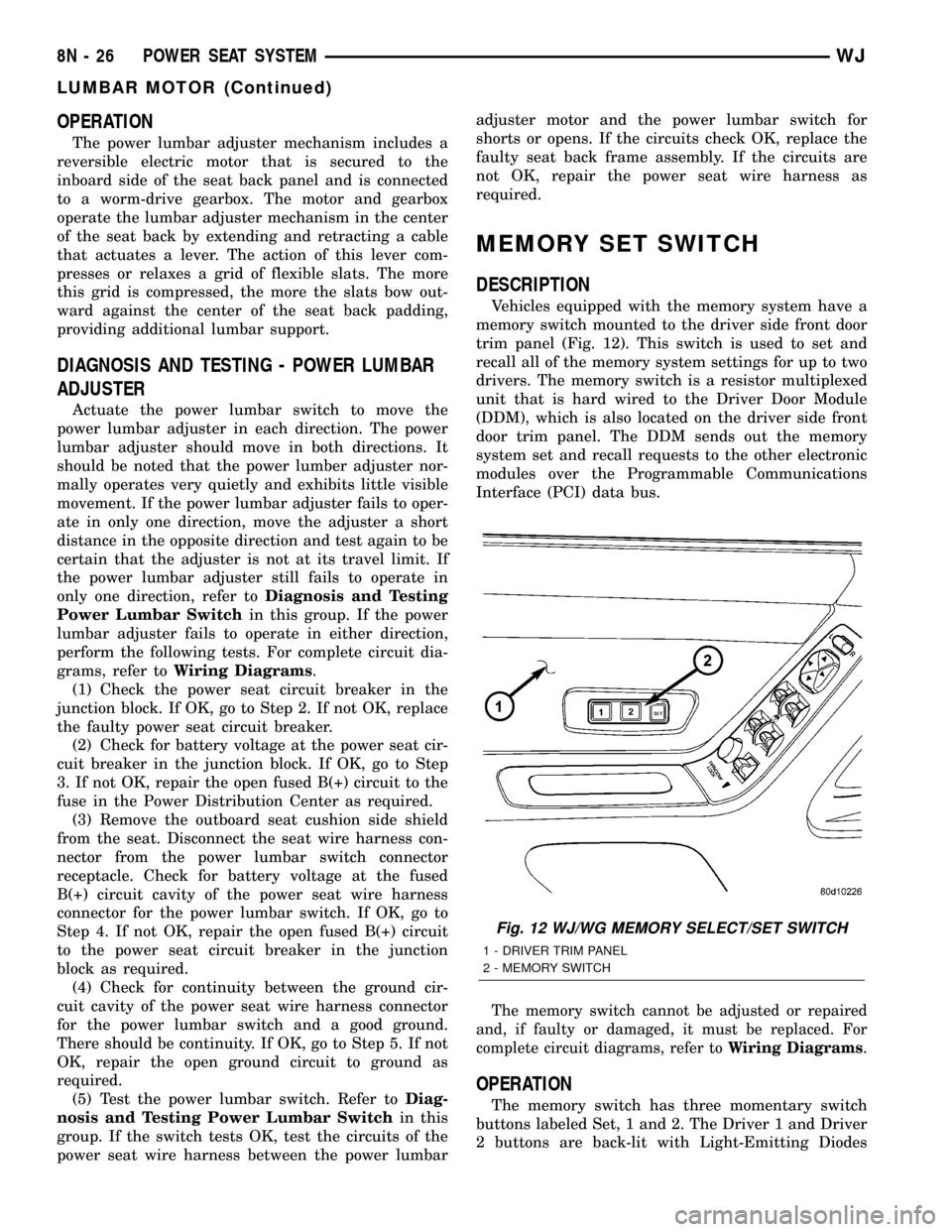
OPERATION
The power lumbar adjuster mechanism includes a
reversible electric motor that is secured to the
inboard side of the seat back panel and is connected
to a worm-drive gearbox. The motor and gearbox
operate the lumbar adjuster mechanism in the center
of the seat back by extending and retracting a cable
that actuates a lever. The action of this lever com-
presses or relaxes a grid of flexible slats. The more
this grid is compressed, the more the slats bow out-
ward against the center of the seat back padding,
providing additional lumbar support.
DIAGNOSIS AND TESTING - POWER LUMBAR
ADJUSTER
Actuate the power lumbar switch to move the
power lumbar adjuster in each direction. The power
lumbar adjuster should move in both directions. It
should be noted that the power lumber adjuster nor-
mally operates very quietly and exhibits little visible
movement. If the power lumbar adjuster fails to oper-
ate in only one direction, move the adjuster a short
distance in the opposite direction and test again to be
certain that the adjuster is not at its travel limit. If
the power lumbar adjuster still fails to operate in
only one direction, refer toDiagnosis and Testing
Power Lumbar Switchin this group. If the power
lumbar adjuster fails to operate in either direction,
perform the following tests. For complete circuit dia-
grams, refer toWiring Diagrams.
(1) Check the power seat circuit breaker in the
junction block. If OK, go to Step 2. If not OK, replace
the faulty power seat circuit breaker.
(2) Check for battery voltage at the power seat cir-
cuit breaker in the junction block. If OK, go to Step
3. If not OK, repair the open fused B(+) circuit to the
fuse in the Power Distribution Center as required.
(3) Remove the outboard seat cushion side shield
from the seat. Disconnect the seat wire harness con-
nector from the power lumbar switch connector
receptacle. Check for battery voltage at the fused
B(+) circuit cavity of the power seat wire harness
connector for the power lumbar switch. If OK, go to
Step 4. If not OK, repair the open fused B(+) circuit
to the power seat circuit breaker in the junction
block as required.
(4) Check for continuity between the ground cir-
cuit cavity of the power seat wire harness connector
for the power lumbar switch and a good ground.
There should be continuity. If OK, go to Step 5. If not
OK, repair the open ground circuit to ground as
required.
(5) Test the power lumbar switch. Refer toDiag-
nosis and Testing Power Lumbar Switchin this
group. If the switch tests OK, test the circuits of the
power seat wire harness between the power lumbaradjuster motor and the power lumbar switch for
shorts or opens. If the circuits check OK, replace the
faulty seat back frame assembly. If the circuits are
not OK, repair the power seat wire harness as
required.
MEMORY SET SWITCH
DESCRIPTION
Vehicles equipped with the memory system have a
memory switch mounted to the driver side front door
trim panel (Fig. 12). This switch is used to set and
recall all of the memory system settings for up to two
drivers. The memory switch is a resistor multiplexed
unit that is hard wired to the Driver Door Module
(DDM), which is also located on the driver side front
door trim panel. The DDM sends out the memory
system set and recall requests to the other electronic
modules over the Programmable Communications
Interface (PCI) data bus.
The memory switch cannot be adjusted or repaired
and, if faulty or damaged, it must be replaced. For
complete circuit diagrams, refer toWiring Diagrams
.
OPERATION
The memory switch has three momentary switch
buttons labeled Set, 1 and 2. The Driver 1 and Driver
2 buttons are back-lit with Light-Emitting Diodes
Fig. 12 WJ/WG MEMORY SELECT/SET SWITCH
1 - DRIVER TRIM PANEL
2 - MEMORY SWITCH
8N - 26 POWER SEAT SYSTEMWJ
LUMBAR MOTOR (Continued)
Page 1429 of 2199
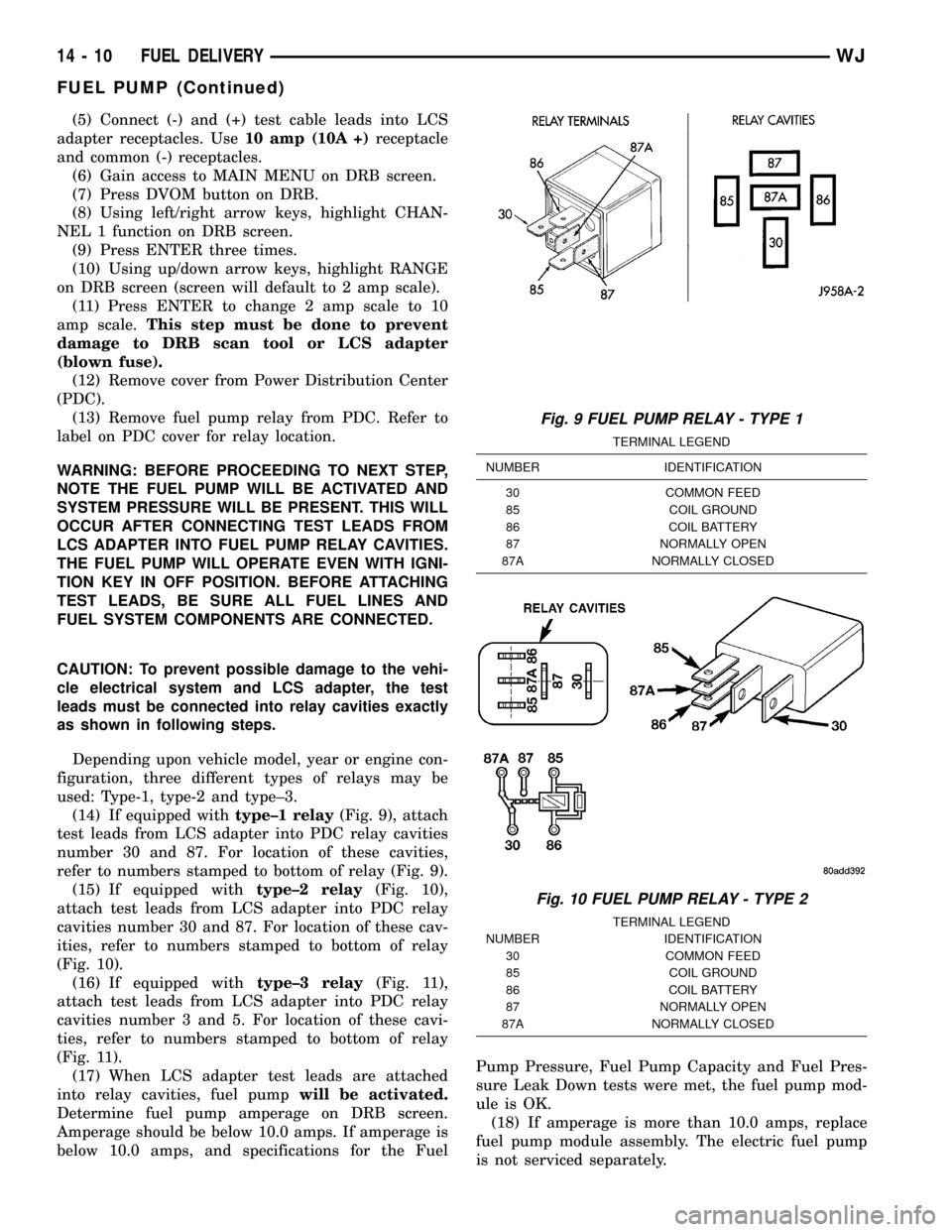
(5) Connect (-) and (+) test cable leads into LCS
adapter receptacles. Use10 amp (10A +)receptacle
and common (-) receptacles.
(6) Gain access to MAIN MENU on DRB screen.
(7) Press DVOM button on DRB.
(8) Using left/right arrow keys, highlight CHAN-
NEL 1 function on DRB screen.
(9) Press ENTER three times.
(10) Using up/down arrow keys, highlight RANGE
on DRB screen (screen will default to 2 amp scale).
(11) Press ENTER to change 2 amp scale to 10
amp scale.This step must be done to prevent
damage to DRB scan tool or LCS adapter
(blown fuse).
(12) Remove cover from Power Distribution Center
(PDC).
(13) Remove fuel pump relay from PDC. Refer to
label on PDC cover for relay location.
WARNING: BEFORE PROCEEDING TO NEXT STEP,
NOTE THE FUEL PUMP WILL BE ACTIVATED AND
SYSTEM PRESSURE WILL BE PRESENT. THIS WILL
OCCUR AFTER CONNECTING TEST LEADS FROM
LCS ADAPTER INTO FUEL PUMP RELAY CAVITIES.
THE FUEL PUMP WILL OPERATE EVEN WITH IGNI-
TION KEY IN OFF POSITION. BEFORE ATTACHING
TEST LEADS, BE SURE ALL FUEL LINES AND
FUEL SYSTEM COMPONENTS ARE CONNECTED.
CAUTION: To prevent possible damage to the vehi-
cle electrical system and LCS adapter, the test
leads must be connected into relay cavities exactly
as shown in following steps.
Depending upon vehicle model, year or engine con-
figuration, three different types of relays may be
used: Type-1, type-2 and type±3.
(14) If equipped withtype±1 relay(Fig. 9), attach
test leads from LCS adapter into PDC relay cavities
number 30 and 87. For location of these cavities,
refer to numbers stamped to bottom of relay (Fig. 9).
(15) If equipped withtype±2 relay(Fig. 10),
attach test leads from LCS adapter into PDC relay
cavities number 30 and 87. For location of these cav-
ities, refer to numbers stamped to bottom of relay
(Fig. 10).
(16) If equipped withtype±3 relay(Fig. 11),
attach test leads from LCS adapter into PDC relay
cavities number 3 and 5. For location of these cavi-
ties, refer to numbers stamped to bottom of relay
(Fig. 11).
(17) When LCS adapter test leads are attached
into relay cavities, fuel pumpwill be activated.
Determine fuel pump amperage on DRB screen.
Amperage should be below 10.0 amps. If amperage is
below 10.0 amps, and specifications for the FuelPump Pressure, Fuel Pump Capacity and Fuel Pres-
sure Leak Down tests were met, the fuel pump mod-
ule is OK.
(18) If amperage is more than 10.0 amps, replace
fuel pump module assembly. The electric fuel pump
is not serviced separately.
Fig. 9 FUEL PUMP RELAY - TYPE 1
TERMINAL LEGEND
NUMBER IDENTIFICATION
30 COMMON FEED
85 COIL GROUND
86 COIL BATTERY
87 NORMALLY OPEN
87A NORMALLY CLOSED
Fig. 10 FUEL PUMP RELAY - TYPE 2
TERMINAL LEGEND
NUMBER IDENTIFICATION
30 COMMON FEED
85 COIL GROUND
86 COIL BATTERY
87 NORMALLY OPEN
87A NORMALLY CLOSED
14 - 10 FUEL DELIVERYWJ
FUEL PUMP (Continued)