connector JEEP GRAND CHEROKEE 2002 WJ / 2.G Workshop Manual
[x] Cancel search | Manufacturer: JEEP, Model Year: 2002, Model line: GRAND CHEROKEE, Model: JEEP GRAND CHEROKEE 2002 WJ / 2.GPages: 2199, PDF Size: 76.01 MB
Page 585 of 2199
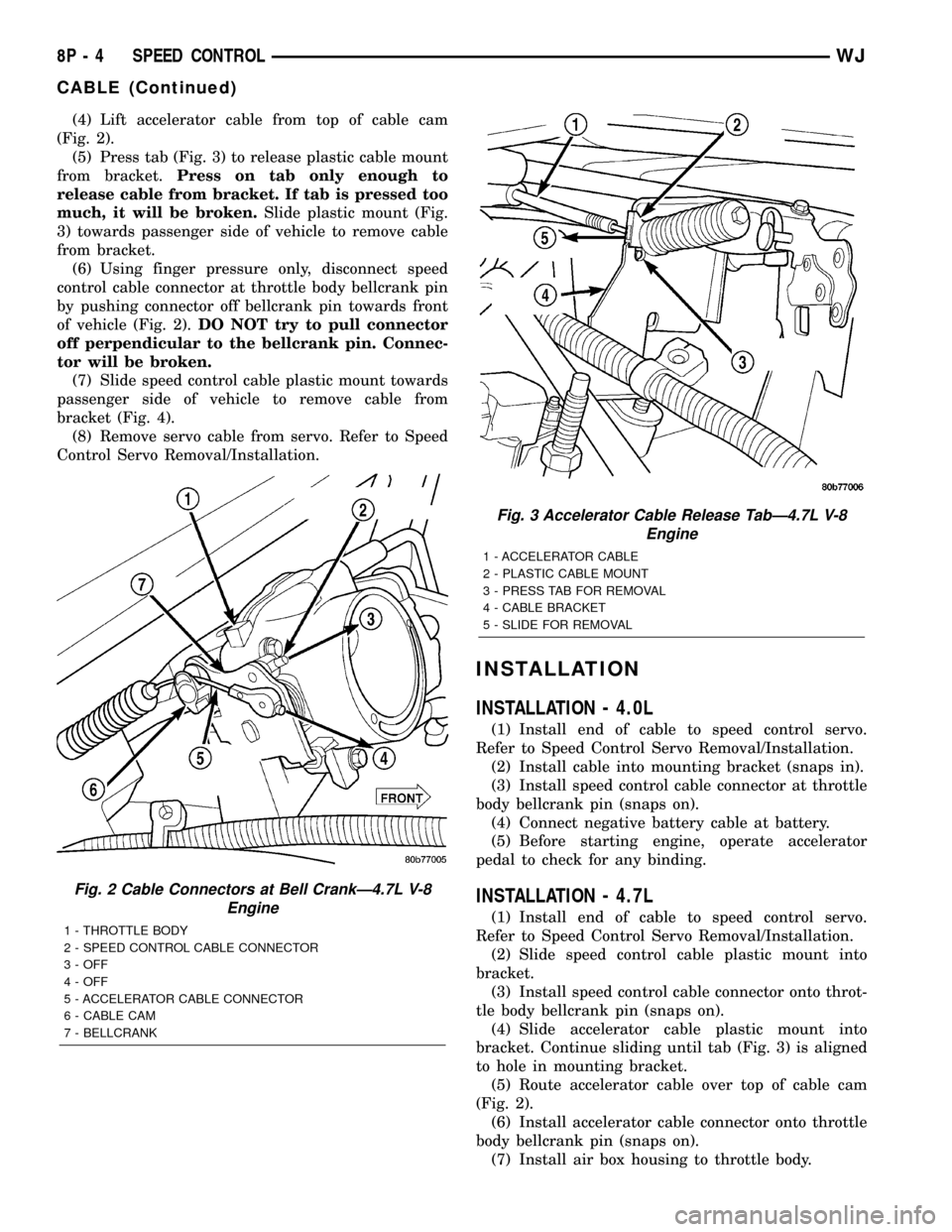
(4) Lift accelerator cable from top of cable cam
(Fig. 2).
(5) Press tab (Fig. 3) to release plastic cable mount
from bracket.Press on tab only enough to
release cable from bracket. If tab is pressed too
much, it will be broken.Slide plastic mount (Fig.
3) towards passenger side of vehicle to remove cable
from bracket.
(6) Using finger pressure only, disconnect speed
control cable connector at throttle body bellcrank pin
by pushing connector off bellcrank pin towards front
of vehicle (Fig. 2).DO NOT try to pull connector
off perpendicular to the bellcrank pin. Connec-
tor will be broken.
(7) Slide speed control cable plastic mount towards
passenger side of vehicle to remove cable from
bracket (Fig. 4).
(8) Remove servo cable from servo. Refer to Speed
Control Servo Removal/Installation.
INSTALLATION
INSTALLATION - 4.0L
(1) Install end of cable to speed control servo.
Refer to Speed Control Servo Removal/Installation.
(2) Install cable into mounting bracket (snaps in).
(3) Install speed control cable connector at throttle
body bellcrank pin (snaps on).
(4) Connect negative battery cable at battery.
(5) Before starting engine, operate accelerator
pedal to check for any binding.
INSTALLATION - 4.7L
(1) Install end of cable to speed control servo.
Refer to Speed Control Servo Removal/Installation.
(2) Slide speed control cable plastic mount into
bracket.
(3) Install speed control cable connector onto throt-
tle body bellcrank pin (snaps on).
(4) Slide accelerator cable plastic mount into
bracket. Continue sliding until tab (Fig. 3) is aligned
to hole in mounting bracket.
(5) Route accelerator cable over top of cable cam
(Fig. 2).
(6) Install accelerator cable connector onto throttle
body bellcrank pin (snaps on).
(7) Install air box housing to throttle body.
Fig. 2 Cable Connectors at Bell CrankÐ4.7L V-8
Engine
1 - THROTTLE BODY
2 - SPEED CONTROL CABLE CONNECTOR
3 - OFF
4 - OFF
5 - ACCELERATOR CABLE CONNECTOR
6 - CABLE CAM
7 - BELLCRANK
Fig. 3 Accelerator Cable Release TabÐ4.7L V-8
Engine
1 - ACCELERATOR CABLE
2 - PLASTIC CABLE MOUNT
3 - PRESS TAB FOR REMOVAL
4 - CABLE BRACKET
5 - SLIDE FOR REMOVAL
8P - 4 SPEED CONTROLWJ
CABLE (Continued)
Page 586 of 2199
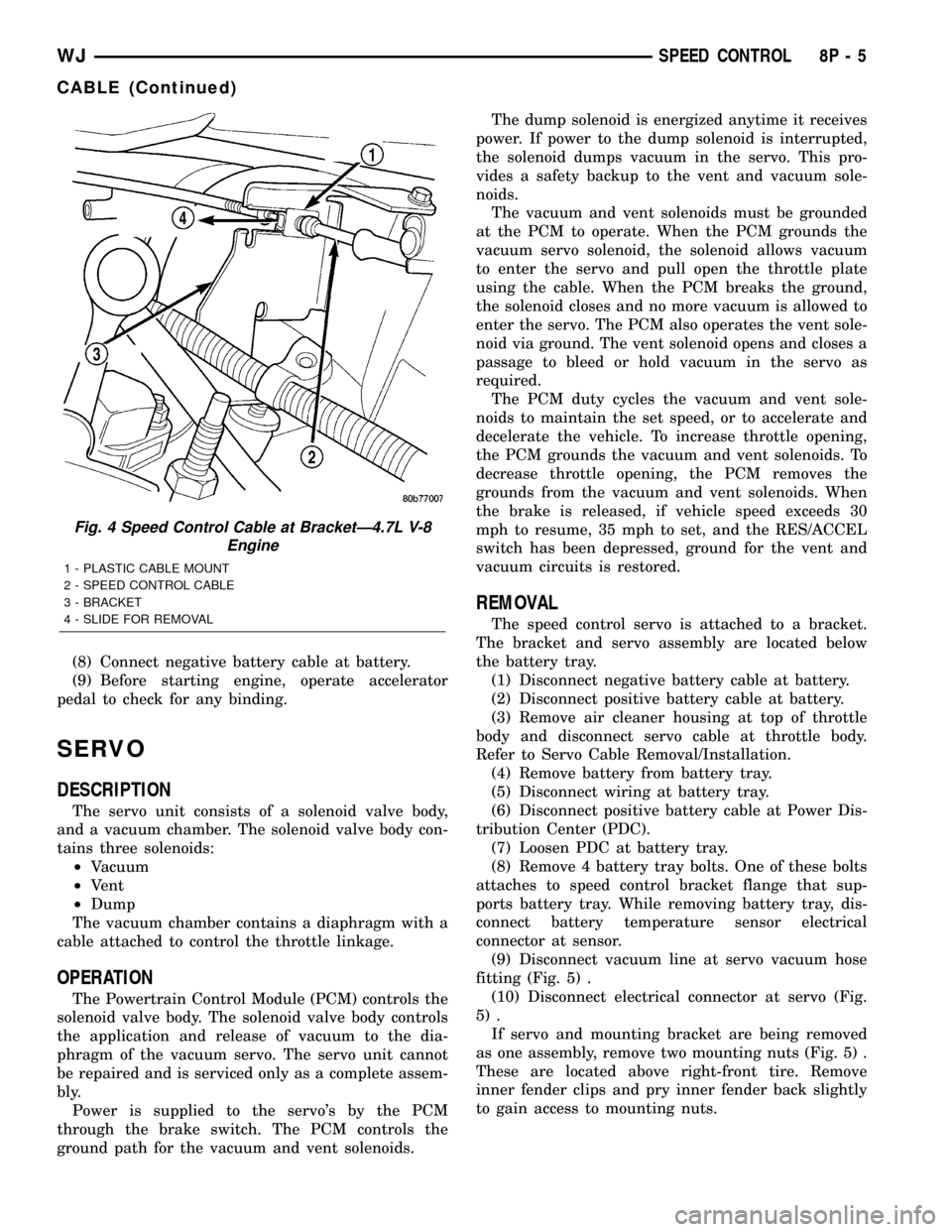
(8) Connect negative battery cable at battery.
(9) Before starting engine, operate accelerator
pedal to check for any binding.
SERVO
DESCRIPTION
The servo unit consists of a solenoid valve body,
and a vacuum chamber. The solenoid valve body con-
tains three solenoids:
²Vacuum
²Vent
²Dump
The vacuum chamber contains a diaphragm with a
cable attached to control the throttle linkage.
OPERATION
The Powertrain Control Module (PCM) controls the
solenoid valve body. The solenoid valve body controls
the application and release of vacuum to the dia-
phragm of the vacuum servo. The servo unit cannot
be repaired and is serviced only as a complete assem-
bly.
Power is supplied to the servo's by the PCM
through the brake switch. The PCM controls the
ground path for the vacuum and vent solenoids.The dump solenoid is energized anytime it receives
power. If power to the dump solenoid is interrupted,
the solenoid dumps vacuum in the servo. This pro-
vides a safety backup to the vent and vacuum sole-
noids.
The vacuum and vent solenoids must be grounded
at the PCM to operate. When the PCM grounds the
vacuum servo solenoid, the solenoid allows vacuum
to enter the servo and pull open the throttle plate
using the cable. When the PCM breaks the ground,
the solenoid closes and no more vacuum is allowed to
enter the servo. The PCM also operates the vent sole-
noid via ground. The vent solenoid opens and closes a
passage to bleed or hold vacuum in the servo as
required.
The PCM duty cycles the vacuum and vent sole-
noids to maintain the set speed, or to accelerate and
decelerate the vehicle. To increase throttle opening,
the PCM grounds the vacuum and vent solenoids. To
decrease throttle opening, the PCM removes the
grounds from the vacuum and vent solenoids. When
the brake is released, if vehicle speed exceeds 30
mph to resume, 35 mph to set, and the RES/ACCEL
switch has been depressed, ground for the vent and
vacuum circuits is restored.
REMOVAL
The speed control servo is attached to a bracket.
The bracket and servo assembly are located below
the battery tray.
(1) Disconnect negative battery cable at battery.
(2) Disconnect positive battery cable at battery.
(3) Remove air cleaner housing at top of throttle
body and disconnect servo cable at throttle body.
Refer to Servo Cable Removal/Installation.
(4) Remove battery from battery tray.
(5) Disconnect wiring at battery tray.
(6) Disconnect positive battery cable at Power Dis-
tribution Center (PDC).
(7) Loosen PDC at battery tray.
(8) Remove 4 battery tray bolts. One of these bolts
attaches to speed control bracket flange that sup-
ports battery tray. While removing battery tray, dis-
connect battery temperature sensor electrical
connector at sensor.
(9) Disconnect vacuum line at servo vacuum hose
fitting (Fig. 5) .
(10) Disconnect electrical connector at servo (Fig.
5) .
If servo and mounting bracket are being removed
as one assembly, remove two mounting nuts (Fig. 5) .
These are located above right-front tire. Remove
inner fender clips and pry inner fender back slightly
to gain access to mounting nuts.
Fig. 4 Speed Control Cable at BracketÐ4.7L V-8
Engine
1 - PLASTIC CABLE MOUNT
2 - SPEED CONTROL CABLE
3 - BRACKET
4 - SLIDE FOR REMOVAL
WJSPEED CONTROL 8P - 5
CABLE (Continued)
Page 587 of 2199
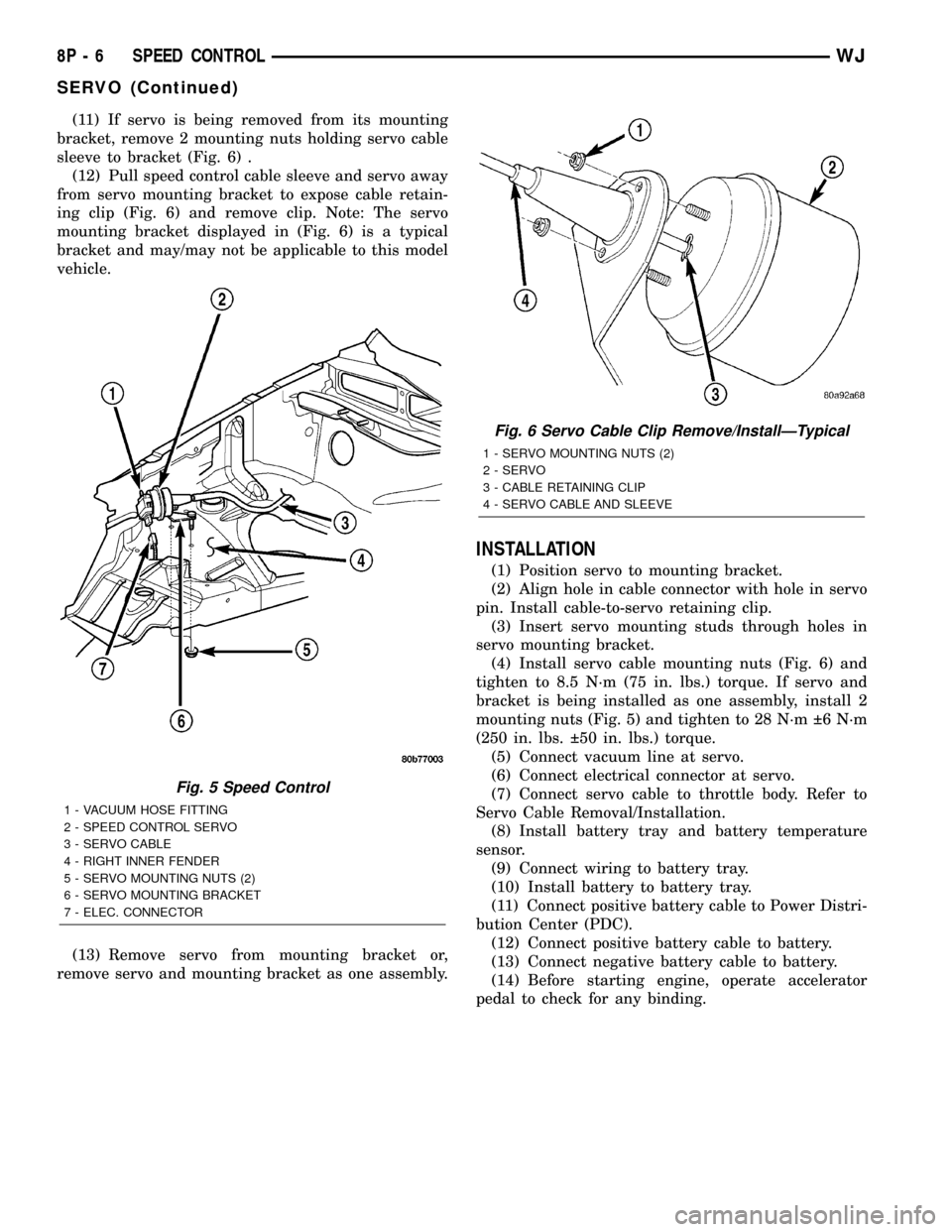
(11) If servo is being removed from its mounting
bracket, remove 2 mounting nuts holding servo cable
sleeve to bracket (Fig. 6) .
(12) Pull speed control cable sleeve and servo away
from servo mounting bracket to expose cable retain-
ing clip (Fig. 6) and remove clip. Note: The servo
mounting bracket displayed in (Fig. 6) is a typical
bracket and may/may not be applicable to this model
vehicle.
(13) Remove servo from mounting bracket or,
remove servo and mounting bracket as one assembly.
INSTALLATION
(1) Position servo to mounting bracket.
(2) Align hole in cable connector with hole in servo
pin. Install cable-to-servo retaining clip.
(3) Insert servo mounting studs through holes in
servo mounting bracket.
(4) Install servo cable mounting nuts (Fig. 6) and
tighten to 8.5 N´m (75 in. lbs.) torque. If servo and
bracket is being installed as one assembly, install 2
mounting nuts (Fig. 5) and tighten to 28 N´m 6 N´m
(250 in. lbs. 50 in. lbs.) torque.
(5) Connect vacuum line at servo.
(6) Connect electrical connector at servo.
(7) Connect servo cable to throttle body. Refer to
Servo Cable Removal/Installation.
(8) Install battery tray and battery temperature
sensor.
(9) Connect wiring to battery tray.
(10) Install battery to battery tray.
(11) Connect positive battery cable to Power Distri-
bution Center (PDC).
(12) Connect positive battery cable to battery.
(13) Connect negative battery cable to battery.
(14) Before starting engine, operate accelerator
pedal to check for any binding.
Fig. 5 Speed Control
1 - VACUUM HOSE FITTING
2 - SPEED CONTROL SERVO
3 - SERVO CABLE
4 - RIGHT INNER FENDER
5 - SERVO MOUNTING NUTS (2)
6 - SERVO MOUNTING BRACKET
7 - ELEC. CONNECTOR
Fig. 6 Servo Cable Clip Remove/InstallÐTypical
1 - SERVO MOUNTING NUTS (2)
2 - SERVO
3 - CABLE RETAINING CLIP
4 - SERVO CABLE AND SLEEVE
8P - 6 SPEED CONTROLWJ
SERVO (Continued)
Page 588 of 2199
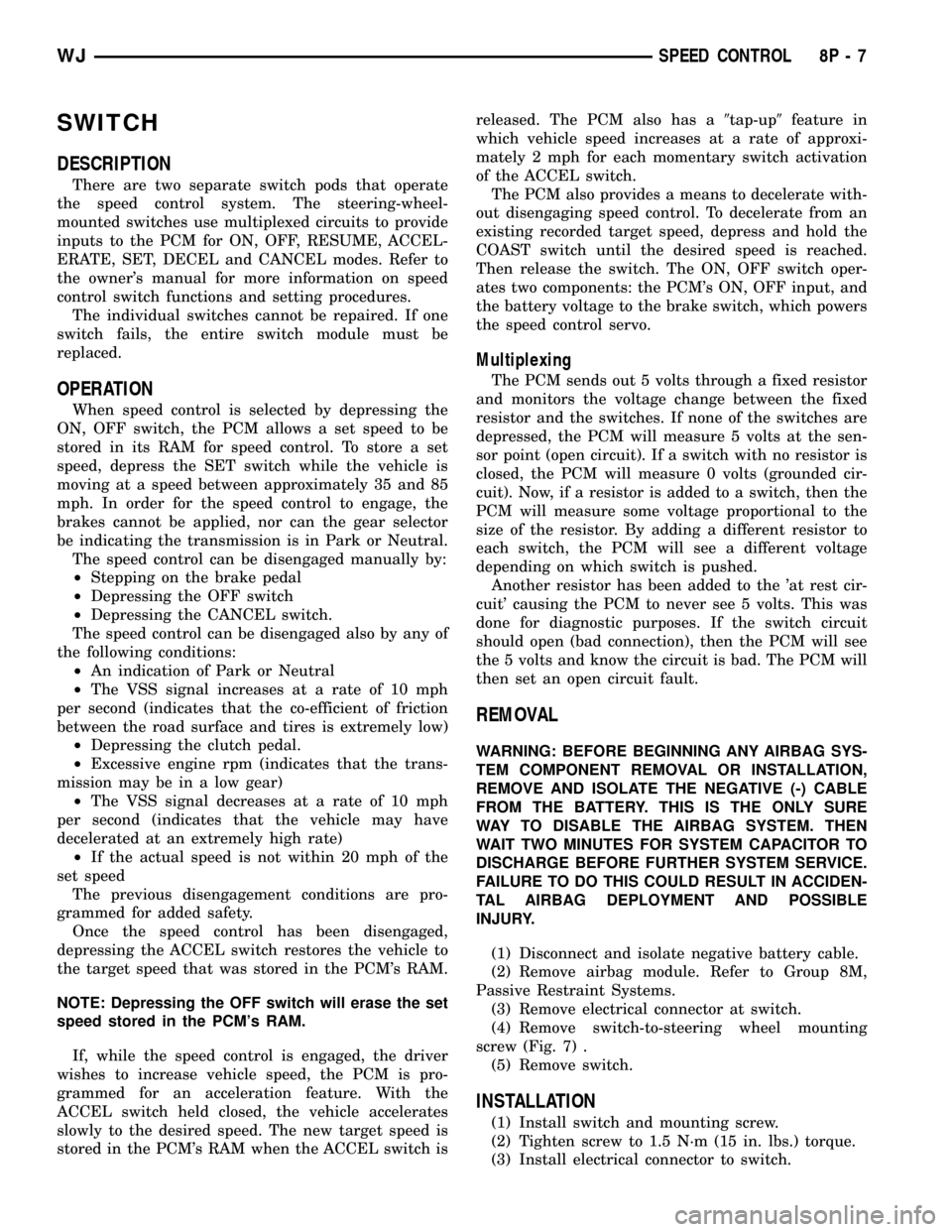
SWITCH
DESCRIPTION
There are two separate switch pods that operate
the speed control system. The steering-wheel-
mounted switches use multiplexed circuits to provide
inputs to the PCM for ON, OFF, RESUME, ACCEL-
ERATE, SET, DECEL and CANCEL modes. Refer to
the owner's manual for more information on speed
control switch functions and setting procedures.
The individual switches cannot be repaired. If one
switch fails, the entire switch module must be
replaced.
OPERATION
When speed control is selected by depressing the
ON, OFF switch, the PCM allows a set speed to be
stored in its RAM for speed control. To store a set
speed, depress the SET switch while the vehicle is
moving at a speed between approximately 35 and 85
mph. In order for the speed control to engage, the
brakes cannot be applied, nor can the gear selector
be indicating the transmission is in Park or Neutral.
The speed control can be disengaged manually by:
²Stepping on the brake pedal
²Depressing the OFF switch
²Depressing the CANCEL switch.
The speed control can be disengaged also by any of
the following conditions:
²An indication of Park or Neutral
²The VSS signal increases at a rate of 10 mph
per second (indicates that the co-efficient of friction
between the road surface and tires is extremely low)
²Depressing the clutch pedal.
²Excessive engine rpm (indicates that the trans-
mission may be in a low gear)
²The VSS signal decreases at a rate of 10 mph
per second (indicates that the vehicle may have
decelerated at an extremely high rate)
²If the actual speed is not within 20 mph of the
set speed
The previous disengagement conditions are pro-
grammed for added safety.
Once the speed control has been disengaged,
depressing the ACCEL switch restores the vehicle to
the target speed that was stored in the PCM's RAM.
NOTE: Depressing the OFF switch will erase the set
speed stored in the PCM's RAM.
If, while the speed control is engaged, the driver
wishes to increase vehicle speed, the PCM is pro-
grammed for an acceleration feature. With the
ACCEL switch held closed, the vehicle accelerates
slowly to the desired speed. The new target speed is
stored in the PCM's RAM when the ACCEL switch isreleased. The PCM also has a9tap-up9feature in
which vehicle speed increases at a rate of approxi-
mately 2 mph for each momentary switch activation
of the ACCEL switch.
The PCM also provides a means to decelerate with-
out disengaging speed control. To decelerate from an
existing recorded target speed, depress and hold the
COAST switch until the desired speed is reached.
Then release the switch. The ON, OFF switch oper-
ates two components: the PCM's ON, OFF input, and
the battery voltage to the brake switch, which powers
the speed control servo.
Multiplexing
The PCM sends out 5 volts through a fixed resistor
and monitors the voltage change between the fixed
resistor and the switches. If none of the switches are
depressed, the PCM will measure 5 volts at the sen-
sor point (open circuit). If a switch with no resistor is
closed, the PCM will measure 0 volts (grounded cir-
cuit). Now, if a resistor is added to a switch, then the
PCM will measure some voltage proportional to the
size of the resistor. By adding a different resistor to
each switch, the PCM will see a different voltage
depending on which switch is pushed.
Another resistor has been added to the 'at rest cir-
cuit' causing the PCM to never see 5 volts. This was
done for diagnostic purposes. If the switch circuit
should open (bad connection), then the PCM will see
the 5 volts and know the circuit is bad. The PCM will
then set an open circuit fault.
REMOVAL
WARNING: BEFORE BEGINNING ANY AIRBAG SYS-
TEM COMPONENT REMOVAL OR INSTALLATION,
REMOVE AND ISOLATE THE NEGATIVE (-) CABLE
FROM THE BATTERY. THIS IS THE ONLY SURE
WAY TO DISABLE THE AIRBAG SYSTEM. THEN
WAIT TWO MINUTES FOR SYSTEM CAPACITOR TO
DISCHARGE BEFORE FURTHER SYSTEM SERVICE.
FAILURE TO DO THIS COULD RESULT IN ACCIDEN-
TAL AIRBAG DEPLOYMENT AND POSSIBLE
INJURY.
(1) Disconnect and isolate negative battery cable.
(2) Remove airbag module. Refer to Group 8M,
Passive Restraint Systems.
(3) Remove electrical connector at switch.
(4) Remove switch-to-steering wheel mounting
screw (Fig. 7) .
(5) Remove switch.
INSTALLATION
(1) Install switch and mounting screw.
(2) Tighten screw to 1.5 N´m (15 in. lbs.) torque.
(3) Install electrical connector to switch.
WJSPEED CONTROL 8P - 7
Page 596 of 2199
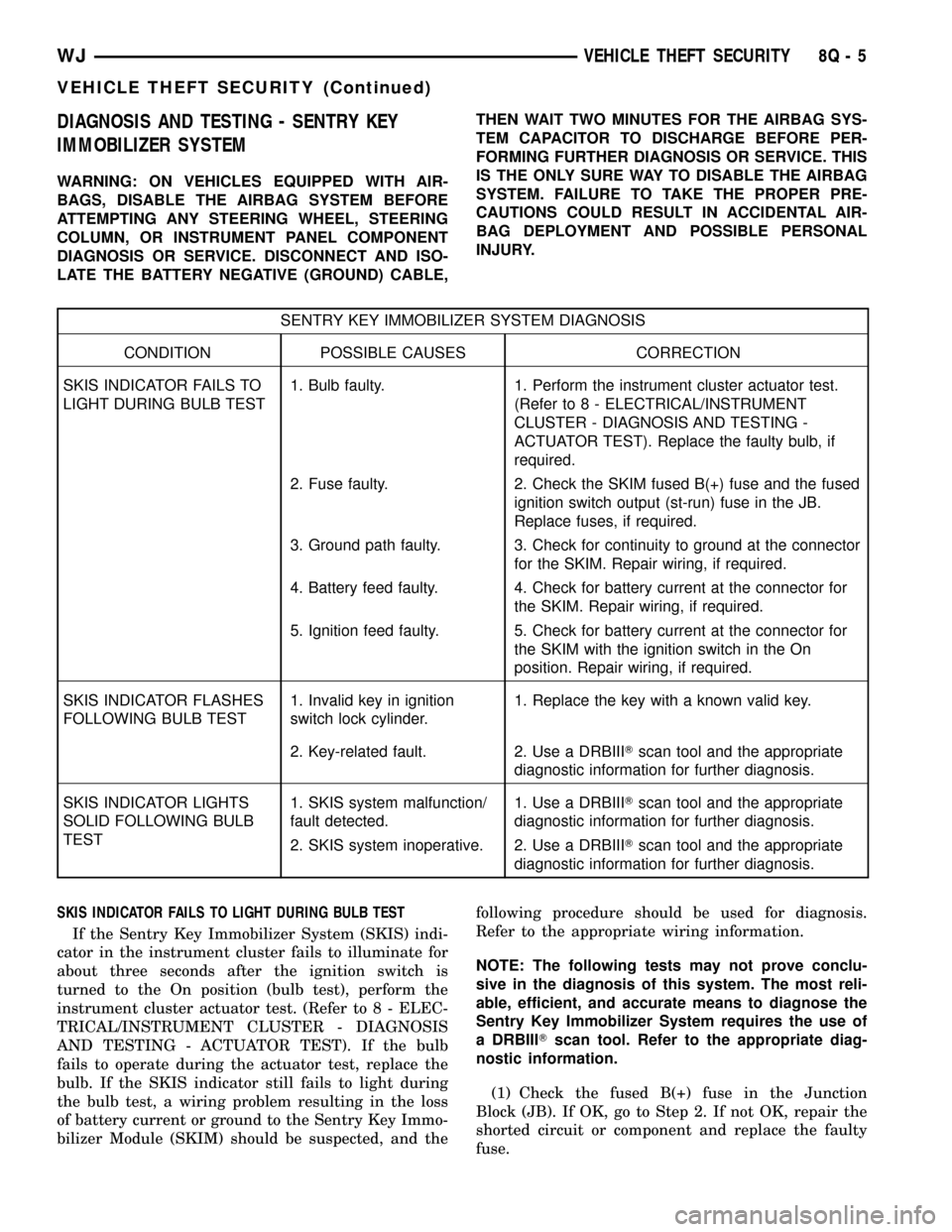
DIAGNOSIS AND TESTING - SENTRY KEY
IMMOBILIZER SYSTEM
WARNING: ON VEHICLES EQUIPPED WITH AIR-
BAGS, DISABLE THE AIRBAG SYSTEM BEFORE
ATTEMPTING ANY STEERING WHEEL, STEERING
COLUMN, OR INSTRUMENT PANEL COMPONENT
DIAGNOSIS OR SERVICE. DISCONNECT AND ISO-
LATE THE BATTERY NEGATIVE (GROUND) CABLE,THEN WAIT TWO MINUTES FOR THE AIRBAG SYS-
TEM CAPACITOR TO DISCHARGE BEFORE PER-
FORMING FURTHER DIAGNOSIS OR SERVICE. THIS
IS THE ONLY SURE WAY TO DISABLE THE AIRBAG
SYSTEM. FAILURE TO TAKE THE PROPER PRE-
CAUTIONS COULD RESULT IN ACCIDENTAL AIR-
BAG DEPLOYMENT AND POSSIBLE PERSONAL
INJURY.
SENTRY KEY IMMOBILIZER SYSTEM DIAGNOSIS
CONDITION POSSIBLE CAUSES CORRECTION
SKIS INDICATOR FAILS TO
LIGHT DURING BULB TEST1. Bulb faulty. 1. Perform the instrument cluster actuator test.
(Refer to 8 - ELECTRICAL/INSTRUMENT
CLUSTER - DIAGNOSIS AND TESTING -
ACTUATOR TEST). Replace the faulty bulb, if
required.
2. Fuse faulty. 2. Check the SKIM fused B(+) fuse and the fused
ignition switch output (st-run) fuse in the JB.
Replace fuses, if required.
3. Ground path faulty. 3. Check for continuity to ground at the connector
for the SKIM. Repair wiring, if required.
4. Battery feed faulty. 4. Check for battery current at the connector for
the SKIM. Repair wiring, if required.
5. Ignition feed faulty. 5. Check for battery current at the connector for
the SKIM with the ignition switch in the On
position. Repair wiring, if required.
SKIS INDICATOR FLASHES
FOLLOWING BULB TEST1. Invalid key in ignition
switch lock cylinder.1. Replace the key with a known valid key.
2. Key-related fault. 2. Use a DRBIIITscan tool and the appropriate
diagnostic information for further diagnosis.
SKIS INDICATOR LIGHTS
SOLID FOLLOWING BULB
TEST1. SKIS system malfunction/
fault detected.1. Use a DRBIIITscan tool and the appropriate
diagnostic information for further diagnosis.
2. SKIS system inoperative. 2. Use a DRBIIITscan tool and the appropriate
diagnostic information for further diagnosis.
SKIS INDICATOR FAILS TO LIGHT DURING BULB TEST
If the Sentry Key Immobilizer System (SKIS) indi-
cator in the instrument cluster fails to illuminate for
about three seconds after the ignition switch is
turned to the On position (bulb test), perform the
instrument cluster actuator test. (Refer to 8 - ELEC-
TRICAL/INSTRUMENT CLUSTER - DIAGNOSIS
AND TESTING - ACTUATOR TEST). If the bulb
fails to operate during the actuator test, replace the
bulb. If the SKIS indicator still fails to light during
the bulb test, a wiring problem resulting in the loss
of battery current or ground to the Sentry Key Immo-
bilizer Module (SKIM) should be suspected, and thefollowing procedure should be used for diagnosis.
Refer to the appropriate wiring information.
NOTE: The following tests may not prove conclu-
sive in the diagnosis of this system. The most reli-
able, efficient, and accurate means to diagnose the
Sentry Key Immobilizer System requires the use of
a DRBIIITscan tool. Refer to the appropriate diag-
nostic information.
(1) Check the fused B(+) fuse in the Junction
Block (JB). If OK, go to Step 2. If not OK, repair the
shorted circuit or component and replace the faulty
fuse.
WJVEHICLE THEFT SECURITY 8Q - 5
VEHICLE THEFT SECURITY (Continued)
Page 597 of 2199
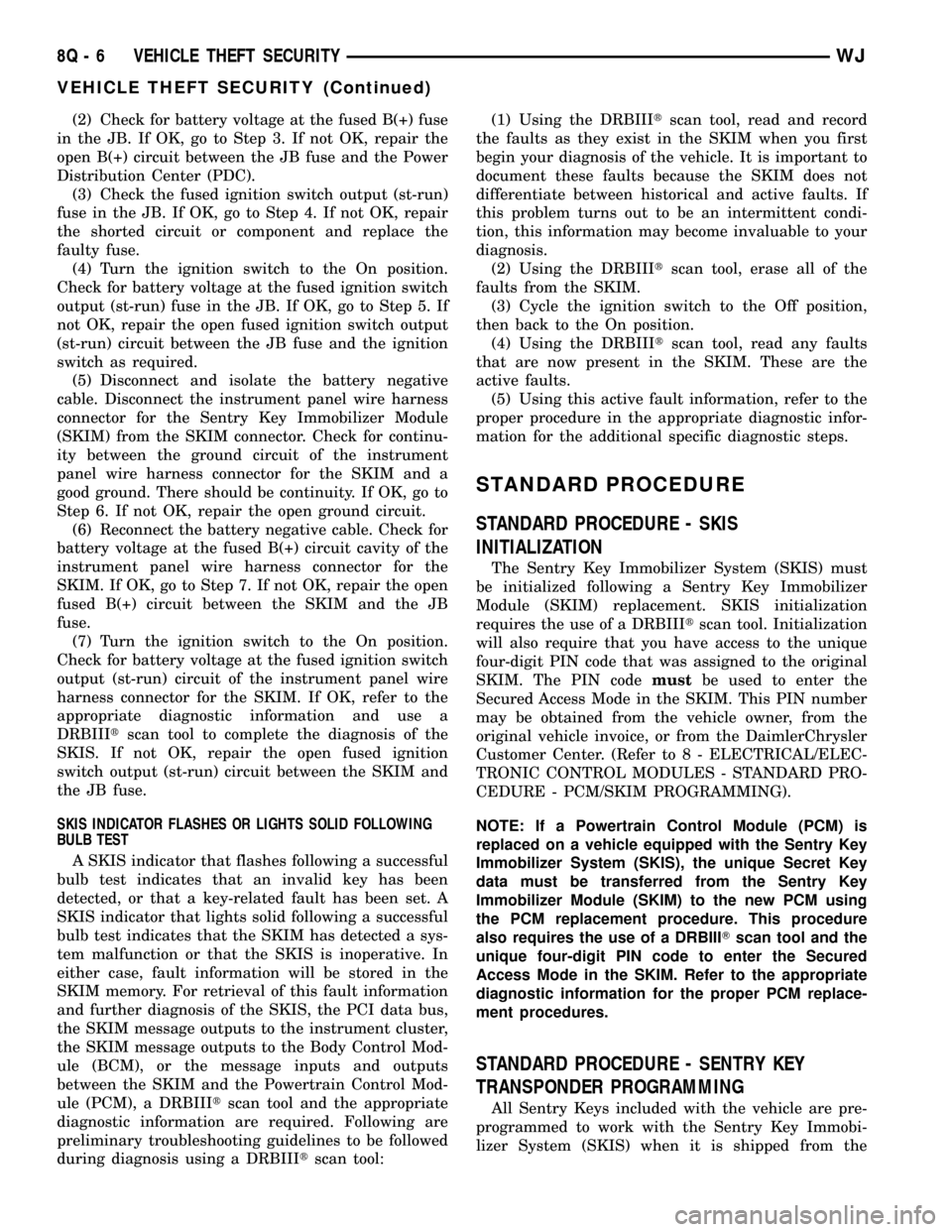
(2) Check for battery voltage at the fused B(+) fuse
in the JB. If OK, go to Step 3. If not OK, repair the
open B(+) circuit between the JB fuse and the Power
Distribution Center (PDC).
(3) Check the fused ignition switch output (st-run)
fuse in the JB. If OK, go to Step 4. If not OK, repair
the shorted circuit or component and replace the
faulty fuse.
(4) Turn the ignition switch to the On position.
Check for battery voltage at the fused ignition switch
output (st-run) fuse in the JB. If OK, go to Step 5. If
not OK, repair the open fused ignition switch output
(st-run) circuit between the JB fuse and the ignition
switch as required.
(5) Disconnect and isolate the battery negative
cable. Disconnect the instrument panel wire harness
connector for the Sentry Key Immobilizer Module
(SKIM) from the SKIM connector. Check for continu-
ity between the ground circuit of the instrument
panel wire harness connector for the SKIM and a
good ground. There should be continuity. If OK, go to
Step 6. If not OK, repair the open ground circuit.
(6) Reconnect the battery negative cable. Check for
battery voltage at the fused B(+) circuit cavity of the
instrument panel wire harness connector for the
SKIM. If OK, go to Step 7. If not OK, repair the open
fused B(+) circuit between the SKIM and the JB
fuse.
(7) Turn the ignition switch to the On position.
Check for battery voltage at the fused ignition switch
output (st-run) circuit of the instrument panel wire
harness connector for the SKIM. If OK, refer to the
appropriate diagnostic information and use a
DRBIIItscan tool to complete the diagnosis of the
SKIS. If not OK, repair the open fused ignition
switch output (st-run) circuit between the SKIM and
the JB fuse.
SKIS INDICATOR FLASHES OR LIGHTS SOLID FOLLOWING
BULB TEST
A SKIS indicator that flashes following a successful
bulb test indicates that an invalid key has been
detected, or that a key-related fault has been set. A
SKIS indicator that lights solid following a successful
bulb test indicates that the SKIM has detected a sys-
tem malfunction or that the SKIS is inoperative. In
either case, fault information will be stored in the
SKIM memory. For retrieval of this fault information
and further diagnosis of the SKIS, the PCI data bus,
the SKIM message outputs to the instrument cluster,
the SKIM message outputs to the Body Control Mod-
ule (BCM), or the message inputs and outputs
between the SKIM and the Powertrain Control Mod-
ule (PCM), a DRBIIItscan tool and the appropriate
diagnostic information are required. Following are
preliminary troubleshooting guidelines to be followed
during diagnosis using a DRBIIItscan tool:(1) Using the DRBIIItscan tool, read and record
the faults as they exist in the SKIM when you first
begin your diagnosis of the vehicle. It is important to
document these faults because the SKIM does not
differentiate between historical and active faults. If
this problem turns out to be an intermittent condi-
tion, this information may become invaluable to your
diagnosis.
(2) Using the DRBIIItscan tool, erase all of the
faults from the SKIM.
(3) Cycle the ignition switch to the Off position,
then back to the On position.
(4) Using the DRBIIItscan tool, read any faults
that are now present in the SKIM. These are the
active faults.
(5) Using this active fault information, refer to the
proper procedure in the appropriate diagnostic infor-
mation for the additional specific diagnostic steps.
STANDARD PROCEDURE
STANDARD PROCEDURE - SKIS
INITIALIZATION
The Sentry Key Immobilizer System (SKIS) must
be initialized following a Sentry Key Immobilizer
Module (SKIM) replacement. SKIS initialization
requires the use of a DRBIIItscan tool. Initialization
will also require that you have access to the unique
four-digit PIN code that was assigned to the original
SKIM. The PIN codemustbe used to enter the
Secured Access Mode in the SKIM. This PIN number
may be obtained from the vehicle owner, from the
original vehicle invoice, or from the DaimlerChrysler
Customer Center. (Refer to 8 - ELECTRICAL/ELEC-
TRONIC CONTROL MODULES - STANDARD PRO-
CEDURE - PCM/SKIM PROGRAMMING).
NOTE: If a Powertrain Control Module (PCM) is
replaced on a vehicle equipped with the Sentry Key
Immobilizer System (SKIS), the unique Secret Key
data must be transferred from the Sentry Key
Immobilizer Module (SKIM) to the new PCM using
the PCM replacement procedure. This procedure
also requires the use of a DRBIIITscan tool and the
unique four-digit PIN code to enter the Secured
Access Mode in the SKIM. Refer to the appropriate
diagnostic information for the proper PCM replace-
ment procedures.
STANDARD PROCEDURE - SENTRY KEY
TRANSPONDER PROGRAMMING
All Sentry Keys included with the vehicle are pre-
programmed to work with the Sentry Key Immobi-
lizer System (SKIS) when it is shipped from the
8Q - 6 VEHICLE THEFT SECURITYWJ
VEHICLE THEFT SECURITY (Continued)
Page 599 of 2199
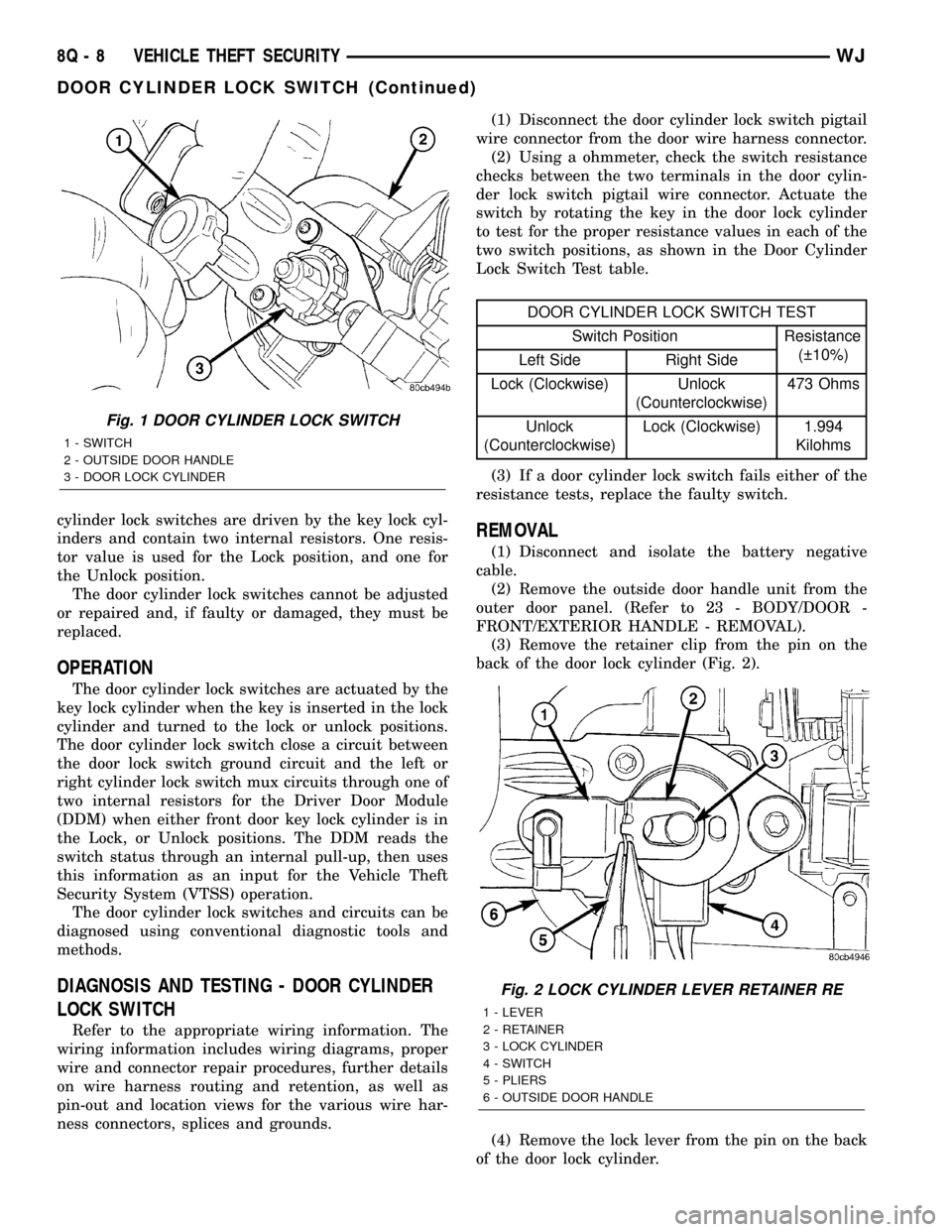
cylinder lock switches are driven by the key lock cyl-
inders and contain two internal resistors. One resis-
tor value is used for the Lock position, and one for
the Unlock position.
The door cylinder lock switches cannot be adjusted
or repaired and, if faulty or damaged, they must be
replaced.
OPERATION
The door cylinder lock switches are actuated by the
key lock cylinder when the key is inserted in the lock
cylinder and turned to the lock or unlock positions.
The door cylinder lock switch close a circuit between
the door lock switch ground circuit and the left or
right cylinder lock switch mux circuits through one of
two internal resistors for the Driver Door Module
(DDM) when either front door key lock cylinder is in
the Lock, or Unlock positions. The DDM reads the
switch status through an internal pull-up, then uses
this information as an input for the Vehicle Theft
Security System (VTSS) operation.
The door cylinder lock switches and circuits can be
diagnosed using conventional diagnostic tools and
methods.
DIAGNOSIS AND TESTING - DOOR CYLINDER
LOCK SWITCH
Refer to the appropriate wiring information. The
wiring information includes wiring diagrams, proper
wire and connector repair procedures, further details
on wire harness routing and retention, as well as
pin-out and location views for the various wire har-
ness connectors, splices and grounds.(1) Disconnect the door cylinder lock switch pigtail
wire connector from the door wire harness connector.
(2) Using a ohmmeter, check the switch resistance
checks between the two terminals in the door cylin-
der lock switch pigtail wire connector. Actuate the
switch by rotating the key in the door lock cylinder
to test for the proper resistance values in each of the
two switch positions, as shown in the Door Cylinder
Lock Switch Test table.
DOOR CYLINDER LOCK SWITCH TEST
Switch Position Resistance
( 10%)
Left Side Right Side
Lock (Clockwise) Unlock
(Counterclockwise)473 Ohms
Unlock
(Counterclockwise)Lock (Clockwise) 1.994
Kilohms
(3) If a door cylinder lock switch fails either of the
resistance tests, replace the faulty switch.
REMOVAL
(1) Disconnect and isolate the battery negative
cable.
(2) Remove the outside door handle unit from the
outer door panel. (Refer to 23 - BODY/DOOR -
FRONT/EXTERIOR HANDLE - REMOVAL).
(3) Remove the retainer clip from the pin on the
back of the door lock cylinder (Fig. 2).
(4) Remove the lock lever from the pin on the back
of the door lock cylinder.
Fig. 1 DOOR CYLINDER LOCK SWITCH
1 - SWITCH
2 - OUTSIDE DOOR HANDLE
3 - DOOR LOCK CYLINDER
Fig. 2 LOCK CYLINDER LEVER RETAINER RE
1 - LEVER
2 - RETAINER
3 - LOCK CYLINDER
4 - SWITCH
5 - PLIERS
6 - OUTSIDE DOOR HANDLE
8Q - 8 VEHICLE THEFT SECURITYWJ
DOOR CYLINDER LOCK SWITCH (Continued)
Page 600 of 2199
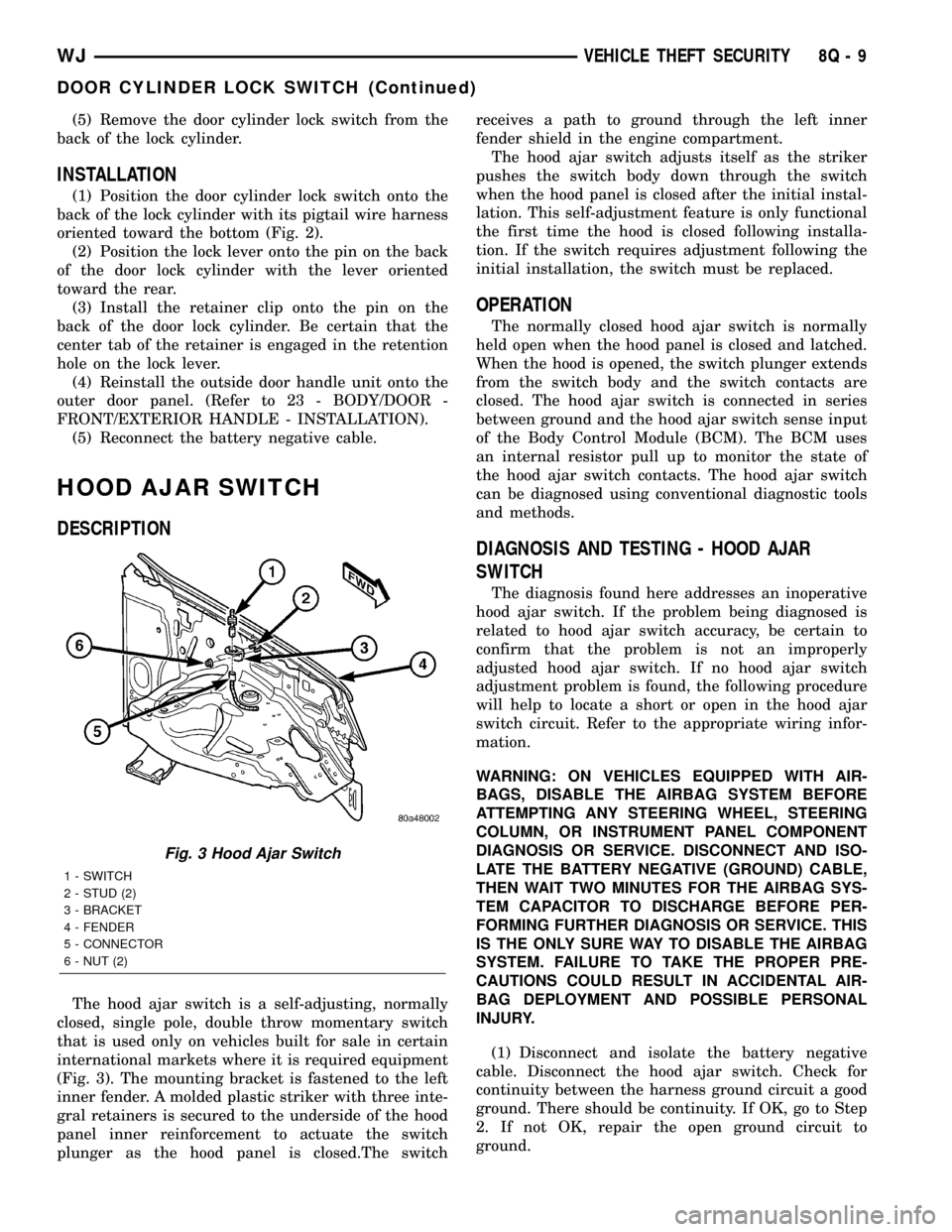
(5) Remove the door cylinder lock switch from the
back of the lock cylinder.
INSTALLATION
(1) Position the door cylinder lock switch onto the
back of the lock cylinder with its pigtail wire harness
oriented toward the bottom (Fig. 2).
(2) Position the lock lever onto the pin on the back
of the door lock cylinder with the lever oriented
toward the rear.
(3) Install the retainer clip onto the pin on the
back of the door lock cylinder. Be certain that the
center tab of the retainer is engaged in the retention
hole on the lock lever.
(4) Reinstall the outside door handle unit onto the
outer door panel. (Refer to 23 - BODY/DOOR -
FRONT/EXTERIOR HANDLE - INSTALLATION).
(5) Reconnect the battery negative cable.
HOOD AJAR SWITCH
DESCRIPTION
The hood ajar switch is a self-adjusting, normally
closed, single pole, double throw momentary switch
that is used only on vehicles built for sale in certain
international markets where it is required equipment
(Fig. 3). The mounting bracket is fastened to the left
inner fender. A molded plastic striker with three inte-
gral retainers is secured to the underside of the hood
panel inner reinforcement to actuate the switch
plunger as the hood panel is closed.The switchreceives a path to ground through the left inner
fender shield in the engine compartment.
The hood ajar switch adjusts itself as the striker
pushes the switch body down through the switch
when the hood panel is closed after the initial instal-
lation. This self-adjustment feature is only functional
the first time the hood is closed following installa-
tion. If the switch requires adjustment following the
initial installation, the switch must be replaced.
OPERATION
The normally closed hood ajar switch is normally
held open when the hood panel is closed and latched.
When the hood is opened, the switch plunger extends
from the switch body and the switch contacts are
closed. The hood ajar switch is connected in series
between ground and the hood ajar switch sense input
of the Body Control Module (BCM). The BCM uses
an internal resistor pull up to monitor the state of
the hood ajar switch contacts. The hood ajar switch
can be diagnosed using conventional diagnostic tools
and methods.
DIAGNOSIS AND TESTING - HOOD AJAR
SWITCH
The diagnosis found here addresses an inoperative
hood ajar switch. If the problem being diagnosed is
related to hood ajar switch accuracy, be certain to
confirm that the problem is not an improperly
adjusted hood ajar switch. If no hood ajar switch
adjustment problem is found, the following procedure
will help to locate a short or open in the hood ajar
switch circuit. Refer to the appropriate wiring infor-
mation.
WARNING: ON VEHICLES EQUIPPED WITH AIR-
BAGS, DISABLE THE AIRBAG SYSTEM BEFORE
ATTEMPTING ANY STEERING WHEEL, STEERING
COLUMN, OR INSTRUMENT PANEL COMPONENT
DIAGNOSIS OR SERVICE. DISCONNECT AND ISO-
LATE THE BATTERY NEGATIVE (GROUND) CABLE,
THEN WAIT TWO MINUTES FOR THE AIRBAG SYS-
TEM CAPACITOR TO DISCHARGE BEFORE PER-
FORMING FURTHER DIAGNOSIS OR SERVICE. THIS
IS THE ONLY SURE WAY TO DISABLE THE AIRBAG
SYSTEM. FAILURE TO TAKE THE PROPER PRE-
CAUTIONS COULD RESULT IN ACCIDENTAL AIR-
BAG DEPLOYMENT AND POSSIBLE PERSONAL
INJURY.
(1) Disconnect and isolate the battery negative
cable. Disconnect the hood ajar switch. Check for
continuity between the harness ground circuit a good
ground. There should be continuity. If OK, go to Step
2. If not OK, repair the open ground circuit to
ground.
Fig. 3 Hood Ajar Switch
1 - SWITCH
2 - STUD (2)
3 - BRACKET
4 - FENDER
5 - CONNECTOR
6 - NUT (2)
WJVEHICLE THEFT SECURITY 8Q - 9
DOOR CYLINDER LOCK SWITCH (Continued)
Page 601 of 2199
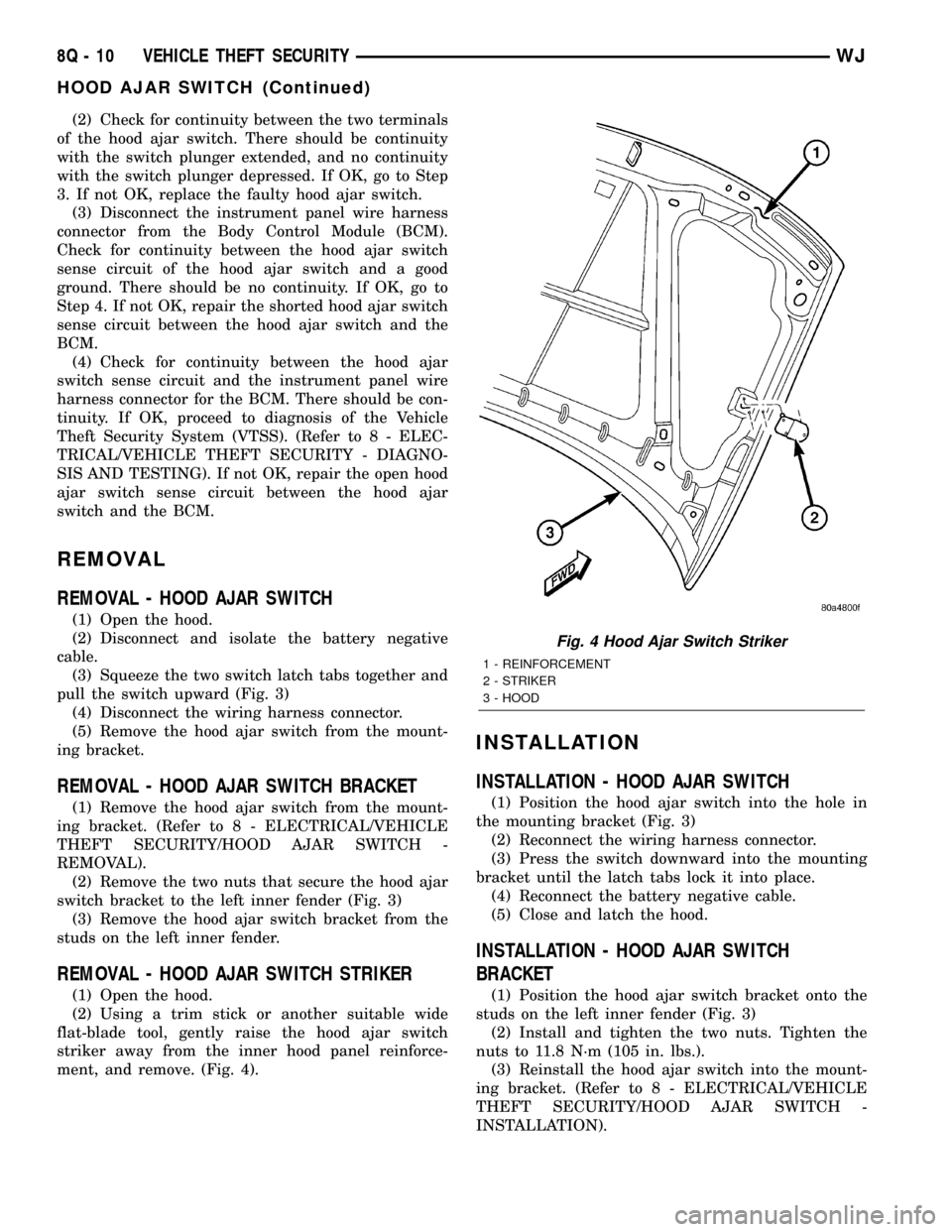
(2) Check for continuity between the two terminals
of the hood ajar switch. There should be continuity
with the switch plunger extended, and no continuity
with the switch plunger depressed. If OK, go to Step
3. If not OK, replace the faulty hood ajar switch.
(3) Disconnect the instrument panel wire harness
connector from the Body Control Module (BCM).
Check for continuity between the hood ajar switch
sense circuit of the hood ajar switch and a good
ground. There should be no continuity. If OK, go to
Step 4. If not OK, repair the shorted hood ajar switch
sense circuit between the hood ajar switch and the
BCM.
(4) Check for continuity between the hood ajar
switch sense circuit and the instrument panel wire
harness connector for the BCM. There should be con-
tinuity. If OK, proceed to diagnosis of the Vehicle
Theft Security System (VTSS). (Refer to 8 - ELEC-
TRICAL/VEHICLE THEFT SECURITY - DIAGNO-
SIS AND TESTING). If not OK, repair the open hood
ajar switch sense circuit between the hood ajar
switch and the BCM.
REMOVAL
REMOVAL - HOOD AJAR SWITCH
(1) Open the hood.
(2) Disconnect and isolate the battery negative
cable.
(3) Squeeze the two switch latch tabs together and
pull the switch upward (Fig. 3)
(4) Disconnect the wiring harness connector.
(5) Remove the hood ajar switch from the mount-
ing bracket.
REMOVAL - HOOD AJAR SWITCH BRACKET
(1) Remove the hood ajar switch from the mount-
ing bracket. (Refer to 8 - ELECTRICAL/VEHICLE
THEFT SECURITY/HOOD AJAR SWITCH -
REMOVAL).
(2) Remove the two nuts that secure the hood ajar
switch bracket to the left inner fender (Fig. 3)
(3) Remove the hood ajar switch bracket from the
studs on the left inner fender.
REMOVAL - HOOD AJAR SWITCH STRIKER
(1) Open the hood.
(2) Using a trim stick or another suitable wide
flat-blade tool, gently raise the hood ajar switch
striker away from the inner hood panel reinforce-
ment, and remove. (Fig. 4).
INSTALLATION
INSTALLATION - HOOD AJAR SWITCH
(1) Position the hood ajar switch into the hole in
the mounting bracket (Fig. 3)
(2) Reconnect the wiring harness connector.
(3) Press the switch downward into the mounting
bracket until the latch tabs lock it into place.
(4) Reconnect the battery negative cable.
(5) Close and latch the hood.
INSTALLATION - HOOD AJAR SWITCH
BRACKET
(1) Position the hood ajar switch bracket onto the
studs on the left inner fender (Fig. 3)
(2) Install and tighten the two nuts. Tighten the
nuts to 11.8 N´m (105 in. lbs.).
(3) Reinstall the hood ajar switch into the mount-
ing bracket. (Refer to 8 - ELECTRICAL/VEHICLE
THEFT SECURITY/HOOD AJAR SWITCH -
INSTALLATION).
Fig. 4 Hood Ajar Switch Striker
1 - REINFORCEMENT
2 - STRIKER
3 - HOOD
8Q - 10 VEHICLE THEFT SECURITYWJ
HOOD AJAR SWITCH (Continued)
Page 602 of 2199
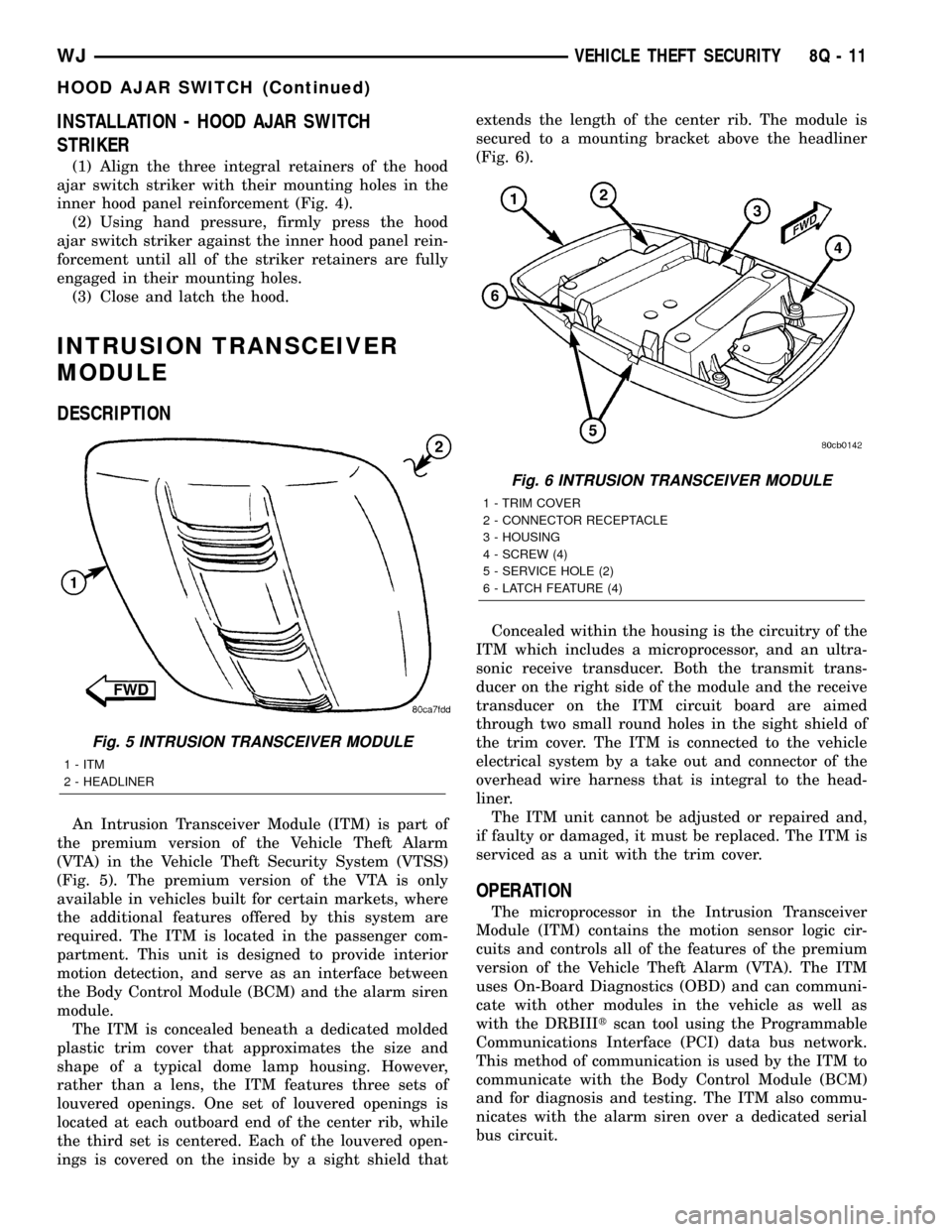
INSTALLATION - HOOD AJAR SWITCH
STRIKER
(1) Align the three integral retainers of the hood
ajar switch striker with their mounting holes in the
inner hood panel reinforcement (Fig. 4).
(2) Using hand pressure, firmly press the hood
ajar switch striker against the inner hood panel rein-
forcement until all of the striker retainers are fully
engaged in their mounting holes.
(3) Close and latch the hood.
INTRUSION TRANSCEIVER
MODULE
DESCRIPTION
An Intrusion Transceiver Module (ITM) is part of
the premium version of the Vehicle Theft Alarm
(VTA) in the Vehicle Theft Security System (VTSS)
(Fig. 5). The premium version of the VTA is only
available in vehicles built for certain markets, where
the additional features offered by this system are
required. The ITM is located in the passenger com-
partment. This unit is designed to provide interior
motion detection, and serve as an interface between
the Body Control Module (BCM) and the alarm siren
module.
The ITM is concealed beneath a dedicated molded
plastic trim cover that approximates the size and
shape of a typical dome lamp housing. However,
rather than a lens, the ITM features three sets of
louvered openings. One set of louvered openings is
located at each outboard end of the center rib, while
the third set is centered. Each of the louvered open-
ings is covered on the inside by a sight shield thatextends the length of the center rib. The module is
secured to a mounting bracket above the headliner
(Fig. 6).
Concealed within the housing is the circuitry of the
ITM which includes a microprocessor, and an ultra-
sonic receive transducer. Both the transmit trans-
ducer on the right side of the module and the receive
transducer on the ITM circuit board are aimed
through two small round holes in the sight shield of
the trim cover. The ITM is connected to the vehicle
electrical system by a take out and connector of the
overhead wire harness that is integral to the head-
liner.
The ITM unit cannot be adjusted or repaired and,
if faulty or damaged, it must be replaced. The ITM is
serviced as a unit with the trim cover.
OPERATION
The microprocessor in the Intrusion Transceiver
Module (ITM) contains the motion sensor logic cir-
cuits and controls all of the features of the premium
version of the Vehicle Theft Alarm (VTA). The ITM
uses On-Board Diagnostics (OBD) and can communi-
cate with other modules in the vehicle as well as
with the DRBIIItscan tool using the Programmable
Communications Interface (PCI) data bus network.
This method of communication is used by the ITM to
communicate with the Body Control Module (BCM)
and for diagnosis and testing. The ITM also commu-
nicates with the alarm siren over a dedicated serial
bus circuit.
Fig. 5 INTRUSION TRANSCEIVER MODULE
1 - ITM
2 - HEADLINER
Fig. 6 INTRUSION TRANSCEIVER MODULE
1 - TRIM COVER
2 - CONNECTOR RECEPTACLE
3 - HOUSING
4 - SCREW (4)
5 - SERVICE HOLE (2)
6 - LATCH FEATURE (4)
WJVEHICLE THEFT SECURITY 8Q - 11
HOOD AJAR SWITCH (Continued)