connector JEEP GRAND CHEROKEE 2002 WJ / 2.G Workshop Manual
[x] Cancel search | Manufacturer: JEEP, Model Year: 2002, Model line: GRAND CHEROKEE, Model: JEEP GRAND CHEROKEE 2002 WJ / 2.GPages: 2199, PDF Size: 76.01 MB
Page 603 of 2199
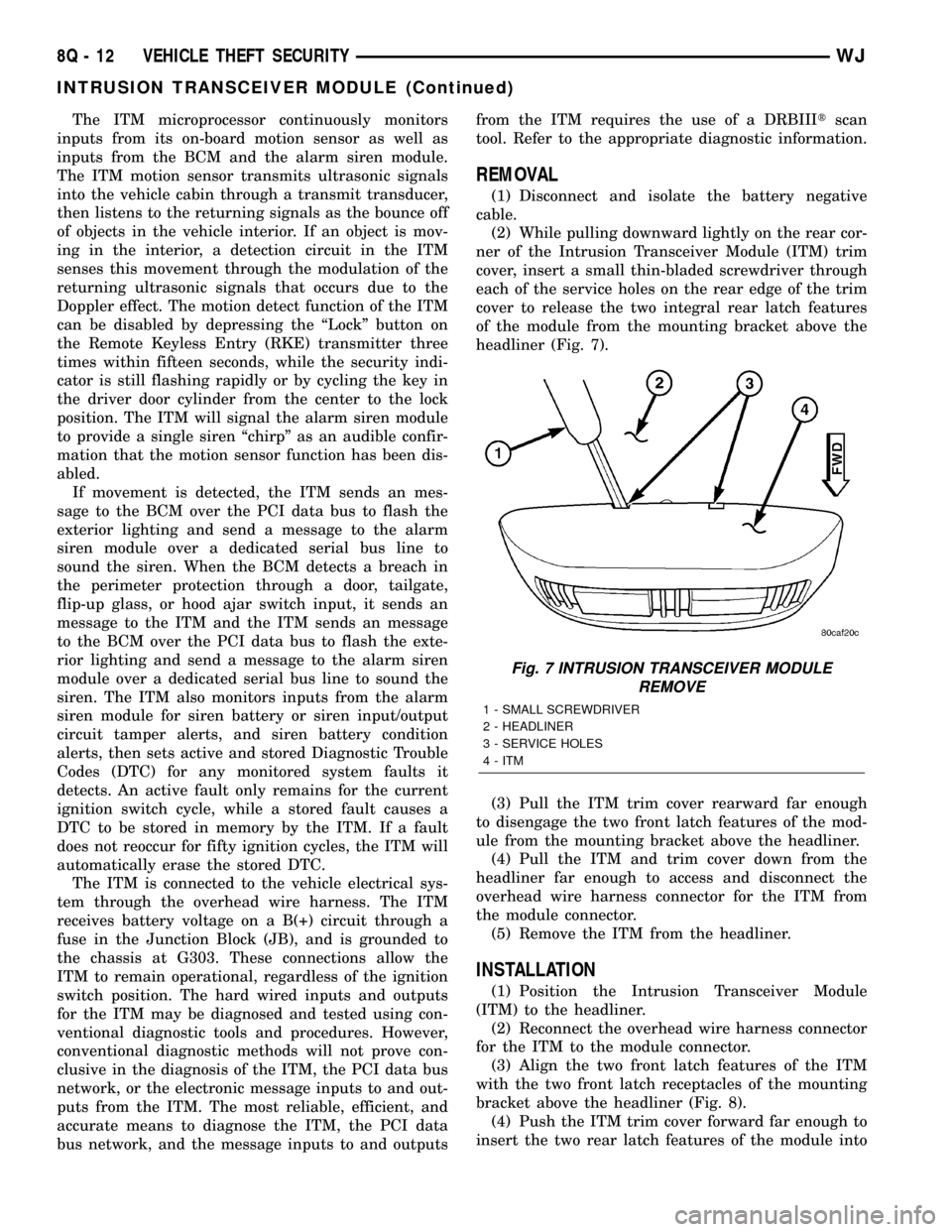
The ITM microprocessor continuously monitors
inputs from its on-board motion sensor as well as
inputs from the BCM and the alarm siren module.
The ITM motion sensor transmits ultrasonic signals
into the vehicle cabin through a transmit transducer,
then listens to the returning signals as the bounce off
of objects in the vehicle interior. If an object is mov-
ing in the interior, a detection circuit in the ITM
senses this movement through the modulation of the
returning ultrasonic signals that occurs due to the
Doppler effect. The motion detect function of the ITM
can be disabled by depressing the ªLockº button on
the Remote Keyless Entry (RKE) transmitter three
times within fifteen seconds, while the security indi-
cator is still flashing rapidly or by cycling the key in
the driver door cylinder from the center to the lock
position. The ITM will signal the alarm siren module
to provide a single siren ªchirpº as an audible confir-
mation that the motion sensor function has been dis-
abled.
If movement is detected, the ITM sends an mes-
sage to the BCM over the PCI data bus to flash the
exterior lighting and send a message to the alarm
siren module over a dedicated serial bus line to
sound the siren. When the BCM detects a breach in
the perimeter protection through a door, tailgate,
flip-up glass, or hood ajar switch input, it sends an
message to the ITM and the ITM sends an message
to the BCM over the PCI data bus to flash the exte-
rior lighting and send a message to the alarm siren
module over a dedicated serial bus line to sound the
siren. The ITM also monitors inputs from the alarm
siren module for siren battery or siren input/output
circuit tamper alerts, and siren battery condition
alerts, then sets active and stored Diagnostic Trouble
Codes (DTC) for any monitored system faults it
detects. An active fault only remains for the current
ignition switch cycle, while a stored fault causes a
DTC to be stored in memory by the ITM. If a fault
does not reoccur for fifty ignition cycles, the ITM will
automatically erase the stored DTC.
The ITM is connected to the vehicle electrical sys-
tem through the overhead wire harness. The ITM
receives battery voltage on a B(+) circuit through a
fuse in the Junction Block (JB), and is grounded to
the chassis at G303. These connections allow the
ITM to remain operational, regardless of the ignition
switch position. The hard wired inputs and outputs
for the ITM may be diagnosed and tested using con-
ventional diagnostic tools and procedures. However,
conventional diagnostic methods will not prove con-
clusive in the diagnosis of the ITM, the PCI data bus
network, or the electronic message inputs to and out-
puts from the ITM. The most reliable, efficient, and
accurate means to diagnose the ITM, the PCI data
bus network, and the message inputs to and outputsfrom the ITM requires the use of a DRBIIItscan
tool. Refer to the appropriate diagnostic information.
REMOVAL
(1) Disconnect and isolate the battery negative
cable.
(2) While pulling downward lightly on the rear cor-
ner of the Intrusion Transceiver Module (ITM) trim
cover, insert a small thin-bladed screwdriver through
each of the service holes on the rear edge of the trim
cover to release the two integral rear latch features
of the module from the mounting bracket above the
headliner (Fig. 7).
(3) Pull the ITM trim cover rearward far enough
to disengage the two front latch features of the mod-
ule from the mounting bracket above the headliner.
(4) Pull the ITM and trim cover down from the
headliner far enough to access and disconnect the
overhead wire harness connector for the ITM from
the module connector.
(5) Remove the ITM from the headliner.
INSTALLATION
(1) Position the Intrusion Transceiver Module
(ITM) to the headliner.
(2) Reconnect the overhead wire harness connector
for the ITM to the module connector.
(3) Align the two front latch features of the ITM
with the two front latch receptacles of the mounting
bracket above the headliner (Fig. 8).
(4) Push the ITM trim cover forward far enough to
insert the two rear latch features of the module into
Fig. 7 INTRUSION TRANSCEIVER MODULE
REMOVE
1 - SMALL SCREWDRIVER
2 - HEADLINER
3 - SERVICE HOLES
4 - ITM
8Q - 12 VEHICLE THEFT SECURITYWJ
INTRUSION TRANSCEIVER MODULE (Continued)
Page 605 of 2199
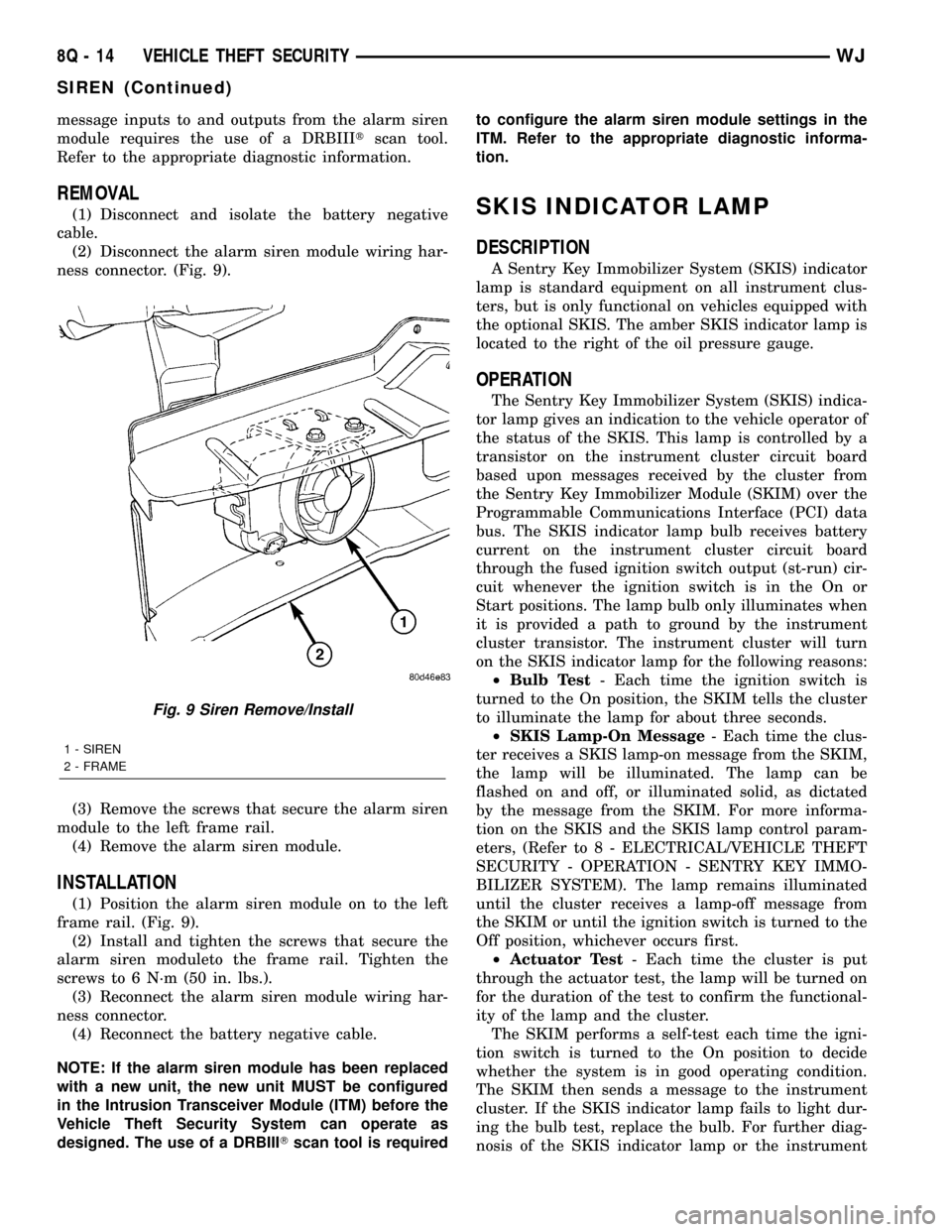
message inputs to and outputs from the alarm siren
module requires the use of a DRBIIItscan tool.
Refer to the appropriate diagnostic information.
REMOVAL
(1) Disconnect and isolate the battery negative
cable.
(2) Disconnect the alarm siren module wiring har-
ness connector. (Fig. 9).
(3) Remove the screws that secure the alarm siren
module to the left frame rail.
(4) Remove the alarm siren module.
INSTALLATION
(1) Position the alarm siren module on to the left
frame rail. (Fig. 9).
(2) Install and tighten the screws that secure the
alarm siren moduleto the frame rail. Tighten the
screws to 6 N´m (50 in. lbs.).
(3) Reconnect the alarm siren module wiring har-
ness connector.
(4) Reconnect the battery negative cable.
NOTE: If the alarm siren module has been replaced
with a new unit, the new unit MUST be configured
in the Intrusion Transceiver Module (ITM) before the
Vehicle Theft Security System can operate as
designed. The use of a DRBIIITscan tool is requiredto configure the alarm siren module settings in the
ITM. Refer to the appropriate diagnostic informa-
tion.
SKIS INDICATOR LAMP
DESCRIPTION
A Sentry Key Immobilizer System (SKIS) indicator
lamp is standard equipment on all instrument clus-
ters, but is only functional on vehicles equipped with
the optional SKIS. The amber SKIS indicator lamp is
located to the right of the oil pressure gauge.
OPERATION
The Sentry Key Immobilizer System (SKIS) indica-
tor lamp gives an indication to the vehicle operator of
the status of the SKIS. This lamp is controlled by a
transistor on the instrument cluster circuit board
based upon messages received by the cluster from
the Sentry Key Immobilizer Module (SKIM) over the
Programmable Communications Interface (PCI) data
bus. The SKIS indicator lamp bulb receives battery
current on the instrument cluster circuit board
through the fused ignition switch output (st-run) cir-
cuit whenever the ignition switch is in the On or
Start positions. The lamp bulb only illuminates when
it is provided a path to ground by the instrument
cluster transistor. The instrument cluster will turn
on the SKIS indicator lamp for the following reasons:
²Bulb Test- Each time the ignition switch is
turned to the On position, the SKIM tells the cluster
to illuminate the lamp for about three seconds.
²SKIS Lamp-On Message- Each time the clus-
ter receives a SKIS lamp-on message from the SKIM,
the lamp will be illuminated. The lamp can be
flashed on and off, or illuminated solid, as dictated
by the message from the SKIM. For more informa-
tion on the SKIS and the SKIS lamp control param-
eters, (Refer to 8 - ELECTRICAL/VEHICLE THEFT
SECURITY - OPERATION - SENTRY KEY IMMO-
BILIZER SYSTEM). The lamp remains illuminated
until the cluster receives a lamp-off message from
the SKIM or until the ignition switch is turned to the
Off position, whichever occurs first.
²Actuator Test- Each time the cluster is put
through the actuator test, the lamp will be turned on
for the duration of the test to confirm the functional-
ity of the lamp and the cluster.
The SKIM performs a self-test each time the igni-
tion switch is turned to the On position to decide
whether the system is in good operating condition.
The SKIM then sends a message to the instrument
cluster. If the SKIS indicator lamp fails to light dur-
ing the bulb test, replace the bulb. For further diag-
nosis of the SKIS indicator lamp or the instrument
Fig. 9 Siren Remove/Install
1 - SIREN
2 - FRAME
8Q - 14 VEHICLE THEFT SECURITYWJ
SIREN (Continued)
Page 607 of 2199
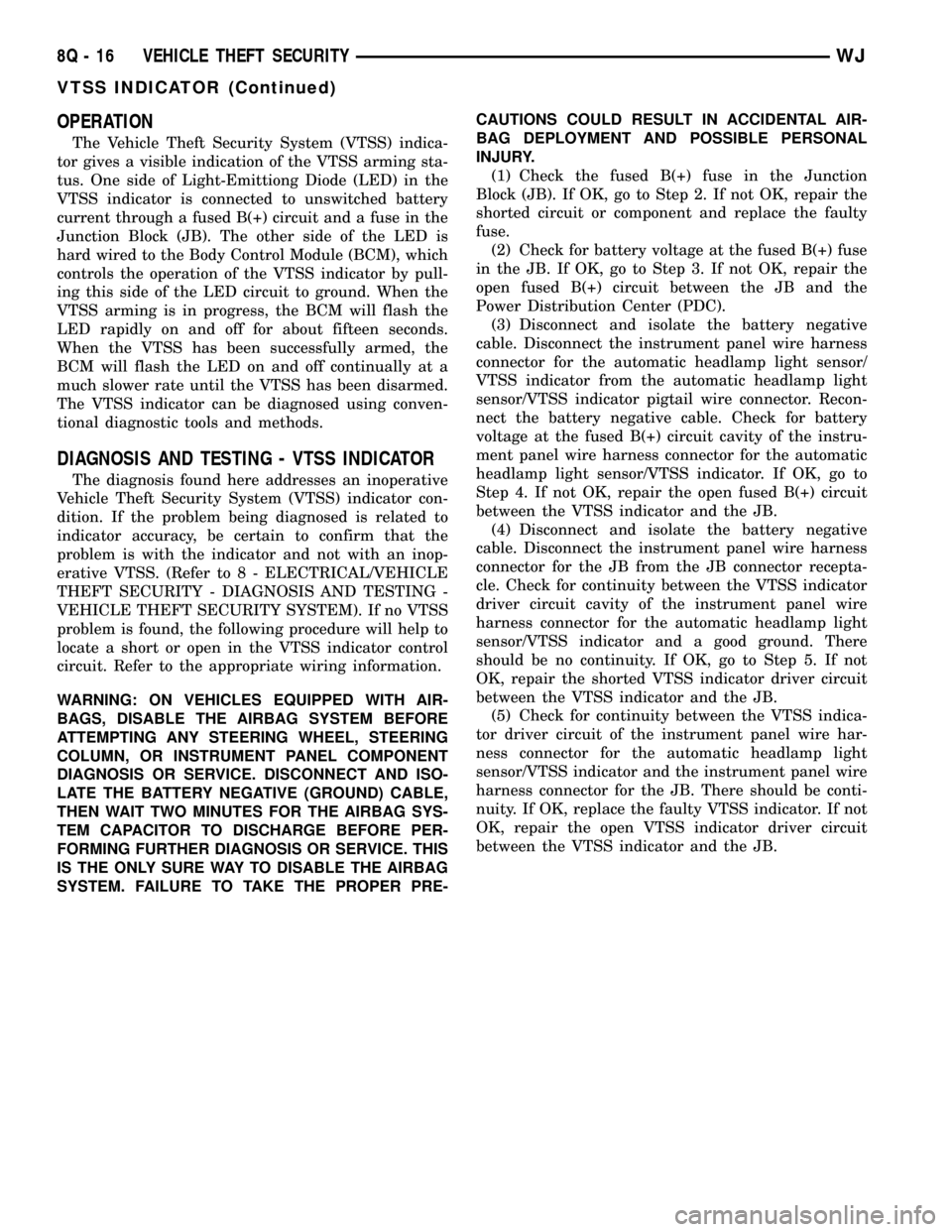
OPERATION
The Vehicle Theft Security System (VTSS) indica-
tor gives a visible indication of the VTSS arming sta-
tus. One side of Light-Emittiong Diode (LED) in the
VTSS indicator is connected to unswitched battery
current through a fused B(+) circuit and a fuse in the
Junction Block (JB). The other side of the LED is
hard wired to the Body Control Module (BCM), which
controls the operation of the VTSS indicator by pull-
ing this side of the LED circuit to ground. When the
VTSS arming is in progress, the BCM will flash the
LED rapidly on and off for about fifteen seconds.
When the VTSS has been successfully armed, the
BCM will flash the LED on and off continually at a
much slower rate until the VTSS has been disarmed.
The VTSS indicator can be diagnosed using conven-
tional diagnostic tools and methods.
DIAGNOSIS AND TESTING - VTSS INDICATOR
The diagnosis found here addresses an inoperative
Vehicle Theft Security System (VTSS) indicator con-
dition. If the problem being diagnosed is related to
indicator accuracy, be certain to confirm that the
problem is with the indicator and not with an inop-
erative VTSS. (Refer to 8 - ELECTRICAL/VEHICLE
THEFT SECURITY - DIAGNOSIS AND TESTING -
VEHICLE THEFT SECURITY SYSTEM). If no VTSS
problem is found, the following procedure will help to
locate a short or open in the VTSS indicator control
circuit. Refer to the appropriate wiring information.
WARNING: ON VEHICLES EQUIPPED WITH AIR-
BAGS, DISABLE THE AIRBAG SYSTEM BEFORE
ATTEMPTING ANY STEERING WHEEL, STEERING
COLUMN, OR INSTRUMENT PANEL COMPONENT
DIAGNOSIS OR SERVICE. DISCONNECT AND ISO-
LATE THE BATTERY NEGATIVE (GROUND) CABLE,
THEN WAIT TWO MINUTES FOR THE AIRBAG SYS-
TEM CAPACITOR TO DISCHARGE BEFORE PER-
FORMING FURTHER DIAGNOSIS OR SERVICE. THIS
IS THE ONLY SURE WAY TO DISABLE THE AIRBAG
SYSTEM. FAILURE TO TAKE THE PROPER PRE-CAUTIONS COULD RESULT IN ACCIDENTAL AIR-
BAG DEPLOYMENT AND POSSIBLE PERSONAL
INJURY.
(1) Check the fused B(+) fuse in the Junction
Block (JB). If OK, go to Step 2. If not OK, repair the
shorted circuit or component and replace the faulty
fuse.
(2) Check for battery voltage at the fused B(+) fuse
in the JB. If OK, go to Step 3. If not OK, repair the
open fused B(+) circuit between the JB and the
Power Distribution Center (PDC).
(3) Disconnect and isolate the battery negative
cable. Disconnect the instrument panel wire harness
connector for the automatic headlamp light sensor/
VTSS indicator from the automatic headlamp light
sensor/VTSS indicator pigtail wire connector. Recon-
nect the battery negative cable. Check for battery
voltage at the fused B(+) circuit cavity of the instru-
ment panel wire harness connector for the automatic
headlamp light sensor/VTSS indicator. If OK, go to
Step 4. If not OK, repair the open fused B(+) circuit
between the VTSS indicator and the JB.
(4) Disconnect and isolate the battery negative
cable. Disconnect the instrument panel wire harness
connector for the JB from the JB connector recepta-
cle. Check for continuity between the VTSS indicator
driver circuit cavity of the instrument panel wire
harness connector for the automatic headlamp light
sensor/VTSS indicator and a good ground. There
should be no continuity. If OK, go to Step 5. If not
OK, repair the shorted VTSS indicator driver circuit
between the VTSS indicator and the JB.
(5) Check for continuity between the VTSS indica-
tor driver circuit of the instrument panel wire har-
ness connector for the automatic headlamp light
sensor/VTSS indicator and the instrument panel wire
harness connector for the JB. There should be conti-
nuity. If OK, replace the faulty VTSS indicator. If not
OK, repair the open VTSS indicator driver circuit
between the VTSS indicator and the JB.
8Q - 16 VEHICLE THEFT SECURITYWJ
VTSS INDICATOR (Continued)
Page 610 of 2199
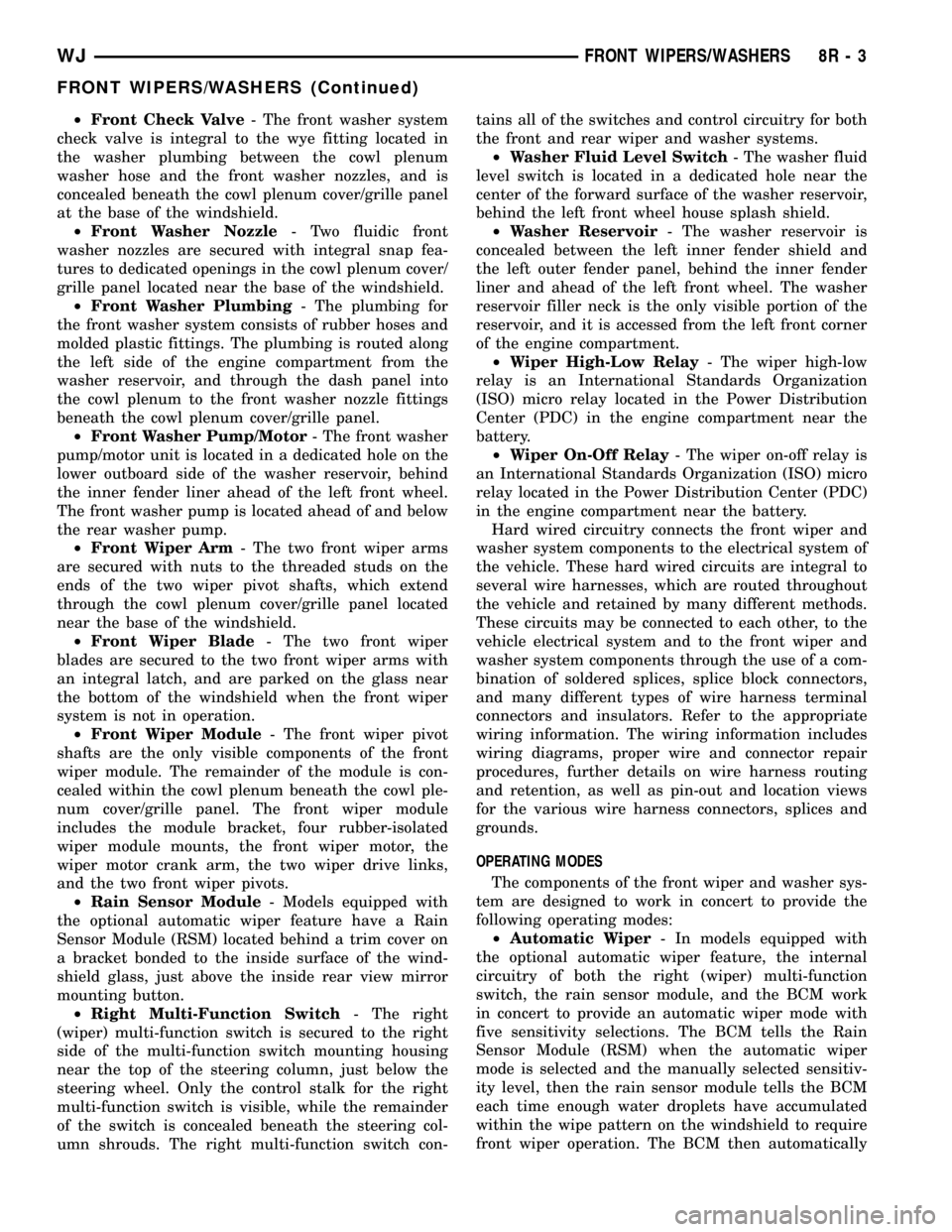
²Front Check Valve- The front washer system
check valve is integral to the wye fitting located in
the washer plumbing between the cowl plenum
washer hose and the front washer nozzles, and is
concealed beneath the cowl plenum cover/grille panel
at the base of the windshield.
²Front Washer Nozzle- Two fluidic front
washer nozzles are secured with integral snap fea-
tures to dedicated openings in the cowl plenum cover/
grille panel located near the base of the windshield.
²Front Washer Plumbing- The plumbing for
the front washer system consists of rubber hoses and
molded plastic fittings. The plumbing is routed along
the left side of the engine compartment from the
washer reservoir, and through the dash panel into
the cowl plenum to the front washer nozzle fittings
beneath the cowl plenum cover/grille panel.
²Front Washer Pump/Motor- The front washer
pump/motor unit is located in a dedicated hole on the
lower outboard side of the washer reservoir, behind
the inner fender liner ahead of the left front wheel.
The front washer pump is located ahead of and below
the rear washer pump.
²Front Wiper Arm- The two front wiper arms
are secured with nuts to the threaded studs on the
ends of the two wiper pivot shafts, which extend
through the cowl plenum cover/grille panel located
near the base of the windshield.
²Front Wiper Blade- The two front wiper
blades are secured to the two front wiper arms with
an integral latch, and are parked on the glass near
the bottom of the windshield when the front wiper
system is not in operation.
²Front Wiper Module- The front wiper pivot
shafts are the only visible components of the front
wiper module. The remainder of the module is con-
cealed within the cowl plenum beneath the cowl ple-
num cover/grille panel. The front wiper module
includes the module bracket, four rubber-isolated
wiper module mounts, the front wiper motor, the
wiper motor crank arm, the two wiper drive links,
and the two front wiper pivots.
²Rain Sensor Module- Models equipped with
the optional automatic wiper feature have a Rain
Sensor Module (RSM) located behind a trim cover on
a bracket bonded to the inside surface of the wind-
shield glass, just above the inside rear view mirror
mounting button.
²Right Multi-Function Switch- The right
(wiper) multi-function switch is secured to the right
side of the multi-function switch mounting housing
near the top of the steering column, just below the
steering wheel. Only the control stalk for the right
multi-function switch is visible, while the remainder
of the switch is concealed beneath the steering col-
umn shrouds. The right multi-function switch con-tains all of the switches and control circuitry for both
the front and rear wiper and washer systems.
²Washer Fluid Level Switch- The washer fluid
level switch is located in a dedicated hole near the
center of the forward surface of the washer reservoir,
behind the left front wheel house splash shield.
²Washer Reservoir- The washer reservoir is
concealed between the left inner fender shield and
the left outer fender panel, behind the inner fender
liner and ahead of the left front wheel. The washer
reservoir filler neck is the only visible portion of the
reservoir, and it is accessed from the left front corner
of the engine compartment.
²Wiper High-Low Relay- The wiper high-low
relay is an International Standards Organization
(ISO) micro relay located in the Power Distribution
Center (PDC) in the engine compartment near the
battery.
²Wiper On-Off Relay- The wiper on-off relay is
an International Standards Organization (ISO) micro
relay located in the Power Distribution Center (PDC)
in the engine compartment near the battery.
Hard wired circuitry connects the front wiper and
washer system components to the electrical system of
the vehicle. These hard wired circuits are integral to
several wire harnesses, which are routed throughout
the vehicle and retained by many different methods.
These circuits may be connected to each other, to the
vehicle electrical system and to the front wiper and
washer system components through the use of a com-
bination of soldered splices, splice block connectors,
and many different types of wire harness terminal
connectors and insulators. Refer to the appropriate
wiring information. The wiring information includes
wiring diagrams, proper wire and connector repair
procedures, further details on wire harness routing
and retention, as well as pin-out and location views
for the various wire harness connectors, splices and
grounds.
OPERATING MODES
The components of the front wiper and washer sys-
tem are designed to work in concert to provide the
following operating modes:
²Automatic Wiper- In models equipped with
the optional automatic wiper feature, the internal
circuitry of both the right (wiper) multi-function
switch, the rain sensor module, and the BCM work
in concert to provide an automatic wiper mode with
five sensitivity selections. The BCM tells the Rain
Sensor Module (RSM) when the automatic wiper
mode is selected and the manually selected sensitiv-
ity level, then the rain sensor module tells the BCM
each time enough water droplets have accumulated
within the wipe pattern on the windshield to require
front wiper operation. The BCM then automatically
WJFRONT WIPERS/WASHERS 8R - 3
FRONT WIPERS/WASHERS (Continued)
Page 613 of 2199
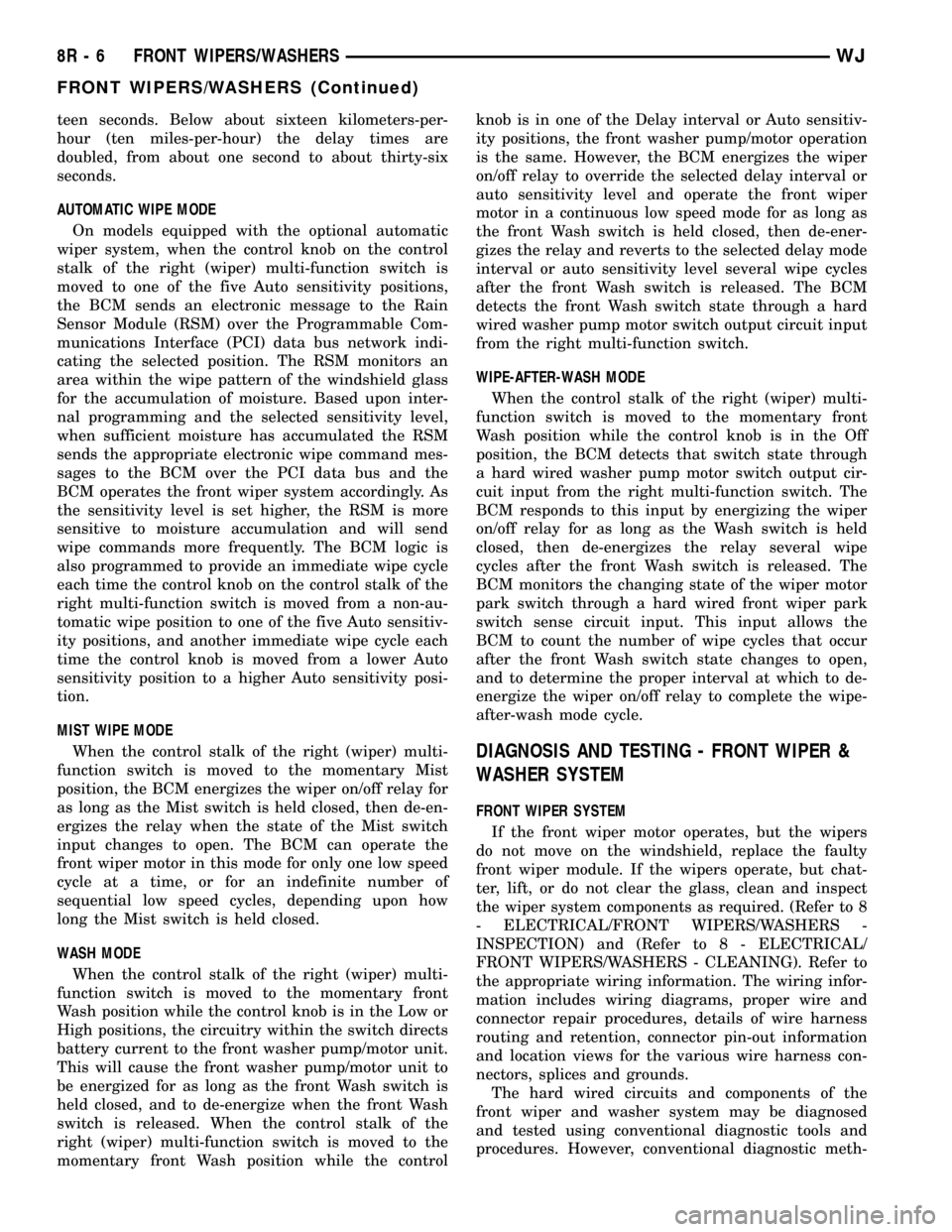
teen seconds. Below about sixteen kilometers-per-
hour (ten miles-per-hour) the delay times are
doubled, from about one second to about thirty-six
seconds.
AUTOMATIC WIPE MODE
On models equipped with the optional automatic
wiper system, when the control knob on the control
stalk of the right (wiper) multi-function switch is
moved to one of the five Auto sensitivity positions,
the BCM sends an electronic message to the Rain
Sensor Module (RSM) over the Programmable Com-
munications Interface (PCI) data bus network indi-
cating the selected position. The RSM monitors an
area within the wipe pattern of the windshield glass
for the accumulation of moisture. Based upon inter-
nal programming and the selected sensitivity level,
when sufficient moisture has accumulated the RSM
sends the appropriate electronic wipe command mes-
sages to the BCM over the PCI data bus and the
BCM operates the front wiper system accordingly. As
the sensitivity level is set higher, the RSM is more
sensitive to moisture accumulation and will send
wipe commands more frequently. The BCM logic is
also programmed to provide an immediate wipe cycle
each time the control knob on the control stalk of the
right multi-function switch is moved from a non-au-
tomatic wipe position to one of the five Auto sensitiv-
ity positions, and another immediate wipe cycle each
time the control knob is moved from a lower Auto
sensitivity position to a higher Auto sensitivity posi-
tion.
MIST WIPE MODE
When the control stalk of the right (wiper) multi-
function switch is moved to the momentary Mist
position, the BCM energizes the wiper on/off relay for
as long as the Mist switch is held closed, then de-en-
ergizes the relay when the state of the Mist switch
input changes to open. The BCM can operate the
front wiper motor in this mode for only one low speed
cycle at a time, or for an indefinite number of
sequential low speed cycles, depending upon how
long the Mist switch is held closed.
WASH MODE
When the control stalk of the right (wiper) multi-
function switch is moved to the momentary front
Wash position while the control knob is in the Low or
High positions, the circuitry within the switch directs
battery current to the front washer pump/motor unit.
This will cause the front washer pump/motor unit to
be energized for as long as the front Wash switch is
held closed, and to de-energize when the front Wash
switch is released. When the control stalk of the
right (wiper) multi-function switch is moved to the
momentary front Wash position while the controlknob is in one of the Delay interval or Auto sensitiv-
ity positions, the front washer pump/motor operation
is the same. However, the BCM energizes the wiper
on/off relay to override the selected delay interval or
auto sensitivity level and operate the front wiper
motor in a continuous low speed mode for as long as
the front Wash switch is held closed, then de-ener-
gizes the relay and reverts to the selected delay mode
interval or auto sensitivity level several wipe cycles
after the front Wash switch is released. The BCM
detects the front Wash switch state through a hard
wired washer pump motor switch output circuit input
from the right multi-function switch.
WIPE-AFTER-WASH MODE
When the control stalk of the right (wiper) multi-
function switch is moved to the momentary front
Wash position while the control knob is in the Off
position, the BCM detects that switch state through
a hard wired washer pump motor switch output cir-
cuit input from the right multi-function switch. The
BCM responds to this input by energizing the wiper
on/off relay for as long as the Wash switch is held
closed, then de-energizes the relay several wipe
cycles after the front Wash switch is released. The
BCM monitors the changing state of the wiper motor
park switch through a hard wired front wiper park
switch sense circuit input. This input allows the
BCM to count the number of wipe cycles that occur
after the front Wash switch state changes to open,
and to determine the proper interval at which to de-
energize the wiper on/off relay to complete the wipe-
after-wash mode cycle.
DIAGNOSIS AND TESTING - FRONT WIPER &
WASHER SYSTEM
FRONT WIPER SYSTEM
If the front wiper motor operates, but the wipers
do not move on the windshield, replace the faulty
front wiper module. If the wipers operate, but chat-
ter, lift, or do not clear the glass, clean and inspect
the wiper system components as required. (Refer to 8
- ELECTRICAL/FRONT WIPERS/WASHERS -
INSPECTION) and (Refer to 8 - ELECTRICAL/
FRONT WIPERS/WASHERS - CLEANING). Refer to
the appropriate wiring information. The wiring infor-
mation includes wiring diagrams, proper wire and
connector repair procedures, details of wire harness
routing and retention, connector pin-out information
and location views for the various wire harness con-
nectors, splices and grounds.
The hard wired circuits and components of the
front wiper and washer system may be diagnosed
and tested using conventional diagnostic tools and
procedures. However, conventional diagnostic meth-
8R - 6 FRONT WIPERS/WASHERSWJ
FRONT WIPERS/WASHERS (Continued)
Page 614 of 2199
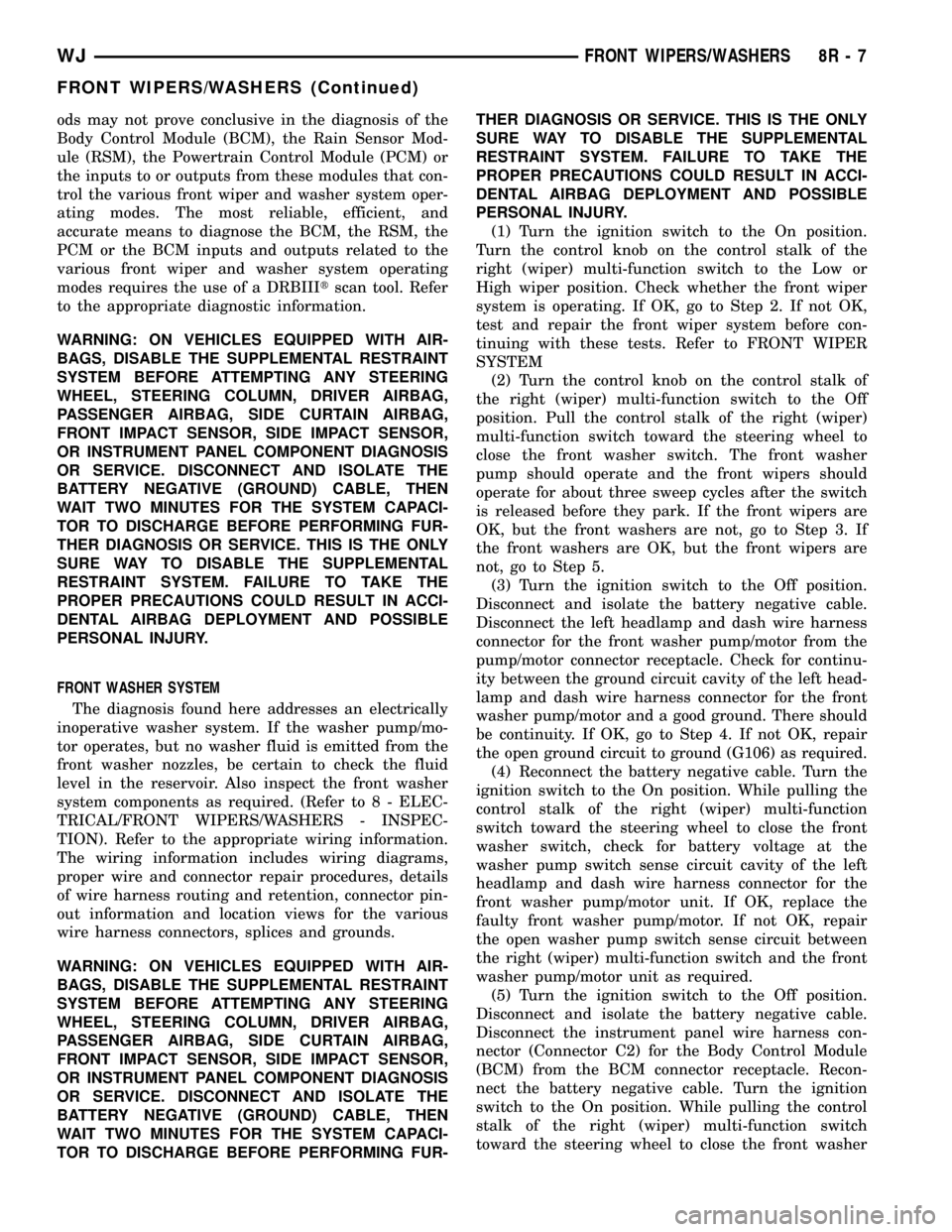
ods may not prove conclusive in the diagnosis of the
Body Control Module (BCM), the Rain Sensor Mod-
ule (RSM), the Powertrain Control Module (PCM) or
the inputs to or outputs from these modules that con-
trol the various front wiper and washer system oper-
ating modes. The most reliable, efficient, and
accurate means to diagnose the BCM, the RSM, the
PCM or the BCM inputs and outputs related to the
various front wiper and washer system operating
modes requires the use of a DRBIIItscan tool. Refer
to the appropriate diagnostic information.
WARNING: ON VEHICLES EQUIPPED WITH AIR-
BAGS, DISABLE THE SUPPLEMENTAL RESTRAINT
SYSTEM BEFORE ATTEMPTING ANY STEERING
WHEEL, STEERING COLUMN, DRIVER AIRBAG,
PASSENGER AIRBAG, SIDE CURTAIN AIRBAG,
FRONT IMPACT SENSOR, SIDE IMPACT SENSOR,
OR INSTRUMENT PANEL COMPONENT DIAGNOSIS
OR SERVICE. DISCONNECT AND ISOLATE THE
BATTERY NEGATIVE (GROUND) CABLE, THEN
WAIT TWO MINUTES FOR THE SYSTEM CAPACI-
TOR TO DISCHARGE BEFORE PERFORMING FUR-
THER DIAGNOSIS OR SERVICE. THIS IS THE ONLY
SURE WAY TO DISABLE THE SUPPLEMENTAL
RESTRAINT SYSTEM. FAILURE TO TAKE THE
PROPER PRECAUTIONS COULD RESULT IN ACCI-
DENTAL AIRBAG DEPLOYMENT AND POSSIBLE
PERSONAL INJURY.
FRONT WASHER SYSTEM
The diagnosis found here addresses an electrically
inoperative washer system. If the washer pump/mo-
tor operates, but no washer fluid is emitted from the
front washer nozzles, be certain to check the fluid
level in the reservoir. Also inspect the front washer
system components as required. (Refer to 8 - ELEC-
TRICAL/FRONT WIPERS/WASHERS - INSPEC-
TION). Refer to the appropriate wiring information.
The wiring information includes wiring diagrams,
proper wire and connector repair procedures, details
of wire harness routing and retention, connector pin-
out information and location views for the various
wire harness connectors, splices and grounds.
WARNING: ON VEHICLES EQUIPPED WITH AIR-
BAGS, DISABLE THE SUPPLEMENTAL RESTRAINT
SYSTEM BEFORE ATTEMPTING ANY STEERING
WHEEL, STEERING COLUMN, DRIVER AIRBAG,
PASSENGER AIRBAG, SIDE CURTAIN AIRBAG,
FRONT IMPACT SENSOR, SIDE IMPACT SENSOR,
OR INSTRUMENT PANEL COMPONENT DIAGNOSIS
OR SERVICE. DISCONNECT AND ISOLATE THE
BATTERY NEGATIVE (GROUND) CABLE, THEN
WAIT TWO MINUTES FOR THE SYSTEM CAPACI-
TOR TO DISCHARGE BEFORE PERFORMING FUR-THER DIAGNOSIS OR SERVICE. THIS IS THE ONLY
SURE WAY TO DISABLE THE SUPPLEMENTAL
RESTRAINT SYSTEM. FAILURE TO TAKE THE
PROPER PRECAUTIONS COULD RESULT IN ACCI-
DENTAL AIRBAG DEPLOYMENT AND POSSIBLE
PERSONAL INJURY.
(1) Turn the ignition switch to the On position.
Turn the control knob on the control stalk of the
right (wiper) multi-function switch to the Low or
High wiper position. Check whether the front wiper
system is operating. If OK, go to Step 2. If not OK,
test and repair the front wiper system before con-
tinuing with these tests. Refer to FRONT WIPER
SYSTEM
(2) Turn the control knob on the control stalk of
the right (wiper) multi-function switch to the Off
position. Pull the control stalk of the right (wiper)
multi-function switch toward the steering wheel to
close the front washer switch. The front washer
pump should operate and the front wipers should
operate for about three sweep cycles after the switch
is released before they park. If the front wipers are
OK, but the front washers are not, go to Step 3. If
the front washers are OK, but the front wipers are
not, go to Step 5.
(3) Turn the ignition switch to the Off position.
Disconnect and isolate the battery negative cable.
Disconnect the left headlamp and dash wire harness
connector for the front washer pump/motor from the
pump/motor connector receptacle. Check for continu-
ity between the ground circuit cavity of the left head-
lamp and dash wire harness connector for the front
washer pump/motor and a good ground. There should
be continuity. If OK, go to Step 4. If not OK, repair
the open ground circuit to ground (G106) as required.
(4) Reconnect the battery negative cable. Turn the
ignition switch to the On position. While pulling the
control stalk of the right (wiper) multi-function
switch toward the steering wheel to close the front
washer switch, check for battery voltage at the
washer pump switch sense circuit cavity of the left
headlamp and dash wire harness connector for the
front washer pump/motor unit. If OK, replace the
faulty front washer pump/motor. If not OK, repair
the open washer pump switch sense circuit between
the right (wiper) multi-function switch and the front
washer pump/motor unit as required.
(5) Turn the ignition switch to the Off position.
Disconnect and isolate the battery negative cable.
Disconnect the instrument panel wire harness con-
nector (Connector C2) for the Body Control Module
(BCM) from the BCM connector receptacle. Recon-
nect the battery negative cable. Turn the ignition
switch to the On position. While pulling the control
stalk of the right (wiper) multi-function switch
toward the steering wheel to close the front washer
WJFRONT WIPERS/WASHERS 8R - 7
FRONT WIPERS/WASHERS (Continued)
Page 615 of 2199
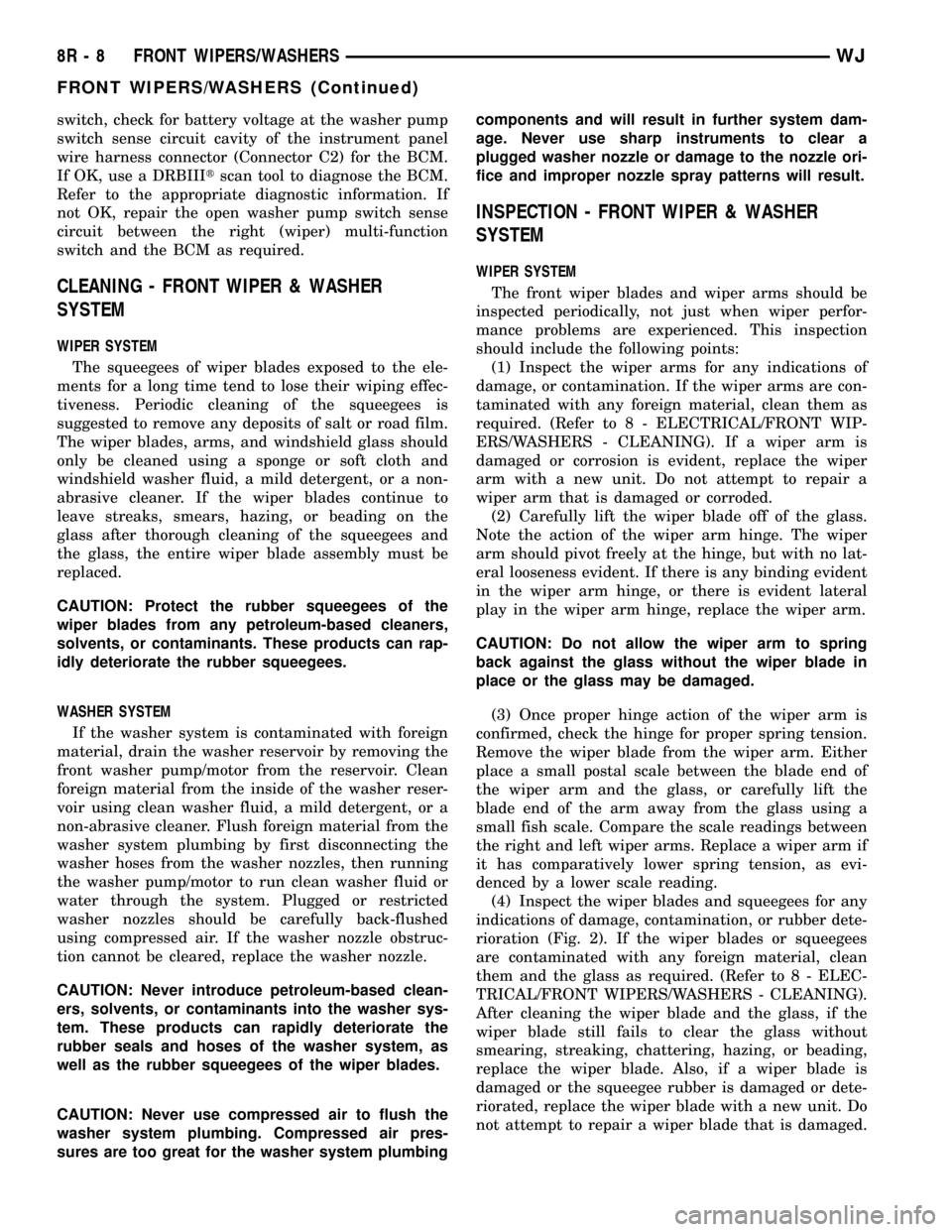
switch, check for battery voltage at the washer pump
switch sense circuit cavity of the instrument panel
wire harness connector (Connector C2) for the BCM.
If OK, use a DRBIIItscan tool to diagnose the BCM.
Refer to the appropriate diagnostic information. If
not OK, repair the open washer pump switch sense
circuit between the right (wiper) multi-function
switch and the BCM as required.
CLEANING - FRONT WIPER & WASHER
SYSTEM
WIPER SYSTEM
The squeegees of wiper blades exposed to the ele-
ments for a long time tend to lose their wiping effec-
tiveness. Periodic cleaning of the squeegees is
suggested to remove any deposits of salt or road film.
The wiper blades, arms, and windshield glass should
only be cleaned using a sponge or soft cloth and
windshield washer fluid, a mild detergent, or a non-
abrasive cleaner. If the wiper blades continue to
leave streaks, smears, hazing, or beading on the
glass after thorough cleaning of the squeegees and
the glass, the entire wiper blade assembly must be
replaced.
CAUTION: Protect the rubber squeegees of the
wiper blades from any petroleum-based cleaners,
solvents, or contaminants. These products can rap-
idly deteriorate the rubber squeegees.
WASHER SYSTEM
If the washer system is contaminated with foreign
material, drain the washer reservoir by removing the
front washer pump/motor from the reservoir. Clean
foreign material from the inside of the washer reser-
voir using clean washer fluid, a mild detergent, or a
non-abrasive cleaner. Flush foreign material from the
washer system plumbing by first disconnecting the
washer hoses from the washer nozzles, then running
the washer pump/motor to run clean washer fluid or
water through the system. Plugged or restricted
washer nozzles should be carefully back-flushed
using compressed air. If the washer nozzle obstruc-
tion cannot be cleared, replace the washer nozzle.
CAUTION: Never introduce petroleum-based clean-
ers, solvents, or contaminants into the washer sys-
tem. These products can rapidly deteriorate the
rubber seals and hoses of the washer system, as
well as the rubber squeegees of the wiper blades.
CAUTION: Never use compressed air to flush the
washer system plumbing. Compressed air pres-
sures are too great for the washer system plumbingcomponents and will result in further system dam-
age. Never use sharp instruments to clear a
plugged washer nozzle or damage to the nozzle ori-
fice and improper nozzle spray patterns will result.
INSPECTION - FRONT WIPER & WASHER
SYSTEM
WIPER SYSTEM
The front wiper blades and wiper arms should be
inspected periodically, not just when wiper perfor-
mance problems are experienced. This inspection
should include the following points:
(1) Inspect the wiper arms for any indications of
damage, or contamination. If the wiper arms are con-
taminated with any foreign material, clean them as
required. (Refer to 8 - ELECTRICAL/FRONT WIP-
ERS/WASHERS - CLEANING). If a wiper arm is
damaged or corrosion is evident, replace the wiper
arm with a new unit. Do not attempt to repair a
wiper arm that is damaged or corroded.
(2) Carefully lift the wiper blade off of the glass.
Note the action of the wiper arm hinge. The wiper
arm should pivot freely at the hinge, but with no lat-
eral looseness evident. If there is any binding evident
in the wiper arm hinge, or there is evident lateral
play in the wiper arm hinge, replace the wiper arm.
CAUTION: Do not allow the wiper arm to spring
back against the glass without the wiper blade in
place or the glass may be damaged.
(3) Once proper hinge action of the wiper arm is
confirmed, check the hinge for proper spring tension.
Remove the wiper blade from the wiper arm. Either
place a small postal scale between the blade end of
the wiper arm and the glass, or carefully lift the
blade end of the arm away from the glass using a
small fish scale. Compare the scale readings between
the right and left wiper arms. Replace a wiper arm if
it has comparatively lower spring tension, as evi-
denced by a lower scale reading.
(4) Inspect the wiper blades and squeegees for any
indications of damage, contamination, or rubber dete-
rioration (Fig. 2). If the wiper blades or squeegees
are contaminated with any foreign material, clean
them and the glass as required. (Refer to 8 - ELEC-
TRICAL/FRONT WIPERS/WASHERS - CLEANING).
After cleaning the wiper blade and the glass, if the
wiper blade still fails to clear the glass without
smearing, streaking, chattering, hazing, or beading,
replace the wiper blade. Also, if a wiper blade is
damaged or the squeegee rubber is damaged or dete-
riorated, replace the wiper blade with a new unit. Do
not attempt to repair a wiper blade that is damaged.
8R - 8 FRONT WIPERS/WASHERSWJ
FRONT WIPERS/WASHERS (Continued)
Page 616 of 2199
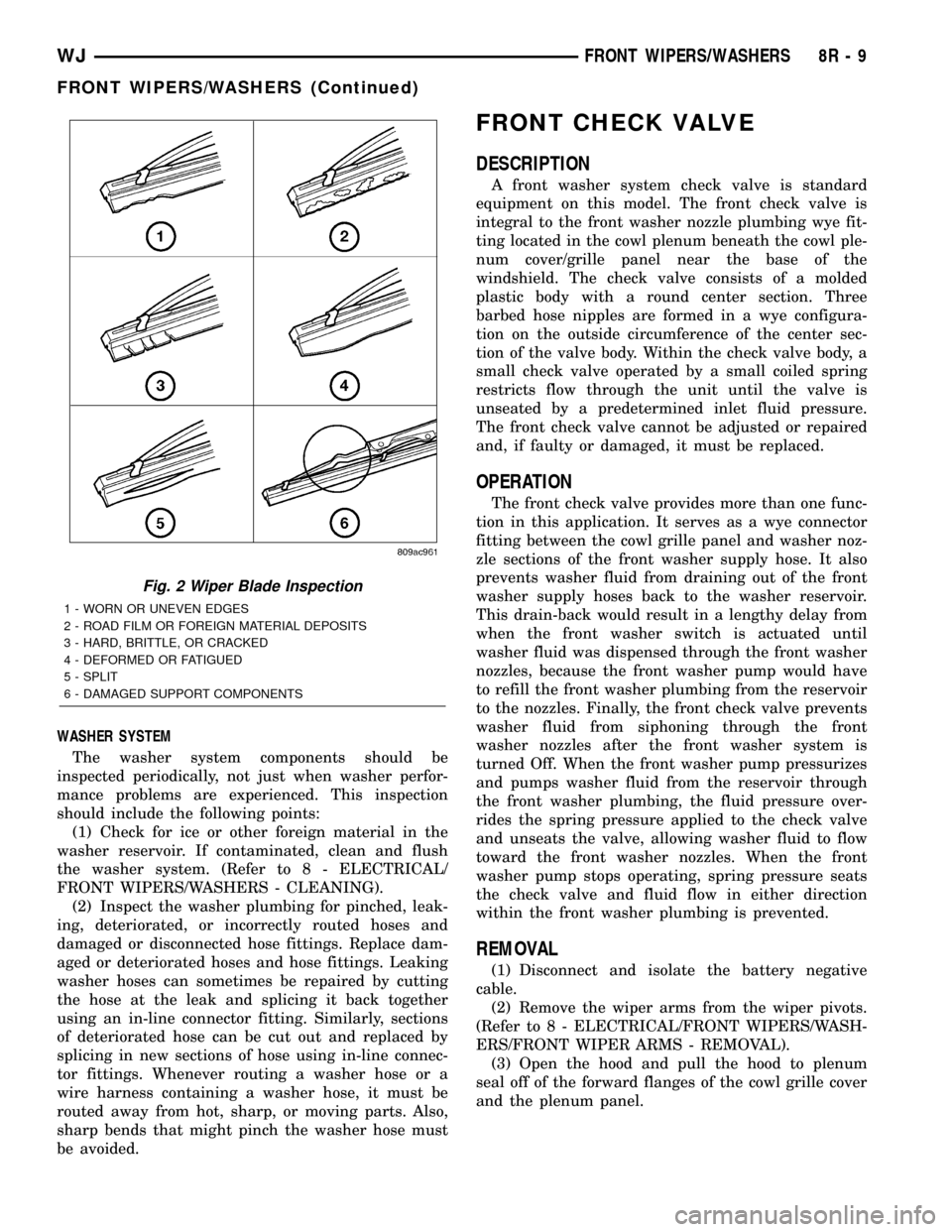
WASHER SYSTEM
The washer system components should be
inspected periodically, not just when washer perfor-
mance problems are experienced. This inspection
should include the following points:
(1) Check for ice or other foreign material in the
washer reservoir. If contaminated, clean and flush
the washer system. (Refer to 8 - ELECTRICAL/
FRONT WIPERS/WASHERS - CLEANING).
(2) Inspect the washer plumbing for pinched, leak-
ing, deteriorated, or incorrectly routed hoses and
damaged or disconnected hose fittings. Replace dam-
aged or deteriorated hoses and hose fittings. Leaking
washer hoses can sometimes be repaired by cutting
the hose at the leak and splicing it back together
using an in-line connector fitting. Similarly, sections
of deteriorated hose can be cut out and replaced by
splicing in new sections of hose using in-line connec-
tor fittings. Whenever routing a washer hose or a
wire harness containing a washer hose, it must be
routed away from hot, sharp, or moving parts. Also,
sharp bends that might pinch the washer hose must
be avoided.
FRONT CHECK VALVE
DESCRIPTION
A front washer system check valve is standard
equipment on this model. The front check valve is
integral to the front washer nozzle plumbing wye fit-
ting located in the cowl plenum beneath the cowl ple-
num cover/grille panel near the base of the
windshield. The check valve consists of a molded
plastic body with a round center section. Three
barbed hose nipples are formed in a wye configura-
tion on the outside circumference of the center sec-
tion of the valve body. Within the check valve body, a
small check valve operated by a small coiled spring
restricts flow through the unit until the valve is
unseated by a predetermined inlet fluid pressure.
The front check valve cannot be adjusted or repaired
and, if faulty or damaged, it must be replaced.
OPERATION
The front check valve provides more than one func-
tion in this application. It serves as a wye connector
fitting between the cowl grille panel and washer noz-
zle sections of the front washer supply hose. It also
prevents washer fluid from draining out of the front
washer supply hoses back to the washer reservoir.
This drain-back would result in a lengthy delay from
when the front washer switch is actuated until
washer fluid was dispensed through the front washer
nozzles, because the front washer pump would have
to refill the front washer plumbing from the reservoir
to the nozzles. Finally, the front check valve prevents
washer fluid from siphoning through the front
washer nozzles after the front washer system is
turned Off. When the front washer pump pressurizes
and pumps washer fluid from the reservoir through
the front washer plumbing, the fluid pressure over-
rides the spring pressure applied to the check valve
and unseats the valve, allowing washer fluid to flow
toward the front washer nozzles. When the front
washer pump stops operating, spring pressure seats
the check valve and fluid flow in either direction
within the front washer plumbing is prevented.
REMOVAL
(1) Disconnect and isolate the battery negative
cable.
(2) Remove the wiper arms from the wiper pivots.
(Refer to 8 - ELECTRICAL/FRONT WIPERS/WASH-
ERS/FRONT WIPER ARMS - REMOVAL).
(3) Open the hood and pull the hood to plenum
seal off of the forward flanges of the cowl grille cover
and the plenum panel.
Fig. 2 Wiper Blade Inspection
1 - WORN OR UNEVEN EDGES
2 - ROAD FILM OR FOREIGN MATERIAL DEPOSITS
3 - HARD, BRITTLE, OR CRACKED
4 - DEFORMED OR FATIGUED
5 - SPLIT
6 - DAMAGED SUPPORT COMPONENTS
WJFRONT WIPERS/WASHERS 8R - 9
FRONT WIPERS/WASHERS (Continued)
Page 617 of 2199
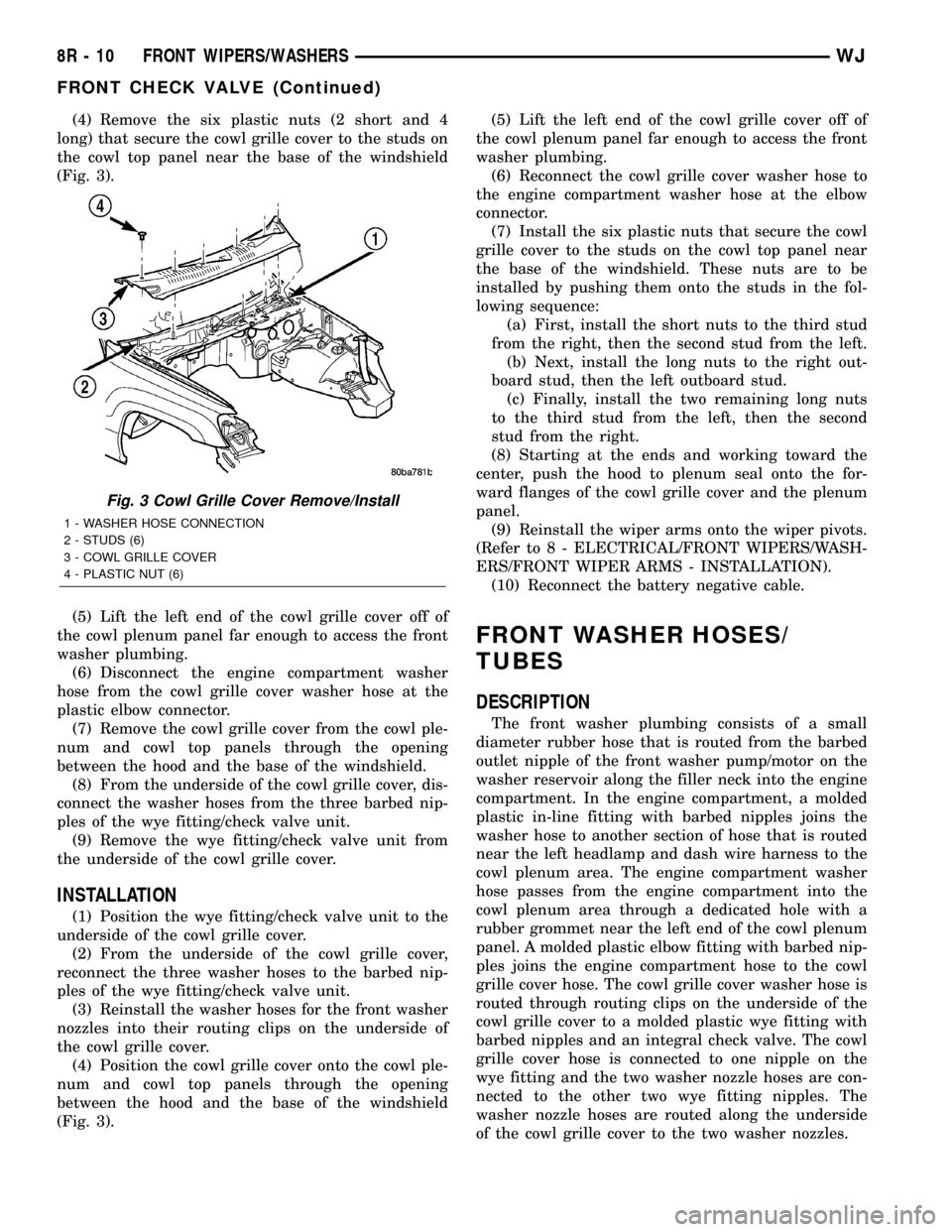
(4) Remove the six plastic nuts (2 short and 4
long) that secure the cowl grille cover to the studs on
the cowl top panel near the base of the windshield
(Fig. 3).
(5) Lift the left end of the cowl grille cover off of
the cowl plenum panel far enough to access the front
washer plumbing.
(6) Disconnect the engine compartment washer
hose from the cowl grille cover washer hose at the
plastic elbow connector.
(7) Remove the cowl grille cover from the cowl ple-
num and cowl top panels through the opening
between the hood and the base of the windshield.
(8) From the underside of the cowl grille cover, dis-
connect the washer hoses from the three barbed nip-
ples of the wye fitting/check valve unit.
(9) Remove the wye fitting/check valve unit from
the underside of the cowl grille cover.
INSTALLATION
(1) Position the wye fitting/check valve unit to the
underside of the cowl grille cover.
(2) From the underside of the cowl grille cover,
reconnect the three washer hoses to the barbed nip-
ples of the wye fitting/check valve unit.
(3) Reinstall the washer hoses for the front washer
nozzles into their routing clips on the underside of
the cowl grille cover.
(4) Position the cowl grille cover onto the cowl ple-
num and cowl top panels through the opening
between the hood and the base of the windshield
(Fig. 3).(5) Lift the left end of the cowl grille cover off of
the cowl plenum panel far enough to access the front
washer plumbing.
(6) Reconnect the cowl grille cover washer hose to
the engine compartment washer hose at the elbow
connector.
(7) Install the six plastic nuts that secure the cowl
grille cover to the studs on the cowl top panel near
the base of the windshield. These nuts are to be
installed by pushing them onto the studs in the fol-
lowing sequence:
(a) First, install the short nuts to the third stud
from the right, then the second stud from the left.
(b) Next, install the long nuts to the right out-
board stud, then the left outboard stud.
(c) Finally, install the two remaining long nuts
to the third stud from the left, then the second
stud from the right.
(8) Starting at the ends and working toward the
center, push the hood to plenum seal onto the for-
ward flanges of the cowl grille cover and the plenum
panel.
(9) Reinstall the wiper arms onto the wiper pivots.
(Refer to 8 - ELECTRICAL/FRONT WIPERS/WASH-
ERS/FRONT WIPER ARMS - INSTALLATION).
(10) Reconnect the battery negative cable.
FRONT WASHER HOSES/
TUBES
DESCRIPTION
The front washer plumbing consists of a small
diameter rubber hose that is routed from the barbed
outlet nipple of the front washer pump/motor on the
washer reservoir along the filler neck into the engine
compartment. In the engine compartment, a molded
plastic in-line fitting with barbed nipples joins the
washer hose to another section of hose that is routed
near the left headlamp and dash wire harness to the
cowl plenum area. The engine compartment washer
hose passes from the engine compartment into the
cowl plenum area through a dedicated hole with a
rubber grommet near the left end of the cowl plenum
panel. A molded plastic elbow fitting with barbed nip-
ples joins the engine compartment hose to the cowl
grille cover hose. The cowl grille cover washer hose is
routed through routing clips on the underside of the
cowl grille cover to a molded plastic wye fitting with
barbed nipples and an integral check valve. The cowl
grille cover hose is connected to one nipple on the
wye fitting and the two washer nozzle hoses are con-
nected to the other two wye fitting nipples. The
washer nozzle hoses are routed along the underside
of the cowl grille cover to the two washer nozzles.
Fig. 3 Cowl Grille Cover Remove/Install
1 - WASHER HOSE CONNECTION
2 - STUDS (6)
3 - COWL GRILLE COVER
4 - PLASTIC NUT (6)
8R - 10 FRONT WIPERS/WASHERSWJ
FRONT CHECK VALVE (Continued)
Page 618 of 2199
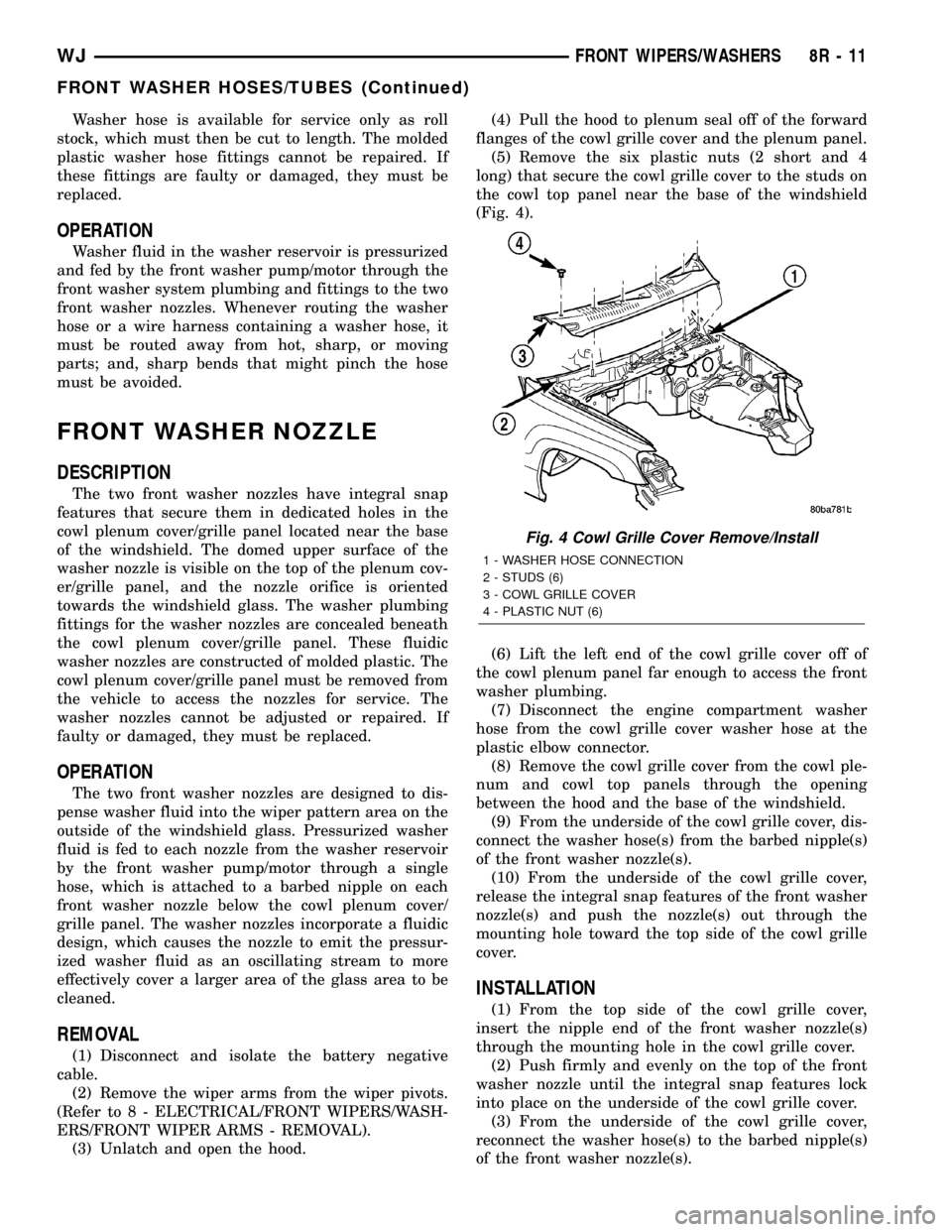
Washer hose is available for service only as roll
stock, which must then be cut to length. The molded
plastic washer hose fittings cannot be repaired. If
these fittings are faulty or damaged, they must be
replaced.
OPERATION
Washer fluid in the washer reservoir is pressurized
and fed by the front washer pump/motor through the
front washer system plumbing and fittings to the two
front washer nozzles. Whenever routing the washer
hose or a wire harness containing a washer hose, it
must be routed away from hot, sharp, or moving
parts; and, sharp bends that might pinch the hose
must be avoided.
FRONT WASHER NOZZLE
DESCRIPTION
The two front washer nozzles have integral snap
features that secure them in dedicated holes in the
cowl plenum cover/grille panel located near the base
of the windshield. The domed upper surface of the
washer nozzle is visible on the top of the plenum cov-
er/grille panel, and the nozzle orifice is oriented
towards the windshield glass. The washer plumbing
fittings for the washer nozzles are concealed beneath
the cowl plenum cover/grille panel. These fluidic
washer nozzles are constructed of molded plastic. The
cowl plenum cover/grille panel must be removed from
the vehicle to access the nozzles for service. The
washer nozzles cannot be adjusted or repaired. If
faulty or damaged, they must be replaced.
OPERATION
The two front washer nozzles are designed to dis-
pense washer fluid into the wiper pattern area on the
outside of the windshield glass. Pressurized washer
fluid is fed to each nozzle from the washer reservoir
by the front washer pump/motor through a single
hose, which is attached to a barbed nipple on each
front washer nozzle below the cowl plenum cover/
grille panel. The washer nozzles incorporate a fluidic
design, which causes the nozzle to emit the pressur-
ized washer fluid as an oscillating stream to more
effectively cover a larger area of the glass area to be
cleaned.
REMOVAL
(1) Disconnect and isolate the battery negative
cable.
(2) Remove the wiper arms from the wiper pivots.
(Refer to 8 - ELECTRICAL/FRONT WIPERS/WASH-
ERS/FRONT WIPER ARMS - REMOVAL).
(3) Unlatch and open the hood.(4) Pull the hood to plenum seal off of the forward
flanges of the cowl grille cover and the plenum panel.
(5) Remove the six plastic nuts (2 short and 4
long) that secure the cowl grille cover to the studs on
the cowl top panel near the base of the windshield
(Fig. 4).
(6) Lift the left end of the cowl grille cover off of
the cowl plenum panel far enough to access the front
washer plumbing.
(7) Disconnect the engine compartment washer
hose from the cowl grille cover washer hose at the
plastic elbow connector.
(8) Remove the cowl grille cover from the cowl ple-
num and cowl top panels through the opening
between the hood and the base of the windshield.
(9) From the underside of the cowl grille cover, dis-
connect the washer hose(s) from the barbed nipple(s)
of the front washer nozzle(s).
(10) From the underside of the cowl grille cover,
release the integral snap features of the front washer
nozzle(s) and push the nozzle(s) out through the
mounting hole toward the top side of the cowl grille
cover.
INSTALLATION
(1) From the top side of the cowl grille cover,
insert the nipple end of the front washer nozzle(s)
through the mounting hole in the cowl grille cover.
(2) Push firmly and evenly on the top of the front
washer nozzle until the integral snap features lock
into place on the underside of the cowl grille cover.
(3) From the underside of the cowl grille cover,
reconnect the washer hose(s) to the barbed nipple(s)
of the front washer nozzle(s).
Fig. 4 Cowl Grille Cover Remove/Install
1 - WASHER HOSE CONNECTION
2 - STUDS (6)
3 - COWL GRILLE COVER
4 - PLASTIC NUT (6)
WJFRONT WIPERS/WASHERS 8R - 11
FRONT WASHER HOSES/TUBES (Continued)