head JEEP GRAND CHEROKEE 2002 WJ / 2.G Service Manual
[x] Cancel search | Manufacturer: JEEP, Model Year: 2002, Model line: GRAND CHEROKEE, Model: JEEP GRAND CHEROKEE 2002 WJ / 2.GPages: 2199, PDF Size: 76.01 MB
Page 284 of 2199
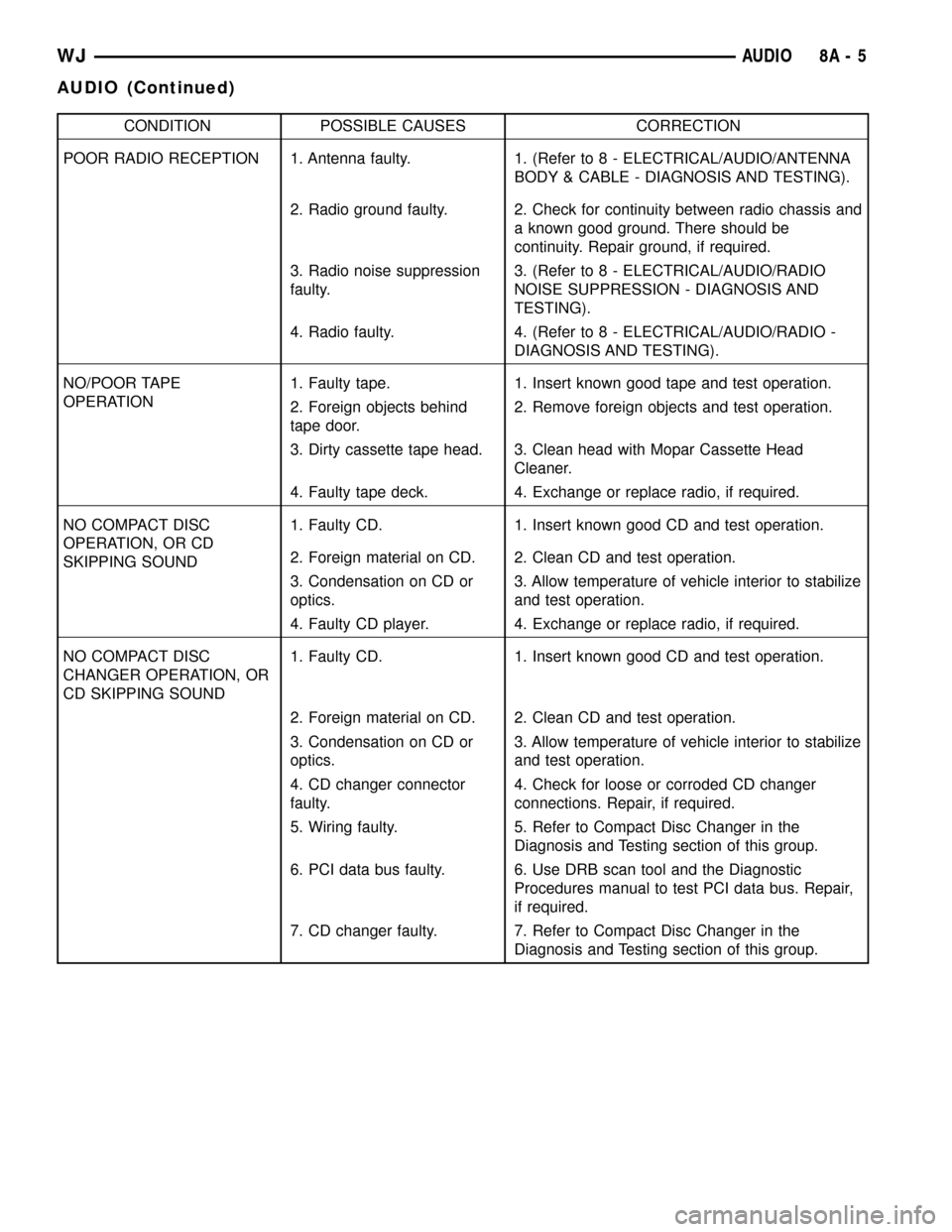
CONDITION POSSIBLE CAUSES CORRECTION
POOR RADIO RECEPTION 1. Antenna faulty. 1. (Refer to 8 - ELECTRICAL/AUDIO/ANTENNA
BODY & CABLE - DIAGNOSIS AND TESTING).
2. Radio ground faulty. 2. Check for continuity between radio chassis and
a known good ground. There should be
continuity. Repair ground, if required.
3. Radio noise suppression
faulty.3. (Refer to 8 - ELECTRICAL/AUDIO/RADIO
NOISE SUPPRESSION - DIAGNOSIS AND
TESTING).
4. Radio faulty. 4. (Refer to 8 - ELECTRICAL/AUDIO/RADIO -
DIAGNOSIS AND TESTING).
NO/POOR TAPE
OPERATION1. Faulty tape. 1. Insert known good tape and test operation.
2. Foreign objects behind
tape door.2. Remove foreign objects and test operation.
3. Dirty cassette tape head. 3. Clean head with Mopar Cassette Head
Cleaner.
4. Faulty tape deck. 4. Exchange or replace radio, if required.
NO COMPACT DISC
OPERATION, OR CD
SKIPPING SOUND1. Faulty CD. 1. Insert known good CD and test operation.
2. Foreign material on CD. 2. Clean CD and test operation.
3. Condensation on CD or
optics.3. Allow temperature of vehicle interior to stabilize
and test operation.
4. Faulty CD player. 4. Exchange or replace radio, if required.
NO COMPACT DISC
CHANGER OPERATION, OR
CD SKIPPING SOUND1. Faulty CD. 1. Insert known good CD and test operation.
2. Foreign material on CD. 2. Clean CD and test operation.
3. Condensation on CD or
optics.3. Allow temperature of vehicle interior to stabilize
and test operation.
4. CD changer connector
faulty.4. Check for loose or corroded CD changer
connections. Repair, if required.
5. Wiring faulty. 5. Refer to Compact Disc Changer in the
Diagnosis and Testing section of this group.
6. PCI data bus faulty. 6. Use DRB scan tool and the Diagnostic
Procedures manual to test PCI data bus. Repair,
if required.
7. CD changer faulty. 7. Refer to Compact Disc Changer in the
Diagnosis and Testing section of this group.
WJAUDIO 8A - 5
AUDIO (Continued)
Page 289 of 2199
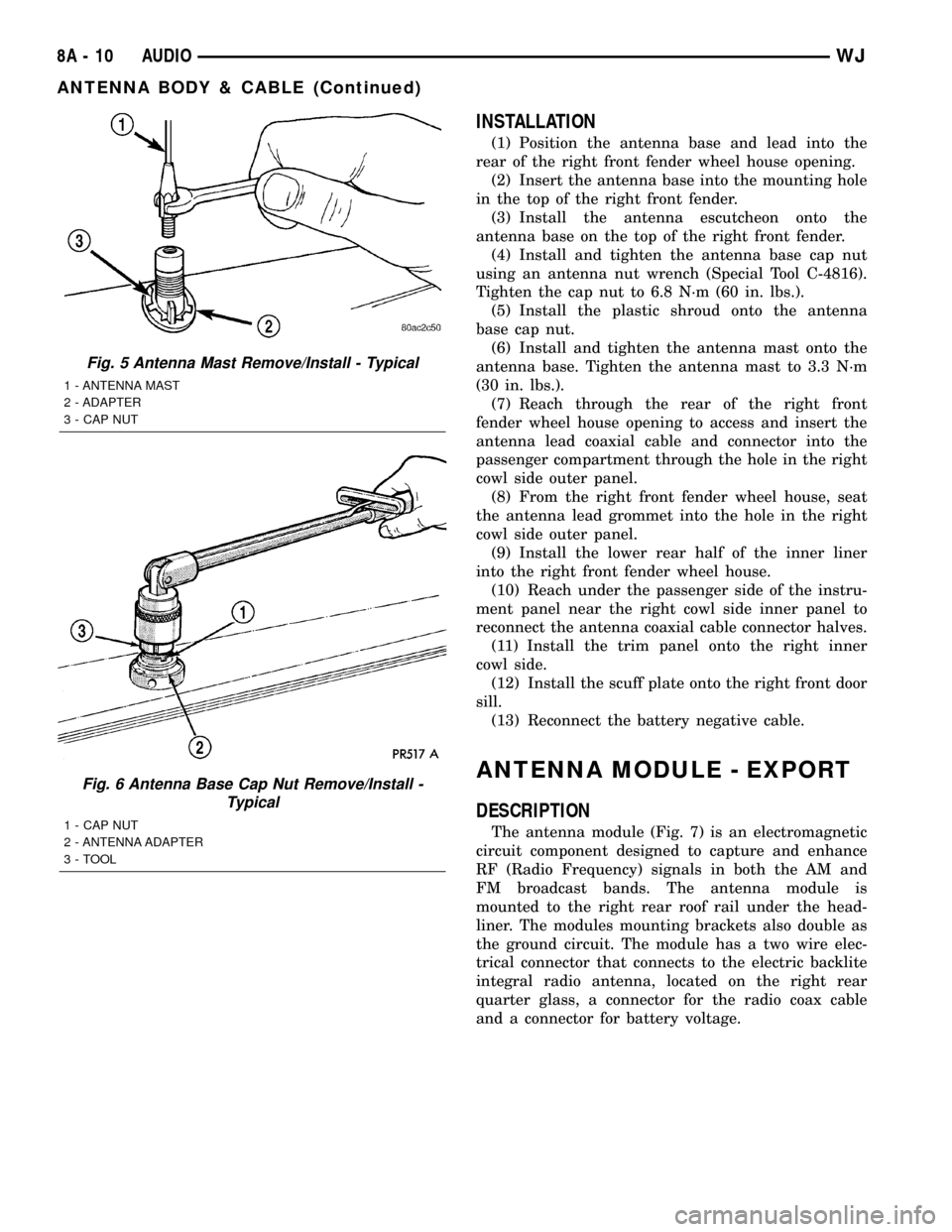
INSTALLATION
(1) Position the antenna base and lead into the
rear of the right front fender wheel house opening.
(2) Insert the antenna base into the mounting hole
in the top of the right front fender.
(3) Install the antenna escutcheon onto the
antenna base on the top of the right front fender.
(4) Install and tighten the antenna base cap nut
using an antenna nut wrench (Special Tool C-4816).
Tighten the cap nut to 6.8 N´m (60 in. lbs.).
(5) Install the plastic shroud onto the antenna
base cap nut.
(6) Install and tighten the antenna mast onto the
antenna base. Tighten the antenna mast to 3.3 N´m
(30 in. lbs.).
(7) Reach through the rear of the right front
fender wheel house opening to access and insert the
antenna lead coaxial cable and connector into the
passenger compartment through the hole in the right
cowl side outer panel.
(8) From the right front fender wheel house, seat
the antenna lead grommet into the hole in the right
cowl side outer panel.
(9) Install the lower rear half of the inner liner
into the right front fender wheel house.
(10) Reach under the passenger side of the instru-
ment panel near the right cowl side inner panel to
reconnect the antenna coaxial cable connector halves.
(11) Install the trim panel onto the right inner
cowl side.
(12) Install the scuff plate onto the right front door
sill.
(13) Reconnect the battery negative cable.
ANTENNA MODULE - EXPORT
DESCRIPTION
The antenna module (Fig. 7) is an electromagnetic
circuit component designed to capture and enhance
RF (Radio Frequency) signals in both the AM and
FM broadcast bands. The antenna module is
mounted to the right rear roof rail under the head-
liner. The modules mounting brackets also double as
the ground circuit. The module has a two wire elec-
trical connector that connects to the electric backlite
integral radio antenna, located on the right rear
quarter glass, a connector for the radio coax cable
and a connector for battery voltage.
Fig. 5 Antenna Mast Remove/Install - Typical
1 - ANTENNA MAST
2 - ADAPTER
3 - CAP NUT
Fig. 6 Antenna Base Cap Nut Remove/Install -
Typical
1 - CAP NUT
2 - ANTENNA ADAPTER
3 - TOOL
8A - 10 AUDIOWJ
ANTENNA BODY & CABLE (Continued)
Page 291 of 2199
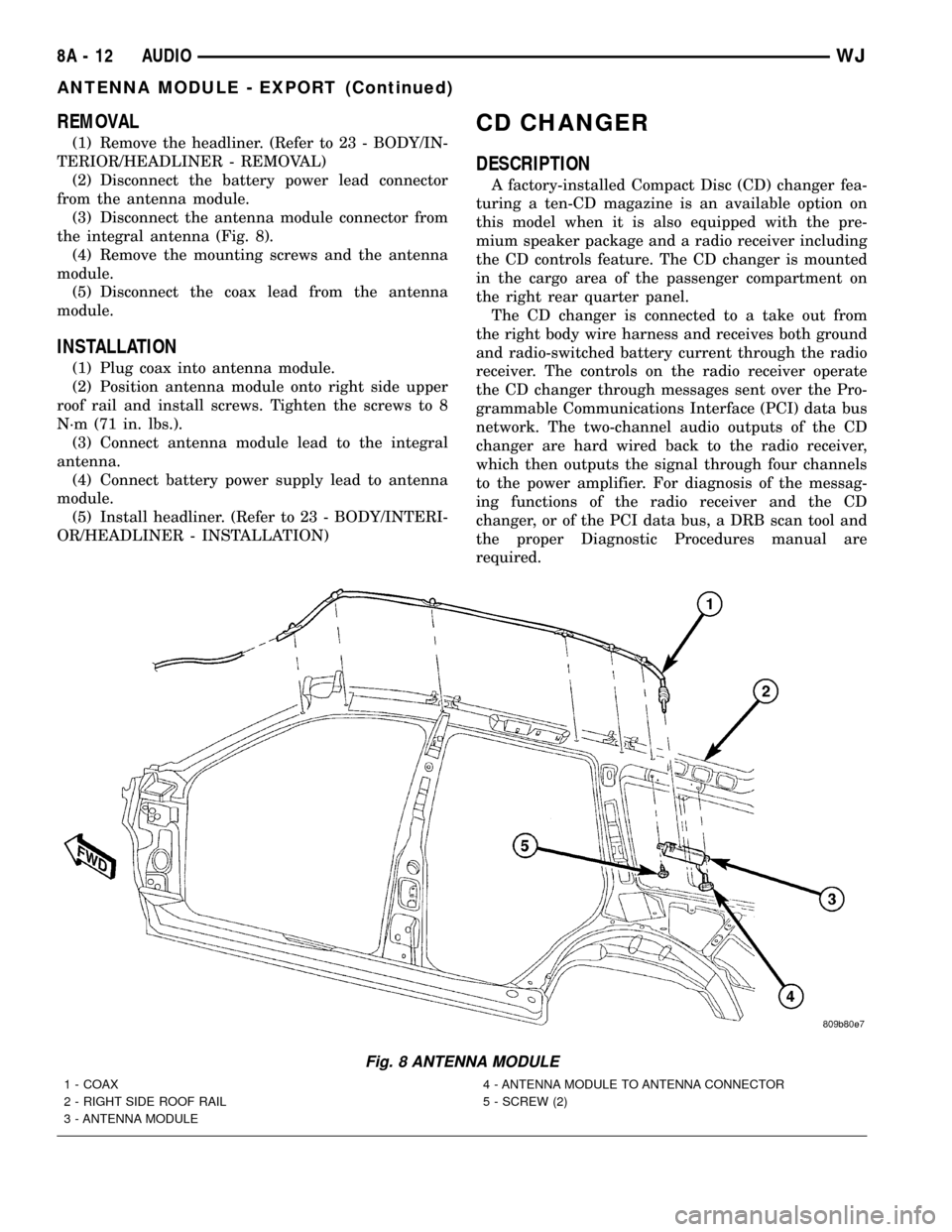
REMOVAL
(1) Remove the headliner. (Refer to 23 - BODY/IN-
TERIOR/HEADLINER - REMOVAL)
(2) Disconnect the battery power lead connector
from the antenna module.
(3) Disconnect the antenna module connector from
the integral antenna (Fig. 8).
(4) Remove the mounting screws and the antenna
module.
(5) Disconnect the coax lead from the antenna
module.
INSTALLATION
(1) Plug coax into antenna module.
(2) Position antenna module onto right side upper
roof rail and install screws. Tighten the screws to 8
N´m (71 in. lbs.).
(3) Connect antenna module lead to the integral
antenna.
(4) Connect battery power supply lead to antenna
module.
(5) Install headliner. (Refer to 23 - BODY/INTERI-
OR/HEADLINER - INSTALLATION)
CD CHANGER
DESCRIPTION
A factory-installed Compact Disc (CD) changer fea-
turing a ten-CD magazine is an available option on
this model when it is also equipped with the pre-
mium speaker package and a radio receiver including
the CD controls feature. The CD changer is mounted
in the cargo area of the passenger compartment on
the right rear quarter panel.
The CD changer is connected to a take out from
the right body wire harness and receives both ground
and radio-switched battery current through the radio
receiver. The controls on the radio receiver operate
the CD changer through messages sent over the Pro-
grammable Communications Interface (PCI) data bus
network. The two-channel audio outputs of the CD
changer are hard wired back to the radio receiver,
which then outputs the signal through four channels
to the power amplifier. For diagnosis of the messag-
ing functions of the radio receiver and the CD
changer, or of the PCI data bus, a DRB scan tool and
the proper Diagnostic Procedures manual are
required.
Fig. 8 ANTENNA MODULE
1 - COAX
2 - RIGHT SIDE ROOF RAIL
3 - ANTENNA MODULE4 - ANTENNA MODULE TO ANTENNA CONNECTOR
5 - SCREW (2)
8A - 12 AUDIOWJ
ANTENNA MODULE - EXPORT (Continued)
Page 297 of 2199
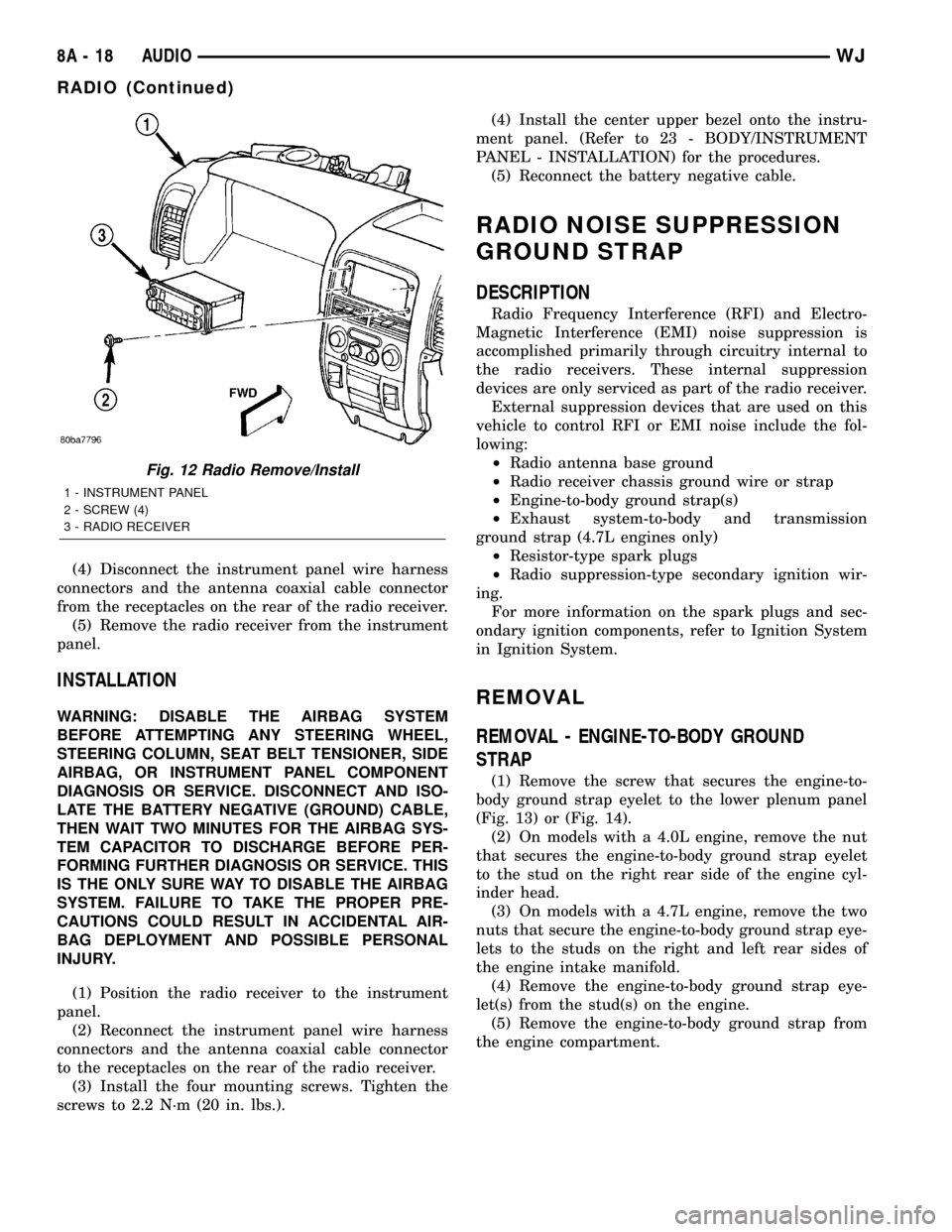
(4) Disconnect the instrument panel wire harness
connectors and the antenna coaxial cable connector
from the receptacles on the rear of the radio receiver.
(5) Remove the radio receiver from the instrument
panel.
INSTALLATION
WARNING: DISABLE THE AIRBAG SYSTEM
BEFORE ATTEMPTING ANY STEERING WHEEL,
STEERING COLUMN, SEAT BELT TENSIONER, SIDE
AIRBAG, OR INSTRUMENT PANEL COMPONENT
DIAGNOSIS OR SERVICE. DISCONNECT AND ISO-
LATE THE BATTERY NEGATIVE (GROUND) CABLE,
THEN WAIT TWO MINUTES FOR THE AIRBAG SYS-
TEM CAPACITOR TO DISCHARGE BEFORE PER-
FORMING FURTHER DIAGNOSIS OR SERVICE. THIS
IS THE ONLY SURE WAY TO DISABLE THE AIRBAG
SYSTEM. FAILURE TO TAKE THE PROPER PRE-
CAUTIONS COULD RESULT IN ACCIDENTAL AIR-
BAG DEPLOYMENT AND POSSIBLE PERSONAL
INJURY.
(1) Position the radio receiver to the instrument
panel.
(2) Reconnect the instrument panel wire harness
connectors and the antenna coaxial cable connector
to the receptacles on the rear of the radio receiver.
(3) Install the four mounting screws. Tighten the
screws to 2.2 N´m (20 in. lbs.).(4) Install the center upper bezel onto the instru-
ment panel. (Refer to 23 - BODY/INSTRUMENT
PANEL - INSTALLATION) for the procedures.
(5) Reconnect the battery negative cable.
RADIO NOISE SUPPRESSION
GROUND STRAP
DESCRIPTION
Radio Frequency Interference (RFI) and Electro-
Magnetic Interference (EMI) noise suppression is
accomplished primarily through circuitry internal to
the radio receivers. These internal suppression
devices are only serviced as part of the radio receiver.
External suppression devices that are used on this
vehicle to control RFI or EMI noise include the fol-
lowing:
²Radio antenna base ground
²Radio receiver chassis ground wire or strap
²Engine-to-body ground strap(s)
²Exhaust system-to-body and transmission
ground strap (4.7L engines only)
²Resistor-type spark plugs
²Radio suppression-type secondary ignition wir-
ing.
For more information on the spark plugs and sec-
ondary ignition components, refer to Ignition System
in Ignition System.
REMOVAL
REMOVAL - ENGINE-TO-BODY GROUND
STRAP
(1) Remove the screw that secures the engine-to-
body ground strap eyelet to the lower plenum panel
(Fig. 13) or (Fig. 14).
(2) On models with a 4.0L engine, remove the nut
that secures the engine-to-body ground strap eyelet
to the stud on the right rear side of the engine cyl-
inder head.
(3) On models with a 4.7L engine, remove the two
nuts that secure the engine-to-body ground strap eye-
lets to the studs on the right and left rear sides of
the engine intake manifold.
(4) Remove the engine-to-body ground strap eye-
let(s) from the stud(s) on the engine.
(5) Remove the engine-to-body ground strap from
the engine compartment.
Fig. 12 Radio Remove/Install
1 - INSTRUMENT PANEL
2 - SCREW (4)
3 - RADIO RECEIVER
8A - 18 AUDIOWJ
RADIO (Continued)
Page 298 of 2199
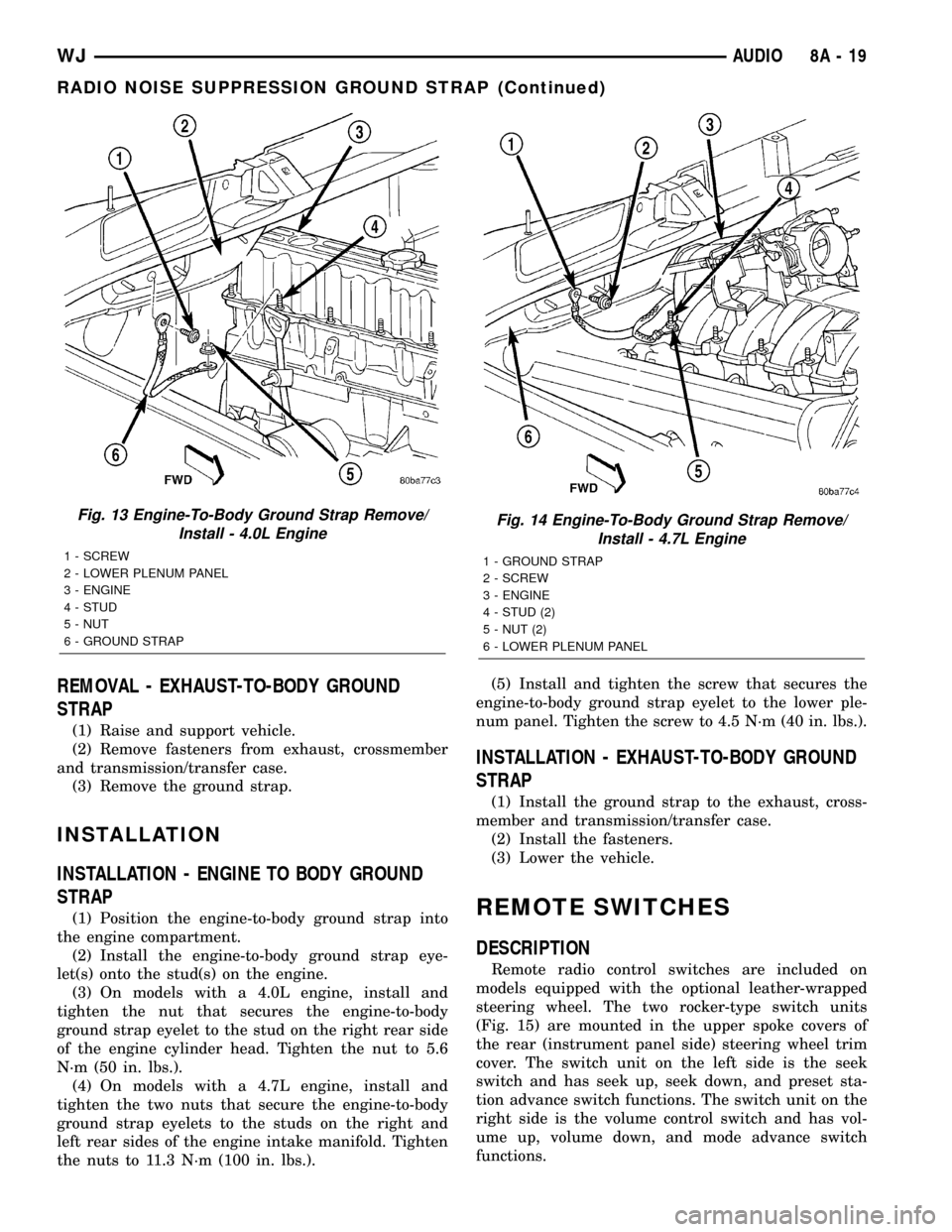
REMOVAL - EXHAUST-TO-BODY GROUND
STRAP
(1) Raise and support vehicle.
(2) Remove fasteners from exhaust, crossmember
and transmission/transfer case.
(3) Remove the ground strap.
INSTALLATION
INSTALLATION - ENGINE TO BODY GROUND
STRAP
(1) Position the engine-to-body ground strap into
the engine compartment.
(2) Install the engine-to-body ground strap eye-
let(s) onto the stud(s) on the engine.
(3) On models with a 4.0L engine, install and
tighten the nut that secures the engine-to-body
ground strap eyelet to the stud on the right rear side
of the engine cylinder head. Tighten the nut to 5.6
N´m (50 in. lbs.).
(4) On models with a 4.7L engine, install and
tighten the two nuts that secure the engine-to-body
ground strap eyelets to the studs on the right and
left rear sides of the engine intake manifold. Tighten
the nuts to 11.3 N´m (100 in. lbs.).(5) Install and tighten the screw that secures the
engine-to-body ground strap eyelet to the lower ple-
num panel. Tighten the screw to 4.5 N´m (40 in. lbs.).
INSTALLATION - EXHAUST-TO-BODY GROUND
STRAP
(1) Install the ground strap to the exhaust, cross-
member and transmission/transfer case.
(2) Install the fasteners.
(3) Lower the vehicle.
REMOTE SWITCHES
DESCRIPTION
Remote radio control switches are included on
models equipped with the optional leather-wrapped
steering wheel. The two rocker-type switch units
(Fig. 15) are mounted in the upper spoke covers of
the rear (instrument panel side) steering wheel trim
cover. The switch unit on the left side is the seek
switch and has seek up, seek down, and preset sta-
tion advance switch functions. The switch unit on the
right side is the volume control switch and has vol-
ume up, volume down, and mode advance switch
functions.
Fig. 13 Engine-To-Body Ground Strap Remove/
Install - 4.0L Engine
1 - SCREW
2 - LOWER PLENUM PANEL
3 - ENGINE
4 - STUD
5 - NUT
6 - GROUND STRAP
Fig. 14 Engine-To-Body Ground Strap Remove/
Install - 4.7L Engine
1 - GROUND STRAP
2 - SCREW
3 - ENGINE
4 - STUD (2)
5 - NUT (2)
6 - LOWER PLENUM PANEL
WJAUDIO 8A - 19
RADIO NOISE SUPPRESSION GROUND STRAP (Continued)
Page 306 of 2199
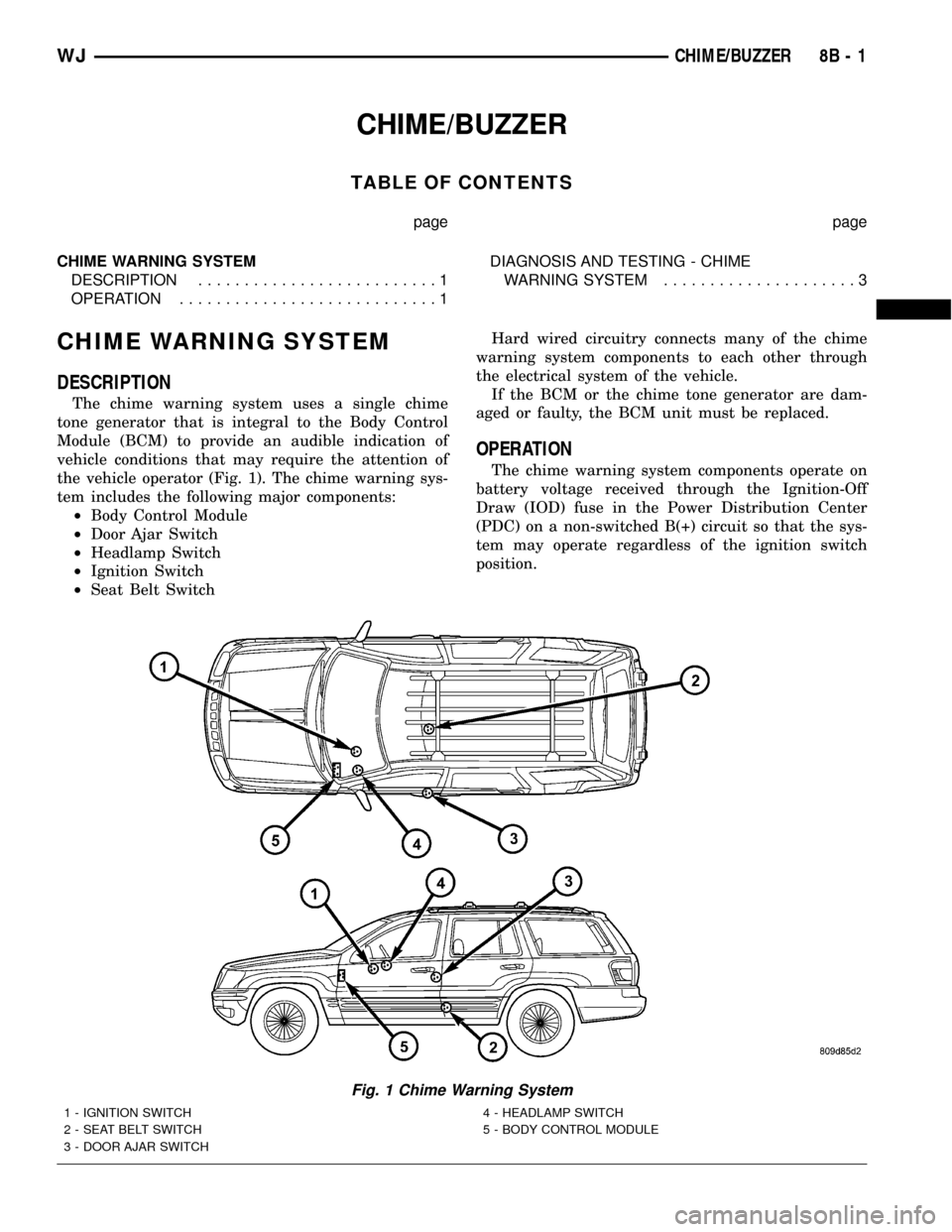
CHIME/BUZZER
TABLE OF CONTENTS
page page
CHIME WARNING SYSTEM
DESCRIPTION..........................1
OPERATION............................1DIAGNOSIS AND TESTING - CHIME
WARNING SYSTEM.....................3
CHIME WARNING SYSTEM
DESCRIPTION
The chime warning system uses a single chime
tone generator that is integral to the Body Control
Module (BCM) to provide an audible indication of
vehicle conditions that may require the attention of
the vehicle operator (Fig. 1). The chime warning sys-
tem includes the following major components:
²Body Control Module
²Door Ajar Switch
²Headlamp Switch
²Ignition Switch
²Seat Belt SwitchHard wired circuitry connects many of the chime
warning system components to each other through
the electrical system of the vehicle.
If the BCM or the chime tone generator are dam-
aged or faulty, the BCM unit must be replaced.
OPERATION
The chime warning system components operate on
battery voltage received through the Ignition-Off
Draw (IOD) fuse in the Power Distribution Center
(PDC) on a non-switched B(+) circuit so that the sys-
tem may operate regardless of the ignition switch
position.
Fig. 1 Chime Warning System
1 - IGNITION SWITCH
2 - SEAT BELT SWITCH
3 - DOOR AJAR SWITCH4 - HEADLAMP SWITCH
5 - BODY CONTROL MODULE
WJCHIME/BUZZER 8B - 1
Page 307 of 2199
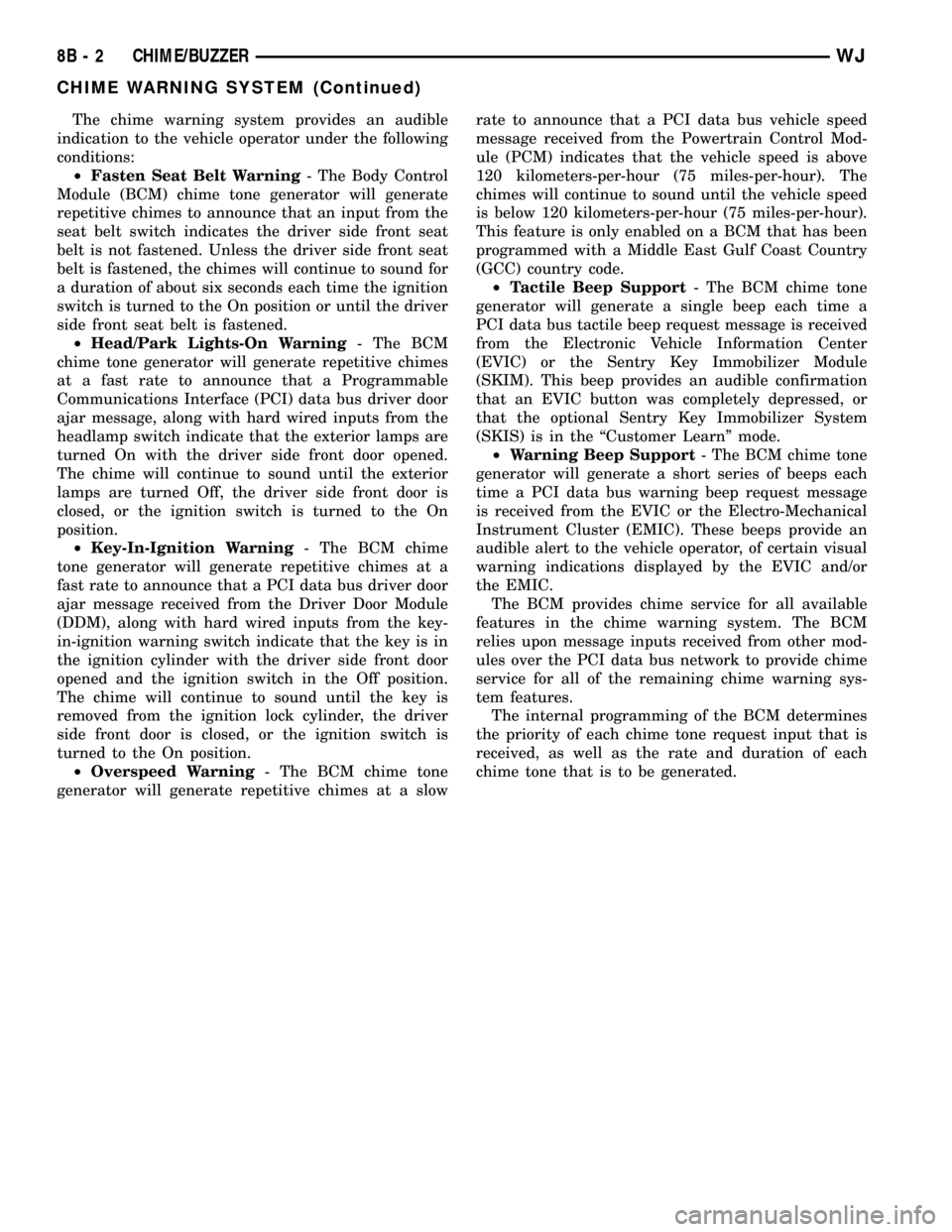
The chime warning system provides an audible
indication to the vehicle operator under the following
conditions:
²Fasten Seat Belt Warning- The Body Control
Module (BCM) chime tone generator will generate
repetitive chimes to announce that an input from the
seat belt switch indicates the driver side front seat
belt is not fastened. Unless the driver side front seat
belt is fastened, the chimes will continue to sound for
a duration of about six seconds each time the ignition
switch is turned to the On position or until the driver
side front seat belt is fastened.
²Head/Park Lights-On Warning- The BCM
chime tone generator will generate repetitive chimes
at a fast rate to announce that a Programmable
Communications Interface (PCI) data bus driver door
ajar message, along with hard wired inputs from the
headlamp switch indicate that the exterior lamps are
turned On with the driver side front door opened.
The chime will continue to sound until the exterior
lamps are turned Off, the driver side front door is
closed, or the ignition switch is turned to the On
position.
²Key-In-Ignition Warning- The BCM chime
tone generator will generate repetitive chimes at a
fast rate to announce that a PCI data bus driver door
ajar message received from the Driver Door Module
(DDM), along with hard wired inputs from the key-
in-ignition warning switch indicate that the key is in
the ignition cylinder with the driver side front door
opened and the ignition switch in the Off position.
The chime will continue to sound until the key is
removed from the ignition lock cylinder, the driver
side front door is closed, or the ignition switch is
turned to the On position.
²Overspeed Warning- The BCM chime tone
generator will generate repetitive chimes at a slowrate to announce that a PCI data bus vehicle speed
message received from the Powertrain Control Mod-
ule (PCM) indicates that the vehicle speed is above
120 kilometers-per-hour (75 miles-per-hour). The
chimes will continue to sound until the vehicle speed
is below 120 kilometers-per-hour (75 miles-per-hour).
This feature is only enabled on a BCM that has been
programmed with a Middle East Gulf Coast Country
(GCC) country code.
²Tactile Beep Support- The BCM chime tone
generator will generate a single beep each time a
PCI data bus tactile beep request message is received
from the Electronic Vehicle Information Center
(EVIC) or the Sentry Key Immobilizer Module
(SKIM). This beep provides an audible confirmation
that an EVIC button was completely depressed, or
that the optional Sentry Key Immobilizer System
(SKIS) is in the ªCustomer Learnº mode.
²Warning Beep Support- The BCM chime tone
generator will generate a short series of beeps each
time a PCI data bus warning beep request message
is received from the EVIC or the Electro-Mechanical
Instrument Cluster (EMIC). These beeps provide an
audible alert to the vehicle operator, of certain visual
warning indications displayed by the EVIC and/or
the EMIC.
The BCM provides chime service for all available
features in the chime warning system. The BCM
relies upon message inputs received from other mod-
ules over the PCI data bus network to provide chime
service for all of the remaining chime warning sys-
tem features.
The internal programming of the BCM determines
the priority of each chime tone request input that is
received, as well as the rate and duration of each
chime tone that is to be generated.
8B - 2 CHIME/BUZZERWJ
CHIME WARNING SYSTEM (Continued)
Page 309 of 2199
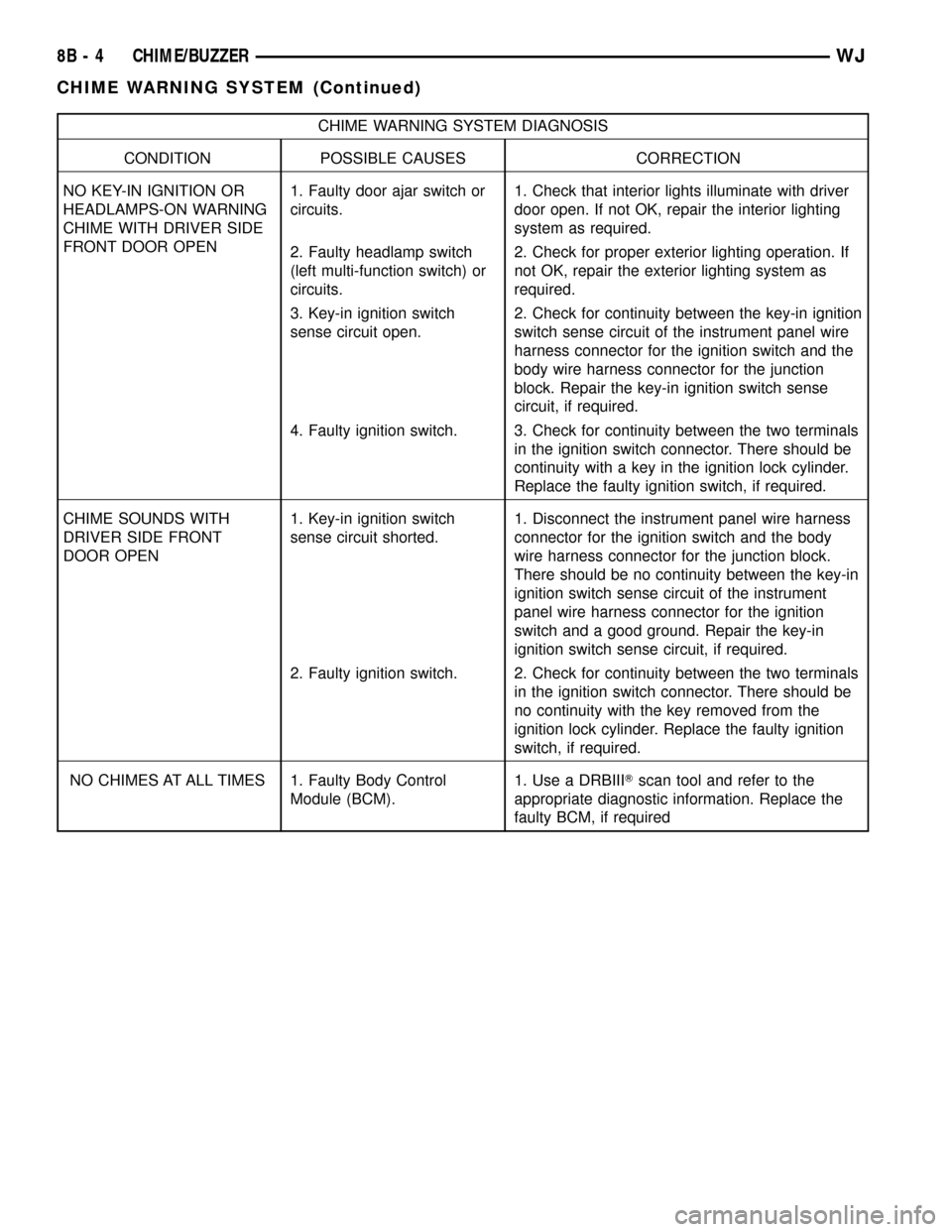
CHIME WARNING SYSTEM DIAGNOSIS
CONDITION POSSIBLE CAUSES CORRECTION
NO KEY-IN IGNITION OR
HEADLAMPS-ON WARNING
CHIME WITH DRIVER SIDE
FRONT DOOR OPEN1. Faulty door ajar switch or
circuits.1. Check that interior lights illuminate with driver
door open. If not OK, repair the interior lighting
system as required.
2. Faulty headlamp switch
(left multi-function switch) or
circuits.2. Check for proper exterior lighting operation. If
not OK, repair the exterior lighting system as
required.
3. Key-in ignition switch
sense circuit open.2. Check for continuity between the key-in ignition
switch sense circuit of the instrument panel wire
harness connector for the ignition switch and the
body wire harness connector for the junction
block. Repair the key-in ignition switch sense
circuit, if required.
4. Faulty ignition switch. 3. Check for continuity between the two terminals
in the ignition switch connector. There should be
continuity with a key in the ignition lock cylinder.
Replace the faulty ignition switch, if required.
CHIME SOUNDS WITH
DRIVER SIDE FRONT
DOOR OPEN1. Key-in ignition switch
sense circuit shorted.1. Disconnect the instrument panel wire harness
connector for the ignition switch and the body
wire harness connector for the junction block.
There should be no continuity between the key-in
ignition switch sense circuit of the instrument
panel wire harness connector for the ignition
switch and a good ground. Repair the key-in
ignition switch sense circuit, if required.
2. Faulty ignition switch. 2. Check for continuity between the two terminals
in the ignition switch connector. There should be
no continuity with the key removed from the
ignition lock cylinder. Replace the faulty ignition
switch, if required.
NO CHIMES AT ALL TIMES 1. Faulty Body Control
Module (BCM).1. Use a DRBIIITscan tool and refer to the
appropriate diagnostic information. Replace the
faulty BCM, if required
8B - 4 CHIME/BUZZERWJ
CHIME WARNING SYSTEM (Continued)
Page 313 of 2199
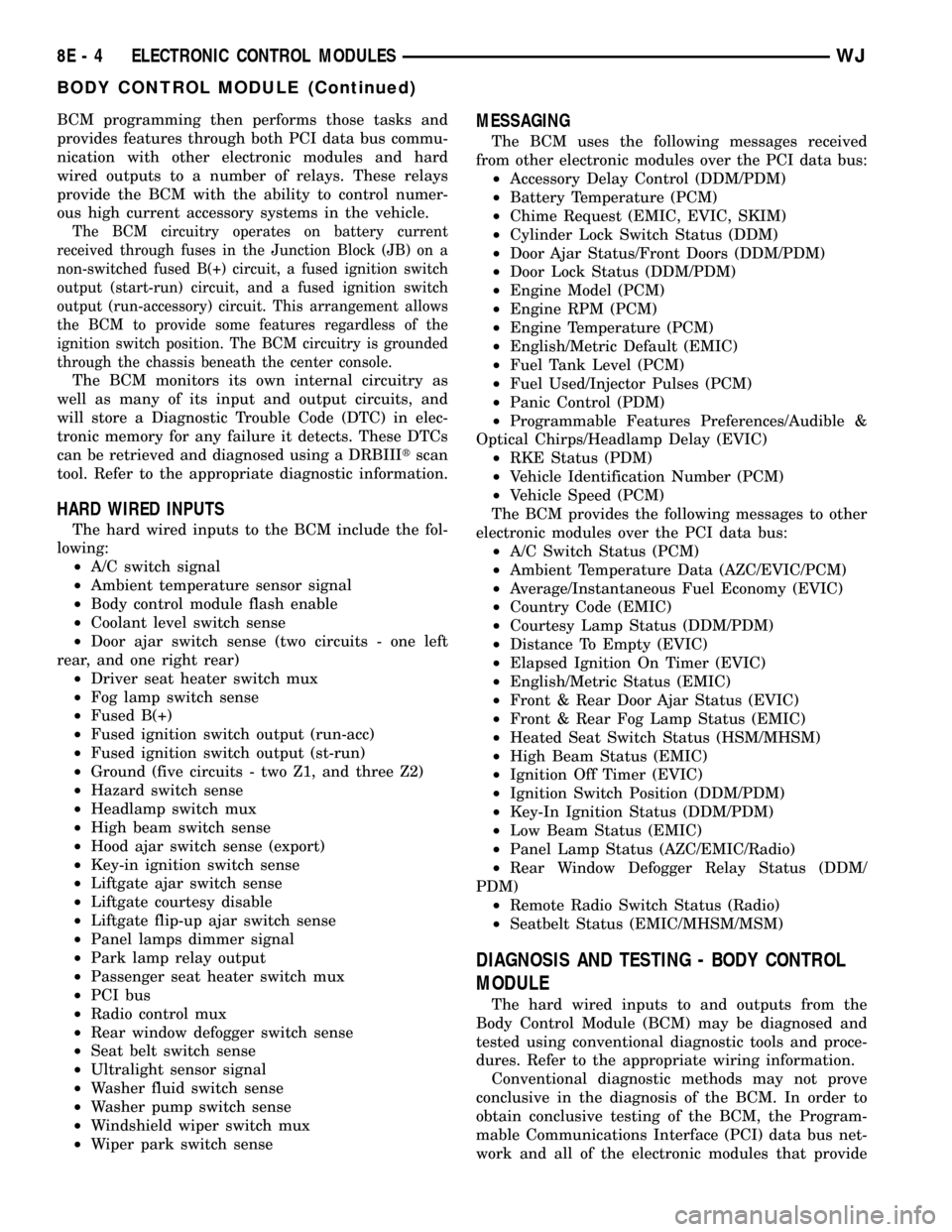
BCM programming then performs those tasks and
provides features through both PCI data bus commu-
nication with other electronic modules and hard
wired outputs to a number of relays. These relays
provide the BCM with the ability to control numer-
ous high current accessory systems in the vehicle.
The BCM circuitry operates on battery current
received through fuses in the Junction Block (JB) on a
non-switched fused B(+) circuit, a fused ignition switch
output (start-run) circuit, and a fused ignition switch
output (run-accessory) circuit. This arrangement allows
the BCM to provide some features regardless of the
ignition switch position. The BCM circuitry is grounded
through the chassis beneath the center console.
The BCM monitors its own internal circuitry as
well as many of its input and output circuits, and
will store a Diagnostic Trouble Code (DTC) in elec-
tronic memory for any failure it detects. These DTCs
can be retrieved and diagnosed using a DRBIIItscan
tool. Refer to the appropriate diagnostic information.
HARD WIRED INPUTS
The hard wired inputs to the BCM include the fol-
lowing:
²A/C switch signal
²Ambient temperature sensor signal
²Body control module flash enable
²Coolant level switch sense
²Door ajar switch sense (two circuits - one left
rear, and one right rear)
²Driver seat heater switch mux
²Fog lamp switch sense
²Fused B(+)
²Fused ignition switch output (run-acc)
²Fused ignition switch output (st-run)
²Ground (five circuits - two Z1, and three Z2)
²Hazard switch sense
²Headlamp switch mux
²High beam switch sense
²Hood ajar switch sense (export)
²Key-in ignition switch sense
²Liftgate ajar switch sense
²Liftgate courtesy disable
²Liftgate flip-up ajar switch sense
²Panel lamps dimmer signal
²Park lamp relay output
²Passenger seat heater switch mux
²PCI bus
²Radio control mux
²Rear window defogger switch sense
²Seat belt switch sense
²Ultralight sensor signal
²Washer fluid switch sense
²Washer pump switch sense
²Windshield wiper switch mux
²Wiper park switch sense
MESSAGING
The BCM uses the following messages received
from other electronic modules over the PCI data bus:
²Accessory Delay Control (DDM/PDM)
²Battery Temperature (PCM)
²Chime Request (EMIC, EVIC, SKIM)
²Cylinder Lock Switch Status (DDM)
²Door Ajar Status/Front Doors (DDM/PDM)
²Door Lock Status (DDM/PDM)
²Engine Model (PCM)
²Engine RPM (PCM)
²Engine Temperature (PCM)
²English/Metric Default (EMIC)
²Fuel Tank Level (PCM)
²Fuel Used/Injector Pulses (PCM)
²Panic Control (PDM)
²Programmable Features Preferences/Audible &
Optical Chirps/Headlamp Delay (EVIC)
²RKE Status (PDM)
²Vehicle Identification Number (PCM)
²Vehicle Speed (PCM)
The BCM provides the following messages to other
electronic modules over the PCI data bus:
²A/C Switch Status (PCM)
²Ambient Temperature Data (AZC/EVIC/PCM)
²Average/Instantaneous Fuel Economy (EVIC)
²Country Code (EMIC)
²Courtesy Lamp Status (DDM/PDM)
²Distance To Empty (EVIC)
²Elapsed Ignition On Timer (EVIC)
²English/Metric Status (EMIC)
²Front & Rear Door Ajar Status (EVIC)
²Front & Rear Fog Lamp Status (EMIC)
²Heated Seat Switch Status (HSM/MHSM)
²High Beam Status (EMIC)
²Ignition Off Timer (EVIC)
²Ignition Switch Position (DDM/PDM)
²Key-In Ignition Status (DDM/PDM)
²Low Beam Status (EMIC)
²Panel Lamp Status (AZC/EMIC/Radio)
²Rear Window Defogger Relay Status (DDM/
PDM)
²Remote Radio Switch Status (Radio)
²Seatbelt Status (EMIC/MHSM/MSM)
DIAGNOSIS AND TESTING - BODY CONTROL
MODULE
The hard wired inputs to and outputs from the
Body Control Module (BCM) may be diagnosed and
tested using conventional diagnostic tools and proce-
dures. Refer to the appropriate wiring information.
Conventional diagnostic methods may not prove
conclusive in the diagnosis of the BCM. In order to
obtain conclusive testing of the BCM, the Program-
mable Communications Interface (PCI) data bus net-
work and all of the electronic modules that provide
8E - 4 ELECTRONIC CONTROL MODULESWJ
BODY CONTROL MODULE (Continued)
Page 343 of 2199
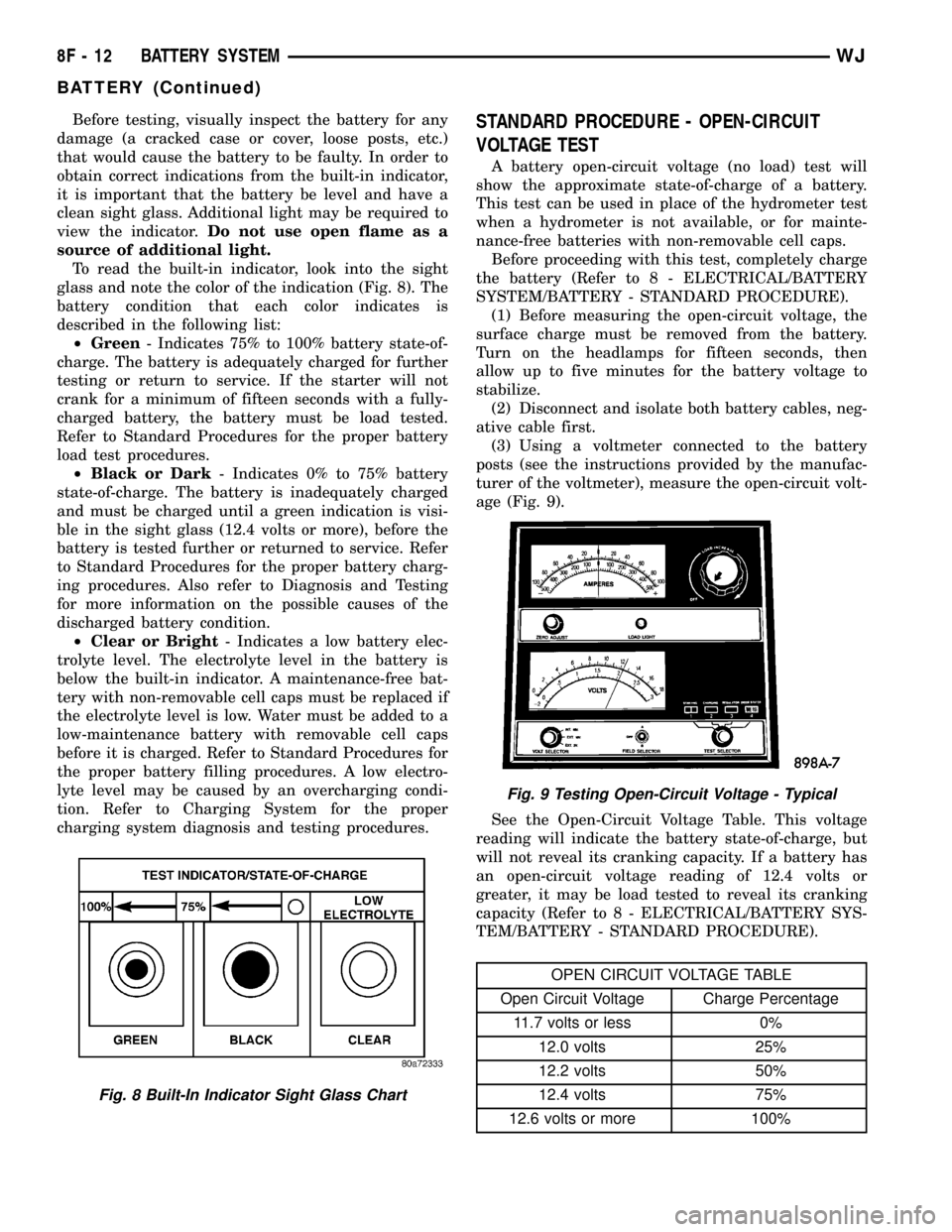
Before testing, visually inspect the battery for any
damage (a cracked case or cover, loose posts, etc.)
that would cause the battery to be faulty. In order to
obtain correct indications from the built-in indicator,
it is important that the battery be level and have a
clean sight glass. Additional light may be required to
view the indicator.Do not use open flame as a
source of additional light.
To read the built-in indicator, look into the sight
glass and note the color of the indication (Fig. 8). The
battery condition that each color indicates is
described in the following list:
²Green- Indicates 75% to 100% battery state-of-
charge. The battery is adequately charged for further
testing or return to service. If the starter will not
crank for a minimum of fifteen seconds with a fully-
charged battery, the battery must be load tested.
Refer to Standard Procedures for the proper battery
load test procedures.
²Black or Dark- Indicates 0% to 75% battery
state-of-charge. The battery is inadequately charged
and must be charged until a green indication is visi-
ble in the sight glass (12.4 volts or more), before the
battery is tested further or returned to service. Refer
to Standard Procedures for the proper battery charg-
ing procedures. Also refer to Diagnosis and Testing
for more information on the possible causes of the
discharged battery condition.
²Clear or Bright- Indicates a low battery elec-
trolyte level. The electrolyte level in the battery is
below the built-in indicator. A maintenance-free bat-
tery with non-removable cell caps must be replaced if
the electrolyte level is low. Water must be added to a
low-maintenance battery with removable cell caps
before it is charged. Refer to Standard Procedures for
the proper battery filling procedures. A low electro-
lyte level may be caused by an overcharging condi-
tion. Refer to Charging System for the proper
charging system diagnosis and testing procedures.STANDARD PROCEDURE - OPEN-CIRCUIT
VOLTAGE TEST
A battery open-circuit voltage (no load) test will
show the approximate state-of-charge of a battery.
This test can be used in place of the hydrometer test
when a hydrometer is not available, or for mainte-
nance-free batteries with non-removable cell caps.
Before proceeding with this test, completely charge
the battery (Refer to 8 - ELECTRICAL/BATTERY
SYSTEM/BATTERY - STANDARD PROCEDURE).
(1) Before measuring the open-circuit voltage, the
surface charge must be removed from the battery.
Turn on the headlamps for fifteen seconds, then
allow up to five minutes for the battery voltage to
stabilize.
(2) Disconnect and isolate both battery cables, neg-
ative cable first.
(3) Using a voltmeter connected to the battery
posts (see the instructions provided by the manufac-
turer of the voltmeter), measure the open-circuit volt-
age (Fig. 9).
See the Open-Circuit Voltage Table. This voltage
reading will indicate the battery state-of-charge, but
will not reveal its cranking capacity. If a battery has
an open-circuit voltage reading of 12.4 volts or
greater, it may be load tested to reveal its cranking
capacity (Refer to 8 - ELECTRICAL/BATTERY SYS-
TEM/BATTERY - STANDARD PROCEDURE).
OPEN CIRCUIT VOLTAGE TABLE
Open Circuit Voltage Charge Percentage
11.7 volts or less 0%
12.0 volts 25%
12.2 volts 50%
12.4 volts 75%
12.6 volts or more 100%
Fig. 8 Built-In Indicator Sight Glass Chart
Fig. 9 Testing Open-Circuit Voltage - Typical
8F - 12 BATTERY SYSTEMWJ
BATTERY (Continued)