heater JEEP GRAND CHEROKEE 2002 WJ / 2.G Service Manual
[x] Cancel search | Manufacturer: JEEP, Model Year: 2002, Model line: GRAND CHEROKEE, Model: JEEP GRAND CHEROKEE 2002 WJ / 2.GPages: 2199, PDF Size: 76.01 MB
Page 388 of 2199
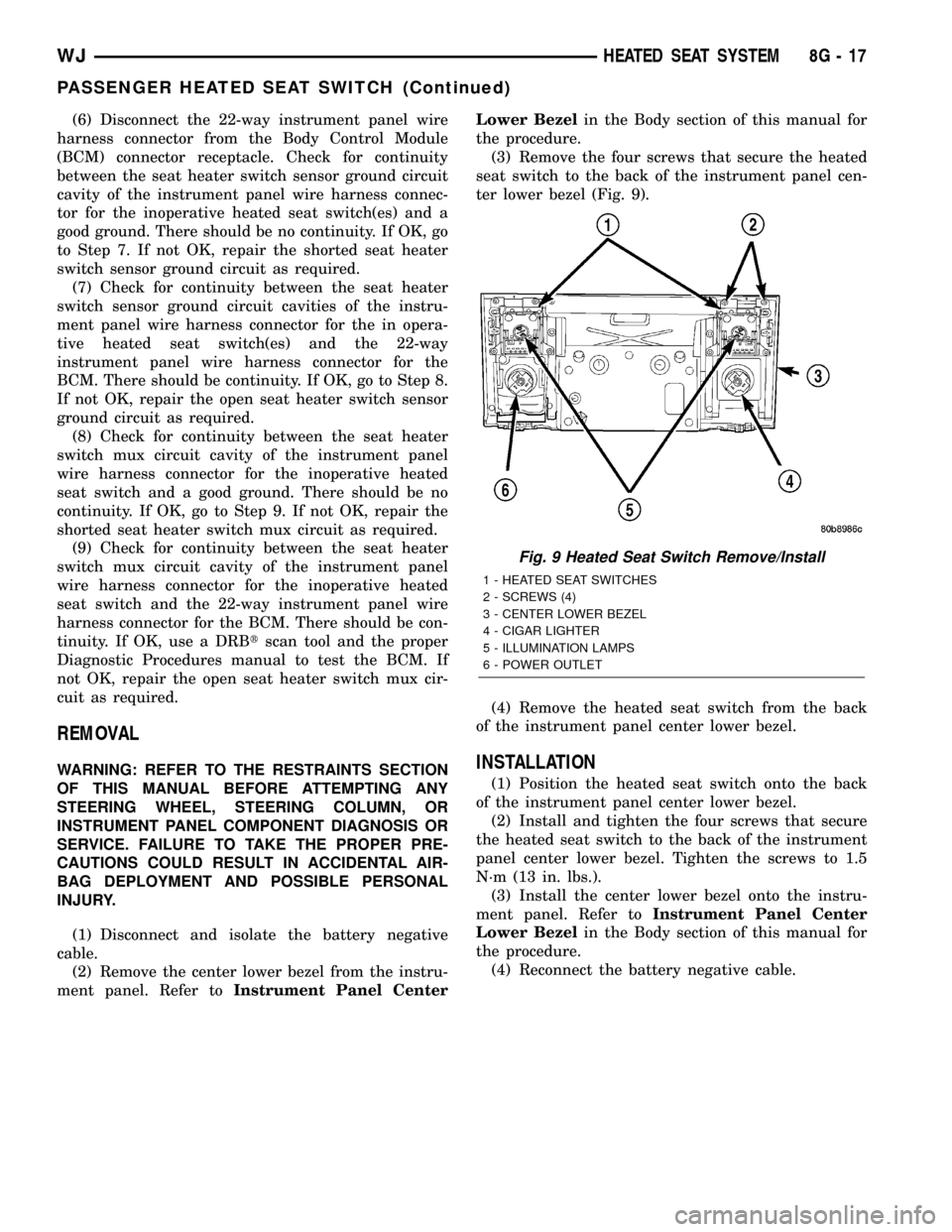
(6) Disconnect the 22-way instrument panel wire
harness connector from the Body Control Module
(BCM) connector receptacle. Check for continuity
between the seat heater switch sensor ground circuit
cavity of the instrument panel wire harness connec-
tor for the inoperative heated seat switch(es) and a
good ground. There should be no continuity. If OK, go
to Step 7. If not OK, repair the shorted seat heater
switch sensor ground circuit as required.
(7) Check for continuity between the seat heater
switch sensor ground circuit cavities of the instru-
ment panel wire harness connector for the in opera-
tive heated seat switch(es) and the 22-way
instrument panel wire harness connector for the
BCM. There should be continuity. If OK, go to Step 8.
If not OK, repair the open seat heater switch sensor
ground circuit as required.
(8) Check for continuity between the seat heater
switch mux circuit cavity of the instrument panel
wire harness connector for the inoperative heated
seat switch and a good ground. There should be no
continuity. If OK, go to Step 9. If not OK, repair the
shorted seat heater switch mux circuit as required.
(9) Check for continuity between the seat heater
switch mux circuit cavity of the instrument panel
wire harness connector for the inoperative heated
seat switch and the 22-way instrument panel wire
harness connector for the BCM. There should be con-
tinuity. If OK, use a DRBtscan tool and the proper
Diagnostic Procedures manual to test the BCM. If
not OK, repair the open seat heater switch mux cir-
cuit as required.
REMOVAL
WARNING: REFER TO THE RESTRAINTS SECTION
OF THIS MANUAL BEFORE ATTEMPTING ANY
STEERING WHEEL, STEERING COLUMN, OR
INSTRUMENT PANEL COMPONENT DIAGNOSIS OR
SERVICE. FAILURE TO TAKE THE PROPER PRE-
CAUTIONS COULD RESULT IN ACCIDENTAL AIR-
BAG DEPLOYMENT AND POSSIBLE PERSONAL
INJURY.
(1) Disconnect and isolate the battery negative
cable.
(2) Remove the center lower bezel from the instru-
ment panel. Refer toInstrument Panel CenterLower Bezelin the Body section of this manual for
the procedure.
(3) Remove the four screws that secure the heated
seat switch to the back of the instrument panel cen-
ter lower bezel (Fig. 9).
(4) Remove the heated seat switch from the back
of the instrument panel center lower bezel.INSTALLATION
(1) Position the heated seat switch onto the back
of the instrument panel center lower bezel.
(2) Install and tighten the four screws that secure
the heated seat switch to the back of the instrument
panel center lower bezel. Tighten the screws to 1.5
N´m (13 in. lbs.).
(3) Install the center lower bezel onto the instru-
ment panel. Refer toInstrument Panel Center
Lower Bezelin the Body section of this manual for
the procedure.
(4) Reconnect the battery negative cable.
Fig. 9 Heated Seat Switch Remove/Install
1 - HEATED SEAT SWITCHES
2 - SCREWS (4)
3 - CENTER LOWER BEZEL
4 - CIGAR LIGHTER
5 - ILLUMINATION LAMPS
6 - POWER OUTLET
WJHEATED SEAT SYSTEM 8G - 17
PASSENGER HEATED SEAT SWITCH (Continued)
Page 401 of 2199
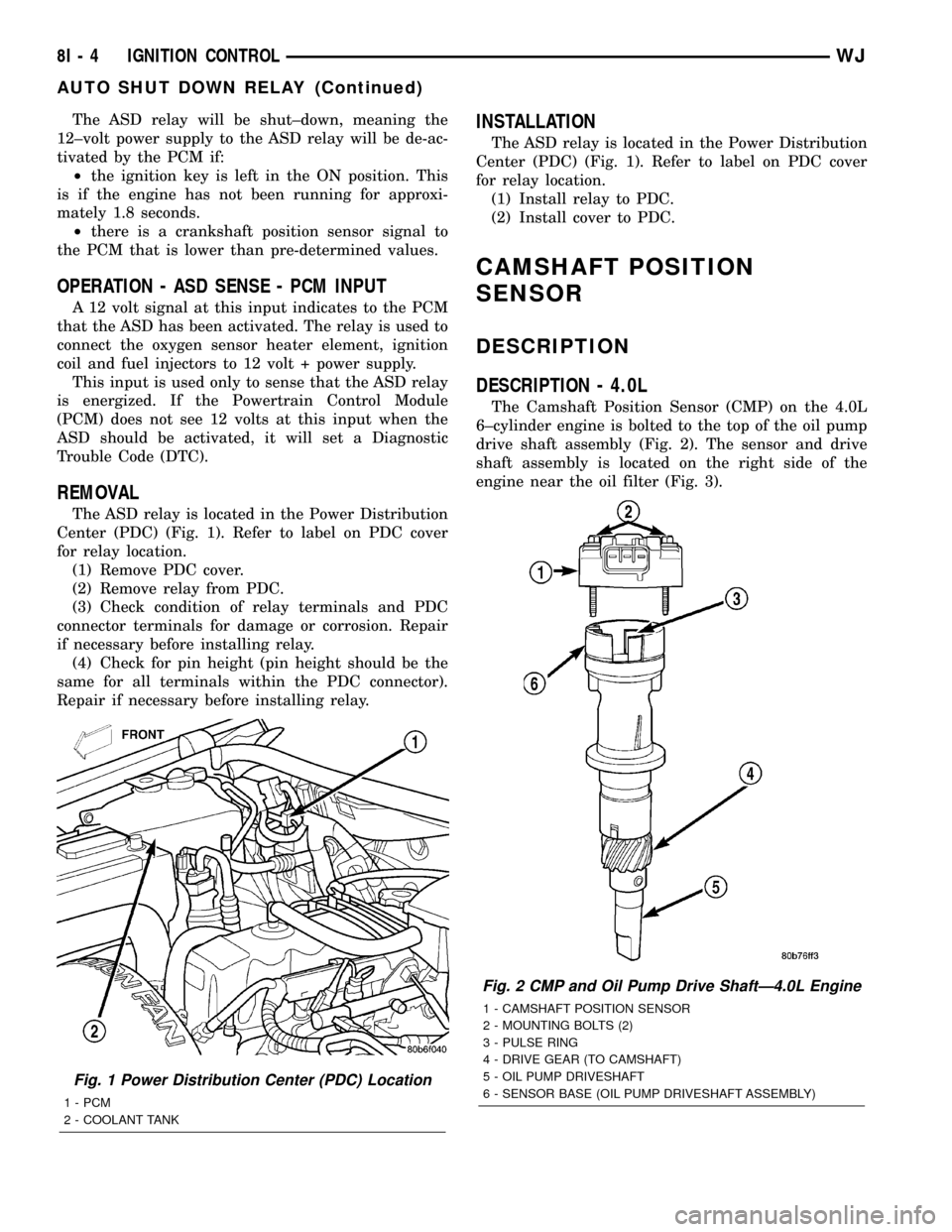
The ASD relay will be shut±down, meaning the
12±volt power supply to the ASD relay will be de-ac-
tivated by the PCM if:
²the ignition key is left in the ON position. This
is if the engine has not been running for approxi-
mately 1.8 seconds.
²there is a crankshaft position sensor signal to
the PCM that is lower than pre-determined values.
OPERATION - ASD SENSE - PCM INPUT
A 12 volt signal at this input indicates to the PCM
that the ASD has been activated. The relay is used to
connect the oxygen sensor heater element, ignition
coil and fuel injectors to 12 volt + power supply.
This input is used only to sense that the ASD relay
is energized. If the Powertrain Control Module
(PCM) does not see 12 volts at this input when the
ASD should be activated, it will set a Diagnostic
Trouble Code (DTC).
REMOVAL
The ASD relay is located in the Power Distribution
Center (PDC) (Fig. 1). Refer to label on PDC cover
for relay location.
(1) Remove PDC cover.
(2) Remove relay from PDC.
(3) Check condition of relay terminals and PDC
connector terminals for damage or corrosion. Repair
if necessary before installing relay.
(4) Check for pin height (pin height should be the
same for all terminals within the PDC connector).
Repair if necessary before installing relay.
INSTALLATION
The ASD relay is located in the Power Distribution
Center (PDC) (Fig. 1). Refer to label on PDC cover
for relay location.
(1) Install relay to PDC.
(2) Install cover to PDC.
CAMSHAFT POSITION
SENSOR
DESCRIPTION
DESCRIPTION - 4.0L
The Camshaft Position Sensor (CMP) on the 4.0L
6±cylinder engine is bolted to the top of the oil pump
drive shaft assembly (Fig. 2). The sensor and drive
shaft assembly is located on the right side of the
engine near the oil filter (Fig. 3).
Fig. 1 Power Distribution Center (PDC) Location
1 - PCM
2 - COOLANT TANK
Fig. 2 CMP and Oil Pump Drive ShaftÐ4.0L Engine
1 - CAMSHAFT POSITION SENSOR
2 - MOUNTING BOLTS (2)
3 - PULSE RING
4 - DRIVE GEAR (TO CAMSHAFT)
5 - OIL PUMP DRIVESHAFT
6 - SENSOR BASE (OIL PUMP DRIVESHAFT ASSEMBLY)
8I - 4 IGNITION CONTROLWJ
AUTO SHUT DOWN RELAY (Continued)
Page 450 of 2199
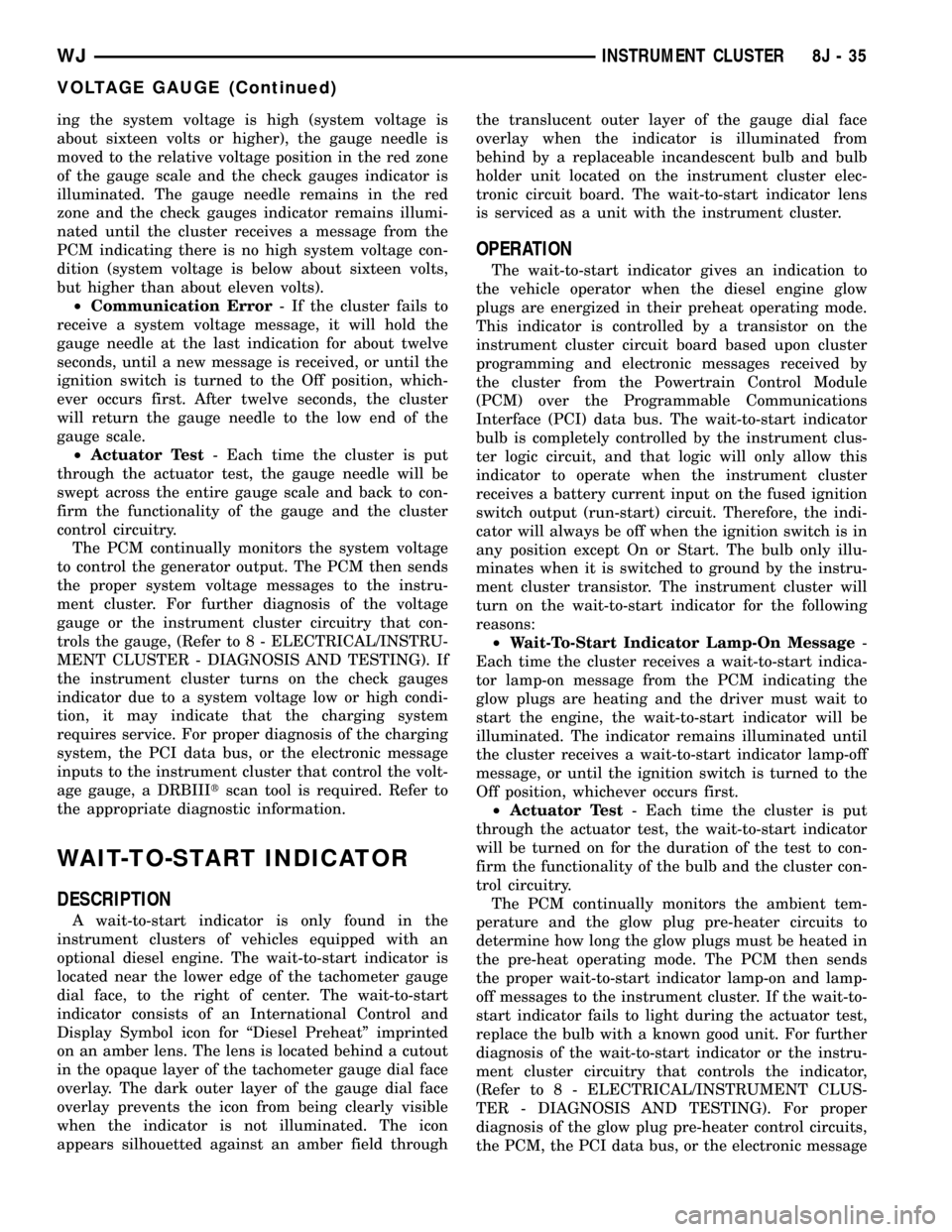
ing the system voltage is high (system voltage is
about sixteen volts or higher), the gauge needle is
moved to the relative voltage position in the red zone
of the gauge scale and the check gauges indicator is
illuminated. The gauge needle remains in the red
zone and the check gauges indicator remains illumi-
nated until the cluster receives a message from the
PCM indicating there is no high system voltage con-
dition (system voltage is below about sixteen volts,
but higher than about eleven volts).
²Communication Error- If the cluster fails to
receive a system voltage message, it will hold the
gauge needle at the last indication for about twelve
seconds, until a new message is received, or until the
ignition switch is turned to the Off position, which-
ever occurs first. After twelve seconds, the cluster
will return the gauge needle to the low end of the
gauge scale.
²Actuator Test- Each time the cluster is put
through the actuator test, the gauge needle will be
swept across the entire gauge scale and back to con-
firm the functionality of the gauge and the cluster
control circuitry.
The PCM continually monitors the system voltage
to control the generator output. The PCM then sends
the proper system voltage messages to the instru-
ment cluster. For further diagnosis of the voltage
gauge or the instrument cluster circuitry that con-
trols the gauge, (Refer to 8 - ELECTRICAL/INSTRU-
MENT CLUSTER - DIAGNOSIS AND TESTING). If
the instrument cluster turns on the check gauges
indicator due to a system voltage low or high condi-
tion, it may indicate that the charging system
requires service. For proper diagnosis of the charging
system, the PCI data bus, or the electronic message
inputs to the instrument cluster that control the volt-
age gauge, a DRBIIItscan tool is required. Refer to
the appropriate diagnostic information.
WAIT-TO-START INDICATOR
DESCRIPTION
A wait-to-start indicator is only found in the
instrument clusters of vehicles equipped with an
optional diesel engine. The wait-to-start indicator is
located near the lower edge of the tachometer gauge
dial face, to the right of center. The wait-to-start
indicator consists of an International Control and
Display Symbol icon for ªDiesel Preheatº imprinted
on an amber lens. The lens is located behind a cutout
in the opaque layer of the tachometer gauge dial face
overlay. The dark outer layer of the gauge dial face
overlay prevents the icon from being clearly visible
when the indicator is not illuminated. The icon
appears silhouetted against an amber field throughthe translucent outer layer of the gauge dial face
overlay when the indicator is illuminated from
behind by a replaceable incandescent bulb and bulb
holder unit located on the instrument cluster elec-
tronic circuit board. The wait-to-start indicator lens
is serviced as a unit with the instrument cluster.
OPERATION
The wait-to-start indicator gives an indication to
the vehicle operator when the diesel engine glow
plugs are energized in their preheat operating mode.
This indicator is controlled by a transistor on the
instrument cluster circuit board based upon cluster
programming and electronic messages received by
the cluster from the Powertrain Control Module
(PCM) over the Programmable Communications
Interface (PCI) data bus. The wait-to-start indicator
bulb is completely controlled by the instrument clus-
ter logic circuit, and that logic will only allow this
indicator to operate when the instrument cluster
receives a battery current input on the fused ignition
switch output (run-start) circuit. Therefore, the indi-
cator will always be off when the ignition switch is in
any position except On or Start. The bulb only illu-
minates when it is switched to ground by the instru-
ment cluster transistor. The instrument cluster will
turn on the wait-to-start indicator for the following
reasons:
²Wait-To-Start Indicator Lamp-On Message-
Each time the cluster receives a wait-to-start indica-
tor lamp-on message from the PCM indicating the
glow plugs are heating and the driver must wait to
start the engine, the wait-to-start indicator will be
illuminated. The indicator remains illuminated until
the cluster receives a wait-to-start indicator lamp-off
message, or until the ignition switch is turned to the
Off position, whichever occurs first.
²Actuator Test- Each time the cluster is put
through the actuator test, the wait-to-start indicator
will be turned on for the duration of the test to con-
firm the functionality of the bulb and the cluster con-
trol circuitry.
The PCM continually monitors the ambient tem-
perature and the glow plug pre-heater circuits to
determine how long the glow plugs must be heated in
the pre-heat operating mode. The PCM then sends
the proper wait-to-start indicator lamp-on and lamp-
off messages to the instrument cluster. If the wait-to-
start indicator fails to light during the actuator test,
replace the bulb with a known good unit. For further
diagnosis of the wait-to-start indicator or the instru-
ment cluster circuitry that controls the indicator,
(Refer to 8 - ELECTRICAL/INSTRUMENT CLUS-
TER - DIAGNOSIS AND TESTING). For proper
diagnosis of the glow plug pre-heater control circuits,
the PCM, the PCI data bus, or the electronic message
WJINSTRUMENT CLUSTER 8J - 35
VOLTAGE GAUGE (Continued)
Page 479 of 2199
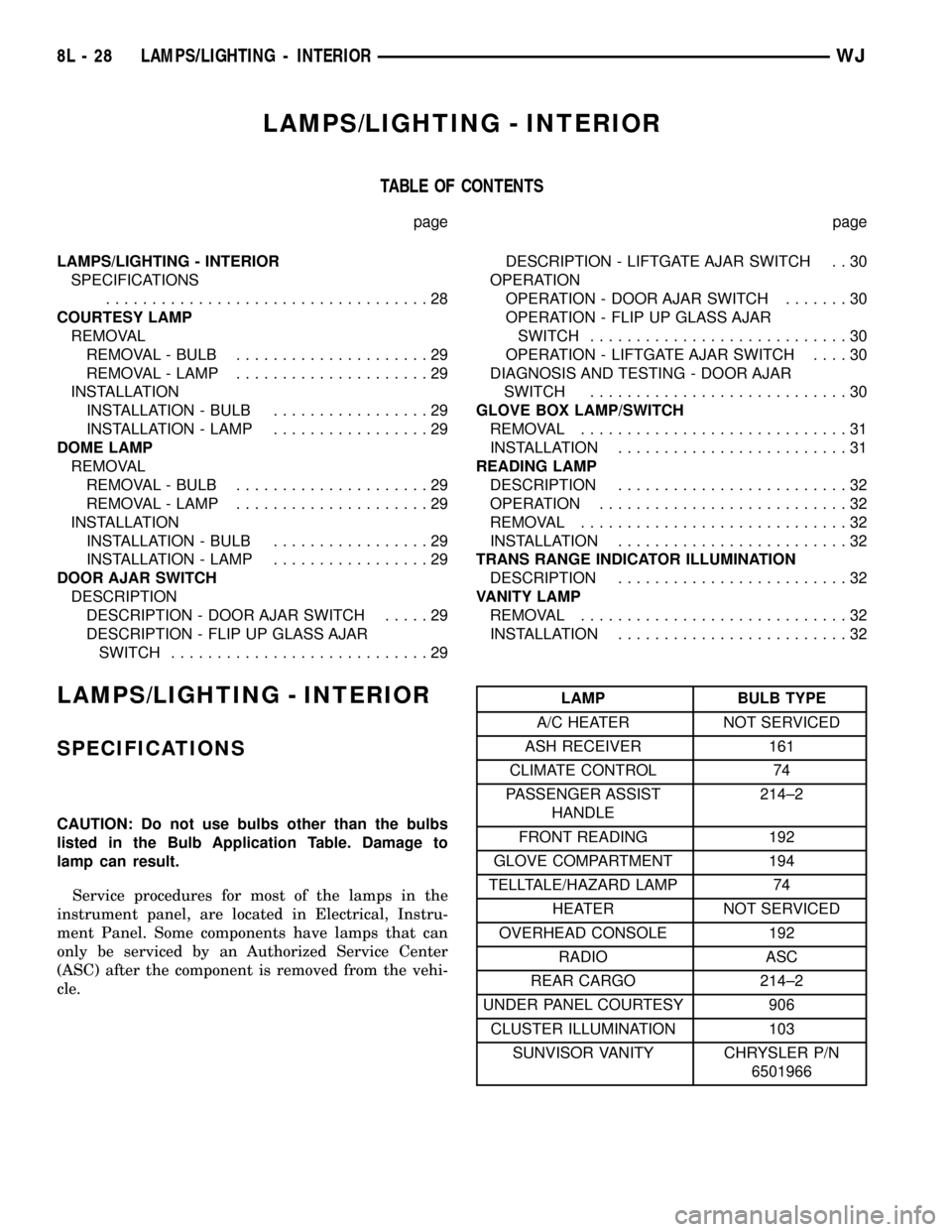
LAMPS/LIGHTING - INTERIOR
TABLE OF CONTENTS
page page
LAMPS/LIGHTING - INTERIOR
SPECIFICATIONS
...................................28
COURTESY LAMP
REMOVAL
REMOVAL - BULB.....................29
REMOVAL - LAMP.....................29
INSTALLATION
INSTALLATION - BULB.................29
INSTALLATION - LAMP.................29
DOME LAMP
REMOVAL
REMOVAL - BULB.....................29
REMOVAL - LAMP.....................29
INSTALLATION
INSTALLATION - BULB.................29
INSTALLATION - LAMP.................29
DOOR AJAR SWITCH
DESCRIPTION
DESCRIPTION - DOOR AJAR SWITCH.....29
DESCRIPTION - FLIP UP GLASS AJAR
SWITCH............................29DESCRIPTION - LIFTGATE AJAR SWITCH . . 30
OPERATION
OPERATION - DOOR AJAR SWITCH.......30
OPERATION - FLIP UP GLASS AJAR
SWITCH............................30
OPERATION - LIFTGATE AJAR SWITCH....30
DIAGNOSIS AND TESTING - DOOR AJAR
SWITCH............................30
GLOVE BOX LAMP/SWITCH
REMOVAL.............................31
INSTALLATION.........................31
READING LAMP
DESCRIPTION.........................32
OPERATION...........................32
REMOVAL.............................32
INSTALLATION.........................32
TRANS RANGE INDICATOR ILLUMINATION
DESCRIPTION.........................32
VANITY LAMP
REMOVAL.............................32
INSTALLATION.........................32
LAMPS/LIGHTING - INTERIOR
SPECIFICATIONS
CAUTION: Do not use bulbs other than the bulbs
listed in the Bulb Application Table. Damage to
lamp can result.
Service procedures for most of the lamps in the
instrument panel, are located in Electrical, Instru-
ment Panel. Some components have lamps that can
only be serviced by an Authorized Service Center
(ASC) after the component is removed from the vehi-
cle.
LAMP BULB TYPE
A/C HEATER NOT SERVICED
ASH RECEIVER 161
CLIMATE CONTROL 74
PASSENGER ASSIST
HANDLE214±2
FRONT READING 192
GLOVE COMPARTMENT 194
TELLTALE/HAZARD LAMP 74
HEATER NOT SERVICED
OVERHEAD CONSOLE 192
RADIO ASC
REAR CARGO 214±2
UNDER PANEL COURTESY 906
CLUSTER ILLUMINATION 103
SUNVISOR VANITY CHRYSLER P/N
6501966
8L - 28 LAMPS/LIGHTING - INTERIORWJ
Page 508 of 2199
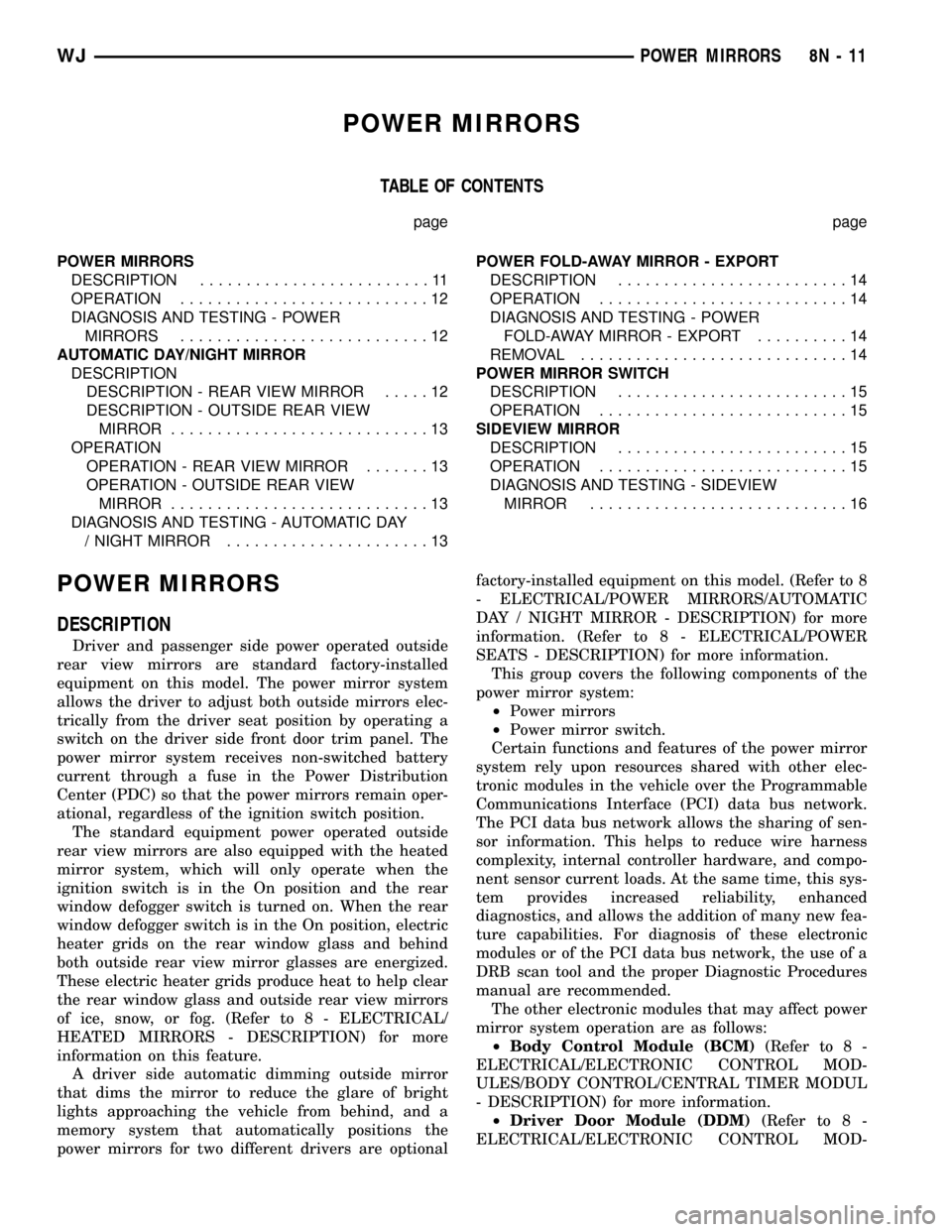
POWER MIRRORS
TABLE OF CONTENTS
page page
POWER MIRRORS
DESCRIPTION.........................11
OPERATION...........................12
DIAGNOSIS AND TESTING - POWER
MIRRORS...........................12
AUTOMATIC DAY/NIGHT MIRROR
DESCRIPTION
DESCRIPTION - REAR VIEW MIRROR.....12
DESCRIPTION - OUTSIDE REAR VIEW
MIRROR............................13
OPERATION
OPERATION - REAR VIEW MIRROR.......13
OPERATION - OUTSIDE REAR VIEW
MIRROR............................13
DIAGNOSIS AND TESTING - AUTOMATIC DAY
/ NIGHT MIRROR......................13POWER FOLD-AWAY MIRROR - EXPORT
DESCRIPTION.........................14
OPERATION...........................14
DIAGNOSIS AND TESTING - POWER
FOLD-AWAY MIRROR - EXPORT..........14
REMOVAL.............................14
POWER MIRROR SWITCH
DESCRIPTION.........................15
OPERATION...........................15
SIDEVIEW MIRROR
DESCRIPTION.........................15
OPERATION...........................15
DIAGNOSIS AND TESTING - SIDEVIEW
MIRROR............................16
POWER MIRRORS
DESCRIPTION
Driver and passenger side power operated outside
rear view mirrors are standard factory-installed
equipment on this model. The power mirror system
allows the driver to adjust both outside mirrors elec-
trically from the driver seat position by operating a
switch on the driver side front door trim panel. The
power mirror system receives non-switched battery
current through a fuse in the Power Distribution
Center (PDC) so that the power mirrors remain oper-
ational, regardless of the ignition switch position.
The standard equipment power operated outside
rear view mirrors are also equipped with the heated
mirror system, which will only operate when the
ignition switch is in the On position and the rear
window defogger switch is turned on. When the rear
window defogger switch is in the On position, electric
heater grids on the rear window glass and behind
both outside rear view mirror glasses are energized.
These electric heater grids produce heat to help clear
the rear window glass and outside rear view mirrors
of ice, snow, or fog. (Refer to 8 - ELECTRICAL/
HEATED MIRRORS - DESCRIPTION) for more
information on this feature.
A driver side automatic dimming outside mirror
that dims the mirror to reduce the glare of bright
lights approaching the vehicle from behind, and a
memory system that automatically positions the
power mirrors for two different drivers are optionalfactory-installed equipment on this model. (Refer to 8
- ELECTRICAL/POWER MIRRORS/AUTOMATIC
DAY / NIGHT MIRROR - DESCRIPTION) for more
information. (Refer to 8 - ELECTRICAL/POWER
SEATS - DESCRIPTION) for more information.
This group covers the following components of the
power mirror system:
²Power mirrors
²Power mirror switch.
Certain functions and features of the power mirror
system rely upon resources shared with other elec-
tronic modules in the vehicle over the Programmable
Communications Interface (PCI) data bus network.
The PCI data bus network allows the sharing of sen-
sor information. This helps to reduce wire harness
complexity, internal controller hardware, and compo-
nent sensor current loads. At the same time, this sys-
tem provides increased reliability, enhanced
diagnostics, and allows the addition of many new fea-
ture capabilities. For diagnosis of these electronic
modules or of the PCI data bus network, the use of a
DRB scan tool and the proper Diagnostic Procedures
manual are recommended.
The other electronic modules that may affect power
mirror system operation are as follows:
²Body Control Module (BCM)(Refer to 8 -
ELECTRICAL/ELECTRONIC CONTROL MOD-
ULES/BODY CONTROL/CENTRAL TIMER MODUL
- DESCRIPTION) for more information.
²Driver Door Module (DDM)(Refer to 8 -
ELECTRICAL/ELECTRONIC CONTROL MOD-
WJPOWER MIRRORS 8N - 11
Page 509 of 2199
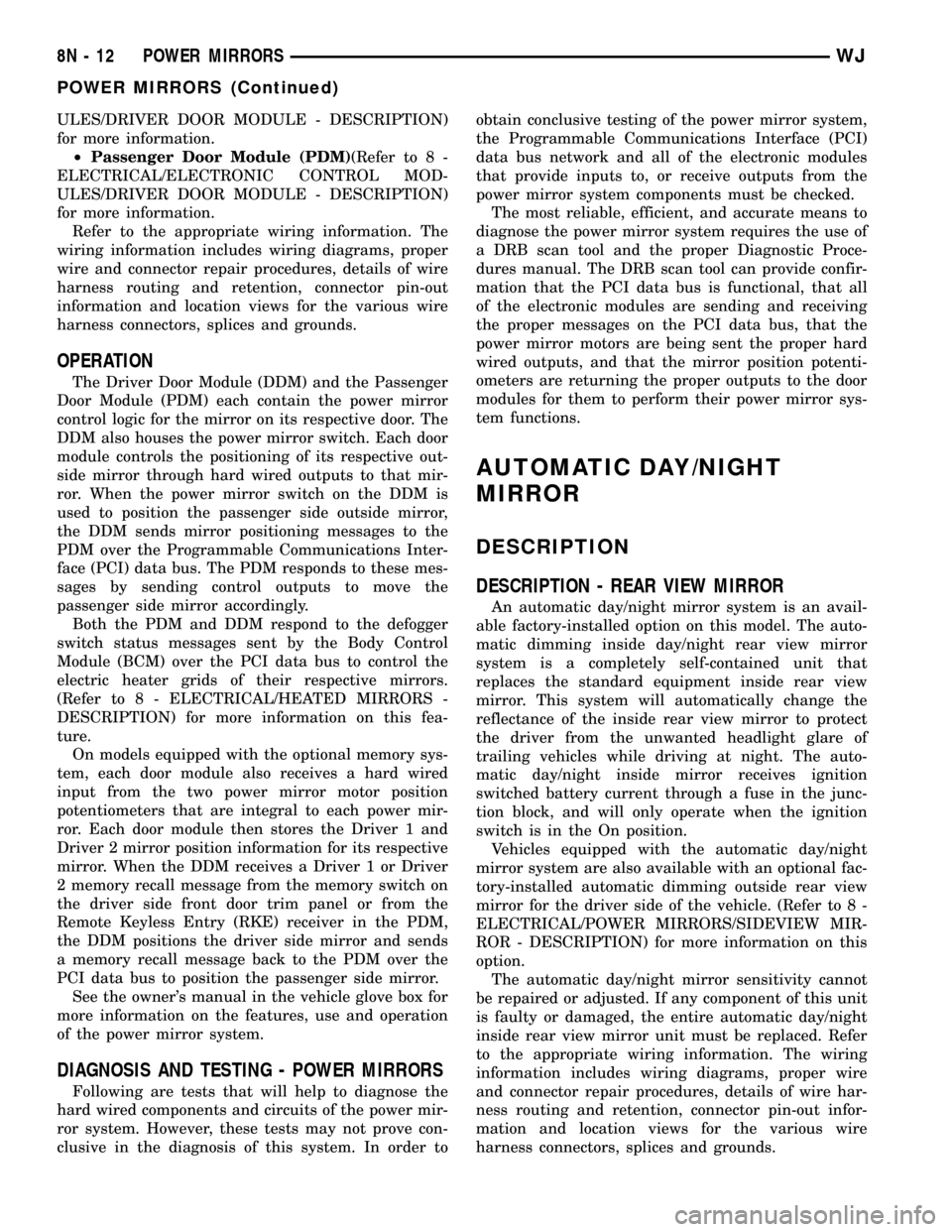
ULES/DRIVER DOOR MODULE - DESCRIPTION)
for more information.
²Passenger Door Module (PDM)(Refer to 8 -
ELECTRICAL/ELECTRONIC CONTROL MOD-
ULES/DRIVER DOOR MODULE - DESCRIPTION)
for more information.
Refer to the appropriate wiring information. The
wiring information includes wiring diagrams, proper
wire and connector repair procedures, details of wire
harness routing and retention, connector pin-out
information and location views for the various wire
harness connectors, splices and grounds.
OPERATION
The Driver Door Module (DDM) and the Passenger
Door Module (PDM) each contain the power mirror
control logic for the mirror on its respective door. The
DDM also houses the power mirror switch. Each door
module controls the positioning of its respective out-
side mirror through hard wired outputs to that mir-
ror. When the power mirror switch on the DDM is
used to position the passenger side outside mirror,
the DDM sends mirror positioning messages to the
PDM over the Programmable Communications Inter-
face (PCI) data bus. The PDM responds to these mes-
sages by sending control outputs to move the
passenger side mirror accordingly.
Both the PDM and DDM respond to the defogger
switch status messages sent by the Body Control
Module (BCM) over the PCI data bus to control the
electric heater grids of their respective mirrors.
(Refer to 8 - ELECTRICAL/HEATED MIRRORS -
DESCRIPTION) for more information on this fea-
ture.
On models equipped with the optional memory sys-
tem, each door module also receives a hard wired
input from the two power mirror motor position
potentiometers that are integral to each power mir-
ror. Each door module then stores the Driver 1 and
Driver 2 mirror position information for its respective
mirror. When the DDM receives a Driver 1 or Driver
2 memory recall message from the memory switch on
the driver side front door trim panel or from the
Remote Keyless Entry (RKE) receiver in the PDM,
the DDM positions the driver side mirror and sends
a memory recall message back to the PDM over the
PCI data bus to position the passenger side mirror.
See the owner's manual in the vehicle glove box for
more information on the features, use and operation
of the power mirror system.
DIAGNOSIS AND TESTING - POWER MIRRORS
Following are tests that will help to diagnose the
hard wired components and circuits of the power mir-
ror system. However, these tests may not prove con-
clusive in the diagnosis of this system. In order toobtain conclusive testing of the power mirror system,
the Programmable Communications Interface (PCI)
data bus network and all of the electronic modules
that provide inputs to, or receive outputs from the
power mirror system components must be checked.
The most reliable, efficient, and accurate means to
diagnose the power mirror system requires the use of
a DRB scan tool and the proper Diagnostic Proce-
dures manual. The DRB scan tool can provide confir-
mation that the PCI data bus is functional, that all
of the electronic modules are sending and receiving
the proper messages on the PCI data bus, that the
power mirror motors are being sent the proper hard
wired outputs, and that the mirror position potenti-
ometers are returning the proper outputs to the door
modules for them to perform their power mirror sys-
tem functions.
AUTOMATIC DAY/NIGHT
MIRROR
DESCRIPTION
DESCRIPTION - REAR VIEW MIRROR
An automatic day/night mirror system is an avail-
able factory-installed option on this model. The auto-
matic dimming inside day/night rear view mirror
system is a completely self-contained unit that
replaces the standard equipment inside rear view
mirror. This system will automatically change the
reflectance of the inside rear view mirror to protect
the driver from the unwanted headlight glare of
trailing vehicles while driving at night. The auto-
matic day/night inside mirror receives ignition
switched battery current through a fuse in the junc-
tion block, and will only operate when the ignition
switch is in the On position.
Vehicles equipped with the automatic day/night
mirror system are also available with an optional fac-
tory-installed automatic dimming outside rear view
mirror for the driver side of the vehicle. (Refer to 8 -
ELECTRICAL/POWER MIRRORS/SIDEVIEW MIR-
ROR - DESCRIPTION) for more information on this
option.
The automatic day/night mirror sensitivity cannot
be repaired or adjusted. If any component of this unit
is faulty or damaged, the entire automatic day/night
inside rear view mirror unit must be replaced. Refer
to the appropriate wiring information. The wiring
information includes wiring diagrams, proper wire
and connector repair procedures, details of wire har-
ness routing and retention, connector pin-out infor-
mation and location views for the various wire
harness connectors, splices and grounds.
8N - 12 POWER MIRRORSWJ
POWER MIRRORS (Continued)
Page 513 of 2199
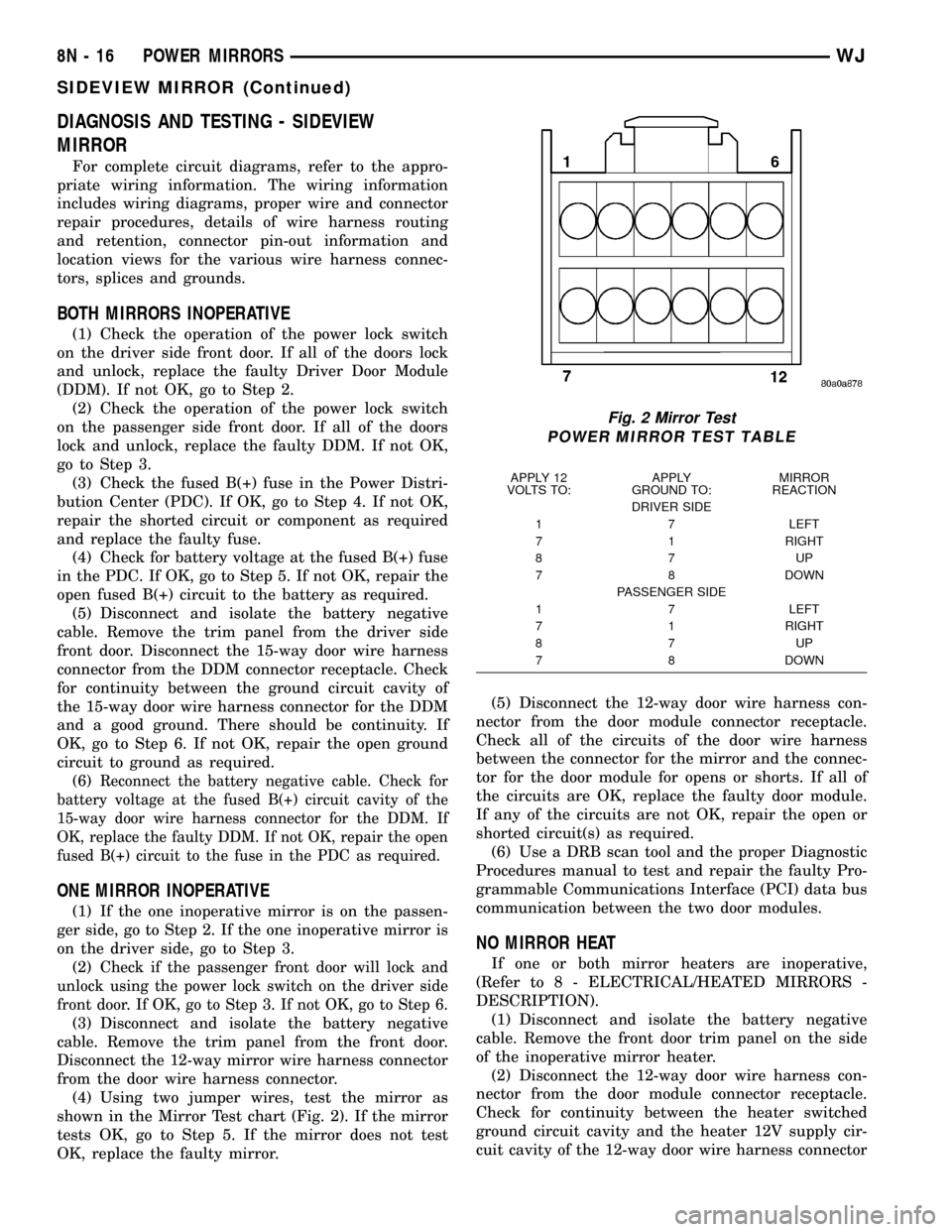
DIAGNOSIS AND TESTING - SIDEVIEW
MIRROR
For complete circuit diagrams, refer to the appro-
priate wiring information. The wiring information
includes wiring diagrams, proper wire and connector
repair procedures, details of wire harness routing
and retention, connector pin-out information and
location views for the various wire harness connec-
tors, splices and grounds.
BOTH MIRRORS INOPERATIVE
(1) Check the operation of the power lock switch
on the driver side front door. If all of the doors lock
and unlock, replace the faulty Driver Door Module
(DDM). If not OK, go to Step 2.
(2) Check the operation of the power lock switch
on the passenger side front door. If all of the doors
lock and unlock, replace the faulty DDM. If not OK,
go to Step 3.
(3) Check the fused B(+) fuse in the Power Distri-
bution Center (PDC). If OK, go to Step 4. If not OK,
repair the shorted circuit or component as required
and replace the faulty fuse.
(4) Check for battery voltage at the fused B(+) fuse
in the PDC. If OK, go to Step 5. If not OK, repair the
open fused B(+) circuit to the battery as required.
(5) Disconnect and isolate the battery negative
cable. Remove the trim panel from the driver side
front door. Disconnect the 15-way door wire harness
connector from the DDM connector receptacle. Check
for continuity between the ground circuit cavity of
the 15-way door wire harness connector for the DDM
and a good ground. There should be continuity. If
OK, go to Step 6. If not OK, repair the open ground
circuit to ground as required.
(6)
Reconnect the battery negative cable. Check for
battery voltage at the fused B(+) circuit cavity of the
15-way door wire harness connector for the DDM. If
OK, replace the faulty DDM. If not OK, repair the open
fused B(+) circuit to the fuse in the PDC as required.
ONE MIRROR INOPERATIVE
(1) If the one inoperative mirror is on the passen-
ger side, go to Step 2. If the one inoperative mirror is
on the driver side, go to Step 3.
(2)
Check if the passenger front door will lock and
unlock using the power lock switch on the driver side
front door. If OK, go to Step 3. If not OK, go to Step 6.
(3) Disconnect and isolate the battery negative
cable. Remove the trim panel from the front door.
Disconnect the 12-way mirror wire harness connector
from the door wire harness connector.
(4) Using two jumper wires, test the mirror as
shown in the Mirror Test chart (Fig. 2). If the mirror
tests OK, go to Step 5. If the mirror does not test
OK, replace the faulty mirror.(5) Disconnect the 12-way door wire harness con-
nector from the door module connector receptacle.
Check all of the circuits of the door wire harness
between the connector for the mirror and the connec-
tor for the door module for opens or shorts. If all of
the circuits are OK, replace the faulty door module.
If any of the circuits are not OK, repair the open or
shorted circuit(s) as required.
(6) Use a DRB scan tool and the proper Diagnostic
Procedures manual to test and repair the faulty Pro-
grammable Communications Interface (PCI) data bus
communication between the two door modules.
NO MIRROR HEAT
If one or both mirror heaters are inoperative,
(Refer to 8 - ELECTRICAL/HEATED MIRRORS -
DESCRIPTION).
(1) Disconnect and isolate the battery negative
cable. Remove the front door trim panel on the side
of the inoperative mirror heater.
(2) Disconnect the 12-way door wire harness con-
nector from the door module connector receptacle.
Check for continuity between the heater switched
ground circuit cavity and the heater 12V supply cir-
cuit cavity of the 12-way door wire harness connector
Fig. 2 Mirror Test
POWER MIRROR TEST TABLE
APPLY 12
VOLTS TO:APPLY
GROUND TO:MIRROR
REACTION
DRIVER SIDE
1 7 LEFT
7 1 RIGHT
87UP
7 8 DOWN
PASSENGER SIDE
1 7 LEFT
7 1 RIGHT
87UP
7 8 DOWN
8N - 16 POWER MIRRORSWJ
SIDEVIEW MIRROR (Continued)
Page 545 of 2199
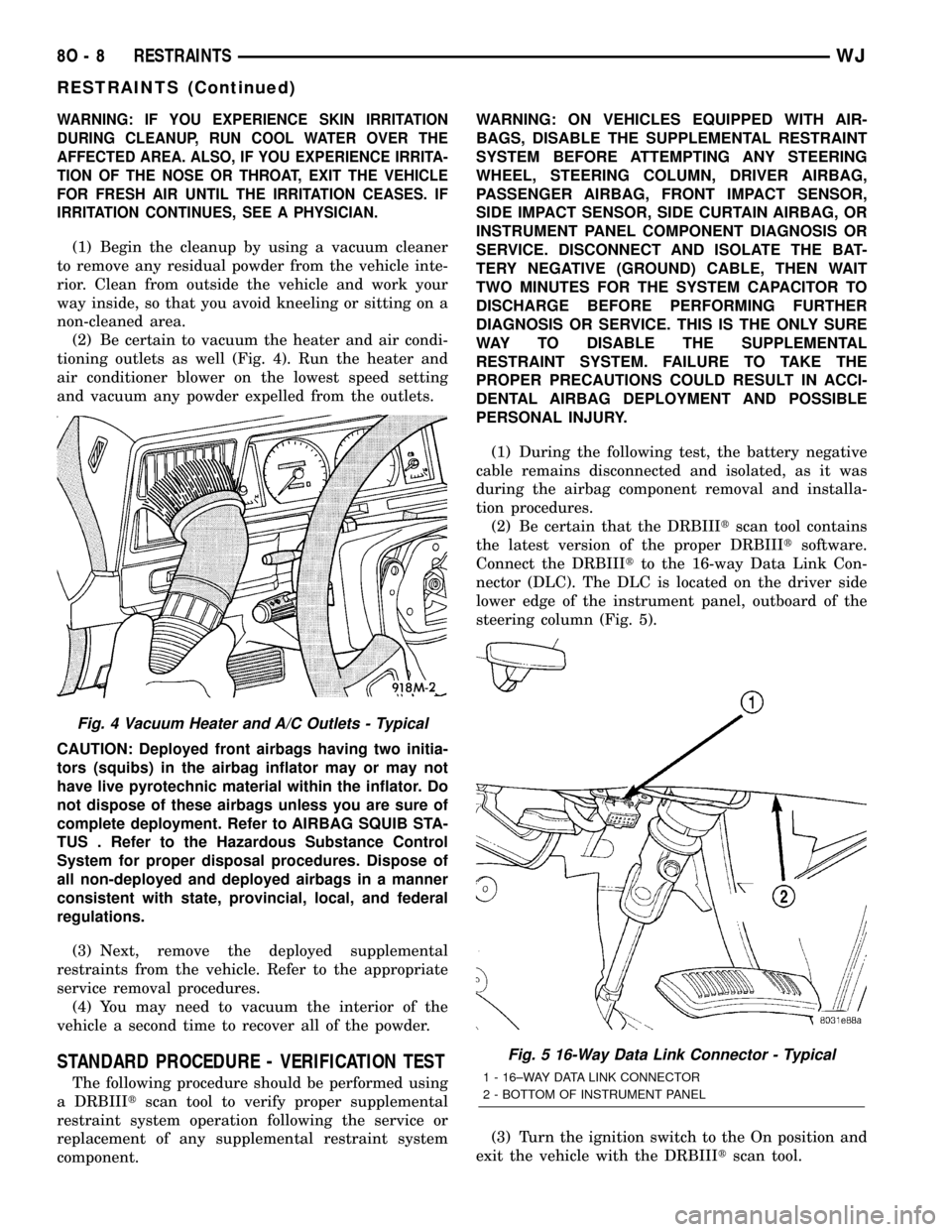
WARNING: IF YOU EXPERIENCE SKIN IRRITATION
DURING CLEANUP, RUN COOL WATER OVER THE
AFFECTED AREA. ALSO, IF YOU EXPERIENCE IRRITA-
TION OF THE NOSE OR THROAT, EXIT THE VEHICLE
FOR FRESH AIR UNTIL THE IRRITATION CEASES. IF
IRRITATION CONTINUES, SEE A PHYSICIAN.
(1) Begin the cleanup by using a vacuum cleaner
to remove any residual powder from the vehicle inte-
rior. Clean from outside the vehicle and work your
way inside, so that you avoid kneeling or sitting on a
non-cleaned area.
(2) Be certain to vacuum the heater and air condi-
tioning outlets as well (Fig. 4). Run the heater and
air conditioner blower on the lowest speed setting
and vacuum any powder expelled from the outlets.
CAUTION: Deployed front airbags having two initia-
tors (squibs) in the airbag inflator may or may not
have live pyrotechnic material within the inflator. Do
not dispose of these airbags unless you are sure of
complete deployment. Refer to AIRBAG SQUIB STA-
TUS . Refer to the Hazardous Substance Control
System for proper disposal procedures. Dispose of
all non-deployed and deployed airbags in a manner
consistent with state, provincial, local, and federal
regulations.
(3) Next, remove the deployed supplemental
restraints from the vehicle. Refer to the appropriate
service removal procedures.
(4) You may need to vacuum the interior of the
vehicle a second time to recover all of the powder.
STANDARD PROCEDURE - VERIFICATION TEST
The following procedure should be performed using
a DRBIIItscan tool to verify proper supplemental
restraint system operation following the service or
replacement of any supplemental restraint system
component.WARNING: ON VEHICLES EQUIPPED WITH AIR-
BAGS, DISABLE THE SUPPLEMENTAL RESTRAINT
SYSTEM BEFORE ATTEMPTING ANY STEERING
WHEEL, STEERING COLUMN, DRIVER AIRBAG,
PASSENGER AIRBAG, FRONT IMPACT SENSOR,
SIDE IMPACT SENSOR, SIDE CURTAIN AIRBAG, OR
INSTRUMENT PANEL COMPONENT DIAGNOSIS OR
SERVICE. DISCONNECT AND ISOLATE THE BAT-
TERY NEGATIVE (GROUND) CABLE, THEN WAIT
TWO MINUTES FOR THE SYSTEM CAPACITOR TO
DISCHARGE BEFORE PERFORMING FURTHER
DIAGNOSIS OR SERVICE. THIS IS THE ONLY SURE
WAY TO DISABLE THE SUPPLEMENTAL
RESTRAINT SYSTEM. FAILURE TO TAKE THE
PROPER PRECAUTIONS COULD RESULT IN ACCI-
DENTAL AIRBAG DEPLOYMENT AND POSSIBLE
PERSONAL INJURY.
(1) During the following test, the battery negative
cable remains disconnected and isolated, as it was
during the airbag component removal and installa-
tion procedures.
(2) Be certain that the DRBIIItscan tool contains
the latest version of the proper DRBIIItsoftware.
Connect the DRBIIItto the 16-way Data Link Con-
nector (DLC). The DLC is located on the driver side
lower edge of the instrument panel, outboard of the
steering column (Fig. 5).
(3) Turn the ignition switch to the On position and
exit the vehicle with the DRBIIItscan tool.
Fig. 4 Vacuum Heater and A/C Outlets - Typical
Fig. 5 16-Way Data Link Connector - Typical
1 - 16±WAY DATA LINK CONNECTOR
2 - BOTTOM OF INSTRUMENT PANEL
8O - 8 RESTRAINTSWJ
RESTRAINTS (Continued)
Page 654 of 2199
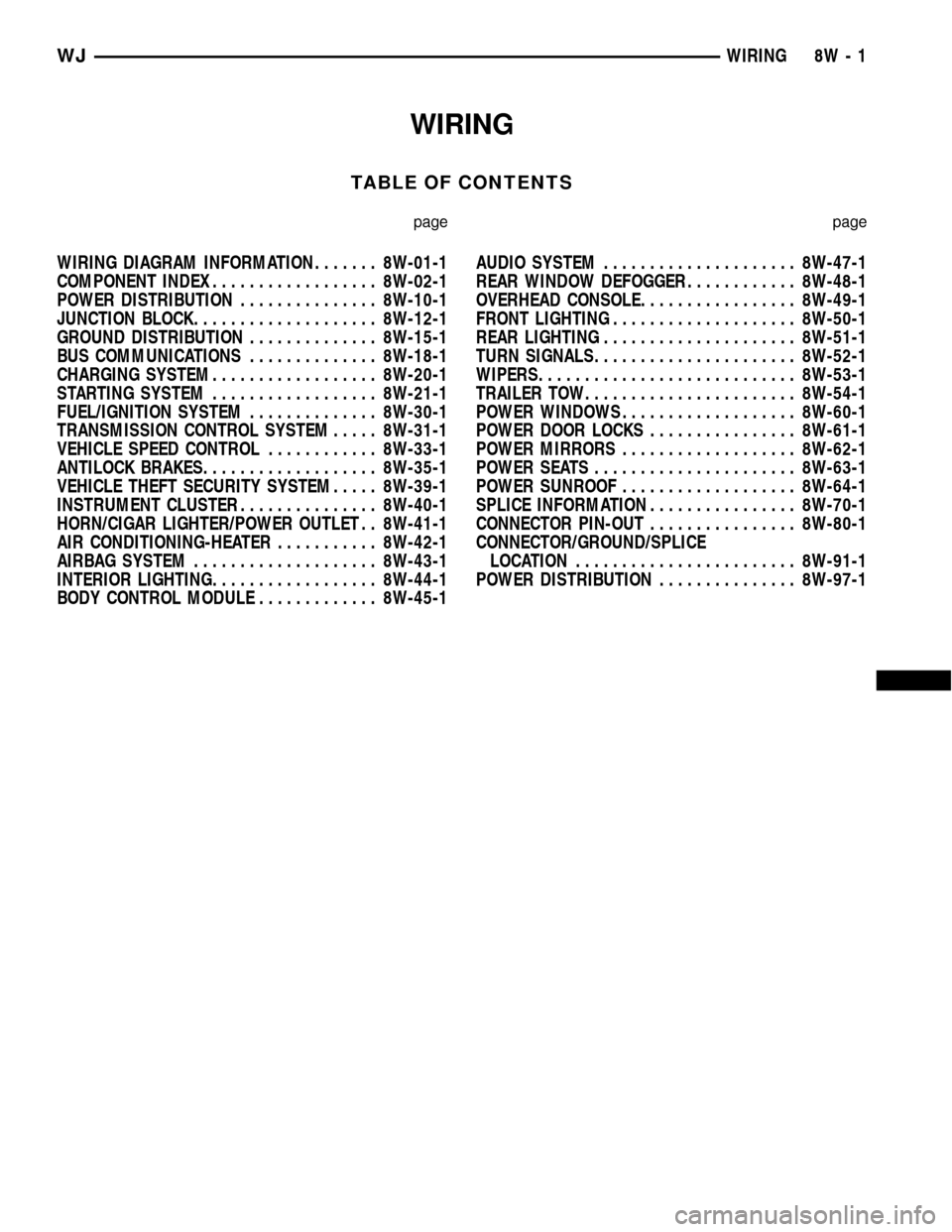
WIRING
TABLE OF CONTENTS
page page
WIRING DIAGRAM INFORMATION....... 8W-01-1
COMPONENT INDEX.................. 8W-02-1
POWER DISTRIBUTION............... 8W-10-1
JUNCTION BLOCK.................... 8W-12-1
GROUND DISTRIBUTION.............. 8W-15-1
BUS COMMUNICATIONS.............. 8W-18-1
CHARGING SYSTEM.................. 8W-20-1
STARTING SYSTEM.................. 8W-21-1
FUEL/IGNITION SYSTEM.............. 8W-30-1
TRANSMISSION CONTROL SYSTEM..... 8W-31-1
VEHICLE SPEED CONTROL............ 8W-33-1
ANTILOCK BRAKES................... 8W-35-1
VEHICLE THEFT SECURITY SYSTEM..... 8W-39-1
INSTRUMENT CLUSTER............... 8W-40-1
HORN/CIGAR LIGHTER/POWER OUTLET . . 8W-41-1
AIR CONDITIONING-HEATER........... 8W-42-1
AIRBAG SYSTEM.................... 8W-43-1
INTERIOR LIGHTING.................. 8W-44-1
BODY CONTROL MODULE............. 8W-45-1AUDIO SYSTEM..................... 8W-47-1
REAR WINDOW DEFOGGER............ 8W-48-1
OVERHEAD CONSOLE................. 8W-49-1
FRONT LIGHTING.................... 8W-50-1
REAR LIGHTING..................... 8W-51-1
TURN SIGNALS...................... 8W-52-1
WIPERS............................ 8W-53-1
TRAILER TOW....................... 8W-54-1
POWER WINDOWS................... 8W-60-1
POWER DOOR LOCKS................ 8W-61-1
POWER MIRRORS................... 8W-62-1
POWER SEATS...................... 8W-63-1
POWER SUNROOF................... 8W-64-1
SPLICE INFORMATION................ 8W-70-1
CONNECTOR PIN-OUT................ 8W-80-1
CONNECTOR/GROUND/SPLICE
LOCATION........................ 8W-91-1
POWER DISTRIBUTION............... 8W-97-1 WJWIRING 8W - 1
Page 672 of 2199
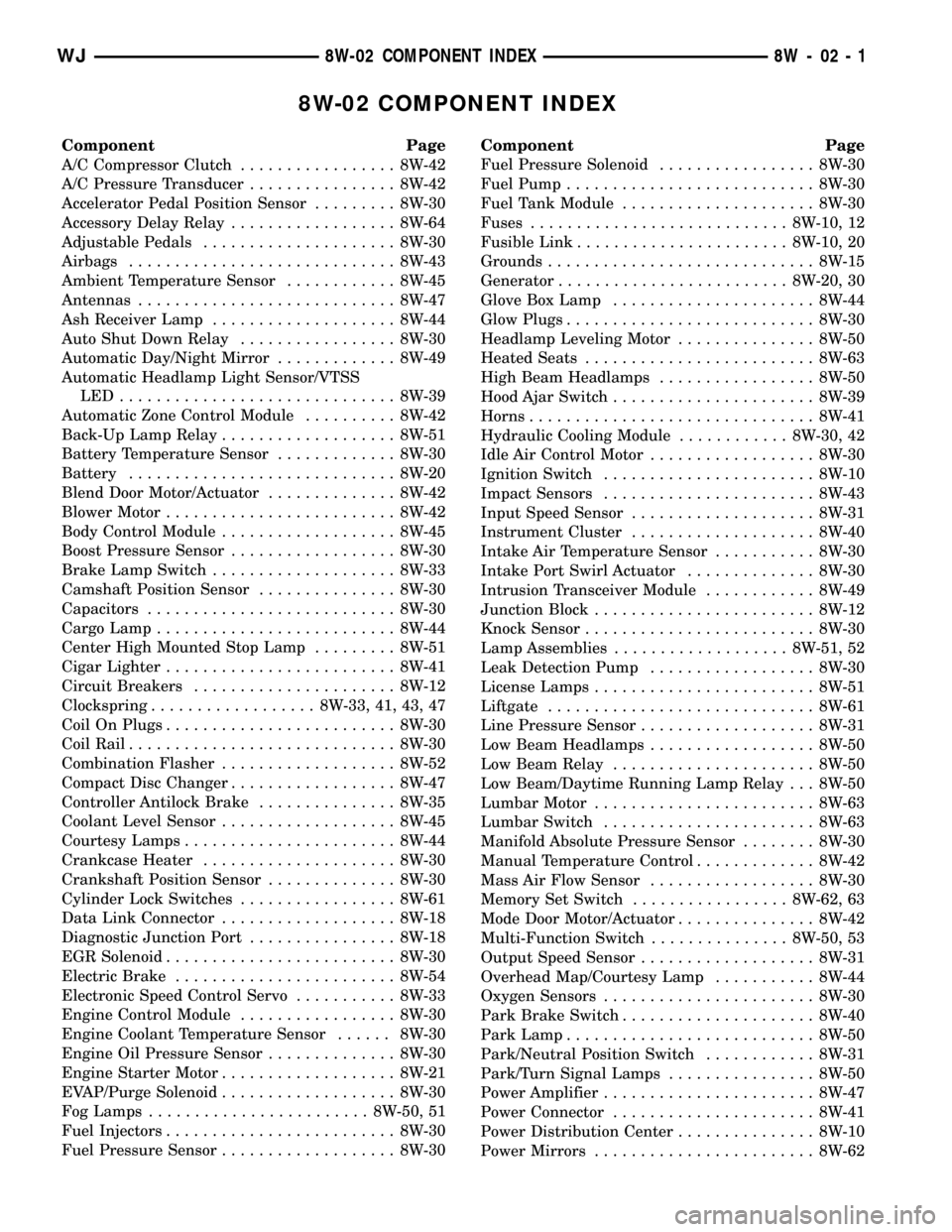
8W-02 COMPONENT INDEX
Component Page
A/C Compressor Clutch................. 8W-42
A/C Pressure Transducer................ 8W-42
Accelerator Pedal Position Sensor......... 8W-30
Accessory Delay Relay.................. 8W-64
Adjustable Pedals..................... 8W-30
Airbags............................. 8W-43
Ambient Temperature Sensor............ 8W-45
Antennas............................ 8W-47
Ash Receiver Lamp.................... 8W-44
Auto Shut Down Relay................. 8W-30
Automatic Day/Night Mirror............. 8W-49
Automatic Headlamp Light Sensor/VTSS
LED.............................. 8W-39
Automatic Zone Control Module.......... 8W-42
Back-Up Lamp Relay................... 8W-51
Battery Temperature Sensor............. 8W-30
Battery............................. 8W-20
Blend Door Motor/Actuator.............. 8W-42
Blower Motor......................... 8W-42
Body Control Module................... 8W-45
Boost Pressure Sensor.................. 8W-30
Brake Lamp Switch.................... 8W-33
Camshaft Position Sensor............... 8W-30
Capacitors........................... 8W-30
Cargo Lamp.......................... 8W-44
Center High Mounted Stop Lamp......... 8W-51
Cigar Lighter......................... 8W-41
Circuit Breakers...................... 8W-12
Clockspring.................. 8W-33, 41, 43, 47
Coil On Plugs......................... 8W-30
Coil Rail............................. 8W-30
Combination Flasher................... 8W-52
Compact Disc Changer.................. 8W-47
Controller Antilock Brake............... 8W-35
Coolant Level Sensor................... 8W-45
Courtesy Lamps....................... 8W-44
Crankcase Heater..................... 8W-30
Crankshaft Position Sensor.............. 8W-30
Cylinder Lock Switches................. 8W-61
Data Link Connector................... 8W-18
Diagnostic Junction Port................ 8W-18
EGR Solenoid......................... 8W-30
Electric Brake........................ 8W-54
Electronic Speed Control Servo........... 8W-33
Engine Control Module................. 8W-30
Engine Coolant Temperature Sensor...... 8W-30
Engine Oil Pressure Sensor.............. 8W-30
Engine Starter Motor................... 8W-21
EVAP/Purge Solenoid................... 8W-30
Fog Lamps........................ 8W-50, 51
Fuel Injectors......................... 8W-30
Fuel Pressure Sensor................... 8W-30Component Page
Fuel Pressure Solenoid................. 8W-30
Fuel Pump........................... 8W-30
Fuel Tank Module..................... 8W-30
Fuses............................ 8W-10, 12
Fusible Link....................... 8W-10, 20
Grounds............................. 8W-15
Generator......................... 8W-20, 30
Glove Box Lamp...................... 8W-44
Glow Plugs........................... 8W-30
Headlamp Leveling Motor............... 8W-50
Heated Seats......................... 8W-63
High Beam Headlamps................. 8W-50
Hood Ajar Switch...................... 8W-39
Horns............................... 8W-41
Hydraulic Cooling Module............ 8W-30, 42
Idle Air Control Motor.................. 8W-30
Ignition Switch....................... 8W-10
Impact Sensors....................... 8W-43
Input Speed Sensor.................... 8W-31
Instrument Cluster.................... 8W-40
Intake Air Temperature Sensor........... 8W-30
Intake Port Swirl Actuator.............. 8W-30
Intrusion Transceiver Module............ 8W-49
Junction Block........................ 8W-12
Knock Sensor......................... 8W-30
Lamp Assemblies................... 8W-51, 52
Leak Detection Pump.................. 8W-30
License Lamps........................ 8W-51
Liftgate............................. 8W-61
Line Pressure Sensor................... 8W-31
Low Beam Headlamps.................. 8W-50
Low Beam Relay...................... 8W-50
Low Beam/Daytime Running Lamp Relay . . . 8W-50
Lumbar Motor........................ 8W-63
Lumbar Switch....................... 8W-63
Manifold Absolute Pressure Sensor........ 8W-30
Manual Temperature Control............. 8W-42
Mass Air Flow Sensor.................. 8W-30
Memory Set Switch................. 8W-62, 63
Mode Door Motor/Actuator............... 8W-42
Multi-Function Switch............... 8W-50, 53
Output Speed Sensor................... 8W-31
Overhead Map/Courtesy Lamp........... 8W-44
Oxygen Sensors....................... 8W-30
Park Brake Switch..................... 8W-40
Park Lamp........................... 8W-50
Park/Neutral Position Switch............ 8W-31
Park/Turn Signal Lamps................ 8W-50
Power Amplifier....................... 8W-47
Power Connector...................... 8W-41
Power Distribution Center............... 8W-10
Power Mirrors........................ 8W-62
WJ8W-02 COMPONENT INDEX 8W - 02 - 1