steering wheel switch JEEP GRAND CHEROKEE 2002 WJ / 2.G Repair Manual
[x] Cancel search | Manufacturer: JEEP, Model Year: 2002, Model line: GRAND CHEROKEE, Model: JEEP GRAND CHEROKEE 2002 WJ / 2.GPages: 2199, PDF Size: 76.01 MB
Page 477 of 2199
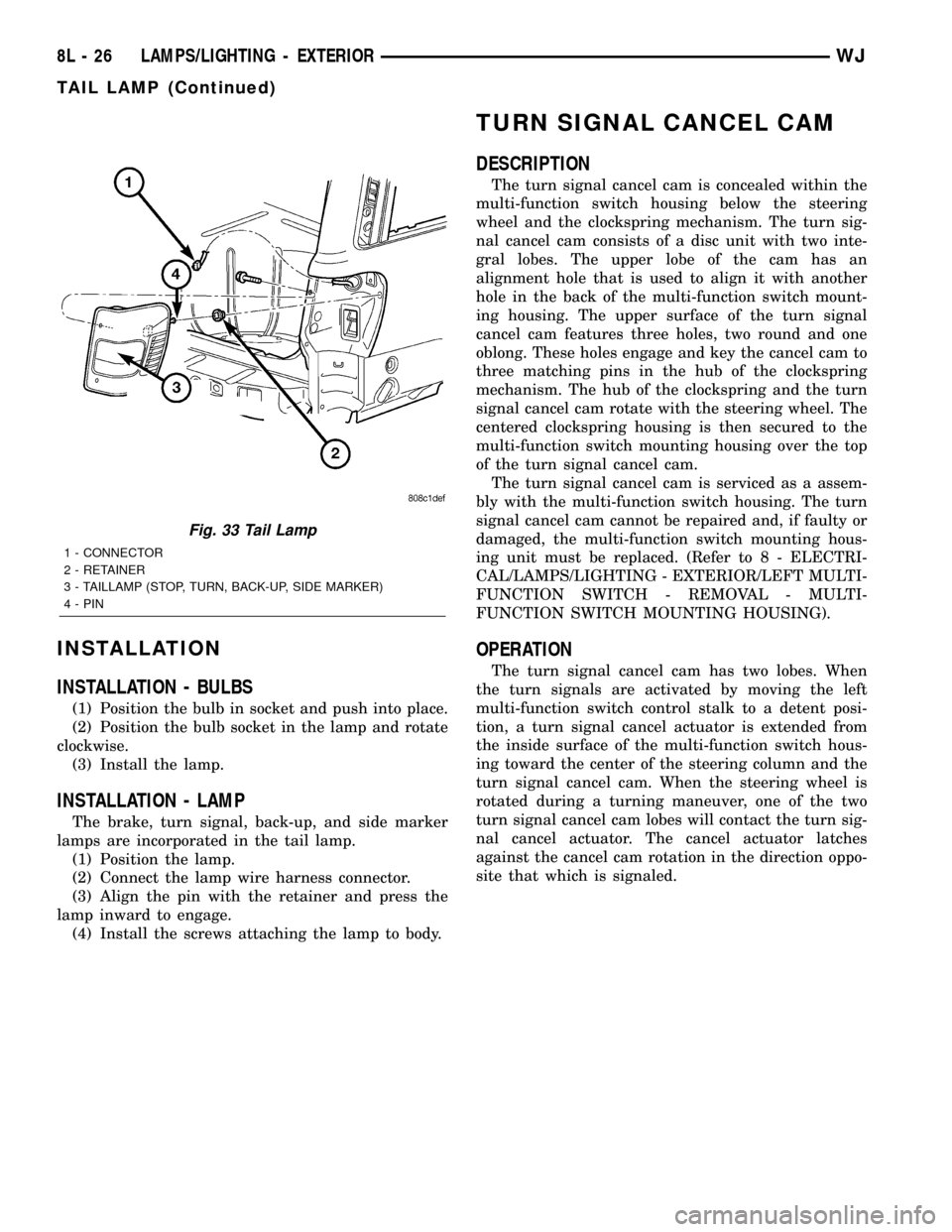
INSTALLATION
INSTALLATION - BULBS
(1) Position the bulb in socket and push into place.
(2) Position the bulb socket in the lamp and rotate
clockwise.
(3) Install the lamp.
INSTALLATION - LAMP
The brake, turn signal, back-up, and side marker
lamps are incorporated in the tail lamp.
(1) Position the lamp.
(2) Connect the lamp wire harness connector.
(3) Align the pin with the retainer and press the
lamp inward to engage.
(4) Install the screws attaching the lamp to body.
TURN SIGNAL CANCEL CAM
DESCRIPTION
The turn signal cancel cam is concealed within the
multi-function switch housing below the steering
wheel and the clockspring mechanism. The turn sig-
nal cancel cam consists of a disc unit with two inte-
gral lobes. The upper lobe of the cam has an
alignment hole that is used to align it with another
hole in the back of the multi-function switch mount-
ing housing. The upper surface of the turn signal
cancel cam features three holes, two round and one
oblong. These holes engage and key the cancel cam to
three matching pins in the hub of the clockspring
mechanism. The hub of the clockspring and the turn
signal cancel cam rotate with the steering wheel. The
centered clockspring housing is then secured to the
multi-function switch mounting housing over the top
of the turn signal cancel cam.
The turn signal cancel cam is serviced as a assem-
bly with the multi-function switch housing. The turn
signal cancel cam cannot be repaired and, if faulty or
damaged, the multi-function switch mounting hous-
ing unit must be replaced. (Refer to 8 - ELECTRI-
CAL/LAMPS/LIGHTING - EXTERIOR/LEFT MULTI-
FUNCTION SWITCH - REMOVAL - MULTI-
FUNCTION SWITCH MOUNTING HOUSING).
OPERATION
The turn signal cancel cam has two lobes. When
the turn signals are activated by moving the left
multi-function switch control stalk to a detent posi-
tion, a turn signal cancel actuator is extended from
the inside surface of the multi-function switch hous-
ing toward the center of the steering column and the
turn signal cancel cam. When the steering wheel is
rotated during a turning maneuver, one of the two
turn signal cancel cam lobes will contact the turn sig-
nal cancel actuator. The cancel actuator latches
against the cancel cam rotation in the direction oppo-
site that which is signaled.
Fig. 33 Tail Lamp
1 - CONNECTOR
2 - RETAINER
3 - TAILLAMP (STOP, TURN, BACK-UP, SIDE MARKER)
4 - PIN
8L - 26 LAMPS/LIGHTING - EXTERIORWJ
TAIL LAMP (Continued)
Page 481 of 2199
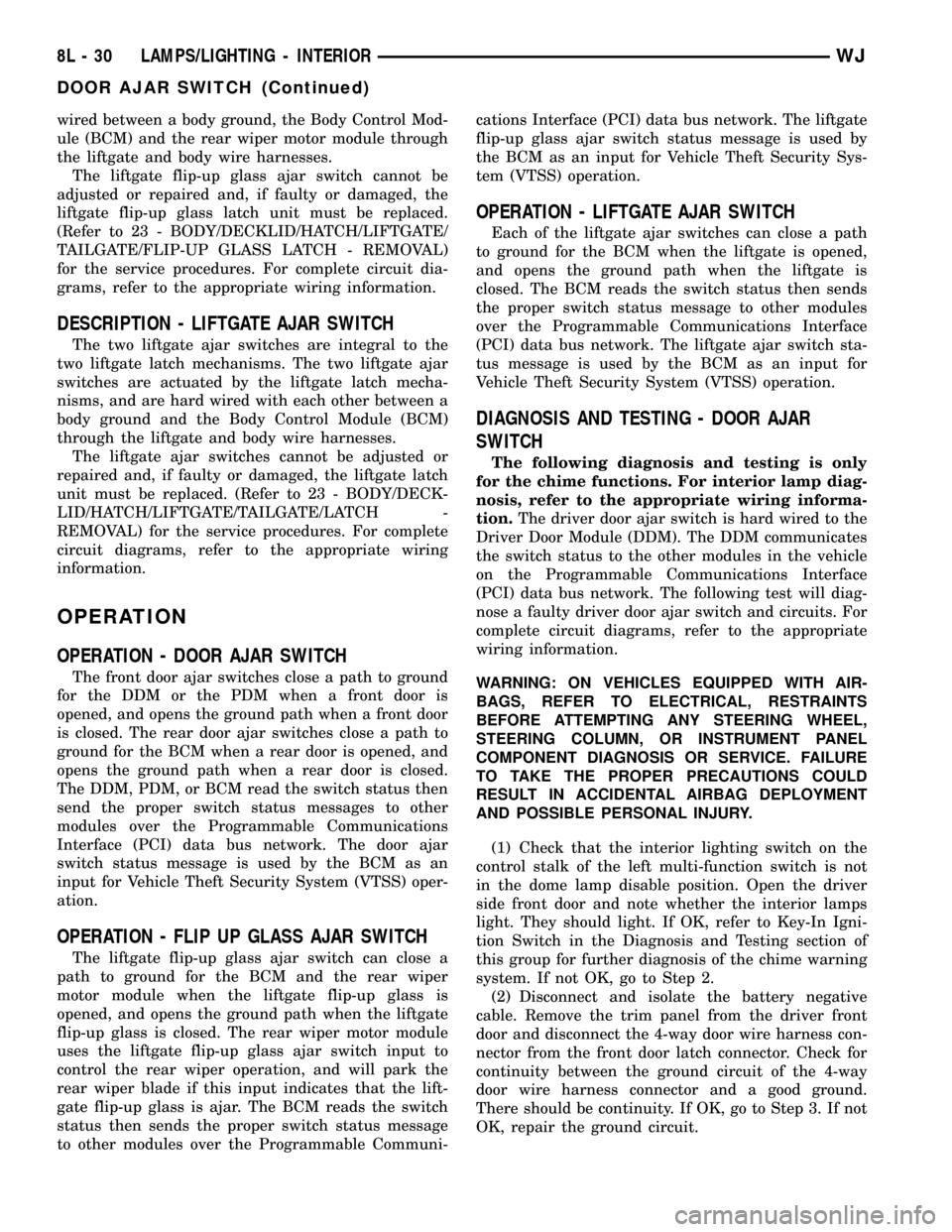
wired between a body ground, the Body Control Mod-
ule (BCM) and the rear wiper motor module through
the liftgate and body wire harnesses.
The liftgate flip-up glass ajar switch cannot be
adjusted or repaired and, if faulty or damaged, the
liftgate flip-up glass latch unit must be replaced.
(Refer to 23 - BODY/DECKLID/HATCH/LIFTGATE/
TAILGATE/FLIP-UP GLASS LATCH - REMOVAL)
for the service procedures. For complete circuit dia-
grams, refer to the appropriate wiring information.
DESCRIPTION - LIFTGATE AJAR SWITCH
The two liftgate ajar switches are integral to the
two liftgate latch mechanisms. The two liftgate ajar
switches are actuated by the liftgate latch mecha-
nisms, and are hard wired with each other between a
body ground and the Body Control Module (BCM)
through the liftgate and body wire harnesses.
The liftgate ajar switches cannot be adjusted or
repaired and, if faulty or damaged, the liftgate latch
unit must be replaced. (Refer to 23 - BODY/DECK-
LID/HATCH/LIFTGATE/TAILGATE/LATCH -
REMOVAL) for the service procedures. For complete
circuit diagrams, refer to the appropriate wiring
information.
OPERATION
OPERATION - DOOR AJAR SWITCH
The front door ajar switches close a path to ground
for the DDM or the PDM when a front door is
opened, and opens the ground path when a front door
is closed. The rear door ajar switches close a path to
ground for the BCM when a rear door is opened, and
opens the ground path when a rear door is closed.
The DDM, PDM, or BCM read the switch status then
send the proper switch status messages to other
modules over the Programmable Communications
Interface (PCI) data bus network. The door ajar
switch status message is used by the BCM as an
input for Vehicle Theft Security System (VTSS) oper-
ation.
OPERATION - FLIP UP GLASS AJAR SWITCH
The liftgate flip-up glass ajar switch can close a
path to ground for the BCM and the rear wiper
motor module when the liftgate flip-up glass is
opened, and opens the ground path when the liftgate
flip-up glass is closed. The rear wiper motor module
uses the liftgate flip-up glass ajar switch input to
control the rear wiper operation, and will park the
rear wiper blade if this input indicates that the lift-
gate flip-up glass is ajar. The BCM reads the switch
status then sends the proper switch status message
to other modules over the Programmable Communi-cations Interface (PCI) data bus network. The liftgate
flip-up glass ajar switch status message is used by
the BCM as an input for Vehicle Theft Security Sys-
tem (VTSS) operation.
OPERATION - LIFTGATE AJAR SWITCH
Each of the liftgate ajar switches can close a path
to ground for the BCM when the liftgate is opened,
and opens the ground path when the liftgate is
closed. The BCM reads the switch status then sends
the proper switch status message to other modules
over the Programmable Communications Interface
(PCI) data bus network. The liftgate ajar switch sta-
tus message is used by the BCM as an input for
Vehicle Theft Security System (VTSS) operation.
DIAGNOSIS AND TESTING - DOOR AJAR
SWITCH
The following diagnosis and testing is only
for the chime functions. For interior lamp diag-
nosis, refer to the appropriate wiring informa-
tion.The driver door ajar switch is hard wired to the
Driver Door Module (DDM). The DDM communicates
the switch status to the other modules in the vehicle
on the Programmable Communications Interface
(PCI) data bus network. The following test will diag-
nose a faulty driver door ajar switch and circuits. For
complete circuit diagrams, refer to the appropriate
wiring information.
WARNING: ON VEHICLES EQUIPPED WITH AIR-
BAGS, REFER TO ELECTRICAL, RESTRAINTS
BEFORE ATTEMPTING ANY STEERING WHEEL,
STEERING COLUMN, OR INSTRUMENT PANEL
COMPONENT DIAGNOSIS OR SERVICE. FAILURE
TO TAKE THE PROPER PRECAUTIONS COULD
RESULT IN ACCIDENTAL AIRBAG DEPLOYMENT
AND POSSIBLE PERSONAL INJURY.
(1) Check that the interior lighting switch on the
control stalk of the left multi-function switch is not
in the dome lamp disable position. Open the driver
side front door and note whether the interior lamps
light. They should light. If OK, refer to Key-In Igni-
tion Switch in the Diagnosis and Testing section of
this group for further diagnosis of the chime warning
system. If not OK, go to Step 2.
(2) Disconnect and isolate the battery negative
cable. Remove the trim panel from the driver front
door and disconnect the 4-way door wire harness con-
nector from the front door latch connector. Check for
continuity between the ground circuit of the 4-way
door wire harness connector and a good ground.
There should be continuity. If OK, go to Step 3. If not
OK, repair the ground circuit.
8L - 30 LAMPS/LIGHTING - INTERIORWJ
DOOR AJAR SWITCH (Continued)
Page 482 of 2199
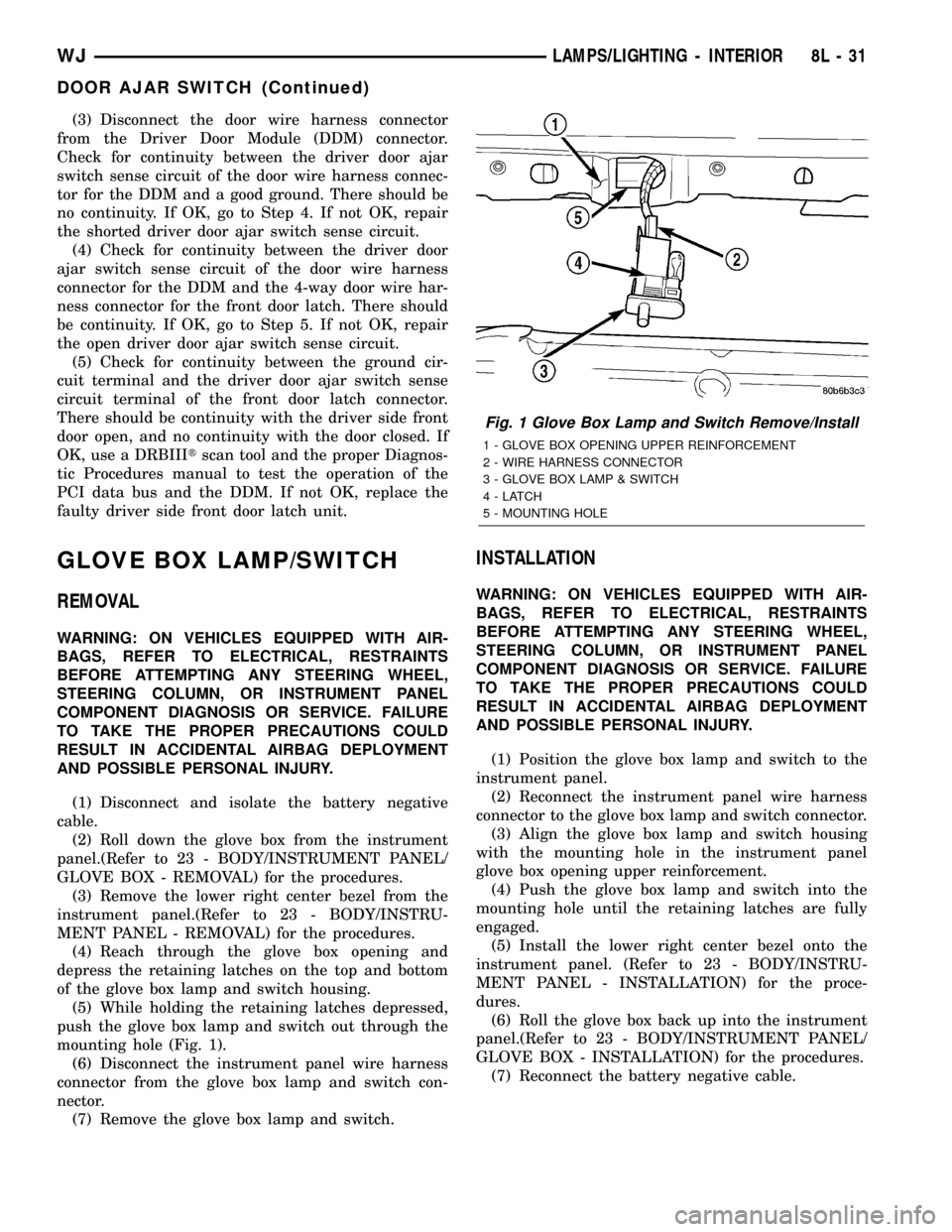
(3) Disconnect the door wire harness connector
from the Driver Door Module (DDM) connector.
Check for continuity between the driver door ajar
switch sense circuit of the door wire harness connec-
tor for the DDM and a good ground. There should be
no continuity. If OK, go to Step 4. If not OK, repair
the shorted driver door ajar switch sense circuit.
(4) Check for continuity between the driver door
ajar switch sense circuit of the door wire harness
connector for the DDM and the 4-way door wire har-
ness connector for the front door latch. There should
be continuity. If OK, go to Step 5. If not OK, repair
the open driver door ajar switch sense circuit.
(5) Check for continuity between the ground cir-
cuit terminal and the driver door ajar switch sense
circuit terminal of the front door latch connector.
There should be continuity with the driver side front
door open, and no continuity with the door closed. If
OK, use a DRBIIItscan tool and the proper Diagnos-
tic Procedures manual to test the operation of the
PCI data bus and the DDM. If not OK, replace the
faulty driver side front door latch unit.
GLOVE BOX LAMP/SWITCH
REMOVAL
WARNING: ON VEHICLES EQUIPPED WITH AIR-
BAGS, REFER TO ELECTRICAL, RESTRAINTS
BEFORE ATTEMPTING ANY STEERING WHEEL,
STEERING COLUMN, OR INSTRUMENT PANEL
COMPONENT DIAGNOSIS OR SERVICE. FAILURE
TO TAKE THE PROPER PRECAUTIONS COULD
RESULT IN ACCIDENTAL AIRBAG DEPLOYMENT
AND POSSIBLE PERSONAL INJURY.
(1) Disconnect and isolate the battery negative
cable.
(2) Roll down the glove box from the instrument
panel.(Refer to 23 - BODY/INSTRUMENT PANEL/
GLOVE BOX - REMOVAL) for the procedures.
(3) Remove the lower right center bezel from the
instrument panel.(Refer to 23 - BODY/INSTRU-
MENT PANEL - REMOVAL) for the procedures.
(4) Reach through the glove box opening and
depress the retaining latches on the top and bottom
of the glove box lamp and switch housing.
(5) While holding the retaining latches depressed,
push the glove box lamp and switch out through the
mounting hole (Fig. 1).
(6) Disconnect the instrument panel wire harness
connector from the glove box lamp and switch con-
nector.
(7) Remove the glove box lamp and switch.
INSTALLATION
WARNING: ON VEHICLES EQUIPPED WITH AIR-
BAGS, REFER TO ELECTRICAL, RESTRAINTS
BEFORE ATTEMPTING ANY STEERING WHEEL,
STEERING COLUMN, OR INSTRUMENT PANEL
COMPONENT DIAGNOSIS OR SERVICE. FAILURE
TO TAKE THE PROPER PRECAUTIONS COULD
RESULT IN ACCIDENTAL AIRBAG DEPLOYMENT
AND POSSIBLE PERSONAL INJURY.
(1) Position the glove box lamp and switch to the
instrument panel.
(2) Reconnect the instrument panel wire harness
connector to the glove box lamp and switch connector.
(3) Align the glove box lamp and switch housing
with the mounting hole in the instrument panel
glove box opening upper reinforcement.
(4) Push the glove box lamp and switch into the
mounting hole until the retaining latches are fully
engaged.
(5) Install the lower right center bezel onto the
instrument panel. (Refer to 23 - BODY/INSTRU-
MENT PANEL - INSTALLATION) for the proce-
dures.
(6) Roll the glove box back up into the instrument
panel.(Refer to 23 - BODY/INSTRUMENT PANEL/
GLOVE BOX - INSTALLATION) for the procedures.
(7) Reconnect the battery negative cable.
Fig. 1 Glove Box Lamp and Switch Remove/Install
1 - GLOVE BOX OPENING UPPER REINFORCEMENT
2 - WIRE HARNESS CONNECTOR
3 - GLOVE BOX LAMP & SWITCH
4-LATCH
5 - MOUNTING HOLE
WJLAMPS/LIGHTING - INTERIOR 8L - 31
DOOR AJAR SWITCH (Continued)
Page 540 of 2199
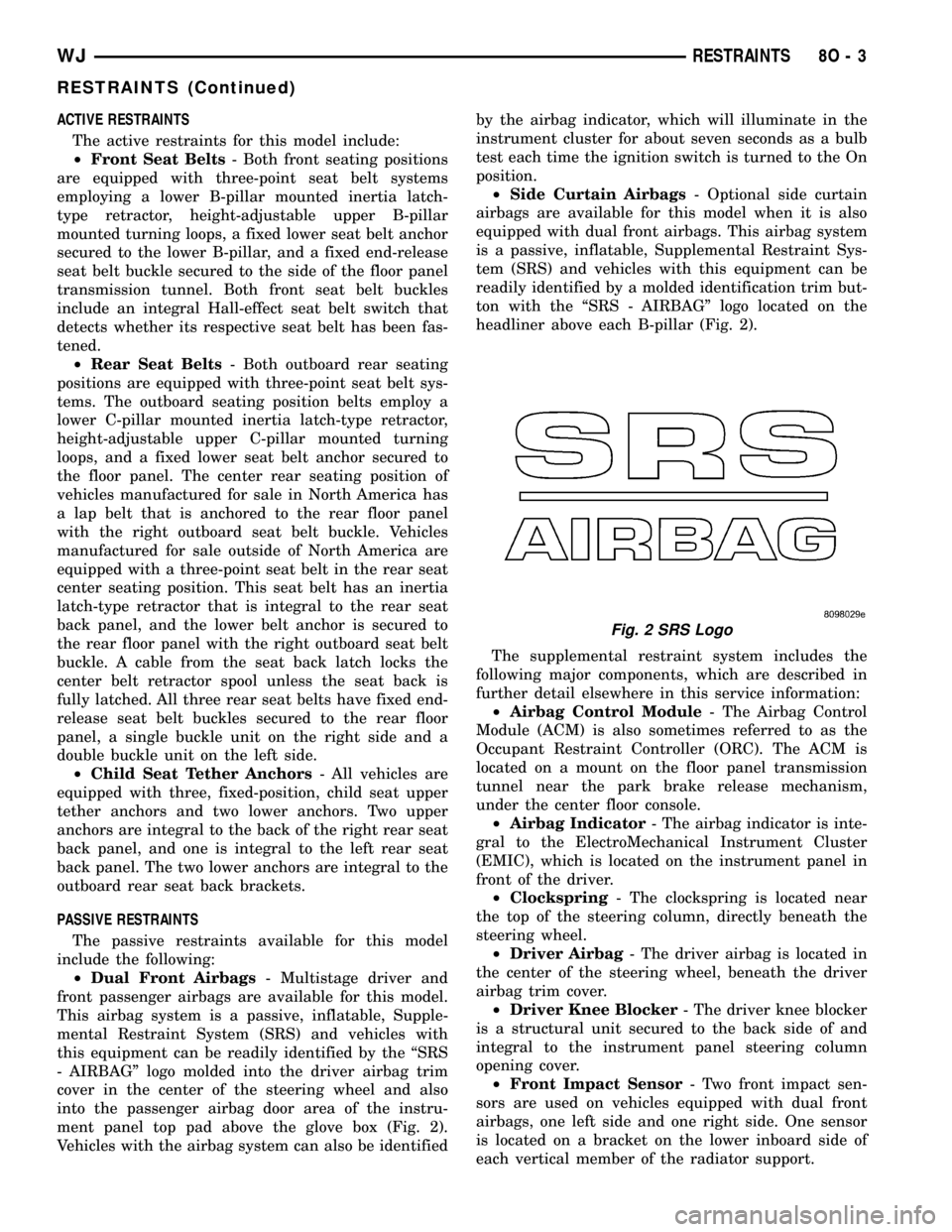
ACTIVE RESTRAINTS
The active restraints for this model include:
²Front Seat Belts- Both front seating positions
are equipped with three-point seat belt systems
employing a lower B-pillar mounted inertia latch-
type retractor, height-adjustable upper B-pillar
mounted turning loops, a fixed lower seat belt anchor
secured to the lower B-pillar, and a fixed end-release
seat belt buckle secured to the side of the floor panel
transmission tunnel. Both front seat belt buckles
include an integral Hall-effect seat belt switch that
detects whether its respective seat belt has been fas-
tened.
²Rear Seat Belts- Both outboard rear seating
positions are equipped with three-point seat belt sys-
tems. The outboard seating position belts employ a
lower C-pillar mounted inertia latch-type retractor,
height-adjustable upper C-pillar mounted turning
loops, and a fixed lower seat belt anchor secured to
the floor panel. The center rear seating position of
vehicles manufactured for sale in North America has
a lap belt that is anchored to the rear floor panel
with the right outboard seat belt buckle. Vehicles
manufactured for sale outside of North America are
equipped with a three-point seat belt in the rear seat
center seating position. This seat belt has an inertia
latch-type retractor that is integral to the rear seat
back panel, and the lower belt anchor is secured to
the rear floor panel with the right outboard seat belt
buckle. A cable from the seat back latch locks the
center belt retractor spool unless the seat back is
fully latched. All three rear seat belts have fixed end-
release seat belt buckles secured to the rear floor
panel, a single buckle unit on the right side and a
double buckle unit on the left side.
²Child Seat Tether Anchors- All vehicles are
equipped with three, fixed-position, child seat upper
tether anchors and two lower anchors. Two upper
anchors are integral to the back of the right rear seat
back panel, and one is integral to the left rear seat
back panel. The two lower anchors are integral to the
outboard rear seat back brackets.
PASSIVE RESTRAINTS
The passive restraints available for this model
include the following:
²Dual Front Airbags- Multistage driver and
front passenger airbags are available for this model.
This airbag system is a passive, inflatable, Supple-
mental Restraint System (SRS) and vehicles with
this equipment can be readily identified by the ªSRS
- AIRBAGº logo molded into the driver airbag trim
cover in the center of the steering wheel and also
into the passenger airbag door area of the instru-
ment panel top pad above the glove box (Fig. 2).
Vehicles with the airbag system can also be identifiedby the airbag indicator, which will illuminate in the
instrument cluster for about seven seconds as a bulb
test each time the ignition switch is turned to the On
position.
²Side Curtain Airbags- Optional side curtain
airbags are available for this model when it is also
equipped with dual front airbags. This airbag system
is a passive, inflatable, Supplemental Restraint Sys-
tem (SRS) and vehicles with this equipment can be
readily identified by a molded identification trim but-
ton with the ªSRS - AIRBAGº logo located on the
headliner above each B-pillar (Fig. 2).
The supplemental restraint system includes the
following major components, which are described in
further detail elsewhere in this service information:
²Airbag Control Module- The Airbag Control
Module (ACM) is also sometimes referred to as the
Occupant Restraint Controller (ORC). The ACM is
located on a mount on the floor panel transmission
tunnel near the park brake release mechanism,
under the center floor console.
²Airbag Indicator- The airbag indicator is inte-
gral to the ElectroMechanical Instrument Cluster
(EMIC), which is located on the instrument panel in
front of the driver.
²Clockspring- The clockspring is located near
the top of the steering column, directly beneath the
steering wheel.
²Driver Airbag- The driver airbag is located in
the center of the steering wheel, beneath the driver
airbag trim cover.
²Driver Knee Blocker- The driver knee blocker
is a structural unit secured to the back side of and
integral to the instrument panel steering column
opening cover.
²Front Impact Sensor- Two front impact sen-
sors are used on vehicles equipped with dual front
airbags, one left side and one right side. One sensor
is located on a bracket on the lower inboard side of
each vertical member of the radiator support.
Fig. 2 SRS Logo
WJRESTRAINTS 8O - 3
RESTRAINTS (Continued)
Page 545 of 2199
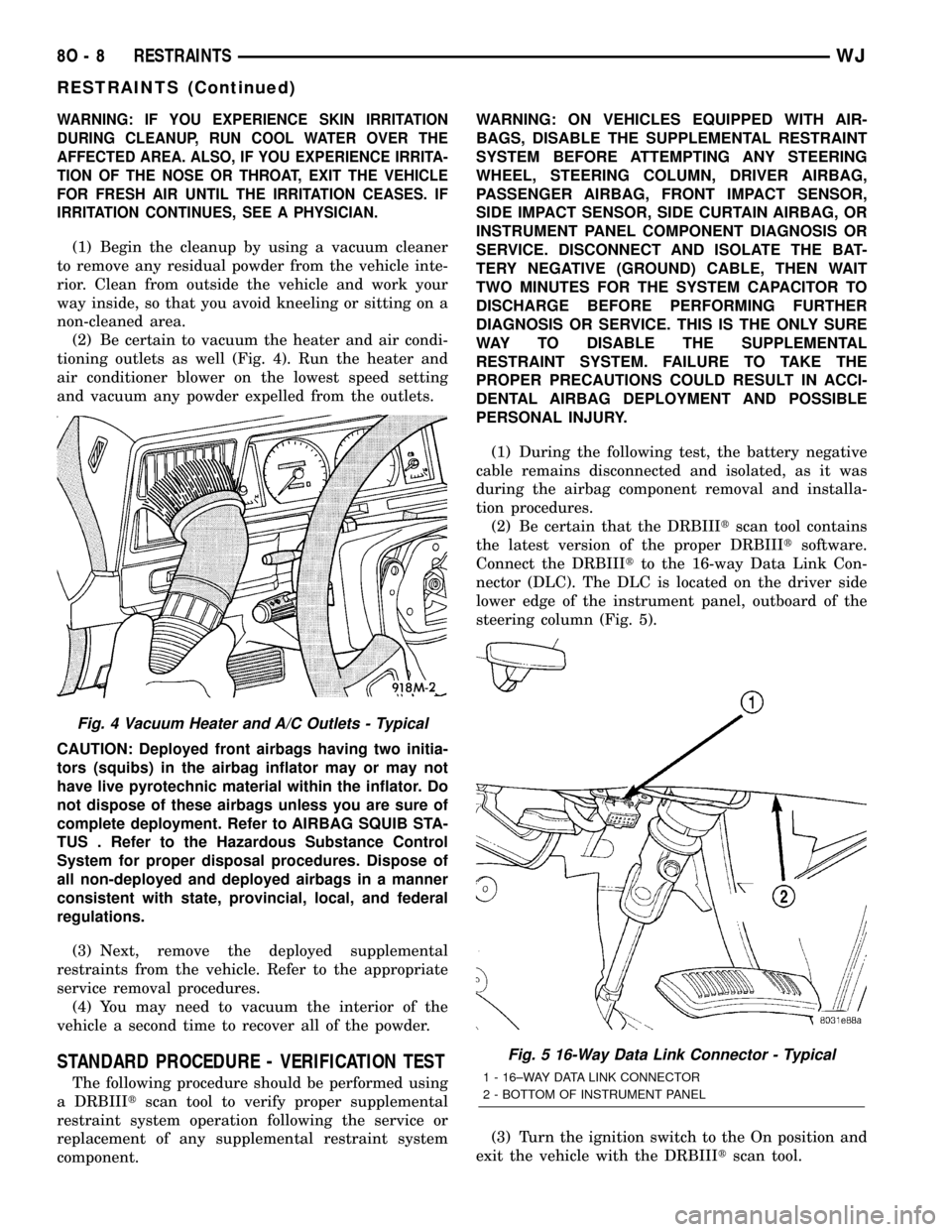
WARNING: IF YOU EXPERIENCE SKIN IRRITATION
DURING CLEANUP, RUN COOL WATER OVER THE
AFFECTED AREA. ALSO, IF YOU EXPERIENCE IRRITA-
TION OF THE NOSE OR THROAT, EXIT THE VEHICLE
FOR FRESH AIR UNTIL THE IRRITATION CEASES. IF
IRRITATION CONTINUES, SEE A PHYSICIAN.
(1) Begin the cleanup by using a vacuum cleaner
to remove any residual powder from the vehicle inte-
rior. Clean from outside the vehicle and work your
way inside, so that you avoid kneeling or sitting on a
non-cleaned area.
(2) Be certain to vacuum the heater and air condi-
tioning outlets as well (Fig. 4). Run the heater and
air conditioner blower on the lowest speed setting
and vacuum any powder expelled from the outlets.
CAUTION: Deployed front airbags having two initia-
tors (squibs) in the airbag inflator may or may not
have live pyrotechnic material within the inflator. Do
not dispose of these airbags unless you are sure of
complete deployment. Refer to AIRBAG SQUIB STA-
TUS . Refer to the Hazardous Substance Control
System for proper disposal procedures. Dispose of
all non-deployed and deployed airbags in a manner
consistent with state, provincial, local, and federal
regulations.
(3) Next, remove the deployed supplemental
restraints from the vehicle. Refer to the appropriate
service removal procedures.
(4) You may need to vacuum the interior of the
vehicle a second time to recover all of the powder.
STANDARD PROCEDURE - VERIFICATION TEST
The following procedure should be performed using
a DRBIIItscan tool to verify proper supplemental
restraint system operation following the service or
replacement of any supplemental restraint system
component.WARNING: ON VEHICLES EQUIPPED WITH AIR-
BAGS, DISABLE THE SUPPLEMENTAL RESTRAINT
SYSTEM BEFORE ATTEMPTING ANY STEERING
WHEEL, STEERING COLUMN, DRIVER AIRBAG,
PASSENGER AIRBAG, FRONT IMPACT SENSOR,
SIDE IMPACT SENSOR, SIDE CURTAIN AIRBAG, OR
INSTRUMENT PANEL COMPONENT DIAGNOSIS OR
SERVICE. DISCONNECT AND ISOLATE THE BAT-
TERY NEGATIVE (GROUND) CABLE, THEN WAIT
TWO MINUTES FOR THE SYSTEM CAPACITOR TO
DISCHARGE BEFORE PERFORMING FURTHER
DIAGNOSIS OR SERVICE. THIS IS THE ONLY SURE
WAY TO DISABLE THE SUPPLEMENTAL
RESTRAINT SYSTEM. FAILURE TO TAKE THE
PROPER PRECAUTIONS COULD RESULT IN ACCI-
DENTAL AIRBAG DEPLOYMENT AND POSSIBLE
PERSONAL INJURY.
(1) During the following test, the battery negative
cable remains disconnected and isolated, as it was
during the airbag component removal and installa-
tion procedures.
(2) Be certain that the DRBIIItscan tool contains
the latest version of the proper DRBIIItsoftware.
Connect the DRBIIItto the 16-way Data Link Con-
nector (DLC). The DLC is located on the driver side
lower edge of the instrument panel, outboard of the
steering column (Fig. 5).
(3) Turn the ignition switch to the On position and
exit the vehicle with the DRBIIItscan tool.
Fig. 4 Vacuum Heater and A/C Outlets - Typical
Fig. 5 16-Way Data Link Connector - Typical
1 - 16±WAY DATA LINK CONNECTOR
2 - BOTTOM OF INSTRUMENT PANEL
8O - 8 RESTRAINTSWJ
RESTRAINTS (Continued)
Page 551 of 2199
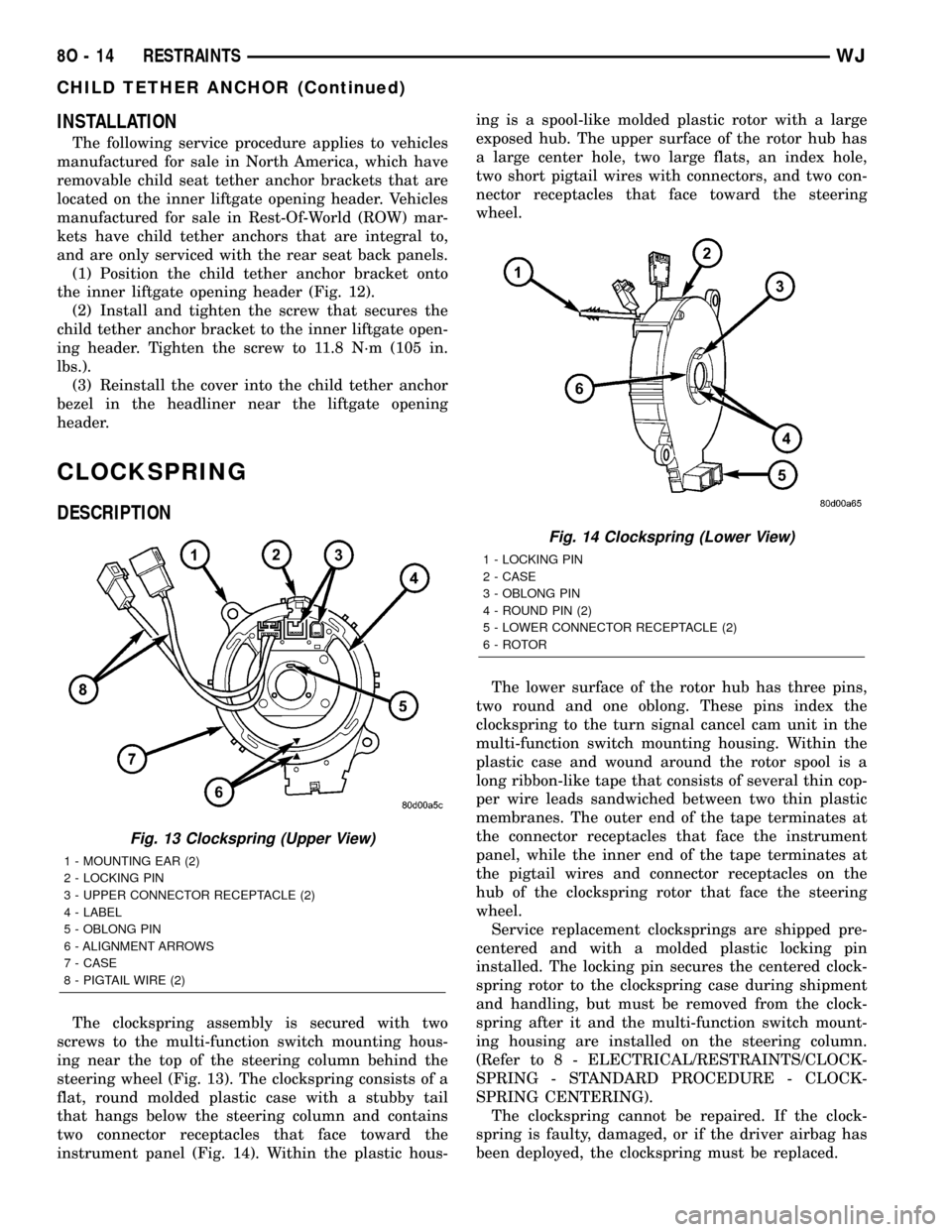
INSTALLATION
The following service procedure applies to vehicles
manufactured for sale in North America, which have
removable child seat tether anchor brackets that are
located on the inner liftgate opening header. Vehicles
manufactured for sale in Rest-Of-World (ROW) mar-
kets have child tether anchors that are integral to,
and are only serviced with the rear seat back panels.
(1) Position the child tether anchor bracket onto
the inner liftgate opening header (Fig. 12).
(2) Install and tighten the screw that secures the
child tether anchor bracket to the inner liftgate open-
ing header. Tighten the screw to 11.8 N´m (105 in.
lbs.).
(3) Reinstall the cover into the child tether anchor
bezel in the headliner near the liftgate opening
header.
CLOCKSPRING
DESCRIPTION
The clockspring assembly is secured with two
screws to the multi-function switch mounting hous-
ing near the top of the steering column behind the
steering wheel (Fig. 13). The clockspring consists of a
flat, round molded plastic case with a stubby tail
that hangs below the steering column and contains
two connector receptacles that face toward the
instrument panel (Fig. 14). Within the plastic hous-ing is a spool-like molded plastic rotor with a large
exposed hub. The upper surface of the rotor hub has
a large center hole, two large flats, an index hole,
two short pigtail wires with connectors, and two con-
nector receptacles that face toward the steering
wheel.
The lower surface of the rotor hub has three pins,
two round and one oblong. These pins index the
clockspring to the turn signal cancel cam unit in the
multi-function switch mounting housing. Within the
plastic case and wound around the rotor spool is a
long ribbon-like tape that consists of several thin cop-
per wire leads sandwiched between two thin plastic
membranes. The outer end of the tape terminates at
the connector receptacles that face the instrument
panel, while the inner end of the tape terminates at
the pigtail wires and connector receptacles on the
hub of the clockspring rotor that face the steering
wheel.
Service replacement clocksprings are shipped pre-
centered and with a molded plastic locking pin
installed. The locking pin secures the centered clock-
spring rotor to the clockspring case during shipment
and handling, but must be removed from the clock-
spring after it and the multi-function switch mount-
ing housing are installed on the steering column.
(Refer to 8 - ELECTRICAL/RESTRAINTS/CLOCK-
SPRING - STANDARD PROCEDURE - CLOCK-
SPRING CENTERING).
The clockspring cannot be repaired. If the clock-
spring is faulty, damaged, or if the driver airbag has
been deployed, the clockspring must be replaced.
Fig. 13 Clockspring (Upper View)
1 - MOUNTING EAR (2)
2 - LOCKING PIN
3 - UPPER CONNECTOR RECEPTACLE (2)
4 - LABEL
5 - OBLONG PIN
6 - ALIGNMENT ARROWS
7 - CASE
8 - PIGTAIL WIRE (2)
Fig. 14 Clockspring (Lower View)
1 - LOCKING PIN
2 - CASE
3 - OBLONG PIN
4 - ROUND PIN (2)
5 - LOWER CONNECTOR RECEPTACLE (2)
6 - ROTOR
8O - 14 RESTRAINTSWJ
CHILD TETHER ANCHOR (Continued)
Page 552 of 2199
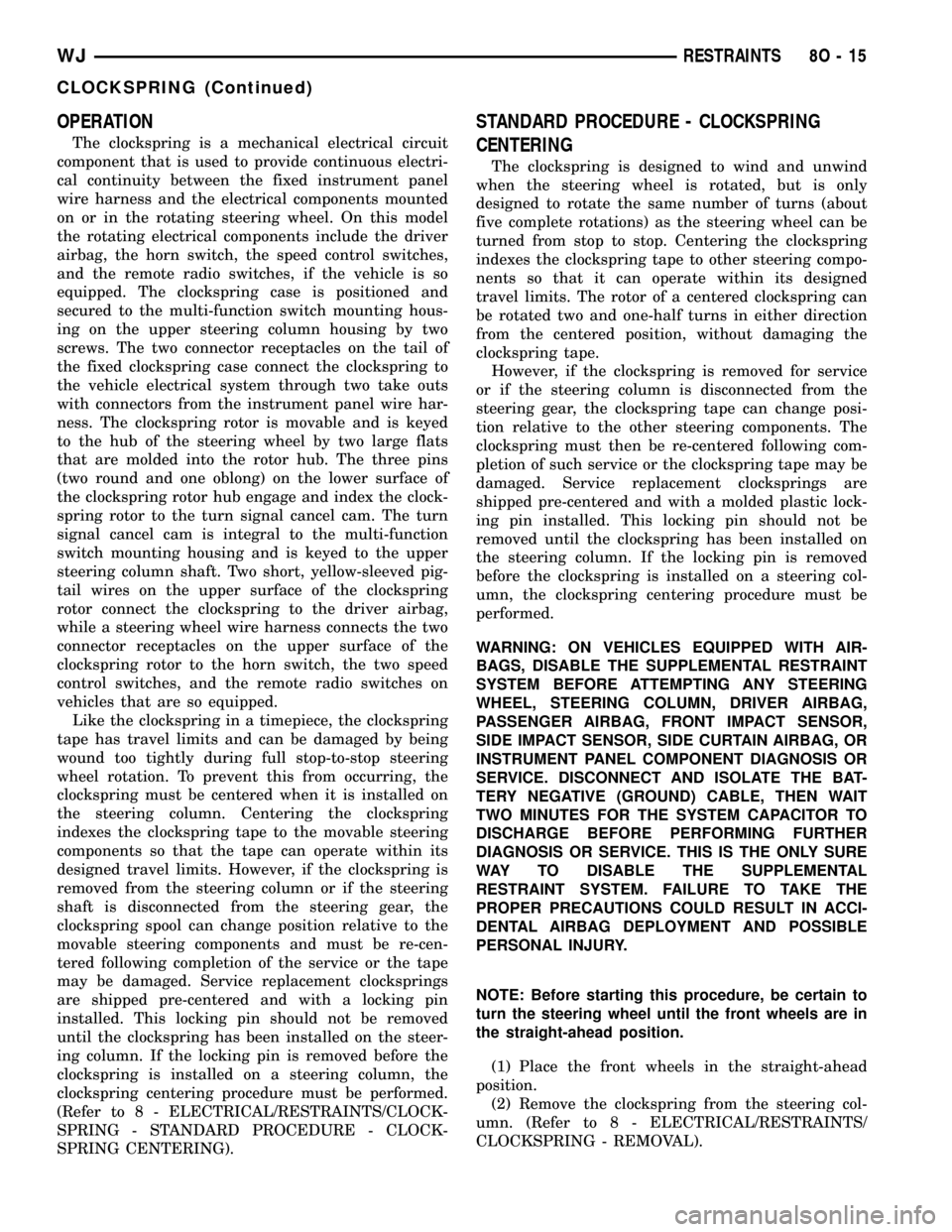
OPERATION
The clockspring is a mechanical electrical circuit
component that is used to provide continuous electri-
cal continuity between the fixed instrument panel
wire harness and the electrical components mounted
on or in the rotating steering wheel. On this model
the rotating electrical components include the driver
airbag, the horn switch, the speed control switches,
and the remote radio switches, if the vehicle is so
equipped. The clockspring case is positioned and
secured to the multi-function switch mounting hous-
ing on the upper steering column housing by two
screws. The two connector receptacles on the tail of
the fixed clockspring case connect the clockspring to
the vehicle electrical system through two take outs
with connectors from the instrument panel wire har-
ness. The clockspring rotor is movable and is keyed
to the hub of the steering wheel by two large flats
that are molded into the rotor hub. The three pins
(two round and one oblong) on the lower surface of
the clockspring rotor hub engage and index the clock-
spring rotor to the turn signal cancel cam. The turn
signal cancel cam is integral to the multi-function
switch mounting housing and is keyed to the upper
steering column shaft. Two short, yellow-sleeved pig-
tail wires on the upper surface of the clockspring
rotor connect the clockspring to the driver airbag,
while a steering wheel wire harness connects the two
connector receptacles on the upper surface of the
clockspring rotor to the horn switch, the two speed
control switches, and the remote radio switches on
vehicles that are so equipped.
Like the clockspring in a timepiece, the clockspring
tape has travel limits and can be damaged by being
wound too tightly during full stop-to-stop steering
wheel rotation. To prevent this from occurring, the
clockspring must be centered when it is installed on
the steering column. Centering the clockspring
indexes the clockspring tape to the movable steering
components so that the tape can operate within its
designed travel limits. However, if the clockspring is
removed from the steering column or if the steering
shaft is disconnected from the steering gear, the
clockspring spool can change position relative to the
movable steering components and must be re-cen-
tered following completion of the service or the tape
may be damaged. Service replacement clocksprings
are shipped pre-centered and with a locking pin
installed. This locking pin should not be removed
until the clockspring has been installed on the steer-
ing column. If the locking pin is removed before the
clockspring is installed on a steering column, the
clockspring centering procedure must be performed.
(Refer to 8 - ELECTRICAL/RESTRAINTS/CLOCK-
SPRING - STANDARD PROCEDURE - CLOCK-
SPRING CENTERING).
STANDARD PROCEDURE - CLOCKSPRING
CENTERING
The clockspring is designed to wind and unwind
when the steering wheel is rotated, but is only
designed to rotate the same number of turns (about
five complete rotations) as the steering wheel can be
turned from stop to stop. Centering the clockspring
indexes the clockspring tape to other steering compo-
nents so that it can operate within its designed
travel limits. The rotor of a centered clockspring can
be rotated two and one-half turns in either direction
from the centered position, without damaging the
clockspring tape.
However, if the clockspring is removed for service
or if the steering column is disconnected from the
steering gear, the clockspring tape can change posi-
tion relative to the other steering components. The
clockspring must then be re-centered following com-
pletion of such service or the clockspring tape may be
damaged. Service replacement clocksprings are
shipped pre-centered and with a molded plastic lock-
ing pin installed. This locking pin should not be
removed until the clockspring has been installed on
the steering column. If the locking pin is removed
before the clockspring is installed on a steering col-
umn, the clockspring centering procedure must be
performed.
WARNING: ON VEHICLES EQUIPPED WITH AIR-
BAGS, DISABLE THE SUPPLEMENTAL RESTRAINT
SYSTEM BEFORE ATTEMPTING ANY STEERING
WHEEL, STEERING COLUMN, DRIVER AIRBAG,
PASSENGER AIRBAG, FRONT IMPACT SENSOR,
SIDE IMPACT SENSOR, SIDE CURTAIN AIRBAG, OR
INSTRUMENT PANEL COMPONENT DIAGNOSIS OR
SERVICE. DISCONNECT AND ISOLATE THE BAT-
TERY NEGATIVE (GROUND) CABLE, THEN WAIT
TWO MINUTES FOR THE SYSTEM CAPACITOR TO
DISCHARGE BEFORE PERFORMING FURTHER
DIAGNOSIS OR SERVICE. THIS IS THE ONLY SURE
WAY TO DISABLE THE SUPPLEMENTAL
RESTRAINT SYSTEM. FAILURE TO TAKE THE
PROPER PRECAUTIONS COULD RESULT IN ACCI-
DENTAL AIRBAG DEPLOYMENT AND POSSIBLE
PERSONAL INJURY.
NOTE: Before starting this procedure, be certain to
turn the steering wheel until the front wheels are in
the straight-ahead position.
(1) Place the front wheels in the straight-ahead
position.
(2) Remove the clockspring from the steering col-
umn. (Refer to 8 - ELECTRICAL/RESTRAINTS/
CLOCKSPRING - REMOVAL).
WJRESTRAINTS 8O - 15
CLOCKSPRING (Continued)
Page 553 of 2199
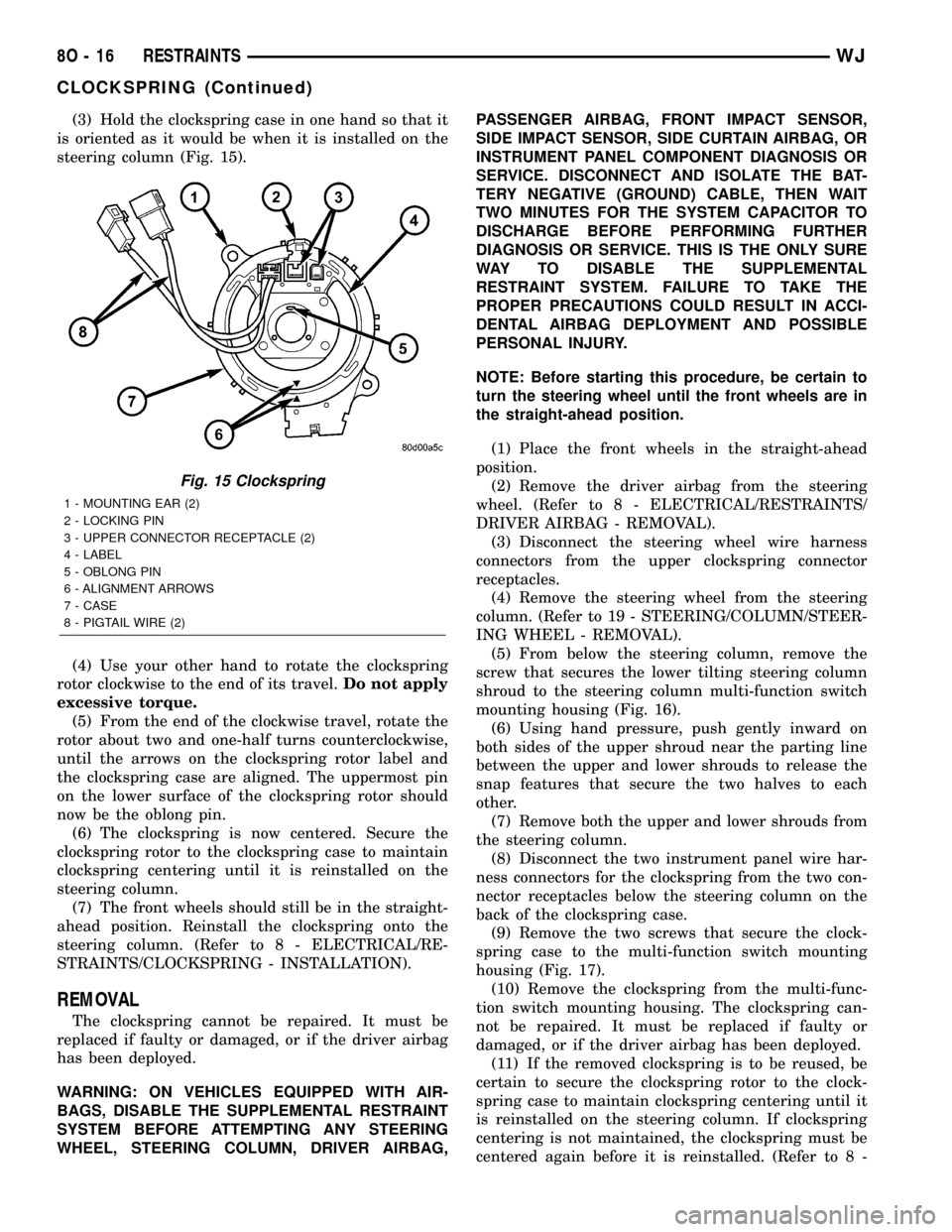
(3) Hold the clockspring case in one hand so that it
is oriented as it would be when it is installed on the
steering column (Fig. 15).
(4) Use your other hand to rotate the clockspring
rotor clockwise to the end of its travel.Do not apply
excessive torque.
(5) From the end of the clockwise travel, rotate the
rotor about two and one-half turns counterclockwise,
until the arrows on the clockspring rotor label and
the clockspring case are aligned. The uppermost pin
on the lower surface of the clockspring rotor should
now be the oblong pin.
(6) The clockspring is now centered. Secure the
clockspring rotor to the clockspring case to maintain
clockspring centering until it is reinstalled on the
steering column.
(7) The front wheels should still be in the straight-
ahead position. Reinstall the clockspring onto the
steering column. (Refer to 8 - ELECTRICAL/RE-
STRAINTS/CLOCKSPRING - INSTALLATION).
REMOVAL
The clockspring cannot be repaired. It must be
replaced if faulty or damaged, or if the driver airbag
has been deployed.
WARNING: ON VEHICLES EQUIPPED WITH AIR-
BAGS, DISABLE THE SUPPLEMENTAL RESTRAINT
SYSTEM BEFORE ATTEMPTING ANY STEERING
WHEEL, STEERING COLUMN, DRIVER AIRBAG,PASSENGER AIRBAG, FRONT IMPACT SENSOR,
SIDE IMPACT SENSOR, SIDE CURTAIN AIRBAG, OR
INSTRUMENT PANEL COMPONENT DIAGNOSIS OR
SERVICE. DISCONNECT AND ISOLATE THE BAT-
TERY NEGATIVE (GROUND) CABLE, THEN WAIT
TWO MINUTES FOR THE SYSTEM CAPACITOR TO
DISCHARGE BEFORE PERFORMING FURTHER
DIAGNOSIS OR SERVICE. THIS IS THE ONLY SURE
WAY TO DISABLE THE SUPPLEMENTAL
RESTRAINT SYSTEM. FAILURE TO TAKE THE
PROPER PRECAUTIONS COULD RESULT IN ACCI-
DENTAL AIRBAG DEPLOYMENT AND POSSIBLE
PERSONAL INJURY.
NOTE: Before starting this procedure, be certain to
turn the steering wheel until the front wheels are in
the straight-ahead position.
(1) Place the front wheels in the straight-ahead
position.
(2) Remove the driver airbag from the steering
wheel. (Refer to 8 - ELECTRICAL/RESTRAINTS/
DRIVER AIRBAG - REMOVAL).
(3) Disconnect the steering wheel wire harness
connectors from the upper clockspring connector
receptacles.
(4) Remove the steering wheel from the steering
column. (Refer to 19 - STEERING/COLUMN/STEER-
ING WHEEL - REMOVAL).
(5) From below the steering column, remove the
screw that secures the lower tilting steering column
shroud to the steering column multi-function switch
mounting housing (Fig. 16).
(6) Using hand pressure, push gently inward on
both sides of the upper shroud near the parting line
between the upper and lower shrouds to release the
snap features that secure the two halves to each
other.
(7) Remove both the upper and lower shrouds from
the steering column.
(8) Disconnect the two instrument panel wire har-
ness connectors for the clockspring from the two con-
nector receptacles below the steering column on the
back of the clockspring case.
(9) Remove the two screws that secure the clock-
spring case to the multi-function switch mounting
housing (Fig. 17).
(10) Remove the clockspring from the multi-func-
tion switch mounting housing. The clockspring can-
not be repaired. It must be replaced if faulty or
damaged, or if the driver airbag has been deployed.
(11) If the removed clockspring is to be reused, be
certain to secure the clockspring rotor to the clock-
spring case to maintain clockspring centering until it
is reinstalled on the steering column. If clockspring
centering is not maintained, the clockspring must be
centered again before it is reinstalled. (Refer to 8 -
Fig. 15 Clockspring
1 - MOUNTING EAR (2)
2 - LOCKING PIN
3 - UPPER CONNECTOR RECEPTACLE (2)
4 - LABEL
5 - OBLONG PIN
6 - ALIGNMENT ARROWS
7 - CASE
8 - PIGTAIL WIRE (2)
8O - 16 RESTRAINTSWJ
CLOCKSPRING (Continued)
Page 554 of 2199
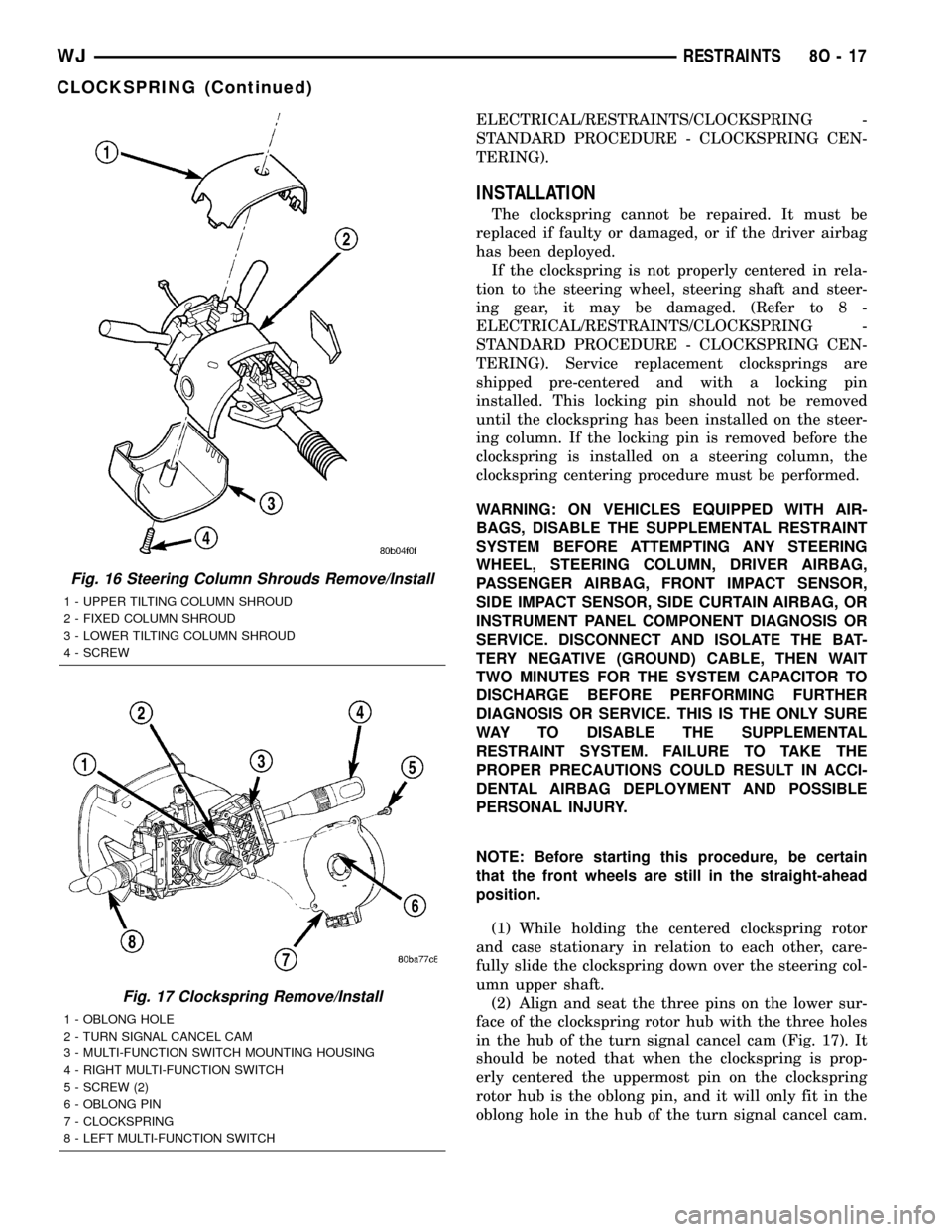
ELECTRICAL/RESTRAINTS/CLOCKSPRING -
STANDARD PROCEDURE - CLOCKSPRING CEN-
TERING).
INSTALLATION
The clockspring cannot be repaired. It must be
replaced if faulty or damaged, or if the driver airbag
has been deployed.
If the clockspring is not properly centered in rela-
tion to the steering wheel, steering shaft and steer-
ing gear, it may be damaged. (Refer to 8 -
ELECTRICAL/RESTRAINTS/CLOCKSPRING -
STANDARD PROCEDURE - CLOCKSPRING CEN-
TERING). Service replacement clocksprings are
shipped pre-centered and with a locking pin
installed. This locking pin should not be removed
until the clockspring has been installed on the steer-
ing column. If the locking pin is removed before the
clockspring is installed on a steering column, the
clockspring centering procedure must be performed.
WARNING: ON VEHICLES EQUIPPED WITH AIR-
BAGS, DISABLE THE SUPPLEMENTAL RESTRAINT
SYSTEM BEFORE ATTEMPTING ANY STEERING
WHEEL, STEERING COLUMN, DRIVER AIRBAG,
PASSENGER AIRBAG, FRONT IMPACT SENSOR,
SIDE IMPACT SENSOR, SIDE CURTAIN AIRBAG, OR
INSTRUMENT PANEL COMPONENT DIAGNOSIS OR
SERVICE. DISCONNECT AND ISOLATE THE BAT-
TERY NEGATIVE (GROUND) CABLE, THEN WAIT
TWO MINUTES FOR THE SYSTEM CAPACITOR TO
DISCHARGE BEFORE PERFORMING FURTHER
DIAGNOSIS OR SERVICE. THIS IS THE ONLY SURE
WAY TO DISABLE THE SUPPLEMENTAL
RESTRAINT SYSTEM. FAILURE TO TAKE THE
PROPER PRECAUTIONS COULD RESULT IN ACCI-
DENTAL AIRBAG DEPLOYMENT AND POSSIBLE
PERSONAL INJURY.
NOTE: Before starting this procedure, be certain
that the front wheels are still in the straight-ahead
position.
(1) While holding the centered clockspring rotor
and case stationary in relation to each other, care-
fully slide the clockspring down over the steering col-
umn upper shaft.
(2) Align and seat the three pins on the lower sur-
face of the clockspring rotor hub with the three holes
in the hub of the turn signal cancel cam (Fig. 17). It
should be noted that when the clockspring is prop-
erly centered the uppermost pin on the clockspring
rotor hub is the oblong pin, and it will only fit in the
oblong hole in the hub of the turn signal cancel cam.
Fig. 16 Steering Column Shrouds Remove/Install
1 - UPPER TILTING COLUMN SHROUD
2 - FIXED COLUMN SHROUD
3 - LOWER TILTING COLUMN SHROUD
4 - SCREW
Fig. 17 Clockspring Remove/Install
1 - OBLONG HOLE
2 - TURN SIGNAL CANCEL CAM
3 - MULTI-FUNCTION SWITCH MOUNTING HOUSING
4 - RIGHT MULTI-FUNCTION SWITCH
5 - SCREW (2)
6 - OBLONG PIN
7 - CLOCKSPRING
8 - LEFT MULTI-FUNCTION SWITCH
WJRESTRAINTS 8O - 17
CLOCKSPRING (Continued)
Page 555 of 2199
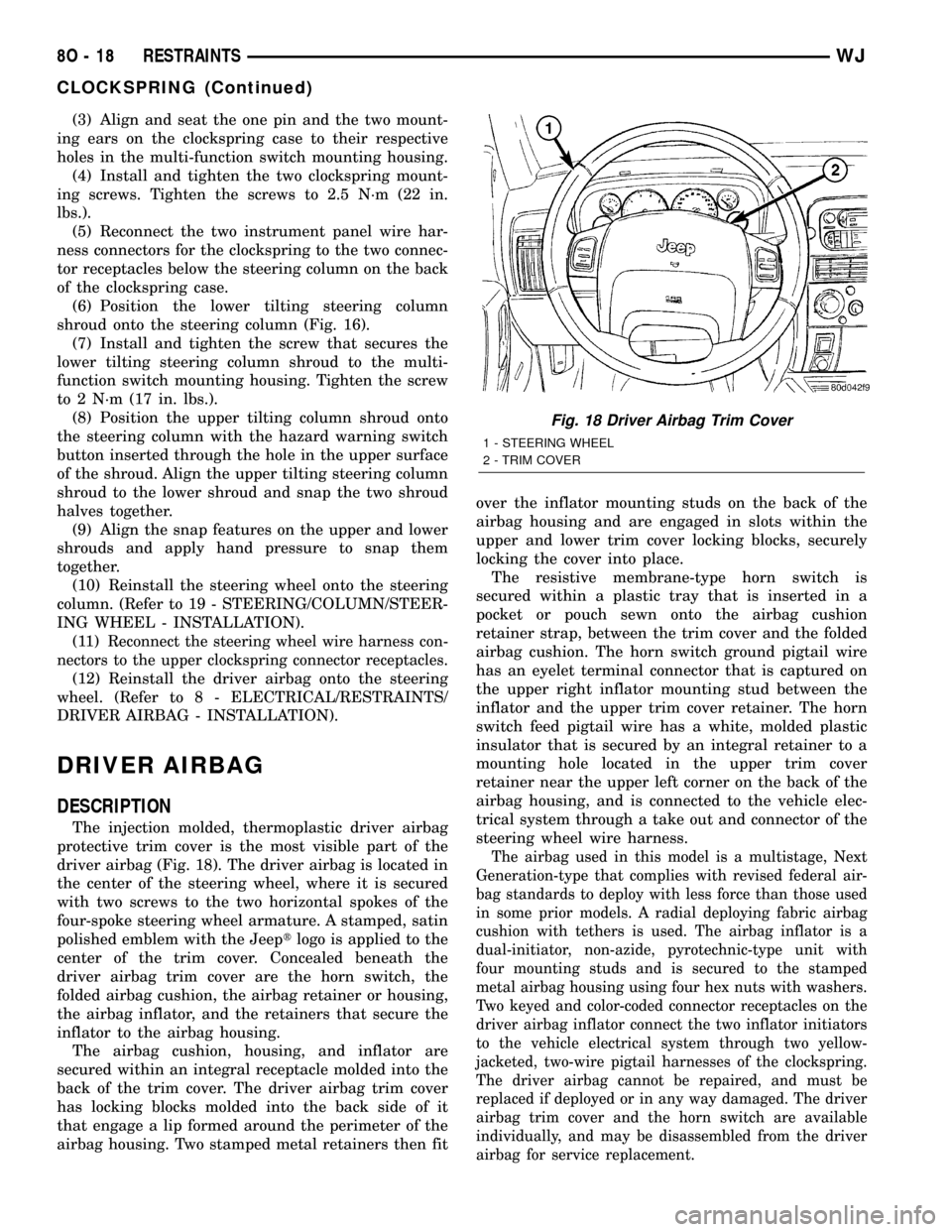
(3) Align and seat the one pin and the two mount-
ing ears on the clockspring case to their respective
holes in the multi-function switch mounting housing.
(4) Install and tighten the two clockspring mount-
ing screws. Tighten the screws to 2.5 N´m (22 in.
lbs.).
(5) Reconnect the two instrument panel wire har-
ness connectors for the clockspring to the two connec-
tor receptacles below the steering column on the back
of the clockspring case.
(6) Position the lower tilting steering column
shroud onto the steering column (Fig. 16).
(7) Install and tighten the screw that secures the
lower tilting steering column shroud to the multi-
function switch mounting housing. Tighten the screw
to 2 N´m (17 in. lbs.).
(8) Position the upper tilting column shroud onto
the steering column with the hazard warning switch
button inserted through the hole in the upper surface
of the shroud. Align the upper tilting steering column
shroud to the lower shroud and snap the two shroud
halves together.
(9) Align the snap features on the upper and lower
shrouds and apply hand pressure to snap them
together.
(10) Reinstall the steering wheel onto the steering
column. (Refer to 19 - STEERING/COLUMN/STEER-
ING WHEEL - INSTALLATION).
(11)
Reconnect the steering wheel wire harness con-
nectors to the upper clockspring connector receptacles.
(12) Reinstall the driver airbag onto the steering
wheel. (Refer to 8 - ELECTRICAL/RESTRAINTS/
DRIVER AIRBAG - INSTALLATION).
DRIVER AIRBAG
DESCRIPTION
The injection molded, thermoplastic driver airbag
protective trim cover is the most visible part of the
driver airbag (Fig. 18). The driver airbag is located in
the center of the steering wheel, where it is secured
with two screws to the two horizontal spokes of the
four-spoke steering wheel armature. A stamped, satin
polished emblem with the Jeeptlogo is applied to the
center of the trim cover. Concealed beneath the
driver airbag trim cover are the horn switch, the
folded airbag cushion, the airbag retainer or housing,
the airbag inflator, and the retainers that secure the
inflator to the airbag housing.
The airbag cushion, housing, and inflator are
secured within an integral receptacle molded into the
back of the trim cover. The driver airbag trim cover
has locking blocks molded into the back side of it
that engage a lip formed around the perimeter of the
airbag housing. Two stamped metal retainers then fitover the inflator mounting studs on the back of the
airbag housing and are engaged in slots within the
upper and lower trim cover locking blocks, securely
locking the cover into place.
The resistive membrane-type horn switch is
secured within a plastic tray that is inserted in a
pocket or pouch sewn onto the airbag cushion
retainer strap, between the trim cover and the folded
airbag cushion. The horn switch ground pigtail wire
has an eyelet terminal connector that is captured on
the upper right inflator mounting stud between the
inflator and the upper trim cover retainer. The horn
switch feed pigtail wire has a white, molded plastic
insulator that is secured by an integral retainer to a
mounting hole located in the upper trim cover
retainer near the upper left corner on the back of the
airbag housing, and is connected to the vehicle elec-
trical system through a take out and connector of the
steering wheel wire harness.
The airbag used in this model is a multistage, Next
Generation-type that complies with revised federal air-
bag standards to deploy with less force than those used
in some prior models. A radial deploying fabric airbag
cushion with tethers is used. The airbag inflator is a
dual-initiator, non-azide, pyrotechnic-type unit with
four mounting studs and is secured to the stamped
metal airbag housing using four hex nuts with washers.
Two keyed and color-coded connector receptacles on the
driver airbag inflator connect the two inflator initiators
to the vehicle electrical system through two yellow-
jacketed, two-wire pigtail harnesses of the clockspring.
The driver airbag cannot be repaired, and must be
replaced if deployed or in any way damaged. The driver
airbag trim cover and the horn switch are available
individually, and may be disassembled from the driver
airbag for service replacement.
Fig. 18 Driver Airbag Trim Cover
1 - STEERING WHEEL
2 - TRIM COVER
8O - 18 RESTRAINTSWJ
CLOCKSPRING (Continued)