warning JEEP GRAND CHEROKEE 2002 WJ / 2.G Repair Manual
[x] Cancel search | Manufacturer: JEEP, Model Year: 2002, Model line: GRAND CHEROKEE, Model: JEEP GRAND CHEROKEE 2002 WJ / 2.GPages: 2199, PDF Size: 76.01 MB
Page 307 of 2199
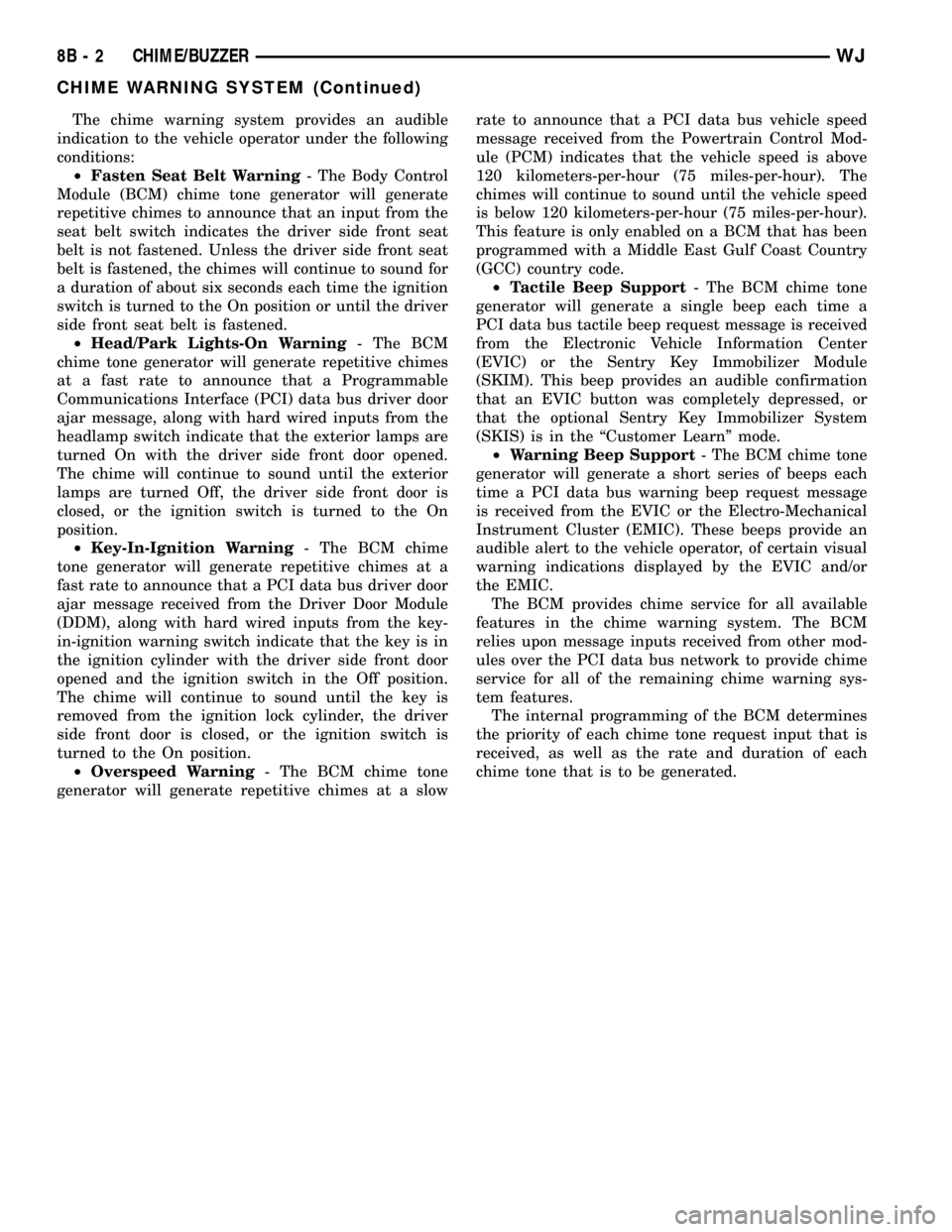
The chime warning system provides an audible
indication to the vehicle operator under the following
conditions:
²Fasten Seat Belt Warning- The Body Control
Module (BCM) chime tone generator will generate
repetitive chimes to announce that an input from the
seat belt switch indicates the driver side front seat
belt is not fastened. Unless the driver side front seat
belt is fastened, the chimes will continue to sound for
a duration of about six seconds each time the ignition
switch is turned to the On position or until the driver
side front seat belt is fastened.
²Head/Park Lights-On Warning- The BCM
chime tone generator will generate repetitive chimes
at a fast rate to announce that a Programmable
Communications Interface (PCI) data bus driver door
ajar message, along with hard wired inputs from the
headlamp switch indicate that the exterior lamps are
turned On with the driver side front door opened.
The chime will continue to sound until the exterior
lamps are turned Off, the driver side front door is
closed, or the ignition switch is turned to the On
position.
²Key-In-Ignition Warning- The BCM chime
tone generator will generate repetitive chimes at a
fast rate to announce that a PCI data bus driver door
ajar message received from the Driver Door Module
(DDM), along with hard wired inputs from the key-
in-ignition warning switch indicate that the key is in
the ignition cylinder with the driver side front door
opened and the ignition switch in the Off position.
The chime will continue to sound until the key is
removed from the ignition lock cylinder, the driver
side front door is closed, or the ignition switch is
turned to the On position.
²Overspeed Warning- The BCM chime tone
generator will generate repetitive chimes at a slowrate to announce that a PCI data bus vehicle speed
message received from the Powertrain Control Mod-
ule (PCM) indicates that the vehicle speed is above
120 kilometers-per-hour (75 miles-per-hour). The
chimes will continue to sound until the vehicle speed
is below 120 kilometers-per-hour (75 miles-per-hour).
This feature is only enabled on a BCM that has been
programmed with a Middle East Gulf Coast Country
(GCC) country code.
²Tactile Beep Support- The BCM chime tone
generator will generate a single beep each time a
PCI data bus tactile beep request message is received
from the Electronic Vehicle Information Center
(EVIC) or the Sentry Key Immobilizer Module
(SKIM). This beep provides an audible confirmation
that an EVIC button was completely depressed, or
that the optional Sentry Key Immobilizer System
(SKIS) is in the ªCustomer Learnº mode.
²Warning Beep Support- The BCM chime tone
generator will generate a short series of beeps each
time a PCI data bus warning beep request message
is received from the EVIC or the Electro-Mechanical
Instrument Cluster (EMIC). These beeps provide an
audible alert to the vehicle operator, of certain visual
warning indications displayed by the EVIC and/or
the EMIC.
The BCM provides chime service for all available
features in the chime warning system. The BCM
relies upon message inputs received from other mod-
ules over the PCI data bus network to provide chime
service for all of the remaining chime warning sys-
tem features.
The internal programming of the BCM determines
the priority of each chime tone request input that is
received, as well as the rate and duration of each
chime tone that is to be generated.
8B - 2 CHIME/BUZZERWJ
CHIME WARNING SYSTEM (Continued)
Page 308 of 2199
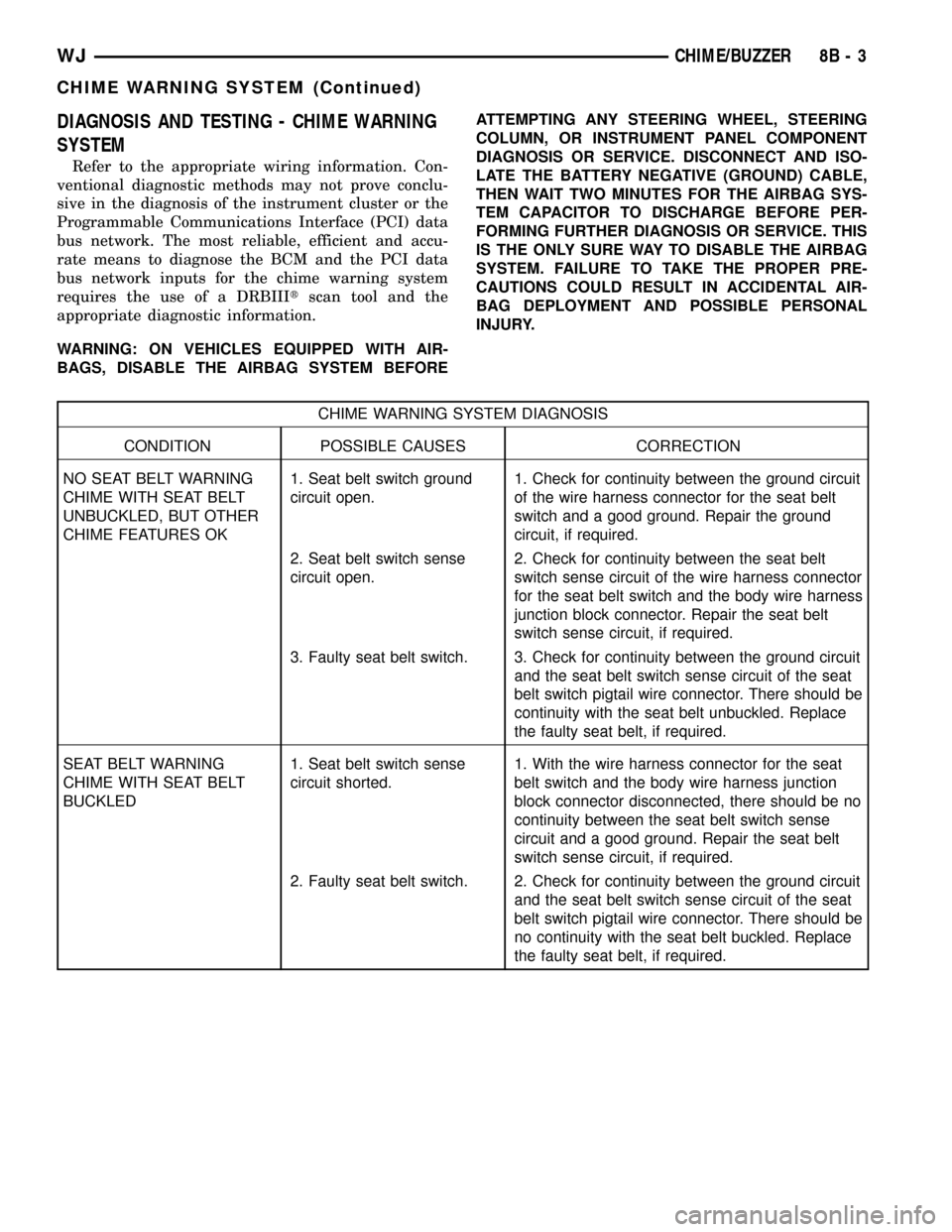
DIAGNOSIS AND TESTING - CHIME WARNING
SYSTEM
Refer to the appropriate wiring information. Con-
ventional diagnostic methods may not prove conclu-
sive in the diagnosis of the instrument cluster or the
Programmable Communications Interface (PCI) data
bus network. The most reliable, efficient and accu-
rate means to diagnose the BCM and the PCI data
bus network inputs for the chime warning system
requires the use of a DRBIIItscan tool and the
appropriate diagnostic information.
WARNING: ON VEHICLES EQUIPPED WITH AIR-
BAGS, DISABLE THE AIRBAG SYSTEM BEFOREATTEMPTING ANY STEERING WHEEL, STEERING
COLUMN, OR INSTRUMENT PANEL COMPONENT
DIAGNOSIS OR SERVICE. DISCONNECT AND ISO-
LATE THE BATTERY NEGATIVE (GROUND) CABLE,
THEN WAIT TWO MINUTES FOR THE AIRBAG SYS-
TEM CAPACITOR TO DISCHARGE BEFORE PER-
FORMING FURTHER DIAGNOSIS OR SERVICE. THIS
IS THE ONLY SURE WAY TO DISABLE THE AIRBAG
SYSTEM. FAILURE TO TAKE THE PROPER PRE-
CAUTIONS COULD RESULT IN ACCIDENTAL AIR-
BAG DEPLOYMENT AND POSSIBLE PERSONAL
INJURY.
CHIME WARNING SYSTEM DIAGNOSIS
CONDITION POSSIBLE CAUSES CORRECTION
NO SEAT BELT WARNING
CHIME WITH SEAT BELT
UNBUCKLED, BUT OTHER
CHIME FEATURES OK1. Seat belt switch ground
circuit open.1. Check for continuity between the ground circuit
of the wire harness connector for the seat belt
switch and a good ground. Repair the ground
circuit, if required.
2. Seat belt switch sense
circuit open.2. Check for continuity between the seat belt
switch sense circuit of the wire harness connector
for the seat belt switch and the body wire harness
junction block connector. Repair the seat belt
switch sense circuit, if required.
3. Faulty seat belt switch. 3. Check for continuity between the ground circuit
and the seat belt switch sense circuit of the seat
belt switch pigtail wire connector. There should be
continuity with the seat belt unbuckled. Replace
the faulty seat belt, if required.
SEAT BELT WARNING
CHIME WITH SEAT BELT
BUCKLED1. Seat belt switch sense
circuit shorted.1. With the wire harness connector for the seat
belt switch and the body wire harness junction
block connector disconnected, there should be no
continuity between the seat belt switch sense
circuit and a good ground. Repair the seat belt
switch sense circuit, if required.
2. Faulty seat belt switch. 2. Check for continuity between the ground circuit
and the seat belt switch sense circuit of the seat
belt switch pigtail wire connector. There should be
no continuity with the seat belt buckled. Replace
the faulty seat belt, if required.
WJCHIME/BUZZER 8B - 3
CHIME WARNING SYSTEM (Continued)
Page 309 of 2199
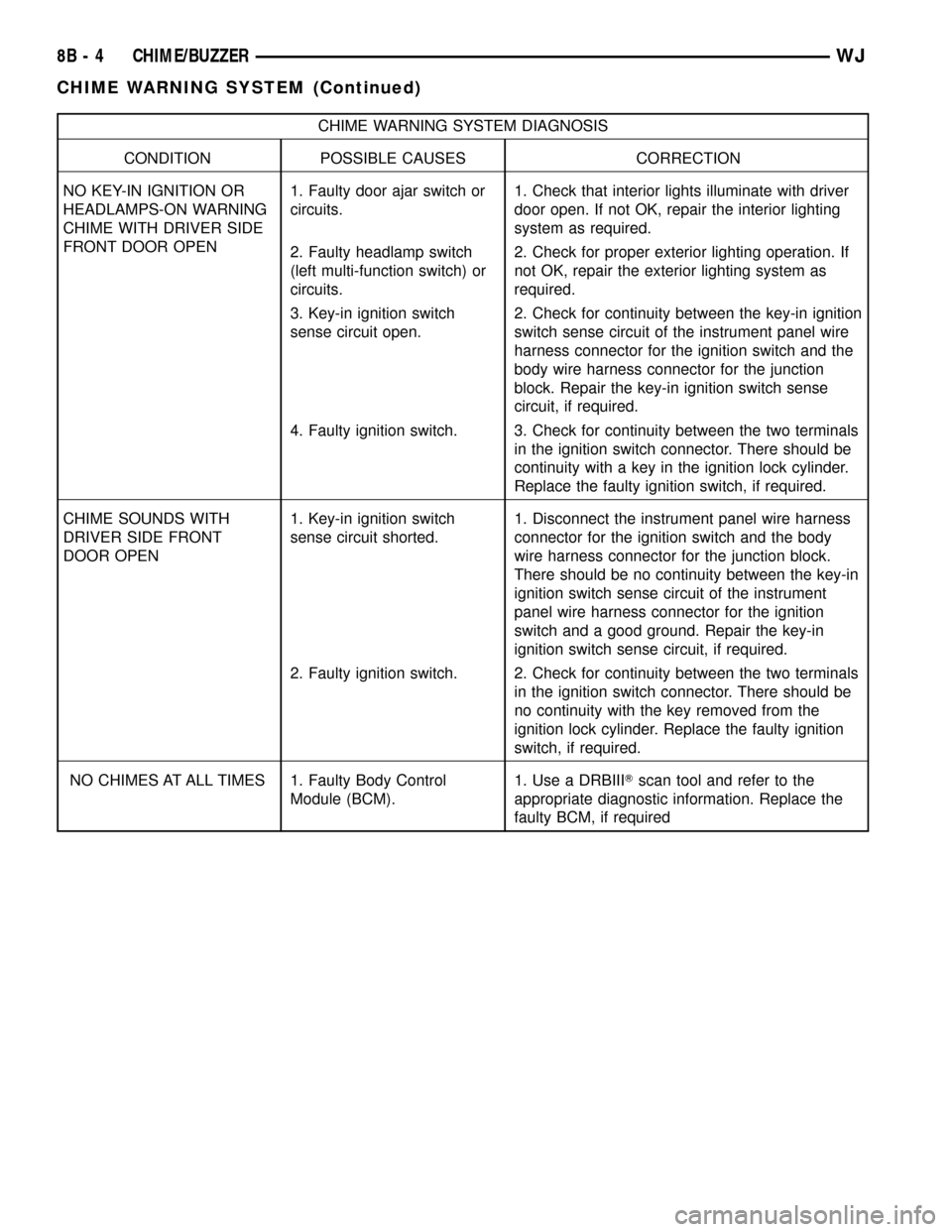
CHIME WARNING SYSTEM DIAGNOSIS
CONDITION POSSIBLE CAUSES CORRECTION
NO KEY-IN IGNITION OR
HEADLAMPS-ON WARNING
CHIME WITH DRIVER SIDE
FRONT DOOR OPEN1. Faulty door ajar switch or
circuits.1. Check that interior lights illuminate with driver
door open. If not OK, repair the interior lighting
system as required.
2. Faulty headlamp switch
(left multi-function switch) or
circuits.2. Check for proper exterior lighting operation. If
not OK, repair the exterior lighting system as
required.
3. Key-in ignition switch
sense circuit open.2. Check for continuity between the key-in ignition
switch sense circuit of the instrument panel wire
harness connector for the ignition switch and the
body wire harness connector for the junction
block. Repair the key-in ignition switch sense
circuit, if required.
4. Faulty ignition switch. 3. Check for continuity between the two terminals
in the ignition switch connector. There should be
continuity with a key in the ignition lock cylinder.
Replace the faulty ignition switch, if required.
CHIME SOUNDS WITH
DRIVER SIDE FRONT
DOOR OPEN1. Key-in ignition switch
sense circuit shorted.1. Disconnect the instrument panel wire harness
connector for the ignition switch and the body
wire harness connector for the junction block.
There should be no continuity between the key-in
ignition switch sense circuit of the instrument
panel wire harness connector for the ignition
switch and a good ground. Repair the key-in
ignition switch sense circuit, if required.
2. Faulty ignition switch. 2. Check for continuity between the two terminals
in the ignition switch connector. There should be
no continuity with the key removed from the
ignition lock cylinder. Replace the faulty ignition
switch, if required.
NO CHIMES AT ALL TIMES 1. Faulty Body Control
Module (BCM).1. Use a DRBIIITscan tool and refer to the
appropriate diagnostic information. Replace the
faulty BCM, if required
8B - 4 CHIME/BUZZERWJ
CHIME WARNING SYSTEM (Continued)
Page 314 of 2199
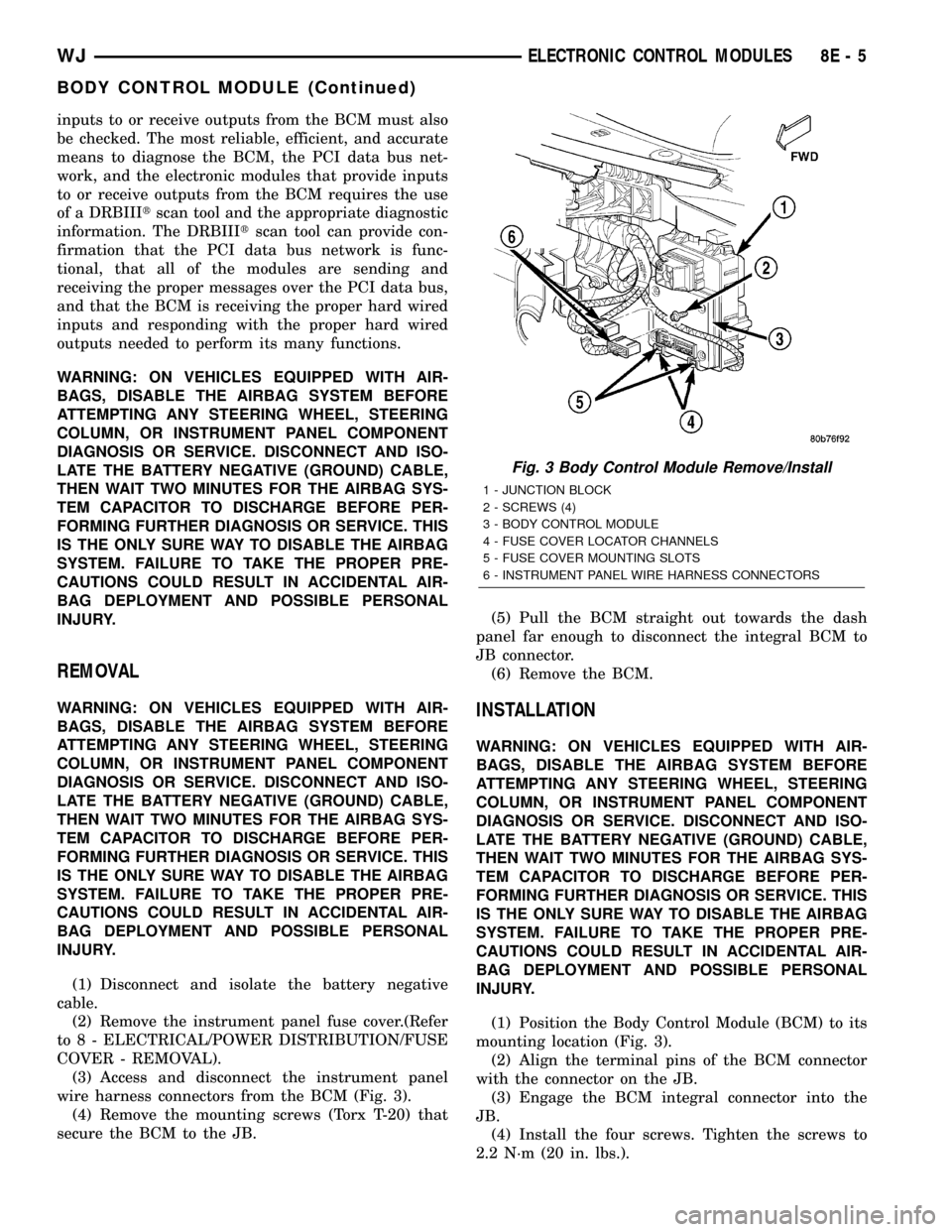
inputs to or receive outputs from the BCM must also
be checked. The most reliable, efficient, and accurate
means to diagnose the BCM, the PCI data bus net-
work, and the electronic modules that provide inputs
to or receive outputs from the BCM requires the use
of a DRBIIItscan tool and the appropriate diagnostic
information. The DRBIIItscan tool can provide con-
firmation that the PCI data bus network is func-
tional, that all of the modules are sending and
receiving the proper messages over the PCI data bus,
and that the BCM is receiving the proper hard wired
inputs and responding with the proper hard wired
outputs needed to perform its many functions.
WARNING: ON VEHICLES EQUIPPED WITH AIR-
BAGS, DISABLE THE AIRBAG SYSTEM BEFORE
ATTEMPTING ANY STEERING WHEEL, STEERING
COLUMN, OR INSTRUMENT PANEL COMPONENT
DIAGNOSIS OR SERVICE. DISCONNECT AND ISO-
LATE THE BATTERY NEGATIVE (GROUND) CABLE,
THEN WAIT TWO MINUTES FOR THE AIRBAG SYS-
TEM CAPACITOR TO DISCHARGE BEFORE PER-
FORMING FURTHER DIAGNOSIS OR SERVICE. THIS
IS THE ONLY SURE WAY TO DISABLE THE AIRBAG
SYSTEM. FAILURE TO TAKE THE PROPER PRE-
CAUTIONS COULD RESULT IN ACCIDENTAL AIR-
BAG DEPLOYMENT AND POSSIBLE PERSONAL
INJURY.
REMOVAL
WARNING: ON VEHICLES EQUIPPED WITH AIR-
BAGS, DISABLE THE AIRBAG SYSTEM BEFORE
ATTEMPTING ANY STEERING WHEEL, STEERING
COLUMN, OR INSTRUMENT PANEL COMPONENT
DIAGNOSIS OR SERVICE. DISCONNECT AND ISO-
LATE THE BATTERY NEGATIVE (GROUND) CABLE,
THEN WAIT TWO MINUTES FOR THE AIRBAG SYS-
TEM CAPACITOR TO DISCHARGE BEFORE PER-
FORMING FURTHER DIAGNOSIS OR SERVICE. THIS
IS THE ONLY SURE WAY TO DISABLE THE AIRBAG
SYSTEM. FAILURE TO TAKE THE PROPER PRE-
CAUTIONS COULD RESULT IN ACCIDENTAL AIR-
BAG DEPLOYMENT AND POSSIBLE PERSONAL
INJURY.
(1) Disconnect and isolate the battery negative
cable.
(2) Remove the instrument panel fuse cover.(Refer
to 8 - ELECTRICAL/POWER DISTRIBUTION/FUSE
COVER - REMOVAL).
(3) Access and disconnect the instrument panel
wire harness connectors from the BCM (Fig. 3).
(4) Remove the mounting screws (Torx T-20) that
secure the BCM to the JB.(5) Pull the BCM straight out towards the dash
panel far enough to disconnect the integral BCM to
JB connector.
(6) Remove the BCM.INSTALLATION
WARNING: ON VEHICLES EQUIPPED WITH AIR-
BAGS, DISABLE THE AIRBAG SYSTEM BEFORE
ATTEMPTING ANY STEERING WHEEL, STEERING
COLUMN, OR INSTRUMENT PANEL COMPONENT
DIAGNOSIS OR SERVICE. DISCONNECT AND ISO-
LATE THE BATTERY NEGATIVE (GROUND) CABLE,
THEN WAIT TWO MINUTES FOR THE AIRBAG SYS-
TEM CAPACITOR TO DISCHARGE BEFORE PER-
FORMING FURTHER DIAGNOSIS OR SERVICE. THIS
IS THE ONLY SURE WAY TO DISABLE THE AIRBAG
SYSTEM. FAILURE TO TAKE THE PROPER PRE-
CAUTIONS COULD RESULT IN ACCIDENTAL AIR-
BAG DEPLOYMENT AND POSSIBLE PERSONAL
INJURY.
(1) Position the Body Control Module (BCM) to its
mounting location (Fig. 3).
(2) Align the terminal pins of the BCM connector
with the connector on the JB.
(3) Engage the BCM integral connector into the
JB.
(4) Install the four screws. Tighten the screws to
2.2 N´m (20 in. lbs.).
Fig. 3 Body Control Module Remove/Install
1 - JUNCTION BLOCK
2 - SCREWS (4)
3 - BODY CONTROL MODULE
4 - FUSE COVER LOCATOR CHANNELS
5 - FUSE COVER MOUNTING SLOTS
6 - INSTRUMENT PANEL WIRE HARNESS CONNECTORS
WJELECTRONIC CONTROL MODULES 8E - 5
BODY CONTROL MODULE (Continued)
Page 315 of 2199
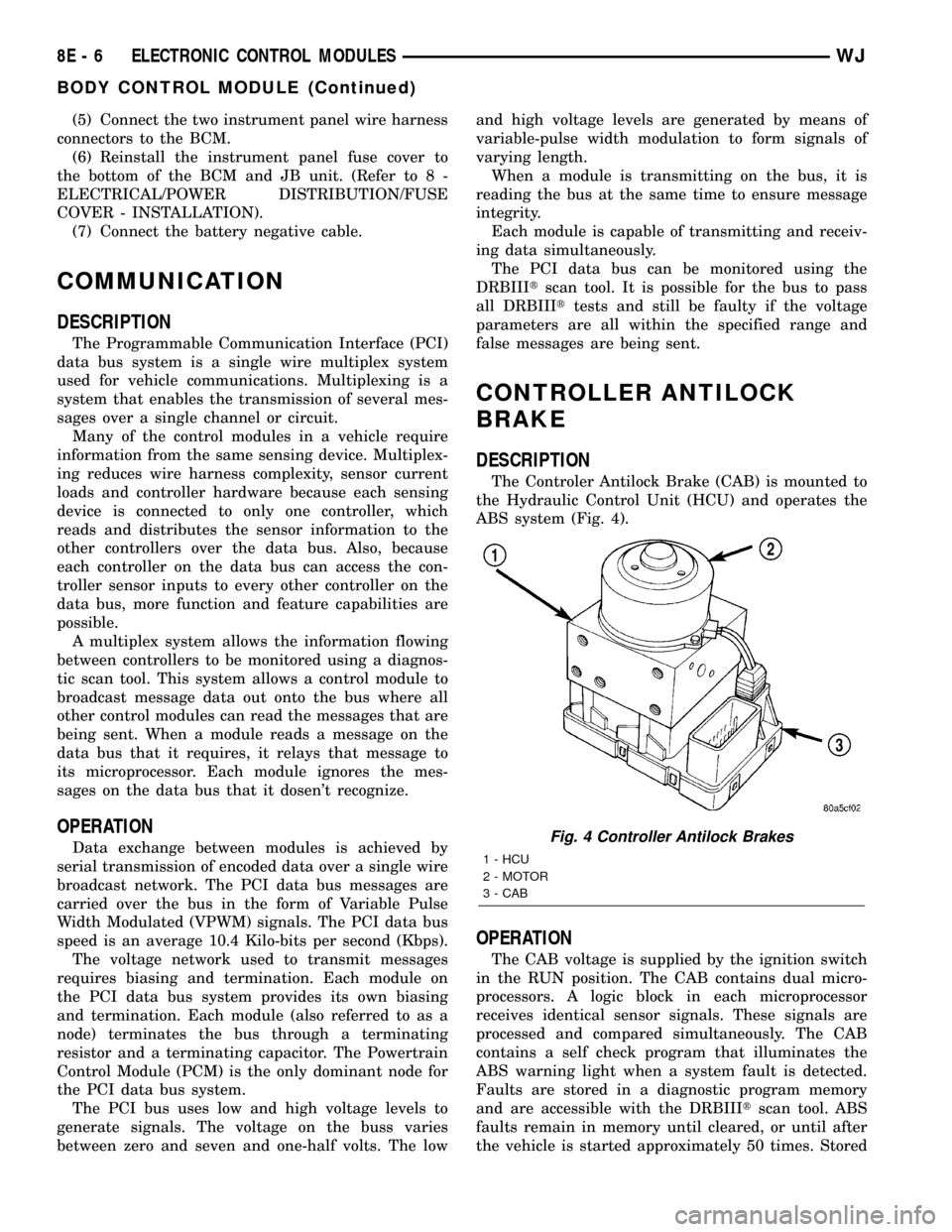
(5) Connect the two instrument panel wire harness
connectors to the BCM.
(6) Reinstall the instrument panel fuse cover to
the bottom of the BCM and JB unit. (Refer to 8 -
ELECTRICAL/POWER DISTRIBUTION/FUSE
COVER - INSTALLATION).
(7) Connect the battery negative cable.
COMMUNICATION
DESCRIPTION
The Programmable Communication Interface (PCI)
data bus system is a single wire multiplex system
used for vehicle communications. Multiplexing is a
system that enables the transmission of several mes-
sages over a single channel or circuit.
Many of the control modules in a vehicle require
information from the same sensing device. Multiplex-
ing reduces wire harness complexity, sensor current
loads and controller hardware because each sensing
device is connected to only one controller, which
reads and distributes the sensor information to the
other controllers over the data bus. Also, because
each controller on the data bus can access the con-
troller sensor inputs to every other controller on the
data bus, more function and feature capabilities are
possible.
A multiplex system allows the information flowing
between controllers to be monitored using a diagnos-
tic scan tool. This system allows a control module to
broadcast message data out onto the bus where all
other control modules can read the messages that are
being sent. When a module reads a message on the
data bus that it requires, it relays that message to
its microprocessor. Each module ignores the mes-
sages on the data bus that it dosen't recognize.
OPERATION
Data exchange between modules is achieved by
serial transmission of encoded data over a single wire
broadcast network. The PCI data bus messages are
carried over the bus in the form of Variable Pulse
Width Modulated (VPWM) signals. The PCI data bus
speed is an average 10.4 Kilo-bits per second (Kbps).
The voltage network used to transmit messages
requires biasing and termination. Each module on
the PCI data bus system provides its own biasing
and termination. Each module (also referred to as a
node) terminates the bus through a terminating
resistor and a terminating capacitor. The Powertrain
Control Module (PCM) is the only dominant node for
the PCI data bus system.
The PCI bus uses low and high voltage levels to
generate signals. The voltage on the buss varies
between zero and seven and one-half volts. The lowand high voltage levels are generated by means of
variable-pulse width modulation to form signals of
varying length.
When a module is transmitting on the bus, it is
reading the bus at the same time to ensure message
integrity.
Each module is capable of transmitting and receiv-
ing data simultaneously.
The PCI data bus can be monitored using the
DRBIIItscan tool. It is possible for the bus to pass
all DRBIIIttests and still be faulty if the voltage
parameters are all within the specified range and
false messages are being sent.
CONTROLLER ANTILOCK
BRAKE
DESCRIPTION
The Controler Antilock Brake (CAB) is mounted to
the Hydraulic Control Unit (HCU) and operates the
ABS system (Fig. 4).
OPERATION
The CAB voltage is supplied by the ignition switch
in the RUN position. The CAB contains dual micro-
processors. A logic block in each microprocessor
receives identical sensor signals. These signals are
processed and compared simultaneously. The CAB
contains a self check program that illuminates the
ABS warning light when a system fault is detected.
Faults are stored in a diagnostic program memory
and are accessible with the DRBIIItscan tool. ABS
faults remain in memory until cleared, or until after
the vehicle is started approximately 50 times. Stored
Fig. 4 Controller Antilock Brakes
1 - HCU
2 - MOTOR
3 - CAB
8E - 6 ELECTRONIC CONTROL MODULESWJ
BODY CONTROL MODULE (Continued)
Page 319 of 2199
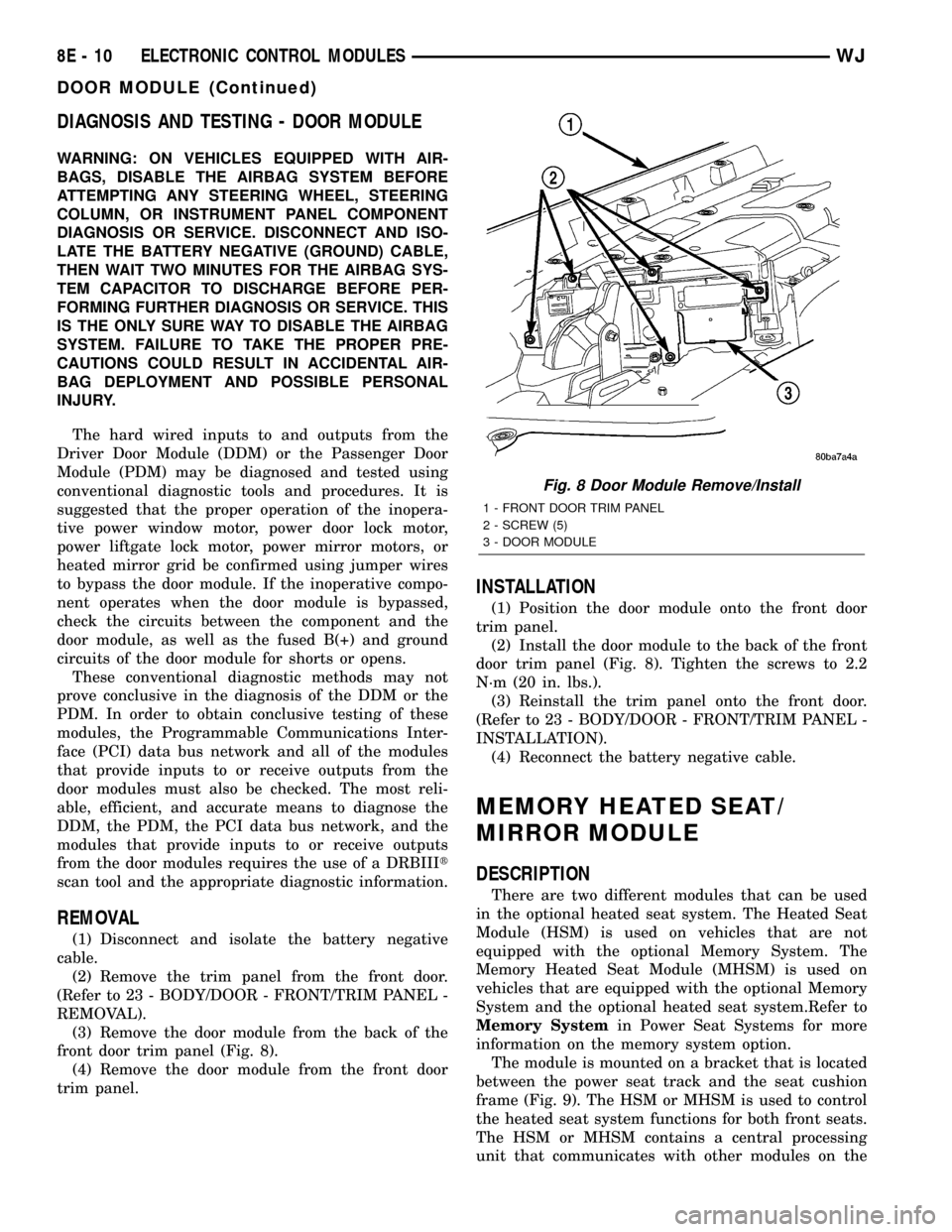
DIAGNOSIS AND TESTING - DOOR MODULE
WARNING: ON VEHICLES EQUIPPED WITH AIR-
BAGS, DISABLE THE AIRBAG SYSTEM BEFORE
ATTEMPTING ANY STEERING WHEEL, STEERING
COLUMN, OR INSTRUMENT PANEL COMPONENT
DIAGNOSIS OR SERVICE. DISCONNECT AND ISO-
LATE THE BATTERY NEGATIVE (GROUND) CABLE,
THEN WAIT TWO MINUTES FOR THE AIRBAG SYS-
TEM CAPACITOR TO DISCHARGE BEFORE PER-
FORMING FURTHER DIAGNOSIS OR SERVICE. THIS
IS THE ONLY SURE WAY TO DISABLE THE AIRBAG
SYSTEM. FAILURE TO TAKE THE PROPER PRE-
CAUTIONS COULD RESULT IN ACCIDENTAL AIR-
BAG DEPLOYMENT AND POSSIBLE PERSONAL
INJURY.
The hard wired inputs to and outputs from the
Driver Door Module (DDM) or the Passenger Door
Module (PDM) may be diagnosed and tested using
conventional diagnostic tools and procedures. It is
suggested that the proper operation of the inopera-
tive power window motor, power door lock motor,
power liftgate lock motor, power mirror motors, or
heated mirror grid be confirmed using jumper wires
to bypass the door module. If the inoperative compo-
nent operates when the door module is bypassed,
check the circuits between the component and the
door module, as well as the fused B(+) and ground
circuits of the door module for shorts or opens.
These conventional diagnostic methods may not
prove conclusive in the diagnosis of the DDM or the
PDM. In order to obtain conclusive testing of these
modules, the Programmable Communications Inter-
face (PCI) data bus network and all of the modules
that provide inputs to or receive outputs from the
door modules must also be checked. The most reli-
able, efficient, and accurate means to diagnose the
DDM, the PDM, the PCI data bus network, and the
modules that provide inputs to or receive outputs
from the door modules requires the use of a DRBIIIt
scan tool and the appropriate diagnostic information.
REMOVAL
(1) Disconnect and isolate the battery negative
cable.
(2) Remove the trim panel from the front door.
(Refer to 23 - BODY/DOOR - FRONT/TRIM PANEL -
REMOVAL).
(3) Remove the door module from the back of the
front door trim panel (Fig. 8).
(4) Remove the door module from the front door
trim panel.
INSTALLATION
(1) Position the door module onto the front door
trim panel.
(2) Install the door module to the back of the front
door trim panel (Fig. 8). Tighten the screws to 2.2
N´m (20 in. lbs.).
(3) Reinstall the trim panel onto the front door.
(Refer to 23 - BODY/DOOR - FRONT/TRIM PANEL -
INSTALLATION).
(4) Reconnect the battery negative cable.
MEMORY HEATED SEAT/
MIRROR MODULE
DESCRIPTION
There are two different modules that can be used
in the optional heated seat system. The Heated Seat
Module (HSM) is used on vehicles that are not
equipped with the optional Memory System. The
Memory Heated Seat Module (MHSM) is used on
vehicles that are equipped with the optional Memory
System and the optional heated seat system.Refer to
Memory Systemin Power Seat Systems for more
information on the memory system option.
The module is mounted on a bracket that is located
between the power seat track and the seat cushion
frame (Fig. 9). The HSM or MHSM is used to control
the heated seat system functions for both front seats.
The HSM or MHSM contains a central processing
unit that communicates with other modules on the
Fig. 8 Door Module Remove/Install
1 - FRONT DOOR TRIM PANEL
2 - SCREW (5)
3 - DOOR MODULE
8E - 10 ELECTRONIC CONTROL MODULESWJ
DOOR MODULE (Continued)
Page 321 of 2199
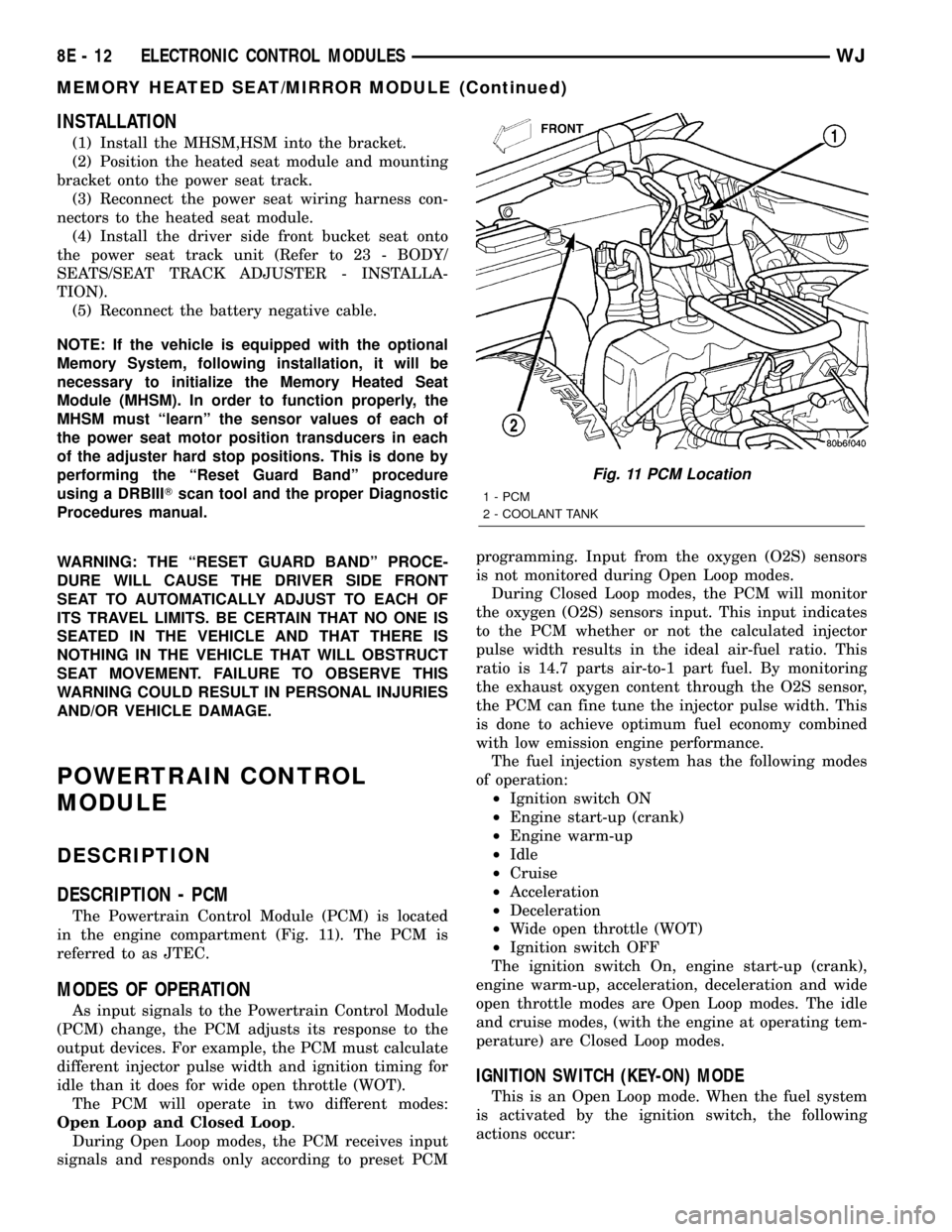
INSTALLATION
(1) Install the MHSM,HSM into the bracket.
(2) Position the heated seat module and mounting
bracket onto the power seat track.
(3) Reconnect the power seat wiring harness con-
nectors to the heated seat module.
(4) Install the driver side front bucket seat onto
the power seat track unit (Refer to 23 - BODY/
SEATS/SEAT TRACK ADJUSTER - INSTALLA-
TION).
(5) Reconnect the battery negative cable.
NOTE: If the vehicle is equipped with the optional
Memory System, following installation, it will be
necessary to initialize the Memory Heated Seat
Module (MHSM). In order to function properly, the
MHSM must ªlearnº the sensor values of each of
the power seat motor position transducers in each
of the adjuster hard stop positions. This is done by
performing the ªReset Guard Bandº procedure
using a DRBIIITscan tool and the proper Diagnostic
Procedures manual.
WARNING: THE ªRESET GUARD BANDº PROCE-
DURE WILL CAUSE THE DRIVER SIDE FRONT
SEAT TO AUTOMATICALLY ADJUST TO EACH OF
ITS TRAVEL LIMITS. BE CERTAIN THAT NO ONE IS
SEATED IN THE VEHICLE AND THAT THERE IS
NOTHING IN THE VEHICLE THAT WILL OBSTRUCT
SEAT MOVEMENT. FAILURE TO OBSERVE THIS
WARNING COULD RESULT IN PERSONAL INJURIES
AND/OR VEHICLE DAMAGE.
POWERTRAIN CONTROL
MODULE
DESCRIPTION
DESCRIPTION - PCM
The Powertrain Control Module (PCM) is located
in the engine compartment (Fig. 11). The PCM is
referred to as JTEC.
MODES OF OPERATION
As input signals to the Powertrain Control Module
(PCM) change, the PCM adjusts its response to the
output devices. For example, the PCM must calculate
different injector pulse width and ignition timing for
idle than it does for wide open throttle (WOT).
The PCM will operate in two different modes:
Open Loop and Closed Loop.
During Open Loop modes, the PCM receives input
signals and responds only according to preset PCMprogramming. Input from the oxygen (O2S) sensors
is not monitored during Open Loop modes.
During Closed Loop modes, the PCM will monitor
the oxygen (O2S) sensors input. This input indicates
to the PCM whether or not the calculated injector
pulse width results in the ideal air-fuel ratio. This
ratio is 14.7 parts air-to-1 part fuel. By monitoring
the exhaust oxygen content through the O2S sensor,
the PCM can fine tune the injector pulse width. This
is done to achieve optimum fuel economy combined
with low emission engine performance.
The fuel injection system has the following modes
of operation:
²Ignition switch ON
²Engine start-up (crank)
²Engine warm-up
²Idle
²Cruise
²Acceleration
²Deceleration
²Wide open throttle (WOT)
²Ignition switch OFF
The ignition switch On, engine start-up (crank),
engine warm-up, acceleration, deceleration and wide
open throttle modes are Open Loop modes. The idle
and cruise modes, (with the engine at operating tem-
perature) are Closed Loop modes.
IGNITION SWITCH (KEY-ON) MODE
This is an Open Loop mode. When the fuel system
is activated by the ignition switch, the following
actions occur:
Fig. 11 PCM Location
1 - PCM
2 - COOLANT TANK
8E - 12 ELECTRONIC CONTROL MODULESWJ
MEMORY HEATED SEAT/MIRROR MODULE (Continued)
Page 327 of 2199
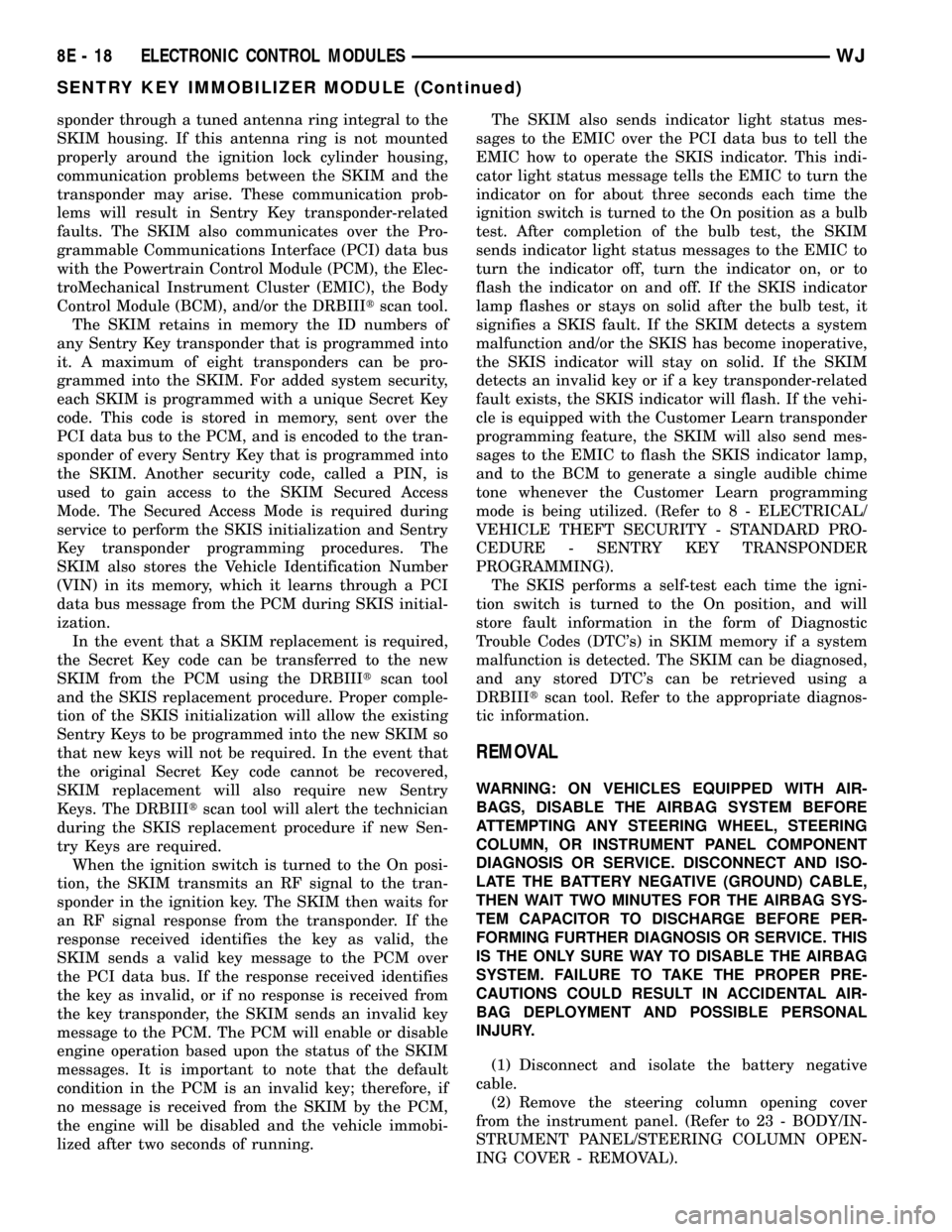
sponder through a tuned antenna ring integral to the
SKIM housing. If this antenna ring is not mounted
properly around the ignition lock cylinder housing,
communication problems between the SKIM and the
transponder may arise. These communication prob-
lems will result in Sentry Key transponder-related
faults. The SKIM also communicates over the Pro-
grammable Communications Interface (PCI) data bus
with the Powertrain Control Module (PCM), the Elec-
troMechanical Instrument Cluster (EMIC), the Body
Control Module (BCM), and/or the DRBIIItscan tool.
The SKIM retains in memory the ID numbers of
any Sentry Key transponder that is programmed into
it. A maximum of eight transponders can be pro-
grammed into the SKIM. For added system security,
each SKIM is programmed with a unique Secret Key
code. This code is stored in memory, sent over the
PCI data bus to the PCM, and is encoded to the tran-
sponder of every Sentry Key that is programmed into
the SKIM. Another security code, called a PIN, is
used to gain access to the SKIM Secured Access
Mode. The Secured Access Mode is required during
service to perform the SKIS initialization and Sentry
Key transponder programming procedures. The
SKIM also stores the Vehicle Identification Number
(VIN) in its memory, which it learns through a PCI
data bus message from the PCM during SKIS initial-
ization.
In the event that a SKIM replacement is required,
the Secret Key code can be transferred to the new
SKIM from the PCM using the DRBIIItscan tool
and the SKIS replacement procedure. Proper comple-
tion of the SKIS initialization will allow the existing
Sentry Keys to be programmed into the new SKIM so
that new keys will not be required. In the event that
the original Secret Key code cannot be recovered,
SKIM replacement will also require new Sentry
Keys. The DRBIIItscan tool will alert the technician
during the SKIS replacement procedure if new Sen-
try Keys are required.
When the ignition switch is turned to the On posi-
tion, the SKIM transmits an RF signal to the tran-
sponder in the ignition key. The SKIM then waits for
an RF signal response from the transponder. If the
response received identifies the key as valid, the
SKIM sends a valid key message to the PCM over
the PCI data bus. If the response received identifies
the key as invalid, or if no response is received from
the key transponder, the SKIM sends an invalid key
message to the PCM. The PCM will enable or disable
engine operation based upon the status of the SKIM
messages. It is important to note that the default
condition in the PCM is an invalid key; therefore, if
no message is received from the SKIM by the PCM,
the engine will be disabled and the vehicle immobi-
lized after two seconds of running.The SKIM also sends indicator light status mes-
sages to the EMIC over the PCI data bus to tell the
EMIC how to operate the SKIS indicator. This indi-
cator light status message tells the EMIC to turn the
indicator on for about three seconds each time the
ignition switch is turned to the On position as a bulb
test. After completion of the bulb test, the SKIM
sends indicator light status messages to the EMIC to
turn the indicator off, turn the indicator on, or to
flash the indicator on and off. If the SKIS indicator
lamp flashes or stays on solid after the bulb test, it
signifies a SKIS fault. If the SKIM detects a system
malfunction and/or the SKIS has become inoperative,
the SKIS indicator will stay on solid. If the SKIM
detects an invalid key or if a key transponder-related
fault exists, the SKIS indicator will flash. If the vehi-
cle is equipped with the Customer Learn transponder
programming feature, the SKIM will also send mes-
sages to the EMIC to flash the SKIS indicator lamp,
and to the BCM to generate a single audible chime
tone whenever the Customer Learn programming
mode is being utilized. (Refer to 8 - ELECTRICAL/
VEHICLE THEFT SECURITY - STANDARD PRO-
CEDURE - SENTRY KEY TRANSPONDER
PROGRAMMING).
The SKIS performs a self-test each time the igni-
tion switch is turned to the On position, and will
store fault information in the form of Diagnostic
Trouble Codes (DTC's) in SKIM memory if a system
malfunction is detected. The SKIM can be diagnosed,
and any stored DTC's can be retrieved using a
DRBIIItscan tool. Refer to the appropriate diagnos-
tic information.
REMOVAL
WARNING: ON VEHICLES EQUIPPED WITH AIR-
BAGS, DISABLE THE AIRBAG SYSTEM BEFORE
ATTEMPTING ANY STEERING WHEEL, STEERING
COLUMN, OR INSTRUMENT PANEL COMPONENT
DIAGNOSIS OR SERVICE. DISCONNECT AND ISO-
LATE THE BATTERY NEGATIVE (GROUND) CABLE,
THEN WAIT TWO MINUTES FOR THE AIRBAG SYS-
TEM CAPACITOR TO DISCHARGE BEFORE PER-
FORMING FURTHER DIAGNOSIS OR SERVICE. THIS
IS THE ONLY SURE WAY TO DISABLE THE AIRBAG
SYSTEM. FAILURE TO TAKE THE PROPER PRE-
CAUTIONS COULD RESULT IN ACCIDENTAL AIR-
BAG DEPLOYMENT AND POSSIBLE PERSONAL
INJURY.
(1) Disconnect and isolate the battery negative
cable.
(2) Remove the steering column opening cover
from the instrument panel. (Refer to 23 - BODY/IN-
STRUMENT PANEL/STEERING COLUMN OPEN-
ING COVER - REMOVAL).
8E - 18 ELECTRONIC CONTROL MODULESWJ
SENTRY KEY IMMOBILIZER MODULE (Continued)
Page 328 of 2199
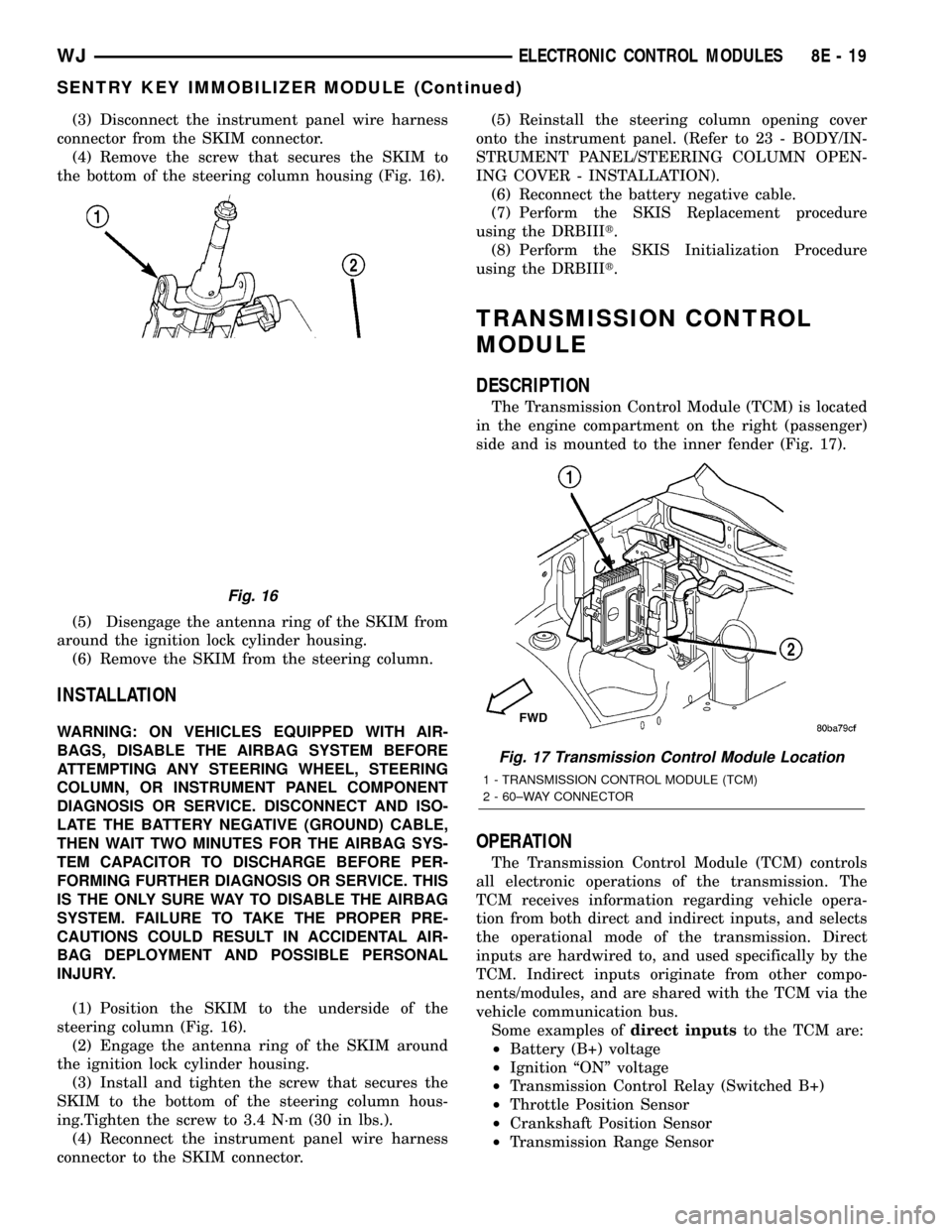
(3) Disconnect the instrument panel wire harness
connector from the SKIM connector.
(4) Remove the screw that secures the SKIM to
the bottom of the steering column housing (Fig. 16).
(5) Disengage the antenna ring of the SKIM from
around the ignition lock cylinder housing.
(6) Remove the SKIM from the steering column.
INSTALLATION
WARNING: ON VEHICLES EQUIPPED WITH AIR-
BAGS, DISABLE THE AIRBAG SYSTEM BEFORE
ATTEMPTING ANY STEERING WHEEL, STEERING
COLUMN, OR INSTRUMENT PANEL COMPONENT
DIAGNOSIS OR SERVICE. DISCONNECT AND ISO-
LATE THE BATTERY NEGATIVE (GROUND) CABLE,
THEN WAIT TWO MINUTES FOR THE AIRBAG SYS-
TEM CAPACITOR TO DISCHARGE BEFORE PER-
FORMING FURTHER DIAGNOSIS OR SERVICE. THIS
IS THE ONLY SURE WAY TO DISABLE THE AIRBAG
SYSTEM. FAILURE TO TAKE THE PROPER PRE-
CAUTIONS COULD RESULT IN ACCIDENTAL AIR-
BAG DEPLOYMENT AND POSSIBLE PERSONAL
INJURY.
(1) Position the SKIM to the underside of the
steering column (Fig. 16).
(2) Engage the antenna ring of the SKIM around
the ignition lock cylinder housing.
(3) Install and tighten the screw that secures the
SKIM to the bottom of the steering column hous-
ing.Tighten the screw to 3.4 N´m (30 in lbs.).
(4) Reconnect the instrument panel wire harness
connector to the SKIM connector.(5) Reinstall the steering column opening cover
onto the instrument panel. (Refer to 23 - BODY/IN-
STRUMENT PANEL/STEERING COLUMN OPEN-
ING COVER - INSTALLATION).
(6) Reconnect the battery negative cable.
(7) Perform the SKIS Replacement procedure
using the DRBIIIt.
(8) Perform the SKIS Initialization Procedure
using the DRBIIIt.
TRANSMISSION CONTROL
MODULE
DESCRIPTION
The Transmission Control Module (TCM) is located
in the engine compartment on the right (passenger)
side and is mounted to the inner fender (Fig. 17).
OPERATION
The Transmission Control Module (TCM) controls
all electronic operations of the transmission. The
TCM receives information regarding vehicle opera-
tion from both direct and indirect inputs, and selects
the operational mode of the transmission. Direct
inputs are hardwired to, and used specifically by the
TCM. Indirect inputs originate from other compo-
nents/modules, and are shared with the TCM via the
vehicle communication bus.
Some examples ofdirect inputsto the TCM are:
²Battery (B+) voltage
²Ignition ªONº voltage
²Transmission Control Relay (Switched B+)
²Throttle Position Sensor
²Crankshaft Position Sensor
²Transmission Range Sensor
Fig. 16
Fig. 17 Transmission Control Module Location
1 - TRANSMISSION CONTROL MODULE (TCM)
2 - 60±WAY CONNECTOR
WJELECTRONIC CONTROL MODULES 8E - 19
SENTRY KEY IMMOBILIZER MODULE (Continued)
Page 339 of 2199
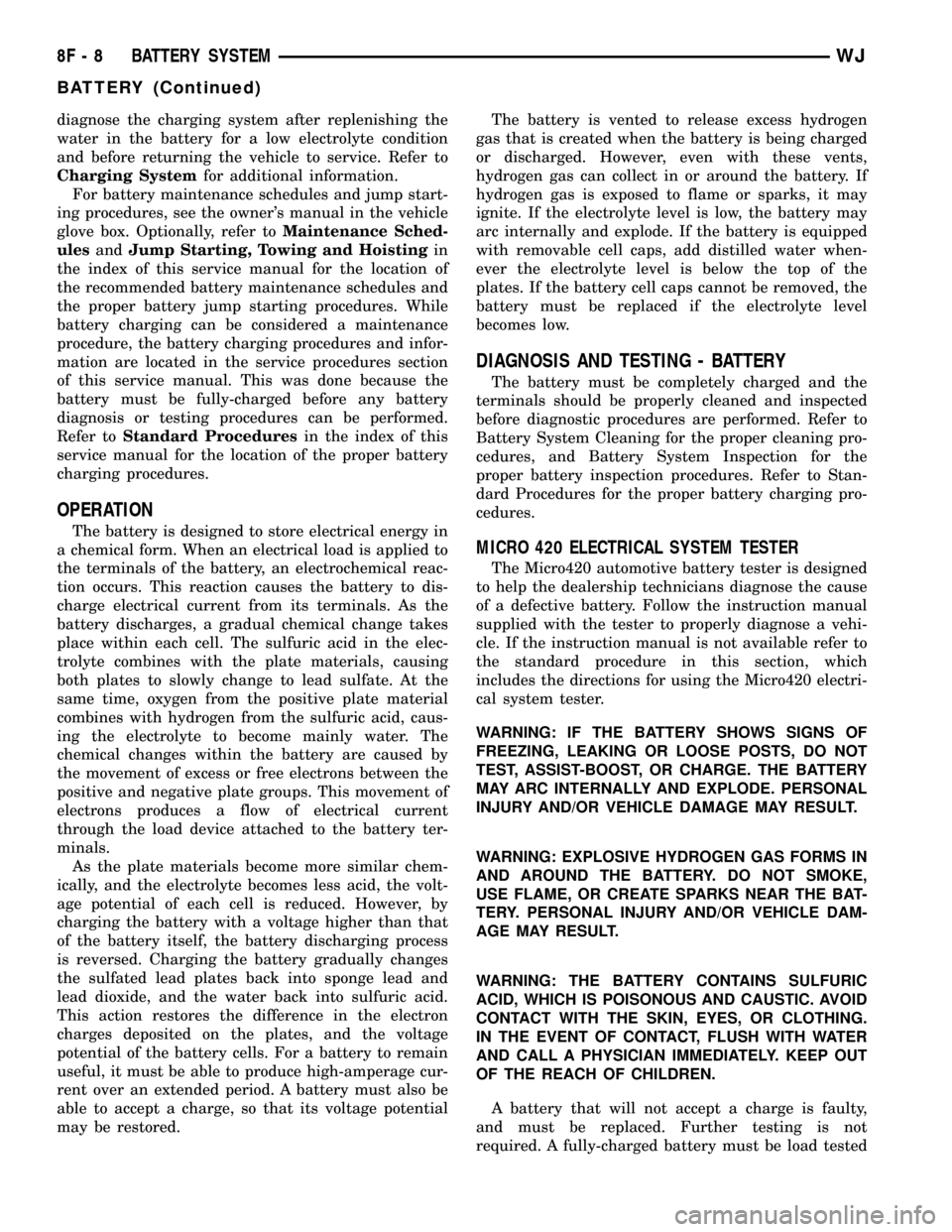
diagnose the charging system after replenishing the
water in the battery for a low electrolyte condition
and before returning the vehicle to service. Refer to
Charging Systemfor additional information.
For battery maintenance schedules and jump start-
ing procedures, see the owner's manual in the vehicle
glove box. Optionally, refer toMaintenance Sched-
ulesandJump Starting, Towing and Hoistingin
the index of this service manual for the location of
the recommended battery maintenance schedules and
the proper battery jump starting procedures. While
battery charging can be considered a maintenance
procedure, the battery charging procedures and infor-
mation are located in the service procedures section
of this service manual. This was done because the
battery must be fully-charged before any battery
diagnosis or testing procedures can be performed.
Refer toStandard Proceduresin the index of this
service manual for the location of the proper battery
charging procedures.
OPERATION
The battery is designed to store electrical energy in
a chemical form. When an electrical load is applied to
the terminals of the battery, an electrochemical reac-
tion occurs. This reaction causes the battery to dis-
charge electrical current from its terminals. As the
battery discharges, a gradual chemical change takes
place within each cell. The sulfuric acid in the elec-
trolyte combines with the plate materials, causing
both plates to slowly change to lead sulfate. At the
same time, oxygen from the positive plate material
combines with hydrogen from the sulfuric acid, caus-
ing the electrolyte to become mainly water. The
chemical changes within the battery are caused by
the movement of excess or free electrons between the
positive and negative plate groups. This movement of
electrons produces a flow of electrical current
through the load device attached to the battery ter-
minals.
As the plate materials become more similar chem-
ically, and the electrolyte becomes less acid, the volt-
age potential of each cell is reduced. However, by
charging the battery with a voltage higher than that
of the battery itself, the battery discharging process
is reversed. Charging the battery gradually changes
the sulfated lead plates back into sponge lead and
lead dioxide, and the water back into sulfuric acid.
This action restores the difference in the electron
charges deposited on the plates, and the voltage
potential of the battery cells. For a battery to remain
useful, it must be able to produce high-amperage cur-
rent over an extended period. A battery must also be
able to accept a charge, so that its voltage potential
may be restored.The battery is vented to release excess hydrogen
gas that is created when the battery is being charged
or discharged. However, even with these vents,
hydrogen gas can collect in or around the battery. If
hydrogen gas is exposed to flame or sparks, it may
ignite. If the electrolyte level is low, the battery may
arc internally and explode. If the battery is equipped
with removable cell caps, add distilled water when-
ever the electrolyte level is below the top of the
plates. If the battery cell caps cannot be removed, the
battery must be replaced if the electrolyte level
becomes low.
DIAGNOSIS AND TESTING - BATTERY
The battery must be completely charged and the
terminals should be properly cleaned and inspected
before diagnostic procedures are performed. Refer to
Battery System Cleaning for the proper cleaning pro-
cedures, and Battery System Inspection for the
proper battery inspection procedures. Refer to Stan-
dard Procedures for the proper battery charging pro-
cedures.
MICRO 420 ELECTRICAL SYSTEM TESTER
The Micro420 automotive battery tester is designed
to help the dealership technicians diagnose the cause
of a defective battery. Follow the instruction manual
supplied with the tester to properly diagnose a vehi-
cle. If the instruction manual is not available refer to
the standard procedure in this section, which
includes the directions for using the Micro420 electri-
cal system tester.
WARNING: IF THE BATTERY SHOWS SIGNS OF
FREEZING, LEAKING OR LOOSE POSTS, DO NOT
TEST, ASSIST-BOOST, OR CHARGE. THE BATTERY
MAY ARC INTERNALLY AND EXPLODE. PERSONAL
INJURY AND/OR VEHICLE DAMAGE MAY RESULT.
WARNING: EXPLOSIVE HYDROGEN GAS FORMS IN
AND AROUND THE BATTERY. DO NOT SMOKE,
USE FLAME, OR CREATE SPARKS NEAR THE BAT-
TERY. PERSONAL INJURY AND/OR VEHICLE DAM-
AGE MAY RESULT.
WARNING: THE BATTERY CONTAINS SULFURIC
ACID, WHICH IS POISONOUS AND CAUSTIC. AVOID
CONTACT WITH THE SKIN, EYES, OR CLOTHING.
IN THE EVENT OF CONTACT, FLUSH WITH WATER
AND CALL A PHYSICIAN IMMEDIATELY. KEEP OUT
OF THE REACH OF CHILDREN.
A battery that will not accept a charge is faulty,
and must be replaced. Further testing is not
required. A fully-charged battery must be load tested
8F - 8 BATTERY SYSTEMWJ
BATTERY (Continued)