sensor JEEP GRAND CHEROKEE 2002 WJ / 2.G Repair Manual
[x] Cancel search | Manufacturer: JEEP, Model Year: 2002, Model line: GRAND CHEROKEE, Model: JEEP GRAND CHEROKEE 2002 WJ / 2.GPages: 2199, PDF Size: 76.01 MB
Page 383 of 2199
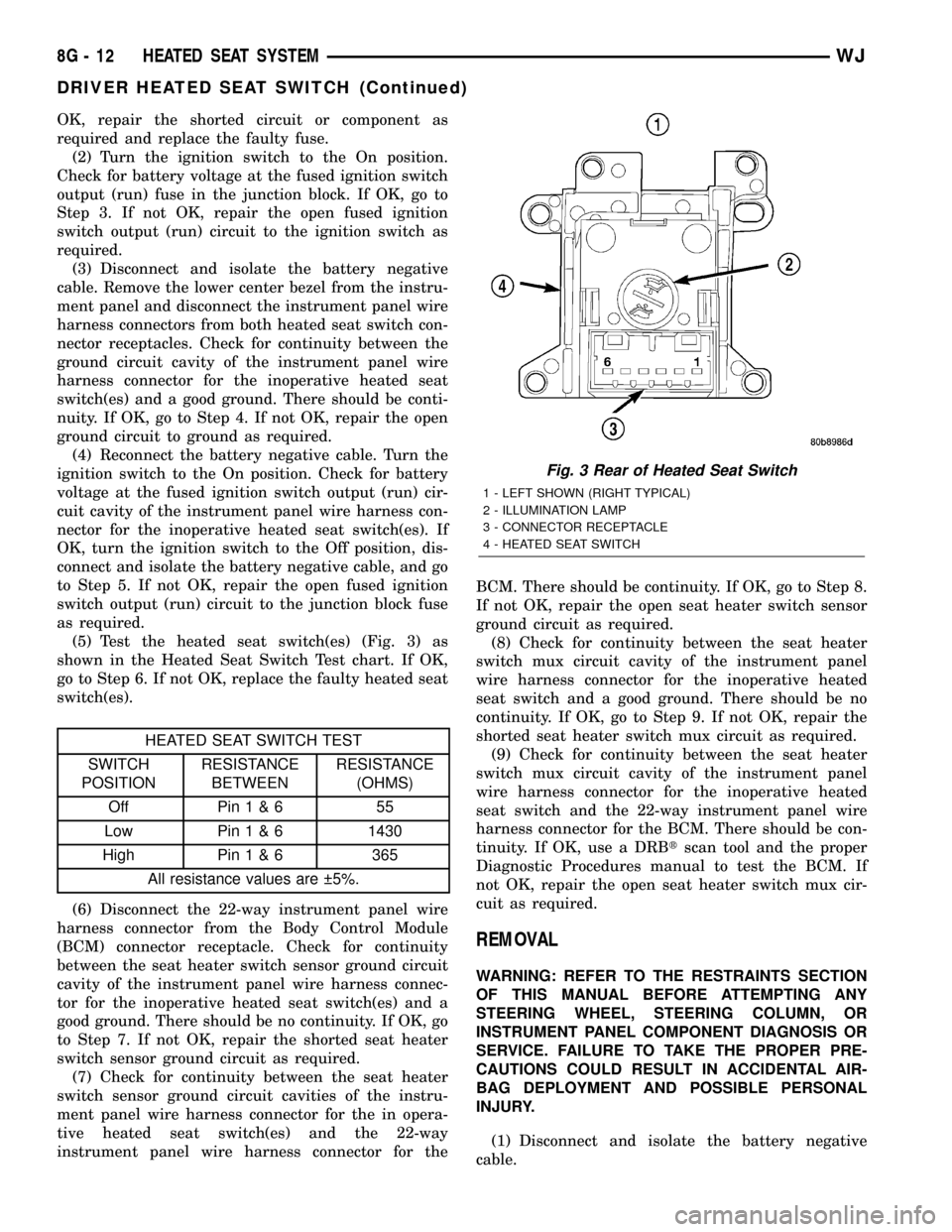
OK, repair the shorted circuit or component as
required and replace the faulty fuse.
(2) Turn the ignition switch to the On position.
Check for battery voltage at the fused ignition switch
output (run) fuse in the junction block. If OK, go to
Step 3. If not OK, repair the open fused ignition
switch output (run) circuit to the ignition switch as
required.
(3) Disconnect and isolate the battery negative
cable. Remove the lower center bezel from the instru-
ment panel and disconnect the instrument panel wire
harness connectors from both heated seat switch con-
nector receptacles. Check for continuity between the
ground circuit cavity of the instrument panel wire
harness connector for the inoperative heated seat
switch(es) and a good ground. There should be conti-
nuity. If OK, go to Step 4. If not OK, repair the open
ground circuit to ground as required.
(4) Reconnect the battery negative cable. Turn the
ignition switch to the On position. Check for battery
voltage at the fused ignition switch output (run) cir-
cuit cavity of the instrument panel wire harness con-
nector for the inoperative heated seat switch(es). If
OK, turn the ignition switch to the Off position, dis-
connect and isolate the battery negative cable, and go
to Step 5. If not OK, repair the open fused ignition
switch output (run) circuit to the junction block fuse
as required.
(5) Test the heated seat switch(es) (Fig. 3) as
shown in the Heated Seat Switch Test chart. If OK,
go to Step 6. If not OK, replace the faulty heated seat
switch(es).
HEATED SEAT SWITCH TEST
SWITCH
POSITIONRESISTANCE
BETWEENRESISTANCE
(OHMS)
Off Pin1&6 55
Low Pin1&61430
High Pin1&6 365
All resistance values are 5%.
(6) Disconnect the 22-way instrument panel wire
harness connector from the Body Control Module
(BCM) connector receptacle. Check for continuity
between the seat heater switch sensor ground circuit
cavity of the instrument panel wire harness connec-
tor for the inoperative heated seat switch(es) and a
good ground. There should be no continuity. If OK, go
to Step 7. If not OK, repair the shorted seat heater
switch sensor ground circuit as required.
(7) Check for continuity between the seat heater
switch sensor ground circuit cavities of the instru-
ment panel wire harness connector for the in opera-
tive heated seat switch(es) and the 22-way
instrument panel wire harness connector for theBCM. There should be continuity. If OK, go to Step 8.
If not OK, repair the open seat heater switch sensor
ground circuit as required.
(8) Check for continuity between the seat heater
switch mux circuit cavity of the instrument panel
wire harness connector for the inoperative heated
seat switch and a good ground. There should be no
continuity. If OK, go to Step 9. If not OK, repair the
shorted seat heater switch mux circuit as required.
(9) Check for continuity between the seat heater
switch mux circuit cavity of the instrument panel
wire harness connector for the inoperative heated
seat switch and the 22-way instrument panel wire
harness connector for the BCM. There should be con-
tinuity. If OK, use a DRBtscan tool and the proper
Diagnostic Procedures manual to test the BCM. If
not OK, repair the open seat heater switch mux cir-
cuit as required.
REMOVAL
WARNING: REFER TO THE RESTRAINTS SECTION
OF THIS MANUAL BEFORE ATTEMPTING ANY
STEERING WHEEL, STEERING COLUMN, OR
INSTRUMENT PANEL COMPONENT DIAGNOSIS OR
SERVICE. FAILURE TO TAKE THE PROPER PRE-
CAUTIONS COULD RESULT IN ACCIDENTAL AIR-
BAG DEPLOYMENT AND POSSIBLE PERSONAL
INJURY.
(1) Disconnect and isolate the battery negative
cable.
Fig. 3 Rear of Heated Seat Switch
1 - LEFT SHOWN (RIGHT TYPICAL)
2 - ILLUMINATION LAMP
3 - CONNECTOR RECEPTACLE
4 - HEATED SEAT SWITCH
8G - 12 HEATED SEAT SYSTEMWJ
DRIVER HEATED SEAT SWITCH (Continued)
Page 384 of 2199
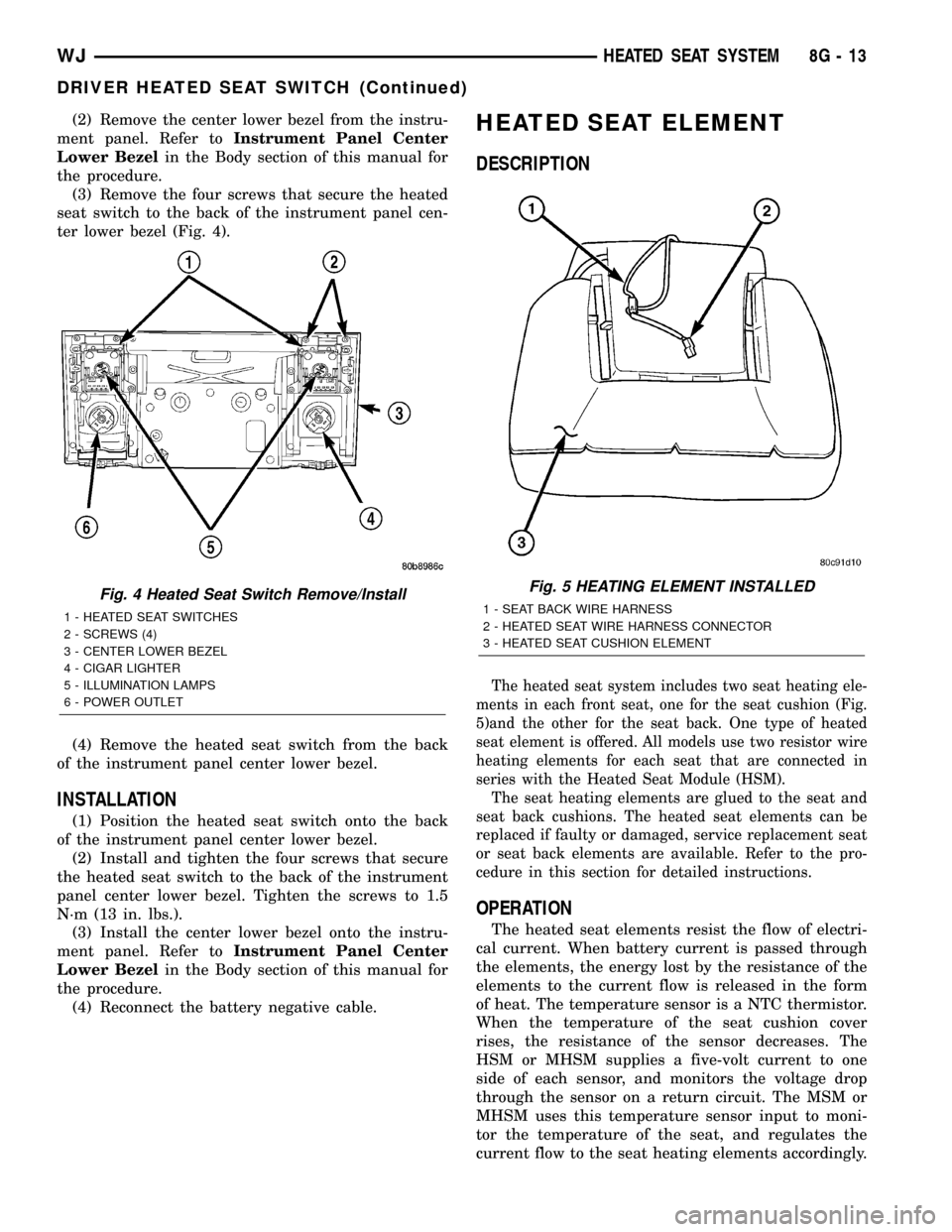
(2) Remove the center lower bezel from the instru-
ment panel. Refer toInstrument Panel Center
Lower Bezelin the Body section of this manual for
the procedure.
(3) Remove the four screws that secure the heated
seat switch to the back of the instrument panel cen-
ter lower bezel (Fig. 4).
(4) Remove the heated seat switch from the back
of the instrument panel center lower bezel.
INSTALLATION
(1) Position the heated seat switch onto the back
of the instrument panel center lower bezel.
(2) Install and tighten the four screws that secure
the heated seat switch to the back of the instrument
panel center lower bezel. Tighten the screws to 1.5
N´m (13 in. lbs.).
(3) Install the center lower bezel onto the instru-
ment panel. Refer toInstrument Panel Center
Lower Bezelin the Body section of this manual for
the procedure.
(4) Reconnect the battery negative cable.
HEATED SEAT ELEMENT
DESCRIPTION
The heated seat system includes two seat heating ele-
ments in each front seat, one for the seat cushion (Fig.
5)and the other for the seat back. One type of heated
seat element is offered. All models use two resistor wire
heating elements for each seat that are connected in
series with the Heated Seat Module (HSM).
The seat heating elements are glued to the seat and
seat back cushions. The heated seat elements can be
replaced if faulty or damaged, service replacement seat
or seat back elements are available. Refer to the pro-
cedure in this section for detailed instructions.
OPERATION
The heated seat elements resist the flow of electri-
cal current. When battery current is passed through
the elements, the energy lost by the resistance of the
elements to the current flow is released in the form
of heat. The temperature sensor is a NTC thermistor.
When the temperature of the seat cushion cover
rises, the resistance of the sensor decreases. The
HSM or MHSM supplies a five-volt current to one
side of each sensor, and monitors the voltage drop
through the sensor on a return circuit. The MSM or
MHSM uses this temperature sensor input to moni-
tor the temperature of the seat, and regulates the
current flow to the seat heating elements accordingly.
Fig. 4 Heated Seat Switch Remove/Install
1 - HEATED SEAT SWITCHES
2 - SCREWS (4)
3 - CENTER LOWER BEZEL
4 - CIGAR LIGHTER
5 - ILLUMINATION LAMPS
6 - POWER OUTLET
Fig. 5 HEATING ELEMENT INSTALLED
1 - SEAT BACK WIRE HARNESS
2 - HEATED SEAT WIRE HARNESS CONNECTOR
3 - HEATED SEAT CUSHION ELEMENT
WJHEATED SEAT SYSTEM 8G - 13
DRIVER HEATED SEAT SWITCH (Continued)
Page 386 of 2199
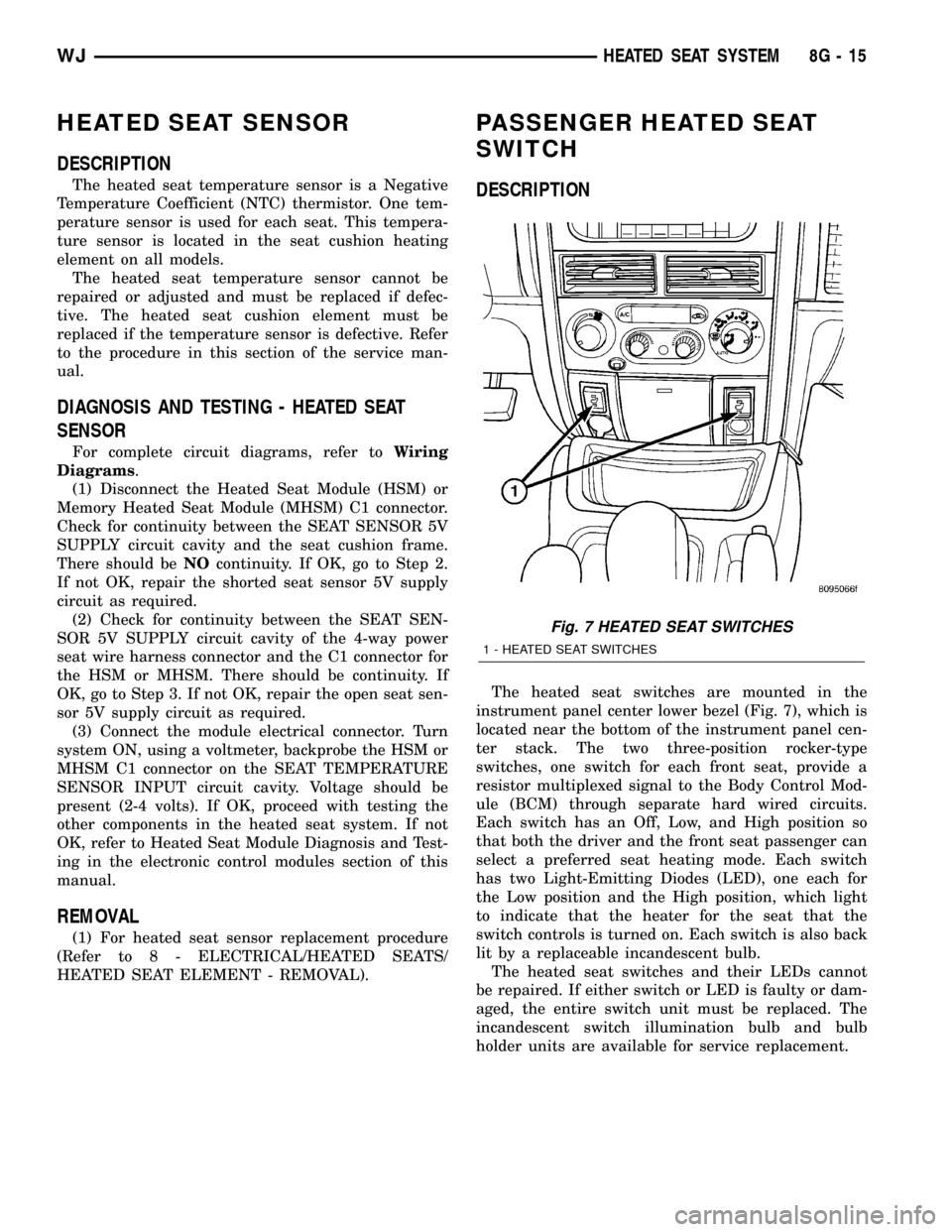
HEATED SEAT SENSOR
DESCRIPTION
The heated seat temperature sensor is a Negative
Temperature Coefficient (NTC) thermistor. One tem-
perature sensor is used for each seat. This tempera-
ture sensor is located in the seat cushion heating
element on all models.
The heated seat temperature sensor cannot be
repaired or adjusted and must be replaced if defec-
tive. The heated seat cushion element must be
replaced if the temperature sensor is defective. Refer
to the procedure in this section of the service man-
ual.
DIAGNOSIS AND TESTING - HEATED SEAT
SENSOR
For complete circuit diagrams, refer toWiring
Diagrams.
(1) Disconnect the Heated Seat Module (HSM) or
Memory Heated Seat Module (MHSM) C1 connector.
Check for continuity between the SEAT SENSOR 5V
SUPPLY circuit cavity and the seat cushion frame.
There should beNOcontinuity. If OK, go to Step 2.
If not OK, repair the shorted seat sensor 5V supply
circuit as required.
(2) Check for continuity between the SEAT SEN-
SOR 5V SUPPLY circuit cavity of the 4-way power
seat wire harness connector and the C1 connector for
the HSM or MHSM. There should be continuity. If
OK, go to Step 3. If not OK, repair the open seat sen-
sor 5V supply circuit as required.
(3) Connect the module electrical connector. Turn
system ON, using a voltmeter, backprobe the HSM or
MHSM C1 connector on the SEAT TEMPERATURE
SENSOR INPUT circuit cavity. Voltage should be
present (2-4 volts). If OK, proceed with testing the
other components in the heated seat system. If not
OK, refer to Heated Seat Module Diagnosis and Test-
ing in the electronic control modules section of this
manual.
REMOVAL
(1) For heated seat sensor replacement procedure
(Refer to 8 - ELECTRICAL/HEATED SEATS/
HEATED SEAT ELEMENT - REMOVAL).
PASSENGER HEATED SEAT
SWITCH
DESCRIPTION
The heated seat switches are mounted in the
instrument panel center lower bezel (Fig. 7), which is
located near the bottom of the instrument panel cen-
ter stack. The two three-position rocker-type
switches, one switch for each front seat, provide a
resistor multiplexed signal to the Body Control Mod-
ule (BCM) through separate hard wired circuits.
Each switch has an Off, Low, and High position so
that both the driver and the front seat passenger can
select a preferred seat heating mode. Each switch
has two Light-Emitting Diodes (LED), one each for
the Low position and the High position, which light
to indicate that the heater for the seat that the
switch controls is turned on. Each switch is also back
lit by a replaceable incandescent bulb.
The heated seat switches and their LEDs cannot
be repaired. If either switch or LED is faulty or dam-
aged, the entire switch unit must be replaced. The
incandescent switch illumination bulb and bulb
holder units are available for service replacement.
Fig. 7 HEATED SEAT SWITCHES
1 - HEATED SEAT SWITCHES
WJHEATED SEAT SYSTEM 8G - 15
Page 388 of 2199
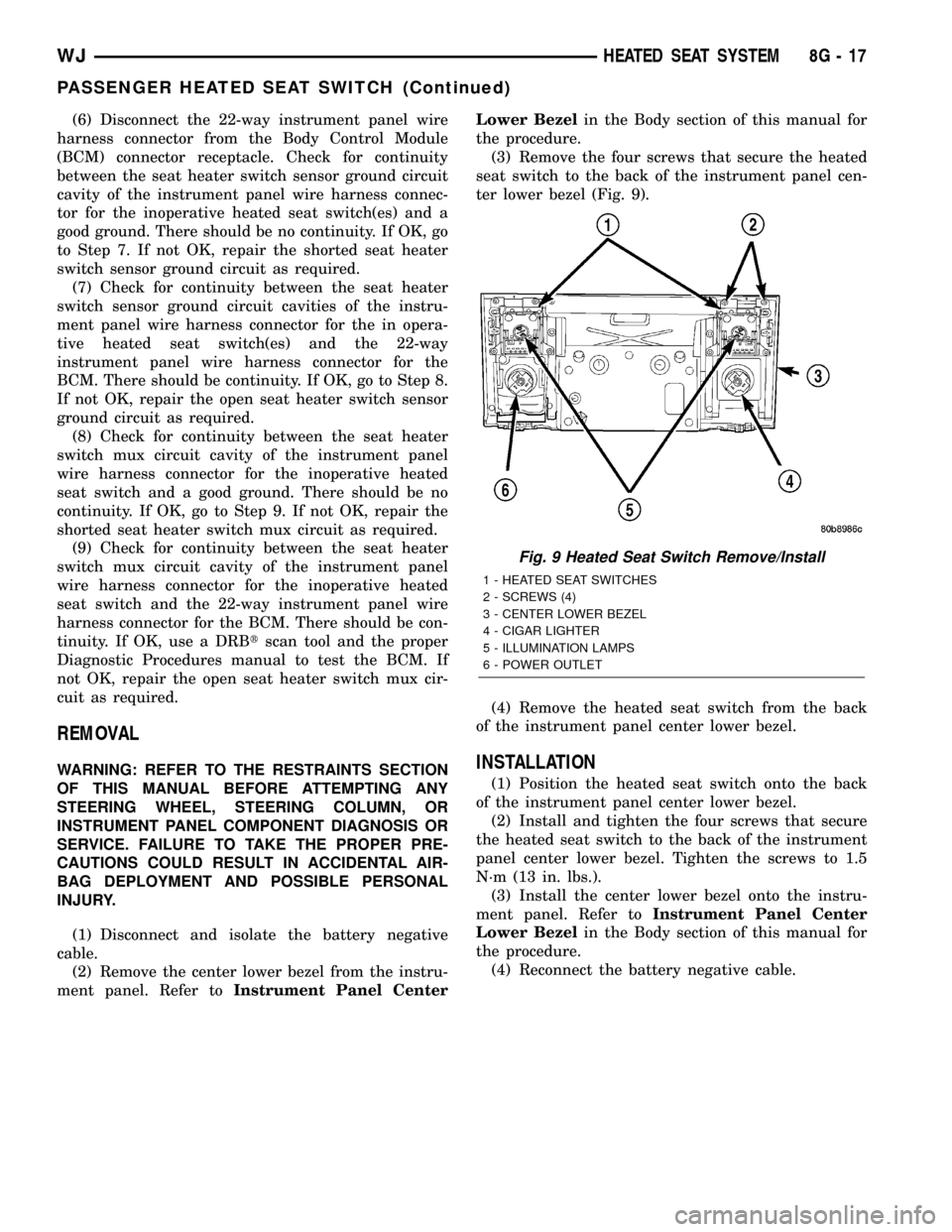
(6) Disconnect the 22-way instrument panel wire
harness connector from the Body Control Module
(BCM) connector receptacle. Check for continuity
between the seat heater switch sensor ground circuit
cavity of the instrument panel wire harness connec-
tor for the inoperative heated seat switch(es) and a
good ground. There should be no continuity. If OK, go
to Step 7. If not OK, repair the shorted seat heater
switch sensor ground circuit as required.
(7) Check for continuity between the seat heater
switch sensor ground circuit cavities of the instru-
ment panel wire harness connector for the in opera-
tive heated seat switch(es) and the 22-way
instrument panel wire harness connector for the
BCM. There should be continuity. If OK, go to Step 8.
If not OK, repair the open seat heater switch sensor
ground circuit as required.
(8) Check for continuity between the seat heater
switch mux circuit cavity of the instrument panel
wire harness connector for the inoperative heated
seat switch and a good ground. There should be no
continuity. If OK, go to Step 9. If not OK, repair the
shorted seat heater switch mux circuit as required.
(9) Check for continuity between the seat heater
switch mux circuit cavity of the instrument panel
wire harness connector for the inoperative heated
seat switch and the 22-way instrument panel wire
harness connector for the BCM. There should be con-
tinuity. If OK, use a DRBtscan tool and the proper
Diagnostic Procedures manual to test the BCM. If
not OK, repair the open seat heater switch mux cir-
cuit as required.
REMOVAL
WARNING: REFER TO THE RESTRAINTS SECTION
OF THIS MANUAL BEFORE ATTEMPTING ANY
STEERING WHEEL, STEERING COLUMN, OR
INSTRUMENT PANEL COMPONENT DIAGNOSIS OR
SERVICE. FAILURE TO TAKE THE PROPER PRE-
CAUTIONS COULD RESULT IN ACCIDENTAL AIR-
BAG DEPLOYMENT AND POSSIBLE PERSONAL
INJURY.
(1) Disconnect and isolate the battery negative
cable.
(2) Remove the center lower bezel from the instru-
ment panel. Refer toInstrument Panel CenterLower Bezelin the Body section of this manual for
the procedure.
(3) Remove the four screws that secure the heated
seat switch to the back of the instrument panel cen-
ter lower bezel (Fig. 9).
(4) Remove the heated seat switch from the back
of the instrument panel center lower bezel.INSTALLATION
(1) Position the heated seat switch onto the back
of the instrument panel center lower bezel.
(2) Install and tighten the four screws that secure
the heated seat switch to the back of the instrument
panel center lower bezel. Tighten the screws to 1.5
N´m (13 in. lbs.).
(3) Install the center lower bezel onto the instru-
ment panel. Refer toInstrument Panel Center
Lower Bezelin the Body section of this manual for
the procedure.
(4) Reconnect the battery negative cable.
Fig. 9 Heated Seat Switch Remove/Install
1 - HEATED SEAT SWITCHES
2 - SCREWS (4)
3 - CENTER LOWER BEZEL
4 - CIGAR LIGHTER
5 - ILLUMINATION LAMPS
6 - POWER OUTLET
WJHEATED SEAT SYSTEM 8G - 17
PASSENGER HEATED SEAT SWITCH (Continued)
Page 390 of 2199
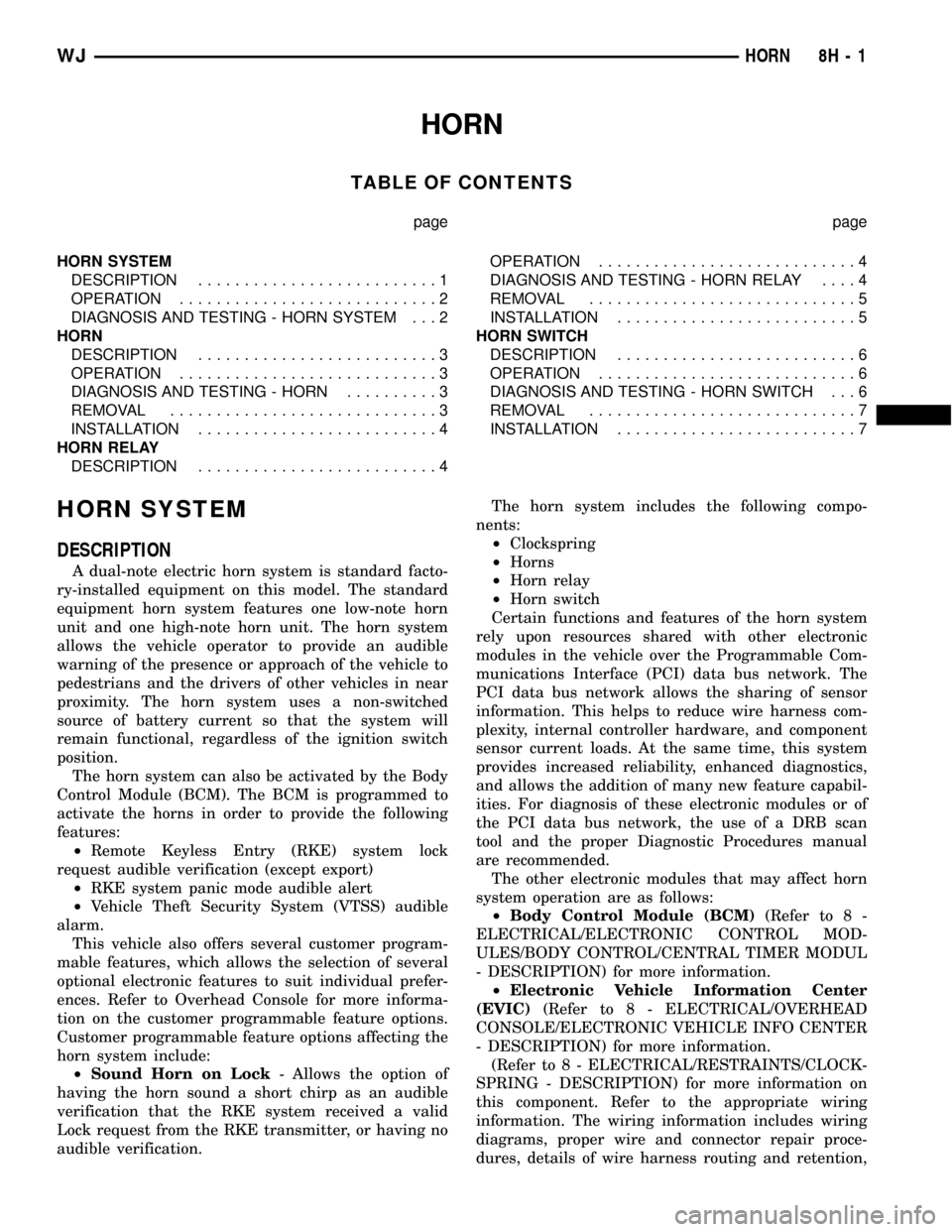
HORN
TABLE OF CONTENTS
page page
HORN SYSTEM
DESCRIPTION..........................1
OPERATION............................2
DIAGNOSIS AND TESTING - HORN SYSTEM . . . 2
HORN
DESCRIPTION..........................3
OPERATION............................3
DIAGNOSIS AND TESTING - HORN..........3
REMOVAL.............................3
INSTALLATION..........................4
HORN RELAY
DESCRIPTION..........................4OPERATION............................4
DIAGNOSIS AND TESTING - HORN RELAY....4
REMOVAL.............................5
INSTALLATION..........................5
HORN SWITCH
DESCRIPTION..........................6
OPERATION............................6
DIAGNOSIS AND TESTING - HORN SWITCH . . . 6
REMOVAL.............................7
INSTALLATION..........................7
HORN SYSTEM
DESCRIPTION
A dual-note electric horn system is standard facto-
ry-installed equipment on this model. The standard
equipment horn system features one low-note horn
unit and one high-note horn unit. The horn system
allows the vehicle operator to provide an audible
warning of the presence or approach of the vehicle to
pedestrians and the drivers of other vehicles in near
proximity. The horn system uses a non-switched
source of battery current so that the system will
remain functional, regardless of the ignition switch
position.
The horn system can also be activated by the Body
Control Module (BCM). The BCM is programmed to
activate the horns in order to provide the following
features:
²Remote Keyless Entry (RKE) system lock
request audible verification (except export)
²RKE system panic mode audible alert
²Vehicle Theft Security System (VTSS) audible
alarm.
This vehicle also offers several customer program-
mable features, which allows the selection of several
optional electronic features to suit individual prefer-
ences. Refer to Overhead Console for more informa-
tion on the customer programmable feature options.
Customer programmable feature options affecting the
horn system include:
²Sound Horn on Lock- Allows the option of
having the horn sound a short chirp as an audible
verification that the RKE system received a valid
Lock request from the RKE transmitter, or having no
audible verification.The horn system includes the following compo-
nents:
²Clockspring
²Horns
²Horn relay
²Horn switch
Certain functions and features of the horn system
rely upon resources shared with other electronic
modules in the vehicle over the Programmable Com-
munications Interface (PCI) data bus network. The
PCI data bus network allows the sharing of sensor
information. This helps to reduce wire harness com-
plexity, internal controller hardware, and component
sensor current loads. At the same time, this system
provides increased reliability, enhanced diagnostics,
and allows the addition of many new feature capabil-
ities. For diagnosis of these electronic modules or of
the PCI data bus network, the use of a DRB scan
tool and the proper Diagnostic Procedures manual
are recommended.
The other electronic modules that may affect horn
system operation are as follows:
²Body Control Module (BCM)(Refer to 8 -
ELECTRICAL/ELECTRONIC CONTROL MOD-
ULES/BODY CONTROL/CENTRAL TIMER MODUL
- DESCRIPTION) for more information.
²Electronic Vehicle Information Center
(EVIC)(Refer to 8 - ELECTRICAL/OVERHEAD
CONSOLE/ELECTRONIC VEHICLE INFO CENTER
- DESCRIPTION) for more information.
(Refer to 8 - ELECTRICAL/RESTRAINTS/CLOCK-
SPRING - DESCRIPTION) for more information on
this component. Refer to the appropriate wiring
information. The wiring information includes wiring
diagrams, proper wire and connector repair proce-
dures, details of wire harness routing and retention,
WJHORN 8H - 1
Page 398 of 2199
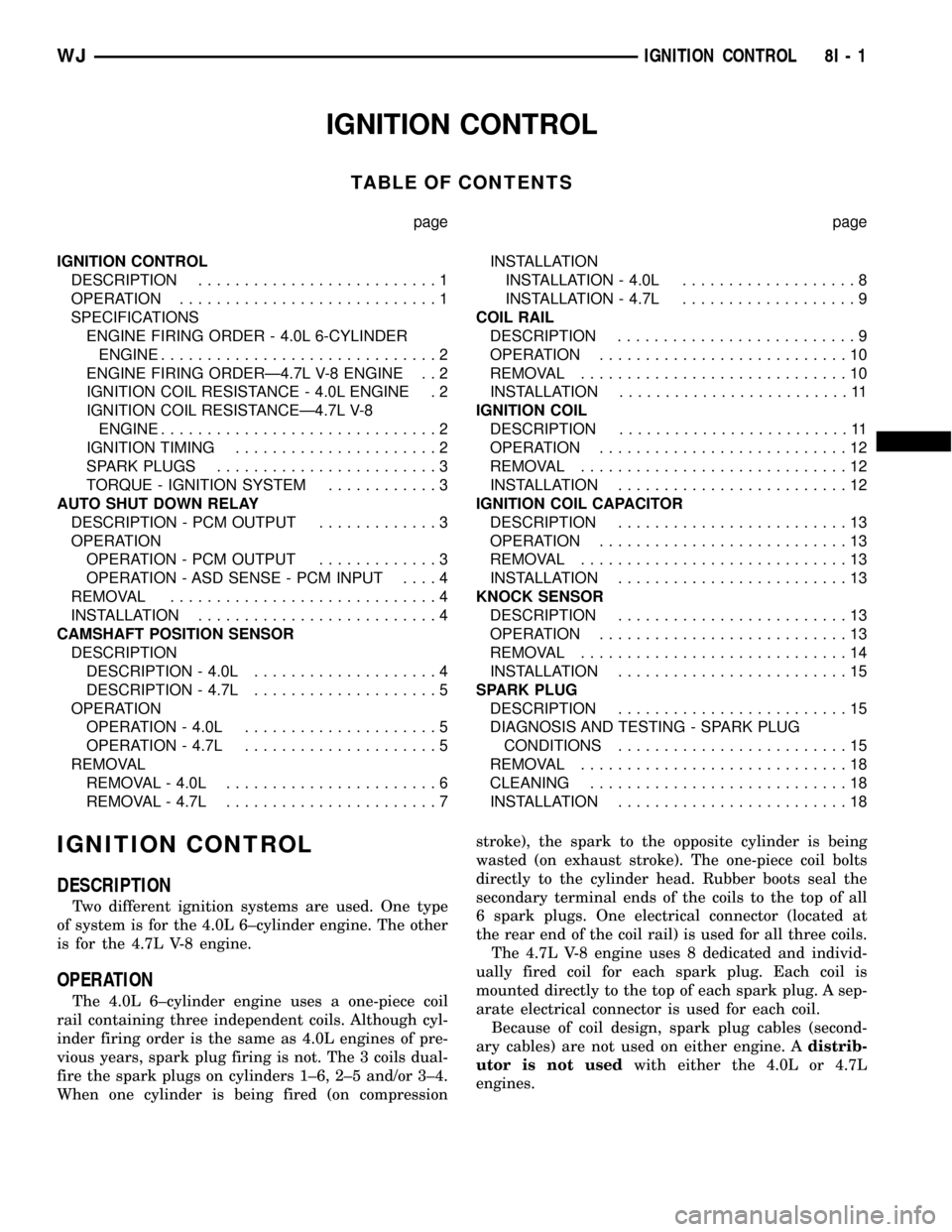
IGNITION CONTROL
TABLE OF CONTENTS
page page
IGNITION CONTROL
DESCRIPTION..........................1
OPERATION............................1
SPECIFICATIONS
ENGINE FIRING ORDER - 4.0L 6-CYLINDER
ENGINE..............................2
ENGINE FIRING ORDERÐ4.7L V-8 ENGINE . . 2
IGNITION COIL RESISTANCE - 4.0L ENGINE . 2
IGNITION COIL RESISTANCEÐ4.7L V-8
ENGINE..............................2
IGNITION TIMING......................2
SPARK PLUGS........................3
TORQUE - IGNITION SYSTEM............3
AUTO SHUT DOWN RELAY
DESCRIPTION - PCM OUTPUT.............3
OPERATION
OPERATION - PCM OUTPUT.............3
OPERATION - ASD SENSE - PCM INPUT....4
REMOVAL.............................4
INSTALLATION..........................4
CAMSHAFT POSITION SENSOR
DESCRIPTION
DESCRIPTION - 4.0L....................4
DESCRIPTION - 4.7L....................5
OPERATION
OPERATION - 4.0L.....................5
OPERATION - 4.7L.....................5
REMOVAL
REMOVAL - 4.0L.......................6
REMOVAL - 4.7L.......................7INSTALLATION
INSTALLATION - 4.0L...................8
INSTALLATION - 4.7L...................9
COIL RAIL
DESCRIPTION..........................9
OPERATION...........................10
REMOVAL.............................10
INSTALLATION.........................11
IGNITION COIL
DESCRIPTION.........................11
OPERATION...........................12
REMOVAL.............................12
INSTALLATION.........................12
IGNITION COIL CAPACITOR
DESCRIPTION.........................13
OPERATION...........................13
REMOVAL.............................13
INSTALLATION.........................13
KNOCK SENSOR
DESCRIPTION.........................13
OPERATION...........................13
REMOVAL.............................14
INSTALLATION.........................15
SPARK PLUG
DESCRIPTION.........................15
DIAGNOSIS AND TESTING - SPARK PLUG
CONDITIONS.........................15
REMOVAL.............................18
CLEANING............................18
INSTALLATION.........................18
IGNITION CONTROL
DESCRIPTION
Two different ignition systems are used. One type
of system is for the 4.0L 6±cylinder engine. The other
is for the 4.7L V-8 engine.
OPERATION
The 4.0L 6±cylinder engine uses a one-piece coil
rail containing three independent coils. Although cyl-
inder firing order is the same as 4.0L engines of pre-
vious years, spark plug firing is not. The 3 coils dual-
fire the spark plugs on cylinders 1±6, 2±5 and/or 3±4.
When one cylinder is being fired (on compressionstroke), the spark to the opposite cylinder is being
wasted (on exhaust stroke). The one-piece coil bolts
directly to the cylinder head. Rubber boots seal the
secondary terminal ends of the coils to the top of all
6 spark plugs. One electrical connector (located at
the rear end of the coil rail) is used for all three coils.
The 4.7L V-8 engine uses 8 dedicated and individ-
ually fired coil for each spark plug. Each coil is
mounted directly to the top of each spark plug. A sep-
arate electrical connector is used for each coil.
Because of coil design, spark plug cables (second-
ary cables) are not used on either engine. Adistrib-
utor is not usedwith either the 4.0L or 4.7L
engines.
WJIGNITION CONTROL 8I - 1
Page 399 of 2199
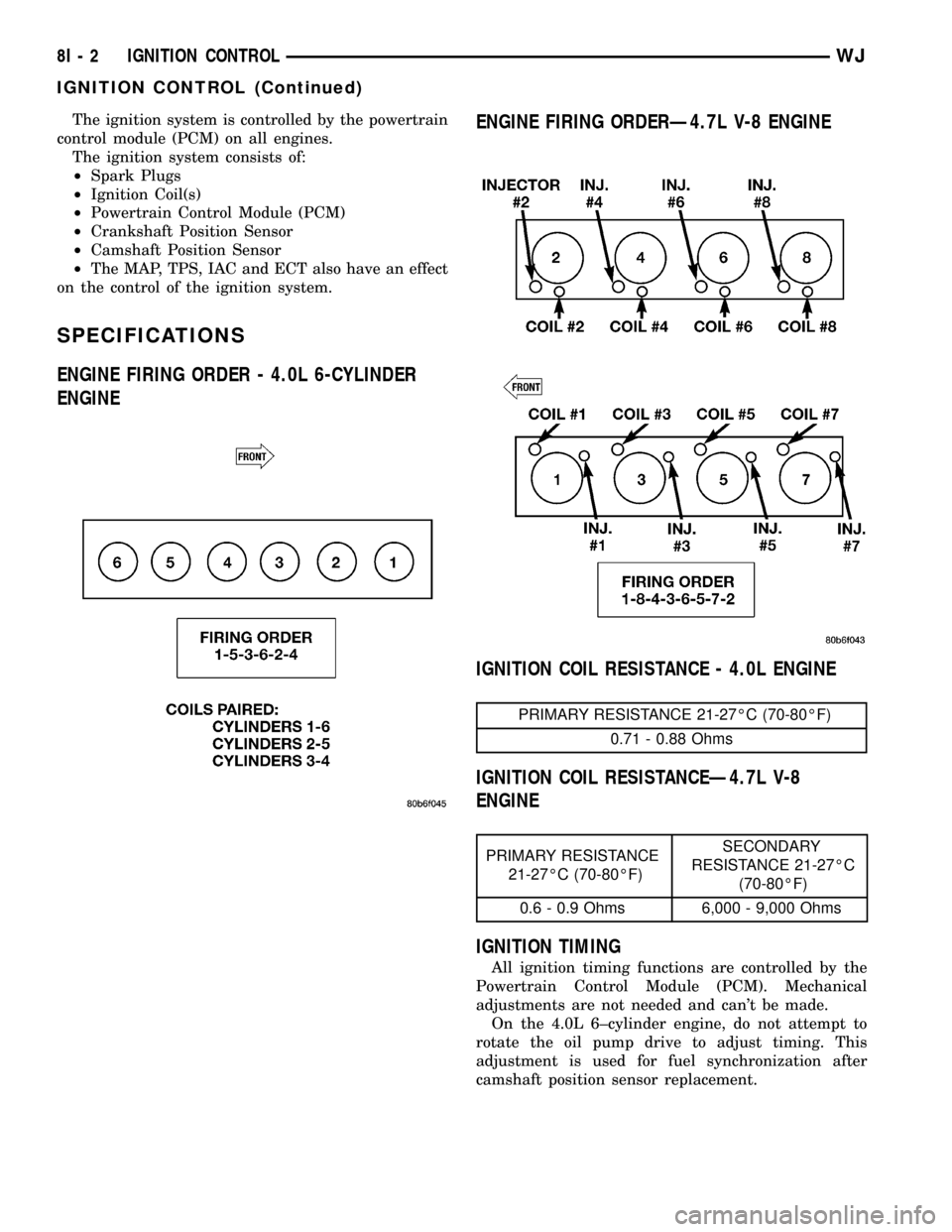
The ignition system is controlled by the powertrain
control module (PCM) on all engines.
The ignition system consists of:
²Spark Plugs
²Ignition Coil(s)
²Powertrain Control Module (PCM)
²Crankshaft Position Sensor
²Camshaft Position Sensor
²The MAP, TPS, IAC and ECT also have an effect
on the control of the ignition system.
SPECIFICATIONS
ENGINE FIRING ORDER - 4.0L 6-CYLINDER
ENGINEENGINE FIRING ORDERÐ4.7L V-8 ENGINE
IGNITION COIL RESISTANCE - 4.0L ENGINE
PRIMARY RESISTANCE 21-27ÉC (70-80ÉF)
0.71 - 0.88 Ohms
IGNITION COIL RESISTANCEÐ4.7L V-8
ENGINE
PRIMARY RESISTANCE
21-27ÉC (70-80ÉF)SECONDARY
RESISTANCE 21-27ÉC
(70-80ÉF)
0.6 - 0.9 Ohms 6,000 - 9,000 Ohms
IGNITION TIMING
All ignition timing functions are controlled by the
Powertrain Control Module (PCM). Mechanical
adjustments are not needed and can't be made.
On the 4.0L 6±cylinder engine, do not attempt to
rotate the oil pump drive to adjust timing. This
adjustment is used for fuel synchronization after
camshaft position sensor replacement.
8I - 2 IGNITION CONTROLWJ
IGNITION CONTROL (Continued)
Page 400 of 2199
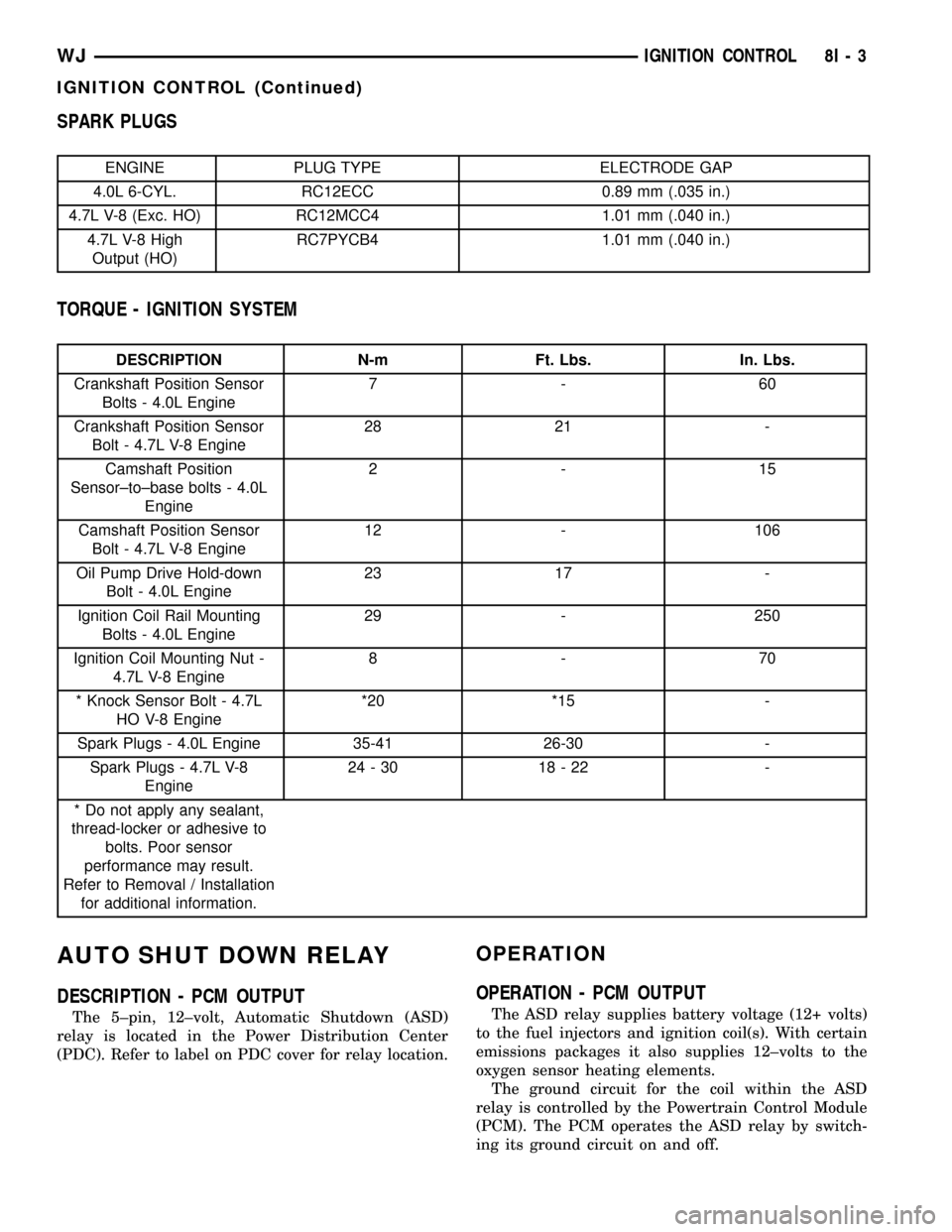
SPARK PLUGS
ENGINE PLUG TYPE ELECTRODE GAP
4.0L 6-CYL. RC12ECC 0.89 mm (.035 in.)
4.7L V-8 (Exc. HO) RC12MCC4 1.01 mm (.040 in.)
4.7L V-8 High
Output (HO)RC7PYCB4 1.01 mm (.040 in.)
TORQUE - IGNITION SYSTEM
DESCRIPTION N-m Ft. Lbs. In. Lbs.
Crankshaft Position Sensor
Bolts - 4.0L Engine7- 60
Crankshaft Position Sensor
Bolt - 4.7L V-8 Engine28 21 -
Camshaft Position
Sensor±to±base bolts - 4.0L
Engine2- 15
Camshaft Position Sensor
Bolt - 4.7L V-8 Engine12 - 106
Oil Pump Drive Hold-down
Bolt - 4.0L Engine23 17 -
Ignition Coil Rail Mounting
Bolts - 4.0L Engine29 - 250
Ignition Coil Mounting Nut -
4.7L V-8 Engine8- 70
* Knock Sensor Bolt - 4.7L
HO V-8 Engine*20 *15 -
Spark Plugs - 4.0L Engine 35-41 26-30 -
Spark Plugs - 4.7L V-8
Engine24-30 18-22 -
* Do not apply any sealant,
thread-locker or adhesive to
bolts. Poor sensor
performance may result.
Refer to Removal / Installation
for additional information.
AUTO SHUT DOWN RELAY
DESCRIPTION - PCM OUTPUT
The 5±pin, 12±volt, Automatic Shutdown (ASD)
relay is located in the Power Distribution Center
(PDC). Refer to label on PDC cover for relay location.
OPERATION
OPERATION - PCM OUTPUT
The ASD relay supplies battery voltage (12+ volts)
to the fuel injectors and ignition coil(s). With certain
emissions packages it also supplies 12±volts to the
oxygen sensor heating elements.
The ground circuit for the coil within the ASD
relay is controlled by the Powertrain Control Module
(PCM). The PCM operates the ASD relay by switch-
ing its ground circuit on and off.
WJIGNITION CONTROL 8I - 3
IGNITION CONTROL (Continued)
Page 401 of 2199
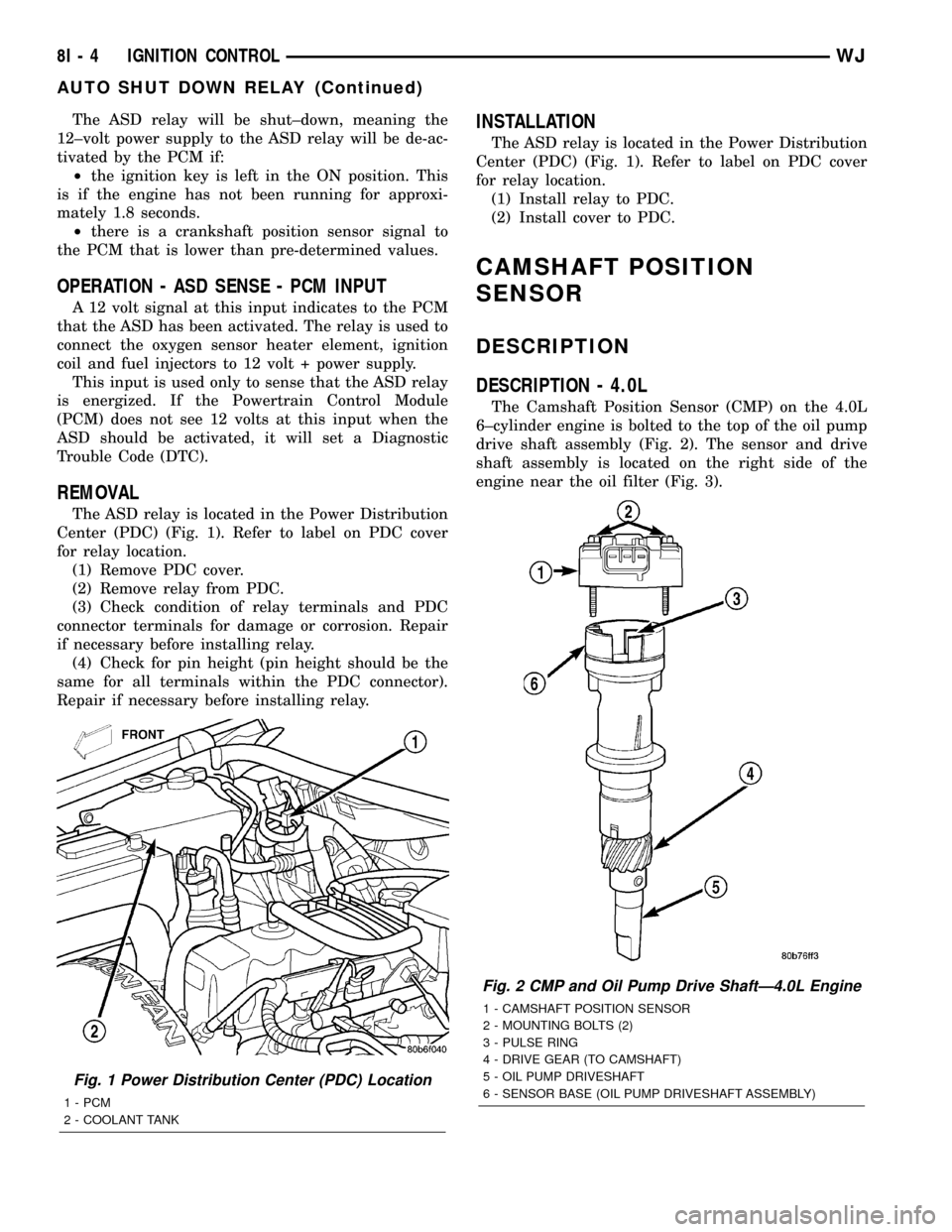
The ASD relay will be shut±down, meaning the
12±volt power supply to the ASD relay will be de-ac-
tivated by the PCM if:
²the ignition key is left in the ON position. This
is if the engine has not been running for approxi-
mately 1.8 seconds.
²there is a crankshaft position sensor signal to
the PCM that is lower than pre-determined values.
OPERATION - ASD SENSE - PCM INPUT
A 12 volt signal at this input indicates to the PCM
that the ASD has been activated. The relay is used to
connect the oxygen sensor heater element, ignition
coil and fuel injectors to 12 volt + power supply.
This input is used only to sense that the ASD relay
is energized. If the Powertrain Control Module
(PCM) does not see 12 volts at this input when the
ASD should be activated, it will set a Diagnostic
Trouble Code (DTC).
REMOVAL
The ASD relay is located in the Power Distribution
Center (PDC) (Fig. 1). Refer to label on PDC cover
for relay location.
(1) Remove PDC cover.
(2) Remove relay from PDC.
(3) Check condition of relay terminals and PDC
connector terminals for damage or corrosion. Repair
if necessary before installing relay.
(4) Check for pin height (pin height should be the
same for all terminals within the PDC connector).
Repair if necessary before installing relay.
INSTALLATION
The ASD relay is located in the Power Distribution
Center (PDC) (Fig. 1). Refer to label on PDC cover
for relay location.
(1) Install relay to PDC.
(2) Install cover to PDC.
CAMSHAFT POSITION
SENSOR
DESCRIPTION
DESCRIPTION - 4.0L
The Camshaft Position Sensor (CMP) on the 4.0L
6±cylinder engine is bolted to the top of the oil pump
drive shaft assembly (Fig. 2). The sensor and drive
shaft assembly is located on the right side of the
engine near the oil filter (Fig. 3).
Fig. 1 Power Distribution Center (PDC) Location
1 - PCM
2 - COOLANT TANK
Fig. 2 CMP and Oil Pump Drive ShaftÐ4.0L Engine
1 - CAMSHAFT POSITION SENSOR
2 - MOUNTING BOLTS (2)
3 - PULSE RING
4 - DRIVE GEAR (TO CAMSHAFT)
5 - OIL PUMP DRIVESHAFT
6 - SENSOR BASE (OIL PUMP DRIVESHAFT ASSEMBLY)
8I - 4 IGNITION CONTROLWJ
AUTO SHUT DOWN RELAY (Continued)
Page 402 of 2199
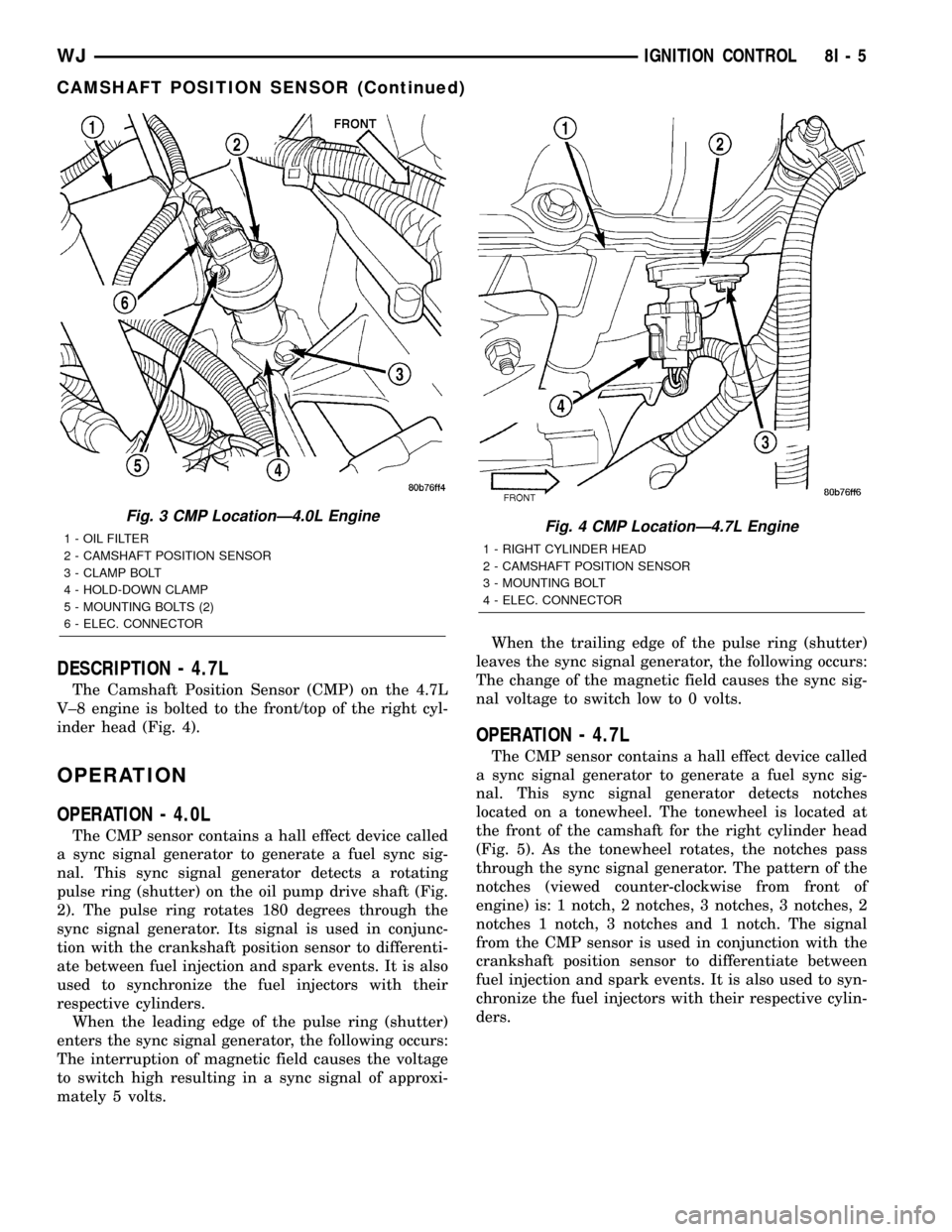
DESCRIPTION - 4.7L
The Camshaft Position Sensor (CMP) on the 4.7L
V±8 engine is bolted to the front/top of the right cyl-
inder head (Fig. 4).
OPERATION
OPERATION - 4.0L
The CMP sensor contains a hall effect device called
a sync signal generator to generate a fuel sync sig-
nal. This sync signal generator detects a rotating
pulse ring (shutter) on the oil pump drive shaft (Fig.
2). The pulse ring rotates 180 degrees through the
sync signal generator. Its signal is used in conjunc-
tion with the crankshaft position sensor to differenti-
ate between fuel injection and spark events. It is also
used to synchronize the fuel injectors with their
respective cylinders.
When the leading edge of the pulse ring (shutter)
enters the sync signal generator, the following occurs:
The interruption of magnetic field causes the voltage
to switch high resulting in a sync signal of approxi-
mately 5 volts.When the trailing edge of the pulse ring (shutter)
leaves the sync signal generator, the following occurs:
The change of the magnetic field causes the sync sig-
nal voltage to switch low to 0 volts.
OPERATION - 4.7L
The CMP sensor contains a hall effect device called
a sync signal generator to generate a fuel sync sig-
nal. This sync signal generator detects notches
located on a tonewheel. The tonewheel is located at
the front of the camshaft for the right cylinder head
(Fig. 5). As the tonewheel rotates, the notches pass
through the sync signal generator. The pattern of the
notches (viewed counter-clockwise from front of
engine) is: 1 notch, 2 notches, 3 notches, 3 notches, 2
notches 1 notch, 3 notches and 1 notch. The signal
from the CMP sensor is used in conjunction with the
crankshaft position sensor to differentiate between
fuel injection and spark events. It is also used to syn-
chronize the fuel injectors with their respective cylin-
ders.
Fig. 3 CMP LocationÐ4.0L Engine
1 - OIL FILTER
2 - CAMSHAFT POSITION SENSOR
3 - CLAMP BOLT
4 - HOLD-DOWN CLAMP
5 - MOUNTING BOLTS (2)
6 - ELEC. CONNECTORFig. 4 CMP LocationÐ4.7L Engine
1 - RIGHT CYLINDER HEAD
2 - CAMSHAFT POSITION SENSOR
3 - MOUNTING BOLT
4 - ELEC. CONNECTOR
WJIGNITION CONTROL 8I - 5
CAMSHAFT POSITION SENSOR (Continued)