Ecu JEEP GRAND CHEROKEE 2002 WJ / 2.G Manual PDF
[x] Cancel search | Manufacturer: JEEP, Model Year: 2002, Model line: GRAND CHEROKEE, Model: JEEP GRAND CHEROKEE 2002 WJ / 2.GPages: 2199, PDF Size: 76.01 MB
Page 428 of 2199
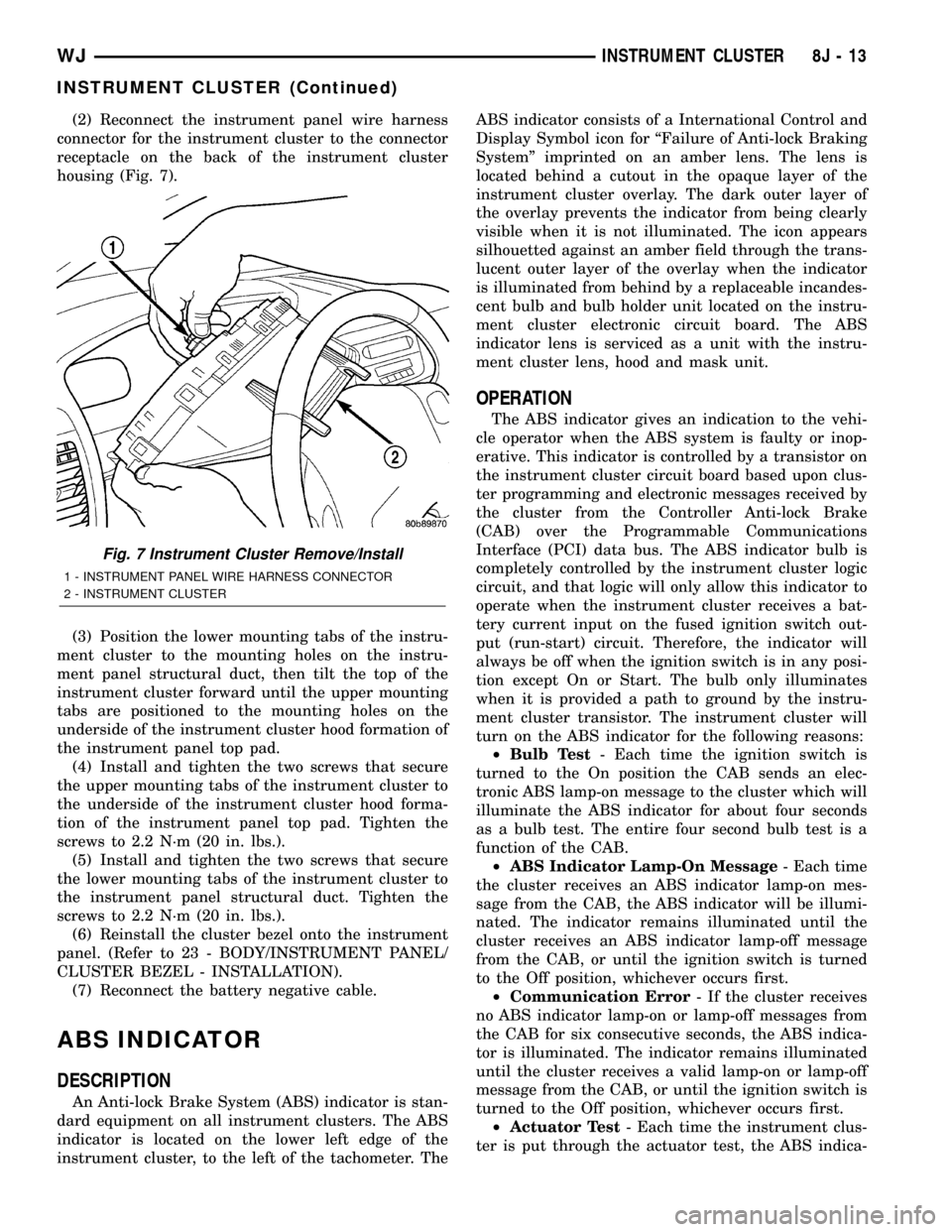
(2) Reconnect the instrument panel wire harness
connector for the instrument cluster to the connector
receptacle on the back of the instrument cluster
housing (Fig. 7).
(3) Position the lower mounting tabs of the instru-
ment cluster to the mounting holes on the instru-
ment panel structural duct, then tilt the top of the
instrument cluster forward until the upper mounting
tabs are positioned to the mounting holes on the
underside of the instrument cluster hood formation of
the instrument panel top pad.
(4) Install and tighten the two screws that secure
the upper mounting tabs of the instrument cluster to
the underside of the instrument cluster hood forma-
tion of the instrument panel top pad. Tighten the
screws to 2.2 N´m (20 in. lbs.).
(5) Install and tighten the two screws that secure
the lower mounting tabs of the instrument cluster to
the instrument panel structural duct. Tighten the
screws to 2.2 N´m (20 in. lbs.).
(6) Reinstall the cluster bezel onto the instrument
panel. (Refer to 23 - BODY/INSTRUMENT PANEL/
CLUSTER BEZEL - INSTALLATION).
(7) Reconnect the battery negative cable.
ABS INDICATOR
DESCRIPTION
An Anti-lock Brake System (ABS) indicator is stan-
dard equipment on all instrument clusters. The ABS
indicator is located on the lower left edge of the
instrument cluster, to the left of the tachometer. TheABS indicator consists of a International Control and
Display Symbol icon for ªFailure of Anti-lock Braking
Systemº imprinted on an amber lens. The lens is
located behind a cutout in the opaque layer of the
instrument cluster overlay. The dark outer layer of
the overlay prevents the indicator from being clearly
visible when it is not illuminated. The icon appears
silhouetted against an amber field through the trans-
lucent outer layer of the overlay when the indicator
is illuminated from behind by a replaceable incandes-
cent bulb and bulb holder unit located on the instru-
ment cluster electronic circuit board. The ABS
indicator lens is serviced as a unit with the instru-
ment cluster lens, hood and mask unit.
OPERATION
The ABS indicator gives an indication to the vehi-
cle operator when the ABS system is faulty or inop-
erative. This indicator is controlled by a transistor on
the instrument cluster circuit board based upon clus-
ter programming and electronic messages received by
the cluster from the Controller Anti-lock Brake
(CAB) over the Programmable Communications
Interface (PCI) data bus. The ABS indicator bulb is
completely controlled by the instrument cluster logic
circuit, and that logic will only allow this indicator to
operate when the instrument cluster receives a bat-
tery current input on the fused ignition switch out-
put (run-start) circuit. Therefore, the indicator will
always be off when the ignition switch is in any posi-
tion except On or Start. The bulb only illuminates
when it is provided a path to ground by the instru-
ment cluster transistor. The instrument cluster will
turn on the ABS indicator for the following reasons:
²Bulb Test- Each time the ignition switch is
turned to the On position the CAB sends an elec-
tronic ABS lamp-on message to the cluster which will
illuminate the ABS indicator for about four seconds
as a bulb test. The entire four second bulb test is a
function of the CAB.
²ABS Indicator Lamp-On Message- Each time
the cluster receives an ABS indicator lamp-on mes-
sage from the CAB, the ABS indicator will be illumi-
nated. The indicator remains illuminated until the
cluster receives an ABS indicator lamp-off message
from the CAB, or until the ignition switch is turned
to the Off position, whichever occurs first.
²Communication Error- If the cluster receives
no ABS indicator lamp-on or lamp-off messages from
the CAB for six consecutive seconds, the ABS indica-
tor is illuminated. The indicator remains illuminated
until the cluster receives a valid lamp-on or lamp-off
message from the CAB, or until the ignition switch is
turned to the Off position, whichever occurs first.
²Actuator Test- Each time the instrument clus-
ter is put through the actuator test, the ABS indica-
Fig. 7 Instrument Cluster Remove/Install
1 - INSTRUMENT PANEL WIRE HARNESS CONNECTOR
2 - INSTRUMENT CLUSTER
WJINSTRUMENT CLUSTER 8J - 13
INSTRUMENT CLUSTER (Continued)
Page 429 of 2199
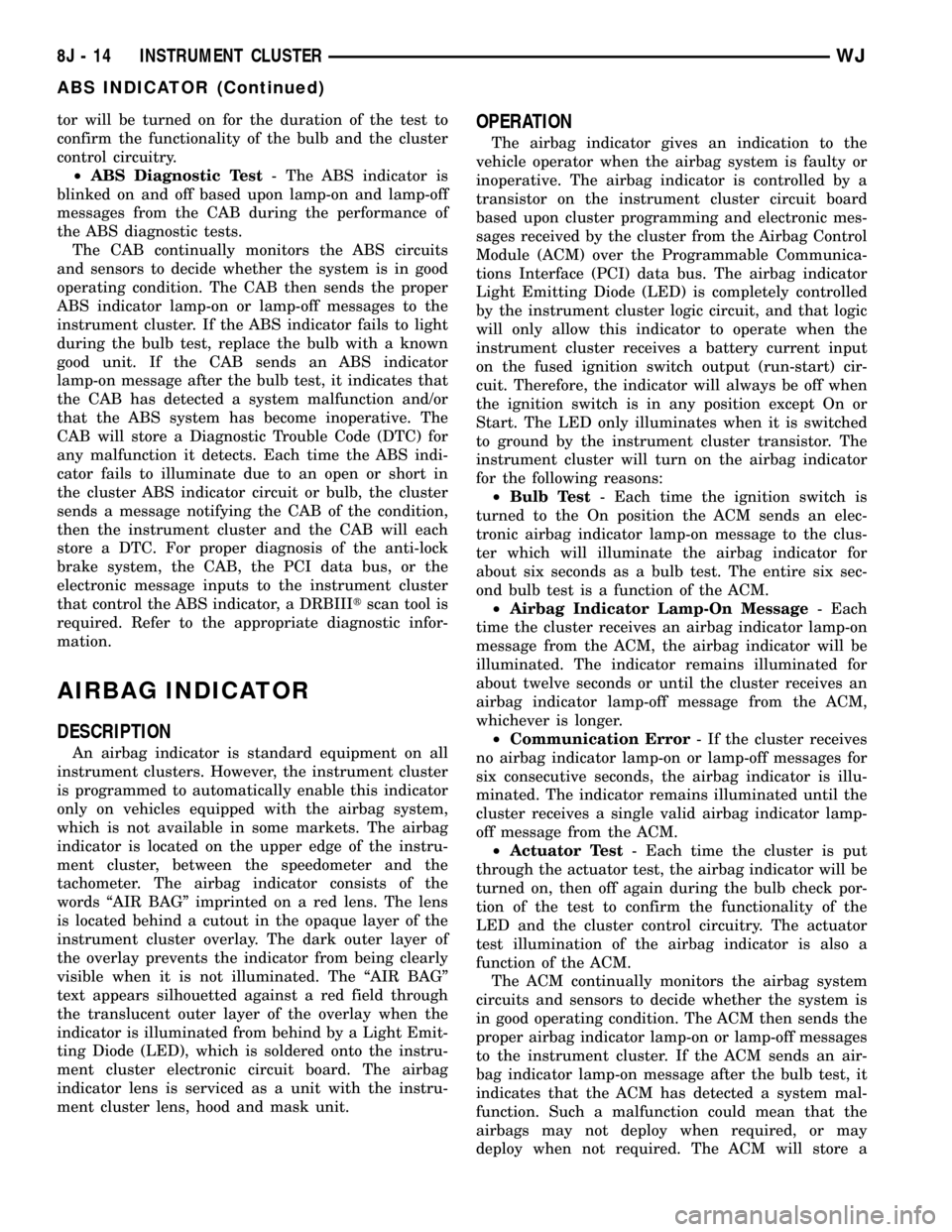
tor will be turned on for the duration of the test to
confirm the functionality of the bulb and the cluster
control circuitry.
²ABS Diagnostic Test- The ABS indicator is
blinked on and off based upon lamp-on and lamp-off
messages from the CAB during the performance of
the ABS diagnostic tests.
The CAB continually monitors the ABS circuits
and sensors to decide whether the system is in good
operating condition. The CAB then sends the proper
ABS indicator lamp-on or lamp-off messages to the
instrument cluster. If the ABS indicator fails to light
during the bulb test, replace the bulb with a known
good unit. If the CAB sends an ABS indicator
lamp-on message after the bulb test, it indicates that
the CAB has detected a system malfunction and/or
that the ABS system has become inoperative. The
CAB will store a Diagnostic Trouble Code (DTC) for
any malfunction it detects. Each time the ABS indi-
cator fails to illuminate due to an open or short in
the cluster ABS indicator circuit or bulb, the cluster
sends a message notifying the CAB of the condition,
then the instrument cluster and the CAB will each
store a DTC. For proper diagnosis of the anti-lock
brake system, the CAB, the PCI data bus, or the
electronic message inputs to the instrument cluster
that control the ABS indicator, a DRBIIItscan tool is
required. Refer to the appropriate diagnostic infor-
mation.
AIRBAG INDICATOR
DESCRIPTION
An airbag indicator is standard equipment on all
instrument clusters. However, the instrument cluster
is programmed to automatically enable this indicator
only on vehicles equipped with the airbag system,
which is not available in some markets. The airbag
indicator is located on the upper edge of the instru-
ment cluster, between the speedometer and the
tachometer. The airbag indicator consists of the
words ªAIR BAGº imprinted on a red lens. The lens
is located behind a cutout in the opaque layer of the
instrument cluster overlay. The dark outer layer of
the overlay prevents the indicator from being clearly
visible when it is not illuminated. The ªAIR BAGº
text appears silhouetted against a red field through
the translucent outer layer of the overlay when the
indicator is illuminated from behind by a Light Emit-
ting Diode (LED), which is soldered onto the instru-
ment cluster electronic circuit board. The airbag
indicator lens is serviced as a unit with the instru-
ment cluster lens, hood and mask unit.
OPERATION
The airbag indicator gives an indication to the
vehicle operator when the airbag system is faulty or
inoperative. The airbag indicator is controlled by a
transistor on the instrument cluster circuit board
based upon cluster programming and electronic mes-
sages received by the cluster from the Airbag Control
Module (ACM) over the Programmable Communica-
tions Interface (PCI) data bus. The airbag indicator
Light Emitting Diode (LED) is completely controlled
by the instrument cluster logic circuit, and that logic
will only allow this indicator to operate when the
instrument cluster receives a battery current input
on the fused ignition switch output (run-start) cir-
cuit. Therefore, the indicator will always be off when
the ignition switch is in any position except On or
Start. The LED only illuminates when it is switched
to ground by the instrument cluster transistor. The
instrument cluster will turn on the airbag indicator
for the following reasons:
²Bulb Test- Each time the ignition switch is
turned to the On position the ACM sends an elec-
tronic airbag indicator lamp-on message to the clus-
ter which will illuminate the airbag indicator for
about six seconds as a bulb test. The entire six sec-
ond bulb test is a function of the ACM.
²Airbag Indicator Lamp-On Message- Each
time the cluster receives an airbag indicator lamp-on
message from the ACM, the airbag indicator will be
illuminated. The indicator remains illuminated for
about twelve seconds or until the cluster receives an
airbag indicator lamp-off message from the ACM,
whichever is longer.
²Communication Error- If the cluster receives
no airbag indicator lamp-on or lamp-off messages for
six consecutive seconds, the airbag indicator is illu-
minated. The indicator remains illuminated until the
cluster receives a single valid airbag indicator lamp-
off message from the ACM.
²Actuator Test- Each time the cluster is put
through the actuator test, the airbag indicator will be
turned on, then off again during the bulb check por-
tion of the test to confirm the functionality of the
LED and the cluster control circuitry. The actuator
test illumination of the airbag indicator is also a
function of the ACM.
The ACM continually monitors the airbag system
circuits and sensors to decide whether the system is
in good operating condition. The ACM then sends the
proper airbag indicator lamp-on or lamp-off messages
to the instrument cluster. If the ACM sends an air-
bag indicator lamp-on message after the bulb test, it
indicates that the ACM has detected a system mal-
function. Such a malfunction could mean that the
airbags may not deploy when required, or may
deploy when not required. The ACM will store a
8J - 14 INSTRUMENT CLUSTERWJ
ABS INDICATOR (Continued)
Page 430 of 2199
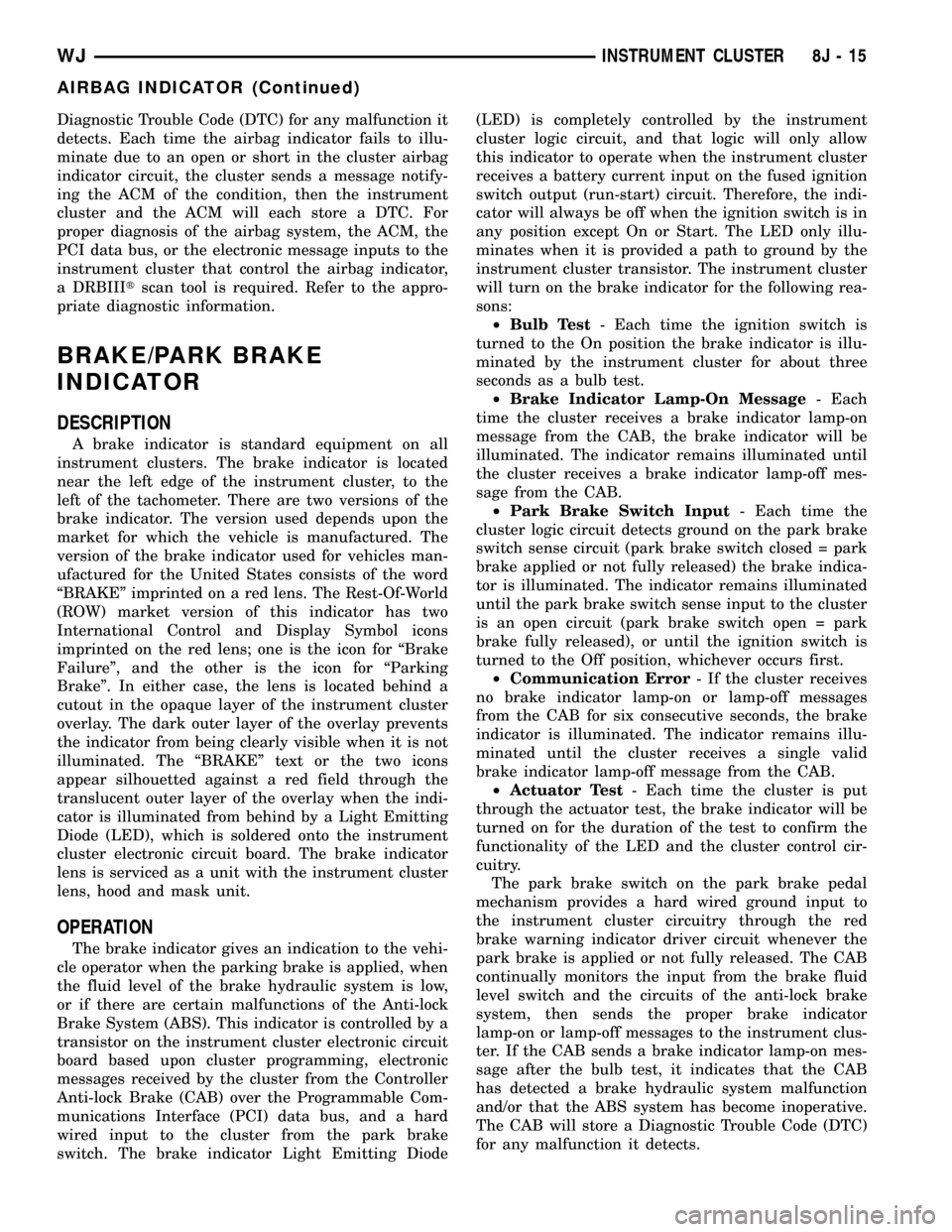
Diagnostic Trouble Code (DTC) for any malfunction it
detects. Each time the airbag indicator fails to illu-
minate due to an open or short in the cluster airbag
indicator circuit, the cluster sends a message notify-
ing the ACM of the condition, then the instrument
cluster and the ACM will each store a DTC. For
proper diagnosis of the airbag system, the ACM, the
PCI data bus, or the electronic message inputs to the
instrument cluster that control the airbag indicator,
a DRBIIItscan tool is required. Refer to the appro-
priate diagnostic information.
BRAKE/PARK BRAKE
INDICATOR
DESCRIPTION
A brake indicator is standard equipment on all
instrument clusters. The brake indicator is located
near the left edge of the instrument cluster, to the
left of the tachometer. There are two versions of the
brake indicator. The version used depends upon the
market for which the vehicle is manufactured. The
version of the brake indicator used for vehicles man-
ufactured for the United States consists of the word
ªBRAKEº imprinted on a red lens. The Rest-Of-World
(ROW) market version of this indicator has two
International Control and Display Symbol icons
imprinted on the red lens; one is the icon for ªBrake
Failureº, and the other is the icon for ªParking
Brakeº. In either case, the lens is located behind a
cutout in the opaque layer of the instrument cluster
overlay. The dark outer layer of the overlay prevents
the indicator from being clearly visible when it is not
illuminated. The ªBRAKEº text or the two icons
appear silhouetted against a red field through the
translucent outer layer of the overlay when the indi-
cator is illuminated from behind by a Light Emitting
Diode (LED), which is soldered onto the instrument
cluster electronic circuit board. The brake indicator
lens is serviced as a unit with the instrument cluster
lens, hood and mask unit.
OPERATION
The brake indicator gives an indication to the vehi-
cle operator when the parking brake is applied, when
the fluid level of the brake hydraulic system is low,
or if there are certain malfunctions of the Anti-lock
Brake System (ABS). This indicator is controlled by a
transistor on the instrument cluster electronic circuit
board based upon cluster programming, electronic
messages received by the cluster from the Controller
Anti-lock Brake (CAB) over the Programmable Com-
munications Interface (PCI) data bus, and a hard
wired input to the cluster from the park brake
switch. The brake indicator Light Emitting Diode(LED) is completely controlled by the instrument
cluster logic circuit, and that logic will only allow
this indicator to operate when the instrument cluster
receives a battery current input on the fused ignition
switch output (run-start) circuit. Therefore, the indi-
cator will always be off when the ignition switch is in
any position except On or Start. The LED only illu-
minates when it is provided a path to ground by the
instrument cluster transistor. The instrument cluster
will turn on the brake indicator for the following rea-
sons:
²Bulb Test- Each time the ignition switch is
turned to the On position the brake indicator is illu-
minated by the instrument cluster for about three
seconds as a bulb test.
²Brake Indicator Lamp-On Message- Each
time the cluster receives a brake indicator lamp-on
message from the CAB, the brake indicator will be
illuminated. The indicator remains illuminated until
the cluster receives a brake indicator lamp-off mes-
sage from the CAB.
²Park Brake Switch Input- Each time the
cluster logic circuit detects ground on the park brake
switch sense circuit (park brake switch closed = park
brake applied or not fully released) the brake indica-
tor is illuminated. The indicator remains illuminated
until the park brake switch sense input to the cluster
is an open circuit (park brake switch open = park
brake fully released), or until the ignition switch is
turned to the Off position, whichever occurs first.
²Communication Error- If the cluster receives
no brake indicator lamp-on or lamp-off messages
from the CAB for six consecutive seconds, the brake
indicator is illuminated. The indicator remains illu-
minated until the cluster receives a single valid
brake indicator lamp-off message from the CAB.
²Actuator Test- Each time the cluster is put
through the actuator test, the brake indicator will be
turned on for the duration of the test to confirm the
functionality of the LED and the cluster control cir-
cuitry.
The park brake switch on the park brake pedal
mechanism provides a hard wired ground input to
the instrument cluster circuitry through the red
brake warning indicator driver circuit whenever the
park brake is applied or not fully released. The CAB
continually monitors the input from the brake fluid
level switch and the circuits of the anti-lock brake
system, then sends the proper brake indicator
lamp-on or lamp-off messages to the instrument clus-
ter. If the CAB sends a brake indicator lamp-on mes-
sage after the bulb test, it indicates that the CAB
has detected a brake hydraulic system malfunction
and/or that the ABS system has become inoperative.
The CAB will store a Diagnostic Trouble Code (DTC)
for any malfunction it detects.
WJINSTRUMENT CLUSTER 8J - 15
AIRBAG INDICATOR (Continued)
Page 439 of 2199
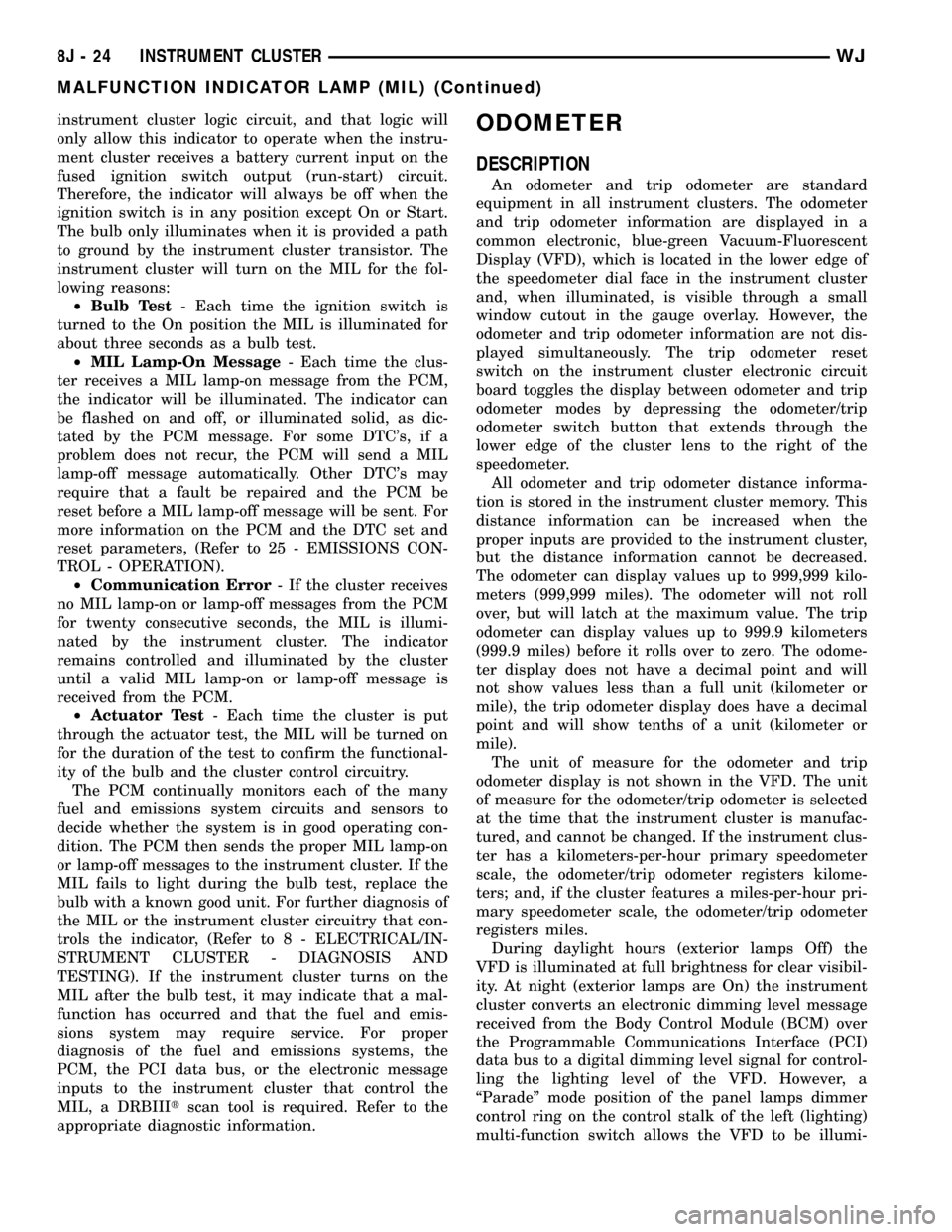
instrument cluster logic circuit, and that logic will
only allow this indicator to operate when the instru-
ment cluster receives a battery current input on the
fused ignition switch output (run-start) circuit.
Therefore, the indicator will always be off when the
ignition switch is in any position except On or Start.
The bulb only illuminates when it is provided a path
to ground by the instrument cluster transistor. The
instrument cluster will turn on the MIL for the fol-
lowing reasons:
²Bulb Test- Each time the ignition switch is
turned to the On position the MIL is illuminated for
about three seconds as a bulb test.
²MIL Lamp-On Message- Each time the clus-
ter receives a MIL lamp-on message from the PCM,
the indicator will be illuminated. The indicator can
be flashed on and off, or illuminated solid, as dic-
tated by the PCM message. For some DTC's, if a
problem does not recur, the PCM will send a MIL
lamp-off message automatically. Other DTC's may
require that a fault be repaired and the PCM be
reset before a MIL lamp-off message will be sent. For
more information on the PCM and the DTC set and
reset parameters, (Refer to 25 - EMISSIONS CON-
TROL - OPERATION).
²Communication Error- If the cluster receives
no MIL lamp-on or lamp-off messages from the PCM
for twenty consecutive seconds, the MIL is illumi-
nated by the instrument cluster. The indicator
remains controlled and illuminated by the cluster
until a valid MIL lamp-on or lamp-off message is
received from the PCM.
²Actuator Test- Each time the cluster is put
through the actuator test, the MIL will be turned on
for the duration of the test to confirm the functional-
ity of the bulb and the cluster control circuitry.
The PCM continually monitors each of the many
fuel and emissions system circuits and sensors to
decide whether the system is in good operating con-
dition. The PCM then sends the proper MIL lamp-on
or lamp-off messages to the instrument cluster. If the
MIL fails to light during the bulb test, replace the
bulb with a known good unit. For further diagnosis of
the MIL or the instrument cluster circuitry that con-
trols the indicator, (Refer to 8 - ELECTRICAL/IN-
STRUMENT CLUSTER - DIAGNOSIS AND
TESTING). If the instrument cluster turns on the
MIL after the bulb test, it may indicate that a mal-
function has occurred and that the fuel and emis-
sions system may require service. For proper
diagnosis of the fuel and emissions systems, the
PCM, the PCI data bus, or the electronic message
inputs to the instrument cluster that control the
MIL, a DRBIIItscan tool is required. Refer to the
appropriate diagnostic information.ODOMETER
DESCRIPTION
An odometer and trip odometer are standard
equipment in all instrument clusters. The odometer
and trip odometer information are displayed in a
common electronic, blue-green Vacuum-Fluorescent
Display (VFD), which is located in the lower edge of
the speedometer dial face in the instrument cluster
and, when illuminated, is visible through a small
window cutout in the gauge overlay. However, the
odometer and trip odometer information are not dis-
played simultaneously. The trip odometer reset
switch on the instrument cluster electronic circuit
board toggles the display between odometer and trip
odometer modes by depressing the odometer/trip
odometer switch button that extends through the
lower edge of the cluster lens to the right of the
speedometer.
All odometer and trip odometer distance informa-
tion is stored in the instrument cluster memory. This
distance information can be increased when the
proper inputs are provided to the instrument cluster,
but the distance information cannot be decreased.
The odometer can display values up to 999,999 kilo-
meters (999,999 miles). The odometer will not roll
over, but will latch at the maximum value. The trip
odometer can display values up to 999.9 kilometers
(999.9 miles) before it rolls over to zero. The odome-
ter display does not have a decimal point and will
not show values less than a full unit (kilometer or
mile), the trip odometer display does have a decimal
point and will show tenths of a unit (kilometer or
mile).
The unit of measure for the odometer and trip
odometer display is not shown in the VFD. The unit
of measure for the odometer/trip odometer is selected
at the time that the instrument cluster is manufac-
tured, and cannot be changed. If the instrument clus-
ter has a kilometers-per-hour primary speedometer
scale, the odometer/trip odometer registers kilome-
ters; and, if the cluster features a miles-per-hour pri-
mary speedometer scale, the odometer/trip odometer
registers miles.
During daylight hours (exterior lamps Off) the
VFD is illuminated at full brightness for clear visibil-
ity. At night (exterior lamps are On) the instrument
cluster converts an electronic dimming level message
received from the Body Control Module (BCM) over
the Programmable Communications Interface (PCI)
data bus to a digital dimming level signal for control-
ling the lighting level of the VFD. However, a
ªParadeº mode position of the panel lamps dimmer
control ring on the control stalk of the left (lighting)
multi-function switch allows the VFD to be illumi-
8J - 24 INSTRUMENT CLUSTERWJ
MALFUNCTION INDICATOR LAMP (MIL) (Continued)
Page 445 of 2199
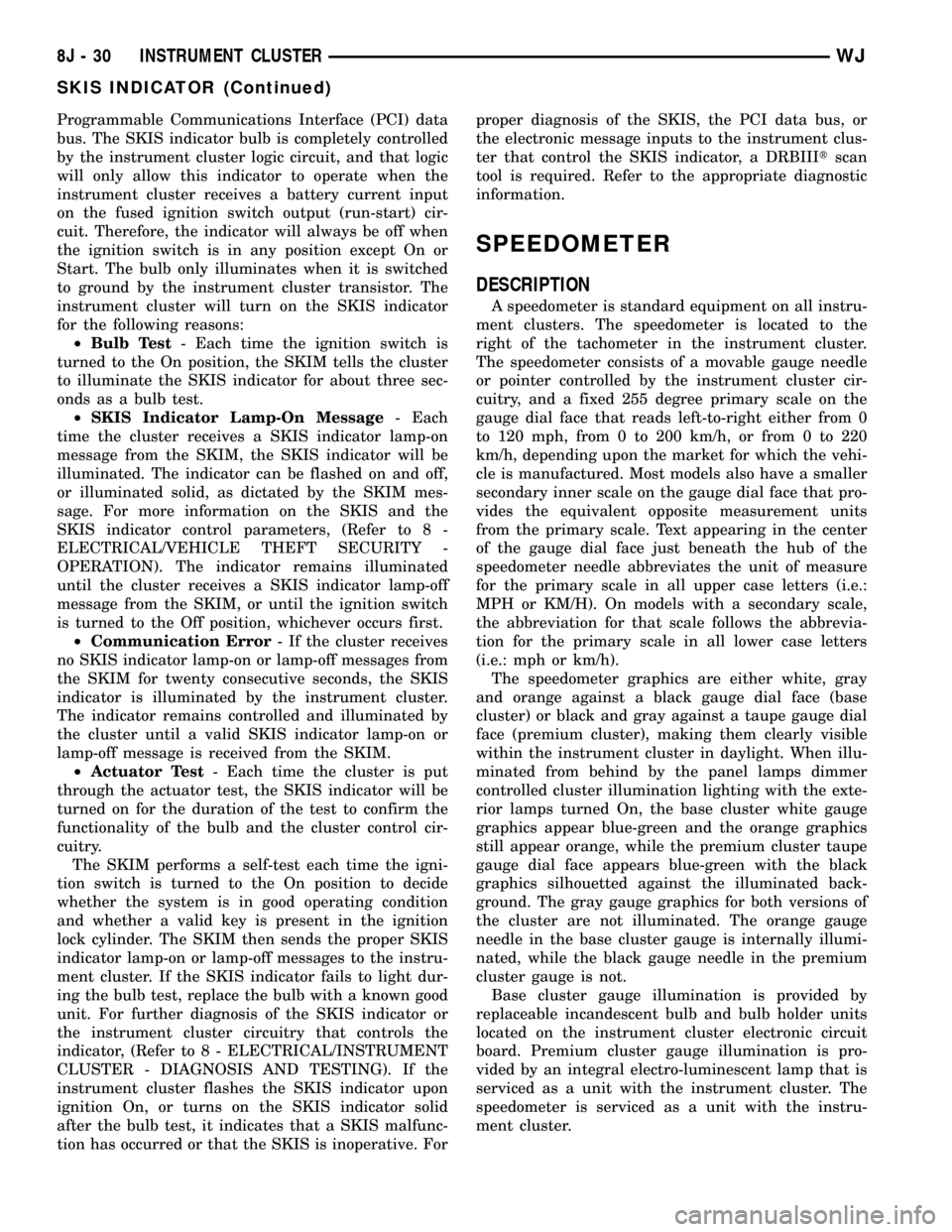
Programmable Communications Interface (PCI) data
bus. The SKIS indicator bulb is completely controlled
by the instrument cluster logic circuit, and that logic
will only allow this indicator to operate when the
instrument cluster receives a battery current input
on the fused ignition switch output (run-start) cir-
cuit. Therefore, the indicator will always be off when
the ignition switch is in any position except On or
Start. The bulb only illuminates when it is switched
to ground by the instrument cluster transistor. The
instrument cluster will turn on the SKIS indicator
for the following reasons:
²Bulb Test- Each time the ignition switch is
turned to the On position, the SKIM tells the cluster
to illuminate the SKIS indicator for about three sec-
onds as a bulb test.
²SKIS Indicator Lamp-On Message- Each
time the cluster receives a SKIS indicator lamp-on
message from the SKIM, the SKIS indicator will be
illuminated. The indicator can be flashed on and off,
or illuminated solid, as dictated by the SKIM mes-
sage. For more information on the SKIS and the
SKIS indicator control parameters, (Refer to 8 -
ELECTRICAL/VEHICLE THEFT SECURITY -
OPERATION). The indicator remains illuminated
until the cluster receives a SKIS indicator lamp-off
message from the SKIM, or until the ignition switch
is turned to the Off position, whichever occurs first.
²Communication Error- If the cluster receives
no SKIS indicator lamp-on or lamp-off messages from
the SKIM for twenty consecutive seconds, the SKIS
indicator is illuminated by the instrument cluster.
The indicator remains controlled and illuminated by
the cluster until a valid SKIS indicator lamp-on or
lamp-off message is received from the SKIM.
²Actuator Test- Each time the cluster is put
through the actuator test, the SKIS indicator will be
turned on for the duration of the test to confirm the
functionality of the bulb and the cluster control cir-
cuitry.
The SKIM performs a self-test each time the igni-
tion switch is turned to the On position to decide
whether the system is in good operating condition
and whether a valid key is present in the ignition
lock cylinder. The SKIM then sends the proper SKIS
indicator lamp-on or lamp-off messages to the instru-
ment cluster. If the SKIS indicator fails to light dur-
ing the bulb test, replace the bulb with a known good
unit. For further diagnosis of the SKIS indicator or
the instrument cluster circuitry that controls the
indicator, (Refer to 8 - ELECTRICAL/INSTRUMENT
CLUSTER - DIAGNOSIS AND TESTING). If the
instrument cluster flashes the SKIS indicator upon
ignition On, or turns on the SKIS indicator solid
after the bulb test, it indicates that a SKIS malfunc-
tion has occurred or that the SKIS is inoperative. Forproper diagnosis of the SKIS, the PCI data bus, or
the electronic message inputs to the instrument clus-
ter that control the SKIS indicator, a DRBIIItscan
tool is required. Refer to the appropriate diagnostic
information.
SPEEDOMETER
DESCRIPTION
A speedometer is standard equipment on all instru-
ment clusters. The speedometer is located to the
right of the tachometer in the instrument cluster.
The speedometer consists of a movable gauge needle
or pointer controlled by the instrument cluster cir-
cuitry, and a fixed 255 degree primary scale on the
gauge dial face that reads left-to-right either from 0
to 120 mph, from 0 to 200 km/h, or from 0 to 220
km/h, depending upon the market for which the vehi-
cle is manufactured. Most models also have a smaller
secondary inner scale on the gauge dial face that pro-
vides the equivalent opposite measurement units
from the primary scale. Text appearing in the center
of the gauge dial face just beneath the hub of the
speedometer needle abbreviates the unit of measure
for the primary scale in all upper case letters (i.e.:
MPH or KM/H). On models with a secondary scale,
the abbreviation for that scale follows the abbrevia-
tion for the primary scale in all lower case letters
(i.e.: mph or km/h).
The speedometer graphics are either white, gray
and orange against a black gauge dial face (base
cluster) or black and gray against a taupe gauge dial
face (premium cluster), making them clearly visible
within the instrument cluster in daylight. When illu-
minated from behind by the panel lamps dimmer
controlled cluster illumination lighting with the exte-
rior lamps turned On, the base cluster white gauge
graphics appear blue-green and the orange graphics
still appear orange, while the premium cluster taupe
gauge dial face appears blue-green with the black
graphics silhouetted against the illuminated back-
ground. The gray gauge graphics for both versions of
the cluster are not illuminated. The orange gauge
needle in the base cluster gauge is internally illumi-
nated, while the black gauge needle in the premium
cluster gauge is not.
Base cluster gauge illumination is provided by
replaceable incandescent bulb and bulb holder units
located on the instrument cluster electronic circuit
board. Premium cluster gauge illumination is pro-
vided by an integral electro-luminescent lamp that is
serviced as a unit with the instrument cluster. The
speedometer is serviced as a unit with the instru-
ment cluster.
8J - 30 INSTRUMENT CLUSTERWJ
SKIS INDICATOR (Continued)
Page 453 of 2199
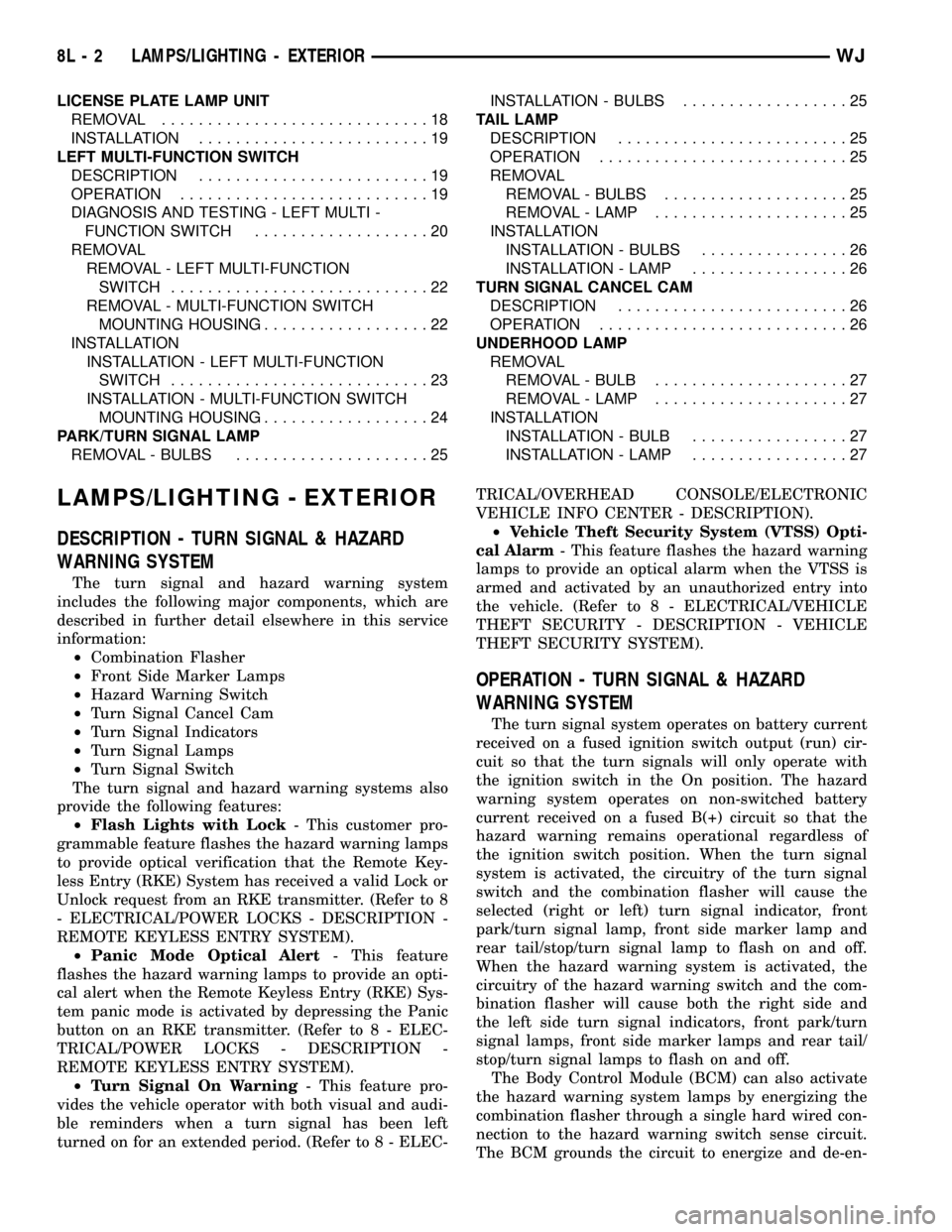
LICENSE PLATE LAMP UNIT
REMOVAL.............................18
INSTALLATION.........................19
LEFT MULTI-FUNCTION SWITCH
DESCRIPTION.........................19
OPERATION...........................19
DIAGNOSIS AND TESTING - LEFT MULTI -
FUNCTION SWITCH...................20
REMOVAL
REMOVAL - LEFT MULTI-FUNCTION
SWITCH............................22
REMOVAL - MULTI-FUNCTION SWITCH
MOUNTING HOUSING..................22
INSTALLATION
INSTALLATION - LEFT MULTI-FUNCTION
SWITCH............................23
INSTALLATION - MULTI-FUNCTION SWITCH
MOUNTING HOUSING..................24
PARK/TURN SIGNAL LAMP
REMOVAL - BULBS.....................25INSTALLATION - BULBS..................25
TAIL LAMP
DESCRIPTION.........................25
OPERATION...........................25
REMOVAL
REMOVAL - BULBS....................25
REMOVAL - LAMP.....................25
INSTALLATION
INSTALLATION - BULBS................26
INSTALLATION - LAMP.................26
TURN SIGNAL CANCEL CAM
DESCRIPTION.........................26
OPERATION...........................26
UNDERHOOD LAMP
REMOVAL
REMOVAL - BULB.....................27
REMOVAL - LAMP.....................27
INSTALLATION
INSTALLATION - BULB.................27
INSTALLATION - LAMP.................27
LAMPS/LIGHTING - EXTERIOR
DESCRIPTION - TURN SIGNAL & HAZARD
WARNING SYSTEM
The turn signal and hazard warning system
includes the following major components, which are
described in further detail elsewhere in this service
information:
²Combination Flasher
²Front Side Marker Lamps
²Hazard Warning Switch
²Turn Signal Cancel Cam
²Turn Signal Indicators
²Turn Signal Lamps
²Turn Signal Switch
The turn signal and hazard warning systems also
provide the following features:
²Flash Lights with Lock- This customer pro-
grammable feature flashes the hazard warning lamps
to provide optical verification that the Remote Key-
less Entry (RKE) System has received a valid Lock or
Unlock request from an RKE transmitter. (Refer to 8
- ELECTRICAL/POWER LOCKS - DESCRIPTION -
REMOTE KEYLESS ENTRY SYSTEM).
²Panic Mode Optical Alert- This feature
flashes the hazard warning lamps to provide an opti-
cal alert when the Remote Keyless Entry (RKE) Sys-
tem panic mode is activated by depressing the Panic
button on an RKE transmitter. (Refer to 8 - ELEC-
TRICAL/POWER LOCKS - DESCRIPTION -
REMOTE KEYLESS ENTRY SYSTEM).
²Turn Signal On Warning- This feature pro-
vides the vehicle operator with both visual and audi-
ble reminders when a turn signal has been left
turned on for an extended period. (Refer to 8 - ELEC-TRICAL/OVERHEAD CONSOLE/ELECTRONIC
VEHICLE INFO CENTER - DESCRIPTION).
²Vehicle Theft Security System (VTSS) Opti-
cal Alarm- This feature flashes the hazard warning
lamps to provide an optical alarm when the VTSS is
armed and activated by an unauthorized entry into
the vehicle. (Refer to 8 - ELECTRICAL/VEHICLE
THEFT SECURITY - DESCRIPTION - VEHICLE
THEFT SECURITY SYSTEM).
OPERATION - TURN SIGNAL & HAZARD
WARNING SYSTEM
The turn signal system operates on battery current
received on a fused ignition switch output (run) cir-
cuit so that the turn signals will only operate with
the ignition switch in the On position. The hazard
warning system operates on non-switched battery
current received on a fused B(+) circuit so that the
hazard warning remains operational regardless of
the ignition switch position. When the turn signal
system is activated, the circuitry of the turn signal
switch and the combination flasher will cause the
selected (right or left) turn signal indicator, front
park/turn signal lamp, front side marker lamp and
rear tail/stop/turn signal lamp to flash on and off.
When the hazard warning system is activated, the
circuitry of the hazard warning switch and the com-
bination flasher will cause both the right side and
the left side turn signal indicators, front park/turn
signal lamps, front side marker lamps and rear tail/
stop/turn signal lamps to flash on and off.
The Body Control Module (BCM) can also activate
the hazard warning system lamps by energizing the
combination flasher through a single hard wired con-
nection to the hazard warning switch sense circuit.
The BCM grounds the circuit to energize and de-en-
8L - 2 LAMPS/LIGHTING - EXTERIORWJ
Page 460 of 2199
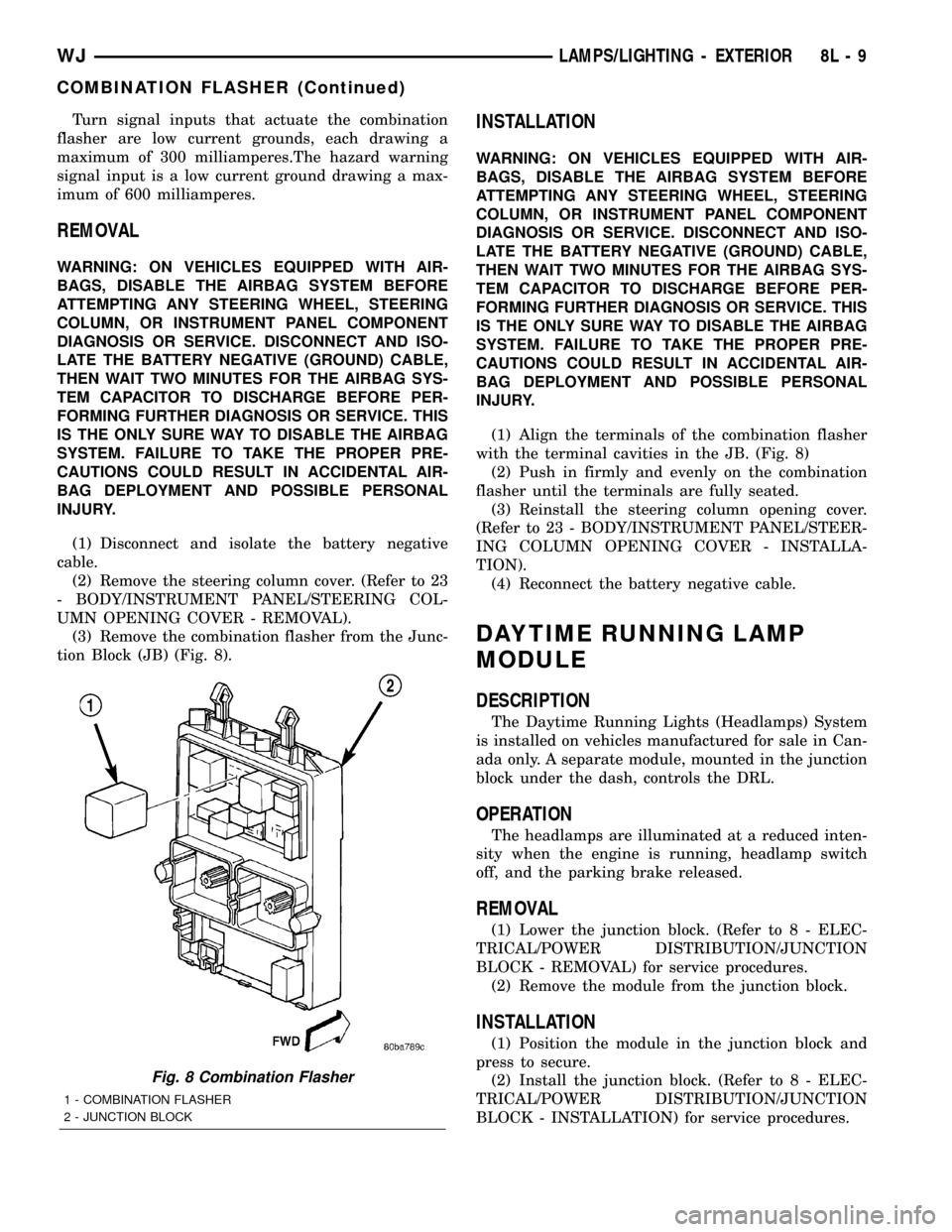
Turn signal inputs that actuate the combination
flasher are low current grounds, each drawing a
maximum of 300 milliamperes.The hazard warning
signal input is a low current ground drawing a max-
imum of 600 milliamperes.
REMOVAL
WARNING: ON VEHICLES EQUIPPED WITH AIR-
BAGS, DISABLE THE AIRBAG SYSTEM BEFORE
ATTEMPTING ANY STEERING WHEEL, STEERING
COLUMN, OR INSTRUMENT PANEL COMPONENT
DIAGNOSIS OR SERVICE. DISCONNECT AND ISO-
LATE THE BATTERY NEGATIVE (GROUND) CABLE,
THEN WAIT TWO MINUTES FOR THE AIRBAG SYS-
TEM CAPACITOR TO DISCHARGE BEFORE PER-
FORMING FURTHER DIAGNOSIS OR SERVICE. THIS
IS THE ONLY SURE WAY TO DISABLE THE AIRBAG
SYSTEM. FAILURE TO TAKE THE PROPER PRE-
CAUTIONS COULD RESULT IN ACCIDENTAL AIR-
BAG DEPLOYMENT AND POSSIBLE PERSONAL
INJURY.
(1) Disconnect and isolate the battery negative
cable.
(2) Remove the steering column cover. (Refer to 23
- BODY/INSTRUMENT PANEL/STEERING COL-
UMN OPENING COVER - REMOVAL).
(3) Remove the combination flasher from the Junc-
tion Block (JB) (Fig. 8).
INSTALLATION
WARNING: ON VEHICLES EQUIPPED WITH AIR-
BAGS, DISABLE THE AIRBAG SYSTEM BEFORE
ATTEMPTING ANY STEERING WHEEL, STEERING
COLUMN, OR INSTRUMENT PANEL COMPONENT
DIAGNOSIS OR SERVICE. DISCONNECT AND ISO-
LATE THE BATTERY NEGATIVE (GROUND) CABLE,
THEN WAIT TWO MINUTES FOR THE AIRBAG SYS-
TEM CAPACITOR TO DISCHARGE BEFORE PER-
FORMING FURTHER DIAGNOSIS OR SERVICE. THIS
IS THE ONLY SURE WAY TO DISABLE THE AIRBAG
SYSTEM. FAILURE TO TAKE THE PROPER PRE-
CAUTIONS COULD RESULT IN ACCIDENTAL AIR-
BAG DEPLOYMENT AND POSSIBLE PERSONAL
INJURY.
(1) Align the terminals of the combination flasher
with the terminal cavities in the JB. (Fig. 8)
(2) Push in firmly and evenly on the combination
flasher until the terminals are fully seated.
(3) Reinstall the steering column opening cover.
(Refer to 23 - BODY/INSTRUMENT PANEL/STEER-
ING COLUMN OPENING COVER - INSTALLA-
TION).
(4) Reconnect the battery negative cable.
DAYTIME RUNNING LAMP
MODULE
DESCRIPTION
The Daytime Running Lights (Headlamps) System
is installed on vehicles manufactured for sale in Can-
ada only. A separate module, mounted in the junction
block under the dash, controls the DRL.
OPERATION
The headlamps are illuminated at a reduced inten-
sity when the engine is running, headlamp switch
off, and the parking brake released.
REMOVAL
(1) Lower the junction block. (Refer to 8 - ELEC-
TRICAL/POWER DISTRIBUTION/JUNCTION
BLOCK - REMOVAL) for service procedures.
(2) Remove the module from the junction block.
INSTALLATION
(1) Position the module in the junction block and
press to secure.
(2) Install the junction block. (Refer to 8 - ELEC-
TRICAL/POWER DISTRIBUTION/JUNCTION
BLOCK - INSTALLATION) for service procedures.
Fig. 8 Combination Flasher
1 - COMBINATION FLASHER
2 - JUNCTION BLOCK
WJLAMPS/LIGHTING - EXTERIOR 8L - 9
COMBINATION FLASHER (Continued)
Page 463 of 2199
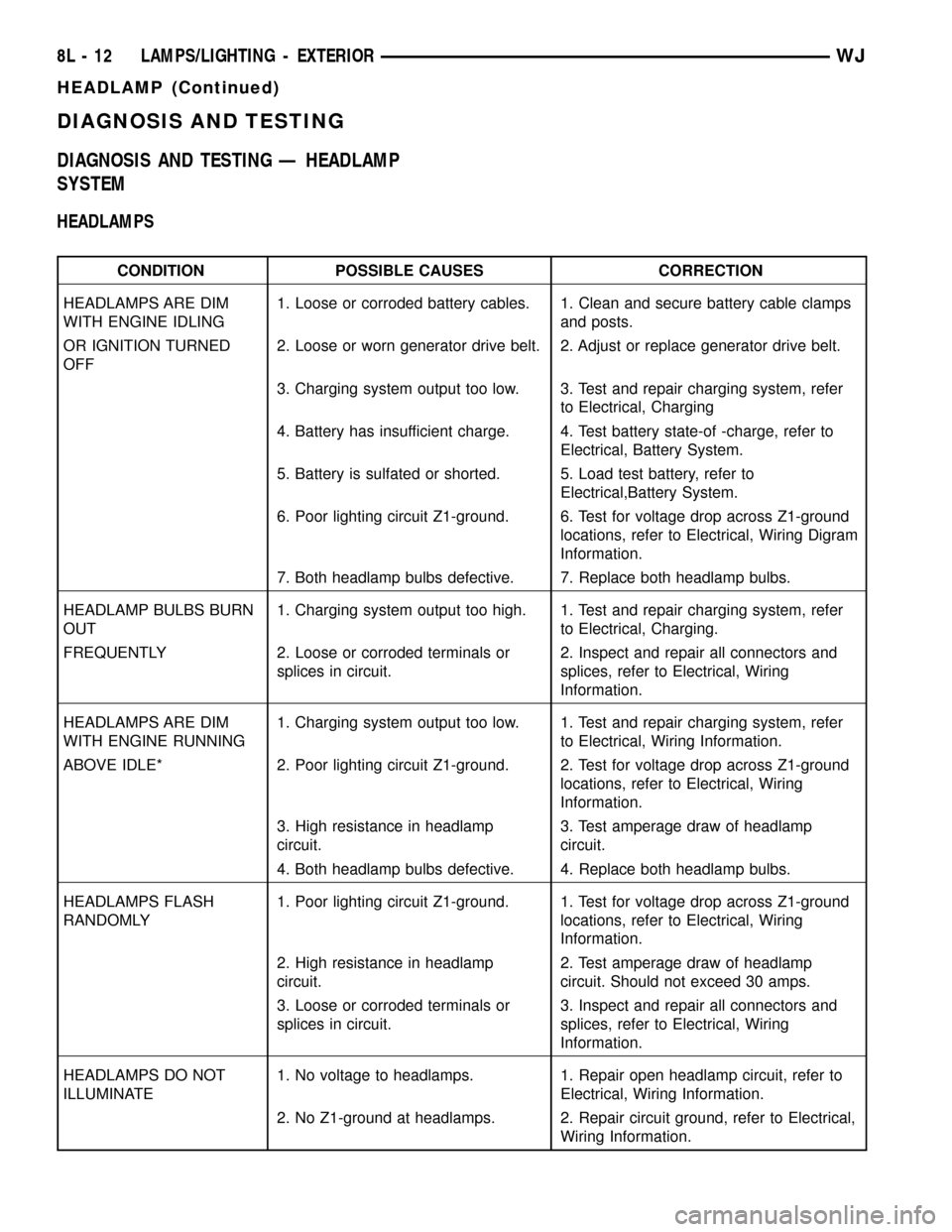
DIAGNOSIS AND TESTING
DIAGNOSIS AND TESTING Ð HEADLAMP
SYSTEM
HEADLAMPS
CONDITION POSSIBLE CAUSES CORRECTION
HEADLAMPS ARE DIM
WITH ENGINE IDLING1. Loose or corroded battery cables. 1. Clean and secure battery cable clamps
and posts.
OR IGNITION TURNED
OFF2. Loose or worn generator drive belt. 2. Adjust or replace generator drive belt.
3. Charging system output too low. 3. Test and repair charging system, refer
to Electrical, Charging
4. Battery has insufficient charge. 4. Test battery state-of -charge, refer to
Electrical, Battery System.
5. Battery is sulfated or shorted. 5. Load test battery, refer to
Electrical,Battery System.
6. Poor lighting circuit Z1-ground. 6. Test for voltage drop across Z1-ground
locations, refer to Electrical, Wiring Digram
Information.
7. Both headlamp bulbs defective. 7. Replace both headlamp bulbs.
HEADLAMP BULBS BURN
OUT1. Charging system output too high. 1. Test and repair charging system, refer
to Electrical, Charging.
FREQUENTLY 2. Loose or corroded terminals or
splices in circuit.2. Inspect and repair all connectors and
splices, refer to Electrical, Wiring
Information.
HEADLAMPS ARE DIM
WITH ENGINE RUNNING1. Charging system output too low. 1. Test and repair charging system, refer
to Electrical, Wiring Information.
ABOVE IDLE* 2. Poor lighting circuit Z1-ground. 2. Test for voltage drop across Z1-ground
locations, refer to Electrical, Wiring
Information.
3. High resistance in headlamp
circuit.3. Test amperage draw of headlamp
circuit.
4. Both headlamp bulbs defective. 4. Replace both headlamp bulbs.
HEADLAMPS FLASH
RANDOMLY1. Poor lighting circuit Z1-ground. 1. Test for voltage drop across Z1-ground
locations, refer to Electrical, Wiring
Information.
2. High resistance in headlamp
circuit.2. Test amperage draw of headlamp
circuit. Should not exceed 30 amps.
3. Loose or corroded terminals or
splices in circuit.3. Inspect and repair all connectors and
splices, refer to Electrical, Wiring
Information.
HEADLAMPS DO NOT
ILLUMINATE1. No voltage to headlamps. 1. Repair open headlamp circuit, refer to
Electrical, Wiring Information.
2. No Z1-ground at headlamps. 2. Repair circuit ground, refer to Electrical,
Wiring Information.
8L - 12 LAMPS/LIGHTING - EXTERIORWJ
HEADLAMP (Continued)
Page 464 of 2199
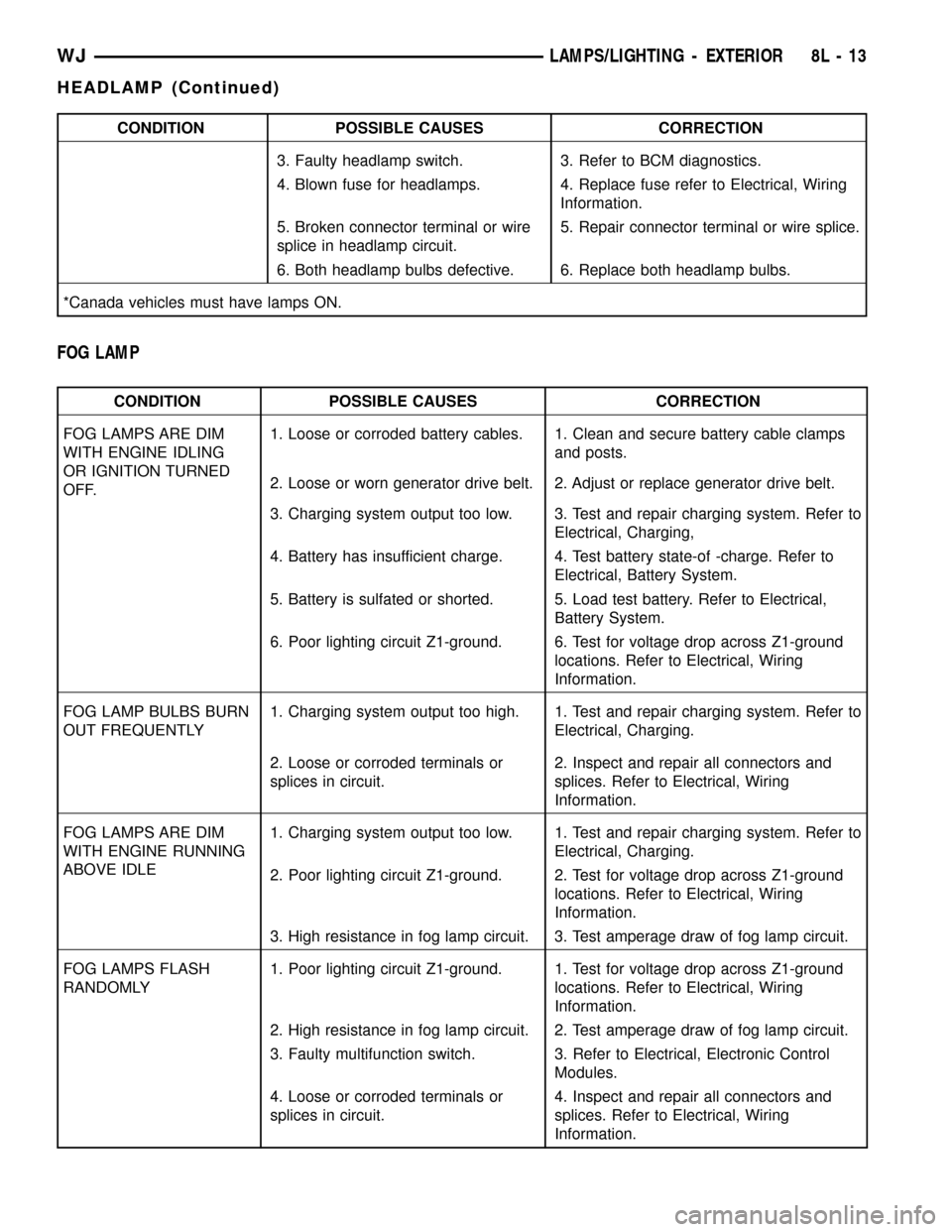
CONDITION POSSIBLE CAUSES CORRECTION
3. Faulty headlamp switch. 3. Refer to BCM diagnostics.
4. Blown fuse for headlamps. 4. Replace fuse refer to Electrical, Wiring
Information.
5. Broken connector terminal or wire
splice in headlamp circuit.5. Repair connector terminal or wire splice.
6. Both headlamp bulbs defective. 6. Replace both headlamp bulbs.
*Canada vehicles must have lamps ON.
FOG LAMP
CONDITION POSSIBLE CAUSES CORRECTION
FOG LAMPS ARE DIM
WITH ENGINE IDLING
OR IGNITION TURNED
OFF.1. Loose or corroded battery cables. 1. Clean and secure battery cable clamps
and posts.
2. Loose or worn generator drive belt. 2. Adjust or replace generator drive belt.
3. Charging system output too low. 3. Test and repair charging system. Refer to
Electrical, Charging,
4. Battery has insufficient charge. 4. Test battery state-of -charge. Refer to
Electrical, Battery System.
5. Battery is sulfated or shorted. 5. Load test battery. Refer to Electrical,
Battery System.
6. Poor lighting circuit Z1-ground. 6. Test for voltage drop across Z1-ground
locations. Refer to Electrical, Wiring
Information.
FOG LAMP BULBS BURN
OUT FREQUENTLY1. Charging system output too high. 1. Test and repair charging system. Refer to
Electrical, Charging.
2. Loose or corroded terminals or
splices in circuit.2. Inspect and repair all connectors and
splices. Refer to Electrical, Wiring
Information.
FOG LAMPS ARE DIM
WITH ENGINE RUNNING
ABOVE IDLE1. Charging system output too low. 1. Test and repair charging system. Refer to
Electrical, Charging.
2. Poor lighting circuit Z1-ground. 2. Test for voltage drop across Z1-ground
locations. Refer to Electrical, Wiring
Information.
3. High resistance in fog lamp circuit. 3. Test amperage draw of fog lamp circuit.
FOG LAMPS FLASH
RANDOMLY1. Poor lighting circuit Z1-ground. 1. Test for voltage drop across Z1-ground
locations. Refer to Electrical, Wiring
Information.
2. High resistance in fog lamp circuit. 2. Test amperage draw of fog lamp circuit.
3. Faulty multifunction switch. 3. Refer to Electrical, Electronic Control
Modules.
4. Loose or corroded terminals or
splices in circuit.4. Inspect and repair all connectors and
splices. Refer to Electrical, Wiring
Information.
WJLAMPS/LIGHTING - EXTERIOR 8L - 13
HEADLAMP (Continued)
Page 465 of 2199
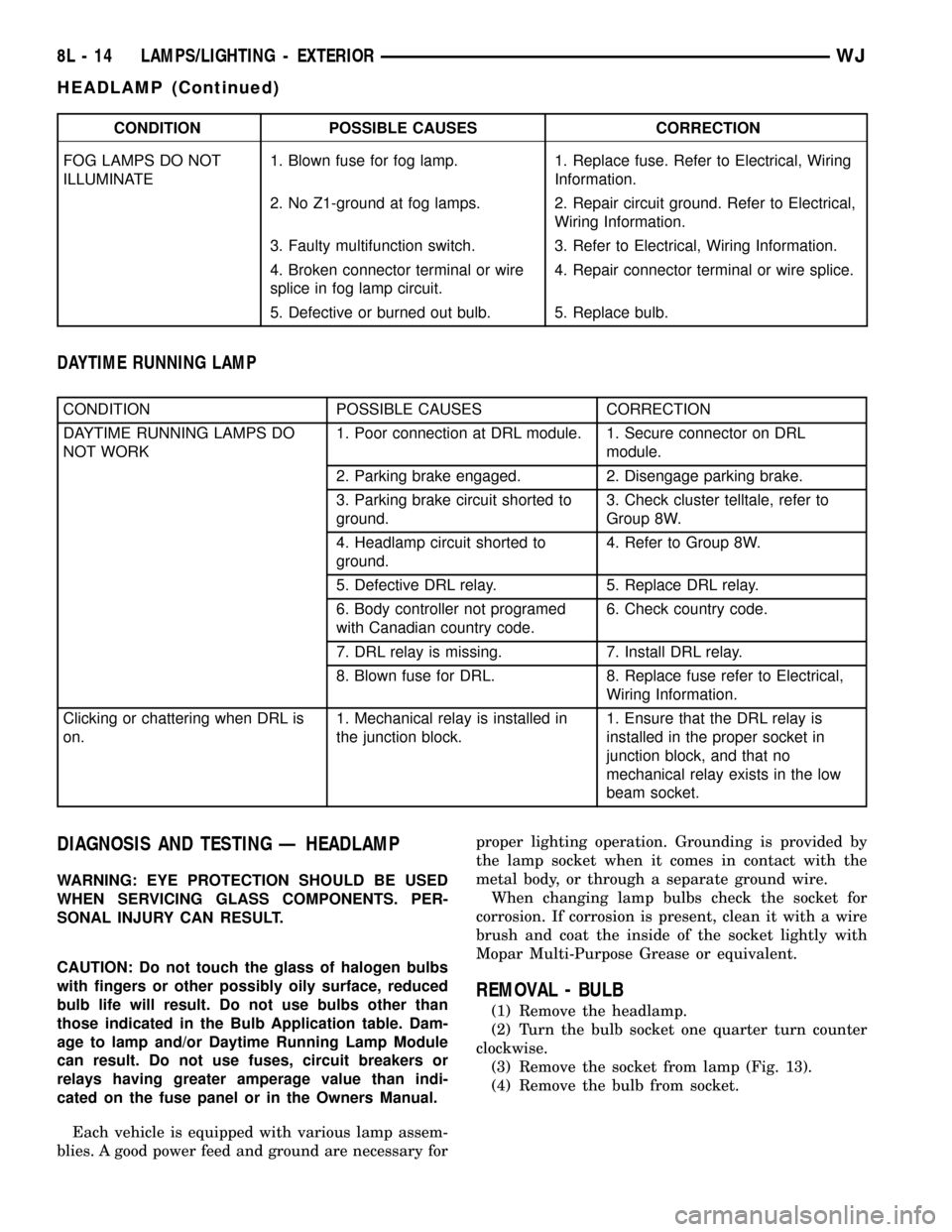
CONDITION POSSIBLE CAUSES CORRECTION
FOG LAMPS DO NOT
ILLUMINATE1. Blown fuse for fog lamp. 1. Replace fuse. Refer to Electrical, Wiring
Information.
2. No Z1-ground at fog lamps. 2. Repair circuit ground. Refer to Electrical,
Wiring Information.
3. Faulty multifunction switch. 3. Refer to Electrical, Wiring Information.
4. Broken connector terminal or wire
splice in fog lamp circuit.4. Repair connector terminal or wire splice.
5. Defective or burned out bulb. 5. Replace bulb.
DAYTIME RUNNING LAMP
CONDITION POSSIBLE CAUSES CORRECTION
DAYTIME RUNNING LAMPS DO
NOT WORK1. Poor connection at DRL module. 1. Secure connector on DRL
module.
2. Parking brake engaged. 2. Disengage parking brake.
3. Parking brake circuit shorted to
ground.3. Check cluster telltale, refer to
Group 8W.
4. Headlamp circuit shorted to
ground.4. Refer to Group 8W.
5. Defective DRL relay. 5. Replace DRL relay.
6. Body controller not programed
with Canadian country code.6. Check country code.
7. DRL relay is missing. 7. Install DRL relay.
8. Blown fuse for DRL. 8. Replace fuse refer to Electrical,
Wiring Information.
Clicking or chattering when DRL is
on.1. Mechanical relay is installed in
the junction block.1. Ensure that the DRL relay is
installed in the proper socket in
junction block, and that no
mechanical relay exists in the low
beam socket.
DIAGNOSIS AND TESTING Ð HEADLAMP
WARNING: EYE PROTECTION SHOULD BE USED
WHEN SERVICING GLASS COMPONENTS. PER-
SONAL INJURY CAN RESULT.
CAUTION: Do not touch the glass of halogen bulbs
with fingers or other possibly oily surface, reduced
bulb life will result. Do not use bulbs other than
those indicated in the Bulb Application table. Dam-
age to lamp and/or Daytime Running Lamp Module
can result. Do not use fuses, circuit breakers or
relays having greater amperage value than indi-
cated on the fuse panel or in the Owners Manual.
Each vehicle is equipped with various lamp assem-
blies. A good power feed and ground are necessary forproper lighting operation. Grounding is provided by
the lamp socket when it comes in contact with the
metal body, or through a separate ground wire.
When changing lamp bulbs check the socket for
corrosion. If corrosion is present, clean it with a wire
brush and coat the inside of the socket lightly with
Mopar Multi-Purpose Grease or equivalent.
REMOVAL - BULB
(1) Remove the headlamp.
(2) Turn the bulb socket one quarter turn counter
clockwise.
(3) Remove the socket from lamp (Fig. 13).
(4) Remove the bulb from socket.
8L - 14 LAMPS/LIGHTING - EXTERIORWJ
HEADLAMP (Continued)