Message JEEP GRAND CHEROKEE 2002 WJ / 2.G Manual PDF
[x] Cancel search | Manufacturer: JEEP, Model Year: 2002, Model line: GRAND CHEROKEE, Model: JEEP GRAND CHEROKEE 2002 WJ / 2.GPages: 2199, PDF Size: 76.01 MB
Page 502 of 2199
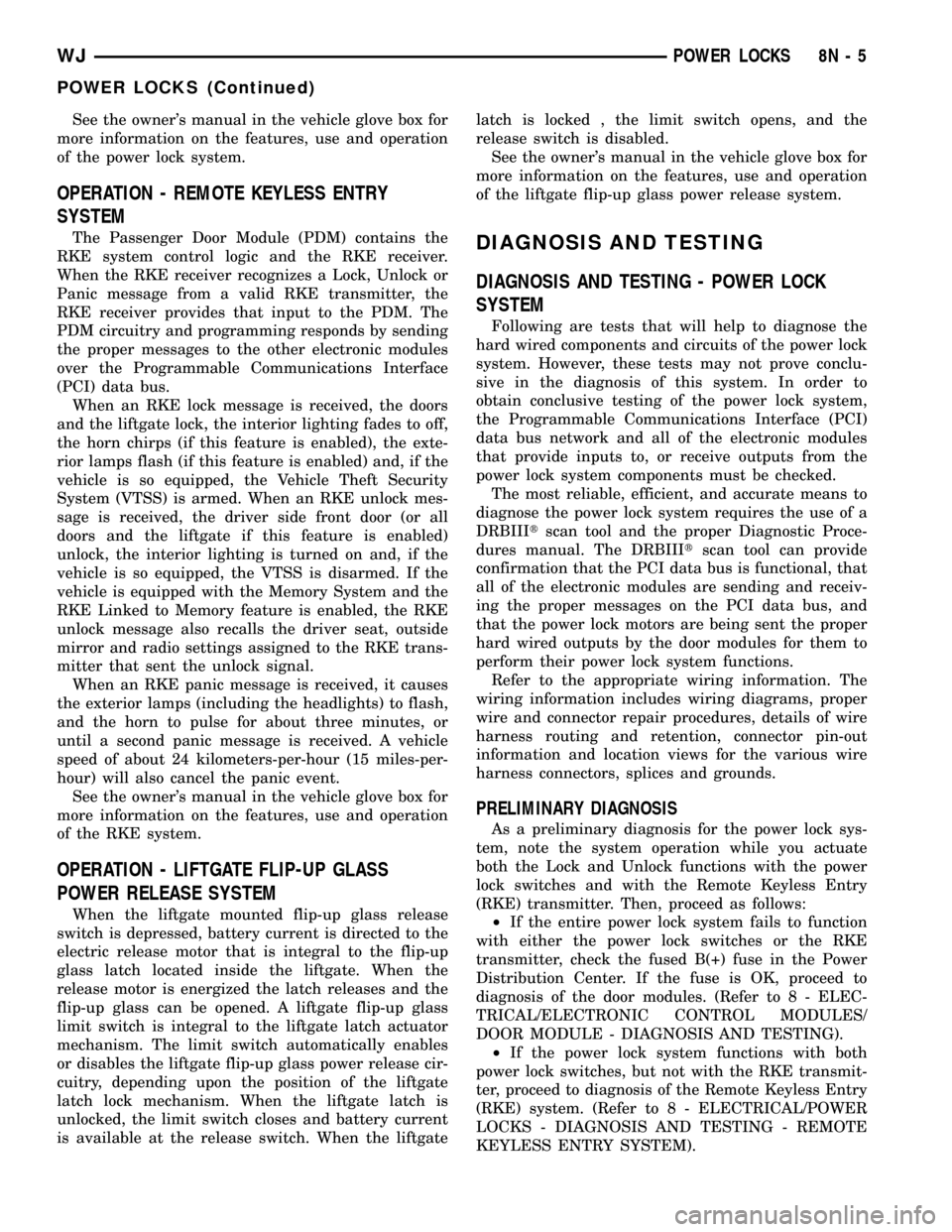
See the owner's manual in the vehicle glove box for
more information on the features, use and operation
of the power lock system.
OPERATION - REMOTE KEYLESS ENTRY
SYSTEM
The Passenger Door Module (PDM) contains the
RKE system control logic and the RKE receiver.
When the RKE receiver recognizes a Lock, Unlock or
Panic message from a valid RKE transmitter, the
RKE receiver provides that input to the PDM. The
PDM circuitry and programming responds by sending
the proper messages to the other electronic modules
over the Programmable Communications Interface
(PCI) data bus.
When an RKE lock message is received, the doors
and the liftgate lock, the interior lighting fades to off,
the horn chirps (if this feature is enabled), the exte-
rior lamps flash (if this feature is enabled) and, if the
vehicle is so equipped, the Vehicle Theft Security
System (VTSS) is armed. When an RKE unlock mes-
sage is received, the driver side front door (or all
doors and the liftgate if this feature is enabled)
unlock, the interior lighting is turned on and, if the
vehicle is so equipped, the VTSS is disarmed. If the
vehicle is equipped with the Memory System and the
RKE Linked to Memory feature is enabled, the RKE
unlock message also recalls the driver seat, outside
mirror and radio settings assigned to the RKE trans-
mitter that sent the unlock signal.
When an RKE panic message is received, it causes
the exterior lamps (including the headlights) to flash,
and the horn to pulse for about three minutes, or
until a second panic message is received. A vehicle
speed of about 24 kilometers-per-hour (15 miles-per-
hour) will also cancel the panic event.
See the owner's manual in the vehicle glove box for
more information on the features, use and operation
of the RKE system.
OPERATION - LIFTGATE FLIP-UP GLASS
POWER RELEASE SYSTEM
When the liftgate mounted flip-up glass release
switch is depressed, battery current is directed to the
electric release motor that is integral to the flip-up
glass latch located inside the liftgate. When the
release motor is energized the latch releases and the
flip-up glass can be opened. A liftgate flip-up glass
limit switch is integral to the liftgate latch actuator
mechanism. The limit switch automatically enables
or disables the liftgate flip-up glass power release cir-
cuitry, depending upon the position of the liftgate
latch lock mechanism. When the liftgate latch is
unlocked, the limit switch closes and battery current
is available at the release switch. When the liftgatelatch is locked , the limit switch opens, and the
release switch is disabled.
See the owner's manual in the vehicle glove box for
more information on the features, use and operation
of the liftgate flip-up glass power release system.
DIAGNOSIS AND TESTING
DIAGNOSIS AND TESTING - POWER LOCK
SYSTEM
Following are tests that will help to diagnose the
hard wired components and circuits of the power lock
system. However, these tests may not prove conclu-
sive in the diagnosis of this system. In order to
obtain conclusive testing of the power lock system,
the Programmable Communications Interface (PCI)
data bus network and all of the electronic modules
that provide inputs to, or receive outputs from the
power lock system components must be checked.
The most reliable, efficient, and accurate means to
diagnose the power lock system requires the use of a
DRBIIItscan tool and the proper Diagnostic Proce-
dures manual. The DRBIIItscan tool can provide
confirmation that the PCI data bus is functional, that
all of the electronic modules are sending and receiv-
ing the proper messages on the PCI data bus, and
that the power lock motors are being sent the proper
hard wired outputs by the door modules for them to
perform their power lock system functions.
Refer to the appropriate wiring information. The
wiring information includes wiring diagrams, proper
wire and connector repair procedures, details of wire
harness routing and retention, connector pin-out
information and location views for the various wire
harness connectors, splices and grounds.
PRELIMINARY DIAGNOSIS
As a preliminary diagnosis for the power lock sys-
tem, note the system operation while you actuate
both the Lock and Unlock functions with the power
lock switches and with the Remote Keyless Entry
(RKE) transmitter. Then, proceed as follows:
²If the entire power lock system fails to function
with either the power lock switches or the RKE
transmitter, check the fused B(+) fuse in the Power
Distribution Center. If the fuse is OK, proceed to
diagnosis of the door modules. (Refer to 8 - ELEC-
TRICAL/ELECTRONIC CONTROL MODULES/
DOOR MODULE - DIAGNOSIS AND TESTING).
²If the power lock system functions with both
power lock switches, but not with the RKE transmit-
ter, proceed to diagnosis of the Remote Keyless Entry
(RKE) system. (Refer to 8 - ELECTRICAL/POWER
LOCKS - DIAGNOSIS AND TESTING - REMOTE
KEYLESS ENTRY SYSTEM).
WJPOWER LOCKS 8N - 5
POWER LOCKS (Continued)
Page 503 of 2199
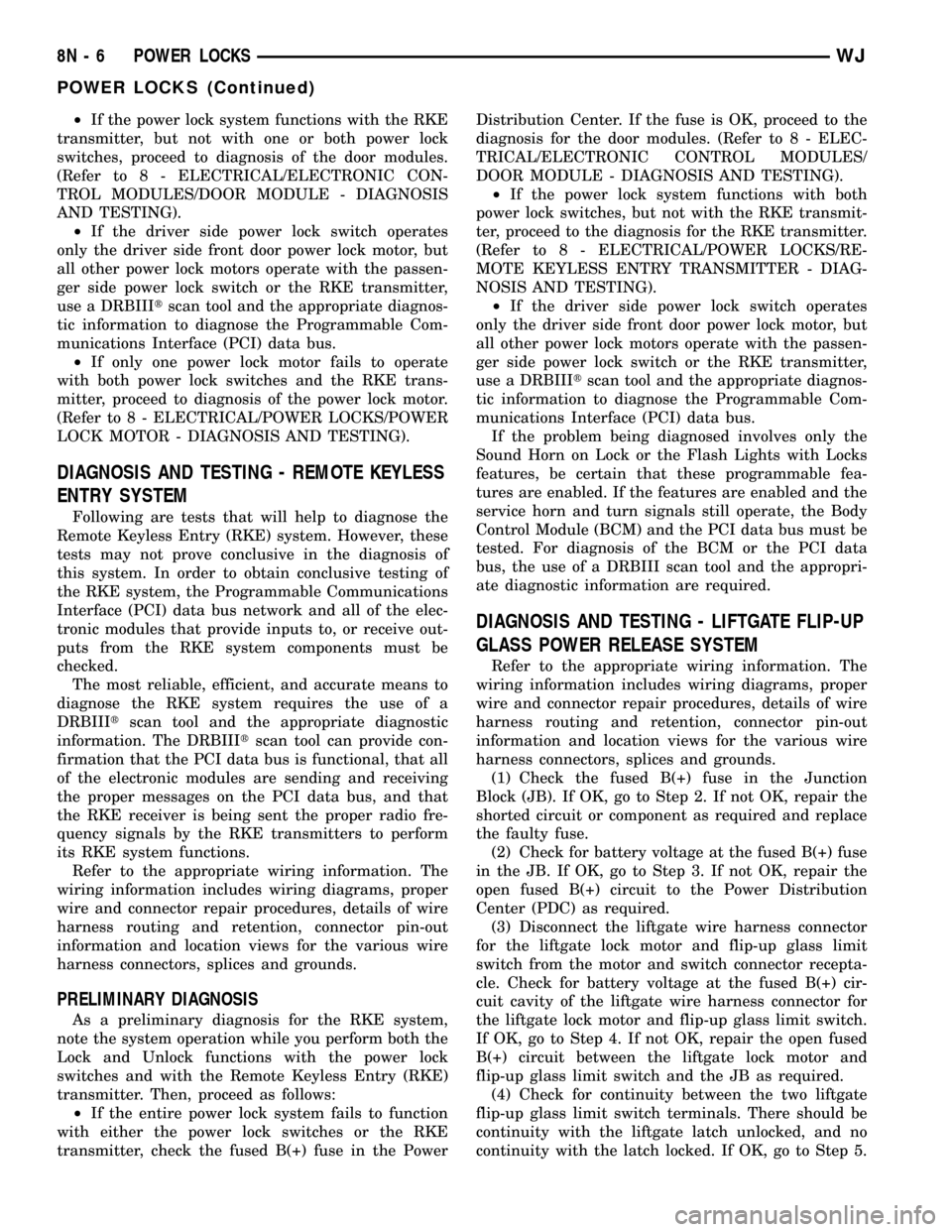
²If the power lock system functions with the RKE
transmitter, but not with one or both power lock
switches, proceed to diagnosis of the door modules.
(Refer to 8 - ELECTRICAL/ELECTRONIC CON-
TROL MODULES/DOOR MODULE - DIAGNOSIS
AND TESTING).
²If the driver side power lock switch operates
only the driver side front door power lock motor, but
all other power lock motors operate with the passen-
ger side power lock switch or the RKE transmitter,
use a DRBIIItscan tool and the appropriate diagnos-
tic information to diagnose the Programmable Com-
munications Interface (PCI) data bus.
²If only one power lock motor fails to operate
with both power lock switches and the RKE trans-
mitter, proceed to diagnosis of the power lock motor.
(Refer to 8 - ELECTRICAL/POWER LOCKS/POWER
LOCK MOTOR - DIAGNOSIS AND TESTING).
DIAGNOSIS AND TESTING - REMOTE KEYLESS
ENTRY SYSTEM
Following are tests that will help to diagnose the
Remote Keyless Entry (RKE) system. However, these
tests may not prove conclusive in the diagnosis of
this system. In order to obtain conclusive testing of
the RKE system, the Programmable Communications
Interface (PCI) data bus network and all of the elec-
tronic modules that provide inputs to, or receive out-
puts from the RKE system components must be
checked.
The most reliable, efficient, and accurate means to
diagnose the RKE system requires the use of a
DRBIIItscan tool and the appropriate diagnostic
information. The DRBIIItscan tool can provide con-
firmation that the PCI data bus is functional, that all
of the electronic modules are sending and receiving
the proper messages on the PCI data bus, and that
the RKE receiver is being sent the proper radio fre-
quency signals by the RKE transmitters to perform
its RKE system functions.
Refer to the appropriate wiring information. The
wiring information includes wiring diagrams, proper
wire and connector repair procedures, details of wire
harness routing and retention, connector pin-out
information and location views for the various wire
harness connectors, splices and grounds.
PRELIMINARY DIAGNOSIS
As a preliminary diagnosis for the RKE system,
note the system operation while you perform both the
Lock and Unlock functions with the power lock
switches and with the Remote Keyless Entry (RKE)
transmitter. Then, proceed as follows:
²If the entire power lock system fails to function
with either the power lock switches or the RKE
transmitter, check the fused B(+) fuse in the PowerDistribution Center. If the fuse is OK, proceed to the
diagnosis for the door modules. (Refer to 8 - ELEC-
TRICAL/ELECTRONIC CONTROL MODULES/
DOOR MODULE - DIAGNOSIS AND TESTING).
²If the power lock system functions with both
power lock switches, but not with the RKE transmit-
ter, proceed to the diagnosis for the RKE transmitter.
(Refer to 8 - ELECTRICAL/POWER LOCKS/RE-
MOTE KEYLESS ENTRY TRANSMITTER - DIAG-
NOSIS AND TESTING).
²If the driver side power lock switch operates
only the driver side front door power lock motor, but
all other power lock motors operate with the passen-
ger side power lock switch or the RKE transmitter,
use a DRBIIItscan tool and the appropriate diagnos-
tic information to diagnose the Programmable Com-
munications Interface (PCI) data bus.
If the problem being diagnosed involves only the
Sound Horn on Lock or the Flash Lights with Locks
features, be certain that these programmable fea-
tures are enabled. If the features are enabled and the
service horn and turn signals still operate, the Body
Control Module (BCM) and the PCI data bus must be
tested. For diagnosis of the BCM or the PCI data
bus, the use of a DRBIII scan tool and the appropri-
ate diagnostic information are required.
DIAGNOSIS AND TESTING - LIFTGATE FLIP-UP
GLASS POWER RELEASE SYSTEM
Refer to the appropriate wiring information. The
wiring information includes wiring diagrams, proper
wire and connector repair procedures, details of wire
harness routing and retention, connector pin-out
information and location views for the various wire
harness connectors, splices and grounds.
(1) Check the fused B(+) fuse in the Junction
Block (JB). If OK, go to Step 2. If not OK, repair the
shorted circuit or component as required and replace
the faulty fuse.
(2) Check for battery voltage at the fused B(+) fuse
in the JB. If OK, go to Step 3. If not OK, repair the
open fused B(+) circuit to the Power Distribution
Center (PDC) as required.
(3) Disconnect the liftgate wire harness connector
for the liftgate lock motor and flip-up glass limit
switch from the motor and switch connector recepta-
cle. Check for battery voltage at the fused B(+) cir-
cuit cavity of the liftgate wire harness connector for
the liftgate lock motor and flip-up glass limit switch.
If OK, go to Step 4. If not OK, repair the open fused
B(+) circuit between the liftgate lock motor and
flip-up glass limit switch and the JB as required.
(4) Check for continuity between the two liftgate
flip-up glass limit switch terminals. There should be
continuity with the liftgate latch unlocked, and no
continuity with the latch locked. If OK, go to Step 5.
8N - 6 POWER LOCKSWJ
POWER LOCKS (Continued)
Page 504 of 2199
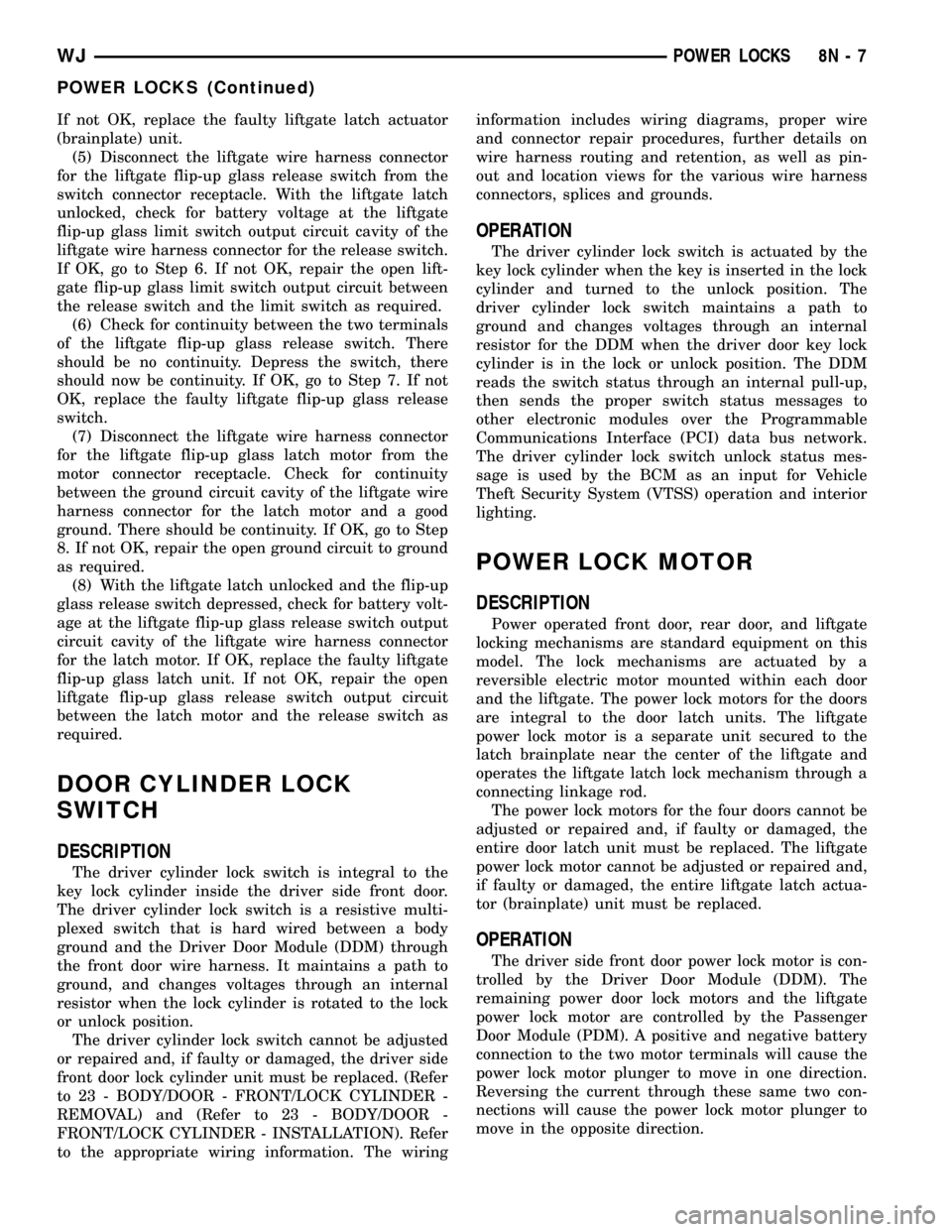
If not OK, replace the faulty liftgate latch actuator
(brainplate) unit.
(5) Disconnect the liftgate wire harness connector
for the liftgate flip-up glass release switch from the
switch connector receptacle. With the liftgate latch
unlocked, check for battery voltage at the liftgate
flip-up glass limit switch output circuit cavity of the
liftgate wire harness connector for the release switch.
If OK, go to Step 6. If not OK, repair the open lift-
gate flip-up glass limit switch output circuit between
the release switch and the limit switch as required.
(6) Check for continuity between the two terminals
of the liftgate flip-up glass release switch. There
should be no continuity. Depress the switch, there
should now be continuity. If OK, go to Step 7. If not
OK, replace the faulty liftgate flip-up glass release
switch.
(7) Disconnect the liftgate wire harness connector
for the liftgate flip-up glass latch motor from the
motor connector receptacle. Check for continuity
between the ground circuit cavity of the liftgate wire
harness connector for the latch motor and a good
ground. There should be continuity. If OK, go to Step
8. If not OK, repair the open ground circuit to ground
as required.
(8) With the liftgate latch unlocked and the flip-up
glass release switch depressed, check for battery volt-
age at the liftgate flip-up glass release switch output
circuit cavity of the liftgate wire harness connector
for the latch motor. If OK, replace the faulty liftgate
flip-up glass latch unit. If not OK, repair the open
liftgate flip-up glass release switch output circuit
between the latch motor and the release switch as
required.
DOOR CYLINDER LOCK
SWITCH
DESCRIPTION
The driver cylinder lock switch is integral to the
key lock cylinder inside the driver side front door.
The driver cylinder lock switch is a resistive multi-
plexed switch that is hard wired between a body
ground and the Driver Door Module (DDM) through
the front door wire harness. It maintains a path to
ground, and changes voltages through an internal
resistor when the lock cylinder is rotated to the lock
or unlock position.
The driver cylinder lock switch cannot be adjusted
or repaired and, if faulty or damaged, the driver side
front door lock cylinder unit must be replaced. (Refer
to 23 - BODY/DOOR - FRONT/LOCK CYLINDER -
REMOVAL) and (Refer to 23 - BODY/DOOR -
FRONT/LOCK CYLINDER - INSTALLATION). Refer
to the appropriate wiring information. The wiringinformation includes wiring diagrams, proper wire
and connector repair procedures, further details on
wire harness routing and retention, as well as pin-
out and location views for the various wire harness
connectors, splices and grounds.
OPERATION
The driver cylinder lock switch is actuated by the
key lock cylinder when the key is inserted in the lock
cylinder and turned to the unlock position. The
driver cylinder lock switch maintains a path to
ground and changes voltages through an internal
resistor for the DDM when the driver door key lock
cylinder is in the lock or unlock position. The DDM
reads the switch status through an internal pull-up,
then sends the proper switch status messages to
other electronic modules over the Programmable
Communications Interface (PCI) data bus network.
The driver cylinder lock switch unlock status mes-
sage is used by the BCM as an input for Vehicle
Theft Security System (VTSS) operation and interior
lighting.
POWER LOCK MOTOR
DESCRIPTION
Power operated front door, rear door, and liftgate
locking mechanisms are standard equipment on this
model. The lock mechanisms are actuated by a
reversible electric motor mounted within each door
and the liftgate. The power lock motors for the doors
are integral to the door latch units. The liftgate
power lock motor is a separate unit secured to the
latch brainplate near the center of the liftgate and
operates the liftgate latch lock mechanism through a
connecting linkage rod.
The power lock motors for the four doors cannot be
adjusted or repaired and, if faulty or damaged, the
entire door latch unit must be replaced. The liftgate
power lock motor cannot be adjusted or repaired and,
if faulty or damaged, the entire liftgate latch actua-
tor (brainplate) unit must be replaced.
OPERATION
The driver side front door power lock motor is con-
trolled by the Driver Door Module (DDM). The
remaining power door lock motors and the liftgate
power lock motor are controlled by the Passenger
Door Module (PDM). A positive and negative battery
connection to the two motor terminals will cause the
power lock motor plunger to move in one direction.
Reversing the current through these same two con-
nections will cause the power lock motor plunger to
move in the opposite direction.
WJPOWER LOCKS 8N - 7
POWER LOCKS (Continued)
Page 505 of 2199
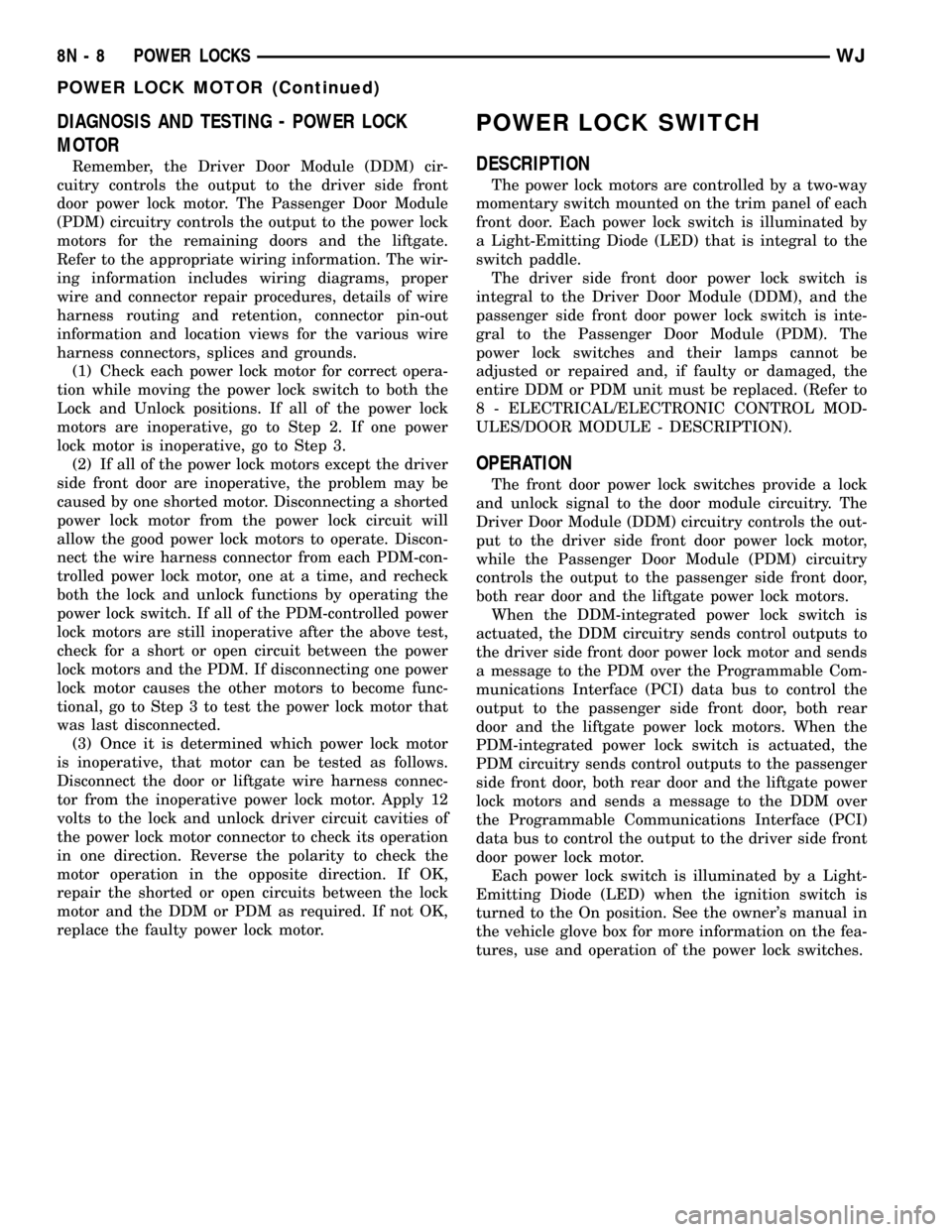
DIAGNOSIS AND TESTING - POWER LOCK
MOTOR
Remember, the Driver Door Module (DDM) cir-
cuitry controls the output to the driver side front
door power lock motor. The Passenger Door Module
(PDM) circuitry controls the output to the power lock
motors for the remaining doors and the liftgate.
Refer to the appropriate wiring information. The wir-
ing information includes wiring diagrams, proper
wire and connector repair procedures, details of wire
harness routing and retention, connector pin-out
information and location views for the various wire
harness connectors, splices and grounds.
(1) Check each power lock motor for correct opera-
tion while moving the power lock switch to both the
Lock and Unlock positions. If all of the power lock
motors are inoperative, go to Step 2. If one power
lock motor is inoperative, go to Step 3.
(2) If all of the power lock motors except the driver
side front door are inoperative, the problem may be
caused by one shorted motor. Disconnecting a shorted
power lock motor from the power lock circuit will
allow the good power lock motors to operate. Discon-
nect the wire harness connector from each PDM-con-
trolled power lock motor, one at a time, and recheck
both the lock and unlock functions by operating the
power lock switch. If all of the PDM-controlled power
lock motors are still inoperative after the above test,
check for a short or open circuit between the power
lock motors and the PDM. If disconnecting one power
lock motor causes the other motors to become func-
tional, go to Step 3 to test the power lock motor that
was last disconnected.
(3) Once it is determined which power lock motor
is inoperative, that motor can be tested as follows.
Disconnect the door or liftgate wire harness connec-
tor from the inoperative power lock motor. Apply 12
volts to the lock and unlock driver circuit cavities of
the power lock motor connector to check its operation
in one direction. Reverse the polarity to check the
motor operation in the opposite direction. If OK,
repair the shorted or open circuits between the lock
motor and the DDM or PDM as required. If not OK,
replace the faulty power lock motor.
POWER LOCK SWITCH
DESCRIPTION
The power lock motors are controlled by a two-way
momentary switch mounted on the trim panel of each
front door. Each power lock switch is illuminated by
a Light-Emitting Diode (LED) that is integral to the
switch paddle.
The driver side front door power lock switch is
integral to the Driver Door Module (DDM), and the
passenger side front door power lock switch is inte-
gral to the Passenger Door Module (PDM). The
power lock switches and their lamps cannot be
adjusted or repaired and, if faulty or damaged, the
entire DDM or PDM unit must be replaced. (Refer to
8 - ELECTRICAL/ELECTRONIC CONTROL MOD-
ULES/DOOR MODULE - DESCRIPTION).
OPERATION
The front door power lock switches provide a lock
and unlock signal to the door module circuitry. The
Driver Door Module (DDM) circuitry controls the out-
put to the driver side front door power lock motor,
while the Passenger Door Module (PDM) circuitry
controls the output to the passenger side front door,
both rear door and the liftgate power lock motors.
When the DDM-integrated power lock switch is
actuated, the DDM circuitry sends control outputs to
the driver side front door power lock motor and sends
a message to the PDM over the Programmable Com-
munications Interface (PCI) data bus to control the
output to the passenger side front door, both rear
door and the liftgate power lock motors. When the
PDM-integrated power lock switch is actuated, the
PDM circuitry sends control outputs to the passenger
side front door, both rear door and the liftgate power
lock motors and sends a message to the DDM over
the Programmable Communications Interface (PCI)
data bus to control the output to the driver side front
door power lock motor.
Each power lock switch is illuminated by a Light-
Emitting Diode (LED) when the ignition switch is
turned to the On position. See the owner's manual in
the vehicle glove box for more information on the fea-
tures, use and operation of the power lock switches.
8N - 8 POWER LOCKSWJ
POWER LOCK MOTOR (Continued)
Page 506 of 2199
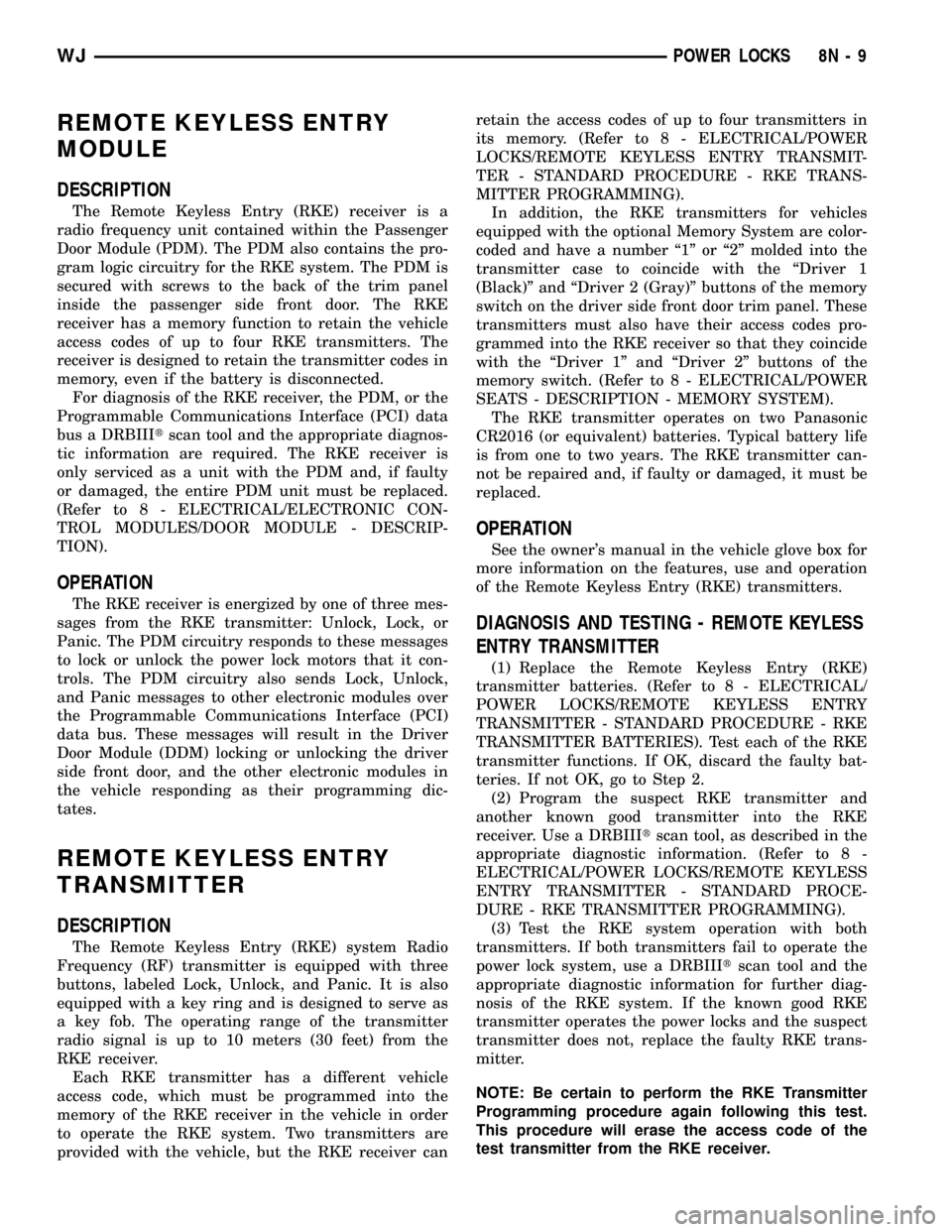
REMOTE KEYLESS ENTRY
MODULE
DESCRIPTION
The Remote Keyless Entry (RKE) receiver is a
radio frequency unit contained within the Passenger
Door Module (PDM). The PDM also contains the pro-
gram logic circuitry for the RKE system. The PDM is
secured with screws to the back of the trim panel
inside the passenger side front door. The RKE
receiver has a memory function to retain the vehicle
access codes of up to four RKE transmitters. The
receiver is designed to retain the transmitter codes in
memory, even if the battery is disconnected.
For diagnosis of the RKE receiver, the PDM, or the
Programmable Communications Interface (PCI) data
bus a DRBIIItscan tool and the appropriate diagnos-
tic information are required. The RKE receiver is
only serviced as a unit with the PDM and, if faulty
or damaged, the entire PDM unit must be replaced.
(Refer to 8 - ELECTRICAL/ELECTRONIC CON-
TROL MODULES/DOOR MODULE - DESCRIP-
TION).
OPERATION
The RKE receiver is energized by one of three mes-
sages from the RKE transmitter: Unlock, Lock, or
Panic. The PDM circuitry responds to these messages
to lock or unlock the power lock motors that it con-
trols. The PDM circuitry also sends Lock, Unlock,
and Panic messages to other electronic modules over
the Programmable Communications Interface (PCI)
data bus. These messages will result in the Driver
Door Module (DDM) locking or unlocking the driver
side front door, and the other electronic modules in
the vehicle responding as their programming dic-
tates.
REMOTE KEYLESS ENTRY
TRANSMITTER
DESCRIPTION
The Remote Keyless Entry (RKE) system Radio
Frequency (RF) transmitter is equipped with three
buttons, labeled Lock, Unlock, and Panic. It is also
equipped with a key ring and is designed to serve as
a key fob. The operating range of the transmitter
radio signal is up to 10 meters (30 feet) from the
RKE receiver.
Each RKE transmitter has a different vehicle
access code, which must be programmed into the
memory of the RKE receiver in the vehicle in order
to operate the RKE system. Two transmitters are
provided with the vehicle, but the RKE receiver canretain the access codes of up to four transmitters in
its memory. (Refer to 8 - ELECTRICAL/POWER
LOCKS/REMOTE KEYLESS ENTRY TRANSMIT-
TER - STANDARD PROCEDURE - RKE TRANS-
MITTER PROGRAMMING).
In addition, the RKE transmitters for vehicles
equipped with the optional Memory System are color-
coded and have a number ª1º or ª2º molded into the
transmitter case to coincide with the ªDriver 1
(Black)º and ªDriver 2 (Gray)º buttons of the memory
switch on the driver side front door trim panel. These
transmitters must also have their access codes pro-
grammed into the RKE receiver so that they coincide
with the ªDriver 1º and ªDriver 2º buttons of the
memory switch. (Refer to 8 - ELECTRICAL/POWER
SEATS - DESCRIPTION - MEMORY SYSTEM).
The RKE transmitter operates on two Panasonic
CR2016 (or equivalent) batteries. Typical battery life
is from one to two years. The RKE transmitter can-
not be repaired and, if faulty or damaged, it must be
replaced.
OPERATION
See the owner's manual in the vehicle glove box for
more information on the features, use and operation
of the Remote Keyless Entry (RKE) transmitters.
DIAGNOSIS AND TESTING - REMOTE KEYLESS
ENTRY TRANSMITTER
(1) Replace the Remote Keyless Entry (RKE)
transmitter batteries. (Refer to 8 - ELECTRICAL/
POWER LOCKS/REMOTE KEYLESS ENTRY
TRANSMITTER - STANDARD PROCEDURE - RKE
TRANSMITTER BATTERIES). Test each of the RKE
transmitter functions. If OK, discard the faulty bat-
teries. If not OK, go to Step 2.
(2) Program the suspect RKE transmitter and
another known good transmitter into the RKE
receiver. Use a DRBIIItscan tool, as described in the
appropriate diagnostic information. (Refer to 8 -
ELECTRICAL/POWER LOCKS/REMOTE KEYLESS
ENTRY TRANSMITTER - STANDARD PROCE-
DURE - RKE TRANSMITTER PROGRAMMING).
(3) Test the RKE system operation with both
transmitters. If both transmitters fail to operate the
power lock system, use a DRBIIItscan tool and the
appropriate diagnostic information for further diag-
nosis of the RKE system. If the known good RKE
transmitter operates the power locks and the suspect
transmitter does not, replace the faulty RKE trans-
mitter.
NOTE: Be certain to perform the RKE Transmitter
Programming procedure again following this test.
This procedure will erase the access code of the
test transmitter from the RKE receiver.
WJPOWER LOCKS 8N - 9
Page 509 of 2199
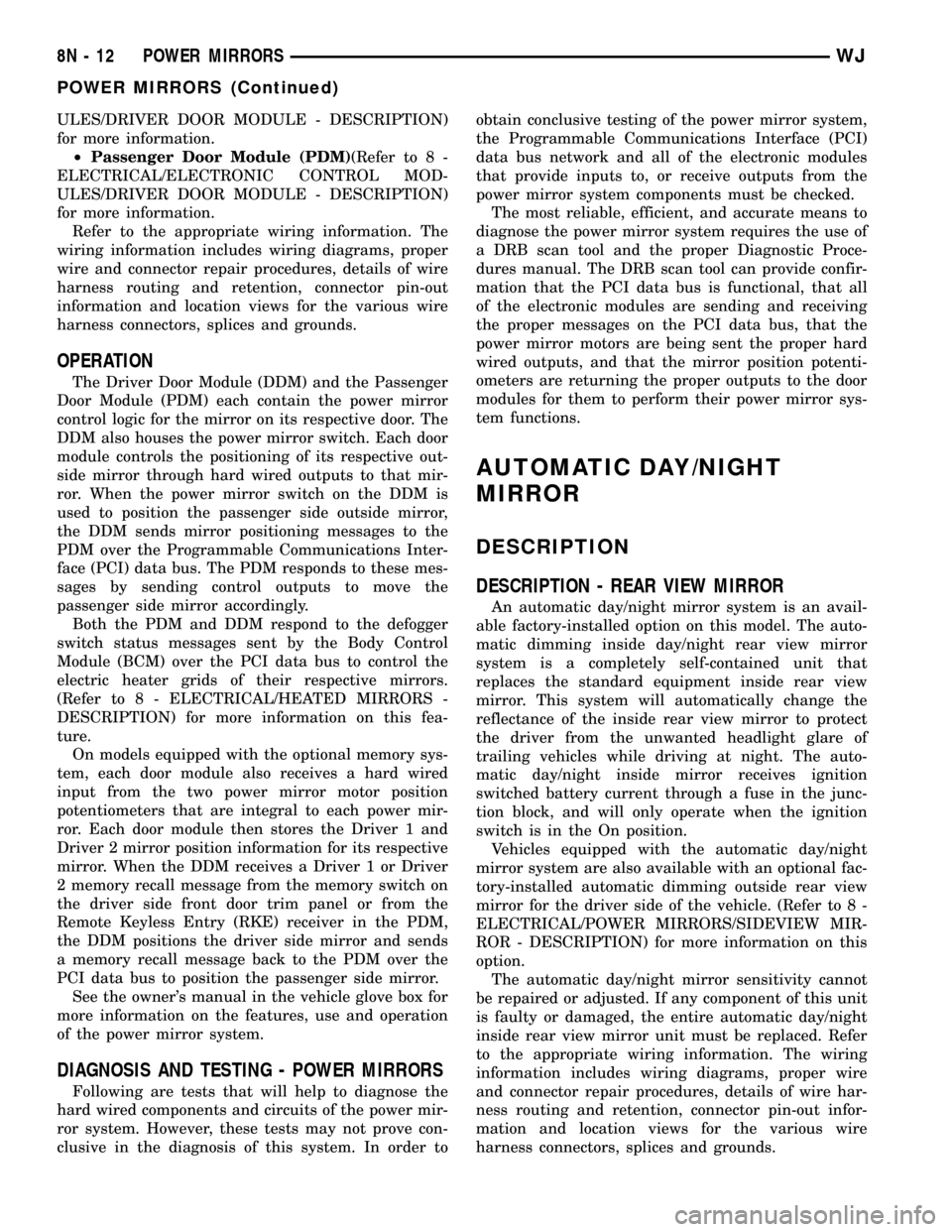
ULES/DRIVER DOOR MODULE - DESCRIPTION)
for more information.
²Passenger Door Module (PDM)(Refer to 8 -
ELECTRICAL/ELECTRONIC CONTROL MOD-
ULES/DRIVER DOOR MODULE - DESCRIPTION)
for more information.
Refer to the appropriate wiring information. The
wiring information includes wiring diagrams, proper
wire and connector repair procedures, details of wire
harness routing and retention, connector pin-out
information and location views for the various wire
harness connectors, splices and grounds.
OPERATION
The Driver Door Module (DDM) and the Passenger
Door Module (PDM) each contain the power mirror
control logic for the mirror on its respective door. The
DDM also houses the power mirror switch. Each door
module controls the positioning of its respective out-
side mirror through hard wired outputs to that mir-
ror. When the power mirror switch on the DDM is
used to position the passenger side outside mirror,
the DDM sends mirror positioning messages to the
PDM over the Programmable Communications Inter-
face (PCI) data bus. The PDM responds to these mes-
sages by sending control outputs to move the
passenger side mirror accordingly.
Both the PDM and DDM respond to the defogger
switch status messages sent by the Body Control
Module (BCM) over the PCI data bus to control the
electric heater grids of their respective mirrors.
(Refer to 8 - ELECTRICAL/HEATED MIRRORS -
DESCRIPTION) for more information on this fea-
ture.
On models equipped with the optional memory sys-
tem, each door module also receives a hard wired
input from the two power mirror motor position
potentiometers that are integral to each power mir-
ror. Each door module then stores the Driver 1 and
Driver 2 mirror position information for its respective
mirror. When the DDM receives a Driver 1 or Driver
2 memory recall message from the memory switch on
the driver side front door trim panel or from the
Remote Keyless Entry (RKE) receiver in the PDM,
the DDM positions the driver side mirror and sends
a memory recall message back to the PDM over the
PCI data bus to position the passenger side mirror.
See the owner's manual in the vehicle glove box for
more information on the features, use and operation
of the power mirror system.
DIAGNOSIS AND TESTING - POWER MIRRORS
Following are tests that will help to diagnose the
hard wired components and circuits of the power mir-
ror system. However, these tests may not prove con-
clusive in the diagnosis of this system. In order toobtain conclusive testing of the power mirror system,
the Programmable Communications Interface (PCI)
data bus network and all of the electronic modules
that provide inputs to, or receive outputs from the
power mirror system components must be checked.
The most reliable, efficient, and accurate means to
diagnose the power mirror system requires the use of
a DRB scan tool and the proper Diagnostic Proce-
dures manual. The DRB scan tool can provide confir-
mation that the PCI data bus is functional, that all
of the electronic modules are sending and receiving
the proper messages on the PCI data bus, that the
power mirror motors are being sent the proper hard
wired outputs, and that the mirror position potenti-
ometers are returning the proper outputs to the door
modules for them to perform their power mirror sys-
tem functions.
AUTOMATIC DAY/NIGHT
MIRROR
DESCRIPTION
DESCRIPTION - REAR VIEW MIRROR
An automatic day/night mirror system is an avail-
able factory-installed option on this model. The auto-
matic dimming inside day/night rear view mirror
system is a completely self-contained unit that
replaces the standard equipment inside rear view
mirror. This system will automatically change the
reflectance of the inside rear view mirror to protect
the driver from the unwanted headlight glare of
trailing vehicles while driving at night. The auto-
matic day/night inside mirror receives ignition
switched battery current through a fuse in the junc-
tion block, and will only operate when the ignition
switch is in the On position.
Vehicles equipped with the automatic day/night
mirror system are also available with an optional fac-
tory-installed automatic dimming outside rear view
mirror for the driver side of the vehicle. (Refer to 8 -
ELECTRICAL/POWER MIRRORS/SIDEVIEW MIR-
ROR - DESCRIPTION) for more information on this
option.
The automatic day/night mirror sensitivity cannot
be repaired or adjusted. If any component of this unit
is faulty or damaged, the entire automatic day/night
inside rear view mirror unit must be replaced. Refer
to the appropriate wiring information. The wiring
information includes wiring diagrams, proper wire
and connector repair procedures, details of wire har-
ness routing and retention, connector pin-out infor-
mation and location views for the various wire
harness connectors, splices and grounds.
8N - 12 POWER MIRRORSWJ
POWER MIRRORS (Continued)
Page 511 of 2199
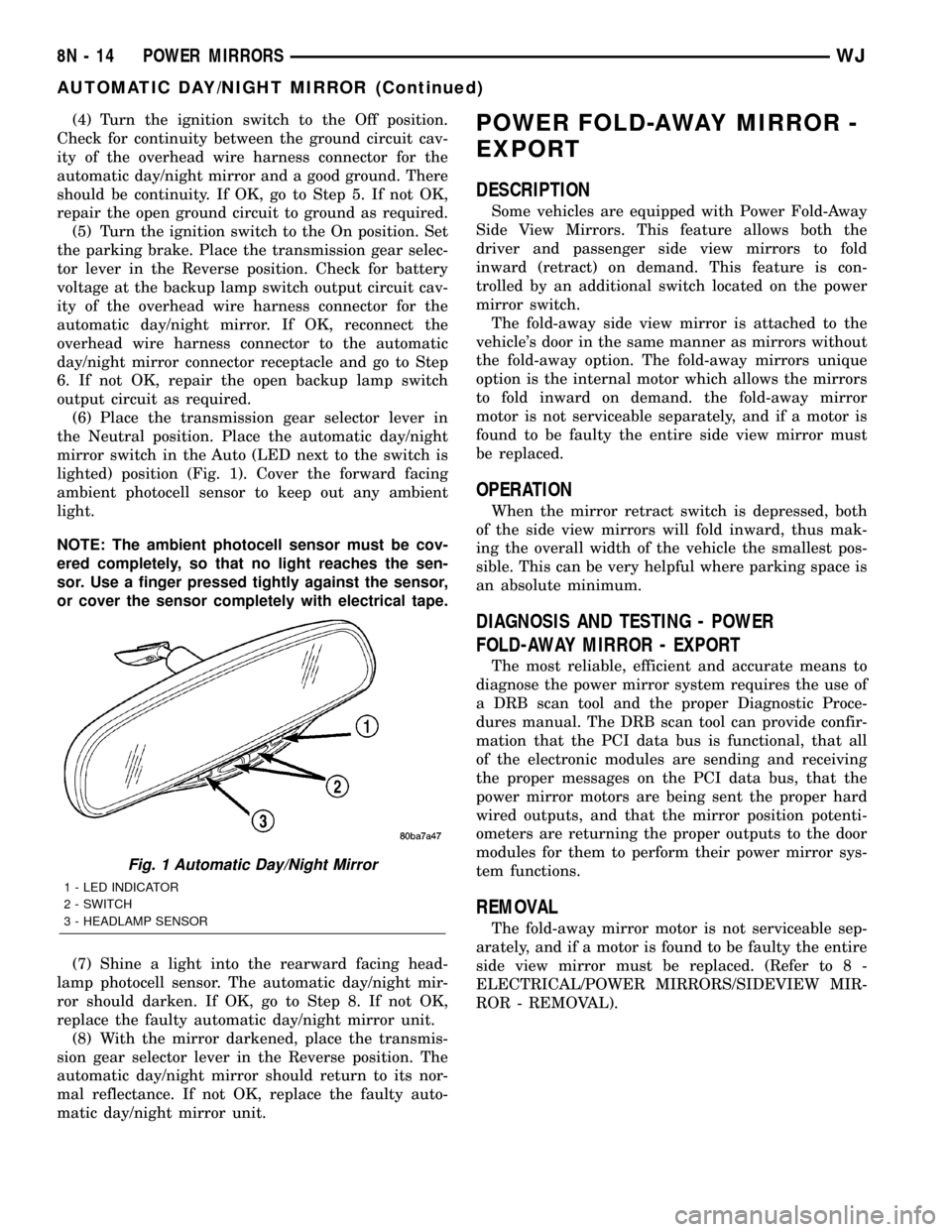
(4) Turn the ignition switch to the Off position.
Check for continuity between the ground circuit cav-
ity of the overhead wire harness connector for the
automatic day/night mirror and a good ground. There
should be continuity. If OK, go to Step 5. If not OK,
repair the open ground circuit to ground as required.
(5) Turn the ignition switch to the On position. Set
the parking brake. Place the transmission gear selec-
tor lever in the Reverse position. Check for battery
voltage at the backup lamp switch output circuit cav-
ity of the overhead wire harness connector for the
automatic day/night mirror. If OK, reconnect the
overhead wire harness connector to the automatic
day/night mirror connector receptacle and go to Step
6. If not OK, repair the open backup lamp switch
output circuit as required.
(6) Place the transmission gear selector lever in
the Neutral position. Place the automatic day/night
mirror switch in the Auto (LED next to the switch is
lighted) position (Fig. 1). Cover the forward facing
ambient photocell sensor to keep out any ambient
light.
NOTE: The ambient photocell sensor must be cov-
ered completely, so that no light reaches the sen-
sor. Use a finger pressed tightly against the sensor,
or cover the sensor completely with electrical tape.
(7) Shine a light into the rearward facing head-
lamp photocell sensor. The automatic day/night mir-
ror should darken. If OK, go to Step 8. If not OK,
replace the faulty automatic day/night mirror unit.
(8) With the mirror darkened, place the transmis-
sion gear selector lever in the Reverse position. The
automatic day/night mirror should return to its nor-
mal reflectance. If not OK, replace the faulty auto-
matic day/night mirror unit.POWER FOLD-AWAY MIRROR -
EXPORT
DESCRIPTION
Some vehicles are equipped with Power Fold-Away
Side View Mirrors. This feature allows both the
driver and passenger side view mirrors to fold
inward (retract) on demand. This feature is con-
trolled by an additional switch located on the power
mirror switch.
The fold-away side view mirror is attached to the
vehicle's door in the same manner as mirrors without
the fold-away option. The fold-away mirrors unique
option is the internal motor which allows the mirrors
to fold inward on demand. the fold-away mirror
motor is not serviceable separately, and if a motor is
found to be faulty the entire side view mirror must
be replaced.
OPERATION
When the mirror retract switch is depressed, both
of the side view mirrors will fold inward, thus mak-
ing the overall width of the vehicle the smallest pos-
sible. This can be very helpful where parking space is
an absolute minimum.
DIAGNOSIS AND TESTING - POWER
FOLD-AWAY MIRROR - EXPORT
The most reliable, efficient and accurate means to
diagnose the power mirror system requires the use of
a DRB scan tool and the proper Diagnostic Proce-
dures manual. The DRB scan tool can provide confir-
mation that the PCI data bus is functional, that all
of the electronic modules are sending and receiving
the proper messages on the PCI data bus, that the
power mirror motors are being sent the proper hard
wired outputs, and that the mirror position potenti-
ometers are returning the proper outputs to the door
modules for them to perform their power mirror sys-
tem functions.
REMOVAL
The fold-away mirror motor is not serviceable sep-
arately, and if a motor is found to be faulty the entire
side view mirror must be replaced. (Refer to 8 -
ELECTRICAL/POWER MIRRORS/SIDEVIEW MIR-
ROR - REMOVAL).
Fig. 1 Automatic Day/Night Mirror
1 - LED INDICATOR
2 - SWITCH
3 - HEADLAMP SENSOR
8N - 14 POWER MIRRORSWJ
AUTOMATIC DAY/NIGHT MIRROR (Continued)
Page 517 of 2199
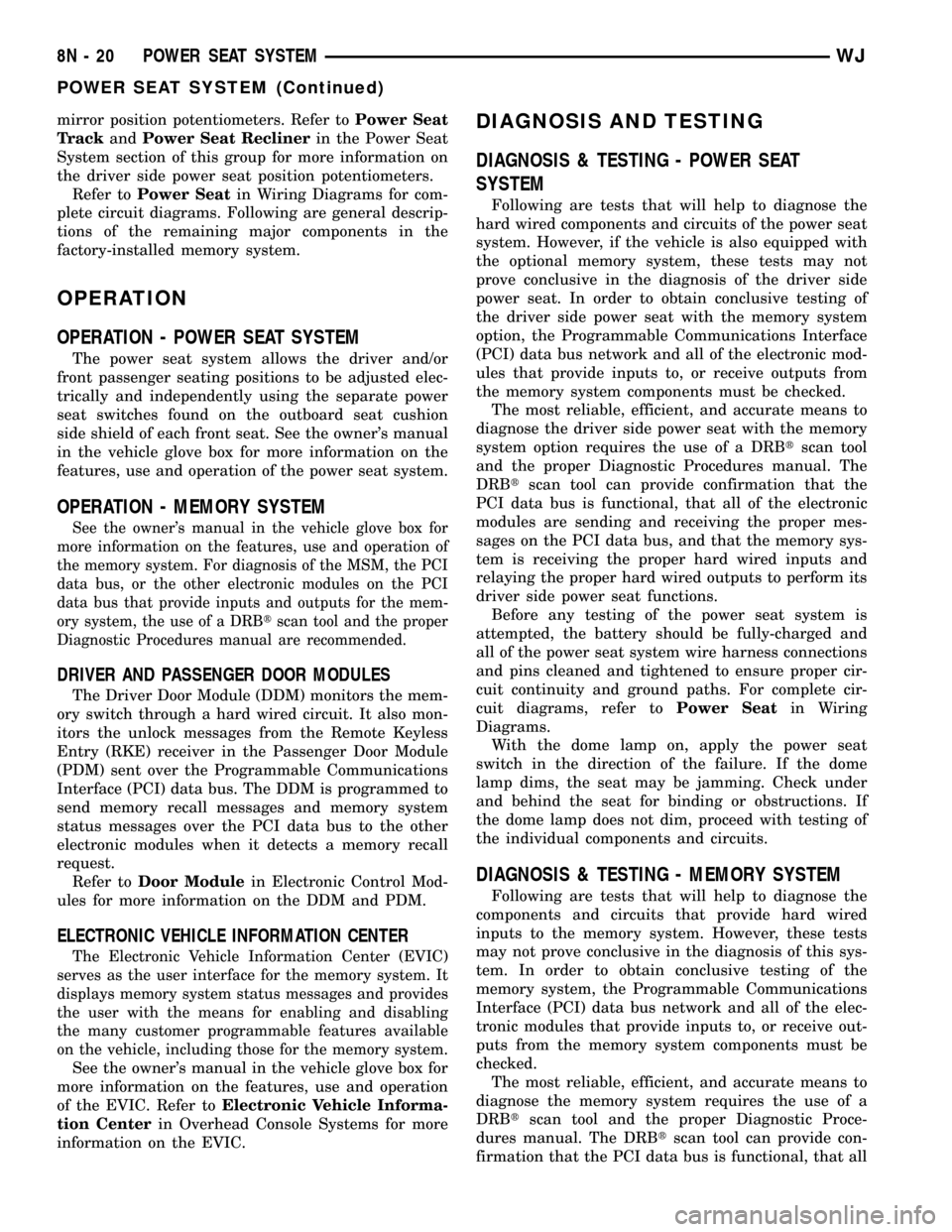
mirror position potentiometers. Refer toPower Seat
TrackandPower Seat Reclinerin the Power Seat
System section of this group for more information on
the driver side power seat position potentiometers.
Refer toPower Seatin Wiring Diagrams for com-
plete circuit diagrams. Following are general descrip-
tions of the remaining major components in the
factory-installed memory system.
OPERATION
OPERATION - POWER SEAT SYSTEM
The power seat system allows the driver and/or
front passenger seating positions to be adjusted elec-
trically and independently using the separate power
seat switches found on the outboard seat cushion
side shield of each front seat. See the owner's manual
in the vehicle glove box for more information on the
features, use and operation of the power seat system.
OPERATION - MEMORY SYSTEM
See the owner's manual in the vehicle glove box for
more information on the features, use and operation of
the memory system. For diagnosis of the MSM, the PCI
data bus, or the other electronic modules on the PCI
data bus that provide inputs and outputs for the mem-
ory system, the use of a DRBtscan tool and the proper
Diagnostic Procedures manual are recommended.
DRIVER AND PASSENGER DOOR MODULES
The Driver Door Module (DDM) monitors the mem-
ory switch through a hard wired circuit. It also mon-
itors the unlock messages from the Remote Keyless
Entry (RKE) receiver in the Passenger Door Module
(PDM) sent over the Programmable Communications
Interface (PCI) data bus. The DDM is programmed to
send memory recall messages and memory system
status messages over the PCI data bus to the other
electronic modules when it detects a memory recall
request.
Refer toDoor Modulein Electronic Control Mod-
ules for more information on the DDM and PDM.
ELECTRONIC VEHICLE INFORMATION CENTER
The Electronic Vehicle Information Center (EVIC)
serves as the user interface for the memory system. It
displays memory system status messages and provides
the user with the means for enabling and disabling
the many customer programmable features available
on the vehicle, including those for the memory system.
See the owner's manual in the vehicle glove box for
more information on the features, use and operation
of the EVIC. Refer toElectronic Vehicle Informa-
tion Centerin Overhead Console Systems for more
information on the EVIC.
DIAGNOSIS AND TESTING
DIAGNOSIS & TESTING - POWER SEAT
SYSTEM
Following are tests that will help to diagnose the
hard wired components and circuits of the power seat
system. However, if the vehicle is also equipped with
the optional memory system, these tests may not
prove conclusive in the diagnosis of the driver side
power seat. In order to obtain conclusive testing of
the driver side power seat with the memory system
option, the Programmable Communications Interface
(PCI) data bus network and all of the electronic mod-
ules that provide inputs to, or receive outputs from
the memory system components must be checked.
The most reliable, efficient, and accurate means to
diagnose the driver side power seat with the memory
system option requires the use of a DRBtscan tool
and the proper Diagnostic Procedures manual. The
DRBtscan tool can provide confirmation that the
PCI data bus is functional, that all of the electronic
modules are sending and receiving the proper mes-
sages on the PCI data bus, and that the memory sys-
tem is receiving the proper hard wired inputs and
relaying the proper hard wired outputs to perform its
driver side power seat functions.
Before any testing of the power seat system is
attempted, the battery should be fully-charged and
all of the power seat system wire harness connections
and pins cleaned and tightened to ensure proper cir-
cuit continuity and ground paths. For complete cir-
cuit diagrams, refer toPower Seatin Wiring
Diagrams.
With the dome lamp on, apply the power seat
switch in the direction of the failure. If the dome
lamp dims, the seat may be jamming. Check under
and behind the seat for binding or obstructions. If
the dome lamp does not dim, proceed with testing of
the individual components and circuits.
DIAGNOSIS & TESTING - MEMORY SYSTEM
Following are tests that will help to diagnose the
components and circuits that provide hard wired
inputs to the memory system. However, these tests
may not prove conclusive in the diagnosis of this sys-
tem. In order to obtain conclusive testing of the
memory system, the Programmable Communications
Interface (PCI) data bus network and all of the elec-
tronic modules that provide inputs to, or receive out-
puts from the memory system components must be
checked.
The most reliable, efficient, and accurate means to
diagnose the memory system requires the use of a
DRBtscan tool and the proper Diagnostic Proce-
dures manual. The DRBtscan tool can provide con-
firmation that the PCI data bus is functional, that all
8N - 20 POWER SEAT SYSTEMWJ
POWER SEAT SYSTEM (Continued)
Page 518 of 2199
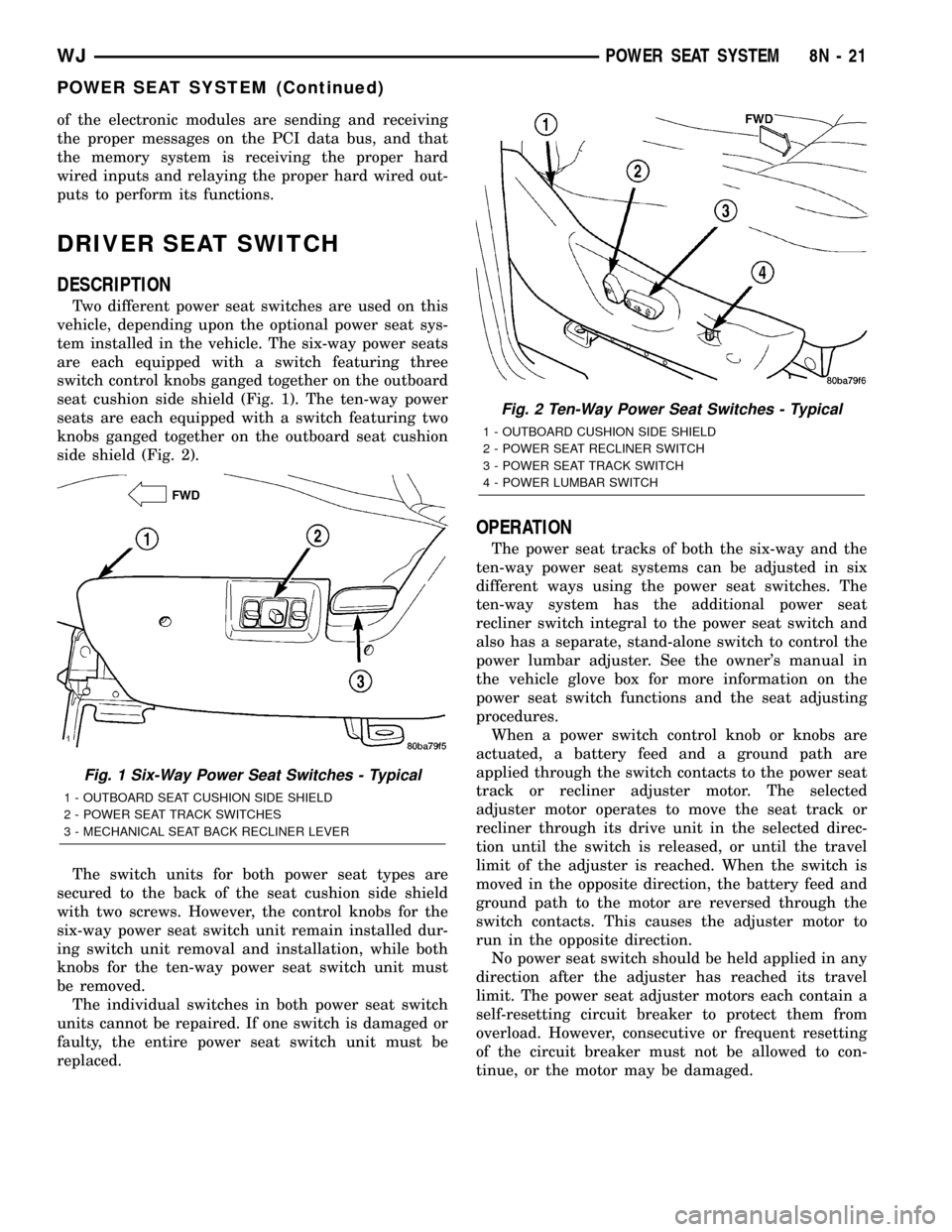
of the electronic modules are sending and receiving
the proper messages on the PCI data bus, and that
the memory system is receiving the proper hard
wired inputs and relaying the proper hard wired out-
puts to perform its functions.
DRIVER SEAT SWITCH
DESCRIPTION
Two different power seat switches are used on this
vehicle, depending upon the optional power seat sys-
tem installed in the vehicle. The six-way power seats
are each equipped with a switch featuring three
switch control knobs ganged together on the outboard
seat cushion side shield (Fig. 1). The ten-way power
seats are each equipped with a switch featuring two
knobs ganged together on the outboard seat cushion
side shield (Fig. 2).
The switch units for both power seat types are
secured to the back of the seat cushion side shield
with two screws. However, the control knobs for the
six-way power seat switch unit remain installed dur-
ing switch unit removal and installation, while both
knobs for the ten-way power seat switch unit must
be removed.
The individual switches in both power seat switch
units cannot be repaired. If one switch is damaged or
faulty, the entire power seat switch unit must be
replaced.
OPERATION
The power seat tracks of both the six-way and the
ten-way power seat systems can be adjusted in six
different ways using the power seat switches. The
ten-way system has the additional power seat
recliner switch integral to the power seat switch and
also has a separate, stand-alone switch to control the
power lumbar adjuster. See the owner's manual in
the vehicle glove box for more information on the
power seat switch functions and the seat adjusting
procedures.
When a power switch control knob or knobs are
actuated, a battery feed and a ground path are
applied through the switch contacts to the power seat
track or recliner adjuster motor. The selected
adjuster motor operates to move the seat track or
recliner through its drive unit in the selected direc-
tion until the switch is released, or until the travel
limit of the adjuster is reached. When the switch is
moved in the opposite direction, the battery feed and
ground path to the motor are reversed through the
switch contacts. This causes the adjuster motor to
run in the opposite direction.
No power seat switch should be held applied in any
direction after the adjuster has reached its travel
limit. The power seat adjuster motors each contain a
self-resetting circuit breaker to protect them from
overload. However, consecutive or frequent resetting
of the circuit breaker must not be allowed to con-
tinue, or the motor may be damaged.
Fig. 1 Six-Way Power Seat Switches - Typical
1 - OUTBOARD SEAT CUSHION SIDE SHIELD
2 - POWER SEAT TRACK SWITCHES
3 - MECHANICAL SEAT BACK RECLINER LEVER
Fig. 2 Ten-Way Power Seat Switches - Typical
1 - OUTBOARD CUSHION SIDE SHIELD
2 - POWER SEAT RECLINER SWITCH
3 - POWER SEAT TRACK SWITCH
4 - POWER LUMBAR SWITCH
WJPOWER SEAT SYSTEM 8N - 21
POWER SEAT SYSTEM (Continued)
Page 531 of 2199
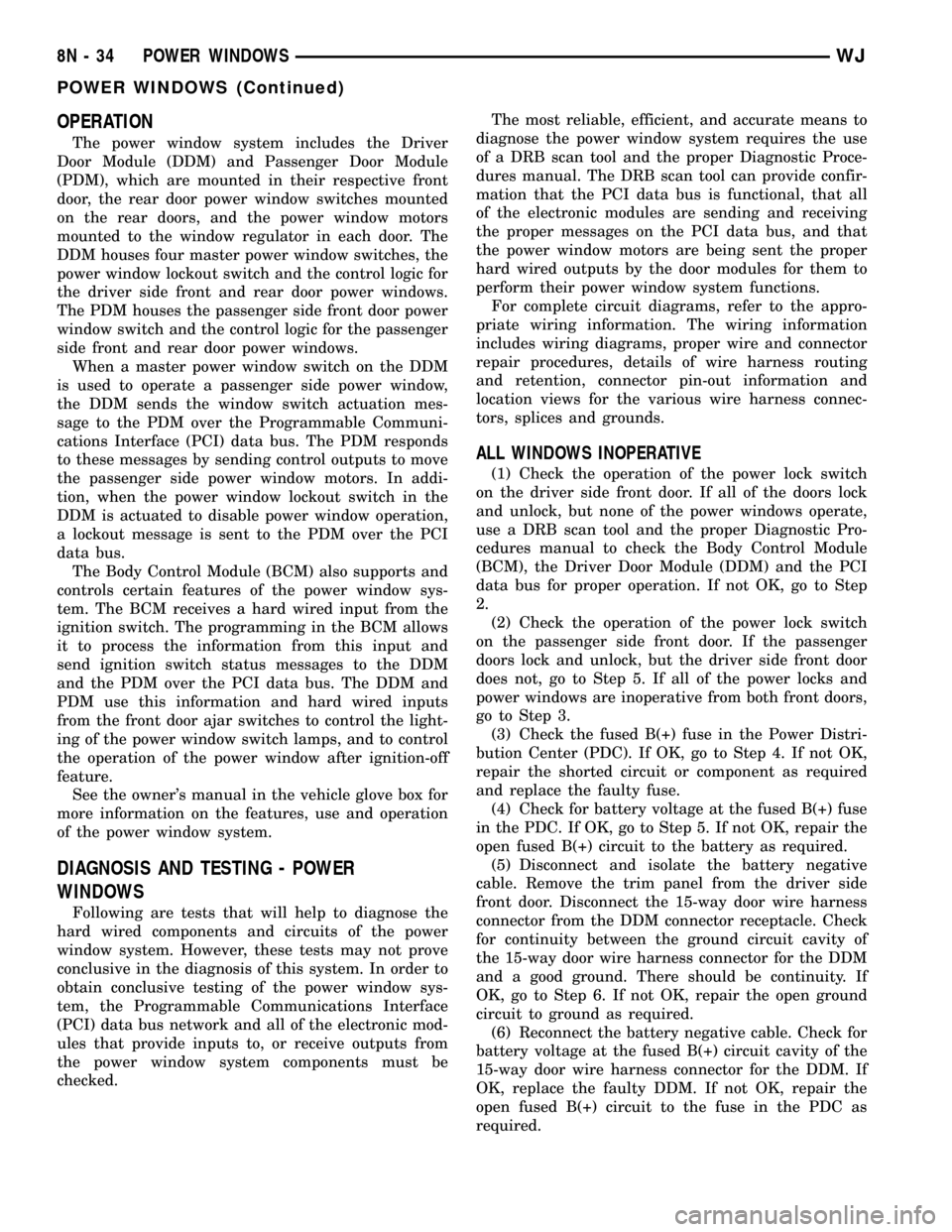
OPERATION
The power window system includes the Driver
Door Module (DDM) and Passenger Door Module
(PDM), which are mounted in their respective front
door, the rear door power window switches mounted
on the rear doors, and the power window motors
mounted to the window regulator in each door. The
DDM houses four master power window switches, the
power window lockout switch and the control logic for
the driver side front and rear door power windows.
The PDM houses the passenger side front door power
window switch and the control logic for the passenger
side front and rear door power windows.
When a master power window switch on the DDM
is used to operate a passenger side power window,
the DDM sends the window switch actuation mes-
sage to the PDM over the Programmable Communi-
cations Interface (PCI) data bus. The PDM responds
to these messages by sending control outputs to move
the passenger side power window motors. In addi-
tion, when the power window lockout switch in the
DDM is actuated to disable power window operation,
a lockout message is sent to the PDM over the PCI
data bus.
The Body Control Module (BCM) also supports and
controls certain features of the power window sys-
tem. The BCM receives a hard wired input from the
ignition switch. The programming in the BCM allows
it to process the information from this input and
send ignition switch status messages to the DDM
and the PDM over the PCI data bus. The DDM and
PDM use this information and hard wired inputs
from the front door ajar switches to control the light-
ing of the power window switch lamps, and to control
the operation of the power window after ignition-off
feature.
See the owner's manual in the vehicle glove box for
more information on the features, use and operation
of the power window system.
DIAGNOSIS AND TESTING - POWER
WINDOWS
Following are tests that will help to diagnose the
hard wired components and circuits of the power
window system. However, these tests may not prove
conclusive in the diagnosis of this system. In order to
obtain conclusive testing of the power window sys-
tem, the Programmable Communications Interface
(PCI) data bus network and all of the electronic mod-
ules that provide inputs to, or receive outputs from
the power window system components must be
checked.The most reliable, efficient, and accurate means to
diagnose the power window system requires the use
of a DRB scan tool and the proper Diagnostic Proce-
dures manual. The DRB scan tool can provide confir-
mation that the PCI data bus is functional, that all
of the electronic modules are sending and receiving
the proper messages on the PCI data bus, and that
the power window motors are being sent the proper
hard wired outputs by the door modules for them to
perform their power window system functions.
For complete circuit diagrams, refer to the appro-
priate wiring information. The wiring information
includes wiring diagrams, proper wire and connector
repair procedures, details of wire harness routing
and retention, connector pin-out information and
location views for the various wire harness connec-
tors, splices and grounds.
ALL WINDOWS INOPERATIVE
(1) Check the operation of the power lock switch
on the driver side front door. If all of the doors lock
and unlock, but none of the power windows operate,
use a DRB scan tool and the proper Diagnostic Pro-
cedures manual to check the Body Control Module
(BCM), the Driver Door Module (DDM) and the PCI
data bus for proper operation. If not OK, go to Step
2.
(2) Check the operation of the power lock switch
on the passenger side front door. If the passenger
doors lock and unlock, but the driver side front door
does not, go to Step 5. If all of the power locks and
power windows are inoperative from both front doors,
go to Step 3.
(3) Check the fused B(+) fuse in the Power Distri-
bution Center (PDC). If OK, go to Step 4. If not OK,
repair the shorted circuit or component as required
and replace the faulty fuse.
(4) Check for battery voltage at the fused B(+) fuse
in the PDC. If OK, go to Step 5. If not OK, repair the
open fused B(+) circuit to the battery as required.
(5) Disconnect and isolate the battery negative
cable. Remove the trim panel from the driver side
front door. Disconnect the 15-way door wire harness
connector from the DDM connector receptacle. Check
for continuity between the ground circuit cavity of
the 15-way door wire harness connector for the DDM
and a good ground. There should be continuity. If
OK, go to Step 6. If not OK, repair the open ground
circuit to ground as required.
(6) Reconnect the battery negative cable. Check for
battery voltage at the fused B(+) circuit cavity of the
15-way door wire harness connector for the DDM. If
OK, replace the faulty DDM. If not OK, repair the
open fused B(+) circuit to the fuse in the PDC as
required.
8N - 34 POWER WINDOWSWJ
POWER WINDOWS (Continued)