2.7 diesel JEEP GRAND CHEROKEE 2002 WJ / 2.G Workshop Manual
[x] Cancel search | Manufacturer: JEEP, Model Year: 2002, Model line: GRAND CHEROKEE, Model: JEEP GRAND CHEROKEE 2002 WJ / 2.GPages: 2199, PDF Size: 76.01 MB
Page 12 of 2199
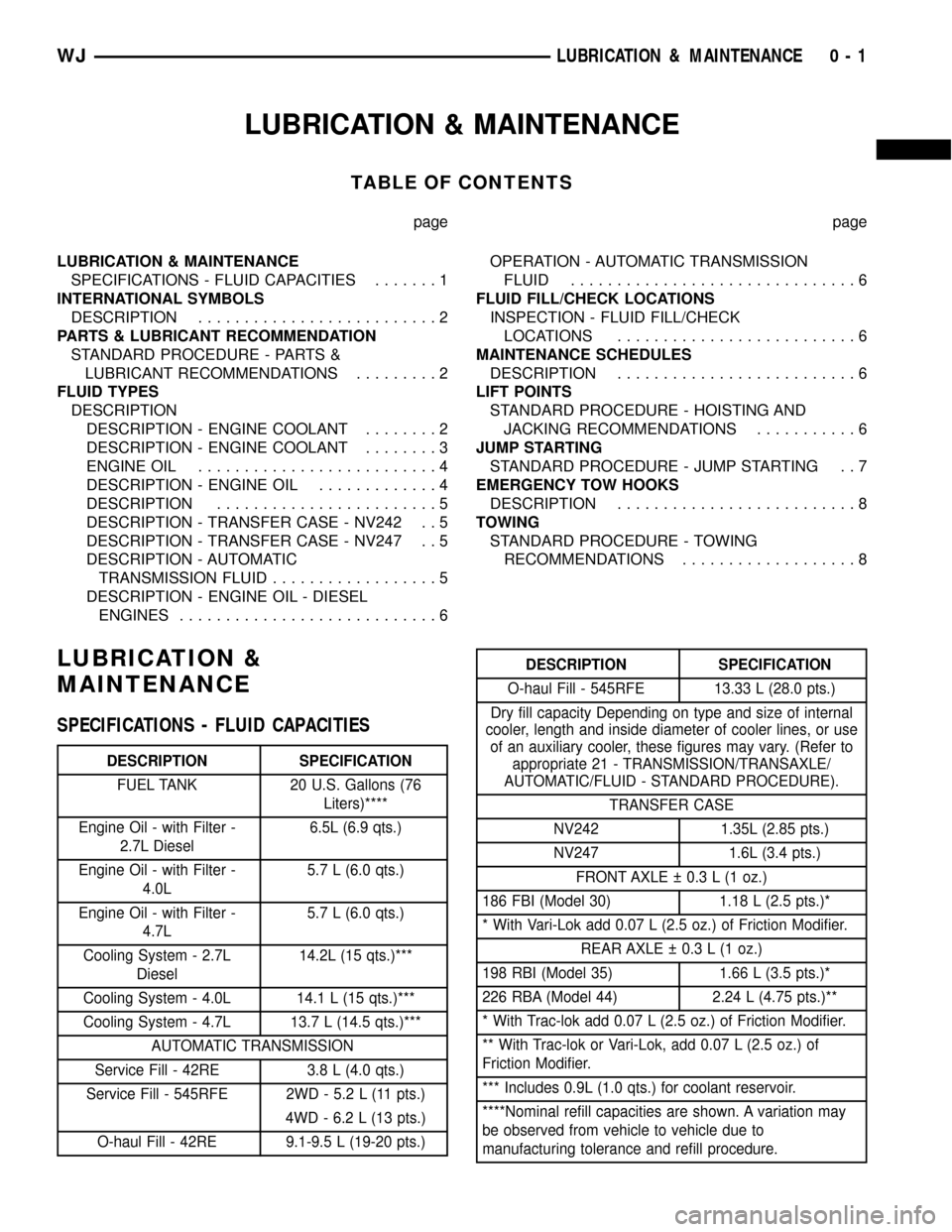
LUBRICATION & MAINTENANCE
TABLE OF CONTENTS
page page
LUBRICATION & MAINTENANCE
SPECIFICATIONS - FLUID CAPACITIES.......1
INTERNATIONAL SYMBOLS
DESCRIPTION..........................2
PARTS & LUBRICANT RECOMMENDATION
STANDARD PROCEDURE - PARTS &
LUBRICANT RECOMMENDATIONS.........2
FLUID TYPES
DESCRIPTION
DESCRIPTION - ENGINE COOLANT........2
DESCRIPTION - ENGINE COOLANT........3
ENGINE OIL..........................4
DESCRIPTION - ENGINE OIL.............4
DESCRIPTION........................5
DESCRIPTION - TRANSFER CASE - NV242 . . 5
DESCRIPTION - TRANSFER CASE - NV247 . . 5
DESCRIPTION - AUTOMATIC
TRANSMISSION FLUID..................5
DESCRIPTION - ENGINE OIL - DIESEL
ENGINES............................6OPERATION - AUTOMATIC TRANSMISSION
FLUID...............................6
FLUID FILL/CHECK LOCATIONS
INSPECTION - FLUID FILL/CHECK
LOCATIONS..........................6
MAINTENANCE SCHEDULES
DESCRIPTION..........................6
LIFT POINTS
STANDARD PROCEDURE - HOISTING AND
JACKING RECOMMENDATIONS...........6
JUMP STARTING
STANDARD PROCEDURE - JUMP STARTING . . 7
EMERGENCY TOW HOOKS
DESCRIPTION..........................8
TOWING
STANDARD PROCEDURE - TOWING
RECOMMENDATIONS...................8
LUBRICATION &
MAINTENANCE
SPECIFICATIONS - FLUID CAPACITIES
DESCRIPTION SPECIFICATION
FUEL TANK 20 U.S. Gallons (76
Liters)****
Engine Oil - with Filter -
2.7L Diesel6.5L (6.9 qts.)
Engine Oil - with Filter -
4.0L5.7 L (6.0 qts.)
Engine Oil - with Filter -
4.7L5.7 L (6.0 qts.)
Cooling System - 2.7L
Diesel14.2L (15 qts.)***
Cooling System - 4.0L 14.1 L (15 qts.)***
Cooling System - 4.7L 13.7 L (14.5 qts.)***
AUTOMATIC TRANSMISSION
Service Fill - 42RE 3.8 L (4.0 qts.)
Service Fill - 545RFE 2WD - 5.2 L (11 pts.)
4WD - 6.2 L (13 pts.)
O-haul Fill - 42RE 9.1-9.5 L (19-20 pts.)
DESCRIPTION SPECIFICATION
O-haul Fill - 545RFE 13.33 L (28.0 pts.)
Dry fill capacity Depending on type and size of internal
cooler, length and inside diameter of cooler lines, or use
of an auxiliary cooler, these figures may vary. (Refer to
appropriate 21 - TRANSMISSION/TRANSAXLE/
AUTOMATIC/FLUID - STANDARD PROCEDURE).
TRANSFER CASE
NV242 1.35L (2.85 pts.)
NV247 1.6L (3.4 pts.)
FRONT AXLE 0.3 L (1 oz.)
186 FBI (Model 30) 1.18 L (2.5 pts.)*
* With Vari-Lok add 0.07 L (2.5 oz.) of Friction Modifier.
REAR AXLE 0.3 L (1 oz.)
198 RBI (Model 35) 1.66 L (3.5 pts.)*
226 RBA (Model 44) 2.24 L (4.75 pts.)**
* With Trac-lok add 0.07 L (2.5 oz.) of Friction Modifier.
** With Trac-lok or Vari-Lok, add 0.07 L (2.5 oz.) of
Friction Modifier.
*** Includes 0.9L (1.0 qts.) for coolant reservoir.
****Nominal refill capacities are shown. A variation may
be observed from vehicle to vehicle due to
manufacturing tolerance and refill procedure.
WJLUBRICATION & MAINTENANCE 0 - 1
Page 1199 of 2199
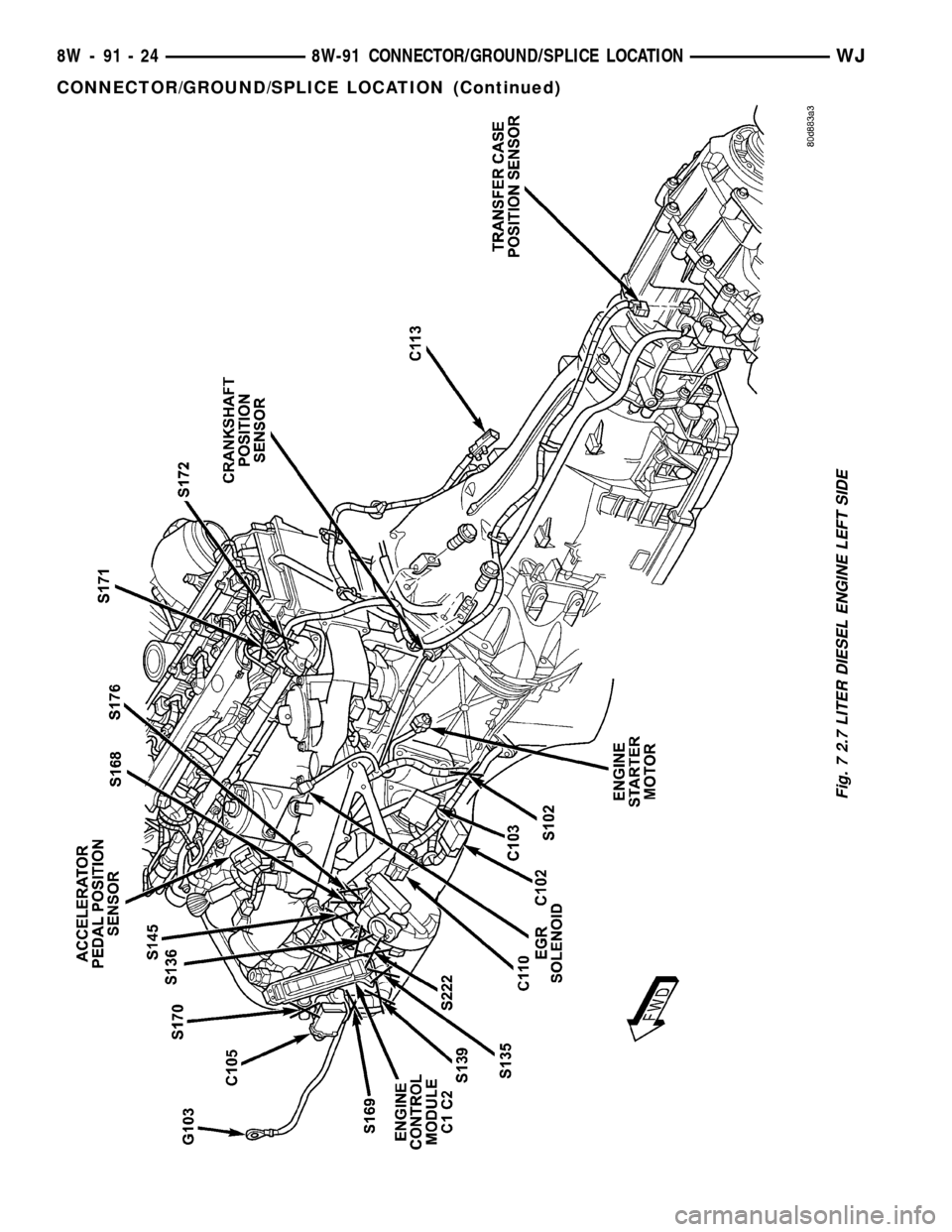
Fig. 7 2.7 LITER DIESEL ENGINE LEFT SIDE
8W - 91 - 24 8W-91 CONNECTOR/GROUND/SPLICE LOCATIONWJ
CONNECTOR/GROUND/SPLICE LOCATION (Continued)
Page 1200 of 2199
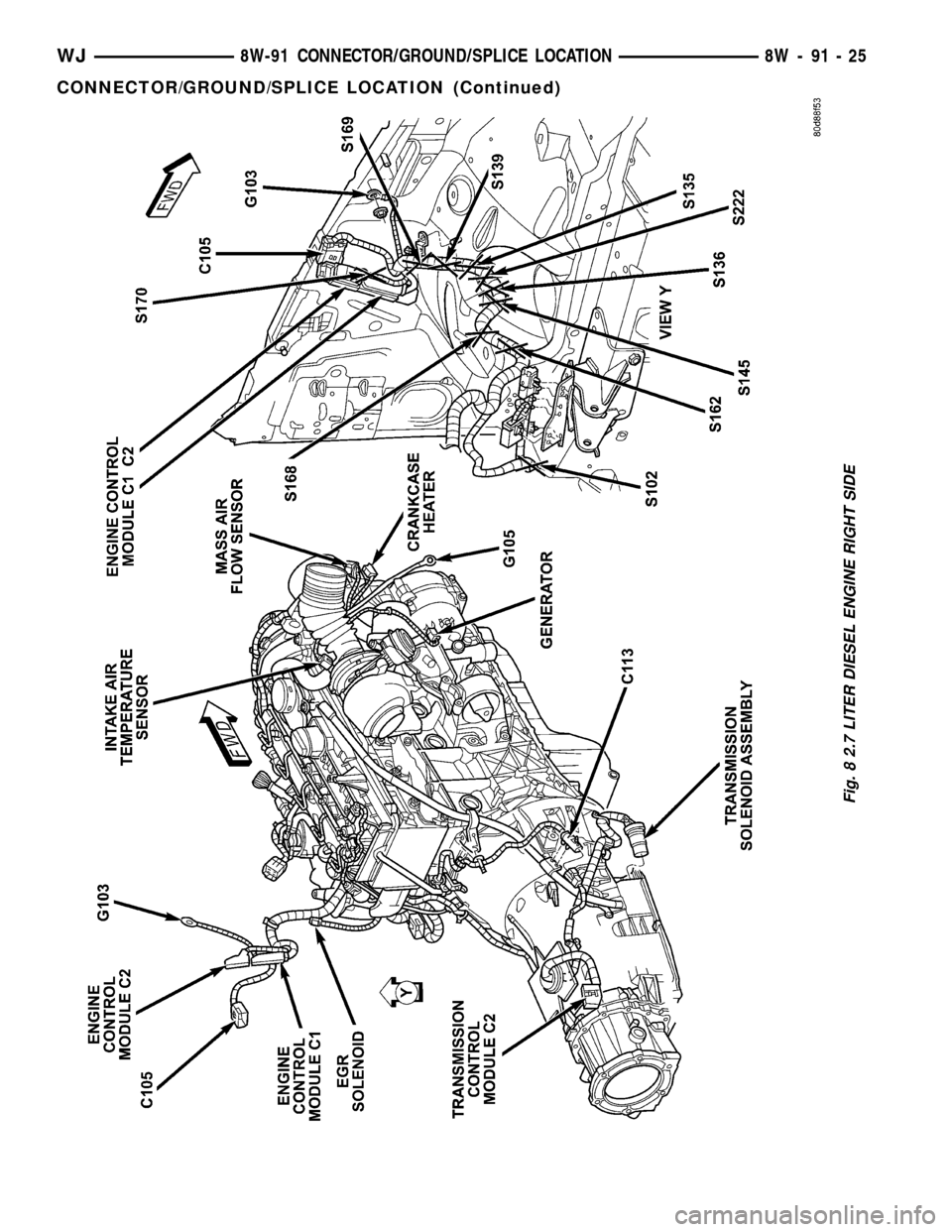
Fig. 8 2.7 LITER DIESEL ENGINE RIGHT SIDE
WJ8W-91 CONNECTOR/GROUND/SPLICE LOCATION 8W - 91 - 25
CONNECTOR/GROUND/SPLICE LOCATION (Continued)
Page 2085 of 2199
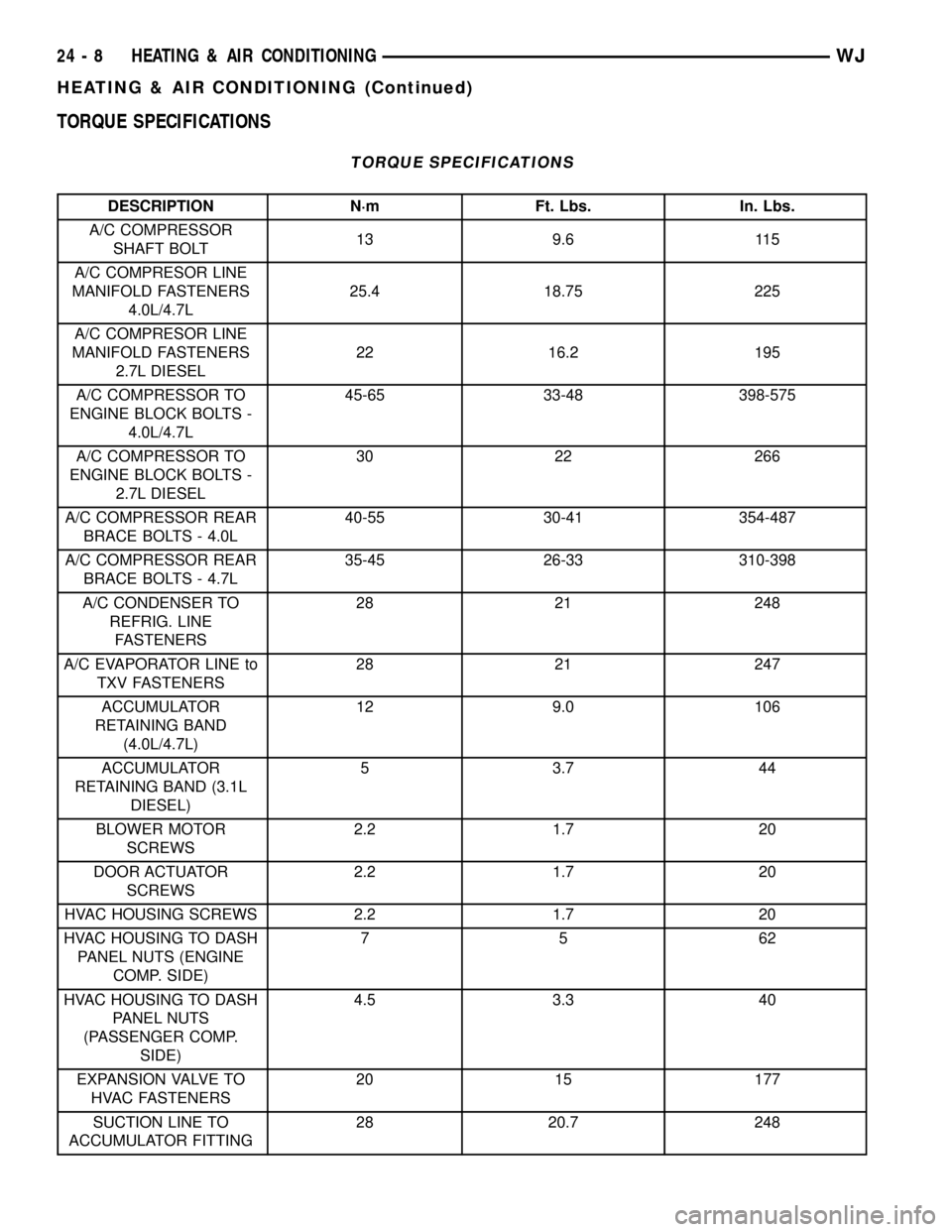
TORQUE SPECIFICATIONS
TORQUE SPECIFICATIONS
DESCRIPTION N´m Ft. Lbs. In. Lbs.
A/C COMPRESSOR
SHAFT BOLT13 9.6 115
A/C COMPRESOR LINE
MANIFOLD FASTENERS
4.0L/4.7L25.4 18.75 225
A/C COMPRESOR LINE
MANIFOLD FASTENERS
2.7L DIESEL22 16.2 195
A/C COMPRESSOR TO
ENGINE BLOCK BOLTS -
4.0L/4.7L45-65 33-48 398-575
A/C COMPRESSOR TO
ENGINE BLOCK BOLTS -
2.7L DIESEL30 22 266
A/C COMPRESSOR REAR
BRACE BOLTS - 4.0L40-55 30-41 354-487
A/C COMPRESSOR REAR
BRACE BOLTS - 4.7L35-45 26-33 310-398
A/C CONDENSER TO
REFRIG. LINE
FASTENERS28 21 248
A/C EVAPORATOR LINE to
TXV FASTENERS28 21 247
ACCUMULATOR
RETAINING BAND
(4.0L/4.7L)12 9.0 106
ACCUMULATOR
RETAINING BAND (3.1L
DIESEL)5 3.7 44
BLOWER MOTOR
SCREWS2.2 1.7 20
DOOR ACTUATOR
SCREWS2.2 1.7 20
HVAC HOUSING SCREWS 2.2 1.7 20
HVAC HOUSING TO DASH
PANEL NUTS (ENGINE
COMP. SIDE)75 62
HVAC HOUSING TO DASH
PANEL NUTS
(PASSENGER COMP.
SIDE)4.5 3.3 40
EXPANSION VALVE TO
HVAC FASTENERS20 15 177
SUCTION LINE TO
ACCUMULATOR FITTING28 20.7 248
24 - 8 HEATING & AIR CONDITIONINGWJ
HEATING & AIR CONDITIONING (Continued)
Page 2128 of 2199
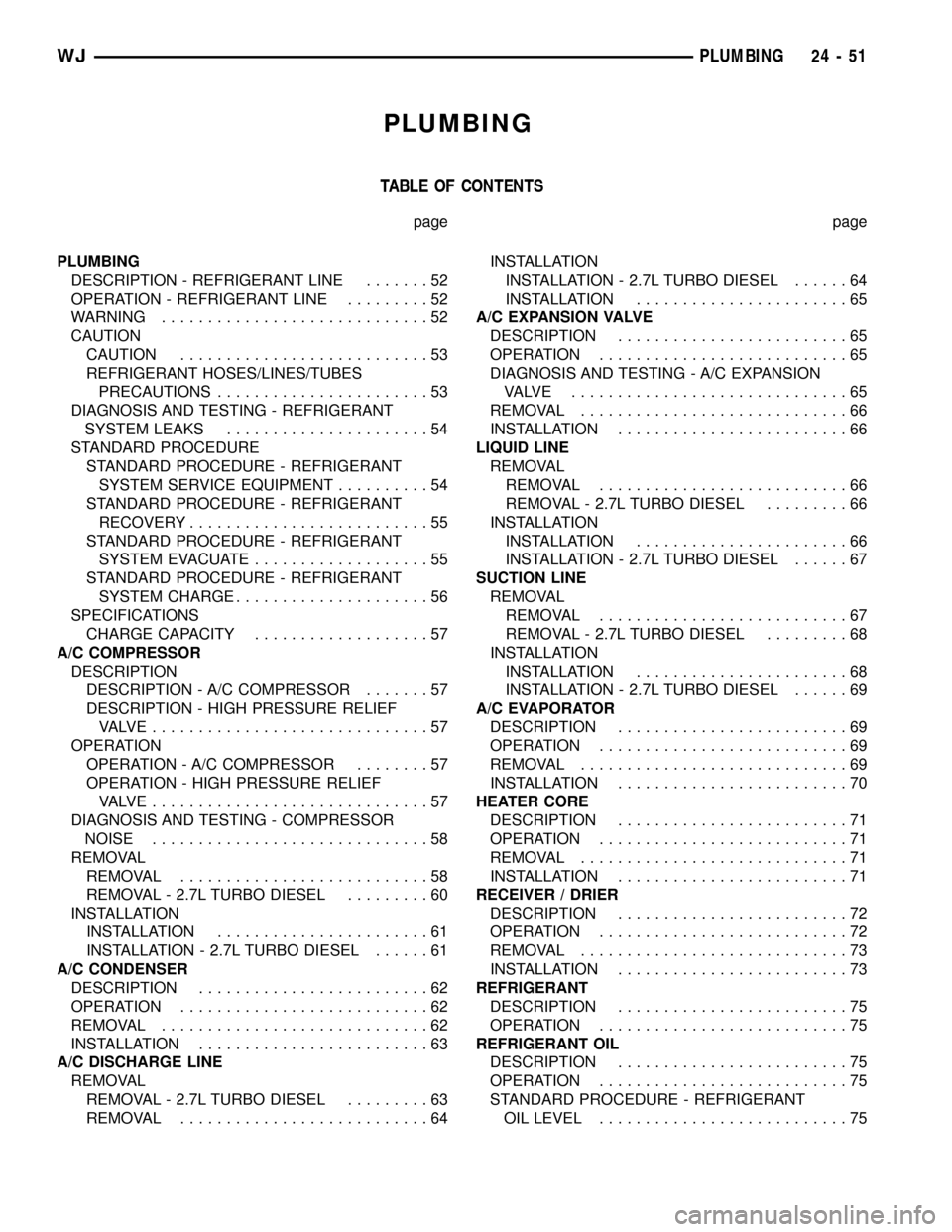
PLUMBING
TABLE OF CONTENTS
page page
PLUMBING
DESCRIPTION - REFRIGERANT LINE.......52
OPERATION - REFRIGERANT LINE.........52
WARNING.............................52
CAUTION
CAUTION...........................53
REFRIGERANT HOSES/LINES/TUBES
PRECAUTIONS.......................53
DIAGNOSIS AND TESTING - REFRIGERANT
SYSTEM LEAKS......................54
STANDARD PROCEDURE
STANDARD PROCEDURE - REFRIGERANT
SYSTEM SERVICE EQUIPMENT..........54
STANDARD PROCEDURE - REFRIGERANT
RECOVERY..........................55
STANDARD PROCEDURE - REFRIGERANT
SYSTEM EVACUATE...................55
STANDARD PROCEDURE - REFRIGERANT
SYSTEM CHARGE.....................56
SPECIFICATIONS
CHARGE CAPACITY...................57
A/C COMPRESSOR
DESCRIPTION
DESCRIPTION - A/C COMPRESSOR.......57
DESCRIPTION - HIGH PRESSURE RELIEF
VALVE..............................57
OPERATION
OPERATION - A/C COMPRESSOR........57
OPERATION - HIGH PRESSURE RELIEF
VALVE..............................57
DIAGNOSIS AND TESTING - COMPRESSOR
NOISE..............................58
REMOVAL
REMOVAL...........................58
REMOVAL - 2.7L TURBO DIESEL.........60
INSTALLATION
INSTALLATION.......................61
INSTALLATION - 2.7L TURBO DIESEL......61
A/C CONDENSER
DESCRIPTION.........................62
OPERATION...........................62
REMOVAL.............................62
INSTALLATION.........................63
A/C DISCHARGE LINE
REMOVAL
REMOVAL - 2.7L TURBO DIESEL.........63
REMOVAL...........................64INSTALLATION
INSTALLATION - 2.7L TURBO DIESEL......64
INSTALLATION.......................65
A/C EXPANSION VALVE
DESCRIPTION.........................65
OPERATION...........................65
DIAGNOSIS AND TESTING - A/C EXPANSION
VALVE ..............................65
REMOVAL.............................66
INSTALLATION.........................66
LIQUID LINE
REMOVAL
REMOVAL...........................66
REMOVAL - 2.7L TURBO DIESEL.........66
INSTALLATION
INSTALLATION.......................66
INSTALLATION - 2.7L TURBO DIESEL......67
SUCTION LINE
REMOVAL
REMOVAL...........................67
REMOVAL - 2.7L TURBO DIESEL.........68
INSTALLATION
INSTALLATION.......................68
INSTALLATION - 2.7L TURBO DIESEL......69
A/C EVAPORATOR
DESCRIPTION.........................69
OPERATION...........................69
REMOVAL.............................69
INSTALLATION.........................70
HEATER CORE
DESCRIPTION.........................71
OPERATION...........................71
REMOVAL.............................71
INSTALLATION.........................71
RECEIVER / DRIER
DESCRIPTION.........................72
OPERATION...........................72
REMOVAL.............................73
INSTALLATION.........................73
REFRIGERANT
DESCRIPTION.........................75
OPERATION...........................75
REFRIGERANT OIL
DESCRIPTION.........................75
OPERATION...........................75
STANDARD PROCEDURE - REFRIGERANT
OIL LEVEL...........................75
WJPLUMBING 24 - 51
Page 2137 of 2199
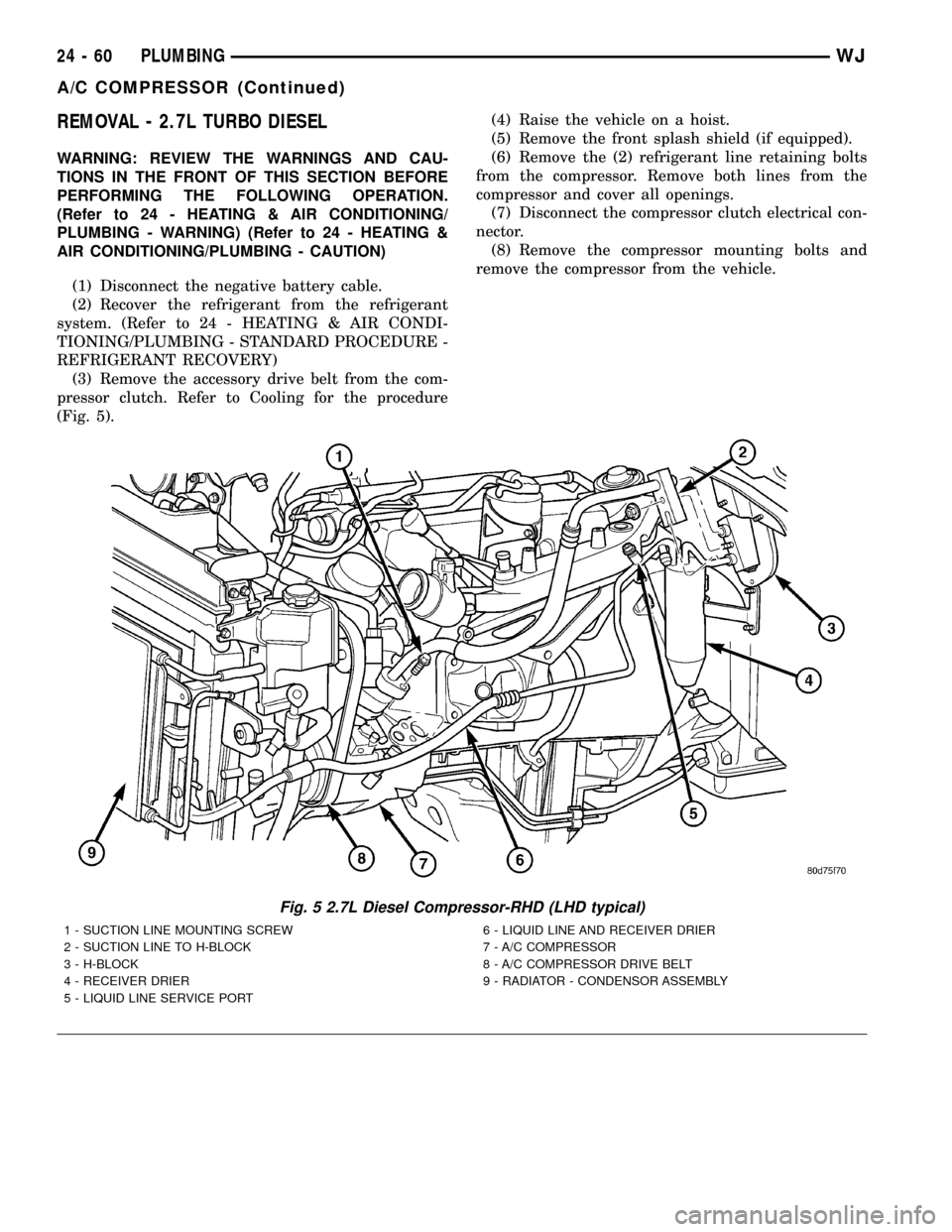
REMOVAL - 2.7L TURBO DIESEL
WARNING: REVIEW THE WARNINGS AND CAU-
TIONS IN THE FRONT OF THIS SECTION BEFORE
PERFORMING THE FOLLOWING OPERATION.
(Refer to 24 - HEATING & AIR CONDITIONING/
PLUMBING - WARNING) (Refer to 24 - HEATING &
AIR CONDITIONING/PLUMBING - CAUTION)
(1) Disconnect the negative battery cable.
(2) Recover the refrigerant from the refrigerant
system. (Refer to 24 - HEATING & AIR CONDI-
TIONING/PLUMBING - STANDARD PROCEDURE -
REFRIGERANT RECOVERY)
(3) Remove the accessory drive belt from the com-
pressor clutch. Refer to Cooling for the procedure
(Fig. 5).(4) Raise the vehicle on a hoist.
(5) Remove the front splash shield (if equipped).
(6) Remove the (2) refrigerant line retaining bolts
from the compressor. Remove both lines from the
compressor and cover all openings.
(7) Disconnect the compressor clutch electrical con-
nector.
(8) Remove the compressor mounting bolts and
remove the compressor from the vehicle.
Fig. 5 2.7L Diesel Compressor-RHD (LHD typical)
1 - SUCTION LINE MOUNTING SCREW
2 - SUCTION LINE TO H-BLOCK
3 - H-BLOCK
4 - RECEIVER DRIER
5 - LIQUID LINE SERVICE PORT6 - LIQUID LINE AND RECEIVER DRIER
7 - A/C COMPRESSOR
8 - A/C COMPRESSOR DRIVE BELT
9 - RADIATOR - CONDENSOR ASSEMBLY
24 - 60 PLUMBINGWJ
A/C COMPRESSOR (Continued)
Page 2138 of 2199
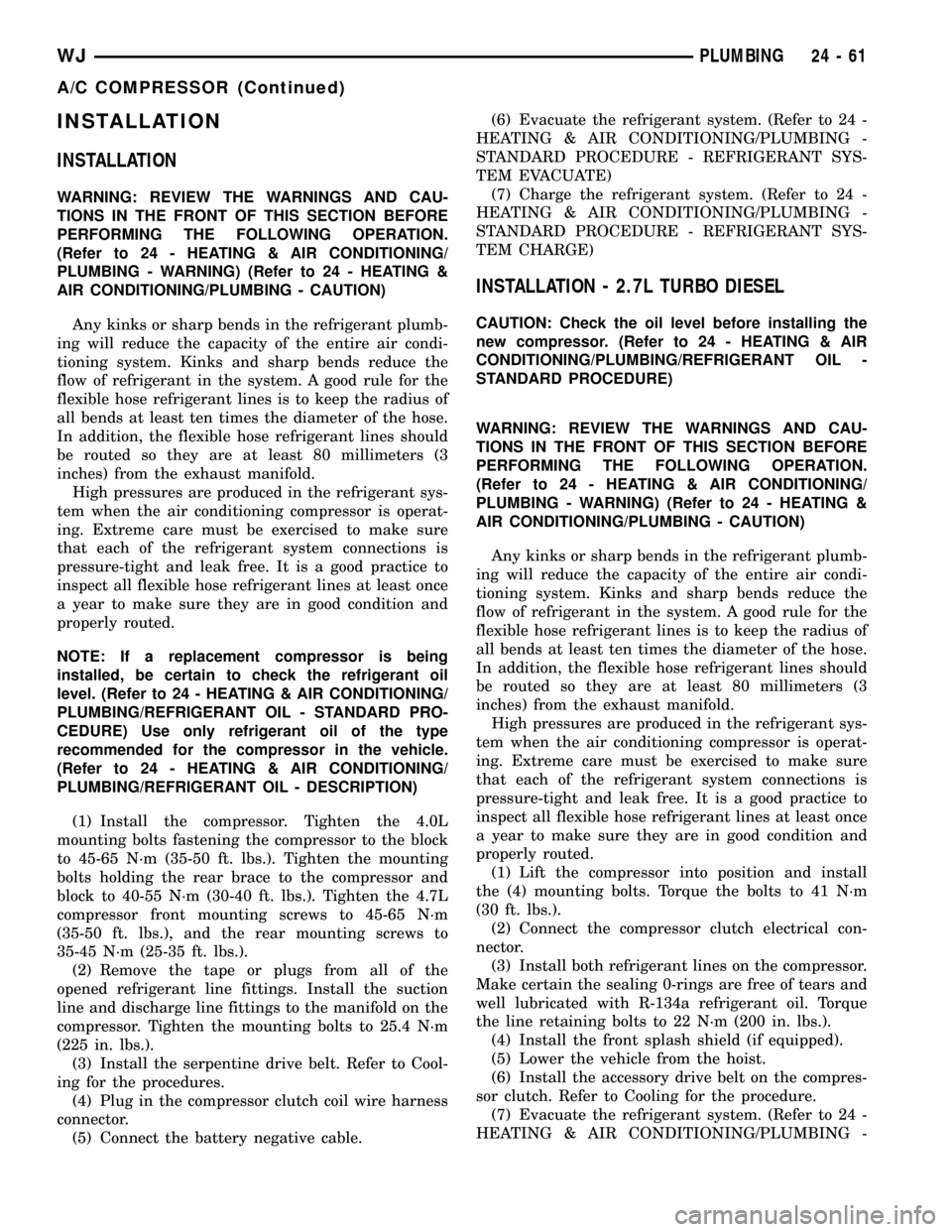
INSTALLATION
INSTALLATION
WARNING: REVIEW THE WARNINGS AND CAU-
TIONS IN THE FRONT OF THIS SECTION BEFORE
PERFORMING THE FOLLOWING OPERATION.
(Refer to 24 - HEATING & AIR CONDITIONING/
PLUMBING - WARNING) (Refer to 24 - HEATING &
AIR CONDITIONING/PLUMBING - CAUTION)
Any kinks or sharp bends in the refrigerant plumb-
ing will reduce the capacity of the entire air condi-
tioning system. Kinks and sharp bends reduce the
flow of refrigerant in the system. A good rule for the
flexible hose refrigerant lines is to keep the radius of
all bends at least ten times the diameter of the hose.
In addition, the flexible hose refrigerant lines should
be routed so they are at least 80 millimeters (3
inches) from the exhaust manifold.
High pressures are produced in the refrigerant sys-
tem when the air conditioning compressor is operat-
ing. Extreme care must be exercised to make sure
that each of the refrigerant system connections is
pressure-tight and leak free. It is a good practice to
inspect all flexible hose refrigerant lines at least once
a year to make sure they are in good condition and
properly routed.
NOTE: If a replacement compressor is being
installed, be certain to check the refrigerant oil
level. (Refer to 24 - HEATING & AIR CONDITIONING/
PLUMBING/REFRIGERANT OIL - STANDARD PRO-
CEDURE) Use only refrigerant oil of the type
recommended for the compressor in the vehicle.
(Refer to 24 - HEATING & AIR CONDITIONING/
PLUMBING/REFRIGERANT OIL - DESCRIPTION)
(1) Install the compressor. Tighten the 4.0L
mounting bolts fastening the compressor to the block
to 45-65 N´m (35-50 ft. lbs.). Tighten the mounting
bolts holding the rear brace to the compressor and
block to 40-55 N´m (30-40 ft. lbs.). Tighten the 4.7L
compressor front mounting screws to 45-65 N´m
(35-50 ft. lbs.), and the rear mounting screws to
35-45 N´m (25-35 ft. lbs.).
(2) Remove the tape or plugs from all of the
opened refrigerant line fittings. Install the suction
line and discharge line fittings to the manifold on the
compressor. Tighten the mounting bolts to 25.4 N´m
(225 in. lbs.).
(3) Install the serpentine drive belt. Refer to Cool-
ing for the procedures.
(4) Plug in the compressor clutch coil wire harness
connector.
(5) Connect the battery negative cable.(6) Evacuate the refrigerant system. (Refer to 24 -
HEATING & AIR CONDITIONING/PLUMBING -
STANDARD PROCEDURE - REFRIGERANT SYS-
TEM EVACUATE)
(7) Charge the refrigerant system. (Refer to 24 -
HEATING & AIR CONDITIONING/PLUMBING -
STANDARD PROCEDURE - REFRIGERANT SYS-
TEM CHARGE)
INSTALLATION - 2.7L TURBO DIESEL
CAUTION: Check the oil level before installing the
new compressor. (Refer to 24 - HEATING & AIR
CONDITIONING/PLUMBING/REFRIGERANT OIL -
STANDARD PROCEDURE)
WARNING: REVIEW THE WARNINGS AND CAU-
TIONS IN THE FRONT OF THIS SECTION BEFORE
PERFORMING THE FOLLOWING OPERATION.
(Refer to 24 - HEATING & AIR CONDITIONING/
PLUMBING - WARNING) (Refer to 24 - HEATING &
AIR CONDITIONING/PLUMBING - CAUTION)
Any kinks or sharp bends in the refrigerant plumb-
ing will reduce the capacity of the entire air condi-
tioning system. Kinks and sharp bends reduce the
flow of refrigerant in the system. A good rule for the
flexible hose refrigerant lines is to keep the radius of
all bends at least ten times the diameter of the hose.
In addition, the flexible hose refrigerant lines should
be routed so they are at least 80 millimeters (3
inches) from the exhaust manifold.
High pressures are produced in the refrigerant sys-
tem when the air conditioning compressor is operat-
ing. Extreme care must be exercised to make sure
that each of the refrigerant system connections is
pressure-tight and leak free. It is a good practice to
inspect all flexible hose refrigerant lines at least once
a year to make sure they are in good condition and
properly routed.
(1) Lift the compressor into position and install
the (4) mounting bolts. Torque the bolts to 41 N´m
(30 ft. lbs.).
(2) Connect the compressor clutch electrical con-
nector.
(3) Install both refrigerant lines on the compressor.
Make certain the sealing 0-rings are free of tears and
well lubricated with R-134a refrigerant oil. Torque
the line retaining bolts to 22 N´m (200 in. lbs.).
(4) Install the front splash shield (if equipped).
(5) Lower the vehicle from the hoist.
(6) Install the accessory drive belt on the compres-
sor clutch. Refer to Cooling for the procedure.
(7) Evacuate the refrigerant system. (Refer to 24 -
HEATING & AIR CONDITIONING/PLUMBING -
WJPLUMBING 24 - 61
A/C COMPRESSOR (Continued)
Page 2140 of 2199
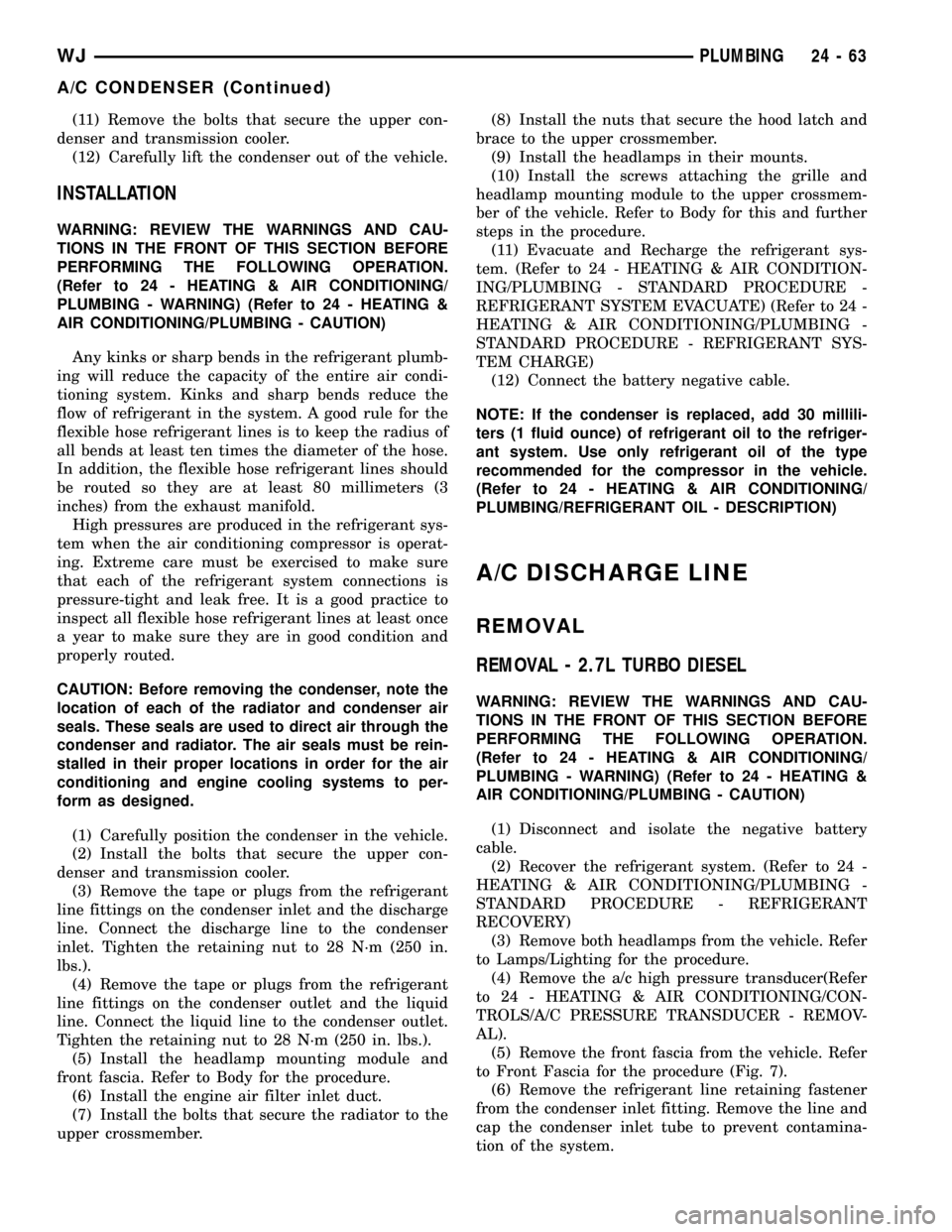
(11) Remove the bolts that secure the upper con-
denser and transmission cooler.
(12) Carefully lift the condenser out of the vehicle.
INSTALLATION
WARNING: REVIEW THE WARNINGS AND CAU-
TIONS IN THE FRONT OF THIS SECTION BEFORE
PERFORMING THE FOLLOWING OPERATION.
(Refer to 24 - HEATING & AIR CONDITIONING/
PLUMBING - WARNING) (Refer to 24 - HEATING &
AIR CONDITIONING/PLUMBING - CAUTION)
Any kinks or sharp bends in the refrigerant plumb-
ing will reduce the capacity of the entire air condi-
tioning system. Kinks and sharp bends reduce the
flow of refrigerant in the system. A good rule for the
flexible hose refrigerant lines is to keep the radius of
all bends at least ten times the diameter of the hose.
In addition, the flexible hose refrigerant lines should
be routed so they are at least 80 millimeters (3
inches) from the exhaust manifold.
High pressures are produced in the refrigerant sys-
tem when the air conditioning compressor is operat-
ing. Extreme care must be exercised to make sure
that each of the refrigerant system connections is
pressure-tight and leak free. It is a good practice to
inspect all flexible hose refrigerant lines at least once
a year to make sure they are in good condition and
properly routed.
CAUTION: Before removing the condenser, note the
location of each of the radiator and condenser air
seals. These seals are used to direct air through the
condenser and radiator. The air seals must be rein-
stalled in their proper locations in order for the air
conditioning and engine cooling systems to per-
form as designed.
(1) Carefully position the condenser in the vehicle.
(2) Install the bolts that secure the upper con-
denser and transmission cooler.
(3) Remove the tape or plugs from the refrigerant
line fittings on the condenser inlet and the discharge
line. Connect the discharge line to the condenser
inlet. Tighten the retaining nut to 28 N´m (250 in.
lbs.).
(4) Remove the tape or plugs from the refrigerant
line fittings on the condenser outlet and the liquid
line. Connect the liquid line to the condenser outlet.
Tighten the retaining nut to 28 N´m (250 in. lbs.).
(5) Install the headlamp mounting module and
front fascia. Refer to Body for the procedure.
(6) Install the engine air filter inlet duct.
(7) Install the bolts that secure the radiator to the
upper crossmember.(8) Install the nuts that secure the hood latch and
brace to the upper crossmember.
(9) Install the headlamps in their mounts.
(10) Install the screws attaching the grille and
headlamp mounting module to the upper crossmem-
ber of the vehicle. Refer to Body for this and further
steps in the procedure.
(11) Evacuate and Recharge the refrigerant sys-
tem. (Refer to 24 - HEATING & AIR CONDITION-
ING/PLUMBING - STANDARD PROCEDURE -
REFRIGERANT SYSTEM EVACUATE) (Refer to 24 -
HEATING & AIR CONDITIONING/PLUMBING -
STANDARD PROCEDURE - REFRIGERANT SYS-
TEM CHARGE)
(12) Connect the battery negative cable.
NOTE: If the condenser is replaced, add 30 millili-
ters (1 fluid ounce) of refrigerant oil to the refriger-
ant system. Use only refrigerant oil of the type
recommended for the compressor in the vehicle.
(Refer to 24 - HEATING & AIR CONDITIONING/
PLUMBING/REFRIGERANT OIL - DESCRIPTION)
A/C DISCHARGE LINE
REMOVAL
REMOVAL - 2.7L TURBO DIESEL
WARNING: REVIEW THE WARNINGS AND CAU-
TIONS IN THE FRONT OF THIS SECTION BEFORE
PERFORMING THE FOLLOWING OPERATION.
(Refer to 24 - HEATING & AIR CONDITIONING/
PLUMBING - WARNING) (Refer to 24 - HEATING &
AIR CONDITIONING/PLUMBING - CAUTION)
(1) Disconnect and isolate the negative battery
cable.
(2) Recover the refrigerant system. (Refer to 24 -
HEATING & AIR CONDITIONING/PLUMBING -
STANDARD PROCEDURE - REFRIGERANT
RECOVERY)
(3) Remove both headlamps from the vehicle. Refer
to Lamps/Lighting for the procedure.
(4) Remove the a/c high pressure transducer(Refer
to 24 - HEATING & AIR CONDITIONING/CON-
TROLS/A/C PRESSURE TRANSDUCER - REMOV-
AL).
(5) Remove the front fascia from the vehicle. Refer
to Front Fascia for the procedure (Fig. 7).
(6) Remove the refrigerant line retaining fastener
from the condenser inlet fitting. Remove the line and
cap the condenser inlet tube to prevent contamina-
tion of the system.
WJPLUMBING 24 - 63
A/C CONDENSER (Continued)
Page 2141 of 2199
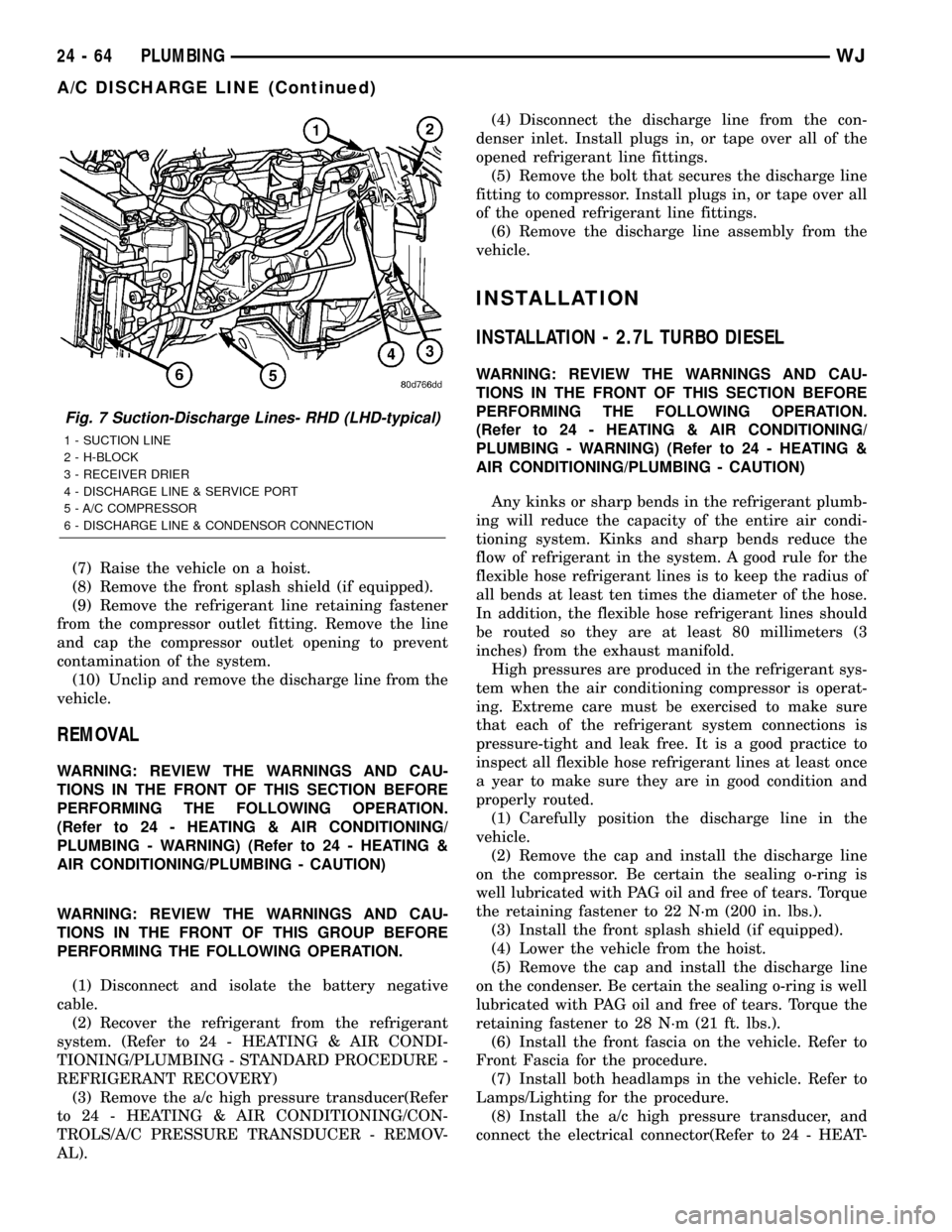
(7) Raise the vehicle on a hoist.
(8) Remove the front splash shield (if equipped).
(9) Remove the refrigerant line retaining fastener
from the compressor outlet fitting. Remove the line
and cap the compressor outlet opening to prevent
contamination of the system.
(10) Unclip and remove the discharge line from the
vehicle.
REMOVAL
WARNING: REVIEW THE WARNINGS AND CAU-
TIONS IN THE FRONT OF THIS SECTION BEFORE
PERFORMING THE FOLLOWING OPERATION.
(Refer to 24 - HEATING & AIR CONDITIONING/
PLUMBING - WARNING) (Refer to 24 - HEATING &
AIR CONDITIONING/PLUMBING - CAUTION)
WARNING: REVIEW THE WARNINGS AND CAU-
TIONS IN THE FRONT OF THIS GROUP BEFORE
PERFORMING THE FOLLOWING OPERATION.
(1) Disconnect and isolate the battery negative
cable.
(2) Recover the refrigerant from the refrigerant
system. (Refer to 24 - HEATING & AIR CONDI-
TIONING/PLUMBING - STANDARD PROCEDURE -
REFRIGERANT RECOVERY)
(3) Remove the a/c high pressure transducer(Refer
to 24 - HEATING & AIR CONDITIONING/CON-
TROLS/A/C PRESSURE TRANSDUCER - REMOV-
AL).(4) Disconnect the discharge line from the con-
denser inlet. Install plugs in, or tape over all of the
opened refrigerant line fittings.
(5) Remove the bolt that secures the discharge line
fitting to compressor. Install plugs in, or tape over all
of the opened refrigerant line fittings.
(6) Remove the discharge line assembly from the
vehicle.
INSTALLATION
INSTALLATION - 2.7L TURBO DIESEL
WARNING: REVIEW THE WARNINGS AND CAU-
TIONS IN THE FRONT OF THIS SECTION BEFORE
PERFORMING THE FOLLOWING OPERATION.
(Refer to 24 - HEATING & AIR CONDITIONING/
PLUMBING - WARNING) (Refer to 24 - HEATING &
AIR CONDITIONING/PLUMBING - CAUTION)
Any kinks or sharp bends in the refrigerant plumb-
ing will reduce the capacity of the entire air condi-
tioning system. Kinks and sharp bends reduce the
flow of refrigerant in the system. A good rule for the
flexible hose refrigerant lines is to keep the radius of
all bends at least ten times the diameter of the hose.
In addition, the flexible hose refrigerant lines should
be routed so they are at least 80 millimeters (3
inches) from the exhaust manifold.
High pressures are produced in the refrigerant sys-
tem when the air conditioning compressor is operat-
ing. Extreme care must be exercised to make sure
that each of the refrigerant system connections is
pressure-tight and leak free. It is a good practice to
inspect all flexible hose refrigerant lines at least once
a year to make sure they are in good condition and
properly routed.
(1) Carefully position the discharge line in the
vehicle.
(2) Remove the cap and install the discharge line
on the compressor. Be certain the sealing o-ring is
well lubricated with PAG oil and free of tears. Torque
the retaining fastener to 22 N´m (200 in. lbs.).
(3) Install the front splash shield (if equipped).
(4) Lower the vehicle from the hoist.
(5) Remove the cap and install the discharge line
on the condenser. Be certain the sealing o-ring is well
lubricated with PAG oil and free of tears. Torque the
retaining fastener to 28 N´m (21 ft. lbs.).
(6) Install the front fascia on the vehicle. Refer to
Front Fascia for the procedure.
(7) Install both headlamps in the vehicle. Refer to
Lamps/Lighting for the procedure.
(8) Install the a/c high pressure transducer, and
connect the electrical connector(Refer to 24 - HEAT-
Fig. 7 Suction-Discharge Lines- RHD (LHD-typical)
1 - SUCTION LINE
2 - H-BLOCK
3 - RECEIVER DRIER
4 - DISCHARGE LINE & SERVICE PORT
5 - A/C COMPRESSOR
6 - DISCHARGE LINE & CONDENSOR CONNECTION
24 - 64 PLUMBINGWJ
A/C DISCHARGE LINE (Continued)
Page 2143 of 2199
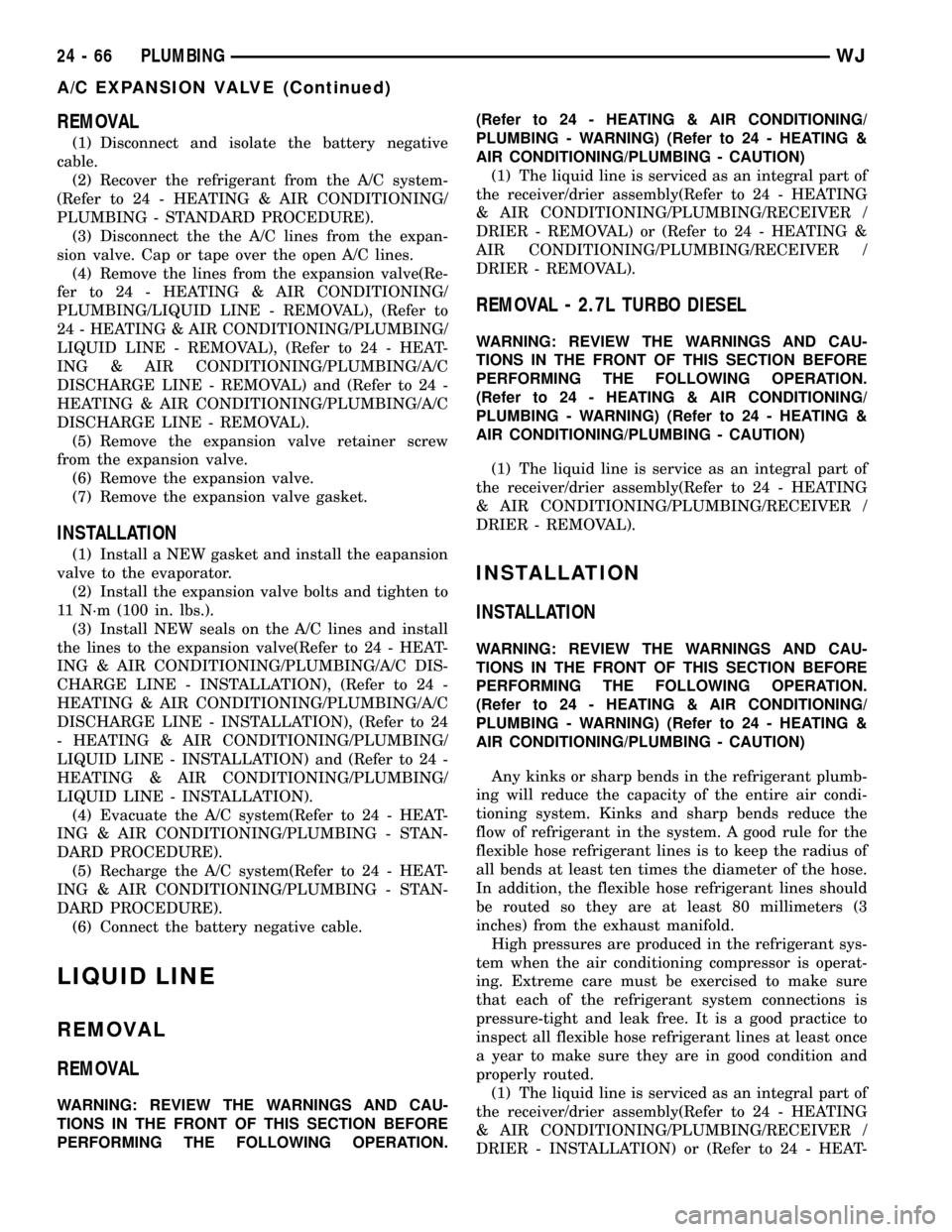
REMOVAL
(1) Disconnect and isolate the battery negative
cable.
(2) Recover the refrigerant from the A/C system-
(Refer to 24 - HEATING & AIR CONDITIONING/
PLUMBING - STANDARD PROCEDURE).
(3) Disconnect the the A/C lines from the expan-
sion valve. Cap or tape over the open A/C lines.
(4) Remove the lines from the expansion valve(Re-
fer to 24 - HEATING & AIR CONDITIONING/
PLUMBING/LIQUID LINE - REMOVAL), (Refer to
24 - HEATING & AIR CONDITIONING/PLUMBING/
LIQUID LINE - REMOVAL), (Refer to 24 - HEAT-
ING & AIR CONDITIONING/PLUMBING/A/C
DISCHARGE LINE - REMOVAL) and (Refer to 24 -
HEATING & AIR CONDITIONING/PLUMBING/A/C
DISCHARGE LINE - REMOVAL).
(5) Remove the expansion valve retainer screw
from the expansion valve.
(6) Remove the expansion valve.
(7) Remove the expansion valve gasket.
INSTALLATION
(1) Install a NEW gasket and install the eapansion
valve to the evaporator.
(2) Install the expansion valve bolts and tighten to
11 N´m (100 in. lbs.).
(3) Install NEW seals on the A/C lines and install
the lines to the expansion valve(Refer to 24 - HEAT-
ING & AIR CONDITIONING/PLUMBING/A/C DIS-
CHARGE LINE - INSTALLATION), (Refer to 24 -
HEATING & AIR CONDITIONING/PLUMBING/A/C
DISCHARGE LINE - INSTALLATION), (Refer to 24
- HEATING & AIR CONDITIONING/PLUMBING/
LIQUID LINE - INSTALLATION) and (Refer to 24 -
HEATING & AIR CONDITIONING/PLUMBING/
LIQUID LINE - INSTALLATION).
(4) Evacuate the A/C system(Refer to 24 - HEAT-
ING & AIR CONDITIONING/PLUMBING - STAN-
DARD PROCEDURE).
(5) Recharge the A/C system(Refer to 24 - HEAT-
ING & AIR CONDITIONING/PLUMBING - STAN-
DARD PROCEDURE).
(6) Connect the battery negative cable.
LIQUID LINE
REMOVAL
REMOVAL
WARNING: REVIEW THE WARNINGS AND CAU-
TIONS IN THE FRONT OF THIS SECTION BEFORE
PERFORMING THE FOLLOWING OPERATION.(Refer to 24 - HEATING & AIR CONDITIONING/
PLUMBING - WARNING) (Refer to 24 - HEATING &
AIR CONDITIONING/PLUMBING - CAUTION)
(1) The liquid line is serviced as an integral part of
the receiver/drier assembly(Refer to 24 - HEATING
& AIR CONDITIONING/PLUMBING/RECEIVER /
DRIER - REMOVAL) or (Refer to 24 - HEATING &
AIR CONDITIONING/PLUMBING/RECEIVER /
DRIER - REMOVAL).
REMOVAL - 2.7L TURBO DIESEL
WARNING: REVIEW THE WARNINGS AND CAU-
TIONS IN THE FRONT OF THIS SECTION BEFORE
PERFORMING THE FOLLOWING OPERATION.
(Refer to 24 - HEATING & AIR CONDITIONING/
PLUMBING - WARNING) (Refer to 24 - HEATING &
AIR CONDITIONING/PLUMBING - CAUTION)
(1) The liquid line is service as an integral part of
the receiver/drier assembly(Refer to 24 - HEATING
& AIR CONDITIONING/PLUMBING/RECEIVER /
DRIER - REMOVAL).
INSTALLATION
INSTALLATION
WARNING: REVIEW THE WARNINGS AND CAU-
TIONS IN THE FRONT OF THIS SECTION BEFORE
PERFORMING THE FOLLOWING OPERATION.
(Refer to 24 - HEATING & AIR CONDITIONING/
PLUMBING - WARNING) (Refer to 24 - HEATING &
AIR CONDITIONING/PLUMBING - CAUTION)
Any kinks or sharp bends in the refrigerant plumb-
ing will reduce the capacity of the entire air condi-
tioning system. Kinks and sharp bends reduce the
flow of refrigerant in the system. A good rule for the
flexible hose refrigerant lines is to keep the radius of
all bends at least ten times the diameter of the hose.
In addition, the flexible hose refrigerant lines should
be routed so they are at least 80 millimeters (3
inches) from the exhaust manifold.
High pressures are produced in the refrigerant sys-
tem when the air conditioning compressor is operat-
ing. Extreme care must be exercised to make sure
that each of the refrigerant system connections is
pressure-tight and leak free. It is a good practice to
inspect all flexible hose refrigerant lines at least once
a year to make sure they are in good condition and
properly routed.
(1) The liquid line is serviced as an integral part of
the receiver/drier assembly(Refer to 24 - HEATING
& AIR CONDITIONING/PLUMBING/RECEIVER /
DRIER - INSTALLATION) or (Refer to 24 - HEAT-
24 - 66 PLUMBINGWJ
A/C EXPANSION VALVE (Continued)