electrical circuit JEEP GRAND CHEROKEE 2002 WJ / 2.G Workshop Manual
[x] Cancel search | Manufacturer: JEEP, Model Year: 2002, Model line: GRAND CHEROKEE, Model: JEEP GRAND CHEROKEE 2002 WJ / 2.GPages: 2199, PDF Size: 76.01 MB
Page 216 of 2199
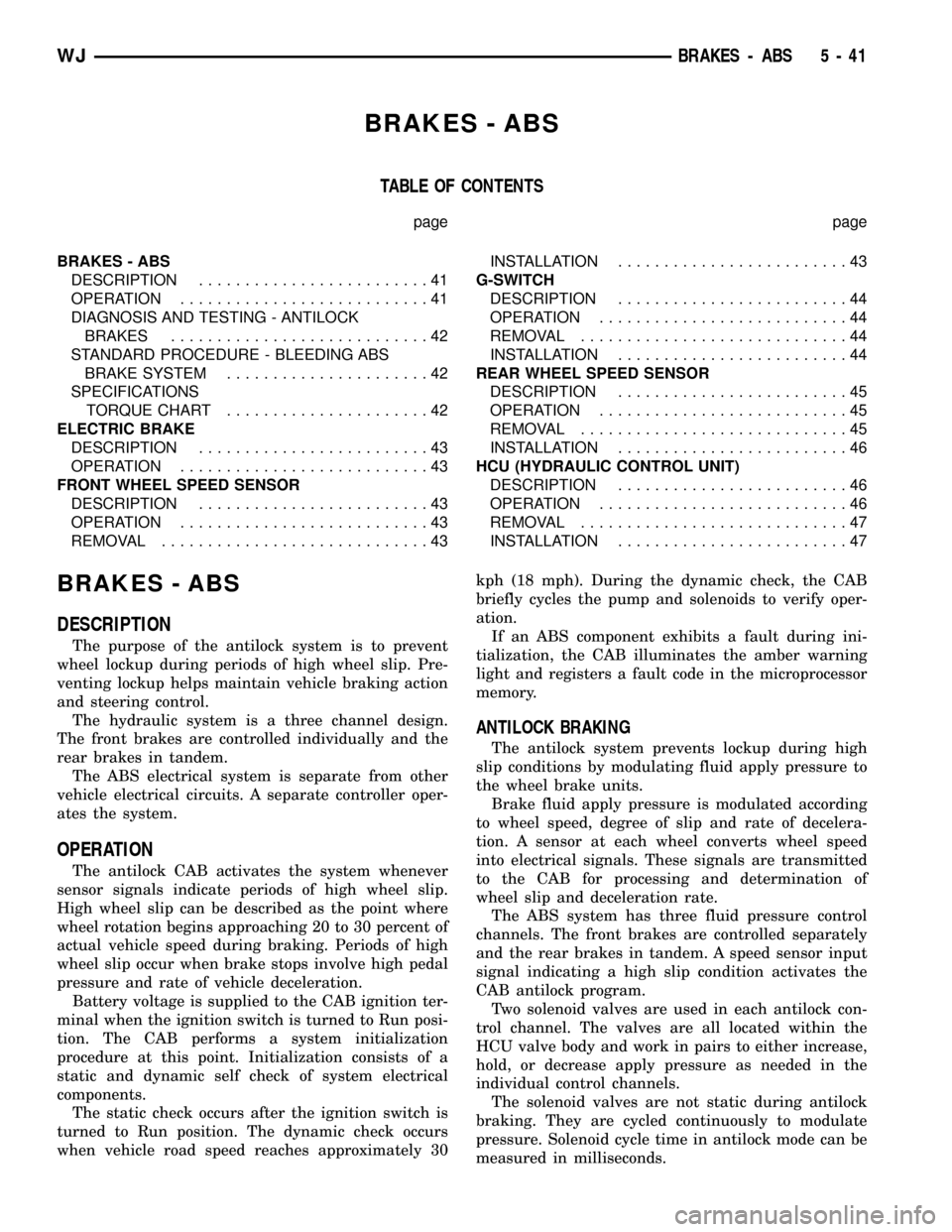
BRAKES - ABS
TABLE OF CONTENTS
page page
BRAKES - ABS
DESCRIPTION.........................41
OPERATION...........................41
DIAGNOSIS AND TESTING - ANTILOCK
BRAKES............................42
STANDARD PROCEDURE - BLEEDING ABS
BRAKE SYSTEM......................42
SPECIFICATIONS
TORQUE CHART......................42
ELECTRIC BRAKE
DESCRIPTION.........................43
OPERATION...........................43
FRONT WHEEL SPEED SENSOR
DESCRIPTION.........................43
OPERATION...........................43
REMOVAL.............................43INSTALLATION.........................43
G-SWITCH
DESCRIPTION.........................44
OPERATION...........................44
REMOVAL.............................44
INSTALLATION.........................44
REAR WHEEL SPEED SENSOR
DESCRIPTION.........................45
OPERATION...........................45
REMOVAL.............................45
INSTALLATION.........................46
HCU (HYDRAULIC CONTROL UNIT)
DESCRIPTION.........................46
OPERATION...........................46
REMOVAL.............................47
INSTALLATION.........................47
BRAKES - ABS
DESCRIPTION
The purpose of the antilock system is to prevent
wheel lockup during periods of high wheel slip. Pre-
venting lockup helps maintain vehicle braking action
and steering control.
The hydraulic system is a three channel design.
The front brakes are controlled individually and the
rear brakes in tandem.
The ABS electrical system is separate from other
vehicle electrical circuits. A separate controller oper-
ates the system.
OPERATION
The antilock CAB activates the system whenever
sensor signals indicate periods of high wheel slip.
High wheel slip can be described as the point where
wheel rotation begins approaching 20 to 30 percent of
actual vehicle speed during braking. Periods of high
wheel slip occur when brake stops involve high pedal
pressure and rate of vehicle deceleration.
Battery voltage is supplied to the CAB ignition ter-
minal when the ignition switch is turned to Run posi-
tion. The CAB performs a system initialization
procedure at this point. Initialization consists of a
static and dynamic self check of system electrical
components.
The static check occurs after the ignition switch is
turned to Run position. The dynamic check occurs
when vehicle road speed reaches approximately 30kph (18 mph). During the dynamic check, the CAB
briefly cycles the pump and solenoids to verify oper-
ation.
If an ABS component exhibits a fault during ini-
tialization, the CAB illuminates the amber warning
light and registers a fault code in the microprocessor
memory.
ANTILOCK BRAKING
The antilock system prevents lockup during high
slip conditions by modulating fluid apply pressure to
the wheel brake units.
Brake fluid apply pressure is modulated according
to wheel speed, degree of slip and rate of decelera-
tion. A sensor at each wheel converts wheel speed
into electrical signals. These signals are transmitted
to the CAB for processing and determination of
wheel slip and deceleration rate.
The ABS system has three fluid pressure control
channels. The front brakes are controlled separately
and the rear brakes in tandem. A speed sensor input
signal indicating a high slip condition activates the
CAB antilock program.
Two solenoid valves are used in each antilock con-
trol channel. The valves are all located within the
HCU valve body and work in pairs to either increase,
hold, or decrease apply pressure as needed in the
individual control channels.
The solenoid valves are not static during antilock
braking. They are cycled continuously to modulate
pressure. Solenoid cycle time in antilock mode can be
measured in milliseconds.
WJBRAKES - ABS 5 - 41
Page 217 of 2199
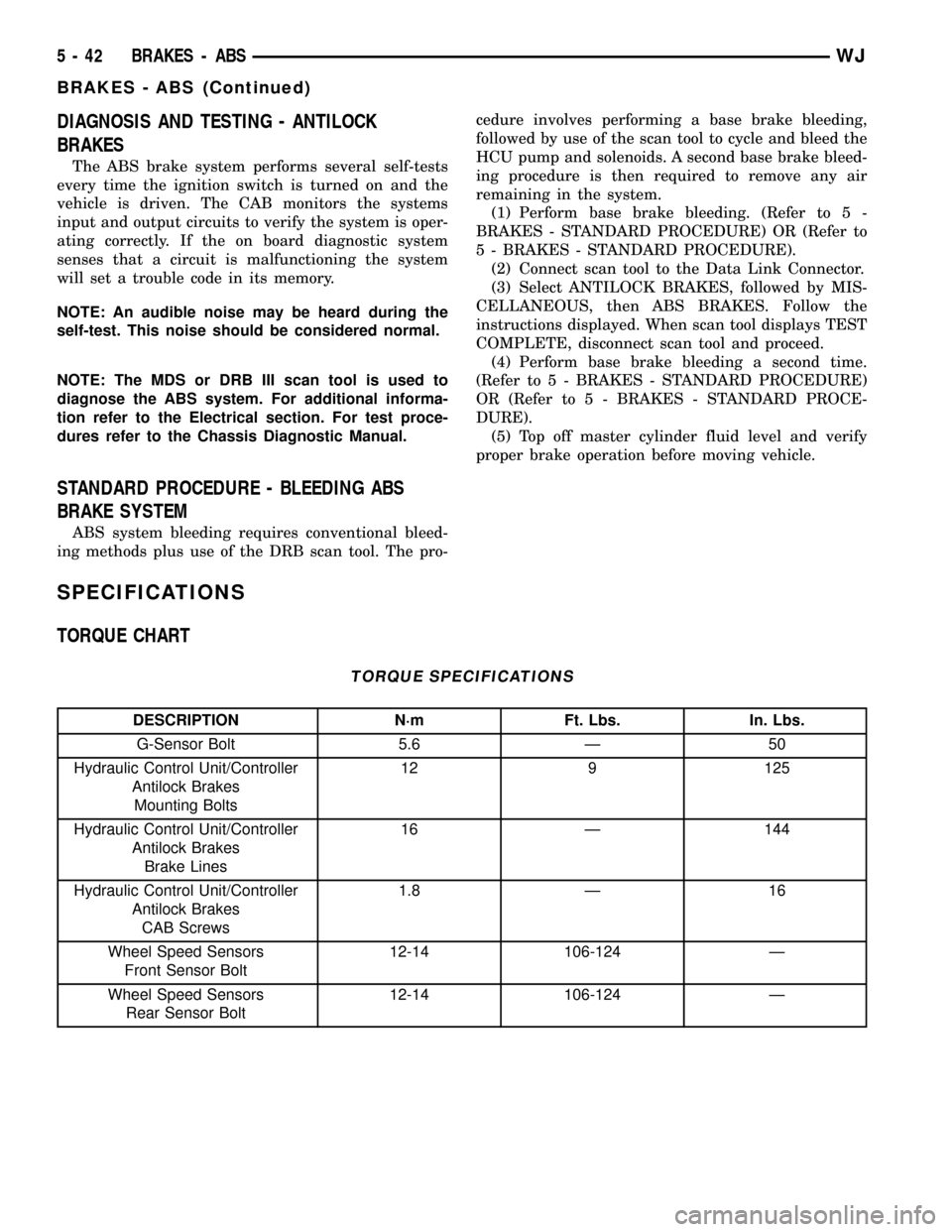
DIAGNOSIS AND TESTING - ANTILOCK
BRAKES
The ABS brake system performs several self-tests
every time the ignition switch is turned on and the
vehicle is driven. The CAB monitors the systems
input and output circuits to verify the system is oper-
ating correctly. If the on board diagnostic system
senses that a circuit is malfunctioning the system
will set a trouble code in its memory.
NOTE: An audible noise may be heard during the
self-test. This noise should be considered normal.
NOTE: The MDS or DRB III scan tool is used to
diagnose the ABS system. For additional informa-
tion refer to the Electrical section. For test proce-
dures refer to the Chassis Diagnostic Manual.
STANDARD PROCEDURE - BLEEDING ABS
BRAKE SYSTEM
ABS system bleeding requires conventional bleed-
ing methods plus use of the DRB scan tool. The pro-cedure involves performing a base brake bleeding,
followed by use of the scan tool to cycle and bleed the
HCU pump and solenoids. A second base brake bleed-
ing procedure is then required to remove any air
remaining in the system.
(1) Perform base brake bleeding. (Refer to 5 -
BRAKES - STANDARD PROCEDURE) OR (Refer to
5 - BRAKES - STANDARD PROCEDURE).
(2) Connect scan tool to the Data Link Connector.
(3) Select ANTILOCK BRAKES, followed by MIS-
CELLANEOUS, then ABS BRAKES. Follow the
instructions displayed. When scan tool displays TEST
COMPLETE, disconnect scan tool and proceed.
(4) Perform base brake bleeding a second time.
(Refer to 5 - BRAKES - STANDARD PROCEDURE)
OR (Refer to 5 - BRAKES - STANDARD PROCE-
DURE).
(5) Top off master cylinder fluid level and verify
proper brake operation before moving vehicle.
SPECIFICATIONS
TORQUE CHART
TORQUE SPECIFICATIONS
DESCRIPTION N´m Ft. Lbs. In. Lbs.
G-Sensor Bolt 5.6 Ð 50
Hydraulic Control Unit/Controller
Antilock Brakes
Mounting Bolts12 9 125
Hydraulic Control Unit/Controller
Antilock Brakes
Brake Lines16 Ð 144
Hydraulic Control Unit/Controller
Antilock Brakes
CAB Screws1.8 Ð 16
Wheel Speed Sensors
Front Sensor Bolt12-14 106-124 Ð
Wheel Speed Sensors
Rear Sensor Bolt12-14 106-124 Ð
5 - 42 BRAKES - ABSWJ
BRAKES - ABS (Continued)
Page 252 of 2199
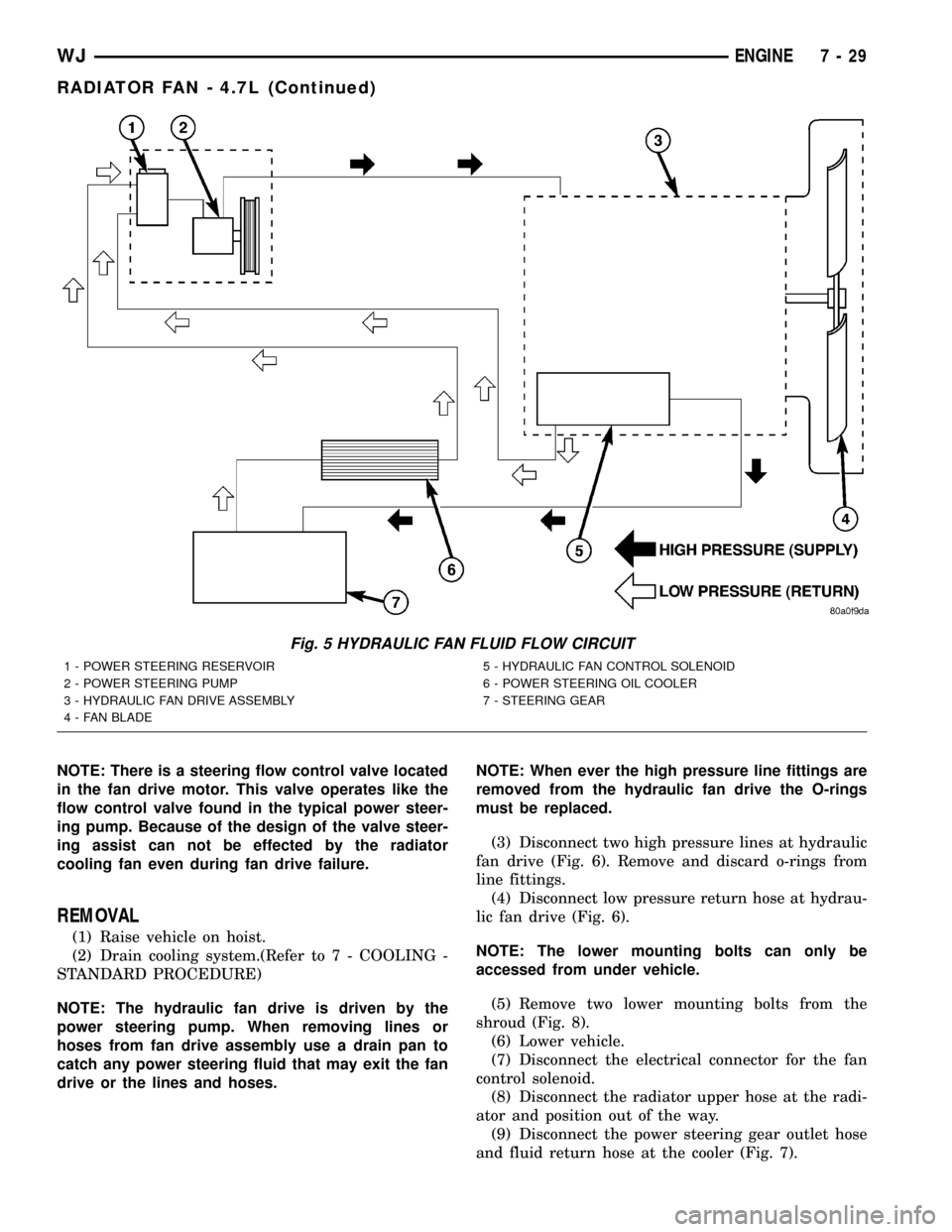
NOTE: There is a steering flow control valve located
in the fan drive motor. This valve operates like the
flow control valve found in the typical power steer-
ing pump. Because of the design of the valve steer-
ing assist can not be effected by the radiator
cooling fan even during fan drive failure.
REMOVAL
(1) Raise vehicle on hoist.
(2) Drain cooling system.(Refer to 7 - COOLING -
STANDARD PROCEDURE)
NOTE: The hydraulic fan drive is driven by the
power steering pump. When removing lines or
hoses from fan drive assembly use a drain pan to
catch any power steering fluid that may exit the fan
drive or the lines and hoses.NOTE: When ever the high pressure line fittings are
removed from the hydraulic fan drive the O-rings
must be replaced.
(3) Disconnect two high pressure lines at hydraulic
fan drive (Fig. 6). Remove and discard o-rings from
line fittings.
(4) Disconnect low pressure return hose at hydrau-
lic fan drive (Fig. 6).
NOTE: The lower mounting bolts can only be
accessed from under vehicle.
(5) Remove two lower mounting bolts from the
shroud (Fig. 8).
(6) Lower vehicle.
(7) Disconnect the electrical connector for the fan
control solenoid.
(8) Disconnect the radiator upper hose at the radi-
ator and position out of the way.
(9) Disconnect the power steering gear outlet hose
and fluid return hose at the cooler (Fig. 7).
Fig. 5 HYDRAULIC FAN FLUID FLOW CIRCUIT
1 - POWER STEERING RESERVOIR
2 - POWER STEERING PUMP
3 - HYDRAULIC FAN DRIVE ASSEMBLY
4 - FAN BLADE5 - HYDRAULIC FAN CONTROL SOLENOID
6 - POWER STEERING OIL COOLER
7 - STEERING GEAR
WJENGINE 7 - 29
RADIATOR FAN - 4.7L (Continued)
Page 270 of 2199
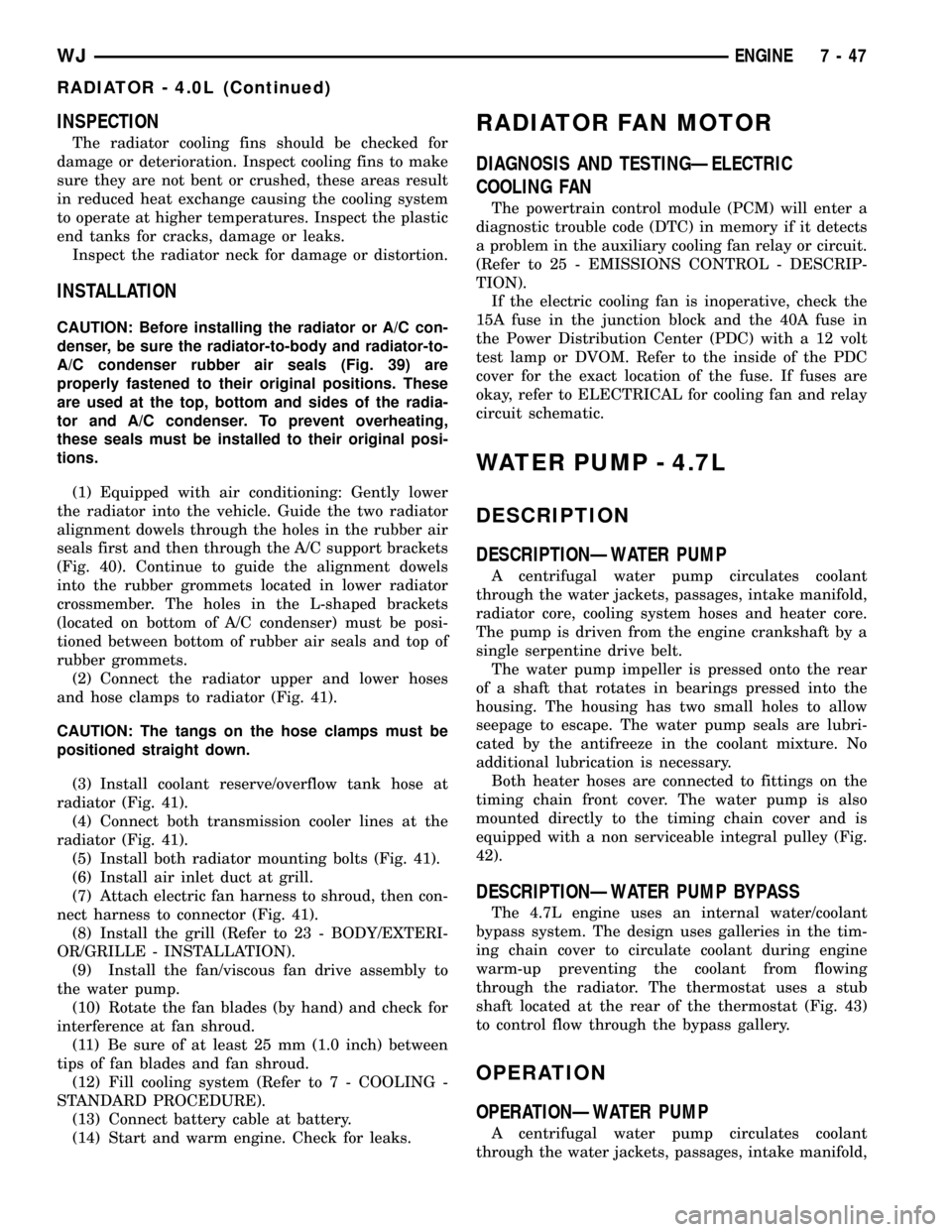
INSPECTION
The radiator cooling fins should be checked for
damage or deterioration. Inspect cooling fins to make
sure they are not bent or crushed, these areas result
in reduced heat exchange causing the cooling system
to operate at higher temperatures. Inspect the plastic
end tanks for cracks, damage or leaks.
Inspect the radiator neck for damage or distortion.
INSTALLATION
CAUTION: Before installing the radiator or A/C con-
denser, be sure the radiator-to-body and radiator-to-
A/C condenser rubber air seals (Fig. 39) are
properly fastened to their original positions. These
are used at the top, bottom and sides of the radia-
tor and A/C condenser. To prevent overheating,
these seals must be installed to their original posi-
tions.
(1) Equipped with air conditioning: Gently lower
the radiator into the vehicle. Guide the two radiator
alignment dowels through the holes in the rubber air
seals first and then through the A/C support brackets
(Fig. 40). Continue to guide the alignment dowels
into the rubber grommets located in lower radiator
crossmember. The holes in the L-shaped brackets
(located on bottom of A/C condenser) must be posi-
tioned between bottom of rubber air seals and top of
rubber grommets.
(2) Connect the radiator upper and lower hoses
and hose clamps to radiator (Fig. 41).
CAUTION: The tangs on the hose clamps must be
positioned straight down.
(3) Install coolant reserve/overflow tank hose at
radiator (Fig. 41).
(4) Connect both transmission cooler lines at the
radiator (Fig. 41).
(5) Install both radiator mounting bolts (Fig. 41).
(6) Install air inlet duct at grill.
(7) Attach electric fan harness to shroud, then con-
nect harness to connector (Fig. 41).
(8) Install the grill (Refer to 23 - BODY/EXTERI-
OR/GRILLE - INSTALLATION).
(9) Install the fan/viscous fan drive assembly to
the water pump.
(10) Rotate the fan blades (by hand) and check for
interference at fan shroud.
(11) Be sure of at least 25 mm (1.0 inch) between
tips of fan blades and fan shroud.
(12) Fill cooling system (Refer to 7 - COOLING -
STANDARD PROCEDURE).
(13) Connect battery cable at battery.
(14) Start and warm engine. Check for leaks.
RADIATOR FAN MOTOR
DIAGNOSIS AND TESTINGÐELECTRIC
COOLING FAN
The powertrain control module (PCM) will enter a
diagnostic trouble code (DTC) in memory if it detects
a problem in the auxiliary cooling fan relay or circuit.
(Refer to 25 - EMISSIONS CONTROL - DESCRIP-
TION).
If the electric cooling fan is inoperative, check the
15A fuse in the junction block and the 40A fuse in
the Power Distribution Center (PDC) with a 12 volt
test lamp or DVOM. Refer to the inside of the PDC
cover for the exact location of the fuse. If fuses are
okay, refer to ELECTRICAL for cooling fan and relay
circuit schematic.
WATER PUMP - 4.7L
DESCRIPTION
DESCRIPTIONÐWATER PUMP
A centrifugal water pump circulates coolant
through the water jackets, passages, intake manifold,
radiator core, cooling system hoses and heater core.
The pump is driven from the engine crankshaft by a
single serpentine drive belt.
The water pump impeller is pressed onto the rear
of a shaft that rotates in bearings pressed into the
housing. The housing has two small holes to allow
seepage to escape. The water pump seals are lubri-
cated by the antifreeze in the coolant mixture. No
additional lubrication is necessary.
Both heater hoses are connected to fittings on the
timing chain front cover. The water pump is also
mounted directly to the timing chain cover and is
equipped with a non serviceable integral pulley (Fig.
42).
DESCRIPTIONÐWATER PUMP BYPASS
The 4.7L engine uses an internal water/coolant
bypass system. The design uses galleries in the tim-
ing chain cover to circulate coolant during engine
warm-up preventing the coolant from flowing
through the radiator. The thermostat uses a stub
shaft located at the rear of the thermostat (Fig. 43)
to control flow through the bypass gallery.
OPERATION
OPERATIONÐWATER PUMP
A centrifugal water pump circulates coolant
through the water jackets, passages, intake manifold,
WJENGINE 7 - 47
RADIATOR - 4.0L (Continued)
Page 281 of 2199
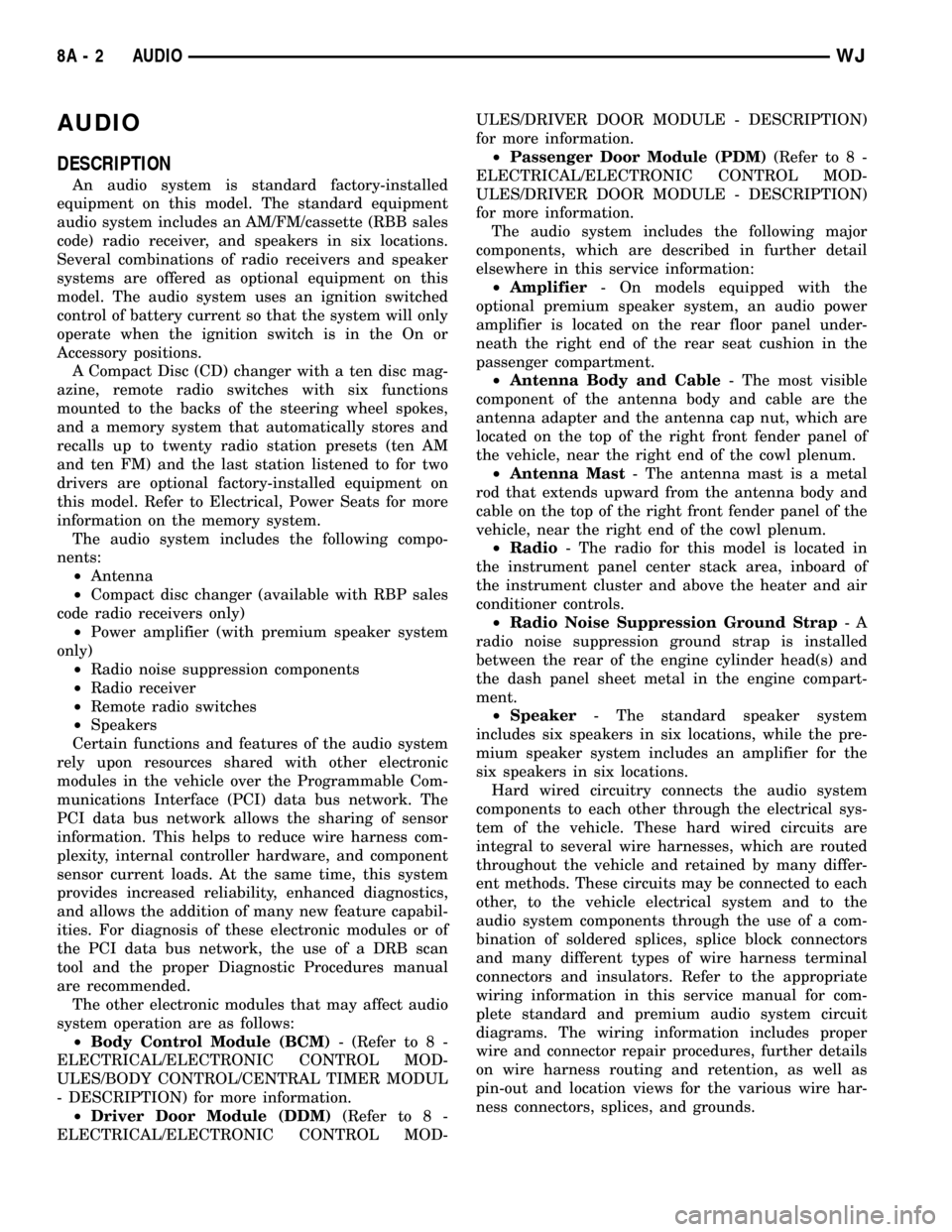
AUDIO
DESCRIPTION
An audio system is standard factory-installed
equipment on this model. The standard equipment
audio system includes an AM/FM/cassette (RBB sales
code) radio receiver, and speakers in six locations.
Several combinations of radio receivers and speaker
systems are offered as optional equipment on this
model. The audio system uses an ignition switched
control of battery current so that the system will only
operate when the ignition switch is in the On or
Accessory positions.
A Compact Disc (CD) changer with a ten disc mag-
azine, remote radio switches with six functions
mounted to the backs of the steering wheel spokes,
and a memory system that automatically stores and
recalls up to twenty radio station presets (ten AM
and ten FM) and the last station listened to for two
drivers are optional factory-installed equipment on
this model. Refer to Electrical, Power Seats for more
information on the memory system.
The audio system includes the following compo-
nents:
²Antenna
²Compact disc changer (available with RBP sales
code radio receivers only)
²Power amplifier (with premium speaker system
only)
²Radio noise suppression components
²Radio receiver
²Remote radio switches
²Speakers
Certain functions and features of the audio system
rely upon resources shared with other electronic
modules in the vehicle over the Programmable Com-
munications Interface (PCI) data bus network. The
PCI data bus network allows the sharing of sensor
information. This helps to reduce wire harness com-
plexity, internal controller hardware, and component
sensor current loads. At the same time, this system
provides increased reliability, enhanced diagnostics,
and allows the addition of many new feature capabil-
ities. For diagnosis of these electronic modules or of
the PCI data bus network, the use of a DRB scan
tool and the proper Diagnostic Procedures manual
are recommended.
The other electronic modules that may affect audio
system operation are as follows:
²Body Control Module (BCM)- (Refer to 8 -
ELECTRICAL/ELECTRONIC CONTROL MOD-
ULES/BODY CONTROL/CENTRAL TIMER MODUL
- DESCRIPTION) for more information.
²Driver Door Module (DDM)(Refer to 8 -
ELECTRICAL/ELECTRONIC CONTROL MOD-ULES/DRIVER DOOR MODULE - DESCRIPTION)
for more information.
²Passenger Door Module (PDM)(Refer to 8 -
ELECTRICAL/ELECTRONIC CONTROL MOD-
ULES/DRIVER DOOR MODULE - DESCRIPTION)
for more information.
The audio system includes the following major
components, which are described in further detail
elsewhere in this service information:
²Amplifier- On models equipped with the
optional premium speaker system, an audio power
amplifier is located on the rear floor panel under-
neath the right end of the rear seat cushion in the
passenger compartment.
²Antenna Body and Cable- The most visible
component of the antenna body and cable are the
antenna adapter and the antenna cap nut, which are
located on the top of the right front fender panel of
the vehicle, near the right end of the cowl plenum.
²Antenna Mast- The antenna mast is a metal
rod that extends upward from the antenna body and
cable on the top of the right front fender panel of the
vehicle, near the right end of the cowl plenum.
²Radio- The radio for this model is located in
the instrument panel center stack area, inboard of
the instrument cluster and above the heater and air
conditioner controls.
²Radio Noise Suppression Ground Strap-A
radio noise suppression ground strap is installed
between the rear of the engine cylinder head(s) and
the dash panel sheet metal in the engine compart-
ment.
²Speaker- The standard speaker system
includes six speakers in six locations, while the pre-
mium speaker system includes an amplifier for the
six speakers in six locations.
Hard wired circuitry connects the audio system
components to each other through the electrical sys-
tem of the vehicle. These hard wired circuits are
integral to several wire harnesses, which are routed
throughout the vehicle and retained by many differ-
ent methods. These circuits may be connected to each
other, to the vehicle electrical system and to the
audio system components through the use of a com-
bination of soldered splices, splice block connectors
and many different types of wire harness terminal
connectors and insulators. Refer to the appropriate
wiring information in this service manual for com-
plete standard and premium audio system circuit
diagrams. The wiring information includes proper
wire and connector repair procedures, further details
on wire harness routing and retention, as well as
pin-out and location views for the various wire har-
ness connectors, splices, and grounds.
8A - 2 AUDIOWJ
Page 285 of 2199
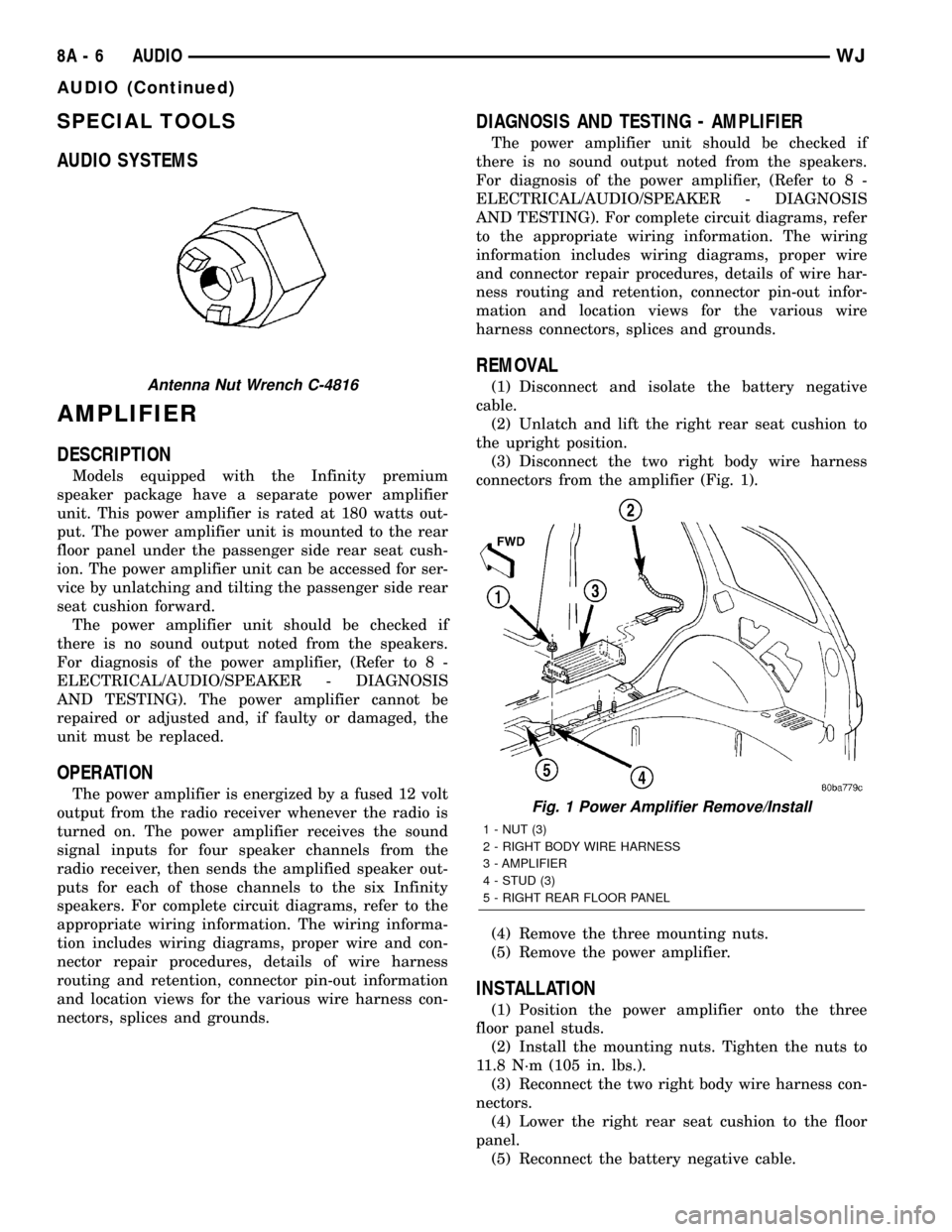
SPECIAL TOOLS
AUDIO SYSTEMS
AMPLIFIER
DESCRIPTION
Models equipped with the Infinity premium
speaker package have a separate power amplifier
unit. This power amplifier is rated at 180 watts out-
put. The power amplifier unit is mounted to the rear
floor panel under the passenger side rear seat cush-
ion. The power amplifier unit can be accessed for ser-
vice by unlatching and tilting the passenger side rear
seat cushion forward.
The power amplifier unit should be checked if
there is no sound output noted from the speakers.
For diagnosis of the power amplifier, (Refer to 8 -
ELECTRICAL/AUDIO/SPEAKER - DIAGNOSIS
AND TESTING). The power amplifier cannot be
repaired or adjusted and, if faulty or damaged, the
unit must be replaced.
OPERATION
The power amplifier is energized by a fused 12 volt
output from the radio receiver whenever the radio is
turned on. The power amplifier receives the sound
signal inputs for four speaker channels from the
radio receiver, then sends the amplified speaker out-
puts for each of those channels to the six Infinity
speakers. For complete circuit diagrams, refer to the
appropriate wiring information. The wiring informa-
tion includes wiring diagrams, proper wire and con-
nector repair procedures, details of wire harness
routing and retention, connector pin-out information
and location views for the various wire harness con-
nectors, splices and grounds.
DIAGNOSIS AND TESTING - AMPLIFIER
The power amplifier unit should be checked if
there is no sound output noted from the speakers.
For diagnosis of the power amplifier, (Refer to 8 -
ELECTRICAL/AUDIO/SPEAKER - DIAGNOSIS
AND TESTING). For complete circuit diagrams, refer
to the appropriate wiring information. The wiring
information includes wiring diagrams, proper wire
and connector repair procedures, details of wire har-
ness routing and retention, connector pin-out infor-
mation and location views for the various wire
harness connectors, splices and grounds.
REMOVAL
(1) Disconnect and isolate the battery negative
cable.
(2) Unlatch and lift the right rear seat cushion to
the upright position.
(3) Disconnect the two right body wire harness
connectors from the amplifier (Fig. 1).
(4) Remove the three mounting nuts.
(5) Remove the power amplifier.
INSTALLATION
(1) Position the power amplifier onto the three
floor panel studs.
(2) Install the mounting nuts. Tighten the nuts to
11.8 N´m (105 in. lbs.).
(3) Reconnect the two right body wire harness con-
nectors.
(4) Lower the right rear seat cushion to the floor
panel.
(5) Reconnect the battery negative cable.
Antenna Nut Wrench C-4816
Fig. 1 Power Amplifier Remove/Install
1 - NUT (3)
2 - RIGHT BODY WIRE HARNESS
3 - AMPLIFIER
4 - STUD (3)
5 - RIGHT REAR FLOOR PANEL
8A - 6 AUDIOWJ
AUDIO (Continued)
Page 286 of 2199
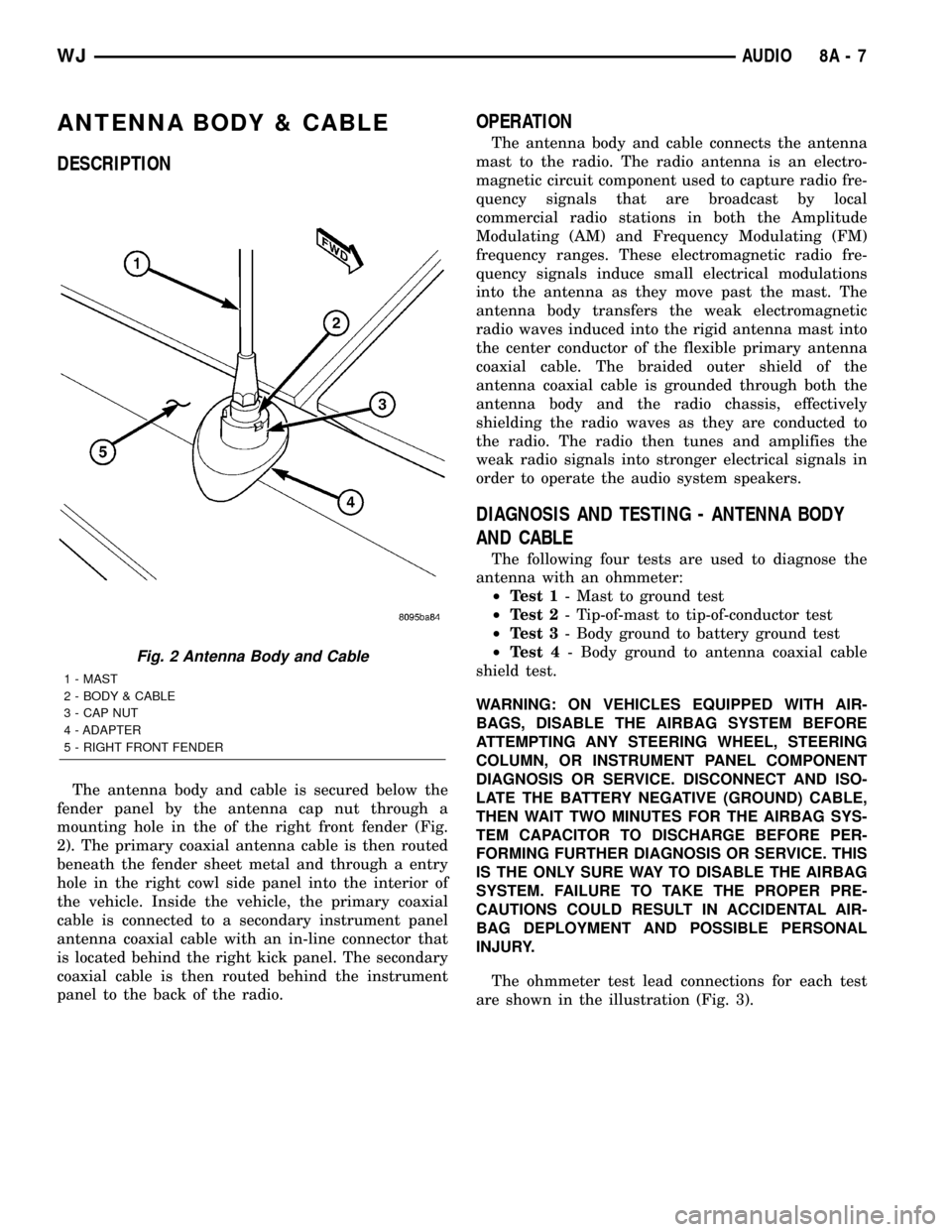
ANTENNA BODY & CABLE
DESCRIPTION
The antenna body and cable is secured below the
fender panel by the antenna cap nut through a
mounting hole in the of the right front fender (Fig.
2). The primary coaxial antenna cable is then routed
beneath the fender sheet metal and through a entry
hole in the right cowl side panel into the interior of
the vehicle. Inside the vehicle, the primary coaxial
cable is connected to a secondary instrument panel
antenna coaxial cable with an in-line connector that
is located behind the right kick panel. The secondary
coaxial cable is then routed behind the instrument
panel to the back of the radio.
OPERATION
The antenna body and cable connects the antenna
mast to the radio. The radio antenna is an electro-
magnetic circuit component used to capture radio fre-
quency signals that are broadcast by local
commercial radio stations in both the Amplitude
Modulating (AM) and Frequency Modulating (FM)
frequency ranges. These electromagnetic radio fre-
quency signals induce small electrical modulations
into the antenna as they move past the mast. The
antenna body transfers the weak electromagnetic
radio waves induced into the rigid antenna mast into
the center conductor of the flexible primary antenna
coaxial cable. The braided outer shield of the
antenna coaxial cable is grounded through both the
antenna body and the radio chassis, effectively
shielding the radio waves as they are conducted to
the radio. The radio then tunes and amplifies the
weak radio signals into stronger electrical signals in
order to operate the audio system speakers.
DIAGNOSIS AND TESTING - ANTENNA BODY
AND CABLE
The following four tests are used to diagnose the
antenna with an ohmmeter:
²Test 1- Mast to ground test
²Test 2- Tip-of-mast to tip-of-conductor test
²Test 3- Body ground to battery ground test
²Test 4- Body ground to antenna coaxial cable
shield test.
WARNING: ON VEHICLES EQUIPPED WITH AIR-
BAGS, DISABLE THE AIRBAG SYSTEM BEFORE
ATTEMPTING ANY STEERING WHEEL, STEERING
COLUMN, OR INSTRUMENT PANEL COMPONENT
DIAGNOSIS OR SERVICE. DISCONNECT AND ISO-
LATE THE BATTERY NEGATIVE (GROUND) CABLE,
THEN WAIT TWO MINUTES FOR THE AIRBAG SYS-
TEM CAPACITOR TO DISCHARGE BEFORE PER-
FORMING FURTHER DIAGNOSIS OR SERVICE. THIS
IS THE ONLY SURE WAY TO DISABLE THE AIRBAG
SYSTEM. FAILURE TO TAKE THE PROPER PRE-
CAUTIONS COULD RESULT IN ACCIDENTAL AIR-
BAG DEPLOYMENT AND POSSIBLE PERSONAL
INJURY.
The ohmmeter test lead connections for each test
are shown in the illustration (Fig. 3).
Fig. 2 Antenna Body and Cable
1 - MAST
2 - BODY & CABLE
3 - CAP NUT
4 - ADAPTER
5 - RIGHT FRONT FENDER
WJAUDIO 8A - 7
Page 292 of 2199
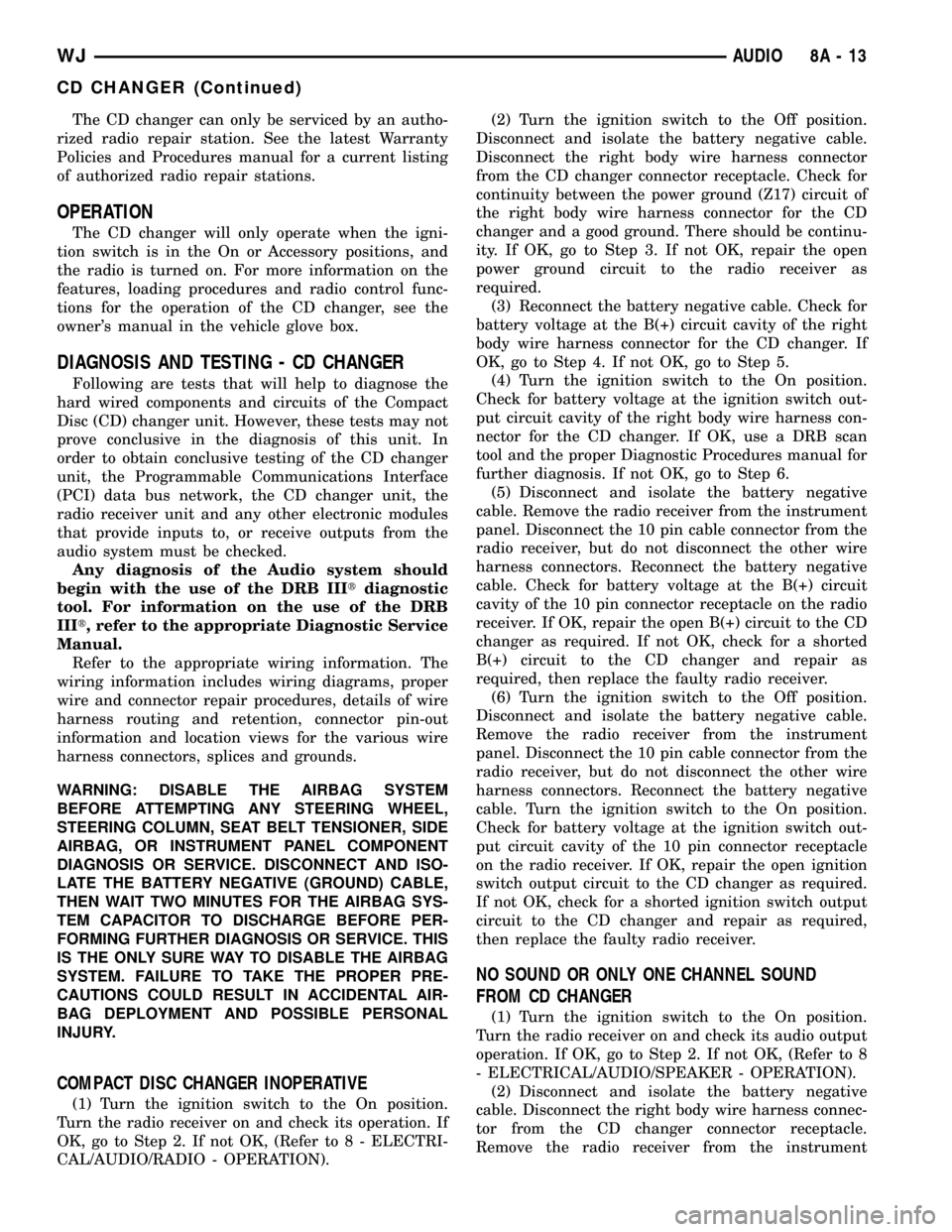
The CD changer can only be serviced by an autho-
rized radio repair station. See the latest Warranty
Policies and Procedures manual for a current listing
of authorized radio repair stations.
OPERATION
The CD changer will only operate when the igni-
tion switch is in the On or Accessory positions, and
the radio is turned on. For more information on the
features, loading procedures and radio control func-
tions for the operation of the CD changer, see the
owner's manual in the vehicle glove box.
DIAGNOSIS AND TESTING - CD CHANGER
Following are tests that will help to diagnose the
hard wired components and circuits of the Compact
Disc (CD) changer unit. However, these tests may not
prove conclusive in the diagnosis of this unit. In
order to obtain conclusive testing of the CD changer
unit, the Programmable Communications Interface
(PCI) data bus network, the CD changer unit, the
radio receiver unit and any other electronic modules
that provide inputs to, or receive outputs from the
audio system must be checked.
Any diagnosis of the Audio system should
begin with the use of the DRB IIItdiagnostic
tool. For information on the use of the DRB
IIIt, refer to the appropriate Diagnostic Service
Manual.
Refer to the appropriate wiring information. The
wiring information includes wiring diagrams, proper
wire and connector repair procedures, details of wire
harness routing and retention, connector pin-out
information and location views for the various wire
harness connectors, splices and grounds.
WARNING: DISABLE THE AIRBAG SYSTEM
BEFORE ATTEMPTING ANY STEERING WHEEL,
STEERING COLUMN, SEAT BELT TENSIONER, SIDE
AIRBAG, OR INSTRUMENT PANEL COMPONENT
DIAGNOSIS OR SERVICE. DISCONNECT AND ISO-
LATE THE BATTERY NEGATIVE (GROUND) CABLE,
THEN WAIT TWO MINUTES FOR THE AIRBAG SYS-
TEM CAPACITOR TO DISCHARGE BEFORE PER-
FORMING FURTHER DIAGNOSIS OR SERVICE. THIS
IS THE ONLY SURE WAY TO DISABLE THE AIRBAG
SYSTEM. FAILURE TO TAKE THE PROPER PRE-
CAUTIONS COULD RESULT IN ACCIDENTAL AIR-
BAG DEPLOYMENT AND POSSIBLE PERSONAL
INJURY.
COMPACT DISC CHANGER INOPERATIVE
(1) Turn the ignition switch to the On position.
Turn the radio receiver on and check its operation. If
OK, go to Step 2. If not OK, (Refer to 8 - ELECTRI-
CAL/AUDIO/RADIO - OPERATION).(2) Turn the ignition switch to the Off position.
Disconnect and isolate the battery negative cable.
Disconnect the right body wire harness connector
from the CD changer connector receptacle. Check for
continuity between the power ground (Z17) circuit of
the right body wire harness connector for the CD
changer and a good ground. There should be continu-
ity. If OK, go to Step 3. If not OK, repair the open
power ground circuit to the radio receiver as
required.
(3) Reconnect the battery negative cable. Check for
battery voltage at the B(+) circuit cavity of the right
body wire harness connector for the CD changer. If
OK, go to Step 4. If not OK, go to Step 5.
(4) Turn the ignition switch to the On position.
Check for battery voltage at the ignition switch out-
put circuit cavity of the right body wire harness con-
nector for the CD changer. If OK, use a DRB scan
tool and the proper Diagnostic Procedures manual for
further diagnosis. If not OK, go to Step 6.
(5) Disconnect and isolate the battery negative
cable. Remove the radio receiver from the instrument
panel. Disconnect the 10 pin cable connector from the
radio receiver, but do not disconnect the other wire
harness connectors. Reconnect the battery negative
cable. Check for battery voltage at the B(+) circuit
cavity of the 10 pin connector receptacle on the radio
receiver. If OK, repair the open B(+) circuit to the CD
changer as required. If not OK, check for a shorted
B(+) circuit to the CD changer and repair as
required, then replace the faulty radio receiver.
(6) Turn the ignition switch to the Off position.
Disconnect and isolate the battery negative cable.
Remove the radio receiver from the instrument
panel. Disconnect the 10 pin cable connector from the
radio receiver, but do not disconnect the other wire
harness connectors. Reconnect the battery negative
cable. Turn the ignition switch to the On position.
Check for battery voltage at the ignition switch out-
put circuit cavity of the 10 pin connector receptacle
on the radio receiver. If OK, repair the open ignition
switch output circuit to the CD changer as required.
If not OK, check for a shorted ignition switch output
circuit to the CD changer and repair as required,
then replace the faulty radio receiver.
NO SOUND OR ONLY ONE CHANNEL SOUND
FROM CD CHANGER
(1) Turn the ignition switch to the On position.
Turn the radio receiver on and check its audio output
operation. If OK, go to Step 2. If not OK, (Refer to 8
- ELECTRICAL/AUDIO/SPEAKER - OPERATION).
(2) Disconnect and isolate the battery negative
cable. Disconnect the right body wire harness connec-
tor from the CD changer connector receptacle.
Remove the radio receiver from the instrument
WJAUDIO 8A - 13
CD CHANGER (Continued)
Page 295 of 2199
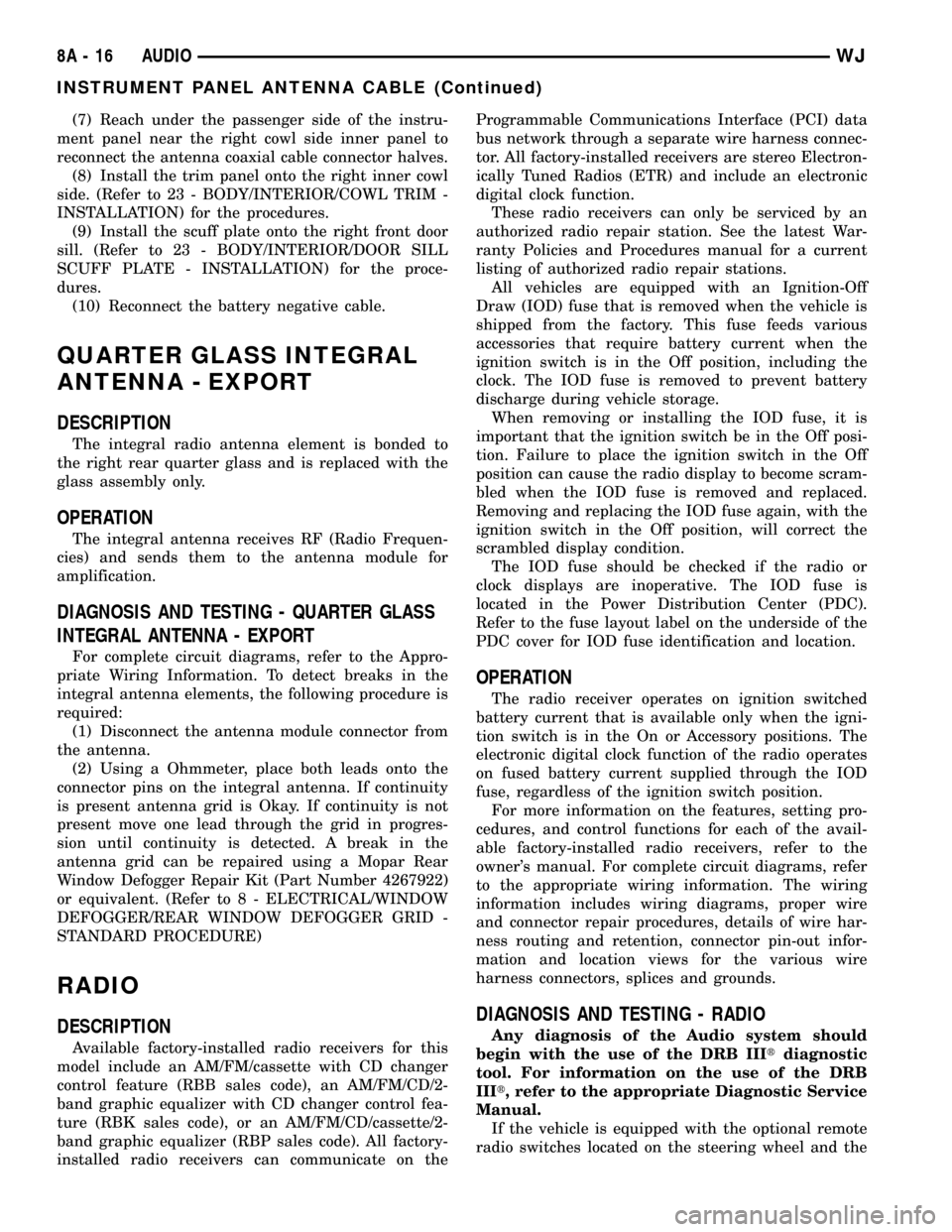
(7) Reach under the passenger side of the instru-
ment panel near the right cowl side inner panel to
reconnect the antenna coaxial cable connector halves.
(8) Install the trim panel onto the right inner cowl
side. (Refer to 23 - BODY/INTERIOR/COWL TRIM -
INSTALLATION) for the procedures.
(9) Install the scuff plate onto the right front door
sill. (Refer to 23 - BODY/INTERIOR/DOOR SILL
SCUFF PLATE - INSTALLATION) for the proce-
dures.
(10) Reconnect the battery negative cable.
QUARTER GLASS INTEGRAL
ANTENNA - EXPORT
DESCRIPTION
The integral radio antenna element is bonded to
the right rear quarter glass and is replaced with the
glass assembly only.
OPERATION
The integral antenna receives RF (Radio Frequen-
cies) and sends them to the antenna module for
amplification.
DIAGNOSIS AND TESTING - QUARTER GLASS
INTEGRAL ANTENNA - EXPORT
For complete circuit diagrams, refer to the Appro-
priate Wiring Information. To detect breaks in the
integral antenna elements, the following procedure is
required:
(1) Disconnect the antenna module connector from
the antenna.
(2) Using a Ohmmeter, place both leads onto the
connector pins on the integral antenna. If continuity
is present antenna grid is Okay. If continuity is not
present move one lead through the grid in progres-
sion until continuity is detected. A break in the
antenna grid can be repaired using a Mopar Rear
Window Defogger Repair Kit (Part Number 4267922)
or equivalent. (Refer to 8 - ELECTRICAL/WINDOW
DEFOGGER/REAR WINDOW DEFOGGER GRID -
STANDARD PROCEDURE)
RADIO
DESCRIPTION
Available factory-installed radio receivers for this
model include an AM/FM/cassette with CD changer
control feature (RBB sales code), an AM/FM/CD/2-
band graphic equalizer with CD changer control fea-
ture (RBK sales code), or an AM/FM/CD/cassette/2-
band graphic equalizer (RBP sales code). All factory-
installed radio receivers can communicate on theProgrammable Communications Interface (PCI) data
bus network through a separate wire harness connec-
tor. All factory-installed receivers are stereo Electron-
ically Tuned Radios (ETR) and include an electronic
digital clock function.
These radio receivers can only be serviced by an
authorized radio repair station. See the latest War-
ranty Policies and Procedures manual for a current
listing of authorized radio repair stations.
All vehicles are equipped with an Ignition-Off
Draw (IOD) fuse that is removed when the vehicle is
shipped from the factory. This fuse feeds various
accessories that require battery current when the
ignition switch is in the Off position, including the
clock. The IOD fuse is removed to prevent battery
discharge during vehicle storage.
When removing or installing the IOD fuse, it is
important that the ignition switch be in the Off posi-
tion. Failure to place the ignition switch in the Off
position can cause the radio display to become scram-
bled when the IOD fuse is removed and replaced.
Removing and replacing the IOD fuse again, with the
ignition switch in the Off position, will correct the
scrambled display condition.
The IOD fuse should be checked if the radio or
clock displays are inoperative. The IOD fuse is
located in the Power Distribution Center (PDC).
Refer to the fuse layout label on the underside of the
PDC cover for IOD fuse identification and location.
OPERATION
The radio receiver operates on ignition switched
battery current that is available only when the igni-
tion switch is in the On or Accessory positions. The
electronic digital clock function of the radio operates
on fused battery current supplied through the IOD
fuse, regardless of the ignition switch position.
For more information on the features, setting pro-
cedures, and control functions for each of the avail-
able factory-installed radio receivers, refer to the
owner's manual. For complete circuit diagrams, refer
to the appropriate wiring information. The wiring
information includes wiring diagrams, proper wire
and connector repair procedures, details of wire har-
ness routing and retention, connector pin-out infor-
mation and location views for the various wire
harness connectors, splices and grounds.
DIAGNOSIS AND TESTING - RADIO
Any diagnosis of the Audio system should
begin with the use of the DRB IIItdiagnostic
tool. For information on the use of the DRB
IIIt, refer to the appropriate Diagnostic Service
Manual.
If the vehicle is equipped with the optional remote
radio switches located on the steering wheel and the
8A - 16 AUDIOWJ
INSTRUMENT PANEL ANTENNA CABLE (Continued)
Page 296 of 2199
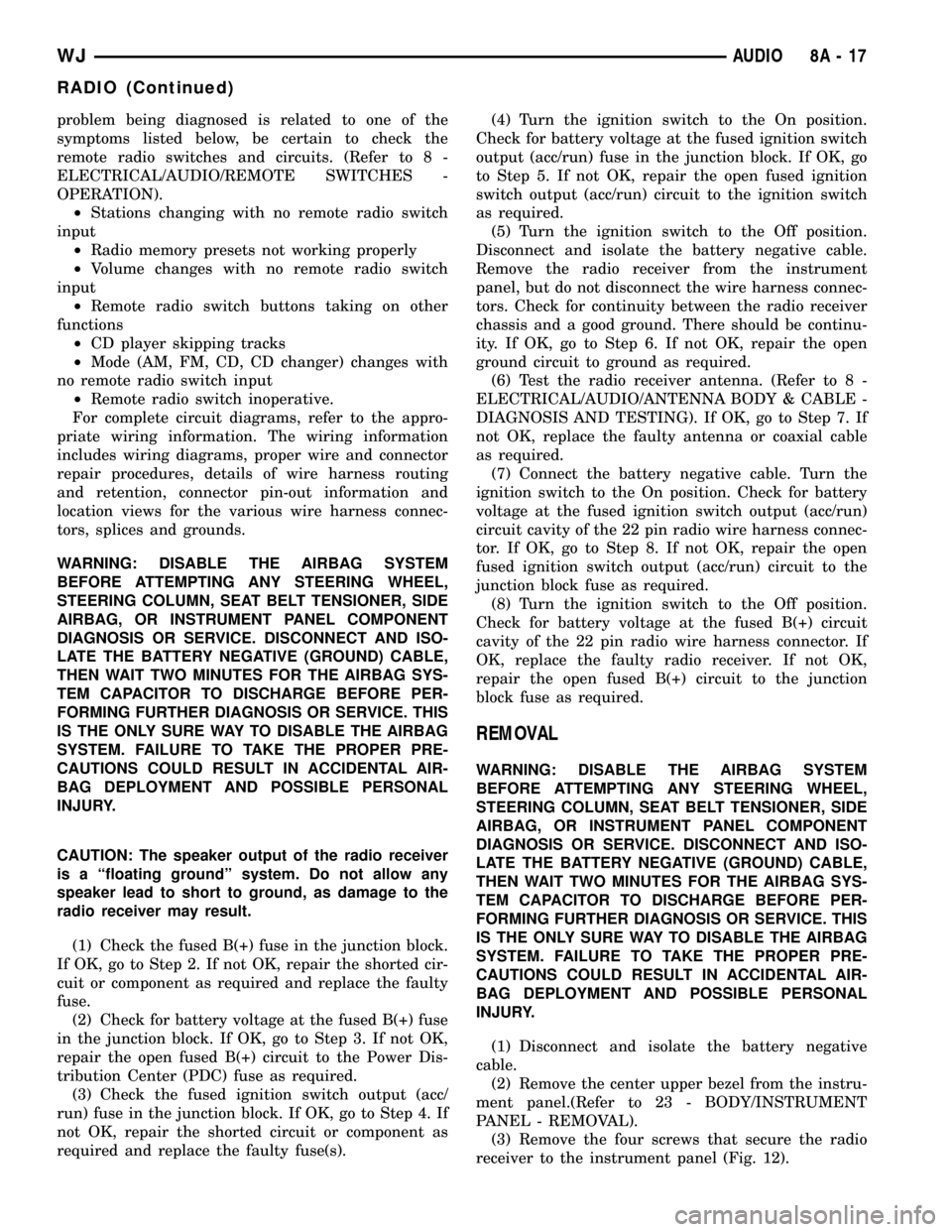
problem being diagnosed is related to one of the
symptoms listed below, be certain to check the
remote radio switches and circuits. (Refer to 8 -
ELECTRICAL/AUDIO/REMOTE SWITCHES -
OPERATION).
²Stations changing with no remote radio switch
input
²Radio memory presets not working properly
²Volume changes with no remote radio switch
input
²Remote radio switch buttons taking on other
functions
²CD player skipping tracks
²Mode (AM, FM, CD, CD changer) changes with
no remote radio switch input
²Remote radio switch inoperative.
For complete circuit diagrams, refer to the appro-
priate wiring information. The wiring information
includes wiring diagrams, proper wire and connector
repair procedures, details of wire harness routing
and retention, connector pin-out information and
location views for the various wire harness connec-
tors, splices and grounds.
WARNING: DISABLE THE AIRBAG SYSTEM
BEFORE ATTEMPTING ANY STEERING WHEEL,
STEERING COLUMN, SEAT BELT TENSIONER, SIDE
AIRBAG, OR INSTRUMENT PANEL COMPONENT
DIAGNOSIS OR SERVICE. DISCONNECT AND ISO-
LATE THE BATTERY NEGATIVE (GROUND) CABLE,
THEN WAIT TWO MINUTES FOR THE AIRBAG SYS-
TEM CAPACITOR TO DISCHARGE BEFORE PER-
FORMING FURTHER DIAGNOSIS OR SERVICE. THIS
IS THE ONLY SURE WAY TO DISABLE THE AIRBAG
SYSTEM. FAILURE TO TAKE THE PROPER PRE-
CAUTIONS COULD RESULT IN ACCIDENTAL AIR-
BAG DEPLOYMENT AND POSSIBLE PERSONAL
INJURY.
CAUTION: The speaker output of the radio receiver
is a ªfloating groundº system. Do not allow any
speaker lead to short to ground, as damage to the
radio receiver may result.
(1) Check the fused B(+) fuse in the junction block.
If OK, go to Step 2. If not OK, repair the shorted cir-
cuit or component as required and replace the faulty
fuse.
(2) Check for battery voltage at the fused B(+) fuse
in the junction block. If OK, go to Step 3. If not OK,
repair the open fused B(+) circuit to the Power Dis-
tribution Center (PDC) fuse as required.
(3) Check the fused ignition switch output (acc/
run) fuse in the junction block. If OK, go to Step 4. If
not OK, repair the shorted circuit or component as
required and replace the faulty fuse(s).(4) Turn the ignition switch to the On position.
Check for battery voltage at the fused ignition switch
output (acc/run) fuse in the junction block. If OK, go
to Step 5. If not OK, repair the open fused ignition
switch output (acc/run) circuit to the ignition switch
as required.
(5) Turn the ignition switch to the Off position.
Disconnect and isolate the battery negative cable.
Remove the radio receiver from the instrument
panel, but do not disconnect the wire harness connec-
tors. Check for continuity between the radio receiver
chassis and a good ground. There should be continu-
ity. If OK, go to Step 6. If not OK, repair the open
ground circuit to ground as required.
(6) Test the radio receiver antenna. (Refer to 8 -
ELECTRICAL/AUDIO/ANTENNA BODY & CABLE -
DIAGNOSIS AND TESTING). If OK, go to Step 7. If
not OK, replace the faulty antenna or coaxial cable
as required.
(7) Connect the battery negative cable. Turn the
ignition switch to the On position. Check for battery
voltage at the fused ignition switch output (acc/run)
circuit cavity of the 22 pin radio wire harness connec-
tor. If OK, go to Step 8. If not OK, repair the open
fused ignition switch output (acc/run) circuit to the
junction block fuse as required.
(8) Turn the ignition switch to the Off position.
Check for battery voltage at the fused B(+) circuit
cavity of the 22 pin radio wire harness connector. If
OK, replace the faulty radio receiver. If not OK,
repair the open fused B(+) circuit to the junction
block fuse as required.
REMOVAL
WARNING: DISABLE THE AIRBAG SYSTEM
BEFORE ATTEMPTING ANY STEERING WHEEL,
STEERING COLUMN, SEAT BELT TENSIONER, SIDE
AIRBAG, OR INSTRUMENT PANEL COMPONENT
DIAGNOSIS OR SERVICE. DISCONNECT AND ISO-
LATE THE BATTERY NEGATIVE (GROUND) CABLE,
THEN WAIT TWO MINUTES FOR THE AIRBAG SYS-
TEM CAPACITOR TO DISCHARGE BEFORE PER-
FORMING FURTHER DIAGNOSIS OR SERVICE. THIS
IS THE ONLY SURE WAY TO DISABLE THE AIRBAG
SYSTEM. FAILURE TO TAKE THE PROPER PRE-
CAUTIONS COULD RESULT IN ACCIDENTAL AIR-
BAG DEPLOYMENT AND POSSIBLE PERSONAL
INJURY.
(1) Disconnect and isolate the battery negative
cable.
(2) Remove the center upper bezel from the instru-
ment panel.(Refer to 23 - BODY/INSTRUMENT
PANEL - REMOVAL).
(3) Remove the four screws that secure the radio
receiver to the instrument panel (Fig. 12).
WJAUDIO 8A - 17
RADIO (Continued)