remote start JEEP GRAND CHEROKEE 2002 WJ / 2.G Workshop Manual
[x] Cancel search | Manufacturer: JEEP, Model Year: 2002, Model line: GRAND CHEROKEE, Model: JEEP GRAND CHEROKEE 2002 WJ / 2.GPages: 2199, PDF Size: 76.01 MB
Page 313 of 2199
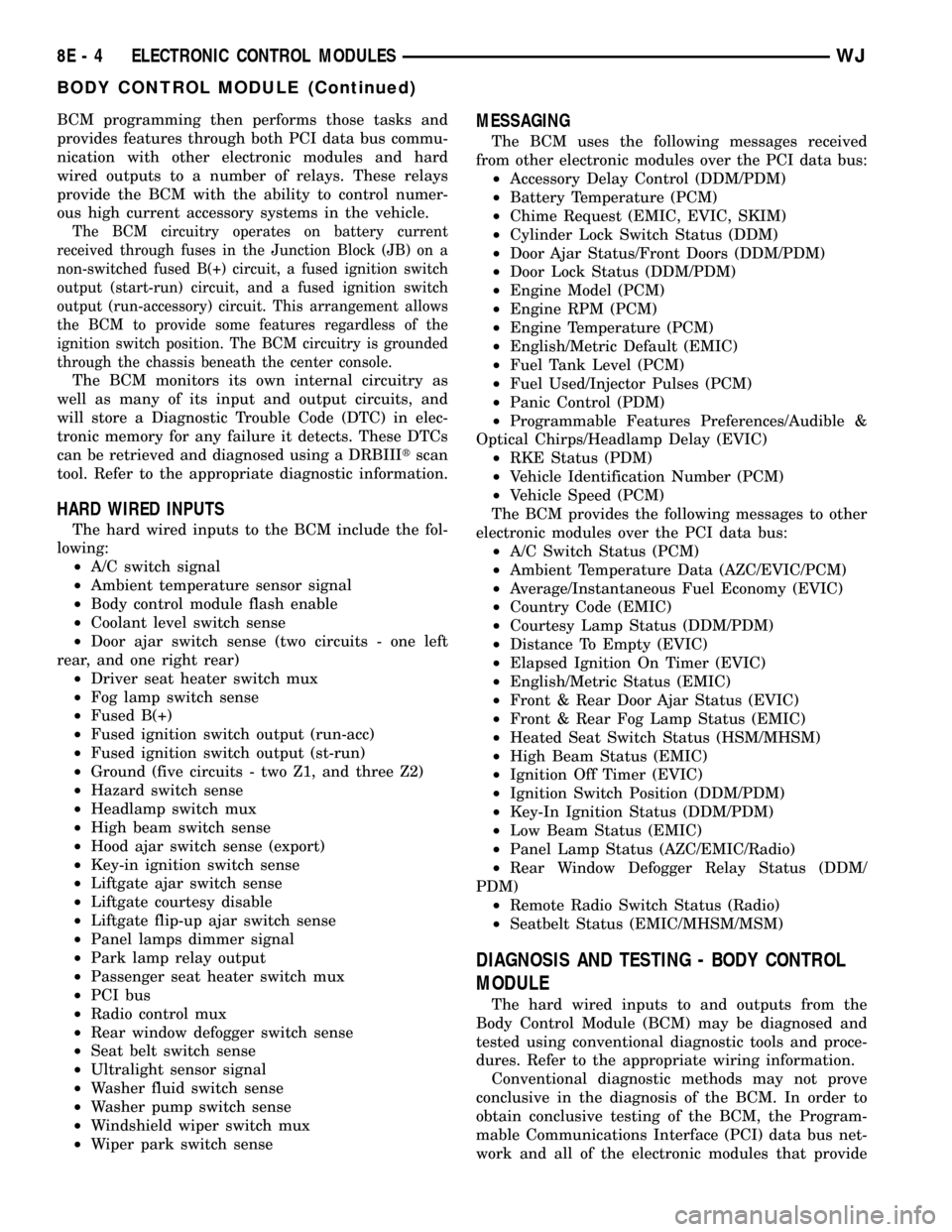
BCM programming then performs those tasks and
provides features through both PCI data bus commu-
nication with other electronic modules and hard
wired outputs to a number of relays. These relays
provide the BCM with the ability to control numer-
ous high current accessory systems in the vehicle.
The BCM circuitry operates on battery current
received through fuses in the Junction Block (JB) on a
non-switched fused B(+) circuit, a fused ignition switch
output (start-run) circuit, and a fused ignition switch
output (run-accessory) circuit. This arrangement allows
the BCM to provide some features regardless of the
ignition switch position. The BCM circuitry is grounded
through the chassis beneath the center console.
The BCM monitors its own internal circuitry as
well as many of its input and output circuits, and
will store a Diagnostic Trouble Code (DTC) in elec-
tronic memory for any failure it detects. These DTCs
can be retrieved and diagnosed using a DRBIIItscan
tool. Refer to the appropriate diagnostic information.
HARD WIRED INPUTS
The hard wired inputs to the BCM include the fol-
lowing:
²A/C switch signal
²Ambient temperature sensor signal
²Body control module flash enable
²Coolant level switch sense
²Door ajar switch sense (two circuits - one left
rear, and one right rear)
²Driver seat heater switch mux
²Fog lamp switch sense
²Fused B(+)
²Fused ignition switch output (run-acc)
²Fused ignition switch output (st-run)
²Ground (five circuits - two Z1, and three Z2)
²Hazard switch sense
²Headlamp switch mux
²High beam switch sense
²Hood ajar switch sense (export)
²Key-in ignition switch sense
²Liftgate ajar switch sense
²Liftgate courtesy disable
²Liftgate flip-up ajar switch sense
²Panel lamps dimmer signal
²Park lamp relay output
²Passenger seat heater switch mux
²PCI bus
²Radio control mux
²Rear window defogger switch sense
²Seat belt switch sense
²Ultralight sensor signal
²Washer fluid switch sense
²Washer pump switch sense
²Windshield wiper switch mux
²Wiper park switch sense
MESSAGING
The BCM uses the following messages received
from other electronic modules over the PCI data bus:
²Accessory Delay Control (DDM/PDM)
²Battery Temperature (PCM)
²Chime Request (EMIC, EVIC, SKIM)
²Cylinder Lock Switch Status (DDM)
²Door Ajar Status/Front Doors (DDM/PDM)
²Door Lock Status (DDM/PDM)
²Engine Model (PCM)
²Engine RPM (PCM)
²Engine Temperature (PCM)
²English/Metric Default (EMIC)
²Fuel Tank Level (PCM)
²Fuel Used/Injector Pulses (PCM)
²Panic Control (PDM)
²Programmable Features Preferences/Audible &
Optical Chirps/Headlamp Delay (EVIC)
²RKE Status (PDM)
²Vehicle Identification Number (PCM)
²Vehicle Speed (PCM)
The BCM provides the following messages to other
electronic modules over the PCI data bus:
²A/C Switch Status (PCM)
²Ambient Temperature Data (AZC/EVIC/PCM)
²Average/Instantaneous Fuel Economy (EVIC)
²Country Code (EMIC)
²Courtesy Lamp Status (DDM/PDM)
²Distance To Empty (EVIC)
²Elapsed Ignition On Timer (EVIC)
²English/Metric Status (EMIC)
²Front & Rear Door Ajar Status (EVIC)
²Front & Rear Fog Lamp Status (EMIC)
²Heated Seat Switch Status (HSM/MHSM)
²High Beam Status (EMIC)
²Ignition Off Timer (EVIC)
²Ignition Switch Position (DDM/PDM)
²Key-In Ignition Status (DDM/PDM)
²Low Beam Status (EMIC)
²Panel Lamp Status (AZC/EMIC/Radio)
²Rear Window Defogger Relay Status (DDM/
PDM)
²Remote Radio Switch Status (Radio)
²Seatbelt Status (EMIC/MHSM/MSM)
DIAGNOSIS AND TESTING - BODY CONTROL
MODULE
The hard wired inputs to and outputs from the
Body Control Module (BCM) may be diagnosed and
tested using conventional diagnostic tools and proce-
dures. Refer to the appropriate wiring information.
Conventional diagnostic methods may not prove
conclusive in the diagnosis of the BCM. In order to
obtain conclusive testing of the BCM, the Program-
mable Communications Interface (PCI) data bus net-
work and all of the electronic modules that provide
8E - 4 ELECTRONIC CONTROL MODULESWJ
BODY CONTROL MODULE (Continued)
Page 487 of 2199
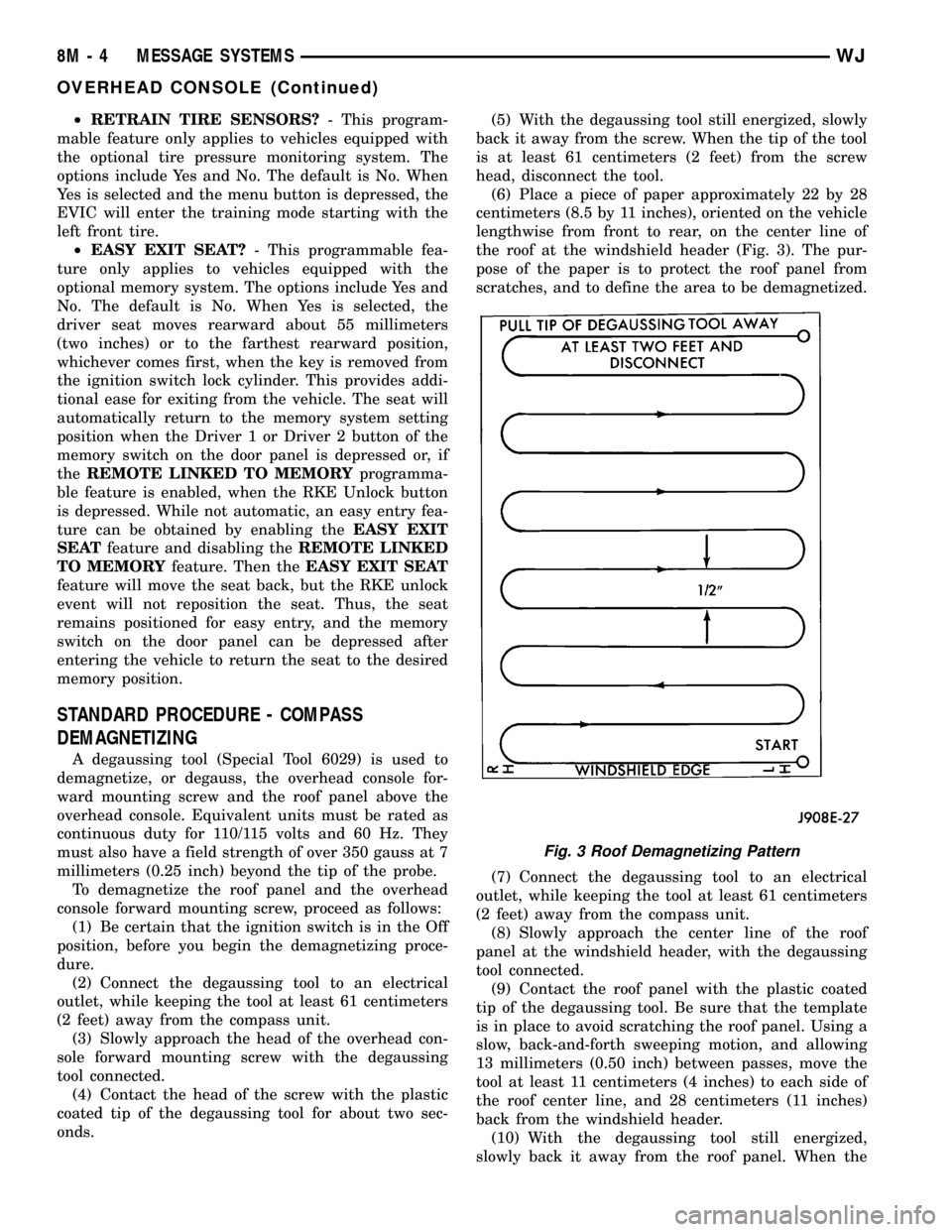
²RETRAIN TIRE SENSORS?- This program-
mable feature only applies to vehicles equipped with
the optional tire pressure monitoring system. The
options include Yes and No. The default is No. When
Yes is selected and the menu button is depressed, the
EVIC will enter the training mode starting with the
left front tire.
²EASY EXIT SEAT?- This programmable fea-
ture only applies to vehicles equipped with the
optional memory system. The options include Yes and
No. The default is No. When Yes is selected, the
driver seat moves rearward about 55 millimeters
(two inches) or to the farthest rearward position,
whichever comes first, when the key is removed from
the ignition switch lock cylinder. This provides addi-
tional ease for exiting from the vehicle. The seat will
automatically return to the memory system setting
position when the Driver 1 or Driver 2 button of the
memory switch on the door panel is depressed or, if
theREMOTE LINKED TO MEMORYprogramma-
ble feature is enabled, when the RKE Unlock button
is depressed. While not automatic, an easy entry fea-
ture can be obtained by enabling theEASY EXIT
SEATfeature and disabling theREMOTE LINKED
TO MEMORYfeature. Then theEASY EXIT SEAT
feature will move the seat back, but the RKE unlock
event will not reposition the seat. Thus, the seat
remains positioned for easy entry, and the memory
switch on the door panel can be depressed after
entering the vehicle to return the seat to the desired
memory position.
STANDARD PROCEDURE - COMPASS
DEMAGNETIZING
A degaussing tool (Special Tool 6029) is used to
demagnetize, or degauss, the overhead console for-
ward mounting screw and the roof panel above the
overhead console. Equivalent units must be rated as
continuous duty for 110/115 volts and 60 Hz. They
must also have a field strength of over 350 gauss at 7
millimeters (0.25 inch) beyond the tip of the probe.
To demagnetize the roof panel and the overhead
console forward mounting screw, proceed as follows:
(1) Be certain that the ignition switch is in the Off
position, before you begin the demagnetizing proce-
dure.
(2) Connect the degaussing tool to an electrical
outlet, while keeping the tool at least 61 centimeters
(2 feet) away from the compass unit.
(3) Slowly approach the head of the overhead con-
sole forward mounting screw with the degaussing
tool connected.
(4) Contact the head of the screw with the plastic
coated tip of the degaussing tool for about two sec-
onds.(5) With the degaussing tool still energized, slowly
back it away from the screw. When the tip of the tool
is at least 61 centimeters (2 feet) from the screw
head, disconnect the tool.
(6) Place a piece of paper approximately 22 by 28
centimeters (8.5 by 11 inches), oriented on the vehicle
lengthwise from front to rear, on the center line of
the roof at the windshield header (Fig. 3). The pur-
pose of the paper is to protect the roof panel from
scratches, and to define the area to be demagnetized.
(7) Connect the degaussing tool to an electrical
outlet, while keeping the tool at least 61 centimeters
(2 feet) away from the compass unit.
(8) Slowly approach the center line of the roof
panel at the windshield header, with the degaussing
tool connected.
(9) Contact the roof panel with the plastic coated
tip of the degaussing tool. Be sure that the template
is in place to avoid scratching the roof panel. Using a
slow, back-and-forth sweeping motion, and allowing
13 millimeters (0.50 inch) between passes, move the
tool at least 11 centimeters (4 inches) to each side of
the roof center line, and 28 centimeters (11 inches)
back from the windshield header.
(10) With the degaussing tool still energized,
slowly back it away from the roof panel. When the
Fig. 3 Roof Demagnetizing Pattern
8M - 4 MESSAGE SYSTEMSWJ
OVERHEAD CONSOLE (Continued)
Page 547 of 2199
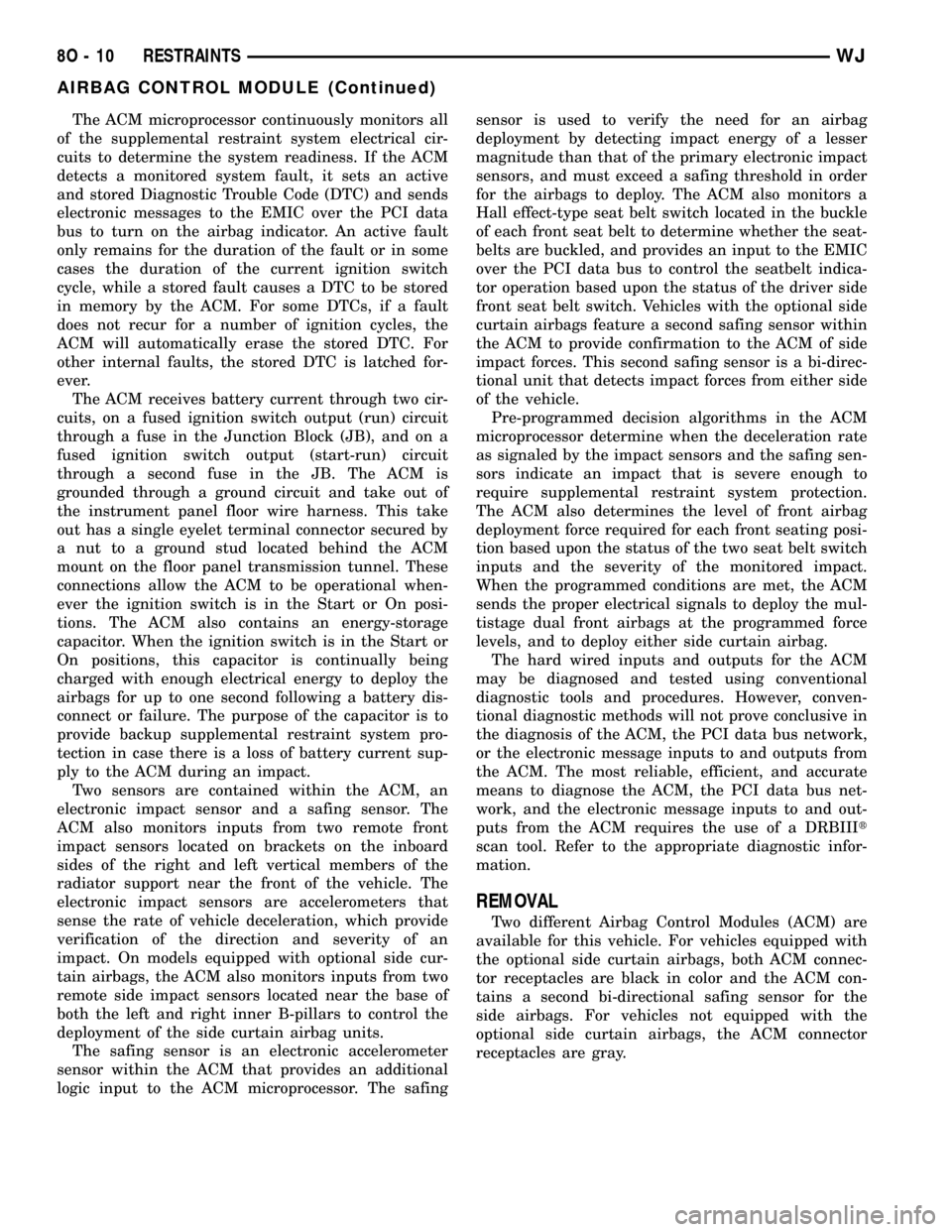
The ACM microprocessor continuously monitors all
of the supplemental restraint system electrical cir-
cuits to determine the system readiness. If the ACM
detects a monitored system fault, it sets an active
and stored Diagnostic Trouble Code (DTC) and sends
electronic messages to the EMIC over the PCI data
bus to turn on the airbag indicator. An active fault
only remains for the duration of the fault or in some
cases the duration of the current ignition switch
cycle, while a stored fault causes a DTC to be stored
in memory by the ACM. For some DTCs, if a fault
does not recur for a number of ignition cycles, the
ACM will automatically erase the stored DTC. For
other internal faults, the stored DTC is latched for-
ever.
The ACM receives battery current through two cir-
cuits, on a fused ignition switch output (run) circuit
through a fuse in the Junction Block (JB), and on a
fused ignition switch output (start-run) circuit
through a second fuse in the JB. The ACM is
grounded through a ground circuit and take out of
the instrument panel floor wire harness. This take
out has a single eyelet terminal connector secured by
a nut to a ground stud located behind the ACM
mount on the floor panel transmission tunnel. These
connections allow the ACM to be operational when-
ever the ignition switch is in the Start or On posi-
tions. The ACM also contains an energy-storage
capacitor. When the ignition switch is in the Start or
On positions, this capacitor is continually being
charged with enough electrical energy to deploy the
airbags for up to one second following a battery dis-
connect or failure. The purpose of the capacitor is to
provide backup supplemental restraint system pro-
tection in case there is a loss of battery current sup-
ply to the ACM during an impact.
Two sensors are contained within the ACM, an
electronic impact sensor and a safing sensor. The
ACM also monitors inputs from two remote front
impact sensors located on brackets on the inboard
sides of the right and left vertical members of the
radiator support near the front of the vehicle. The
electronic impact sensors are accelerometers that
sense the rate of vehicle deceleration, which provide
verification of the direction and severity of an
impact. On models equipped with optional side cur-
tain airbags, the ACM also monitors inputs from two
remote side impact sensors located near the base of
both the left and right inner B-pillars to control the
deployment of the side curtain airbag units.
The safing sensor is an electronic accelerometer
sensor within the ACM that provides an additional
logic input to the ACM microprocessor. The safingsensor is used to verify the need for an airbag
deployment by detecting impact energy of a lesser
magnitude than that of the primary electronic impact
sensors, and must exceed a safing threshold in order
for the airbags to deploy. The ACM also monitors a
Hall effect-type seat belt switch located in the buckle
of each front seat belt to determine whether the seat-
belts are buckled, and provides an input to the EMIC
over the PCI data bus to control the seatbelt indica-
tor operation based upon the status of the driver side
front seat belt switch. Vehicles with the optional side
curtain airbags feature a second safing sensor within
the ACM to provide confirmation to the ACM of side
impact forces. This second safing sensor is a bi-direc-
tional unit that detects impact forces from either side
of the vehicle.
Pre-programmed decision algorithms in the ACM
microprocessor determine when the deceleration rate
as signaled by the impact sensors and the safing sen-
sors indicate an impact that is severe enough to
require supplemental restraint system protection.
The ACM also determines the level of front airbag
deployment force required for each front seating posi-
tion based upon the status of the two seat belt switch
inputs and the severity of the monitored impact.
When the programmed conditions are met, the ACM
sends the proper electrical signals to deploy the mul-
tistage dual front airbags at the programmed force
levels, and to deploy either side curtain airbag.
The hard wired inputs and outputs for the ACM
may be diagnosed and tested using conventional
diagnostic tools and procedures. However, conven-
tional diagnostic methods will not prove conclusive in
the diagnosis of the ACM, the PCI data bus network,
or the electronic message inputs to and outputs from
the ACM. The most reliable, efficient, and accurate
means to diagnose the ACM, the PCI data bus net-
work, and the electronic message inputs to and out-
puts from the ACM requires the use of a DRBIIIt
scan tool. Refer to the appropriate diagnostic infor-
mation.
REMOVAL
Two different Airbag Control Modules (ACM) are
available for this vehicle. For vehicles equipped with
the optional side curtain airbags, both ACM connec-
tor receptacles are black in color and the ACM con-
tains a second bi-directional safing sensor for the
side airbags. For vehicles not equipped with the
optional side curtain airbags, the ACM connector
receptacles are gray.
8O - 10 RESTRAINTSWJ
AIRBAG CONTROL MODULE (Continued)
Page 552 of 2199
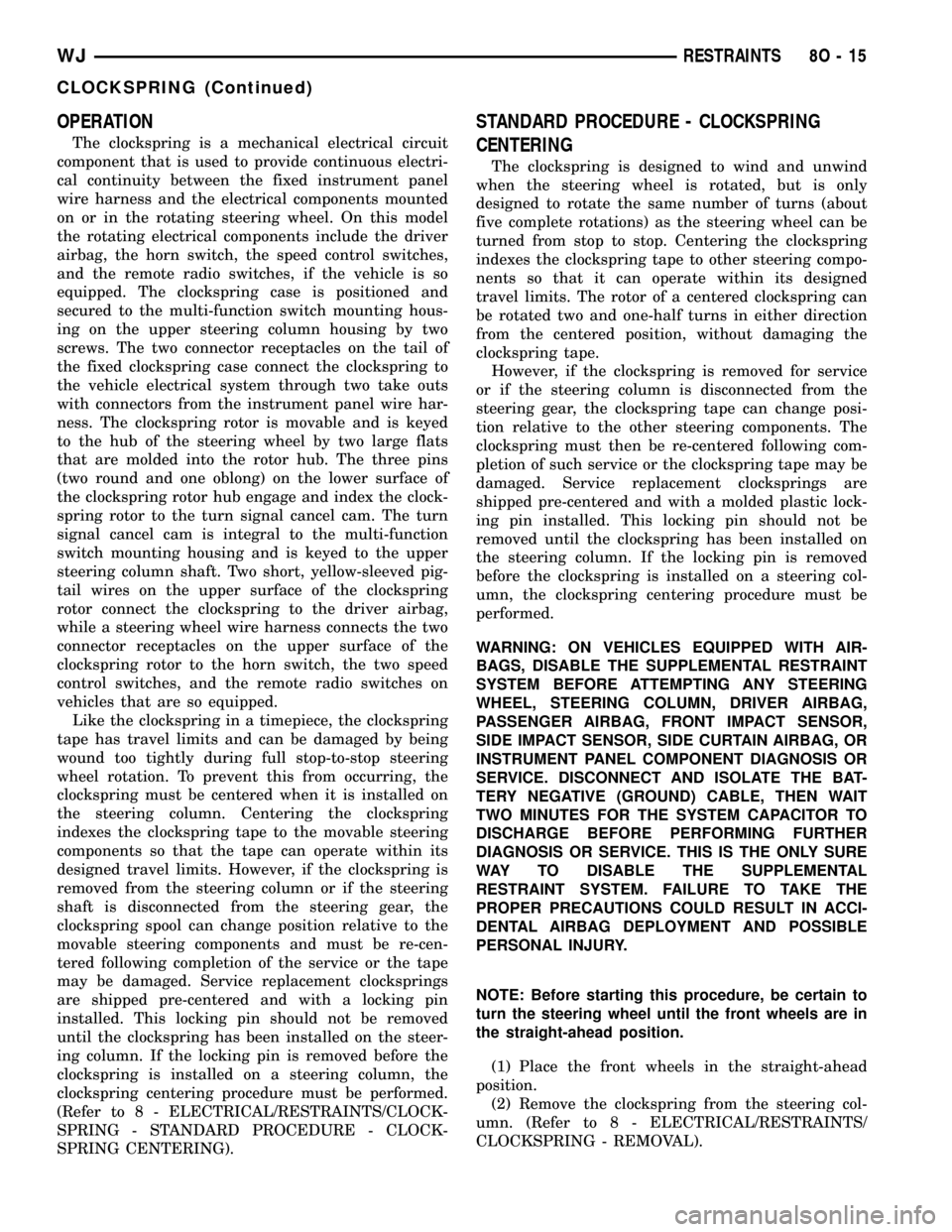
OPERATION
The clockspring is a mechanical electrical circuit
component that is used to provide continuous electri-
cal continuity between the fixed instrument panel
wire harness and the electrical components mounted
on or in the rotating steering wheel. On this model
the rotating electrical components include the driver
airbag, the horn switch, the speed control switches,
and the remote radio switches, if the vehicle is so
equipped. The clockspring case is positioned and
secured to the multi-function switch mounting hous-
ing on the upper steering column housing by two
screws. The two connector receptacles on the tail of
the fixed clockspring case connect the clockspring to
the vehicle electrical system through two take outs
with connectors from the instrument panel wire har-
ness. The clockspring rotor is movable and is keyed
to the hub of the steering wheel by two large flats
that are molded into the rotor hub. The three pins
(two round and one oblong) on the lower surface of
the clockspring rotor hub engage and index the clock-
spring rotor to the turn signal cancel cam. The turn
signal cancel cam is integral to the multi-function
switch mounting housing and is keyed to the upper
steering column shaft. Two short, yellow-sleeved pig-
tail wires on the upper surface of the clockspring
rotor connect the clockspring to the driver airbag,
while a steering wheel wire harness connects the two
connector receptacles on the upper surface of the
clockspring rotor to the horn switch, the two speed
control switches, and the remote radio switches on
vehicles that are so equipped.
Like the clockspring in a timepiece, the clockspring
tape has travel limits and can be damaged by being
wound too tightly during full stop-to-stop steering
wheel rotation. To prevent this from occurring, the
clockspring must be centered when it is installed on
the steering column. Centering the clockspring
indexes the clockspring tape to the movable steering
components so that the tape can operate within its
designed travel limits. However, if the clockspring is
removed from the steering column or if the steering
shaft is disconnected from the steering gear, the
clockspring spool can change position relative to the
movable steering components and must be re-cen-
tered following completion of the service or the tape
may be damaged. Service replacement clocksprings
are shipped pre-centered and with a locking pin
installed. This locking pin should not be removed
until the clockspring has been installed on the steer-
ing column. If the locking pin is removed before the
clockspring is installed on a steering column, the
clockspring centering procedure must be performed.
(Refer to 8 - ELECTRICAL/RESTRAINTS/CLOCK-
SPRING - STANDARD PROCEDURE - CLOCK-
SPRING CENTERING).
STANDARD PROCEDURE - CLOCKSPRING
CENTERING
The clockspring is designed to wind and unwind
when the steering wheel is rotated, but is only
designed to rotate the same number of turns (about
five complete rotations) as the steering wheel can be
turned from stop to stop. Centering the clockspring
indexes the clockspring tape to other steering compo-
nents so that it can operate within its designed
travel limits. The rotor of a centered clockspring can
be rotated two and one-half turns in either direction
from the centered position, without damaging the
clockspring tape.
However, if the clockspring is removed for service
or if the steering column is disconnected from the
steering gear, the clockspring tape can change posi-
tion relative to the other steering components. The
clockspring must then be re-centered following com-
pletion of such service or the clockspring tape may be
damaged. Service replacement clocksprings are
shipped pre-centered and with a molded plastic lock-
ing pin installed. This locking pin should not be
removed until the clockspring has been installed on
the steering column. If the locking pin is removed
before the clockspring is installed on a steering col-
umn, the clockspring centering procedure must be
performed.
WARNING: ON VEHICLES EQUIPPED WITH AIR-
BAGS, DISABLE THE SUPPLEMENTAL RESTRAINT
SYSTEM BEFORE ATTEMPTING ANY STEERING
WHEEL, STEERING COLUMN, DRIVER AIRBAG,
PASSENGER AIRBAG, FRONT IMPACT SENSOR,
SIDE IMPACT SENSOR, SIDE CURTAIN AIRBAG, OR
INSTRUMENT PANEL COMPONENT DIAGNOSIS OR
SERVICE. DISCONNECT AND ISOLATE THE BAT-
TERY NEGATIVE (GROUND) CABLE, THEN WAIT
TWO MINUTES FOR THE SYSTEM CAPACITOR TO
DISCHARGE BEFORE PERFORMING FURTHER
DIAGNOSIS OR SERVICE. THIS IS THE ONLY SURE
WAY TO DISABLE THE SUPPLEMENTAL
RESTRAINT SYSTEM. FAILURE TO TAKE THE
PROPER PRECAUTIONS COULD RESULT IN ACCI-
DENTAL AIRBAG DEPLOYMENT AND POSSIBLE
PERSONAL INJURY.
NOTE: Before starting this procedure, be certain to
turn the steering wheel until the front wheels are in
the straight-ahead position.
(1) Place the front wheels in the straight-ahead
position.
(2) Remove the clockspring from the steering col-
umn. (Refer to 8 - ELECTRICAL/RESTRAINTS/
CLOCKSPRING - REMOVAL).
WJRESTRAINTS 8O - 15
CLOCKSPRING (Continued)
Page 594 of 2199
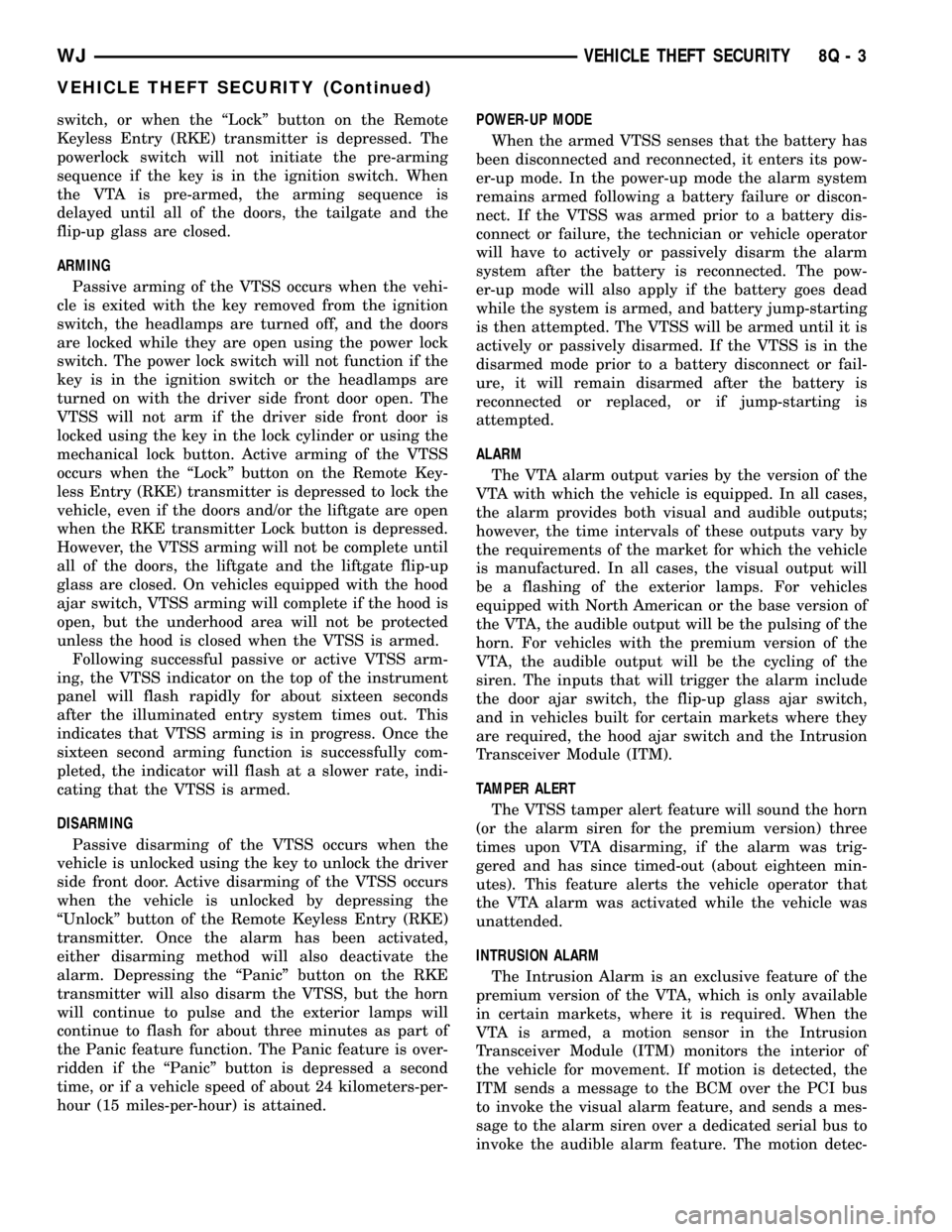
switch, or when the ªLockº button on the Remote
Keyless Entry (RKE) transmitter is depressed. The
powerlock switch will not initiate the pre-arming
sequence if the key is in the ignition switch. When
the VTA is pre-armed, the arming sequence is
delayed until all of the doors, the tailgate and the
flip-up glass are closed.
ARMING
Passive arming of the VTSS occurs when the vehi-
cle is exited with the key removed from the ignition
switch, the headlamps are turned off, and the doors
are locked while they are open using the power lock
switch. The power lock switch will not function if the
key is in the ignition switch or the headlamps are
turned on with the driver side front door open. The
VTSS will not arm if the driver side front door is
locked using the key in the lock cylinder or using the
mechanical lock button. Active arming of the VTSS
occurs when the ªLockº button on the Remote Key-
less Entry (RKE) transmitter is depressed to lock the
vehicle, even if the doors and/or the liftgate are open
when the RKE transmitter Lock button is depressed.
However, the VTSS arming will not be complete until
all of the doors, the liftgate and the liftgate flip-up
glass are closed. On vehicles equipped with the hood
ajar switch, VTSS arming will complete if the hood is
open, but the underhood area will not be protected
unless the hood is closed when the VTSS is armed.
Following successful passive or active VTSS arm-
ing, the VTSS indicator on the top of the instrument
panel will flash rapidly for about sixteen seconds
after the illuminated entry system times out. This
indicates that VTSS arming is in progress. Once the
sixteen second arming function is successfully com-
pleted, the indicator will flash at a slower rate, indi-
cating that the VTSS is armed.
DISARMING
Passive disarming of the VTSS occurs when the
vehicle is unlocked using the key to unlock the driver
side front door. Active disarming of the VTSS occurs
when the vehicle is unlocked by depressing the
ªUnlockº button of the Remote Keyless Entry (RKE)
transmitter. Once the alarm has been activated,
either disarming method will also deactivate the
alarm. Depressing the ªPanicº button on the RKE
transmitter will also disarm the VTSS, but the horn
will continue to pulse and the exterior lamps will
continue to flash for about three minutes as part of
the Panic feature function. The Panic feature is over-
ridden if the ªPanicº button is depressed a second
time, or if a vehicle speed of about 24 kilometers-per-
hour (15 miles-per-hour) is attained.POWER-UP MODE
When the armed VTSS senses that the battery has
been disconnected and reconnected, it enters its pow-
er-up mode. In the power-up mode the alarm system
remains armed following a battery failure or discon-
nect. If the VTSS was armed prior to a battery dis-
connect or failure, the technician or vehicle operator
will have to actively or passively disarm the alarm
system after the battery is reconnected. The pow-
er-up mode will also apply if the battery goes dead
while the system is armed, and battery jump-starting
is then attempted. The VTSS will be armed until it is
actively or passively disarmed. If the VTSS is in the
disarmed mode prior to a battery disconnect or fail-
ure, it will remain disarmed after the battery is
reconnected or replaced, or if jump-starting is
attempted.
ALARM
The VTA alarm output varies by the version of the
VTA with which the vehicle is equipped. In all cases,
the alarm provides both visual and audible outputs;
however, the time intervals of these outputs vary by
the requirements of the market for which the vehicle
is manufactured. In all cases, the visual output will
be a flashing of the exterior lamps. For vehicles
equipped with North American or the base version of
the VTA, the audible output will be the pulsing of the
horn. For vehicles with the premium version of the
VTA, the audible output will be the cycling of the
siren. The inputs that will trigger the alarm include
the door ajar switch, the flip-up glass ajar switch,
and in vehicles built for certain markets where they
are required, the hood ajar switch and the Intrusion
Transceiver Module (ITM).
TAMPER ALERT
The VTSS tamper alert feature will sound the horn
(or the alarm siren for the premium version) three
times upon VTA disarming, if the alarm was trig-
gered and has since timed-out (about eighteen min-
utes). This feature alerts the vehicle operator that
the VTA alarm was activated while the vehicle was
unattended.
INTRUSION ALARM
The Intrusion Alarm is an exclusive feature of the
premium version of the VTA, which is only available
in certain markets, where it is required. When the
VTA is armed, a motion sensor in the Intrusion
Transceiver Module (ITM) monitors the interior of
the vehicle for movement. If motion is detected, the
ITM sends a message to the BCM over the PCI bus
to invoke the visual alarm feature, and sends a mes-
sage to the alarm siren over a dedicated serial bus to
invoke the audible alarm feature. The motion detec-
WJVEHICLE THEFT SECURITY 8Q - 3
VEHICLE THEFT SECURITY (Continued)
Page 706 of 2199
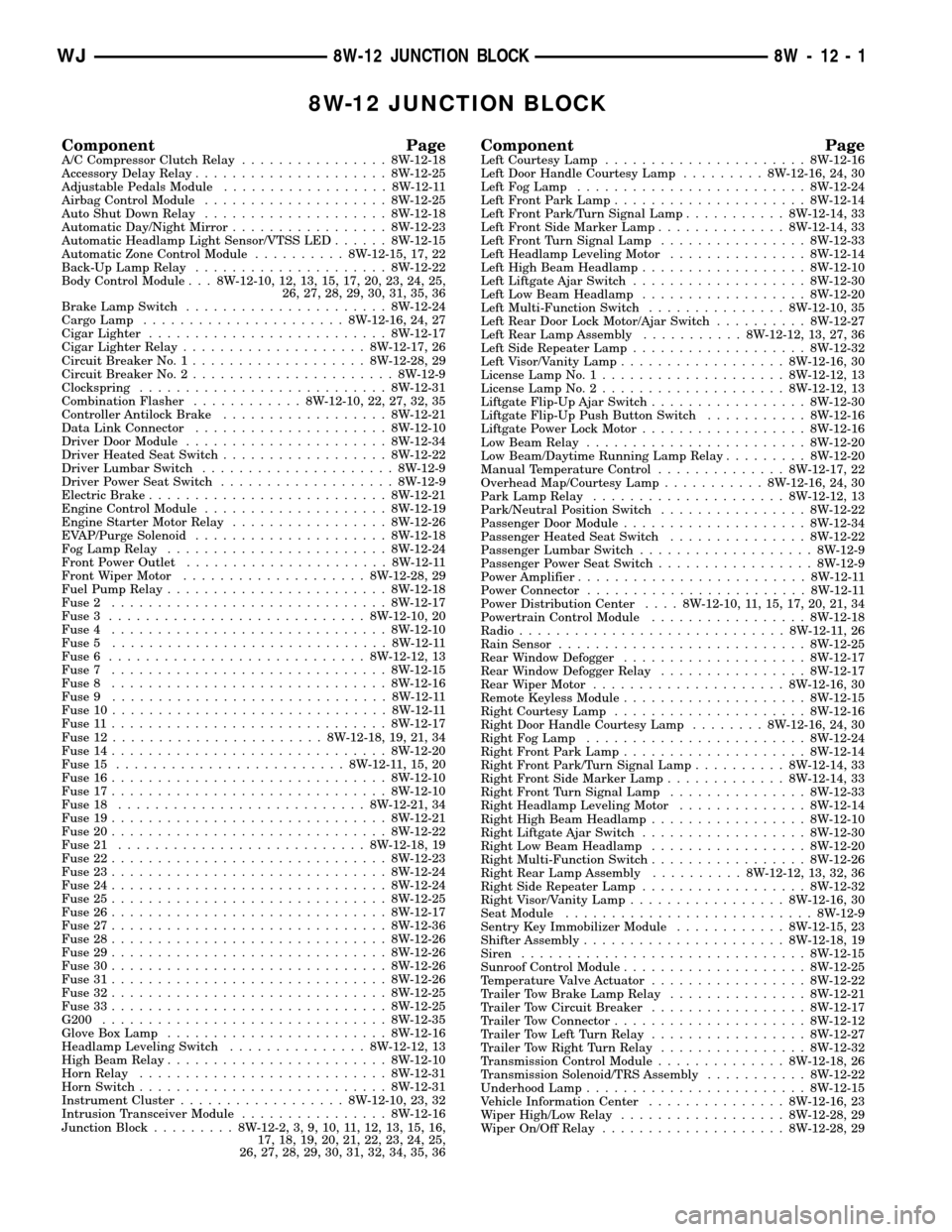
8W-12 JUNCTION BLOCK
Component PageA/C Compressor Clutch Relay................8W-12-18
Accessory Delay Relay.....................8W-12-25
Adjustable Pedals Module..................8W-12-11
Airbag Control Module....................8W-12-25
Auto Shut Down Relay....................8W-12-18
Automatic Day/Night Mirror.................8W-12-23
Automatic Headlamp Light Sensor/VTSS LED......8W-12-15
Automatic Zone Control Module..........8W-12-15, 17, 22
Back-Up Lamp Relay.....................8W-12-22
Body Control Module . . . 8W-12-10, 12, 13, 15, 17, 20, 23, 24, 25,
26, 27, 28, 29, 30, 31, 35, 36
Brake Lamp Switch......................8W-12-24
Cargo Lamp......................8W-12-16, 24, 27
Cigar Lighter..........................8W-12-17
Cigar Lighter Relay....................8W-12-17, 26
Circuit Breaker No. 1...................8W-12-28, 29
Circuit Breaker No. 2......................8W-12-9
Clockspring...........................8W-12-31
Combination Flasher............8W-12-10, 22, 27, 32, 35
Controller Antilock Brake..................8W-12-21
Data Link Connector.....................8W-12-10
Driver Door Module......................8W-12-34
Driver Heated Seat Switch..................8W-12-22
Driver Lumbar Switch.....................8W-12-9
Driver Power Seat Switch...................8W-12-9
Electric Brake..........................8W-12-21
Engine Control Module....................8W-12-19
Engine Starter Motor Relay.................8W-12-26
EVAP/Purge Solenoid.....................8W-12-18
Fog Lamp Relay........................8W-12-24
Front Power Outlet......................8W-12-11
Front Wiper Motor....................8W-12-28, 29
Fuel Pump Relay........................8W-12-18
Fuse 2..............................8W-12-17
Fuse 3............................8W-12-10, 20
Fuse 4..............................8W-12-10
Fuse 5..............................8W-12-11
Fuse 6............................8W-12-12, 13
Fuse 7..............................8W-12-15
Fuse 8..............................8W-12-16
Fuse 9..............................8W-12-11
Fuse 10..............................8W-12-11
Fuse 11..............................8W-12-17
Fuse 12.......................8W-12-18, 19, 21, 34
Fuse 14..............................8W-12-20
Fuse 15.........................8W-12-11, 15, 20
Fuse 16..............................8W-12-10
Fuse 17..............................8W-12-10
Fuse 18...........................8W-12-21, 34
Fuse 19..............................8W-12-21
Fuse 20..............................8W-12-22
Fuse 21...........................8W-12-18, 19
Fuse 22..............................8W-12-23
Fuse 23..............................8W-12-24
Fuse 24..............................8W-12-24
Fuse 25..............................8W-12-25
Fuse 26..............................8W-12-17
Fuse 27..............................8W-12-36
Fuse 28..............................8W-12-26
Fuse 29..............................8W-12-26
Fuse 30..............................8W-12-26
Fuse 31..............................8W-12-26
Fuse 32..............................8W-12-25
Fuse 33..............................8W-12-25
G200...............................8W-12-35
Glove Box Lamp........................8W-12-16
Headlamp Leveling Switch...............8W-12-12, 13
High Beam Relay........................8W-12-10
Horn Relay...........................8W-12-31
Horn Switch...........................8W-12-31
Instrument Cluster..................8W-12-10, 23, 32
Intrusion Transceiver Module................8W-12-16
Junction Block.........8W-12-2, 3, 9, 10, 11, 12, 13, 15, 16,
17, 18, 19, 20, 21, 22, 23, 24, 25,
26, 27, 28, 29, 30, 31, 32, 34, 35, 36Component PageLeft Courtesy Lamp......................8W-12-16
Left Door Handle Courtesy Lamp.........8W-12-16, 24, 30
Left Fog Lamp.........................8W-12-24
Left Front Park Lamp.....................8W-12-14
Left Front Park/Turn Signal Lamp...........8W-12-14, 33
Left Front Side Marker Lamp..............8W-12-14, 33
Left Front Turn Signal Lamp................8W-12-33
Left Headlamp Leveling Motor...............8W-12-14
Left High Beam Headlamp..................8W-12-10
Left Liftgate Ajar Switch...................8W-12-30
Left Low Beam Headlamp..................8W-12-20
Left Multi-Function Switch...............8W-12-10, 35
Left Rear Door Lock Motor/Ajar Switch..........8W-12-27
Left Rear Lamp Assembly...........8W-12-12, 13, 27, 36
Left Side Repeater Lamp...................8W-12-32
Left Visor/Vanity Lamp..................8W-12-16, 30
License Lamp No. 1....................8W-12-12, 13
License Lamp No. 2....................8W-12-12, 13
Liftgate Flip-Up Ajar Switch.................8W-12-30
Liftgate Flip-Up Push Button Switch...........8W-12-16
Liftgate Power Lock Motor..................8W-12-16
Low Beam Relay........................8W-12-20
Low Beam/Daytime Running Lamp Relay.........8W-12-20
Manual Temperature Control..............8W-12-17, 22
Overhead Map/Courtesy Lamp...........8W-12-16, 24, 30
Park Lamp Relay.....................8W-12-12, 13
Park/Neutral Position Switch................8W-12-22
Passenger Door Module....................8W-12-34
Passenger Heated Seat Switch...............8W-12-22
Passenger Lumbar Switch...................8W-12-9
Passenger Power Seat Switch.................8W-12-9
Power Amplifier.........................8W-12-11
Power Connector........................8W-12-11
Power Distribution Center....8W-12-10, 11, 15, 17, 20, 21, 34
Powertrain Control Module.................8W-12-18
Radio.............................8W-12-11, 26
Rain Sensor...........................8W-12-25
Rear Window Defogger....................8W-12-17
Rear Window Defogger Relay................8W-12-17
Rear Wiper Motor.....................8W-12-16, 30
Remote Keyless Module....................8W-12-15
Right Courtesy Lamp.....................8W-12-16
Right Door Handle Courtesy Lamp........8W-12-16, 24, 30
Right Fog Lamp........................8W-12-24
Right Front Park Lamp....................8W-12-14
Right Front Park/Turn Signal Lamp..........8W-12-14, 33
Right Front Side Marker Lamp.............8W-12-14, 33
Right Front Turn Signal Lamp...............8W-12-33
Right Headlamp Leveling Motor..............8W-12-14
Right High Beam Headlamp.................8W-12-10
Right Liftgate Ajar Switch..................8W-12-30
Right Low Beam Headlamp.................8W-12-20
Right Multi-Function Switch.................8W-12-26
Right Rear Lamp Assembly..........8W-12-12, 13, 32, 36
Right Side Repeater Lamp..................8W-12-32
Right Visor/Vanity Lamp.................8W-12-16, 30
Seat Module...........................8W-12-9
Sentry Key Immobilizer Module............8W-12-15, 23
Shifter Assembly......................8W-12-18, 19
Siren...............................8W-12-15
Sunroof Control Module....................8W-12-25
Temperature Valve Actuator.................8W-12-22
Trailer Tow Brake Lamp Relay...............8W-12-21
Trailer Tow Circuit Breaker.................8W-12-17
Trailer Tow Connector.....................8W-12-12
Trailer Tow Left Turn Relay.................8W-12-27
Trailer Tow Right Turn Relay................8W-12-32
Transmission Control Module..............8W-12-18, 26
Transmission Solenoid/TRS Assembly...........8W-12-22
Underhood Lamp........................8W-12-15
Vehicle Information Center...............8W-12-16, 23
Wiper High/Low Relay..................8W-12-28, 29
Wiper On/Off Relay....................8W-12-28, 29
WJ8W-12 JUNCTION BLOCK 8W - 12 - 1
Page 864 of 2199
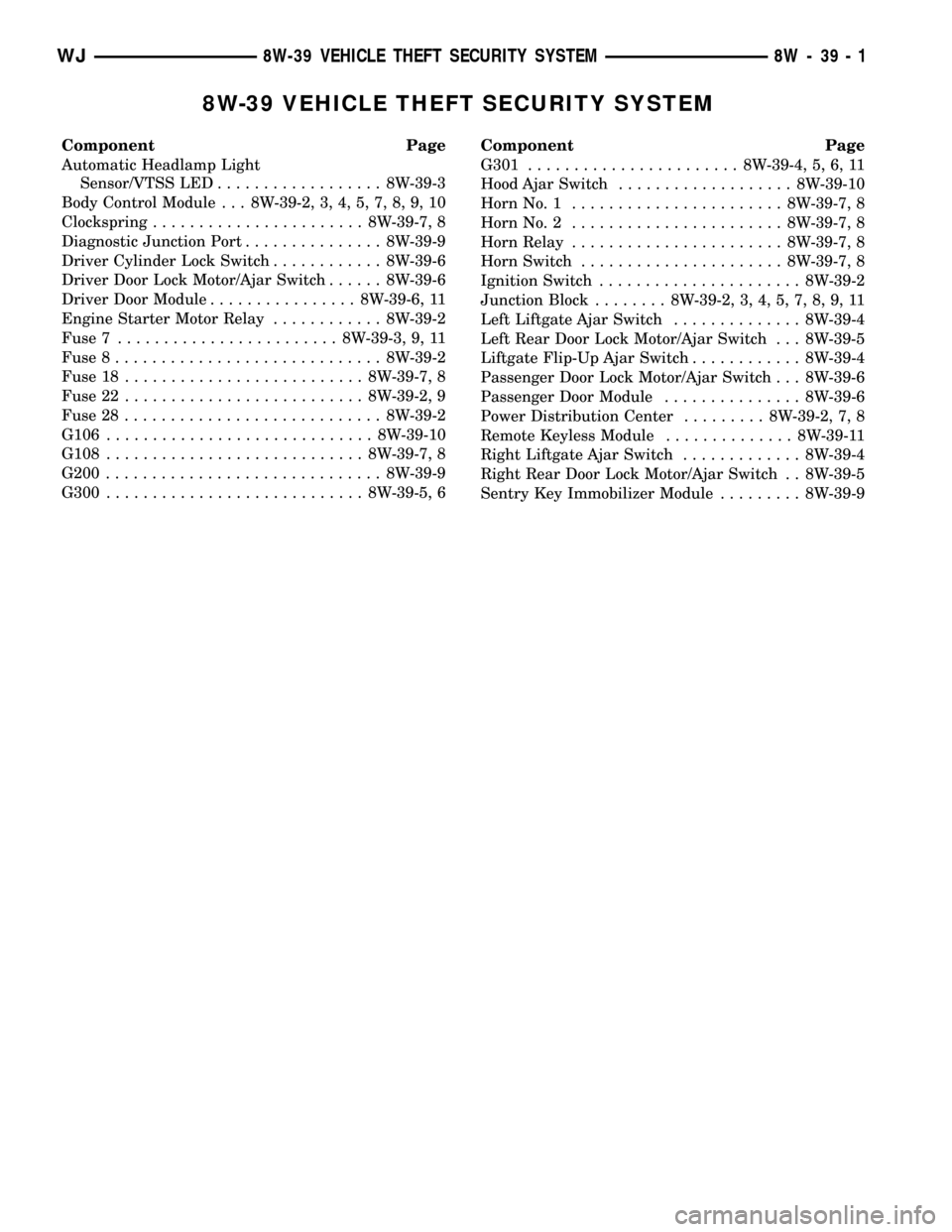
8W-39 VEHICLE THEFT SECURITY SYSTEM
Component Page
Automatic Headlamp Light
Sensor/VTSS LED.................. 8W-39-3
Body Control Module . . . 8W-39-2, 3, 4, 5, 7, 8, 9, 10
Clockspring....................... 8W-39-7, 8
Diagnostic Junction Port............... 8W-39-9
Driver Cylinder Lock Switch............ 8W-39-6
Driver Door Lock Motor/Ajar Switch...... 8W-39-6
Driver Door Module................ 8W-39-6, 11
Engine Starter Motor Relay............ 8W-39-2
Fuse 7........................ 8W-39-3, 9, 11
Fuse 8............................. 8W-39-2
Fuse 18.......................... 8W-39-7, 8
Fuse 22.......................... 8W-39-2, 9
Fuse 28............................ 8W-39-2
G106............................. 8W-39-10
G108............................ 8W-39-7, 8
G200.............................. 8W-39-9
G300............................ 8W-39-5, 6Component Page
G301....................... 8W-39-4, 5, 6, 11
Hood Ajar Switch................... 8W-39-10
Horn No. 1....................... 8W-39-7, 8
Horn No. 2....................... 8W-39-7, 8
Horn Relay....................... 8W-39-7, 8
Horn Switch...................... 8W-39-7, 8
Ignition Switch...................... 8W-39-2
Junction Block........ 8W-39-2, 3, 4, 5, 7, 8, 9, 11
Left Liftgate Ajar Switch.............. 8W-39-4
Left Rear Door Lock Motor/Ajar Switch . . . 8W-39-5
Liftgate Flip-Up Ajar Switch............ 8W-39-4
Passenger Door Lock Motor/Ajar Switch . . . 8W-39-6
Passenger Door Module............... 8W-39-6
Power Distribution Center......... 8W-39-2, 7, 8
Remote Keyless Module.............. 8W-39-11
Right Liftgate Ajar Switch............. 8W-39-4
Right Rear Door Lock Motor/Ajar Switch . . 8W-39-5
Sentry Key Immobilizer Module......... 8W-39-9
WJ8W-39 VEHICLE THEFT SECURITY SYSTEM 8W - 39 - 1
Page 1425 of 2199
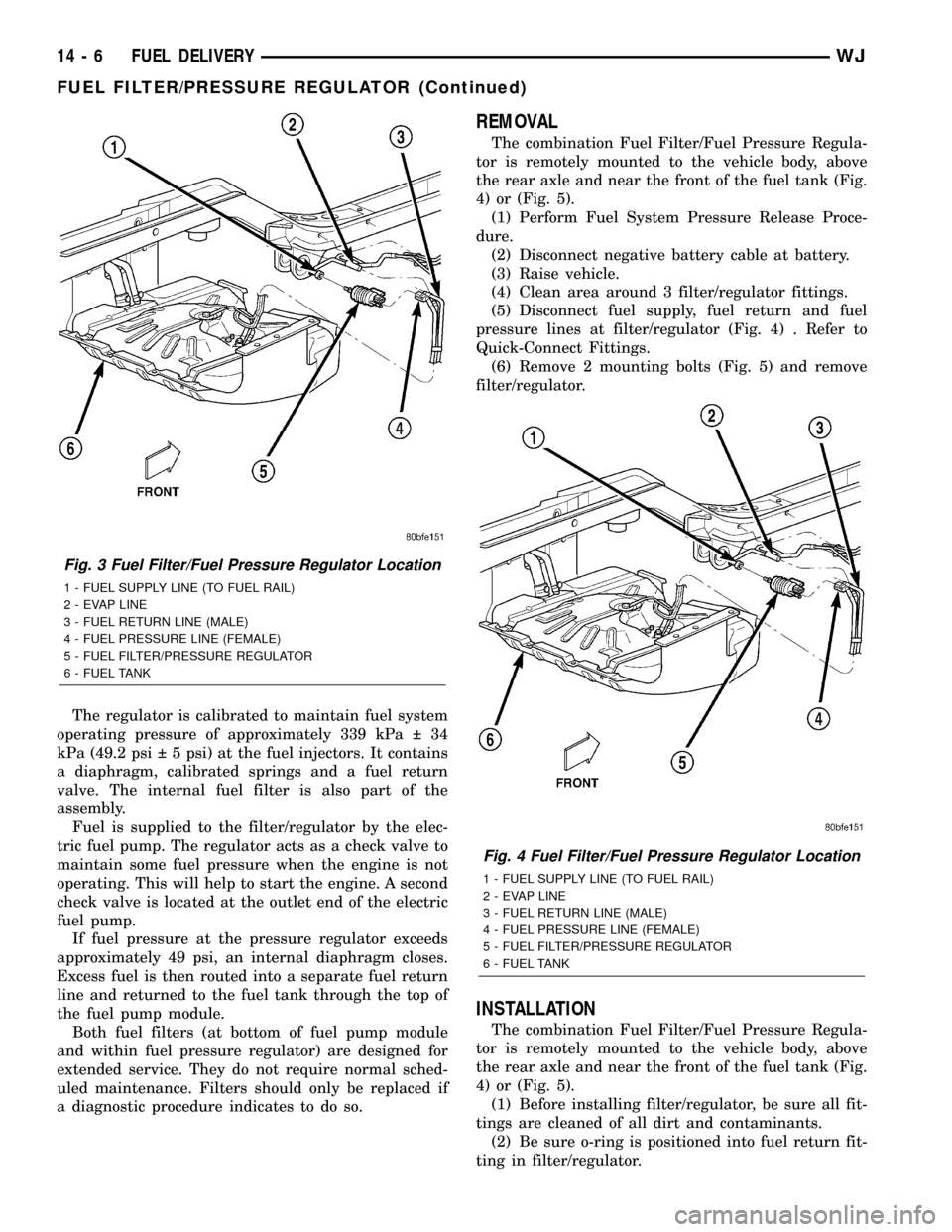
The regulator is calibrated to maintain fuel system
operating pressure of approximately 339 kPa 34
kPa (49.2 psi 5 psi) at the fuel injectors. It contains
a diaphragm, calibrated springs and a fuel return
valve. The internal fuel filter is also part of the
assembly.
Fuel is supplied to the filter/regulator by the elec-
tric fuel pump. The regulator acts as a check valve to
maintain some fuel pressure when the engine is not
operating. This will help to start the engine. A second
check valve is located at the outlet end of the electric
fuel pump.
If fuel pressure at the pressure regulator exceeds
approximately 49 psi, an internal diaphragm closes.
Excess fuel is then routed into a separate fuel return
line and returned to the fuel tank through the top of
the fuel pump module.
Both fuel filters (at bottom of fuel pump module
and within fuel pressure regulator) are designed for
extended service. They do not require normal sched-
uled maintenance. Filters should only be replaced if
a diagnostic procedure indicates to do so.
REMOVAL
The combination Fuel Filter/Fuel Pressure Regula-
tor is remotely mounted to the vehicle body, above
the rear axle and near the front of the fuel tank (Fig.
4) or (Fig. 5).
(1) Perform Fuel System Pressure Release Proce-
dure.
(2) Disconnect negative battery cable at battery.
(3) Raise vehicle.
(4) Clean area around 3 filter/regulator fittings.
(5) Disconnect fuel supply, fuel return and fuel
pressure lines at filter/regulator (Fig. 4) . Refer to
Quick-Connect Fittings.
(6) Remove 2 mounting bolts (Fig. 5) and remove
filter/regulator.
INSTALLATION
The combination Fuel Filter/Fuel Pressure Regula-
tor is remotely mounted to the vehicle body, above
the rear axle and near the front of the fuel tank (Fig.
4) or (Fig. 5).
(1) Before installing filter/regulator, be sure all fit-
tings are cleaned of all dirt and contaminants.
(2) Be sure o-ring is positioned into fuel return fit-
ting in filter/regulator.
Fig. 3 Fuel Filter/Fuel Pressure Regulator Location
1 - FUEL SUPPLY LINE (TO FUEL RAIL)
2 - EVAP LINE
3 - FUEL RETURN LINE (MALE)
4 - FUEL PRESSURE LINE (FEMALE)
5 - FUEL FILTER/PRESSURE REGULATOR
6 - FUEL TANK
Fig. 4 Fuel Filter/Fuel Pressure Regulator Location
1 - FUEL SUPPLY LINE (TO FUEL RAIL)
2 - EVAP LINE
3 - FUEL RETURN LINE (MALE)
4 - FUEL PRESSURE LINE (FEMALE)
5 - FUEL FILTER/PRESSURE REGULATOR
6 - FUEL TANK
14 - 6 FUEL DELIVERYWJ
FUEL FILTER/PRESSURE REGULATOR (Continued)