gauge JEEP GRAND CHEROKEE 2003 WJ / 2.G Workshop Manual
[x] Cancel search | Manufacturer: JEEP, Model Year: 2003, Model line: GRAND CHEROKEE, Model: JEEP GRAND CHEROKEE 2003 WJ / 2.GPages: 2199, PDF Size: 76.01 MB
Page 1700 of 2199
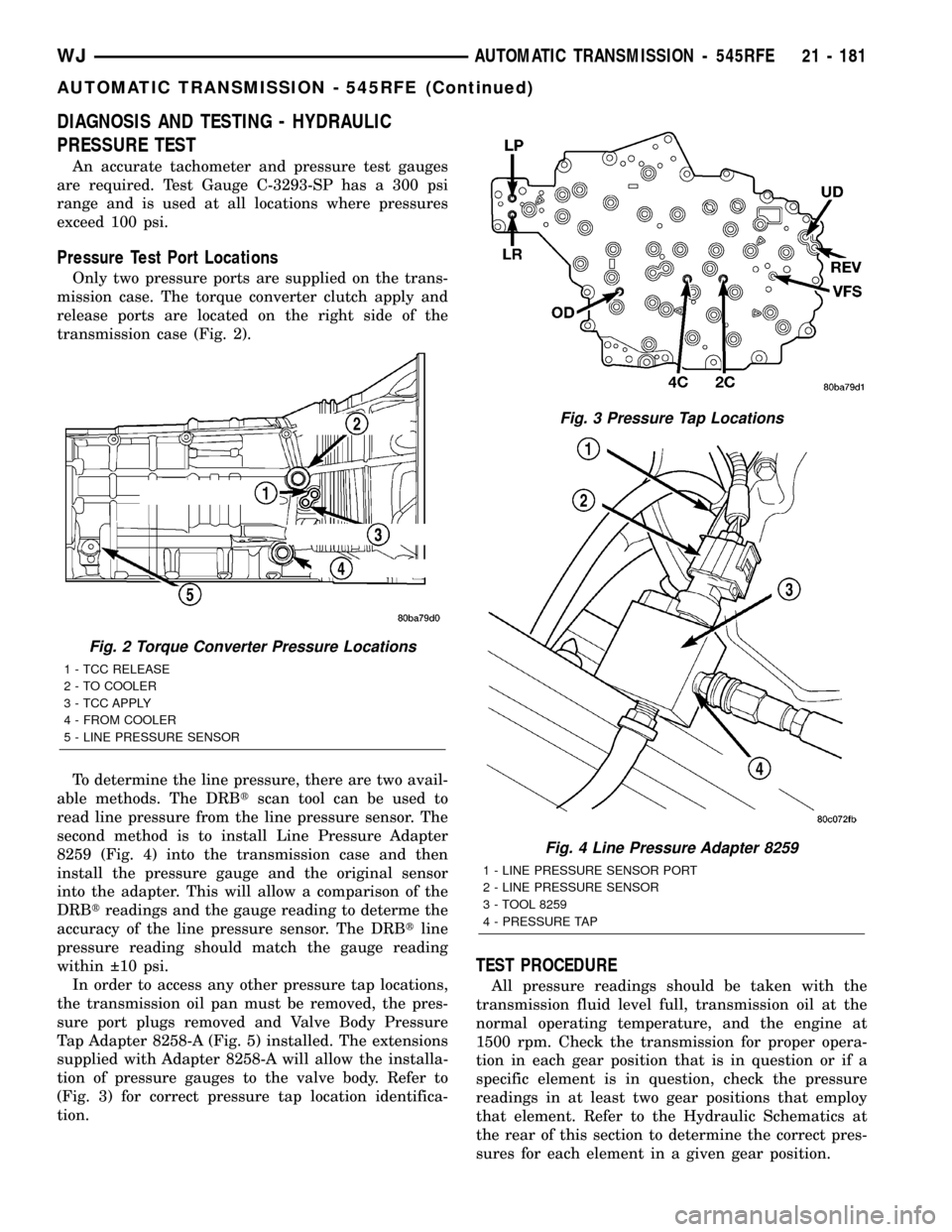
DIAGNOSIS AND TESTING - HYDRAULIC
PRESSURE TEST
An accurate tachometer and pressure test gauges
are required. Test Gauge C-3293-SP has a 300 psi
range and is used at all locations where pressures
exceed 100 psi.
Pressure Test Port Locations
Only two pressure ports are supplied on the trans-
mission case. The torque converter clutch apply and
release ports are located on the right side of the
transmission case (Fig. 2).
To determine the line pressure, there are two avail-
able methods. The DRBtscan tool can be used to
read line pressure from the line pressure sensor. The
second method is to install Line Pressure Adapter
8259 (Fig. 4) into the transmission case and then
install the pressure gauge and the original sensor
into the adapter. This will allow a comparison of the
DRBtreadings and the gauge reading to determe the
accuracy of the line pressure sensor. The DRBtline
pressure reading should match the gauge reading
within 10 psi.
In order to access any other pressure tap locations,
the transmission oil pan must be removed, the pres-
sure port plugs removed and Valve Body Pressure
Tap Adapter 8258-A (Fig. 5) installed. The extensions
supplied with Adapter 8258-A will allow the installa-
tion of pressure gauges to the valve body. Refer to
(Fig. 3) for correct pressure tap location identifica-
tion.
TEST PROCEDURE
All pressure readings should be taken with the
transmission fluid level full, transmission oil at the
normal operating temperature, and the engine at
1500 rpm. Check the transmission for proper opera-
tion in each gear position that is in question or if a
specific element is in question, check the pressure
readings in at least two gear positions that employ
that element. Refer to the Hydraulic Schematics at
the rear of this section to determine the correct pres-
sures for each element in a given gear position.
Fig. 2 Torque Converter Pressure Locations
1 - TCC RELEASE
2 - TO COOLER
3 - TCC APPLY
4 - FROM COOLER
5 - LINE PRESSURE SENSOR
Fig. 3 Pressure Tap Locations
Fig. 4 Line Pressure Adapter 8259
1 - LINE PRESSURE SENSOR PORT
2 - LINE PRESSURE SENSOR
3 - TOOL 8259
4 - PRESSURE TAP
WJAUTOMATIC TRANSMISSION - 545RFE 21 - 181
AUTOMATIC TRANSMISSION - 545RFE (Continued)
Page 1711 of 2199
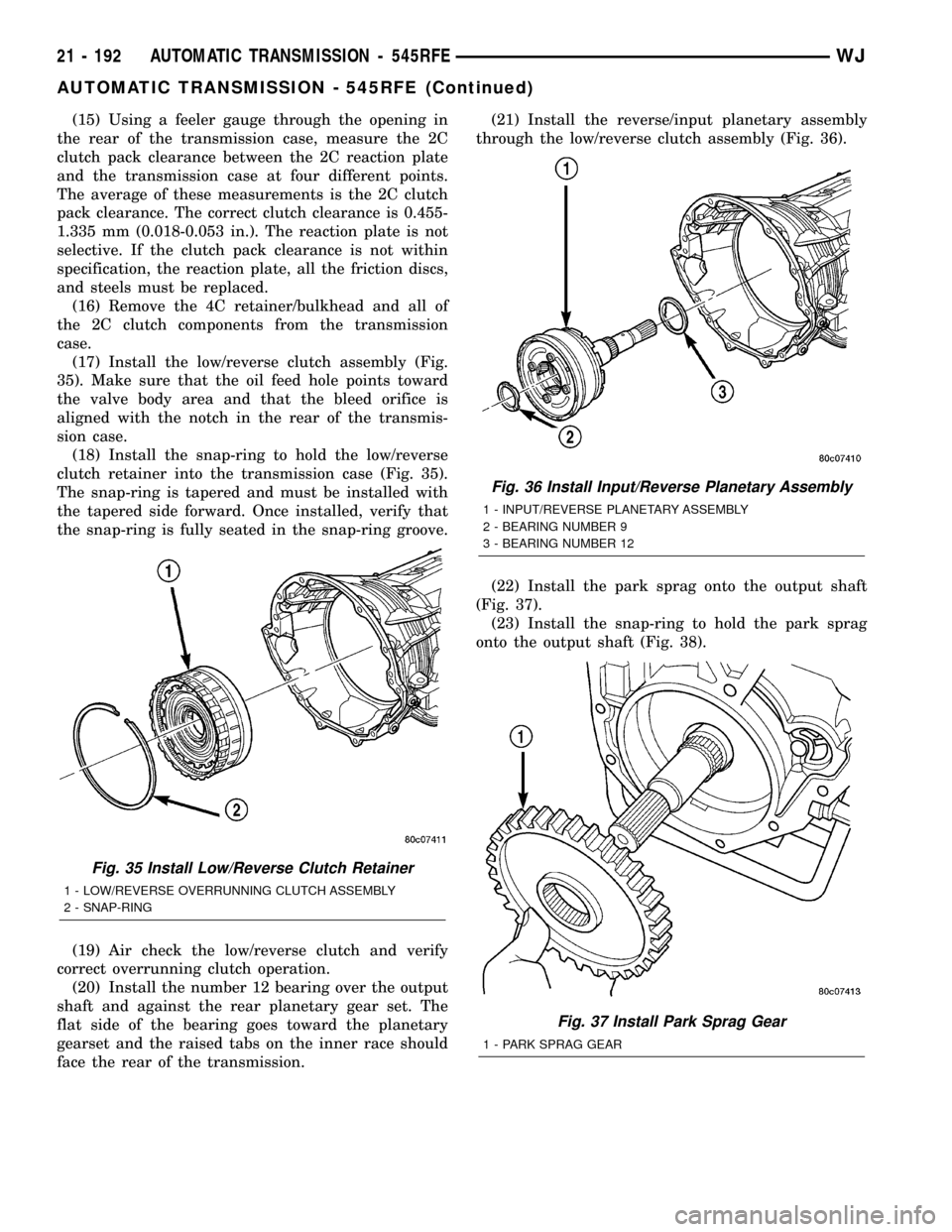
(15) Using a feeler gauge through the opening in
the rear of the transmission case, measure the 2C
clutch pack clearance between the 2C reaction plate
and the transmission case at four different points.
The average of these measurements is the 2C clutch
pack clearance. The correct clutch clearance is 0.455-
1.335 mm (0.018-0.053 in.). The reaction plate is not
selective. If the clutch pack clearance is not within
specification, the reaction plate, all the friction discs,
and steels must be replaced.
(16) Remove the 4C retainer/bulkhead and all of
the 2C clutch components from the transmission
case.
(17) Install the low/reverse clutch assembly (Fig.
35). Make sure that the oil feed hole points toward
the valve body area and that the bleed orifice is
aligned with the notch in the rear of the transmis-
sion case.
(18) Install the snap-ring to hold the low/reverse
clutch retainer into the transmission case (Fig. 35).
The snap-ring is tapered and must be installed with
the tapered side forward. Once installed, verify that
the snap-ring is fully seated in the snap-ring groove.
(19) Air check the low/reverse clutch and verify
correct overrunning clutch operation.
(20) Install the number 12 bearing over the output
shaft and against the rear planetary gear set. The
flat side of the bearing goes toward the planetary
gearset and the raised tabs on the inner race should
face the rear of the transmission.(21) Install the reverse/input planetary assembly
through the low/reverse clutch assembly (Fig. 36).
(22) Install the park sprag onto the output shaft
(Fig. 37).
(23) Install the snap-ring to hold the park sprag
onto the output shaft (Fig. 38).
Fig. 35 Install Low/Reverse Clutch Retainer
1 - LOW/REVERSE OVERRUNNING CLUTCH ASSEMBLY
2 - SNAP-RING
Fig. 36 Install Input/Reverse Planetary Assembly
1 - INPUT/REVERSE PLANETARY ASSEMBLY
2 - BEARING NUMBER 9
3 - BEARING NUMBER 12
Fig. 37 Install Park Sprag Gear
1 - PARK SPRAG GEAR
21 - 192 AUTOMATIC TRANSMISSION - 545RFEWJ
AUTOMATIC TRANSMISSION - 545RFE (Continued)
Page 1740 of 2199
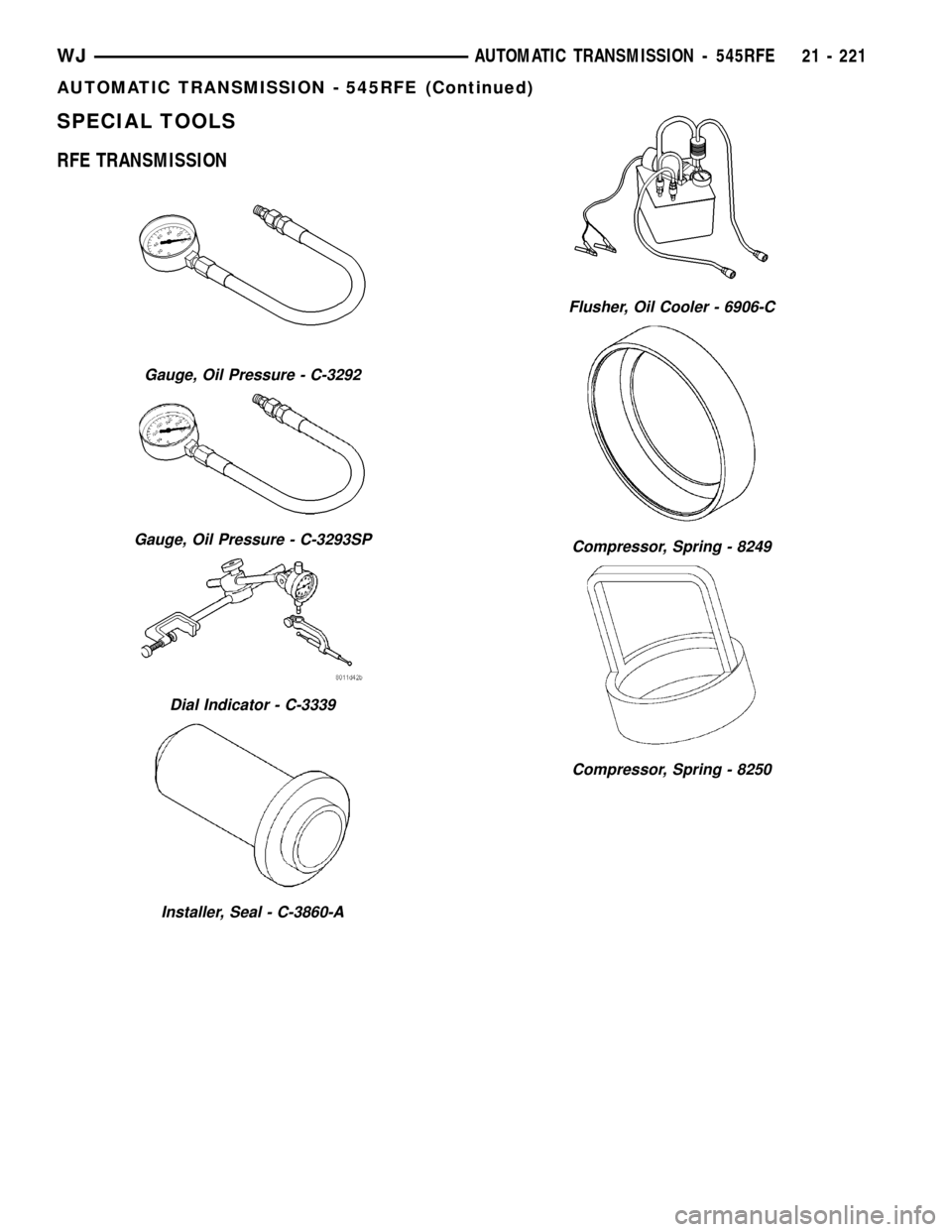
SPECIAL TOOLS
RFE TRANSMISSION
Gauge, Oil Pressure - C-3292
Gauge, Oil Pressure - C-3293SP
Dial Indicator - C-3339
Installer, Seal - C-3860-A
Flusher, Oil Cooler - 6906-C
Compressor, Spring - 8249
Compressor, Spring - 8250
WJAUTOMATIC TRANSMISSION - 545RFE 21 - 221
AUTOMATIC TRANSMISSION - 545RFE (Continued)
Page 1860 of 2199
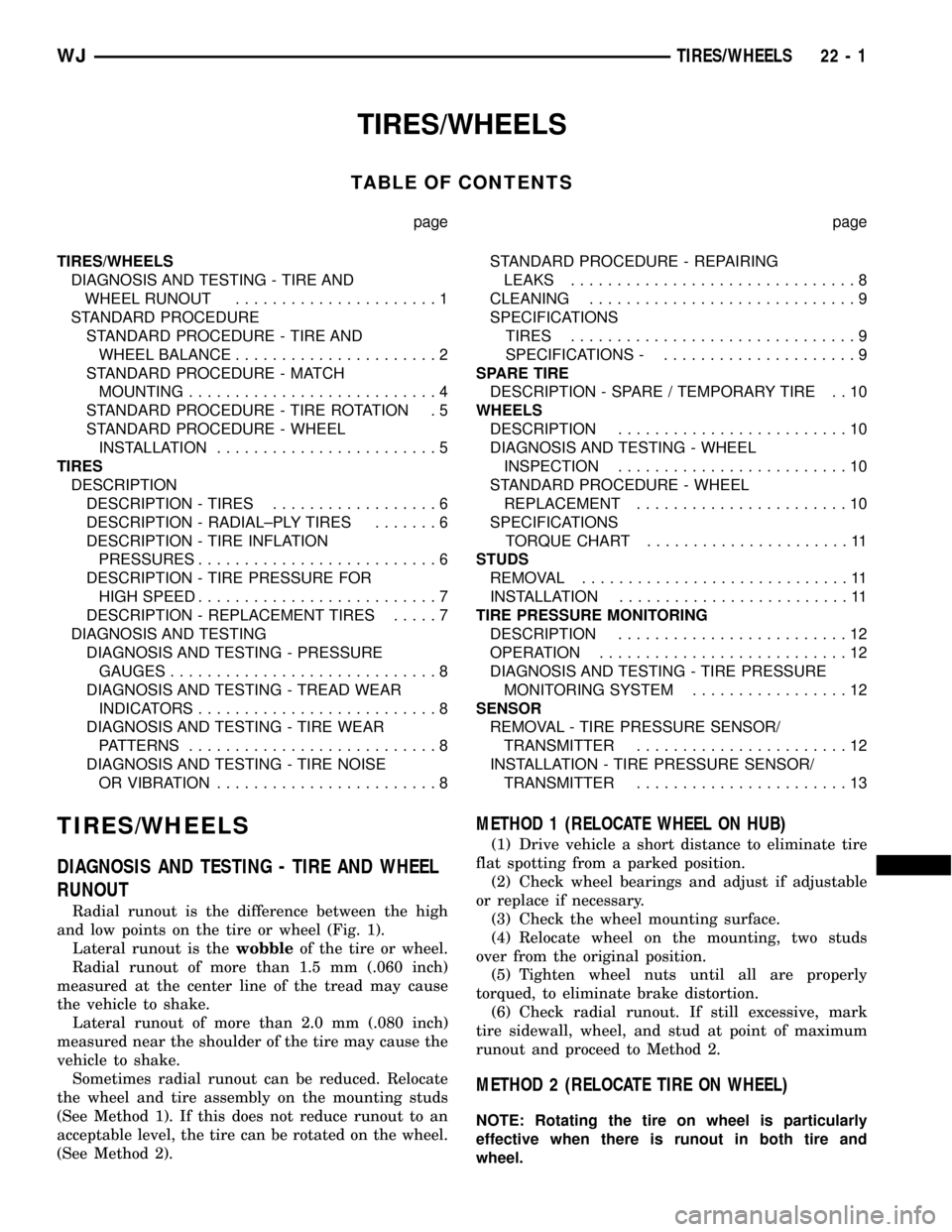
TIRES/WHEELS
TABLE OF CONTENTS
page page
TIRES/WHEELS
DIAGNOSIS AND TESTING - TIRE AND
WHEEL RUNOUT......................1
STANDARD PROCEDURE
STANDARD PROCEDURE - TIRE AND
WHEEL BALANCE......................2
STANDARD PROCEDURE - MATCH
MOUNTING...........................4
STANDARD PROCEDURE - TIRE ROTATION . 5
STANDARD PROCEDURE - WHEEL
INSTALLATION........................5
TIRES
DESCRIPTION
DESCRIPTION - TIRES..................6
DESCRIPTION - RADIAL±PLY TIRES.......6
DESCRIPTION - TIRE INFLATION
PRESSURES..........................6
DESCRIPTION - TIRE PRESSURE FOR
HIGH SPEED..........................7
DESCRIPTION - REPLACEMENT TIRES.....7
DIAGNOSIS AND TESTING
DIAGNOSIS AND TESTING - PRESSURE
GAUGES.............................8
DIAGNOSIS AND TESTING - TREAD WEAR
INDICATORS..........................8
DIAGNOSIS AND TESTING - TIRE WEAR
PATTERNS...........................8
DIAGNOSIS AND TESTING - TIRE NOISE
OR VIBRATION........................8STANDARD PROCEDURE - REPAIRING
LEAKS...............................8
CLEANING.............................9
SPECIFICATIONS
TIRES...............................9
SPECIFICATIONS -.....................9
SPARE TIRE
DESCRIPTION - SPARE / TEMPORARY TIRE . . 10
WHEELS
DESCRIPTION.........................10
DIAGNOSIS AND TESTING - WHEEL
INSPECTION.........................10
STANDARD PROCEDURE - WHEEL
REPLACEMENT.......................10
SPECIFICATIONS
TORQUE CHART......................11
STUDS
REMOVAL.............................11
INSTALLATION.........................11
TIRE PRESSURE MONITORING
DESCRIPTION.........................12
OPERATION...........................12
DIAGNOSIS AND TESTING - TIRE PRESSURE
MONITORING SYSTEM.................12
SENSOR
REMOVAL - TIRE PRESSURE SENSOR/
TRANSMITTER.......................12
INSTALLATION - TIRE PRESSURE SENSOR/
TRANSMITTER.......................13
TIRES/WHEELS
DIAGNOSIS AND TESTING - TIRE AND WHEEL
RUNOUT
Radial runout is the difference between the high
and low points on the tire or wheel (Fig. 1).
Lateral runout is thewobbleof the tire or wheel.
Radial runout of more than 1.5 mm (.060 inch)
measured at the center line of the tread may cause
the vehicle to shake.
Lateral runout of more than 2.0 mm (.080 inch)
measured near the shoulder of the tire may cause the
vehicle to shake.
Sometimes radial runout can be reduced. Relocate
the wheel and tire assembly on the mounting studs
(See Method 1). If this does not reduce runout to an
acceptable level, the tire can be rotated on the wheel.
(See Method 2).
METHOD 1 (RELOCATE WHEEL ON HUB)
(1) Drive vehicle a short distance to eliminate tire
flat spotting from a parked position.
(2) Check wheel bearings and adjust if adjustable
or replace if necessary.
(3) Check the wheel mounting surface.
(4) Relocate wheel on the mounting, two studs
over from the original position.
(5) Tighten wheel nuts until all are properly
torqued, to eliminate brake distortion.
(6) Check radial runout. If still excessive, mark
tire sidewall, wheel, and stud at point of maximum
runout and proceed to Method 2.
METHOD 2 (RELOCATE TIRE ON WHEEL)
NOTE: Rotating the tire on wheel is particularly
effective when there is runout in both tire and
wheel.
WJTIRES/WHEELS 22 - 1
Page 1867 of 2199
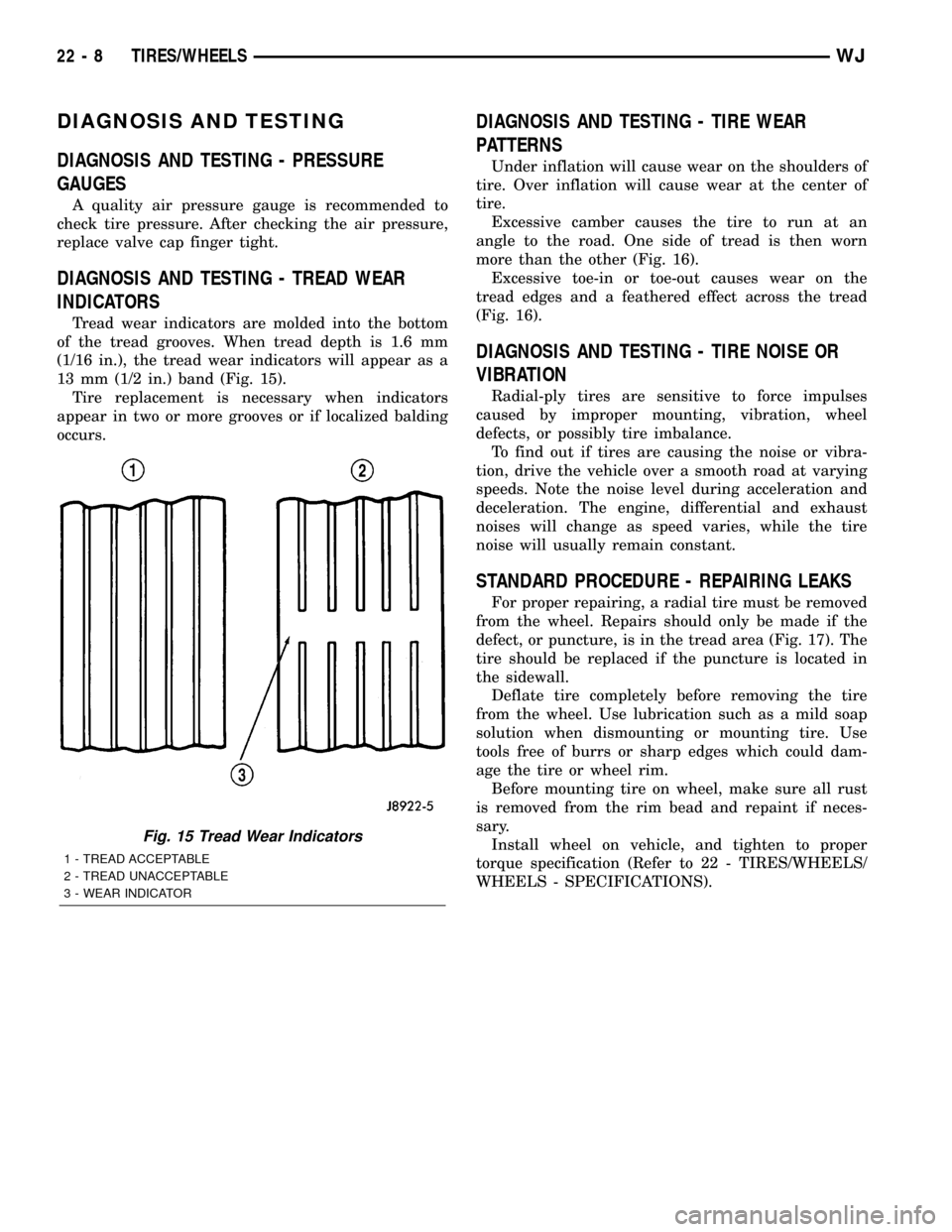
DIAGNOSIS AND TESTING
DIAGNOSIS AND TESTING - PRESSURE
GAUGES
A quality air pressure gauge is recommended to
check tire pressure. After checking the air pressure,
replace valve cap finger tight.
DIAGNOSIS AND TESTING - TREAD WEAR
INDICATORS
Tread wear indicators are molded into the bottom
of the tread grooves. When tread depth is 1.6 mm
(1/16 in.), the tread wear indicators will appear as a
13 mm (1/2 in.) band (Fig. 15).
Tire replacement is necessary when indicators
appear in two or more grooves or if localized balding
occurs.
DIAGNOSIS AND TESTING - TIRE WEAR
PATTERNS
Under inflation will cause wear on the shoulders of
tire. Over inflation will cause wear at the center of
tire.
Excessive camber causes the tire to run at an
angle to the road. One side of tread is then worn
more than the other (Fig. 16).
Excessive toe-in or toe-out causes wear on the
tread edges and a feathered effect across the tread
(Fig. 16).
DIAGNOSIS AND TESTING - TIRE NOISE OR
VIBRATION
Radial-ply tires are sensitive to force impulses
caused by improper mounting, vibration, wheel
defects, or possibly tire imbalance.
To find out if tires are causing the noise or vibra-
tion, drive the vehicle over a smooth road at varying
speeds. Note the noise level during acceleration and
deceleration. The engine, differential and exhaust
noises will change as speed varies, while the tire
noise will usually remain constant.
STANDARD PROCEDURE - REPAIRING LEAKS
For proper repairing, a radial tire must be removed
from the wheel. Repairs should only be made if the
defect, or puncture, is in the tread area (Fig. 17). The
tire should be replaced if the puncture is located in
the sidewall.
Deflate tire completely before removing the tire
from the wheel. Use lubrication such as a mild soap
solution when dismounting or mounting tire. Use
tools free of burrs or sharp edges which could dam-
age the tire or wheel rim.
Before mounting tire on wheel, make sure all rust
is removed from the rim bead and repaint if neces-
sary.
Install wheel on vehicle, and tighten to proper
torque specification (Refer to 22 - TIRES/WHEELS/
WHEELS - SPECIFICATIONS).
Fig. 15 Tread Wear Indicators
1 - TREAD ACCEPTABLE
2 - TREAD UNACCEPTABLE
3 - WEAR INDICATOR
22 - 8 TIRES/WHEELSWJ
Page 1955 of 2199
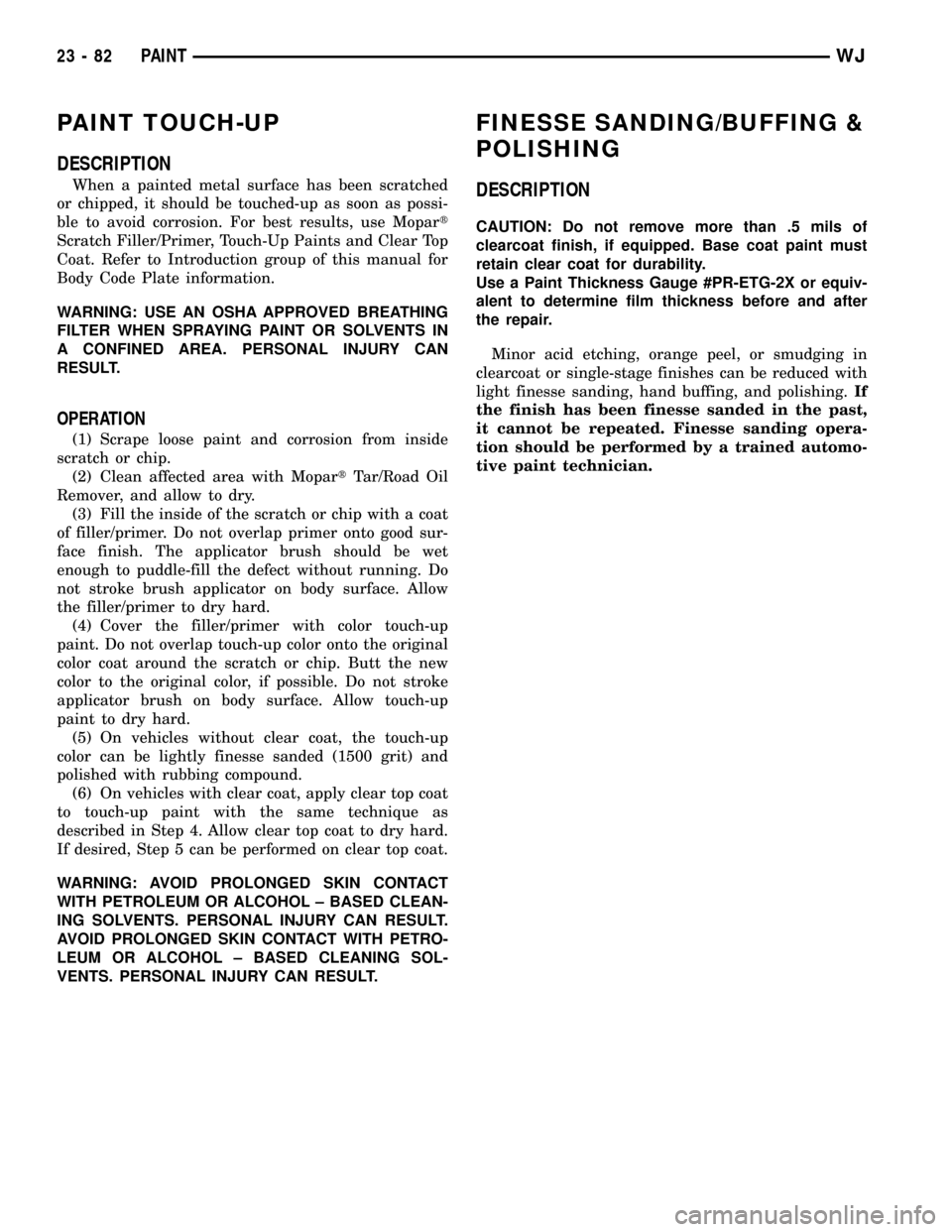
PAINT TOUCH-UP
DESCRIPTION
When a painted metal surface has been scratched
or chipped, it should be touched-up as soon as possi-
ble to avoid corrosion. For best results, use Mopart
Scratch Filler/Primer, Touch-Up Paints and Clear Top
Coat. Refer to Introduction group of this manual for
Body Code Plate information.
WARNING: USE AN OSHA APPROVED BREATHING
FILTER WHEN SPRAYING PAINT OR SOLVENTS IN
A CONFINED AREA. PERSONAL INJURY CAN
RESULT.
OPERATION
(1) Scrape loose paint and corrosion from inside
scratch or chip.
(2) Clean affected area with MopartTar/Road Oil
Remover, and allow to dry.
(3) Fill the inside of the scratch or chip with a coat
of filler/primer. Do not overlap primer onto good sur-
face finish. The applicator brush should be wet
enough to puddle-fill the defect without running. Do
not stroke brush applicator on body surface. Allow
the filler/primer to dry hard.
(4) Cover the filler/primer with color touch-up
paint. Do not overlap touch-up color onto the original
color coat around the scratch or chip. Butt the new
color to the original color, if possible. Do not stroke
applicator brush on body surface. Allow touch-up
paint to dry hard.
(5) On vehicles without clear coat, the touch-up
color can be lightly finesse sanded (1500 grit) and
polished with rubbing compound.
(6) On vehicles with clear coat, apply clear top coat
to touch-up paint with the same technique as
described in Step 4. Allow clear top coat to dry hard.
If desired, Step 5 can be performed on clear top coat.
WARNING: AVOID PROLONGED SKIN CONTACT
WITH PETROLEUM OR ALCOHOL ± BASED CLEAN-
ING SOLVENTS. PERSONAL INJURY CAN RESULT.
AVOID PROLONGED SKIN CONTACT WITH PETRO-
LEUM OR ALCOHOL ± BASED CLEANING SOL-
VENTS. PERSONAL INJURY CAN RESULT.
FINESSE SANDING/BUFFING &
POLISHING
DESCRIPTION
CAUTION: Do not remove more than .5 mils of
clearcoat finish, if equipped. Base coat paint must
retain clear coat for durability.
Use a Paint Thickness Gauge #PR-ETG-2X or equiv-
alent to determine film thickness before and after
the repair.
Minor acid etching, orange peel, or smudging in
clearcoat or single-stage finishes can be reduced with
light finesse sanding, hand buffing, and polishing.If
the finish has been finesse sanded in the past,
it cannot be repeated. Finesse sanding opera-
tion should be performed by a trained automo-
tive paint technician.
23 - 82 PAINTWJ
Page 2080 of 2199
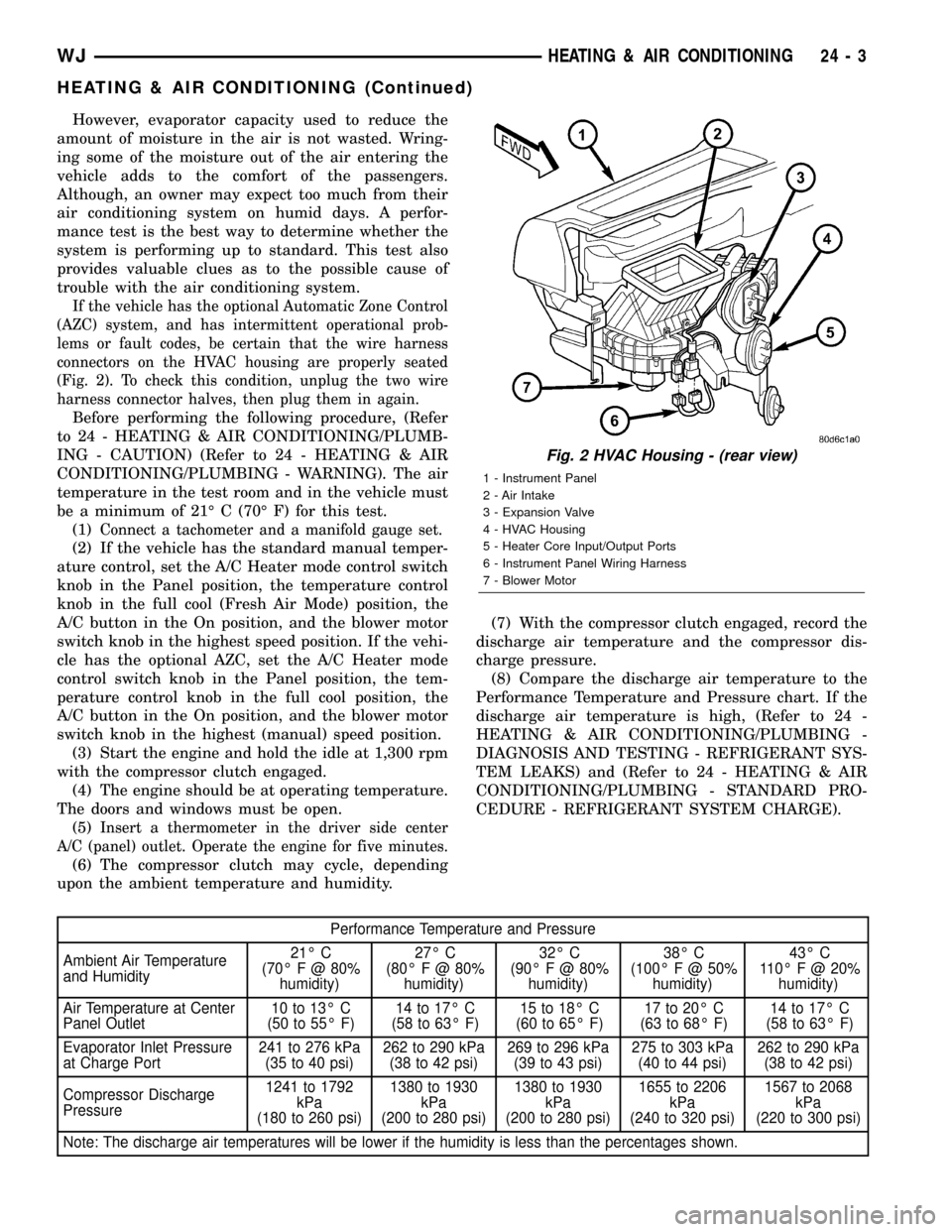
However, evaporator capacity used to reduce the
amount of moisture in the air is not wasted. Wring-
ing some of the moisture out of the air entering the
vehicle adds to the comfort of the passengers.
Although, an owner may expect too much from their
air conditioning system on humid days. A perfor-
mance test is the best way to determine whether the
system is performing up to standard. This test also
provides valuable clues as to the possible cause of
trouble with the air conditioning system.
If the vehicle has the optional Automatic Zone Control
(AZC) system, and has intermittent operational prob-
lems or fault codes, be certain that the wire harness
connectors on the HVAC housing are properly seated
(Fig. 2). To check this condition, unplug the two wire
harness connector halves, then plug them in again.
Before performing the following procedure, (Refer
to 24 - HEATING & AIR CONDITIONING/PLUMB-
ING - CAUTION) (Refer to 24 - HEATING & AIR
CONDITIONING/PLUMBING - WARNING). The air
temperature in the test room and in the vehicle must
be a minimum of 21É C (70É F) for this test.
(1)
Connect a tachometer and a manifold gauge set.
(2) If the vehicle has the standard manual temper-
ature control, set the A/C Heater mode control switch
knob in the Panel position, the temperature control
knob in the full cool (Fresh Air Mode) position, the
A/C button in the On position, and the blower motor
switch knob in the highest speed position. If the vehi-
cle has the optional AZC, set the A/C Heater mode
control switch knob in the Panel position, the tem-
perature control knob in the full cool position, the
A/C button in the On position, and the blower motor
switch knob in the highest (manual) speed position.
(3) Start the engine and hold the idle at 1,300 rpm
with the compressor clutch engaged.
(4) The engine should be at operating temperature.
The doors and windows must be open.
(5)
Insert a thermometer in the driver side center
A/C (panel) outlet. Operate the engine for five minutes.
(6) The compressor clutch may cycle, depending
upon the ambient temperature and humidity.(7) With the compressor clutch engaged, record the
discharge air temperature and the compressor dis-
charge pressure.
(8) Compare the discharge air temperature to the
Performance Temperature and Pressure chart. If the
discharge air temperature is high, (Refer to 24 -
HEATING & AIR CONDITIONING/PLUMBING -
DIAGNOSIS AND TESTING - REFRIGERANT SYS-
TEM LEAKS) and (Refer to 24 - HEATING & AIR
CONDITIONING/PLUMBING - STANDARD PRO-
CEDURE - REFRIGERANT SYSTEM CHARGE).
Performance Temperature and Pressure
Ambient Air Temperature
and Humidity21É C
(70É F @ 80%
humidity)27É C
(80É F @ 80%
humidity)32É C
(90É F @ 80%
humidity)38É C
(100ÉF@50%
humidity)43É C
110É F @ 20%
humidity)
Air Temperature at Center
Panel Outlet10 to 13É C
(50 to 55É F)14 to 17É C
(58 to 63É F)15 to 18É C
(60 to 65É F)17 to 20É C
(63 to 68É F)14 to 17É C
(58 to 63É F)
Evaporator Inlet Pressure
at Charge Port241 to 276 kPa
(35 to 40 psi)262 to 290 kPa
(38 to 42 psi)269 to 296 kPa
(39 to 43 psi)275 to 303 kPa
(40 to 44 psi)262 to 290 kPa
(38 to 42 psi)
Compressor Discharge
Pressure1241 to 1792
kPa
(180 to 260 psi)1380 to 1930
kPa
(200 to 280 psi)1380 to 1930
kPa
(200 to 280 psi)1655 to 2206
kPa
(240 to 320 psi)1567 to 2068
kPa
(220 to 300 psi)
Note: The discharge air temperatures will be lower if the humidity is less than the percentages shown.
Fig. 2 HVAC Housing - (rear view)
1 - Instrument Panel
2 - Air Intake
3 - Expansion Valve
4 - HVAC Housing
5 - Heater Core Input/Output Ports
6 - Instrument Panel Wiring Harness
7 - Blower Motor
WJHEATING & AIR CONDITIONING 24 - 3
HEATING & AIR CONDITIONING (Continued)
Page 2087 of 2199
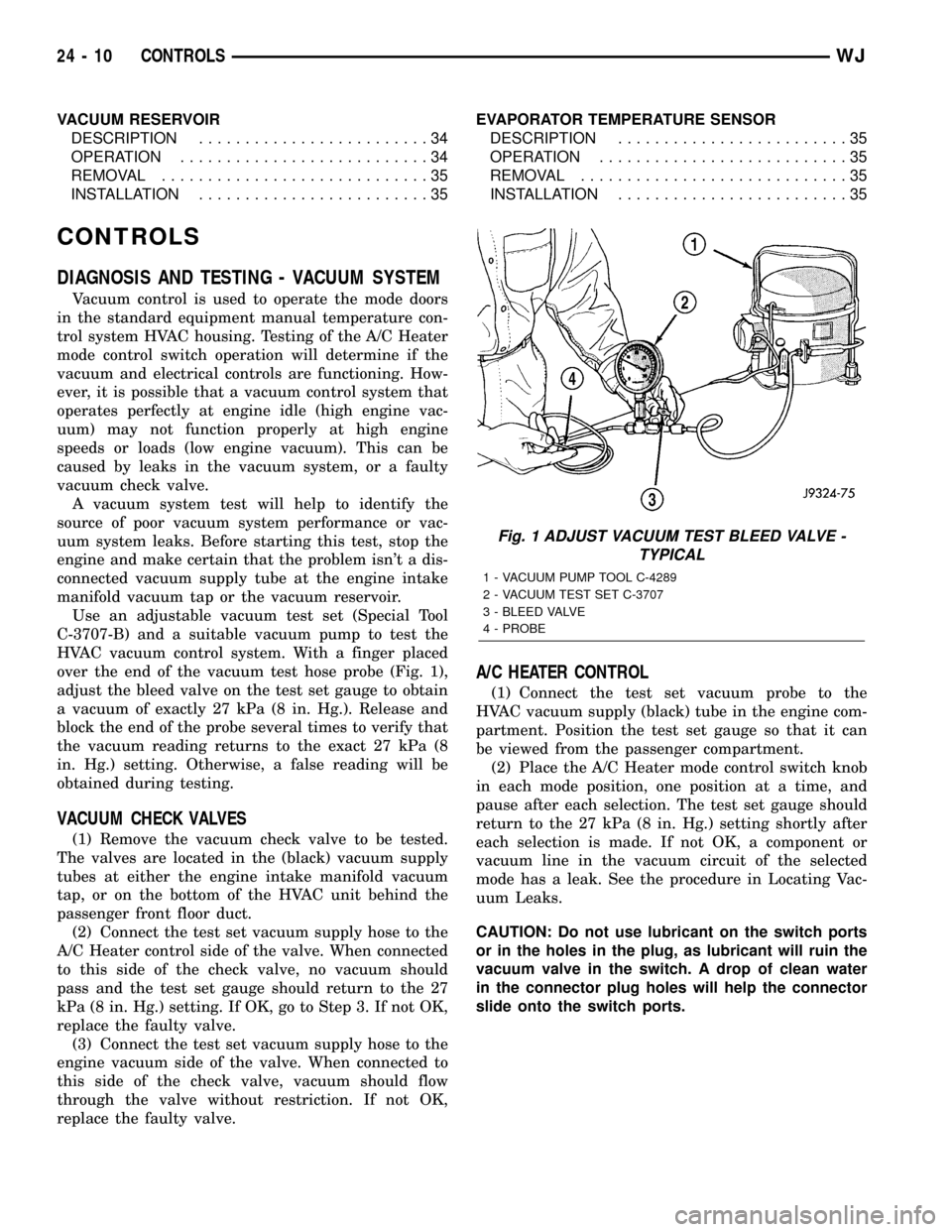
VACUUM RESERVOIR
DESCRIPTION.........................34
OPERATION...........................34
REMOVAL.............................35
INSTALLATION.........................35EVAPORATOR TEMPERATURE SENSOR
DESCRIPTION.........................35
OPERATION...........................35
REMOVAL.............................35
INSTALLATION.........................35
CONTROLS
DIAGNOSIS AND TESTING - VACUUM SYSTEM
Vacuum control is used to operate the mode doors
in the standard equipment manual temperature con-
trol system HVAC housing. Testing of the A/C Heater
mode control switch operation will determine if the
vacuum and electrical controls are functioning. How-
ever, it is possible that a vacuum control system that
operates perfectly at engine idle (high engine vac-
uum) may not function properly at high engine
speeds or loads (low engine vacuum). This can be
caused by leaks in the vacuum system, or a faulty
vacuum check valve.
A vacuum system test will help to identify the
source of poor vacuum system performance or vac-
uum system leaks. Before starting this test, stop the
engine and make certain that the problem isn't a dis-
connected vacuum supply tube at the engine intake
manifold vacuum tap or the vacuum reservoir.
Use an adjustable vacuum test set (Special Tool
C-3707-B) and a suitable vacuum pump to test the
HVAC vacuum control system. With a finger placed
over the end of the vacuum test hose probe (Fig. 1),
adjust the bleed valve on the test set gauge to obtain
a vacuum of exactly 27 kPa (8 in. Hg.). Release and
block the end of the probe several times to verify that
the vacuum reading returns to the exact 27 kPa (8
in. Hg.) setting. Otherwise, a false reading will be
obtained during testing.
VACUUM CHECK VALVES
(1) Remove the vacuum check valve to be tested.
The valves are located in the (black) vacuum supply
tubes at either the engine intake manifold vacuum
tap, or on the bottom of the HVAC unit behind the
passenger front floor duct.
(2) Connect the test set vacuum supply hose to the
A/C Heater control side of the valve. When connected
to this side of the check valve, no vacuum should
pass and the test set gauge should return to the 27
kPa (8 in. Hg.) setting. If OK, go to Step 3. If not OK,
replace the faulty valve.
(3) Connect the test set vacuum supply hose to the
engine vacuum side of the valve. When connected to
this side of the check valve, vacuum should flow
through the valve without restriction. If not OK,
replace the faulty valve.
A/C HEATER CONTROL
(1) Connect the test set vacuum probe to the
HVAC vacuum supply (black) tube in the engine com-
partment. Position the test set gauge so that it can
be viewed from the passenger compartment.
(2) Place the A/C Heater mode control switch knob
in each mode position, one position at a time, and
pause after each selection. The test set gauge should
return to the 27 kPa (8 in. Hg.) setting shortly after
each selection is made. If not OK, a component or
vacuum line in the vacuum circuit of the selected
mode has a leak. See the procedure in Locating Vac-
uum Leaks.
CAUTION: Do not use lubricant on the switch ports
or in the holes in the plug, as lubricant will ruin the
vacuum valve in the switch. A drop of clean water
in the connector plug holes will help the connector
slide onto the switch ports.
Fig. 1 ADJUST VACUUM TEST BLEED VALVE -
TYPICAL
1 - VACUUM PUMP TOOL C-4289
2 - VACUUM TEST SET C-3707
3 - BLEED VALVE
4 - PROBE
24 - 10 CONTROLSWJ
Page 2088 of 2199
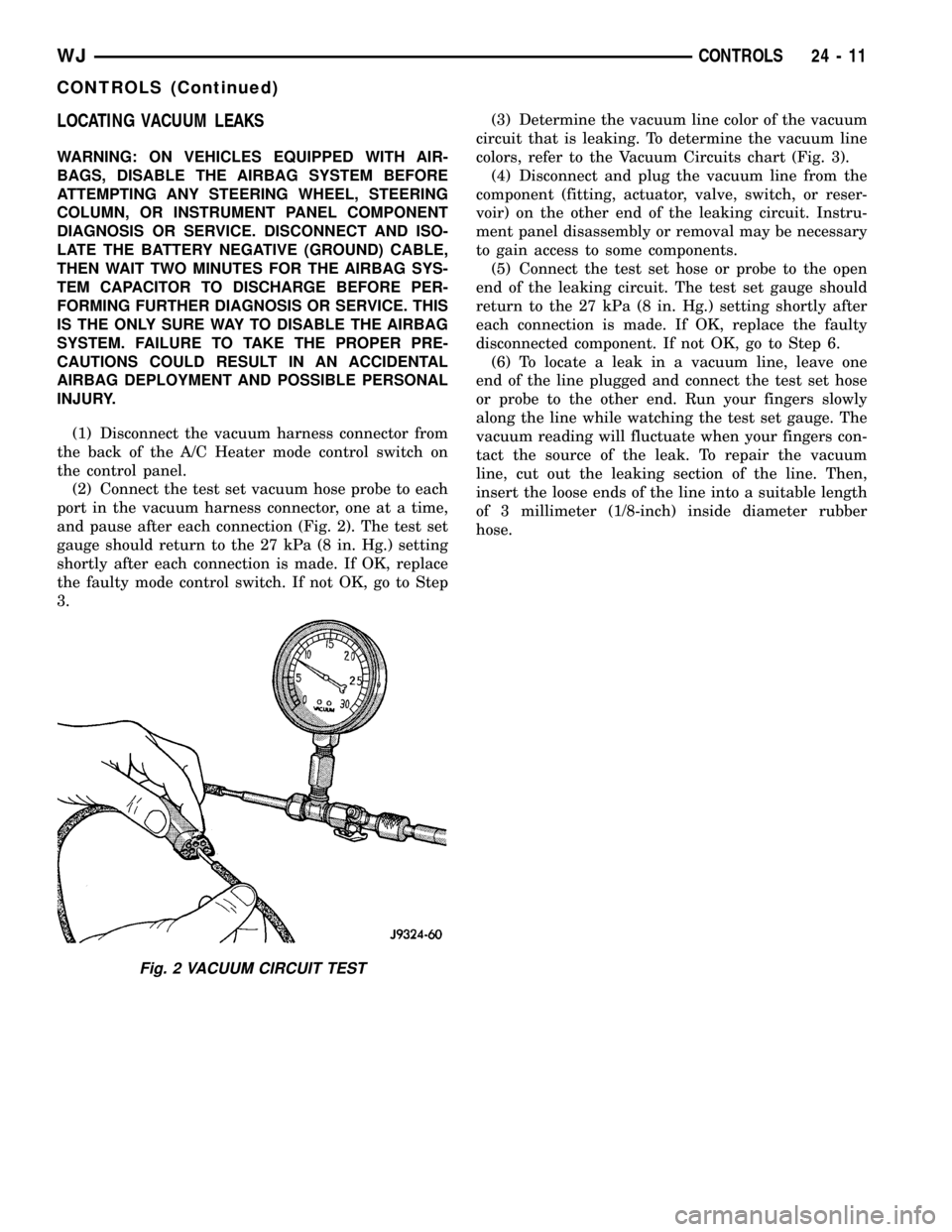
LOCATING VACUUM LEAKS
WARNING: ON VEHICLES EQUIPPED WITH AIR-
BAGS, DISABLE THE AIRBAG SYSTEM BEFORE
ATTEMPTING ANY STEERING WHEEL, STEERING
COLUMN, OR INSTRUMENT PANEL COMPONENT
DIAGNOSIS OR SERVICE. DISCONNECT AND ISO-
LATE THE BATTERY NEGATIVE (GROUND) CABLE,
THEN WAIT TWO MINUTES FOR THE AIRBAG SYS-
TEM CAPACITOR TO DISCHARGE BEFORE PER-
FORMING FURTHER DIAGNOSIS OR SERVICE. THIS
IS THE ONLY SURE WAY TO DISABLE THE AIRBAG
SYSTEM. FAILURE TO TAKE THE PROPER PRE-
CAUTIONS COULD RESULT IN AN ACCIDENTAL
AIRBAG DEPLOYMENT AND POSSIBLE PERSONAL
INJURY.
(1) Disconnect the vacuum harness connector from
the back of the A/C Heater mode control switch on
the control panel.
(2) Connect the test set vacuum hose probe to each
port in the vacuum harness connector, one at a time,
and pause after each connection (Fig. 2). The test set
gauge should return to the 27 kPa (8 in. Hg.) setting
shortly after each connection is made. If OK, replace
the faulty mode control switch. If not OK, go to Step
3.(3) Determine the vacuum line color of the vacuum
circuit that is leaking. To determine the vacuum line
colors, refer to the Vacuum Circuits chart (Fig. 3).
(4) Disconnect and plug the vacuum line from the
component (fitting, actuator, valve, switch, or reser-
voir) on the other end of the leaking circuit. Instru-
ment panel disassembly or removal may be necessary
to gain access to some components.
(5) Connect the test set hose or probe to the open
end of the leaking circuit. The test set gauge should
return to the 27 kPa (8 in. Hg.) setting shortly after
each connection is made. If OK, replace the faulty
disconnected component. If not OK, go to Step 6.
(6) To locate a leak in a vacuum line, leave one
end of the line plugged and connect the test set hose
or probe to the other end. Run your fingers slowly
along the line while watching the test set gauge. The
vacuum reading will fluctuate when your fingers con-
tact the source of the leak. To repair the vacuum
line, cut out the leaking section of the line. Then,
insert the loose ends of the line into a suitable length
of 3 millimeter (1/8-inch) inside diameter rubber
hose.
Fig. 2 VACUUM CIRCUIT TEST
WJCONTROLS 24 - 11
CONTROLS (Continued)
Page 2092 of 2199
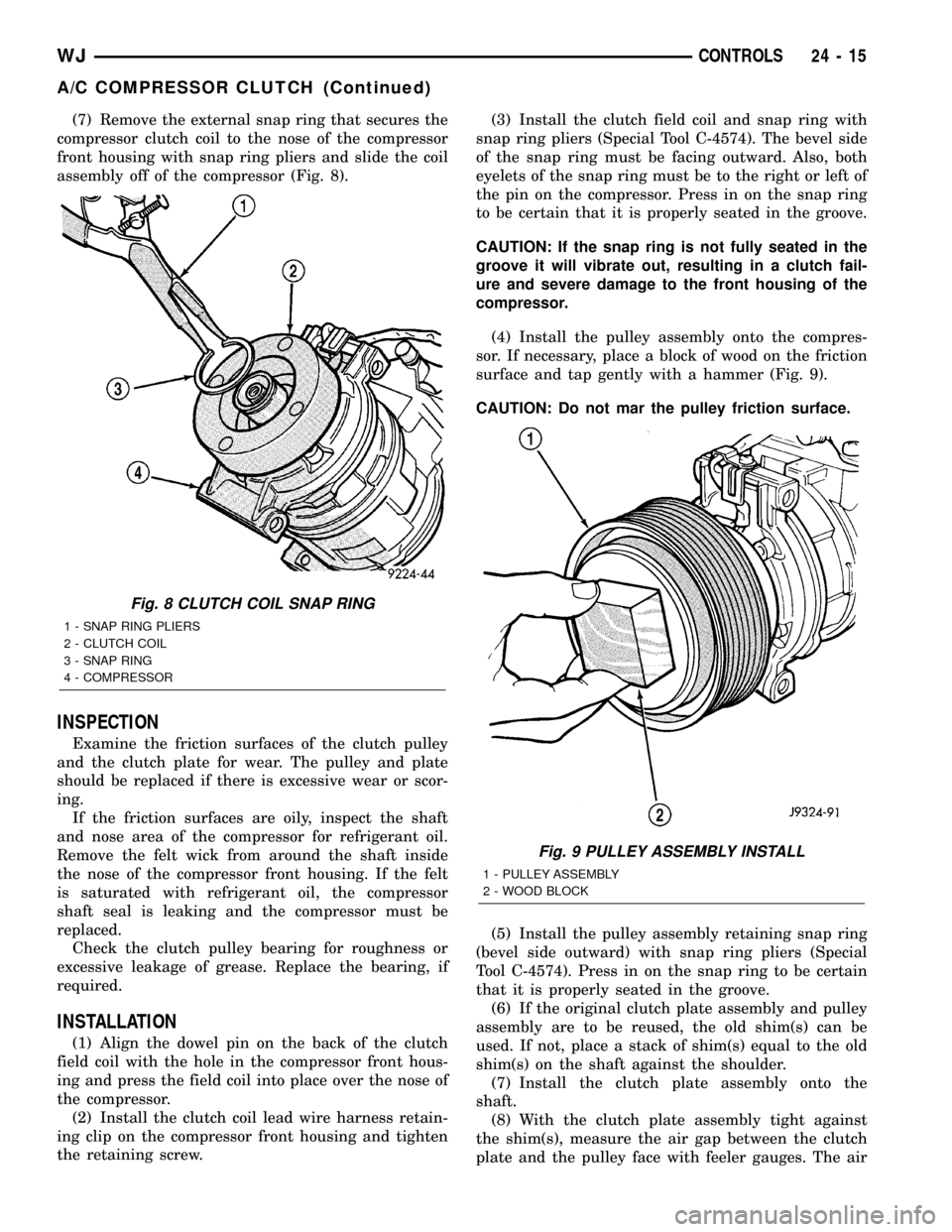
(7) Remove the external snap ring that secures the
compressor clutch coil to the nose of the compressor
front housing with snap ring pliers and slide the coil
assembly off of the compressor (Fig. 8).
INSPECTION
Examine the friction surfaces of the clutch pulley
and the clutch plate for wear. The pulley and plate
should be replaced if there is excessive wear or scor-
ing.
If the friction surfaces are oily, inspect the shaft
and nose area of the compressor for refrigerant oil.
Remove the felt wick from around the shaft inside
the nose of the compressor front housing. If the felt
is saturated with refrigerant oil, the compressor
shaft seal is leaking and the compressor must be
replaced.
Check the clutch pulley bearing for roughness or
excessive leakage of grease. Replace the bearing, if
required.
INSTALLATION
(1) Align the dowel pin on the back of the clutch
field coil with the hole in the compressor front hous-
ing and press the field coil into place over the nose of
the compressor.
(2) Install the clutch coil lead wire harness retain-
ing clip on the compressor front housing and tighten
the retaining screw.(3) Install the clutch field coil and snap ring with
snap ring pliers (Special Tool C-4574). The bevel side
of the snap ring must be facing outward. Also, both
eyelets of the snap ring must be to the right or left of
the pin on the compressor. Press in on the snap ring
to be certain that it is properly seated in the groove.
CAUTION: If the snap ring is not fully seated in the
groove it will vibrate out, resulting in a clutch fail-
ure and severe damage to the front housing of the
compressor.
(4) Install the pulley assembly onto the compres-
sor. If necessary, place a block of wood on the friction
surface and tap gently with a hammer (Fig. 9).
CAUTION: Do not mar the pulley friction surface.
(5) Install the pulley assembly retaining snap ring
(bevel side outward) with snap ring pliers (Special
Tool C-4574). Press in on the snap ring to be certain
that it is properly seated in the groove.
(6) If the original clutch plate assembly and pulley
assembly are to be reused, the old shim(s) can be
used. If not, place a stack of shim(s) equal to the old
shim(s) on the shaft against the shoulder.
(7) Install the clutch plate assembly onto the
shaft.
(8) With the clutch plate assembly tight against
the shim(s), measure the air gap between the clutch
plate and the pulley face with feeler gauges. The air
Fig. 8 CLUTCH COIL SNAP RING
1 - SNAP RING PLIERS
2 - CLUTCH COIL
3 - SNAP RING
4 - COMPRESSOR
Fig. 9 PULLEY ASSEMBLY INSTALL
1 - PULLEY ASSEMBLY
2 - WOOD BLOCK
WJCONTROLS 24 - 15
A/C COMPRESSOR CLUTCH (Continued)