fuse block JEEP GRAND CHEROKEE 2003 WJ / 2.G User Guide
[x] Cancel search | Manufacturer: JEEP, Model Year: 2003, Model line: GRAND CHEROKEE, Model: JEEP GRAND CHEROKEE 2003 WJ / 2.GPages: 2199, PDF Size: 76.01 MB
Page 349 of 2199
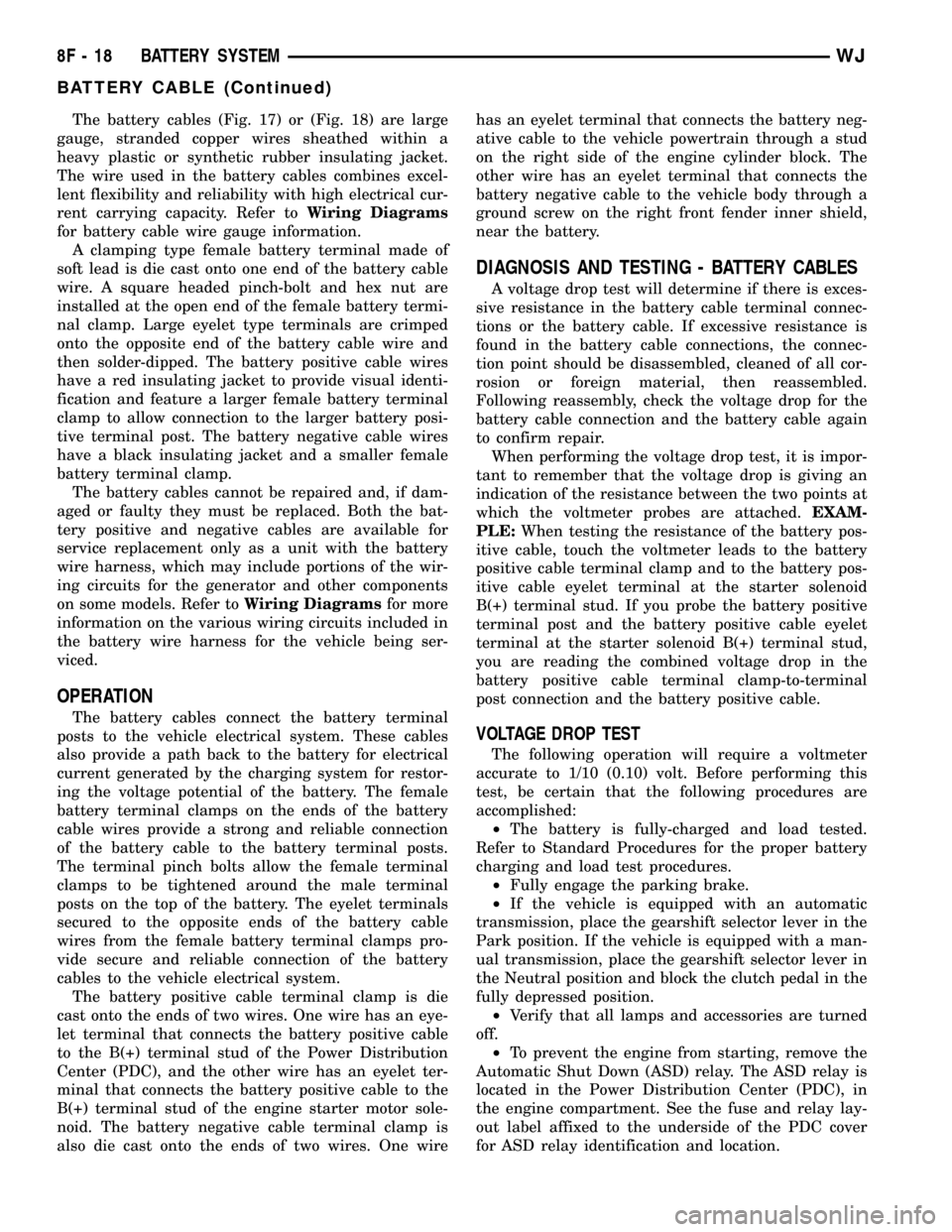
The battery cables (Fig. 17) or (Fig. 18) are large
gauge, stranded copper wires sheathed within a
heavy plastic or synthetic rubber insulating jacket.
The wire used in the battery cables combines excel-
lent flexibility and reliability with high electrical cur-
rent carrying capacity. Refer toWiring Diagrams
for battery cable wire gauge information.
A clamping type female battery terminal made of
soft lead is die cast onto one end of the battery cable
wire. A square headed pinch-bolt and hex nut are
installed at the open end of the female battery termi-
nal clamp. Large eyelet type terminals are crimped
onto the opposite end of the battery cable wire and
then solder-dipped. The battery positive cable wires
have a red insulating jacket to provide visual identi-
fication and feature a larger female battery terminal
clamp to allow connection to the larger battery posi-
tive terminal post. The battery negative cable wires
have a black insulating jacket and a smaller female
battery terminal clamp.
The battery cables cannot be repaired and, if dam-
aged or faulty they must be replaced. Both the bat-
tery positive and negative cables are available for
service replacement only as a unit with the battery
wire harness, which may include portions of the wir-
ing circuits for the generator and other components
on some models. Refer toWiring Diagramsfor more
information on the various wiring circuits included in
the battery wire harness for the vehicle being ser-
viced.
OPERATION
The battery cables connect the battery terminal
posts to the vehicle electrical system. These cables
also provide a path back to the battery for electrical
current generated by the charging system for restor-
ing the voltage potential of the battery. The female
battery terminal clamps on the ends of the battery
cable wires provide a strong and reliable connection
of the battery cable to the battery terminal posts.
The terminal pinch bolts allow the female terminal
clamps to be tightened around the male terminal
posts on the top of the battery. The eyelet terminals
secured to the opposite ends of the battery cable
wires from the female battery terminal clamps pro-
vide secure and reliable connection of the battery
cables to the vehicle electrical system.
The battery positive cable terminal clamp is die
cast onto the ends of two wires. One wire has an eye-
let terminal that connects the battery positive cable
to the B(+) terminal stud of the Power Distribution
Center (PDC), and the other wire has an eyelet ter-
minal that connects the battery positive cable to the
B(+) terminal stud of the engine starter motor sole-
noid. The battery negative cable terminal clamp is
also die cast onto the ends of two wires. One wirehas an eyelet terminal that connects the battery neg-
ative cable to the vehicle powertrain through a stud
on the right side of the engine cylinder block. The
other wire has an eyelet terminal that connects the
battery negative cable to the vehicle body through a
ground screw on the right front fender inner shield,
near the battery.
DIAGNOSIS AND TESTING - BATTERY CABLES
A voltage drop test will determine if there is exces-
sive resistance in the battery cable terminal connec-
tions or the battery cable. If excessive resistance is
found in the battery cable connections, the connec-
tion point should be disassembled, cleaned of all cor-
rosion or foreign material, then reassembled.
Following reassembly, check the voltage drop for the
battery cable connection and the battery cable again
to confirm repair.
When performing the voltage drop test, it is impor-
tant to remember that the voltage drop is giving an
indication of the resistance between the two points at
which the voltmeter probes are attached.EXAM-
PLE:When testing the resistance of the battery pos-
itive cable, touch the voltmeter leads to the battery
positive cable terminal clamp and to the battery pos-
itive cable eyelet terminal at the starter solenoid
B(+) terminal stud. If you probe the battery positive
terminal post and the battery positive cable eyelet
terminal at the starter solenoid B(+) terminal stud,
you are reading the combined voltage drop in the
battery positive cable terminal clamp-to-terminal
post connection and the battery positive cable.
VOLTAGE DROP TEST
The following operation will require a voltmeter
accurate to 1/10 (0.10) volt. Before performing this
test, be certain that the following procedures are
accomplished:
²The battery is fully-charged and load tested.
Refer to Standard Procedures for the proper battery
charging and load test procedures.
²Fully engage the parking brake.
²If the vehicle is equipped with an automatic
transmission, place the gearshift selector lever in the
Park position. If the vehicle is equipped with a man-
ual transmission, place the gearshift selector lever in
the Neutral position and block the clutch pedal in the
fully depressed position.
²Verify that all lamps and accessories are turned
off.
²To prevent the engine from starting, remove the
Automatic Shut Down (ASD) relay. The ASD relay is
located in the Power Distribution Center (PDC), in
the engine compartment. See the fuse and relay lay-
out label affixed to the underside of the PDC cover
for ASD relay identification and location.
8F - 18 BATTERY SYSTEMWJ
BATTERY CABLE (Continued)
Page 356 of 2199
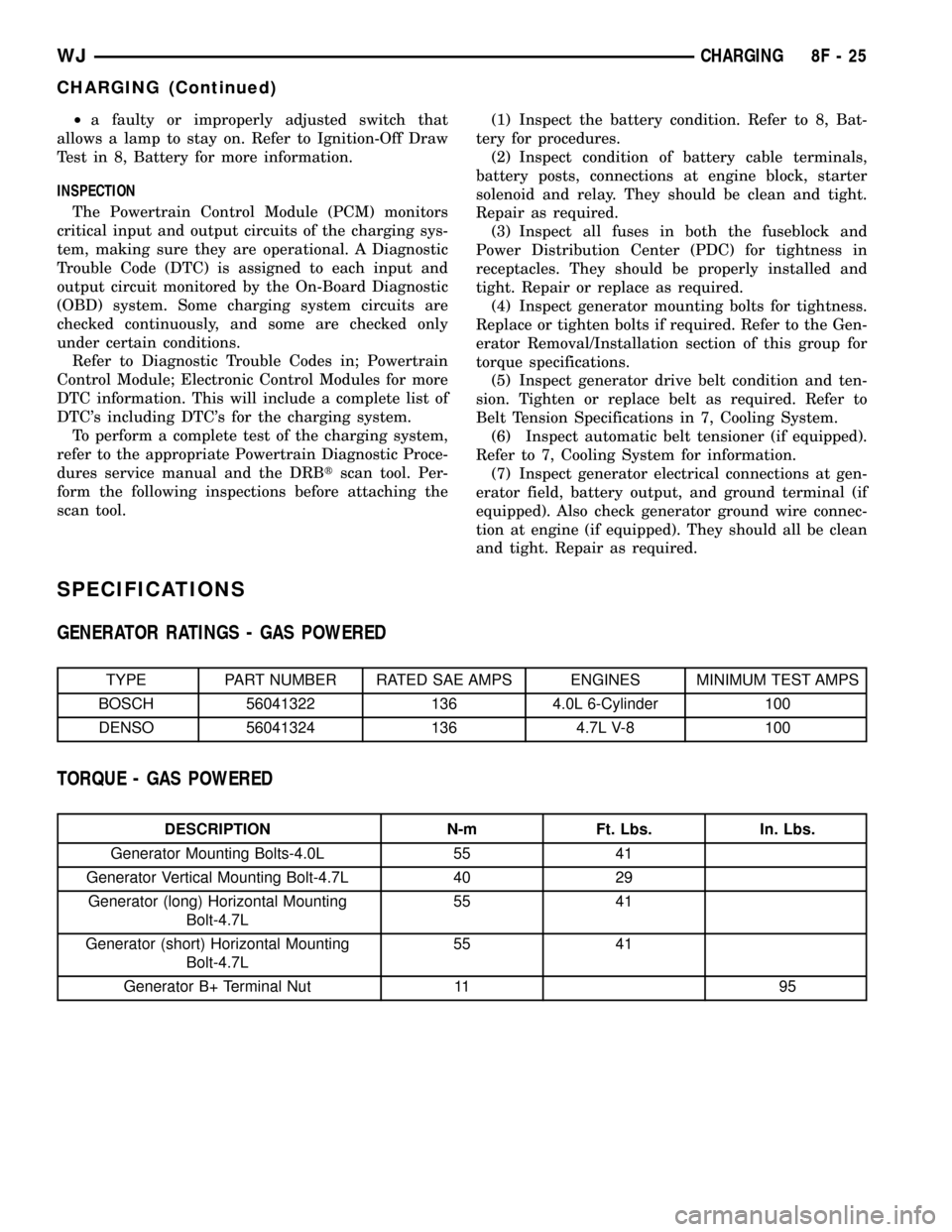
²a faulty or improperly adjusted switch that
allows a lamp to stay on. Refer to Ignition-Off Draw
Test in 8, Battery for more information.
INSPECTION
The Powertrain Control Module (PCM) monitors
critical input and output circuits of the charging sys-
tem, making sure they are operational. A Diagnostic
Trouble Code (DTC) is assigned to each input and
output circuit monitored by the On-Board Diagnostic
(OBD) system. Some charging system circuits are
checked continuously, and some are checked only
under certain conditions.
Refer to Diagnostic Trouble Codes in; Powertrain
Control Module; Electronic Control Modules for more
DTC information. This will include a complete list of
DTC's including DTC's for the charging system.
To perform a complete test of the charging system,
refer to the appropriate Powertrain Diagnostic Proce-
dures service manual and the DRBtscan tool. Per-
form the following inspections before attaching the
scan tool.(1) Inspect the battery condition. Refer to 8, Bat-
tery for procedures.
(2) Inspect condition of battery cable terminals,
battery posts, connections at engine block, starter
solenoid and relay. They should be clean and tight.
Repair as required.
(3) Inspect all fuses in both the fuseblock and
Power Distribution Center (PDC) for tightness in
receptacles. They should be properly installed and
tight. Repair or replace as required.
(4) Inspect generator mounting bolts for tightness.
Replace or tighten bolts if required. Refer to the Gen-
erator Removal/Installation section of this group for
torque specifications.
(5) Inspect generator drive belt condition and ten-
sion. Tighten or replace belt as required. Refer to
Belt Tension Specifications in 7, Cooling System.
(6) Inspect automatic belt tensioner (if equipped).
Refer to 7, Cooling System for information.
(7) Inspect generator electrical connections at gen-
erator field, battery output, and ground terminal (if
equipped). Also check generator ground wire connec-
tion at engine (if equipped). They should all be clean
and tight. Repair as required.
SPECIFICATIONS
GENERATOR RATINGS - GAS POWERED
TYPE PART NUMBER RATED SAE AMPS ENGINES MINIMUM TEST AMPS
BOSCH 56041322 136 4.0L 6-Cylinder 100
DENSO 56041324 136 4.7L V-8 100
TORQUE - GAS POWERED
DESCRIPTION N-m Ft. Lbs. In. Lbs.
Generator Mounting Bolts-4.0L 55 41
Generator Vertical Mounting Bolt-4.7L 40 29
Generator (long) Horizontal Mounting
Bolt-4.7L55 41
Generator (short) Horizontal Mounting
Bolt-4.7L55 41
Generator B+ Terminal Nut 11 95
WJCHARGING 8F - 25
CHARGING (Continued)
Page 376 of 2199
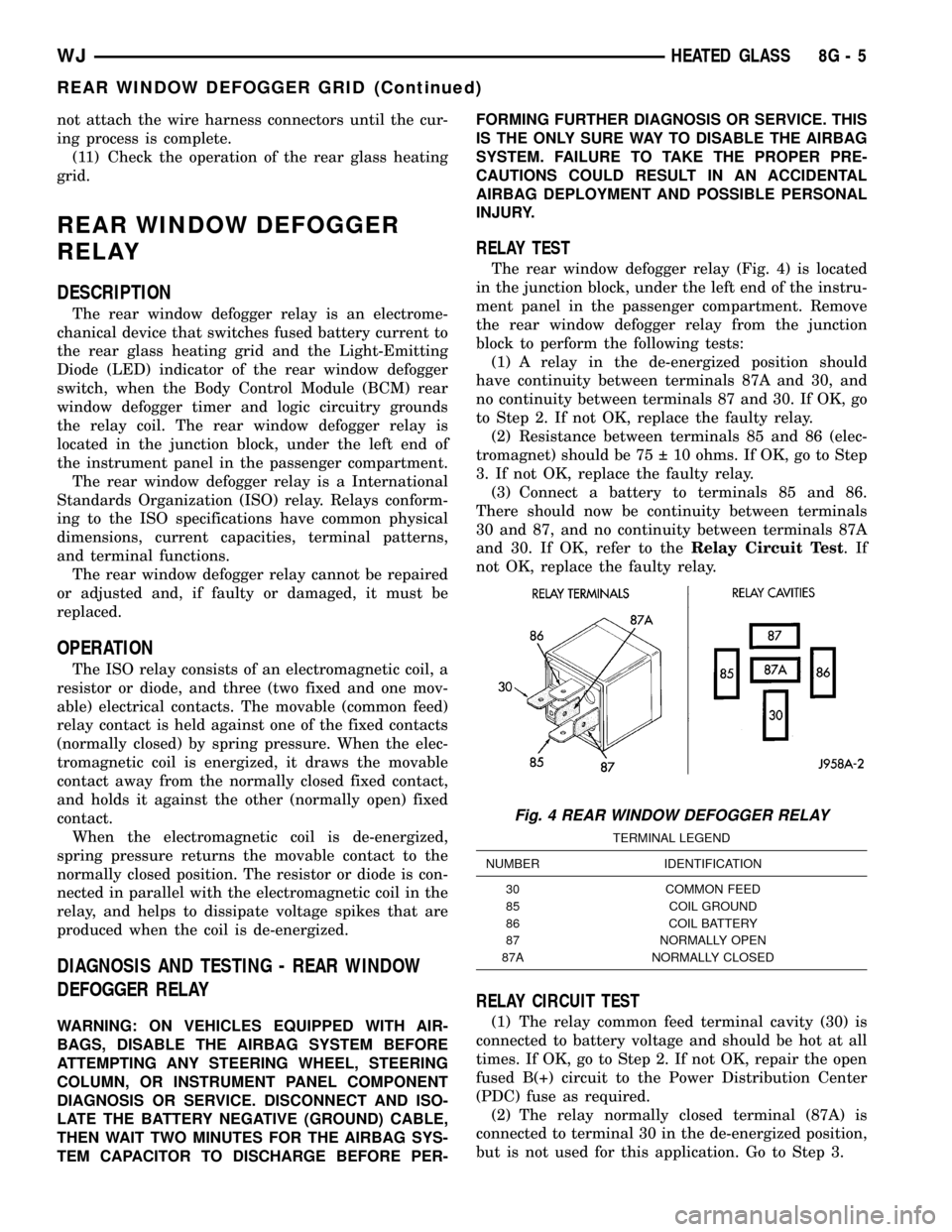
not attach the wire harness connectors until the cur-
ing process is complete.
(11) Check the operation of the rear glass heating
grid.
REAR WINDOW DEFOGGER
RELAY
DESCRIPTION
The rear window defogger relay is an electrome-
chanical device that switches fused battery current to
the rear glass heating grid and the Light-Emitting
Diode (LED) indicator of the rear window defogger
switch, when the Body Control Module (BCM) rear
window defogger timer and logic circuitry grounds
the relay coil. The rear window defogger relay is
located in the junction block, under the left end of
the instrument panel in the passenger compartment.
The rear window defogger relay is a International
Standards Organization (ISO) relay. Relays conform-
ing to the ISO specifications have common physical
dimensions, current capacities, terminal patterns,
and terminal functions.
The rear window defogger relay cannot be repaired
or adjusted and, if faulty or damaged, it must be
replaced.
OPERATION
The ISO relay consists of an electromagnetic coil, a
resistor or diode, and three (two fixed and one mov-
able) electrical contacts. The movable (common feed)
relay contact is held against one of the fixed contacts
(normally closed) by spring pressure. When the elec-
tromagnetic coil is energized, it draws the movable
contact away from the normally closed fixed contact,
and holds it against the other (normally open) fixed
contact.
When the electromagnetic coil is de-energized,
spring pressure returns the movable contact to the
normally closed position. The resistor or diode is con-
nected in parallel with the electromagnetic coil in the
relay, and helps to dissipate voltage spikes that are
produced when the coil is de-energized.
DIAGNOSIS AND TESTING - REAR WINDOW
DEFOGGER RELAY
WARNING: ON VEHICLES EQUIPPED WITH AIR-
BAGS, DISABLE THE AIRBAG SYSTEM BEFORE
ATTEMPTING ANY STEERING WHEEL, STEERING
COLUMN, OR INSTRUMENT PANEL COMPONENT
DIAGNOSIS OR SERVICE. DISCONNECT AND ISO-
LATE THE BATTERY NEGATIVE (GROUND) CABLE,
THEN WAIT TWO MINUTES FOR THE AIRBAG SYS-
TEM CAPACITOR TO DISCHARGE BEFORE PER-FORMING FURTHER DIAGNOSIS OR SERVICE. THIS
IS THE ONLY SURE WAY TO DISABLE THE AIRBAG
SYSTEM. FAILURE TO TAKE THE PROPER PRE-
CAUTIONS COULD RESULT IN AN ACCIDENTAL
AIRBAG DEPLOYMENT AND POSSIBLE PERSONAL
INJURY.
RELAY TEST
The rear window defogger relay (Fig. 4) is located
in the junction block, under the left end of the instru-
ment panel in the passenger compartment. Remove
the rear window defogger relay from the junction
block to perform the following tests:
(1) A relay in the de-energized position should
have continuity between terminals 87A and 30, and
no continuity between terminals 87 and 30. If OK, go
to Step 2. If not OK, replace the faulty relay.
(2) Resistance between terminals 85 and 86 (elec-
tromagnet) should be 75 10 ohms. If OK, go to Step
3. If not OK, replace the faulty relay.
(3) Connect a battery to terminals 85 and 86.
There should now be continuity between terminals
30 and 87, and no continuity between terminals 87A
and 30. If OK, refer to theRelay Circuit Test.If
not OK, replace the faulty relay.
RELAY CIRCUIT TEST
(1) The relay common feed terminal cavity (30) is
connected to battery voltage and should be hot at all
times. If OK, go to Step 2. If not OK, repair the open
fused B(+) circuit to the Power Distribution Center
(PDC) fuse as required.
(2) The relay normally closed terminal (87A) is
connected to terminal 30 in the de-energized position,
but is not used for this application. Go to Step 3.
Fig. 4 REAR WINDOW DEFOGGER RELAY
TERMINAL LEGEND
NUMBER IDENTIFICATION
30 COMMON FEED
85 COIL GROUND
86 COIL BATTERY
87 NORMALLY OPEN
87A NORMALLY CLOSED
WJHEATED GLASS 8G - 5
REAR WINDOW DEFOGGER GRID (Continued)
Page 377 of 2199
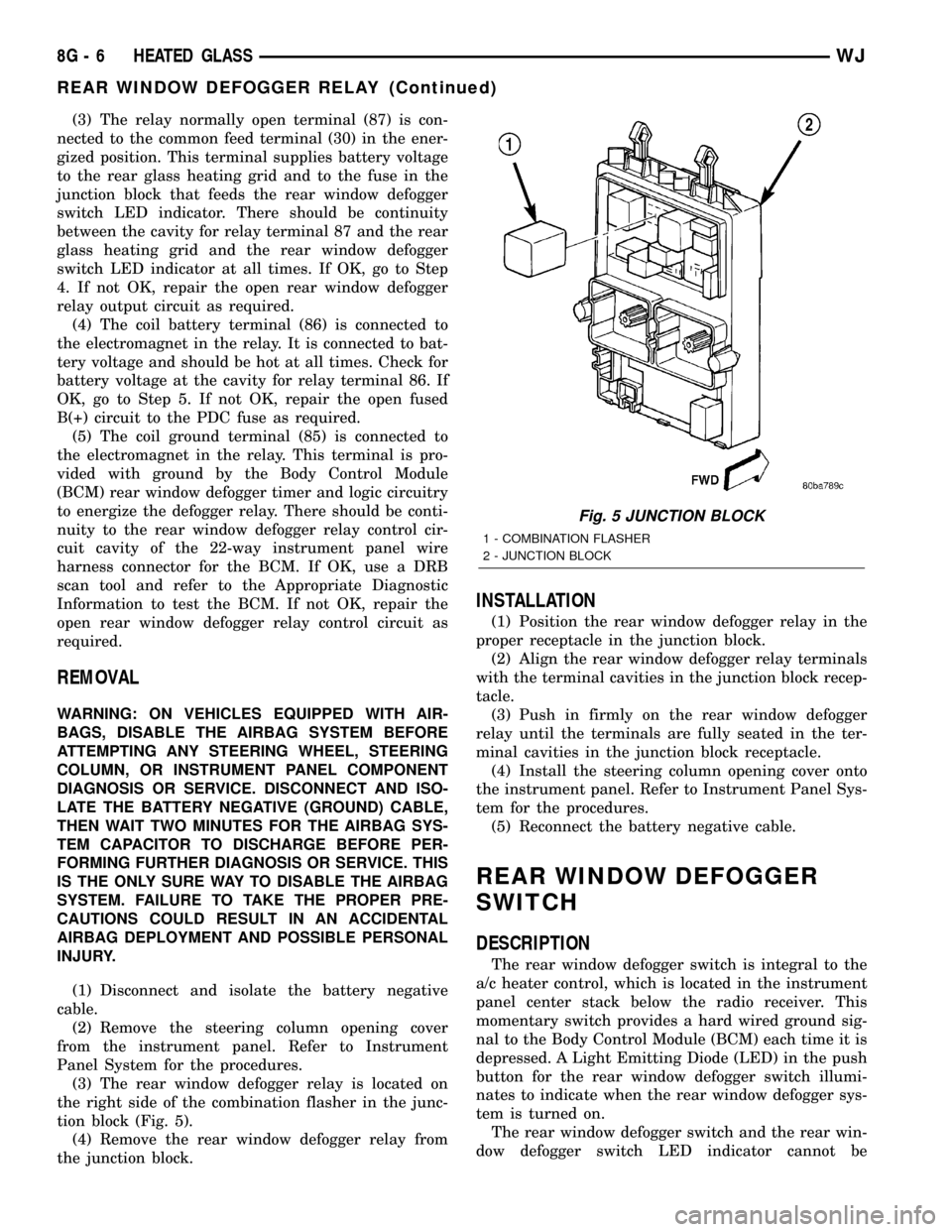
(3) The relay normally open terminal (87) is con-
nected to the common feed terminal (30) in the ener-
gized position. This terminal supplies battery voltage
to the rear glass heating grid and to the fuse in the
junction block that feeds the rear window defogger
switch LED indicator. There should be continuity
between the cavity for relay terminal 87 and the rear
glass heating grid and the rear window defogger
switch LED indicator at all times. If OK, go to Step
4. If not OK, repair the open rear window defogger
relay output circuit as required.
(4) The coil battery terminal (86) is connected to
the electromagnet in the relay. It is connected to bat-
tery voltage and should be hot at all times. Check for
battery voltage at the cavity for relay terminal 86. If
OK, go to Step 5. If not OK, repair the open fused
B(+) circuit to the PDC fuse as required.
(5) The coil ground terminal (85) is connected to
the electromagnet in the relay. This terminal is pro-
vided with ground by the Body Control Module
(BCM) rear window defogger timer and logic circuitry
to energize the defogger relay. There should be conti-
nuity to the rear window defogger relay control cir-
cuit cavity of the 22-way instrument panel wire
harness connector for the BCM. If OK, use a DRB
scan tool and refer to the Appropriate Diagnostic
Information to test the BCM. If not OK, repair the
open rear window defogger relay control circuit as
required.
REMOVAL
WARNING: ON VEHICLES EQUIPPED WITH AIR-
BAGS, DISABLE THE AIRBAG SYSTEM BEFORE
ATTEMPTING ANY STEERING WHEEL, STEERING
COLUMN, OR INSTRUMENT PANEL COMPONENT
DIAGNOSIS OR SERVICE. DISCONNECT AND ISO-
LATE THE BATTERY NEGATIVE (GROUND) CABLE,
THEN WAIT TWO MINUTES FOR THE AIRBAG SYS-
TEM CAPACITOR TO DISCHARGE BEFORE PER-
FORMING FURTHER DIAGNOSIS OR SERVICE. THIS
IS THE ONLY SURE WAY TO DISABLE THE AIRBAG
SYSTEM. FAILURE TO TAKE THE PROPER PRE-
CAUTIONS COULD RESULT IN AN ACCIDENTAL
AIRBAG DEPLOYMENT AND POSSIBLE PERSONAL
INJURY.
(1) Disconnect and isolate the battery negative
cable.
(2) Remove the steering column opening cover
from the instrument panel. Refer to Instrument
Panel System for the procedures.
(3) The rear window defogger relay is located on
the right side of the combination flasher in the junc-
tion block (Fig. 5).
(4) Remove the rear window defogger relay from
the junction block.
INSTALLATION
(1) Position the rear window defogger relay in the
proper receptacle in the junction block.
(2) Align the rear window defogger relay terminals
with the terminal cavities in the junction block recep-
tacle.
(3) Push in firmly on the rear window defogger
relay until the terminals are fully seated in the ter-
minal cavities in the junction block receptacle.
(4) Install the steering column opening cover onto
the instrument panel. Refer to Instrument Panel Sys-
tem for the procedures.
(5) Reconnect the battery negative cable.
REAR WINDOW DEFOGGER
SWITCH
DESCRIPTION
The rear window defogger switch is integral to the
a/c heater control, which is located in the instrument
panel center stack below the radio receiver. This
momentary switch provides a hard wired ground sig-
nal to the Body Control Module (BCM) each time it is
depressed. A Light Emitting Diode (LED) in the push
button for the rear window defogger switch illumi-
nates to indicate when the rear window defogger sys-
tem is turned on.
The rear window defogger switch and the rear win-
dow defogger switch LED indicator cannot be
Fig. 5 JUNCTION BLOCK
1 - COMBINATION FLASHER
2 - JUNCTION BLOCK
8G - 6 HEATED GLASSWJ
REAR WINDOW DEFOGGER RELAY (Continued)
Page 378 of 2199
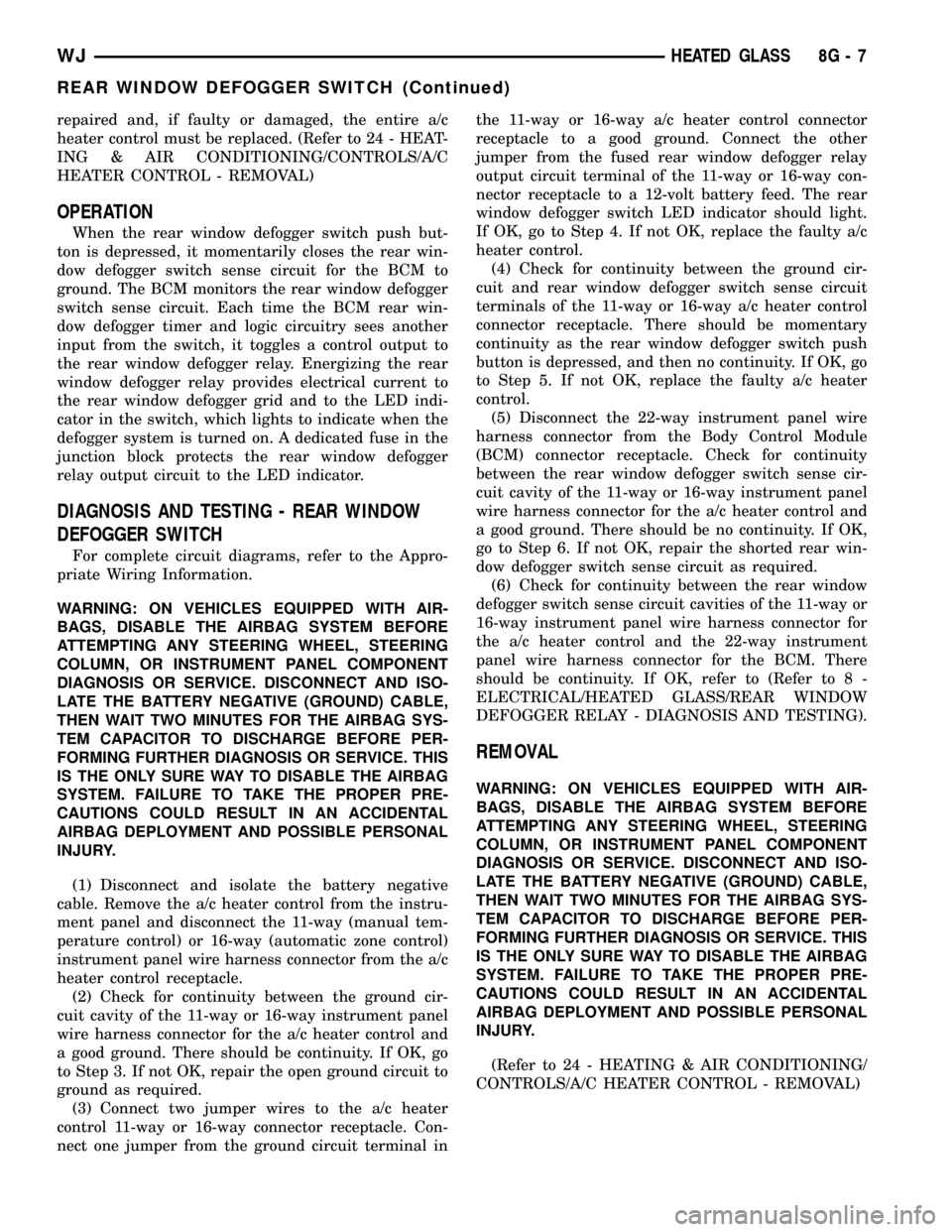
repaired and, if faulty or damaged, the entire a/c
heater control must be replaced. (Refer to 24 - HEAT-
ING & AIR CONDITIONING/CONTROLS/A/C
HEATER CONTROL - REMOVAL)
OPERATION
When the rear window defogger switch push but-
ton is depressed, it momentarily closes the rear win-
dow defogger switch sense circuit for the BCM to
ground. The BCM monitors the rear window defogger
switch sense circuit. Each time the BCM rear win-
dow defogger timer and logic circuitry sees another
input from the switch, it toggles a control output to
the rear window defogger relay. Energizing the rear
window defogger relay provides electrical current to
the rear window defogger grid and to the LED indi-
cator in the switch, which lights to indicate when the
defogger system is turned on. A dedicated fuse in the
junction block protects the rear window defogger
relay output circuit to the LED indicator.
DIAGNOSIS AND TESTING - REAR WINDOW
DEFOGGER SWITCH
For complete circuit diagrams, refer to the Appro-
priate Wiring Information.
WARNING: ON VEHICLES EQUIPPED WITH AIR-
BAGS, DISABLE THE AIRBAG SYSTEM BEFORE
ATTEMPTING ANY STEERING WHEEL, STEERING
COLUMN, OR INSTRUMENT PANEL COMPONENT
DIAGNOSIS OR SERVICE. DISCONNECT AND ISO-
LATE THE BATTERY NEGATIVE (GROUND) CABLE,
THEN WAIT TWO MINUTES FOR THE AIRBAG SYS-
TEM CAPACITOR TO DISCHARGE BEFORE PER-
FORMING FURTHER DIAGNOSIS OR SERVICE. THIS
IS THE ONLY SURE WAY TO DISABLE THE AIRBAG
SYSTEM. FAILURE TO TAKE THE PROPER PRE-
CAUTIONS COULD RESULT IN AN ACCIDENTAL
AIRBAG DEPLOYMENT AND POSSIBLE PERSONAL
INJURY.
(1) Disconnect and isolate the battery negative
cable. Remove the a/c heater control from the instru-
ment panel and disconnect the 11-way (manual tem-
perature control) or 16-way (automatic zone control)
instrument panel wire harness connector from the a/c
heater control receptacle.
(2) Check for continuity between the ground cir-
cuit cavity of the 11-way or 16-way instrument panel
wire harness connector for the a/c heater control and
a good ground. There should be continuity. If OK, go
to Step 3. If not OK, repair the open ground circuit to
ground as required.
(3) Connect two jumper wires to the a/c heater
control 11-way or 16-way connector receptacle. Con-
nect one jumper from the ground circuit terminal inthe 11-way or 16-way a/c heater control connector
receptacle to a good ground. Connect the other
jumper from the fused rear window defogger relay
output circuit terminal of the 11-way or 16-way con-
nector receptacle to a 12-volt battery feed. The rear
window defogger switch LED indicator should light.
If OK, go to Step 4. If not OK, replace the faulty a/c
heater control.
(4) Check for continuity between the ground cir-
cuit and rear window defogger switch sense circuit
terminals of the 11-way or 16-way a/c heater control
connector receptacle. There should be momentary
continuity as the rear window defogger switch push
button is depressed, and then no continuity. If OK, go
to Step 5. If not OK, replace the faulty a/c heater
control.
(5) Disconnect the 22-way instrument panel wire
harness connector from the Body Control Module
(BCM) connector receptacle. Check for continuity
between the rear window defogger switch sense cir-
cuit cavity of the 11-way or 16-way instrument panel
wire harness connector for the a/c heater control and
a good ground. There should be no continuity. If OK,
go to Step 6. If not OK, repair the shorted rear win-
dow defogger switch sense circuit as required.
(6) Check for continuity between the rear window
defogger switch sense circuit cavities of the 11-way or
16-way instrument panel wire harness connector for
the a/c heater control and the 22-way instrument
panel wire harness connector for the BCM. There
should be continuity. If OK, refer to (Refer to 8 -
ELECTRICAL/HEATED GLASS/REAR WINDOW
DEFOGGER RELAY - DIAGNOSIS AND TESTING).
REMOVAL
WARNING: ON VEHICLES EQUIPPED WITH AIR-
BAGS, DISABLE THE AIRBAG SYSTEM BEFORE
ATTEMPTING ANY STEERING WHEEL, STEERING
COLUMN, OR INSTRUMENT PANEL COMPONENT
DIAGNOSIS OR SERVICE. DISCONNECT AND ISO-
LATE THE BATTERY NEGATIVE (GROUND) CABLE,
THEN WAIT TWO MINUTES FOR THE AIRBAG SYS-
TEM CAPACITOR TO DISCHARGE BEFORE PER-
FORMING FURTHER DIAGNOSIS OR SERVICE. THIS
IS THE ONLY SURE WAY TO DISABLE THE AIRBAG
SYSTEM. FAILURE TO TAKE THE PROPER PRE-
CAUTIONS COULD RESULT IN AN ACCIDENTAL
AIRBAG DEPLOYMENT AND POSSIBLE PERSONAL
INJURY.
(Refer to 24 - HEATING & AIR CONDITIONING/
CONTROLS/A/C HEATER CONTROL - REMOVAL)
WJHEATED GLASS 8G - 7
REAR WINDOW DEFOGGER SWITCH (Continued)
Page 380 of 2199
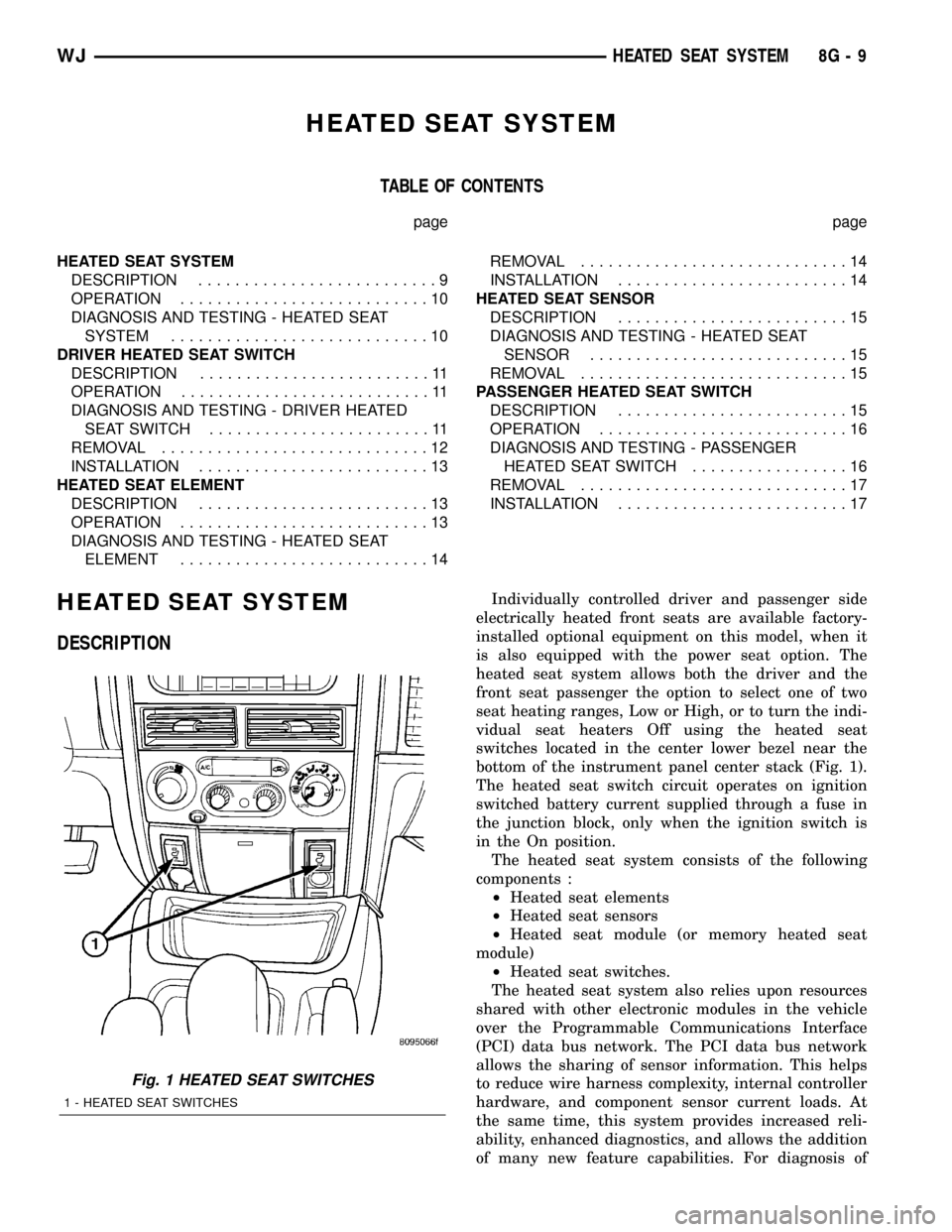
HEATED SEAT SYSTEM
TABLE OF CONTENTS
page page
HEATED SEAT SYSTEM
DESCRIPTION..........................9
OPERATION...........................10
DIAGNOSIS AND TESTING - HEATED SEAT
SYSTEM............................10
DRIVER HEATED SEAT SWITCH
DESCRIPTION.........................11
OPERATION...........................11
DIAGNOSIS AND TESTING - DRIVER HEATED
SEAT SWITCH........................11
REMOVAL.............................12
INSTALLATION.........................13
HEATED SEAT ELEMENT
DESCRIPTION.........................13
OPERATION...........................13
DIAGNOSIS AND TESTING - HEATED SEAT
ELEMENT...........................14REMOVAL.............................14
INSTALLATION.........................14
HEATED SEAT SENSOR
DESCRIPTION.........................15
DIAGNOSIS AND TESTING - HEATED SEAT
SENSOR............................15
REMOVAL.............................15
PASSENGER HEATED SEAT SWITCH
DESCRIPTION.........................15
OPERATION...........................16
DIAGNOSIS AND TESTING - PASSENGER
HEATED SEAT SWITCH.................16
REMOVAL.............................17
INSTALLATION.........................17
HEATED SEAT SYSTEM
DESCRIPTION
Individually controlled driver and passenger side
electrically heated front seats are available factory-
installed optional equipment on this model, when it
is also equipped with the power seat option. The
heated seat system allows both the driver and the
front seat passenger the option to select one of two
seat heating ranges, Low or High, or to turn the indi-
vidual seat heaters Off using the heated seat
switches located in the center lower bezel near the
bottom of the instrument panel center stack (Fig. 1).
The heated seat switch circuit operates on ignition
switched battery current supplied through a fuse in
the junction block, only when the ignition switch is
in the On position.
The heated seat system consists of the following
components :
²Heated seat elements
²Heated seat sensors
²Heated seat module (or memory heated seat
module)
²Heated seat switches.
The heated seat system also relies upon resources
shared with other electronic modules in the vehicle
over the Programmable Communications Interface
(PCI) data bus network. The PCI data bus network
allows the sharing of sensor information. This helps
to reduce wire harness complexity, internal controller
hardware, and component sensor current loads. At
the same time, this system provides increased reli-
ability, enhanced diagnostics, and allows the addition
of many new feature capabilities. For diagnosis of
Fig. 1 HEATED SEAT SWITCHES
1 - HEATED SEAT SWITCHES
WJHEATED SEAT SYSTEM 8G - 9
Page 382 of 2199
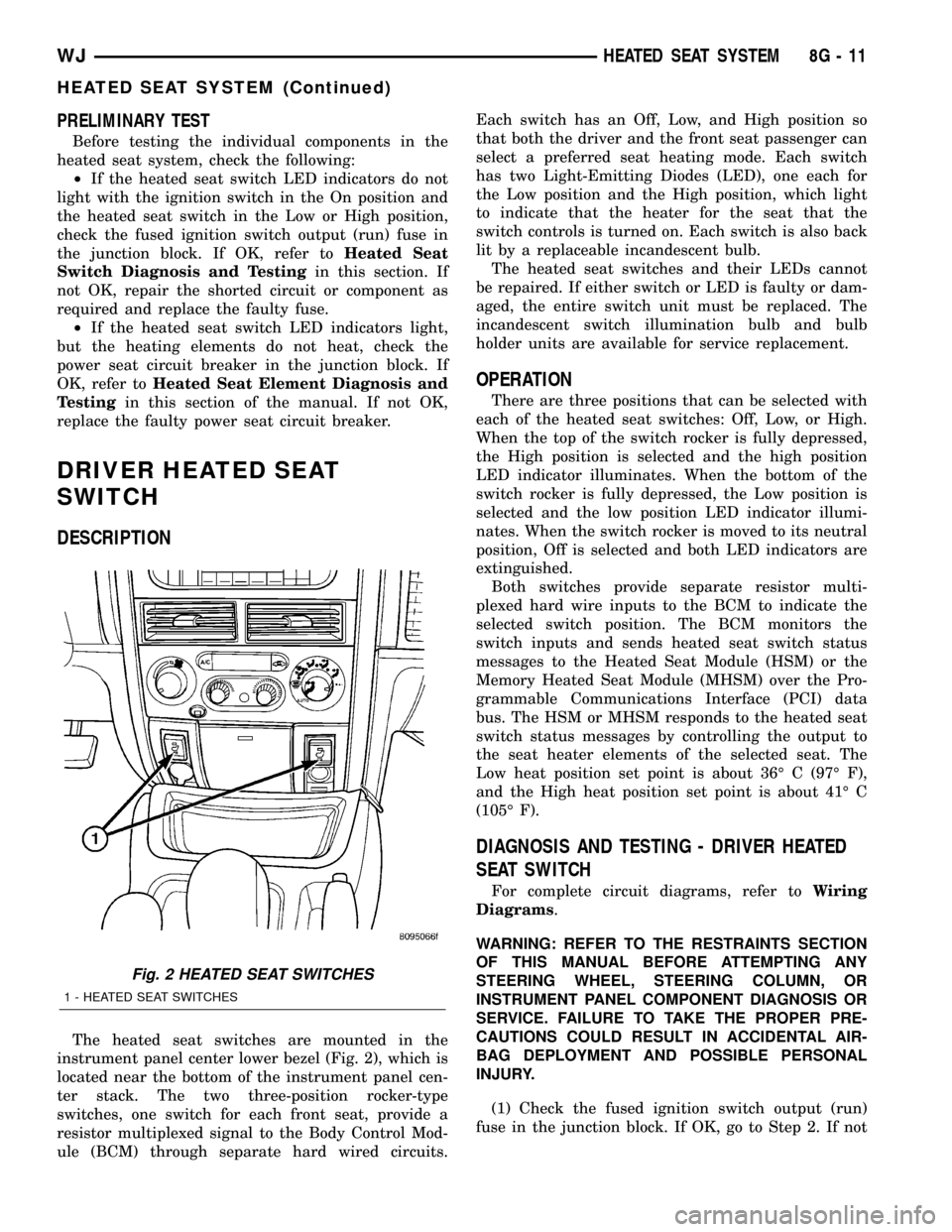
PRELIMINARY TEST
Before testing the individual components in the
heated seat system, check the following:
²If the heated seat switch LED indicators do not
light with the ignition switch in the On position and
the heated seat switch in the Low or High position,
check the fused ignition switch output (run) fuse in
the junction block. If OK, refer toHeated Seat
Switch Diagnosis and Testingin this section. If
not OK, repair the shorted circuit or component as
required and replace the faulty fuse.
²If the heated seat switch LED indicators light,
but the heating elements do not heat, check the
power seat circuit breaker in the junction block. If
OK, refer toHeated Seat Element Diagnosis and
Testingin this section of the manual. If not OK,
replace the faulty power seat circuit breaker.
DRIVER HEATED SEAT
SWITCH
DESCRIPTION
The heated seat switches are mounted in the
instrument panel center lower bezel (Fig. 2), which is
located near the bottom of the instrument panel cen-
ter stack. The two three-position rocker-type
switches, one switch for each front seat, provide a
resistor multiplexed signal to the Body Control Mod-
ule (BCM) through separate hard wired circuits.Each switch has an Off, Low, and High position so
that both the driver and the front seat passenger can
select a preferred seat heating mode. Each switch
has two Light-Emitting Diodes (LED), one each for
the Low position and the High position, which light
to indicate that the heater for the seat that the
switch controls is turned on. Each switch is also back
lit by a replaceable incandescent bulb.
The heated seat switches and their LEDs cannot
be repaired. If either switch or LED is faulty or dam-
aged, the entire switch unit must be replaced. The
incandescent switch illumination bulb and bulb
holder units are available for service replacement.
OPERATION
There are three positions that can be selected with
each of the heated seat switches: Off, Low, or High.
When the top of the switch rocker is fully depressed,
the High position is selected and the high position
LED indicator illuminates. When the bottom of the
switch rocker is fully depressed, the Low position is
selected and the low position LED indicator illumi-
nates. When the switch rocker is moved to its neutral
position, Off is selected and both LED indicators are
extinguished.
Both switches provide separate resistor multi-
plexed hard wire inputs to the BCM to indicate the
selected switch position. The BCM monitors the
switch inputs and sends heated seat switch status
messages to the Heated Seat Module (HSM) or the
Memory Heated Seat Module (MHSM) over the Pro-
grammable Communications Interface (PCI) data
bus. The HSM or MHSM responds to the heated seat
switch status messages by controlling the output to
the seat heater elements of the selected seat. The
Low heat position set point is about 36É C (97É F),
and the High heat position set point is about 41É C
(105É F).
DIAGNOSIS AND TESTING - DRIVER HEATED
SEAT SWITCH
For complete circuit diagrams, refer toWiring
Diagrams.
WARNING: REFER TO THE RESTRAINTS SECTION
OF THIS MANUAL BEFORE ATTEMPTING ANY
STEERING WHEEL, STEERING COLUMN, OR
INSTRUMENT PANEL COMPONENT DIAGNOSIS OR
SERVICE. FAILURE TO TAKE THE PROPER PRE-
CAUTIONS COULD RESULT IN ACCIDENTAL AIR-
BAG DEPLOYMENT AND POSSIBLE PERSONAL
INJURY.
(1) Check the fused ignition switch output (run)
fuse in the junction block. If OK, go to Step 2. If not
Fig. 2 HEATED SEAT SWITCHES
1 - HEATED SEAT SWITCHES
WJHEATED SEAT SYSTEM 8G - 11
HEATED SEAT SYSTEM (Continued)
Page 383 of 2199
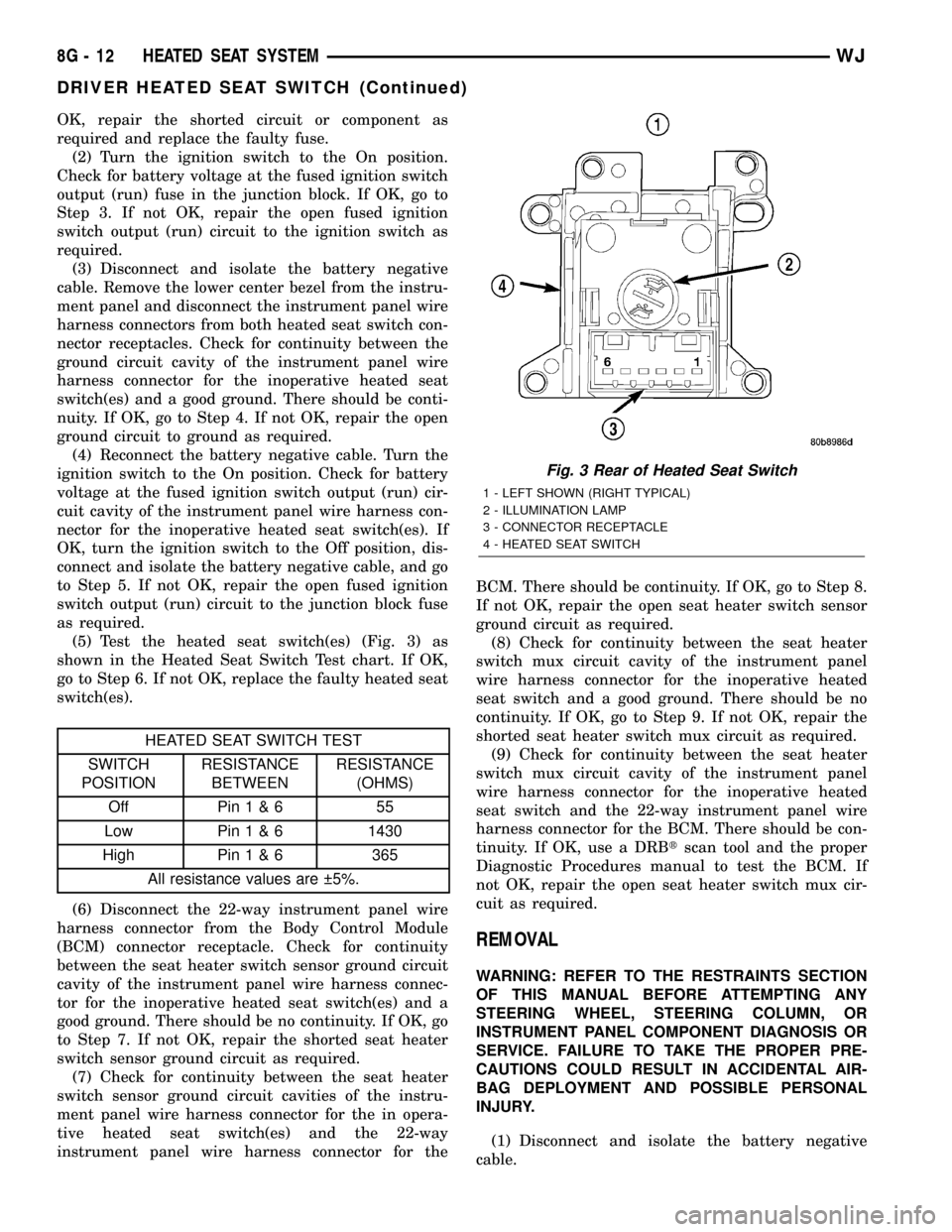
OK, repair the shorted circuit or component as
required and replace the faulty fuse.
(2) Turn the ignition switch to the On position.
Check for battery voltage at the fused ignition switch
output (run) fuse in the junction block. If OK, go to
Step 3. If not OK, repair the open fused ignition
switch output (run) circuit to the ignition switch as
required.
(3) Disconnect and isolate the battery negative
cable. Remove the lower center bezel from the instru-
ment panel and disconnect the instrument panel wire
harness connectors from both heated seat switch con-
nector receptacles. Check for continuity between the
ground circuit cavity of the instrument panel wire
harness connector for the inoperative heated seat
switch(es) and a good ground. There should be conti-
nuity. If OK, go to Step 4. If not OK, repair the open
ground circuit to ground as required.
(4) Reconnect the battery negative cable. Turn the
ignition switch to the On position. Check for battery
voltage at the fused ignition switch output (run) cir-
cuit cavity of the instrument panel wire harness con-
nector for the inoperative heated seat switch(es). If
OK, turn the ignition switch to the Off position, dis-
connect and isolate the battery negative cable, and go
to Step 5. If not OK, repair the open fused ignition
switch output (run) circuit to the junction block fuse
as required.
(5) Test the heated seat switch(es) (Fig. 3) as
shown in the Heated Seat Switch Test chart. If OK,
go to Step 6. If not OK, replace the faulty heated seat
switch(es).
HEATED SEAT SWITCH TEST
SWITCH
POSITIONRESISTANCE
BETWEENRESISTANCE
(OHMS)
Off Pin1&6 55
Low Pin1&61430
High Pin1&6 365
All resistance values are 5%.
(6) Disconnect the 22-way instrument panel wire
harness connector from the Body Control Module
(BCM) connector receptacle. Check for continuity
between the seat heater switch sensor ground circuit
cavity of the instrument panel wire harness connec-
tor for the inoperative heated seat switch(es) and a
good ground. There should be no continuity. If OK, go
to Step 7. If not OK, repair the shorted seat heater
switch sensor ground circuit as required.
(7) Check for continuity between the seat heater
switch sensor ground circuit cavities of the instru-
ment panel wire harness connector for the in opera-
tive heated seat switch(es) and the 22-way
instrument panel wire harness connector for theBCM. There should be continuity. If OK, go to Step 8.
If not OK, repair the open seat heater switch sensor
ground circuit as required.
(8) Check for continuity between the seat heater
switch mux circuit cavity of the instrument panel
wire harness connector for the inoperative heated
seat switch and a good ground. There should be no
continuity. If OK, go to Step 9. If not OK, repair the
shorted seat heater switch mux circuit as required.
(9) Check for continuity between the seat heater
switch mux circuit cavity of the instrument panel
wire harness connector for the inoperative heated
seat switch and the 22-way instrument panel wire
harness connector for the BCM. There should be con-
tinuity. If OK, use a DRBtscan tool and the proper
Diagnostic Procedures manual to test the BCM. If
not OK, repair the open seat heater switch mux cir-
cuit as required.
REMOVAL
WARNING: REFER TO THE RESTRAINTS SECTION
OF THIS MANUAL BEFORE ATTEMPTING ANY
STEERING WHEEL, STEERING COLUMN, OR
INSTRUMENT PANEL COMPONENT DIAGNOSIS OR
SERVICE. FAILURE TO TAKE THE PROPER PRE-
CAUTIONS COULD RESULT IN ACCIDENTAL AIR-
BAG DEPLOYMENT AND POSSIBLE PERSONAL
INJURY.
(1) Disconnect and isolate the battery negative
cable.
Fig. 3 Rear of Heated Seat Switch
1 - LEFT SHOWN (RIGHT TYPICAL)
2 - ILLUMINATION LAMP
3 - CONNECTOR RECEPTACLE
4 - HEATED SEAT SWITCH
8G - 12 HEATED SEAT SYSTEMWJ
DRIVER HEATED SEAT SWITCH (Continued)
Page 387 of 2199
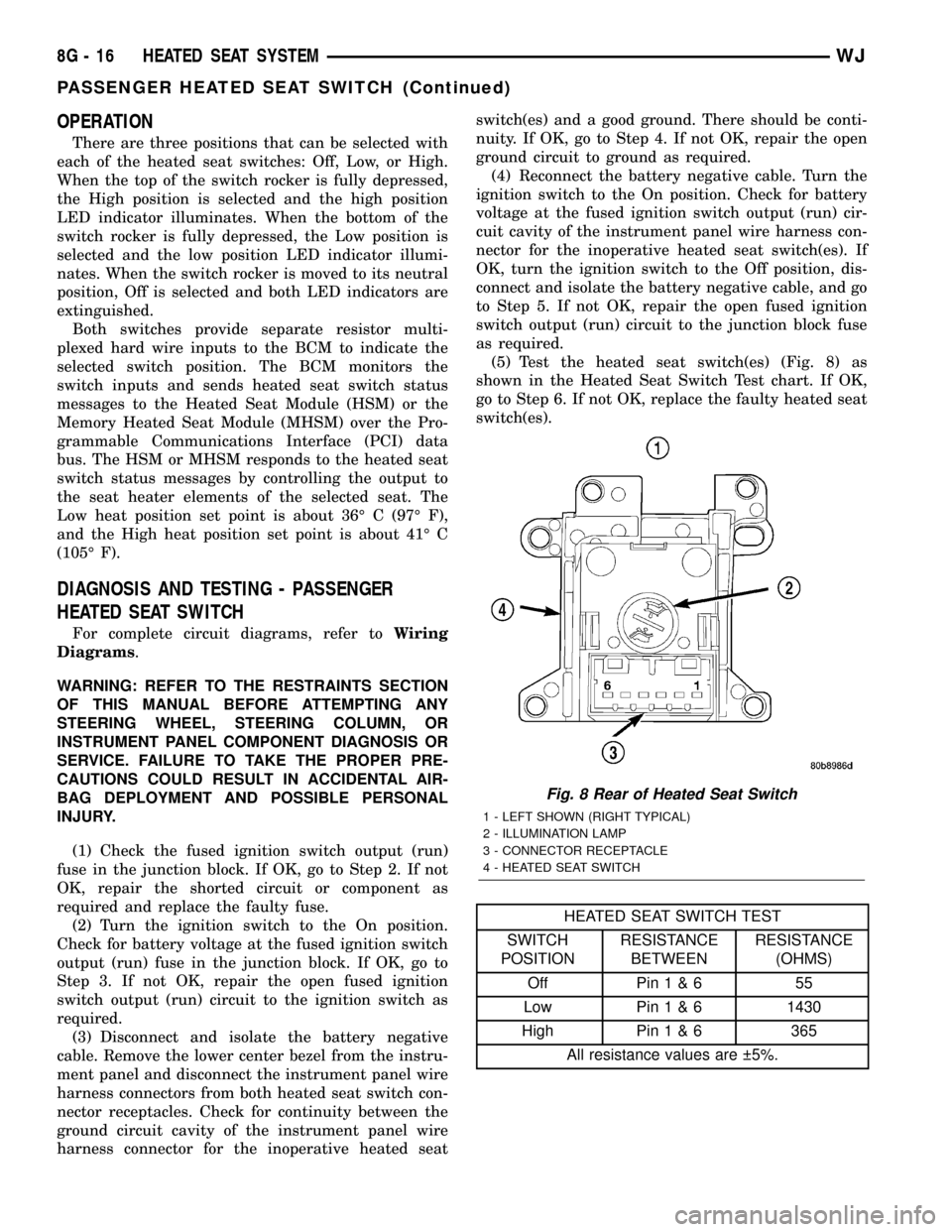
OPERATION
There are three positions that can be selected with
each of the heated seat switches: Off, Low, or High.
When the top of the switch rocker is fully depressed,
the High position is selected and the high position
LED indicator illuminates. When the bottom of the
switch rocker is fully depressed, the Low position is
selected and the low position LED indicator illumi-
nates. When the switch rocker is moved to its neutral
position, Off is selected and both LED indicators are
extinguished.
Both switches provide separate resistor multi-
plexed hard wire inputs to the BCM to indicate the
selected switch position. The BCM monitors the
switch inputs and sends heated seat switch status
messages to the Heated Seat Module (HSM) or the
Memory Heated Seat Module (MHSM) over the Pro-
grammable Communications Interface (PCI) data
bus. The HSM or MHSM responds to the heated seat
switch status messages by controlling the output to
the seat heater elements of the selected seat. The
Low heat position set point is about 36É C (97É F),
and the High heat position set point is about 41É C
(105É F).
DIAGNOSIS AND TESTING - PASSENGER
HEATED SEAT SWITCH
For complete circuit diagrams, refer toWiring
Diagrams.
WARNING: REFER TO THE RESTRAINTS SECTION
OF THIS MANUAL BEFORE ATTEMPTING ANY
STEERING WHEEL, STEERING COLUMN, OR
INSTRUMENT PANEL COMPONENT DIAGNOSIS OR
SERVICE. FAILURE TO TAKE THE PROPER PRE-
CAUTIONS COULD RESULT IN ACCIDENTAL AIR-
BAG DEPLOYMENT AND POSSIBLE PERSONAL
INJURY.
(1) Check the fused ignition switch output (run)
fuse in the junction block. If OK, go to Step 2. If not
OK, repair the shorted circuit or component as
required and replace the faulty fuse.
(2) Turn the ignition switch to the On position.
Check for battery voltage at the fused ignition switch
output (run) fuse in the junction block. If OK, go to
Step 3. If not OK, repair the open fused ignition
switch output (run) circuit to the ignition switch as
required.
(3) Disconnect and isolate the battery negative
cable. Remove the lower center bezel from the instru-
ment panel and disconnect the instrument panel wire
harness connectors from both heated seat switch con-
nector receptacles. Check for continuity between the
ground circuit cavity of the instrument panel wire
harness connector for the inoperative heated seatswitch(es) and a good ground. There should be conti-
nuity. If OK, go to Step 4. If not OK, repair the open
ground circuit to ground as required.
(4) Reconnect the battery negative cable. Turn the
ignition switch to the On position. Check for battery
voltage at the fused ignition switch output (run) cir-
cuit cavity of the instrument panel wire harness con-
nector for the inoperative heated seat switch(es). If
OK, turn the ignition switch to the Off position, dis-
connect and isolate the battery negative cable, and go
to Step 5. If not OK, repair the open fused ignition
switch output (run) circuit to the junction block fuse
as required.
(5) Test the heated seat switch(es) (Fig. 8) as
shown in the Heated Seat Switch Test chart. If OK,
go to Step 6. If not OK, replace the faulty heated seat
switch(es).
HEATED SEAT SWITCH TEST
SWITCH
POSITIONRESISTANCE
BETWEENRESISTANCE
(OHMS)
Off Pin1&6 55
Low Pin1&61430
High Pin1&6 365
All resistance values are 5%.
Fig. 8 Rear of Heated Seat Switch
1 - LEFT SHOWN (RIGHT TYPICAL)
2 - ILLUMINATION LAMP
3 - CONNECTOR RECEPTACLE
4 - HEATED SEAT SWITCH
8G - 16 HEATED SEAT SYSTEMWJ
PASSENGER HEATED SEAT SWITCH (Continued)
Page 391 of 2199
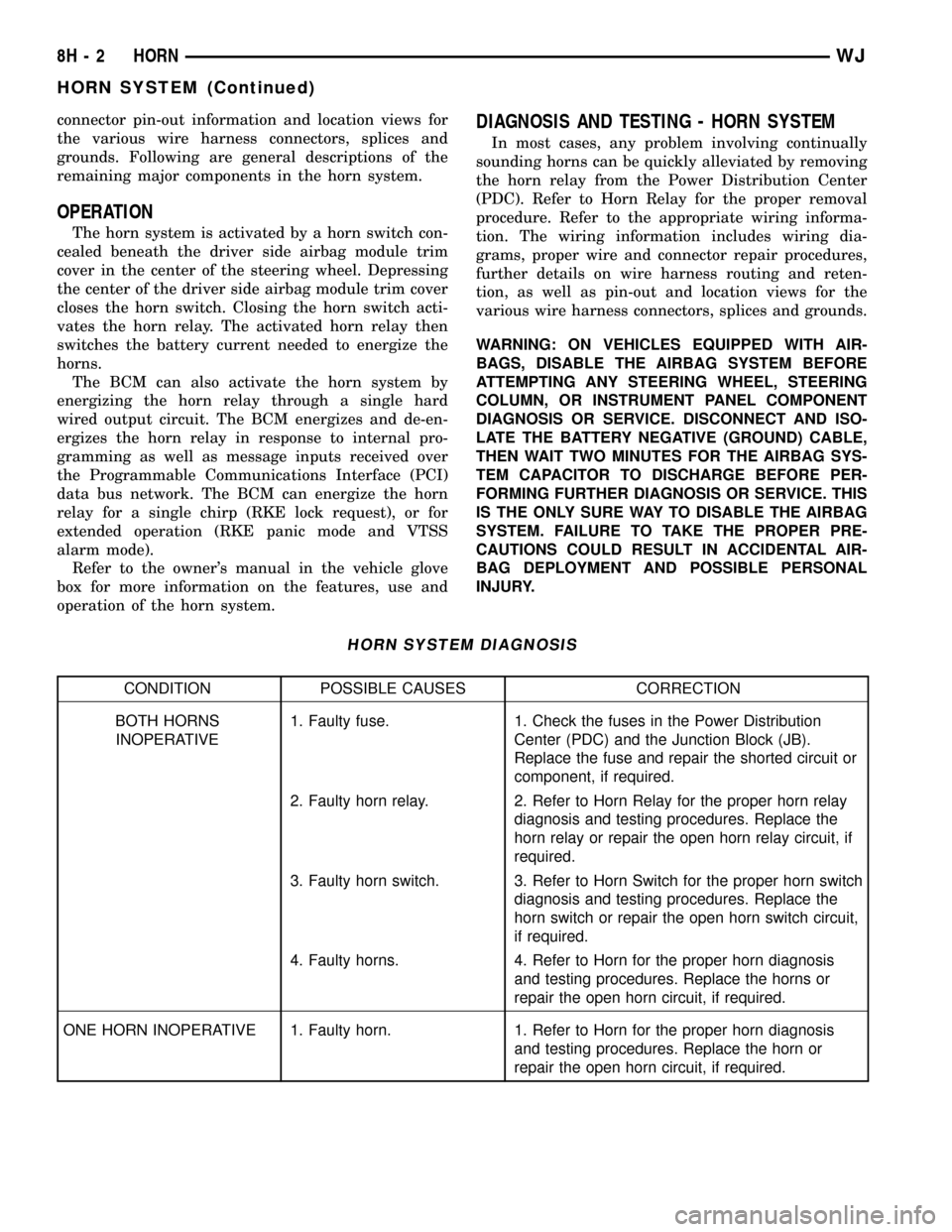
connector pin-out information and location views for
the various wire harness connectors, splices and
grounds. Following are general descriptions of the
remaining major components in the horn system.
OPERATION
The horn system is activated by a horn switch con-
cealed beneath the driver side airbag module trim
cover in the center of the steering wheel. Depressing
the center of the driver side airbag module trim cover
closes the horn switch. Closing the horn switch acti-
vates the horn relay. The activated horn relay then
switches the battery current needed to energize the
horns.
The BCM can also activate the horn system by
energizing the horn relay through a single hard
wired output circuit. The BCM energizes and de-en-
ergizes the horn relay in response to internal pro-
gramming as well as message inputs received over
the Programmable Communications Interface (PCI)
data bus network. The BCM can energize the horn
relay for a single chirp (RKE lock request), or for
extended operation (RKE panic mode and VTSS
alarm mode).
Refer to the owner's manual in the vehicle glove
box for more information on the features, use and
operation of the horn system.
DIAGNOSIS AND TESTING - HORN SYSTEM
In most cases, any problem involving continually
sounding horns can be quickly alleviated by removing
the horn relay from the Power Distribution Center
(PDC). Refer to Horn Relay for the proper removal
procedure. Refer to the appropriate wiring informa-
tion. The wiring information includes wiring dia-
grams, proper wire and connector repair procedures,
further details on wire harness routing and reten-
tion, as well as pin-out and location views for the
various wire harness connectors, splices and grounds.
WARNING: ON VEHICLES EQUIPPED WITH AIR-
BAGS, DISABLE THE AIRBAG SYSTEM BEFORE
ATTEMPTING ANY STEERING WHEEL, STEERING
COLUMN, OR INSTRUMENT PANEL COMPONENT
DIAGNOSIS OR SERVICE. DISCONNECT AND ISO-
LATE THE BATTERY NEGATIVE (GROUND) CABLE,
THEN WAIT TWO MINUTES FOR THE AIRBAG SYS-
TEM CAPACITOR TO DISCHARGE BEFORE PER-
FORMING FURTHER DIAGNOSIS OR SERVICE. THIS
IS THE ONLY SURE WAY TO DISABLE THE AIRBAG
SYSTEM. FAILURE TO TAKE THE PROPER PRE-
CAUTIONS COULD RESULT IN ACCIDENTAL AIR-
BAG DEPLOYMENT AND POSSIBLE PERSONAL
INJURY.
HORN SYSTEM DIAGNOSIS
CONDITION POSSIBLE CAUSES CORRECTION
BOTH HORNS
INOPERATIVE1. Faulty fuse. 1. Check the fuses in the Power Distribution
Center (PDC) and the Junction Block (JB).
Replace the fuse and repair the shorted circuit or
component, if required.
2. Faulty horn relay. 2. Refer to Horn Relay for the proper horn relay
diagnosis and testing procedures. Replace the
horn relay or repair the open horn relay circuit, if
required.
3. Faulty horn switch. 3. Refer to Horn Switch for the proper horn switch
diagnosis and testing procedures. Replace the
horn switch or repair the open horn switch circuit,
if required.
4. Faulty horns. 4. Refer to Horn for the proper horn diagnosis
and testing procedures. Replace the horns or
repair the open horn circuit, if required.
ONE HORN INOPERATIVE 1. Faulty horn. 1. Refer to Horn for the proper horn diagnosis
and testing procedures. Replace the horn or
repair the open horn circuit, if required.
8H - 2 HORNWJ
HORN SYSTEM (Continued)