fuse block JEEP GRAND CHEROKEE 2003 WJ / 2.G Owner's Manual
[x] Cancel search | Manufacturer: JEEP, Model Year: 2003, Model line: GRAND CHEROKEE, Model: JEEP GRAND CHEROKEE 2003 WJ / 2.GPages: 2199, PDF Size: 76.01 MB
Page 420 of 2199
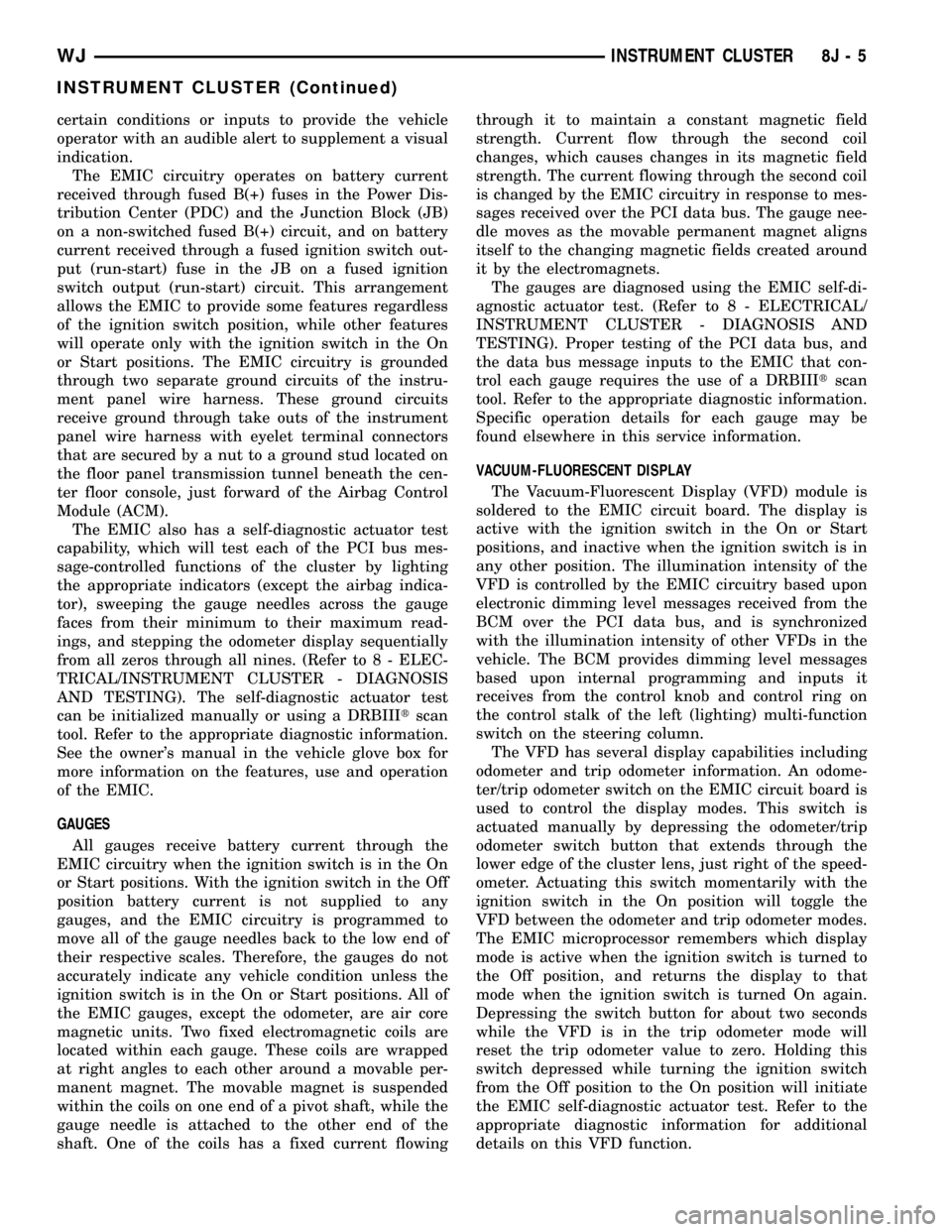
certain conditions or inputs to provide the vehicle
operator with an audible alert to supplement a visual
indication.
The EMIC circuitry operates on battery current
received through fused B(+) fuses in the Power Dis-
tribution Center (PDC) and the Junction Block (JB)
on a non-switched fused B(+) circuit, and on battery
current received through a fused ignition switch out-
put (run-start) fuse in the JB on a fused ignition
switch output (run-start) circuit. This arrangement
allows the EMIC to provide some features regardless
of the ignition switch position, while other features
will operate only with the ignition switch in the On
or Start positions. The EMIC circuitry is grounded
through two separate ground circuits of the instru-
ment panel wire harness. These ground circuits
receive ground through take outs of the instrument
panel wire harness with eyelet terminal connectors
that are secured by a nut to a ground stud located on
the floor panel transmission tunnel beneath the cen-
ter floor console, just forward of the Airbag Control
Module (ACM).
The EMIC also has a self-diagnostic actuator test
capability, which will test each of the PCI bus mes-
sage-controlled functions of the cluster by lighting
the appropriate indicators (except the airbag indica-
tor), sweeping the gauge needles across the gauge
faces from their minimum to their maximum read-
ings, and stepping the odometer display sequentially
from all zeros through all nines. (Refer to 8 - ELEC-
TRICAL/INSTRUMENT CLUSTER - DIAGNOSIS
AND TESTING). The self-diagnostic actuator test
can be initialized manually or using a DRBIIItscan
tool. Refer to the appropriate diagnostic information.
See the owner's manual in the vehicle glove box for
more information on the features, use and operation
of the EMIC.
GAUGES
All gauges receive battery current through the
EMIC circuitry when the ignition switch is in the On
or Start positions. With the ignition switch in the Off
position battery current is not supplied to any
gauges, and the EMIC circuitry is programmed to
move all of the gauge needles back to the low end of
their respective scales. Therefore, the gauges do not
accurately indicate any vehicle condition unless the
ignition switch is in the On or Start positions. All of
the EMIC gauges, except the odometer, are air core
magnetic units. Two fixed electromagnetic coils are
located within each gauge. These coils are wrapped
at right angles to each other around a movable per-
manent magnet. The movable magnet is suspended
within the coils on one end of a pivot shaft, while the
gauge needle is attached to the other end of the
shaft. One of the coils has a fixed current flowingthrough it to maintain a constant magnetic field
strength. Current flow through the second coil
changes, which causes changes in its magnetic field
strength. The current flowing through the second coil
is changed by the EMIC circuitry in response to mes-
sages received over the PCI data bus. The gauge nee-
dle moves as the movable permanent magnet aligns
itself to the changing magnetic fields created around
it by the electromagnets.
The gauges are diagnosed using the EMIC self-di-
agnostic actuator test. (Refer to 8 - ELECTRICAL/
INSTRUMENT CLUSTER - DIAGNOSIS AND
TESTING). Proper testing of the PCI data bus, and
the data bus message inputs to the EMIC that con-
trol each gauge requires the use of a DRBIIItscan
tool. Refer to the appropriate diagnostic information.
Specific operation details for each gauge may be
found elsewhere in this service information.
VACUUM-FLUORESCENT DISPLAY
The Vacuum-Fluorescent Display (VFD) module is
soldered to the EMIC circuit board. The display is
active with the ignition switch in the On or Start
positions, and inactive when the ignition switch is in
any other position. The illumination intensity of the
VFD is controlled by the EMIC circuitry based upon
electronic dimming level messages received from the
BCM over the PCI data bus, and is synchronized
with the illumination intensity of other VFDs in the
vehicle. The BCM provides dimming level messages
based upon internal programming and inputs it
receives from the control knob and control ring on
the control stalk of the left (lighting) multi-function
switch on the steering column.
The VFD has several display capabilities including
odometer and trip odometer information. An odome-
ter/trip odometer switch on the EMIC circuit board is
used to control the display modes. This switch is
actuated manually by depressing the odometer/trip
odometer switch button that extends through the
lower edge of the cluster lens, just right of the speed-
ometer. Actuating this switch momentarily with the
ignition switch in the On position will toggle the
VFD between the odometer and trip odometer modes.
The EMIC microprocessor remembers which display
mode is active when the ignition switch is turned to
the Off position, and returns the display to that
mode when the ignition switch is turned On again.
Depressing the switch button for about two seconds
while the VFD is in the trip odometer mode will
reset the trip odometer value to zero. Holding this
switch depressed while turning the ignition switch
from the Off position to the On position will initiate
the EMIC self-diagnostic actuator test. Refer to the
appropriate diagnostic information for additional
details on this VFD function.
WJINSTRUMENT CLUSTER 8J - 5
INSTRUMENT CLUSTER (Continued)
Page 422 of 2199
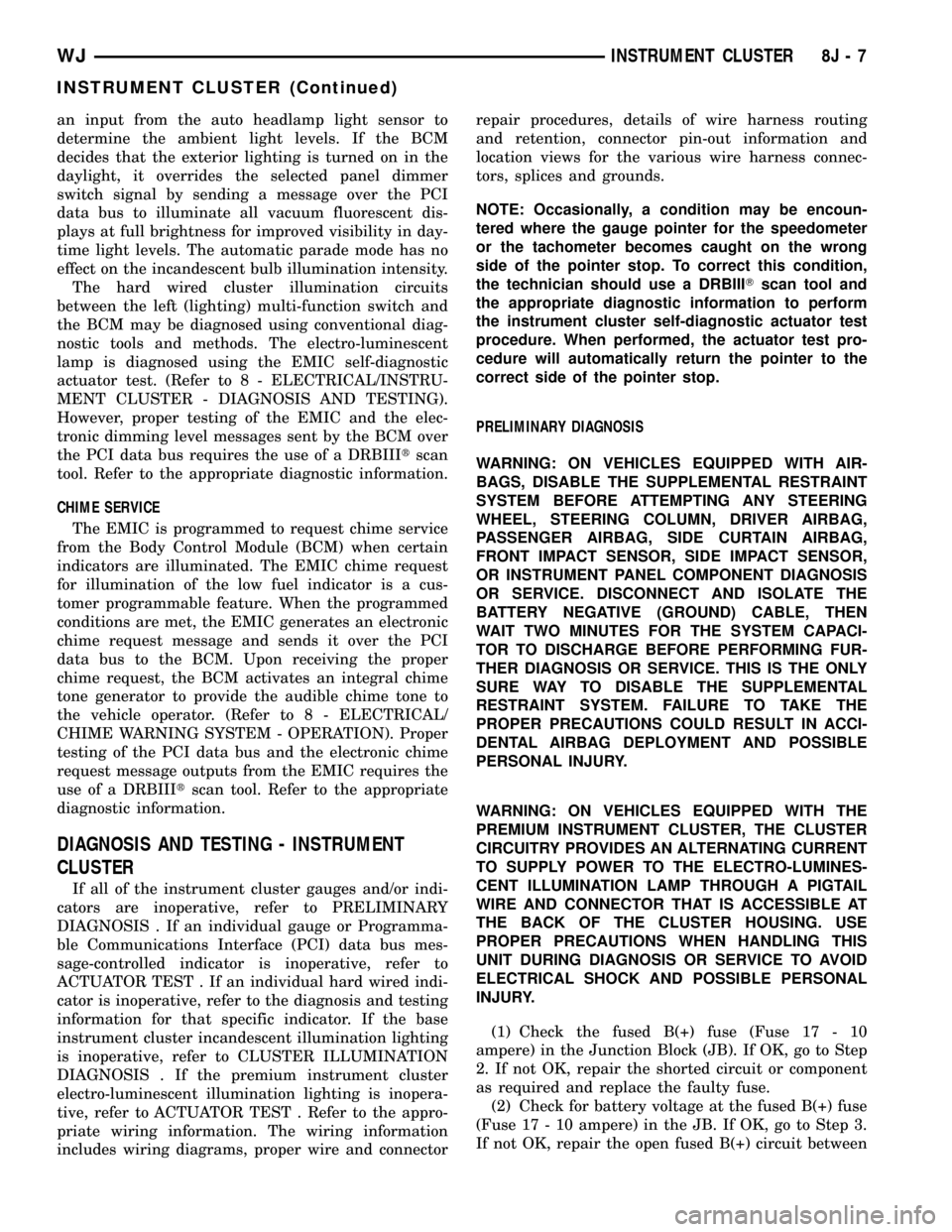
an input from the auto headlamp light sensor to
determine the ambient light levels. If the BCM
decides that the exterior lighting is turned on in the
daylight, it overrides the selected panel dimmer
switch signal by sending a message over the PCI
data bus to illuminate all vacuum fluorescent dis-
plays at full brightness for improved visibility in day-
time light levels. The automatic parade mode has no
effect on the incandescent bulb illumination intensity.
The hard wired cluster illumination circuits
between the left (lighting) multi-function switch and
the BCM may be diagnosed using conventional diag-
nostic tools and methods. The electro-luminescent
lamp is diagnosed using the EMIC self-diagnostic
actuator test. (Refer to 8 - ELECTRICAL/INSTRU-
MENT CLUSTER - DIAGNOSIS AND TESTING).
However, proper testing of the EMIC and the elec-
tronic dimming level messages sent by the BCM over
the PCI data bus requires the use of a DRBIIItscan
tool. Refer to the appropriate diagnostic information.
CHIME SERVICE
The EMIC is programmed to request chime service
from the Body Control Module (BCM) when certain
indicators are illuminated. The EMIC chime request
for illumination of the low fuel indicator is a cus-
tomer programmable feature. When the programmed
conditions are met, the EMIC generates an electronic
chime request message and sends it over the PCI
data bus to the BCM. Upon receiving the proper
chime request, the BCM activates an integral chime
tone generator to provide the audible chime tone to
the vehicle operator. (Refer to 8 - ELECTRICAL/
CHIME WARNING SYSTEM - OPERATION). Proper
testing of the PCI data bus and the electronic chime
request message outputs from the EMIC requires the
use of a DRBIIItscan tool. Refer to the appropriate
diagnostic information.
DIAGNOSIS AND TESTING - INSTRUMENT
CLUSTER
If all of the instrument cluster gauges and/or indi-
cators are inoperative, refer to PRELIMINARY
DIAGNOSIS . If an individual gauge or Programma-
ble Communications Interface (PCI) data bus mes-
sage-controlled indicator is inoperative, refer to
ACTUATOR TEST . If an individual hard wired indi-
cator is inoperative, refer to the diagnosis and testing
information for that specific indicator. If the base
instrument cluster incandescent illumination lighting
is inoperative, refer to CLUSTER ILLUMINATION
DIAGNOSIS . If the premium instrument cluster
electro-luminescent illumination lighting is inopera-
tive, refer to ACTUATOR TEST . Refer to the appro-
priate wiring information. The wiring information
includes wiring diagrams, proper wire and connectorrepair procedures, details of wire harness routing
and retention, connector pin-out information and
location views for the various wire harness connec-
tors, splices and grounds.
NOTE: Occasionally, a condition may be encoun-
tered where the gauge pointer for the speedometer
or the tachometer becomes caught on the wrong
side of the pointer stop. To correct this condition,
the technician should use a DRBIIITscan tool and
the appropriate diagnostic information to perform
the instrument cluster self-diagnostic actuator test
procedure. When performed, the actuator test pro-
cedure will automatically return the pointer to the
correct side of the pointer stop.
PRELIMINARY DIAGNOSIS
WARNING: ON VEHICLES EQUIPPED WITH AIR-
BAGS, DISABLE THE SUPPLEMENTAL RESTRAINT
SYSTEM BEFORE ATTEMPTING ANY STEERING
WHEEL, STEERING COLUMN, DRIVER AIRBAG,
PASSENGER AIRBAG, SIDE CURTAIN AIRBAG,
FRONT IMPACT SENSOR, SIDE IMPACT SENSOR,
OR INSTRUMENT PANEL COMPONENT DIAGNOSIS
OR SERVICE. DISCONNECT AND ISOLATE THE
BATTERY NEGATIVE (GROUND) CABLE, THEN
WAIT TWO MINUTES FOR THE SYSTEM CAPACI-
TOR TO DISCHARGE BEFORE PERFORMING FUR-
THER DIAGNOSIS OR SERVICE. THIS IS THE ONLY
SURE WAY TO DISABLE THE SUPPLEMENTAL
RESTRAINT SYSTEM. FAILURE TO TAKE THE
PROPER PRECAUTIONS COULD RESULT IN ACCI-
DENTAL AIRBAG DEPLOYMENT AND POSSIBLE
PERSONAL INJURY.
WARNING: ON VEHICLES EQUIPPED WITH THE
PREMIUM INSTRUMENT CLUSTER, THE CLUSTER
CIRCUITRY PROVIDES AN ALTERNATING CURRENT
TO SUPPLY POWER TO THE ELECTRO-LUMINES-
CENT ILLUMINATION LAMP THROUGH A PIGTAIL
WIRE AND CONNECTOR THAT IS ACCESSIBLE AT
THE BACK OF THE CLUSTER HOUSING. USE
PROPER PRECAUTIONS WHEN HANDLING THIS
UNIT DURING DIAGNOSIS OR SERVICE TO AVOID
ELECTRICAL SHOCK AND POSSIBLE PERSONAL
INJURY.
(1) Check the fused B(+) fuse (Fuse 17 - 10
ampere) in the Junction Block (JB). If OK, go to Step
2. If not OK, repair the shorted circuit or component
as required and replace the faulty fuse.
(2) Check for battery voltage at the fused B(+) fuse
(Fuse 17 - 10 ampere) in the JB. If OK, go to Step 3.
If not OK, repair the open fused B(+) circuit between
WJINSTRUMENT CLUSTER 8J - 7
INSTRUMENT CLUSTER (Continued)
Page 449 of 2199
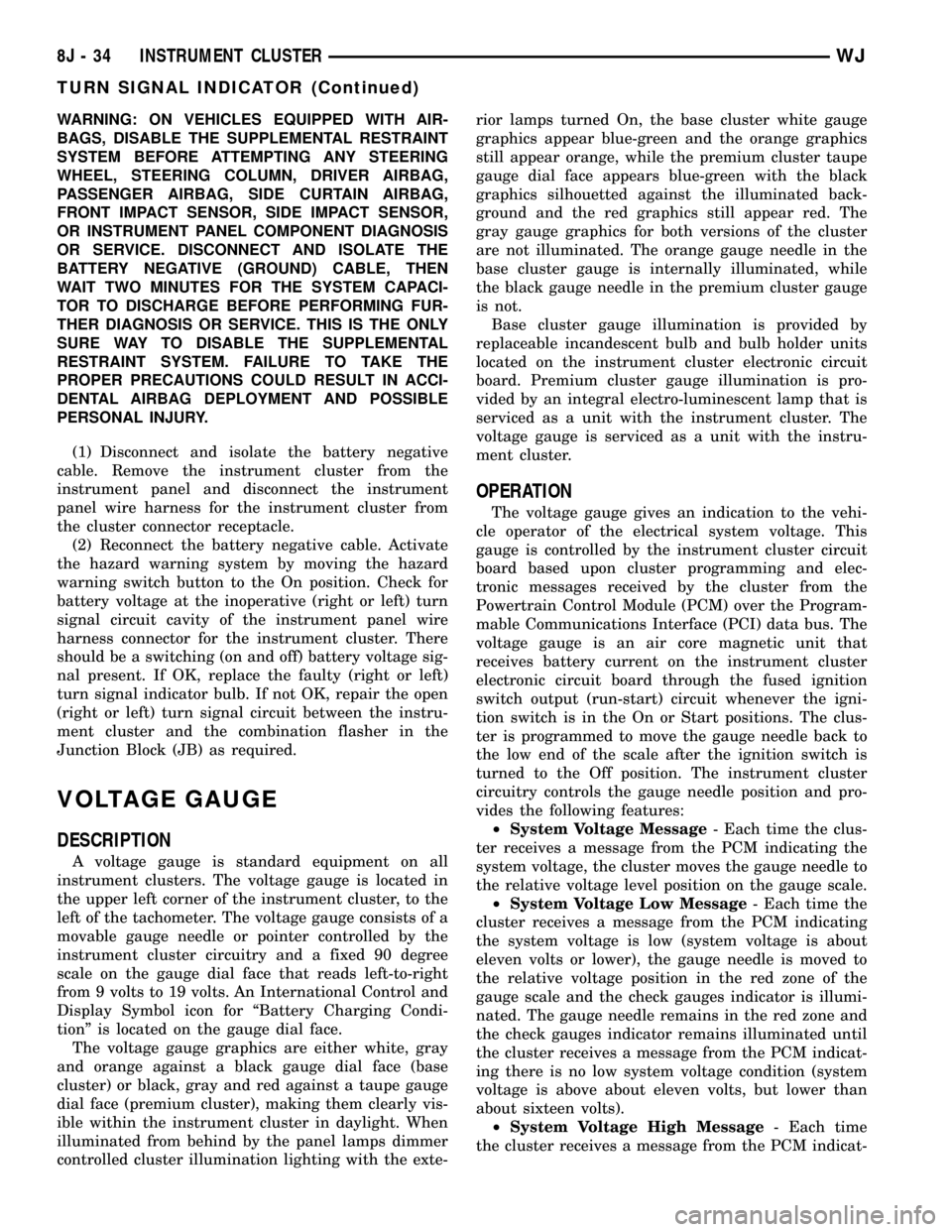
WARNING: ON VEHICLES EQUIPPED WITH AIR-
BAGS, DISABLE THE SUPPLEMENTAL RESTRAINT
SYSTEM BEFORE ATTEMPTING ANY STEERING
WHEEL, STEERING COLUMN, DRIVER AIRBAG,
PASSENGER AIRBAG, SIDE CURTAIN AIRBAG,
FRONT IMPACT SENSOR, SIDE IMPACT SENSOR,
OR INSTRUMENT PANEL COMPONENT DIAGNOSIS
OR SERVICE. DISCONNECT AND ISOLATE THE
BATTERY NEGATIVE (GROUND) CABLE, THEN
WAIT TWO MINUTES FOR THE SYSTEM CAPACI-
TOR TO DISCHARGE BEFORE PERFORMING FUR-
THER DIAGNOSIS OR SERVICE. THIS IS THE ONLY
SURE WAY TO DISABLE THE SUPPLEMENTAL
RESTRAINT SYSTEM. FAILURE TO TAKE THE
PROPER PRECAUTIONS COULD RESULT IN ACCI-
DENTAL AIRBAG DEPLOYMENT AND POSSIBLE
PERSONAL INJURY.
(1) Disconnect and isolate the battery negative
cable. Remove the instrument cluster from the
instrument panel and disconnect the instrument
panel wire harness for the instrument cluster from
the cluster connector receptacle.
(2) Reconnect the battery negative cable. Activate
the hazard warning system by moving the hazard
warning switch button to the On position. Check for
battery voltage at the inoperative (right or left) turn
signal circuit cavity of the instrument panel wire
harness connector for the instrument cluster. There
should be a switching (on and off) battery voltage sig-
nal present. If OK, replace the faulty (right or left)
turn signal indicator bulb. If not OK, repair the open
(right or left) turn signal circuit between the instru-
ment cluster and the combination flasher in the
Junction Block (JB) as required.
VOLTAGE GAUGE
DESCRIPTION
A voltage gauge is standard equipment on all
instrument clusters. The voltage gauge is located in
the upper left corner of the instrument cluster, to the
left of the tachometer. The voltage gauge consists of a
movable gauge needle or pointer controlled by the
instrument cluster circuitry and a fixed 90 degree
scale on the gauge dial face that reads left-to-right
from 9 volts to 19 volts. An International Control and
Display Symbol icon for ªBattery Charging Condi-
tionº is located on the gauge dial face.
The voltage gauge graphics are either white, gray
and orange against a black gauge dial face (base
cluster) or black, gray and red against a taupe gauge
dial face (premium cluster), making them clearly vis-
ible within the instrument cluster in daylight. When
illuminated from behind by the panel lamps dimmer
controlled cluster illumination lighting with the exte-rior lamps turned On, the base cluster white gauge
graphics appear blue-green and the orange graphics
still appear orange, while the premium cluster taupe
gauge dial face appears blue-green with the black
graphics silhouetted against the illuminated back-
ground and the red graphics still appear red. The
gray gauge graphics for both versions of the cluster
are not illuminated. The orange gauge needle in the
base cluster gauge is internally illuminated, while
the black gauge needle in the premium cluster gauge
is not.
Base cluster gauge illumination is provided by
replaceable incandescent bulb and bulb holder units
located on the instrument cluster electronic circuit
board. Premium cluster gauge illumination is pro-
vided by an integral electro-luminescent lamp that is
serviced as a unit with the instrument cluster. The
voltage gauge is serviced as a unit with the instru-
ment cluster.
OPERATION
The voltage gauge gives an indication to the vehi-
cle operator of the electrical system voltage. This
gauge is controlled by the instrument cluster circuit
board based upon cluster programming and elec-
tronic messages received by the cluster from the
Powertrain Control Module (PCM) over the Program-
mable Communications Interface (PCI) data bus. The
voltage gauge is an air core magnetic unit that
receives battery current on the instrument cluster
electronic circuit board through the fused ignition
switch output (run-start) circuit whenever the igni-
tion switch is in the On or Start positions. The clus-
ter is programmed to move the gauge needle back to
the low end of the scale after the ignition switch is
turned to the Off position. The instrument cluster
circuitry controls the gauge needle position and pro-
vides the following features:
²System Voltage Message- Each time the clus-
ter receives a message from the PCM indicating the
system voltage, the cluster moves the gauge needle to
the relative voltage level position on the gauge scale.
²System Voltage Low Message- Each time the
cluster receives a message from the PCM indicating
the system voltage is low (system voltage is about
eleven volts or lower), the gauge needle is moved to
the relative voltage position in the red zone of the
gauge scale and the check gauges indicator is illumi-
nated. The gauge needle remains in the red zone and
the check gauges indicator remains illuminated until
the cluster receives a message from the PCM indicat-
ing there is no low system voltage condition (system
voltage is above about eleven volts, but lower than
about sixteen volts).
²System Voltage High Message- Each time
the cluster receives a message from the PCM indicat-
8J - 34 INSTRUMENT CLUSTERWJ
TURN SIGNAL INDICATOR (Continued)
Page 454 of 2199
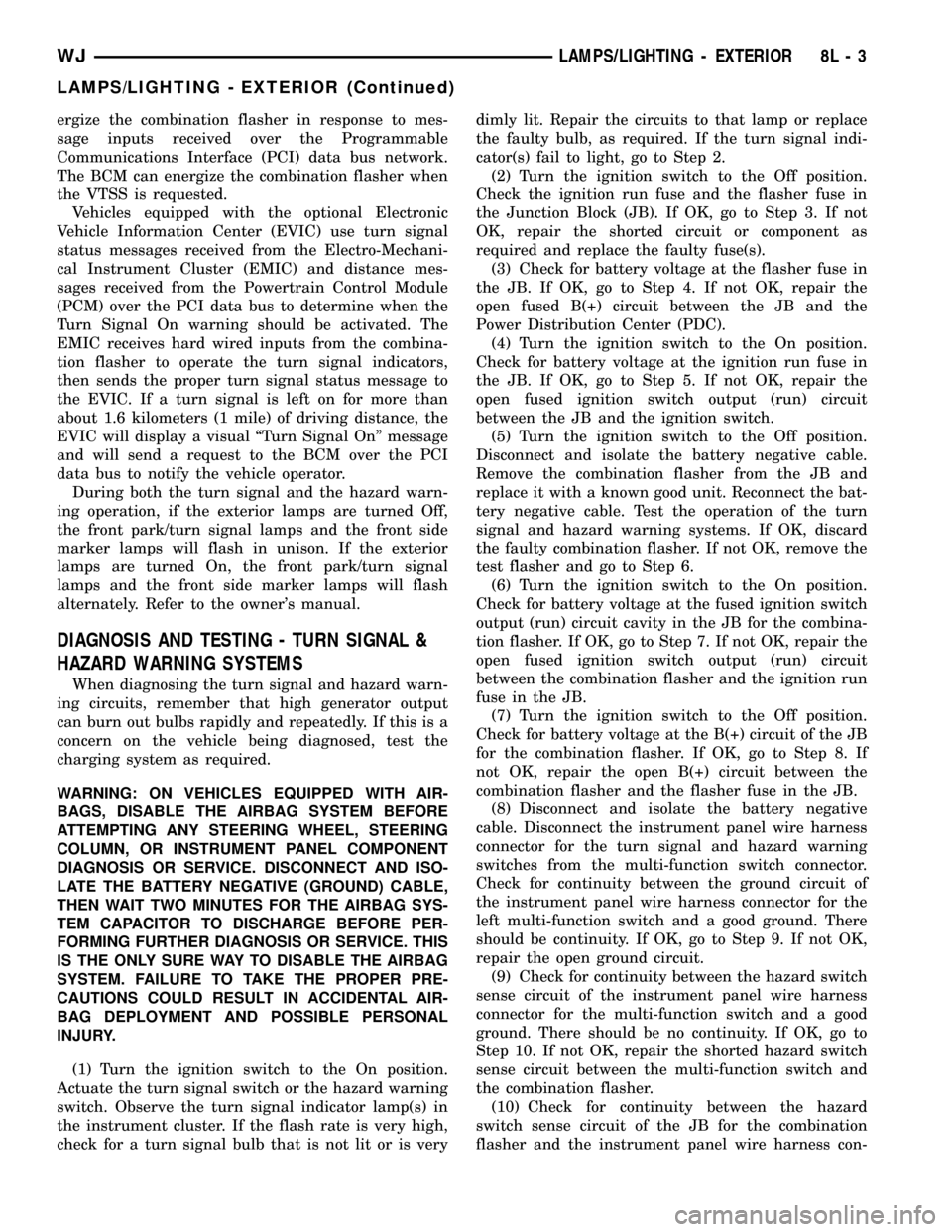
ergize the combination flasher in response to mes-
sage inputs received over the Programmable
Communications Interface (PCI) data bus network.
The BCM can energize the combination flasher when
the VTSS is requested.
Vehicles equipped with the optional Electronic
Vehicle Information Center (EVIC) use turn signal
status messages received from the Electro-Mechani-
cal Instrument Cluster (EMIC) and distance mes-
sages received from the Powertrain Control Module
(PCM) over the PCI data bus to determine when the
Turn Signal On warning should be activated. The
EMIC receives hard wired inputs from the combina-
tion flasher to operate the turn signal indicators,
then sends the proper turn signal status message to
the EVIC. If a turn signal is left on for more than
about 1.6 kilometers (1 mile) of driving distance, the
EVIC will display a visual ªTurn Signal Onº message
and will send a request to the BCM over the PCI
data bus to notify the vehicle operator.
During both the turn signal and the hazard warn-
ing operation, if the exterior lamps are turned Off,
the front park/turn signal lamps and the front side
marker lamps will flash in unison. If the exterior
lamps are turned On, the front park/turn signal
lamps and the front side marker lamps will flash
alternately. Refer to the owner's manual.
DIAGNOSIS AND TESTING - TURN SIGNAL &
HAZARD WARNING SYSTEMS
When diagnosing the turn signal and hazard warn-
ing circuits, remember that high generator output
can burn out bulbs rapidly and repeatedly. If this is a
concern on the vehicle being diagnosed, test the
charging system as required.
WARNING: ON VEHICLES EQUIPPED WITH AIR-
BAGS, DISABLE THE AIRBAG SYSTEM BEFORE
ATTEMPTING ANY STEERING WHEEL, STEERING
COLUMN, OR INSTRUMENT PANEL COMPONENT
DIAGNOSIS OR SERVICE. DISCONNECT AND ISO-
LATE THE BATTERY NEGATIVE (GROUND) CABLE,
THEN WAIT TWO MINUTES FOR THE AIRBAG SYS-
TEM CAPACITOR TO DISCHARGE BEFORE PER-
FORMING FURTHER DIAGNOSIS OR SERVICE. THIS
IS THE ONLY SURE WAY TO DISABLE THE AIRBAG
SYSTEM. FAILURE TO TAKE THE PROPER PRE-
CAUTIONS COULD RESULT IN ACCIDENTAL AIR-
BAG DEPLOYMENT AND POSSIBLE PERSONAL
INJURY.
(1) Turn the ignition switch to the On position.
Actuate the turn signal switch or the hazard warning
switch. Observe the turn signal indicator lamp(s) in
the instrument cluster. If the flash rate is very high,
check for a turn signal bulb that is not lit or is verydimly lit. Repair the circuits to that lamp or replace
the faulty bulb, as required. If the turn signal indi-
cator(s) fail to light, go to Step 2.
(2) Turn the ignition switch to the Off position.
Check the ignition run fuse and the flasher fuse in
the Junction Block (JB). If OK, go to Step 3. If not
OK, repair the shorted circuit or component as
required and replace the faulty fuse(s).
(3) Check for battery voltage at the flasher fuse in
the JB. If OK, go to Step 4. If not OK, repair the
open fused B(+) circuit between the JB and the
Power Distribution Center (PDC).
(4) Turn the ignition switch to the On position.
Check for battery voltage at the ignition run fuse in
the JB. If OK, go to Step 5. If not OK, repair the
open fused ignition switch output (run) circuit
between the JB and the ignition switch.
(5) Turn the ignition switch to the Off position.
Disconnect and isolate the battery negative cable.
Remove the combination flasher from the JB and
replace it with a known good unit. Reconnect the bat-
tery negative cable. Test the operation of the turn
signal and hazard warning systems. If OK, discard
the faulty combination flasher. If not OK, remove the
test flasher and go to Step 6.
(6) Turn the ignition switch to the On position.
Check for battery voltage at the fused ignition switch
output (run) circuit cavity in the JB for the combina-
tion flasher. If OK, go to Step 7. If not OK, repair the
open fused ignition switch output (run) circuit
between the combination flasher and the ignition run
fuse in the JB.
(7) Turn the ignition switch to the Off position.
Check for battery voltage at the B(+) circuit of the JB
for the combination flasher. If OK, go to Step 8. If
not OK, repair the open B(+) circuit between the
combination flasher and the flasher fuse in the JB.
(8) Disconnect and isolate the battery negative
cable. Disconnect the instrument panel wire harness
connector for the turn signal and hazard warning
switches from the multi-function switch connector.
Check for continuity between the ground circuit of
the instrument panel wire harness connector for the
left multi-function switch and a good ground. There
should be continuity. If OK, go to Step 9. If not OK,
repair the open ground circuit.
(9) Check for continuity between the hazard switch
sense circuit of the instrument panel wire harness
connector for the multi-function switch and a good
ground. There should be no continuity. If OK, go to
Step 10. If not OK, repair the shorted hazard switch
sense circuit between the multi-function switch and
the combination flasher.
(10) Check for continuity between the hazard
switch sense circuit of the JB for the combination
flasher and the instrument panel wire harness con-
WJLAMPS/LIGHTING - EXTERIOR 8L - 3
LAMPS/LIGHTING - EXTERIOR (Continued)
Page 458 of 2199
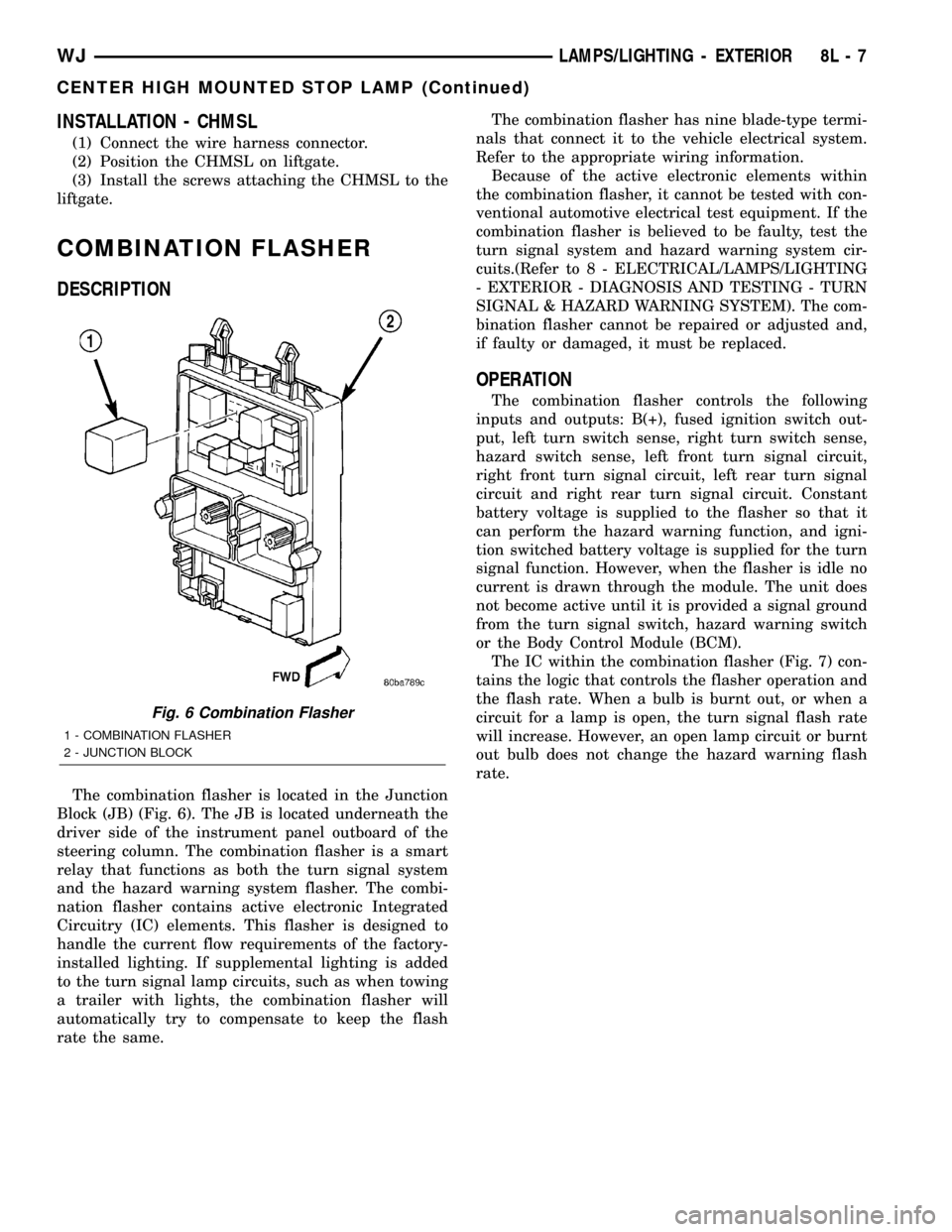
INSTALLATION - CHMSL
(1) Connect the wire harness connector.
(2) Position the CHMSL on liftgate.
(3) Install the screws attaching the CHMSL to the
liftgate.
COMBINATION FLASHER
DESCRIPTION
The combination flasher is located in the Junction
Block (JB) (Fig. 6). The JB is located underneath the
driver side of the instrument panel outboard of the
steering column. The combination flasher is a smart
relay that functions as both the turn signal system
and the hazard warning system flasher. The combi-
nation flasher contains active electronic Integrated
Circuitry (IC) elements. This flasher is designed to
handle the current flow requirements of the factory-
installed lighting. If supplemental lighting is added
to the turn signal lamp circuits, such as when towing
a trailer with lights, the combination flasher will
automatically try to compensate to keep the flash
rate the same.The combination flasher has nine blade-type termi-
nals that connect it to the vehicle electrical system.
Refer to the appropriate wiring information.
Because of the active electronic elements within
the combination flasher, it cannot be tested with con-
ventional automotive electrical test equipment. If the
combination flasher is believed to be faulty, test the
turn signal system and hazard warning system cir-
cuits.(Refer to 8 - ELECTRICAL/LAMPS/LIGHTING
- EXTERIOR - DIAGNOSIS AND TESTING - TURN
SIGNAL & HAZARD WARNING SYSTEM). The com-
bination flasher cannot be repaired or adjusted and,
if faulty or damaged, it must be replaced.
OPERATION
The combination flasher controls the following
inputs and outputs: B(+), fused ignition switch out-
put, left turn switch sense, right turn switch sense,
hazard switch sense, left front turn signal circuit,
right front turn signal circuit, left rear turn signal
circuit and right rear turn signal circuit. Constant
battery voltage is supplied to the flasher so that it
can perform the hazard warning function, and igni-
tion switched battery voltage is supplied for the turn
signal function. However, when the flasher is idle no
current is drawn through the module. The unit does
not become active until it is provided a signal ground
from the turn signal switch, hazard warning switch
or the Body Control Module (BCM).
The IC within the combination flasher (Fig. 7) con-
tains the logic that controls the flasher operation and
the flash rate. When a bulb is burnt out, or when a
circuit for a lamp is open, the turn signal flash rate
will increase. However, an open lamp circuit or burnt
out bulb does not change the hazard warning flash
rate.
Fig. 6 Combination Flasher
1 - COMBINATION FLASHER
2 - JUNCTION BLOCK
WJLAMPS/LIGHTING - EXTERIOR 8L - 7
CENTER HIGH MOUNTED STOP LAMP (Continued)
Page 465 of 2199
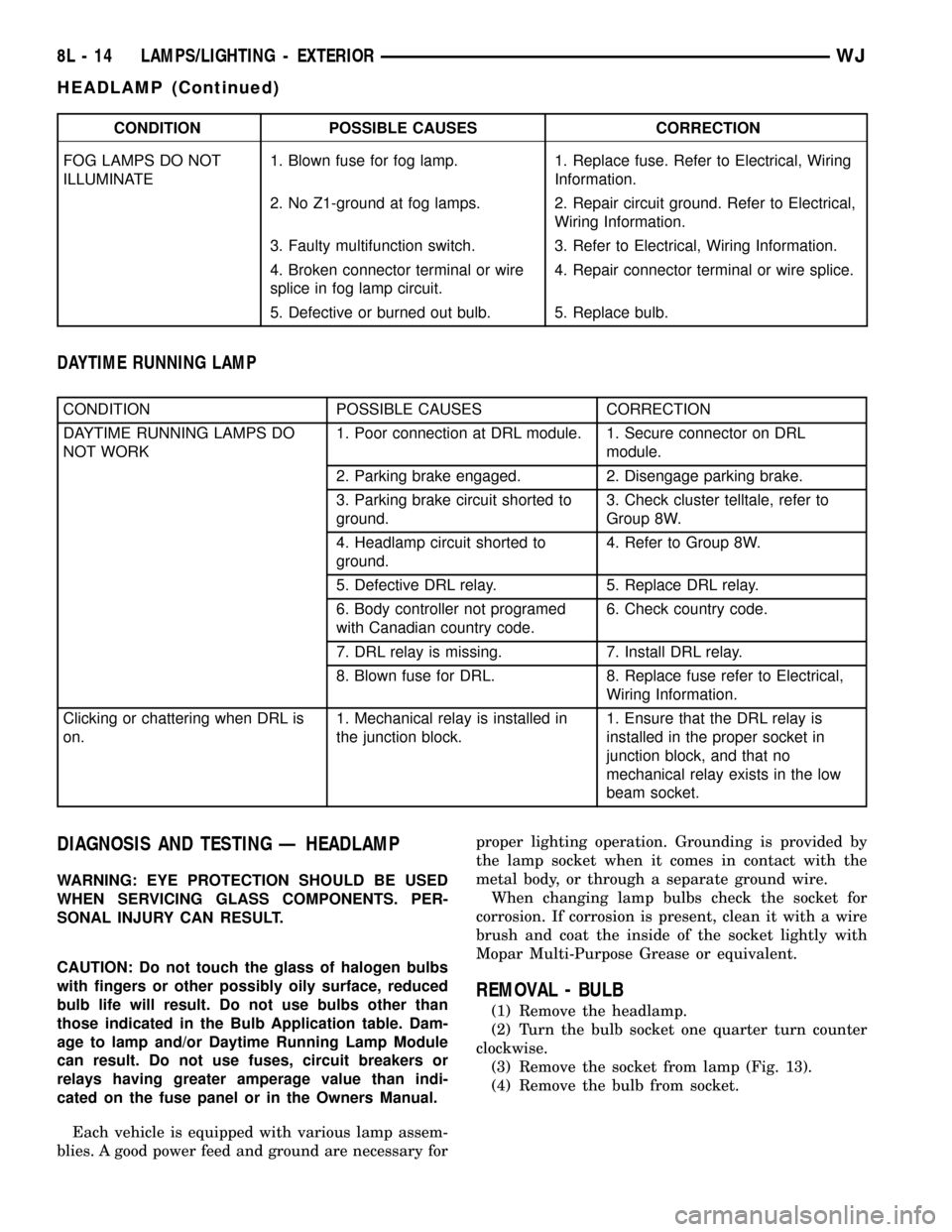
CONDITION POSSIBLE CAUSES CORRECTION
FOG LAMPS DO NOT
ILLUMINATE1. Blown fuse for fog lamp. 1. Replace fuse. Refer to Electrical, Wiring
Information.
2. No Z1-ground at fog lamps. 2. Repair circuit ground. Refer to Electrical,
Wiring Information.
3. Faulty multifunction switch. 3. Refer to Electrical, Wiring Information.
4. Broken connector terminal or wire
splice in fog lamp circuit.4. Repair connector terminal or wire splice.
5. Defective or burned out bulb. 5. Replace bulb.
DAYTIME RUNNING LAMP
CONDITION POSSIBLE CAUSES CORRECTION
DAYTIME RUNNING LAMPS DO
NOT WORK1. Poor connection at DRL module. 1. Secure connector on DRL
module.
2. Parking brake engaged. 2. Disengage parking brake.
3. Parking brake circuit shorted to
ground.3. Check cluster telltale, refer to
Group 8W.
4. Headlamp circuit shorted to
ground.4. Refer to Group 8W.
5. Defective DRL relay. 5. Replace DRL relay.
6. Body controller not programed
with Canadian country code.6. Check country code.
7. DRL relay is missing. 7. Install DRL relay.
8. Blown fuse for DRL. 8. Replace fuse refer to Electrical,
Wiring Information.
Clicking or chattering when DRL is
on.1. Mechanical relay is installed in
the junction block.1. Ensure that the DRL relay is
installed in the proper socket in
junction block, and that no
mechanical relay exists in the low
beam socket.
DIAGNOSIS AND TESTING Ð HEADLAMP
WARNING: EYE PROTECTION SHOULD BE USED
WHEN SERVICING GLASS COMPONENTS. PER-
SONAL INJURY CAN RESULT.
CAUTION: Do not touch the glass of halogen bulbs
with fingers or other possibly oily surface, reduced
bulb life will result. Do not use bulbs other than
those indicated in the Bulb Application table. Dam-
age to lamp and/or Daytime Running Lamp Module
can result. Do not use fuses, circuit breakers or
relays having greater amperage value than indi-
cated on the fuse panel or in the Owners Manual.
Each vehicle is equipped with various lamp assem-
blies. A good power feed and ground are necessary forproper lighting operation. Grounding is provided by
the lamp socket when it comes in contact with the
metal body, or through a separate ground wire.
When changing lamp bulbs check the socket for
corrosion. If corrosion is present, clean it with a wire
brush and coat the inside of the socket lightly with
Mopar Multi-Purpose Grease or equivalent.
REMOVAL - BULB
(1) Remove the headlamp.
(2) Turn the bulb socket one quarter turn counter
clockwise.
(3) Remove the socket from lamp (Fig. 13).
(4) Remove the bulb from socket.
8L - 14 LAMPS/LIGHTING - EXTERIORWJ
HEADLAMP (Continued)
Page 492 of 2199
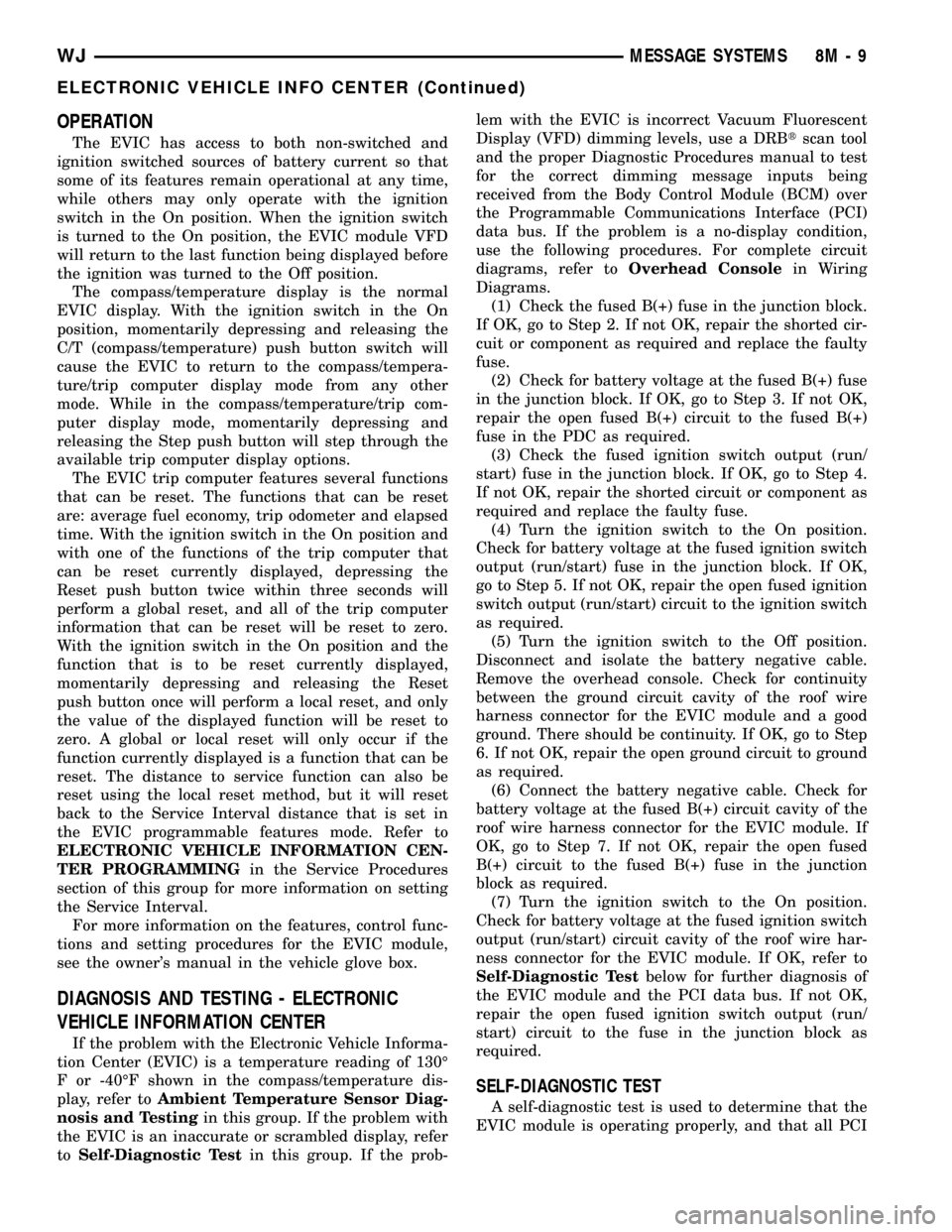
OPERATION
The EVIC has access to both non-switched and
ignition switched sources of battery current so that
some of its features remain operational at any time,
while others may only operate with the ignition
switch in the On position. When the ignition switch
is turned to the On position, the EVIC module VFD
will return to the last function being displayed before
the ignition was turned to the Off position.
The compass/temperature display is the normal
EVIC display. With the ignition switch in the On
position, momentarily depressing and releasing the
C/T (compass/temperature) push button switch will
cause the EVIC to return to the compass/tempera-
ture/trip computer display mode from any other
mode. While in the compass/temperature/trip com-
puter display mode, momentarily depressing and
releasing the Step push button will step through the
available trip computer display options.
The EVIC trip computer features several functions
that can be reset. The functions that can be reset
are: average fuel economy, trip odometer and elapsed
time. With the ignition switch in the On position and
with one of the functions of the trip computer that
can be reset currently displayed, depressing the
Reset push button twice within three seconds will
perform a global reset, and all of the trip computer
information that can be reset will be reset to zero.
With the ignition switch in the On position and the
function that is to be reset currently displayed,
momentarily depressing and releasing the Reset
push button once will perform a local reset, and only
the value of the displayed function will be reset to
zero. A global or local reset will only occur if the
function currently displayed is a function that can be
reset. The distance to service function can also be
reset using the local reset method, but it will reset
back to the Service Interval distance that is set in
the EVIC programmable features mode. Refer to
ELECTRONIC VEHICLE INFORMATION CEN-
TER PROGRAMMINGin the Service Procedures
section of this group for more information on setting
the Service Interval.
For more information on the features, control func-
tions and setting procedures for the EVIC module,
see the owner's manual in the vehicle glove box.
DIAGNOSIS AND TESTING - ELECTRONIC
VEHICLE INFORMATION CENTER
If the problem with the Electronic Vehicle Informa-
tion Center (EVIC) is a temperature reading of 130É
F or -40ÉF shown in the compass/temperature dis-
play, refer toAmbient Temperature Sensor Diag-
nosis and Testingin this group. If the problem with
the EVIC is an inaccurate or scrambled display, refer
toSelf-Diagnostic Testin this group. If the prob-lem with the EVIC is incorrect Vacuum Fluorescent
Display (VFD) dimming levels, use a DRBtscan tool
and the proper Diagnostic Procedures manual to test
for the correct dimming message inputs being
received from the Body Control Module (BCM) over
the Programmable Communications Interface (PCI)
data bus. If the problem is a no-display condition,
use the following procedures. For complete circuit
diagrams, refer toOverhead Consolein Wiring
Diagrams.
(1) Check the fused B(+) fuse in the junction block.
If OK, go to Step 2. If not OK, repair the shorted cir-
cuit or component as required and replace the faulty
fuse.
(2) Check for battery voltage at the fused B(+) fuse
in the junction block. If OK, go to Step 3. If not OK,
repair the open fused B(+) circuit to the fused B(+)
fuse in the PDC as required.
(3) Check the fused ignition switch output (run/
start) fuse in the junction block. If OK, go to Step 4.
If not OK, repair the shorted circuit or component as
required and replace the faulty fuse.
(4) Turn the ignition switch to the On position.
Check for battery voltage at the fused ignition switch
output (run/start) fuse in the junction block. If OK,
go to Step 5. If not OK, repair the open fused ignition
switch output (run/start) circuit to the ignition switch
as required.
(5) Turn the ignition switch to the Off position.
Disconnect and isolate the battery negative cable.
Remove the overhead console. Check for continuity
between the ground circuit cavity of the roof wire
harness connector for the EVIC module and a good
ground. There should be continuity. If OK, go to Step
6. If not OK, repair the open ground circuit to ground
as required.
(6) Connect the battery negative cable. Check for
battery voltage at the fused B(+) circuit cavity of the
roof wire harness connector for the EVIC module. If
OK, go to Step 7. If not OK, repair the open fused
B(+) circuit to the fused B(+) fuse in the junction
block as required.
(7) Turn the ignition switch to the On position.
Check for battery voltage at the fused ignition switch
output (run/start) circuit cavity of the roof wire har-
ness connector for the EVIC module. If OK, refer to
Self-Diagnostic Testbelow for further diagnosis of
the EVIC module and the PCI data bus. If not OK,
repair the open fused ignition switch output (run/
start) circuit to the fuse in the junction block as
required.
SELF-DIAGNOSTIC TEST
A self-diagnostic test is used to determine that the
EVIC module is operating properly, and that all PCI
WJMESSAGE SYSTEMS 8M - 9
ELECTRONIC VEHICLE INFO CENTER (Continued)
Page 499 of 2199
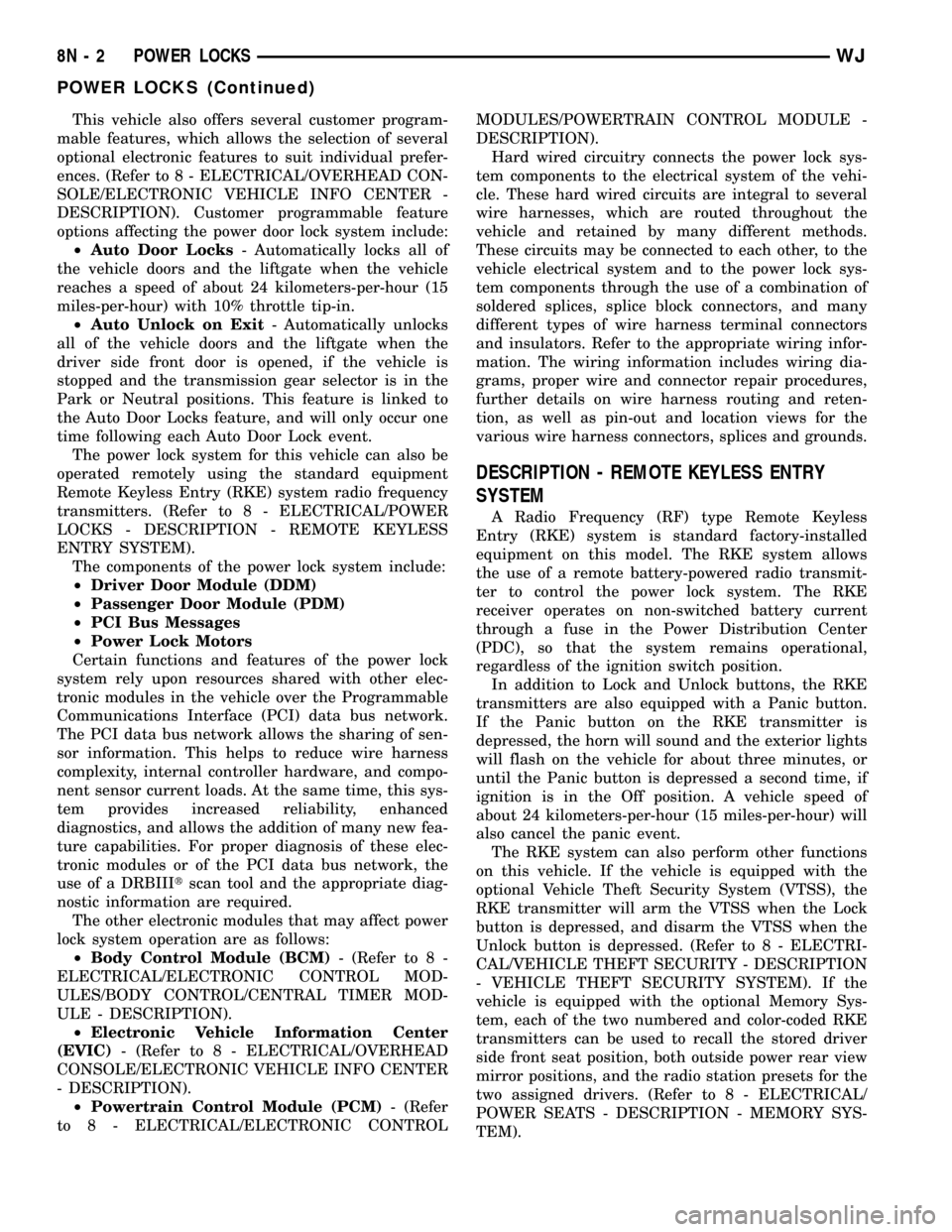
This vehicle also offers several customer program-
mable features, which allows the selection of several
optional electronic features to suit individual prefer-
ences. (Refer to 8 - ELECTRICAL/OVERHEAD CON-
SOLE/ELECTRONIC VEHICLE INFO CENTER -
DESCRIPTION). Customer programmable feature
options affecting the power door lock system include:
²Auto Door Locks- Automatically locks all of
the vehicle doors and the liftgate when the vehicle
reaches a speed of about 24 kilometers-per-hour (15
miles-per-hour) with 10% throttle tip-in.
²Auto Unlock on Exit- Automatically unlocks
all of the vehicle doors and the liftgate when the
driver side front door is opened, if the vehicle is
stopped and the transmission gear selector is in the
Park or Neutral positions. This feature is linked to
the Auto Door Locks feature, and will only occur one
time following each Auto Door Lock event.
The power lock system for this vehicle can also be
operated remotely using the standard equipment
Remote Keyless Entry (RKE) system radio frequency
transmitters. (Refer to 8 - ELECTRICAL/POWER
LOCKS - DESCRIPTION - REMOTE KEYLESS
ENTRY SYSTEM).
The components of the power lock system include:
²Driver Door Module (DDM)
²Passenger Door Module (PDM)
²PCI Bus Messages
²Power Lock Motors
Certain functions and features of the power lock
system rely upon resources shared with other elec-
tronic modules in the vehicle over the Programmable
Communications Interface (PCI) data bus network.
The PCI data bus network allows the sharing of sen-
sor information. This helps to reduce wire harness
complexity, internal controller hardware, and compo-
nent sensor current loads. At the same time, this sys-
tem provides increased reliability, enhanced
diagnostics, and allows the addition of many new fea-
ture capabilities. For proper diagnosis of these elec-
tronic modules or of the PCI data bus network, the
use of a DRBIIItscan tool and the appropriate diag-
nostic information are required.
The other electronic modules that may affect power
lock system operation are as follows:
²Body Control Module (BCM)- (Refer to 8 -
ELECTRICAL/ELECTRONIC CONTROL MOD-
ULES/BODY CONTROL/CENTRAL TIMER MOD-
ULE - DESCRIPTION).
²Electronic Vehicle Information Center
(EVIC)- (Refer to 8 - ELECTRICAL/OVERHEAD
CONSOLE/ELECTRONIC VEHICLE INFO CENTER
- DESCRIPTION).
²Powertrain Control Module (PCM)- (Refer
to 8 - ELECTRICAL/ELECTRONIC CONTROLMODULES/POWERTRAIN CONTROL MODULE -
DESCRIPTION).
Hard wired circuitry connects the power lock sys-
tem components to the electrical system of the vehi-
cle. These hard wired circuits are integral to several
wire harnesses, which are routed throughout the
vehicle and retained by many different methods.
These circuits may be connected to each other, to the
vehicle electrical system and to the power lock sys-
tem components through the use of a combination of
soldered splices, splice block connectors, and many
different types of wire harness terminal connectors
and insulators. Refer to the appropriate wiring infor-
mation. The wiring information includes wiring dia-
grams, proper wire and connector repair procedures,
further details on wire harness routing and reten-
tion, as well as pin-out and location views for the
various wire harness connectors, splices and grounds.
DESCRIPTION - REMOTE KEYLESS ENTRY
SYSTEM
A Radio Frequency (RF) type Remote Keyless
Entry (RKE) system is standard factory-installed
equipment on this model. The RKE system allows
the use of a remote battery-powered radio transmit-
ter to control the power lock system. The RKE
receiver operates on non-switched battery current
through a fuse in the Power Distribution Center
(PDC), so that the system remains operational,
regardless of the ignition switch position.
In addition to Lock and Unlock buttons, the RKE
transmitters are also equipped with a Panic button.
If the Panic button on the RKE transmitter is
depressed, the horn will sound and the exterior lights
will flash on the vehicle for about three minutes, or
until the Panic button is depressed a second time, if
ignition is in the Off position. A vehicle speed of
about 24 kilometers-per-hour (15 miles-per-hour) will
also cancel the panic event.
The RKE system can also perform other functions
on this vehicle. If the vehicle is equipped with the
optional Vehicle Theft Security System (VTSS), the
RKE transmitter will arm the VTSS when the Lock
button is depressed, and disarm the VTSS when the
Unlock button is depressed. (Refer to 8 - ELECTRI-
CAL/VEHICLE THEFT SECURITY - DESCRIPTION
- VEHICLE THEFT SECURITY SYSTEM). If the
vehicle is equipped with the optional Memory Sys-
tem, each of the two numbered and color-coded RKE
transmitters can be used to recall the stored driver
side front seat position, both outside power rear view
mirror positions, and the radio station presets for the
two assigned drivers. (Refer to 8 - ELECTRICAL/
POWER SEATS - DESCRIPTION - MEMORY SYS-
TEM).
8N - 2 POWER LOCKSWJ
POWER LOCKS (Continued)
Page 501 of 2199
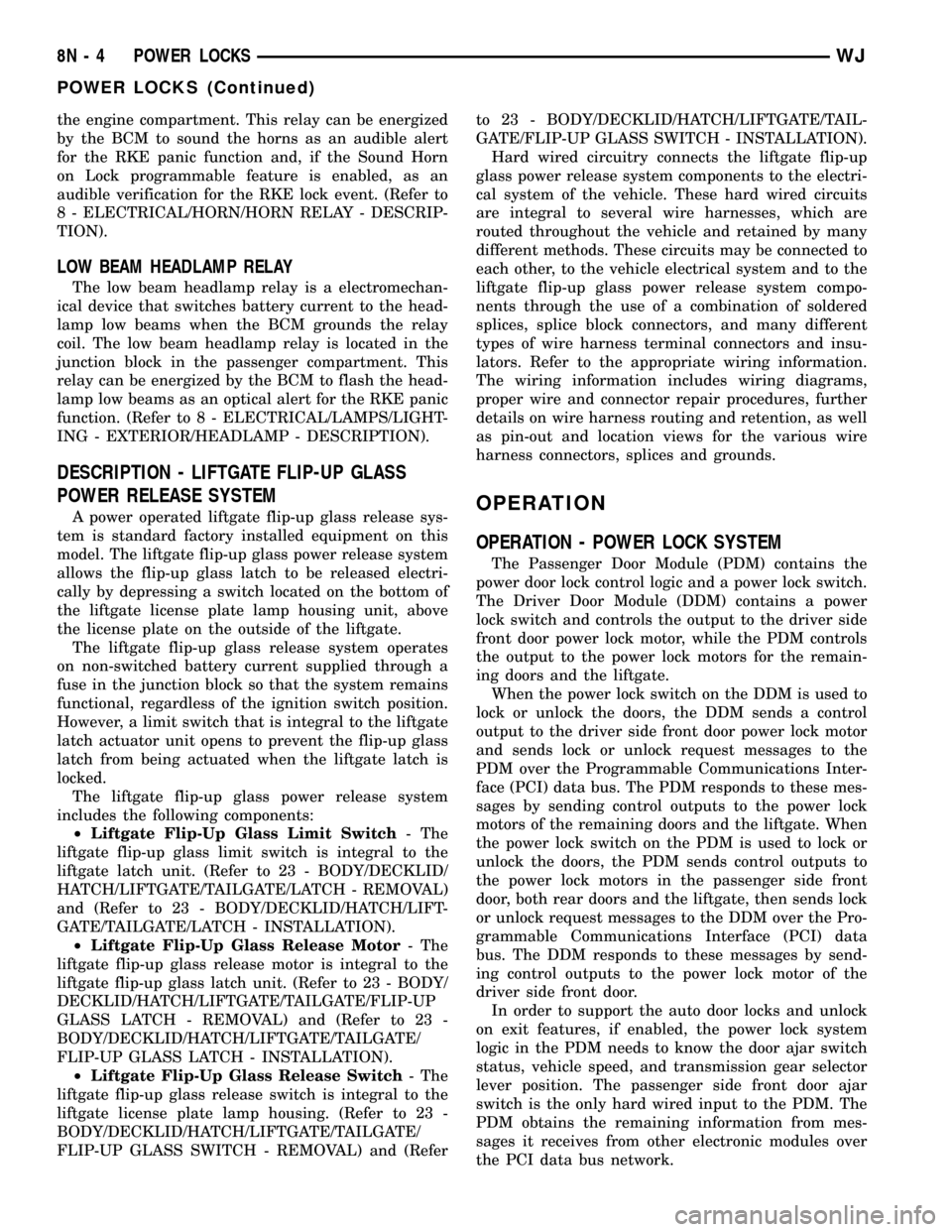
the engine compartment. This relay can be energized
by the BCM to sound the horns as an audible alert
for the RKE panic function and, if the Sound Horn
on Lock programmable feature is enabled, as an
audible verification for the RKE lock event. (Refer to
8 - ELECTRICAL/HORN/HORN RELAY - DESCRIP-
TION).
LOW BEAM HEADLAMP RELAY
The low beam headlamp relay is a electromechan-
ical device that switches battery current to the head-
lamp low beams when the BCM grounds the relay
coil. The low beam headlamp relay is located in the
junction block in the passenger compartment. This
relay can be energized by the BCM to flash the head-
lamp low beams as an optical alert for the RKE panic
function. (Refer to 8 - ELECTRICAL/LAMPS/LIGHT-
ING - EXTERIOR/HEADLAMP - DESCRIPTION).
DESCRIPTION - LIFTGATE FLIP-UP GLASS
POWER RELEASE SYSTEM
A power operated liftgate flip-up glass release sys-
tem is standard factory installed equipment on this
model. The liftgate flip-up glass power release system
allows the flip-up glass latch to be released electri-
cally by depressing a switch located on the bottom of
the liftgate license plate lamp housing unit, above
the license plate on the outside of the liftgate.
The liftgate flip-up glass release system operates
on non-switched battery current supplied through a
fuse in the junction block so that the system remains
functional, regardless of the ignition switch position.
However, a limit switch that is integral to the liftgate
latch actuator unit opens to prevent the flip-up glass
latch from being actuated when the liftgate latch is
locked.
The liftgate flip-up glass power release system
includes the following components:
²Liftgate Flip-Up Glass Limit Switch- The
liftgate flip-up glass limit switch is integral to the
liftgate latch unit. (Refer to 23 - BODY/DECKLID/
HATCH/LIFTGATE/TAILGATE/LATCH - REMOVAL)
and (Refer to 23 - BODY/DECKLID/HATCH/LIFT-
GATE/TAILGATE/LATCH - INSTALLATION).
²Liftgate Flip-Up Glass Release Motor- The
liftgate flip-up glass release motor is integral to the
liftgate flip-up glass latch unit. (Refer to 23 - BODY/
DECKLID/HATCH/LIFTGATE/TAILGATE/FLIP-UP
GLASS LATCH - REMOVAL) and (Refer to 23 -
BODY/DECKLID/HATCH/LIFTGATE/TAILGATE/
FLIP-UP GLASS LATCH - INSTALLATION).
²Liftgate Flip-Up Glass Release Switch- The
liftgate flip-up glass release switch is integral to the
liftgate license plate lamp housing. (Refer to 23 -
BODY/DECKLID/HATCH/LIFTGATE/TAILGATE/
FLIP-UP GLASS SWITCH - REMOVAL) and (Referto 23 - BODY/DECKLID/HATCH/LIFTGATE/TAIL-
GATE/FLIP-UP GLASS SWITCH - INSTALLATION).
Hard wired circuitry connects the liftgate flip-up
glass power release system components to the electri-
cal system of the vehicle. These hard wired circuits
are integral to several wire harnesses, which are
routed throughout the vehicle and retained by many
different methods. These circuits may be connected to
each other, to the vehicle electrical system and to the
liftgate flip-up glass power release system compo-
nents through the use of a combination of soldered
splices, splice block connectors, and many different
types of wire harness terminal connectors and insu-
lators. Refer to the appropriate wiring information.
The wiring information includes wiring diagrams,
proper wire and connector repair procedures, further
details on wire harness routing and retention, as well
as pin-out and location views for the various wire
harness connectors, splices and grounds.OPERATION
OPERATION - POWER LOCK SYSTEM
The Passenger Door Module (PDM) contains the
power door lock control logic and a power lock switch.
The Driver Door Module (DDM) contains a power
lock switch and controls the output to the driver side
front door power lock motor, while the PDM controls
the output to the power lock motors for the remain-
ing doors and the liftgate.
When the power lock switch on the DDM is used to
lock or unlock the doors, the DDM sends a control
output to the driver side front door power lock motor
and sends lock or unlock request messages to the
PDM over the Programmable Communications Inter-
face (PCI) data bus. The PDM responds to these mes-
sages by sending control outputs to the power lock
motors of the remaining doors and the liftgate. When
the power lock switch on the PDM is used to lock or
unlock the doors, the PDM sends control outputs to
the power lock motors in the passenger side front
door, both rear doors and the liftgate, then sends lock
or unlock request messages to the DDM over the Pro-
grammable Communications Interface (PCI) data
bus. The DDM responds to these messages by send-
ing control outputs to the power lock motor of the
driver side front door.
In order to support the auto door locks and unlock
on exit features, if enabled, the power lock system
logic in the PDM needs to know the door ajar switch
status, vehicle speed, and transmission gear selector
lever position. The passenger side front door ajar
switch is the only hard wired input to the PDM. The
PDM obtains the remaining information from mes-
sages it receives from other electronic modules over
the PCI data bus network.
8N - 4 POWER LOCKSWJ
POWER LOCKS (Continued)
Page 503 of 2199
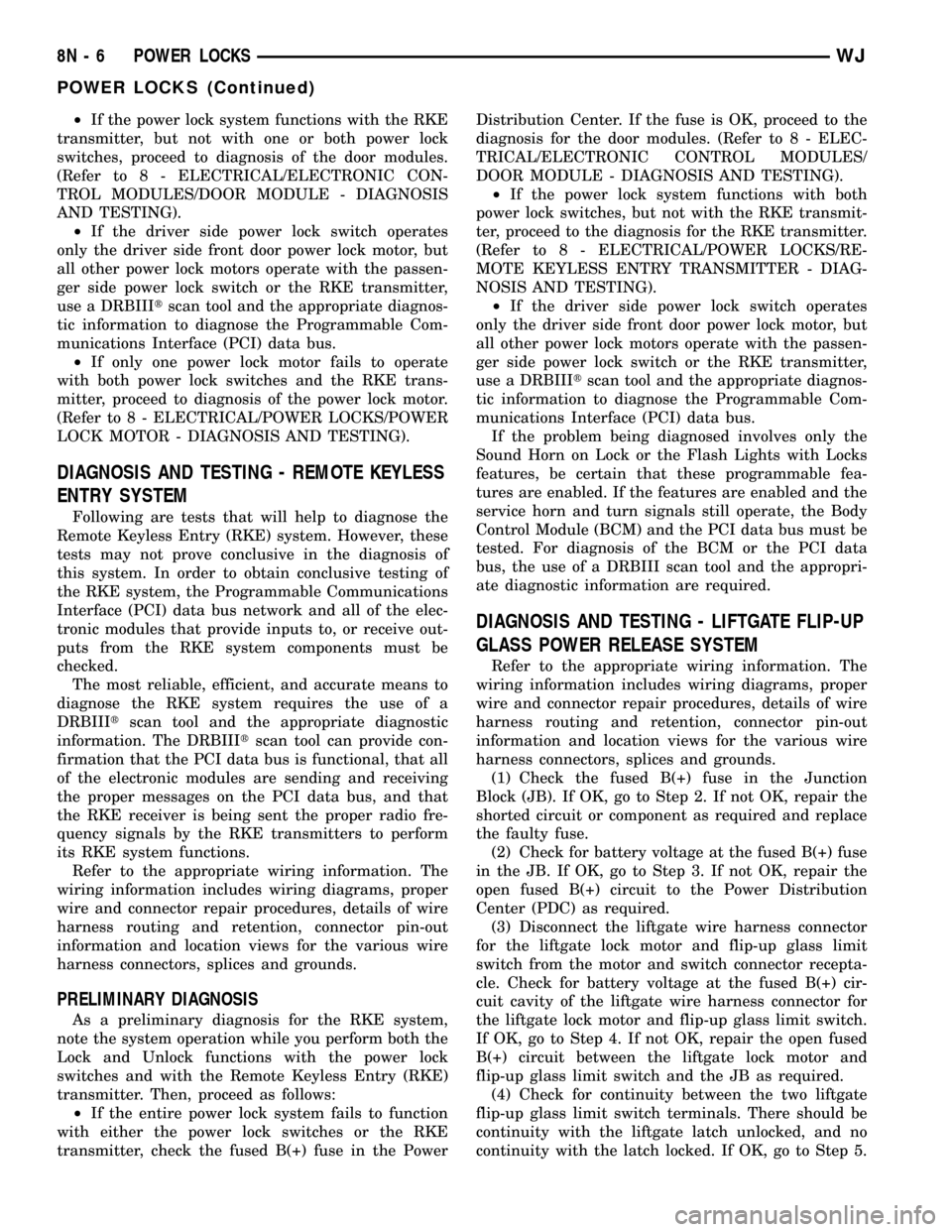
²If the power lock system functions with the RKE
transmitter, but not with one or both power lock
switches, proceed to diagnosis of the door modules.
(Refer to 8 - ELECTRICAL/ELECTRONIC CON-
TROL MODULES/DOOR MODULE - DIAGNOSIS
AND TESTING).
²If the driver side power lock switch operates
only the driver side front door power lock motor, but
all other power lock motors operate with the passen-
ger side power lock switch or the RKE transmitter,
use a DRBIIItscan tool and the appropriate diagnos-
tic information to diagnose the Programmable Com-
munications Interface (PCI) data bus.
²If only one power lock motor fails to operate
with both power lock switches and the RKE trans-
mitter, proceed to diagnosis of the power lock motor.
(Refer to 8 - ELECTRICAL/POWER LOCKS/POWER
LOCK MOTOR - DIAGNOSIS AND TESTING).
DIAGNOSIS AND TESTING - REMOTE KEYLESS
ENTRY SYSTEM
Following are tests that will help to diagnose the
Remote Keyless Entry (RKE) system. However, these
tests may not prove conclusive in the diagnosis of
this system. In order to obtain conclusive testing of
the RKE system, the Programmable Communications
Interface (PCI) data bus network and all of the elec-
tronic modules that provide inputs to, or receive out-
puts from the RKE system components must be
checked.
The most reliable, efficient, and accurate means to
diagnose the RKE system requires the use of a
DRBIIItscan tool and the appropriate diagnostic
information. The DRBIIItscan tool can provide con-
firmation that the PCI data bus is functional, that all
of the electronic modules are sending and receiving
the proper messages on the PCI data bus, and that
the RKE receiver is being sent the proper radio fre-
quency signals by the RKE transmitters to perform
its RKE system functions.
Refer to the appropriate wiring information. The
wiring information includes wiring diagrams, proper
wire and connector repair procedures, details of wire
harness routing and retention, connector pin-out
information and location views for the various wire
harness connectors, splices and grounds.
PRELIMINARY DIAGNOSIS
As a preliminary diagnosis for the RKE system,
note the system operation while you perform both the
Lock and Unlock functions with the power lock
switches and with the Remote Keyless Entry (RKE)
transmitter. Then, proceed as follows:
²If the entire power lock system fails to function
with either the power lock switches or the RKE
transmitter, check the fused B(+) fuse in the PowerDistribution Center. If the fuse is OK, proceed to the
diagnosis for the door modules. (Refer to 8 - ELEC-
TRICAL/ELECTRONIC CONTROL MODULES/
DOOR MODULE - DIAGNOSIS AND TESTING).
²If the power lock system functions with both
power lock switches, but not with the RKE transmit-
ter, proceed to the diagnosis for the RKE transmitter.
(Refer to 8 - ELECTRICAL/POWER LOCKS/RE-
MOTE KEYLESS ENTRY TRANSMITTER - DIAG-
NOSIS AND TESTING).
²If the driver side power lock switch operates
only the driver side front door power lock motor, but
all other power lock motors operate with the passen-
ger side power lock switch or the RKE transmitter,
use a DRBIIItscan tool and the appropriate diagnos-
tic information to diagnose the Programmable Com-
munications Interface (PCI) data bus.
If the problem being diagnosed involves only the
Sound Horn on Lock or the Flash Lights with Locks
features, be certain that these programmable fea-
tures are enabled. If the features are enabled and the
service horn and turn signals still operate, the Body
Control Module (BCM) and the PCI data bus must be
tested. For diagnosis of the BCM or the PCI data
bus, the use of a DRBIII scan tool and the appropri-
ate diagnostic information are required.
DIAGNOSIS AND TESTING - LIFTGATE FLIP-UP
GLASS POWER RELEASE SYSTEM
Refer to the appropriate wiring information. The
wiring information includes wiring diagrams, proper
wire and connector repair procedures, details of wire
harness routing and retention, connector pin-out
information and location views for the various wire
harness connectors, splices and grounds.
(1) Check the fused B(+) fuse in the Junction
Block (JB). If OK, go to Step 2. If not OK, repair the
shorted circuit or component as required and replace
the faulty fuse.
(2) Check for battery voltage at the fused B(+) fuse
in the JB. If OK, go to Step 3. If not OK, repair the
open fused B(+) circuit to the Power Distribution
Center (PDC) as required.
(3) Disconnect the liftgate wire harness connector
for the liftgate lock motor and flip-up glass limit
switch from the motor and switch connector recepta-
cle. Check for battery voltage at the fused B(+) cir-
cuit cavity of the liftgate wire harness connector for
the liftgate lock motor and flip-up glass limit switch.
If OK, go to Step 4. If not OK, repair the open fused
B(+) circuit between the liftgate lock motor and
flip-up glass limit switch and the JB as required.
(4) Check for continuity between the two liftgate
flip-up glass limit switch terminals. There should be
continuity with the liftgate latch unlocked, and no
continuity with the latch locked. If OK, go to Step 5.
8N - 6 POWER LOCKSWJ
POWER LOCKS (Continued)