pcm voltage JEEP GRAND CHEROKEE 2003 WJ / 2.G User Guide
[x] Cancel search | Manufacturer: JEEP, Model Year: 2003, Model line: GRAND CHEROKEE, Model: JEEP GRAND CHEROKEE 2003 WJ / 2.GPages: 2199, PDF Size: 76.01 MB
Page 359 of 2199
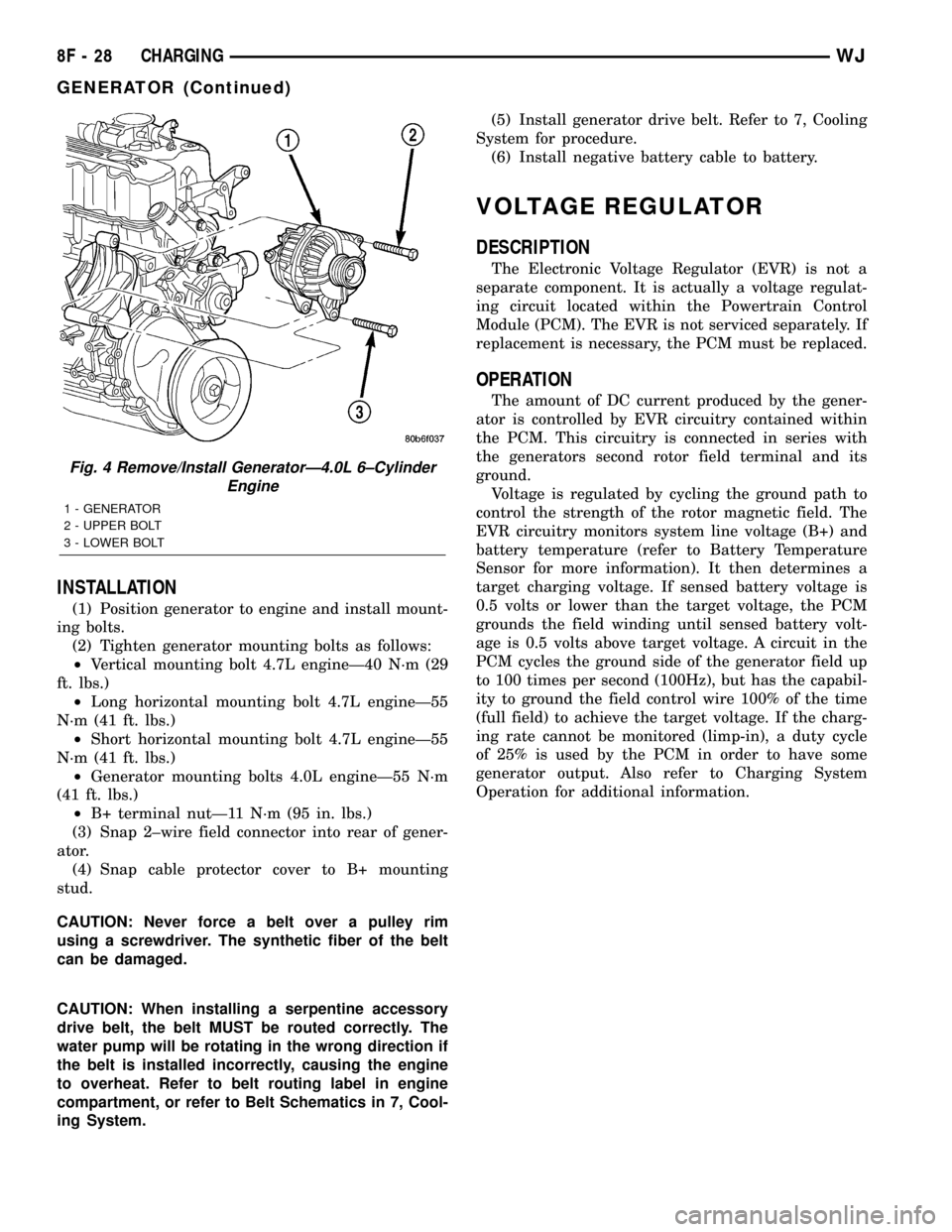
INSTALLATION
(1) Position generator to engine and install mount-
ing bolts.
(2) Tighten generator mounting bolts as follows:
²Vertical mounting bolt 4.7L engineÐ40 N´m (29
ft. lbs.)
²Long horizontal mounting bolt 4.7L engineÐ55
N´m (41 ft. lbs.)
²Short horizontal mounting bolt 4.7L engineÐ55
N´m (41 ft. lbs.)
²Generator mounting bolts 4.0L engineÐ55 N´m
(41 ft. lbs.)
²B+ terminal nutÐ11 N´m (95 in. lbs.)
(3) Snap 2±wire field connector into rear of gener-
ator.
(4) Snap cable protector cover to B+ mounting
stud.
CAUTION: Never force a belt over a pulley rim
using a screwdriver. The synthetic fiber of the belt
can be damaged.
CAUTION: When installing a serpentine accessory
drive belt, the belt MUST be routed correctly. The
water pump will be rotating in the wrong direction if
the belt is installed incorrectly, causing the engine
to overheat. Refer to belt routing label in engine
compartment, or refer to Belt Schematics in 7, Cool-
ing System.(5) Install generator drive belt. Refer to 7, Cooling
System for procedure.
(6) Install negative battery cable to battery.
VOLTAGE REGULATOR
DESCRIPTION
The Electronic Voltage Regulator (EVR) is not a
separate component. It is actually a voltage regulat-
ing circuit located within the Powertrain Control
Module (PCM). The EVR is not serviced separately. If
replacement is necessary, the PCM must be replaced.
OPERATION
The amount of DC current produced by the gener-
ator is controlled by EVR circuitry contained within
the PCM. This circuitry is connected in series with
the generators second rotor field terminal and its
ground.
Voltage is regulated by cycling the ground path to
control the strength of the rotor magnetic field. The
EVR circuitry monitors system line voltage (B+) and
battery temperature (refer to Battery Temperature
Sensor for more information). It then determines a
target charging voltage. If sensed battery voltage is
0.5 volts or lower than the target voltage, the PCM
grounds the field winding until sensed battery volt-
age is 0.5 volts above target voltage. A circuit in the
PCM cycles the ground side of the generator field up
to 100 times per second (100Hz), but has the capabil-
ity to ground the field control wire 100% of the time
(full field) to achieve the target voltage. If the charg-
ing rate cannot be monitored (limp-in), a duty cycle
of 25% is used by the PCM in order to have some
generator output. Also refer to Charging System
Operation for additional information.
Fig. 4 Remove/Install GeneratorÐ4.0L 6±Cylinder
Engine
1 - GENERATOR
2 - UPPER BOLT
3 - LOWER BOLT
8F - 28 CHARGINGWJ
GENERATOR (Continued)
Page 361 of 2199
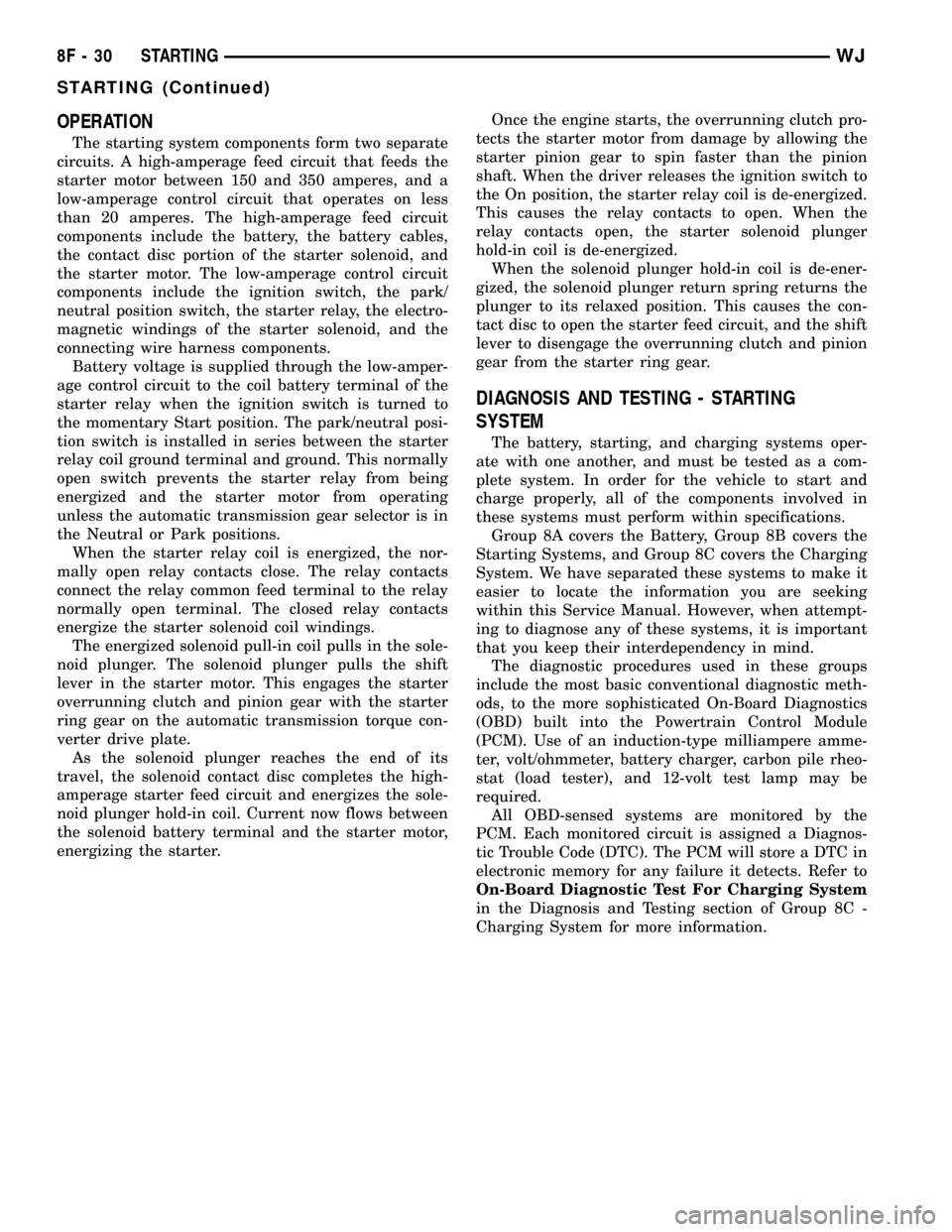
OPERATION
The starting system components form two separate
circuits. A high-amperage feed circuit that feeds the
starter motor between 150 and 350 amperes, and a
low-amperage control circuit that operates on less
than 20 amperes. The high-amperage feed circuit
components include the battery, the battery cables,
the contact disc portion of the starter solenoid, and
the starter motor. The low-amperage control circuit
components include the ignition switch, the park/
neutral position switch, the starter relay, the electro-
magnetic windings of the starter solenoid, and the
connecting wire harness components.
Battery voltage is supplied through the low-amper-
age control circuit to the coil battery terminal of the
starter relay when the ignition switch is turned to
the momentary Start position. The park/neutral posi-
tion switch is installed in series between the starter
relay coil ground terminal and ground. This normally
open switch prevents the starter relay from being
energized and the starter motor from operating
unless the automatic transmission gear selector is in
the Neutral or Park positions.
When the starter relay coil is energized, the nor-
mally open relay contacts close. The relay contacts
connect the relay common feed terminal to the relay
normally open terminal. The closed relay contacts
energize the starter solenoid coil windings.
The energized solenoid pull-in coil pulls in the sole-
noid plunger. The solenoid plunger pulls the shift
lever in the starter motor. This engages the starter
overrunning clutch and pinion gear with the starter
ring gear on the automatic transmission torque con-
verter drive plate.
As the solenoid plunger reaches the end of its
travel, the solenoid contact disc completes the high-
amperage starter feed circuit and energizes the sole-
noid plunger hold-in coil. Current now flows between
the solenoid battery terminal and the starter motor,
energizing the starter.Once the engine starts, the overrunning clutch pro-
tects the starter motor from damage by allowing the
starter pinion gear to spin faster than the pinion
shaft. When the driver releases the ignition switch to
the On position, the starter relay coil is de-energized.
This causes the relay contacts to open. When the
relay contacts open, the starter solenoid plunger
hold-in coil is de-energized.
When the solenoid plunger hold-in coil is de-ener-
gized, the solenoid plunger return spring returns the
plunger to its relaxed position. This causes the con-
tact disc to open the starter feed circuit, and the shift
lever to disengage the overrunning clutch and pinion
gear from the starter ring gear.
DIAGNOSIS AND TESTING - STARTING
SYSTEM
The battery, starting, and charging systems oper-
ate with one another, and must be tested as a com-
plete system. In order for the vehicle to start and
charge properly, all of the components involved in
these systems must perform within specifications.
Group 8A covers the Battery, Group 8B covers the
Starting Systems, and Group 8C covers the Charging
System. We have separated these systems to make it
easier to locate the information you are seeking
within this Service Manual. However, when attempt-
ing to diagnose any of these systems, it is important
that you keep their interdependency in mind.
The diagnostic procedures used in these groups
include the most basic conventional diagnostic meth-
ods, to the more sophisticated On-Board Diagnostics
(OBD) built into the Powertrain Control Module
(PCM). Use of an induction-type milliampere amme-
ter, volt/ohmmeter, battery charger, carbon pile rheo-
stat (load tester), and 12-volt test lamp may be
required.
All OBD-sensed systems are monitored by the
PCM. Each monitored circuit is assigned a Diagnos-
tic Trouble Code (DTC). The PCM will store a DTC in
electronic memory for any failure it detects. Refer to
On-Board Diagnostic Test For Charging System
in the Diagnosis and Testing section of Group 8C -
Charging System for more information.
8F - 30 STARTINGWJ
STARTING (Continued)
Page 400 of 2199
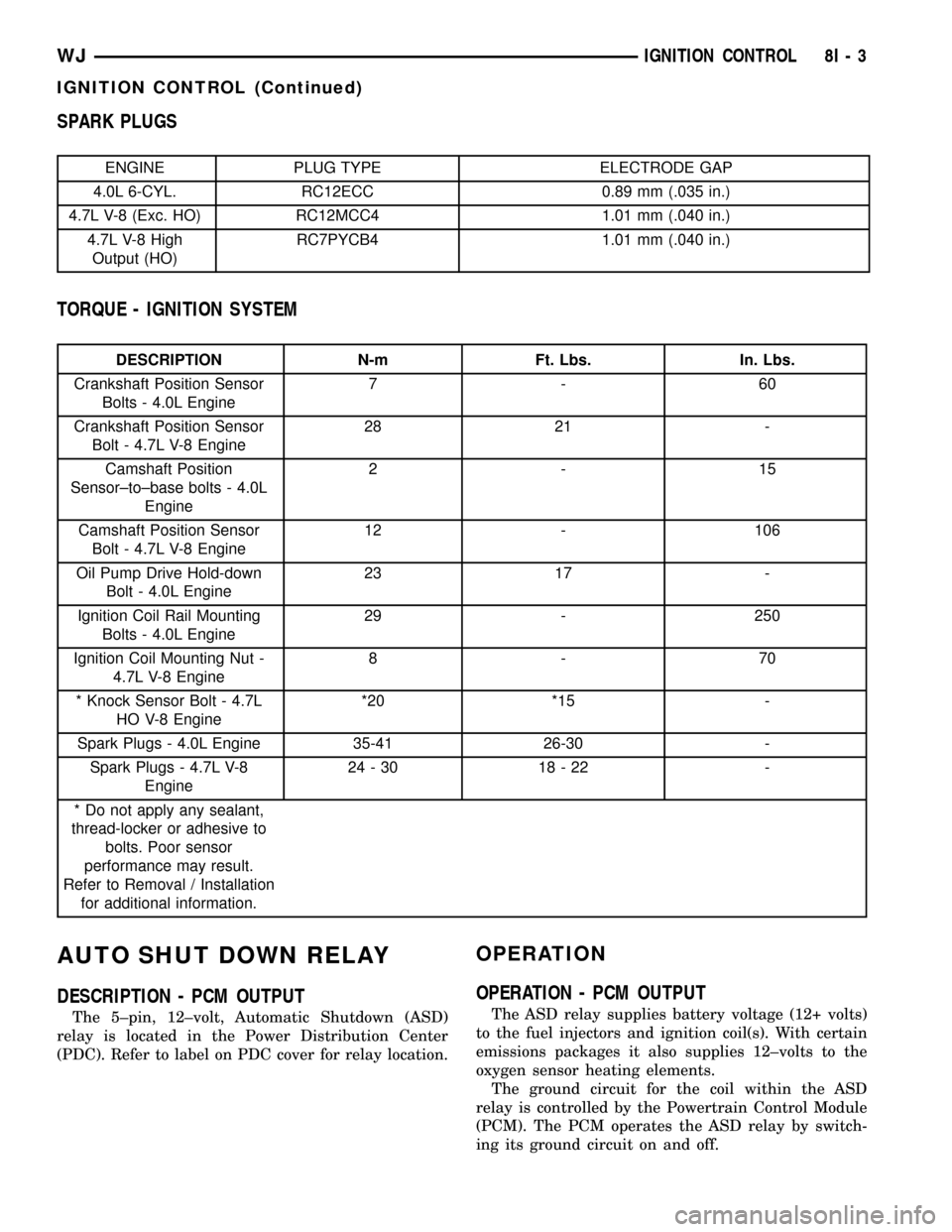
SPARK PLUGS
ENGINE PLUG TYPE ELECTRODE GAP
4.0L 6-CYL. RC12ECC 0.89 mm (.035 in.)
4.7L V-8 (Exc. HO) RC12MCC4 1.01 mm (.040 in.)
4.7L V-8 High
Output (HO)RC7PYCB4 1.01 mm (.040 in.)
TORQUE - IGNITION SYSTEM
DESCRIPTION N-m Ft. Lbs. In. Lbs.
Crankshaft Position Sensor
Bolts - 4.0L Engine7- 60
Crankshaft Position Sensor
Bolt - 4.7L V-8 Engine28 21 -
Camshaft Position
Sensor±to±base bolts - 4.0L
Engine2- 15
Camshaft Position Sensor
Bolt - 4.7L V-8 Engine12 - 106
Oil Pump Drive Hold-down
Bolt - 4.0L Engine23 17 -
Ignition Coil Rail Mounting
Bolts - 4.0L Engine29 - 250
Ignition Coil Mounting Nut -
4.7L V-8 Engine8- 70
* Knock Sensor Bolt - 4.7L
HO V-8 Engine*20 *15 -
Spark Plugs - 4.0L Engine 35-41 26-30 -
Spark Plugs - 4.7L V-8
Engine24-30 18-22 -
* Do not apply any sealant,
thread-locker or adhesive to
bolts. Poor sensor
performance may result.
Refer to Removal / Installation
for additional information.
AUTO SHUT DOWN RELAY
DESCRIPTION - PCM OUTPUT
The 5±pin, 12±volt, Automatic Shutdown (ASD)
relay is located in the Power Distribution Center
(PDC). Refer to label on PDC cover for relay location.
OPERATION
OPERATION - PCM OUTPUT
The ASD relay supplies battery voltage (12+ volts)
to the fuel injectors and ignition coil(s). With certain
emissions packages it also supplies 12±volts to the
oxygen sensor heating elements.
The ground circuit for the coil within the ASD
relay is controlled by the Powertrain Control Module
(PCM). The PCM operates the ASD relay by switch-
ing its ground circuit on and off.
WJIGNITION CONTROL 8I - 3
IGNITION CONTROL (Continued)
Page 407 of 2199
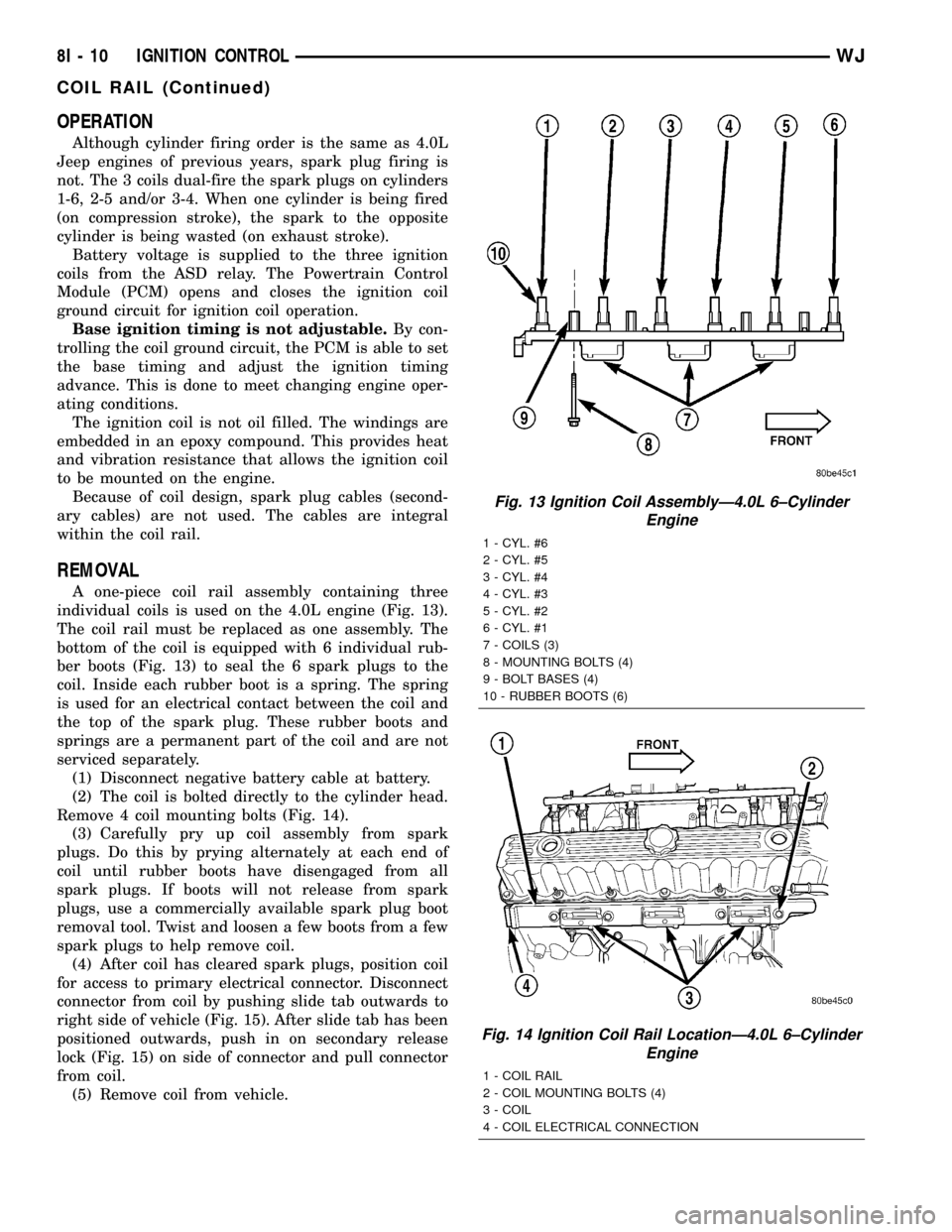
OPERATION
Although cylinder firing order is the same as 4.0L
Jeep engines of previous years, spark plug firing is
not. The 3 coils dual-fire the spark plugs on cylinders
1-6, 2-5 and/or 3-4. When one cylinder is being fired
(on compression stroke), the spark to the opposite
cylinder is being wasted (on exhaust stroke).
Battery voltage is supplied to the three ignition
coils from the ASD relay. The Powertrain Control
Module (PCM) opens and closes the ignition coil
ground circuit for ignition coil operation.
Base ignition timing is not adjustable.By con-
trolling the coil ground circuit, the PCM is able to set
the base timing and adjust the ignition timing
advance. This is done to meet changing engine oper-
ating conditions.
The ignition coil is not oil filled. The windings are
embedded in an epoxy compound. This provides heat
and vibration resistance that allows the ignition coil
to be mounted on the engine.
Because of coil design, spark plug cables (second-
ary cables) are not used. The cables are integral
within the coil rail.
REMOVAL
A one-piece coil rail assembly containing three
individual coils is used on the 4.0L engine (Fig. 13).
The coil rail must be replaced as one assembly. The
bottom of the coil is equipped with 6 individual rub-
ber boots (Fig. 13) to seal the 6 spark plugs to the
coil. Inside each rubber boot is a spring. The spring
is used for an electrical contact between the coil and
the top of the spark plug. These rubber boots and
springs are a permanent part of the coil and are not
serviced separately.
(1) Disconnect negative battery cable at battery.
(2) The coil is bolted directly to the cylinder head.
Remove 4 coil mounting bolts (Fig. 14).
(3) Carefully pry up coil assembly from spark
plugs. Do this by prying alternately at each end of
coil until rubber boots have disengaged from all
spark plugs. If boots will not release from spark
plugs, use a commercially available spark plug boot
removal tool. Twist and loosen a few boots from a few
spark plugs to help remove coil.
(4) After coil has cleared spark plugs, position coil
for access to primary electrical connector. Disconnect
connector from coil by pushing slide tab outwards to
right side of vehicle (Fig. 15). After slide tab has been
positioned outwards, push in on secondary release
lock (Fig. 15) on side of connector and pull connector
from coil.
(5) Remove coil from vehicle.
Fig. 13 Ignition Coil AssemblyÐ4.0L 6±Cylinder
Engine
1 - CYL. #6
2 - CYL. #5
3 - CYL. #4
4 - CYL. #3
5 - CYL. #2
6 - CYL. #1
7 - COILS (3)
8 - MOUNTING BOLTS (4)
9 - BOLT BASES (4)
10 - RUBBER BOOTS (6)
Fig. 14 Ignition Coil Rail LocationÐ4.0L 6±Cylinder
Engine
1 - COIL RAIL
2 - COIL MOUNTING BOLTS (4)
3 - COIL
4 - COIL ELECTRICAL CONNECTION
8I - 10 IGNITION CONTROLWJ
COIL RAIL (Continued)
Page 409 of 2199
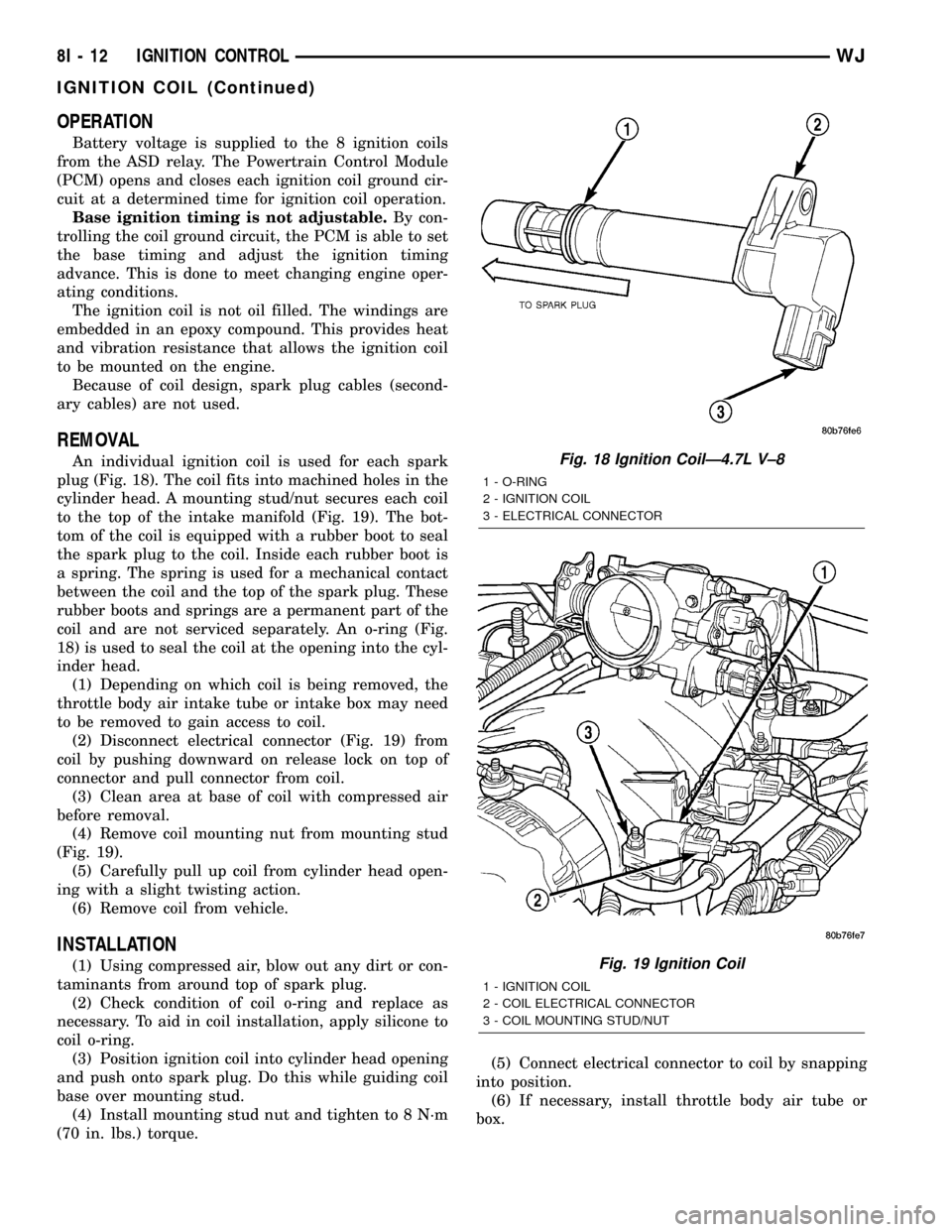
OPERATION
Battery voltage is supplied to the 8 ignition coils
from the ASD relay. The Powertrain Control Module
(PCM) opens and closes each ignition coil ground cir-
cuit at a determined time for ignition coil operation.
Base ignition timing is not adjustable.By con-
trolling the coil ground circuit, the PCM is able to set
the base timing and adjust the ignition timing
advance. This is done to meet changing engine oper-
ating conditions.
The ignition coil is not oil filled. The windings are
embedded in an epoxy compound. This provides heat
and vibration resistance that allows the ignition coil
to be mounted on the engine.
Because of coil design, spark plug cables (second-
ary cables) are not used.
REMOVAL
An individual ignition coil is used for each spark
plug (Fig. 18). The coil fits into machined holes in the
cylinder head. A mounting stud/nut secures each coil
to the top of the intake manifold (Fig. 19). The bot-
tom of the coil is equipped with a rubber boot to seal
the spark plug to the coil. Inside each rubber boot is
a spring. The spring is used for a mechanical contact
between the coil and the top of the spark plug. These
rubber boots and springs are a permanent part of the
coil and are not serviced separately. An o-ring (Fig.
18) is used to seal the coil at the opening into the cyl-
inder head.
(1) Depending on which coil is being removed, the
throttle body air intake tube or intake box may need
to be removed to gain access to coil.
(2) Disconnect electrical connector (Fig. 19) from
coil by pushing downward on release lock on top of
connector and pull connector from coil.
(3) Clean area at base of coil with compressed air
before removal.
(4) Remove coil mounting nut from mounting stud
(Fig. 19).
(5) Carefully pull up coil from cylinder head open-
ing with a slight twisting action.
(6) Remove coil from vehicle.
INSTALLATION
(1) Using compressed air, blow out any dirt or con-
taminants from around top of spark plug.
(2) Check condition of coil o-ring and replace as
necessary. To aid in coil installation, apply silicone to
coil o-ring.
(3) Position ignition coil into cylinder head opening
and push onto spark plug. Do this while guiding coil
base over mounting stud.
(4) Install mounting stud nut and tighten to 8 N´m
(70 in. lbs.) torque.(5) Connect electrical connector to coil by snapping
into position.
(6) If necessary, install throttle body air tube or
box.
Fig. 18 Ignition CoilÐ4.7L V±8
1 - O-RING
2 - IGNITION COIL
3 - ELECTRICAL CONNECTOR
Fig. 19 Ignition Coil
1 - IGNITION COIL
2 - COIL ELECTRICAL CONNECTOR
3 - COIL MOUNTING STUD/NUT
8I - 12 IGNITION CONTROLWJ
IGNITION COIL (Continued)
Page 410 of 2199
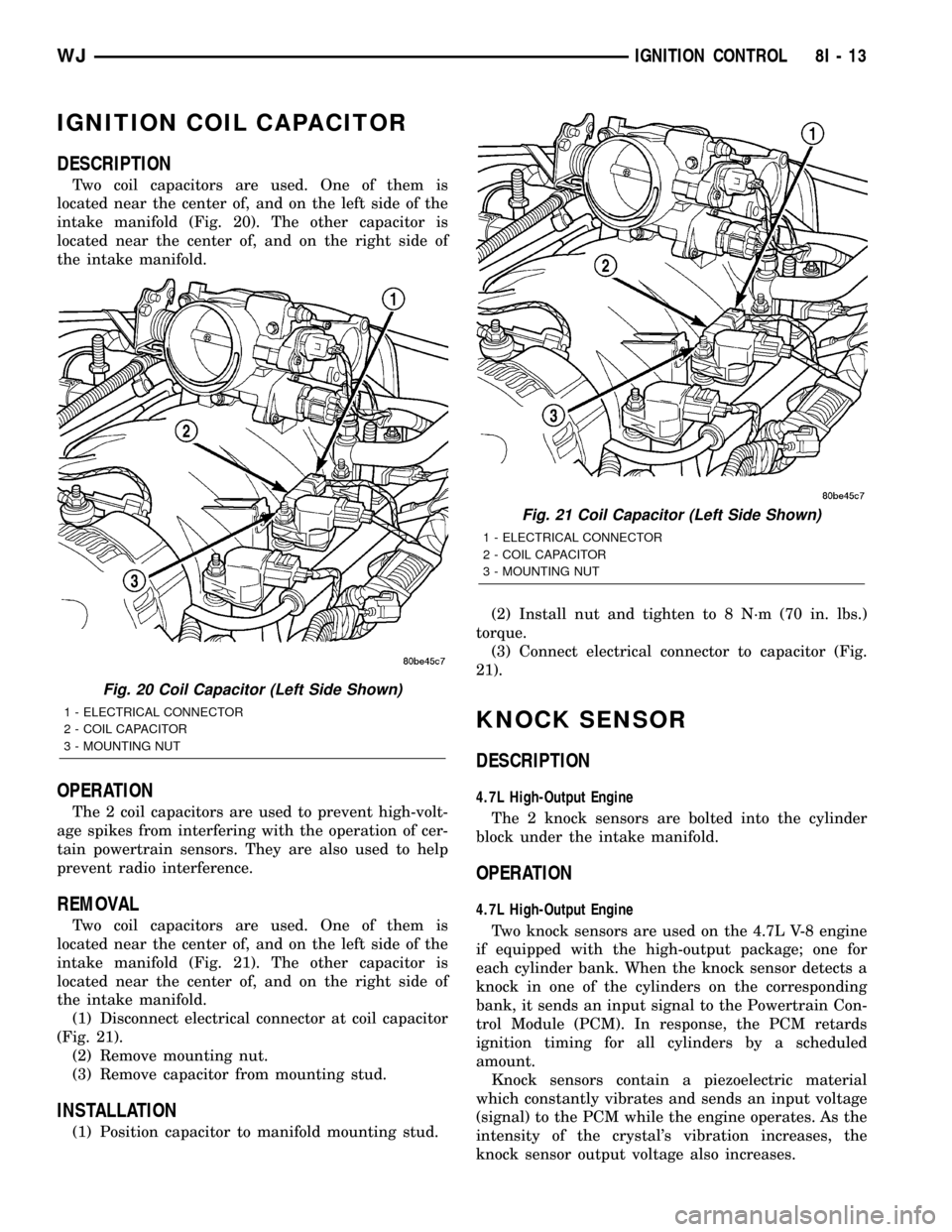
IGNITION COIL CAPACITOR
DESCRIPTION
Two coil capacitors are used. One of them is
located near the center of, and on the left side of the
intake manifold (Fig. 20). The other capacitor is
located near the center of, and on the right side of
the intake manifold.
OPERATION
The 2 coil capacitors are used to prevent high-volt-
age spikes from interfering with the operation of cer-
tain powertrain sensors. They are also used to help
prevent radio interference.
REMOVAL
Two coil capacitors are used. One of them is
located near the center of, and on the left side of the
intake manifold (Fig. 21). The other capacitor is
located near the center of, and on the right side of
the intake manifold.
(1) Disconnect electrical connector at coil capacitor
(Fig. 21).
(2) Remove mounting nut.
(3) Remove capacitor from mounting stud.
INSTALLATION
(1) Position capacitor to manifold mounting stud.(2) Install nut and tighten to 8 N´m (70 in. lbs.)
torque.
(3) Connect electrical connector to capacitor (Fig.
21).
KNOCK SENSOR
DESCRIPTION
4.7L High-Output Engine
The 2 knock sensors are bolted into the cylinder
block under the intake manifold.
OPERATION
4.7L High-Output Engine
Two knock sensors are used on the 4.7L V-8 engine
if equipped with the high-output package; one for
each cylinder bank. When the knock sensor detects a
knock in one of the cylinders on the corresponding
bank, it sends an input signal to the Powertrain Con-
trol Module (PCM). In response, the PCM retards
ignition timing for all cylinders by a scheduled
amount.
Knock sensors contain a piezoelectric material
which constantly vibrates and sends an input voltage
(signal) to the PCM while the engine operates. As the
intensity of the crystal's vibration increases, the
knock sensor output voltage also increases.
Fig. 20 Coil Capacitor (Left Side Shown)
1 - ELECTRICAL CONNECTOR
2 - COIL CAPACITOR
3 - MOUNTING NUT
Fig. 21 Coil Capacitor (Left Side Shown)
1 - ELECTRICAL CONNECTOR
2 - COIL CAPACITOR
3 - MOUNTING NUT
WJIGNITION CONTROL 8I - 13
Page 411 of 2199
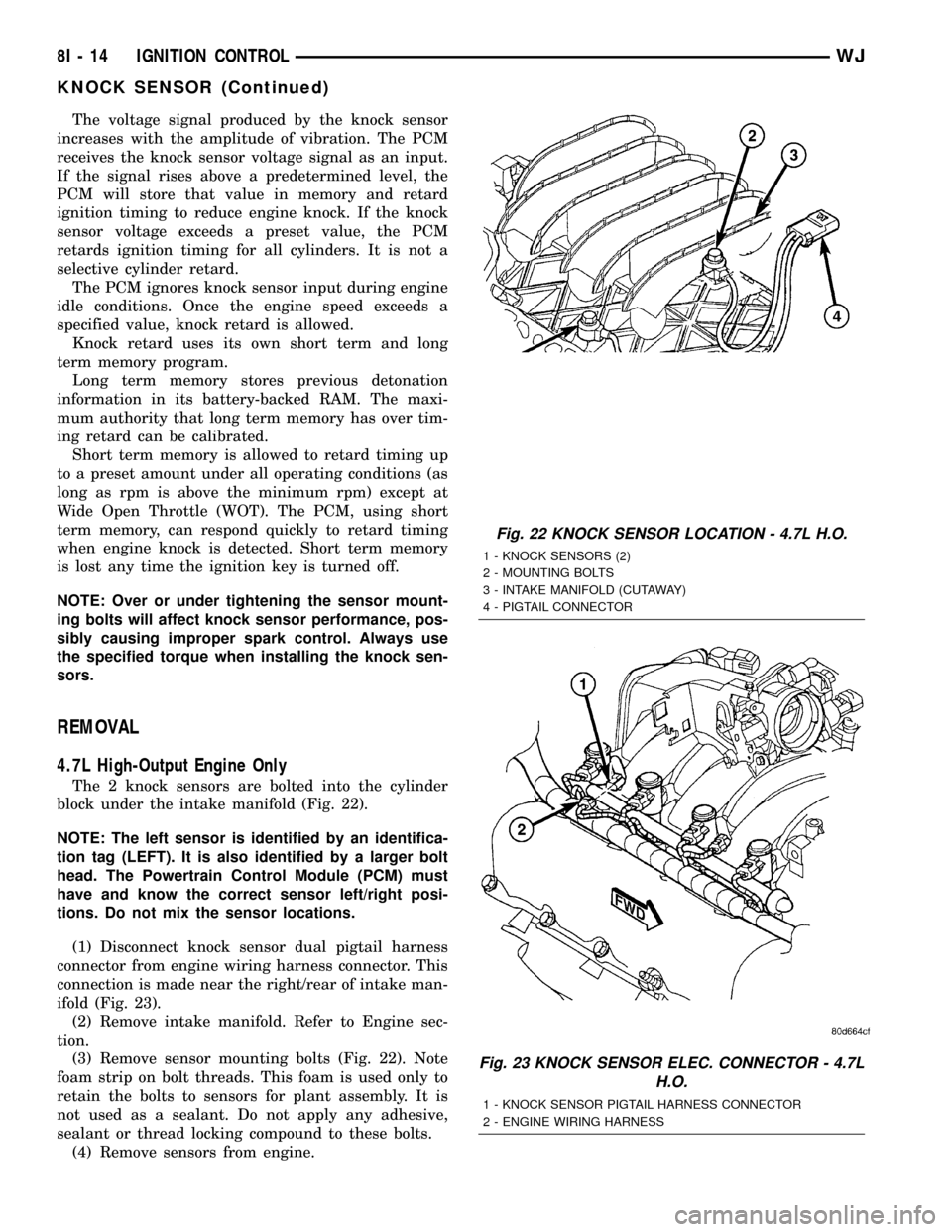
The voltage signal produced by the knock sensor
increases with the amplitude of vibration. The PCM
receives the knock sensor voltage signal as an input.
If the signal rises above a predetermined level, the
PCM will store that value in memory and retard
ignition timing to reduce engine knock. If the knock
sensor voltage exceeds a preset value, the PCM
retards ignition timing for all cylinders. It is not a
selective cylinder retard.
The PCM ignores knock sensor input during engine
idle conditions. Once the engine speed exceeds a
specified value, knock retard is allowed.
Knock retard uses its own short term and long
term memory program.
Long term memory stores previous detonation
information in its battery-backed RAM. The maxi-
mum authority that long term memory has over tim-
ing retard can be calibrated.
Short term memory is allowed to retard timing up
to a preset amount under all operating conditions (as
long as rpm is above the minimum rpm) except at
Wide Open Throttle (WOT). The PCM, using short
term memory, can respond quickly to retard timing
when engine knock is detected. Short term memory
is lost any time the ignition key is turned off.
NOTE: Over or under tightening the sensor mount-
ing bolts will affect knock sensor performance, pos-
sibly causing improper spark control. Always use
the specified torque when installing the knock sen-
sors.
REMOVAL
4.7L High-Output Engine Only
The 2 knock sensors are bolted into the cylinder
block under the intake manifold (Fig. 22).
NOTE: The left sensor is identified by an identifica-
tion tag (LEFT). It is also identified by a larger bolt
head. The Powertrain Control Module (PCM) must
have and know the correct sensor left/right posi-
tions. Do not mix the sensor locations.
(1) Disconnect knock sensor dual pigtail harness
connector from engine wiring harness connector. This
connection is made near the right/rear of intake man-
ifold (Fig. 23).
(2) Remove intake manifold. Refer to Engine sec-
tion.
(3) Remove sensor mounting bolts (Fig. 22). Note
foam strip on bolt threads. This foam is used only to
retain the bolts to sensors for plant assembly. It is
not used as a sealant. Do not apply any adhesive,
sealant or thread locking compound to these bolts.
(4) Remove sensors from engine.
Fig. 22 KNOCK SENSOR LOCATION - 4.7L H.O.
1 - KNOCK SENSORS (2)
2 - MOUNTING BOLTS
3 - INTAKE MANIFOLD (CUTAWAY)
4 - PIGTAIL CONNECTOR
Fig. 23 KNOCK SENSOR ELEC. CONNECTOR - 4.7L
H.O.
1 - KNOCK SENSOR PIGTAIL HARNESS CONNECTOR
2 - ENGINE WIRING HARNESS
8I - 14 IGNITION CONTROLWJ
KNOCK SENSOR (Continued)
Page 432 of 2199
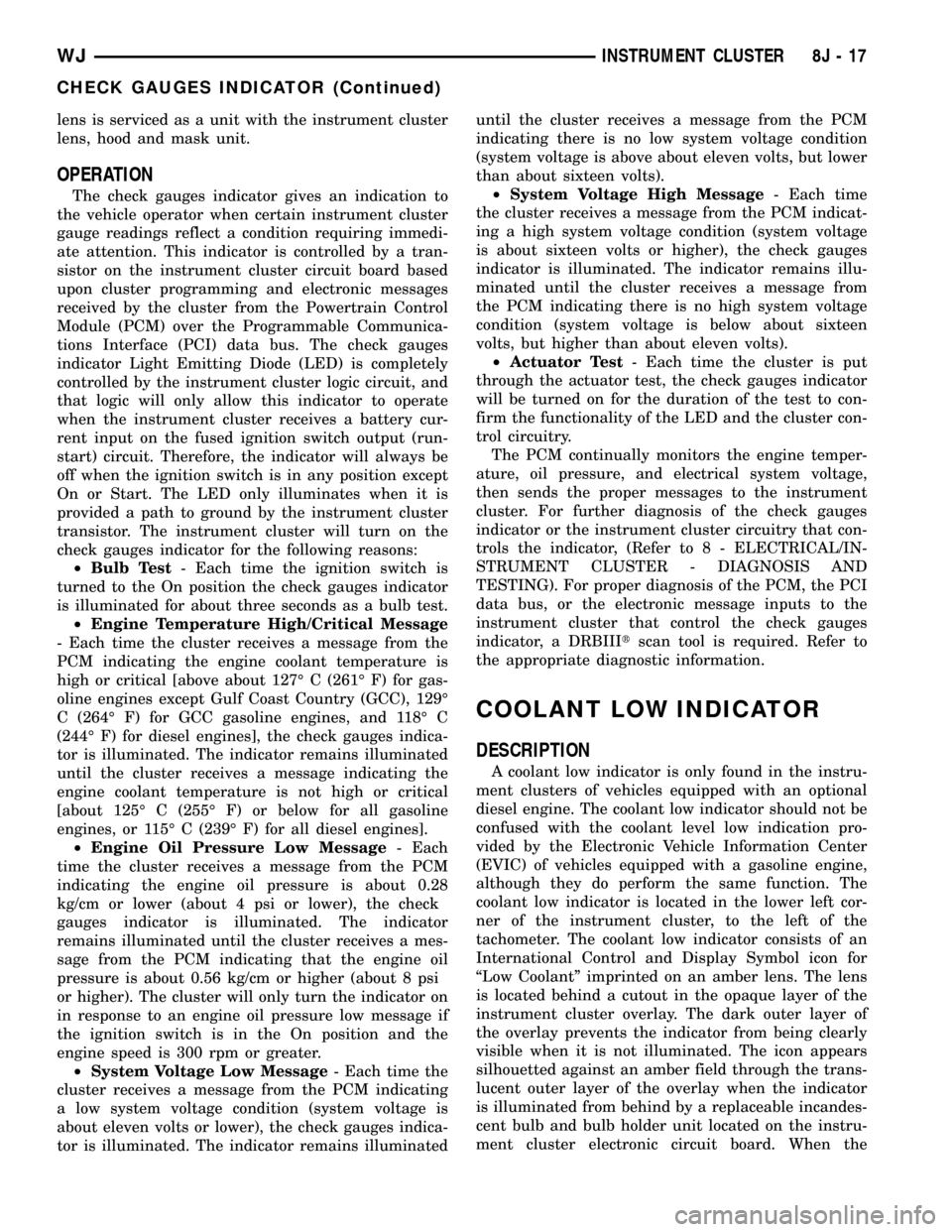
lens is serviced as a unit with the instrument cluster
lens, hood and mask unit.
OPERATION
The check gauges indicator gives an indication to
the vehicle operator when certain instrument cluster
gauge readings reflect a condition requiring immedi-
ate attention. This indicator is controlled by a tran-
sistor on the instrument cluster circuit board based
upon cluster programming and electronic messages
received by the cluster from the Powertrain Control
Module (PCM) over the Programmable Communica-
tions Interface (PCI) data bus. The check gauges
indicator Light Emitting Diode (LED) is completely
controlled by the instrument cluster logic circuit, and
that logic will only allow this indicator to operate
when the instrument cluster receives a battery cur-
rent input on the fused ignition switch output (run-
start) circuit. Therefore, the indicator will always be
off when the ignition switch is in any position except
On or Start. The LED only illuminates when it is
provided a path to ground by the instrument cluster
transistor. The instrument cluster will turn on the
check gauges indicator for the following reasons:
²Bulb Test- Each time the ignition switch is
turned to the On position the check gauges indicator
is illuminated for about three seconds as a bulb test.
²Engine Temperature High/Critical Message
- Each time the cluster receives a message from the
PCM indicating the engine coolant temperature is
high or critical [above about 127É C (261É F) for gas-
oline engines except Gulf Coast Country (GCC), 129É
C (264É F) for GCC gasoline engines, and 118É C
(244É F) for diesel engines], the check gauges indica-
tor is illuminated. The indicator remains illuminated
until the cluster receives a message indicating the
engine coolant temperature is not high or critical
[about 125É C (255É F) or below for all gasoline
engines, or 115É C (239É F) for all diesel engines].
²Engine Oil Pressure Low Message- Each
time the cluster receives a message from the PCM
indicating the engine oil pressure is about 0.28
kg/cm or lower (about 4 psi or lower), the check
gauges indicator is illuminated. The indicator
remains illuminated until the cluster receives a mes-
sage from the PCM indicating that the engine oil
pressure is about 0.56 kg/cm or higher (about 8 psi
or higher). The cluster will only turn the indicator on
in response to an engine oil pressure low message if
the ignition switch is in the On position and the
engine speed is 300 rpm or greater.
²System Voltage Low Message- Each time the
cluster receives a message from the PCM indicating
a low system voltage condition (system voltage is
about eleven volts or lower), the check gauges indica-
tor is illuminated. The indicator remains illuminateduntil the cluster receives a message from the PCM
indicating there is no low system voltage condition
(system voltage is above about eleven volts, but lower
than about sixteen volts).
²System Voltage High Message- Each time
the cluster receives a message from the PCM indicat-
ing a high system voltage condition (system voltage
is about sixteen volts or higher), the check gauges
indicator is illuminated. The indicator remains illu-
minated until the cluster receives a message from
the PCM indicating there is no high system voltage
condition (system voltage is below about sixteen
volts, but higher than about eleven volts).
²Actuator Test- Each time the cluster is put
through the actuator test, the check gauges indicator
will be turned on for the duration of the test to con-
firm the functionality of the LED and the cluster con-
trol circuitry.
The PCM continually monitors the engine temper-
ature, oil pressure, and electrical system voltage,
then sends the proper messages to the instrument
cluster. For further diagnosis of the check gauges
indicator or the instrument cluster circuitry that con-
trols the indicator, (Refer to 8 - ELECTRICAL/IN-
STRUMENT CLUSTER - DIAGNOSIS AND
TESTING). For proper diagnosis of the PCM, the PCI
data bus, or the electronic message inputs to the
instrument cluster that control the check gauges
indicator, a DRBIIItscan tool is required. Refer to
the appropriate diagnostic information.
COOLANT LOW INDICATOR
DESCRIPTION
A coolant low indicator is only found in the instru-
ment clusters of vehicles equipped with an optional
diesel engine. The coolant low indicator should not be
confused with the coolant level low indication pro-
vided by the Electronic Vehicle Information Center
(EVIC) of vehicles equipped with a gasoline engine,
although they do perform the same function. The
coolant low indicator is located in the lower left cor-
ner of the instrument cluster, to the left of the
tachometer. The coolant low indicator consists of an
International Control and Display Symbol icon for
ªLow Coolantº imprinted on an amber lens. The lens
is located behind a cutout in the opaque layer of the
instrument cluster overlay. The dark outer layer of
the overlay prevents the indicator from being clearly
visible when it is not illuminated. The icon appears
silhouetted against an amber field through the trans-
lucent outer layer of the overlay when the indicator
is illuminated from behind by a replaceable incandes-
cent bulb and bulb holder unit located on the instru-
ment cluster electronic circuit board. When the
WJINSTRUMENT CLUSTER 8J - 17
CHECK GAUGES INDICATOR (Continued)
Page 449 of 2199
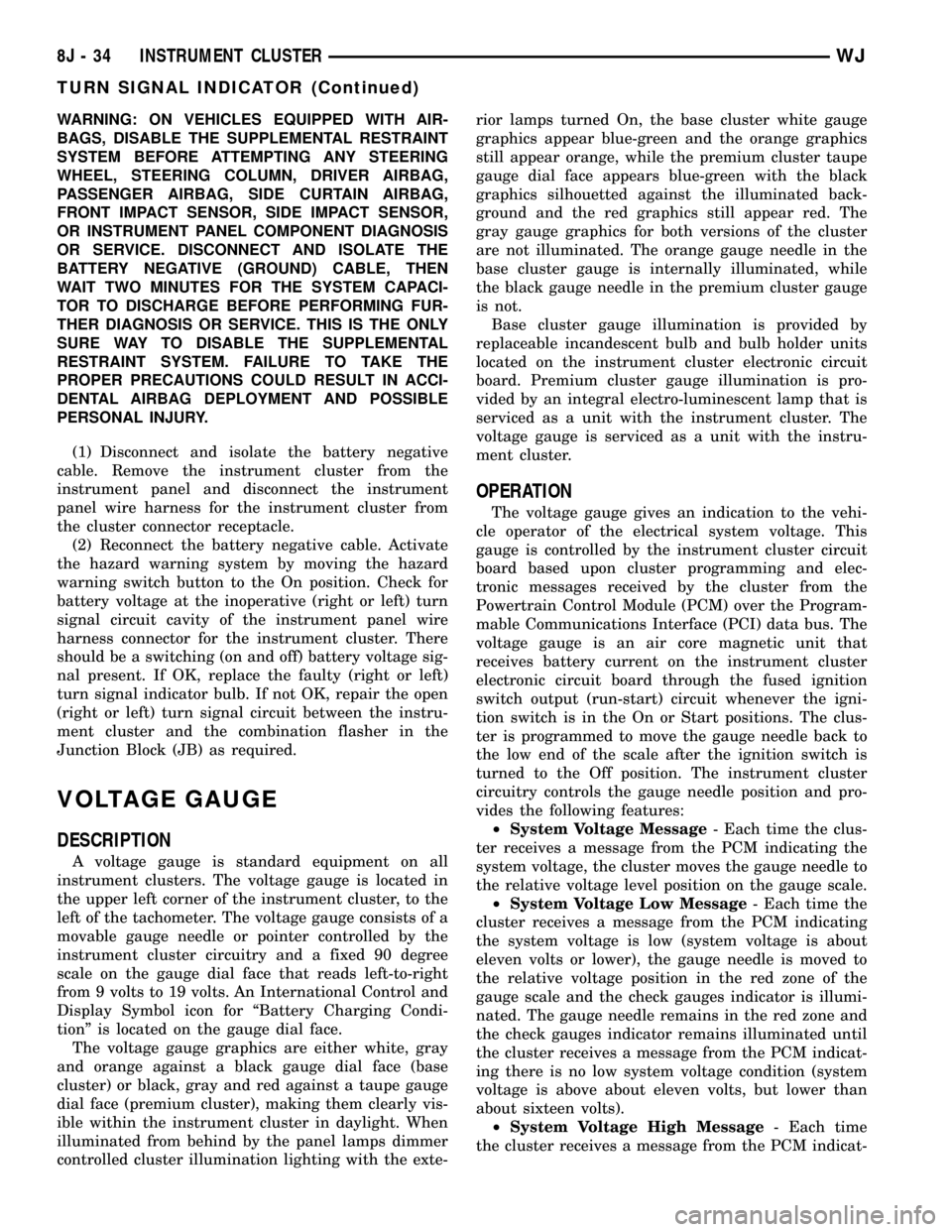
WARNING: ON VEHICLES EQUIPPED WITH AIR-
BAGS, DISABLE THE SUPPLEMENTAL RESTRAINT
SYSTEM BEFORE ATTEMPTING ANY STEERING
WHEEL, STEERING COLUMN, DRIVER AIRBAG,
PASSENGER AIRBAG, SIDE CURTAIN AIRBAG,
FRONT IMPACT SENSOR, SIDE IMPACT SENSOR,
OR INSTRUMENT PANEL COMPONENT DIAGNOSIS
OR SERVICE. DISCONNECT AND ISOLATE THE
BATTERY NEGATIVE (GROUND) CABLE, THEN
WAIT TWO MINUTES FOR THE SYSTEM CAPACI-
TOR TO DISCHARGE BEFORE PERFORMING FUR-
THER DIAGNOSIS OR SERVICE. THIS IS THE ONLY
SURE WAY TO DISABLE THE SUPPLEMENTAL
RESTRAINT SYSTEM. FAILURE TO TAKE THE
PROPER PRECAUTIONS COULD RESULT IN ACCI-
DENTAL AIRBAG DEPLOYMENT AND POSSIBLE
PERSONAL INJURY.
(1) Disconnect and isolate the battery negative
cable. Remove the instrument cluster from the
instrument panel and disconnect the instrument
panel wire harness for the instrument cluster from
the cluster connector receptacle.
(2) Reconnect the battery negative cable. Activate
the hazard warning system by moving the hazard
warning switch button to the On position. Check for
battery voltage at the inoperative (right or left) turn
signal circuit cavity of the instrument panel wire
harness connector for the instrument cluster. There
should be a switching (on and off) battery voltage sig-
nal present. If OK, replace the faulty (right or left)
turn signal indicator bulb. If not OK, repair the open
(right or left) turn signal circuit between the instru-
ment cluster and the combination flasher in the
Junction Block (JB) as required.
VOLTAGE GAUGE
DESCRIPTION
A voltage gauge is standard equipment on all
instrument clusters. The voltage gauge is located in
the upper left corner of the instrument cluster, to the
left of the tachometer. The voltage gauge consists of a
movable gauge needle or pointer controlled by the
instrument cluster circuitry and a fixed 90 degree
scale on the gauge dial face that reads left-to-right
from 9 volts to 19 volts. An International Control and
Display Symbol icon for ªBattery Charging Condi-
tionº is located on the gauge dial face.
The voltage gauge graphics are either white, gray
and orange against a black gauge dial face (base
cluster) or black, gray and red against a taupe gauge
dial face (premium cluster), making them clearly vis-
ible within the instrument cluster in daylight. When
illuminated from behind by the panel lamps dimmer
controlled cluster illumination lighting with the exte-rior lamps turned On, the base cluster white gauge
graphics appear blue-green and the orange graphics
still appear orange, while the premium cluster taupe
gauge dial face appears blue-green with the black
graphics silhouetted against the illuminated back-
ground and the red graphics still appear red. The
gray gauge graphics for both versions of the cluster
are not illuminated. The orange gauge needle in the
base cluster gauge is internally illuminated, while
the black gauge needle in the premium cluster gauge
is not.
Base cluster gauge illumination is provided by
replaceable incandescent bulb and bulb holder units
located on the instrument cluster electronic circuit
board. Premium cluster gauge illumination is pro-
vided by an integral electro-luminescent lamp that is
serviced as a unit with the instrument cluster. The
voltage gauge is serviced as a unit with the instru-
ment cluster.
OPERATION
The voltage gauge gives an indication to the vehi-
cle operator of the electrical system voltage. This
gauge is controlled by the instrument cluster circuit
board based upon cluster programming and elec-
tronic messages received by the cluster from the
Powertrain Control Module (PCM) over the Program-
mable Communications Interface (PCI) data bus. The
voltage gauge is an air core magnetic unit that
receives battery current on the instrument cluster
electronic circuit board through the fused ignition
switch output (run-start) circuit whenever the igni-
tion switch is in the On or Start positions. The clus-
ter is programmed to move the gauge needle back to
the low end of the scale after the ignition switch is
turned to the Off position. The instrument cluster
circuitry controls the gauge needle position and pro-
vides the following features:
²System Voltage Message- Each time the clus-
ter receives a message from the PCM indicating the
system voltage, the cluster moves the gauge needle to
the relative voltage level position on the gauge scale.
²System Voltage Low Message- Each time the
cluster receives a message from the PCM indicating
the system voltage is low (system voltage is about
eleven volts or lower), the gauge needle is moved to
the relative voltage position in the red zone of the
gauge scale and the check gauges indicator is illumi-
nated. The gauge needle remains in the red zone and
the check gauges indicator remains illuminated until
the cluster receives a message from the PCM indicat-
ing there is no low system voltage condition (system
voltage is above about eleven volts, but lower than
about sixteen volts).
²System Voltage High Message- Each time
the cluster receives a message from the PCM indicat-
8J - 34 INSTRUMENT CLUSTERWJ
TURN SIGNAL INDICATOR (Continued)
Page 450 of 2199
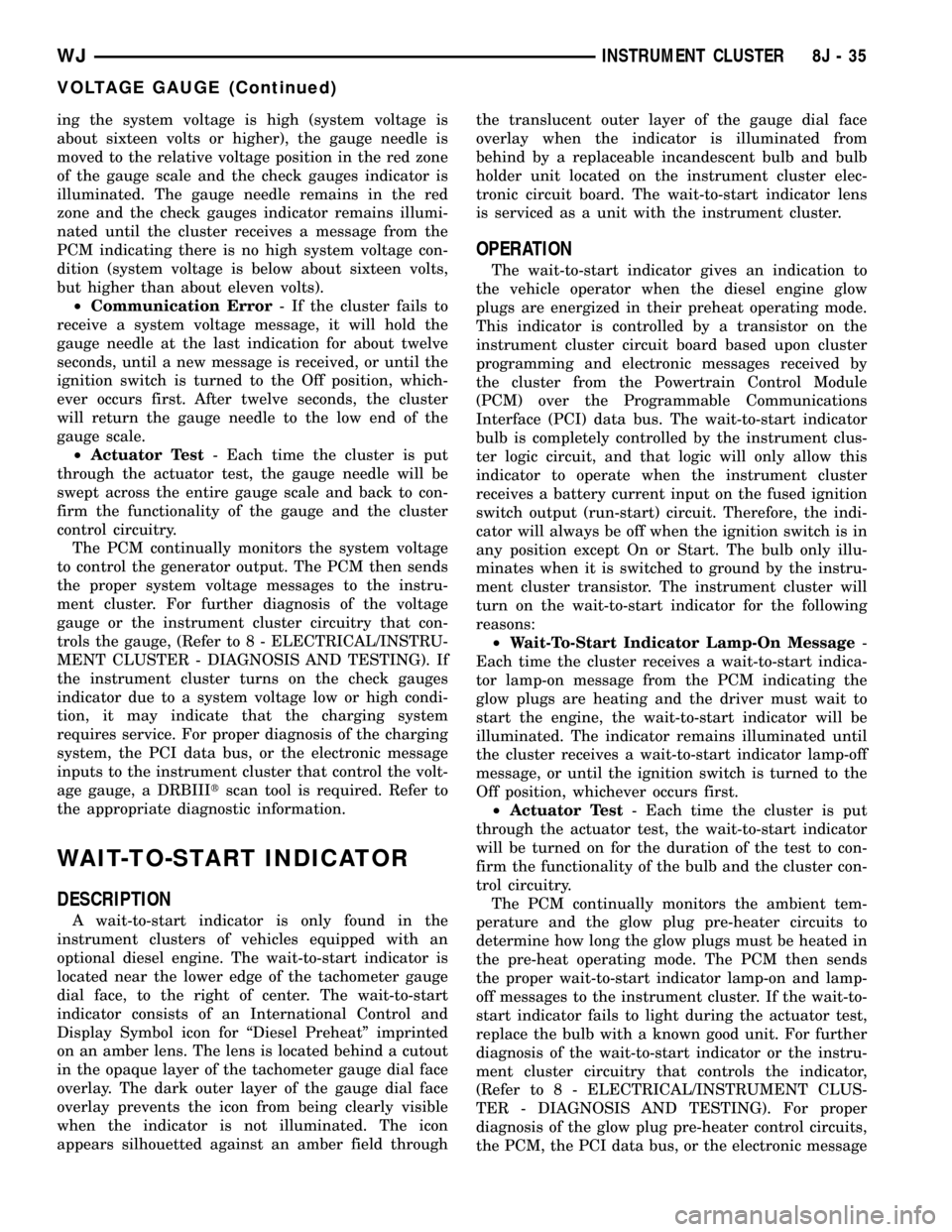
ing the system voltage is high (system voltage is
about sixteen volts or higher), the gauge needle is
moved to the relative voltage position in the red zone
of the gauge scale and the check gauges indicator is
illuminated. The gauge needle remains in the red
zone and the check gauges indicator remains illumi-
nated until the cluster receives a message from the
PCM indicating there is no high system voltage con-
dition (system voltage is below about sixteen volts,
but higher than about eleven volts).
²Communication Error- If the cluster fails to
receive a system voltage message, it will hold the
gauge needle at the last indication for about twelve
seconds, until a new message is received, or until the
ignition switch is turned to the Off position, which-
ever occurs first. After twelve seconds, the cluster
will return the gauge needle to the low end of the
gauge scale.
²Actuator Test- Each time the cluster is put
through the actuator test, the gauge needle will be
swept across the entire gauge scale and back to con-
firm the functionality of the gauge and the cluster
control circuitry.
The PCM continually monitors the system voltage
to control the generator output. The PCM then sends
the proper system voltage messages to the instru-
ment cluster. For further diagnosis of the voltage
gauge or the instrument cluster circuitry that con-
trols the gauge, (Refer to 8 - ELECTRICAL/INSTRU-
MENT CLUSTER - DIAGNOSIS AND TESTING). If
the instrument cluster turns on the check gauges
indicator due to a system voltage low or high condi-
tion, it may indicate that the charging system
requires service. For proper diagnosis of the charging
system, the PCI data bus, or the electronic message
inputs to the instrument cluster that control the volt-
age gauge, a DRBIIItscan tool is required. Refer to
the appropriate diagnostic information.
WAIT-TO-START INDICATOR
DESCRIPTION
A wait-to-start indicator is only found in the
instrument clusters of vehicles equipped with an
optional diesel engine. The wait-to-start indicator is
located near the lower edge of the tachometer gauge
dial face, to the right of center. The wait-to-start
indicator consists of an International Control and
Display Symbol icon for ªDiesel Preheatº imprinted
on an amber lens. The lens is located behind a cutout
in the opaque layer of the tachometer gauge dial face
overlay. The dark outer layer of the gauge dial face
overlay prevents the icon from being clearly visible
when the indicator is not illuminated. The icon
appears silhouetted against an amber field throughthe translucent outer layer of the gauge dial face
overlay when the indicator is illuminated from
behind by a replaceable incandescent bulb and bulb
holder unit located on the instrument cluster elec-
tronic circuit board. The wait-to-start indicator lens
is serviced as a unit with the instrument cluster.
OPERATION
The wait-to-start indicator gives an indication to
the vehicle operator when the diesel engine glow
plugs are energized in their preheat operating mode.
This indicator is controlled by a transistor on the
instrument cluster circuit board based upon cluster
programming and electronic messages received by
the cluster from the Powertrain Control Module
(PCM) over the Programmable Communications
Interface (PCI) data bus. The wait-to-start indicator
bulb is completely controlled by the instrument clus-
ter logic circuit, and that logic will only allow this
indicator to operate when the instrument cluster
receives a battery current input on the fused ignition
switch output (run-start) circuit. Therefore, the indi-
cator will always be off when the ignition switch is in
any position except On or Start. The bulb only illu-
minates when it is switched to ground by the instru-
ment cluster transistor. The instrument cluster will
turn on the wait-to-start indicator for the following
reasons:
²Wait-To-Start Indicator Lamp-On Message-
Each time the cluster receives a wait-to-start indica-
tor lamp-on message from the PCM indicating the
glow plugs are heating and the driver must wait to
start the engine, the wait-to-start indicator will be
illuminated. The indicator remains illuminated until
the cluster receives a wait-to-start indicator lamp-off
message, or until the ignition switch is turned to the
Off position, whichever occurs first.
²Actuator Test- Each time the cluster is put
through the actuator test, the wait-to-start indicator
will be turned on for the duration of the test to con-
firm the functionality of the bulb and the cluster con-
trol circuitry.
The PCM continually monitors the ambient tem-
perature and the glow plug pre-heater circuits to
determine how long the glow plugs must be heated in
the pre-heat operating mode. The PCM then sends
the proper wait-to-start indicator lamp-on and lamp-
off messages to the instrument cluster. If the wait-to-
start indicator fails to light during the actuator test,
replace the bulb with a known good unit. For further
diagnosis of the wait-to-start indicator or the instru-
ment cluster circuitry that controls the indicator,
(Refer to 8 - ELECTRICAL/INSTRUMENT CLUS-
TER - DIAGNOSIS AND TESTING). For proper
diagnosis of the glow plug pre-heater control circuits,
the PCM, the PCI data bus, or the electronic message
WJINSTRUMENT CLUSTER 8J - 35
VOLTAGE GAUGE (Continued)