JEEP GRAND CHEROKEE 2003 WJ / 2.G Workshop Manual
Manufacturer: JEEP, Model Year: 2003, Model line: GRAND CHEROKEE, Model: JEEP GRAND CHEROKEE 2003 WJ / 2.GPages: 2199, PDF Size: 76.01 MB
Page 2191 of 2199
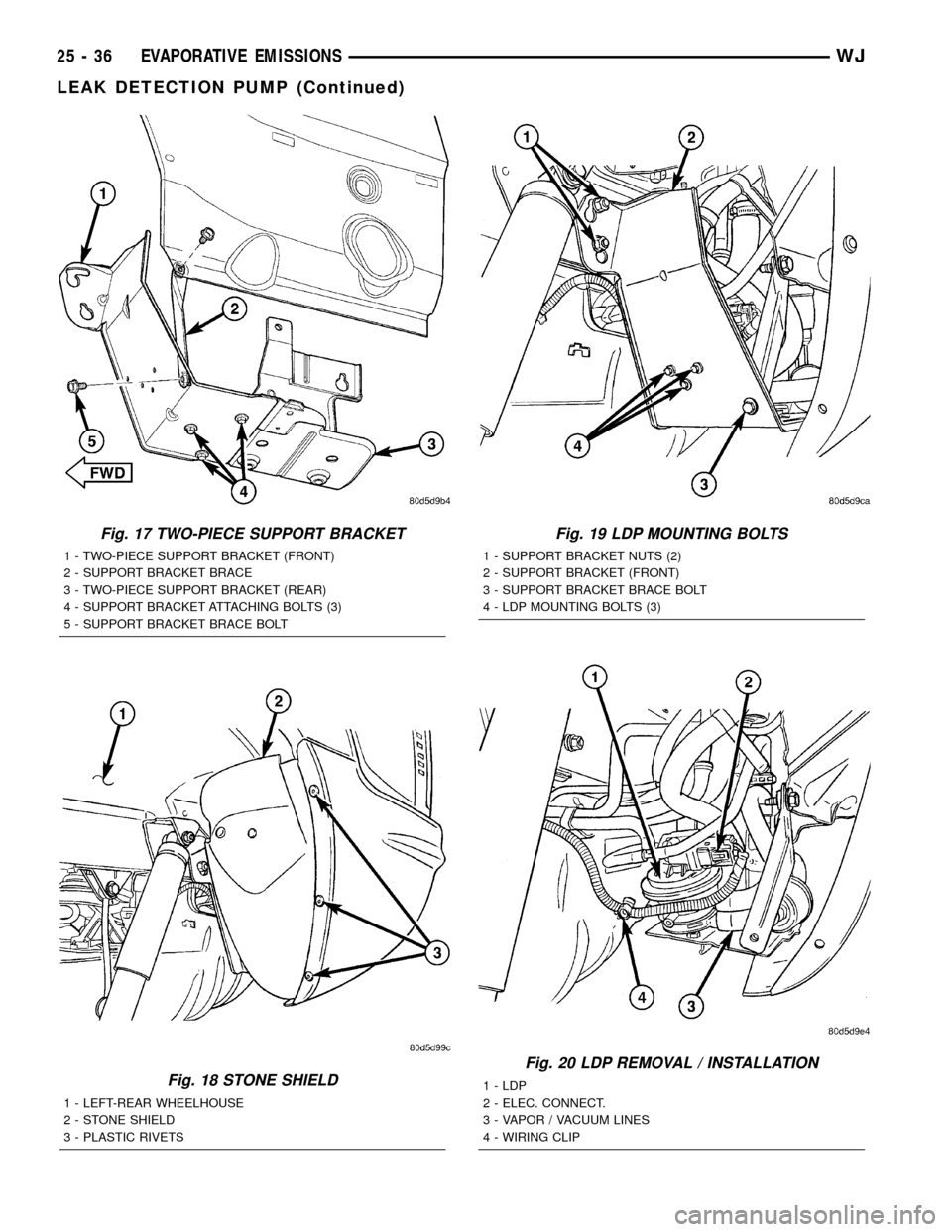
Fig. 17 TWO-PIECE SUPPORT BRACKET
1 - TWO-PIECE SUPPORT BRACKET (FRONT)
2 - SUPPORT BRACKET BRACE
3 - TWO-PIECE SUPPORT BRACKET (REAR)
4 - SUPPORT BRACKET ATTACHING BOLTS (3)
5 - SUPPORT BRACKET BRACE BOLT
Fig. 18 STONE SHIELD
1 - LEFT-REAR WHEELHOUSE
2 - STONE SHIELD
3 - PLASTIC RIVETS
Fig. 19 LDP MOUNTING BOLTS
1 - SUPPORT BRACKET NUTS (2)
2 - SUPPORT BRACKET (FRONT)
3 - SUPPORT BRACKET BRACE BOLT
4 - LDP MOUNTING BOLTS (3)
Fig. 20 LDP REMOVAL / INSTALLATION
1 - LDP
2 - ELEC. CONNECT.
3 - VAPOR / VACUUM LINES
4 - WIRING CLIP
25 - 36 EVAPORATIVE EMISSIONSWJ
LEAK DETECTION PUMP (Continued)
Page 2192 of 2199
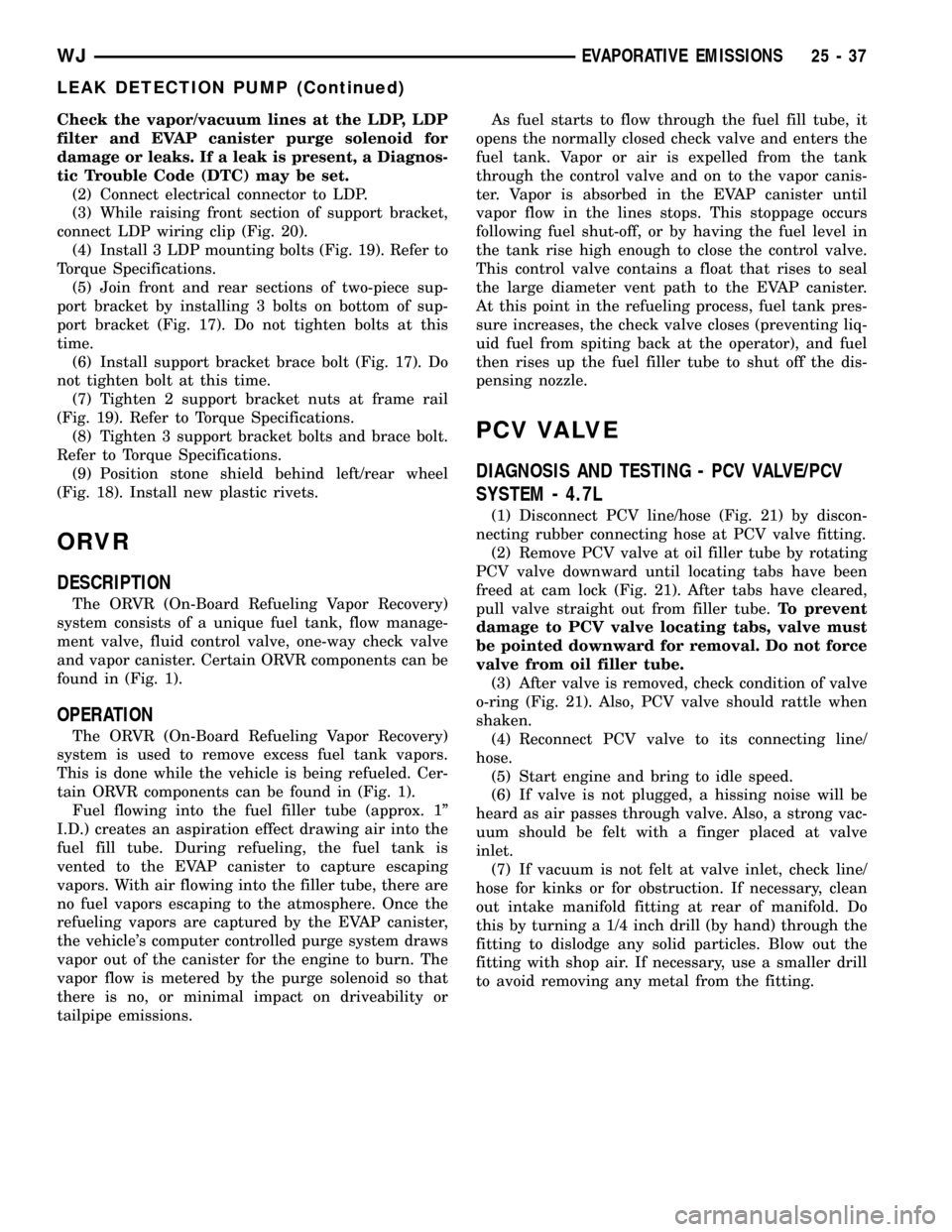
Check the vapor/vacuum lines at the LDP, LDP
filter and EVAP canister purge solenoid for
damage or leaks. If a leak is present, a Diagnos-
tic Trouble Code (DTC) may be set.
(2) Connect electrical connector to LDP.
(3) While raising front section of support bracket,
connect LDP wiring clip (Fig. 20).
(4) Install 3 LDP mounting bolts (Fig. 19). Refer to
Torque Specifications.
(5) Join front and rear sections of two-piece sup-
port bracket by installing 3 bolts on bottom of sup-
port bracket (Fig. 17). Do not tighten bolts at this
time.
(6) Install support bracket brace bolt (Fig. 17). Do
not tighten bolt at this time.
(7) Tighten 2 support bracket nuts at frame rail
(Fig. 19). Refer to Torque Specifications.
(8) Tighten 3 support bracket bolts and brace bolt.
Refer to Torque Specifications.
(9) Position stone shield behind left/rear wheel
(Fig. 18). Install new plastic rivets.
ORVR
DESCRIPTION
The ORVR (On-Board Refueling Vapor Recovery)
system consists of a unique fuel tank, flow manage-
ment valve, fluid control valve, one-way check valve
and vapor canister. Certain ORVR components can be
found in (Fig. 1).
OPERATION
The ORVR (On-Board Refueling Vapor Recovery)
system is used to remove excess fuel tank vapors.
This is done while the vehicle is being refueled. Cer-
tain ORVR components can be found in (Fig. 1).
Fuel flowing into the fuel filler tube (approx. 1º
I.D.) creates an aspiration effect drawing air into the
fuel fill tube. During refueling, the fuel tank is
vented to the EVAP canister to capture escaping
vapors. With air flowing into the filler tube, there are
no fuel vapors escaping to the atmosphere. Once the
refueling vapors are captured by the EVAP canister,
the vehicle's computer controlled purge system draws
vapor out of the canister for the engine to burn. The
vapor flow is metered by the purge solenoid so that
there is no, or minimal impact on driveability or
tailpipe emissions.As fuel starts to flow through the fuel fill tube, it
opens the normally closed check valve and enters the
fuel tank. Vapor or air is expelled from the tank
through the control valve and on to the vapor canis-
ter. Vapor is absorbed in the EVAP canister until
vapor flow in the lines stops. This stoppage occurs
following fuel shut-off, or by having the fuel level in
the tank rise high enough to close the control valve.
This control valve contains a float that rises to seal
the large diameter vent path to the EVAP canister.
At this point in the refueling process, fuel tank pres-
sure increases, the check valve closes (preventing liq-
uid fuel from spiting back at the operator), and fuel
then rises up the fuel filler tube to shut off the dis-
pensing nozzle.
PCV VALVE
DIAGNOSIS AND TESTING - PCV VALVE/PCV
SYSTEM - 4.7L
(1) Disconnect PCV line/hose (Fig. 21) by discon-
necting rubber connecting hose at PCV valve fitting.
(2) Remove PCV valve at oil filler tube by rotating
PCV valve downward until locating tabs have been
freed at cam lock (Fig. 21). After tabs have cleared,
pull valve straight out from filler tube.To prevent
damage to PCV valve locating tabs, valve must
be pointed downward for removal. Do not force
valve from oil filler tube.
(3) After valve is removed, check condition of valve
o-ring (Fig. 21). Also, PCV valve should rattle when
shaken.
(4) Reconnect PCV valve to its connecting line/
hose.
(5) Start engine and bring to idle speed.
(6) If valve is not plugged, a hissing noise will be
heard as air passes through valve. Also, a strong vac-
uum should be felt with a finger placed at valve
inlet.
(7) If vacuum is not felt at valve inlet, check line/
hose for kinks or for obstruction. If necessary, clean
out intake manifold fitting at rear of manifold. Do
this by turning a 1/4 inch drill (by hand) through the
fitting to dislodge any solid particles. Blow out the
fitting with shop air. If necessary, use a smaller drill
to avoid removing any metal from the fitting.
WJEVAPORATIVE EMISSIONS 25 - 37
LEAK DETECTION PUMP (Continued)
Page 2193 of 2199
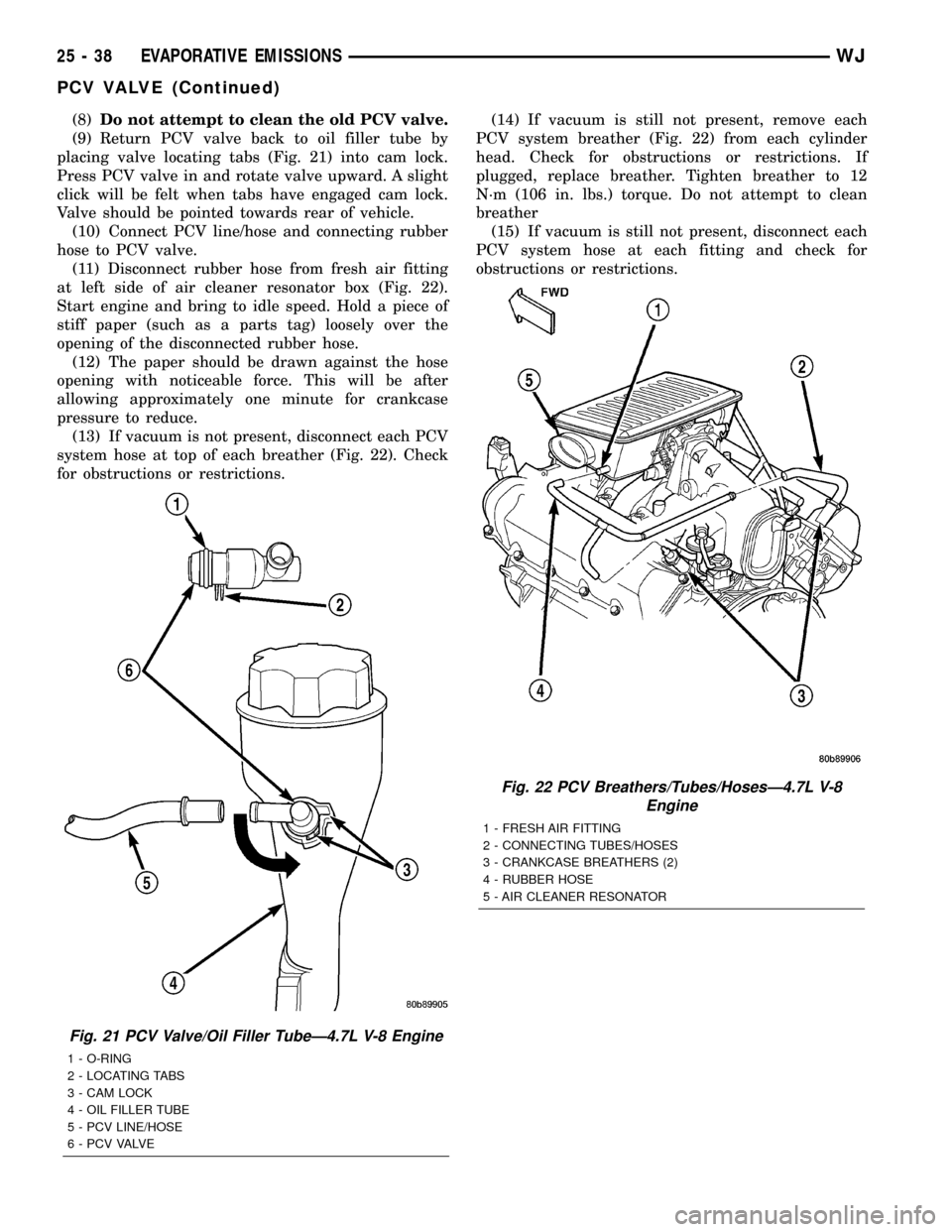
(8)Do not attempt to clean the old PCV valve.
(9) Return PCV valve back to oil filler tube by
placing valve locating tabs (Fig. 21) into cam lock.
Press PCV valve in and rotate valve upward. A slight
click will be felt when tabs have engaged cam lock.
Valve should be pointed towards rear of vehicle.
(10) Connect PCV line/hose and connecting rubber
hose to PCV valve.
(11) Disconnect rubber hose from fresh air fitting
at left side of air cleaner resonator box (Fig. 22).
Start engine and bring to idle speed. Hold a piece of
stiff paper (such as a parts tag) loosely over the
opening of the disconnected rubber hose.
(12) The paper should be drawn against the hose
opening with noticeable force. This will be after
allowing approximately one minute for crankcase
pressure to reduce.
(13) If vacuum is not present, disconnect each PCV
system hose at top of each breather (Fig. 22). Check
for obstructions or restrictions.(14) If vacuum is still not present, remove each
PCV system breather (Fig. 22) from each cylinder
head. Check for obstructions or restrictions. If
plugged, replace breather. Tighten breather to 12
N´m (106 in. lbs.) torque. Do not attempt to clean
breather
(15) If vacuum is still not present, disconnect each
PCV system hose at each fitting and check for
obstructions or restrictions.
Fig. 21 PCV Valve/Oil Filler TubeÐ4.7L V-8 Engine
1 - O-RING
2 - LOCATING TABS
3 - CAM LOCK
4 - OIL FILLER TUBE
5 - PCV LINE/HOSE
6 - P C V VA LV E
Fig. 22 PCV Breathers/Tubes/HosesÐ4.7L V-8
Engine
1 - FRESH AIR FITTING
2 - CONNECTING TUBES/HOSES
3 - CRANKCASE BREATHERS (2)
4 - RUBBER HOSE
5 - AIR CLEANER RESONATOR
25 - 38 EVAPORATIVE EMISSIONSWJ
PCV VALVE (Continued)
Page 2194 of 2199
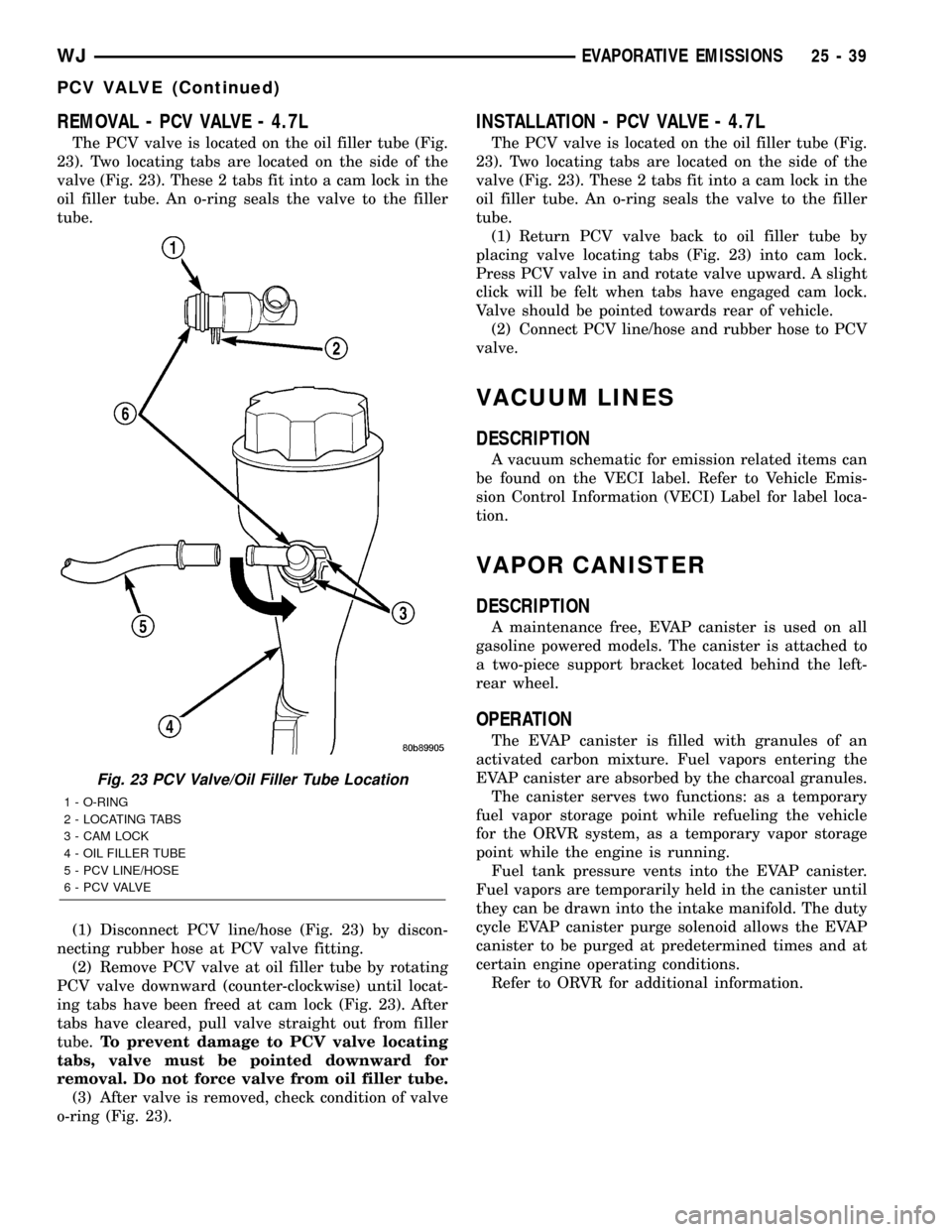
REMOVAL - PCV VALVE - 4.7L
The PCV valve is located on the oil filler tube (Fig.
23). Two locating tabs are located on the side of the
valve (Fig. 23). These 2 tabs fit into a cam lock in the
oil filler tube. An o-ring seals the valve to the filler
tube.
(1) Disconnect PCV line/hose (Fig. 23) by discon-
necting rubber hose at PCV valve fitting.
(2) Remove PCV valve at oil filler tube by rotating
PCV valve downward (counter-clockwise) until locat-
ing tabs have been freed at cam lock (Fig. 23). After
tabs have cleared, pull valve straight out from filler
tube.To prevent damage to PCV valve locating
tabs, valve must be pointed downward for
removal. Do not force valve from oil filler tube.
(3) After valve is removed, check condition of valve
o-ring (Fig. 23).
INSTALLATION - PCV VALVE - 4.7L
The PCV valve is located on the oil filler tube (Fig.
23). Two locating tabs are located on the side of the
valve (Fig. 23). These 2 tabs fit into a cam lock in the
oil filler tube. An o-ring seals the valve to the filler
tube.
(1) Return PCV valve back to oil filler tube by
placing valve locating tabs (Fig. 23) into cam lock.
Press PCV valve in and rotate valve upward. A slight
click will be felt when tabs have engaged cam lock.
Valve should be pointed towards rear of vehicle.
(2) Connect PCV line/hose and rubber hose to PCV
valve.
VACUUM LINES
DESCRIPTION
A vacuum schematic for emission related items can
be found on the VECI label. Refer to Vehicle Emis-
sion Control Information (VECI) Label for label loca-
tion.
VAPOR CANISTER
DESCRIPTION
A maintenance free, EVAP canister is used on all
gasoline powered models. The canister is attached to
a two-piece support bracket located behind the left-
rear wheel.
OPERATION
The EVAP canister is filled with granules of an
activated carbon mixture. Fuel vapors entering the
EVAP canister are absorbed by the charcoal granules.
The canister serves two functions: as a temporary
fuel vapor storage point while refueling the vehicle
for the ORVR system, as a temporary vapor storage
point while the engine is running.
Fuel tank pressure vents into the EVAP canister.
Fuel vapors are temporarily held in the canister until
they can be drawn into the intake manifold. The duty
cycle EVAP canister purge solenoid allows the EVAP
canister to be purged at predetermined times and at
certain engine operating conditions.
Refer to ORVR for additional information.
Fig. 23 PCV Valve/Oil Filler Tube Location
1 - O-RING
2 - LOCATING TABS
3 - CAM LOCK
4 - OIL FILLER TUBE
5 - PCV LINE/HOSE
6 - P C V VA LV E
WJEVAPORATIVE EMISSIONS 25 - 39
PCV VALVE (Continued)
Page 2195 of 2199
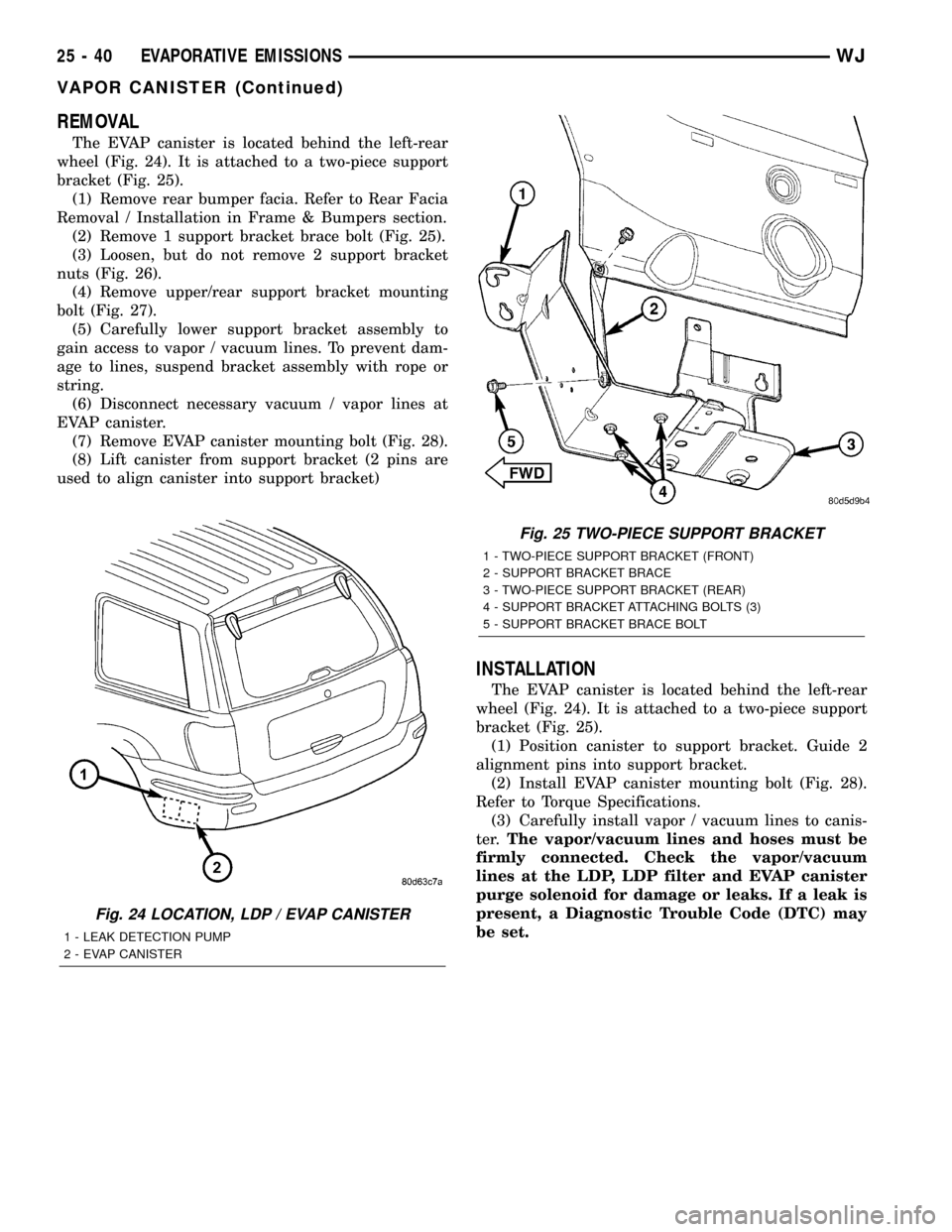
REMOVAL
The EVAP canister is located behind the left-rear
wheel (Fig. 24). It is attached to a two-piece support
bracket (Fig. 25).
(1) Remove rear bumper facia. Refer to Rear Facia
Removal / Installation in Frame & Bumpers section.
(2) Remove 1 support bracket brace bolt (Fig. 25).
(3) Loosen, but do not remove 2 support bracket
nuts (Fig. 26).
(4) Remove upper/rear support bracket mounting
bolt (Fig. 27).
(5) Carefully lower support bracket assembly to
gain access to vapor / vacuum lines. To prevent dam-
age to lines, suspend bracket assembly with rope or
string.
(6) Disconnect necessary vacuum / vapor lines at
EVAP canister.
(7) Remove EVAP canister mounting bolt (Fig. 28).
(8) Lift canister from support bracket (2 pins are
used to align canister into support bracket)
INSTALLATION
The EVAP canister is located behind the left-rear
wheel (Fig. 24). It is attached to a two-piece support
bracket (Fig. 25).
(1) Position canister to support bracket. Guide 2
alignment pins into support bracket.
(2) Install EVAP canister mounting bolt (Fig. 28).
Refer to Torque Specifications.
(3) Carefully install vapor / vacuum lines to canis-
ter.The vapor/vacuum lines and hoses must be
firmly connected. Check the vapor/vacuum
lines at the LDP, LDP filter and EVAP canister
purge solenoid for damage or leaks. If a leak is
present, a Diagnostic Trouble Code (DTC) may
be set.
Fig. 24 LOCATION, LDP / EVAP CANISTER
1 - LEAK DETECTION PUMP
2 - EVAP CANISTER
Fig. 25 TWO-PIECE SUPPORT BRACKET
1 - TWO-PIECE SUPPORT BRACKET (FRONT)
2 - SUPPORT BRACKET BRACE
3 - TWO-PIECE SUPPORT BRACKET (REAR)
4 - SUPPORT BRACKET ATTACHING BOLTS (3)
5 - SUPPORT BRACKET BRACE BOLT
25 - 40 EVAPORATIVE EMISSIONSWJ
VAPOR CANISTER (Continued)
Page 2196 of 2199
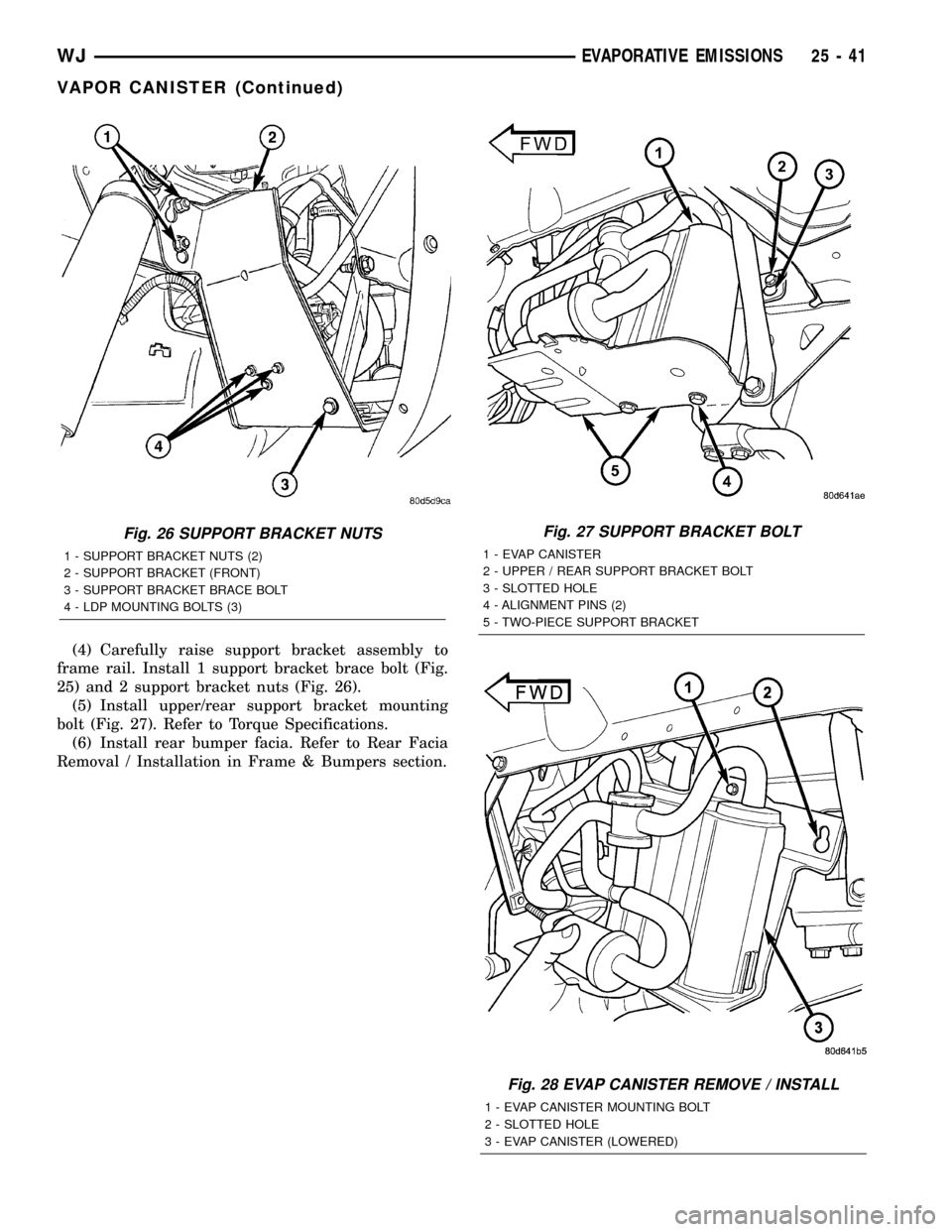
(4) Carefully raise support bracket assembly to
frame rail. Install 1 support bracket brace bolt (Fig.
25) and 2 support bracket nuts (Fig. 26).
(5) Install upper/rear support bracket mounting
bolt (Fig. 27). Refer to Torque Specifications.
(6) Install rear bumper facia. Refer to Rear Facia
Removal / Installation in Frame & Bumpers section.
Fig. 27 SUPPORT BRACKET BOLT
1 - EVAP CANISTER
2 - UPPER / REAR SUPPORT BRACKET BOLT
3 - SLOTTED HOLE
4 - ALIGNMENT PINS (2)
5 - TWO-PIECE SUPPORT BRACKET
Fig. 28 EVAP CANISTER REMOVE / INSTALL
1 - EVAP CANISTER MOUNTING BOLT
2 - SLOTTED HOLE
3 - EVAP CANISTER (LOWERED)
Fig. 26 SUPPORT BRACKET NUTS
1 - SUPPORT BRACKET NUTS (2)
2 - SUPPORT BRACKET (FRONT)
3 - SUPPORT BRACKET BRACE BOLT
4 - LDP MOUNTING BOLTS (3)
WJEVAPORATIVE EMISSIONS 25 - 41
VAPOR CANISTER (Continued)
Page 2197 of 2199
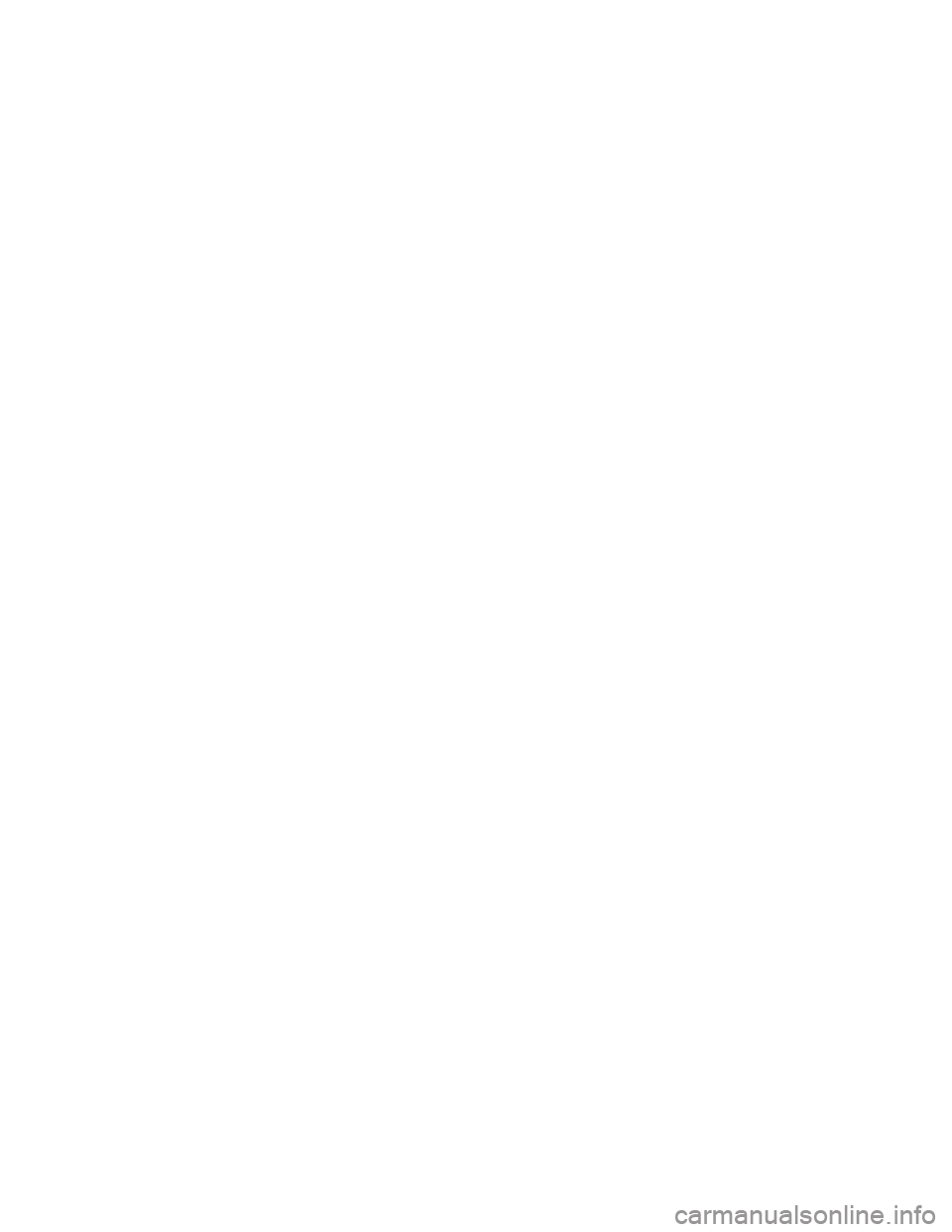
Page 2198 of 2199
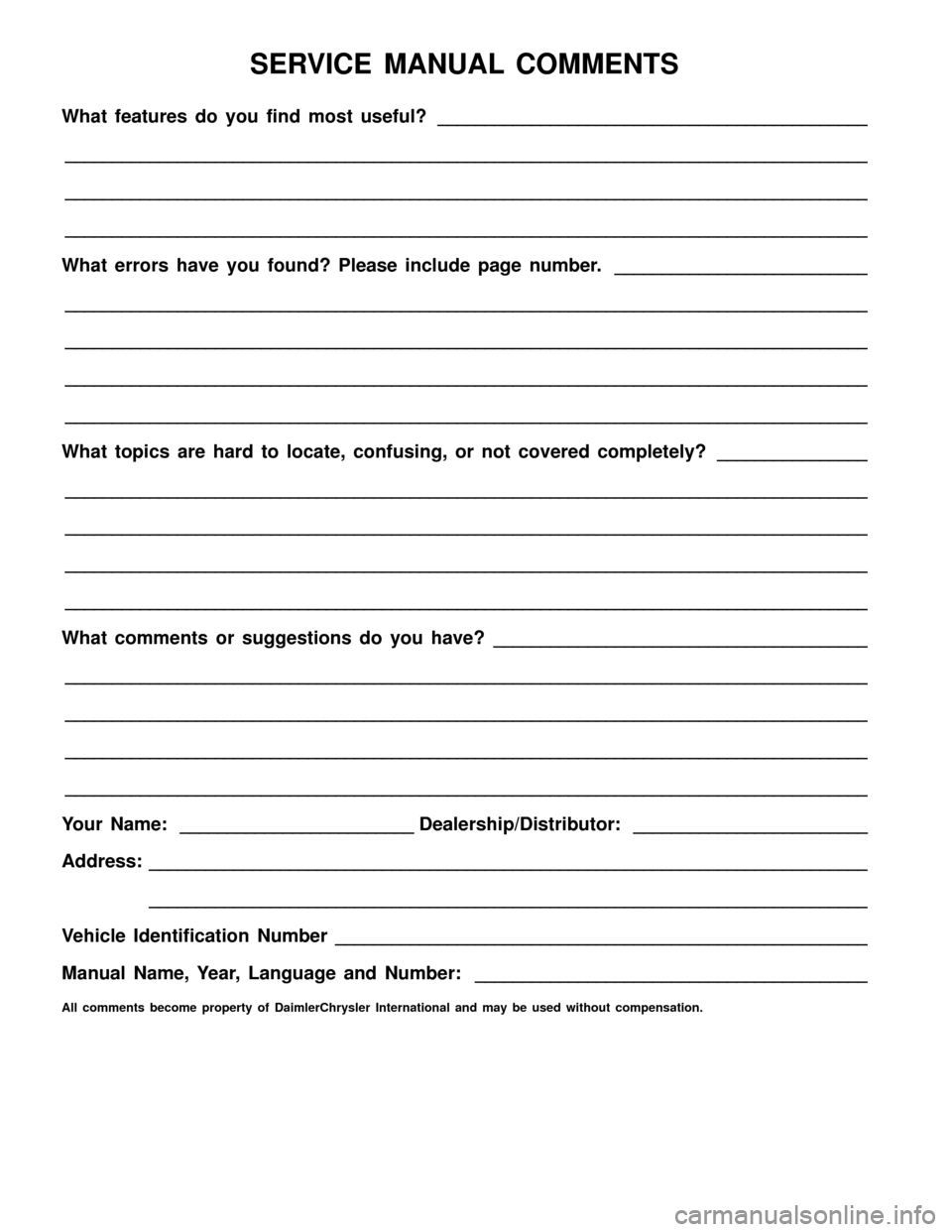
SERVICE MANUAL COMMENTS
What features do you find most useful?______________________________________________
______________________________________________________________________________________
______________________________________________________________________________________
______________________________________________________________________________________
What errors have you found? Please include page number.___________________________
______________________________________________________________________________________
______________________________________________________________________________________
______________________________________________________________________________________
______________________________________________________________________________________
What topics are hard to locate, confusing, or not covered completely?________________
______________________________________________________________________________________
______________________________________________________________________________________
______________________________________________________________________________________
______________________________________________________________________________________
What comments or suggestions do you have?________________________________________
______________________________________________________________________________________
______________________________________________________________________________________
______________________________________________________________________________________
______________________________________________________________________________________
Your Name:_________________________Dealership/Distributor:_________________________
Address:_____________________________________________________________________________
_____________________________________________________________________________
Vehicle Identification Number_________________________________________________________
Manual Name, Year, Language and Number:__________________________________________
All comments become property of DaimlerChrysler International and may be used without compensation.
Page 2199 of 2199
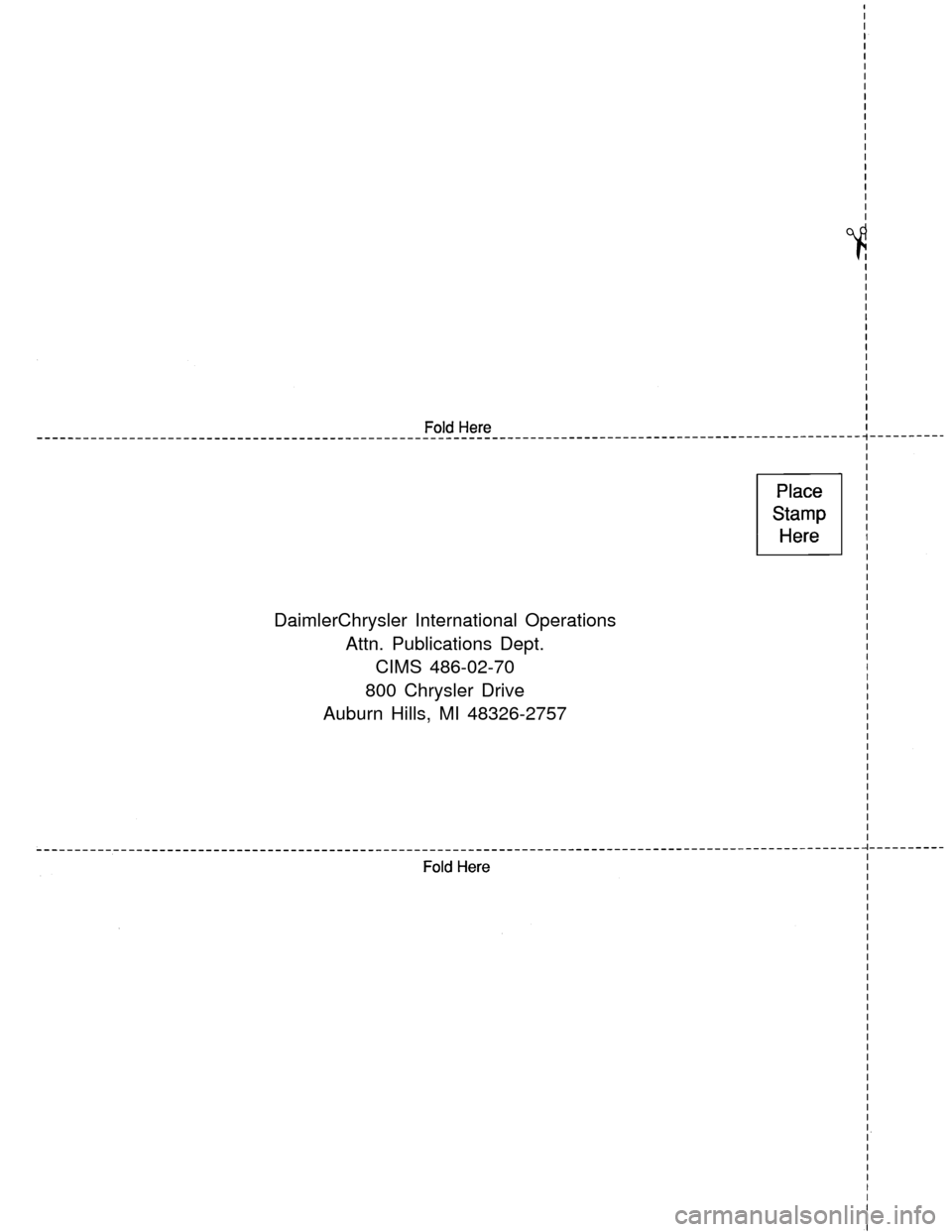
DaimlerChrysler International Operations
Attn. Publications Dept.
CIMS 486-02-70
800 Chrysler Drive
Auburn Hills, MI 48326-2757
#