Power steering JEEP GRAND CHEROKEE 2003 WJ / 2.G Owner's Manual
[x] Cancel search | Manufacturer: JEEP, Model Year: 2003, Model line: GRAND CHEROKEE, Model: JEEP GRAND CHEROKEE 2003 WJ / 2.GPages: 2199, PDF Size: 76.01 MB
Page 301 of 2199
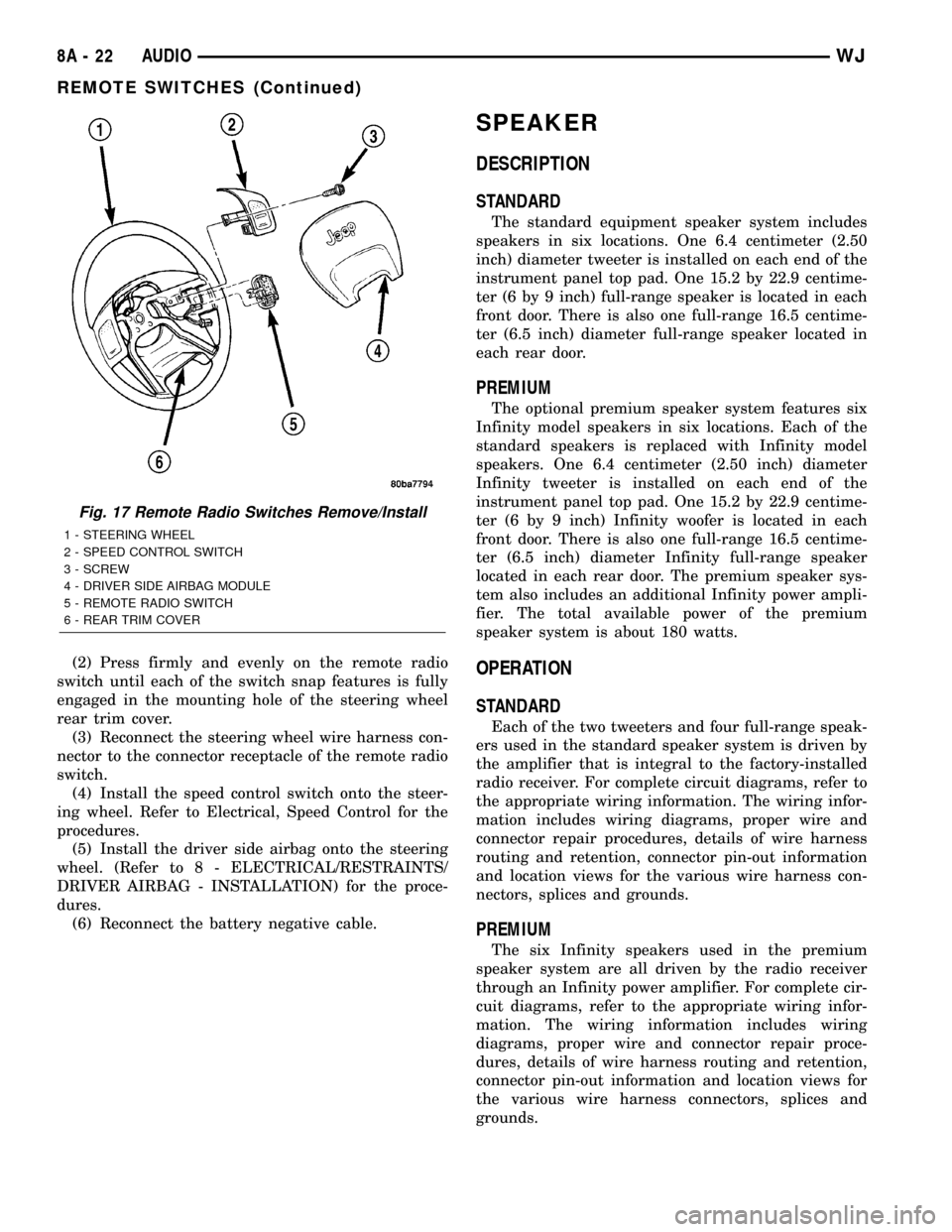
(2) Press firmly and evenly on the remote radio
switch until each of the switch snap features is fully
engaged in the mounting hole of the steering wheel
rear trim cover.
(3) Reconnect the steering wheel wire harness con-
nector to the connector receptacle of the remote radio
switch.
(4) Install the speed control switch onto the steer-
ing wheel. Refer to Electrical, Speed Control for the
procedures.
(5) Install the driver side airbag onto the steering
wheel. (Refer to 8 - ELECTRICAL/RESTRAINTS/
DRIVER AIRBAG - INSTALLATION) for the proce-
dures.
(6) Reconnect the battery negative cable.
SPEAKER
DESCRIPTION
STANDARD
The standard equipment speaker system includes
speakers in six locations. One 6.4 centimeter (2.50
inch) diameter tweeter is installed on each end of the
instrument panel top pad. One 15.2 by 22.9 centime-
ter (6 by 9 inch) full-range speaker is located in each
front door. There is also one full-range 16.5 centime-
ter (6.5 inch) diameter full-range speaker located in
each rear door.
PREMIUM
The optional premium speaker system features six
Infinity model speakers in six locations. Each of the
standard speakers is replaced with Infinity model
speakers. One 6.4 centimeter (2.50 inch) diameter
Infinity tweeter is installed on each end of the
instrument panel top pad. One 15.2 by 22.9 centime-
ter (6 by 9 inch) Infinity woofer is located in each
front door. There is also one full-range 16.5 centime-
ter (6.5 inch) diameter Infinity full-range speaker
located in each rear door. The premium speaker sys-
tem also includes an additional Infinity power ampli-
fier. The total available power of the premium
speaker system is about 180 watts.
OPERATION
STANDARD
Each of the two tweeters and four full-range speak-
ers used in the standard speaker system is driven by
the amplifier that is integral to the factory-installed
radio receiver. For complete circuit diagrams, refer to
the appropriate wiring information. The wiring infor-
mation includes wiring diagrams, proper wire and
connector repair procedures, details of wire harness
routing and retention, connector pin-out information
and location views for the various wire harness con-
nectors, splices and grounds.
PREMIUM
The six Infinity speakers used in the premium
speaker system are all driven by the radio receiver
through an Infinity power amplifier. For complete cir-
cuit diagrams, refer to the appropriate wiring infor-
mation. The wiring information includes wiring
diagrams, proper wire and connector repair proce-
dures, details of wire harness routing and retention,
connector pin-out information and location views for
the various wire harness connectors, splices and
grounds.
Fig. 17 Remote Radio Switches Remove/Install
1 - STEERING WHEEL
2 - SPEED CONTROL SWITCH
3 - SCREW
4 - DRIVER SIDE AIRBAG MODULE
5 - REMOTE RADIO SWITCH
6 - REAR TRIM COVER
8A - 22 AUDIOWJ
REMOTE SWITCHES (Continued)
Page 302 of 2199
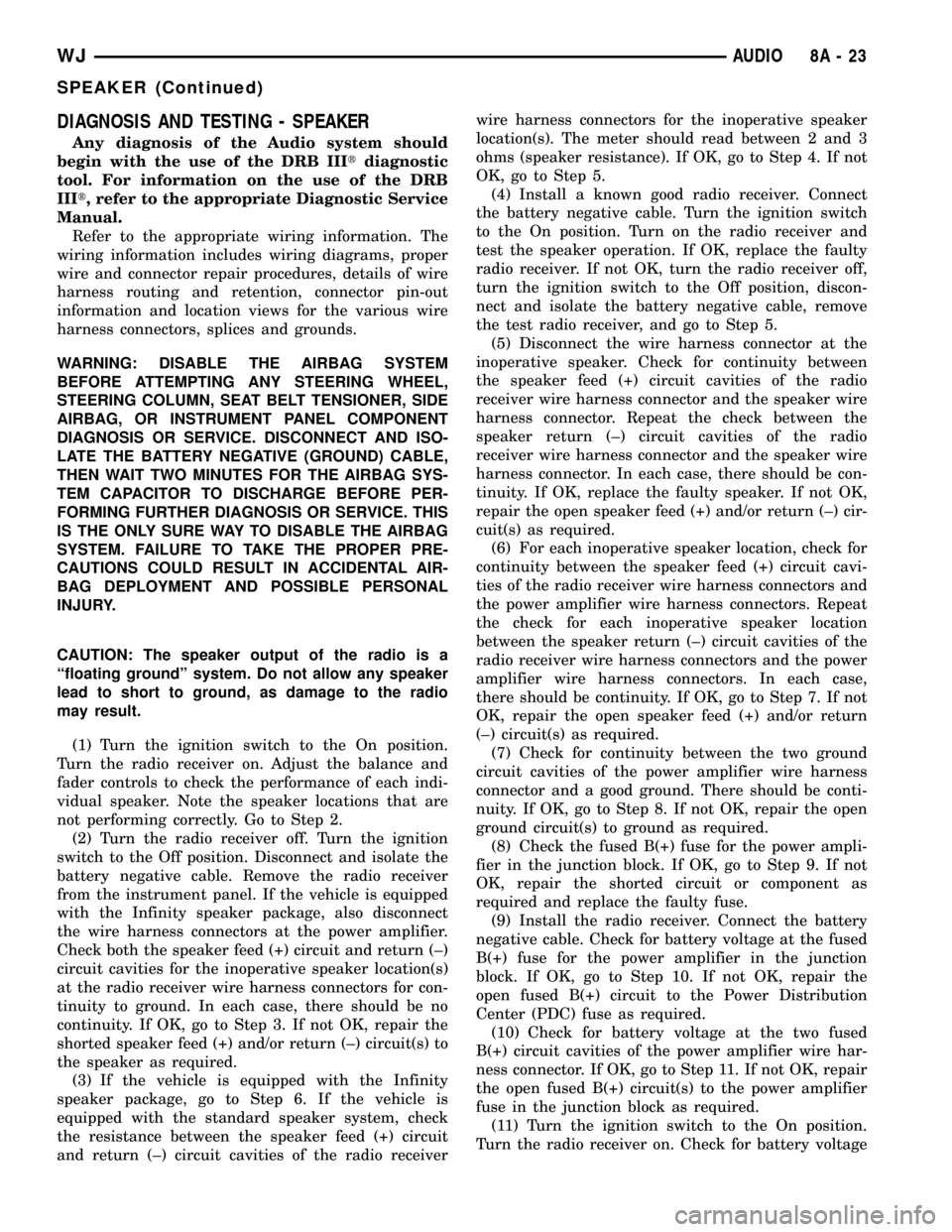
DIAGNOSIS AND TESTING - SPEAKER
Any diagnosis of the Audio system should
begin with the use of the DRB IIItdiagnostic
tool. For information on the use of the DRB
IIIt, refer to the appropriate Diagnostic Service
Manual.
Refer to the appropriate wiring information. The
wiring information includes wiring diagrams, proper
wire and connector repair procedures, details of wire
harness routing and retention, connector pin-out
information and location views for the various wire
harness connectors, splices and grounds.
WARNING: DISABLE THE AIRBAG SYSTEM
BEFORE ATTEMPTING ANY STEERING WHEEL,
STEERING COLUMN, SEAT BELT TENSIONER, SIDE
AIRBAG, OR INSTRUMENT PANEL COMPONENT
DIAGNOSIS OR SERVICE. DISCONNECT AND ISO-
LATE THE BATTERY NEGATIVE (GROUND) CABLE,
THEN WAIT TWO MINUTES FOR THE AIRBAG SYS-
TEM CAPACITOR TO DISCHARGE BEFORE PER-
FORMING FURTHER DIAGNOSIS OR SERVICE. THIS
IS THE ONLY SURE WAY TO DISABLE THE AIRBAG
SYSTEM. FAILURE TO TAKE THE PROPER PRE-
CAUTIONS COULD RESULT IN ACCIDENTAL AIR-
BAG DEPLOYMENT AND POSSIBLE PERSONAL
INJURY.
CAUTION: The speaker output of the radio is a
ªfloating groundº system. Do not allow any speaker
lead to short to ground, as damage to the radio
may result.
(1) Turn the ignition switch to the On position.
Turn the radio receiver on. Adjust the balance and
fader controls to check the performance of each indi-
vidual speaker. Note the speaker locations that are
not performing correctly. Go to Step 2.
(2) Turn the radio receiver off. Turn the ignition
switch to the Off position. Disconnect and isolate the
battery negative cable. Remove the radio receiver
from the instrument panel. If the vehicle is equipped
with the Infinity speaker package, also disconnect
the wire harness connectors at the power amplifier.
Check both the speaker feed (+) circuit and return (±)
circuit cavities for the inoperative speaker location(s)
at the radio receiver wire harness connectors for con-
tinuity to ground. In each case, there should be no
continuity. If OK, go to Step 3. If not OK, repair the
shorted speaker feed (+) and/or return (±) circuit(s) to
the speaker as required.
(3) If the vehicle is equipped with the Infinity
speaker package, go to Step 6. If the vehicle is
equipped with the standard speaker system, check
the resistance between the speaker feed (+) circuit
and return (±) circuit cavities of the radio receiverwire harness connectors for the inoperative speaker
location(s). The meter should read between 2 and 3
ohms (speaker resistance). If OK, go to Step 4. If not
OK, go to Step 5.
(4) Install a known good radio receiver. Connect
the battery negative cable. Turn the ignition switch
to the On position. Turn on the radio receiver and
test the speaker operation. If OK, replace the faulty
radio receiver. If not OK, turn the radio receiver off,
turn the ignition switch to the Off position, discon-
nect and isolate the battery negative cable, remove
the test radio receiver, and go to Step 5.
(5) Disconnect the wire harness connector at the
inoperative speaker. Check for continuity between
the speaker feed (+) circuit cavities of the radio
receiver wire harness connector and the speaker wire
harness connector. Repeat the check between the
speaker return (±) circuit cavities of the radio
receiver wire harness connector and the speaker wire
harness connector. In each case, there should be con-
tinuity. If OK, replace the faulty speaker. If not OK,
repair the open speaker feed (+) and/or return (±) cir-
cuit(s) as required.
(6) For each inoperative speaker location, check for
continuity between the speaker feed (+) circuit cavi-
ties of the radio receiver wire harness connectors and
the power amplifier wire harness connectors. Repeat
the check for each inoperative speaker location
between the speaker return (±) circuit cavities of the
radio receiver wire harness connectors and the power
amplifier wire harness connectors. In each case,
there should be continuity. If OK, go to Step 7. If not
OK, repair the open speaker feed (+) and/or return
(±) circuit(s) as required.
(7) Check for continuity between the two ground
circuit cavities of the power amplifier wire harness
connector and a good ground. There should be conti-
nuity. If OK, go to Step 8. If not OK, repair the open
ground circuit(s) to ground as required.
(8) Check the fused B(+) fuse for the power ampli-
fier in the junction block. If OK, go to Step 9. If not
OK, repair the shorted circuit or component as
required and replace the faulty fuse.
(9) Install the radio receiver. Connect the battery
negative cable. Check for battery voltage at the fused
B(+) fuse for the power amplifier in the junction
block. If OK, go to Step 10. If not OK, repair the
open fused B(+) circuit to the Power Distribution
Center (PDC) fuse as required.
(10) Check for battery voltage at the two fused
B(+) circuit cavities of the power amplifier wire har-
ness connector. If OK, go to Step 11. If not OK, repair
the open fused B(+) circuit(s) to the power amplifier
fuse in the junction block as required.
(11) Turn the ignition switch to the On position.
Turn the radio receiver on. Check for battery voltage
WJAUDIO 8A - 23
SPEAKER (Continued)
Page 314 of 2199
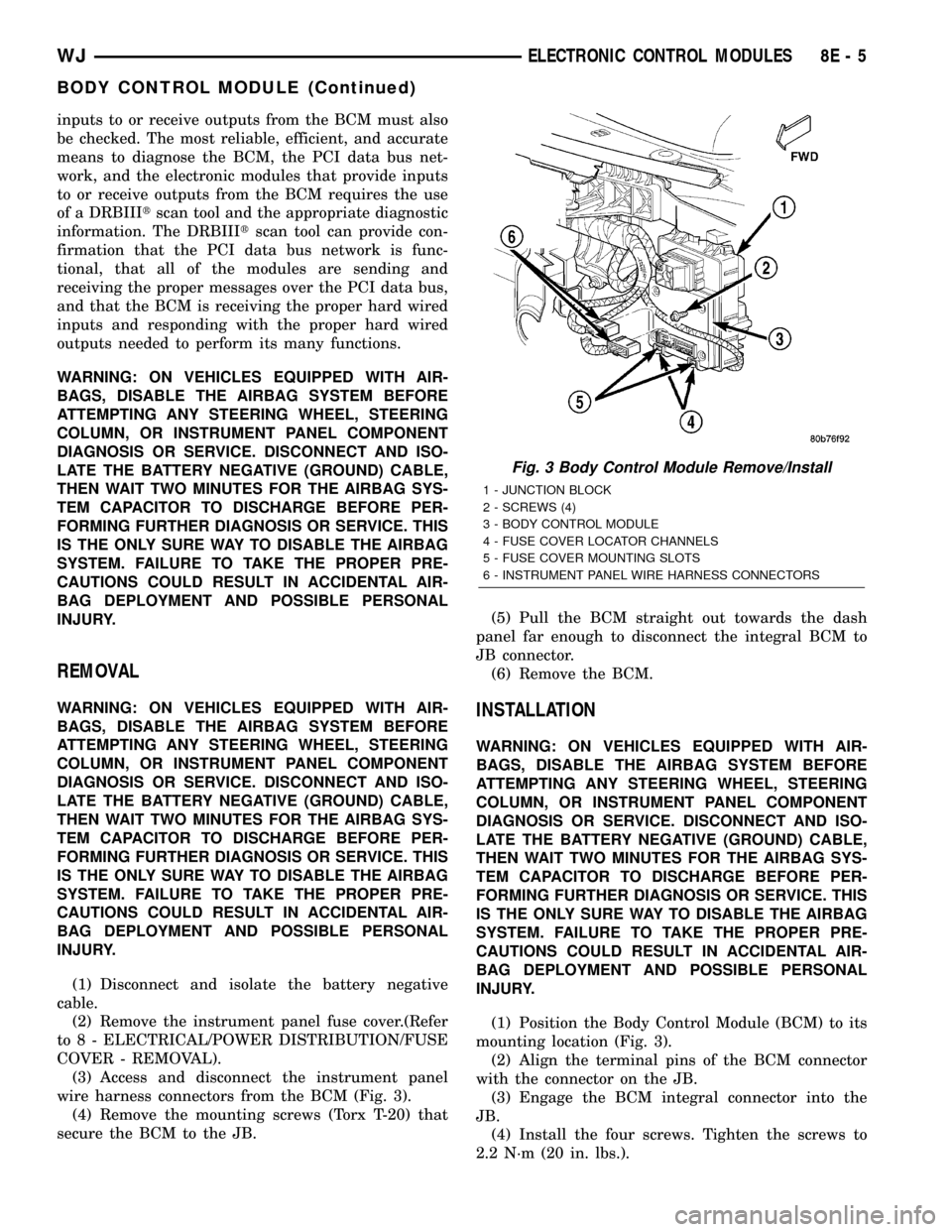
inputs to or receive outputs from the BCM must also
be checked. The most reliable, efficient, and accurate
means to diagnose the BCM, the PCI data bus net-
work, and the electronic modules that provide inputs
to or receive outputs from the BCM requires the use
of a DRBIIItscan tool and the appropriate diagnostic
information. The DRBIIItscan tool can provide con-
firmation that the PCI data bus network is func-
tional, that all of the modules are sending and
receiving the proper messages over the PCI data bus,
and that the BCM is receiving the proper hard wired
inputs and responding with the proper hard wired
outputs needed to perform its many functions.
WARNING: ON VEHICLES EQUIPPED WITH AIR-
BAGS, DISABLE THE AIRBAG SYSTEM BEFORE
ATTEMPTING ANY STEERING WHEEL, STEERING
COLUMN, OR INSTRUMENT PANEL COMPONENT
DIAGNOSIS OR SERVICE. DISCONNECT AND ISO-
LATE THE BATTERY NEGATIVE (GROUND) CABLE,
THEN WAIT TWO MINUTES FOR THE AIRBAG SYS-
TEM CAPACITOR TO DISCHARGE BEFORE PER-
FORMING FURTHER DIAGNOSIS OR SERVICE. THIS
IS THE ONLY SURE WAY TO DISABLE THE AIRBAG
SYSTEM. FAILURE TO TAKE THE PROPER PRE-
CAUTIONS COULD RESULT IN ACCIDENTAL AIR-
BAG DEPLOYMENT AND POSSIBLE PERSONAL
INJURY.
REMOVAL
WARNING: ON VEHICLES EQUIPPED WITH AIR-
BAGS, DISABLE THE AIRBAG SYSTEM BEFORE
ATTEMPTING ANY STEERING WHEEL, STEERING
COLUMN, OR INSTRUMENT PANEL COMPONENT
DIAGNOSIS OR SERVICE. DISCONNECT AND ISO-
LATE THE BATTERY NEGATIVE (GROUND) CABLE,
THEN WAIT TWO MINUTES FOR THE AIRBAG SYS-
TEM CAPACITOR TO DISCHARGE BEFORE PER-
FORMING FURTHER DIAGNOSIS OR SERVICE. THIS
IS THE ONLY SURE WAY TO DISABLE THE AIRBAG
SYSTEM. FAILURE TO TAKE THE PROPER PRE-
CAUTIONS COULD RESULT IN ACCIDENTAL AIR-
BAG DEPLOYMENT AND POSSIBLE PERSONAL
INJURY.
(1) Disconnect and isolate the battery negative
cable.
(2) Remove the instrument panel fuse cover.(Refer
to 8 - ELECTRICAL/POWER DISTRIBUTION/FUSE
COVER - REMOVAL).
(3) Access and disconnect the instrument panel
wire harness connectors from the BCM (Fig. 3).
(4) Remove the mounting screws (Torx T-20) that
secure the BCM to the JB.(5) Pull the BCM straight out towards the dash
panel far enough to disconnect the integral BCM to
JB connector.
(6) Remove the BCM.INSTALLATION
WARNING: ON VEHICLES EQUIPPED WITH AIR-
BAGS, DISABLE THE AIRBAG SYSTEM BEFORE
ATTEMPTING ANY STEERING WHEEL, STEERING
COLUMN, OR INSTRUMENT PANEL COMPONENT
DIAGNOSIS OR SERVICE. DISCONNECT AND ISO-
LATE THE BATTERY NEGATIVE (GROUND) CABLE,
THEN WAIT TWO MINUTES FOR THE AIRBAG SYS-
TEM CAPACITOR TO DISCHARGE BEFORE PER-
FORMING FURTHER DIAGNOSIS OR SERVICE. THIS
IS THE ONLY SURE WAY TO DISABLE THE AIRBAG
SYSTEM. FAILURE TO TAKE THE PROPER PRE-
CAUTIONS COULD RESULT IN ACCIDENTAL AIR-
BAG DEPLOYMENT AND POSSIBLE PERSONAL
INJURY.
(1) Position the Body Control Module (BCM) to its
mounting location (Fig. 3).
(2) Align the terminal pins of the BCM connector
with the connector on the JB.
(3) Engage the BCM integral connector into the
JB.
(4) Install the four screws. Tighten the screws to
2.2 N´m (20 in. lbs.).
Fig. 3 Body Control Module Remove/Install
1 - JUNCTION BLOCK
2 - SCREWS (4)
3 - BODY CONTROL MODULE
4 - FUSE COVER LOCATOR CHANNELS
5 - FUSE COVER MOUNTING SLOTS
6 - INSTRUMENT PANEL WIRE HARNESS CONNECTORS
WJELECTRONIC CONTROL MODULES 8E - 5
BODY CONTROL MODULE (Continued)
Page 316 of 2199
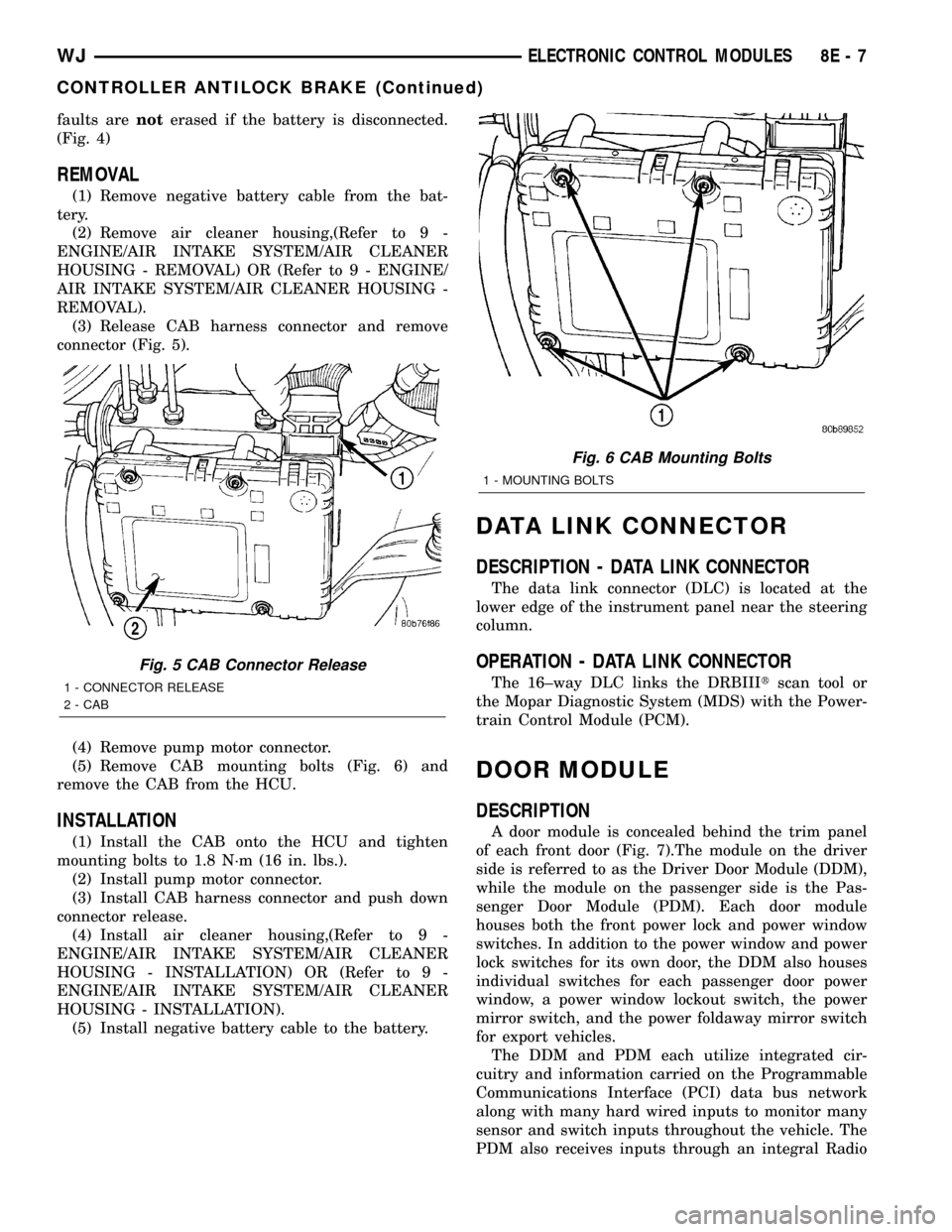
faults arenoterased if the battery is disconnected.
(Fig. 4)
REMOVAL
(1) Remove negative battery cable from the bat-
tery.
(2) Remove air cleaner housing,(Refer to 9 -
ENGINE/AIR INTAKE SYSTEM/AIR CLEANER
HOUSING - REMOVAL) OR (Refer to 9 - ENGINE/
AIR INTAKE SYSTEM/AIR CLEANER HOUSING -
REMOVAL).
(3) Release CAB harness connector and remove
connector (Fig. 5).
(4) Remove pump motor connector.
(5) Remove CAB mounting bolts (Fig. 6) and
remove the CAB from the HCU.
INSTALLATION
(1) Install the CAB onto the HCU and tighten
mounting bolts to 1.8 N´m (16 in. lbs.).
(2) Install pump motor connector.
(3) Install CAB harness connector and push down
connector release.
(4) Install air cleaner housing,(Refer to 9 -
ENGINE/AIR INTAKE SYSTEM/AIR CLEANER
HOUSING - INSTALLATION) OR (Refer to 9 -
ENGINE/AIR INTAKE SYSTEM/AIR CLEANER
HOUSING - INSTALLATION).
(5) Install negative battery cable to the battery.
DATA LINK CONNECTOR
DESCRIPTION - DATA LINK CONNECTOR
The data link connector (DLC) is located at the
lower edge of the instrument panel near the steering
column.
OPERATION - DATA LINK CONNECTOR
The 16±way DLC links the DRBIIItscan tool or
the Mopar Diagnostic System (MDS) with the Power-
train Control Module (PCM).
DOOR MODULE
DESCRIPTION
A door module is concealed behind the trim panel
of each front door (Fig. 7).The module on the driver
side is referred to as the Driver Door Module (DDM),
while the module on the passenger side is the Pas-
senger Door Module (PDM). Each door module
houses both the front power lock and power window
switches. In addition to the power window and power
lock switches for its own door, the DDM also houses
individual switches for each passenger door power
window, a power window lockout switch, the power
mirror switch, and the power foldaway mirror switch
for export vehicles.
The DDM and PDM each utilize integrated cir-
cuitry and information carried on the Programmable
Communications Interface (PCI) data bus network
along with many hard wired inputs to monitor many
sensor and switch inputs throughout the vehicle. The
PDM also receives inputs through an integral Radio
Fig. 5 CAB Connector Release
1 - CONNECTOR RELEASE
2 - CAB
Fig. 6 CAB Mounting Bolts
1 - MOUNTING BOLTS
WJELECTRONIC CONTROL MODULES 8E - 7
CONTROLLER ANTILOCK BRAKE (Continued)
Page 319 of 2199
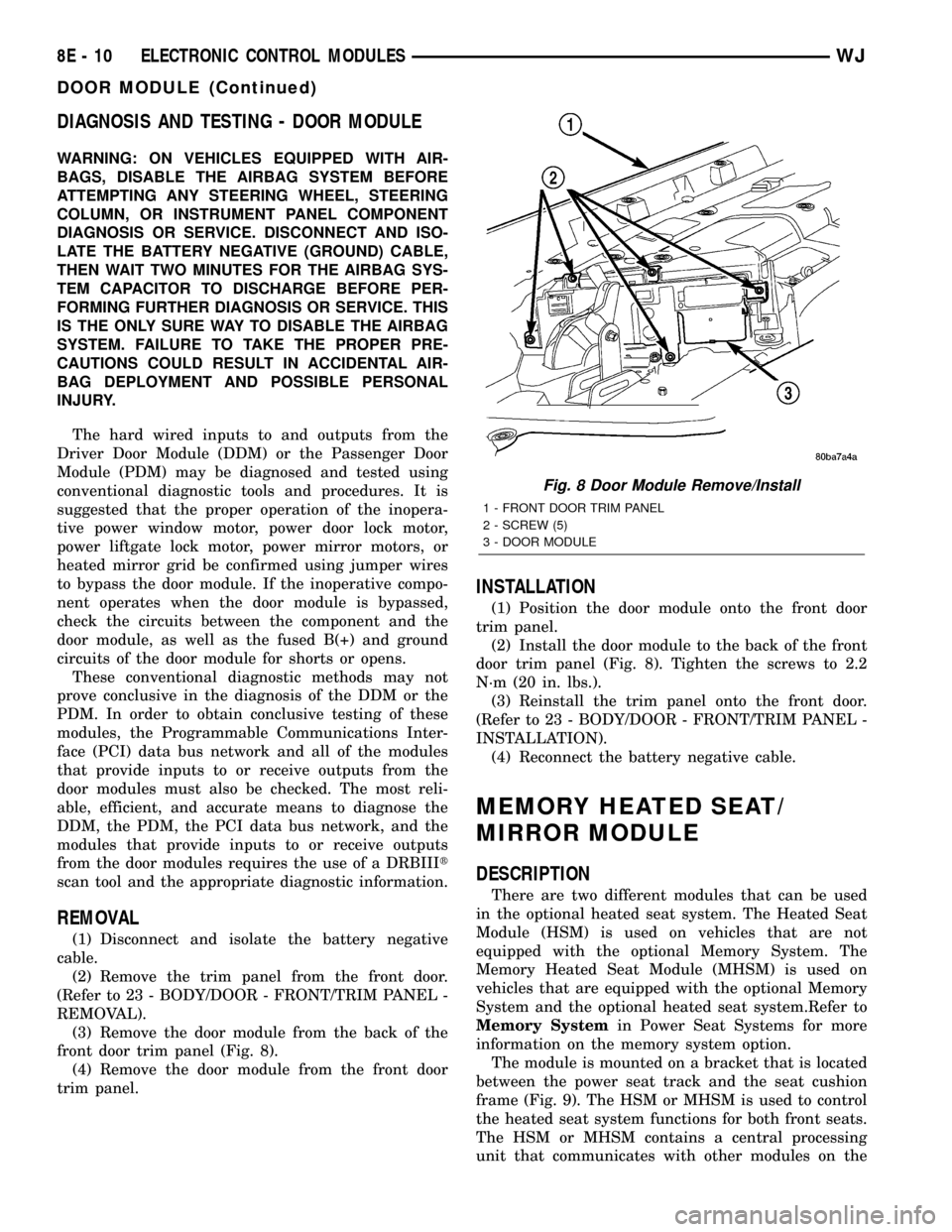
DIAGNOSIS AND TESTING - DOOR MODULE
WARNING: ON VEHICLES EQUIPPED WITH AIR-
BAGS, DISABLE THE AIRBAG SYSTEM BEFORE
ATTEMPTING ANY STEERING WHEEL, STEERING
COLUMN, OR INSTRUMENT PANEL COMPONENT
DIAGNOSIS OR SERVICE. DISCONNECT AND ISO-
LATE THE BATTERY NEGATIVE (GROUND) CABLE,
THEN WAIT TWO MINUTES FOR THE AIRBAG SYS-
TEM CAPACITOR TO DISCHARGE BEFORE PER-
FORMING FURTHER DIAGNOSIS OR SERVICE. THIS
IS THE ONLY SURE WAY TO DISABLE THE AIRBAG
SYSTEM. FAILURE TO TAKE THE PROPER PRE-
CAUTIONS COULD RESULT IN ACCIDENTAL AIR-
BAG DEPLOYMENT AND POSSIBLE PERSONAL
INJURY.
The hard wired inputs to and outputs from the
Driver Door Module (DDM) or the Passenger Door
Module (PDM) may be diagnosed and tested using
conventional diagnostic tools and procedures. It is
suggested that the proper operation of the inopera-
tive power window motor, power door lock motor,
power liftgate lock motor, power mirror motors, or
heated mirror grid be confirmed using jumper wires
to bypass the door module. If the inoperative compo-
nent operates when the door module is bypassed,
check the circuits between the component and the
door module, as well as the fused B(+) and ground
circuits of the door module for shorts or opens.
These conventional diagnostic methods may not
prove conclusive in the diagnosis of the DDM or the
PDM. In order to obtain conclusive testing of these
modules, the Programmable Communications Inter-
face (PCI) data bus network and all of the modules
that provide inputs to or receive outputs from the
door modules must also be checked. The most reli-
able, efficient, and accurate means to diagnose the
DDM, the PDM, the PCI data bus network, and the
modules that provide inputs to or receive outputs
from the door modules requires the use of a DRBIIIt
scan tool and the appropriate diagnostic information.
REMOVAL
(1) Disconnect and isolate the battery negative
cable.
(2) Remove the trim panel from the front door.
(Refer to 23 - BODY/DOOR - FRONT/TRIM PANEL -
REMOVAL).
(3) Remove the door module from the back of the
front door trim panel (Fig. 8).
(4) Remove the door module from the front door
trim panel.
INSTALLATION
(1) Position the door module onto the front door
trim panel.
(2) Install the door module to the back of the front
door trim panel (Fig. 8). Tighten the screws to 2.2
N´m (20 in. lbs.).
(3) Reinstall the trim panel onto the front door.
(Refer to 23 - BODY/DOOR - FRONT/TRIM PANEL -
INSTALLATION).
(4) Reconnect the battery negative cable.
MEMORY HEATED SEAT/
MIRROR MODULE
DESCRIPTION
There are two different modules that can be used
in the optional heated seat system. The Heated Seat
Module (HSM) is used on vehicles that are not
equipped with the optional Memory System. The
Memory Heated Seat Module (MHSM) is used on
vehicles that are equipped with the optional Memory
System and the optional heated seat system.Refer to
Memory Systemin Power Seat Systems for more
information on the memory system option.
The module is mounted on a bracket that is located
between the power seat track and the seat cushion
frame (Fig. 9). The HSM or MHSM is used to control
the heated seat system functions for both front seats.
The HSM or MHSM contains a central processing
unit that communicates with other modules on the
Fig. 8 Door Module Remove/Install
1 - FRONT DOOR TRIM PANEL
2 - SCREW (5)
3 - DOOR MODULE
8E - 10 ELECTRONIC CONTROL MODULESWJ
DOOR MODULE (Continued)
Page 326 of 2199
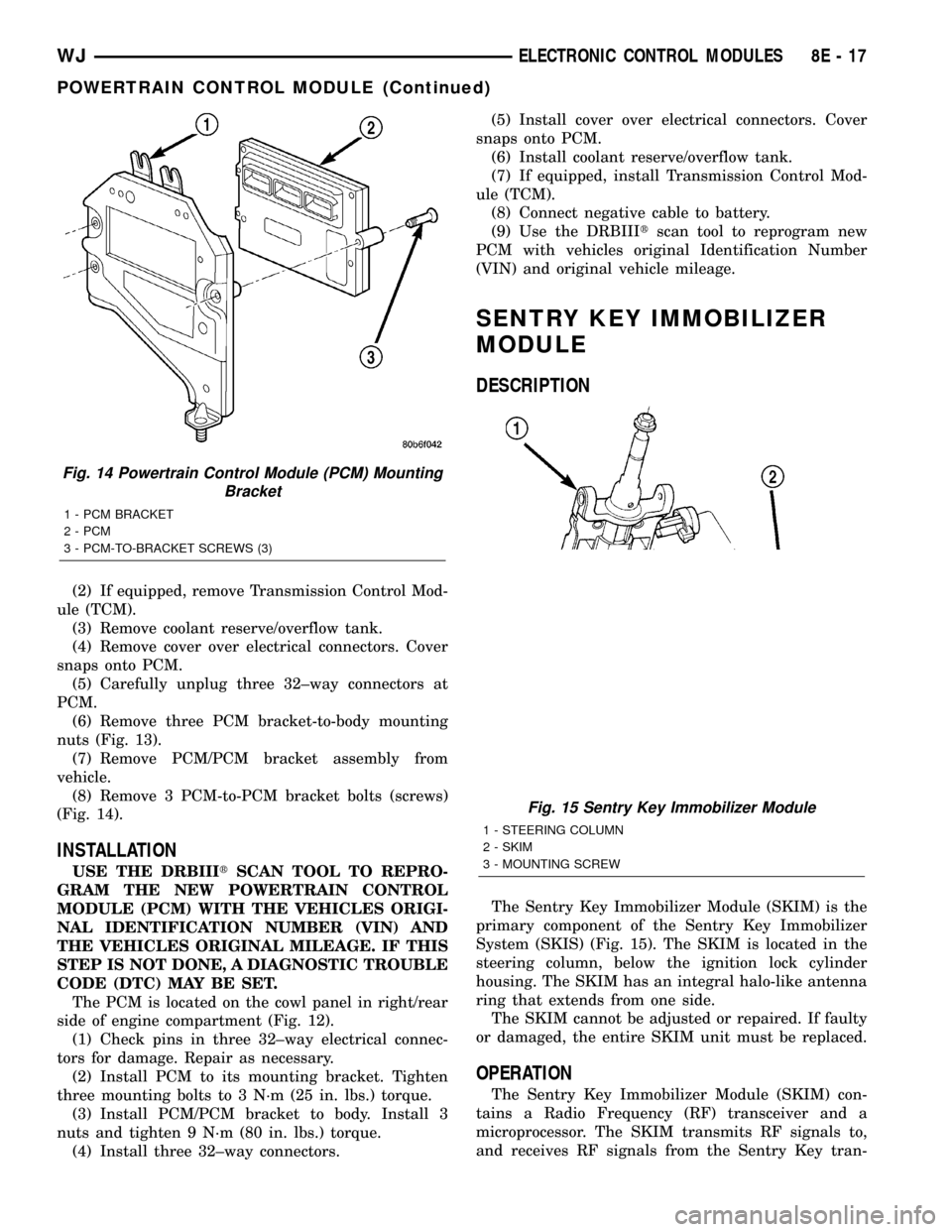
(2) If equipped, remove Transmission Control Mod-
ule (TCM).
(3) Remove coolant reserve/overflow tank.
(4) Remove cover over electrical connectors. Cover
snaps onto PCM.
(5) Carefully unplug three 32±way connectors at
PCM.
(6) Remove three PCM bracket-to-body mounting
nuts (Fig. 13).
(7) Remove PCM/PCM bracket assembly from
vehicle.
(8) Remove 3 PCM-to-PCM bracket bolts (screws)
(Fig. 14).
INSTALLATION
USE THE DRBIIItSCAN TOOL TO REPRO-
GRAM THE NEW POWERTRAIN CONTROL
MODULE (PCM) WITH THE VEHICLES ORIGI-
NAL IDENTIFICATION NUMBER (VIN) AND
THE VEHICLES ORIGINAL MILEAGE. IF THIS
STEP IS NOT DONE, A DIAGNOSTIC TROUBLE
CODE (DTC) MAY BE SET.
The PCM is located on the cowl panel in right/rear
side of engine compartment (Fig. 12).
(1) Check pins in three 32±way electrical connec-
tors for damage. Repair as necessary.
(2) Install PCM to its mounting bracket. Tighten
three mounting bolts to 3 N´m (25 in. lbs.) torque.
(3) Install PCM/PCM bracket to body. Install 3
nuts and tighten 9 N´m (80 in. lbs.) torque.
(4) Install three 32±way connectors.(5) Install cover over electrical connectors. Cover
snaps onto PCM.
(6) Install coolant reserve/overflow tank.
(7) If equipped, install Transmission Control Mod-
ule (TCM).
(8) Connect negative cable to battery.
(9) Use the DRBIIItscan tool to reprogram new
PCM with vehicles original Identification Number
(VIN) and original vehicle mileage.
SENTRY KEY IMMOBILIZER
MODULE
DESCRIPTION
The Sentry Key Immobilizer Module (SKIM) is the
primary component of the Sentry Key Immobilizer
System (SKIS) (Fig. 15). The SKIM is located in the
steering column, below the ignition lock cylinder
housing. The SKIM has an integral halo-like antenna
ring that extends from one side.
The SKIM cannot be adjusted or repaired. If faulty
or damaged, the entire SKIM unit must be replaced.
OPERATION
The Sentry Key Immobilizer Module (SKIM) con-
tains a Radio Frequency (RF) transceiver and a
microprocessor. The SKIM transmits RF signals to,
and receives RF signals from the Sentry Key tran-
Fig. 14 Powertrain Control Module (PCM) Mounting
Bracket
1 - PCM BRACKET
2 - PCM
3 - PCM-TO-BRACKET SCREWS (3)
Fig. 15 Sentry Key Immobilizer Module
1 - STEERING COLUMN
2 - SKIM
3 - MOUNTING SCREW
WJELECTRONIC CONTROL MODULES 8E - 17
POWERTRAIN CONTROL MODULE (Continued)
Page 327 of 2199
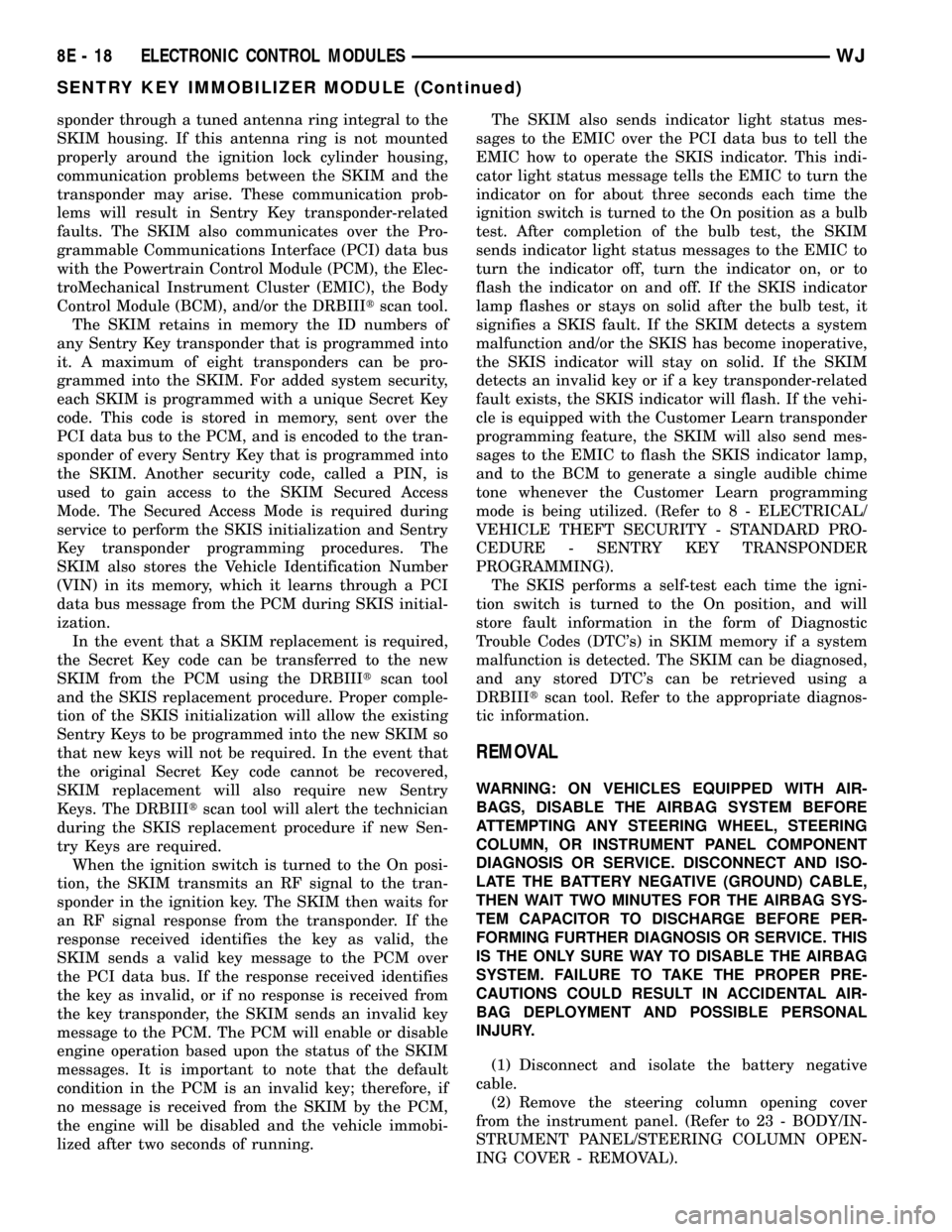
sponder through a tuned antenna ring integral to the
SKIM housing. If this antenna ring is not mounted
properly around the ignition lock cylinder housing,
communication problems between the SKIM and the
transponder may arise. These communication prob-
lems will result in Sentry Key transponder-related
faults. The SKIM also communicates over the Pro-
grammable Communications Interface (PCI) data bus
with the Powertrain Control Module (PCM), the Elec-
troMechanical Instrument Cluster (EMIC), the Body
Control Module (BCM), and/or the DRBIIItscan tool.
The SKIM retains in memory the ID numbers of
any Sentry Key transponder that is programmed into
it. A maximum of eight transponders can be pro-
grammed into the SKIM. For added system security,
each SKIM is programmed with a unique Secret Key
code. This code is stored in memory, sent over the
PCI data bus to the PCM, and is encoded to the tran-
sponder of every Sentry Key that is programmed into
the SKIM. Another security code, called a PIN, is
used to gain access to the SKIM Secured Access
Mode. The Secured Access Mode is required during
service to perform the SKIS initialization and Sentry
Key transponder programming procedures. The
SKIM also stores the Vehicle Identification Number
(VIN) in its memory, which it learns through a PCI
data bus message from the PCM during SKIS initial-
ization.
In the event that a SKIM replacement is required,
the Secret Key code can be transferred to the new
SKIM from the PCM using the DRBIIItscan tool
and the SKIS replacement procedure. Proper comple-
tion of the SKIS initialization will allow the existing
Sentry Keys to be programmed into the new SKIM so
that new keys will not be required. In the event that
the original Secret Key code cannot be recovered,
SKIM replacement will also require new Sentry
Keys. The DRBIIItscan tool will alert the technician
during the SKIS replacement procedure if new Sen-
try Keys are required.
When the ignition switch is turned to the On posi-
tion, the SKIM transmits an RF signal to the tran-
sponder in the ignition key. The SKIM then waits for
an RF signal response from the transponder. If the
response received identifies the key as valid, the
SKIM sends a valid key message to the PCM over
the PCI data bus. If the response received identifies
the key as invalid, or if no response is received from
the key transponder, the SKIM sends an invalid key
message to the PCM. The PCM will enable or disable
engine operation based upon the status of the SKIM
messages. It is important to note that the default
condition in the PCM is an invalid key; therefore, if
no message is received from the SKIM by the PCM,
the engine will be disabled and the vehicle immobi-
lized after two seconds of running.The SKIM also sends indicator light status mes-
sages to the EMIC over the PCI data bus to tell the
EMIC how to operate the SKIS indicator. This indi-
cator light status message tells the EMIC to turn the
indicator on for about three seconds each time the
ignition switch is turned to the On position as a bulb
test. After completion of the bulb test, the SKIM
sends indicator light status messages to the EMIC to
turn the indicator off, turn the indicator on, or to
flash the indicator on and off. If the SKIS indicator
lamp flashes or stays on solid after the bulb test, it
signifies a SKIS fault. If the SKIM detects a system
malfunction and/or the SKIS has become inoperative,
the SKIS indicator will stay on solid. If the SKIM
detects an invalid key or if a key transponder-related
fault exists, the SKIS indicator will flash. If the vehi-
cle is equipped with the Customer Learn transponder
programming feature, the SKIM will also send mes-
sages to the EMIC to flash the SKIS indicator lamp,
and to the BCM to generate a single audible chime
tone whenever the Customer Learn programming
mode is being utilized. (Refer to 8 - ELECTRICAL/
VEHICLE THEFT SECURITY - STANDARD PRO-
CEDURE - SENTRY KEY TRANSPONDER
PROGRAMMING).
The SKIS performs a self-test each time the igni-
tion switch is turned to the On position, and will
store fault information in the form of Diagnostic
Trouble Codes (DTC's) in SKIM memory if a system
malfunction is detected. The SKIM can be diagnosed,
and any stored DTC's can be retrieved using a
DRBIIItscan tool. Refer to the appropriate diagnos-
tic information.
REMOVAL
WARNING: ON VEHICLES EQUIPPED WITH AIR-
BAGS, DISABLE THE AIRBAG SYSTEM BEFORE
ATTEMPTING ANY STEERING WHEEL, STEERING
COLUMN, OR INSTRUMENT PANEL COMPONENT
DIAGNOSIS OR SERVICE. DISCONNECT AND ISO-
LATE THE BATTERY NEGATIVE (GROUND) CABLE,
THEN WAIT TWO MINUTES FOR THE AIRBAG SYS-
TEM CAPACITOR TO DISCHARGE BEFORE PER-
FORMING FURTHER DIAGNOSIS OR SERVICE. THIS
IS THE ONLY SURE WAY TO DISABLE THE AIRBAG
SYSTEM. FAILURE TO TAKE THE PROPER PRE-
CAUTIONS COULD RESULT IN ACCIDENTAL AIR-
BAG DEPLOYMENT AND POSSIBLE PERSONAL
INJURY.
(1) Disconnect and isolate the battery negative
cable.
(2) Remove the steering column opening cover
from the instrument panel. (Refer to 23 - BODY/IN-
STRUMENT PANEL/STEERING COLUMN OPEN-
ING COVER - REMOVAL).
8E - 18 ELECTRONIC CONTROL MODULESWJ
SENTRY KEY IMMOBILIZER MODULE (Continued)
Page 363 of 2199
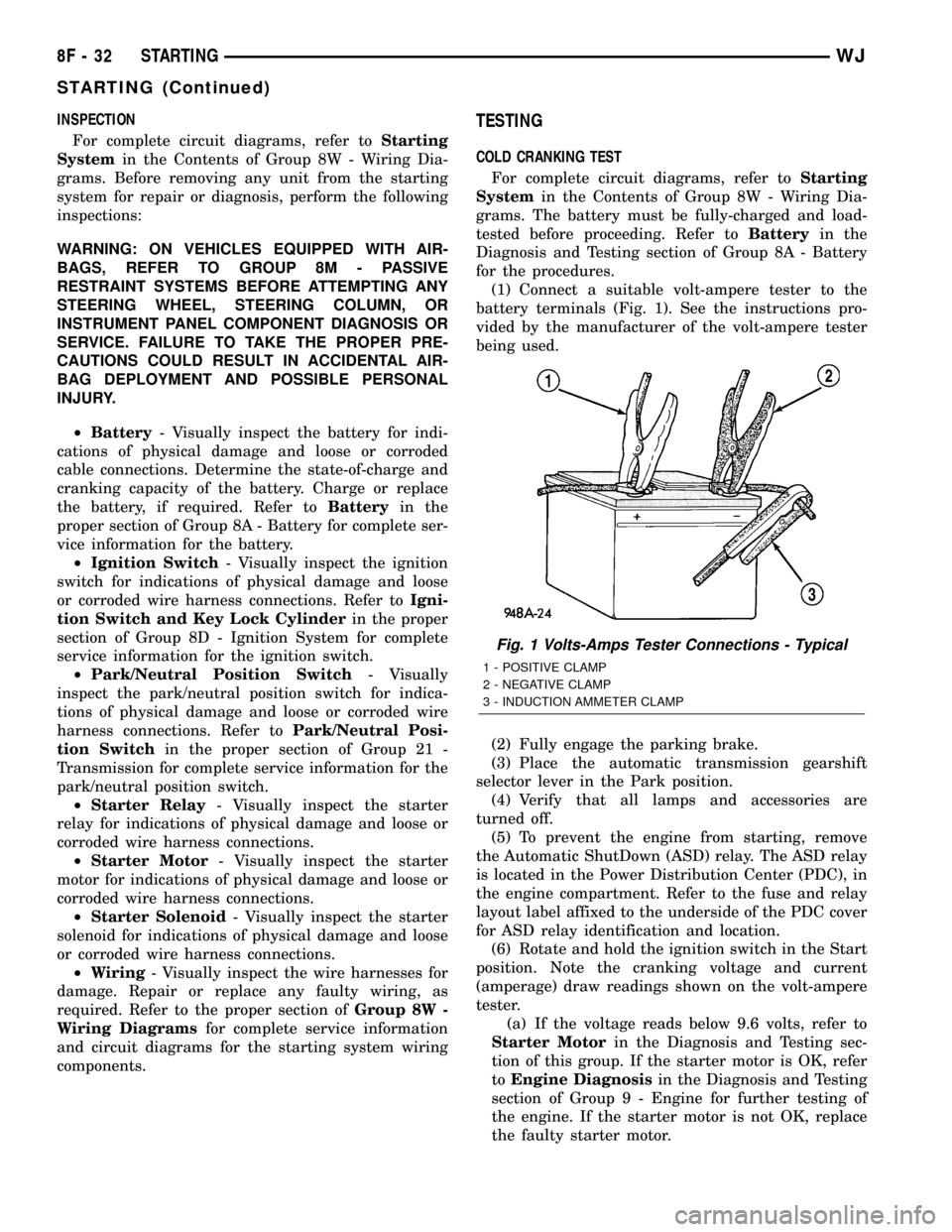
INSPECTION
For complete circuit diagrams, refer toStarting
Systemin the Contents of Group 8W - Wiring Dia-
grams. Before removing any unit from the starting
system for repair or diagnosis, perform the following
inspections:
WARNING: ON VEHICLES EQUIPPED WITH AIR-
BAGS, REFER TO GROUP 8M - PASSIVE
RESTRAINT SYSTEMS BEFORE ATTEMPTING ANY
STEERING WHEEL, STEERING COLUMN, OR
INSTRUMENT PANEL COMPONENT DIAGNOSIS OR
SERVICE. FAILURE TO TAKE THE PROPER PRE-
CAUTIONS COULD RESULT IN ACCIDENTAL AIR-
BAG DEPLOYMENT AND POSSIBLE PERSONAL
INJURY.
²Battery- Visually inspect the battery for indi-
cations of physical damage and loose or corroded
cable connections. Determine the state-of-charge and
cranking capacity of the battery. Charge or replace
the battery, if required. Refer toBatteryin the
proper section of Group 8A - Battery for complete ser-
vice information for the battery.
²Ignition Switch- Visually inspect the ignition
switch for indications of physical damage and loose
or corroded wire harness connections. Refer toIgni-
tion Switch and Key Lock Cylinderin the proper
section of Group 8D - Ignition System for complete
service information for the ignition switch.
²Park/Neutral Position Switch- Visually
inspect the park/neutral position switch for indica-
tions of physical damage and loose or corroded wire
harness connections. Refer toPark/Neutral Posi-
tion Switchin the proper section of Group 21 -
Transmission for complete service information for the
park/neutral position switch.
²Starter Relay- Visually inspect the starter
relay for indications of physical damage and loose or
corroded wire harness connections.
²Starter Motor- Visually inspect the starter
motor for indications of physical damage and loose or
corroded wire harness connections.
²Starter Solenoid- Visually inspect the starter
solenoid for indications of physical damage and loose
or corroded wire harness connections.
²Wiring- Visually inspect the wire harnesses for
damage. Repair or replace any faulty wiring, as
required. Refer to the proper section ofGroup 8W -
Wiring Diagramsfor complete service information
and circuit diagrams for the starting system wiring
components.TESTING
COLD CRANKING TEST
For complete circuit diagrams, refer toStarting
Systemin the Contents of Group 8W - Wiring Dia-
grams. The battery must be fully-charged and load-
tested before proceeding. Refer toBatteryin the
Diagnosis and Testing section of Group 8A - Battery
for the procedures.
(1) Connect a suitable volt-ampere tester to the
battery terminals (Fig. 1). See the instructions pro-
vided by the manufacturer of the volt-ampere tester
being used.
(2) Fully engage the parking brake.
(3) Place the automatic transmission gearshift
selector lever in the Park position.
(4) Verify that all lamps and accessories are
turned off.
(5) To prevent the engine from starting, remove
the Automatic ShutDown (ASD) relay. The ASD relay
is located in the Power Distribution Center (PDC), in
the engine compartment. Refer to the fuse and relay
layout label affixed to the underside of the PDC cover
for ASD relay identification and location.
(6) Rotate and hold the ignition switch in the Start
position. Note the cranking voltage and current
(amperage) draw readings shown on the volt-ampere
tester.
(a) If the voltage reads below 9.6 volts, refer to
Starter Motorin the Diagnosis and Testing sec-
tion of this group. If the starter motor is OK, refer
toEngine Diagnosisin the Diagnosis and Testing
section of Group 9 - Engine for further testing of
the engine. If the starter motor is not OK, replace
the faulty starter motor.
Fig. 1 Volts-Amps Tester Connections - Typical
1 - POSITIVE CLAMP
2 - NEGATIVE CLAMP
3 - INDUCTION AMMETER CLAMP
8F - 32 STARTINGWJ
STARTING (Continued)
Page 376 of 2199
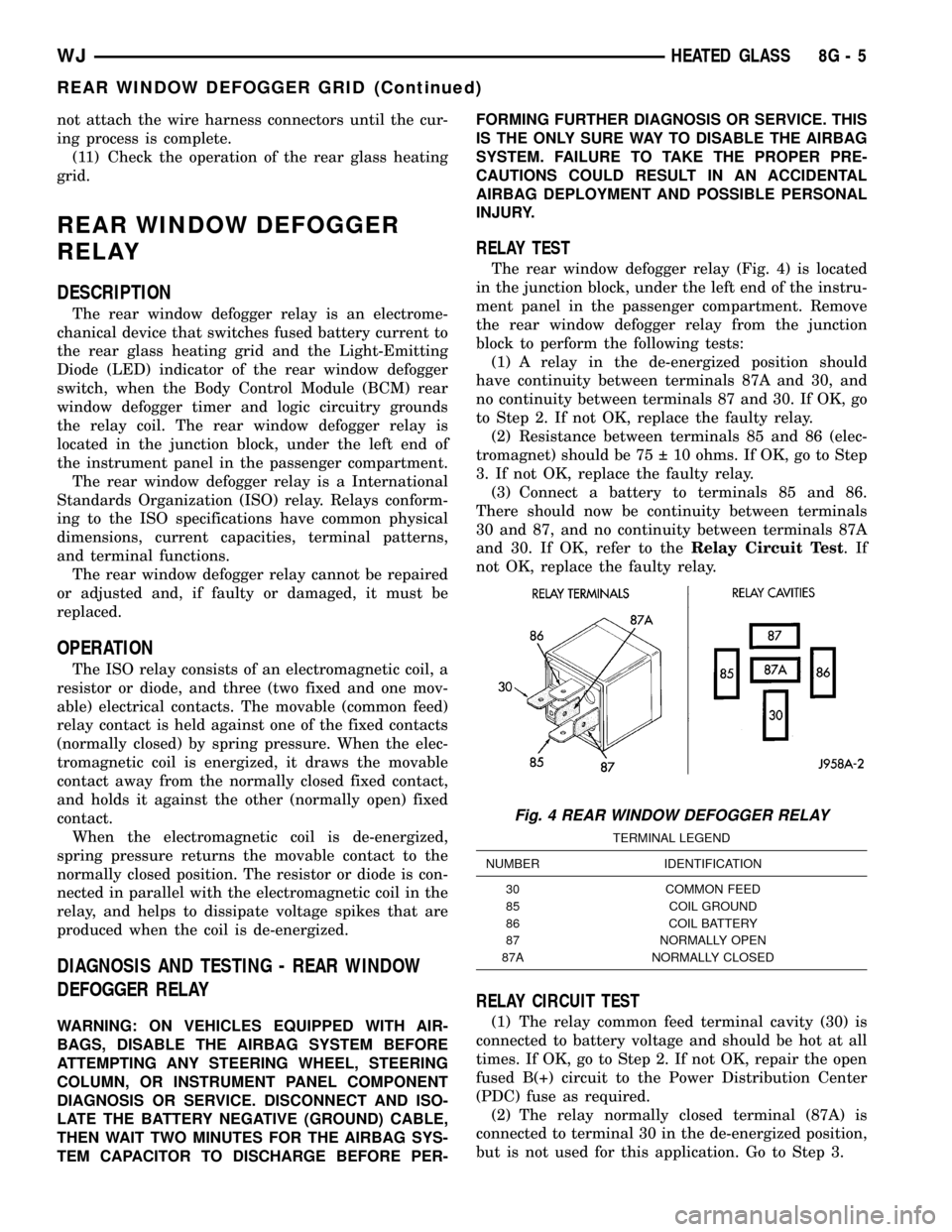
not attach the wire harness connectors until the cur-
ing process is complete.
(11) Check the operation of the rear glass heating
grid.
REAR WINDOW DEFOGGER
RELAY
DESCRIPTION
The rear window defogger relay is an electrome-
chanical device that switches fused battery current to
the rear glass heating grid and the Light-Emitting
Diode (LED) indicator of the rear window defogger
switch, when the Body Control Module (BCM) rear
window defogger timer and logic circuitry grounds
the relay coil. The rear window defogger relay is
located in the junction block, under the left end of
the instrument panel in the passenger compartment.
The rear window defogger relay is a International
Standards Organization (ISO) relay. Relays conform-
ing to the ISO specifications have common physical
dimensions, current capacities, terminal patterns,
and terminal functions.
The rear window defogger relay cannot be repaired
or adjusted and, if faulty or damaged, it must be
replaced.
OPERATION
The ISO relay consists of an electromagnetic coil, a
resistor or diode, and three (two fixed and one mov-
able) electrical contacts. The movable (common feed)
relay contact is held against one of the fixed contacts
(normally closed) by spring pressure. When the elec-
tromagnetic coil is energized, it draws the movable
contact away from the normally closed fixed contact,
and holds it against the other (normally open) fixed
contact.
When the electromagnetic coil is de-energized,
spring pressure returns the movable contact to the
normally closed position. The resistor or diode is con-
nected in parallel with the electromagnetic coil in the
relay, and helps to dissipate voltage spikes that are
produced when the coil is de-energized.
DIAGNOSIS AND TESTING - REAR WINDOW
DEFOGGER RELAY
WARNING: ON VEHICLES EQUIPPED WITH AIR-
BAGS, DISABLE THE AIRBAG SYSTEM BEFORE
ATTEMPTING ANY STEERING WHEEL, STEERING
COLUMN, OR INSTRUMENT PANEL COMPONENT
DIAGNOSIS OR SERVICE. DISCONNECT AND ISO-
LATE THE BATTERY NEGATIVE (GROUND) CABLE,
THEN WAIT TWO MINUTES FOR THE AIRBAG SYS-
TEM CAPACITOR TO DISCHARGE BEFORE PER-FORMING FURTHER DIAGNOSIS OR SERVICE. THIS
IS THE ONLY SURE WAY TO DISABLE THE AIRBAG
SYSTEM. FAILURE TO TAKE THE PROPER PRE-
CAUTIONS COULD RESULT IN AN ACCIDENTAL
AIRBAG DEPLOYMENT AND POSSIBLE PERSONAL
INJURY.
RELAY TEST
The rear window defogger relay (Fig. 4) is located
in the junction block, under the left end of the instru-
ment panel in the passenger compartment. Remove
the rear window defogger relay from the junction
block to perform the following tests:
(1) A relay in the de-energized position should
have continuity between terminals 87A and 30, and
no continuity between terminals 87 and 30. If OK, go
to Step 2. If not OK, replace the faulty relay.
(2) Resistance between terminals 85 and 86 (elec-
tromagnet) should be 75 Â 10 ohms. If OK, go to Step
3. If not OK, replace the faulty relay.
(3) Connect a battery to terminals 85 and 86.
There should now be continuity between terminals
30 and 87, and no continuity between terminals 87A
and 30. If OK, refer to theRelay Circuit Test.If
not OK, replace the faulty relay.
RELAY CIRCUIT TEST
(1) The relay common feed terminal cavity (30) is
connected to battery voltage and should be hot at all
times. If OK, go to Step 2. If not OK, repair the open
fused B(+) circuit to the Power Distribution Center
(PDC) fuse as required.
(2) The relay normally closed terminal (87A) is
connected to terminal 30 in the de-energized position,
but is not used for this application. Go to Step 3.
Fig. 4 REAR WINDOW DEFOGGER RELAY
TERMINAL LEGEND
NUMBER IDENTIFICATION
30 COMMON FEED
85 COIL GROUND
86 COIL BATTERY
87 NORMALLY OPEN
87A NORMALLY CLOSED
WJHEATED GLASS 8G - 5
REAR WINDOW DEFOGGER GRID (Continued)
Page 381 of 2199
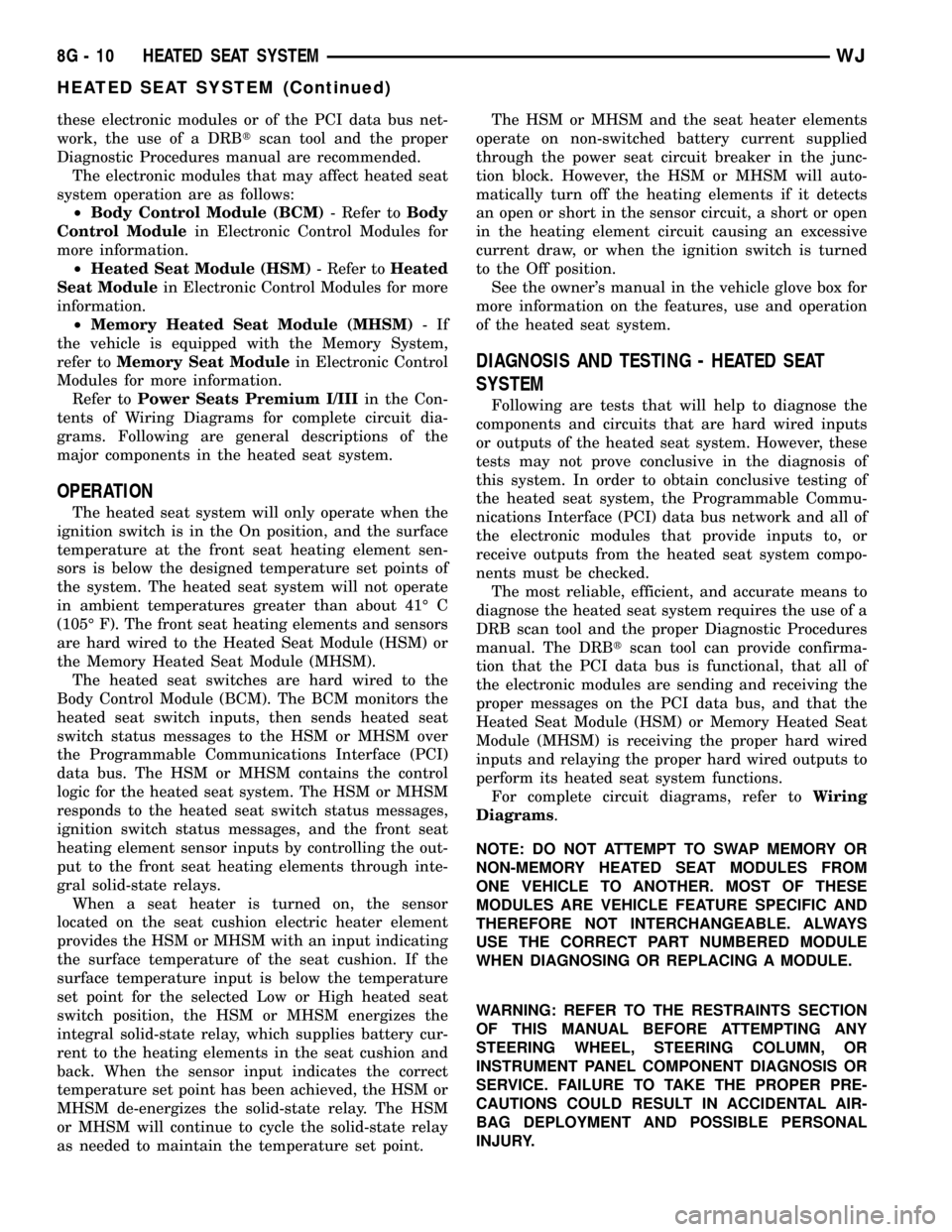
these electronic modules or of the PCI data bus net-
work, the use of a DRBtscan tool and the proper
Diagnostic Procedures manual are recommended.
The electronic modules that may affect heated seat
system operation are as follows:
²Body Control Module (BCM)- Refer toBody
Control Modulein Electronic Control Modules for
more information.
²Heated Seat Module (HSM)- Refer toHeated
Seat Modulein Electronic Control Modules for more
information.
²Memory Heated Seat Module (MHSM)-If
the vehicle is equipped with the Memory System,
refer toMemory Seat Modulein Electronic Control
Modules for more information.
Refer toPower Seats Premium I/IIIin the Con-
tents of Wiring Diagrams for complete circuit dia-
grams. Following are general descriptions of the
major components in the heated seat system.
OPERATION
The heated seat system will only operate when the
ignition switch is in the On position, and the surface
temperature at the front seat heating element sen-
sors is below the designed temperature set points of
the system. The heated seat system will not operate
in ambient temperatures greater than about 41É C
(105É F). The front seat heating elements and sensors
are hard wired to the Heated Seat Module (HSM) or
the Memory Heated Seat Module (MHSM).
The heated seat switches are hard wired to the
Body Control Module (BCM). The BCM monitors the
heated seat switch inputs, then sends heated seat
switch status messages to the HSM or MHSM over
the Programmable Communications Interface (PCI)
data bus. The HSM or MHSM contains the control
logic for the heated seat system. The HSM or MHSM
responds to the heated seat switch status messages,
ignition switch status messages, and the front seat
heating element sensor inputs by controlling the out-
put to the front seat heating elements through inte-
gral solid-state relays.
When a seat heater is turned on, the sensor
located on the seat cushion electric heater element
provides the HSM or MHSM with an input indicating
the surface temperature of the seat cushion. If the
surface temperature input is below the temperature
set point for the selected Low or High heated seat
switch position, the HSM or MHSM energizes the
integral solid-state relay, which supplies battery cur-
rent to the heating elements in the seat cushion and
back. When the sensor input indicates the correct
temperature set point has been achieved, the HSM or
MHSM de-energizes the solid-state relay. The HSM
or MHSM will continue to cycle the solid-state relay
as needed to maintain the temperature set point.The HSM or MHSM and the seat heater elements
operate on non-switched battery current supplied
through the power seat circuit breaker in the junc-
tion block. However, the HSM or MHSM will auto-
matically turn off the heating elements if it detects
an open or short in the sensor circuit, a short or open
in the heating element circuit causing an excessive
current draw, or when the ignition switch is turned
to the Off position.
See the owner's manual in the vehicle glove box for
more information on the features, use and operation
of the heated seat system.
DIAGNOSIS AND TESTING - HEATED SEAT
SYSTEM
Following are tests that will help to diagnose the
components and circuits that are hard wired inputs
or outputs of the heated seat system. However, these
tests may not prove conclusive in the diagnosis of
this system. In order to obtain conclusive testing of
the heated seat system, the Programmable Commu-
nications Interface (PCI) data bus network and all of
the electronic modules that provide inputs to, or
receive outputs from the heated seat system compo-
nents must be checked.
The most reliable, efficient, and accurate means to
diagnose the heated seat system requires the use of a
DRB scan tool and the proper Diagnostic Procedures
manual. The DRBtscan tool can provide confirma-
tion that the PCI data bus is functional, that all of
the electronic modules are sending and receiving the
proper messages on the PCI data bus, and that the
Heated Seat Module (HSM) or Memory Heated Seat
Module (MHSM) is receiving the proper hard wired
inputs and relaying the proper hard wired outputs to
perform its heated seat system functions.
For complete circuit diagrams, refer toWiring
Diagrams.
NOTE: DO NOT ATTEMPT TO SWAP MEMORY OR
NON-MEMORY HEATED SEAT MODULES FROM
ONE VEHICLE TO ANOTHER. MOST OF THESE
MODULES ARE VEHICLE FEATURE SPECIFIC AND
THEREFORE NOT INTERCHANGEABLE. ALWAYS
USE THE CORRECT PART NUMBERED MODULE
WHEN DIAGNOSING OR REPLACING A MODULE.
WARNING: REFER TO THE RESTRAINTS SECTION
OF THIS MANUAL BEFORE ATTEMPTING ANY
STEERING WHEEL, STEERING COLUMN, OR
INSTRUMENT PANEL COMPONENT DIAGNOSIS OR
SERVICE. FAILURE TO TAKE THE PROPER PRE-
CAUTIONS COULD RESULT IN ACCIDENTAL AIR-
BAG DEPLOYMENT AND POSSIBLE PERSONAL
INJURY.
8G - 10 HEATED SEAT SYSTEMWJ
HEATED SEAT SYSTEM (Continued)