headlamp JEEP GRAND CHEROKEE 2003 WJ / 2.G Owner's Manual
[x] Cancel search | Manufacturer: JEEP, Model Year: 2003, Model line: GRAND CHEROKEE, Model: JEEP GRAND CHEROKEE 2003 WJ / 2.GPages: 2199, PDF Size: 76.01 MB
Page 464 of 2199
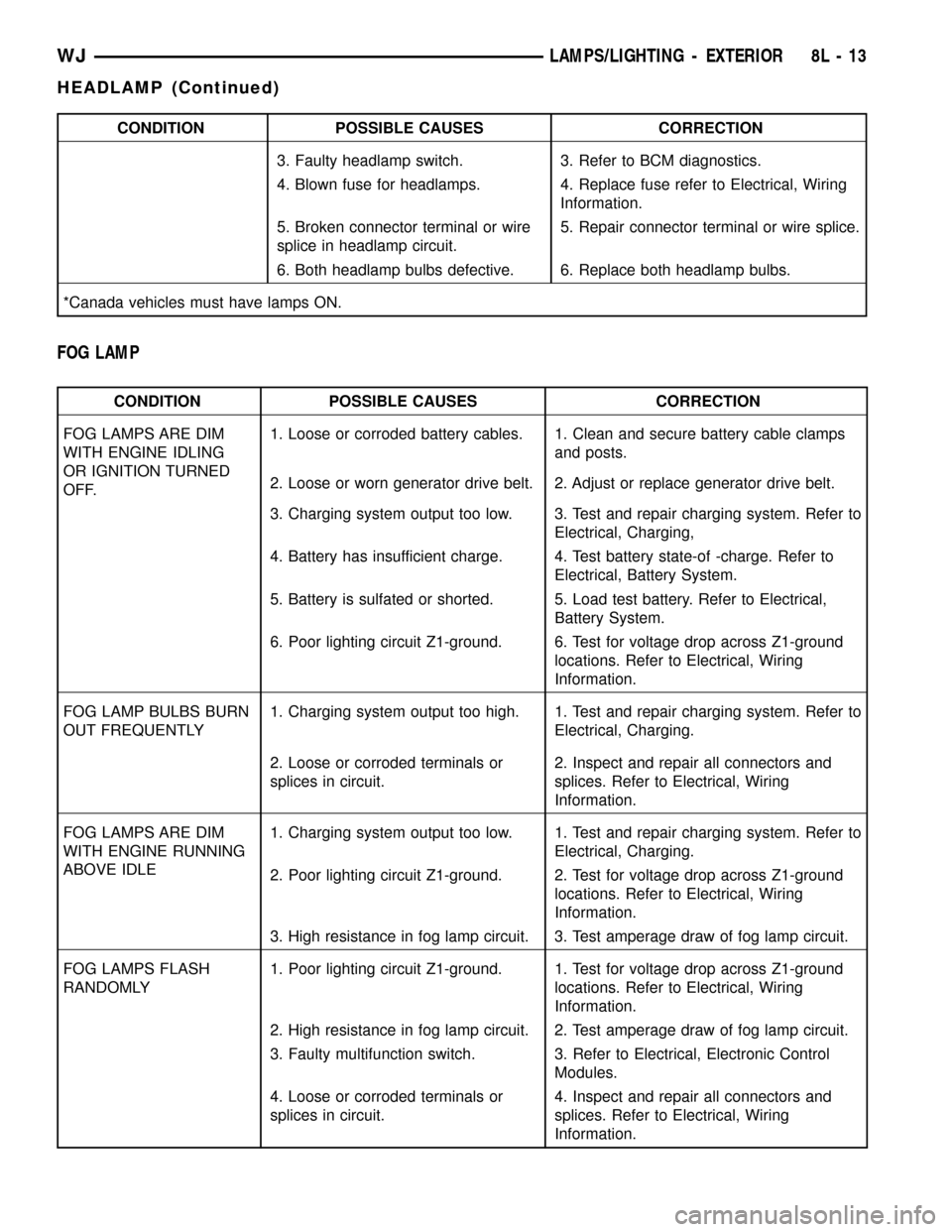
CONDITION POSSIBLE CAUSES CORRECTION
3. Faulty headlamp switch. 3. Refer to BCM diagnostics.
4. Blown fuse for headlamps. 4. Replace fuse refer to Electrical, Wiring
Information.
5. Broken connector terminal or wire
splice in headlamp circuit.5. Repair connector terminal or wire splice.
6. Both headlamp bulbs defective. 6. Replace both headlamp bulbs.
*Canada vehicles must have lamps ON.
FOG LAMP
CONDITION POSSIBLE CAUSES CORRECTION
FOG LAMPS ARE DIM
WITH ENGINE IDLING
OR IGNITION TURNED
OFF.1. Loose or corroded battery cables. 1. Clean and secure battery cable clamps
and posts.
2. Loose or worn generator drive belt. 2. Adjust or replace generator drive belt.
3. Charging system output too low. 3. Test and repair charging system. Refer to
Electrical, Charging,
4. Battery has insufficient charge. 4. Test battery state-of -charge. Refer to
Electrical, Battery System.
5. Battery is sulfated or shorted. 5. Load test battery. Refer to Electrical,
Battery System.
6. Poor lighting circuit Z1-ground. 6. Test for voltage drop across Z1-ground
locations. Refer to Electrical, Wiring
Information.
FOG LAMP BULBS BURN
OUT FREQUENTLY1. Charging system output too high. 1. Test and repair charging system. Refer to
Electrical, Charging.
2. Loose or corroded terminals or
splices in circuit.2. Inspect and repair all connectors and
splices. Refer to Electrical, Wiring
Information.
FOG LAMPS ARE DIM
WITH ENGINE RUNNING
ABOVE IDLE1. Charging system output too low. 1. Test and repair charging system. Refer to
Electrical, Charging.
2. Poor lighting circuit Z1-ground. 2. Test for voltage drop across Z1-ground
locations. Refer to Electrical, Wiring
Information.
3. High resistance in fog lamp circuit. 3. Test amperage draw of fog lamp circuit.
FOG LAMPS FLASH
RANDOMLY1. Poor lighting circuit Z1-ground. 1. Test for voltage drop across Z1-ground
locations. Refer to Electrical, Wiring
Information.
2. High resistance in fog lamp circuit. 2. Test amperage draw of fog lamp circuit.
3. Faulty multifunction switch. 3. Refer to Electrical, Electronic Control
Modules.
4. Loose or corroded terminals or
splices in circuit.4. Inspect and repair all connectors and
splices. Refer to Electrical, Wiring
Information.
WJLAMPS/LIGHTING - EXTERIOR 8L - 13
HEADLAMP (Continued)
Page 465 of 2199
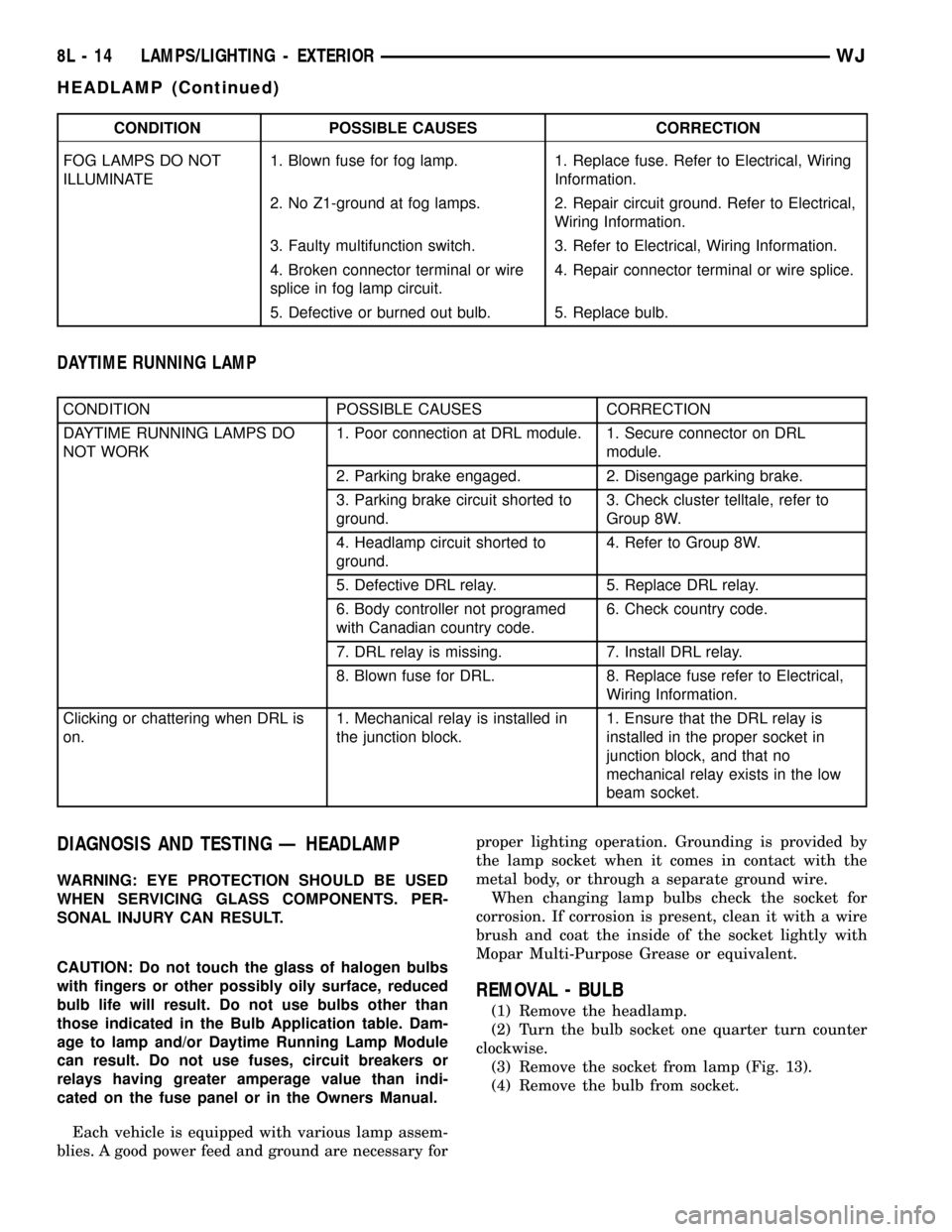
CONDITION POSSIBLE CAUSES CORRECTION
FOG LAMPS DO NOT
ILLUMINATE1. Blown fuse for fog lamp. 1. Replace fuse. Refer to Electrical, Wiring
Information.
2. No Z1-ground at fog lamps. 2. Repair circuit ground. Refer to Electrical,
Wiring Information.
3. Faulty multifunction switch. 3. Refer to Electrical, Wiring Information.
4. Broken connector terminal or wire
splice in fog lamp circuit.4. Repair connector terminal or wire splice.
5. Defective or burned out bulb. 5. Replace bulb.
DAYTIME RUNNING LAMP
CONDITION POSSIBLE CAUSES CORRECTION
DAYTIME RUNNING LAMPS DO
NOT WORK1. Poor connection at DRL module. 1. Secure connector on DRL
module.
2. Parking brake engaged. 2. Disengage parking brake.
3. Parking brake circuit shorted to
ground.3. Check cluster telltale, refer to
Group 8W.
4. Headlamp circuit shorted to
ground.4. Refer to Group 8W.
5. Defective DRL relay. 5. Replace DRL relay.
6. Body controller not programed
with Canadian country code.6. Check country code.
7. DRL relay is missing. 7. Install DRL relay.
8. Blown fuse for DRL. 8. Replace fuse refer to Electrical,
Wiring Information.
Clicking or chattering when DRL is
on.1. Mechanical relay is installed in
the junction block.1. Ensure that the DRL relay is
installed in the proper socket in
junction block, and that no
mechanical relay exists in the low
beam socket.
DIAGNOSIS AND TESTING Ð HEADLAMP
WARNING: EYE PROTECTION SHOULD BE USED
WHEN SERVICING GLASS COMPONENTS. PER-
SONAL INJURY CAN RESULT.
CAUTION: Do not touch the glass of halogen bulbs
with fingers or other possibly oily surface, reduced
bulb life will result. Do not use bulbs other than
those indicated in the Bulb Application table. Dam-
age to lamp and/or Daytime Running Lamp Module
can result. Do not use fuses, circuit breakers or
relays having greater amperage value than indi-
cated on the fuse panel or in the Owners Manual.
Each vehicle is equipped with various lamp assem-
blies. A good power feed and ground are necessary forproper lighting operation. Grounding is provided by
the lamp socket when it comes in contact with the
metal body, or through a separate ground wire.
When changing lamp bulbs check the socket for
corrosion. If corrosion is present, clean it with a wire
brush and coat the inside of the socket lightly with
Mopar Multi-Purpose Grease or equivalent.
REMOVAL - BULB
(1) Remove the headlamp.
(2) Turn the bulb socket one quarter turn counter
clockwise.
(3) Remove the socket from lamp (Fig. 13).
(4) Remove the bulb from socket.
8L - 14 LAMPS/LIGHTING - EXTERIORWJ
HEADLAMP (Continued)
Page 466 of 2199

INSTALLATION - BULB
CAUTION: Do not touch the bulb glass with fingers
or other oily surfaces. Reduced bulb life will result.
(1) Position the bulb into socket and push into
place.
(2) Position the bulb socket in headlamp and turn
the bulb socket one quarter turn clockwise.
(3) Install the headlamp.
HEADLAMP SWITCH
DESCRIPTION
The headlamp switch is part of the left multi-func-
tion switch. A knob on the end of the multi-function
switch control stalk controls all of the exterior light-
ing switch functions. The exterior lighting switch is
hard wired to the Body Control Module (BCM).
The exterior lighting switch cannot be adjusted or
repaired and, if faulty or damaged, the entire left
multi-function switch unit must be replaced. (Refer
to 8 - ELECTRICAL/LAMPS/LIGHTING - EXTERI-
OR/TURN SIGNAL/HAZARD SWITCH - REMOVAL)
for the service procedures. (Refer to 8 - ELECTRI-
CAL/ELECTRONIC CONTROL MODULES/BODY
CONTROL/CENTRAL TIMER MODUL - DESCRIP-
TION) for more information on this component.
OPERATION
The exterior lighting switch uses a hard wired five
volt reference circuit from the BCM, resistor multi-
plexing and a hard wired switch output circuit to
provide the BCM with a zero to five volt signal thatindicates the status of all of the exterior lighting
switch settings. The BCM then uses control outputs
to energize the headlamp and park lamp relays that
activate the exterior lighting circuits.
The BCM monitors the exterior lighting switch sta-
tus, then sends the proper switch status messages to
other modules over the Programmable Communica-
tions Interface (PCI) data bus network. The exterior
lighting switch status is also used by the BCM as an
input for chime warning system operation.
DIAGNOSIS AND TESTING Ð HEADLAMP
SWITCH
Before testing the headlamp switch, turn on the
exterior lighting and open the driver side front door.
If the exterior lamps of the vehicle operate, but there
is no chime warning issued with the driver side front
door open, (Refer to 8 - ELECTRICAL/LAMPS/
LIGHTING - INTERIOR/DOOR AJAR SWITCH -
DIAGNOSIS AND TESTING). If the exterior lamps
of the vehicle are inoperative, but the chime warning
is issued, (Refer to 8 - ELECTRICAL/LAMPS/LIGHT-
ING - EXTERIOR - DIAGNOSIS AND TESTING).
If the exterior lamps and the chime warning are
both inoperative, test the left multi-function switch.
(Refer to 8 - ELECTRICAL/LAMPS/LIGHTING -
EXTERIOR - DIAGNOSIS AND TESTING). If the
multi-function switch tests OK, proceed as follows.
The following tests will help to locate a short or open
in the hard wired circuits between the multi-function
switch and the Body Control Module (BCM). For
complete circuit diagrams, refer to the appropriate
wiring information.
WARNING: ON VEHICLES EQUIPPED WITH AIR-
BAGS, REFER TO ELECTRICAL, RESTRAINTS
BEFORE ATTEMPTING ANY STEERING WHEEL,
STEERING COLUMN, OR INSTRUMENT PANEL
COMPONENT DIAGNOSIS OR SERVICE. FAILURE
TO TAKE THE PROPER PRECAUTIONS COULD
RESULT IN ACCIDENTAL AIRBAG DEPLOYMENT
AND POSSIBLE PERSONAL INJURY.
(1) Disconnect and isolate the battery negative
cable. Disconnect the instrument panel wire harness
connector from the left multi-function switch connec-
tor. Disconnect the instrument panel wire harness
connector from the Body Control Module (BCM).
Check for continuity between the headlamp switch
mux circuit of the instrument panel wire harness
connector for the multi-function switch and a good
ground. There should be no continuity. If OK, go to
Step 2. If not OK, repair the shorted headlamp
switch mux circuit.
(2) Check for continuity between the headlamp
switch mux circuit of the instrument panel wire har-
Fig. 13 Headlamp Bulb
1 - HIGH BEAM BULB
2 - LOW BEAM BULB
3 - MARKER BULB
4 - PARK/TURN SIGNAL BULB
WJLAMPS/LIGHTING - EXTERIOR 8L - 15
HEADLAMP (Continued)
Page 467 of 2199
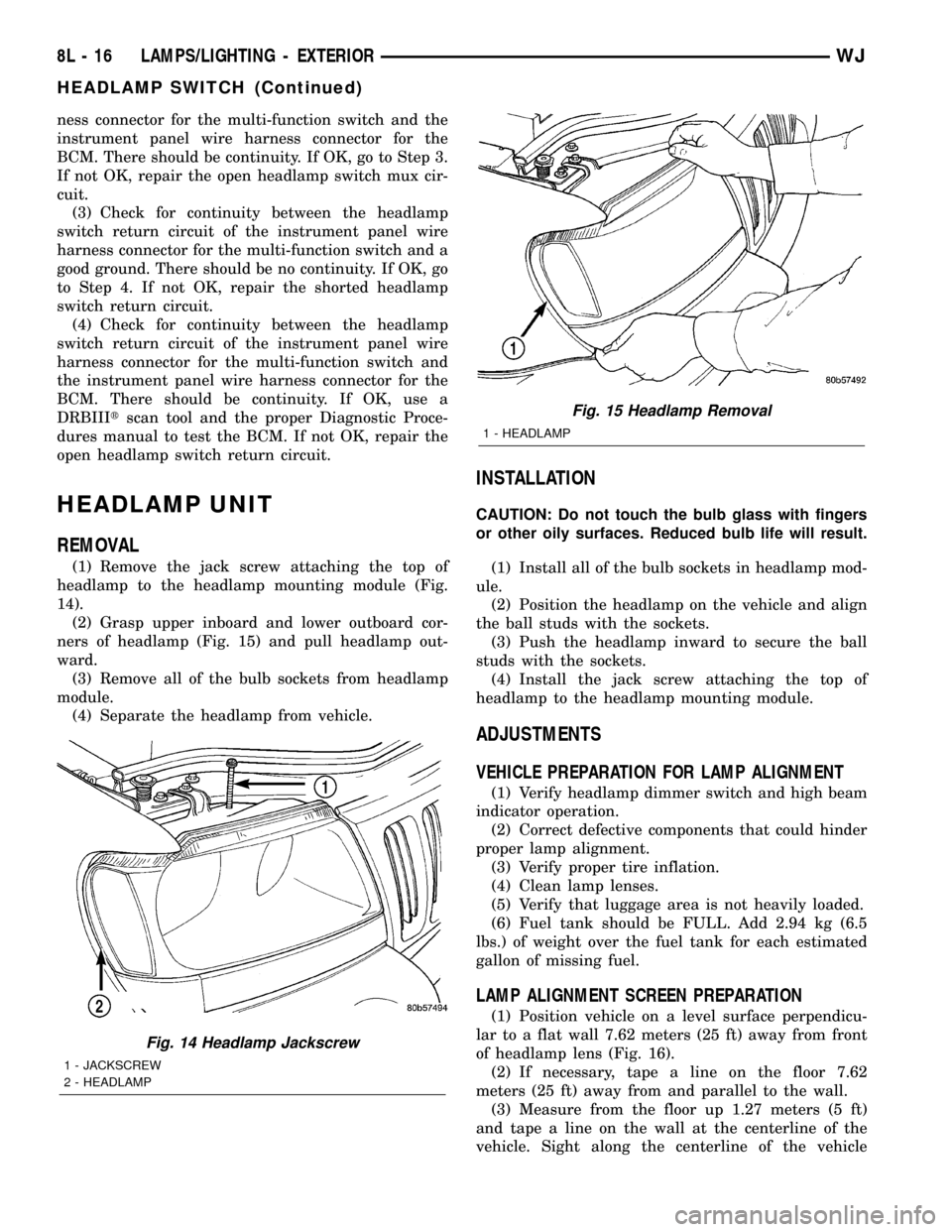
ness connector for the multi-function switch and the
instrument panel wire harness connector for the
BCM. There should be continuity. If OK, go to Step 3.
If not OK, repair the open headlamp switch mux cir-
cuit.
(3) Check for continuity between the headlamp
switch return circuit of the instrument panel wire
harness connector for the multi-function switch and a
good ground. There should be no continuity. If OK, go
to Step 4. If not OK, repair the shorted headlamp
switch return circuit.
(4) Check for continuity between the headlamp
switch return circuit of the instrument panel wire
harness connector for the multi-function switch and
the instrument panel wire harness connector for the
BCM. There should be continuity. If OK, use a
DRBIIItscan tool and the proper Diagnostic Proce-
dures manual to test the BCM. If not OK, repair the
open headlamp switch return circuit.
HEADLAMP UNIT
REMOVAL
(1) Remove the jack screw attaching the top of
headlamp to the headlamp mounting module (Fig.
14).
(2) Grasp upper inboard and lower outboard cor-
ners of headlamp (Fig. 15) and pull headlamp out-
ward.
(3) Remove all of the bulb sockets from headlamp
module.
(4) Separate the headlamp from vehicle.
INSTALLATION
CAUTION: Do not touch the bulb glass with fingers
or other oily surfaces. Reduced bulb life will result.
(1) Install all of the bulb sockets in headlamp mod-
ule.
(2) Position the headlamp on the vehicle and align
the ball studs with the sockets.
(3) Push the headlamp inward to secure the ball
studs with the sockets.
(4) Install the jack screw attaching the top of
headlamp to the headlamp mounting module.
ADJUSTMENTS
VEHICLE PREPARATION FOR LAMP ALIGNMENT
(1) Verify headlamp dimmer switch and high beam
indicator operation.
(2) Correct defective components that could hinder
proper lamp alignment.
(3) Verify proper tire inflation.
(4) Clean lamp lenses.
(5) Verify that luggage area is not heavily loaded.
(6) Fuel tank should be FULL. Add 2.94 kg (6.5
lbs.) of weight over the fuel tank for each estimated
gallon of missing fuel.
LAMP ALIGNMENT SCREEN PREPARATION
(1) Position vehicle on a level surface perpendicu-
lar to a flat wall 7.62 meters (25 ft) away from front
of headlamp lens (Fig. 16).
(2) If necessary, tape a line on the floor 7.62
meters (25 ft) away from and parallel to the wall.
(3) Measure from the floor up 1.27 meters (5 ft)
and tape a line on the wall at the centerline of the
vehicle. Sight along the centerline of the vehicle
Fig. 14 Headlamp Jackscrew
1 - JACKSCREW
2 - HEADLAMP
Fig. 15 Headlamp Removal
1 - HEADLAMP
8L - 16 LAMPS/LIGHTING - EXTERIORWJ
HEADLAMP SWITCH (Continued)
Page 468 of 2199
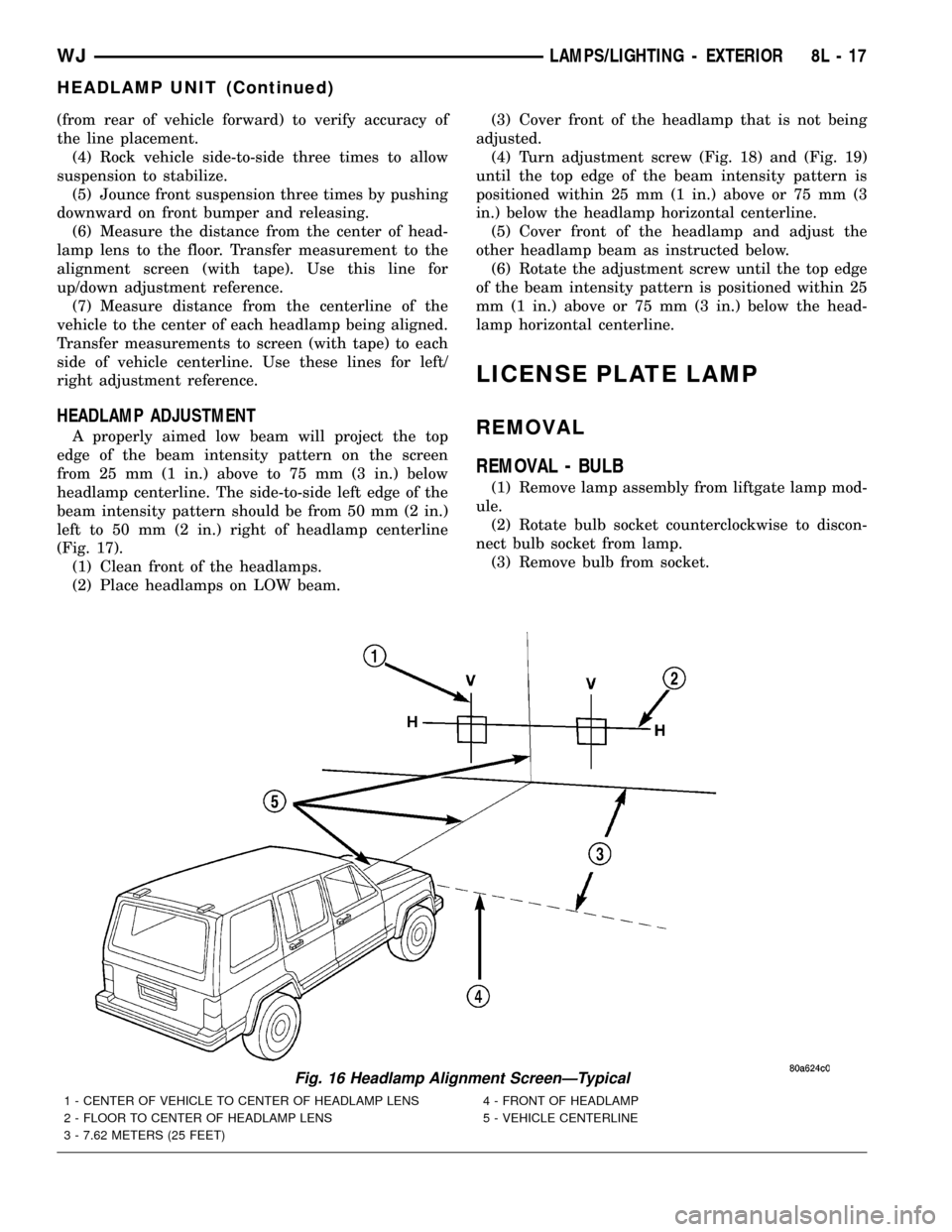
(from rear of vehicle forward) to verify accuracy of
the line placement.
(4) Rock vehicle side-to-side three times to allow
suspension to stabilize.
(5) Jounce front suspension three times by pushing
downward on front bumper and releasing.
(6) Measure the distance from the center of head-
lamp lens to the floor. Transfer measurement to the
alignment screen (with tape). Use this line for
up/down adjustment reference.
(7) Measure distance from the centerline of the
vehicle to the center of each headlamp being aligned.
Transfer measurements to screen (with tape) to each
side of vehicle centerline. Use these lines for left/
right adjustment reference.
HEADLAMP ADJUSTMENT
A properly aimed low beam will project the top
edge of the beam intensity pattern on the screen
from 25 mm (1 in.) above to 75 mm (3 in.) below
headlamp centerline. The side-to-side left edge of the
beam intensity pattern should be from 50 mm (2 in.)
left to 50 mm (2 in.) right of headlamp centerline
(Fig. 17).
(1) Clean front of the headlamps.
(2) Place headlamps on LOW beam.(3) Cover front of the headlamp that is not being
adjusted.
(4) Turn adjustment screw (Fig. 18) and (Fig. 19)
until the top edge of the beam intensity pattern is
positioned within 25 mm (1 in.) above or 75 mm (3
in.) below the headlamp horizontal centerline.
(5) Cover front of the headlamp and adjust the
other headlamp beam as instructed below.
(6) Rotate the adjustment screw until the top edge
of the beam intensity pattern is positioned within 25
mm (1 in.) above or 75 mm (3 in.) below the head-
lamp horizontal centerline.
LICENSE PLATE LAMP
REMOVAL
REMOVAL - BULB
(1) Remove lamp assembly from liftgate lamp mod-
ule.
(2) Rotate bulb socket counterclockwise to discon-
nect bulb socket from lamp.
(3) Remove bulb from socket.
Fig. 16 Headlamp Alignment ScreenÐTypical
1 - CENTER OF VEHICLE TO CENTER OF HEADLAMP LENS
2 - FLOOR TO CENTER OF HEADLAMP LENS
3 - 7.62 METERS (25 FEET)4 - FRONT OF HEADLAMP
5 - VEHICLE CENTERLINE
WJLAMPS/LIGHTING - EXTERIOR 8L - 17
HEADLAMP UNIT (Continued)
Page 469 of 2199
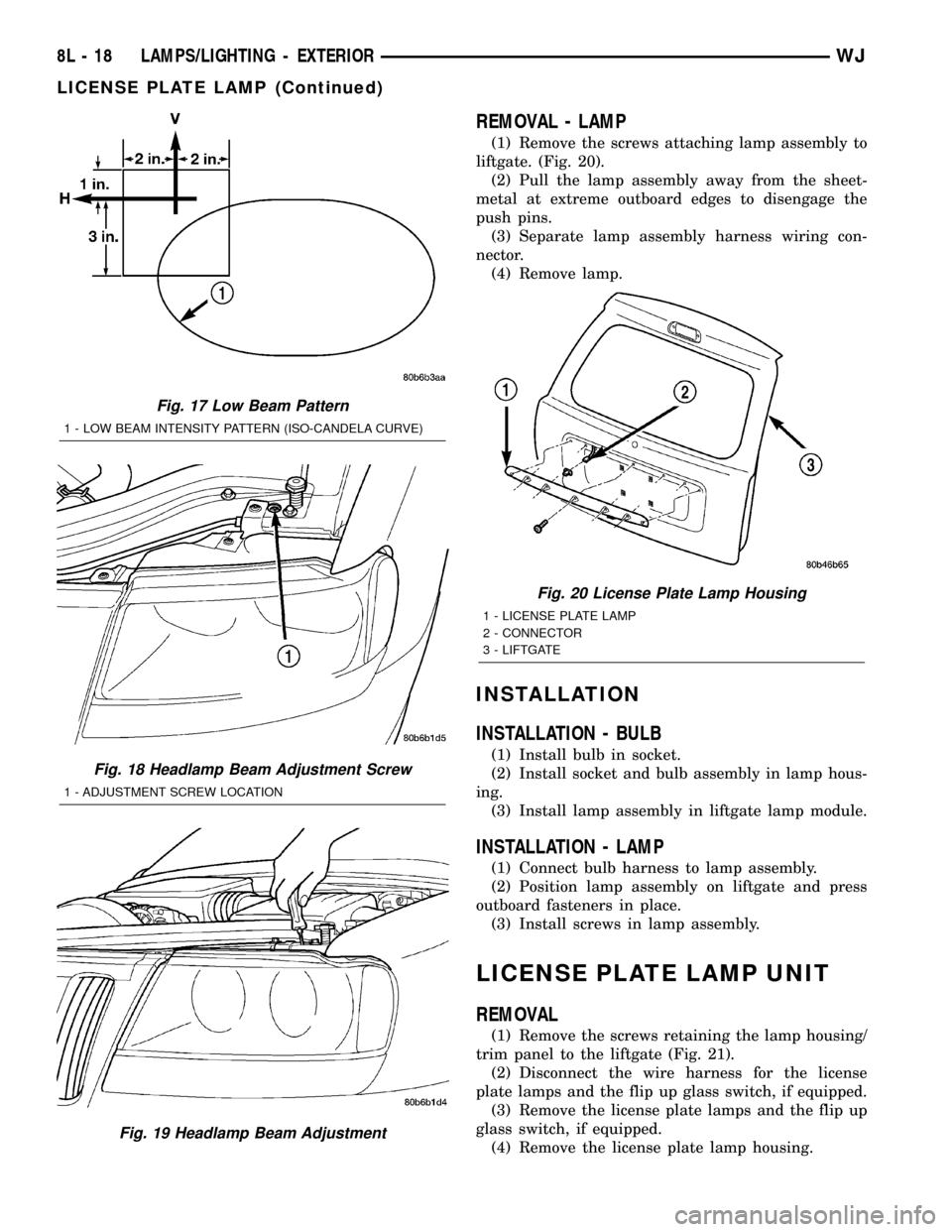
REMOVAL - LAMP
(1) Remove the screws attaching lamp assembly to
liftgate. (Fig. 20).
(2) Pull the lamp assembly away from the sheet-
metal at extreme outboard edges to disengage the
push pins.
(3) Separate lamp assembly harness wiring con-
nector.
(4) Remove lamp.
INSTALLATION
INSTALLATION - BULB
(1) Install bulb in socket.
(2) Install socket and bulb assembly in lamp hous-
ing.
(3) Install lamp assembly in liftgate lamp module.
INSTALLATION - LAMP
(1) Connect bulb harness to lamp assembly.
(2) Position lamp assembly on liftgate and press
outboard fasteners in place.
(3) Install screws in lamp assembly.
LICENSE PLATE LAMP UNIT
REMOVAL
(1) Remove the screws retaining the lamp housing/
trim panel to the liftgate (Fig. 21).
(2) Disconnect the wire harness for the license
plate lamps and the flip up glass switch, if equipped.
(3) Remove the license plate lamps and the flip up
glass switch, if equipped.
(4) Remove the license plate lamp housing.
Fig. 17 Low Beam Pattern
1 - LOW BEAM INTENSITY PATTERN (ISO-CANDELA CURVE)
Fig. 18 Headlamp Beam Adjustment Screw
1 - ADJUSTMENT SCREW LOCATION
Fig. 19 Headlamp Beam Adjustment
Fig. 20 License Plate Lamp Housing
1 - LICENSE PLATE LAMP
2 - CONNECTOR
3 - LIFTGATE
8L - 18 LAMPS/LIGHTING - EXTERIORWJ
LICENSE PLATE LAMP (Continued)
Page 470 of 2199
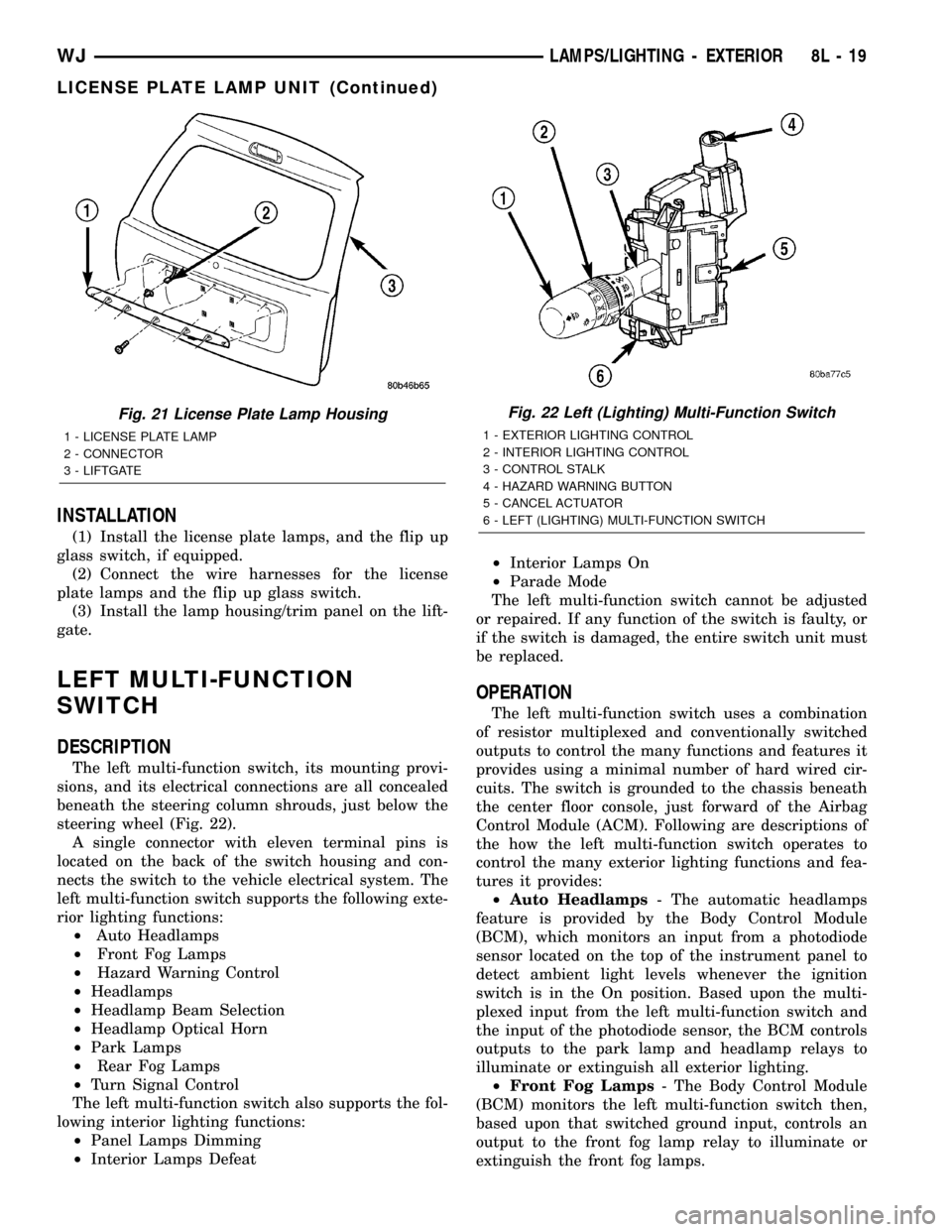
INSTALLATION
(1) Install the license plate lamps, and the flip up
glass switch, if equipped.
(2) Connect the wire harnesses for the license
plate lamps and the flip up glass switch.
(3) Install the lamp housing/trim panel on the lift-
gate.
LEFT MULTI-FUNCTION
SWITCH
DESCRIPTION
The left multi-function switch, its mounting provi-
sions, and its electrical connections are all concealed
beneath the steering column shrouds, just below the
steering wheel (Fig. 22).
A single connector with eleven terminal pins is
located on the back of the switch housing and con-
nects the switch to the vehicle electrical system. The
left multi-function switch supports the following exte-
rior lighting functions:
²Auto Headlamps
²Front Fog Lamps
²Hazard Warning Control
²Headlamps
²Headlamp Beam Selection
²Headlamp Optical Horn
²Park Lamps
²Rear Fog Lamps
²Turn Signal Control
The left multi-function switch also supports the fol-
lowing interior lighting functions:
²Panel Lamps Dimming
²Interior Lamps Defeat²Interior Lamps On
²Parade Mode
The left multi-function switch cannot be adjusted
or repaired. If any function of the switch is faulty, or
if the switch is damaged, the entire switch unit must
be replaced.
OPERATION
The left multi-function switch uses a combination
of resistor multiplexed and conventionally switched
outputs to control the many functions and features it
provides using a minimal number of hard wired cir-
cuits. The switch is grounded to the chassis beneath
the center floor console, just forward of the Airbag
Control Module (ACM). Following are descriptions of
the how the left multi-function switch operates to
control the many exterior lighting functions and fea-
tures it provides:
²Auto Headlamps- The automatic headlamps
feature is provided by the Body Control Module
(BCM), which monitors an input from a photodiode
sensor located on the top of the instrument panel to
detect ambient light levels whenever the ignition
switch is in the On position. Based upon the multi-
plexed input from the left multi-function switch and
the input of the photodiode sensor, the BCM controls
outputs to the park lamp and headlamp relays to
illuminate or extinguish all exterior lighting.
²Front Fog Lamps- The Body Control Module
(BCM) monitors the left multi-function switch then,
based upon that switched ground input, controls an
output to the front fog lamp relay to illuminate or
extinguish the front fog lamps.
Fig. 21 License Plate Lamp Housing
1 - LICENSE PLATE LAMP
2 - CONNECTOR
3 - LIFTGATE
Fig. 22 Left (Lighting) Multi-Function Switch
1 - EXTERIOR LIGHTING CONTROL
2 - INTERIOR LIGHTING CONTROL
3 - CONTROL STALK
4 - HAZARD WARNING BUTTON
5 - CANCEL ACTUATOR
6 - LEFT (LIGHTING) MULTI-FUNCTION SWITCH
WJLAMPS/LIGHTING - EXTERIOR 8L - 19
LICENSE PLATE LAMP UNIT (Continued)
Page 471 of 2199
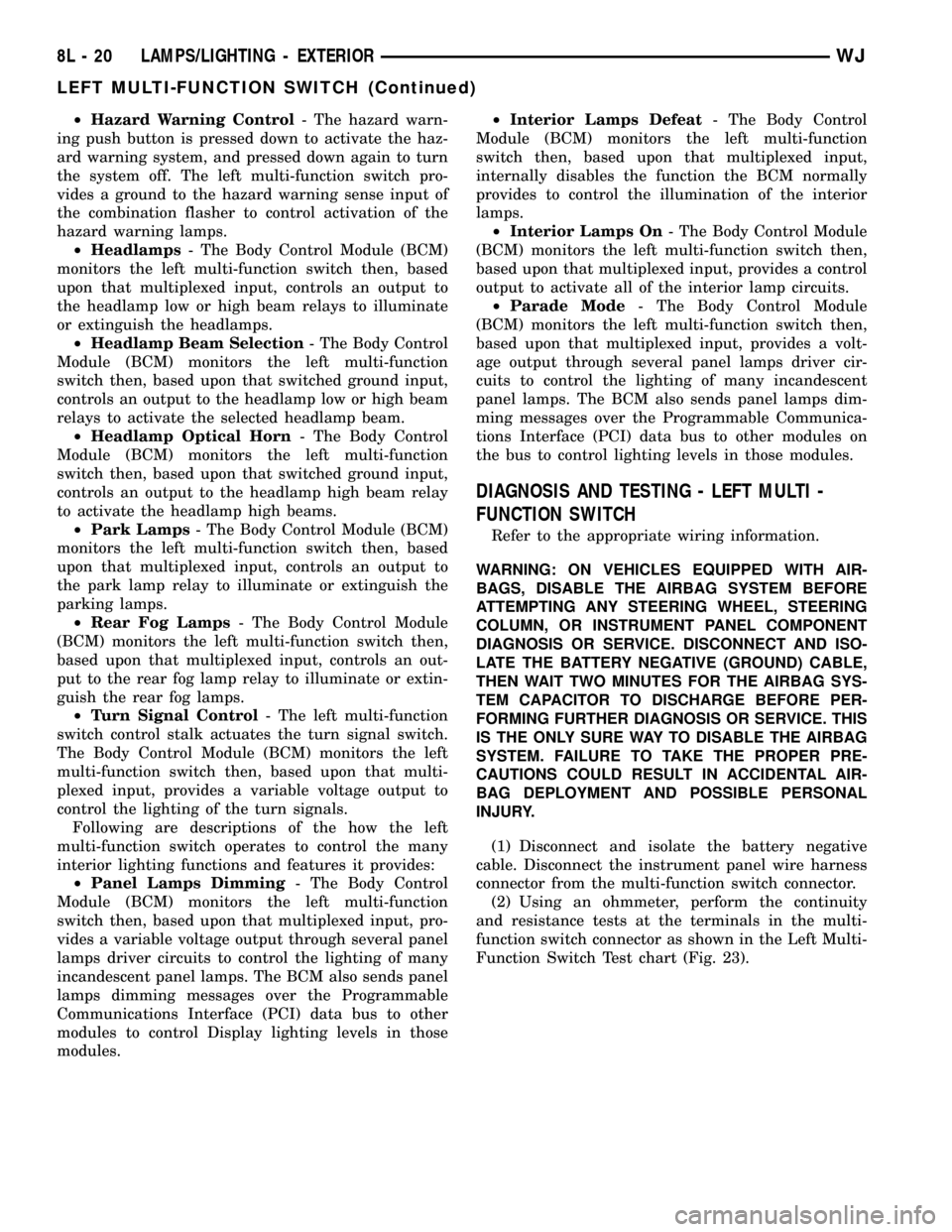
²Hazard Warning Control- The hazard warn-
ing push button is pressed down to activate the haz-
ard warning system, and pressed down again to turn
the system off. The left multi-function switch pro-
vides a ground to the hazard warning sense input of
the combination flasher to control activation of the
hazard warning lamps.
²Headlamps- The Body Control Module (BCM)
monitors the left multi-function switch then, based
upon that multiplexed input, controls an output to
the headlamp low or high beam relays to illuminate
or extinguish the headlamps.
²Headlamp Beam Selection- The Body Control
Module (BCM) monitors the left multi-function
switch then, based upon that switched ground input,
controls an output to the headlamp low or high beam
relays to activate the selected headlamp beam.
²Headlamp Optical Horn- The Body Control
Module (BCM) monitors the left multi-function
switch then, based upon that switched ground input,
controls an output to the headlamp high beam relay
to activate the headlamp high beams.
²Park Lamps- The Body Control Module (BCM)
monitors the left multi-function switch then, based
upon that multiplexed input, controls an output to
the park lamp relay to illuminate or extinguish the
parking lamps.
²Rear Fog Lamps- The Body Control Module
(BCM) monitors the left multi-function switch then,
based upon that multiplexed input, controls an out-
put to the rear fog lamp relay to illuminate or extin-
guish the rear fog lamps.
²Turn Signal Control- The left multi-function
switch control stalk actuates the turn signal switch.
The Body Control Module (BCM) monitors the left
multi-function switch then, based upon that multi-
plexed input, provides a variable voltage output to
control the lighting of the turn signals.
Following are descriptions of the how the left
multi-function switch operates to control the many
interior lighting functions and features it provides:
²Panel Lamps Dimming- The Body Control
Module (BCM) monitors the left multi-function
switch then, based upon that multiplexed input, pro-
vides a variable voltage output through several panel
lamps driver circuits to control the lighting of many
incandescent panel lamps. The BCM also sends panel
lamps dimming messages over the Programmable
Communications Interface (PCI) data bus to other
modules to control Display lighting levels in those
modules.²Interior Lamps Defeat- The Body Control
Module (BCM) monitors the left multi-function
switch then, based upon that multiplexed input,
internally disables the function the BCM normally
provides to control the illumination of the interior
lamps.
²Interior Lamps On- The Body Control Module
(BCM) monitors the left multi-function switch then,
based upon that multiplexed input, provides a control
output to activate all of the interior lamp circuits.
²Parade Mode- The Body Control Module
(BCM) monitors the left multi-function switch then,
based upon that multiplexed input, provides a volt-
age output through several panel lamps driver cir-
cuits to control the lighting of many incandescent
panel lamps. The BCM also sends panel lamps dim-
ming messages over the Programmable Communica-
tions Interface (PCI) data bus to other modules on
the bus to control lighting levels in those modules.
DIAGNOSIS AND TESTING - LEFT MULTI -
FUNCTION SWITCH
Refer to the appropriate wiring information.
WARNING: ON VEHICLES EQUIPPED WITH AIR-
BAGS, DISABLE THE AIRBAG SYSTEM BEFORE
ATTEMPTING ANY STEERING WHEEL, STEERING
COLUMN, OR INSTRUMENT PANEL COMPONENT
DIAGNOSIS OR SERVICE. DISCONNECT AND ISO-
LATE THE BATTERY NEGATIVE (GROUND) CABLE,
THEN WAIT TWO MINUTES FOR THE AIRBAG SYS-
TEM CAPACITOR TO DISCHARGE BEFORE PER-
FORMING FURTHER DIAGNOSIS OR SERVICE. THIS
IS THE ONLY SURE WAY TO DISABLE THE AIRBAG
SYSTEM. FAILURE TO TAKE THE PROPER PRE-
CAUTIONS COULD RESULT IN ACCIDENTAL AIR-
BAG DEPLOYMENT AND POSSIBLE PERSONAL
INJURY.
(1) Disconnect and isolate the battery negative
cable. Disconnect the instrument panel wire harness
connector from the multi-function switch connector.
(2) Using an ohmmeter, perform the continuity
and resistance tests at the terminals in the multi-
function switch connector as shown in the Left Multi-
Function Switch Test chart (Fig. 23).
8L - 20 LAMPS/LIGHTING - EXTERIORWJ
LEFT MULTI-FUNCTION SWITCH (Continued)
Page 472 of 2199
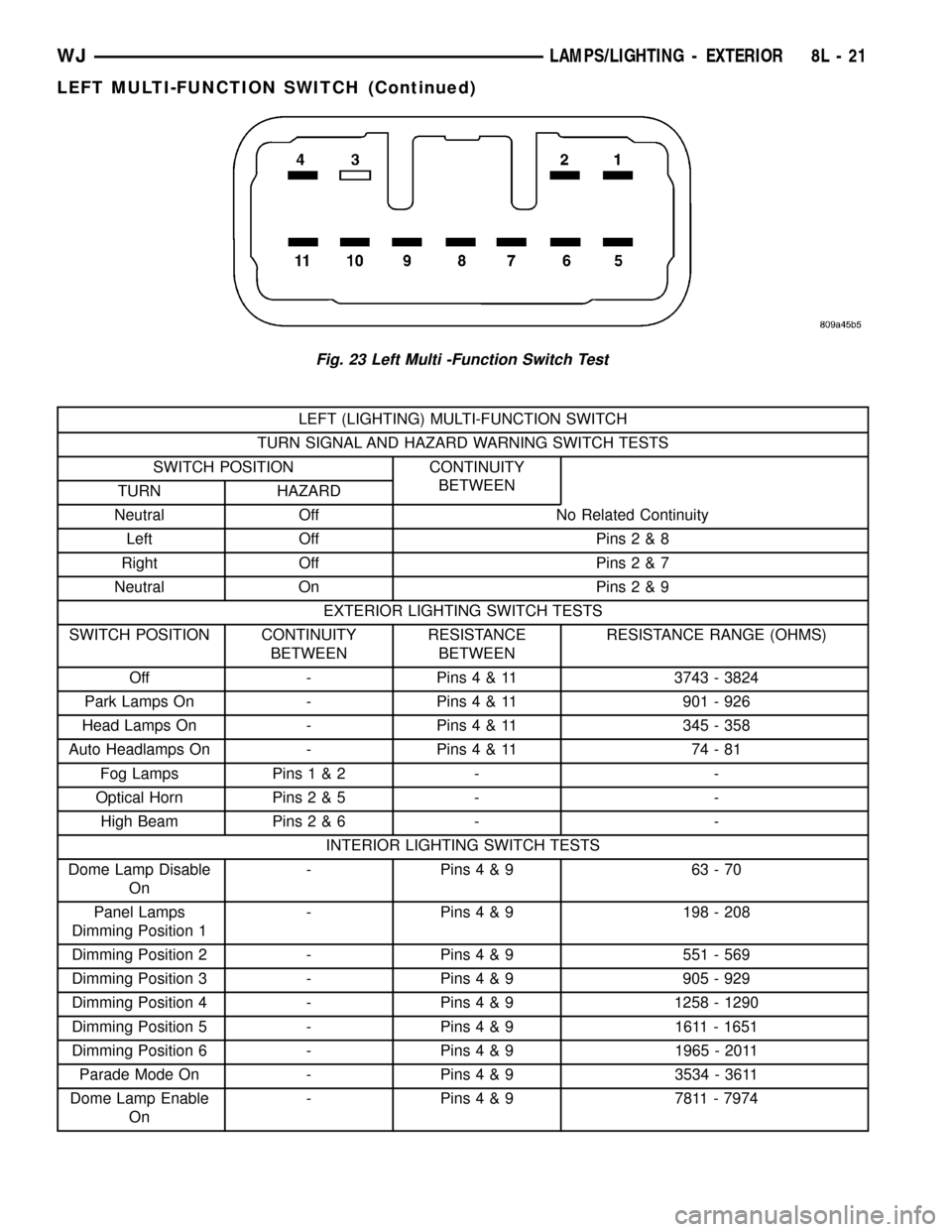
LEFT (LIGHTING) MULTI-FUNCTION SWITCH
TURN SIGNAL AND HAZARD WARNING SWITCH TESTS
SWITCH POSITION CONTINUITY
BETWEEN
TURN HAZARD
Neutral Off No Related Continuity
Left Off Pins2&8
Right Off Pins2&7
Neutral On Pins2&9
EXTERIOR LIGHTING SWITCH TESTS
SWITCH POSITION CONTINUITY
BETWEENRESISTANCE
BETWEENRESISTANCE RANGE (OHMS)
Off - Pins4&113743 - 3824
Park Lamps On - Pins4&11 901-926
Head Lamps On - Pins4&11 345-358
Auto Headlamps On - Pins4&11 74-81
Fog Lamps Pins1&2 - -
Optical Horn Pins2&5 - -
High Beam Pins2&6 - -
INTERIOR LIGHTING SWITCH TESTS
Dome Lamp Disable
On- Pins4&9 63-70
Panel Lamps
Dimming Position 1- Pins4&9 198-208
Dimming Position 2 - Pins4&9 551-569
Dimming Position 3 - Pins4&9 905-929
Dimming Position 4 - Pins4&91258 - 1290
Dimming Position 5 - Pins4&9 1611-1651
Dimming Position 6 - Pins4&91965 - 2011
Parade Mode On - Pins4&93534 - 3611
Dome Lamp Enable
On- Pins4&9 7811-7974
Fig. 23 Left Multi -Function Switch Test
WJLAMPS/LIGHTING - EXTERIOR 8L - 21
LEFT MULTI-FUNCTION SWITCH (Continued)
Page 476 of 2199
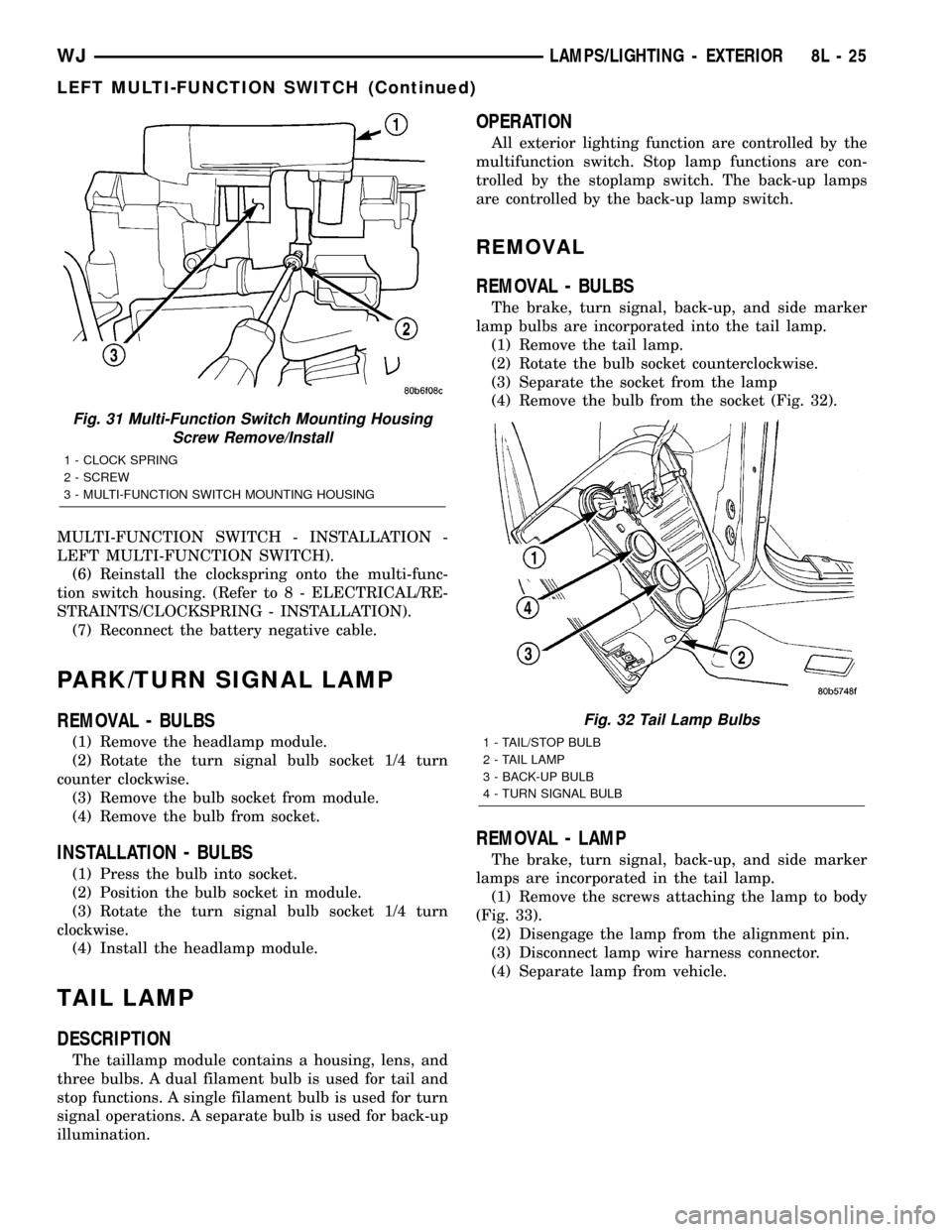
MULTI-FUNCTION SWITCH - INSTALLATION -
LEFT MULTI-FUNCTION SWITCH).
(6) Reinstall the clockspring onto the multi-func-
tion switch housing. (Refer to 8 - ELECTRICAL/RE-
STRAINTS/CLOCKSPRING - INSTALLATION).
(7) Reconnect the battery negative cable.
PARK/TURN SIGNAL LAMP
REMOVAL - BULBS
(1) Remove the headlamp module.
(2) Rotate the turn signal bulb socket 1/4 turn
counter clockwise.
(3) Remove the bulb socket from module.
(4) Remove the bulb from socket.
INSTALLATION - BULBS
(1) Press the bulb into socket.
(2) Position the bulb socket in module.
(3) Rotate the turn signal bulb socket 1/4 turn
clockwise.
(4) Install the headlamp module.
TAIL LAMP
DESCRIPTION
The taillamp module contains a housing, lens, and
three bulbs. A dual filament bulb is used for tail and
stop functions. A single filament bulb is used for turn
signal operations. A separate bulb is used for back-up
illumination.
OPERATION
All exterior lighting function are controlled by the
multifunction switch. Stop lamp functions are con-
trolled by the stoplamp switch. The back-up lamps
are controlled by the back-up lamp switch.
REMOVAL
REMOVAL - BULBS
The brake, turn signal, back-up, and side marker
lamp bulbs are incorporated into the tail lamp.
(1) Remove the tail lamp.
(2) Rotate the bulb socket counterclockwise.
(3) Separate the socket from the lamp
(4) Remove the bulb from the socket (Fig. 32).
REMOVAL - LAMP
The brake, turn signal, back-up, and side marker
lamps are incorporated in the tail lamp.
(1) Remove the screws attaching the lamp to body
(Fig. 33).
(2) Disengage the lamp from the alignment pin.
(3) Disconnect lamp wire harness connector.
(4) Separate lamp from vehicle.
Fig. 31 Multi-Function Switch Mounting Housing
Screw Remove/Install
1 - CLOCK SPRING
2 - SCREW
3 - MULTI-FUNCTION SWITCH MOUNTING HOUSING
Fig. 32 Tail Lamp Bulbs
1 - TAIL/STOP BULB
2 - TAIL LAMP
3 - BACK-UP BULB
4 - TURN SIGNAL BULB
WJLAMPS/LIGHTING - EXTERIOR 8L - 25
LEFT MULTI-FUNCTION SWITCH (Continued)