fuse diagram JEEP GRAND CHEROKEE 2003 WJ / 2.G Workshop Manual
[x] Cancel search | Manufacturer: JEEP, Model Year: 2003, Model line: GRAND CHEROKEE, Model: JEEP GRAND CHEROKEE 2003 WJ / 2.GPages: 2199, PDF Size: 76.01 MB
Page 282 of 2199
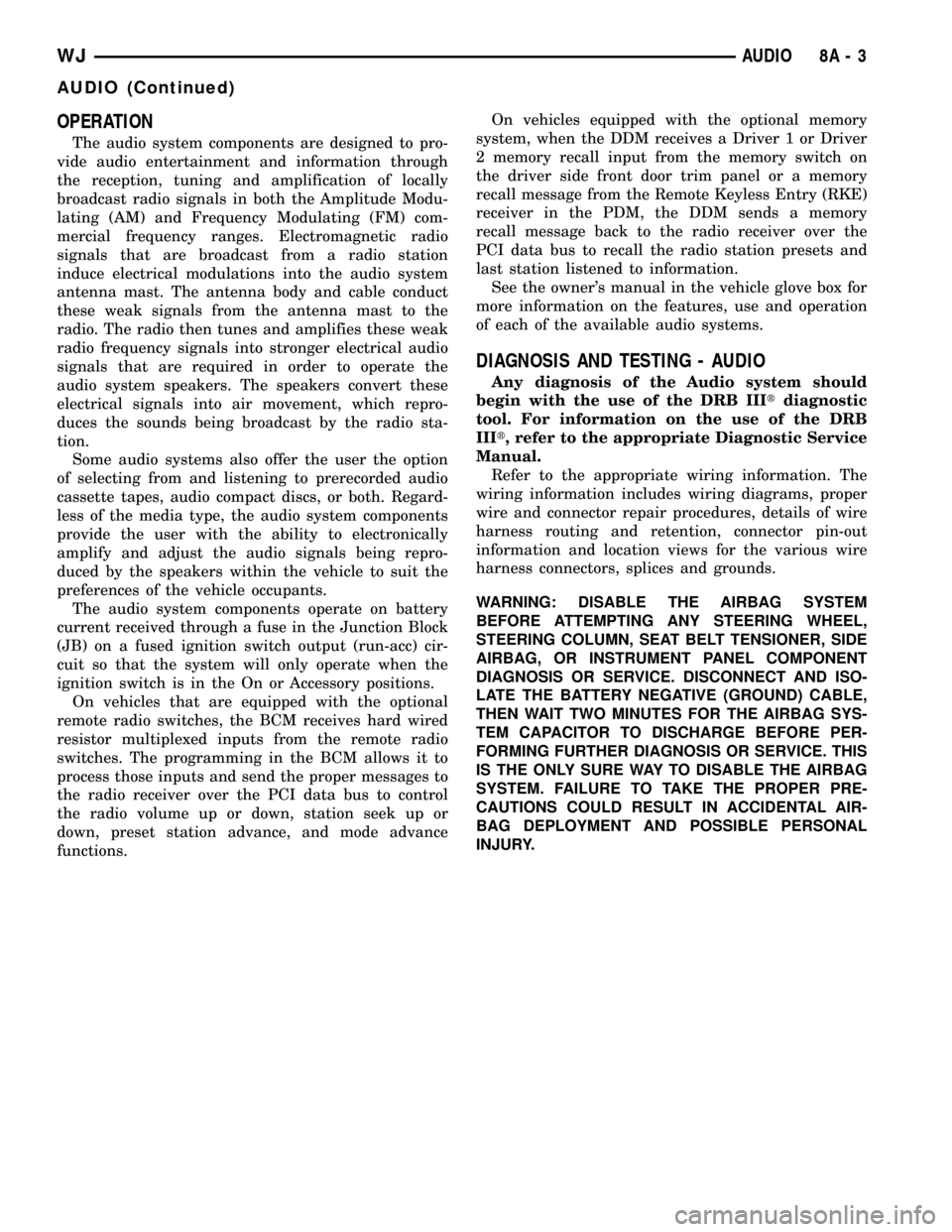
OPERATION
The audio system components are designed to pro-
vide audio entertainment and information through
the reception, tuning and amplification of locally
broadcast radio signals in both the Amplitude Modu-
lating (AM) and Frequency Modulating (FM) com-
mercial frequency ranges. Electromagnetic radio
signals that are broadcast from a radio station
induce electrical modulations into the audio system
antenna mast. The antenna body and cable conduct
these weak signals from the antenna mast to the
radio. The radio then tunes and amplifies these weak
radio frequency signals into stronger electrical audio
signals that are required in order to operate the
audio system speakers. The speakers convert these
electrical signals into air movement, which repro-
duces the sounds being broadcast by the radio sta-
tion.
Some audio systems also offer the user the option
of selecting from and listening to prerecorded audio
cassette tapes, audio compact discs, or both. Regard-
less of the media type, the audio system components
provide the user with the ability to electronically
amplify and adjust the audio signals being repro-
duced by the speakers within the vehicle to suit the
preferences of the vehicle occupants.
The audio system components operate on battery
current received through a fuse in the Junction Block
(JB) on a fused ignition switch output (run-acc) cir-
cuit so that the system will only operate when the
ignition switch is in the On or Accessory positions.
On vehicles that are equipped with the optional
remote radio switches, the BCM receives hard wired
resistor multiplexed inputs from the remote radio
switches. The programming in the BCM allows it to
process those inputs and send the proper messages to
the radio receiver over the PCI data bus to control
the radio volume up or down, station seek up or
down, preset station advance, and mode advance
functions.On vehicles equipped with the optional memory
system, when the DDM receives a Driver 1 or Driver
2 memory recall input from the memory switch on
the driver side front door trim panel or a memory
recall message from the Remote Keyless Entry (RKE)
receiver in the PDM, the DDM sends a memory
recall message back to the radio receiver over the
PCI data bus to recall the radio station presets and
last station listened to information.
See the owner's manual in the vehicle glove box for
more information on the features, use and operation
of each of the available audio systems.
DIAGNOSIS AND TESTING - AUDIO
Any diagnosis of the Audio system should
begin with the use of the DRB IIItdiagnostic
tool. For information on the use of the DRB
IIIt, refer to the appropriate Diagnostic Service
Manual.
Refer to the appropriate wiring information. The
wiring information includes wiring diagrams, proper
wire and connector repair procedures, details of wire
harness routing and retention, connector pin-out
information and location views for the various wire
harness connectors, splices and grounds.
WARNING: DISABLE THE AIRBAG SYSTEM
BEFORE ATTEMPTING ANY STEERING WHEEL,
STEERING COLUMN, SEAT BELT TENSIONER, SIDE
AIRBAG, OR INSTRUMENT PANEL COMPONENT
DIAGNOSIS OR SERVICE. DISCONNECT AND ISO-
LATE THE BATTERY NEGATIVE (GROUND) CABLE,
THEN WAIT TWO MINUTES FOR THE AIRBAG SYS-
TEM CAPACITOR TO DISCHARGE BEFORE PER-
FORMING FURTHER DIAGNOSIS OR SERVICE. THIS
IS THE ONLY SURE WAY TO DISABLE THE AIRBAG
SYSTEM. FAILURE TO TAKE THE PROPER PRE-
CAUTIONS COULD RESULT IN ACCIDENTAL AIR-
BAG DEPLOYMENT AND POSSIBLE PERSONAL
INJURY.
WJAUDIO 8A - 3
AUDIO (Continued)
Page 285 of 2199
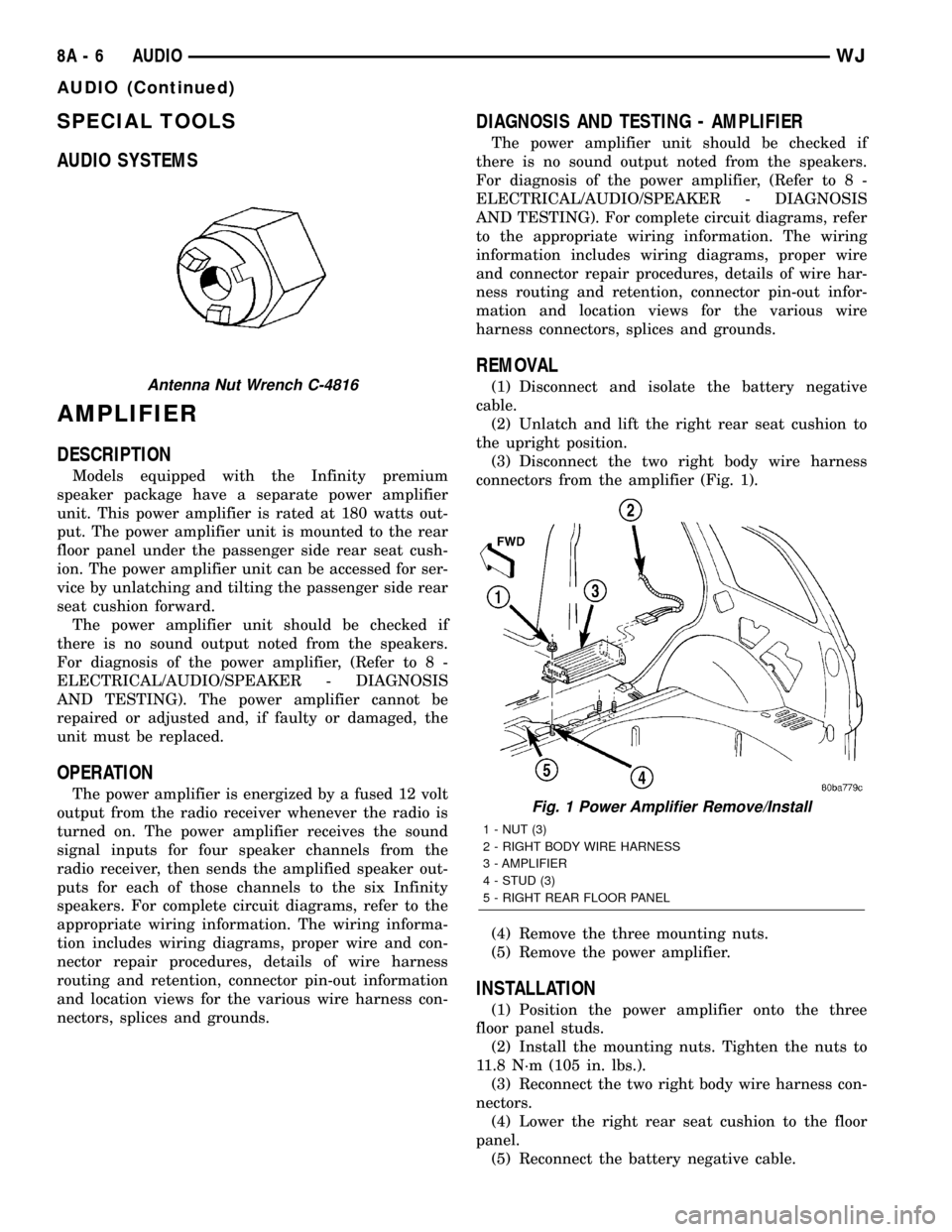
SPECIAL TOOLS
AUDIO SYSTEMS
AMPLIFIER
DESCRIPTION
Models equipped with the Infinity premium
speaker package have a separate power amplifier
unit. This power amplifier is rated at 180 watts out-
put. The power amplifier unit is mounted to the rear
floor panel under the passenger side rear seat cush-
ion. The power amplifier unit can be accessed for ser-
vice by unlatching and tilting the passenger side rear
seat cushion forward.
The power amplifier unit should be checked if
there is no sound output noted from the speakers.
For diagnosis of the power amplifier, (Refer to 8 -
ELECTRICAL/AUDIO/SPEAKER - DIAGNOSIS
AND TESTING). The power amplifier cannot be
repaired or adjusted and, if faulty or damaged, the
unit must be replaced.
OPERATION
The power amplifier is energized by a fused 12 volt
output from the radio receiver whenever the radio is
turned on. The power amplifier receives the sound
signal inputs for four speaker channels from the
radio receiver, then sends the amplified speaker out-
puts for each of those channels to the six Infinity
speakers. For complete circuit diagrams, refer to the
appropriate wiring information. The wiring informa-
tion includes wiring diagrams, proper wire and con-
nector repair procedures, details of wire harness
routing and retention, connector pin-out information
and location views for the various wire harness con-
nectors, splices and grounds.
DIAGNOSIS AND TESTING - AMPLIFIER
The power amplifier unit should be checked if
there is no sound output noted from the speakers.
For diagnosis of the power amplifier, (Refer to 8 -
ELECTRICAL/AUDIO/SPEAKER - DIAGNOSIS
AND TESTING). For complete circuit diagrams, refer
to the appropriate wiring information. The wiring
information includes wiring diagrams, proper wire
and connector repair procedures, details of wire har-
ness routing and retention, connector pin-out infor-
mation and location views for the various wire
harness connectors, splices and grounds.
REMOVAL
(1) Disconnect and isolate the battery negative
cable.
(2) Unlatch and lift the right rear seat cushion to
the upright position.
(3) Disconnect the two right body wire harness
connectors from the amplifier (Fig. 1).
(4) Remove the three mounting nuts.
(5) Remove the power amplifier.
INSTALLATION
(1) Position the power amplifier onto the three
floor panel studs.
(2) Install the mounting nuts. Tighten the nuts to
11.8 N´m (105 in. lbs.).
(3) Reconnect the two right body wire harness con-
nectors.
(4) Lower the right rear seat cushion to the floor
panel.
(5) Reconnect the battery negative cable.
Antenna Nut Wrench C-4816
Fig. 1 Power Amplifier Remove/Install
1 - NUT (3)
2 - RIGHT BODY WIRE HARNESS
3 - AMPLIFIER
4 - STUD (3)
5 - RIGHT REAR FLOOR PANEL
8A - 6 AUDIOWJ
AUDIO (Continued)
Page 295 of 2199
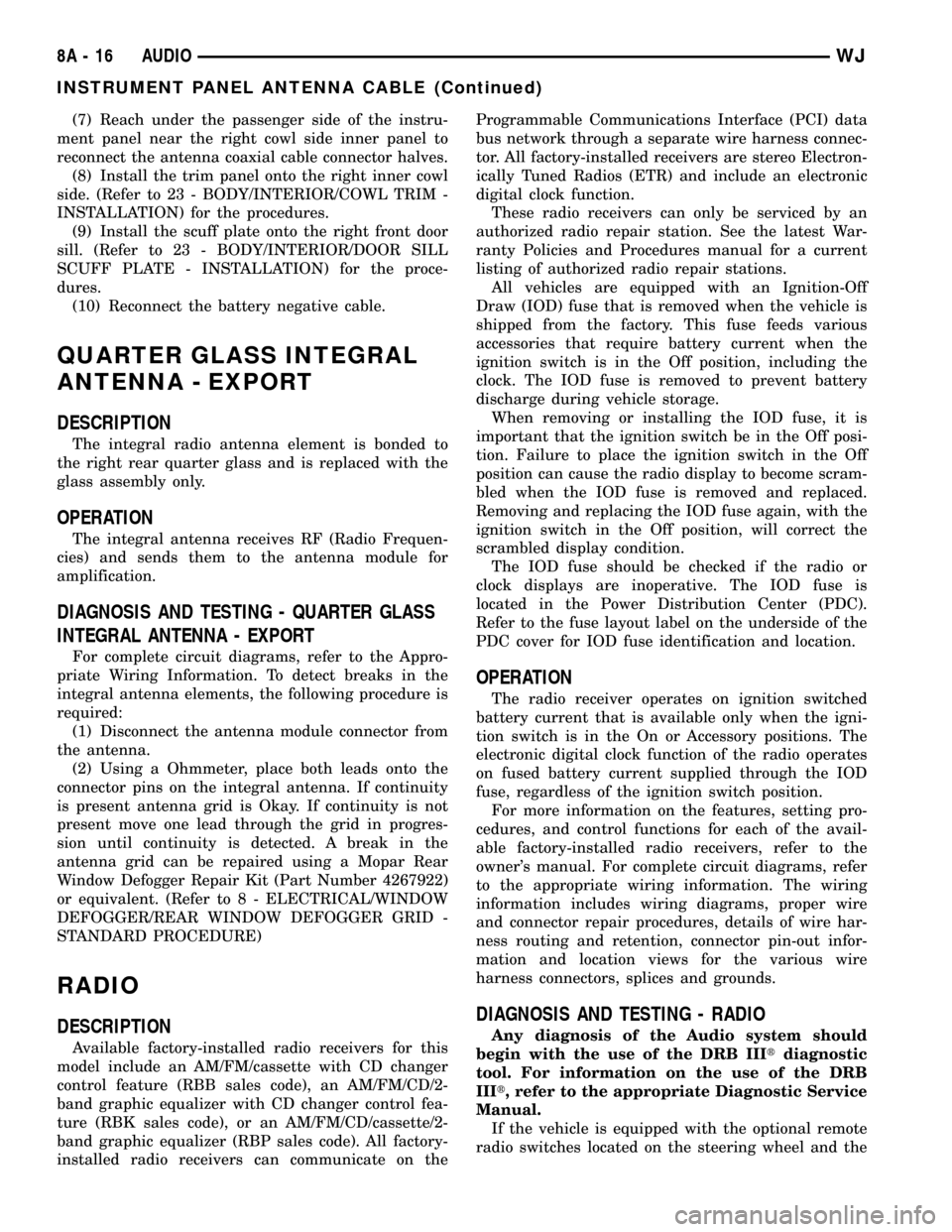
(7) Reach under the passenger side of the instru-
ment panel near the right cowl side inner panel to
reconnect the antenna coaxial cable connector halves.
(8) Install the trim panel onto the right inner cowl
side. (Refer to 23 - BODY/INTERIOR/COWL TRIM -
INSTALLATION) for the procedures.
(9) Install the scuff plate onto the right front door
sill. (Refer to 23 - BODY/INTERIOR/DOOR SILL
SCUFF PLATE - INSTALLATION) for the proce-
dures.
(10) Reconnect the battery negative cable.
QUARTER GLASS INTEGRAL
ANTENNA - EXPORT
DESCRIPTION
The integral radio antenna element is bonded to
the right rear quarter glass and is replaced with the
glass assembly only.
OPERATION
The integral antenna receives RF (Radio Frequen-
cies) and sends them to the antenna module for
amplification.
DIAGNOSIS AND TESTING - QUARTER GLASS
INTEGRAL ANTENNA - EXPORT
For complete circuit diagrams, refer to the Appro-
priate Wiring Information. To detect breaks in the
integral antenna elements, the following procedure is
required:
(1) Disconnect the antenna module connector from
the antenna.
(2) Using a Ohmmeter, place both leads onto the
connector pins on the integral antenna. If continuity
is present antenna grid is Okay. If continuity is not
present move one lead through the grid in progres-
sion until continuity is detected. A break in the
antenna grid can be repaired using a Mopar Rear
Window Defogger Repair Kit (Part Number 4267922)
or equivalent. (Refer to 8 - ELECTRICAL/WINDOW
DEFOGGER/REAR WINDOW DEFOGGER GRID -
STANDARD PROCEDURE)
RADIO
DESCRIPTION
Available factory-installed radio receivers for this
model include an AM/FM/cassette with CD changer
control feature (RBB sales code), an AM/FM/CD/2-
band graphic equalizer with CD changer control fea-
ture (RBK sales code), or an AM/FM/CD/cassette/2-
band graphic equalizer (RBP sales code). All factory-
installed radio receivers can communicate on theProgrammable Communications Interface (PCI) data
bus network through a separate wire harness connec-
tor. All factory-installed receivers are stereo Electron-
ically Tuned Radios (ETR) and include an electronic
digital clock function.
These radio receivers can only be serviced by an
authorized radio repair station. See the latest War-
ranty Policies and Procedures manual for a current
listing of authorized radio repair stations.
All vehicles are equipped with an Ignition-Off
Draw (IOD) fuse that is removed when the vehicle is
shipped from the factory. This fuse feeds various
accessories that require battery current when the
ignition switch is in the Off position, including the
clock. The IOD fuse is removed to prevent battery
discharge during vehicle storage.
When removing or installing the IOD fuse, it is
important that the ignition switch be in the Off posi-
tion. Failure to place the ignition switch in the Off
position can cause the radio display to become scram-
bled when the IOD fuse is removed and replaced.
Removing and replacing the IOD fuse again, with the
ignition switch in the Off position, will correct the
scrambled display condition.
The IOD fuse should be checked if the radio or
clock displays are inoperative. The IOD fuse is
located in the Power Distribution Center (PDC).
Refer to the fuse layout label on the underside of the
PDC cover for IOD fuse identification and location.
OPERATION
The radio receiver operates on ignition switched
battery current that is available only when the igni-
tion switch is in the On or Accessory positions. The
electronic digital clock function of the radio operates
on fused battery current supplied through the IOD
fuse, regardless of the ignition switch position.
For more information on the features, setting pro-
cedures, and control functions for each of the avail-
able factory-installed radio receivers, refer to the
owner's manual. For complete circuit diagrams, refer
to the appropriate wiring information. The wiring
information includes wiring diagrams, proper wire
and connector repair procedures, details of wire har-
ness routing and retention, connector pin-out infor-
mation and location views for the various wire
harness connectors, splices and grounds.
DIAGNOSIS AND TESTING - RADIO
Any diagnosis of the Audio system should
begin with the use of the DRB IIItdiagnostic
tool. For information on the use of the DRB
IIIt, refer to the appropriate Diagnostic Service
Manual.
If the vehicle is equipped with the optional remote
radio switches located on the steering wheel and the
8A - 16 AUDIOWJ
INSTRUMENT PANEL ANTENNA CABLE (Continued)
Page 296 of 2199
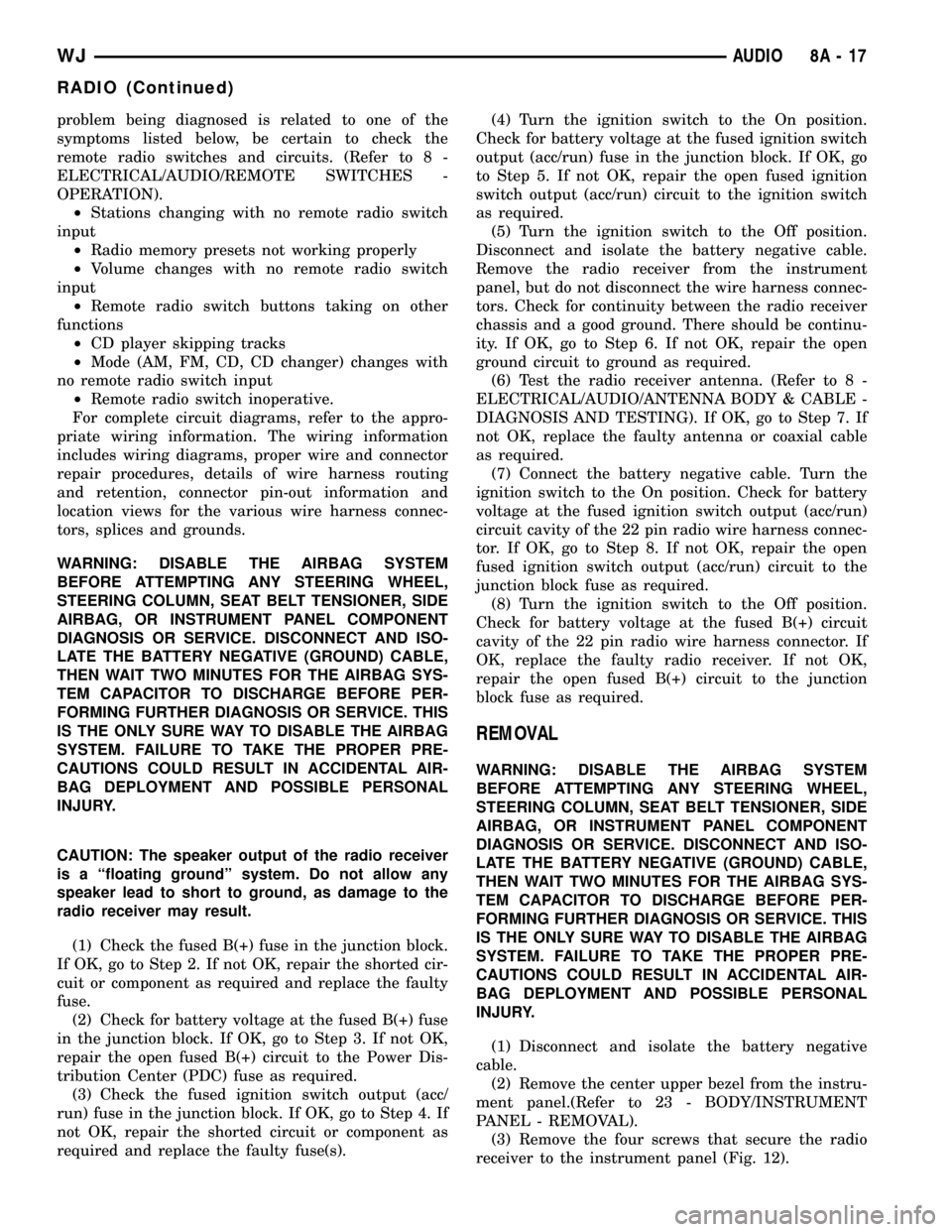
problem being diagnosed is related to one of the
symptoms listed below, be certain to check the
remote radio switches and circuits. (Refer to 8 -
ELECTRICAL/AUDIO/REMOTE SWITCHES -
OPERATION).
²Stations changing with no remote radio switch
input
²Radio memory presets not working properly
²Volume changes with no remote radio switch
input
²Remote radio switch buttons taking on other
functions
²CD player skipping tracks
²Mode (AM, FM, CD, CD changer) changes with
no remote radio switch input
²Remote radio switch inoperative.
For complete circuit diagrams, refer to the appro-
priate wiring information. The wiring information
includes wiring diagrams, proper wire and connector
repair procedures, details of wire harness routing
and retention, connector pin-out information and
location views for the various wire harness connec-
tors, splices and grounds.
WARNING: DISABLE THE AIRBAG SYSTEM
BEFORE ATTEMPTING ANY STEERING WHEEL,
STEERING COLUMN, SEAT BELT TENSIONER, SIDE
AIRBAG, OR INSTRUMENT PANEL COMPONENT
DIAGNOSIS OR SERVICE. DISCONNECT AND ISO-
LATE THE BATTERY NEGATIVE (GROUND) CABLE,
THEN WAIT TWO MINUTES FOR THE AIRBAG SYS-
TEM CAPACITOR TO DISCHARGE BEFORE PER-
FORMING FURTHER DIAGNOSIS OR SERVICE. THIS
IS THE ONLY SURE WAY TO DISABLE THE AIRBAG
SYSTEM. FAILURE TO TAKE THE PROPER PRE-
CAUTIONS COULD RESULT IN ACCIDENTAL AIR-
BAG DEPLOYMENT AND POSSIBLE PERSONAL
INJURY.
CAUTION: The speaker output of the radio receiver
is a ªfloating groundº system. Do not allow any
speaker lead to short to ground, as damage to the
radio receiver may result.
(1) Check the fused B(+) fuse in the junction block.
If OK, go to Step 2. If not OK, repair the shorted cir-
cuit or component as required and replace the faulty
fuse.
(2) Check for battery voltage at the fused B(+) fuse
in the junction block. If OK, go to Step 3. If not OK,
repair the open fused B(+) circuit to the Power Dis-
tribution Center (PDC) fuse as required.
(3) Check the fused ignition switch output (acc/
run) fuse in the junction block. If OK, go to Step 4. If
not OK, repair the shorted circuit or component as
required and replace the faulty fuse(s).(4) Turn the ignition switch to the On position.
Check for battery voltage at the fused ignition switch
output (acc/run) fuse in the junction block. If OK, go
to Step 5. If not OK, repair the open fused ignition
switch output (acc/run) circuit to the ignition switch
as required.
(5) Turn the ignition switch to the Off position.
Disconnect and isolate the battery negative cable.
Remove the radio receiver from the instrument
panel, but do not disconnect the wire harness connec-
tors. Check for continuity between the radio receiver
chassis and a good ground. There should be continu-
ity. If OK, go to Step 6. If not OK, repair the open
ground circuit to ground as required.
(6) Test the radio receiver antenna. (Refer to 8 -
ELECTRICAL/AUDIO/ANTENNA BODY & CABLE -
DIAGNOSIS AND TESTING). If OK, go to Step 7. If
not OK, replace the faulty antenna or coaxial cable
as required.
(7) Connect the battery negative cable. Turn the
ignition switch to the On position. Check for battery
voltage at the fused ignition switch output (acc/run)
circuit cavity of the 22 pin radio wire harness connec-
tor. If OK, go to Step 8. If not OK, repair the open
fused ignition switch output (acc/run) circuit to the
junction block fuse as required.
(8) Turn the ignition switch to the Off position.
Check for battery voltage at the fused B(+) circuit
cavity of the 22 pin radio wire harness connector. If
OK, replace the faulty radio receiver. If not OK,
repair the open fused B(+) circuit to the junction
block fuse as required.
REMOVAL
WARNING: DISABLE THE AIRBAG SYSTEM
BEFORE ATTEMPTING ANY STEERING WHEEL,
STEERING COLUMN, SEAT BELT TENSIONER, SIDE
AIRBAG, OR INSTRUMENT PANEL COMPONENT
DIAGNOSIS OR SERVICE. DISCONNECT AND ISO-
LATE THE BATTERY NEGATIVE (GROUND) CABLE,
THEN WAIT TWO MINUTES FOR THE AIRBAG SYS-
TEM CAPACITOR TO DISCHARGE BEFORE PER-
FORMING FURTHER DIAGNOSIS OR SERVICE. THIS
IS THE ONLY SURE WAY TO DISABLE THE AIRBAG
SYSTEM. FAILURE TO TAKE THE PROPER PRE-
CAUTIONS COULD RESULT IN ACCIDENTAL AIR-
BAG DEPLOYMENT AND POSSIBLE PERSONAL
INJURY.
(1) Disconnect and isolate the battery negative
cable.
(2) Remove the center upper bezel from the instru-
ment panel.(Refer to 23 - BODY/INSTRUMENT
PANEL - REMOVAL).
(3) Remove the four screws that secure the radio
receiver to the instrument panel (Fig. 12).
WJAUDIO 8A - 17
RADIO (Continued)
Page 302 of 2199
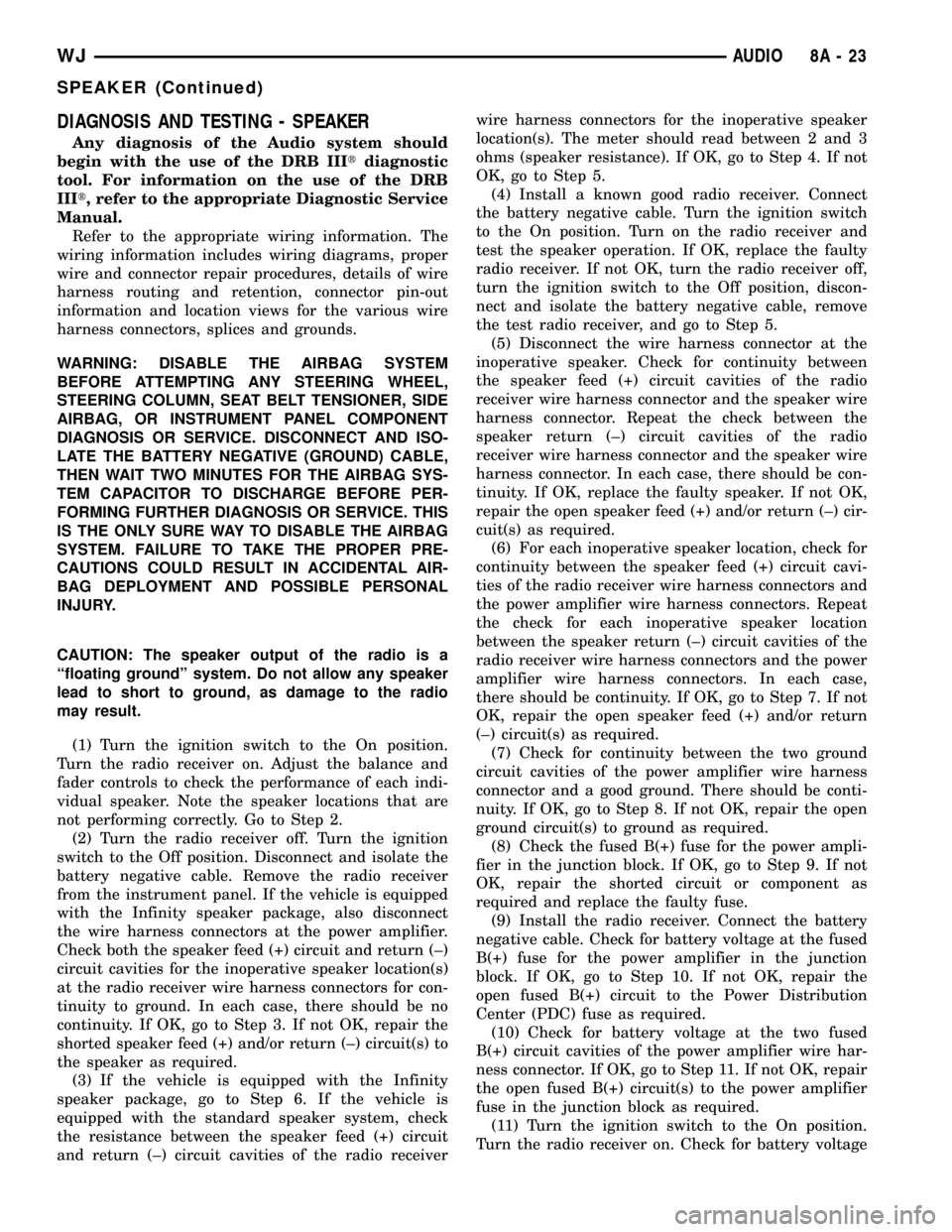
DIAGNOSIS AND TESTING - SPEAKER
Any diagnosis of the Audio system should
begin with the use of the DRB IIItdiagnostic
tool. For information on the use of the DRB
IIIt, refer to the appropriate Diagnostic Service
Manual.
Refer to the appropriate wiring information. The
wiring information includes wiring diagrams, proper
wire and connector repair procedures, details of wire
harness routing and retention, connector pin-out
information and location views for the various wire
harness connectors, splices and grounds.
WARNING: DISABLE THE AIRBAG SYSTEM
BEFORE ATTEMPTING ANY STEERING WHEEL,
STEERING COLUMN, SEAT BELT TENSIONER, SIDE
AIRBAG, OR INSTRUMENT PANEL COMPONENT
DIAGNOSIS OR SERVICE. DISCONNECT AND ISO-
LATE THE BATTERY NEGATIVE (GROUND) CABLE,
THEN WAIT TWO MINUTES FOR THE AIRBAG SYS-
TEM CAPACITOR TO DISCHARGE BEFORE PER-
FORMING FURTHER DIAGNOSIS OR SERVICE. THIS
IS THE ONLY SURE WAY TO DISABLE THE AIRBAG
SYSTEM. FAILURE TO TAKE THE PROPER PRE-
CAUTIONS COULD RESULT IN ACCIDENTAL AIR-
BAG DEPLOYMENT AND POSSIBLE PERSONAL
INJURY.
CAUTION: The speaker output of the radio is a
ªfloating groundº system. Do not allow any speaker
lead to short to ground, as damage to the radio
may result.
(1) Turn the ignition switch to the On position.
Turn the radio receiver on. Adjust the balance and
fader controls to check the performance of each indi-
vidual speaker. Note the speaker locations that are
not performing correctly. Go to Step 2.
(2) Turn the radio receiver off. Turn the ignition
switch to the Off position. Disconnect and isolate the
battery negative cable. Remove the radio receiver
from the instrument panel. If the vehicle is equipped
with the Infinity speaker package, also disconnect
the wire harness connectors at the power amplifier.
Check both the speaker feed (+) circuit and return (±)
circuit cavities for the inoperative speaker location(s)
at the radio receiver wire harness connectors for con-
tinuity to ground. In each case, there should be no
continuity. If OK, go to Step 3. If not OK, repair the
shorted speaker feed (+) and/or return (±) circuit(s) to
the speaker as required.
(3) If the vehicle is equipped with the Infinity
speaker package, go to Step 6. If the vehicle is
equipped with the standard speaker system, check
the resistance between the speaker feed (+) circuit
and return (±) circuit cavities of the radio receiverwire harness connectors for the inoperative speaker
location(s). The meter should read between 2 and 3
ohms (speaker resistance). If OK, go to Step 4. If not
OK, go to Step 5.
(4) Install a known good radio receiver. Connect
the battery negative cable. Turn the ignition switch
to the On position. Turn on the radio receiver and
test the speaker operation. If OK, replace the faulty
radio receiver. If not OK, turn the radio receiver off,
turn the ignition switch to the Off position, discon-
nect and isolate the battery negative cable, remove
the test radio receiver, and go to Step 5.
(5) Disconnect the wire harness connector at the
inoperative speaker. Check for continuity between
the speaker feed (+) circuit cavities of the radio
receiver wire harness connector and the speaker wire
harness connector. Repeat the check between the
speaker return (±) circuit cavities of the radio
receiver wire harness connector and the speaker wire
harness connector. In each case, there should be con-
tinuity. If OK, replace the faulty speaker. If not OK,
repair the open speaker feed (+) and/or return (±) cir-
cuit(s) as required.
(6) For each inoperative speaker location, check for
continuity between the speaker feed (+) circuit cavi-
ties of the radio receiver wire harness connectors and
the power amplifier wire harness connectors. Repeat
the check for each inoperative speaker location
between the speaker return (±) circuit cavities of the
radio receiver wire harness connectors and the power
amplifier wire harness connectors. In each case,
there should be continuity. If OK, go to Step 7. If not
OK, repair the open speaker feed (+) and/or return
(±) circuit(s) as required.
(7) Check for continuity between the two ground
circuit cavities of the power amplifier wire harness
connector and a good ground. There should be conti-
nuity. If OK, go to Step 8. If not OK, repair the open
ground circuit(s) to ground as required.
(8) Check the fused B(+) fuse for the power ampli-
fier in the junction block. If OK, go to Step 9. If not
OK, repair the shorted circuit or component as
required and replace the faulty fuse.
(9) Install the radio receiver. Connect the battery
negative cable. Check for battery voltage at the fused
B(+) fuse for the power amplifier in the junction
block. If OK, go to Step 10. If not OK, repair the
open fused B(+) circuit to the Power Distribution
Center (PDC) fuse as required.
(10) Check for battery voltage at the two fused
B(+) circuit cavities of the power amplifier wire har-
ness connector. If OK, go to Step 11. If not OK, repair
the open fused B(+) circuit(s) to the power amplifier
fuse in the junction block as required.
(11) Turn the ignition switch to the On position.
Turn the radio receiver on. Check for battery voltage
WJAUDIO 8A - 23
SPEAKER (Continued)
Page 349 of 2199
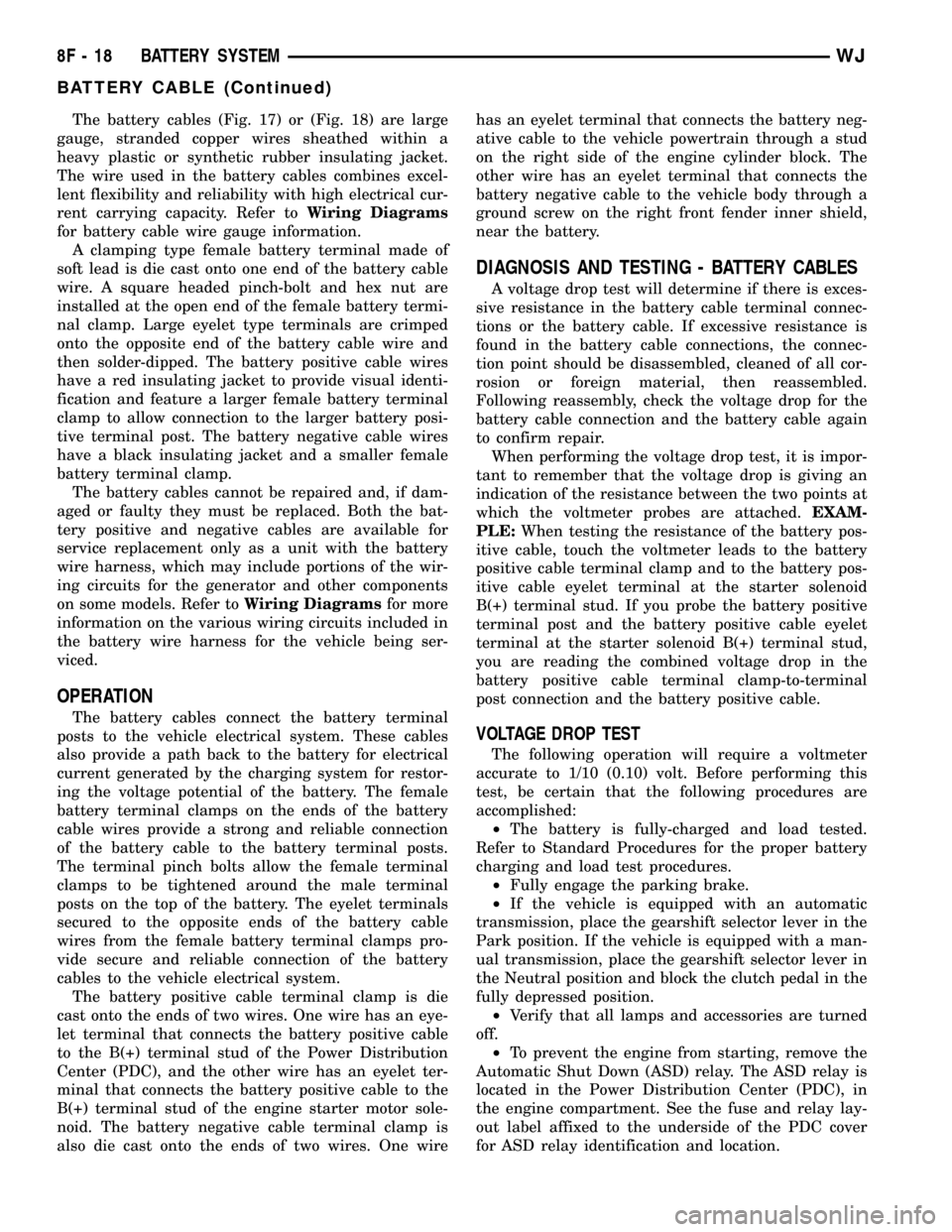
The battery cables (Fig. 17) or (Fig. 18) are large
gauge, stranded copper wires sheathed within a
heavy plastic or synthetic rubber insulating jacket.
The wire used in the battery cables combines excel-
lent flexibility and reliability with high electrical cur-
rent carrying capacity. Refer toWiring Diagrams
for battery cable wire gauge information.
A clamping type female battery terminal made of
soft lead is die cast onto one end of the battery cable
wire. A square headed pinch-bolt and hex nut are
installed at the open end of the female battery termi-
nal clamp. Large eyelet type terminals are crimped
onto the opposite end of the battery cable wire and
then solder-dipped. The battery positive cable wires
have a red insulating jacket to provide visual identi-
fication and feature a larger female battery terminal
clamp to allow connection to the larger battery posi-
tive terminal post. The battery negative cable wires
have a black insulating jacket and a smaller female
battery terminal clamp.
The battery cables cannot be repaired and, if dam-
aged or faulty they must be replaced. Both the bat-
tery positive and negative cables are available for
service replacement only as a unit with the battery
wire harness, which may include portions of the wir-
ing circuits for the generator and other components
on some models. Refer toWiring Diagramsfor more
information on the various wiring circuits included in
the battery wire harness for the vehicle being ser-
viced.
OPERATION
The battery cables connect the battery terminal
posts to the vehicle electrical system. These cables
also provide a path back to the battery for electrical
current generated by the charging system for restor-
ing the voltage potential of the battery. The female
battery terminal clamps on the ends of the battery
cable wires provide a strong and reliable connection
of the battery cable to the battery terminal posts.
The terminal pinch bolts allow the female terminal
clamps to be tightened around the male terminal
posts on the top of the battery. The eyelet terminals
secured to the opposite ends of the battery cable
wires from the female battery terminal clamps pro-
vide secure and reliable connection of the battery
cables to the vehicle electrical system.
The battery positive cable terminal clamp is die
cast onto the ends of two wires. One wire has an eye-
let terminal that connects the battery positive cable
to the B(+) terminal stud of the Power Distribution
Center (PDC), and the other wire has an eyelet ter-
minal that connects the battery positive cable to the
B(+) terminal stud of the engine starter motor sole-
noid. The battery negative cable terminal clamp is
also die cast onto the ends of two wires. One wirehas an eyelet terminal that connects the battery neg-
ative cable to the vehicle powertrain through a stud
on the right side of the engine cylinder block. The
other wire has an eyelet terminal that connects the
battery negative cable to the vehicle body through a
ground screw on the right front fender inner shield,
near the battery.
DIAGNOSIS AND TESTING - BATTERY CABLES
A voltage drop test will determine if there is exces-
sive resistance in the battery cable terminal connec-
tions or the battery cable. If excessive resistance is
found in the battery cable connections, the connec-
tion point should be disassembled, cleaned of all cor-
rosion or foreign material, then reassembled.
Following reassembly, check the voltage drop for the
battery cable connection and the battery cable again
to confirm repair.
When performing the voltage drop test, it is impor-
tant to remember that the voltage drop is giving an
indication of the resistance between the two points at
which the voltmeter probes are attached.EXAM-
PLE:When testing the resistance of the battery pos-
itive cable, touch the voltmeter leads to the battery
positive cable terminal clamp and to the battery pos-
itive cable eyelet terminal at the starter solenoid
B(+) terminal stud. If you probe the battery positive
terminal post and the battery positive cable eyelet
terminal at the starter solenoid B(+) terminal stud,
you are reading the combined voltage drop in the
battery positive cable terminal clamp-to-terminal
post connection and the battery positive cable.
VOLTAGE DROP TEST
The following operation will require a voltmeter
accurate to 1/10 (0.10) volt. Before performing this
test, be certain that the following procedures are
accomplished:
²The battery is fully-charged and load tested.
Refer to Standard Procedures for the proper battery
charging and load test procedures.
²Fully engage the parking brake.
²If the vehicle is equipped with an automatic
transmission, place the gearshift selector lever in the
Park position. If the vehicle is equipped with a man-
ual transmission, place the gearshift selector lever in
the Neutral position and block the clutch pedal in the
fully depressed position.
²Verify that all lamps and accessories are turned
off.
²To prevent the engine from starting, remove the
Automatic Shut Down (ASD) relay. The ASD relay is
located in the Power Distribution Center (PDC), in
the engine compartment. See the fuse and relay lay-
out label affixed to the underside of the PDC cover
for ASD relay identification and location.
8F - 18 BATTERY SYSTEMWJ
BATTERY CABLE (Continued)
Page 363 of 2199
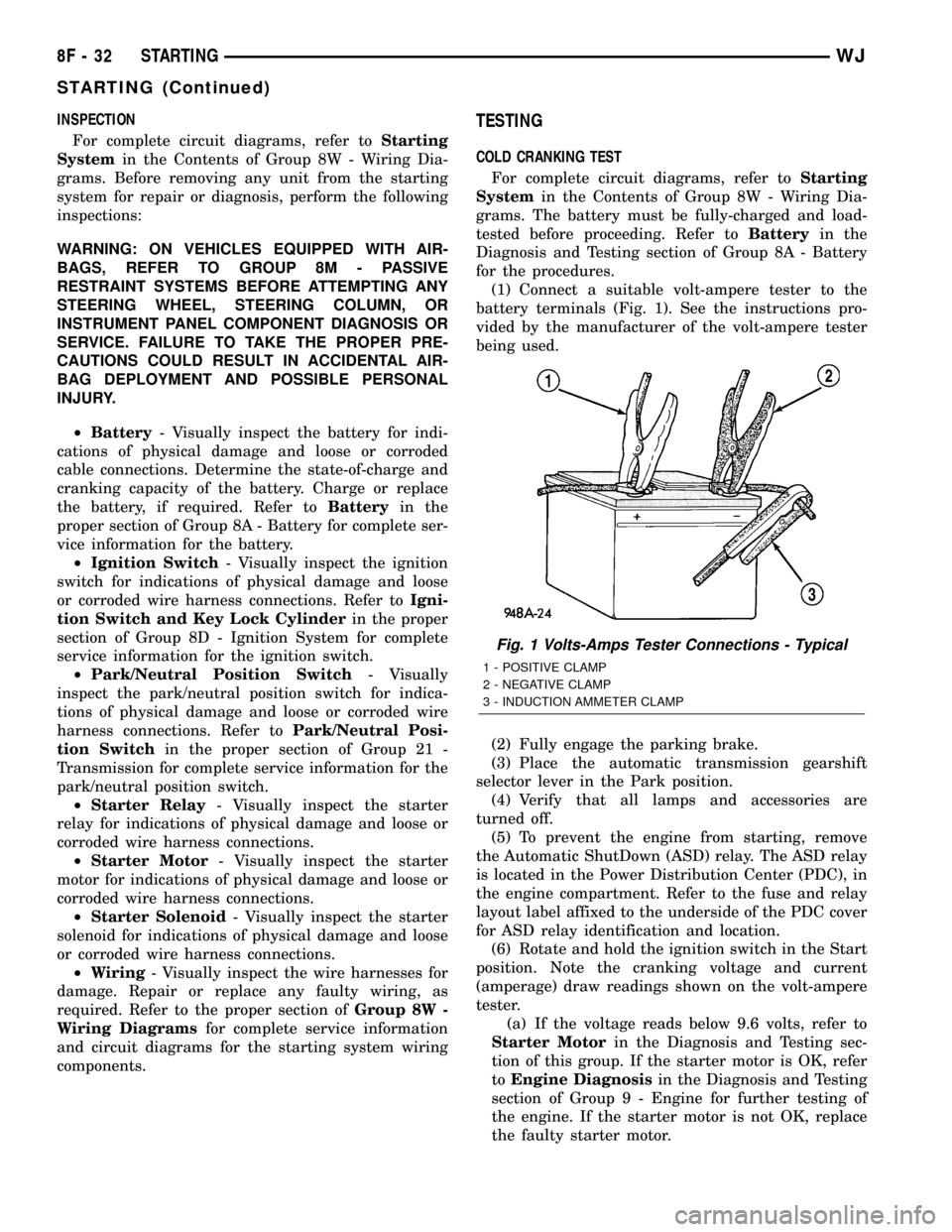
INSPECTION
For complete circuit diagrams, refer toStarting
Systemin the Contents of Group 8W - Wiring Dia-
grams. Before removing any unit from the starting
system for repair or diagnosis, perform the following
inspections:
WARNING: ON VEHICLES EQUIPPED WITH AIR-
BAGS, REFER TO GROUP 8M - PASSIVE
RESTRAINT SYSTEMS BEFORE ATTEMPTING ANY
STEERING WHEEL, STEERING COLUMN, OR
INSTRUMENT PANEL COMPONENT DIAGNOSIS OR
SERVICE. FAILURE TO TAKE THE PROPER PRE-
CAUTIONS COULD RESULT IN ACCIDENTAL AIR-
BAG DEPLOYMENT AND POSSIBLE PERSONAL
INJURY.
²Battery- Visually inspect the battery for indi-
cations of physical damage and loose or corroded
cable connections. Determine the state-of-charge and
cranking capacity of the battery. Charge or replace
the battery, if required. Refer toBatteryin the
proper section of Group 8A - Battery for complete ser-
vice information for the battery.
²Ignition Switch- Visually inspect the ignition
switch for indications of physical damage and loose
or corroded wire harness connections. Refer toIgni-
tion Switch and Key Lock Cylinderin the proper
section of Group 8D - Ignition System for complete
service information for the ignition switch.
²Park/Neutral Position Switch- Visually
inspect the park/neutral position switch for indica-
tions of physical damage and loose or corroded wire
harness connections. Refer toPark/Neutral Posi-
tion Switchin the proper section of Group 21 -
Transmission for complete service information for the
park/neutral position switch.
²Starter Relay- Visually inspect the starter
relay for indications of physical damage and loose or
corroded wire harness connections.
²Starter Motor- Visually inspect the starter
motor for indications of physical damage and loose or
corroded wire harness connections.
²Starter Solenoid- Visually inspect the starter
solenoid for indications of physical damage and loose
or corroded wire harness connections.
²Wiring- Visually inspect the wire harnesses for
damage. Repair or replace any faulty wiring, as
required. Refer to the proper section ofGroup 8W -
Wiring Diagramsfor complete service information
and circuit diagrams for the starting system wiring
components.TESTING
COLD CRANKING TEST
For complete circuit diagrams, refer toStarting
Systemin the Contents of Group 8W - Wiring Dia-
grams. The battery must be fully-charged and load-
tested before proceeding. Refer toBatteryin the
Diagnosis and Testing section of Group 8A - Battery
for the procedures.
(1) Connect a suitable volt-ampere tester to the
battery terminals (Fig. 1). See the instructions pro-
vided by the manufacturer of the volt-ampere tester
being used.
(2) Fully engage the parking brake.
(3) Place the automatic transmission gearshift
selector lever in the Park position.
(4) Verify that all lamps and accessories are
turned off.
(5) To prevent the engine from starting, remove
the Automatic ShutDown (ASD) relay. The ASD relay
is located in the Power Distribution Center (PDC), in
the engine compartment. Refer to the fuse and relay
layout label affixed to the underside of the PDC cover
for ASD relay identification and location.
(6) Rotate and hold the ignition switch in the Start
position. Note the cranking voltage and current
(amperage) draw readings shown on the volt-ampere
tester.
(a) If the voltage reads below 9.6 volts, refer to
Starter Motorin the Diagnosis and Testing sec-
tion of this group. If the starter motor is OK, refer
toEngine Diagnosisin the Diagnosis and Testing
section of Group 9 - Engine for further testing of
the engine. If the starter motor is not OK, replace
the faulty starter motor.
Fig. 1 Volts-Amps Tester Connections - Typical
1 - POSITIVE CLAMP
2 - NEGATIVE CLAMP
3 - INDUCTION AMMETER CLAMP
8F - 32 STARTINGWJ
STARTING (Continued)
Page 364 of 2199
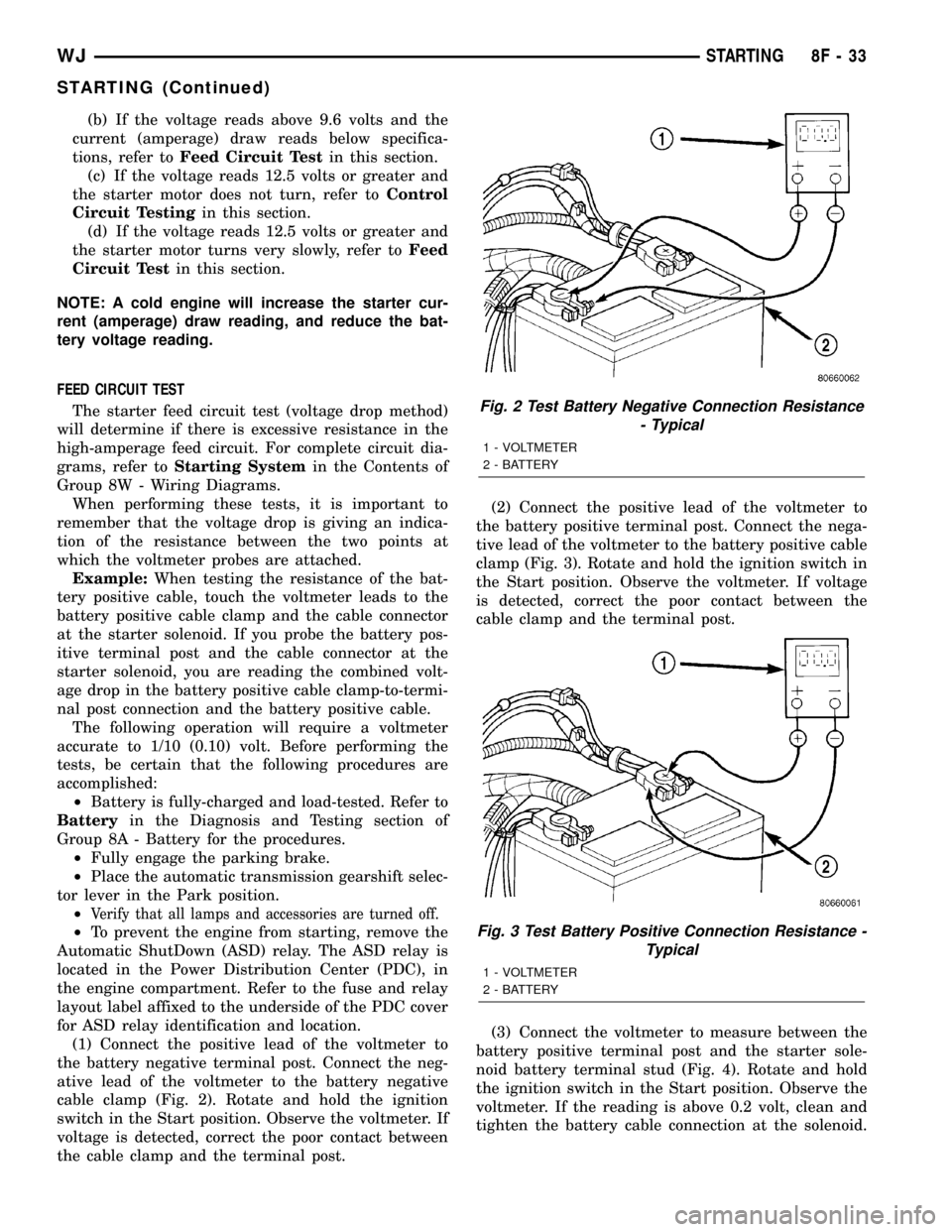
(b) If the voltage reads above 9.6 volts and the
current (amperage) draw reads below specifica-
tions, refer toFeed Circuit Testin this section.
(c) If the voltage reads 12.5 volts or greater and
the starter motor does not turn, refer toControl
Circuit Testingin this section.
(d) If the voltage reads 12.5 volts or greater and
the starter motor turns very slowly, refer toFeed
Circuit Testin this section.
NOTE: A cold engine will increase the starter cur-
rent (amperage) draw reading, and reduce the bat-
tery voltage reading.
FEED CIRCUIT TEST
The starter feed circuit test (voltage drop method)
will determine if there is excessive resistance in the
high-amperage feed circuit. For complete circuit dia-
grams, refer toStarting Systemin the Contents of
Group 8W - Wiring Diagrams.
When performing these tests, it is important to
remember that the voltage drop is giving an indica-
tion of the resistance between the two points at
which the voltmeter probes are attached.
Example:When testing the resistance of the bat-
tery positive cable, touch the voltmeter leads to the
battery positive cable clamp and the cable connector
at the starter solenoid. If you probe the battery pos-
itive terminal post and the cable connector at the
starter solenoid, you are reading the combined volt-
age drop in the battery positive cable clamp-to-termi-
nal post connection and the battery positive cable.
The following operation will require a voltmeter
accurate to 1/10 (0.10) volt. Before performing the
tests, be certain that the following procedures are
accomplished:
²Battery is fully-charged and load-tested. Refer to
Batteryin the Diagnosis and Testing section of
Group 8A - Battery for the procedures.
²Fully engage the parking brake.
²Place the automatic transmission gearshift selec-
tor lever in the Park position.
²
Verify that all lamps and accessories are turned off.
²To prevent the engine from starting, remove the
Automatic ShutDown (ASD) relay. The ASD relay is
located in the Power Distribution Center (PDC), in
the engine compartment. Refer to the fuse and relay
layout label affixed to the underside of the PDC cover
for ASD relay identification and location.
(1) Connect the positive lead of the voltmeter to
the battery negative terminal post. Connect the neg-
ative lead of the voltmeter to the battery negative
cable clamp (Fig. 2). Rotate and hold the ignition
switch in the Start position. Observe the voltmeter. If
voltage is detected, correct the poor contact between
the cable clamp and the terminal post.(2) Connect the positive lead of the voltmeter to
the battery positive terminal post. Connect the nega-
tive lead of the voltmeter to the battery positive cable
clamp (Fig. 3). Rotate and hold the ignition switch in
the Start position. Observe the voltmeter. If voltage
is detected, correct the poor contact between the
cable clamp and the terminal post.
(3) Connect the voltmeter to measure between the
battery positive terminal post and the starter sole-
noid battery terminal stud (Fig. 4). Rotate and hold
the ignition switch in the Start position. Observe the
voltmeter. If the reading is above 0.2 volt, clean and
tighten the battery cable connection at the solenoid.
Fig. 2 Test Battery Negative Connection Resistance
- Typical
1 - VOLTMETER
2 - BATTERY
Fig. 3 Test Battery Positive Connection Resistance -
Typical
1 - VOLTMETER
2 - BATTERY
WJSTARTING 8F - 33
STARTING (Continued)
Page 369 of 2199
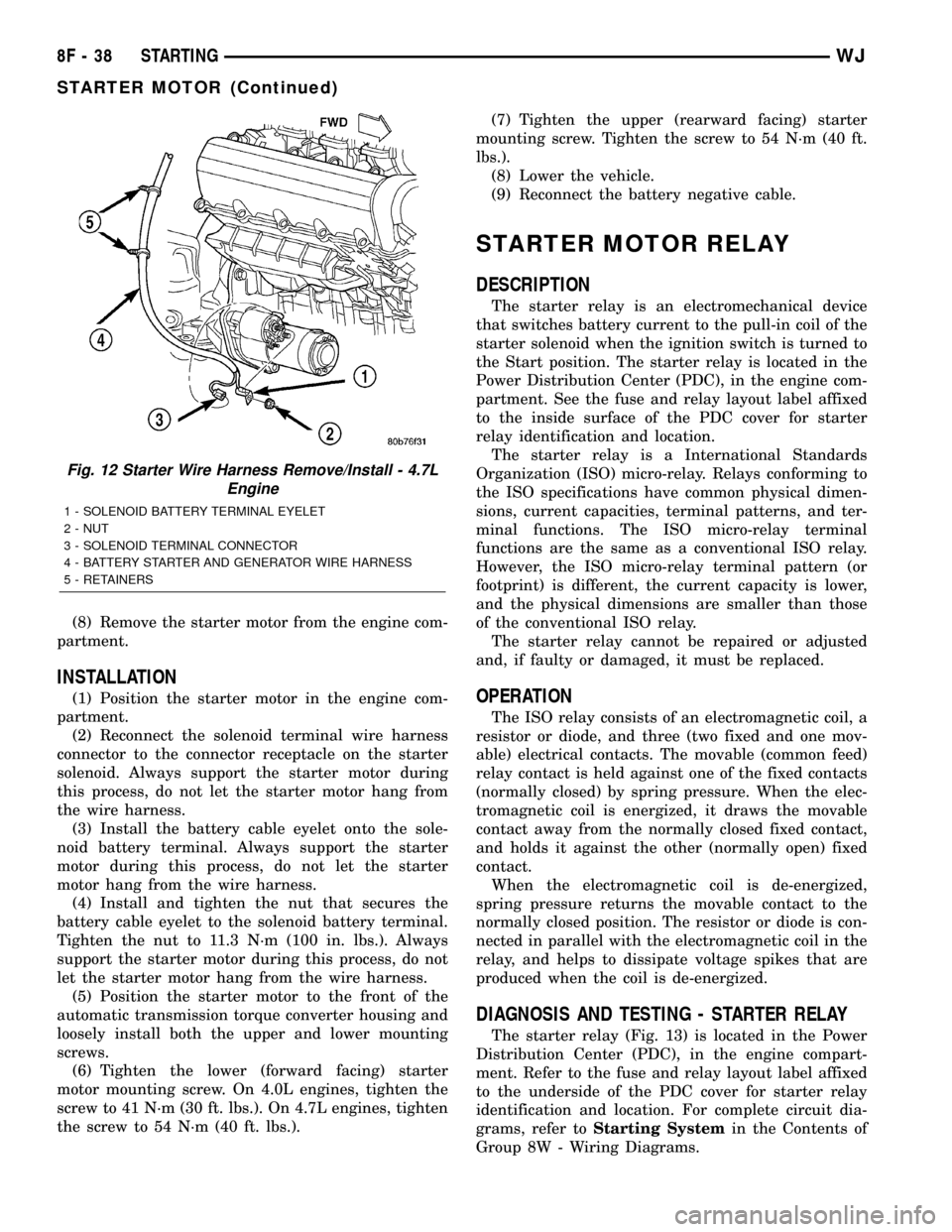
(8) Remove the starter motor from the engine com-
partment.
INSTALLATION
(1) Position the starter motor in the engine com-
partment.
(2) Reconnect the solenoid terminal wire harness
connector to the connector receptacle on the starter
solenoid. Always support the starter motor during
this process, do not let the starter motor hang from
the wire harness.
(3) Install the battery cable eyelet onto the sole-
noid battery terminal. Always support the starter
motor during this process, do not let the starter
motor hang from the wire harness.
(4) Install and tighten the nut that secures the
battery cable eyelet to the solenoid battery terminal.
Tighten the nut to 11.3 N´m (100 in. lbs.). Always
support the starter motor during this process, do not
let the starter motor hang from the wire harness.
(5) Position the starter motor to the front of the
automatic transmission torque converter housing and
loosely install both the upper and lower mounting
screws.
(6) Tighten the lower (forward facing) starter
motor mounting screw. On 4.0L engines, tighten the
screw to 41 N´m (30 ft. lbs.). On 4.7L engines, tighten
the screw to 54 N´m (40 ft. lbs.).(7) Tighten the upper (rearward facing) starter
mounting screw. Tighten the screw to 54 N´m (40 ft.
lbs.).
(8) Lower the vehicle.
(9) Reconnect the battery negative cable.
STARTER MOTOR RELAY
DESCRIPTION
The starter relay is an electromechanical device
that switches battery current to the pull-in coil of the
starter solenoid when the ignition switch is turned to
the Start position. The starter relay is located in the
Power Distribution Center (PDC), in the engine com-
partment. See the fuse and relay layout label affixed
to the inside surface of the PDC cover for starter
relay identification and location.
The starter relay is a International Standards
Organization (ISO) micro-relay. Relays conforming to
the ISO specifications have common physical dimen-
sions, current capacities, terminal patterns, and ter-
minal functions. The ISO micro-relay terminal
functions are the same as a conventional ISO relay.
However, the ISO micro-relay terminal pattern (or
footprint) is different, the current capacity is lower,
and the physical dimensions are smaller than those
of the conventional ISO relay.
The starter relay cannot be repaired or adjusted
and, if faulty or damaged, it must be replaced.
OPERATION
The ISO relay consists of an electromagnetic coil, a
resistor or diode, and three (two fixed and one mov-
able) electrical contacts. The movable (common feed)
relay contact is held against one of the fixed contacts
(normally closed) by spring pressure. When the elec-
tromagnetic coil is energized, it draws the movable
contact away from the normally closed fixed contact,
and holds it against the other (normally open) fixed
contact.
When the electromagnetic coil is de-energized,
spring pressure returns the movable contact to the
normally closed position. The resistor or diode is con-
nected in parallel with the electromagnetic coil in the
relay, and helps to dissipate voltage spikes that are
produced when the coil is de-energized.
DIAGNOSIS AND TESTING - STARTER RELAY
The starter relay (Fig. 13) is located in the Power
Distribution Center (PDC), in the engine compart-
ment. Refer to the fuse and relay layout label affixed
to the underside of the PDC cover for starter relay
identification and location. For complete circuit dia-
grams, refer toStarting Systemin the Contents of
Group 8W - Wiring Diagrams.
Fig. 12 Starter Wire Harness Remove/Install - 4.7L
Engine
1 - SOLENOID BATTERY TERMINAL EYELET
2 - NUT
3 - SOLENOID TERMINAL CONNECTOR
4 - BATTERY STARTER AND GENERATOR WIRE HARNESS
5 - RETAINERS
8F - 38 STARTINGWJ
STARTER MOTOR (Continued)
Page 374 of 2199
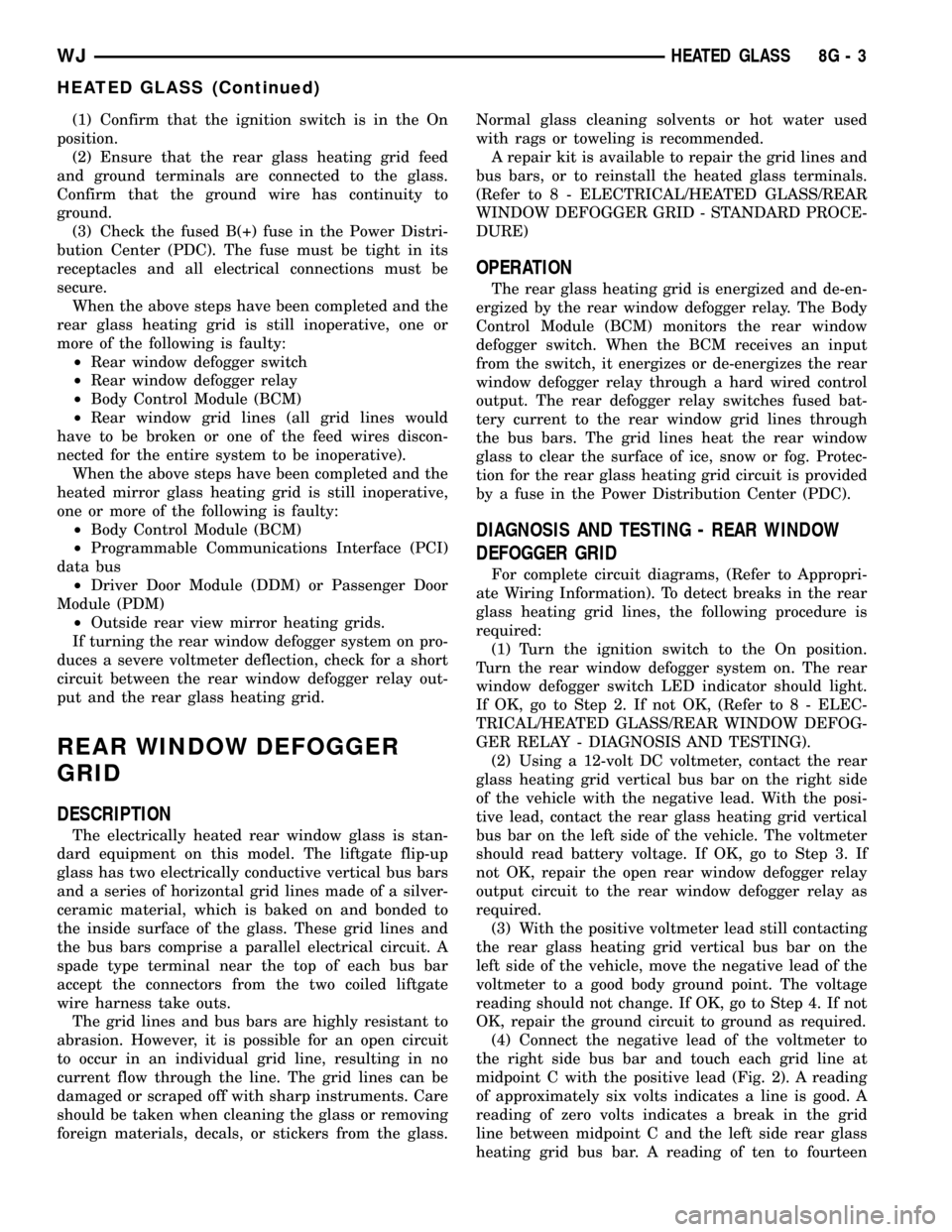
(1) Confirm that the ignition switch is in the On
position.
(2) Ensure that the rear glass heating grid feed
and ground terminals are connected to the glass.
Confirm that the ground wire has continuity to
ground.
(3) Check the fused B(+) fuse in the Power Distri-
bution Center (PDC). The fuse must be tight in its
receptacles and all electrical connections must be
secure.
When the above steps have been completed and the
rear glass heating grid is still inoperative, one or
more of the following is faulty:
²Rear window defogger switch
²Rear window defogger relay
²Body Control Module (BCM)
²Rear window grid lines (all grid lines would
have to be broken or one of the feed wires discon-
nected for the entire system to be inoperative).
When the above steps have been completed and the
heated mirror glass heating grid is still inoperative,
one or more of the following is faulty:
²Body Control Module (BCM)
²Programmable Communications Interface (PCI)
data bus
²Driver Door Module (DDM) or Passenger Door
Module (PDM)
²Outside rear view mirror heating grids.
If turning the rear window defogger system on pro-
duces a severe voltmeter deflection, check for a short
circuit between the rear window defogger relay out-
put and the rear glass heating grid.
REAR WINDOW DEFOGGER
GRID
DESCRIPTION
The electrically heated rear window glass is stan-
dard equipment on this model. The liftgate flip-up
glass has two electrically conductive vertical bus bars
and a series of horizontal grid lines made of a silver-
ceramic material, which is baked on and bonded to
the inside surface of the glass. These grid lines and
the bus bars comprise a parallel electrical circuit. A
spade type terminal near the top of each bus bar
accept the connectors from the two coiled liftgate
wire harness take outs.
The grid lines and bus bars are highly resistant to
abrasion. However, it is possible for an open circuit
to occur in an individual grid line, resulting in no
current flow through the line. The grid lines can be
damaged or scraped off with sharp instruments. Care
should be taken when cleaning the glass or removing
foreign materials, decals, or stickers from the glass.Normal glass cleaning solvents or hot water used
with rags or toweling is recommended.
A repair kit is available to repair the grid lines and
bus bars, or to reinstall the heated glass terminals.
(Refer to 8 - ELECTRICAL/HEATED GLASS/REAR
WINDOW DEFOGGER GRID - STANDARD PROCE-
DURE)
OPERATION
The rear glass heating grid is energized and de-en-
ergized by the rear window defogger relay. The Body
Control Module (BCM) monitors the rear window
defogger switch. When the BCM receives an input
from the switch, it energizes or de-energizes the rear
window defogger relay through a hard wired control
output. The rear defogger relay switches fused bat-
tery current to the rear window grid lines through
the bus bars. The grid lines heat the rear window
glass to clear the surface of ice, snow or fog. Protec-
tion for the rear glass heating grid circuit is provided
by a fuse in the Power Distribution Center (PDC).
DIAGNOSIS AND TESTING - REAR WINDOW
DEFOGGER GRID
For complete circuit diagrams, (Refer to Appropri-
ate Wiring Information). To detect breaks in the rear
glass heating grid lines, the following procedure is
required:
(1) Turn the ignition switch to the On position.
Turn the rear window defogger system on. The rear
window defogger switch LED indicator should light.
If OK, go to Step 2. If not OK, (Refer to 8 - ELEC-
TRICAL/HEATED GLASS/REAR WINDOW DEFOG-
GER RELAY - DIAGNOSIS AND TESTING).
(2) Using a 12-volt DC voltmeter, contact the rear
glass heating grid vertical bus bar on the right side
of the vehicle with the negative lead. With the posi-
tive lead, contact the rear glass heating grid vertical
bus bar on the left side of the vehicle. The voltmeter
should read battery voltage. If OK, go to Step 3. If
not OK, repair the open rear window defogger relay
output circuit to the rear window defogger relay as
required.
(3) With the positive voltmeter lead still contacting
the rear glass heating grid vertical bus bar on the
left side of the vehicle, move the negative lead of the
voltmeter to a good body ground point. The voltage
reading should not change. If OK, go to Step 4. If not
OK, repair the ground circuit to ground as required.
(4) Connect the negative lead of the voltmeter to
the right side bus bar and touch each grid line at
midpoint C with the positive lead (Fig. 2). A reading
of approximately six volts indicates a line is good. A
reading of zero volts indicates a break in the grid
line between midpoint C and the left side rear glass
heating grid bus bar. A reading of ten to fourteen
WJHEATED GLASS 8G - 3
HEATED GLASS (Continued)