lamp replacement JEEP GRAND CHEROKEE 2003 WJ / 2.G Owner's Manual
[x] Cancel search | Manufacturer: JEEP, Model Year: 2003, Model line: GRAND CHEROKEE, Model: JEEP GRAND CHEROKEE 2003 WJ / 2.GPages: 2199, PDF Size: 76.01 MB
Page 478 of 2199

UNDERHOOD LAMP
REMOVAL
REMOVAL - BULB
(1) Insert a small flat blade in access slot between
the lamp base and lamp lens.
(2) Lift the lamp lens upward and remove the
lamp lens (Fig. 34).
(3) Depress bulb terminal inward (Fig. 35) to
release bulb.
REMOVAL - LAMP
(1) Disconnect the wire harness connector from
lamp.
(2) Remove the screw attaching underhood lamp to
inner hood panel (Fig. 36).
(3) Remove the underhood lamp from the vehicle.
INSTALLATION
INSTALLATION - BULB
(1) Engage the replacement bulb wire loop to ter-
minal closest to lamp base wire connector.
(2) Depress the opposite terminal inward and
engage the remaining bulb wire loop.
(3) Position the lamp lens on the lamp base and
press into place.
INSTALLATION - LAMP
(1) Position the underhood lamp on the hood inner
panel.
(2) Install the screw attaching the lamp base to
the inner hood panel.
(3) Install the lamp housing and press into place.
(4) Connect the wire harness connector.
Fig. 34 Underhood Lamp Lens
1 - LAMP
2 - LAMP LENS
Fig. 35 Underhood Lamp Bulb
1 - BULB
2 - DEPRESS TERMINAL INWARD
3 - BULB WIRE LOOP
4 - LAMP BASE
Fig. 36 Underhood Lamp
1 - CONNECTOR
2 - UNDERHOOD LAMP
WJLAMPS/LIGHTING - EXTERIOR 8L - 27
Page 484 of 2199
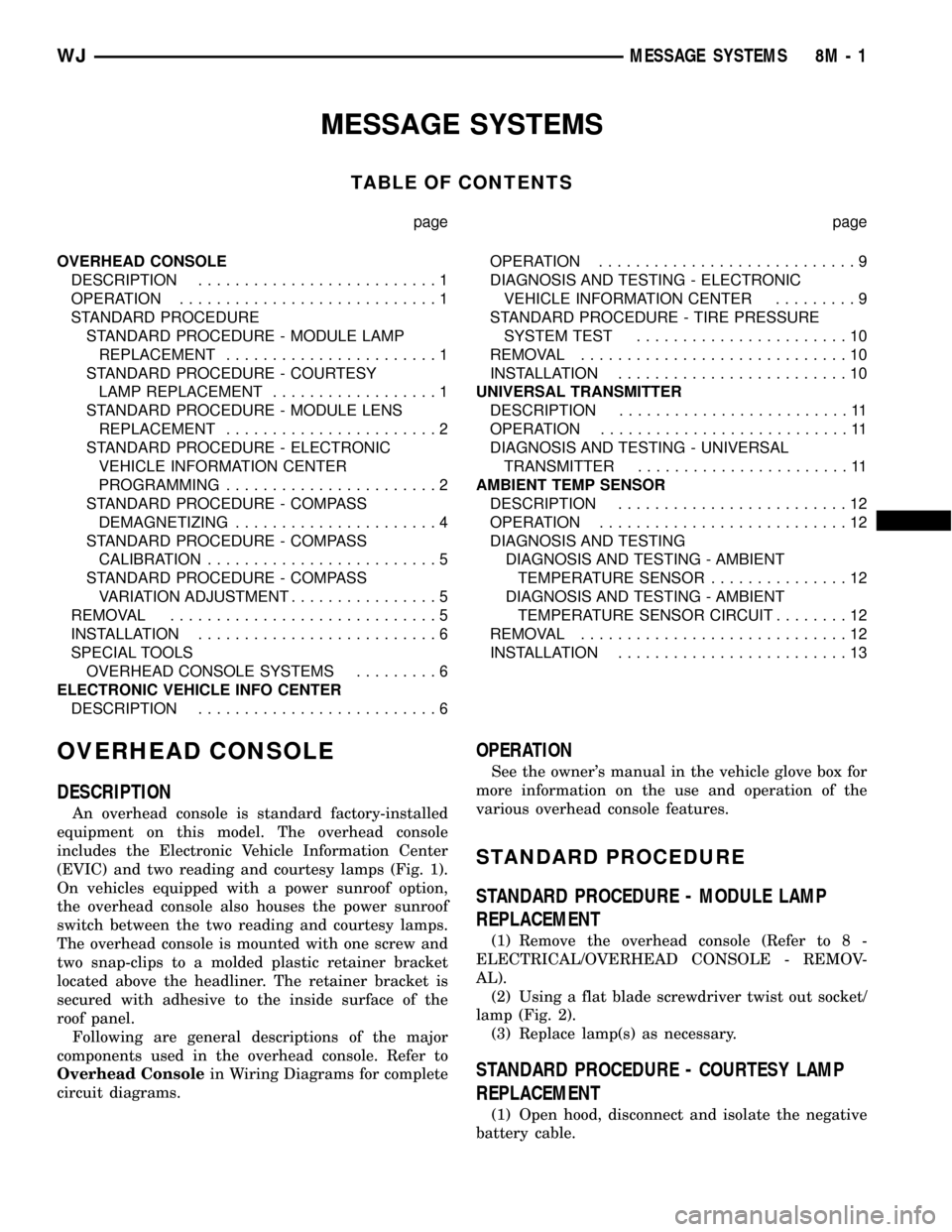
MESSAGE SYSTEMS
TABLE OF CONTENTS
page page
OVERHEAD CONSOLE
DESCRIPTION..........................1
OPERATION............................1
STANDARD PROCEDURE
STANDARD PROCEDURE - MODULE LAMP
REPLACEMENT.......................1
STANDARD PROCEDURE - COURTESY
LAMP REPLACEMENT..................1
STANDARD PROCEDURE - MODULE LENS
REPLACEMENT.......................2
STANDARD PROCEDURE - ELECTRONIC
VEHICLE INFORMATION CENTER
PROGRAMMING.......................2
STANDARD PROCEDURE - COMPASS
DEMAGNETIZING......................4
STANDARD PROCEDURE - COMPASS
CALIBRATION.........................5
STANDARD PROCEDURE - COMPASS
VARIATION ADJUSTMENT................5
REMOVAL.............................5
INSTALLATION..........................6
SPECIAL TOOLS
OVERHEAD CONSOLE SYSTEMS.........6
ELECTRONIC VEHICLE INFO CENTER
DESCRIPTION..........................6OPERATION............................9
DIAGNOSIS AND TESTING - ELECTRONIC
VEHICLE INFORMATION CENTER.........9
STANDARD PROCEDURE - TIRE PRESSURE
SYSTEM TEST.......................10
REMOVAL.............................10
INSTALLATION.........................10
UNIVERSAL TRANSMITTER
DESCRIPTION.........................11
OPERATION...........................11
DIAGNOSIS AND TESTING - UNIVERSAL
TRANSMITTER.......................11
AMBIENT TEMP SENSOR
DESCRIPTION.........................12
OPERATION...........................12
DIAGNOSIS AND TESTING
DIAGNOSIS AND TESTING - AMBIENT
TEMPERATURE SENSOR...............12
DIAGNOSIS AND TESTING - AMBIENT
TEMPERATURE SENSOR CIRCUIT........12
REMOVAL.............................12
INSTALLATION.........................13
OVERHEAD CONSOLE
DESCRIPTION
An overhead console is standard factory-installed
equipment on this model. The overhead console
includes the Electronic Vehicle Information Center
(EVIC) and two reading and courtesy lamps (Fig. 1).
On vehicles equipped with a power sunroof option,
the overhead console also houses the power sunroof
switch between the two reading and courtesy lamps.
The overhead console is mounted with one screw and
two snap-clips to a molded plastic retainer bracket
located above the headliner. The retainer bracket is
secured with adhesive to the inside surface of the
roof panel.
Following are general descriptions of the major
components used in the overhead console. Refer to
Overhead Consolein Wiring Diagrams for complete
circuit diagrams.
OPERATION
See the owner's manual in the vehicle glove box for
more information on the use and operation of the
various overhead console features.
STANDARD PROCEDURE
STANDARD PROCEDURE - MODULE LAMP
REPLACEMENT
(1) Remove the overhead console (Refer to 8 -
ELECTRICAL/OVERHEAD CONSOLE - REMOV-
AL).
(2) Using a flat blade screwdriver twist out socket/
lamp (Fig. 2).
(3) Replace lamp(s) as necessary.
STANDARD PROCEDURE - COURTESY LAMP
REPLACEMENT
(1) Open hood, disconnect and isolate the negative
battery cable.
WJMESSAGE SYSTEMS 8M - 1
Page 485 of 2199
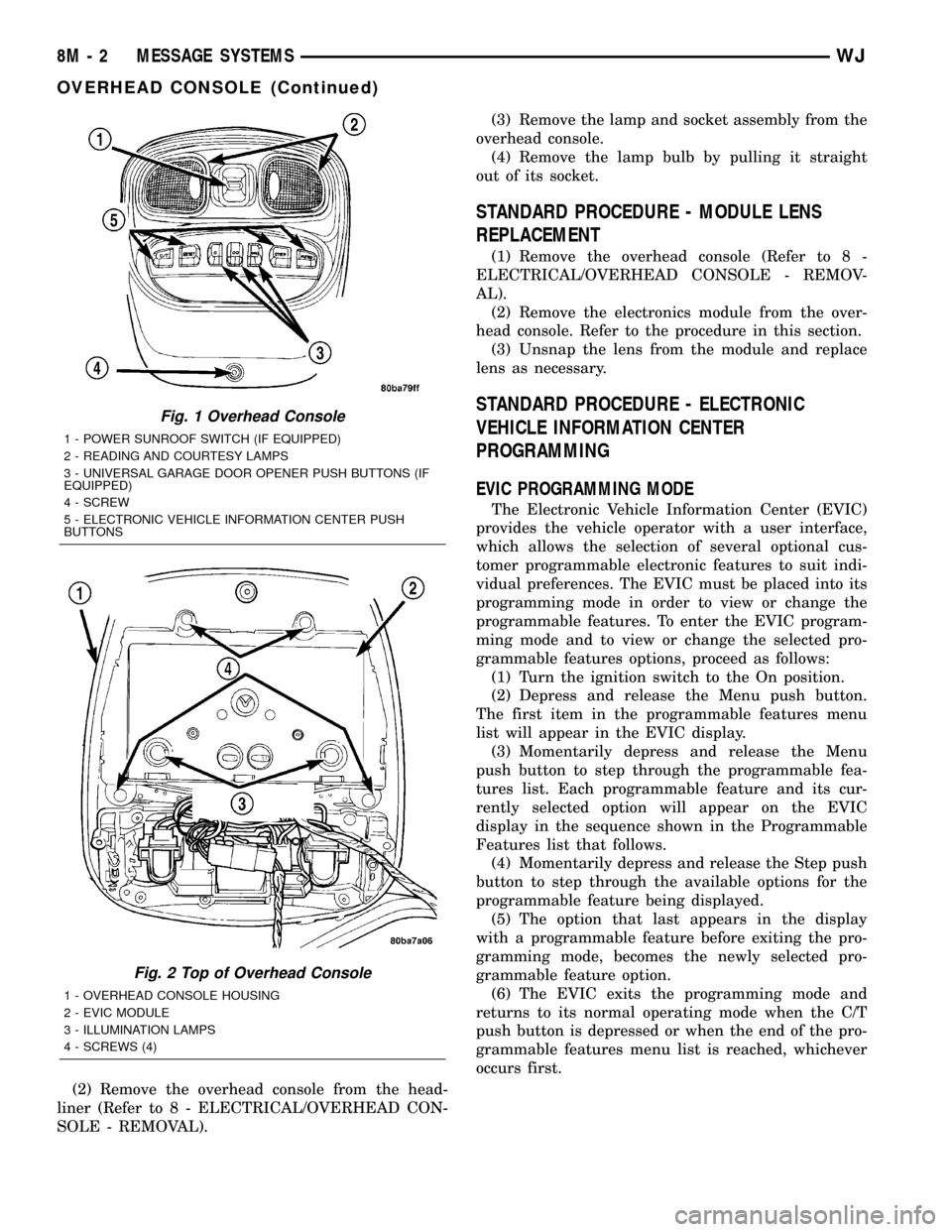
(2) Remove the overhead console from the head-
liner (Refer to 8 - ELECTRICAL/OVERHEAD CON-
SOLE - REMOVAL).(3) Remove the lamp and socket assembly from the
overhead console.
(4) Remove the lamp bulb by pulling it straight
out of its socket.
STANDARD PROCEDURE - MODULE LENS
REPLACEMENT
(1) Remove the overhead console (Refer to 8 -
ELECTRICAL/OVERHEAD CONSOLE - REMOV-
AL).
(2) Remove the electronics module from the over-
head console. Refer to the procedure in this section.
(3) Unsnap the lens from the module and replace
lens as necessary.
STANDARD PROCEDURE - ELECTRONIC
VEHICLE INFORMATION CENTER
PROGRAMMING
EVIC PROGRAMMING MODE
The Electronic Vehicle Information Center (EVIC)
provides the vehicle operator with a user interface,
which allows the selection of several optional cus-
tomer programmable electronic features to suit indi-
vidual preferences. The EVIC must be placed into its
programming mode in order to view or change the
programmable features. To enter the EVIC program-
ming mode and to view or change the selected pro-
grammable features options, proceed as follows:
(1) Turn the ignition switch to the On position.
(2) Depress and release the Menu push button.
The first item in the programmable features menu
list will appear in the EVIC display.
(3) Momentarily depress and release the Menu
push button to step through the programmable fea-
tures list. Each programmable feature and its cur-
rently selected option will appear on the EVIC
display in the sequence shown in the Programmable
Features list that follows.
(4) Momentarily depress and release the Step push
button to step through the available options for the
programmable feature being displayed.
(5) The option that last appears in the display
with a programmable feature before exiting the pro-
gramming mode, becomes the newly selected pro-
grammable feature option.
(6) The EVIC exits the programming mode and
returns to its normal operating mode when the C/T
push button is depressed or when the end of the pro-
grammable features menu list is reached, whichever
occurs first.
Fig. 1 Overhead Console
1 - POWER SUNROOF SWITCH (IF EQUIPPED)
2 - READING AND COURTESY LAMPS
3 - UNIVERSAL GARAGE DOOR OPENER PUSH BUTTONS (IF
EQUIPPED)
4 - SCREW
5 - ELECTRONIC VEHICLE INFORMATION CENTER PUSH
BUTTONS
Fig. 2 Top of Overhead Console
1 - OVERHEAD CONSOLE HOUSING
2 - EVIC MODULE
3 - ILLUMINATION LAMPS
4 - SCREWS (4)
8M - 2 MESSAGE SYSTEMSWJ
OVERHEAD CONSOLE (Continued)
Page 488 of 2199
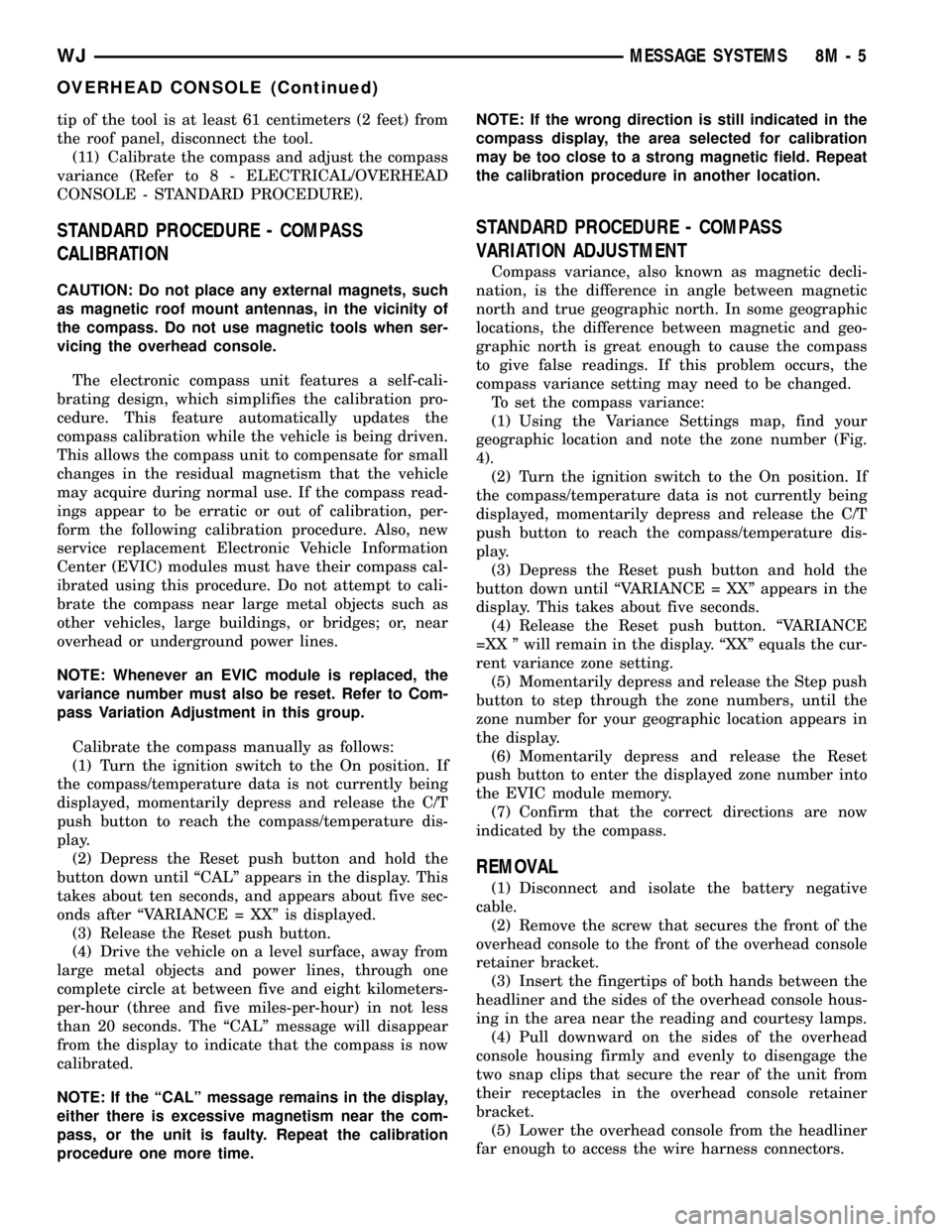
tip of the tool is at least 61 centimeters (2 feet) from
the roof panel, disconnect the tool.
(11) Calibrate the compass and adjust the compass
variance (Refer to 8 - ELECTRICAL/OVERHEAD
CONSOLE - STANDARD PROCEDURE).
STANDARD PROCEDURE - COMPASS
CALIBRATION
CAUTION: Do not place any external magnets, such
as magnetic roof mount antennas, in the vicinity of
the compass. Do not use magnetic tools when ser-
vicing the overhead console.
The electronic compass unit features a self-cali-
brating design, which simplifies the calibration pro-
cedure. This feature automatically updates the
compass calibration while the vehicle is being driven.
This allows the compass unit to compensate for small
changes in the residual magnetism that the vehicle
may acquire during normal use. If the compass read-
ings appear to be erratic or out of calibration, per-
form the following calibration procedure. Also, new
service replacement Electronic Vehicle Information
Center (EVIC) modules must have their compass cal-
ibrated using this procedure. Do not attempt to cali-
brate the compass near large metal objects such as
other vehicles, large buildings, or bridges; or, near
overhead or underground power lines.
NOTE: Whenever an EVIC module is replaced, the
variance number must also be reset. Refer to Com-
pass Variation Adjustment in this group.
Calibrate the compass manually as follows:
(1) Turn the ignition switch to the On position. If
the compass/temperature data is not currently being
displayed, momentarily depress and release the C/T
push button to reach the compass/temperature dis-
play.
(2) Depress the Reset push button and hold the
button down until ªCALº appears in the display. This
takes about ten seconds, and appears about five sec-
onds after ªVARIANCE = XXº is displayed.
(3) Release the Reset push button.
(4) Drive the vehicle on a level surface, away from
large metal objects and power lines, through one
complete circle at between five and eight kilometers-
per-hour (three and five miles-per-hour) in not less
than 20 seconds. The ªCALº message will disappear
from the display to indicate that the compass is now
calibrated.
NOTE: If the ªCALº message remains in the display,
either there is excessive magnetism near the com-
pass, or the unit is faulty. Repeat the calibration
procedure one more time.NOTE: If the wrong direction is still indicated in the
compass display, the area selected for calibration
may be too close to a strong magnetic field. Repeat
the calibration procedure in another location.
STANDARD PROCEDURE - COMPASS
VARIATION ADJUSTMENT
Compass variance, also known as magnetic decli-
nation, is the difference in angle between magnetic
north and true geographic north. In some geographic
locations, the difference between magnetic and geo-
graphic north is great enough to cause the compass
to give false readings. If this problem occurs, the
compass variance setting may need to be changed.
To set the compass variance:
(1) Using the Variance Settings map, find your
geographic location and note the zone number (Fig.
4).
(2) Turn the ignition switch to the On position. If
the compass/temperature data is not currently being
displayed, momentarily depress and release the C/T
push button to reach the compass/temperature dis-
play.
(3) Depress the Reset push button and hold the
button down until ªVARIANCE = XXº appears in the
display. This takes about five seconds.
(4) Release the Reset push button. ªVARIANCE
=XX º will remain in the display. ªXXº equals the cur-
rent variance zone setting.
(5) Momentarily depress and release the Step push
button to step through the zone numbers, until the
zone number for your geographic location appears in
the display.
(6) Momentarily depress and release the Reset
push button to enter the displayed zone number into
the EVIC module memory.
(7) Confirm that the correct directions are now
indicated by the compass.
REMOVAL
(1) Disconnect and isolate the battery negative
cable.
(2) Remove the screw that secures the front of the
overhead console to the front of the overhead console
retainer bracket.
(3) Insert the fingertips of both hands between the
headliner and the sides of the overhead console hous-
ing in the area near the reading and courtesy lamps.
(4) Pull downward on the sides of the overhead
console housing firmly and evenly to disengage the
two snap clips that secure the rear of the unit from
their receptacles in the overhead console retainer
bracket.
(5) Lower the overhead console from the headliner
far enough to access the wire harness connectors.
WJMESSAGE SYSTEMS 8M - 5
OVERHEAD CONSOLE (Continued)
Page 512 of 2199
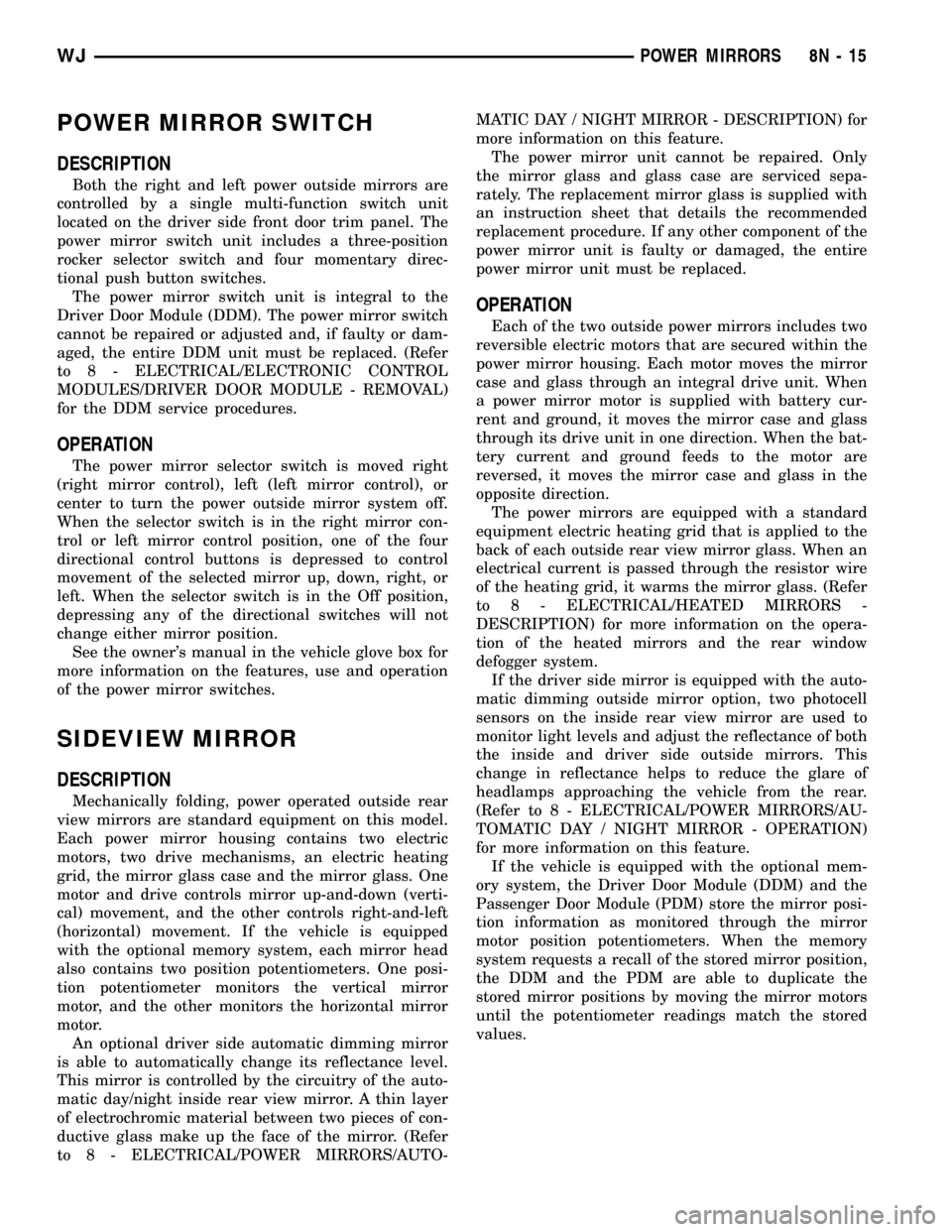
POWER MIRROR SWITCH
DESCRIPTION
Both the right and left power outside mirrors are
controlled by a single multi-function switch unit
located on the driver side front door trim panel. The
power mirror switch unit includes a three-position
rocker selector switch and four momentary direc-
tional push button switches.
The power mirror switch unit is integral to the
Driver Door Module (DDM). The power mirror switch
cannot be repaired or adjusted and, if faulty or dam-
aged, the entire DDM unit must be replaced. (Refer
to 8 - ELECTRICAL/ELECTRONIC CONTROL
MODULES/DRIVER DOOR MODULE - REMOVAL)
for the DDM service procedures.
OPERATION
The power mirror selector switch is moved right
(right mirror control), left (left mirror control), or
center to turn the power outside mirror system off.
When the selector switch is in the right mirror con-
trol or left mirror control position, one of the four
directional control buttons is depressed to control
movement of the selected mirror up, down, right, or
left. When the selector switch is in the Off position,
depressing any of the directional switches will not
change either mirror position.
See the owner's manual in the vehicle glove box for
more information on the features, use and operation
of the power mirror switches.
SIDEVIEW MIRROR
DESCRIPTION
Mechanically folding, power operated outside rear
view mirrors are standard equipment on this model.
Each power mirror housing contains two electric
motors, two drive mechanisms, an electric heating
grid, the mirror glass case and the mirror glass. One
motor and drive controls mirror up-and-down (verti-
cal) movement, and the other controls right-and-left
(horizontal) movement. If the vehicle is equipped
with the optional memory system, each mirror head
also contains two position potentiometers. One posi-
tion potentiometer monitors the vertical mirror
motor, and the other monitors the horizontal mirror
motor.
An optional driver side automatic dimming mirror
is able to automatically change its reflectance level.
This mirror is controlled by the circuitry of the auto-
matic day/night inside rear view mirror. A thin layer
of electrochromic material between two pieces of con-
ductive glass make up the face of the mirror. (Refer
to 8 - ELECTRICAL/POWER MIRRORS/AUTO-MATIC DAY / NIGHT MIRROR - DESCRIPTION) for
more information on this feature.
The power mirror unit cannot be repaired. Only
the mirror glass and glass case are serviced sepa-
rately. The replacement mirror glass is supplied with
an instruction sheet that details the recommended
replacement procedure. If any other component of the
power mirror unit is faulty or damaged, the entire
power mirror unit must be replaced.
OPERATION
Each of the two outside power mirrors includes two
reversible electric motors that are secured within the
power mirror housing. Each motor moves the mirror
case and glass through an integral drive unit. When
a power mirror motor is supplied with battery cur-
rent and ground, it moves the mirror case and glass
through its drive unit in one direction. When the bat-
tery current and ground feeds to the motor are
reversed, it moves the mirror case and glass in the
opposite direction.
The power mirrors are equipped with a standard
equipment electric heating grid that is applied to the
back of each outside rear view mirror glass. When an
electrical current is passed through the resistor wire
of the heating grid, it warms the mirror glass. (Refer
to 8 - ELECTRICAL/HEATED MIRRORS -
DESCRIPTION) for more information on the opera-
tion of the heated mirrors and the rear window
defogger system.
If the driver side mirror is equipped with the auto-
matic dimming outside mirror option, two photocell
sensors on the inside rear view mirror are used to
monitor light levels and adjust the reflectance of both
the inside and driver side outside mirrors. This
change in reflectance helps to reduce the glare of
headlamps approaching the vehicle from the rear.
(Refer to 8 - ELECTRICAL/POWER MIRRORS/AU-
TOMATIC DAY / NIGHT MIRROR - OPERATION)
for more information on this feature.
If the vehicle is equipped with the optional mem-
ory system, the Driver Door Module (DDM) and the
Passenger Door Module (PDM) store the mirror posi-
tion information as monitored through the mirror
motor position potentiometers. When the memory
system requests a recall of the stored mirror position,
the DDM and the PDM are able to duplicate the
stored mirror positions by moving the mirror motors
until the potentiometer readings match the stored
values.
WJPOWER MIRRORS 8N - 15
Page 550 of 2199
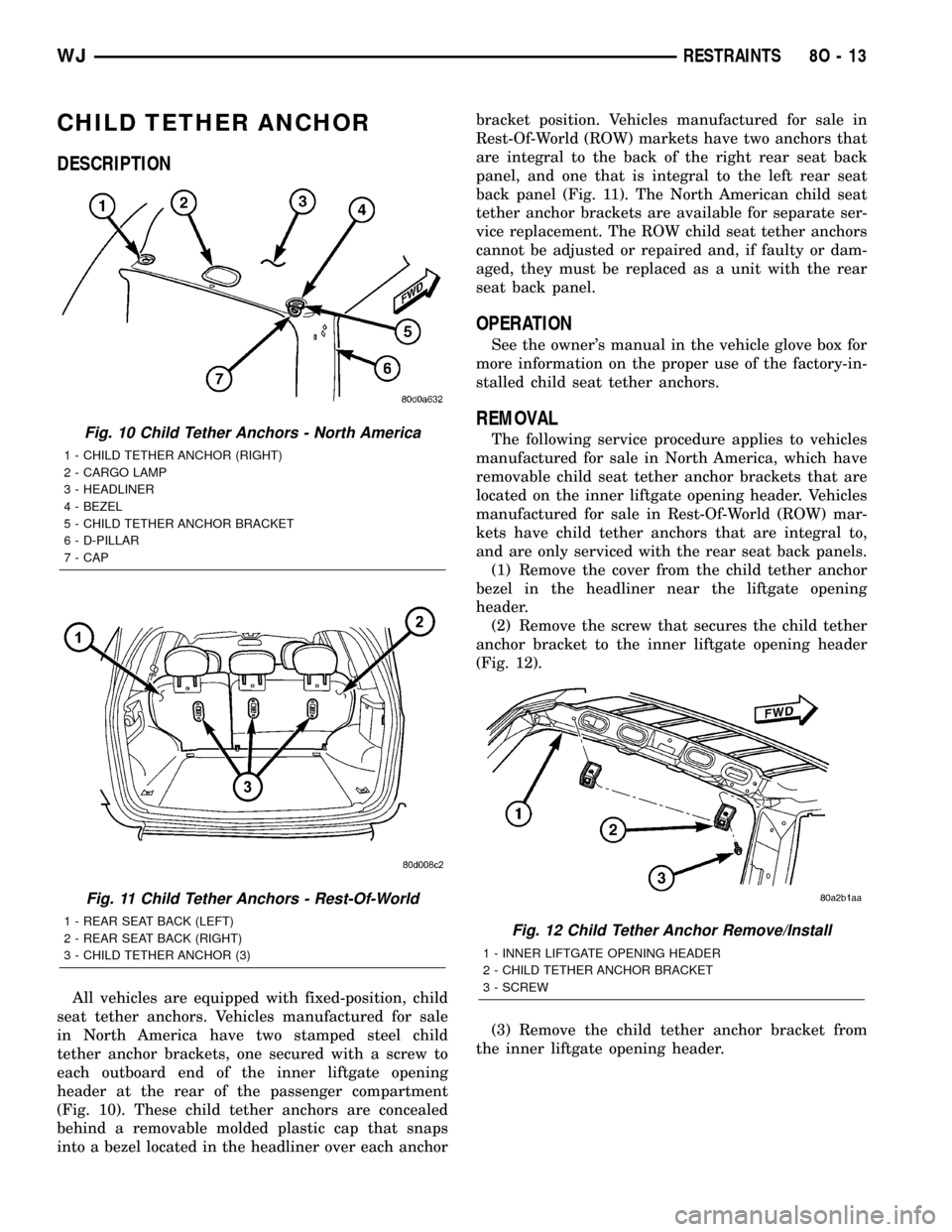
CHILD TETHER ANCHOR
DESCRIPTION
All vehicles are equipped with fixed-position, child
seat tether anchors. Vehicles manufactured for sale
in North America have two stamped steel child
tether anchor brackets, one secured with a screw to
each outboard end of the inner liftgate opening
header at the rear of the passenger compartment
(Fig. 10). These child tether anchors are concealed
behind a removable molded plastic cap that snaps
into a bezel located in the headliner over each anchorbracket position. Vehicles manufactured for sale in
Rest-Of-World (ROW) markets have two anchors that
are integral to the back of the right rear seat back
panel, and one that is integral to the left rear seat
back panel (Fig. 11). The North American child seat
tether anchor brackets are available for separate ser-
vice replacement. The ROW child seat tether anchors
cannot be adjusted or repaired and, if faulty or dam-
aged, they must be replaced as a unit with the rear
seat back panel.
OPERATION
See the owner's manual in the vehicle glove box for
more information on the proper use of the factory-in-
stalled child seat tether anchors.
REMOVAL
The following service procedure applies to vehicles
manufactured for sale in North America, which have
removable child seat tether anchor brackets that are
located on the inner liftgate opening header. Vehicles
manufactured for sale in Rest-Of-World (ROW) mar-
kets have child tether anchors that are integral to,
and are only serviced with the rear seat back panels.
(1) Remove the cover from the child tether anchor
bezel in the headliner near the liftgate opening
header.
(2) Remove the screw that secures the child tether
anchor bracket to the inner liftgate opening header
(Fig. 12).
(3) Remove the child tether anchor bracket from
the inner liftgate opening header.Fig. 10 Child Tether Anchors - North America
1 - CHILD TETHER ANCHOR (RIGHT)
2 - CARGO LAMP
3 - HEADLINER
4 - BEZEL
5 - CHILD TETHER ANCHOR BRACKET
6 - D-PILLAR
7 - CAP
Fig. 11 Child Tether Anchors - Rest-Of-World
1 - REAR SEAT BACK (LEFT)
2 - REAR SEAT BACK (RIGHT)
3 - CHILD TETHER ANCHOR (3)Fig. 12 Child Tether Anchor Remove/Install
1 - INNER LIFTGATE OPENING HEADER
2 - CHILD TETHER ANCHOR BRACKET
3 - SCREW
WJRESTRAINTS 8O - 13
Page 560 of 2199
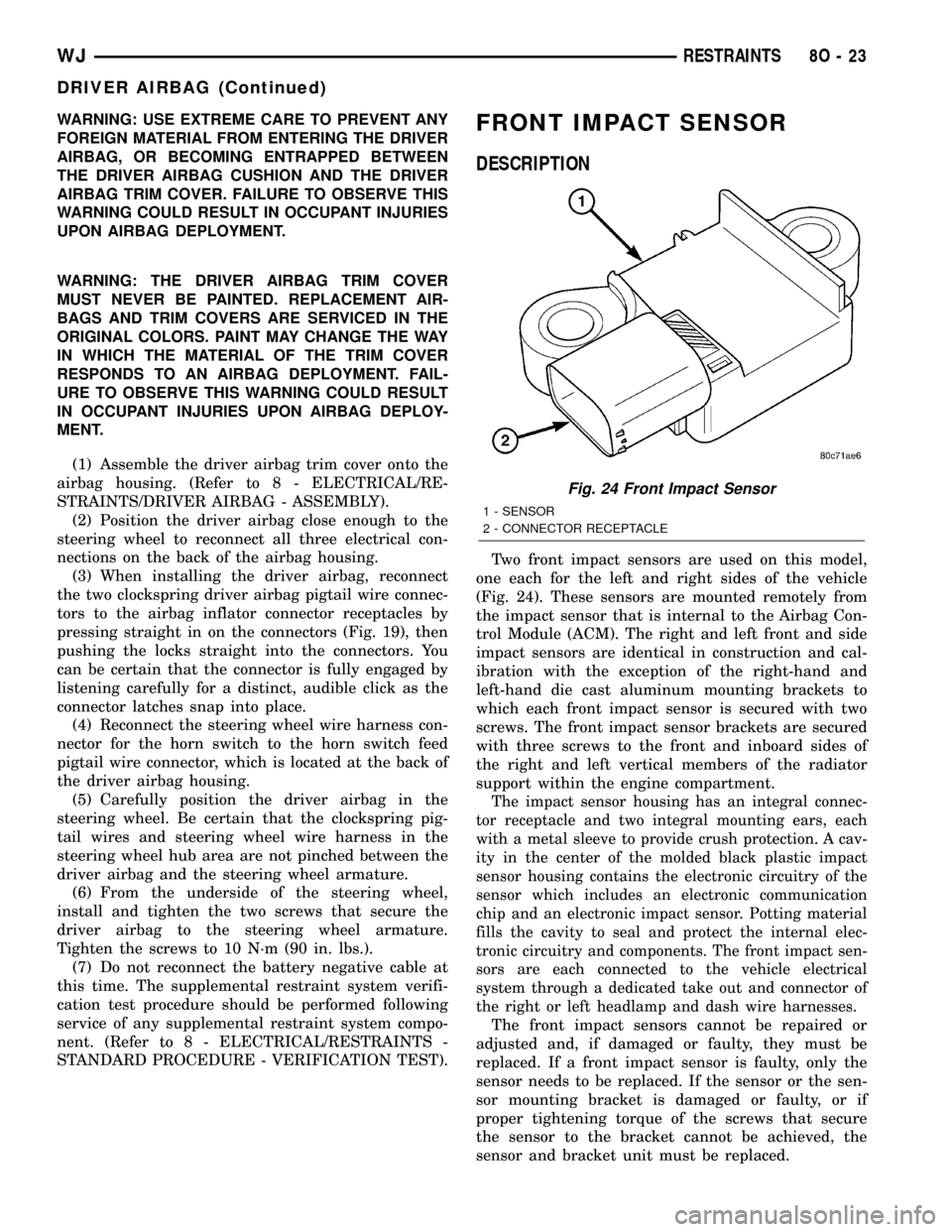
WARNING: USE EXTREME CARE TO PREVENT ANY
FOREIGN MATERIAL FROM ENTERING THE DRIVER
AIRBAG, OR BECOMING ENTRAPPED BETWEEN
THE DRIVER AIRBAG CUSHION AND THE DRIVER
AIRBAG TRIM COVER. FAILURE TO OBSERVE THIS
WARNING COULD RESULT IN OCCUPANT INJURIES
UPON AIRBAG DEPLOYMENT.
WARNING: THE DRIVER AIRBAG TRIM COVER
MUST NEVER BE PAINTED. REPLACEMENT AIR-
BAGS AND TRIM COVERS ARE SERVICED IN THE
ORIGINAL COLORS. PAINT MAY CHANGE THE WAY
IN WHICH THE MATERIAL OF THE TRIM COVER
RESPONDS TO AN AIRBAG DEPLOYMENT. FAIL-
URE TO OBSERVE THIS WARNING COULD RESULT
IN OCCUPANT INJURIES UPON AIRBAG DEPLOY-
MENT.
(1) Assemble the driver airbag trim cover onto the
airbag housing. (Refer to 8 - ELECTRICAL/RE-
STRAINTS/DRIVER AIRBAG - ASSEMBLY).
(2) Position the driver airbag close enough to the
steering wheel to reconnect all three electrical con-
nections on the back of the airbag housing.
(3) When installing the driver airbag, reconnect
the two clockspring driver airbag pigtail wire connec-
tors to the airbag inflator connector receptacles by
pressing straight in on the connectors (Fig. 19), then
pushing the locks straight into the connectors. You
can be certain that the connector is fully engaged by
listening carefully for a distinct, audible click as the
connector latches snap into place.
(4) Reconnect the steering wheel wire harness con-
nector for the horn switch to the horn switch feed
pigtail wire connector, which is located at the back of
the driver airbag housing.
(5) Carefully position the driver airbag in the
steering wheel. Be certain that the clockspring pig-
tail wires and steering wheel wire harness in the
steering wheel hub area are not pinched between the
driver airbag and the steering wheel armature.
(6) From the underside of the steering wheel,
install and tighten the two screws that secure the
driver airbag to the steering wheel armature.
Tighten the screws to 10 N´m (90 in. lbs.).
(7) Do not reconnect the battery negative cable at
this time. The supplemental restraint system verifi-
cation test procedure should be performed following
service of any supplemental restraint system compo-
nent. (Refer to 8 - ELECTRICAL/RESTRAINTS -
STANDARD PROCEDURE - VERIFICATION TEST).FRONT IMPACT SENSOR
DESCRIPTION
Two front impact sensors are used on this model,
one each for the left and right sides of the vehicle
(Fig. 24). These sensors are mounted remotely from
the impact sensor that is internal to the Airbag Con-
trol Module (ACM). The right and left front and side
impact sensors are identical in construction and cal-
ibration with the exception of the right-hand and
left-hand die cast aluminum mounting brackets to
which each front impact sensor is secured with two
screws. The front impact sensor brackets are secured
with three screws to the front and inboard sides of
the right and left vertical members of the radiator
support within the engine compartment.
The impact sensor housing has an integral connec-
tor receptacle and two integral mounting ears, each
with a metal sleeve to provide crush protection. A cav-
ity in the center of the molded black plastic impact
sensor housing contains the electronic circuitry of the
sensor which includes an electronic communication
chip and an electronic impact sensor. Potting material
fills the cavity to seal and protect the internal elec-
tronic circuitry and components. The front impact sen-
sors are each connected to the vehicle electrical
system through a dedicated take out and connector of
the right or left headlamp and dash wire harnesses.
The front impact sensors cannot be repaired or
adjusted and, if damaged or faulty, they must be
replaced. If a front impact sensor is faulty, only the
sensor needs to be replaced. If the sensor or the sen-
sor mounting bracket is damaged or faulty, or if
proper tightening torque of the screws that secure
the sensor to the bracket cannot be achieved, the
sensor and bracket unit must be replaced.
Fig. 24 Front Impact Sensor
1 - SENSOR
2 - CONNECTOR RECEPTACLE
WJRESTRAINTS 8O - 23
DRIVER AIRBAG (Continued)
Page 564 of 2199
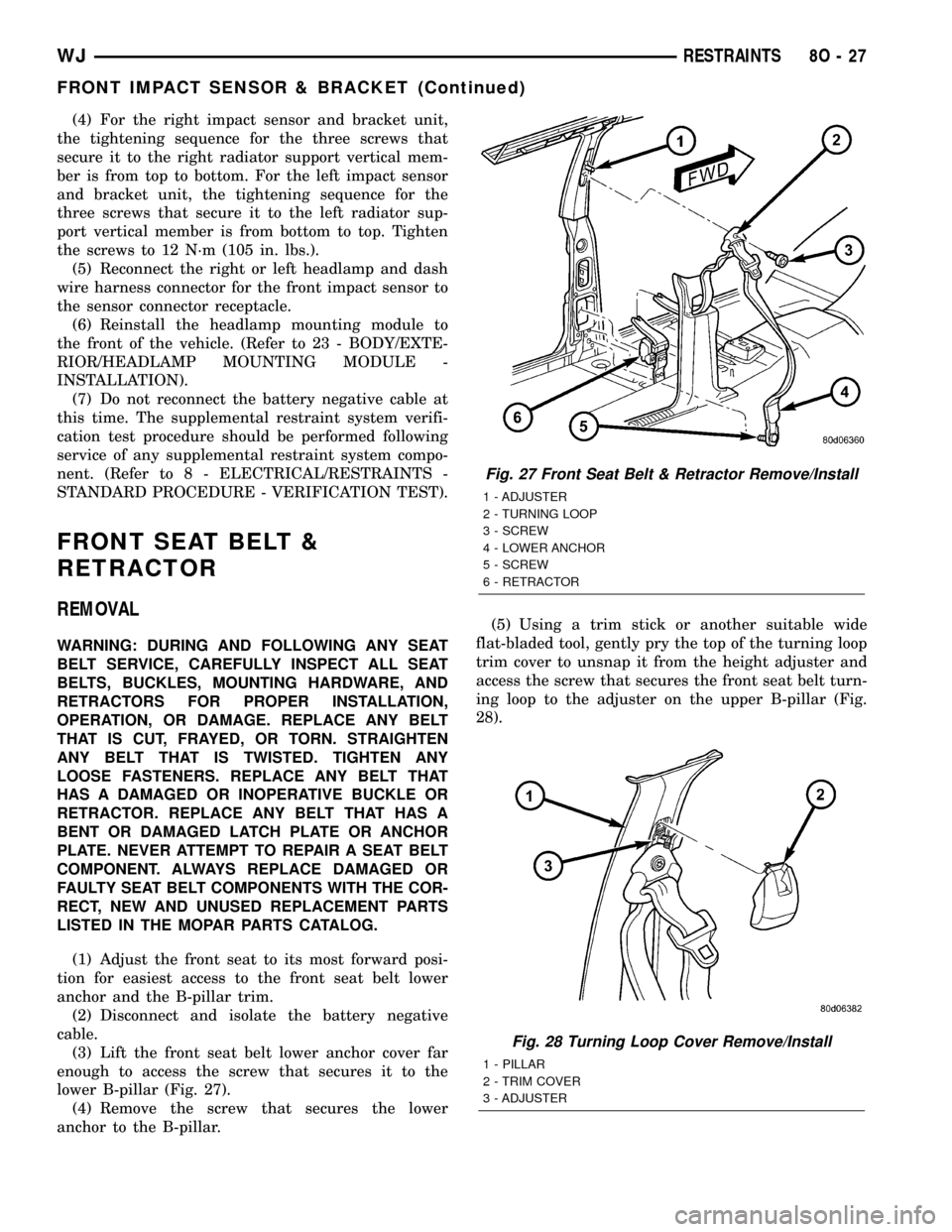
(4) For the right impact sensor and bracket unit,
the tightening sequence for the three screws that
secure it to the right radiator support vertical mem-
ber is from top to bottom. For the left impact sensor
and bracket unit, the tightening sequence for the
three screws that secure it to the left radiator sup-
port vertical member is from bottom to top. Tighten
the screws to 12 N´m (105 in. lbs.).
(5) Reconnect the right or left headlamp and dash
wire harness connector for the front impact sensor to
the sensor connector receptacle.
(6) Reinstall the headlamp mounting module to
the front of the vehicle. (Refer to 23 - BODY/EXTE-
RIOR/HEADLAMP MOUNTING MODULE -
INSTALLATION).
(7) Do not reconnect the battery negative cable at
this time. The supplemental restraint system verifi-
cation test procedure should be performed following
service of any supplemental restraint system compo-
nent. (Refer to 8 - ELECTRICAL/RESTRAINTS -
STANDARD PROCEDURE - VERIFICATION TEST).
FRONT SEAT BELT &
RETRACTOR
REMOVAL
WARNING: DURING AND FOLLOWING ANY SEAT
BELT SERVICE, CAREFULLY INSPECT ALL SEAT
BELTS, BUCKLES, MOUNTING HARDWARE, AND
RETRACTORS FOR PROPER INSTALLATION,
OPERATION, OR DAMAGE. REPLACE ANY BELT
THAT IS CUT, FRAYED, OR TORN. STRAIGHTEN
ANY BELT THAT IS TWISTED. TIGHTEN ANY
LOOSE FASTENERS. REPLACE ANY BELT THAT
HAS A DAMAGED OR INOPERATIVE BUCKLE OR
RETRACTOR. REPLACE ANY BELT THAT HAS A
BENT OR DAMAGED LATCH PLATE OR ANCHOR
PLATE. NEVER ATTEMPT TO REPAIR A SEAT BELT
COMPONENT. ALWAYS REPLACE DAMAGED OR
FAULTY SEAT BELT COMPONENTS WITH THE COR-
RECT, NEW AND UNUSED REPLACEMENT PARTS
LISTED IN THE MOPAR PARTS CATALOG.
(1) Adjust the front seat to its most forward posi-
tion for easiest access to the front seat belt lower
anchor and the B-pillar trim.
(2) Disconnect and isolate the battery negative
cable.
(3) Lift the front seat belt lower anchor cover far
enough to access the screw that secures it to the
lower B-pillar (Fig. 27).
(4) Remove the screw that secures the lower
anchor to the B-pillar.(5) Using a trim stick or another suitable wide
flat-bladed tool, gently pry the top of the turning loop
trim cover to unsnap it from the height adjuster and
access the screw that secures the front seat belt turn-
ing loop to the adjuster on the upper B-pillar (Fig.
28).
Fig. 27 Front Seat Belt & Retractor Remove/Install
1 - ADJUSTER
2 - TURNING LOOP
3 - SCREW
4 - LOWER ANCHOR
5 - SCREW
6 - RETRACTOR
Fig. 28 Turning Loop Cover Remove/Install
1 - PILLAR
2 - TRIM COVER
3 - ADJUSTER
WJRESTRAINTS 8O - 27
FRONT IMPACT SENSOR & BRACKET (Continued)
Page 1230 of 2199
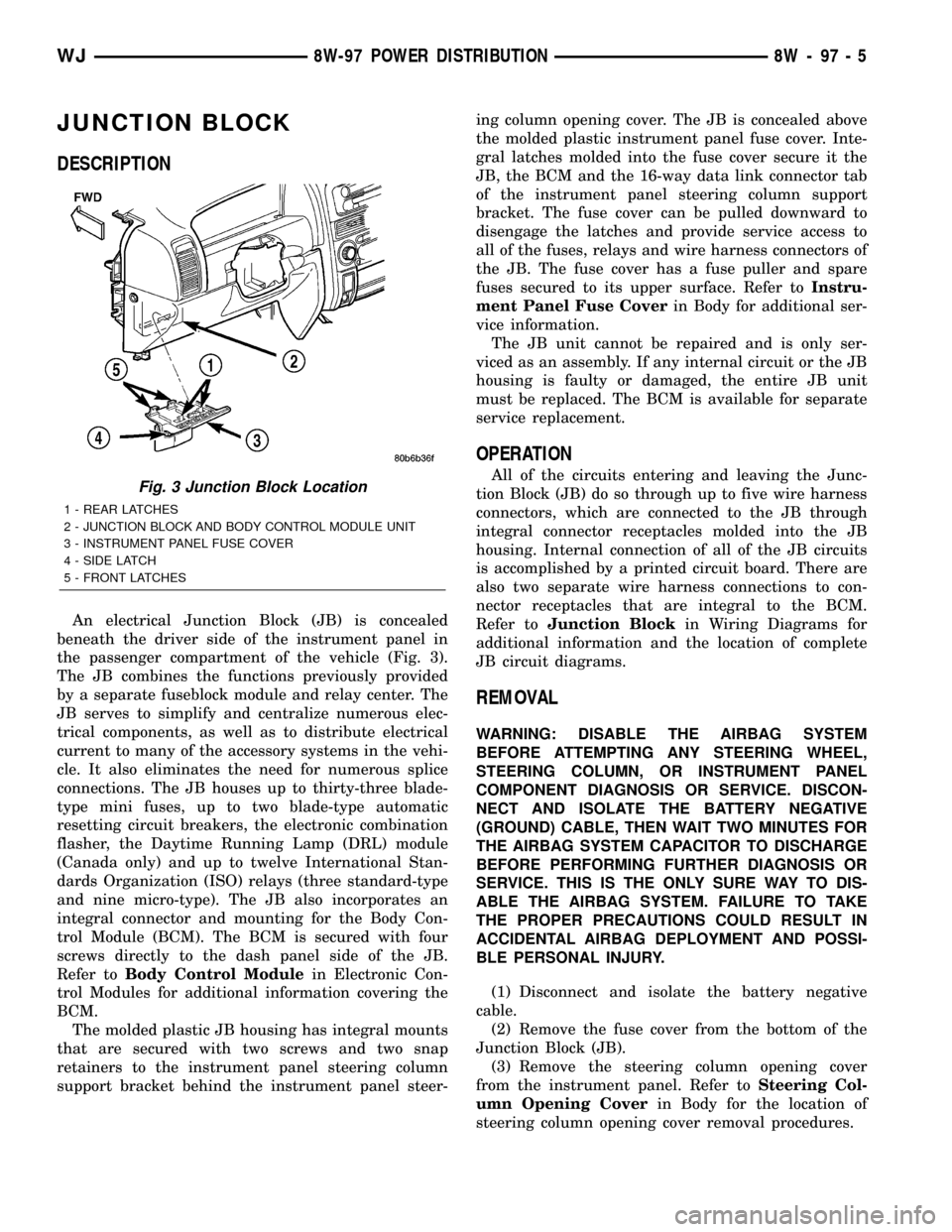
JUNCTION BLOCK
DESCRIPTION
An electrical Junction Block (JB) is concealed
beneath the driver side of the instrument panel in
the passenger compartment of the vehicle (Fig. 3).
The JB combines the functions previously provided
by a separate fuseblock module and relay center. The
JB serves to simplify and centralize numerous elec-
trical components, as well as to distribute electrical
current to many of the accessory systems in the vehi-
cle. It also eliminates the need for numerous splice
connections. The JB houses up to thirty-three blade-
type mini fuses, up to two blade-type automatic
resetting circuit breakers, the electronic combination
flasher, the Daytime Running Lamp (DRL) module
(Canada only) and up to twelve International Stan-
dards Organization (ISO) relays (three standard-type
and nine micro-type). The JB also incorporates an
integral connector and mounting for the Body Con-
trol Module (BCM). The BCM is secured with four
screws directly to the dash panel side of the JB.
Refer toBody Control Modulein Electronic Con-
trol Modules for additional information covering the
BCM.
The molded plastic JB housing has integral mounts
that are secured with two screws and two snap
retainers to the instrument panel steering column
support bracket behind the instrument panel steer-ing column opening cover. The JB is concealed above
the molded plastic instrument panel fuse cover. Inte-
gral latches molded into the fuse cover secure it the
JB, the BCM and the 16-way data link connector tab
of the instrument panel steering column support
bracket. The fuse cover can be pulled downward to
disengage the latches and provide service access to
all of the fuses, relays and wire harness connectors of
the JB. The fuse cover has a fuse puller and spare
fuses secured to its upper surface. Refer toInstru-
ment Panel Fuse Coverin Body for additional ser-
vice information.
The JB unit cannot be repaired and is only ser-
viced as an assembly. If any internal circuit or the JB
housing is faulty or damaged, the entire JB unit
must be replaced. The BCM is available for separate
service replacement.
OPERATION
All of the circuits entering and leaving the Junc-
tion Block (JB) do so through up to five wire harness
connectors, which are connected to the JB through
integral connector receptacles molded into the JB
housing. Internal connection of all of the JB circuits
is accomplished by a printed circuit board. There are
also two separate wire harness connections to con-
nector receptacles that are integral to the BCM.
Refer toJunction Blockin Wiring Diagrams for
additional information and the location of complete
JB circuit diagrams.
REMOVAL
WARNING: DISABLE THE AIRBAG SYSTEM
BEFORE ATTEMPTING ANY STEERING WHEEL,
STEERING COLUMN, OR INSTRUMENT PANEL
COMPONENT DIAGNOSIS OR SERVICE. DISCON-
NECT AND ISOLATE THE BATTERY NEGATIVE
(GROUND) CABLE, THEN WAIT TWO MINUTES FOR
THE AIRBAG SYSTEM CAPACITOR TO DISCHARGE
BEFORE PERFORMING FURTHER DIAGNOSIS OR
SERVICE. THIS IS THE ONLY SURE WAY TO DIS-
ABLE THE AIRBAG SYSTEM. FAILURE TO TAKE
THE PROPER PRECAUTIONS COULD RESULT IN
ACCIDENTAL AIRBAG DEPLOYMENT AND POSSI-
BLE PERSONAL INJURY.
(1) Disconnect and isolate the battery negative
cable.
(2) Remove the fuse cover from the bottom of the
Junction Block (JB).
(3) Remove the steering column opening cover
from the instrument panel. Refer toSteering Col-
umn Opening Coverin Body for the location of
steering column opening cover removal procedures.
Fig. 3 Junction Block Location
1 - REAR LATCHES
2 - JUNCTION BLOCK AND BODY CONTROL MODULE UNIT
3 - INSTRUMENT PANEL FUSE COVER
4 - SIDE LATCH
5 - FRONT LATCHES
WJ8W-97 POWER DISTRIBUTION 8W - 97 - 5
Page 1232 of 2199
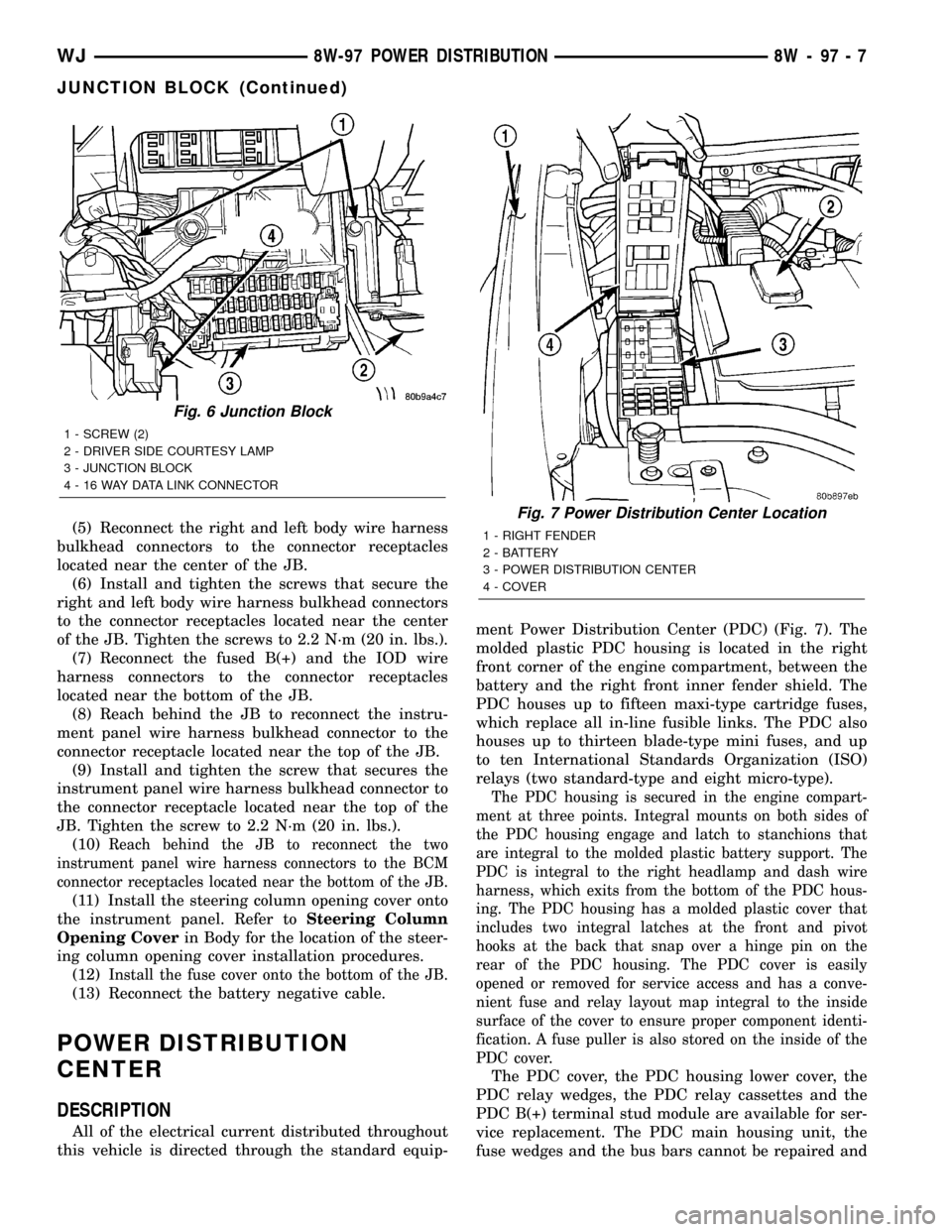
(5) Reconnect the right and left body wire harness
bulkhead connectors to the connector receptacles
located near the center of the JB.
(6) Install and tighten the screws that secure the
right and left body wire harness bulkhead connectors
to the connector receptacles located near the center
of the JB. Tighten the screws to 2.2 N´m (20 in. lbs.).
(7) Reconnect the fused B(+) and the IOD wire
harness connectors to the connector receptacles
located near the bottom of the JB.
(8) Reach behind the JB to reconnect the instru-
ment panel wire harness bulkhead connector to the
connector receptacle located near the top of the JB.
(9) Install and tighten the screw that secures the
instrument panel wire harness bulkhead connector to
the connector receptacle located near the top of the
JB. Tighten the screw to 2.2 N´m (20 in. lbs.).
(10)
Reach behind the JB to reconnect the two
instrument panel wire harness connectors to the BCM
connector receptacles located near the bottom of the JB.
(11) Install the steering column opening cover onto
the instrument panel. Refer toSteering Column
Opening Coverin Body for the location of the steer-
ing column opening cover installation procedures.
(12)
Install the fuse cover onto the bottom of the JB.
(13) Reconnect the battery negative cable.
POWER DISTRIBUTION
CENTER
DESCRIPTION
All of the electrical current distributed throughout
this vehicle is directed through the standard equip-ment Power Distribution Center (PDC) (Fig. 7). The
molded plastic PDC housing is located in the right
front corner of the engine compartment, between the
battery and the right front inner fender shield. The
PDC houses up to fifteen maxi-type cartridge fuses,
which replace all in-line fusible links. The PDC also
houses up to thirteen blade-type mini fuses, and up
to ten International Standards Organization (ISO)
relays (two standard-type and eight micro-type).
The PDC housing is secured in the engine compart-
ment at three points. Integral mounts on both sides of
the PDC housing engage and latch to stanchions that
are integral to the molded plastic battery support. The
PDC is integral to the right headlamp and dash wire
harness, which exits from the bottom of the PDC hous-
ing. The PDC housing has a molded plastic cover that
includes two integral latches at the front and pivot
hooks at the back that snap over a hinge pin on the
rear of the PDC housing. The PDC cover is easily
opened or removed for service access and has a conve-
nient fuse and relay layout map integral to the inside
surface of the cover to ensure proper component identi-
fication. A fuse puller is also stored on the inside of the
PDC cover.
The PDC cover, the PDC housing lower cover, the
PDC relay wedges, the PDC relay cassettes and the
PDC B(+) terminal stud module are available for ser-
vice replacement. The PDC main housing unit, the
fuse wedges and the bus bars cannot be repaired and
Fig. 6 Junction Block
1 - SCREW (2)
2 - DRIVER SIDE COURTESY LAMP
3 - JUNCTION BLOCK
4 - 16 WAY DATA LINK CONNECTOR
Fig. 7 Power Distribution Center Location
1 - RIGHT FENDER
2 - BATTERY
3 - POWER DISTRIBUTION CENTER
4 - COVER
WJ8W-97 POWER DISTRIBUTION 8W - 97 - 7
JUNCTION BLOCK (Continued)