display JEEP GRAND CHEROKEE 2003 WJ / 2.G Service Manual
[x] Cancel search | Manufacturer: JEEP, Model Year: 2003, Model line: GRAND CHEROKEE, Model: JEEP GRAND CHEROKEE 2003 WJ / 2.GPages: 2199, PDF Size: 76.01 MB
Page 491 of 2199
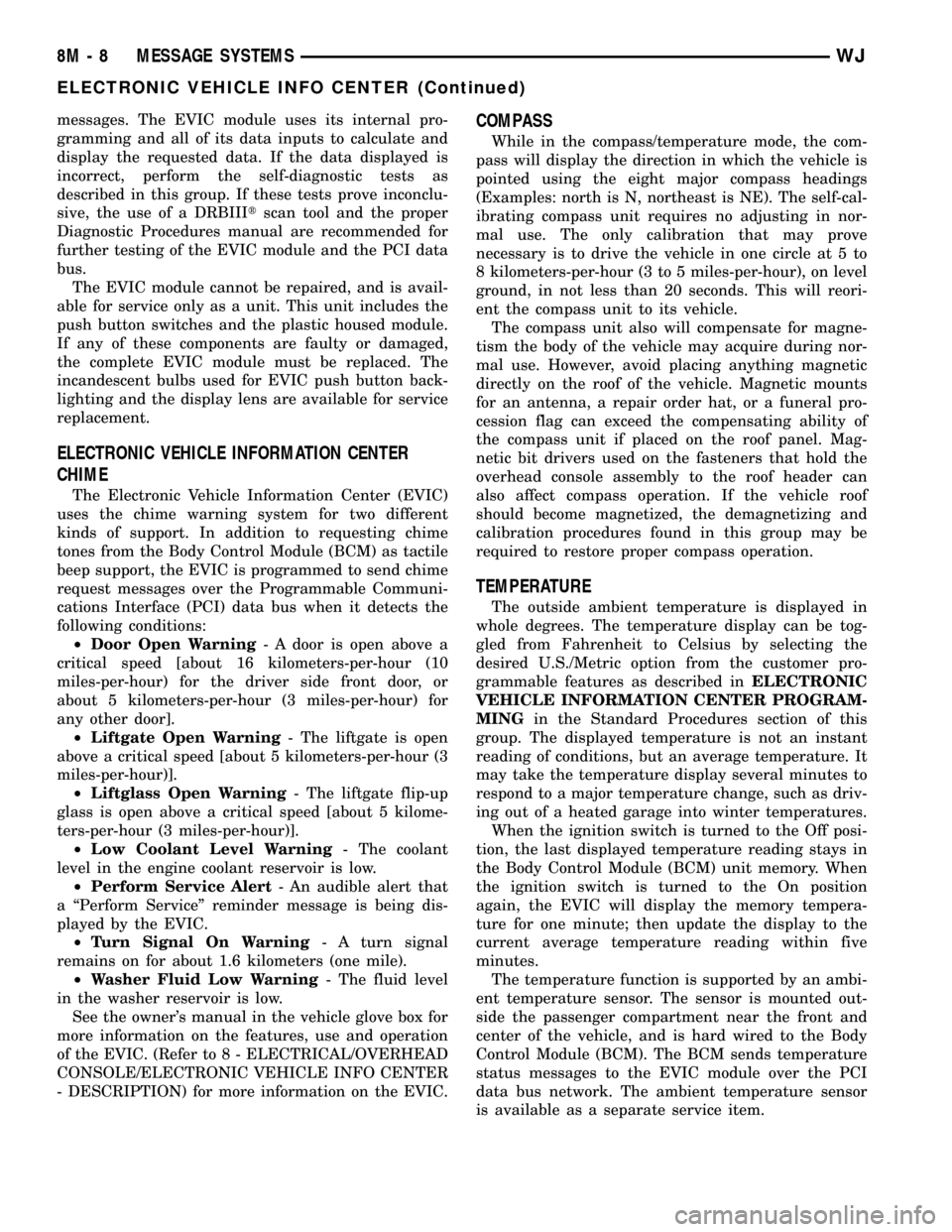
messages. The EVIC module uses its internal pro-
gramming and all of its data inputs to calculate and
display the requested data. If the data displayed is
incorrect, perform the self-diagnostic tests as
described in this group. If these tests prove inconclu-
sive, the use of a DRBIIItscan tool and the proper
Diagnostic Procedures manual are recommended for
further testing of the EVIC module and the PCI data
bus.
The EVIC module cannot be repaired, and is avail-
able for service only as a unit. This unit includes the
push button switches and the plastic housed module.
If any of these components are faulty or damaged,
the complete EVIC module must be replaced. The
incandescent bulbs used for EVIC push button back-
lighting and the display lens are available for service
replacement.
ELECTRONIC VEHICLE INFORMATION CENTER
CHIME
The Electronic Vehicle Information Center (EVIC)
uses the chime warning system for two different
kinds of support. In addition to requesting chime
tones from the Body Control Module (BCM) as tactile
beep support, the EVIC is programmed to send chime
request messages over the Programmable Communi-
cations Interface (PCI) data bus when it detects the
following conditions:
²Door Open Warning- A door is open above a
critical speed [about 16 kilometers-per-hour (10
miles-per-hour) for the driver side front door, or
about 5 kilometers-per-hour (3 miles-per-hour) for
any other door].
²Liftgate Open Warning- The liftgate is open
above a critical speed [about 5 kilometers-per-hour (3
miles-per-hour)].
²Liftglass Open Warning- The liftgate flip-up
glass is open above a critical speed [about 5 kilome-
ters-per-hour (3 miles-per-hour)].
²Low Coolant Level Warning- The coolant
level in the engine coolant reservoir is low.
²Perform Service Alert- An audible alert that
a ªPerform Serviceº reminder message is being dis-
played by the EVIC.
²Turn Signal On Warning- A turn signal
remains on for about 1.6 kilometers (one mile).
²Washer Fluid Low Warning- The fluid level
in the washer reservoir is low.
See the owner's manual in the vehicle glove box for
more information on the features, use and operation
of the EVIC. (Refer to 8 - ELECTRICAL/OVERHEAD
CONSOLE/ELECTRONIC VEHICLE INFO CENTER
- DESCRIPTION) for more information on the EVIC.
COMPASS
While in the compass/temperature mode, the com-
pass will display the direction in which the vehicle is
pointed using the eight major compass headings
(Examples: north is N, northeast is NE). The self-cal-
ibrating compass unit requires no adjusting in nor-
mal use. The only calibration that may prove
necessary is to drive the vehicle in one circle at 5 to
8 kilometers-per-hour (3 to 5 miles-per-hour), on level
ground, in not less than 20 seconds. This will reori-
ent the compass unit to its vehicle.
The compass unit also will compensate for magne-
tism the body of the vehicle may acquire during nor-
mal use. However, avoid placing anything magnetic
directly on the roof of the vehicle. Magnetic mounts
for an antenna, a repair order hat, or a funeral pro-
cession flag can exceed the compensating ability of
the compass unit if placed on the roof panel. Mag-
netic bit drivers used on the fasteners that hold the
overhead console assembly to the roof header can
also affect compass operation. If the vehicle roof
should become magnetized, the demagnetizing and
calibration procedures found in this group may be
required to restore proper compass operation.
TEMPERATURE
The outside ambient temperature is displayed in
whole degrees. The temperature display can be tog-
gled from Fahrenheit to Celsius by selecting the
desired U.S./Metric option from the customer pro-
grammable features as described inELECTRONIC
VEHICLE INFORMATION CENTER PROGRAM-
MINGin the Standard Procedures section of this
group. The displayed temperature is not an instant
reading of conditions, but an average temperature. It
may take the temperature display several minutes to
respond to a major temperature change, such as driv-
ing out of a heated garage into winter temperatures.
When the ignition switch is turned to the Off posi-
tion, the last displayed temperature reading stays in
the Body Control Module (BCM) unit memory. When
the ignition switch is turned to the On position
again, the EVIC will display the memory tempera-
ture for one minute; then update the display to the
current average temperature reading within five
minutes.
The temperature function is supported by an ambi-
ent temperature sensor. The sensor is mounted out-
side the passenger compartment near the front and
center of the vehicle, and is hard wired to the Body
Control Module (BCM). The BCM sends temperature
status messages to the EVIC module over the PCI
data bus network. The ambient temperature sensor
is available as a separate service item.
8M - 8 MESSAGE SYSTEMSWJ
ELECTRONIC VEHICLE INFO CENTER (Continued)
Page 492 of 2199
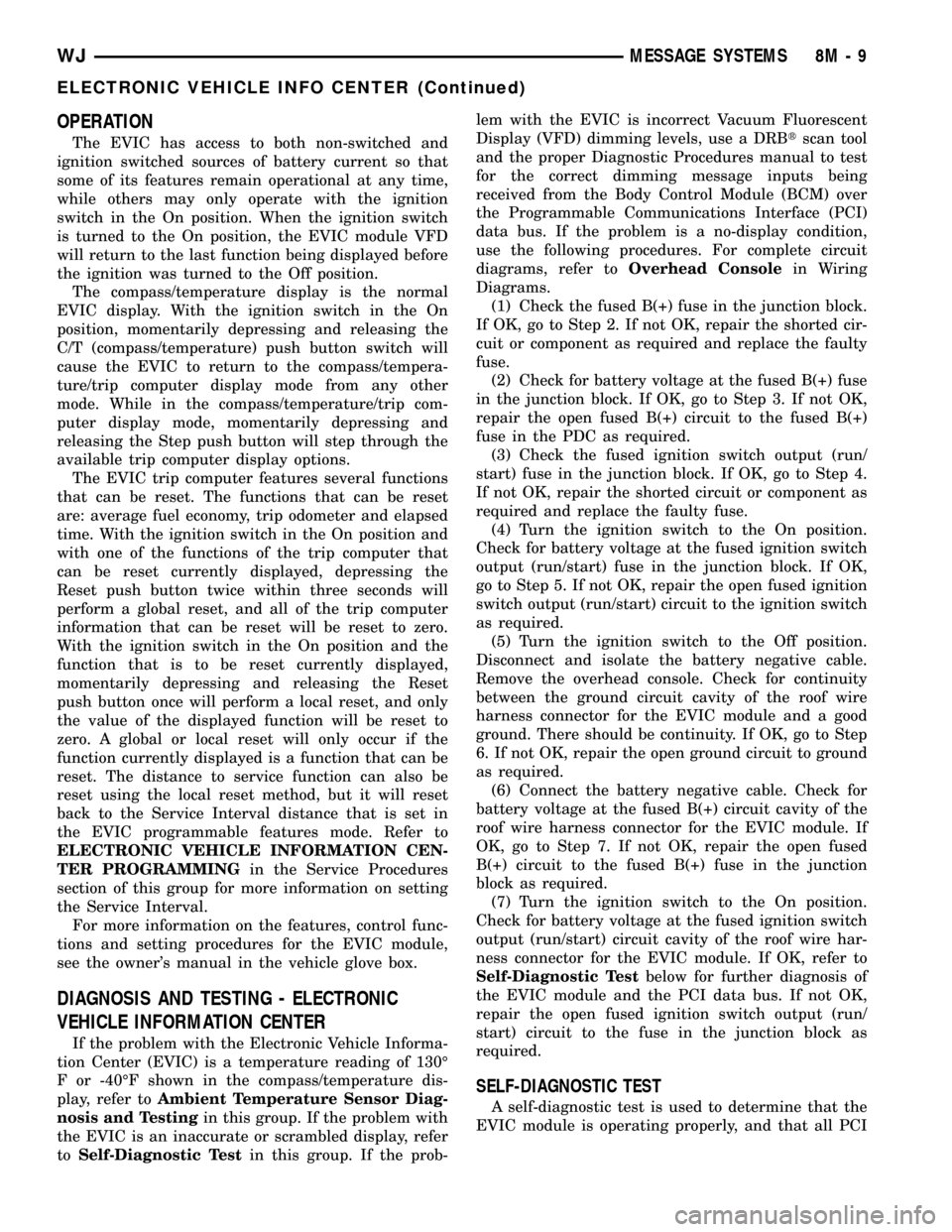
OPERATION
The EVIC has access to both non-switched and
ignition switched sources of battery current so that
some of its features remain operational at any time,
while others may only operate with the ignition
switch in the On position. When the ignition switch
is turned to the On position, the EVIC module VFD
will return to the last function being displayed before
the ignition was turned to the Off position.
The compass/temperature display is the normal
EVIC display. With the ignition switch in the On
position, momentarily depressing and releasing the
C/T (compass/temperature) push button switch will
cause the EVIC to return to the compass/tempera-
ture/trip computer display mode from any other
mode. While in the compass/temperature/trip com-
puter display mode, momentarily depressing and
releasing the Step push button will step through the
available trip computer display options.
The EVIC trip computer features several functions
that can be reset. The functions that can be reset
are: average fuel economy, trip odometer and elapsed
time. With the ignition switch in the On position and
with one of the functions of the trip computer that
can be reset currently displayed, depressing the
Reset push button twice within three seconds will
perform a global reset, and all of the trip computer
information that can be reset will be reset to zero.
With the ignition switch in the On position and the
function that is to be reset currently displayed,
momentarily depressing and releasing the Reset
push button once will perform a local reset, and only
the value of the displayed function will be reset to
zero. A global or local reset will only occur if the
function currently displayed is a function that can be
reset. The distance to service function can also be
reset using the local reset method, but it will reset
back to the Service Interval distance that is set in
the EVIC programmable features mode. Refer to
ELECTRONIC VEHICLE INFORMATION CEN-
TER PROGRAMMINGin the Service Procedures
section of this group for more information on setting
the Service Interval.
For more information on the features, control func-
tions and setting procedures for the EVIC module,
see the owner's manual in the vehicle glove box.
DIAGNOSIS AND TESTING - ELECTRONIC
VEHICLE INFORMATION CENTER
If the problem with the Electronic Vehicle Informa-
tion Center (EVIC) is a temperature reading of 130É
F or -40ÉF shown in the compass/temperature dis-
play, refer toAmbient Temperature Sensor Diag-
nosis and Testingin this group. If the problem with
the EVIC is an inaccurate or scrambled display, refer
toSelf-Diagnostic Testin this group. If the prob-lem with the EVIC is incorrect Vacuum Fluorescent
Display (VFD) dimming levels, use a DRBtscan tool
and the proper Diagnostic Procedures manual to test
for the correct dimming message inputs being
received from the Body Control Module (BCM) over
the Programmable Communications Interface (PCI)
data bus. If the problem is a no-display condition,
use the following procedures. For complete circuit
diagrams, refer toOverhead Consolein Wiring
Diagrams.
(1) Check the fused B(+) fuse in the junction block.
If OK, go to Step 2. If not OK, repair the shorted cir-
cuit or component as required and replace the faulty
fuse.
(2) Check for battery voltage at the fused B(+) fuse
in the junction block. If OK, go to Step 3. If not OK,
repair the open fused B(+) circuit to the fused B(+)
fuse in the PDC as required.
(3) Check the fused ignition switch output (run/
start) fuse in the junction block. If OK, go to Step 4.
If not OK, repair the shorted circuit or component as
required and replace the faulty fuse.
(4) Turn the ignition switch to the On position.
Check for battery voltage at the fused ignition switch
output (run/start) fuse in the junction block. If OK,
go to Step 5. If not OK, repair the open fused ignition
switch output (run/start) circuit to the ignition switch
as required.
(5) Turn the ignition switch to the Off position.
Disconnect and isolate the battery negative cable.
Remove the overhead console. Check for continuity
between the ground circuit cavity of the roof wire
harness connector for the EVIC module and a good
ground. There should be continuity. If OK, go to Step
6. If not OK, repair the open ground circuit to ground
as required.
(6) Connect the battery negative cable. Check for
battery voltage at the fused B(+) circuit cavity of the
roof wire harness connector for the EVIC module. If
OK, go to Step 7. If not OK, repair the open fused
B(+) circuit to the fused B(+) fuse in the junction
block as required.
(7) Turn the ignition switch to the On position.
Check for battery voltage at the fused ignition switch
output (run/start) circuit cavity of the roof wire har-
ness connector for the EVIC module. If OK, refer to
Self-Diagnostic Testbelow for further diagnosis of
the EVIC module and the PCI data bus. If not OK,
repair the open fused ignition switch output (run/
start) circuit to the fuse in the junction block as
required.
SELF-DIAGNOSTIC TEST
A self-diagnostic test is used to determine that the
EVIC module is operating properly, and that all PCI
WJMESSAGE SYSTEMS 8M - 9
ELECTRONIC VEHICLE INFO CENTER (Continued)
Page 493 of 2199
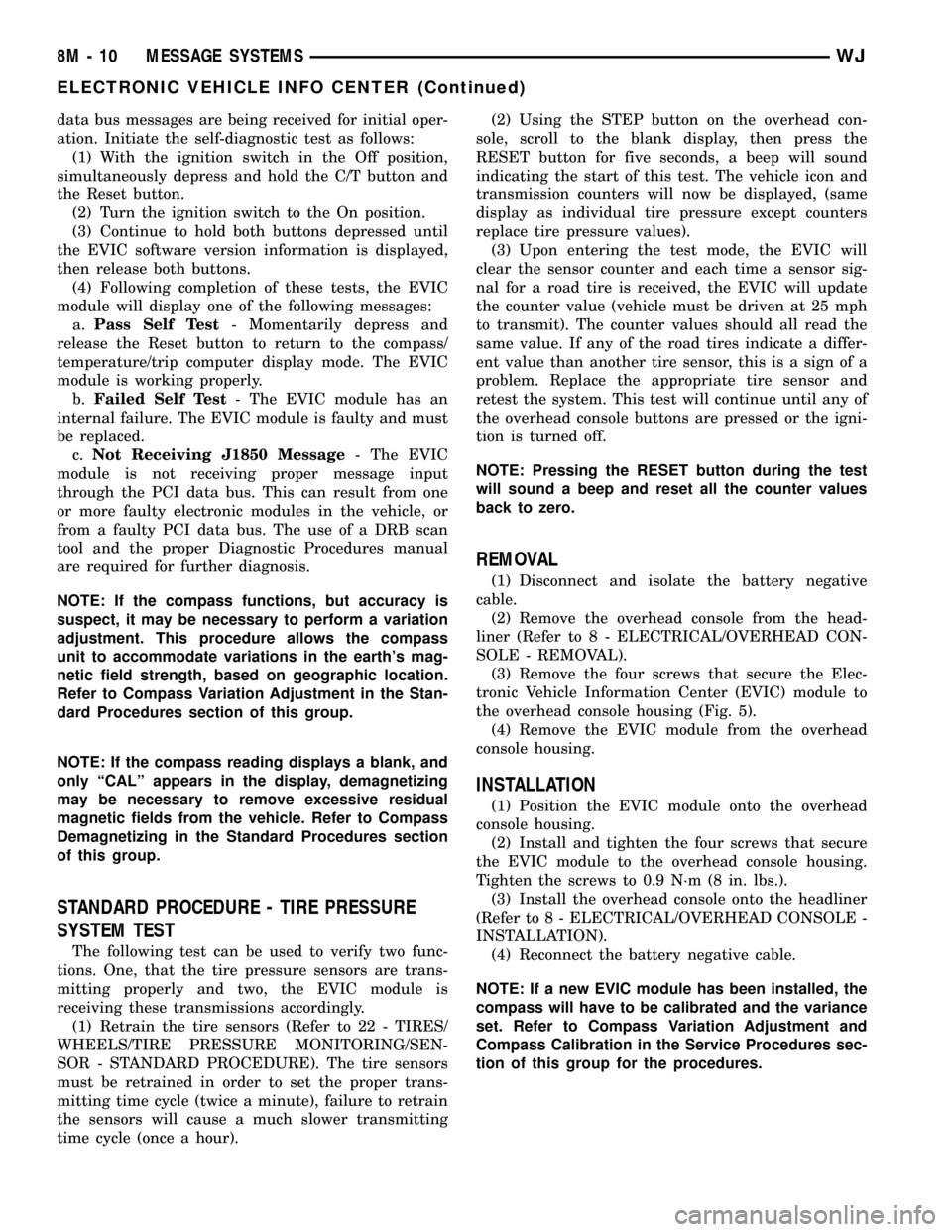
data bus messages are being received for initial oper-
ation. Initiate the self-diagnostic test as follows:
(1) With the ignition switch in the Off position,
simultaneously depress and hold the C/T button and
the Reset button.
(2) Turn the ignition switch to the On position.
(3) Continue to hold both buttons depressed until
the EVIC software version information is displayed,
then release both buttons.
(4) Following completion of these tests, the EVIC
module will display one of the following messages:
a.Pass Self Test- Momentarily depress and
release the Reset button to return to the compass/
temperature/trip computer display mode. The EVIC
module is working properly.
b.Failed Self Test- The EVIC module has an
internal failure. The EVIC module is faulty and must
be replaced.
c.Not Receiving J1850 Message- The EVIC
module is not receiving proper message input
through the PCI data bus. This can result from one
or more faulty electronic modules in the vehicle, or
from a faulty PCI data bus. The use of a DRB scan
tool and the proper Diagnostic Procedures manual
are required for further diagnosis.
NOTE: If the compass functions, but accuracy is
suspect, it may be necessary to perform a variation
adjustment. This procedure allows the compass
unit to accommodate variations in the earth's mag-
netic field strength, based on geographic location.
Refer to Compass Variation Adjustment in the Stan-
dard Procedures section of this group.
NOTE: If the compass reading displays a blank, and
only ªCALº appears in the display, demagnetizing
may be necessary to remove excessive residual
magnetic fields from the vehicle. Refer to Compass
Demagnetizing in the Standard Procedures section
of this group.
STANDARD PROCEDURE - TIRE PRESSURE
SYSTEM TEST
The following test can be used to verify two func-
tions. One, that the tire pressure sensors are trans-
mitting properly and two, the EVIC module is
receiving these transmissions accordingly.
(1) Retrain the tire sensors (Refer to 22 - TIRES/
WHEELS/TIRE PRESSURE MONITORING/SEN-
SOR - STANDARD PROCEDURE). The tire sensors
must be retrained in order to set the proper trans-
mitting time cycle (twice a minute), failure to retrain
the sensors will cause a much slower transmitting
time cycle (once a hour).(2) Using the STEP button on the overhead con-
sole, scroll to the blank display, then press the
RESET button for five seconds, a beep will sound
indicating the start of this test. The vehicle icon and
transmission counters will now be displayed, (same
display as individual tire pressure except counters
replace tire pressure values).
(3) Upon entering the test mode, the EVIC will
clear the sensor counter and each time a sensor sig-
nal for a road tire is received, the EVIC will update
the counter value (vehicle must be driven at 25 mph
to transmit). The counter values should all read the
same value. If any of the road tires indicate a differ-
ent value than another tire sensor, this is a sign of a
problem. Replace the appropriate tire sensor and
retest the system. This test will continue until any of
the overhead console buttons are pressed or the igni-
tion is turned off.
NOTE: Pressing the RESET button during the test
will sound a beep and reset all the counter values
back to zero.
REMOVAL
(1) Disconnect and isolate the battery negative
cable.
(2) Remove the overhead console from the head-
liner (Refer to 8 - ELECTRICAL/OVERHEAD CON-
SOLE - REMOVAL).
(3) Remove the four screws that secure the Elec-
tronic Vehicle Information Center (EVIC) module to
the overhead console housing (Fig. 5).
(4) Remove the EVIC module from the overhead
console housing.
INSTALLATION
(1) Position the EVIC module onto the overhead
console housing.
(2) Install and tighten the four screws that secure
the EVIC module to the overhead console housing.
Tighten the screws to 0.9 N´m (8 in. lbs.).
(3) Install the overhead console onto the headliner
(Refer to 8 - ELECTRICAL/OVERHEAD CONSOLE -
INSTALLATION).
(4) Reconnect the battery negative cable.
NOTE: If a new EVIC module has been installed, the
compass will have to be calibrated and the variance
set. Refer to Compass Variation Adjustment and
Compass Calibration in the Service Procedures sec-
tion of this group for the procedures.
8M - 10 MESSAGE SYSTEMSWJ
ELECTRONIC VEHICLE INFO CENTER (Continued)
Page 494 of 2199
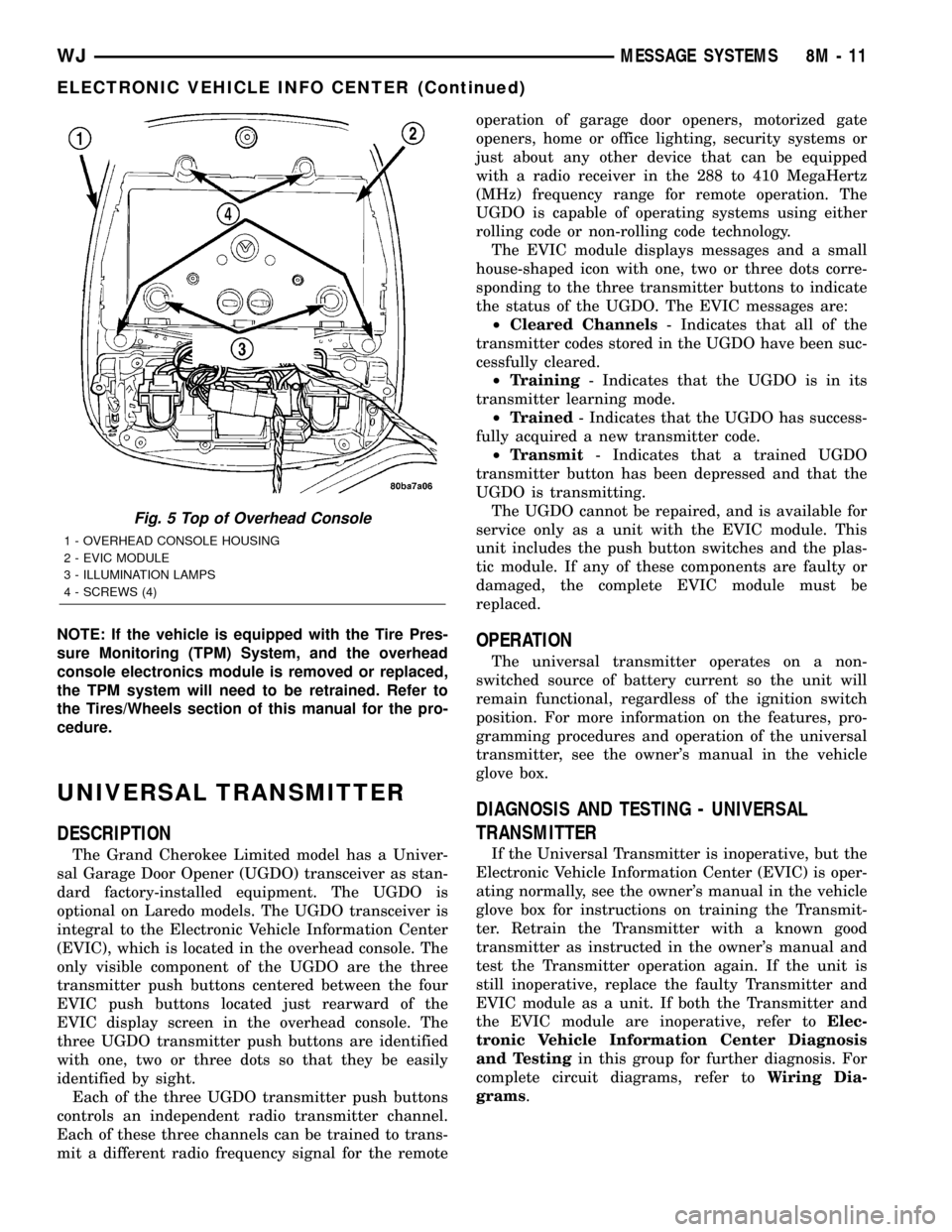
NOTE: If the vehicle is equipped with the Tire Pres-
sure Monitoring (TPM) System, and the overhead
console electronics module is removed or replaced,
the TPM system will need to be retrained. Refer to
the Tires/Wheels section of this manual for the pro-
cedure.
UNIVERSAL TRANSMITTER
DESCRIPTION
The Grand Cherokee Limited model has a Univer-
sal Garage Door Opener (UGDO) transceiver as stan-
dard factory-installed equipment. The UGDO is
optional on Laredo models. The UGDO transceiver is
integral to the Electronic Vehicle Information Center
(EVIC), which is located in the overhead console. The
only visible component of the UGDO are the three
transmitter push buttons centered between the four
EVIC push buttons located just rearward of the
EVIC display screen in the overhead console. The
three UGDO transmitter push buttons are identified
with one, two or three dots so that they be easily
identified by sight.
Each of the three UGDO transmitter push buttons
controls an independent radio transmitter channel.
Each of these three channels can be trained to trans-
mit a different radio frequency signal for the remoteoperation of garage door openers, motorized gate
openers, home or office lighting, security systems or
just about any other device that can be equipped
with a radio receiver in the 288 to 410 MegaHertz
(MHz) frequency range for remote operation. The
UGDO is capable of operating systems using either
rolling code or non-rolling code technology.
The EVIC module displays messages and a small
house-shaped icon with one, two or three dots corre-
sponding to the three transmitter buttons to indicate
the status of the UGDO. The EVIC messages are:
²Cleared Channels- Indicates that all of the
transmitter codes stored in the UGDO have been suc-
cessfully cleared.
²Training- Indicates that the UGDO is in its
transmitter learning mode.
²Trained- Indicates that the UGDO has success-
fully acquired a new transmitter code.
²Transmit- Indicates that a trained UGDO
transmitter button has been depressed and that the
UGDO is transmitting.
The UGDO cannot be repaired, and is available for
service only as a unit with the EVIC module. This
unit includes the push button switches and the plas-
tic module. If any of these components are faulty or
damaged, the complete EVIC module must be
replaced.
OPERATION
The universal transmitter operates on a non-
switched source of battery current so the unit will
remain functional, regardless of the ignition switch
position. For more information on the features, pro-
gramming procedures and operation of the universal
transmitter, see the owner's manual in the vehicle
glove box.
DIAGNOSIS AND TESTING - UNIVERSAL
TRANSMITTER
If the Universal Transmitter is inoperative, but the
Electronic Vehicle Information Center (EVIC) is oper-
ating normally, see the owner's manual in the vehicle
glove box for instructions on training the Transmit-
ter. Retrain the Transmitter with a known good
transmitter as instructed in the owner's manual and
test the Transmitter operation again. If the unit is
still inoperative, replace the faulty Transmitter and
EVIC module as a unit. If both the Transmitter and
the EVIC module are inoperative, refer toElec-
tronic Vehicle Information Center Diagnosis
and Testingin this group for further diagnosis. For
complete circuit diagrams, refer toWiring Dia-
grams.
Fig. 5 Top of Overhead Console
1 - OVERHEAD CONSOLE HOUSING
2 - EVIC MODULE
3 - ILLUMINATION LAMPS
4 - SCREWS (4)
WJMESSAGE SYSTEMS 8M - 11
ELECTRONIC VEHICLE INFO CENTER (Continued)
Page 495 of 2199
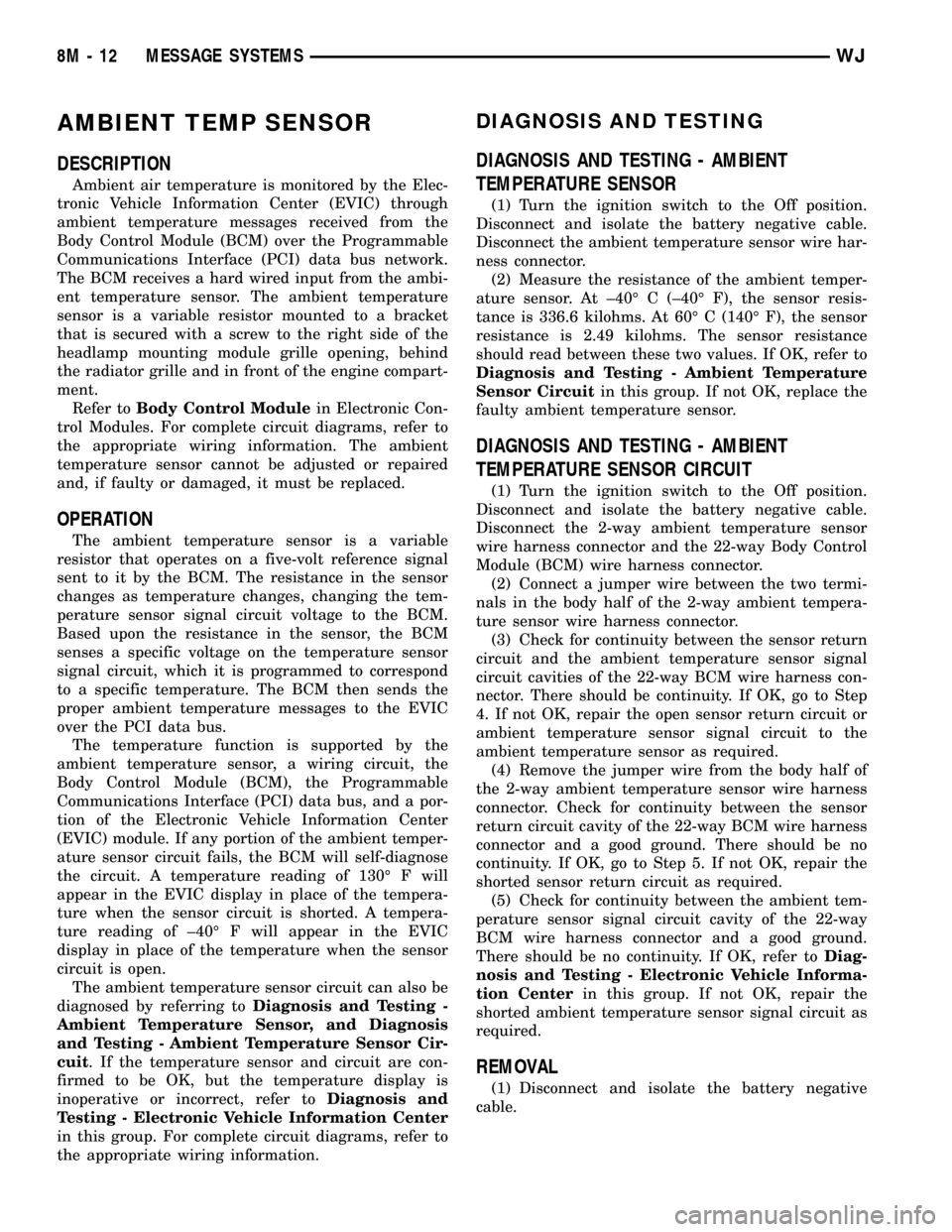
AMBIENT TEMP SENSOR
DESCRIPTION
Ambient air temperature is monitored by the Elec-
tronic Vehicle Information Center (EVIC) through
ambient temperature messages received from the
Body Control Module (BCM) over the Programmable
Communications Interface (PCI) data bus network.
The BCM receives a hard wired input from the ambi-
ent temperature sensor. The ambient temperature
sensor is a variable resistor mounted to a bracket
that is secured with a screw to the right side of the
headlamp mounting module grille opening, behind
the radiator grille and in front of the engine compart-
ment.
Refer toBody Control Modulein Electronic Con-
trol Modules. For complete circuit diagrams, refer to
the appropriate wiring information. The ambient
temperature sensor cannot be adjusted or repaired
and, if faulty or damaged, it must be replaced.
OPERATION
The ambient temperature sensor is a variable
resistor that operates on a five-volt reference signal
sent to it by the BCM. The resistance in the sensor
changes as temperature changes, changing the tem-
perature sensor signal circuit voltage to the BCM.
Based upon the resistance in the sensor, the BCM
senses a specific voltage on the temperature sensor
signal circuit, which it is programmed to correspond
to a specific temperature. The BCM then sends the
proper ambient temperature messages to the EVIC
over the PCI data bus.
The temperature function is supported by the
ambient temperature sensor, a wiring circuit, the
Body Control Module (BCM), the Programmable
Communications Interface (PCI) data bus, and a por-
tion of the Electronic Vehicle Information Center
(EVIC) module. If any portion of the ambient temper-
ature sensor circuit fails, the BCM will self-diagnose
the circuit. A temperature reading of 130É F will
appear in the EVIC display in place of the tempera-
ture when the sensor circuit is shorted. A tempera-
ture reading of ±40É F will appear in the EVIC
display in place of the temperature when the sensor
circuit is open.
The ambient temperature sensor circuit can also be
diagnosed by referring toDiagnosis and Testing -
Ambient Temperature Sensor, and Diagnosis
and Testing - Ambient Temperature Sensor Cir-
cuit. If the temperature sensor and circuit are con-
firmed to be OK, but the temperature display is
inoperative or incorrect, refer toDiagnosis and
Testing - Electronic Vehicle Information Center
in this group. For complete circuit diagrams, refer to
the appropriate wiring information.
DIAGNOSIS AND TESTING
DIAGNOSIS AND TESTING - AMBIENT
TEMPERATURE SENSOR
(1) Turn the ignition switch to the Off position.
Disconnect and isolate the battery negative cable.
Disconnect the ambient temperature sensor wire har-
ness connector.
(2) Measure the resistance of the ambient temper-
ature sensor. At ±40É C (±40É F), the sensor resis-
tance is 336.6 kilohms. At 60É C (140É F), the sensor
resistance is 2.49 kilohms. The sensor resistance
should read between these two values. If OK, refer to
Diagnosis and Testing - Ambient Temperature
Sensor Circuitin this group. If not OK, replace the
faulty ambient temperature sensor.
DIAGNOSIS AND TESTING - AMBIENT
TEMPERATURE SENSOR CIRCUIT
(1) Turn the ignition switch to the Off position.
Disconnect and isolate the battery negative cable.
Disconnect the 2-way ambient temperature sensor
wire harness connector and the 22-way Body Control
Module (BCM) wire harness connector.
(2) Connect a jumper wire between the two termi-
nals in the body half of the 2-way ambient tempera-
ture sensor wire harness connector.
(3) Check for continuity between the sensor return
circuit and the ambient temperature sensor signal
circuit cavities of the 22-way BCM wire harness con-
nector. There should be continuity. If OK, go to Step
4. If not OK, repair the open sensor return circuit or
ambient temperature sensor signal circuit to the
ambient temperature sensor as required.
(4) Remove the jumper wire from the body half of
the 2-way ambient temperature sensor wire harness
connector. Check for continuity between the sensor
return circuit cavity of the 22-way BCM wire harness
connector and a good ground. There should be no
continuity. If OK, go to Step 5. If not OK, repair the
shorted sensor return circuit as required.
(5) Check for continuity between the ambient tem-
perature sensor signal circuit cavity of the 22-way
BCM wire harness connector and a good ground.
There should be no continuity. If OK, refer toDiag-
nosis and Testing - Electronic Vehicle Informa-
tion Centerin this group. If not OK, repair the
shorted ambient temperature sensor signal circuit as
required.
REMOVAL
(1) Disconnect and isolate the battery negative
cable.
8M - 12 MESSAGE SYSTEMSWJ
Page 517 of 2199
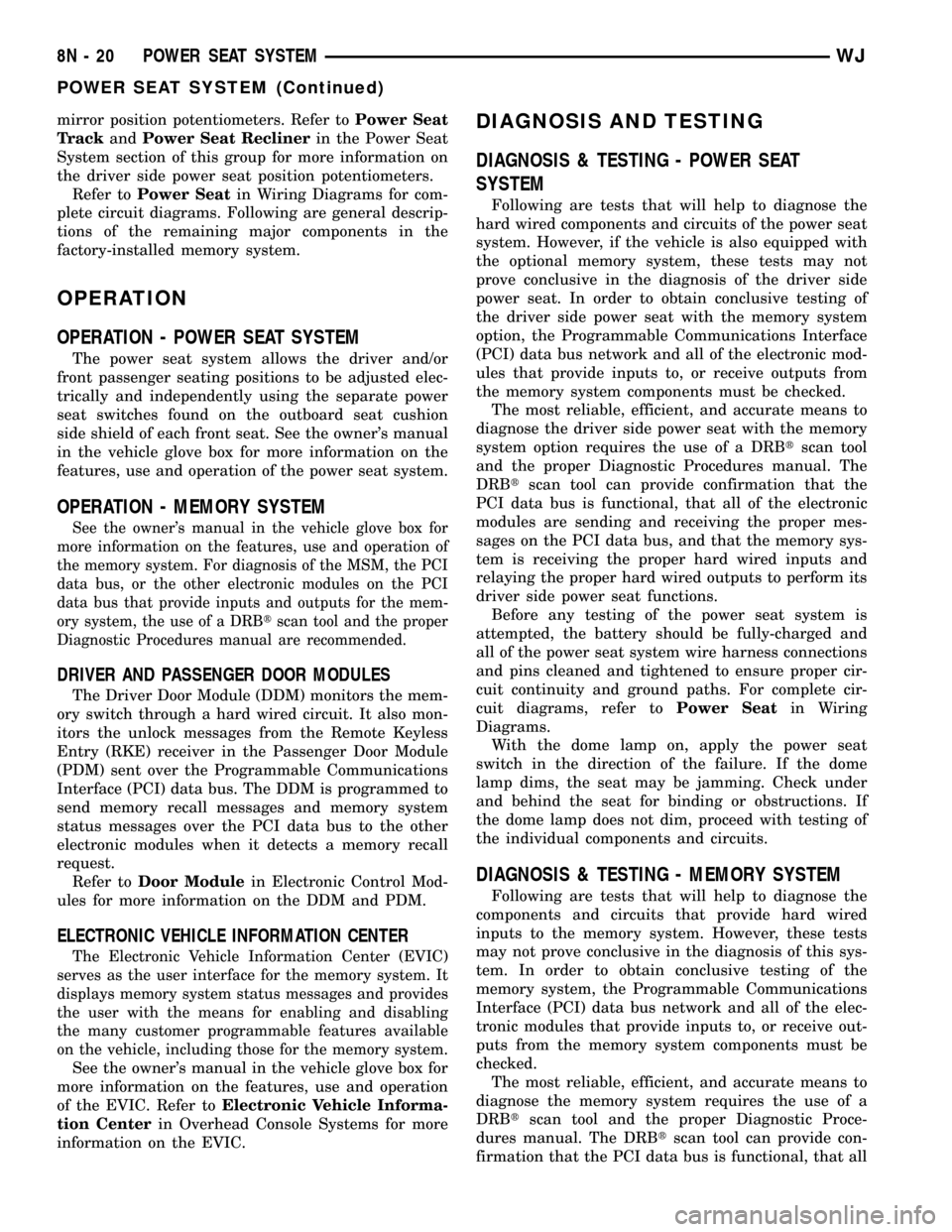
mirror position potentiometers. Refer toPower Seat
TrackandPower Seat Reclinerin the Power Seat
System section of this group for more information on
the driver side power seat position potentiometers.
Refer toPower Seatin Wiring Diagrams for com-
plete circuit diagrams. Following are general descrip-
tions of the remaining major components in the
factory-installed memory system.
OPERATION
OPERATION - POWER SEAT SYSTEM
The power seat system allows the driver and/or
front passenger seating positions to be adjusted elec-
trically and independently using the separate power
seat switches found on the outboard seat cushion
side shield of each front seat. See the owner's manual
in the vehicle glove box for more information on the
features, use and operation of the power seat system.
OPERATION - MEMORY SYSTEM
See the owner's manual in the vehicle glove box for
more information on the features, use and operation of
the memory system. For diagnosis of the MSM, the PCI
data bus, or the other electronic modules on the PCI
data bus that provide inputs and outputs for the mem-
ory system, the use of a DRBtscan tool and the proper
Diagnostic Procedures manual are recommended.
DRIVER AND PASSENGER DOOR MODULES
The Driver Door Module (DDM) monitors the mem-
ory switch through a hard wired circuit. It also mon-
itors the unlock messages from the Remote Keyless
Entry (RKE) receiver in the Passenger Door Module
(PDM) sent over the Programmable Communications
Interface (PCI) data bus. The DDM is programmed to
send memory recall messages and memory system
status messages over the PCI data bus to the other
electronic modules when it detects a memory recall
request.
Refer toDoor Modulein Electronic Control Mod-
ules for more information on the DDM and PDM.
ELECTRONIC VEHICLE INFORMATION CENTER
The Electronic Vehicle Information Center (EVIC)
serves as the user interface for the memory system. It
displays memory system status messages and provides
the user with the means for enabling and disabling
the many customer programmable features available
on the vehicle, including those for the memory system.
See the owner's manual in the vehicle glove box for
more information on the features, use and operation
of the EVIC. Refer toElectronic Vehicle Informa-
tion Centerin Overhead Console Systems for more
information on the EVIC.
DIAGNOSIS AND TESTING
DIAGNOSIS & TESTING - POWER SEAT
SYSTEM
Following are tests that will help to diagnose the
hard wired components and circuits of the power seat
system. However, if the vehicle is also equipped with
the optional memory system, these tests may not
prove conclusive in the diagnosis of the driver side
power seat. In order to obtain conclusive testing of
the driver side power seat with the memory system
option, the Programmable Communications Interface
(PCI) data bus network and all of the electronic mod-
ules that provide inputs to, or receive outputs from
the memory system components must be checked.
The most reliable, efficient, and accurate means to
diagnose the driver side power seat with the memory
system option requires the use of a DRBtscan tool
and the proper Diagnostic Procedures manual. The
DRBtscan tool can provide confirmation that the
PCI data bus is functional, that all of the electronic
modules are sending and receiving the proper mes-
sages on the PCI data bus, and that the memory sys-
tem is receiving the proper hard wired inputs and
relaying the proper hard wired outputs to perform its
driver side power seat functions.
Before any testing of the power seat system is
attempted, the battery should be fully-charged and
all of the power seat system wire harness connections
and pins cleaned and tightened to ensure proper cir-
cuit continuity and ground paths. For complete cir-
cuit diagrams, refer toPower Seatin Wiring
Diagrams.
With the dome lamp on, apply the power seat
switch in the direction of the failure. If the dome
lamp dims, the seat may be jamming. Check under
and behind the seat for binding or obstructions. If
the dome lamp does not dim, proceed with testing of
the individual components and circuits.
DIAGNOSIS & TESTING - MEMORY SYSTEM
Following are tests that will help to diagnose the
components and circuits that provide hard wired
inputs to the memory system. However, these tests
may not prove conclusive in the diagnosis of this sys-
tem. In order to obtain conclusive testing of the
memory system, the Programmable Communications
Interface (PCI) data bus network and all of the elec-
tronic modules that provide inputs to, or receive out-
puts from the memory system components must be
checked.
The most reliable, efficient, and accurate means to
diagnose the memory system requires the use of a
DRBtscan tool and the proper Diagnostic Proce-
dures manual. The DRBtscan tool can provide con-
firmation that the PCI data bus is functional, that all
8N - 20 POWER SEAT SYSTEMWJ
POWER SEAT SYSTEM (Continued)
Page 587 of 2199
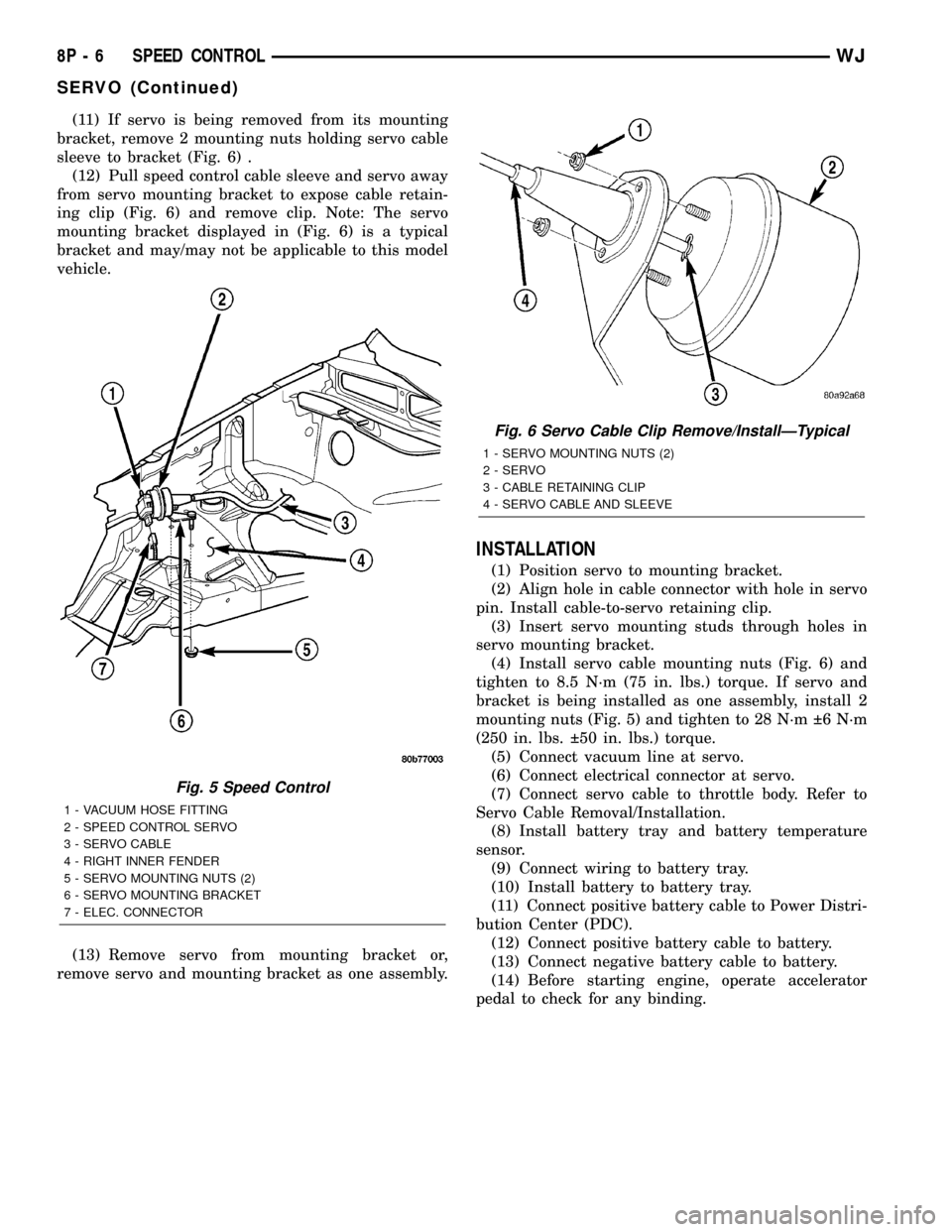
(11) If servo is being removed from its mounting
bracket, remove 2 mounting nuts holding servo cable
sleeve to bracket (Fig. 6) .
(12) Pull speed control cable sleeve and servo away
from servo mounting bracket to expose cable retain-
ing clip (Fig. 6) and remove clip. Note: The servo
mounting bracket displayed in (Fig. 6) is a typical
bracket and may/may not be applicable to this model
vehicle.
(13) Remove servo from mounting bracket or,
remove servo and mounting bracket as one assembly.
INSTALLATION
(1) Position servo to mounting bracket.
(2) Align hole in cable connector with hole in servo
pin. Install cable-to-servo retaining clip.
(3) Insert servo mounting studs through holes in
servo mounting bracket.
(4) Install servo cable mounting nuts (Fig. 6) and
tighten to 8.5 N´m (75 in. lbs.) torque. If servo and
bracket is being installed as one assembly, install 2
mounting nuts (Fig. 5) and tighten to 28 N´m 6 N´m
(250 in. lbs. 50 in. lbs.) torque.
(5) Connect vacuum line at servo.
(6) Connect electrical connector at servo.
(7) Connect servo cable to throttle body. Refer to
Servo Cable Removal/Installation.
(8) Install battery tray and battery temperature
sensor.
(9) Connect wiring to battery tray.
(10) Install battery to battery tray.
(11) Connect positive battery cable to Power Distri-
bution Center (PDC).
(12) Connect positive battery cable to battery.
(13) Connect negative battery cable to battery.
(14) Before starting engine, operate accelerator
pedal to check for any binding.
Fig. 5 Speed Control
1 - VACUUM HOSE FITTING
2 - SPEED CONTROL SERVO
3 - SERVO CABLE
4 - RIGHT INNER FENDER
5 - SERVO MOUNTING NUTS (2)
6 - SERVO MOUNTING BRACKET
7 - ELEC. CONNECTOR
Fig. 6 Servo Cable Clip Remove/InstallÐTypical
1 - SERVO MOUNTING NUTS (2)
2 - SERVO
3 - CABLE RETAINING CLIP
4 - SERVO CABLE AND SLEEVE
8P - 6 SPEED CONTROLWJ
SERVO (Continued)
Page 627 of 2199
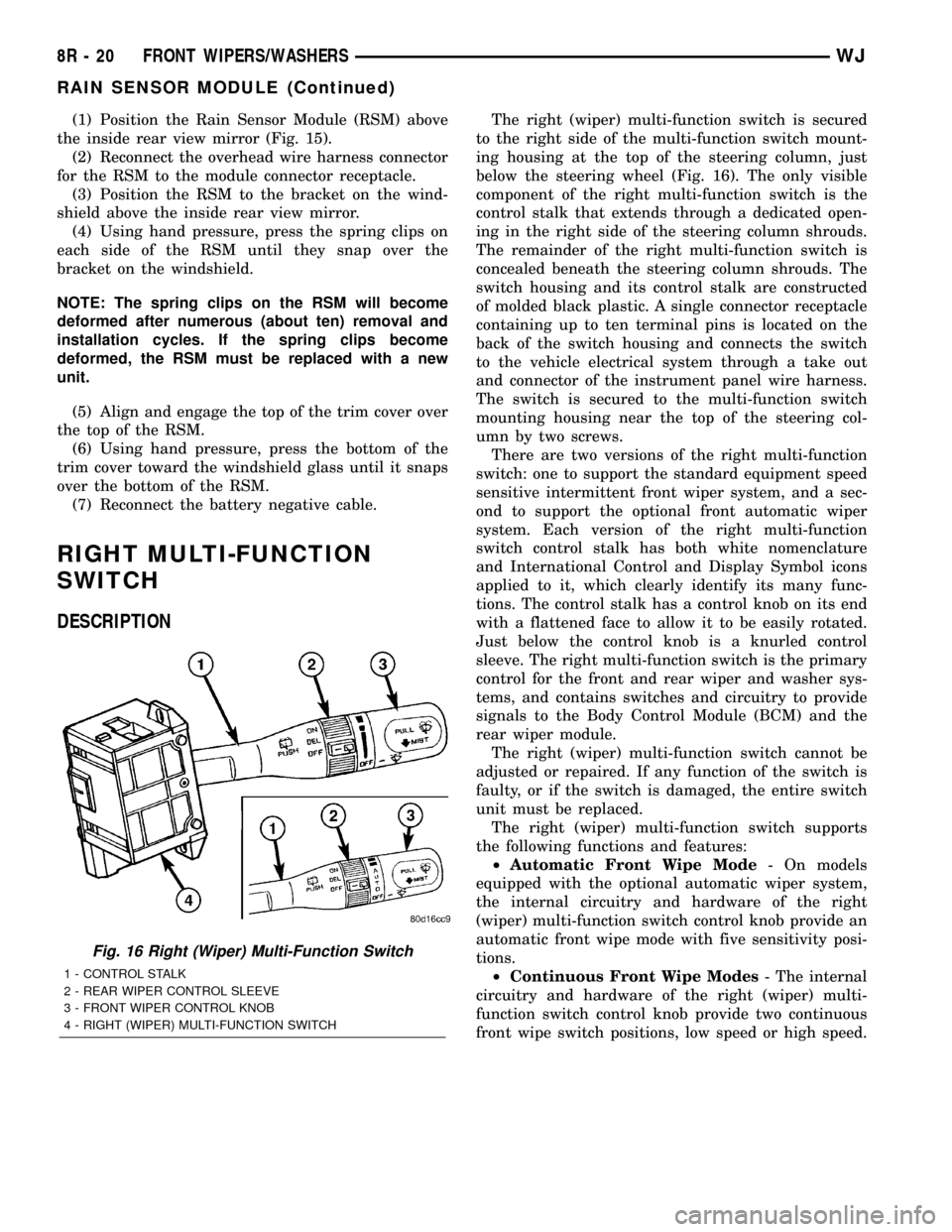
(1) Position the Rain Sensor Module (RSM) above
the inside rear view mirror (Fig. 15).
(2) Reconnect the overhead wire harness connector
for the RSM to the module connector receptacle.
(3) Position the RSM to the bracket on the wind-
shield above the inside rear view mirror.
(4) Using hand pressure, press the spring clips on
each side of the RSM until they snap over the
bracket on the windshield.
NOTE: The spring clips on the RSM will become
deformed after numerous (about ten) removal and
installation cycles. If the spring clips become
deformed, the RSM must be replaced with a new
unit.
(5) Align and engage the top of the trim cover over
the top of the RSM.
(6) Using hand pressure, press the bottom of the
trim cover toward the windshield glass until it snaps
over the bottom of the RSM.
(7) Reconnect the battery negative cable.
RIGHT MULTI-FUNCTION
SWITCH
DESCRIPTION
The right (wiper) multi-function switch is secured
to the right side of the multi-function switch mount-
ing housing at the top of the steering column, just
below the steering wheel (Fig. 16). The only visible
component of the right multi-function switch is the
control stalk that extends through a dedicated open-
ing in the right side of the steering column shrouds.
The remainder of the right multi-function switch is
concealed beneath the steering column shrouds. The
switch housing and its control stalk are constructed
of molded black plastic. A single connector receptacle
containing up to ten terminal pins is located on the
back of the switch housing and connects the switch
to the vehicle electrical system through a take out
and connector of the instrument panel wire harness.
The switch is secured to the multi-function switch
mounting housing near the top of the steering col-
umn by two screws.
There are two versions of the right multi-function
switch: one to support the standard equipment speed
sensitive intermittent front wiper system, and a sec-
ond to support the optional front automatic wiper
system. Each version of the right multi-function
switch control stalk has both white nomenclature
and International Control and Display Symbol icons
applied to it, which clearly identify its many func-
tions. The control stalk has a control knob on its end
with a flattened face to allow it to be easily rotated.
Just below the control knob is a knurled control
sleeve. The right multi-function switch is the primary
control for the front and rear wiper and washer sys-
tems, and contains switches and circuitry to provide
signals to the Body Control Module (BCM) and the
rear wiper module.
The right (wiper) multi-function switch cannot be
adjusted or repaired. If any function of the switch is
faulty, or if the switch is damaged, the entire switch
unit must be replaced.
The right (wiper) multi-function switch supports
the following functions and features:
²Automatic Front Wipe Mode- On models
equipped with the optional automatic wiper system,
the internal circuitry and hardware of the right
(wiper) multi-function switch control knob provide an
automatic front wipe mode with five sensitivity posi-
tions.
²Continuous Front Wipe Modes- The internal
circuitry and hardware of the right (wiper) multi-
function switch control knob provide two continuous
front wipe switch positions, low speed or high speed.
Fig. 16 Right (Wiper) Multi-Function Switch
1 - CONTROL STALK
2 - REAR WIPER CONTROL SLEEVE
3 - FRONT WIPER CONTROL KNOB
4 - RIGHT (WIPER) MULTI-FUNCTION SWITCH
8R - 20 FRONT WIPERS/WASHERSWJ
RAIN SENSOR MODULE (Continued)
Page 632 of 2199
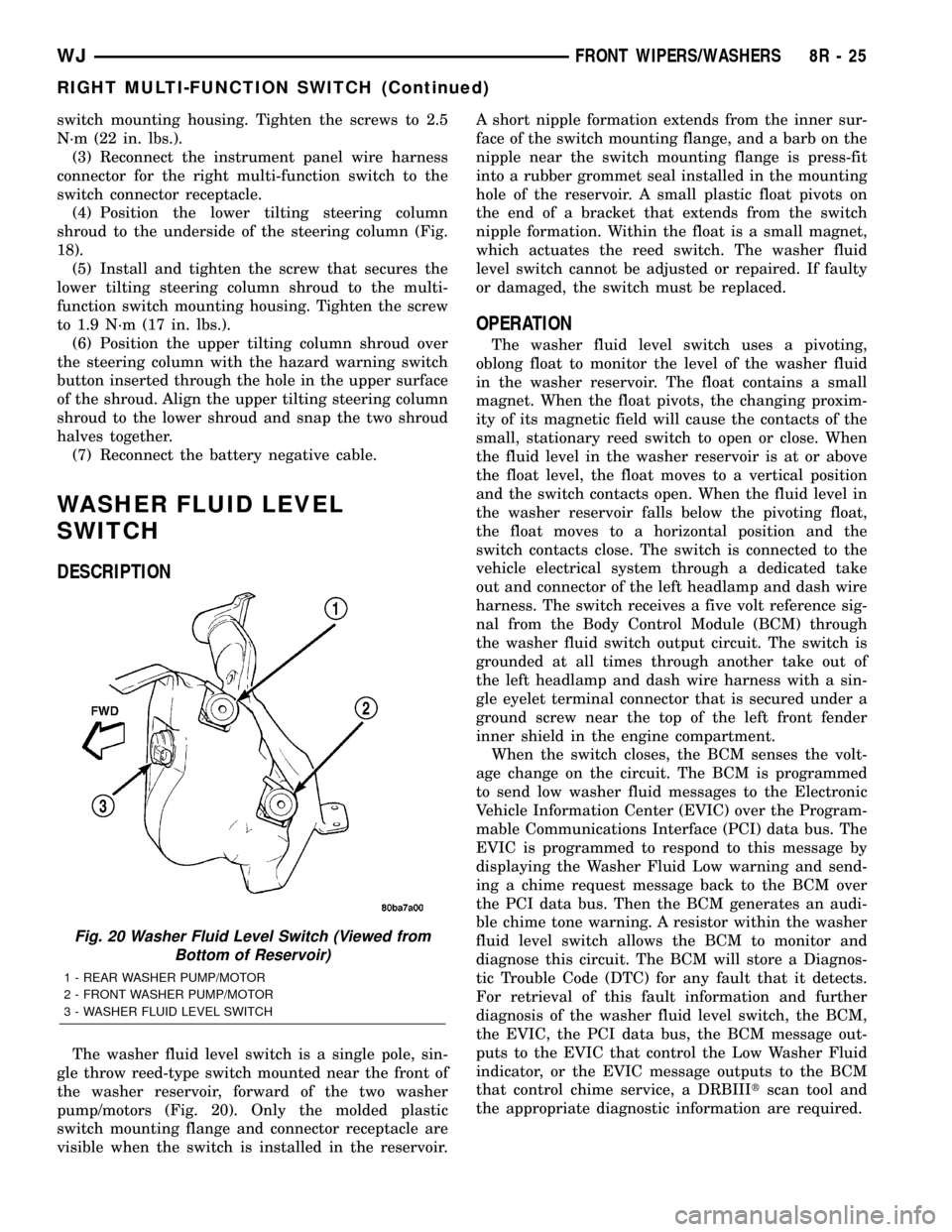
switch mounting housing. Tighten the screws to 2.5
N´m (22 in. lbs.).
(3) Reconnect the instrument panel wire harness
connector for the right multi-function switch to the
switch connector receptacle.
(4) Position the lower tilting steering column
shroud to the underside of the steering column (Fig.
18).
(5) Install and tighten the screw that secures the
lower tilting steering column shroud to the multi-
function switch mounting housing. Tighten the screw
to 1.9 N´m (17 in. lbs.).
(6) Position the upper tilting column shroud over
the steering column with the hazard warning switch
button inserted through the hole in the upper surface
of the shroud. Align the upper tilting steering column
shroud to the lower shroud and snap the two shroud
halves together.
(7) Reconnect the battery negative cable.
WASHER FLUID LEVEL
SWITCH
DESCRIPTION
The washer fluid level switch is a single pole, sin-
gle throw reed-type switch mounted near the front of
the washer reservoir, forward of the two washer
pump/motors (Fig. 20). Only the molded plastic
switch mounting flange and connector receptacle are
visible when the switch is installed in the reservoir.A short nipple formation extends from the inner sur-
face of the switch mounting flange, and a barb on the
nipple near the switch mounting flange is press-fit
into a rubber grommet seal installed in the mounting
hole of the reservoir. A small plastic float pivots on
the end of a bracket that extends from the switch
nipple formation. Within the float is a small magnet,
which actuates the reed switch. The washer fluid
level switch cannot be adjusted or repaired. If faulty
or damaged, the switch must be replaced.
OPERATION
The washer fluid level switch uses a pivoting,
oblong float to monitor the level of the washer fluid
in the washer reservoir. The float contains a small
magnet. When the float pivots, the changing proxim-
ity of its magnetic field will cause the contacts of the
small, stationary reed switch to open or close. When
the fluid level in the washer reservoir is at or above
the float level, the float moves to a vertical position
and the switch contacts open. When the fluid level in
the washer reservoir falls below the pivoting float,
the float moves to a horizontal position and the
switch contacts close. The switch is connected to the
vehicle electrical system through a dedicated take
out and connector of the left headlamp and dash wire
harness. The switch receives a five volt reference sig-
nal from the Body Control Module (BCM) through
the washer fluid switch output circuit. The switch is
grounded at all times through another take out of
the left headlamp and dash wire harness with a sin-
gle eyelet terminal connector that is secured under a
ground screw near the top of the left front fender
inner shield in the engine compartment.
When the switch closes, the BCM senses the volt-
age change on the circuit. The BCM is programmed
to send low washer fluid messages to the Electronic
Vehicle Information Center (EVIC) over the Program-
mable Communications Interface (PCI) data bus. The
EVIC is programmed to respond to this message by
displaying the Washer Fluid Low warning and send-
ing a chime request message back to the BCM over
the PCI data bus. Then the BCM generates an audi-
ble chime tone warning. A resistor within the washer
fluid level switch allows the BCM to monitor and
diagnose this circuit. The BCM will store a Diagnos-
tic Trouble Code (DTC) for any fault that it detects.
For retrieval of this fault information and further
diagnosis of the washer fluid level switch, the BCM,
the EVIC, the PCI data bus, the BCM message out-
puts to the EVIC that control the Low Washer Fluid
indicator, or the EVIC message outputs to the BCM
that control chime service, a DRBIIItscan tool and
the appropriate diagnostic information are required.
Fig. 20 Washer Fluid Level Switch (Viewed from
Bottom of Reservoir)
1 - REAR WASHER PUMP/MOTOR
2 - FRONT WASHER PUMP/MOTOR
3 - WASHER FLUID LEVEL SWITCH
WJFRONT WIPERS/WASHERS 8R - 25
RIGHT MULTI-FUNCTION SWITCH (Continued)
Page 634 of 2199
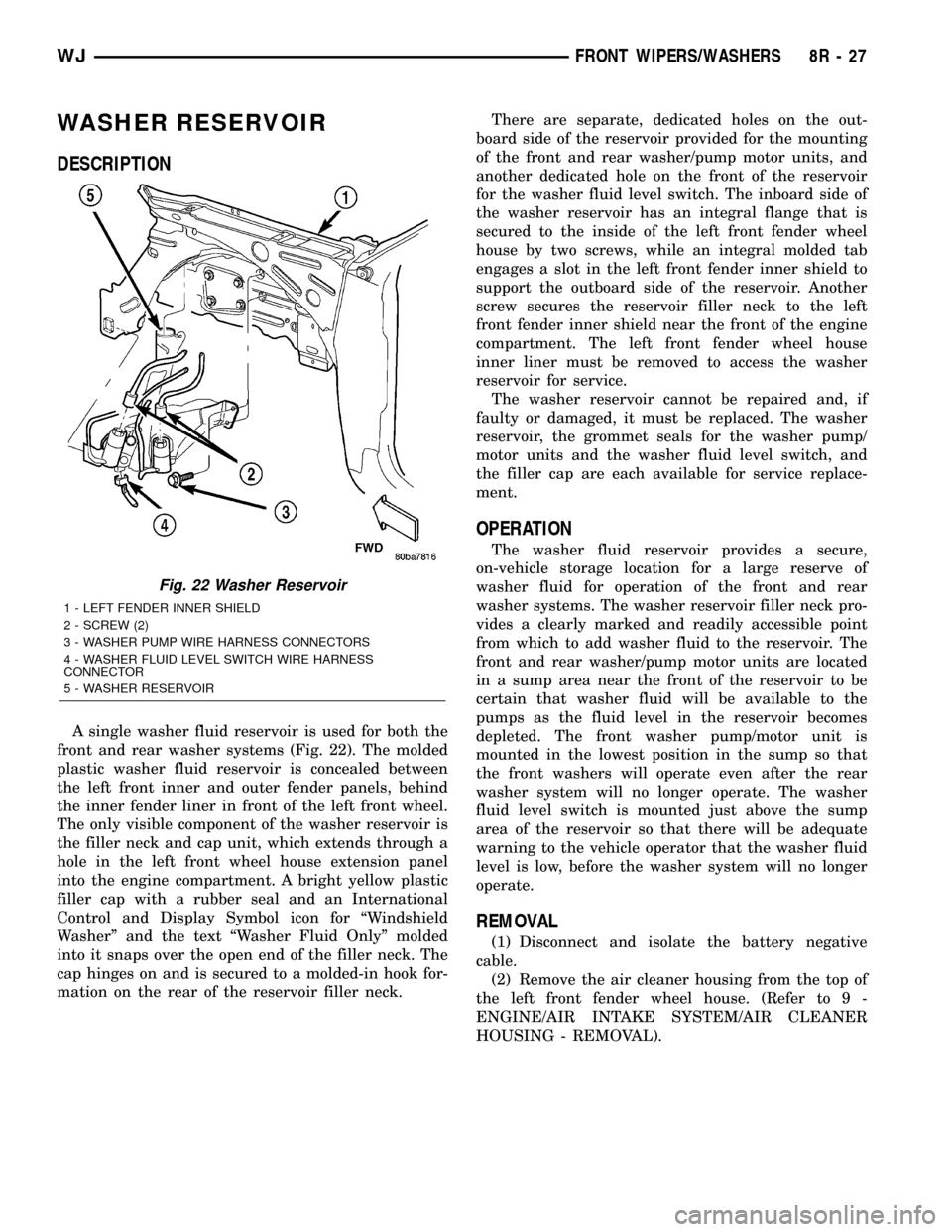
WASHER RESERVOIR
DESCRIPTION
A single washer fluid reservoir is used for both the
front and rear washer systems (Fig. 22). The molded
plastic washer fluid reservoir is concealed between
the left front inner and outer fender panels, behind
the inner fender liner in front of the left front wheel.
The only visible component of the washer reservoir is
the filler neck and cap unit, which extends through a
hole in the left front wheel house extension panel
into the engine compartment. A bright yellow plastic
filler cap with a rubber seal and an International
Control and Display Symbol icon for ªWindshield
Washerº and the text ªWasher Fluid Onlyº molded
into it snaps over the open end of the filler neck. The
cap hinges on and is secured to a molded-in hook for-
mation on the rear of the reservoir filler neck.There are separate, dedicated holes on the out-
board side of the reservoir provided for the mounting
of the front and rear washer/pump motor units, and
another dedicated hole on the front of the reservoir
for the washer fluid level switch. The inboard side of
the washer reservoir has an integral flange that is
secured to the inside of the left front fender wheel
house by two screws, while an integral molded tab
engages a slot in the left front fender inner shield to
support the outboard side of the reservoir. Another
screw secures the reservoir filler neck to the left
front fender inner shield near the front of the engine
compartment. The left front fender wheel house
inner liner must be removed to access the washer
reservoir for service.
The washer reservoir cannot be repaired and, if
faulty or damaged, it must be replaced. The washer
reservoir, the grommet seals for the washer pump/
motor units and the washer fluid level switch, and
the filler cap are each available for service replace-
ment.
OPERATION
The washer fluid reservoir provides a secure,
on-vehicle storage location for a large reserve of
washer fluid for operation of the front and rear
washer systems. The washer reservoir filler neck pro-
vides a clearly marked and readily accessible point
from which to add washer fluid to the reservoir. The
front and rear washer/pump motor units are located
in a sump area near the front of the reservoir to be
certain that washer fluid will be available to the
pumps as the fluid level in the reservoir becomes
depleted. The front washer pump/motor unit is
mounted in the lowest position in the sump so that
the front washers will operate even after the rear
washer system will no longer operate. The washer
fluid level switch is mounted just above the sump
area of the reservoir so that there will be adequate
warning to the vehicle operator that the washer fluid
level is low, before the washer system will no longer
operate.
REMOVAL
(1) Disconnect and isolate the battery negative
cable.
(2) Remove the air cleaner housing from the top of
the left front fender wheel house. (Refer to 9 -
ENGINE/AIR INTAKE SYSTEM/AIR CLEANER
HOUSING - REMOVAL).
Fig. 22 Washer Reservoir
1 - LEFT FENDER INNER SHIELD
2 - SCREW (2)
3 - WASHER PUMP WIRE HARNESS CONNECTORS
4 - WASHER FLUID LEVEL SWITCH WIRE HARNESS
CONNECTOR
5 - WASHER RESERVOIR
WJFRONT WIPERS/WASHERS 8R - 27