Short to ground JEEP GRAND CHEROKEE 2003 WJ / 2.G Repair Manual
[x] Cancel search | Manufacturer: JEEP, Model Year: 2003, Model line: GRAND CHEROKEE, Model: JEEP GRAND CHEROKEE 2003 WJ / 2.GPages: 2199, PDF Size: 76.01 MB
Page 531 of 2199
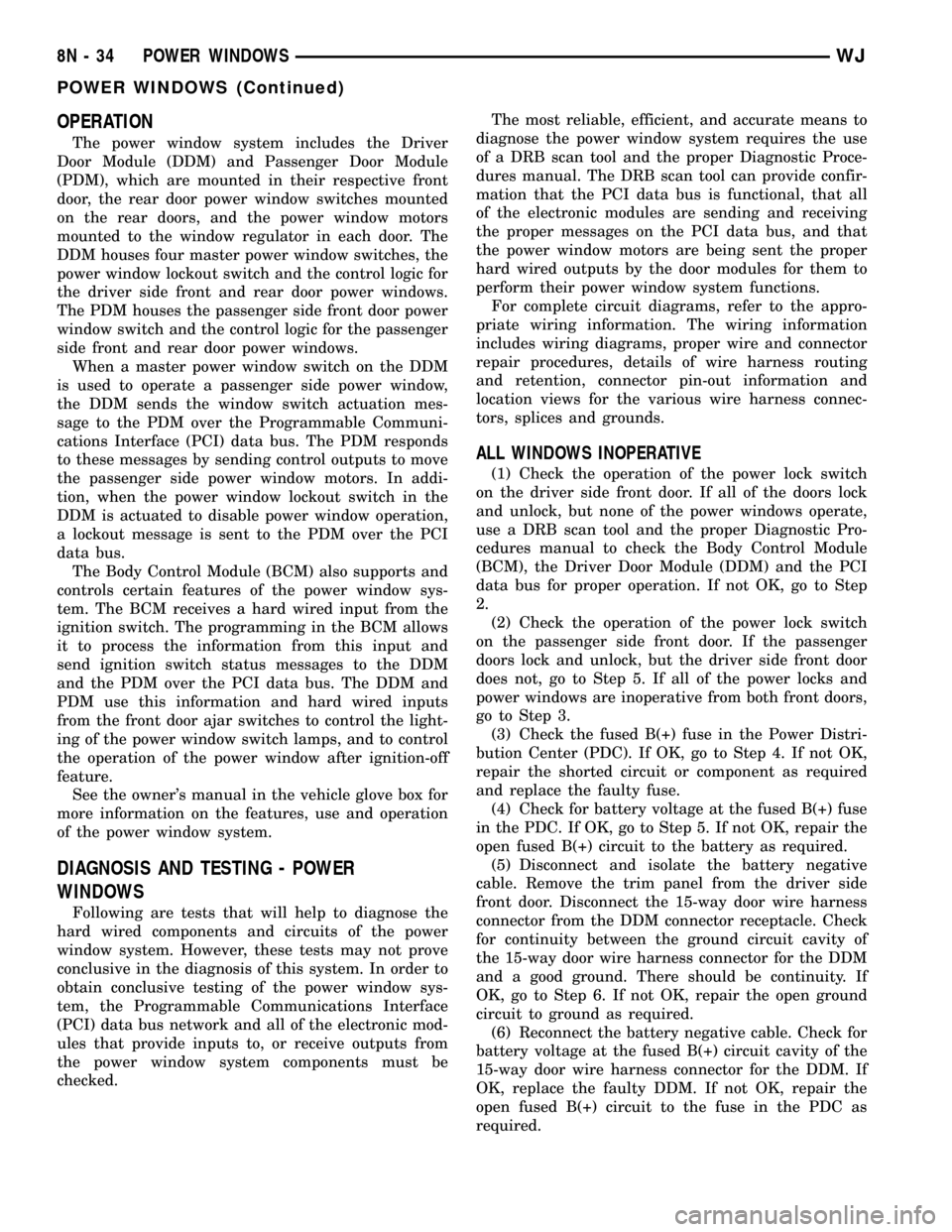
OPERATION
The power window system includes the Driver
Door Module (DDM) and Passenger Door Module
(PDM), which are mounted in their respective front
door, the rear door power window switches mounted
on the rear doors, and the power window motors
mounted to the window regulator in each door. The
DDM houses four master power window switches, the
power window lockout switch and the control logic for
the driver side front and rear door power windows.
The PDM houses the passenger side front door power
window switch and the control logic for the passenger
side front and rear door power windows.
When a master power window switch on the DDM
is used to operate a passenger side power window,
the DDM sends the window switch actuation mes-
sage to the PDM over the Programmable Communi-
cations Interface (PCI) data bus. The PDM responds
to these messages by sending control outputs to move
the passenger side power window motors. In addi-
tion, when the power window lockout switch in the
DDM is actuated to disable power window operation,
a lockout message is sent to the PDM over the PCI
data bus.
The Body Control Module (BCM) also supports and
controls certain features of the power window sys-
tem. The BCM receives a hard wired input from the
ignition switch. The programming in the BCM allows
it to process the information from this input and
send ignition switch status messages to the DDM
and the PDM over the PCI data bus. The DDM and
PDM use this information and hard wired inputs
from the front door ajar switches to control the light-
ing of the power window switch lamps, and to control
the operation of the power window after ignition-off
feature.
See the owner's manual in the vehicle glove box for
more information on the features, use and operation
of the power window system.
DIAGNOSIS AND TESTING - POWER
WINDOWS
Following are tests that will help to diagnose the
hard wired components and circuits of the power
window system. However, these tests may not prove
conclusive in the diagnosis of this system. In order to
obtain conclusive testing of the power window sys-
tem, the Programmable Communications Interface
(PCI) data bus network and all of the electronic mod-
ules that provide inputs to, or receive outputs from
the power window system components must be
checked.The most reliable, efficient, and accurate means to
diagnose the power window system requires the use
of a DRB scan tool and the proper Diagnostic Proce-
dures manual. The DRB scan tool can provide confir-
mation that the PCI data bus is functional, that all
of the electronic modules are sending and receiving
the proper messages on the PCI data bus, and that
the power window motors are being sent the proper
hard wired outputs by the door modules for them to
perform their power window system functions.
For complete circuit diagrams, refer to the appro-
priate wiring information. The wiring information
includes wiring diagrams, proper wire and connector
repair procedures, details of wire harness routing
and retention, connector pin-out information and
location views for the various wire harness connec-
tors, splices and grounds.
ALL WINDOWS INOPERATIVE
(1) Check the operation of the power lock switch
on the driver side front door. If all of the doors lock
and unlock, but none of the power windows operate,
use a DRB scan tool and the proper Diagnostic Pro-
cedures manual to check the Body Control Module
(BCM), the Driver Door Module (DDM) and the PCI
data bus for proper operation. If not OK, go to Step
2.
(2) Check the operation of the power lock switch
on the passenger side front door. If the passenger
doors lock and unlock, but the driver side front door
does not, go to Step 5. If all of the power locks and
power windows are inoperative from both front doors,
go to Step 3.
(3) Check the fused B(+) fuse in the Power Distri-
bution Center (PDC). If OK, go to Step 4. If not OK,
repair the shorted circuit or component as required
and replace the faulty fuse.
(4) Check for battery voltage at the fused B(+) fuse
in the PDC. If OK, go to Step 5. If not OK, repair the
open fused B(+) circuit to the battery as required.
(5) Disconnect and isolate the battery negative
cable. Remove the trim panel from the driver side
front door. Disconnect the 15-way door wire harness
connector from the DDM connector receptacle. Check
for continuity between the ground circuit cavity of
the 15-way door wire harness connector for the DDM
and a good ground. There should be continuity. If
OK, go to Step 6. If not OK, repair the open ground
circuit to ground as required.
(6) Reconnect the battery negative cable. Check for
battery voltage at the fused B(+) circuit cavity of the
15-way door wire harness connector for the DDM. If
OK, replace the faulty DDM. If not OK, repair the
open fused B(+) circuit to the fuse in the PDC as
required.
8N - 34 POWER WINDOWSWJ
POWER WINDOWS (Continued)
Page 532 of 2199
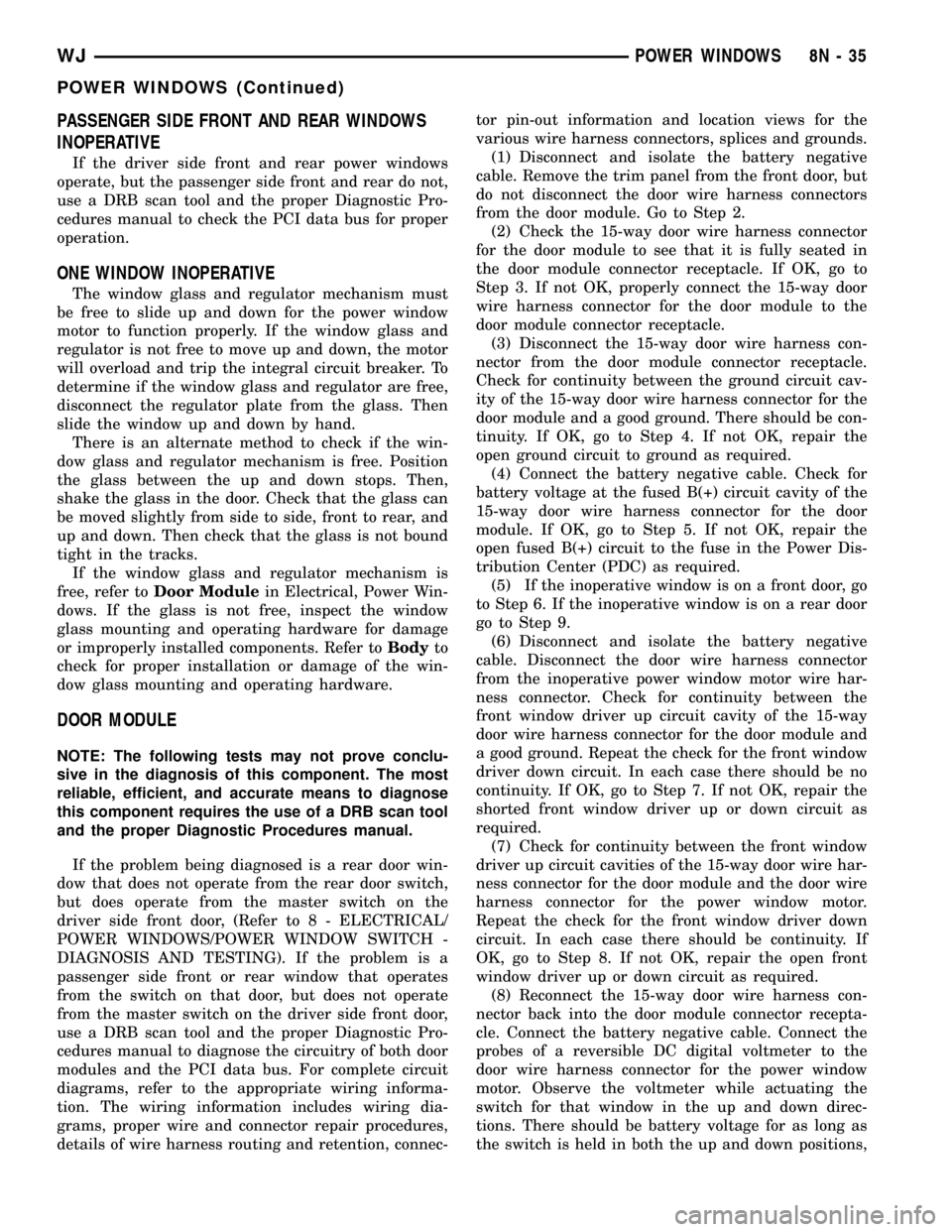
PASSENGER SIDE FRONT AND REAR WINDOWS
INOPERATIVE
If the driver side front and rear power windows
operate, but the passenger side front and rear do not,
use a DRB scan tool and the proper Diagnostic Pro-
cedures manual to check the PCI data bus for proper
operation.
ONE WINDOW INOPERATIVE
The window glass and regulator mechanism must
be free to slide up and down for the power window
motor to function properly. If the window glass and
regulator is not free to move up and down, the motor
will overload and trip the integral circuit breaker. To
determine if the window glass and regulator are free,
disconnect the regulator plate from the glass. Then
slide the window up and down by hand.
There is an alternate method to check if the win-
dow glass and regulator mechanism is free. Position
the glass between the up and down stops. Then,
shake the glass in the door. Check that the glass can
be moved slightly from side to side, front to rear, and
up and down. Then check that the glass is not bound
tight in the tracks.
If the window glass and regulator mechanism is
free, refer toDoor Modulein Electrical, Power Win-
dows. If the glass is not free, inspect the window
glass mounting and operating hardware for damage
or improperly installed components. Refer toBodyto
check for proper installation or damage of the win-
dow glass mounting and operating hardware.
DOOR MODULE
NOTE: The following tests may not prove conclu-
sive in the diagnosis of this component. The most
reliable, efficient, and accurate means to diagnose
this component requires the use of a DRB scan tool
and the proper Diagnostic Procedures manual.
If the problem being diagnosed is a rear door win-
dow that does not operate from the rear door switch,
but does operate from the master switch on the
driver side front door, (Refer to 8 - ELECTRICAL/
POWER WINDOWS/POWER WINDOW SWITCH -
DIAGNOSIS AND TESTING). If the problem is a
passenger side front or rear window that operates
from the switch on that door, but does not operate
from the master switch on the driver side front door,
use a DRB scan tool and the proper Diagnostic Pro-
cedures manual to diagnose the circuitry of both door
modules and the PCI data bus. For complete circuit
diagrams, refer to the appropriate wiring informa-
tion. The wiring information includes wiring dia-
grams, proper wire and connector repair procedures,
details of wire harness routing and retention, connec-tor pin-out information and location views for the
various wire harness connectors, splices and grounds.
(1) Disconnect and isolate the battery negative
cable. Remove the trim panel from the front door, but
do not disconnect the door wire harness connectors
from the door module. Go to Step 2.
(2) Check the 15-way door wire harness connector
for the door module to see that it is fully seated in
the door module connector receptacle. If OK, go to
Step 3. If not OK, properly connect the 15-way door
wire harness connector for the door module to the
door module connector receptacle.
(3) Disconnect the 15-way door wire harness con-
nector from the door module connector receptacle.
Check for continuity between the ground circuit cav-
ity of the 15-way door wire harness connector for the
door module and a good ground. There should be con-
tinuity. If OK, go to Step 4. If not OK, repair the
open ground circuit to ground as required.
(4) Connect the battery negative cable. Check for
battery voltage at the fused B(+) circuit cavity of the
15-way door wire harness connector for the door
module. If OK, go to Step 5. If not OK, repair the
open fused B(+) circuit to the fuse in the Power Dis-
tribution Center (PDC) as required.
(5) If the inoperative window is on a front door, go
to Step 6. If the inoperative window is on a rear door
go to Step 9.
(6) Disconnect and isolate the battery negative
cable. Disconnect the door wire harness connector
from the inoperative power window motor wire har-
ness connector. Check for continuity between the
front window driver up circuit cavity of the 15-way
door wire harness connector for the door module and
a good ground. Repeat the check for the front window
driver down circuit. In each case there should be no
continuity. If OK, go to Step 7. If not OK, repair the
shorted front window driver up or down circuit as
required.
(7) Check for continuity between the front window
driver up circuit cavities of the 15-way door wire har-
ness connector for the door module and the door wire
harness connector for the power window motor.
Repeat the check for the front window driver down
circuit. In each case there should be continuity. If
OK, go to Step 8. If not OK, repair the open front
window driver up or down circuit as required.
(8) Reconnect the 15-way door wire harness con-
nector back into the door module connector recepta-
cle. Connect the battery negative cable. Connect the
probes of a reversible DC digital voltmeter to the
door wire harness connector for the power window
motor. Observe the voltmeter while actuating the
switch for that window in the up and down direc-
tions. There should be battery voltage for as long as
the switch is held in both the up and down positions,
WJPOWER WINDOWS 8N - 35
POWER WINDOWS (Continued)
Page 533 of 2199
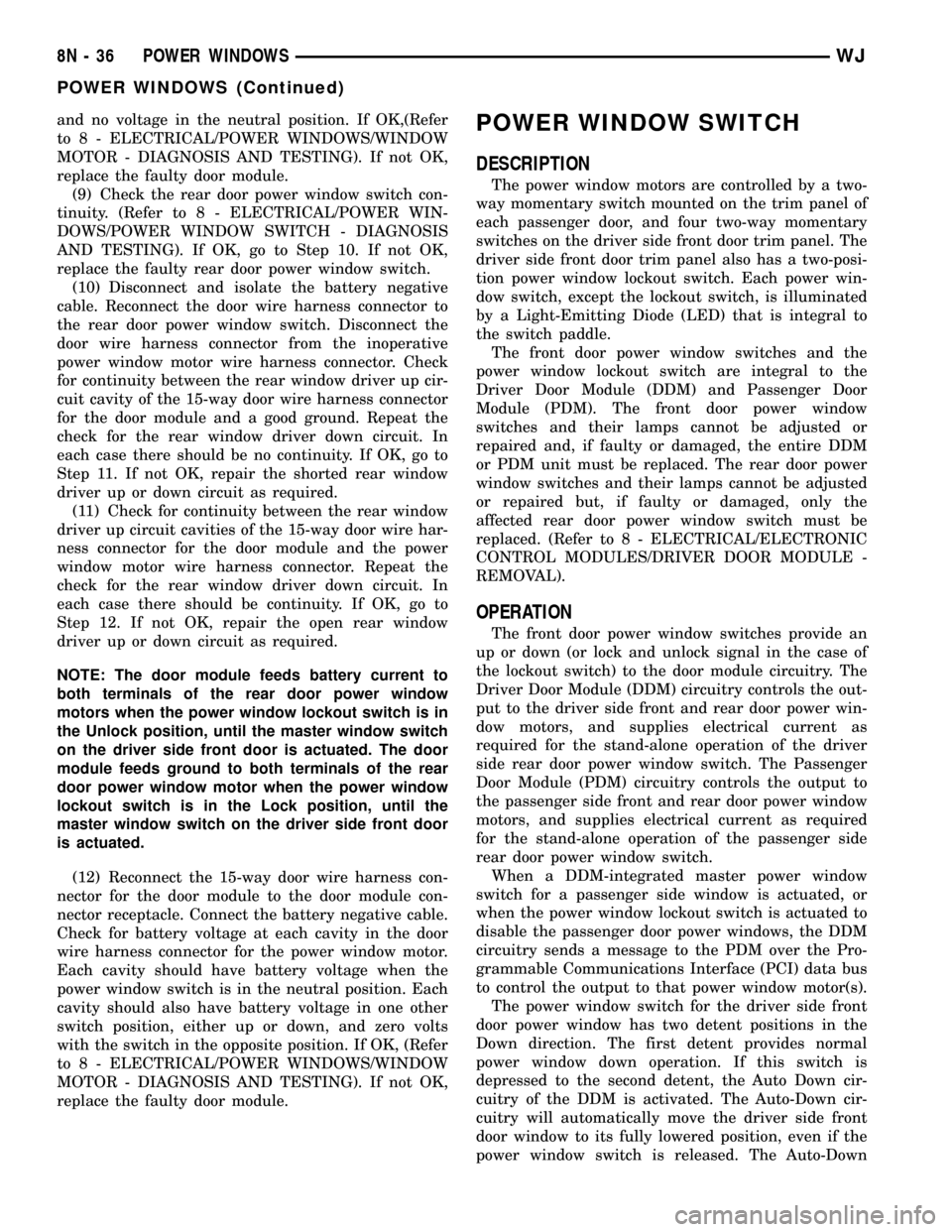
and no voltage in the neutral position. If OK,(Refer
to 8 - ELECTRICAL/POWER WINDOWS/WINDOW
MOTOR - DIAGNOSIS AND TESTING). If not OK,
replace the faulty door module.
(9) Check the rear door power window switch con-
tinuity. (Refer to 8 - ELECTRICAL/POWER WIN-
DOWS/POWER WINDOW SWITCH - DIAGNOSIS
AND TESTING). If OK, go to Step 10. If not OK,
replace the faulty rear door power window switch.
(10) Disconnect and isolate the battery negative
cable. Reconnect the door wire harness connector to
the rear door power window switch. Disconnect the
door wire harness connector from the inoperative
power window motor wire harness connector. Check
for continuity between the rear window driver up cir-
cuit cavity of the 15-way door wire harness connector
for the door module and a good ground. Repeat the
check for the rear window driver down circuit. In
each case there should be no continuity. If OK, go to
Step 11. If not OK, repair the shorted rear window
driver up or down circuit as required.
(11) Check for continuity between the rear window
driver up circuit cavities of the 15-way door wire har-
ness connector for the door module and the power
window motor wire harness connector. Repeat the
check for the rear window driver down circuit. In
each case there should be continuity. If OK, go to
Step 12. If not OK, repair the open rear window
driver up or down circuit as required.
NOTE: The door module feeds battery current to
both terminals of the rear door power window
motors when the power window lockout switch is in
the Unlock position, until the master window switch
on the driver side front door is actuated. The door
module feeds ground to both terminals of the rear
door power window motor when the power window
lockout switch is in the Lock position, until the
master window switch on the driver side front door
is actuated.
(12) Reconnect the 15-way door wire harness con-
nector for the door module to the door module con-
nector receptacle. Connect the battery negative cable.
Check for battery voltage at each cavity in the door
wire harness connector for the power window motor.
Each cavity should have battery voltage when the
power window switch is in the neutral position. Each
cavity should also have battery voltage in one other
switch position, either up or down, and zero volts
with the switch in the opposite position. If OK, (Refer
to 8 - ELECTRICAL/POWER WINDOWS/WINDOW
MOTOR - DIAGNOSIS AND TESTING). If not OK,
replace the faulty door module.POWER WINDOW SWITCH
DESCRIPTION
The power window motors are controlled by a two-
way momentary switch mounted on the trim panel of
each passenger door, and four two-way momentary
switches on the driver side front door trim panel. The
driver side front door trim panel also has a two-posi-
tion power window lockout switch. Each power win-
dow switch, except the lockout switch, is illuminated
by a Light-Emitting Diode (LED) that is integral to
the switch paddle.
The front door power window switches and the
power window lockout switch are integral to the
Driver Door Module (DDM) and Passenger Door
Module (PDM). The front door power window
switches and their lamps cannot be adjusted or
repaired and, if faulty or damaged, the entire DDM
or PDM unit must be replaced. The rear door power
window switches and their lamps cannot be adjusted
or repaired but, if faulty or damaged, only the
affected rear door power window switch must be
replaced. (Refer to 8 - ELECTRICAL/ELECTRONIC
CONTROL MODULES/DRIVER DOOR MODULE -
REMOVAL).
OPERATION
The front door power window switches provide an
up or down (or lock and unlock signal in the case of
the lockout switch) to the door module circuitry. The
Driver Door Module (DDM) circuitry controls the out-
put to the driver side front and rear door power win-
dow motors, and supplies electrical current as
required for the stand-alone operation of the driver
side rear door power window switch. The Passenger
Door Module (PDM) circuitry controls the output to
the passenger side front and rear door power window
motors, and supplies electrical current as required
for the stand-alone operation of the passenger side
rear door power window switch.
When a DDM-integrated master power window
switch for a passenger side window is actuated, or
when the power window lockout switch is actuated to
disable the passenger door power windows, the DDM
circuitry sends a message to the PDM over the Pro-
grammable Communications Interface (PCI) data bus
to control the output to that power window motor(s).
The power window switch for the driver side front
door power window has two detent positions in the
Down direction. The first detent provides normal
power window down operation. If this switch is
depressed to the second detent, the Auto Down cir-
cuitry of the DDM is activated. The Auto-Down cir-
cuitry will automatically move the driver side front
door window to its fully lowered position, even if the
power window switch is released. The Auto-Down
8N - 36 POWER WINDOWSWJ
POWER WINDOWS (Continued)
Page 552 of 2199
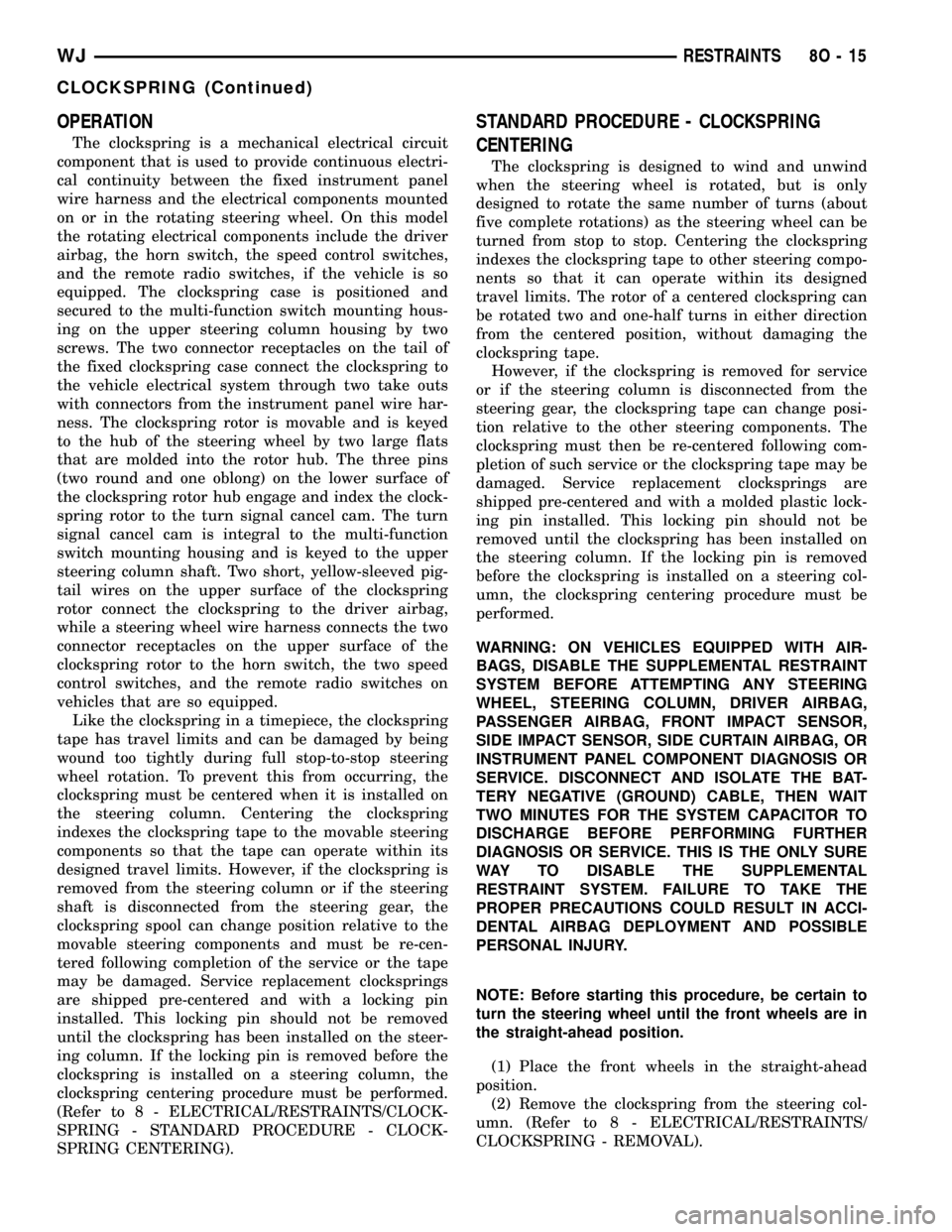
OPERATION
The clockspring is a mechanical electrical circuit
component that is used to provide continuous electri-
cal continuity between the fixed instrument panel
wire harness and the electrical components mounted
on or in the rotating steering wheel. On this model
the rotating electrical components include the driver
airbag, the horn switch, the speed control switches,
and the remote radio switches, if the vehicle is so
equipped. The clockspring case is positioned and
secured to the multi-function switch mounting hous-
ing on the upper steering column housing by two
screws. The two connector receptacles on the tail of
the fixed clockspring case connect the clockspring to
the vehicle electrical system through two take outs
with connectors from the instrument panel wire har-
ness. The clockspring rotor is movable and is keyed
to the hub of the steering wheel by two large flats
that are molded into the rotor hub. The three pins
(two round and one oblong) on the lower surface of
the clockspring rotor hub engage and index the clock-
spring rotor to the turn signal cancel cam. The turn
signal cancel cam is integral to the multi-function
switch mounting housing and is keyed to the upper
steering column shaft. Two short, yellow-sleeved pig-
tail wires on the upper surface of the clockspring
rotor connect the clockspring to the driver airbag,
while a steering wheel wire harness connects the two
connector receptacles on the upper surface of the
clockspring rotor to the horn switch, the two speed
control switches, and the remote radio switches on
vehicles that are so equipped.
Like the clockspring in a timepiece, the clockspring
tape has travel limits and can be damaged by being
wound too tightly during full stop-to-stop steering
wheel rotation. To prevent this from occurring, the
clockspring must be centered when it is installed on
the steering column. Centering the clockspring
indexes the clockspring tape to the movable steering
components so that the tape can operate within its
designed travel limits. However, if the clockspring is
removed from the steering column or if the steering
shaft is disconnected from the steering gear, the
clockspring spool can change position relative to the
movable steering components and must be re-cen-
tered following completion of the service or the tape
may be damaged. Service replacement clocksprings
are shipped pre-centered and with a locking pin
installed. This locking pin should not be removed
until the clockspring has been installed on the steer-
ing column. If the locking pin is removed before the
clockspring is installed on a steering column, the
clockspring centering procedure must be performed.
(Refer to 8 - ELECTRICAL/RESTRAINTS/CLOCK-
SPRING - STANDARD PROCEDURE - CLOCK-
SPRING CENTERING).
STANDARD PROCEDURE - CLOCKSPRING
CENTERING
The clockspring is designed to wind and unwind
when the steering wheel is rotated, but is only
designed to rotate the same number of turns (about
five complete rotations) as the steering wheel can be
turned from stop to stop. Centering the clockspring
indexes the clockspring tape to other steering compo-
nents so that it can operate within its designed
travel limits. The rotor of a centered clockspring can
be rotated two and one-half turns in either direction
from the centered position, without damaging the
clockspring tape.
However, if the clockspring is removed for service
or if the steering column is disconnected from the
steering gear, the clockspring tape can change posi-
tion relative to the other steering components. The
clockspring must then be re-centered following com-
pletion of such service or the clockspring tape may be
damaged. Service replacement clocksprings are
shipped pre-centered and with a molded plastic lock-
ing pin installed. This locking pin should not be
removed until the clockspring has been installed on
the steering column. If the locking pin is removed
before the clockspring is installed on a steering col-
umn, the clockspring centering procedure must be
performed.
WARNING: ON VEHICLES EQUIPPED WITH AIR-
BAGS, DISABLE THE SUPPLEMENTAL RESTRAINT
SYSTEM BEFORE ATTEMPTING ANY STEERING
WHEEL, STEERING COLUMN, DRIVER AIRBAG,
PASSENGER AIRBAG, FRONT IMPACT SENSOR,
SIDE IMPACT SENSOR, SIDE CURTAIN AIRBAG, OR
INSTRUMENT PANEL COMPONENT DIAGNOSIS OR
SERVICE. DISCONNECT AND ISOLATE THE BAT-
TERY NEGATIVE (GROUND) CABLE, THEN WAIT
TWO MINUTES FOR THE SYSTEM CAPACITOR TO
DISCHARGE BEFORE PERFORMING FURTHER
DIAGNOSIS OR SERVICE. THIS IS THE ONLY SURE
WAY TO DISABLE THE SUPPLEMENTAL
RESTRAINT SYSTEM. FAILURE TO TAKE THE
PROPER PRECAUTIONS COULD RESULT IN ACCI-
DENTAL AIRBAG DEPLOYMENT AND POSSIBLE
PERSONAL INJURY.
NOTE: Before starting this procedure, be certain to
turn the steering wheel until the front wheels are in
the straight-ahead position.
(1) Place the front wheels in the straight-ahead
position.
(2) Remove the clockspring from the steering col-
umn. (Refer to 8 - ELECTRICAL/RESTRAINTS/
CLOCKSPRING - REMOVAL).
WJRESTRAINTS 8O - 15
CLOCKSPRING (Continued)
Page 595 of 2199
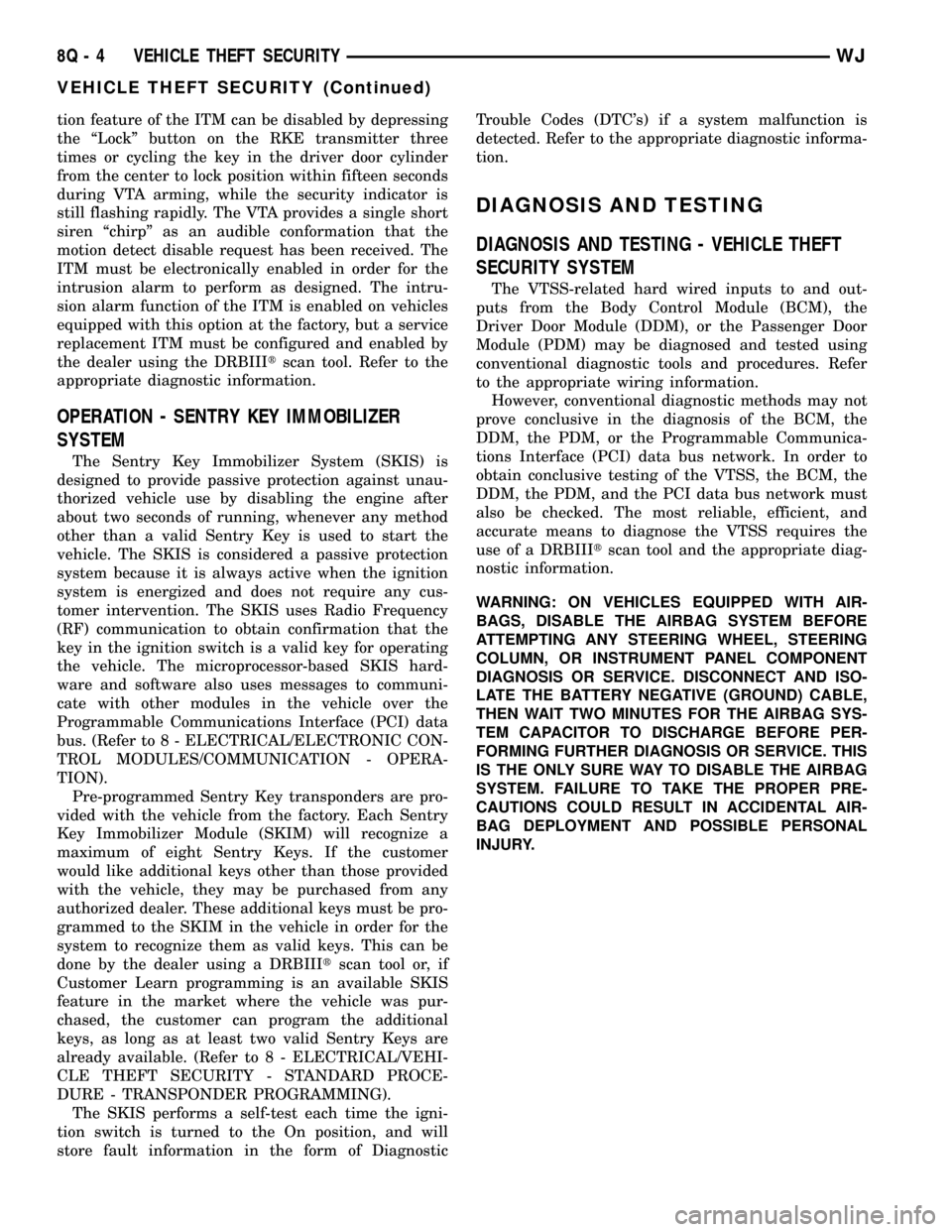
tion feature of the ITM can be disabled by depressing
the ªLockº button on the RKE transmitter three
times or cycling the key in the driver door cylinder
from the center to lock position within fifteen seconds
during VTA arming, while the security indicator is
still flashing rapidly. The VTA provides a single short
siren ªchirpº as an audible conformation that the
motion detect disable request has been received. The
ITM must be electronically enabled in order for the
intrusion alarm to perform as designed. The intru-
sion alarm function of the ITM is enabled on vehicles
equipped with this option at the factory, but a service
replacement ITM must be configured and enabled by
the dealer using the DRBIIItscan tool. Refer to the
appropriate diagnostic information.
OPERATION - SENTRY KEY IMMOBILIZER
SYSTEM
The Sentry Key Immobilizer System (SKIS) is
designed to provide passive protection against unau-
thorized vehicle use by disabling the engine after
about two seconds of running, whenever any method
other than a valid Sentry Key is used to start the
vehicle. The SKIS is considered a passive protection
system because it is always active when the ignition
system is energized and does not require any cus-
tomer intervention. The SKIS uses Radio Frequency
(RF) communication to obtain confirmation that the
key in the ignition switch is a valid key for operating
the vehicle. The microprocessor-based SKIS hard-
ware and software also uses messages to communi-
cate with other modules in the vehicle over the
Programmable Communications Interface (PCI) data
bus. (Refer to 8 - ELECTRICAL/ELECTRONIC CON-
TROL MODULES/COMMUNICATION - OPERA-
TION).
Pre-programmed Sentry Key transponders are pro-
vided with the vehicle from the factory. Each Sentry
Key Immobilizer Module (SKIM) will recognize a
maximum of eight Sentry Keys. If the customer
would like additional keys other than those provided
with the vehicle, they may be purchased from any
authorized dealer. These additional keys must be pro-
grammed to the SKIM in the vehicle in order for the
system to recognize them as valid keys. This can be
done by the dealer using a DRBIIItscan tool or, if
Customer Learn programming is an available SKIS
feature in the market where the vehicle was pur-
chased, the customer can program the additional
keys, as long as at least two valid Sentry Keys are
already available. (Refer to 8 - ELECTRICAL/VEHI-
CLE THEFT SECURITY - STANDARD PROCE-
DURE - TRANSPONDER PROGRAMMING).
The SKIS performs a self-test each time the igni-
tion switch is turned to the On position, and will
store fault information in the form of DiagnosticTrouble Codes (DTC's) if a system malfunction is
detected. Refer to the appropriate diagnostic informa-
tion.
DIAGNOSIS AND TESTING
DIAGNOSIS AND TESTING - VEHICLE THEFT
SECURITY SYSTEM
The VTSS-related hard wired inputs to and out-
puts from the Body Control Module (BCM), the
Driver Door Module (DDM), or the Passenger Door
Module (PDM) may be diagnosed and tested using
conventional diagnostic tools and procedures. Refer
to the appropriate wiring information.
However, conventional diagnostic methods may not
prove conclusive in the diagnosis of the BCM, the
DDM, the PDM, or the Programmable Communica-
tions Interface (PCI) data bus network. In order to
obtain conclusive testing of the VTSS, the BCM, the
DDM, the PDM, and the PCI data bus network must
also be checked. The most reliable, efficient, and
accurate means to diagnose the VTSS requires the
use of a DRBIIItscan tool and the appropriate diag-
nostic information.
WARNING: ON VEHICLES EQUIPPED WITH AIR-
BAGS, DISABLE THE AIRBAG SYSTEM BEFORE
ATTEMPTING ANY STEERING WHEEL, STEERING
COLUMN, OR INSTRUMENT PANEL COMPONENT
DIAGNOSIS OR SERVICE. DISCONNECT AND ISO-
LATE THE BATTERY NEGATIVE (GROUND) CABLE,
THEN WAIT TWO MINUTES FOR THE AIRBAG SYS-
TEM CAPACITOR TO DISCHARGE BEFORE PER-
FORMING FURTHER DIAGNOSIS OR SERVICE. THIS
IS THE ONLY SURE WAY TO DISABLE THE AIRBAG
SYSTEM. FAILURE TO TAKE THE PROPER PRE-
CAUTIONS COULD RESULT IN ACCIDENTAL AIR-
BAG DEPLOYMENT AND POSSIBLE PERSONAL
INJURY.
8Q - 4 VEHICLE THEFT SECURITYWJ
VEHICLE THEFT SECURITY (Continued)
Page 596 of 2199
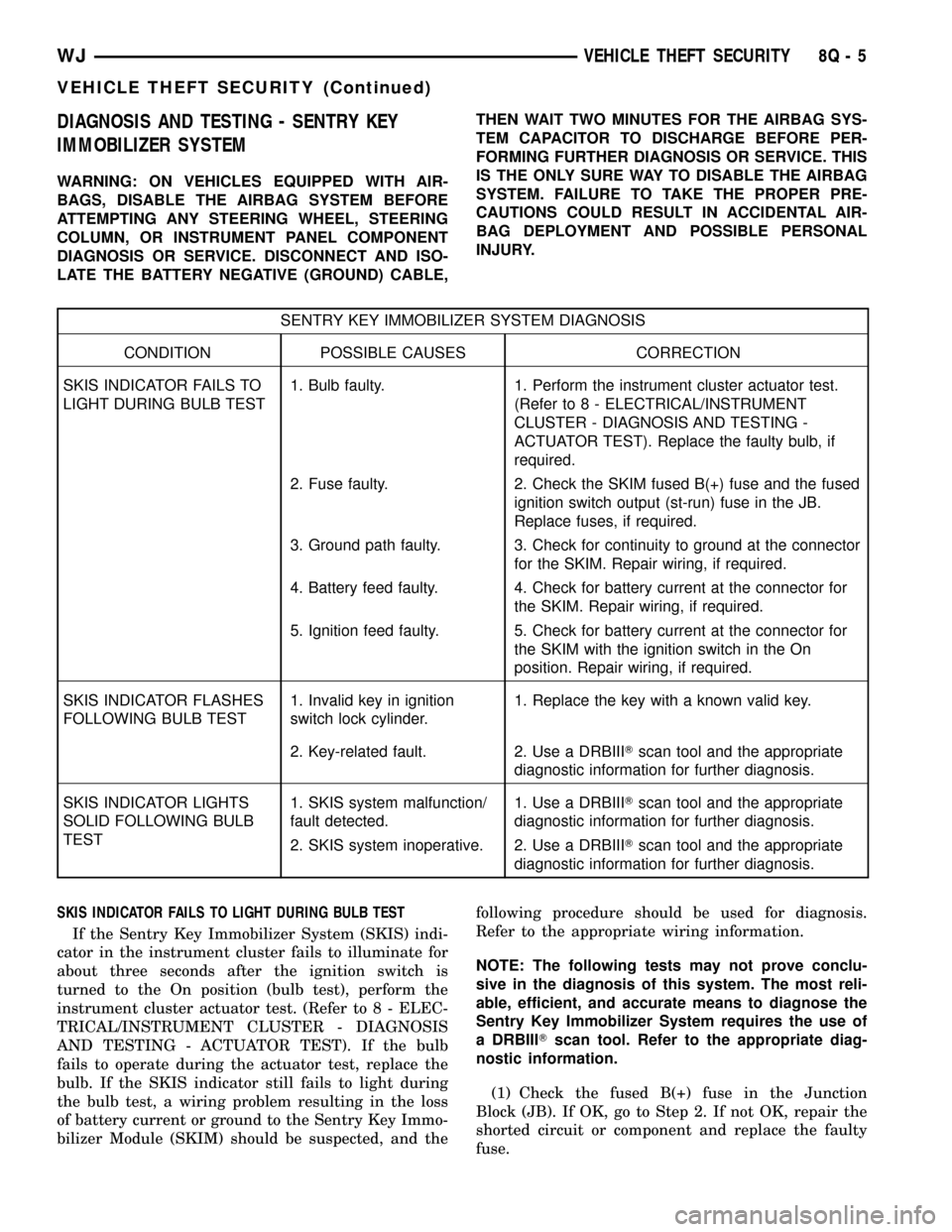
DIAGNOSIS AND TESTING - SENTRY KEY
IMMOBILIZER SYSTEM
WARNING: ON VEHICLES EQUIPPED WITH AIR-
BAGS, DISABLE THE AIRBAG SYSTEM BEFORE
ATTEMPTING ANY STEERING WHEEL, STEERING
COLUMN, OR INSTRUMENT PANEL COMPONENT
DIAGNOSIS OR SERVICE. DISCONNECT AND ISO-
LATE THE BATTERY NEGATIVE (GROUND) CABLE,THEN WAIT TWO MINUTES FOR THE AIRBAG SYS-
TEM CAPACITOR TO DISCHARGE BEFORE PER-
FORMING FURTHER DIAGNOSIS OR SERVICE. THIS
IS THE ONLY SURE WAY TO DISABLE THE AIRBAG
SYSTEM. FAILURE TO TAKE THE PROPER PRE-
CAUTIONS COULD RESULT IN ACCIDENTAL AIR-
BAG DEPLOYMENT AND POSSIBLE PERSONAL
INJURY.
SENTRY KEY IMMOBILIZER SYSTEM DIAGNOSIS
CONDITION POSSIBLE CAUSES CORRECTION
SKIS INDICATOR FAILS TO
LIGHT DURING BULB TEST1. Bulb faulty. 1. Perform the instrument cluster actuator test.
(Refer to 8 - ELECTRICAL/INSTRUMENT
CLUSTER - DIAGNOSIS AND TESTING -
ACTUATOR TEST). Replace the faulty bulb, if
required.
2. Fuse faulty. 2. Check the SKIM fused B(+) fuse and the fused
ignition switch output (st-run) fuse in the JB.
Replace fuses, if required.
3. Ground path faulty. 3. Check for continuity to ground at the connector
for the SKIM. Repair wiring, if required.
4. Battery feed faulty. 4. Check for battery current at the connector for
the SKIM. Repair wiring, if required.
5. Ignition feed faulty. 5. Check for battery current at the connector for
the SKIM with the ignition switch in the On
position. Repair wiring, if required.
SKIS INDICATOR FLASHES
FOLLOWING BULB TEST1. Invalid key in ignition
switch lock cylinder.1. Replace the key with a known valid key.
2. Key-related fault. 2. Use a DRBIIITscan tool and the appropriate
diagnostic information for further diagnosis.
SKIS INDICATOR LIGHTS
SOLID FOLLOWING BULB
TEST1. SKIS system malfunction/
fault detected.1. Use a DRBIIITscan tool and the appropriate
diagnostic information for further diagnosis.
2. SKIS system inoperative. 2. Use a DRBIIITscan tool and the appropriate
diagnostic information for further diagnosis.
SKIS INDICATOR FAILS TO LIGHT DURING BULB TEST
If the Sentry Key Immobilizer System (SKIS) indi-
cator in the instrument cluster fails to illuminate for
about three seconds after the ignition switch is
turned to the On position (bulb test), perform the
instrument cluster actuator test. (Refer to 8 - ELEC-
TRICAL/INSTRUMENT CLUSTER - DIAGNOSIS
AND TESTING - ACTUATOR TEST). If the bulb
fails to operate during the actuator test, replace the
bulb. If the SKIS indicator still fails to light during
the bulb test, a wiring problem resulting in the loss
of battery current or ground to the Sentry Key Immo-
bilizer Module (SKIM) should be suspected, and thefollowing procedure should be used for diagnosis.
Refer to the appropriate wiring information.
NOTE: The following tests may not prove conclu-
sive in the diagnosis of this system. The most reli-
able, efficient, and accurate means to diagnose the
Sentry Key Immobilizer System requires the use of
a DRBIIITscan tool. Refer to the appropriate diag-
nostic information.
(1) Check the fused B(+) fuse in the Junction
Block (JB). If OK, go to Step 2. If not OK, repair the
shorted circuit or component and replace the faulty
fuse.
WJVEHICLE THEFT SECURITY 8Q - 5
VEHICLE THEFT SECURITY (Continued)
Page 597 of 2199
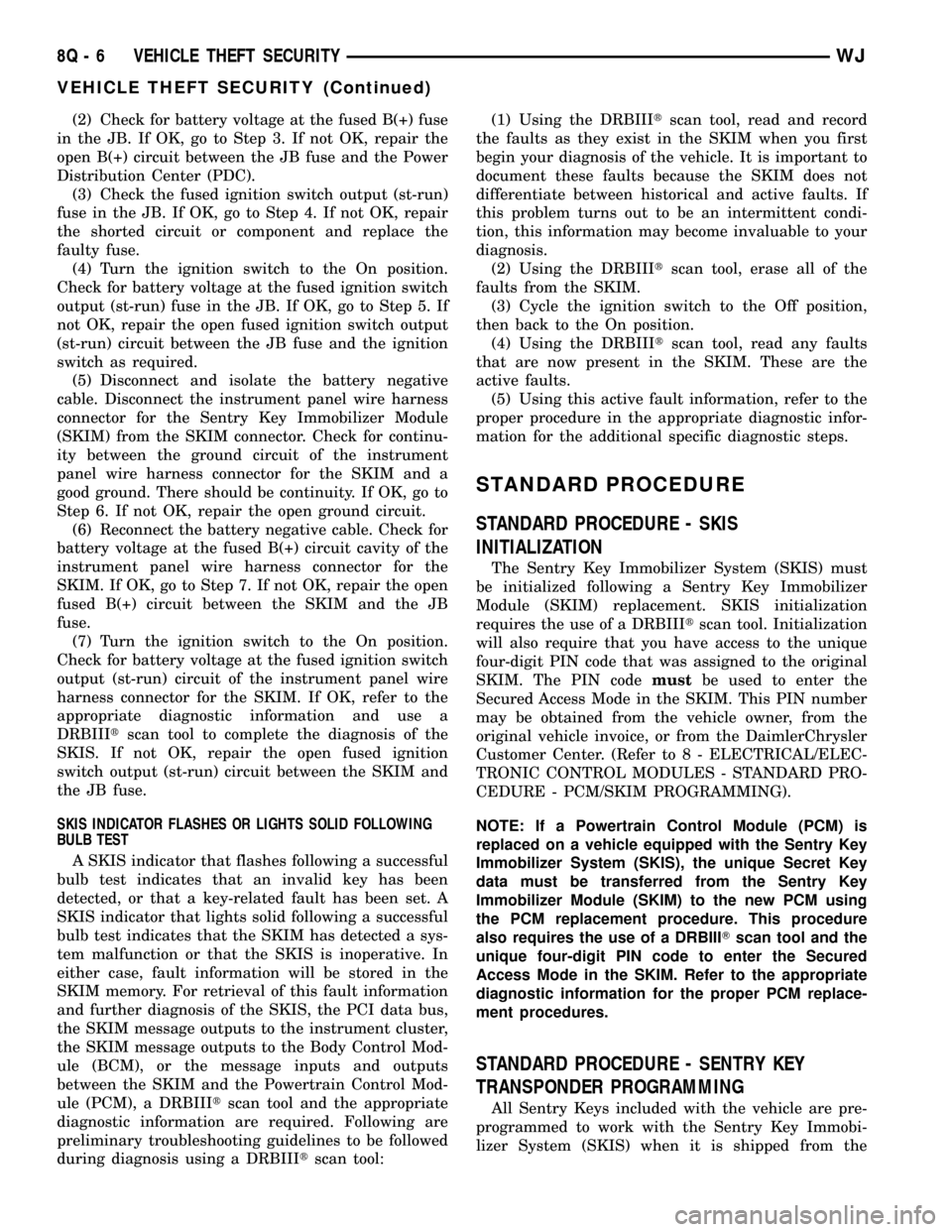
(2) Check for battery voltage at the fused B(+) fuse
in the JB. If OK, go to Step 3. If not OK, repair the
open B(+) circuit between the JB fuse and the Power
Distribution Center (PDC).
(3) Check the fused ignition switch output (st-run)
fuse in the JB. If OK, go to Step 4. If not OK, repair
the shorted circuit or component and replace the
faulty fuse.
(4) Turn the ignition switch to the On position.
Check for battery voltage at the fused ignition switch
output (st-run) fuse in the JB. If OK, go to Step 5. If
not OK, repair the open fused ignition switch output
(st-run) circuit between the JB fuse and the ignition
switch as required.
(5) Disconnect and isolate the battery negative
cable. Disconnect the instrument panel wire harness
connector for the Sentry Key Immobilizer Module
(SKIM) from the SKIM connector. Check for continu-
ity between the ground circuit of the instrument
panel wire harness connector for the SKIM and a
good ground. There should be continuity. If OK, go to
Step 6. If not OK, repair the open ground circuit.
(6) Reconnect the battery negative cable. Check for
battery voltage at the fused B(+) circuit cavity of the
instrument panel wire harness connector for the
SKIM. If OK, go to Step 7. If not OK, repair the open
fused B(+) circuit between the SKIM and the JB
fuse.
(7) Turn the ignition switch to the On position.
Check for battery voltage at the fused ignition switch
output (st-run) circuit of the instrument panel wire
harness connector for the SKIM. If OK, refer to the
appropriate diagnostic information and use a
DRBIIItscan tool to complete the diagnosis of the
SKIS. If not OK, repair the open fused ignition
switch output (st-run) circuit between the SKIM and
the JB fuse.
SKIS INDICATOR FLASHES OR LIGHTS SOLID FOLLOWING
BULB TEST
A SKIS indicator that flashes following a successful
bulb test indicates that an invalid key has been
detected, or that a key-related fault has been set. A
SKIS indicator that lights solid following a successful
bulb test indicates that the SKIM has detected a sys-
tem malfunction or that the SKIS is inoperative. In
either case, fault information will be stored in the
SKIM memory. For retrieval of this fault information
and further diagnosis of the SKIS, the PCI data bus,
the SKIM message outputs to the instrument cluster,
the SKIM message outputs to the Body Control Mod-
ule (BCM), or the message inputs and outputs
between the SKIM and the Powertrain Control Mod-
ule (PCM), a DRBIIItscan tool and the appropriate
diagnostic information are required. Following are
preliminary troubleshooting guidelines to be followed
during diagnosis using a DRBIIItscan tool:(1) Using the DRBIIItscan tool, read and record
the faults as they exist in the SKIM when you first
begin your diagnosis of the vehicle. It is important to
document these faults because the SKIM does not
differentiate between historical and active faults. If
this problem turns out to be an intermittent condi-
tion, this information may become invaluable to your
diagnosis.
(2) Using the DRBIIItscan tool, erase all of the
faults from the SKIM.
(3) Cycle the ignition switch to the Off position,
then back to the On position.
(4) Using the DRBIIItscan tool, read any faults
that are now present in the SKIM. These are the
active faults.
(5) Using this active fault information, refer to the
proper procedure in the appropriate diagnostic infor-
mation for the additional specific diagnostic steps.
STANDARD PROCEDURE
STANDARD PROCEDURE - SKIS
INITIALIZATION
The Sentry Key Immobilizer System (SKIS) must
be initialized following a Sentry Key Immobilizer
Module (SKIM) replacement. SKIS initialization
requires the use of a DRBIIItscan tool. Initialization
will also require that you have access to the unique
four-digit PIN code that was assigned to the original
SKIM. The PIN codemustbe used to enter the
Secured Access Mode in the SKIM. This PIN number
may be obtained from the vehicle owner, from the
original vehicle invoice, or from the DaimlerChrysler
Customer Center. (Refer to 8 - ELECTRICAL/ELEC-
TRONIC CONTROL MODULES - STANDARD PRO-
CEDURE - PCM/SKIM PROGRAMMING).
NOTE: If a Powertrain Control Module (PCM) is
replaced on a vehicle equipped with the Sentry Key
Immobilizer System (SKIS), the unique Secret Key
data must be transferred from the Sentry Key
Immobilizer Module (SKIM) to the new PCM using
the PCM replacement procedure. This procedure
also requires the use of a DRBIIITscan tool and the
unique four-digit PIN code to enter the Secured
Access Mode in the SKIM. Refer to the appropriate
diagnostic information for the proper PCM replace-
ment procedures.
STANDARD PROCEDURE - SENTRY KEY
TRANSPONDER PROGRAMMING
All Sentry Keys included with the vehicle are pre-
programmed to work with the Sentry Key Immobi-
lizer System (SKIS) when it is shipped from the
8Q - 6 VEHICLE THEFT SECURITYWJ
VEHICLE THEFT SECURITY (Continued)
Page 600 of 2199
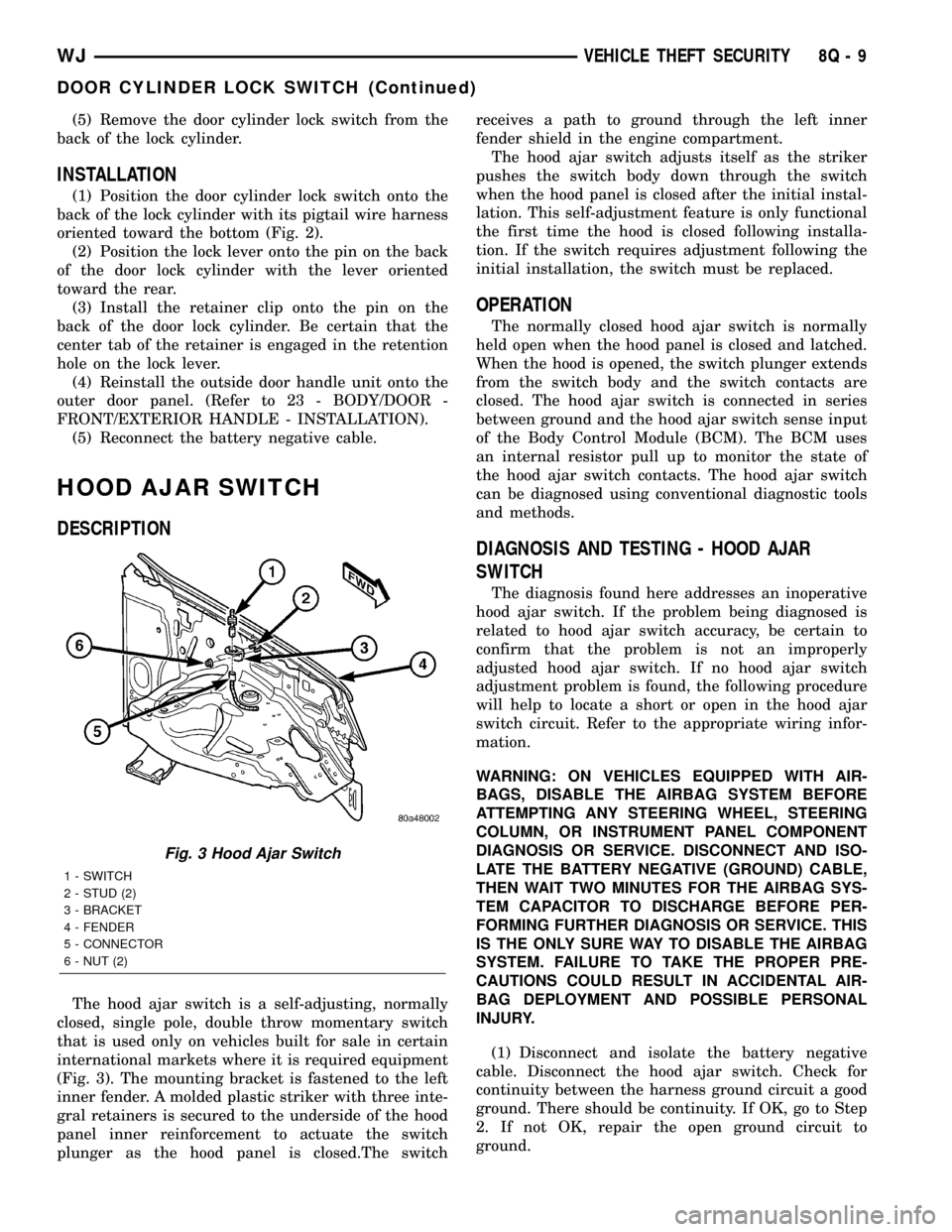
(5) Remove the door cylinder lock switch from the
back of the lock cylinder.
INSTALLATION
(1) Position the door cylinder lock switch onto the
back of the lock cylinder with its pigtail wire harness
oriented toward the bottom (Fig. 2).
(2) Position the lock lever onto the pin on the back
of the door lock cylinder with the lever oriented
toward the rear.
(3) Install the retainer clip onto the pin on the
back of the door lock cylinder. Be certain that the
center tab of the retainer is engaged in the retention
hole on the lock lever.
(4) Reinstall the outside door handle unit onto the
outer door panel. (Refer to 23 - BODY/DOOR -
FRONT/EXTERIOR HANDLE - INSTALLATION).
(5) Reconnect the battery negative cable.
HOOD AJAR SWITCH
DESCRIPTION
The hood ajar switch is a self-adjusting, normally
closed, single pole, double throw momentary switch
that is used only on vehicles built for sale in certain
international markets where it is required equipment
(Fig. 3). The mounting bracket is fastened to the left
inner fender. A molded plastic striker with three inte-
gral retainers is secured to the underside of the hood
panel inner reinforcement to actuate the switch
plunger as the hood panel is closed.The switchreceives a path to ground through the left inner
fender shield in the engine compartment.
The hood ajar switch adjusts itself as the striker
pushes the switch body down through the switch
when the hood panel is closed after the initial instal-
lation. This self-adjustment feature is only functional
the first time the hood is closed following installa-
tion. If the switch requires adjustment following the
initial installation, the switch must be replaced.
OPERATION
The normally closed hood ajar switch is normally
held open when the hood panel is closed and latched.
When the hood is opened, the switch plunger extends
from the switch body and the switch contacts are
closed. The hood ajar switch is connected in series
between ground and the hood ajar switch sense input
of the Body Control Module (BCM). The BCM uses
an internal resistor pull up to monitor the state of
the hood ajar switch contacts. The hood ajar switch
can be diagnosed using conventional diagnostic tools
and methods.
DIAGNOSIS AND TESTING - HOOD AJAR
SWITCH
The diagnosis found here addresses an inoperative
hood ajar switch. If the problem being diagnosed is
related to hood ajar switch accuracy, be certain to
confirm that the problem is not an improperly
adjusted hood ajar switch. If no hood ajar switch
adjustment problem is found, the following procedure
will help to locate a short or open in the hood ajar
switch circuit. Refer to the appropriate wiring infor-
mation.
WARNING: ON VEHICLES EQUIPPED WITH AIR-
BAGS, DISABLE THE AIRBAG SYSTEM BEFORE
ATTEMPTING ANY STEERING WHEEL, STEERING
COLUMN, OR INSTRUMENT PANEL COMPONENT
DIAGNOSIS OR SERVICE. DISCONNECT AND ISO-
LATE THE BATTERY NEGATIVE (GROUND) CABLE,
THEN WAIT TWO MINUTES FOR THE AIRBAG SYS-
TEM CAPACITOR TO DISCHARGE BEFORE PER-
FORMING FURTHER DIAGNOSIS OR SERVICE. THIS
IS THE ONLY SURE WAY TO DISABLE THE AIRBAG
SYSTEM. FAILURE TO TAKE THE PROPER PRE-
CAUTIONS COULD RESULT IN ACCIDENTAL AIR-
BAG DEPLOYMENT AND POSSIBLE PERSONAL
INJURY.
(1) Disconnect and isolate the battery negative
cable. Disconnect the hood ajar switch. Check for
continuity between the harness ground circuit a good
ground. There should be continuity. If OK, go to Step
2. If not OK, repair the open ground circuit to
ground.
Fig. 3 Hood Ajar Switch
1 - SWITCH
2 - STUD (2)
3 - BRACKET
4 - FENDER
5 - CONNECTOR
6 - NUT (2)
WJVEHICLE THEFT SECURITY 8Q - 9
DOOR CYLINDER LOCK SWITCH (Continued)
Page 601 of 2199
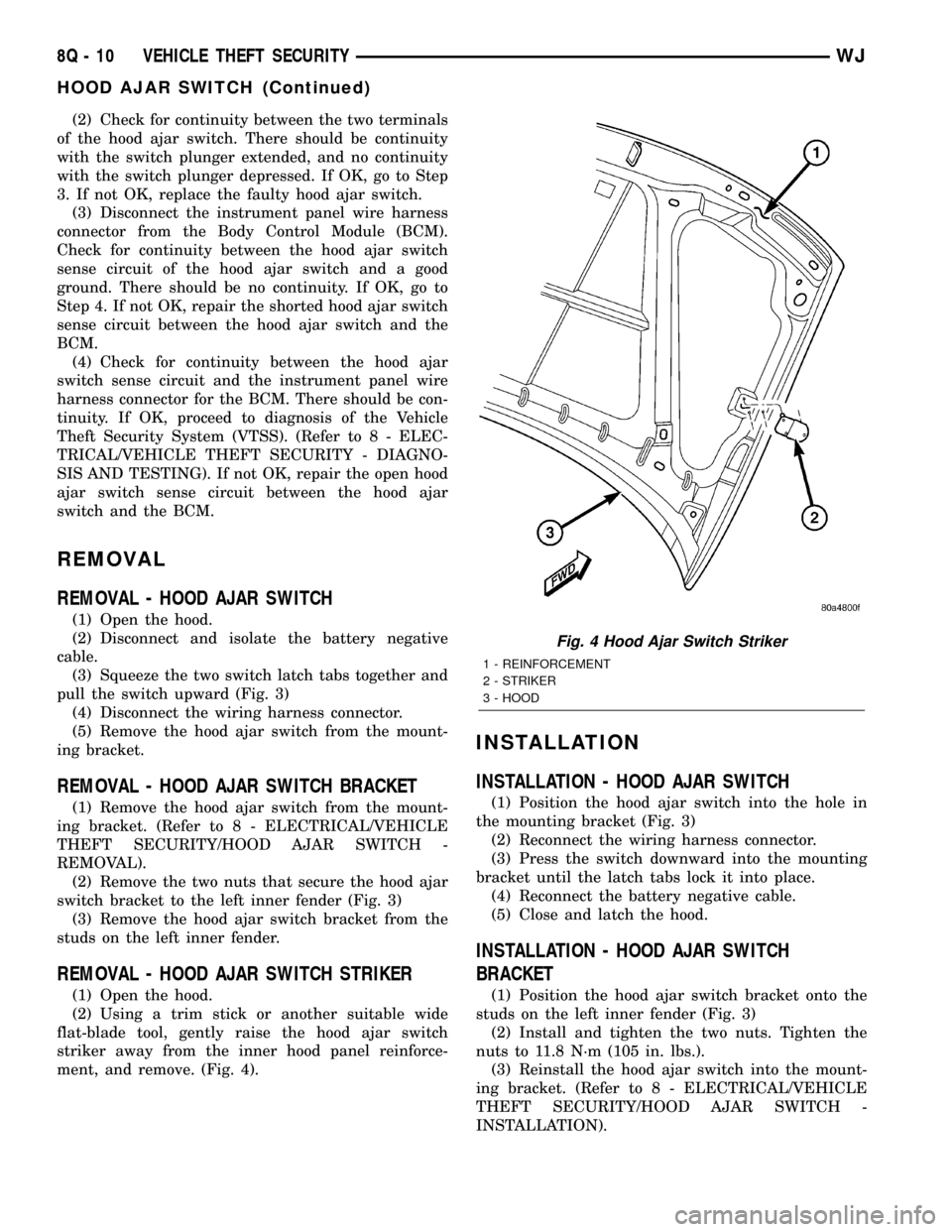
(2) Check for continuity between the two terminals
of the hood ajar switch. There should be continuity
with the switch plunger extended, and no continuity
with the switch plunger depressed. If OK, go to Step
3. If not OK, replace the faulty hood ajar switch.
(3) Disconnect the instrument panel wire harness
connector from the Body Control Module (BCM).
Check for continuity between the hood ajar switch
sense circuit of the hood ajar switch and a good
ground. There should be no continuity. If OK, go to
Step 4. If not OK, repair the shorted hood ajar switch
sense circuit between the hood ajar switch and the
BCM.
(4) Check for continuity between the hood ajar
switch sense circuit and the instrument panel wire
harness connector for the BCM. There should be con-
tinuity. If OK, proceed to diagnosis of the Vehicle
Theft Security System (VTSS). (Refer to 8 - ELEC-
TRICAL/VEHICLE THEFT SECURITY - DIAGNO-
SIS AND TESTING). If not OK, repair the open hood
ajar switch sense circuit between the hood ajar
switch and the BCM.
REMOVAL
REMOVAL - HOOD AJAR SWITCH
(1) Open the hood.
(2) Disconnect and isolate the battery negative
cable.
(3) Squeeze the two switch latch tabs together and
pull the switch upward (Fig. 3)
(4) Disconnect the wiring harness connector.
(5) Remove the hood ajar switch from the mount-
ing bracket.
REMOVAL - HOOD AJAR SWITCH BRACKET
(1) Remove the hood ajar switch from the mount-
ing bracket. (Refer to 8 - ELECTRICAL/VEHICLE
THEFT SECURITY/HOOD AJAR SWITCH -
REMOVAL).
(2) Remove the two nuts that secure the hood ajar
switch bracket to the left inner fender (Fig. 3)
(3) Remove the hood ajar switch bracket from the
studs on the left inner fender.
REMOVAL - HOOD AJAR SWITCH STRIKER
(1) Open the hood.
(2) Using a trim stick or another suitable wide
flat-blade tool, gently raise the hood ajar switch
striker away from the inner hood panel reinforce-
ment, and remove. (Fig. 4).
INSTALLATION
INSTALLATION - HOOD AJAR SWITCH
(1) Position the hood ajar switch into the hole in
the mounting bracket (Fig. 3)
(2) Reconnect the wiring harness connector.
(3) Press the switch downward into the mounting
bracket until the latch tabs lock it into place.
(4) Reconnect the battery negative cable.
(5) Close and latch the hood.
INSTALLATION - HOOD AJAR SWITCH
BRACKET
(1) Position the hood ajar switch bracket onto the
studs on the left inner fender (Fig. 3)
(2) Install and tighten the two nuts. Tighten the
nuts to 11.8 N´m (105 in. lbs.).
(3) Reinstall the hood ajar switch into the mount-
ing bracket. (Refer to 8 - ELECTRICAL/VEHICLE
THEFT SECURITY/HOOD AJAR SWITCH -
INSTALLATION).
Fig. 4 Hood Ajar Switch Striker
1 - REINFORCEMENT
2 - STRIKER
3 - HOOD
8Q - 10 VEHICLE THEFT SECURITYWJ
HOOD AJAR SWITCH (Continued)
Page 607 of 2199
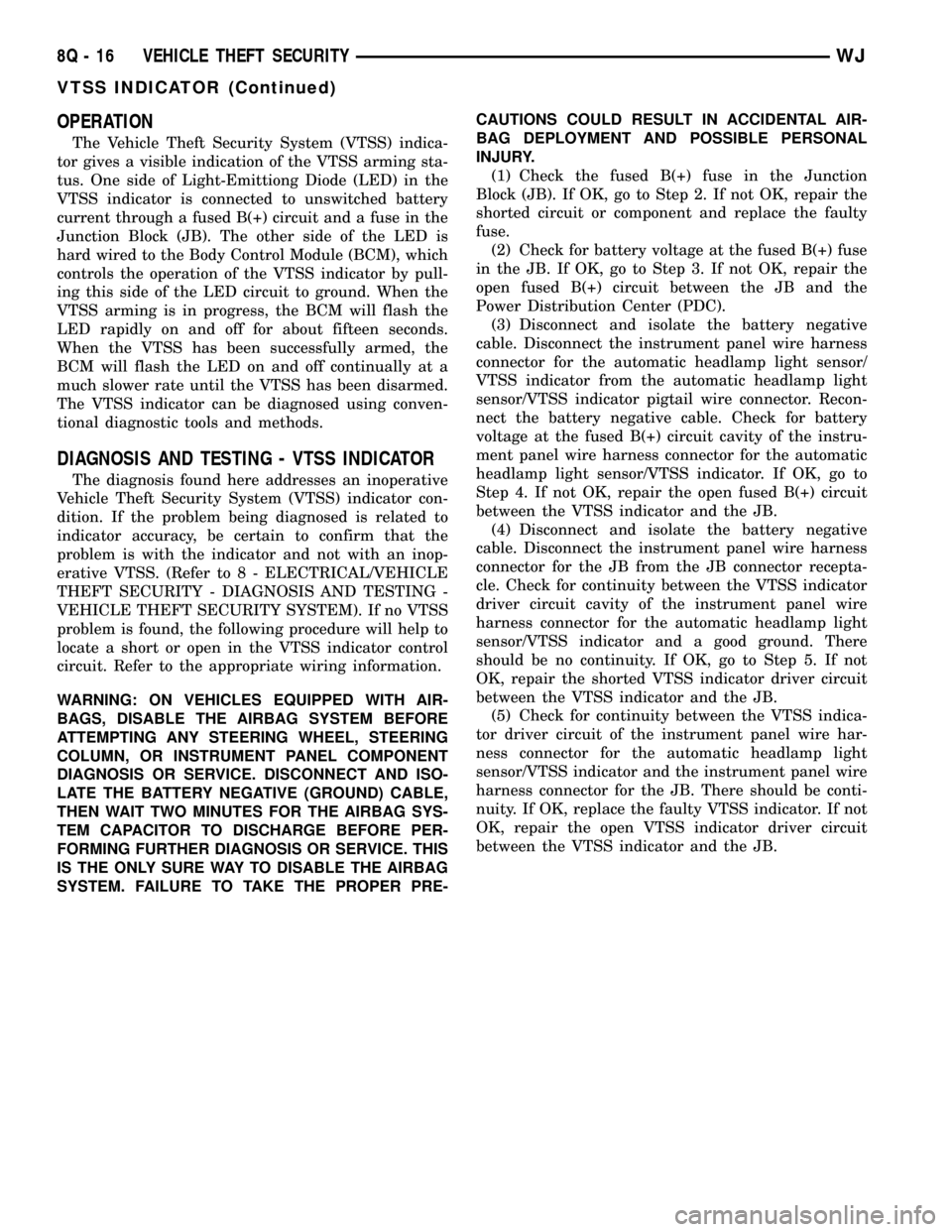
OPERATION
The Vehicle Theft Security System (VTSS) indica-
tor gives a visible indication of the VTSS arming sta-
tus. One side of Light-Emittiong Diode (LED) in the
VTSS indicator is connected to unswitched battery
current through a fused B(+) circuit and a fuse in the
Junction Block (JB). The other side of the LED is
hard wired to the Body Control Module (BCM), which
controls the operation of the VTSS indicator by pull-
ing this side of the LED circuit to ground. When the
VTSS arming is in progress, the BCM will flash the
LED rapidly on and off for about fifteen seconds.
When the VTSS has been successfully armed, the
BCM will flash the LED on and off continually at a
much slower rate until the VTSS has been disarmed.
The VTSS indicator can be diagnosed using conven-
tional diagnostic tools and methods.
DIAGNOSIS AND TESTING - VTSS INDICATOR
The diagnosis found here addresses an inoperative
Vehicle Theft Security System (VTSS) indicator con-
dition. If the problem being diagnosed is related to
indicator accuracy, be certain to confirm that the
problem is with the indicator and not with an inop-
erative VTSS. (Refer to 8 - ELECTRICAL/VEHICLE
THEFT SECURITY - DIAGNOSIS AND TESTING -
VEHICLE THEFT SECURITY SYSTEM). If no VTSS
problem is found, the following procedure will help to
locate a short or open in the VTSS indicator control
circuit. Refer to the appropriate wiring information.
WARNING: ON VEHICLES EQUIPPED WITH AIR-
BAGS, DISABLE THE AIRBAG SYSTEM BEFORE
ATTEMPTING ANY STEERING WHEEL, STEERING
COLUMN, OR INSTRUMENT PANEL COMPONENT
DIAGNOSIS OR SERVICE. DISCONNECT AND ISO-
LATE THE BATTERY NEGATIVE (GROUND) CABLE,
THEN WAIT TWO MINUTES FOR THE AIRBAG SYS-
TEM CAPACITOR TO DISCHARGE BEFORE PER-
FORMING FURTHER DIAGNOSIS OR SERVICE. THIS
IS THE ONLY SURE WAY TO DISABLE THE AIRBAG
SYSTEM. FAILURE TO TAKE THE PROPER PRE-CAUTIONS COULD RESULT IN ACCIDENTAL AIR-
BAG DEPLOYMENT AND POSSIBLE PERSONAL
INJURY.
(1) Check the fused B(+) fuse in the Junction
Block (JB). If OK, go to Step 2. If not OK, repair the
shorted circuit or component and replace the faulty
fuse.
(2) Check for battery voltage at the fused B(+) fuse
in the JB. If OK, go to Step 3. If not OK, repair the
open fused B(+) circuit between the JB and the
Power Distribution Center (PDC).
(3) Disconnect and isolate the battery negative
cable. Disconnect the instrument panel wire harness
connector for the automatic headlamp light sensor/
VTSS indicator from the automatic headlamp light
sensor/VTSS indicator pigtail wire connector. Recon-
nect the battery negative cable. Check for battery
voltage at the fused B(+) circuit cavity of the instru-
ment panel wire harness connector for the automatic
headlamp light sensor/VTSS indicator. If OK, go to
Step 4. If not OK, repair the open fused B(+) circuit
between the VTSS indicator and the JB.
(4) Disconnect and isolate the battery negative
cable. Disconnect the instrument panel wire harness
connector for the JB from the JB connector recepta-
cle. Check for continuity between the VTSS indicator
driver circuit cavity of the instrument panel wire
harness connector for the automatic headlamp light
sensor/VTSS indicator and a good ground. There
should be no continuity. If OK, go to Step 5. If not
OK, repair the shorted VTSS indicator driver circuit
between the VTSS indicator and the JB.
(5) Check for continuity between the VTSS indica-
tor driver circuit of the instrument panel wire har-
ness connector for the automatic headlamp light
sensor/VTSS indicator and the instrument panel wire
harness connector for the JB. There should be conti-
nuity. If OK, replace the faulty VTSS indicator. If not
OK, repair the open VTSS indicator driver circuit
between the VTSS indicator and the JB.
8Q - 16 VEHICLE THEFT SECURITYWJ
VTSS INDICATOR (Continued)