Short to ground JEEP GRAND CHEROKEE 2003 WJ / 2.G Owner's Manual
[x] Cancel search | Manufacturer: JEEP, Model Year: 2003, Model line: GRAND CHEROKEE, Model: JEEP GRAND CHEROKEE 2003 WJ / 2.GPages: 2199, PDF Size: 76.01 MB
Page 391 of 2199
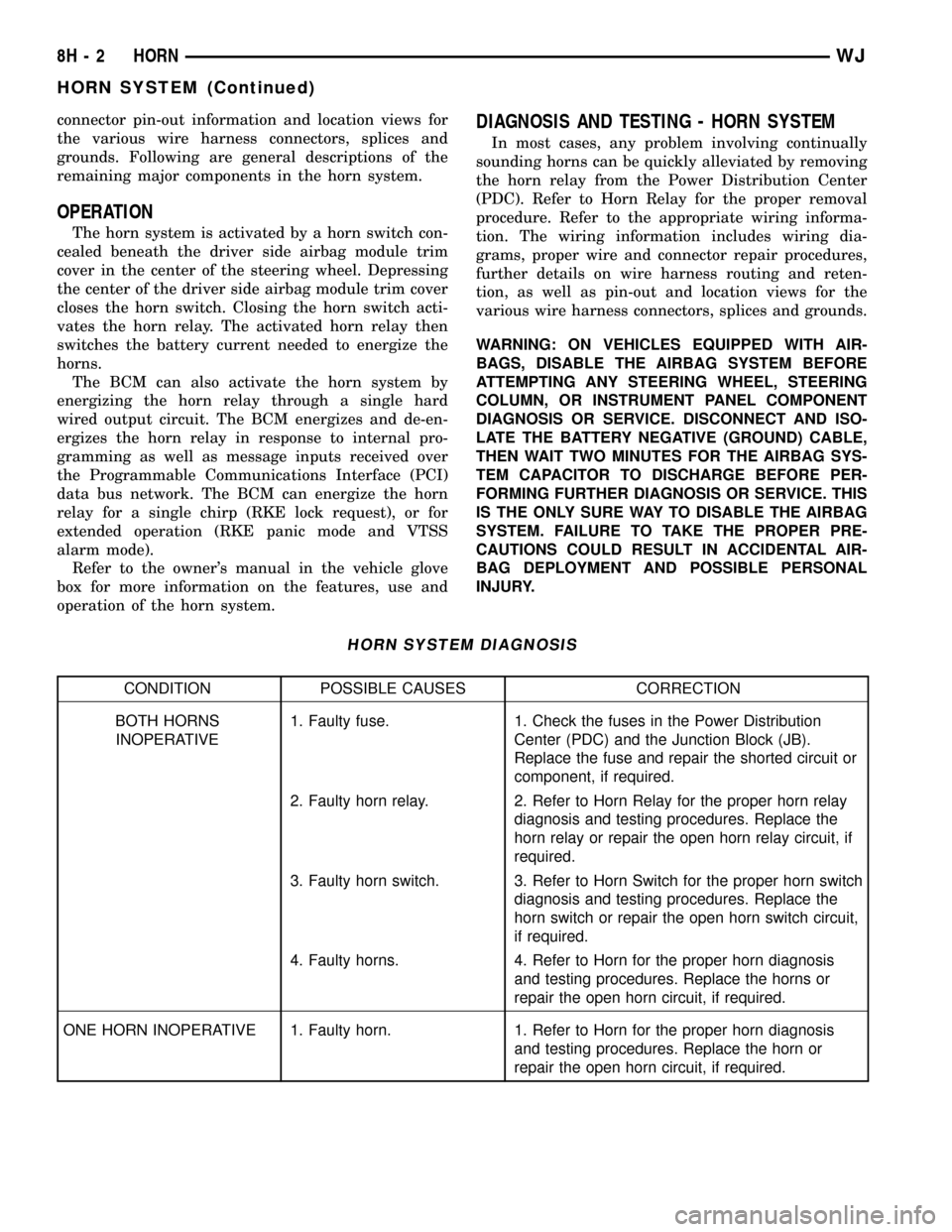
connector pin-out information and location views for
the various wire harness connectors, splices and
grounds. Following are general descriptions of the
remaining major components in the horn system.
OPERATION
The horn system is activated by a horn switch con-
cealed beneath the driver side airbag module trim
cover in the center of the steering wheel. Depressing
the center of the driver side airbag module trim cover
closes the horn switch. Closing the horn switch acti-
vates the horn relay. The activated horn relay then
switches the battery current needed to energize the
horns.
The BCM can also activate the horn system by
energizing the horn relay through a single hard
wired output circuit. The BCM energizes and de-en-
ergizes the horn relay in response to internal pro-
gramming as well as message inputs received over
the Programmable Communications Interface (PCI)
data bus network. The BCM can energize the horn
relay for a single chirp (RKE lock request), or for
extended operation (RKE panic mode and VTSS
alarm mode).
Refer to the owner's manual in the vehicle glove
box for more information on the features, use and
operation of the horn system.
DIAGNOSIS AND TESTING - HORN SYSTEM
In most cases, any problem involving continually
sounding horns can be quickly alleviated by removing
the horn relay from the Power Distribution Center
(PDC). Refer to Horn Relay for the proper removal
procedure. Refer to the appropriate wiring informa-
tion. The wiring information includes wiring dia-
grams, proper wire and connector repair procedures,
further details on wire harness routing and reten-
tion, as well as pin-out and location views for the
various wire harness connectors, splices and grounds.
WARNING: ON VEHICLES EQUIPPED WITH AIR-
BAGS, DISABLE THE AIRBAG SYSTEM BEFORE
ATTEMPTING ANY STEERING WHEEL, STEERING
COLUMN, OR INSTRUMENT PANEL COMPONENT
DIAGNOSIS OR SERVICE. DISCONNECT AND ISO-
LATE THE BATTERY NEGATIVE (GROUND) CABLE,
THEN WAIT TWO MINUTES FOR THE AIRBAG SYS-
TEM CAPACITOR TO DISCHARGE BEFORE PER-
FORMING FURTHER DIAGNOSIS OR SERVICE. THIS
IS THE ONLY SURE WAY TO DISABLE THE AIRBAG
SYSTEM. FAILURE TO TAKE THE PROPER PRE-
CAUTIONS COULD RESULT IN ACCIDENTAL AIR-
BAG DEPLOYMENT AND POSSIBLE PERSONAL
INJURY.
HORN SYSTEM DIAGNOSIS
CONDITION POSSIBLE CAUSES CORRECTION
BOTH HORNS
INOPERATIVE1. Faulty fuse. 1. Check the fuses in the Power Distribution
Center (PDC) and the Junction Block (JB).
Replace the fuse and repair the shorted circuit or
component, if required.
2. Faulty horn relay. 2. Refer to Horn Relay for the proper horn relay
diagnosis and testing procedures. Replace the
horn relay or repair the open horn relay circuit, if
required.
3. Faulty horn switch. 3. Refer to Horn Switch for the proper horn switch
diagnosis and testing procedures. Replace the
horn switch or repair the open horn switch circuit,
if required.
4. Faulty horns. 4. Refer to Horn for the proper horn diagnosis
and testing procedures. Replace the horns or
repair the open horn circuit, if required.
ONE HORN INOPERATIVE 1. Faulty horn. 1. Refer to Horn for the proper horn diagnosis
and testing procedures. Replace the horn or
repair the open horn circuit, if required.
8H - 2 HORNWJ
HORN SYSTEM (Continued)
Page 392 of 2199
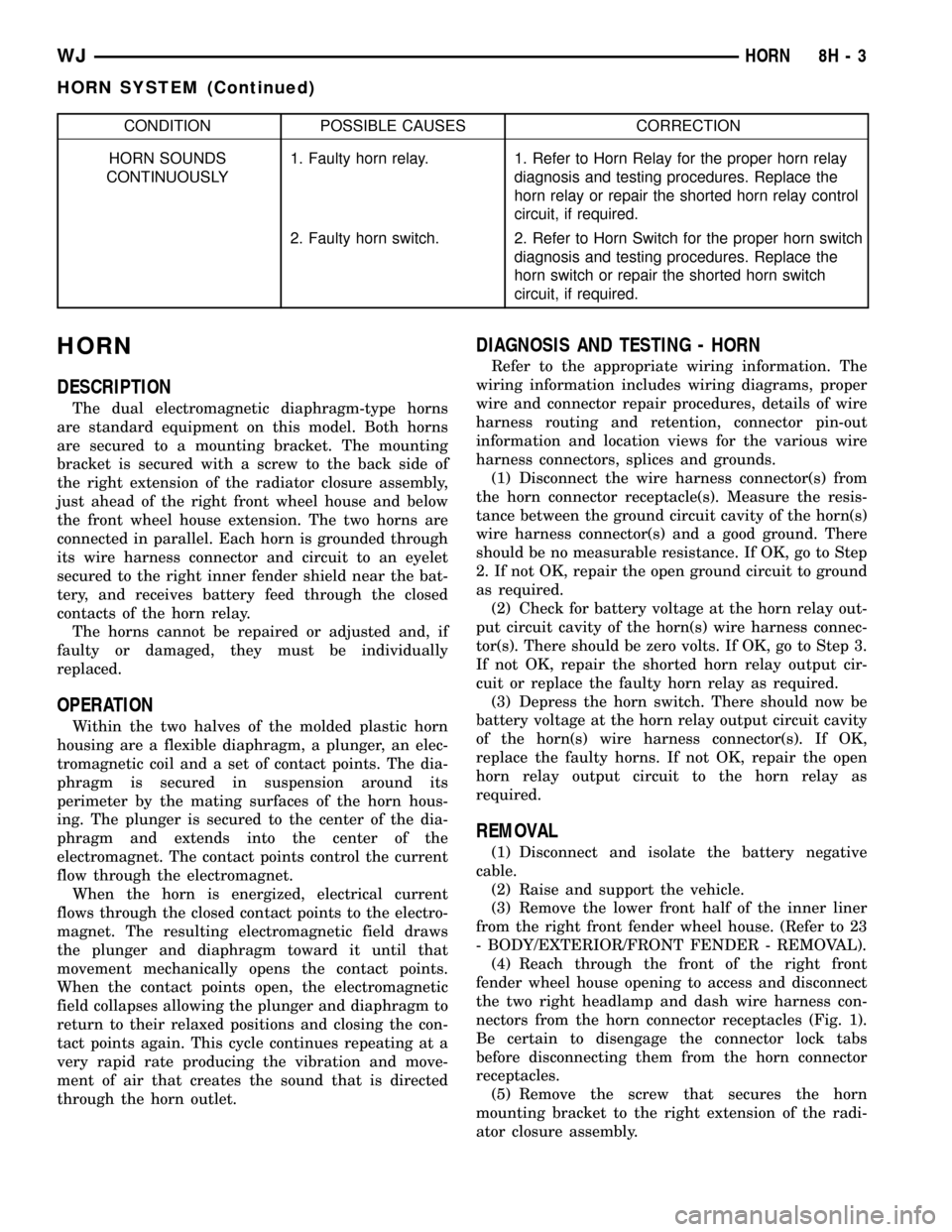
CONDITION POSSIBLE CAUSES CORRECTION
HORN SOUNDS
CONTINUOUSLY1. Faulty horn relay. 1. Refer to Horn Relay for the proper horn relay
diagnosis and testing procedures. Replace the
horn relay or repair the shorted horn relay control
circuit, if required.
2. Faulty horn switch. 2. Refer to Horn Switch for the proper horn switch
diagnosis and testing procedures. Replace the
horn switch or repair the shorted horn switch
circuit, if required.
HORN
DESCRIPTION
The dual electromagnetic diaphragm-type horns
are standard equipment on this model. Both horns
are secured to a mounting bracket. The mounting
bracket is secured with a screw to the back side of
the right extension of the radiator closure assembly,
just ahead of the right front wheel house and below
the front wheel house extension. The two horns are
connected in parallel. Each horn is grounded through
its wire harness connector and circuit to an eyelet
secured to the right inner fender shield near the bat-
tery, and receives battery feed through the closed
contacts of the horn relay.
The horns cannot be repaired or adjusted and, if
faulty or damaged, they must be individually
replaced.
OPERATION
Within the two halves of the molded plastic horn
housing are a flexible diaphragm, a plunger, an elec-
tromagnetic coil and a set of contact points. The dia-
phragm is secured in suspension around its
perimeter by the mating surfaces of the horn hous-
ing. The plunger is secured to the center of the dia-
phragm and extends into the center of the
electromagnet. The contact points control the current
flow through the electromagnet.
When the horn is energized, electrical current
flows through the closed contact points to the electro-
magnet. The resulting electromagnetic field draws
the plunger and diaphragm toward it until that
movement mechanically opens the contact points.
When the contact points open, the electromagnetic
field collapses allowing the plunger and diaphragm to
return to their relaxed positions and closing the con-
tact points again. This cycle continues repeating at a
very rapid rate producing the vibration and move-
ment of air that creates the sound that is directed
through the horn outlet.
DIAGNOSIS AND TESTING - HORN
Refer to the appropriate wiring information. The
wiring information includes wiring diagrams, proper
wire and connector repair procedures, details of wire
harness routing and retention, connector pin-out
information and location views for the various wire
harness connectors, splices and grounds.
(1) Disconnect the wire harness connector(s) from
the horn connector receptacle(s). Measure the resis-
tance between the ground circuit cavity of the horn(s)
wire harness connector(s) and a good ground. There
should be no measurable resistance. If OK, go to Step
2. If not OK, repair the open ground circuit to ground
as required.
(2) Check for battery voltage at the horn relay out-
put circuit cavity of the horn(s) wire harness connec-
tor(s). There should be zero volts. If OK, go to Step 3.
If not OK, repair the shorted horn relay output cir-
cuit or replace the faulty horn relay as required.
(3) Depress the horn switch. There should now be
battery voltage at the horn relay output circuit cavity
of the horn(s) wire harness connector(s). If OK,
replace the faulty horns. If not OK, repair the open
horn relay output circuit to the horn relay as
required.
REMOVAL
(1) Disconnect and isolate the battery negative
cable.
(2) Raise and support the vehicle.
(3) Remove the lower front half of the inner liner
from the right front fender wheel house. (Refer to 23
- BODY/EXTERIOR/FRONT FENDER - REMOVAL).
(4) Reach through the front of the right front
fender wheel house opening to access and disconnect
the two right headlamp and dash wire harness con-
nectors from the horn connector receptacles (Fig. 1).
Be certain to disengage the connector lock tabs
before disconnecting them from the horn connector
receptacles.
(5) Remove the screw that secures the horn
mounting bracket to the right extension of the radi-
ator closure assembly.
WJHORN 8H - 3
HORN SYSTEM (Continued)
Page 395 of 2199
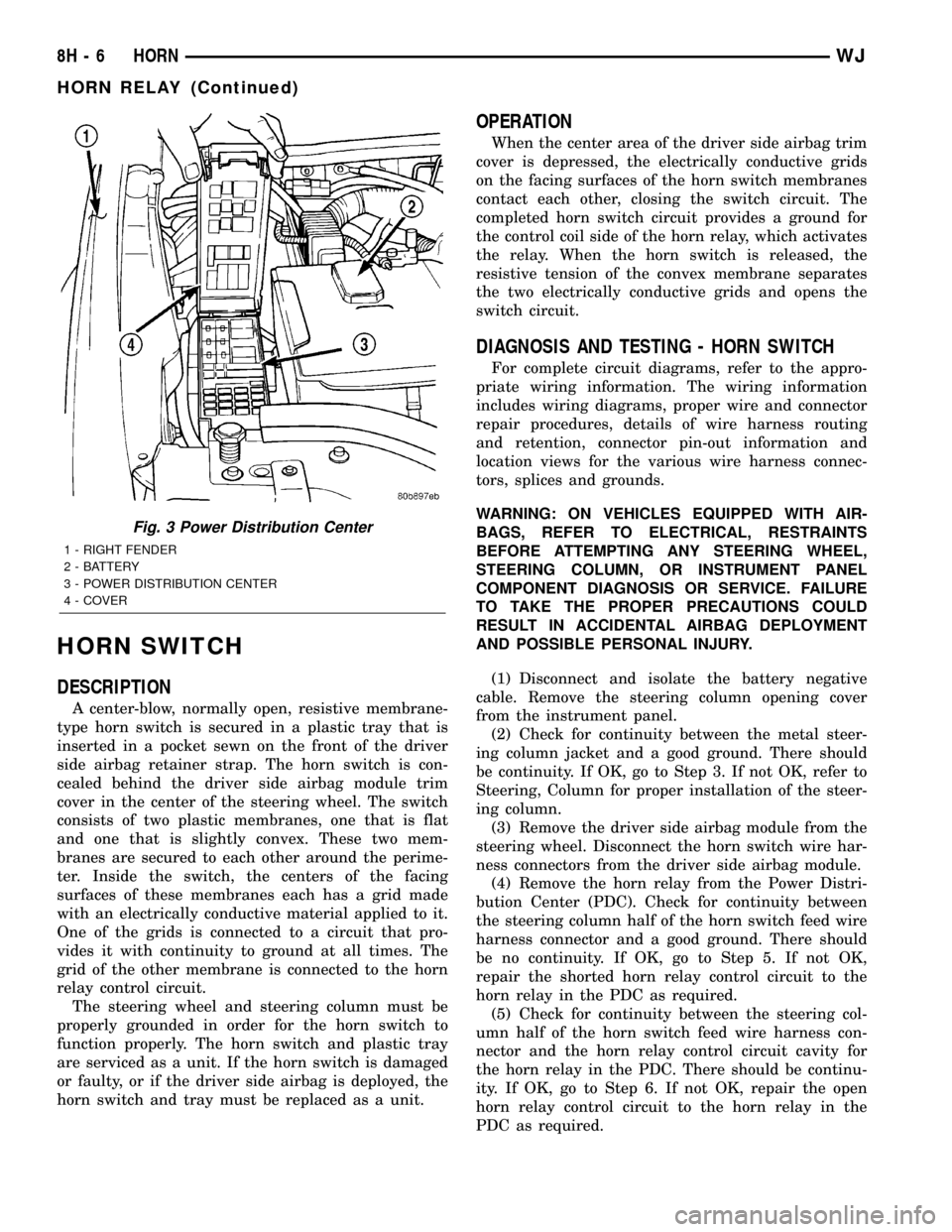
HORN SWITCH
DESCRIPTION
A center-blow, normally open, resistive membrane-
type horn switch is secured in a plastic tray that is
inserted in a pocket sewn on the front of the driver
side airbag retainer strap. The horn switch is con-
cealed behind the driver side airbag module trim
cover in the center of the steering wheel. The switch
consists of two plastic membranes, one that is flat
and one that is slightly convex. These two mem-
branes are secured to each other around the perime-
ter. Inside the switch, the centers of the facing
surfaces of these membranes each has a grid made
with an electrically conductive material applied to it.
One of the grids is connected to a circuit that pro-
vides it with continuity to ground at all times. The
grid of the other membrane is connected to the horn
relay control circuit.
The steering wheel and steering column must be
properly grounded in order for the horn switch to
function properly. The horn switch and plastic tray
are serviced as a unit. If the horn switch is damaged
or faulty, or if the driver side airbag is deployed, the
horn switch and tray must be replaced as a unit.
OPERATION
When the center area of the driver side airbag trim
cover is depressed, the electrically conductive grids
on the facing surfaces of the horn switch membranes
contact each other, closing the switch circuit. The
completed horn switch circuit provides a ground for
the control coil side of the horn relay, which activates
the relay. When the horn switch is released, the
resistive tension of the convex membrane separates
the two electrically conductive grids and opens the
switch circuit.
DIAGNOSIS AND TESTING - HORN SWITCH
For complete circuit diagrams, refer to the appro-
priate wiring information. The wiring information
includes wiring diagrams, proper wire and connector
repair procedures, details of wire harness routing
and retention, connector pin-out information and
location views for the various wire harness connec-
tors, splices and grounds.
WARNING: ON VEHICLES EQUIPPED WITH AIR-
BAGS, REFER TO ELECTRICAL, RESTRAINTS
BEFORE ATTEMPTING ANY STEERING WHEEL,
STEERING COLUMN, OR INSTRUMENT PANEL
COMPONENT DIAGNOSIS OR SERVICE. FAILURE
TO TAKE THE PROPER PRECAUTIONS COULD
RESULT IN ACCIDENTAL AIRBAG DEPLOYMENT
AND POSSIBLE PERSONAL INJURY.
(1) Disconnect and isolate the battery negative
cable. Remove the steering column opening cover
from the instrument panel.
(2) Check for continuity between the metal steer-
ing column jacket and a good ground. There should
be continuity. If OK, go to Step 3. If not OK, refer to
Steering, Column for proper installation of the steer-
ing column.
(3) Remove the driver side airbag module from the
steering wheel. Disconnect the horn switch wire har-
ness connectors from the driver side airbag module.
(4) Remove the horn relay from the Power Distri-
bution Center (PDC). Check for continuity between
the steering column half of the horn switch feed wire
harness connector and a good ground. There should
be no continuity. If OK, go to Step 5. If not OK,
repair the shorted horn relay control circuit to the
horn relay in the PDC as required.
(5) Check for continuity between the steering col-
umn half of the horn switch feed wire harness con-
nector and the horn relay control circuit cavity for
the horn relay in the PDC. There should be continu-
ity. If OK, go to Step 6. If not OK, repair the open
horn relay control circuit to the horn relay in the
PDC as required.
Fig. 3 Power Distribution Center
1 - RIGHT FENDER
2 - BATTERY
3 - POWER DISTRIBUTION CENTER
4 - COVER
8H - 6 HORNWJ
HORN RELAY (Continued)
Page 413 of 2199
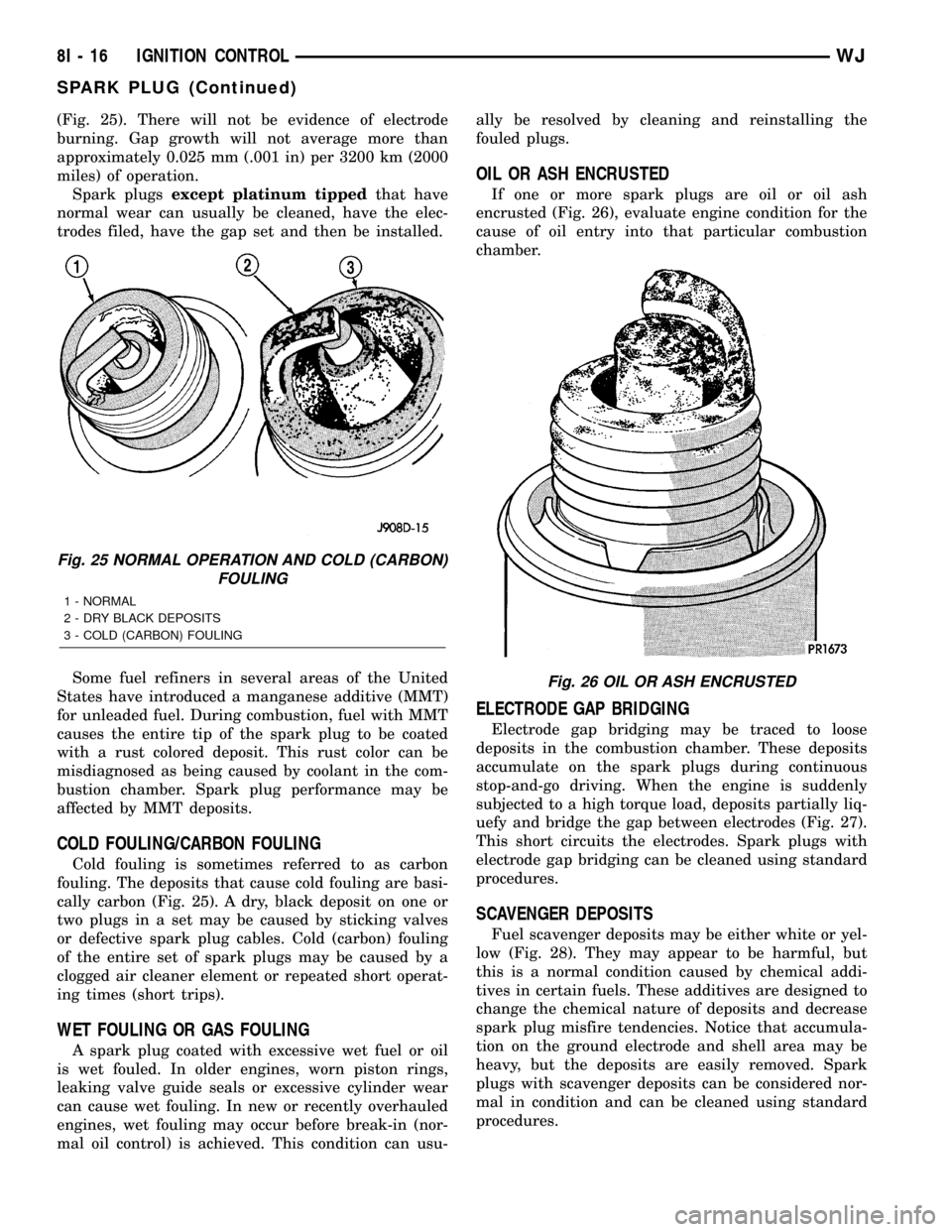
(Fig. 25). There will not be evidence of electrode
burning. Gap growth will not average more than
approximately 0.025 mm (.001 in) per 3200 km (2000
miles) of operation.
Spark plugsexcept platinum tippedthat have
normal wear can usually be cleaned, have the elec-
trodes filed, have the gap set and then be installed.
Some fuel refiners in several areas of the United
States have introduced a manganese additive (MMT)
for unleaded fuel. During combustion, fuel with MMT
causes the entire tip of the spark plug to be coated
with a rust colored deposit. This rust color can be
misdiagnosed as being caused by coolant in the com-
bustion chamber. Spark plug performance may be
affected by MMT deposits.
COLD FOULING/CARBON FOULING
Cold fouling is sometimes referred to as carbon
fouling. The deposits that cause cold fouling are basi-
cally carbon (Fig. 25). A dry, black deposit on one or
two plugs in a set may be caused by sticking valves
or defective spark plug cables. Cold (carbon) fouling
of the entire set of spark plugs may be caused by a
clogged air cleaner element or repeated short operat-
ing times (short trips).
WET FOULING OR GAS FOULING
A spark plug coated with excessive wet fuel or oil
is wet fouled. In older engines, worn piston rings,
leaking valve guide seals or excessive cylinder wear
can cause wet fouling. In new or recently overhauled
engines, wet fouling may occur before break-in (nor-
mal oil control) is achieved. This condition can usu-ally be resolved by cleaning and reinstalling the
fouled plugs.
OIL OR ASH ENCRUSTED
If one or more spark plugs are oil or oil ash
encrusted (Fig. 26), evaluate engine condition for the
cause of oil entry into that particular combustion
chamber.
ELECTRODE GAP BRIDGING
Electrode gap bridging may be traced to loose
deposits in the combustion chamber. These deposits
accumulate on the spark plugs during continuous
stop-and-go driving. When the engine is suddenly
subjected to a high torque load, deposits partially liq-
uefy and bridge the gap between electrodes (Fig. 27).
This short circuits the electrodes. Spark plugs with
electrode gap bridging can be cleaned using standard
procedures.
SCAVENGER DEPOSITS
Fuel scavenger deposits may be either white or yel-
low (Fig. 28). They may appear to be harmful, but
this is a normal condition caused by chemical addi-
tives in certain fuels. These additives are designed to
change the chemical nature of deposits and decrease
spark plug misfire tendencies. Notice that accumula-
tion on the ground electrode and shell area may be
heavy, but the deposits are easily removed. Spark
plugs with scavenger deposits can be considered nor-
mal in condition and can be cleaned using standard
procedures.
Fig. 25 NORMAL OPERATION AND COLD (CARBON)
FOULING
1 - NORMAL
2 - DRY BLACK DEPOSITS
3 - COLD (CARBON) FOULING
Fig. 26 OIL OR ASH ENCRUSTED
8I - 16 IGNITION CONTROLWJ
SPARK PLUG (Continued)
Page 421 of 2199
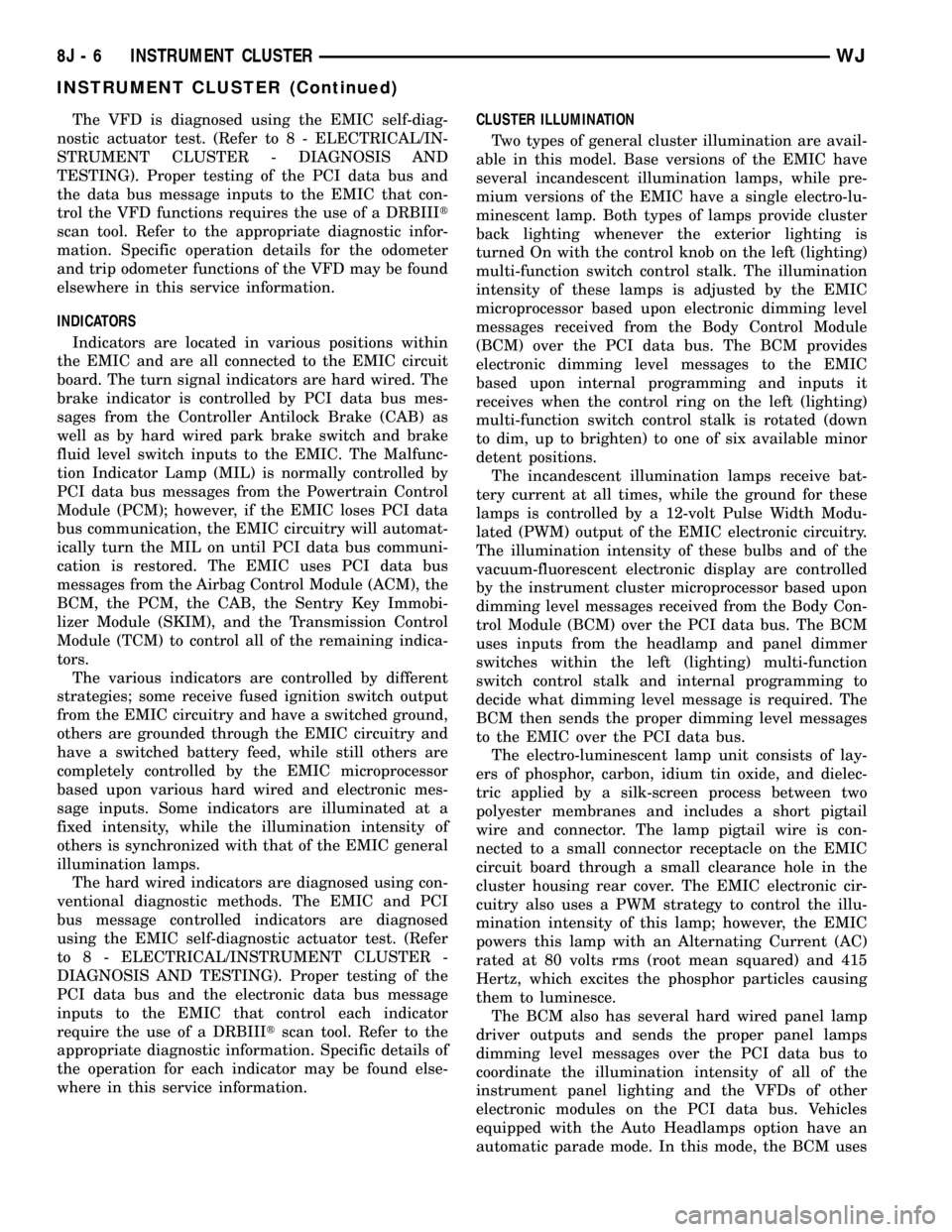
The VFD is diagnosed using the EMIC self-diag-
nostic actuator test. (Refer to 8 - ELECTRICAL/IN-
STRUMENT CLUSTER - DIAGNOSIS AND
TESTING). Proper testing of the PCI data bus and
the data bus message inputs to the EMIC that con-
trol the VFD functions requires the use of a DRBIIIt
scan tool. Refer to the appropriate diagnostic infor-
mation. Specific operation details for the odometer
and trip odometer functions of the VFD may be found
elsewhere in this service information.
INDICATORS
Indicators are located in various positions within
the EMIC and are all connected to the EMIC circuit
board. The turn signal indicators are hard wired. The
brake indicator is controlled by PCI data bus mes-
sages from the Controller Antilock Brake (CAB) as
well as by hard wired park brake switch and brake
fluid level switch inputs to the EMIC. The Malfunc-
tion Indicator Lamp (MIL) is normally controlled by
PCI data bus messages from the Powertrain Control
Module (PCM); however, if the EMIC loses PCI data
bus communication, the EMIC circuitry will automat-
ically turn the MIL on until PCI data bus communi-
cation is restored. The EMIC uses PCI data bus
messages from the Airbag Control Module (ACM), the
BCM, the PCM, the CAB, the Sentry Key Immobi-
lizer Module (SKIM), and the Transmission Control
Module (TCM) to control all of the remaining indica-
tors.
The various indicators are controlled by different
strategies; some receive fused ignition switch output
from the EMIC circuitry and have a switched ground,
others are grounded through the EMIC circuitry and
have a switched battery feed, while still others are
completely controlled by the EMIC microprocessor
based upon various hard wired and electronic mes-
sage inputs. Some indicators are illuminated at a
fixed intensity, while the illumination intensity of
others is synchronized with that of the EMIC general
illumination lamps.
The hard wired indicators are diagnosed using con-
ventional diagnostic methods. The EMIC and PCI
bus message controlled indicators are diagnosed
using the EMIC self-diagnostic actuator test. (Refer
to 8 - ELECTRICAL/INSTRUMENT CLUSTER -
DIAGNOSIS AND TESTING). Proper testing of the
PCI data bus and the electronic data bus message
inputs to the EMIC that control each indicator
require the use of a DRBIIItscan tool. Refer to the
appropriate diagnostic information. Specific details of
the operation for each indicator may be found else-
where in this service information.CLUSTER ILLUMINATION
Two types of general cluster illumination are avail-
able in this model. Base versions of the EMIC have
several incandescent illumination lamps, while pre-
mium versions of the EMIC have a single electro-lu-
minescent lamp. Both types of lamps provide cluster
back lighting whenever the exterior lighting is
turned On with the control knob on the left (lighting)
multi-function switch control stalk. The illumination
intensity of these lamps is adjusted by the EMIC
microprocessor based upon electronic dimming level
messages received from the Body Control Module
(BCM) over the PCI data bus. The BCM provides
electronic dimming level messages to the EMIC
based upon internal programming and inputs it
receives when the control ring on the left (lighting)
multi-function switch control stalk is rotated (down
to dim, up to brighten) to one of six available minor
detent positions.
The incandescent illumination lamps receive bat-
tery current at all times, while the ground for these
lamps is controlled by a 12-volt Pulse Width Modu-
lated (PWM) output of the EMIC electronic circuitry.
The illumination intensity of these bulbs and of the
vacuum-fluorescent electronic display are controlled
by the instrument cluster microprocessor based upon
dimming level messages received from the Body Con-
trol Module (BCM) over the PCI data bus. The BCM
uses inputs from the headlamp and panel dimmer
switches within the left (lighting) multi-function
switch control stalk and internal programming to
decide what dimming level message is required. The
BCM then sends the proper dimming level messages
to the EMIC over the PCI data bus.
The electro-luminescent lamp unit consists of lay-
ers of phosphor, carbon, idium tin oxide, and dielec-
tric applied by a silk-screen process between two
polyester membranes and includes a short pigtail
wire and connector. The lamp pigtail wire is con-
nected to a small connector receptacle on the EMIC
circuit board through a small clearance hole in the
cluster housing rear cover. The EMIC electronic cir-
cuitry also uses a PWM strategy to control the illu-
mination intensity of this lamp; however, the EMIC
powers this lamp with an Alternating Current (AC)
rated at 80 volts rms (root mean squared) and 415
Hertz, which excites the phosphor particles causing
them to luminesce.
The BCM also has several hard wired panel lamp
driver outputs and sends the proper panel lamps
dimming level messages over the PCI data bus to
coordinate the illumination intensity of all of the
instrument panel lighting and the VFDs of other
electronic modules on the PCI data bus. Vehicles
equipped with the Auto Headlamps option have an
automatic parade mode. In this mode, the BCM uses
8J - 6 INSTRUMENT CLUSTERWJ
INSTRUMENT CLUSTER (Continued)
Page 422 of 2199
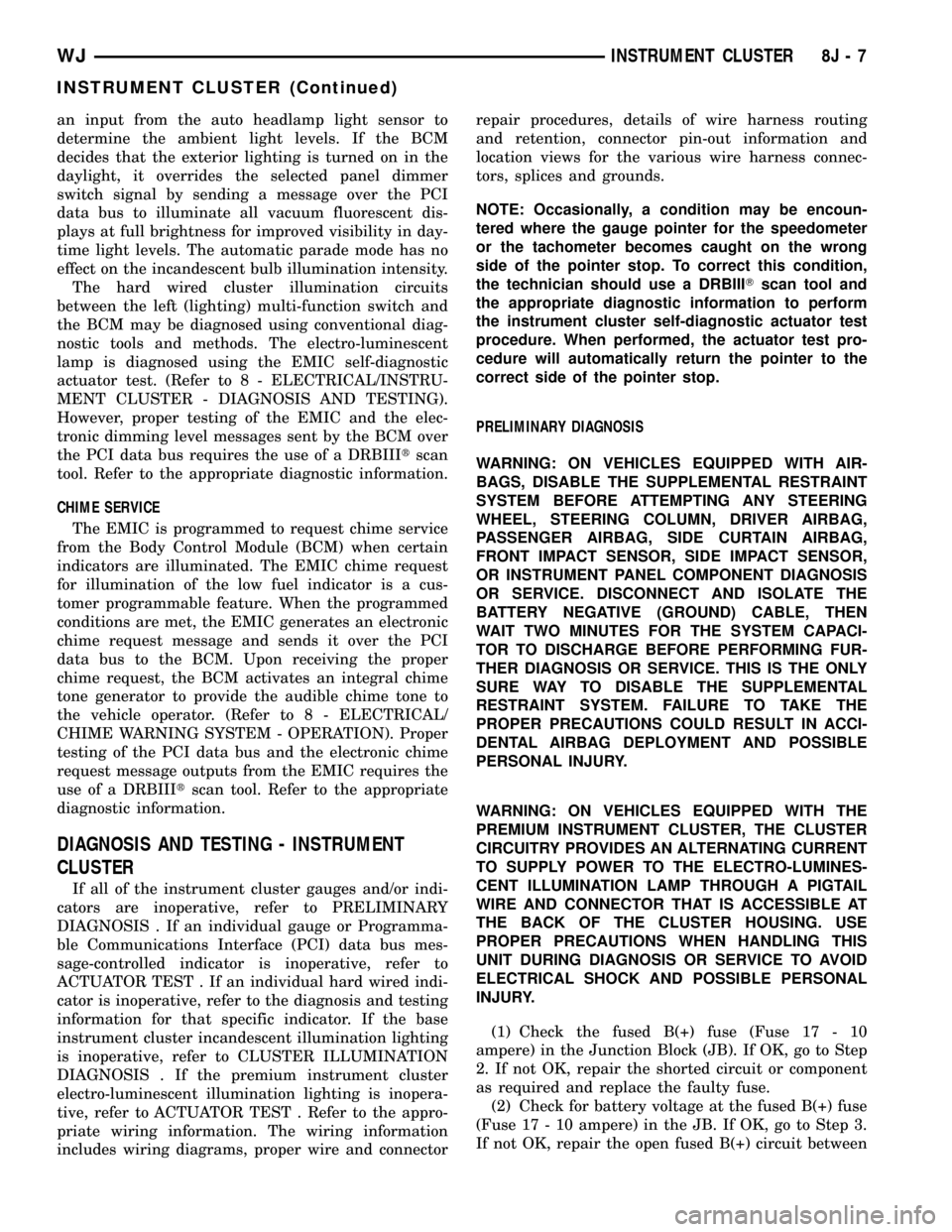
an input from the auto headlamp light sensor to
determine the ambient light levels. If the BCM
decides that the exterior lighting is turned on in the
daylight, it overrides the selected panel dimmer
switch signal by sending a message over the PCI
data bus to illuminate all vacuum fluorescent dis-
plays at full brightness for improved visibility in day-
time light levels. The automatic parade mode has no
effect on the incandescent bulb illumination intensity.
The hard wired cluster illumination circuits
between the left (lighting) multi-function switch and
the BCM may be diagnosed using conventional diag-
nostic tools and methods. The electro-luminescent
lamp is diagnosed using the EMIC self-diagnostic
actuator test. (Refer to 8 - ELECTRICAL/INSTRU-
MENT CLUSTER - DIAGNOSIS AND TESTING).
However, proper testing of the EMIC and the elec-
tronic dimming level messages sent by the BCM over
the PCI data bus requires the use of a DRBIIItscan
tool. Refer to the appropriate diagnostic information.
CHIME SERVICE
The EMIC is programmed to request chime service
from the Body Control Module (BCM) when certain
indicators are illuminated. The EMIC chime request
for illumination of the low fuel indicator is a cus-
tomer programmable feature. When the programmed
conditions are met, the EMIC generates an electronic
chime request message and sends it over the PCI
data bus to the BCM. Upon receiving the proper
chime request, the BCM activates an integral chime
tone generator to provide the audible chime tone to
the vehicle operator. (Refer to 8 - ELECTRICAL/
CHIME WARNING SYSTEM - OPERATION). Proper
testing of the PCI data bus and the electronic chime
request message outputs from the EMIC requires the
use of a DRBIIItscan tool. Refer to the appropriate
diagnostic information.
DIAGNOSIS AND TESTING - INSTRUMENT
CLUSTER
If all of the instrument cluster gauges and/or indi-
cators are inoperative, refer to PRELIMINARY
DIAGNOSIS . If an individual gauge or Programma-
ble Communications Interface (PCI) data bus mes-
sage-controlled indicator is inoperative, refer to
ACTUATOR TEST . If an individual hard wired indi-
cator is inoperative, refer to the diagnosis and testing
information for that specific indicator. If the base
instrument cluster incandescent illumination lighting
is inoperative, refer to CLUSTER ILLUMINATION
DIAGNOSIS . If the premium instrument cluster
electro-luminescent illumination lighting is inopera-
tive, refer to ACTUATOR TEST . Refer to the appro-
priate wiring information. The wiring information
includes wiring diagrams, proper wire and connectorrepair procedures, details of wire harness routing
and retention, connector pin-out information and
location views for the various wire harness connec-
tors, splices and grounds.
NOTE: Occasionally, a condition may be encoun-
tered where the gauge pointer for the speedometer
or the tachometer becomes caught on the wrong
side of the pointer stop. To correct this condition,
the technician should use a DRBIIITscan tool and
the appropriate diagnostic information to perform
the instrument cluster self-diagnostic actuator test
procedure. When performed, the actuator test pro-
cedure will automatically return the pointer to the
correct side of the pointer stop.
PRELIMINARY DIAGNOSIS
WARNING: ON VEHICLES EQUIPPED WITH AIR-
BAGS, DISABLE THE SUPPLEMENTAL RESTRAINT
SYSTEM BEFORE ATTEMPTING ANY STEERING
WHEEL, STEERING COLUMN, DRIVER AIRBAG,
PASSENGER AIRBAG, SIDE CURTAIN AIRBAG,
FRONT IMPACT SENSOR, SIDE IMPACT SENSOR,
OR INSTRUMENT PANEL COMPONENT DIAGNOSIS
OR SERVICE. DISCONNECT AND ISOLATE THE
BATTERY NEGATIVE (GROUND) CABLE, THEN
WAIT TWO MINUTES FOR THE SYSTEM CAPACI-
TOR TO DISCHARGE BEFORE PERFORMING FUR-
THER DIAGNOSIS OR SERVICE. THIS IS THE ONLY
SURE WAY TO DISABLE THE SUPPLEMENTAL
RESTRAINT SYSTEM. FAILURE TO TAKE THE
PROPER PRECAUTIONS COULD RESULT IN ACCI-
DENTAL AIRBAG DEPLOYMENT AND POSSIBLE
PERSONAL INJURY.
WARNING: ON VEHICLES EQUIPPED WITH THE
PREMIUM INSTRUMENT CLUSTER, THE CLUSTER
CIRCUITRY PROVIDES AN ALTERNATING CURRENT
TO SUPPLY POWER TO THE ELECTRO-LUMINES-
CENT ILLUMINATION LAMP THROUGH A PIGTAIL
WIRE AND CONNECTOR THAT IS ACCESSIBLE AT
THE BACK OF THE CLUSTER HOUSING. USE
PROPER PRECAUTIONS WHEN HANDLING THIS
UNIT DURING DIAGNOSIS OR SERVICE TO AVOID
ELECTRICAL SHOCK AND POSSIBLE PERSONAL
INJURY.
(1) Check the fused B(+) fuse (Fuse 17 - 10
ampere) in the Junction Block (JB). If OK, go to Step
2. If not OK, repair the shorted circuit or component
as required and replace the faulty fuse.
(2) Check for battery voltage at the fused B(+) fuse
(Fuse 17 - 10 ampere) in the JB. If OK, go to Step 3.
If not OK, repair the open fused B(+) circuit between
WJINSTRUMENT CLUSTER 8J - 7
INSTRUMENT CLUSTER (Continued)
Page 423 of 2199
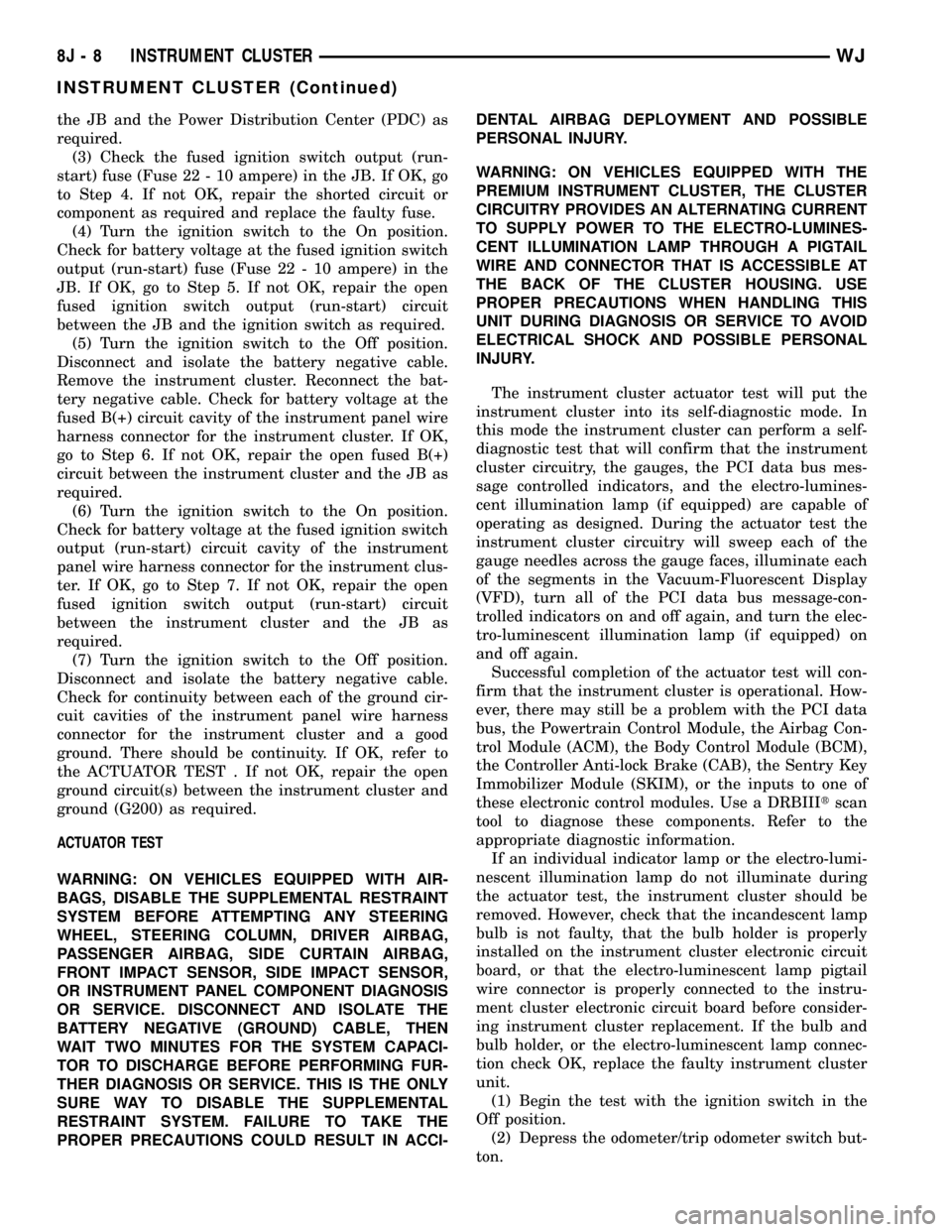
the JB and the Power Distribution Center (PDC) as
required.
(3) Check the fused ignition switch output (run-
start) fuse (Fuse 22 - 10 ampere) in the JB. If OK, go
to Step 4. If not OK, repair the shorted circuit or
component as required and replace the faulty fuse.
(4) Turn the ignition switch to the On position.
Check for battery voltage at the fused ignition switch
output (run-start) fuse (Fuse 22 - 10 ampere) in the
JB. If OK, go to Step 5. If not OK, repair the open
fused ignition switch output (run-start) circuit
between the JB and the ignition switch as required.
(5) Turn the ignition switch to the Off position.
Disconnect and isolate the battery negative cable.
Remove the instrument cluster. Reconnect the bat-
tery negative cable. Check for battery voltage at the
fused B(+) circuit cavity of the instrument panel wire
harness connector for the instrument cluster. If OK,
go to Step 6. If not OK, repair the open fused B(+)
circuit between the instrument cluster and the JB as
required.
(6) Turn the ignition switch to the On position.
Check for battery voltage at the fused ignition switch
output (run-start) circuit cavity of the instrument
panel wire harness connector for the instrument clus-
ter. If OK, go to Step 7. If not OK, repair the open
fused ignition switch output (run-start) circuit
between the instrument cluster and the JB as
required.
(7) Turn the ignition switch to the Off position.
Disconnect and isolate the battery negative cable.
Check for continuity between each of the ground cir-
cuit cavities of the instrument panel wire harness
connector for the instrument cluster and a good
ground. There should be continuity. If OK, refer to
the ACTUATOR TEST . If not OK, repair the open
ground circuit(s) between the instrument cluster and
ground (G200) as required.
ACTUATOR TEST
WARNING: ON VEHICLES EQUIPPED WITH AIR-
BAGS, DISABLE THE SUPPLEMENTAL RESTRAINT
SYSTEM BEFORE ATTEMPTING ANY STEERING
WHEEL, STEERING COLUMN, DRIVER AIRBAG,
PASSENGER AIRBAG, SIDE CURTAIN AIRBAG,
FRONT IMPACT SENSOR, SIDE IMPACT SENSOR,
OR INSTRUMENT PANEL COMPONENT DIAGNOSIS
OR SERVICE. DISCONNECT AND ISOLATE THE
BATTERY NEGATIVE (GROUND) CABLE, THEN
WAIT TWO MINUTES FOR THE SYSTEM CAPACI-
TOR TO DISCHARGE BEFORE PERFORMING FUR-
THER DIAGNOSIS OR SERVICE. THIS IS THE ONLY
SURE WAY TO DISABLE THE SUPPLEMENTAL
RESTRAINT SYSTEM. FAILURE TO TAKE THE
PROPER PRECAUTIONS COULD RESULT IN ACCI-DENTAL AIRBAG DEPLOYMENT AND POSSIBLE
PERSONAL INJURY.
WARNING: ON VEHICLES EQUIPPED WITH THE
PREMIUM INSTRUMENT CLUSTER, THE CLUSTER
CIRCUITRY PROVIDES AN ALTERNATING CURRENT
TO SUPPLY POWER TO THE ELECTRO-LUMINES-
CENT ILLUMINATION LAMP THROUGH A PIGTAIL
WIRE AND CONNECTOR THAT IS ACCESSIBLE AT
THE BACK OF THE CLUSTER HOUSING. USE
PROPER PRECAUTIONS WHEN HANDLING THIS
UNIT DURING DIAGNOSIS OR SERVICE TO AVOID
ELECTRICAL SHOCK AND POSSIBLE PERSONAL
INJURY.
The instrument cluster actuator test will put the
instrument cluster into its self-diagnostic mode. In
this mode the instrument cluster can perform a self-
diagnostic test that will confirm that the instrument
cluster circuitry, the gauges, the PCI data bus mes-
sage controlled indicators, and the electro-lumines-
cent illumination lamp (if equipped) are capable of
operating as designed. During the actuator test the
instrument cluster circuitry will sweep each of the
gauge needles across the gauge faces, illuminate each
of the segments in the Vacuum-Fluorescent Display
(VFD), turn all of the PCI data bus message-con-
trolled indicators on and off again, and turn the elec-
tro-luminescent illumination lamp (if equipped) on
and off again.
Successful completion of the actuator test will con-
firm that the instrument cluster is operational. How-
ever, there may still be a problem with the PCI data
bus, the Powertrain Control Module, the Airbag Con-
trol Module (ACM), the Body Control Module (BCM),
the Controller Anti-lock Brake (CAB), the Sentry Key
Immobilizer Module (SKIM), or the inputs to one of
these electronic control modules. Use a DRBIIItscan
tool to diagnose these components. Refer to the
appropriate diagnostic information.
If an individual indicator lamp or the electro-lumi-
nescent illumination lamp do not illuminate during
the actuator test, the instrument cluster should be
removed. However, check that the incandescent lamp
bulb is not faulty, that the bulb holder is properly
installed on the instrument cluster electronic circuit
board, or that the electro-luminescent lamp pigtail
wire connector is properly connected to the instru-
ment cluster electronic circuit board before consider-
ing instrument cluster replacement. If the bulb and
bulb holder, or the electro-luminescent lamp connec-
tion check OK, replace the faulty instrument cluster
unit.
(1) Begin the test with the ignition switch in the
Off position.
(2) Depress the odometer/trip odometer switch but-
ton.
8J - 8 INSTRUMENT CLUSTERWJ
INSTRUMENT CLUSTER (Continued)
Page 429 of 2199
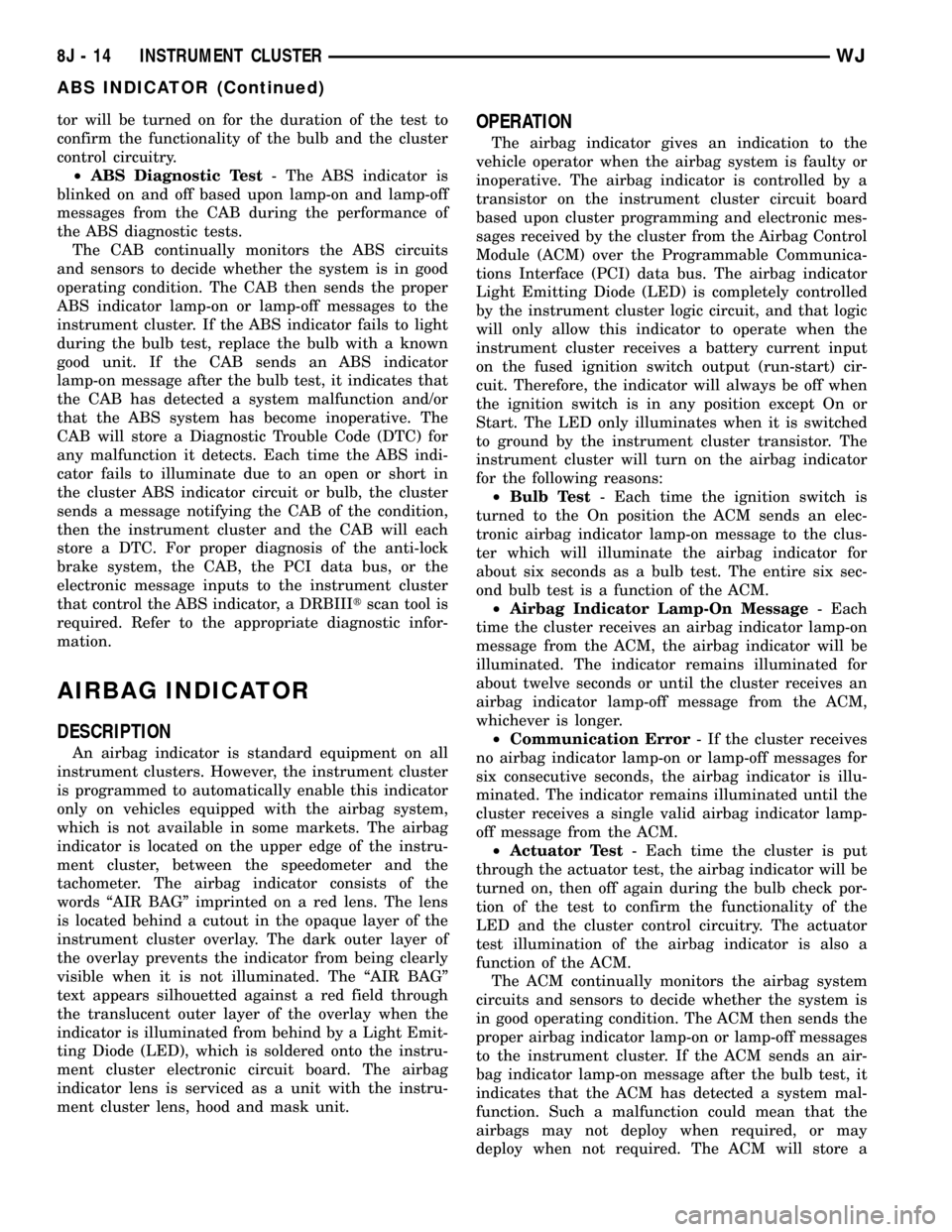
tor will be turned on for the duration of the test to
confirm the functionality of the bulb and the cluster
control circuitry.
²ABS Diagnostic Test- The ABS indicator is
blinked on and off based upon lamp-on and lamp-off
messages from the CAB during the performance of
the ABS diagnostic tests.
The CAB continually monitors the ABS circuits
and sensors to decide whether the system is in good
operating condition. The CAB then sends the proper
ABS indicator lamp-on or lamp-off messages to the
instrument cluster. If the ABS indicator fails to light
during the bulb test, replace the bulb with a known
good unit. If the CAB sends an ABS indicator
lamp-on message after the bulb test, it indicates that
the CAB has detected a system malfunction and/or
that the ABS system has become inoperative. The
CAB will store a Diagnostic Trouble Code (DTC) for
any malfunction it detects. Each time the ABS indi-
cator fails to illuminate due to an open or short in
the cluster ABS indicator circuit or bulb, the cluster
sends a message notifying the CAB of the condition,
then the instrument cluster and the CAB will each
store a DTC. For proper diagnosis of the anti-lock
brake system, the CAB, the PCI data bus, or the
electronic message inputs to the instrument cluster
that control the ABS indicator, a DRBIIItscan tool is
required. Refer to the appropriate diagnostic infor-
mation.
AIRBAG INDICATOR
DESCRIPTION
An airbag indicator is standard equipment on all
instrument clusters. However, the instrument cluster
is programmed to automatically enable this indicator
only on vehicles equipped with the airbag system,
which is not available in some markets. The airbag
indicator is located on the upper edge of the instru-
ment cluster, between the speedometer and the
tachometer. The airbag indicator consists of the
words ªAIR BAGº imprinted on a red lens. The lens
is located behind a cutout in the opaque layer of the
instrument cluster overlay. The dark outer layer of
the overlay prevents the indicator from being clearly
visible when it is not illuminated. The ªAIR BAGº
text appears silhouetted against a red field through
the translucent outer layer of the overlay when the
indicator is illuminated from behind by a Light Emit-
ting Diode (LED), which is soldered onto the instru-
ment cluster electronic circuit board. The airbag
indicator lens is serviced as a unit with the instru-
ment cluster lens, hood and mask unit.
OPERATION
The airbag indicator gives an indication to the
vehicle operator when the airbag system is faulty or
inoperative. The airbag indicator is controlled by a
transistor on the instrument cluster circuit board
based upon cluster programming and electronic mes-
sages received by the cluster from the Airbag Control
Module (ACM) over the Programmable Communica-
tions Interface (PCI) data bus. The airbag indicator
Light Emitting Diode (LED) is completely controlled
by the instrument cluster logic circuit, and that logic
will only allow this indicator to operate when the
instrument cluster receives a battery current input
on the fused ignition switch output (run-start) cir-
cuit. Therefore, the indicator will always be off when
the ignition switch is in any position except On or
Start. The LED only illuminates when it is switched
to ground by the instrument cluster transistor. The
instrument cluster will turn on the airbag indicator
for the following reasons:
²Bulb Test- Each time the ignition switch is
turned to the On position the ACM sends an elec-
tronic airbag indicator lamp-on message to the clus-
ter which will illuminate the airbag indicator for
about six seconds as a bulb test. The entire six sec-
ond bulb test is a function of the ACM.
²Airbag Indicator Lamp-On Message- Each
time the cluster receives an airbag indicator lamp-on
message from the ACM, the airbag indicator will be
illuminated. The indicator remains illuminated for
about twelve seconds or until the cluster receives an
airbag indicator lamp-off message from the ACM,
whichever is longer.
²Communication Error- If the cluster receives
no airbag indicator lamp-on or lamp-off messages for
six consecutive seconds, the airbag indicator is illu-
minated. The indicator remains illuminated until the
cluster receives a single valid airbag indicator lamp-
off message from the ACM.
²Actuator Test- Each time the cluster is put
through the actuator test, the airbag indicator will be
turned on, then off again during the bulb check por-
tion of the test to confirm the functionality of the
LED and the cluster control circuitry. The actuator
test illumination of the airbag indicator is also a
function of the ACM.
The ACM continually monitors the airbag system
circuits and sensors to decide whether the system is
in good operating condition. The ACM then sends the
proper airbag indicator lamp-on or lamp-off messages
to the instrument cluster. If the ACM sends an air-
bag indicator lamp-on message after the bulb test, it
indicates that the ACM has detected a system mal-
function. Such a malfunction could mean that the
airbags may not deploy when required, or may
deploy when not required. The ACM will store a
8J - 14 INSTRUMENT CLUSTERWJ
ABS INDICATOR (Continued)
Page 430 of 2199
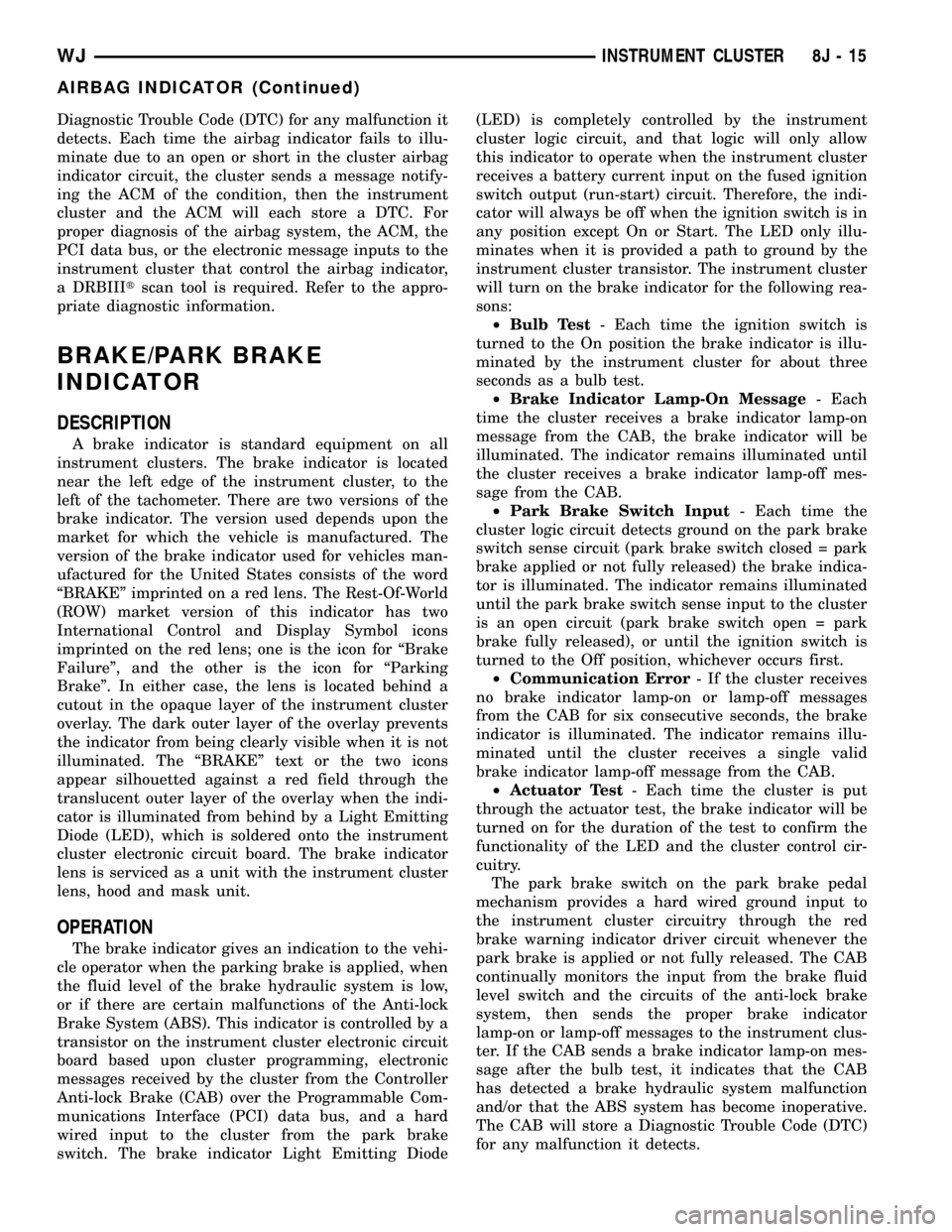
Diagnostic Trouble Code (DTC) for any malfunction it
detects. Each time the airbag indicator fails to illu-
minate due to an open or short in the cluster airbag
indicator circuit, the cluster sends a message notify-
ing the ACM of the condition, then the instrument
cluster and the ACM will each store a DTC. For
proper diagnosis of the airbag system, the ACM, the
PCI data bus, or the electronic message inputs to the
instrument cluster that control the airbag indicator,
a DRBIIItscan tool is required. Refer to the appro-
priate diagnostic information.
BRAKE/PARK BRAKE
INDICATOR
DESCRIPTION
A brake indicator is standard equipment on all
instrument clusters. The brake indicator is located
near the left edge of the instrument cluster, to the
left of the tachometer. There are two versions of the
brake indicator. The version used depends upon the
market for which the vehicle is manufactured. The
version of the brake indicator used for vehicles man-
ufactured for the United States consists of the word
ªBRAKEº imprinted on a red lens. The Rest-Of-World
(ROW) market version of this indicator has two
International Control and Display Symbol icons
imprinted on the red lens; one is the icon for ªBrake
Failureº, and the other is the icon for ªParking
Brakeº. In either case, the lens is located behind a
cutout in the opaque layer of the instrument cluster
overlay. The dark outer layer of the overlay prevents
the indicator from being clearly visible when it is not
illuminated. The ªBRAKEº text or the two icons
appear silhouetted against a red field through the
translucent outer layer of the overlay when the indi-
cator is illuminated from behind by a Light Emitting
Diode (LED), which is soldered onto the instrument
cluster electronic circuit board. The brake indicator
lens is serviced as a unit with the instrument cluster
lens, hood and mask unit.
OPERATION
The brake indicator gives an indication to the vehi-
cle operator when the parking brake is applied, when
the fluid level of the brake hydraulic system is low,
or if there are certain malfunctions of the Anti-lock
Brake System (ABS). This indicator is controlled by a
transistor on the instrument cluster electronic circuit
board based upon cluster programming, electronic
messages received by the cluster from the Controller
Anti-lock Brake (CAB) over the Programmable Com-
munications Interface (PCI) data bus, and a hard
wired input to the cluster from the park brake
switch. The brake indicator Light Emitting Diode(LED) is completely controlled by the instrument
cluster logic circuit, and that logic will only allow
this indicator to operate when the instrument cluster
receives a battery current input on the fused ignition
switch output (run-start) circuit. Therefore, the indi-
cator will always be off when the ignition switch is in
any position except On or Start. The LED only illu-
minates when it is provided a path to ground by the
instrument cluster transistor. The instrument cluster
will turn on the brake indicator for the following rea-
sons:
²Bulb Test- Each time the ignition switch is
turned to the On position the brake indicator is illu-
minated by the instrument cluster for about three
seconds as a bulb test.
²Brake Indicator Lamp-On Message- Each
time the cluster receives a brake indicator lamp-on
message from the CAB, the brake indicator will be
illuminated. The indicator remains illuminated until
the cluster receives a brake indicator lamp-off mes-
sage from the CAB.
²Park Brake Switch Input- Each time the
cluster logic circuit detects ground on the park brake
switch sense circuit (park brake switch closed = park
brake applied or not fully released) the brake indica-
tor is illuminated. The indicator remains illuminated
until the park brake switch sense input to the cluster
is an open circuit (park brake switch open = park
brake fully released), or until the ignition switch is
turned to the Off position, whichever occurs first.
²Communication Error- If the cluster receives
no brake indicator lamp-on or lamp-off messages
from the CAB for six consecutive seconds, the brake
indicator is illuminated. The indicator remains illu-
minated until the cluster receives a single valid
brake indicator lamp-off message from the CAB.
²Actuator Test- Each time the cluster is put
through the actuator test, the brake indicator will be
turned on for the duration of the test to confirm the
functionality of the LED and the cluster control cir-
cuitry.
The park brake switch on the park brake pedal
mechanism provides a hard wired ground input to
the instrument cluster circuitry through the red
brake warning indicator driver circuit whenever the
park brake is applied or not fully released. The CAB
continually monitors the input from the brake fluid
level switch and the circuits of the anti-lock brake
system, then sends the proper brake indicator
lamp-on or lamp-off messages to the instrument clus-
ter. If the CAB sends a brake indicator lamp-on mes-
sage after the bulb test, it indicates that the CAB
has detected a brake hydraulic system malfunction
and/or that the ABS system has become inoperative.
The CAB will store a Diagnostic Trouble Code (DTC)
for any malfunction it detects.
WJINSTRUMENT CLUSTER 8J - 15
AIRBAG INDICATOR (Continued)
Page 431 of 2199
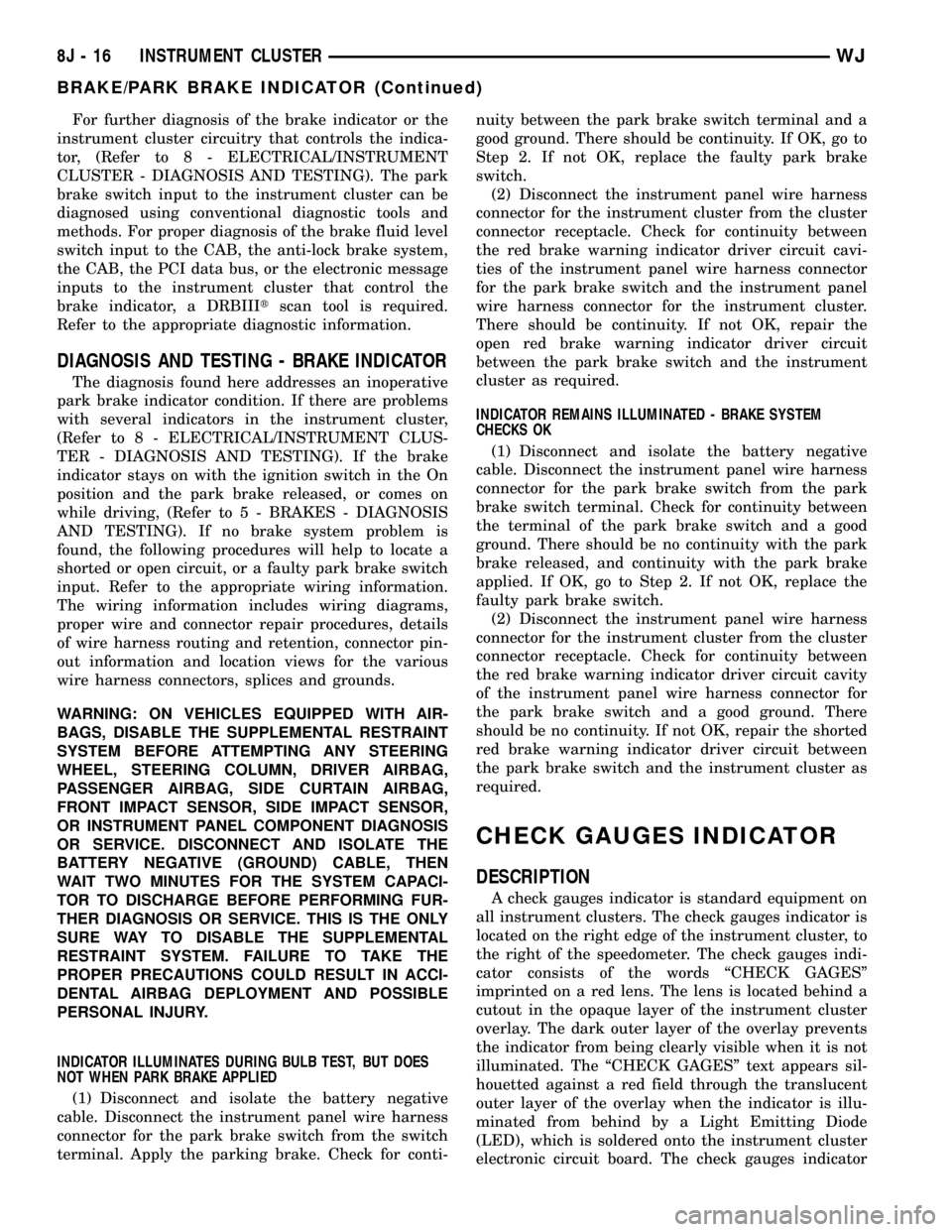
For further diagnosis of the brake indicator or the
instrument cluster circuitry that controls the indica-
tor, (Refer to 8 - ELECTRICAL/INSTRUMENT
CLUSTER - DIAGNOSIS AND TESTING). The park
brake switch input to the instrument cluster can be
diagnosed using conventional diagnostic tools and
methods. For proper diagnosis of the brake fluid level
switch input to the CAB, the anti-lock brake system,
the CAB, the PCI data bus, or the electronic message
inputs to the instrument cluster that control the
brake indicator, a DRBIIItscan tool is required.
Refer to the appropriate diagnostic information.
DIAGNOSIS AND TESTING - BRAKE INDICATOR
The diagnosis found here addresses an inoperative
park brake indicator condition. If there are problems
with several indicators in the instrument cluster,
(Refer to 8 - ELECTRICAL/INSTRUMENT CLUS-
TER - DIAGNOSIS AND TESTING). If the brake
indicator stays on with the ignition switch in the On
position and the park brake released, or comes on
while driving, (Refer to 5 - BRAKES - DIAGNOSIS
AND TESTING). If no brake system problem is
found, the following procedures will help to locate a
shorted or open circuit, or a faulty park brake switch
input. Refer to the appropriate wiring information.
The wiring information includes wiring diagrams,
proper wire and connector repair procedures, details
of wire harness routing and retention, connector pin-
out information and location views for the various
wire harness connectors, splices and grounds.
WARNING: ON VEHICLES EQUIPPED WITH AIR-
BAGS, DISABLE THE SUPPLEMENTAL RESTRAINT
SYSTEM BEFORE ATTEMPTING ANY STEERING
WHEEL, STEERING COLUMN, DRIVER AIRBAG,
PASSENGER AIRBAG, SIDE CURTAIN AIRBAG,
FRONT IMPACT SENSOR, SIDE IMPACT SENSOR,
OR INSTRUMENT PANEL COMPONENT DIAGNOSIS
OR SERVICE. DISCONNECT AND ISOLATE THE
BATTERY NEGATIVE (GROUND) CABLE, THEN
WAIT TWO MINUTES FOR THE SYSTEM CAPACI-
TOR TO DISCHARGE BEFORE PERFORMING FUR-
THER DIAGNOSIS OR SERVICE. THIS IS THE ONLY
SURE WAY TO DISABLE THE SUPPLEMENTAL
RESTRAINT SYSTEM. FAILURE TO TAKE THE
PROPER PRECAUTIONS COULD RESULT IN ACCI-
DENTAL AIRBAG DEPLOYMENT AND POSSIBLE
PERSONAL INJURY.
INDICATOR ILLUMINATES DURING BULB TEST, BUT DOES
NOT WHEN PARK BRAKE APPLIED
(1) Disconnect and isolate the battery negative
cable. Disconnect the instrument panel wire harness
connector for the park brake switch from the switch
terminal. Apply the parking brake. Check for conti-nuity between the park brake switch terminal and a
good ground. There should be continuity. If OK, go to
Step 2. If not OK, replace the faulty park brake
switch.
(2) Disconnect the instrument panel wire harness
connector for the instrument cluster from the cluster
connector receptacle. Check for continuity between
the red brake warning indicator driver circuit cavi-
ties of the instrument panel wire harness connector
for the park brake switch and the instrument panel
wire harness connector for the instrument cluster.
There should be continuity. If not OK, repair the
open red brake warning indicator driver circuit
between the park brake switch and the instrument
cluster as required.
INDICATOR REMAINS ILLUMINATED - BRAKE SYSTEM
CHECKS OK
(1) Disconnect and isolate the battery negative
cable. Disconnect the instrument panel wire harness
connector for the park brake switch from the park
brake switch terminal. Check for continuity between
the terminal of the park brake switch and a good
ground. There should be no continuity with the park
brake released, and continuity with the park brake
applied. If OK, go to Step 2. If not OK, replace the
faulty park brake switch.
(2) Disconnect the instrument panel wire harness
connector for the instrument cluster from the cluster
connector receptacle. Check for continuity between
the red brake warning indicator driver circuit cavity
of the instrument panel wire harness connector for
the park brake switch and a good ground. There
should be no continuity. If not OK, repair the shorted
red brake warning indicator driver circuit between
the park brake switch and the instrument cluster as
required.
CHECK GAUGES INDICATOR
DESCRIPTION
A check gauges indicator is standard equipment on
all instrument clusters. The check gauges indicator is
located on the right edge of the instrument cluster, to
the right of the speedometer. The check gauges indi-
cator consists of the words ªCHECK GAGESº
imprinted on a red lens. The lens is located behind a
cutout in the opaque layer of the instrument cluster
overlay. The dark outer layer of the overlay prevents
the indicator from being clearly visible when it is not
illuminated. The ªCHECK GAGESº text appears sil-
houetted against a red field through the translucent
outer layer of the overlay when the indicator is illu-
minated from behind by a Light Emitting Diode
(LED), which is soldered onto the instrument cluster
electronic circuit board. The check gauges indicator
8J - 16 INSTRUMENT CLUSTERWJ
BRAKE/PARK BRAKE INDICATOR (Continued)