radiator fan JEEP LIBERTY 2002 KJ / 1.G Workshop Manual
[x] Cancel search | Manufacturer: JEEP, Model Year: 2002, Model line: LIBERTY, Model: JEEP LIBERTY 2002 KJ / 1.GPages: 1803, PDF Size: 62.3 MB
Page 15 of 1803
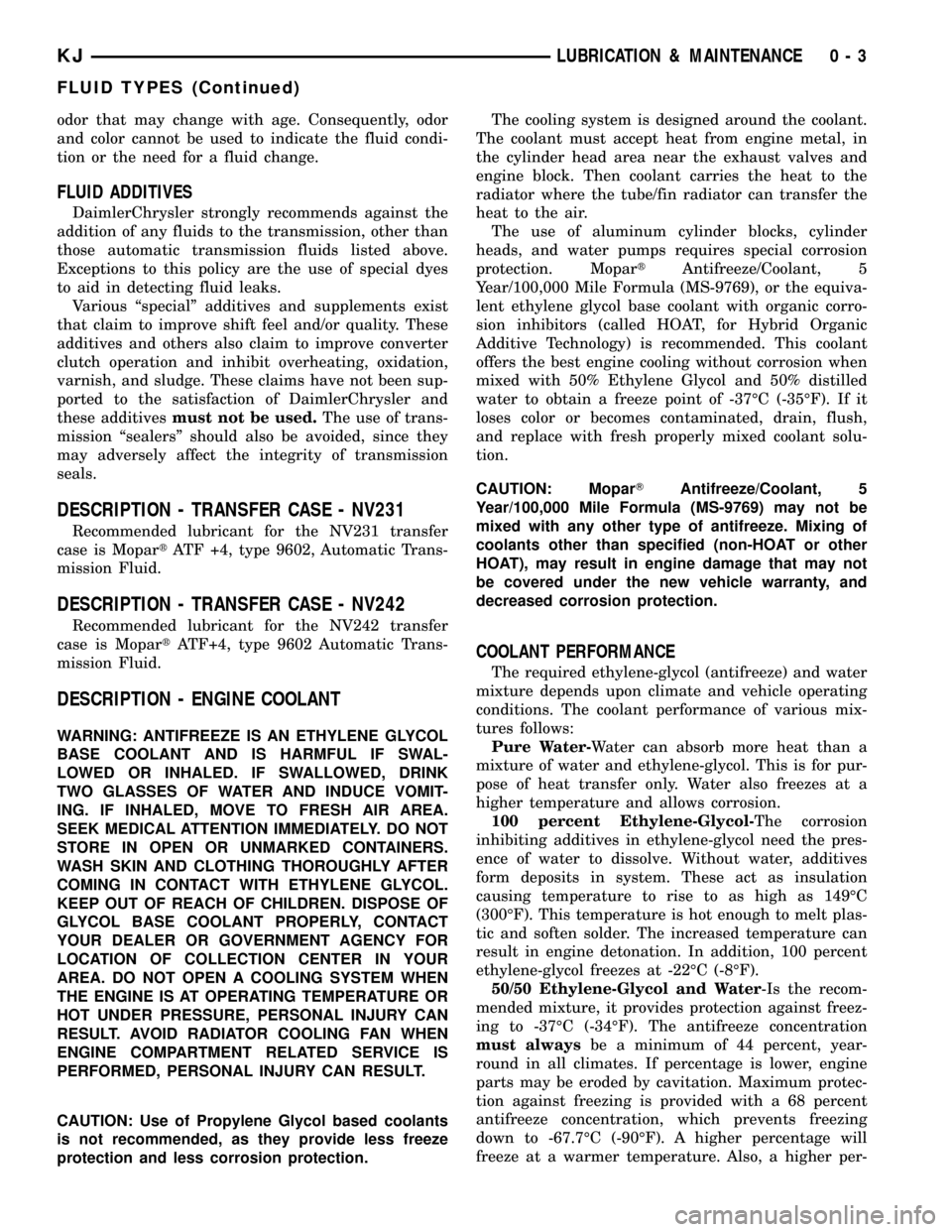
odor that may change with age. Consequently, odor
and color cannot be used to indicate the fluid condi-
tion or the need for a fluid change.
FLUID ADDITIVES
DaimlerChrysler strongly recommends against the
addition of any fluids to the transmission, other than
those automatic transmission fluids listed above.
Exceptions to this policy are the use of special dyes
to aid in detecting fluid leaks.
Various ªspecialº additives and supplements exist
that claim to improve shift feel and/or quality. These
additives and others also claim to improve converter
clutch operation and inhibit overheating, oxidation,
varnish, and sludge. These claims have not been sup-
ported to the satisfaction of DaimlerChrysler and
these additivesmust not be used.The use of trans-
mission ªsealersº should also be avoided, since they
may adversely affect the integrity of transmission
seals.
DESCRIPTION - TRANSFER CASE - NV231
Recommended lubricant for the NV231 transfer
case is MopartATF +4, type 9602, Automatic Trans-
mission Fluid.
DESCRIPTION - TRANSFER CASE - NV242
Recommended lubricant for the NV242 transfer
case is MopartATF+4, type 9602 Automatic Trans-
mission Fluid.
DESCRIPTION - ENGINE COOLANT
WARNING: ANTIFREEZE IS AN ETHYLENE GLYCOL
BASE COOLANT AND IS HARMFUL IF SWAL-
LOWED OR INHALED. IF SWALLOWED, DRINK
TWO GLASSES OF WATER AND INDUCE VOMIT-
ING. IF INHALED, MOVE TO FRESH AIR AREA.
SEEK MEDICAL ATTENTION IMMEDIATELY. DO NOT
STORE IN OPEN OR UNMARKED CONTAINERS.
WASH SKIN AND CLOTHING THOROUGHLY AFTER
COMING IN CONTACT WITH ETHYLENE GLYCOL.
KEEP OUT OF REACH OF CHILDREN. DISPOSE OF
GLYCOL BASE COOLANT PROPERLY, CONTACT
YOUR DEALER OR GOVERNMENT AGENCY FOR
LOCATION OF COLLECTION CENTER IN YOUR
AREA. DO NOT OPEN A COOLING SYSTEM WHEN
THE ENGINE IS AT OPERATING TEMPERATURE OR
HOT UNDER PRESSURE, PERSONAL INJURY CAN
RESULT. AVOID RADIATOR COOLING FAN WHEN
ENGINE COMPARTMENT RELATED SERVICE IS
PERFORMED, PERSONAL INJURY CAN RESULT.
CAUTION: Use of Propylene Glycol based coolants
is not recommended, as they provide less freeze
protection and less corrosion protection.The cooling system is designed around the coolant.
The coolant must accept heat from engine metal, in
the cylinder head area near the exhaust valves and
engine block. Then coolant carries the heat to the
radiator where the tube/fin radiator can transfer the
heat to the air.
The use of aluminum cylinder blocks, cylinder
heads, and water pumps requires special corrosion
protection. MopartAntifreeze/Coolant, 5
Year/100,000 Mile Formula (MS-9769), or the equiva-
lent ethylene glycol base coolant with organic corro-
sion inhibitors (called HOAT, for Hybrid Organic
Additive Technology) is recommended. This coolant
offers the best engine cooling without corrosion when
mixed with 50% Ethylene Glycol and 50% distilled
water to obtain a freeze point of -37ÉC (-35ÉF). If it
loses color or becomes contaminated, drain, flush,
and replace with fresh properly mixed coolant solu-
tion.
CAUTION: MoparTAntifreeze/Coolant, 5
Year/100,000 Mile Formula (MS-9769) may not be
mixed with any other type of antifreeze. Mixing of
coolants other than specified (non-HOAT or other
HOAT), may result in engine damage that may not
be covered under the new vehicle warranty, and
decreased corrosion protection.
COOLANT PERFORMANCE
The required ethylene-glycol (antifreeze) and water
mixture depends upon climate and vehicle operating
conditions. The coolant performance of various mix-
tures follows:
Pure Water-Water can absorb more heat than a
mixture of water and ethylene-glycol. This is for pur-
pose of heat transfer only. Water also freezes at a
higher temperature and allows corrosion.
100 percent Ethylene-Glycol-The corrosion
inhibiting additives in ethylene-glycol need the pres-
ence of water to dissolve. Without water, additives
form deposits in system. These act as insulation
causing temperature to rise to as high as 149ÉC
(300ÉF). This temperature is hot enough to melt plas-
tic and soften solder. The increased temperature can
result in engine detonation. In addition, 100 percent
ethylene-glycol freezes at -22ÉC (-8ÉF).
50/50 Ethylene-Glycol and Water-Is the recom-
mended mixture, it provides protection against freez-
ing to -37ÉC (-34ÉF). The antifreeze concentration
must alwaysbe a minimum of 44 percent, year-
round in all climates. If percentage is lower, engine
parts may be eroded by cavitation. Maximum protec-
tion against freezing is provided with a 68 percent
antifreeze concentration, which prevents freezing
down to -67.7ÉC (-90ÉF). A higher percentage will
freeze at a warmer temperature. Also, a higher per-
KJLUBRICATION & MAINTENANCE 0 - 3
FLUID TYPES (Continued)
Page 216 of 1803

COOLING
TABLE OF CONTENTS
page page
COOLING
DESCRIPTION
DESCRIPTION - COOLING SYSTEM 3.7L
ENGINE..............................1
DESCRIPTION - COOLING SYSTEM
ROUTING 3.7L ENGINE..................2
DESCRIPTION - HOSE CLAMPS...........2
OPERATION
OPERATION - COOLING SYSTEM.........2
OPERATION - HOSE CLAMPS............3
DIAGNOSIS AND TESTING
DIAGNOSIS AND TESTING - ON-BOARD
DIAGNOSTICS (OBD)...................3
DIAGNOSIS AND TESTING - PRELIMINARY
CHECKS.............................3
DIAGNOSIS AND TESTING - COOLING
SYSTEM LEAKS.......................4DIAGNOSIS AND TESTING - COOLING
SYSTEM DIAGNOSIS CHART.............6
STANDARD PROCEDURE
STANDARD PROCEDURE - DRAINING
COOLING SYSTEM 3.7L ENGINE.........12
STANDARD PROCEDURE - REFILLING
COOLING SYSTEM 3.7L ENGINE.........12
STANDARD PROCEDURE - COOLING
SYSTEM - REVERSE FLUSHING..........12
SPECIFICATIONS
TORQUE............................13
SPECIAL TOOLS
COOLING...........................14
ACCESSORY DRIVE......................15
ENGINE...............................19
TRANSMISSION.........................32
COOLING
DESCRIPTION
DESCRIPTION - COOLING SYSTEM 3.7L
ENGINE
The cooling system consists of the following items:
²Electric cooling fan - Standard.
²Electric cooling fan and mechanical thermal vis-
cous fan with low disengaged - Heavy duty cooling
only²Radiator
²Hot bottle pressure cap
²Thermostat
²Coolant reserve/overflow system
²Radiator in-tank transmission oil cooler (if
equipped with an automatic transmission)
²Coolant
²Water pump
²Hoses and hose clamps
KJCOOLING 7 - 1
Page 218 of 1803
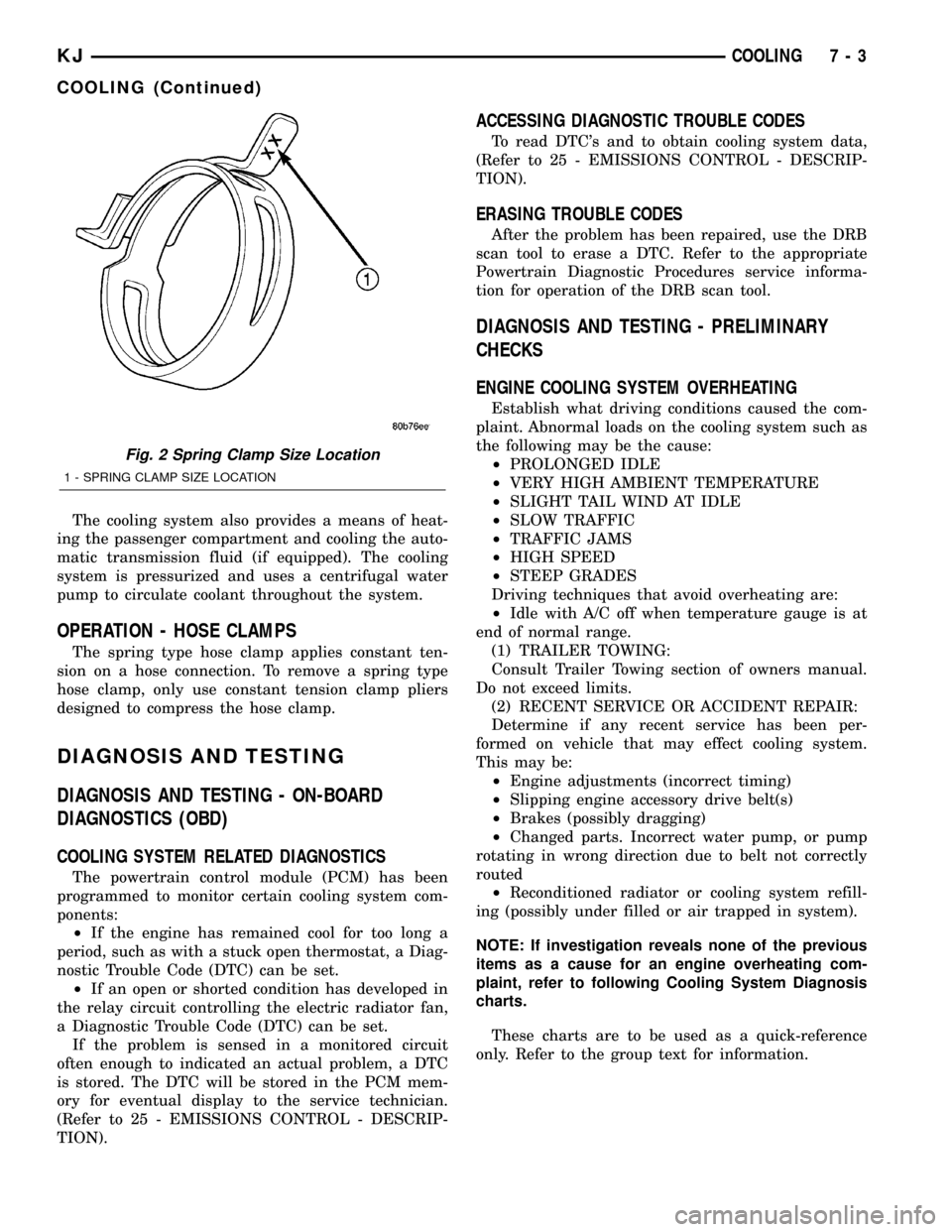
The cooling system also provides a means of heat-
ing the passenger compartment and cooling the auto-
matic transmission fluid (if equipped). The cooling
system is pressurized and uses a centrifugal water
pump to circulate coolant throughout the system.
OPERATION - HOSE CLAMPS
The spring type hose clamp applies constant ten-
sion on a hose connection. To remove a spring type
hose clamp, only use constant tension clamp pliers
designed to compress the hose clamp.
DIAGNOSIS AND TESTING
DIAGNOSIS AND TESTING - ON-BOARD
DIAGNOSTICS (OBD)
COOLING SYSTEM RELATED DIAGNOSTICS
The powertrain control module (PCM) has been
programmed to monitor certain cooling system com-
ponents:
²If the engine has remained cool for too long a
period, such as with a stuck open thermostat, a Diag-
nostic Trouble Code (DTC) can be set.
²If an open or shorted condition has developed in
the relay circuit controlling the electric radiator fan,
a Diagnostic Trouble Code (DTC) can be set.
If the problem is sensed in a monitored circuit
often enough to indicated an actual problem, a DTC
is stored. The DTC will be stored in the PCM mem-
ory for eventual display to the service technician.
(Refer to 25 - EMISSIONS CONTROL - DESCRIP-
TION).
ACCESSING DIAGNOSTIC TROUBLE CODES
To read DTC's and to obtain cooling system data,
(Refer to 25 - EMISSIONS CONTROL - DESCRIP-
TION).
ERASING TROUBLE CODES
After the problem has been repaired, use the DRB
scan tool to erase a DTC. Refer to the appropriate
Powertrain Diagnostic Procedures service informa-
tion for operation of the DRB scan tool.
DIAGNOSIS AND TESTING - PRELIMINARY
CHECKS
ENGINE COOLING SYSTEM OVERHEATING
Establish what driving conditions caused the com-
plaint. Abnormal loads on the cooling system such as
the following may be the cause:
²PROLONGED IDLE
²VERY HIGH AMBIENT TEMPERATURE
²SLIGHT TAIL WIND AT IDLE
²SLOW TRAFFIC
²TRAFFIC JAMS
²HIGH SPEED
²STEEP GRADES
Driving techniques that avoid overheating are:
²Idle with A/C off when temperature gauge is at
end of normal range.
(1) TRAILER TOWING:
Consult Trailer Towing section of owners manual.
Do not exceed limits.
(2) RECENT SERVICE OR ACCIDENT REPAIR:
Determine if any recent service has been per-
formed on vehicle that may effect cooling system.
This may be:
²Engine adjustments (incorrect timing)
²Slipping engine accessory drive belt(s)
²Brakes (possibly dragging)
²Changed parts. Incorrect water pump, or pump
rotating in wrong direction due to belt not correctly
routed
²Reconditioned radiator or cooling system refill-
ing (possibly under filled or air trapped in system).
NOTE: If investigation reveals none of the previous
items as a cause for an engine overheating com-
plaint, refer to following Cooling System Diagnosis
charts.
These charts are to be used as a quick-reference
only. Refer to the group text for information.
Fig. 2 Spring Clamp Size Location
1 - SPRING CLAMP SIZE LOCATION
KJCOOLING 7 - 3
COOLING (Continued)
Page 221 of 1803
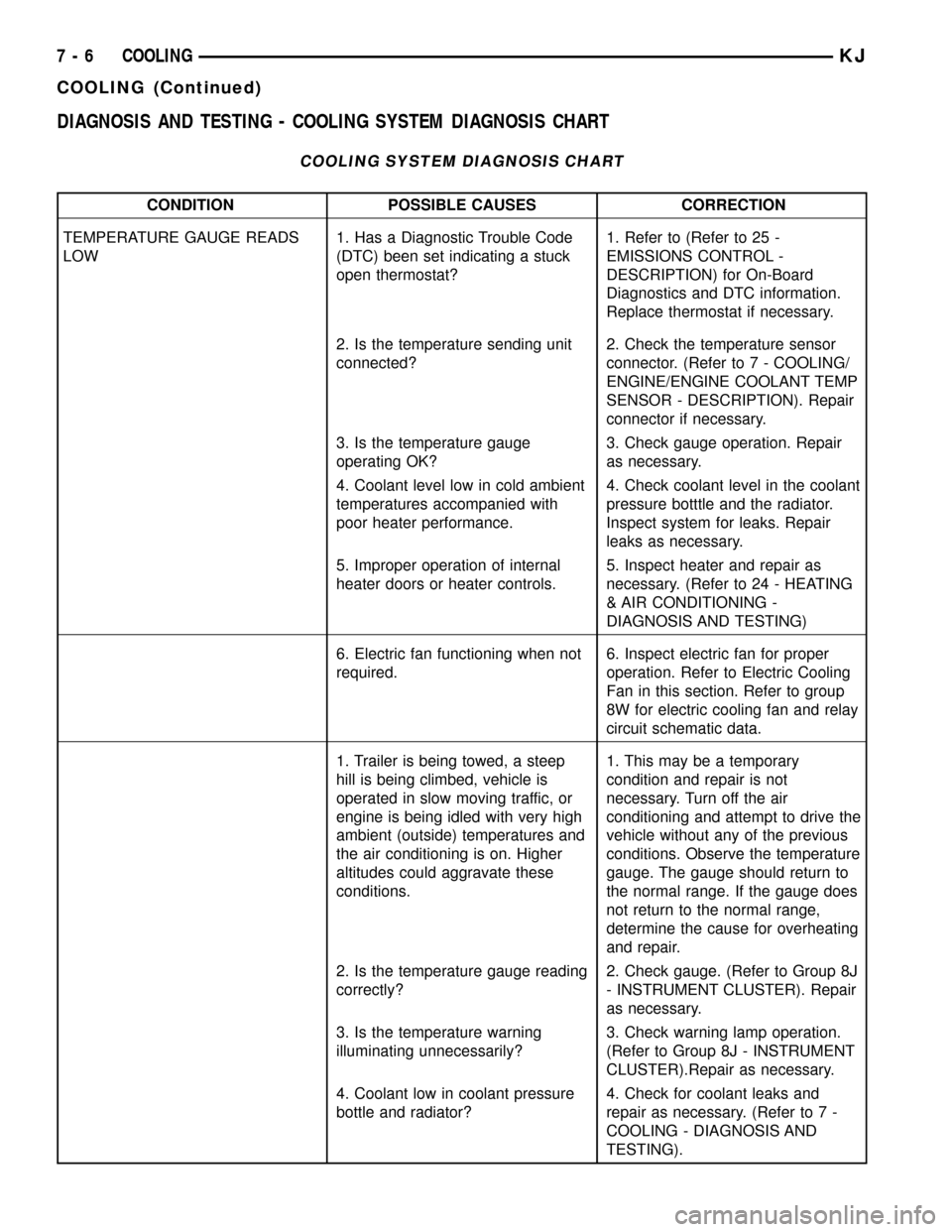
DIAGNOSIS AND TESTING - COOLING SYSTEM DIAGNOSIS CHART
COOLING SYSTEM DIAGNOSIS CHART
CONDITION POSSIBLE CAUSES CORRECTION
TEMPERATURE GAUGE READS
LOW1. Has a Diagnostic Trouble Code
(DTC) been set indicating a stuck
open thermostat?1. Refer to (Refer to 25 -
EMISSIONS CONTROL -
DESCRIPTION) for On-Board
Diagnostics and DTC information.
Replace thermostat if necessary.
2. Is the temperature sending unit
connected?2. Check the temperature sensor
connector. (Refer to 7 - COOLING/
ENGINE/ENGINE COOLANT TEMP
SENSOR - DESCRIPTION). Repair
connector if necessary.
3. Is the temperature gauge
operating OK?3. Check gauge operation. Repair
as necessary.
4. Coolant level low in cold ambient
temperatures accompanied with
poor heater performance.4. Check coolant level in the coolant
pressure botttle and the radiator.
Inspect system for leaks. Repair
leaks as necessary.
5. Improper operation of internal
heater doors or heater controls.5. Inspect heater and repair as
necessary. (Refer to 24 - HEATING
& AIR CONDITIONING -
DIAGNOSIS AND TESTING)
6. Electric fan functioning when not
required.6. Inspect electric fan for proper
operation. Refer to Electric Cooling
Fan in this section. Refer to group
8W for electric cooling fan and relay
circuit schematic data.
1. Trailer is being towed, a steep
hill is being climbed, vehicle is
operated in slow moving traffic, or
engine is being idled with very high
ambient (outside) temperatures and
the air conditioning is on. Higher
altitudes could aggravate these
conditions.1. This may be a temporary
condition and repair is not
necessary. Turn off the air
conditioning and attempt to drive the
vehicle without any of the previous
conditions. Observe the temperature
gauge. The gauge should return to
the normal range. If the gauge does
not return to the normal range,
determine the cause for overheating
and repair.
2. Is the temperature gauge reading
correctly?2. Check gauge. (Refer to Group 8J
- INSTRUMENT CLUSTER). Repair
as necessary.
3. Is the temperature warning
illuminating unnecessarily?3. Check warning lamp operation.
(Refer to Group 8J - INSTRUMENT
CLUSTER).Repair as necessary.
4. Coolant low in coolant pressure
bottle and radiator?4. Check for coolant leaks and
repair as necessary. (Refer to 7 -
COOLING - DIAGNOSIS AND
TESTING).
7 - 6 COOLINGKJ
COOLING (Continued)
Page 222 of 1803
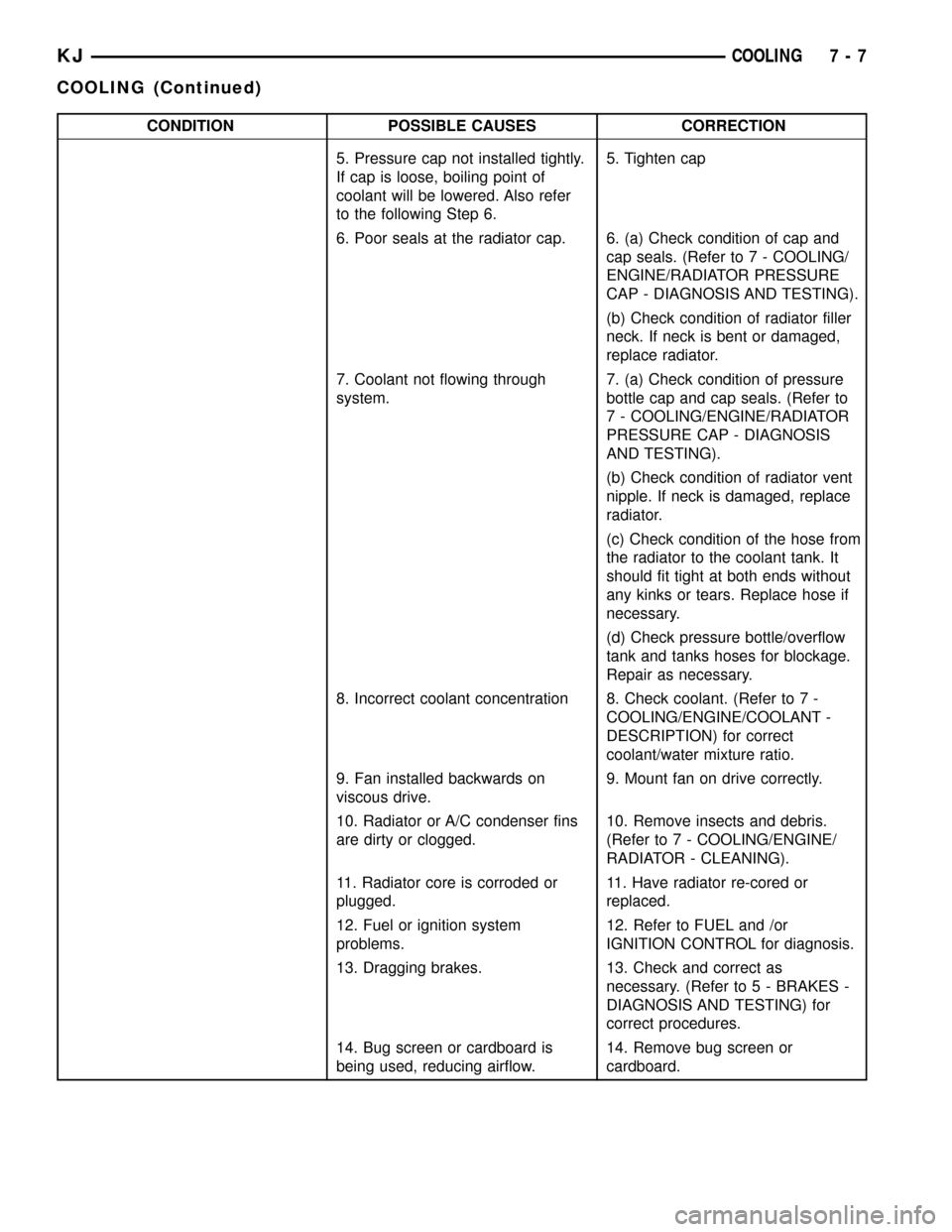
CONDITION POSSIBLE CAUSES CORRECTION
5. Pressure cap not installed tightly.
If cap is loose, boiling point of
coolant will be lowered. Also refer
to the following Step 6.5. Tighten cap
6. Poor seals at the radiator cap. 6. (a) Check condition of cap and
cap seals. (Refer to 7 - COOLING/
ENGINE/RADIATOR PRESSURE
CAP - DIAGNOSIS AND TESTING).
(b) Check condition of radiator filler
neck. If neck is bent or damaged,
replace radiator.
7. Coolant not flowing through
system.7. (a) Check condition of pressure
bottle cap and cap seals. (Refer to
7 - COOLING/ENGINE/RADIATOR
PRESSURE CAP - DIAGNOSIS
AND TESTING).
(b) Check condition of radiator vent
nipple. If neck is damaged, replace
radiator.
(c) Check condition of the hose from
the radiator to the coolant tank. It
should fit tight at both ends without
any kinks or tears. Replace hose if
necessary.
(d) Check pressure bottle/overflow
tank and tanks hoses for blockage.
Repair as necessary.
8. Incorrect coolant concentration 8. Check coolant. (Refer to 7 -
COOLING/ENGINE/COOLANT -
DESCRIPTION) for correct
coolant/water mixture ratio.
9. Fan installed backwards on
viscous drive.9. Mount fan on drive correctly.
10. Radiator or A/C condenser fins
are dirty or clogged.10. Remove insects and debris.
(Refer to 7 - COOLING/ENGINE/
RADIATOR - CLEANING).
11. Radiator core is corroded or
plugged.11. Have radiator re-cored or
replaced.
12. Fuel or ignition system
problems.12. Refer to FUEL and /or
IGNITION CONTROL for diagnosis.
13. Dragging brakes. 13. Check and correct as
necessary. (Refer to 5 - BRAKES -
DIAGNOSIS AND TESTING) for
correct procedures.
14. Bug screen or cardboard is
being used, reducing airflow.14. Remove bug screen or
cardboard.
KJCOOLING 7 - 7
COOLING (Continued)
Page 225 of 1803
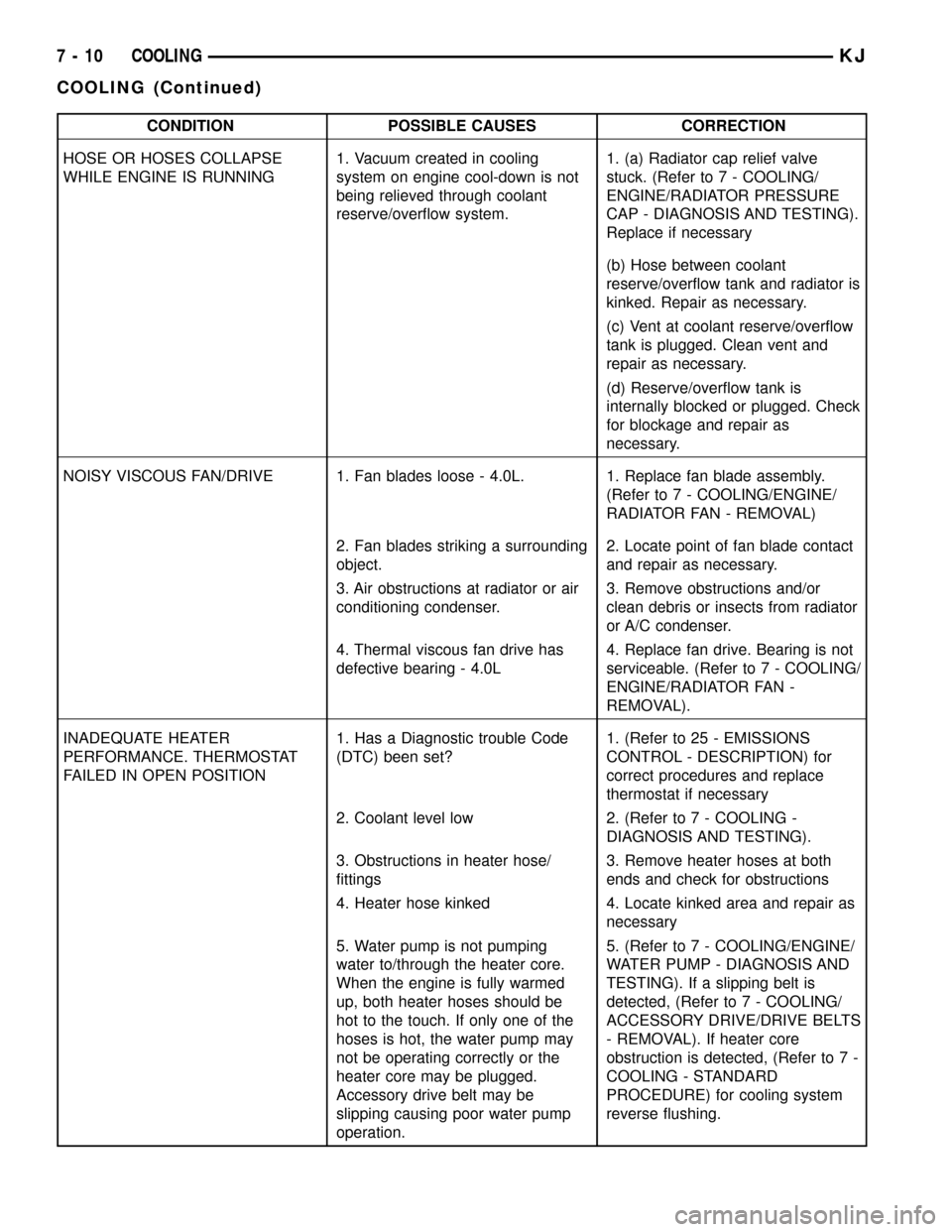
CONDITION POSSIBLE CAUSES CORRECTION
HOSE OR HOSES COLLAPSE
WHILE ENGINE IS RUNNING1. Vacuum created in cooling
system on engine cool-down is not
being relieved through coolant
reserve/overflow system.1. (a) Radiator cap relief valve
stuck. (Refer to 7 - COOLING/
ENGINE/RADIATOR PRESSURE
CAP - DIAGNOSIS AND TESTING).
Replace if necessary
(b) Hose between coolant
reserve/overflow tank and radiator is
kinked. Repair as necessary.
(c) Vent at coolant reserve/overflow
tank is plugged. Clean vent and
repair as necessary.
(d) Reserve/overflow tank is
internally blocked or plugged. Check
for blockage and repair as
necessary.
NOISY VISCOUS FAN/DRIVE 1. Fan blades loose - 4.0L. 1. Replace fan blade assembly.
(Refer to 7 - COOLING/ENGINE/
RADIATOR FAN - REMOVAL)
2. Fan blades striking a surrounding
object.2. Locate point of fan blade contact
and repair as necessary.
3. Air obstructions at radiator or air
conditioning condenser.3. Remove obstructions and/or
clean debris or insects from radiator
or A/C condenser.
4. Thermal viscous fan drive has
defective bearing - 4.0L4. Replace fan drive. Bearing is not
serviceable. (Refer to 7 - COOLING/
ENGINE/RADIATOR FAN -
REMOVAL).
INADEQUATE HEATER
PERFORMANCE. THERMOSTAT
FAILED IN OPEN POSITION1. Has a Diagnostic trouble Code
(DTC) been set?1. (Refer to 25 - EMISSIONS
CONTROL - DESCRIPTION) for
correct procedures and replace
thermostat if necessary
2. Coolant level low 2. (Refer to 7 - COOLING -
DIAGNOSIS AND TESTING).
3. Obstructions in heater hose/
fittings3. Remove heater hoses at both
ends and check for obstructions
4. Heater hose kinked 4. Locate kinked area and repair as
necessary
5. Water pump is not pumping
water to/through the heater core.
When the engine is fully warmed
up, both heater hoses should be
hot to the touch. If only one of the
hoses is hot, the water pump may
not be operating correctly or the
heater core may be plugged.
Accessory drive belt may be
slipping causing poor water pump
operation.5. (Refer to 7 - COOLING/ENGINE/
WATER PUMP - DIAGNOSIS AND
TESTING). If a slipping belt is
detected, (Refer to 7 - COOLING/
ACCESSORY DRIVE/DRIVE BELTS
- REMOVAL). If heater core
obstruction is detected, (Refer to 7 -
COOLING - STANDARD
PROCEDURE) for cooling system
reverse flushing.
7 - 10 COOLINGKJ
COOLING (Continued)
Page 226 of 1803
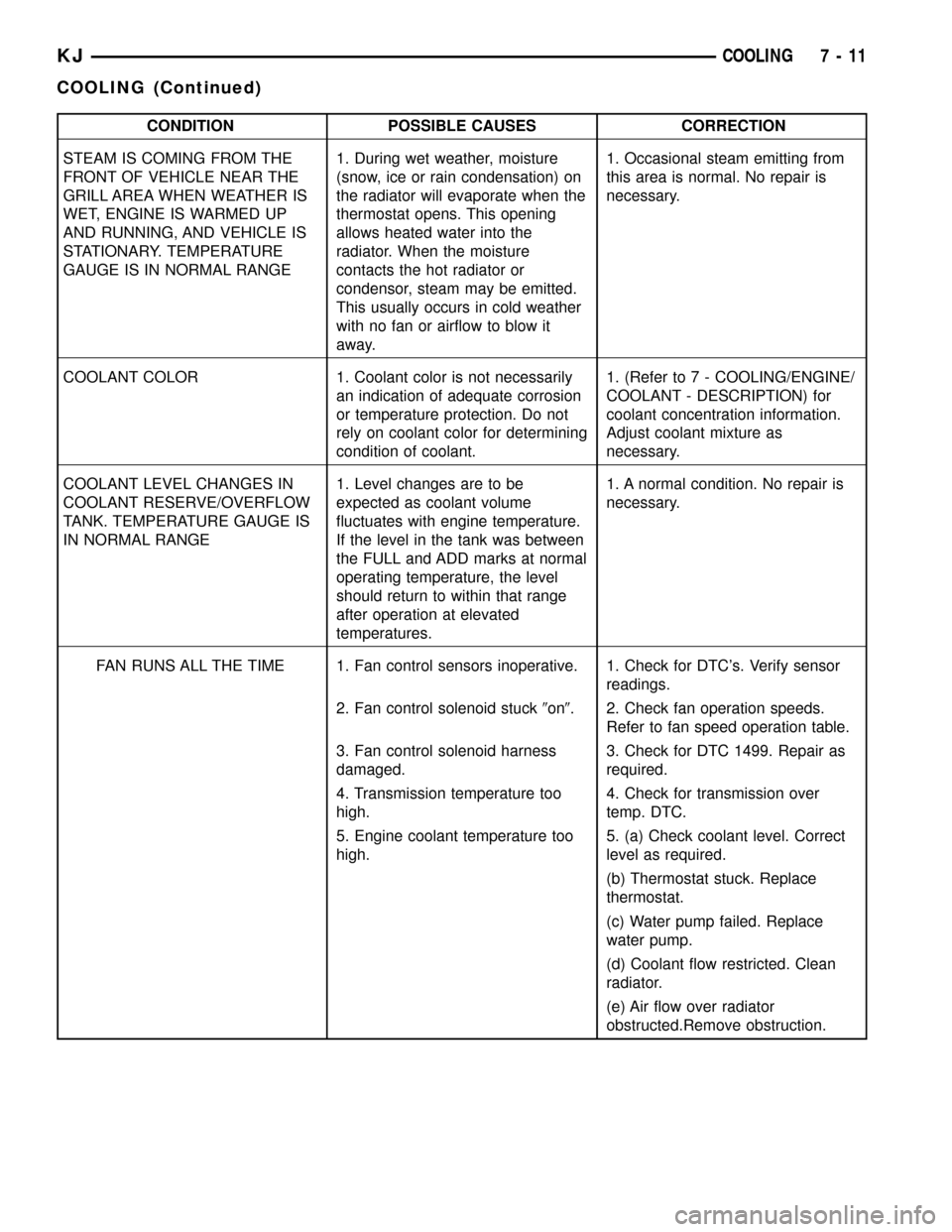
CONDITION POSSIBLE CAUSES CORRECTION
STEAM IS COMING FROM THE
FRONT OF VEHICLE NEAR THE
GRILL AREA WHEN WEATHER IS
WET, ENGINE IS WARMED UP
AND RUNNING, AND VEHICLE IS
STATIONARY. TEMPERATURE
GAUGE IS IN NORMAL RANGE1. During wet weather, moisture
(snow, ice or rain condensation) on
the radiator will evaporate when the
thermostat opens. This opening
allows heated water into the
radiator. When the moisture
contacts the hot radiator or
condensor, steam may be emitted.
This usually occurs in cold weather
with no fan or airflow to blow it
away.1. Occasional steam emitting from
this area is normal. No repair is
necessary.
COOLANT COLOR 1. Coolant color is not necessarily
an indication of adequate corrosion
or temperature protection. Do not
rely on coolant color for determining
condition of coolant.1. (Refer to 7 - COOLING/ENGINE/
COOLANT - DESCRIPTION) for
coolant concentration information.
Adjust coolant mixture as
necessary.
COOLANT LEVEL CHANGES IN
COOLANT RESERVE/OVERFLOW
TANK. TEMPERATURE GAUGE IS
IN NORMAL RANGE1. Level changes are to be
expected as coolant volume
fluctuates with engine temperature.
If the level in the tank was between
the FULL and ADD marks at normal
operating temperature, the level
should return to within that range
after operation at elevated
temperatures.1. A normal condition. No repair is
necessary.
FAN RUNS ALL THE TIME 1. Fan control sensors inoperative. 1. Check for DTC's. Verify sensor
readings.
2. Fan control solenoid stuck9on9. 2. Check fan operation speeds.
Refer to fan speed operation table.
3. Fan control solenoid harness
damaged.3. Check for DTC 1499. Repair as
required.
4. Transmission temperature too
high.4. Check for transmission over
temp. DTC.
5. Engine coolant temperature too
high.5. (a) Check coolant level. Correct
level as required.
(b) Thermostat stuck. Replace
thermostat.
(c) Water pump failed. Replace
water pump.
(d) Coolant flow restricted. Clean
radiator.
(e) Air flow over radiator
obstructed.Remove obstruction.
KJCOOLING 7 - 11
COOLING (Continued)
Page 228 of 1803
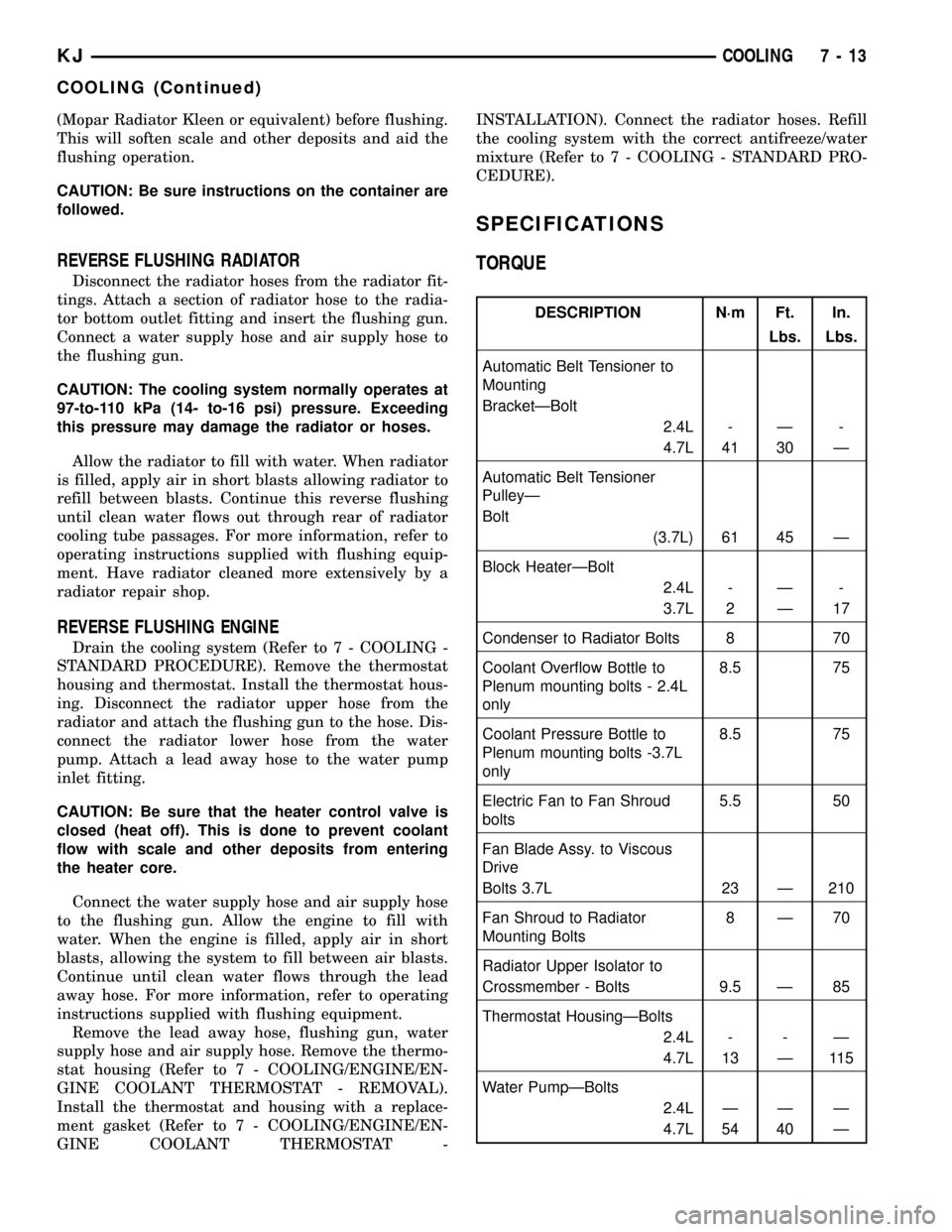
(Mopar Radiator Kleen or equivalent) before flushing.
This will soften scale and other deposits and aid the
flushing operation.
CAUTION: Be sure instructions on the container are
followed.
REVERSE FLUSHING RADIATOR
Disconnect the radiator hoses from the radiator fit-
tings. Attach a section of radiator hose to the radia-
tor bottom outlet fitting and insert the flushing gun.
Connect a water supply hose and air supply hose to
the flushing gun.
CAUTION: The cooling system normally operates at
97-to-110 kPa (14- to-16 psi) pressure. Exceeding
this pressure may damage the radiator or hoses.
Allow the radiator to fill with water. When radiator
is filled, apply air in short blasts allowing radiator to
refill between blasts. Continue this reverse flushing
until clean water flows out through rear of radiator
cooling tube passages. For more information, refer to
operating instructions supplied with flushing equip-
ment. Have radiator cleaned more extensively by a
radiator repair shop.
REVERSE FLUSHING ENGINE
Drain the cooling system (Refer to 7 - COOLING -
STANDARD PROCEDURE). Remove the thermostat
housing and thermostat. Install the thermostat hous-
ing. Disconnect the radiator upper hose from the
radiator and attach the flushing gun to the hose. Dis-
connect the radiator lower hose from the water
pump. Attach a lead away hose to the water pump
inlet fitting.
CAUTION: Be sure that the heater control valve is
closed (heat off). This is done to prevent coolant
flow with scale and other deposits from entering
the heater core.
Connect the water supply hose and air supply hose
to the flushing gun. Allow the engine to fill with
water. When the engine is filled, apply air in short
blasts, allowing the system to fill between air blasts.
Continue until clean water flows through the lead
away hose. For more information, refer to operating
instructions supplied with flushing equipment.
Remove the lead away hose, flushing gun, water
supply hose and air supply hose. Remove the thermo-
stat housing (Refer to 7 - COOLING/ENGINE/EN-
GINE COOLANT THERMOSTAT - REMOVAL).
Install the thermostat and housing with a replace-
ment gasket (Refer to 7 - COOLING/ENGINE/EN-
GINE COOLANT THERMOSTAT -INSTALLATION). Connect the radiator hoses. Refill
the cooling system with the correct antifreeze/water
mixture (Refer to 7 - COOLING - STANDARD PRO-
CEDURE).
SPECIFICATIONS
TORQUE
DESCRIPTION N´m Ft. In.
Lbs. Lbs.
Automatic Belt Tensioner to
Mounting
BracketÐBolt
2.4L - Ð -
4.7L 41 30 Ð
Automatic Belt Tensioner
PulleyÐ
Bolt
(3.7L) 61 45 Ð
Block HeaterÐBolt
2.4L - Ð -
3.7L 2 Ð 17
Condenser to Radiator Bolts 8 70
Coolant Overflow Bottle to
Plenum mounting bolts - 2.4L
only8.5 75
Coolant Pressure Bottle to
Plenum mounting bolts -3.7L
only8.5 75
Electric Fan to Fan Shroud
bolts5.5 50
Fan Blade Assy. to Viscous
Drive
Bolts 3.7L 23 Ð 210
Fan Shroud to Radiator
Mounting Bolts8Ð70
Radiator Upper Isolator to
Crossmember - Bolts 9.5 Ð 85
Thermostat HousingÐBolts
2.4L - - Ð
4.7L 13 Ð 115
Water PumpÐBolts
2.4L Ð Ð Ð
4.7L 54 40 Ð
KJCOOLING 7 - 13
COOLING (Continued)
Page 234 of 1803
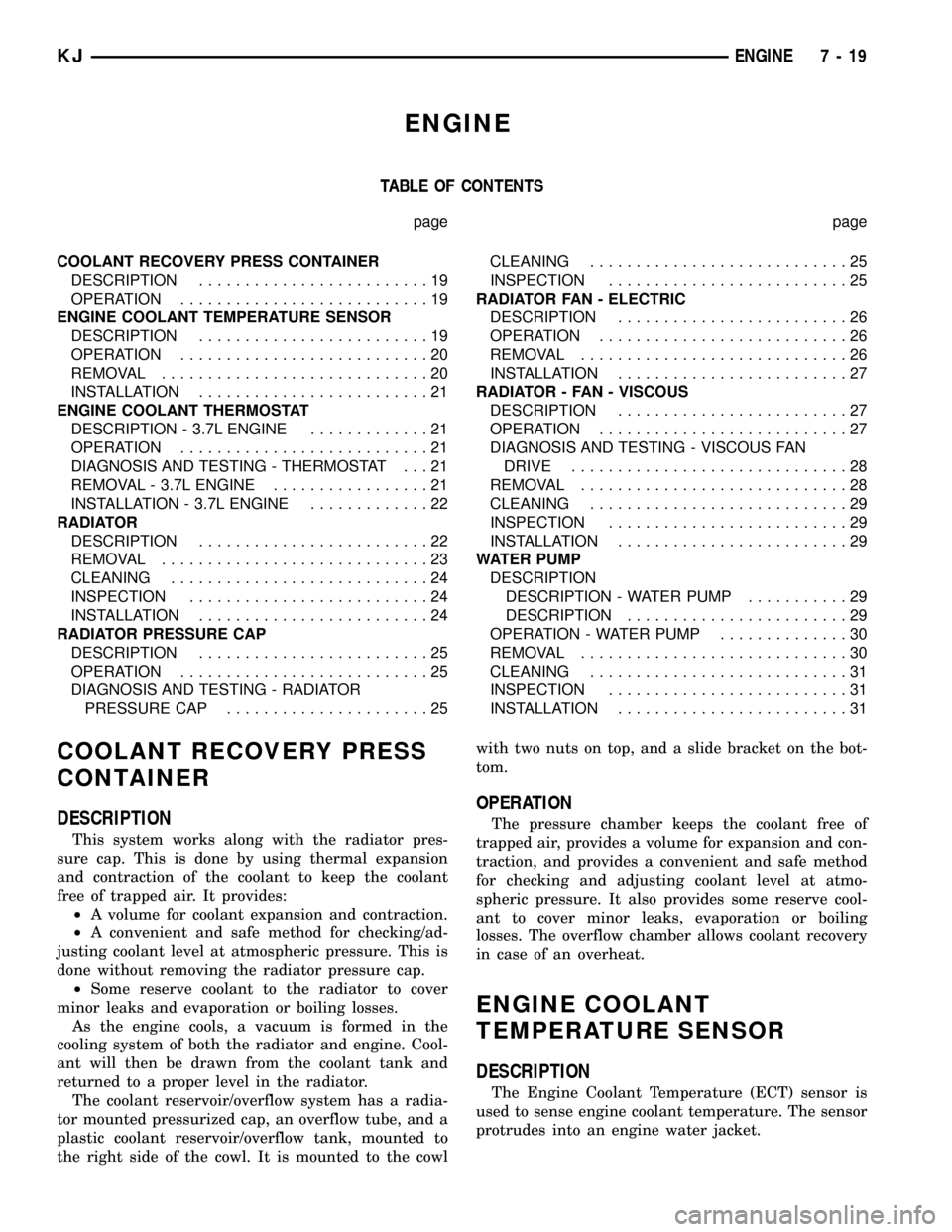
ENGINE
TABLE OF CONTENTS
page page
COOLANT RECOVERY PRESS CONTAINER
DESCRIPTION.........................19
OPERATION...........................19
ENGINE COOLANT TEMPERATURE SENSOR
DESCRIPTION.........................19
OPERATION...........................20
REMOVAL.............................20
INSTALLATION.........................21
ENGINE COOLANT THERMOSTAT
DESCRIPTION - 3.7L ENGINE.............21
OPERATION...........................21
DIAGNOSIS AND TESTING - THERMOSTAT . . . 21
REMOVAL - 3.7L ENGINE.................21
INSTALLATION - 3.7L ENGINE.............22
RADIATOR
DESCRIPTION.........................22
REMOVAL.............................23
CLEANING............................24
INSPECTION..........................24
INSTALLATION.........................24
RADIATOR PRESSURE CAP
DESCRIPTION.........................25
OPERATION...........................25
DIAGNOSIS AND TESTING - RADIATOR
PRESSURE CAP......................25CLEANING............................25
INSPECTION..........................25
RADIATOR FAN - ELECTRIC
DESCRIPTION.........................26
OPERATION...........................26
REMOVAL.............................26
INSTALLATION.........................27
RADIATOR - FAN - VISCOUS
DESCRIPTION.........................27
OPERATION...........................27
DIAGNOSIS AND TESTING - VISCOUS FAN
DRIVE..............................28
REMOVAL.............................28
CLEANING............................29
INSPECTION..........................29
INSTALLATION.........................29
WATER PUMP
DESCRIPTION
DESCRIPTION - WATER PUMP...........29
DESCRIPTION........................29
OPERATION - WATER PUMP..............30
REMOVAL.............................30
CLEANING............................31
INSPECTION..........................31
INSTALLATION.........................31
COOLANT RECOVERY PRESS
CONTAINER
DESCRIPTION
This system works along with the radiator pres-
sure cap. This is done by using thermal expansion
and contraction of the coolant to keep the coolant
free of trapped air. It provides:
²A volume for coolant expansion and contraction.
²A convenient and safe method for checking/ad-
justing coolant level at atmospheric pressure. This is
done without removing the radiator pressure cap.
²Some reserve coolant to the radiator to cover
minor leaks and evaporation or boiling losses.
As the engine cools, a vacuum is formed in the
cooling system of both the radiator and engine. Cool-
ant will then be drawn from the coolant tank and
returned to a proper level in the radiator.
The coolant reservoir/overflow system has a radia-
tor mounted pressurized cap, an overflow tube, and a
plastic coolant reservoir/overflow tank, mounted to
the right side of the cowl. It is mounted to the cowlwith two nuts on top, and a slide bracket on the bot-
tom.
OPERATION
The pressure chamber keeps the coolant free of
trapped air, provides a volume for expansion and con-
traction, and provides a convenient and safe method
for checking and adjusting coolant level at atmo-
spheric pressure. It also provides some reserve cool-
ant to cover minor leaks, evaporation or boiling
losses. The overflow chamber allows coolant recovery
in case of an overheat.
ENGINE COOLANT
TEMPERATURE SENSOR
DESCRIPTION
The Engine Coolant Temperature (ECT) sensor is
used to sense engine coolant temperature. The sensor
protrudes into an engine water jacket.
KJENGINE 7 - 19
Page 235 of 1803
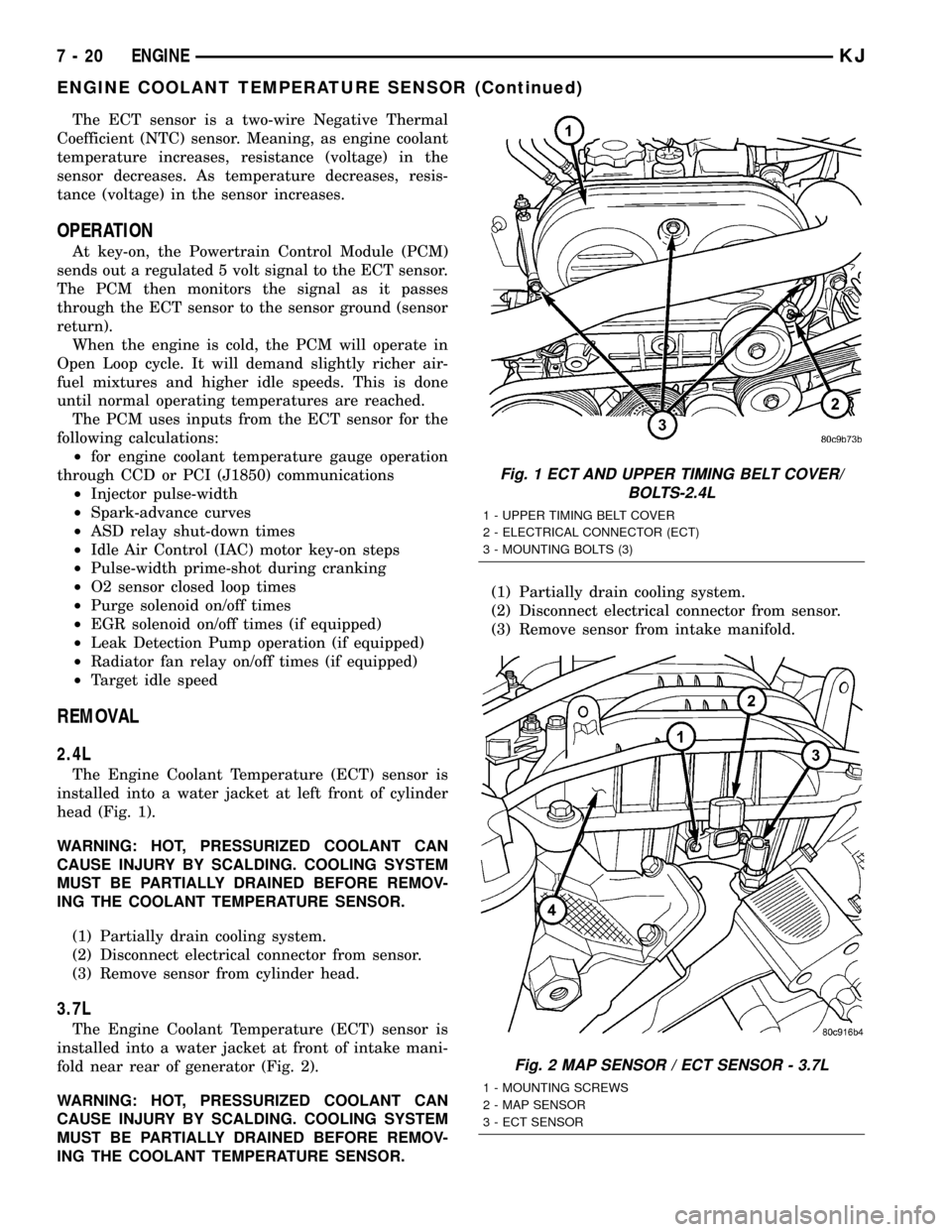
The ECT sensor is a two-wire Negative Thermal
Coefficient (NTC) sensor. Meaning, as engine coolant
temperature increases, resistance (voltage) in the
sensor decreases. As temperature decreases, resis-
tance (voltage) in the sensor increases.
OPERATION
At key-on, the Powertrain Control Module (PCM)
sends out a regulated 5 volt signal to the ECT sensor.
The PCM then monitors the signal as it passes
through the ECT sensor to the sensor ground (sensor
return).
When the engine is cold, the PCM will operate in
Open Loop cycle. It will demand slightly richer air-
fuel mixtures and higher idle speeds. This is done
until normal operating temperatures are reached.
The PCM uses inputs from the ECT sensor for the
following calculations:
²for engine coolant temperature gauge operation
through CCD or PCI (J1850) communications
²Injector pulse-width
²Spark-advance curves
²ASD relay shut-down times
²Idle Air Control (IAC) motor key-on steps
²Pulse-width prime-shot during cranking
²O2 sensor closed loop times
²Purge solenoid on/off times
²EGR solenoid on/off times (if equipped)
²Leak Detection Pump operation (if equipped)
²Radiator fan relay on/off times (if equipped)
²Target idle speed
REMOVAL
2.4L
The Engine Coolant Temperature (ECT) sensor is
installed into a water jacket at left front of cylinder
head (Fig. 1).
WARNING: HOT, PRESSURIZED COOLANT CAN
CAUSE INJURY BY SCALDING. COOLING SYSTEM
MUST BE PARTIALLY DRAINED BEFORE REMOV-
ING THE COOLANT TEMPERATURE SENSOR.
(1) Partially drain cooling system.
(2) Disconnect electrical connector from sensor.
(3) Remove sensor from cylinder head.
3.7L
The Engine Coolant Temperature (ECT) sensor is
installed into a water jacket at front of intake mani-
fold near rear of generator (Fig. 2).
WARNING: HOT, PRESSURIZED COOLANT CAN
CAUSE INJURY BY SCALDING. COOLING SYSTEM
MUST BE PARTIALLY DRAINED BEFORE REMOV-
ING THE COOLANT TEMPERATURE SENSOR.(1) Partially drain cooling system.
(2) Disconnect electrical connector from sensor.
(3) Remove sensor from intake manifold.
Fig. 1 ECT AND UPPER TIMING BELT COVER/
BOLTS-2.4L
1 - UPPER TIMING BELT COVER
2 - ELECTRICAL CONNECTOR (ECT)
3 - MOUNTING BOLTS (3)
Fig. 2 MAP SENSOR / ECT SENSOR - 3.7L
1 - MOUNTING SCREWS
2 - MAP SENSOR
3 - ECT SENSOR
7 - 20 ENGINEKJ
ENGINE COOLANT TEMPERATURE SENSOR (Continued)