spark plugs replace JEEP LIBERTY 2002 KJ / 1.G User Guide
[x] Cancel search | Manufacturer: JEEP, Model Year: 2002, Model line: LIBERTY, Model: JEEP LIBERTY 2002 KJ / 1.GPages: 1803, PDF Size: 62.3 MB
Page 1327 of 1803
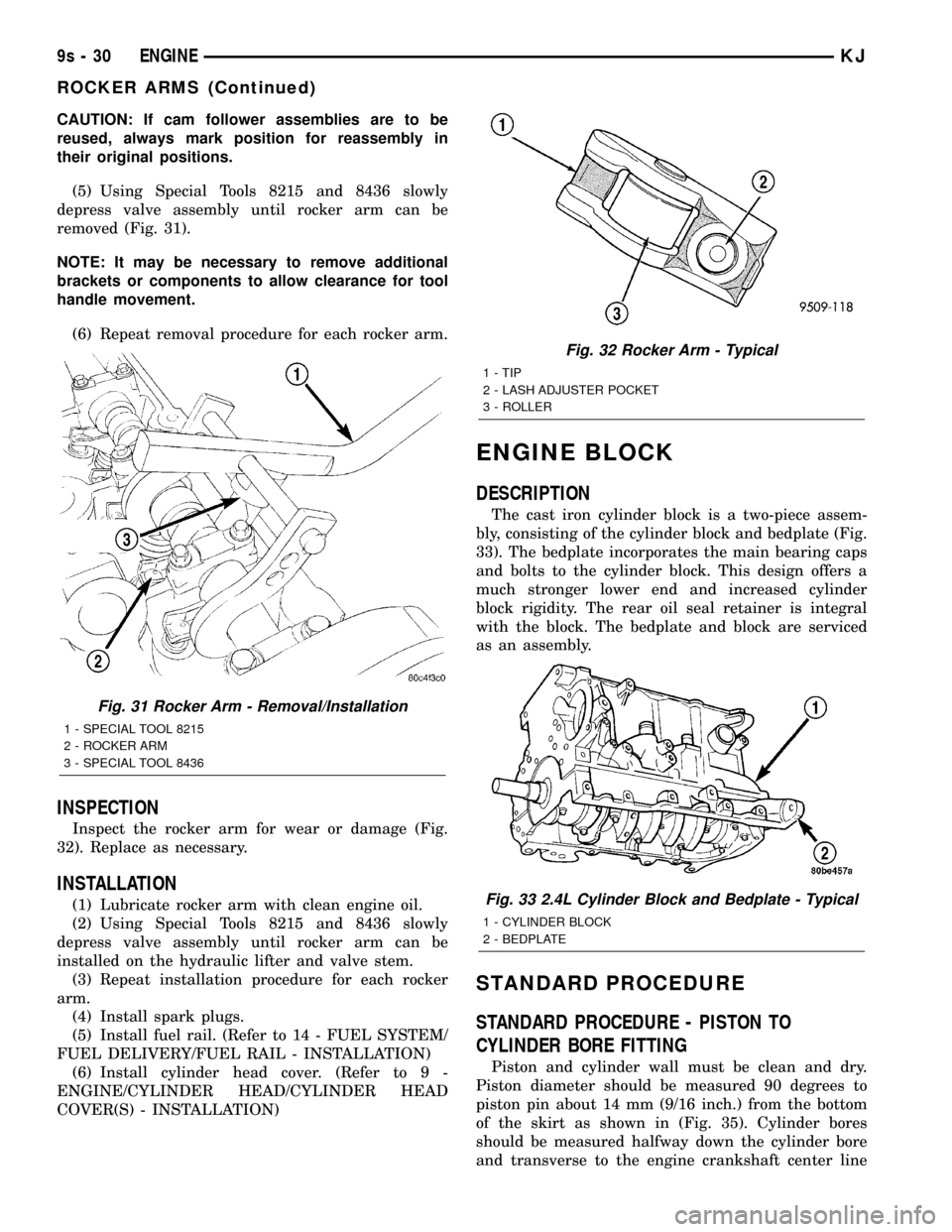
CAUTION: If cam follower assemblies are to be
reused, always mark position for reassembly in
their original positions.
(5) Using Special Tools 8215 and 8436 slowly
depress valve assembly until rocker arm can be
removed (Fig. 31).
NOTE: It may be necessary to remove additional
brackets or components to allow clearance for tool
handle movement.
(6) Repeat removal procedure for each rocker arm.
INSPECTION
Inspect the rocker arm for wear or damage (Fig.
32). Replace as necessary.
INSTALLATION
(1) Lubricate rocker arm with clean engine oil.
(2) Using Special Tools 8215 and 8436 slowly
depress valve assembly until rocker arm can be
installed on the hydraulic lifter and valve stem.
(3) Repeat installation procedure for each rocker
arm.
(4) Install spark plugs.
(5) Install fuel rail. (Refer to 14 - FUEL SYSTEM/
FUEL DELIVERY/FUEL RAIL - INSTALLATION)
(6) Install cylinder head cover. (Refer to 9 -
ENGINE/CYLINDER HEAD/CYLINDER HEAD
COVER(S) - INSTALLATION)
ENGINE BLOCK
DESCRIPTION
The cast iron cylinder block is a two-piece assem-
bly, consisting of the cylinder block and bedplate (Fig.
33). The bedplate incorporates the main bearing caps
and bolts to the cylinder block. This design offers a
much stronger lower end and increased cylinder
block rigidity. The rear oil seal retainer is integral
with the block. The bedplate and block are serviced
as an assembly.
STANDARD PROCEDURE
STANDARD PROCEDURE - PISTON TO
CYLINDER BORE FITTING
Piston and cylinder wall must be clean and dry.
Piston diameter should be measured 90 degrees to
piston pin about 14 mm (9/16 inch.) from the bottom
of the skirt as shown in (Fig. 35). Cylinder bores
should be measured halfway down the cylinder bore
and transverse to the engine crankshaft center line
Fig. 31 Rocker Arm - Removal/Installation
1 - SPECIAL TOOL 8215
2 - ROCKER ARM
3 - SPECIAL TOOL 8436
Fig. 32 Rocker Arm - Typical
1 - TIP
2 - LASH ADJUSTER POCKET
3 - ROLLER
Fig. 33 2.4L Cylinder Block and Bedplate - Typical
1 - CYLINDER BLOCK
2 - BEDPLATE
9s - 30 ENGINEKJ
ROCKER ARMS (Continued)
Page 1363 of 1803
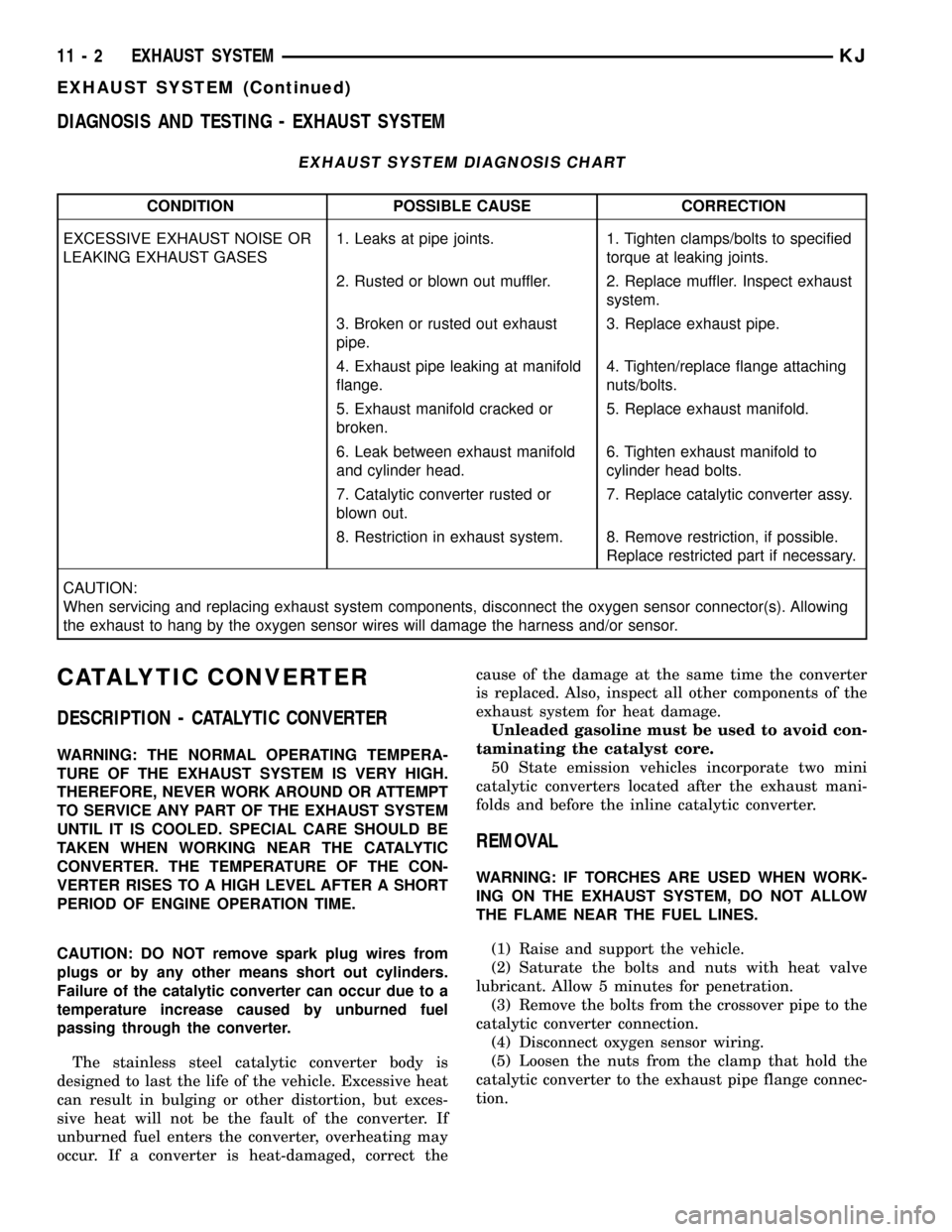
DIAGNOSIS AND TESTING - EXHAUST SYSTEM
EXHAUST SYSTEM DIAGNOSIS CHART
CONDITION POSSIBLE CAUSE CORRECTION
EXCESSIVE EXHAUST NOISE OR
LEAKING EXHAUST GASES1. Leaks at pipe joints. 1. Tighten clamps/bolts to specified
torque at leaking joints.
2. Rusted or blown out muffler. 2. Replace muffler. Inspect exhaust
system.
3. Broken or rusted out exhaust
pipe.3. Replace exhaust pipe.
4. Exhaust pipe leaking at manifold
flange.4. Tighten/replace flange attaching
nuts/bolts.
5. Exhaust manifold cracked or
broken.5. Replace exhaust manifold.
6. Leak between exhaust manifold
and cylinder head.6. Tighten exhaust manifold to
cylinder head bolts.
7. Catalytic converter rusted or
blown out.7. Replace catalytic converter assy.
8. Restriction in exhaust system. 8. Remove restriction, if possible.
Replace restricted part if necessary.
CAUTION:
When servicing and replacing exhaust system components, disconnect the oxygen sensor connector(s). Allowing
the exhaust to hang by the oxygen sensor wires will damage the harness and/or sensor.
CATALYTIC CONVERTER
DESCRIPTION - CATALYTIC CONVERTER
WARNING: THE NORMAL OPERATING TEMPERA-
TURE OF THE EXHAUST SYSTEM IS VERY HIGH.
THEREFORE, NEVER WORK AROUND OR ATTEMPT
TO SERVICE ANY PART OF THE EXHAUST SYSTEM
UNTIL IT IS COOLED. SPECIAL CARE SHOULD BE
TAKEN WHEN WORKING NEAR THE CATALYTIC
CONVERTER. THE TEMPERATURE OF THE CON-
VERTER RISES TO A HIGH LEVEL AFTER A SHORT
PERIOD OF ENGINE OPERATION TIME.
CAUTION: DO NOT remove spark plug wires from
plugs or by any other means short out cylinders.
Failure of the catalytic converter can occur due to a
temperature increase caused by unburned fuel
passing through the converter.
The stainless steel catalytic converter body is
designed to last the life of the vehicle. Excessive heat
can result in bulging or other distortion, but exces-
sive heat will not be the fault of the converter. If
unburned fuel enters the converter, overheating may
occur. If a converter is heat-damaged, correct thecause of the damage at the same time the converter
is replaced. Also, inspect all other components of the
exhaust system for heat damage.
Unleaded gasoline must be used to avoid con-
taminating the catalyst core.
50 State emission vehicles incorporate two mini
catalytic converters located after the exhaust mani-
folds and before the inline catalytic converter.
REMOVAL
WARNING: IF TORCHES ARE USED WHEN WORK-
ING ON THE EXHAUST SYSTEM, DO NOT ALLOW
THE FLAME NEAR THE FUEL LINES.
(1) Raise and support the vehicle.
(2) Saturate the bolts and nuts with heat valve
lubricant. Allow 5 minutes for penetration.
(3) Remove the bolts from the crossover pipe to the
catalytic converter connection.
(4) Disconnect oxygen sensor wiring.
(5) Loosen the nuts from the clamp that hold the
catalytic converter to the exhaust pipe flange connec-
tion.
11 - 2 EXHAUST SYSTEMKJ
EXHAUST SYSTEM (Continued)
Page 1369 of 1803
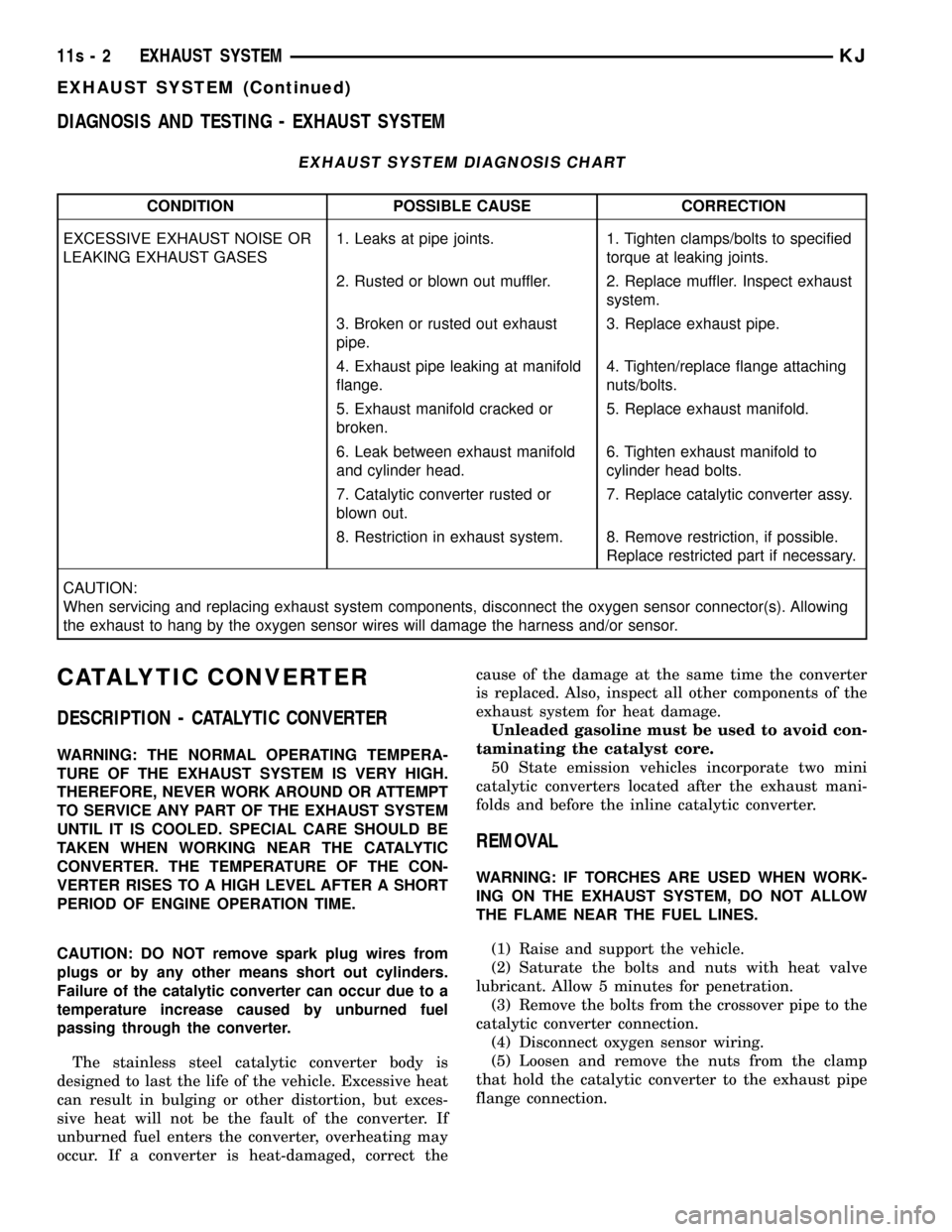
DIAGNOSIS AND TESTING - EXHAUST SYSTEM
EXHAUST SYSTEM DIAGNOSIS CHART
CONDITION POSSIBLE CAUSE CORRECTION
EXCESSIVE EXHAUST NOISE OR
LEAKING EXHAUST GASES1. Leaks at pipe joints. 1. Tighten clamps/bolts to specified
torque at leaking joints.
2. Rusted or blown out muffler. 2. Replace muffler. Inspect exhaust
system.
3. Broken or rusted out exhaust
pipe.3. Replace exhaust pipe.
4. Exhaust pipe leaking at manifold
flange.4. Tighten/replace flange attaching
nuts/bolts.
5. Exhaust manifold cracked or
broken.5. Replace exhaust manifold.
6. Leak between exhaust manifold
and cylinder head.6. Tighten exhaust manifold to
cylinder head bolts.
7. Catalytic converter rusted or
blown out.7. Replace catalytic converter assy.
8. Restriction in exhaust system. 8. Remove restriction, if possible.
Replace restricted part if necessary.
CAUTION:
When servicing and replacing exhaust system components, disconnect the oxygen sensor connector(s). Allowing
the exhaust to hang by the oxygen sensor wires will damage the harness and/or sensor.
CATALYTIC CONVERTER
DESCRIPTION - CATALYTIC CONVERTER
WARNING: THE NORMAL OPERATING TEMPERA-
TURE OF THE EXHAUST SYSTEM IS VERY HIGH.
THEREFORE, NEVER WORK AROUND OR ATTEMPT
TO SERVICE ANY PART OF THE EXHAUST SYSTEM
UNTIL IT IS COOLED. SPECIAL CARE SHOULD BE
TAKEN WHEN WORKING NEAR THE CATALYTIC
CONVERTER. THE TEMPERATURE OF THE CON-
VERTER RISES TO A HIGH LEVEL AFTER A SHORT
PERIOD OF ENGINE OPERATION TIME.
CAUTION: DO NOT remove spark plug wires from
plugs or by any other means short out cylinders.
Failure of the catalytic converter can occur due to a
temperature increase caused by unburned fuel
passing through the converter.
The stainless steel catalytic converter body is
designed to last the life of the vehicle. Excessive heat
can result in bulging or other distortion, but exces-
sive heat will not be the fault of the converter. If
unburned fuel enters the converter, overheating may
occur. If a converter is heat-damaged, correct thecause of the damage at the same time the converter
is replaced. Also, inspect all other components of the
exhaust system for heat damage.
Unleaded gasoline must be used to avoid con-
taminating the catalyst core.
50 State emission vehicles incorporate two mini
catalytic converters located after the exhaust mani-
folds and before the inline catalytic converter.
REMOVAL
WARNING: IF TORCHES ARE USED WHEN WORK-
ING ON THE EXHAUST SYSTEM, DO NOT ALLOW
THE FLAME NEAR THE FUEL LINES.
(1) Raise and support the vehicle.
(2) Saturate the bolts and nuts with heat valve
lubricant. Allow 5 minutes for penetration.
(3) Remove the bolts from the crossover pipe to the
catalytic converter connection.
(4) Disconnect oxygen sensor wiring.
(5) Loosen and remove the nuts from the clamp
that hold the catalytic converter to the exhaust pipe
flange connection.
11s - 2 EXHAUST SYSTEMKJ
EXHAUST SYSTEM (Continued)
Page 1745 of 1803
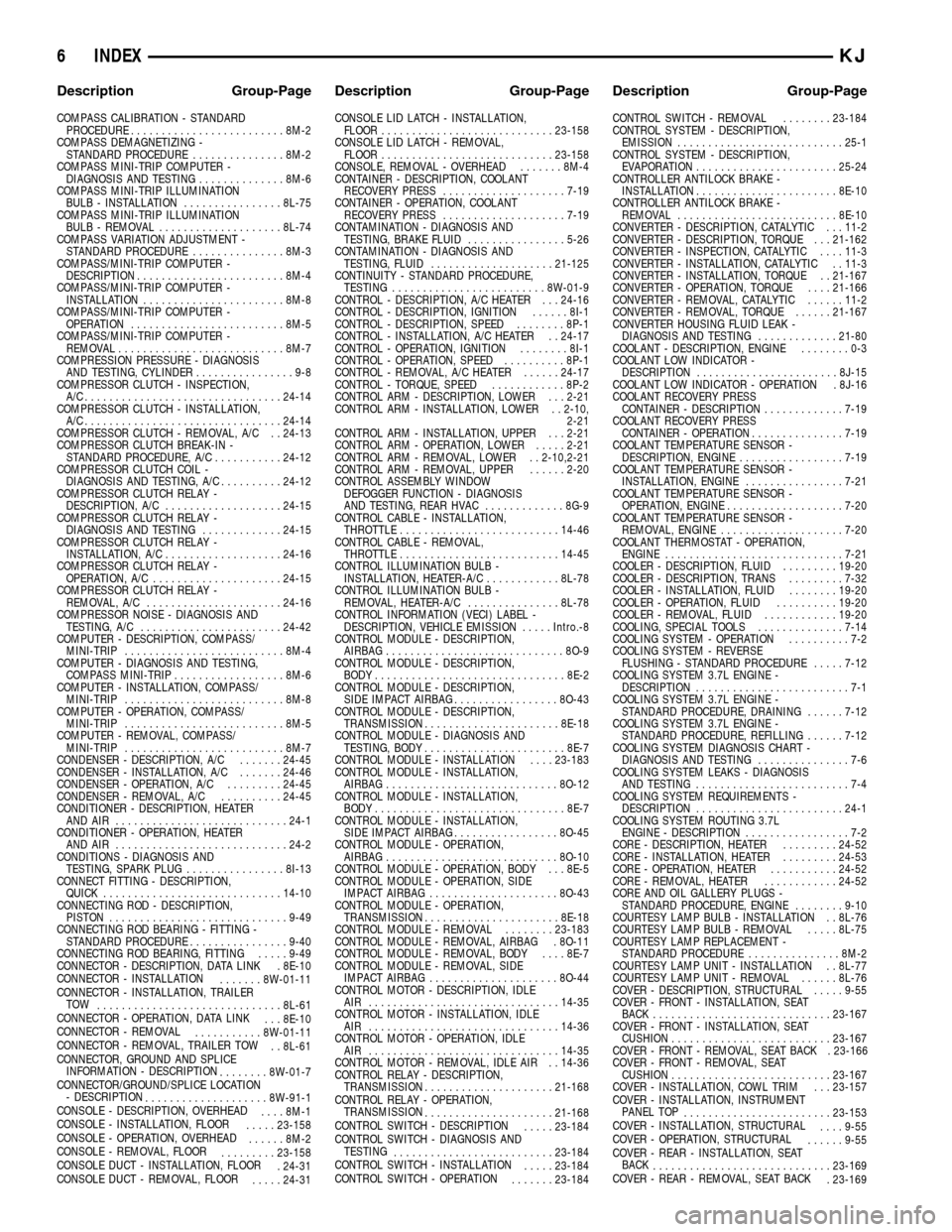
COMPASS CALIBRATION - STANDARD
PROCEDURE.........................8M-2
COMPASS DEMAGNETIZING -
STANDARD PROCEDURE...............8M-2
COMPASS MINI-TRIP COMPUTER -
DIAGNOSIS AND TESTING..............8M-6
COMPASS MINI-TRIP ILLUMINATION
BULB - INSTALLATION................8L-75
COMPASS MINI-TRIP ILLUMINATION
BULB - REMOVAL....................8L-74
COMPASS VARIATION ADJUSTMENT -
STANDARD PROCEDURE...............8M-3
COMPASS/MINI-TRIP COMPUTER -
DESCRIPTION........................8M-4
COMPASS/MINI-TRIP COMPUTER -
INSTALLATION.......................8M-8
COMPASS/MINI-TRIP COMPUTER -
OPERATION.........................8M-5
COMPASS/MINI-TRIP COMPUTER -
REMOVAL...........................8M-7
COMPRESSION PRESSURE - DIAGNOSIS
AND TESTING, CYLINDER................9-8
COMPRESSOR CLUTCH - INSPECTION,
A/C................................24-14
COMPRESSOR CLUTCH - INSTALLATION,
A/C................................24-14
COMPRESSOR CLUTCH - REMOVAL, A/C . . 24-13
COMPRESSOR CLUTCH BREAK-IN -
STANDARD PROCEDURE, A/C...........24-12
COMPRESSOR CLUTCH COIL -
DIAGNOSIS AND TESTING, A/C..........24-12
COMPRESSOR CLUTCH RELAY -
DESCRIPTION, A/C...................24-15
COMPRESSOR CLUTCH RELAY -
DIAGNOSIS AND TESTING.............24-15
COMPRESSOR CLUTCH RELAY -
INSTALLATION, A/C...................24-16
COMPRESSOR CLUTCH RELAY -
OPERATION, A/C.....................24-15
COMPRESSOR CLUTCH RELAY -
REMOVAL, A/C......................24-16
COMPRESSOR NOISE - DIAGNOSIS AND
TESTING, A/C.......................24-42
COMPUTER - DESCRIPTION, COMPASS/
MINI-TRIP..........................8M-4
COMPUTER - DIAGNOSIS AND TESTING,
COMPASS MINI-TRIP..................8M-6
COMPUTER - INSTALLATION, COMPASS/
MINI-TRIP..........................8M-8
COMPUTER - OPERATION, COMPASS/
MINI-TRIP..........................8M-5
COMPUTER - REMOVAL, COMPASS/
MINI-TRIP..........................8M-7
CONDENSER - DESCRIPTION, A/C.......24-45
CONDENSER - INSTALLATION, A/C.......24-46
CONDENSER - OPERATION, A/C.........24-45
CONDENSER - REMOVAL, A/C..........24-45
CONDITIONER - DESCRIPTION, HEATER
AND AIR ............................24-1
CONDITIONER - OPERATION, HEATER
AND AIR ............................24-2
CONDITIONS - DIAGNOSIS AND
TESTING, SPARK PLUG................8I-13
CONNECT FITTING - DESCRIPTION,
QUICK.............................14-10
CONNECTING ROD - DESCRIPTION,
PISTON.............................9-49
CONNECTING ROD BEARING - FITTING -
STANDARD PROCEDURE................9-40
CONNECTING ROD BEARING, FITTING.....9-49
CONNECTOR - DESCRIPTION, DATA LINK . 8E-10
CONNECTOR - INSTALLATION
.......8W-01-11
CONNECTOR - INSTALLATION, TRAILER
TOW
..............................8L-61
CONNECTOR - OPERATION, DATA LINK
. . . 8E-10
CONNECTOR - REMOVAL
...........8W-01-11
CONNECTOR - REMOVAL, TRAILER TOW
. . 8L-61
CONNECTOR, GROUND AND SPLICE
INFORMATION - DESCRIPTION
........8W-01-7
CONNECTOR/GROUND/SPLICE LOCATION
- DESCRIPTION
....................8W-91-1
CONSOLE - DESCRIPTION, OVERHEAD
....8M-1
CONSOLE - INSTALLATION, FLOOR
.....23-158
CONSOLE - OPERATION, OVERHEAD
......8M-2
CONSOLE - REMOVAL, FLOOR
.........23-158
CONSOLE DUCT - INSTALLATION, FLOOR
. 24-31
CONSOLE DUCT - REMOVAL, FLOOR
.....24-31CONSOLE LID LATCH - INSTALLATION,
FLOOR............................23-158
CONSOLE LID LATCH - REMOVAL,
FLOOR............................23-158
CONSOLE, REMOVAL - OVERHEAD.......8M-4
CONTAINER - DESCRIPTION, COOLANT
RECOVERY PRESS....................7-19
CONTAINER - OPERATION, COOLANT
RECOVERY PRESS....................7-19
CONTAMINATION - DIAGNOSIS AND
TESTING, BRAKE FLUID................5-26
CONTAMINATION - DIAGNOSIS AND
TESTING, FLUID....................21-125
CONTINUITY - STANDARD PROCEDURE,
TESTING.........................8W-01-9
CONTROL - DESCRIPTION, A/C HEATER . . . 24-16
CONTROL - DESCRIPTION, IGNITION......8I-1
CONTROL - DESCRIPTION, SPEED........8P-1
CONTROL - INSTALLATION, A/C HEATER . . 24-17
CONTROL - OPERATION, IGNITION........8I-1
CONTROL - OPERATION, SPEED..........8P-1
CONTROL - REMOVAL, A/C HEATER......24-17
CONTROL - TORQUE, SPEED............8P-2
CONTROL ARM - DESCRIPTION, LOWER . . . 2-21
CONTROL ARM - INSTALLATION, LOWER . . 2-10,
2-21
CONTROL ARM - INSTALLATION, UPPER . . . 2-21
CONTROL ARM - OPERATION, LOWER.....2-21
CONTROL ARM - REMOVAL, LOWER . . 2-10,2-21
CONTROL ARM - REMOVAL, UPPER......2-20
CONTROL ASSEMBLY WINDOW
DEFOGGER FUNCTION - DIAGNOSIS
AND TESTING, REAR HVAC.............8G-9
CONTROL CABLE - INSTALLATION,
THROTTLE..........................14-46
CONTROL CABLE - REMOVAL,
THROTTLE..........................14-45
CONTROL ILLUMINATION BULB -
INSTALLATION, HEATER-A/C............8L-78
CONTROL ILLUMINATION BULB -
REMOVAL, HEATER-A/C...............8L-78
CONTROL INFORMATION (VECI) LABEL -
DESCRIPTION, VEHICLE EMISSION.....Intro.-8
CONTROL MODULE - DESCRIPTION,
AIRBAG.............................8O-9
CONTROL MODULE - DESCRIPTION,
BODY...............................8E-2
CONTROL MODULE - DESCRIPTION,
SIDE IMPACT AIRBAG.................8O-43
CONTROL MODULE - DESCRIPTION,
TRANSMISSION......................8E-18
CONTROL MODULE - DIAGNOSIS AND
TESTING, BODY.......................8E-7
CONTROL MODULE - INSTALLATION....23-183
CONTROL MODULE - INSTALLATION,
AIRBAG............................8O-12
CONTROL MODULE - INSTALLATION,
BODY...............................8E-7
CONTROL MODULE - INSTALLATION,
SIDE IMPACT AIRBAG.................8O-45
CONTROL MODULE - OPERATION,
AIRBAG............................8O-10
CONTROL MODULE - OPERATION, BODY . . . 8E-5
CONTROL MODULE - OPERATION, SIDE
IMPACT AIRBAG.....................8O-43
CONTROL MODULE - OPERATION,
TRANSMISSION......................8E-18
CONTROL MODULE - REMOVAL........23-183
CONTROL MODULE - REMOVAL, AIRBAG . 8O-11
CONTROL MODULE - REMOVAL, BODY....8E-7
CONTROL MODULE - REMOVAL, SIDE
IMPACT AIRBAG.....................8O-44
CONTROL MOTOR - DESCRIPTION, IDLE
AIR ...............................14-35
CONTROL MOTOR - INSTALLATION, IDLE
AIR ...............................14-36
CONTROL MOTOR - OPERATION, IDLE
AIR ...............................14-35
CONTROL MOTOR - REMOVAL, IDLE AIR . . 14-36
CONTROL RELAY - DESCRIPTION,
TRANSMISSION.....................21-168
CONTROL RELAY - OPERATION,
TRANSMISSION
.....................21-168
CONTROL SWITCH - DESCRIPTION
.....23-184
CONTROL SWITCH - DIAGNOSIS AND
TESTING
..........................23-184
CONTROL SWITCH - INSTALLATION
.....23-184
CONTROL SWITCH - OPERATION
.......23-184CONTROL SWITCH - REMOVAL........23-184
CONTROL SYSTEM - DESCRIPTION,
EMISSION...........................25-1
CONTROL SYSTEM - DESCRIPTION,
EVAPORATION.......................25-24
CONTROLLER ANTILOCK BRAKE -
INSTALLATION.......................8E-10
CONTROLLER ANTILOCK BRAKE -
REMOVAL..........................8E-10
CONVERTER - DESCRIPTION, CATALYTIC . . . 11-2
CONVERTER - DESCRIPTION, TORQUE . . . 21-162
CONVERTER - INSPECTION, CATALYTIC....11-3
CONVERTER - INSTALLATION, CATALYTIC . . 11-3
CONVERTER - INSTALLATION, TORQUE . . 21-167
CONVERTER - OPERATION, TORQUE....21-166
CONVERTER - REMOVAL, CATALYTIC......11-2
CONVERTER - REMOVAL, TORQUE......21-167
CONVERTER HOUSING FLUID LEAK -
DIAGNOSIS AND TESTING.............21-80
COOLANT - DESCRIPTION, ENGINE........0-3
COOLANT LOW INDICATOR -
DESCRIPTION.......................8J-15
COOLANT LOW INDICATOR - OPERATION . 8J-16
COOLANT RECOVERY PRESS
CONTAINER - DESCRIPTION.............7-19
COOLANT RECOVERY PRESS
CONTAINER - OPERATION...............7-19
COOLANT TEMPERATURE SENSOR -
DESCRIPTION, ENGINE.................7-19
COOLANT TEMPERATURE SENSOR -
INSTALLATION, ENGINE................7-21
COOLANT TEMPERATURE SENSOR -
OPERATION, ENGINE...................7-20
COOLANT TEMPERATURE SENSOR -
REMOVAL, ENGINE....................7-20
COOLANT THERMOSTAT - OPERATION,
ENGINE.............................7-21
COOLER - DESCRIPTION, FLUID.........19-20
COOLER - DESCRIPTION, TRANS.........7-32
COOLER - INSTALLATION, FLUID........19-20
COOLER - OPERATION, FLUID..........19-20
COOLER - REMOVAL, FLUID............19-20
COOLING, SPECIAL TOOLS..............7-14
COOLING SYSTEM - OPERATION..........7-2
COOLING SYSTEM - REVERSE
FLUSHING - STANDARD PROCEDURE.....7-12
COOLING SYSTEM 3.7L ENGINE -
DESCRIPTION.........................7-1
COOLING SYSTEM 3.7L ENGINE -
STANDARD PROCEDURE, DRAINING......7-12
COOLING SYSTEM 3.7L ENGINE -
STANDARD PROCEDURE, REFILLING......7-12
COOLING SYSTEM DIAGNOSIS CHART -
DIAGNOSIS AND TESTING...............7-6
COOLING SYSTEM LEAKS - DIAGNOSIS
AND TESTING.........................7-4
COOLING SYSTEM REQUIREMENTS -
DESCRIPTION........................24-1
COOLING SYSTEM ROUTING 3.7L
ENGINE - DESCRIPTION.................7-2
CORE - DESCRIPTION, HEATER.........24-52
CORE - INSTALLATION, HEATER.........24-53
CORE - OPERATION, HEATER...........24-52
CORE - REMOVAL, HEATER............24-52
CORE AND OIL GALLERY PLUGS -
STANDARD PROCEDURE, ENGINE........9-10
COURTESY LAMP BULB - INSTALLATION . . 8L-76
COURTESY LAMP BULB - REMOVAL.....8L-75
COURTESY LAMP REPLACEMENT -
STANDARD PROCEDURE...............8M-2
COURTESY LAMP UNIT - INSTALLATION . . 8L-77
COURTESY LAMP UNIT - REMOVAL......8L-76
COVER - DESCRIPTION, STRUCTURAL.....9-55
COVER - FRONT - INSTALLATION, SEAT
BACK.............................23-167
COVER - FRONT - INSTALLATION, SEAT
CUSHION..........................23-167
COVER - FRONT - REMOVAL, SEAT BACK . 23-166
COVER - FRONT - REMOVAL, SEAT
CUSHION..........................23-167
COVER - INSTALLATION, COWL TRIM . . . 23-157
COVER - INSTALLATION, INSTRUMENT
PANEL TOP
........................23-153
COVER - INSTALLATION, STRUCTURAL
....9-55
COVER - OPERATION, STRUCTURAL
......9-55
COVER - REAR - INSTALLATION, SEAT
BACK
.............................23-169
COVER - REAR - REMOVAL, SEAT BACK
. 23-169
6 INDEXKJ
Description Group-Page Description Group-Page Description Group-Page