key LAND ROVER DEFENDER 1996 Workshop Manual
[x] Cancel search | Manufacturer: LAND ROVER, Model Year: 1996, Model line: DEFENDER, Model: LAND ROVER DEFENDER 1996Pages: 455, PDF Size: 6.44 MB
Page 12 of 455
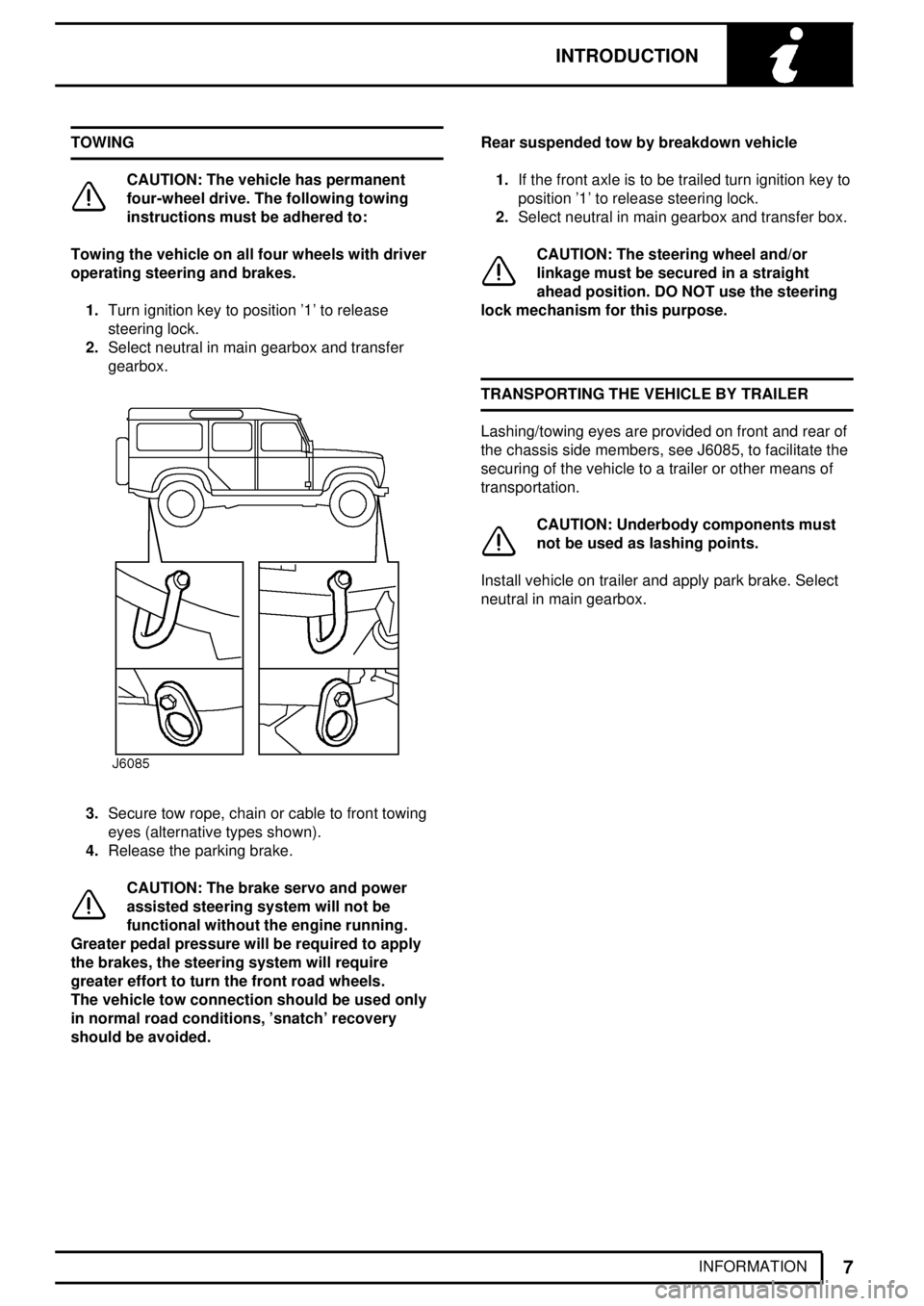
INTRODUCTION
7
INFORMATION TOWING
CAUTION: The vehicle has permanent
four-wheel drive. The following towing
instructions must be adhered to:
Towing the vehicle on all four wheels with driver
operating steering and brakes.
1.Turn ignition key to position '1' to release
steering lock.
2.Select neutral in main gearbox and transfer
gearbox.
3.Secure tow rope, chain or cable to front towing
eyes (alternative types shown).
4.Release the parking brake.
CAUTION: The brake servo and power
assisted steering system will not be
functional without the engine running.
Greater pedal pressure will be required to apply
the brakes, the steering system will require
greater effort to turn the front road wheels.
The vehicle tow connection should be used only
in normal road conditions, 'snatch' recovery
should be avoided.Rear suspended tow by breakdown vehicle
1.If the front axle is to be trailed turn ignition key to
position '1' to release steering lock.
2.Select neutral in main gearbox and transfer box.
CAUTION: The steering wheel and/or
linkage must be secured in a straight
ahead position. DO NOT use the steering
lock mechanism for this purpose.
TRANSPORTING THE VEHICLE BY TRAILER
Lashing/towing eyes are provided on front and rear of
the chassis side members, see J6085, to facilitate the
securing of the vehicle to a trailer or other means of
transportation.
CAUTION: Underbody components must
not be used as lashing points.
Install vehicle on trailer and apply park brake. Select
neutral in main gearbox.
Page 38 of 455
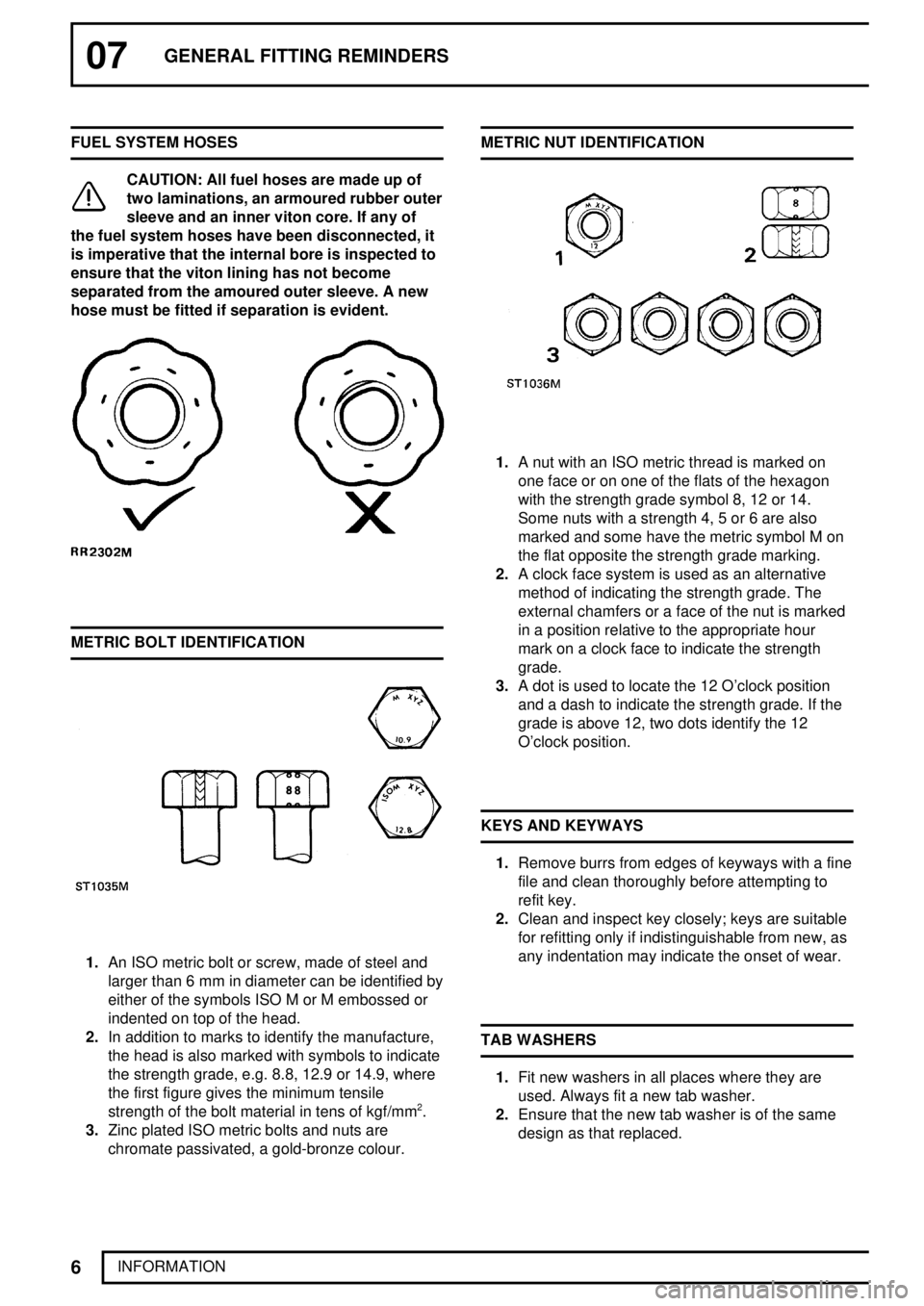
07GENERAL FITTING REMINDERS
6
INFORMATION FUEL SYSTEM HOSES
CAUTION: All fuel hoses are made up of
two laminations, an armoured rubber outer
sleeve and an inner viton core. If any of
the fuel system hoses have been disconnected, it
is imperative that the internal bore is inspected to
ensure that the viton lining has not become
separated from the amoured outer sleeve. A new
hose must be fitted if separation is evident.
METRIC BOLT IDENTIFICATION
1.An ISO metric bolt or screw, made of steel and
larger than 6 mm in diameter can be identified by
either of the symbols ISO M or M embossed or
indented on top of the head.
2.In addition to marks to identify the manufacture,
the head is also marked with symbols to indicate
the strength grade, e.g. 8.8, 12.9 or 14.9, where
the first figure gives the minimum tensile
strength of the bolt material in tens of kgf/mm
2.
3.Zinc plated ISO metric bolts and nuts are
chromate passivated, a gold-bronze colour.METRIC NUT IDENTIFICATION
1.A nut with an ISO metric thread is marked on
one face or on one of the flats of the hexagon
with the strength grade symbol 8, 12 or 14.
Some nuts with a strength 4, 5 or 6 are also
marked and some have the metric symbol M on
the flat opposite the strength grade marking.
2.A clock face system is used as an alternative
method of indicating the strength grade. The
external chamfers or a face of the nut is marked
in a position relative to the appropriate hour
mark on a clock face to indicate the strength
grade.
3.A dot is used to locate the 12 O'clock position
and a dash to indicate the strength grade. If the
grade is above 12, two dots identify the 12
O'clock position.
KEYS AND KEYWAYS
1.Remove burrs from edges of keyways with a fine
file and clean thoroughly before attempting to
refit key.
2.Clean and inspect key closely; keys are suitable
for refitting only if indistinguishable from new, as
any indentation may indicate the onset of wear.
TAB WASHERS
1.Fit new washers in all places where they are
used. Always fit a new tab washer.
2.Ensure that the new tab washer is of the same
design as that replaced.
Page 67 of 455
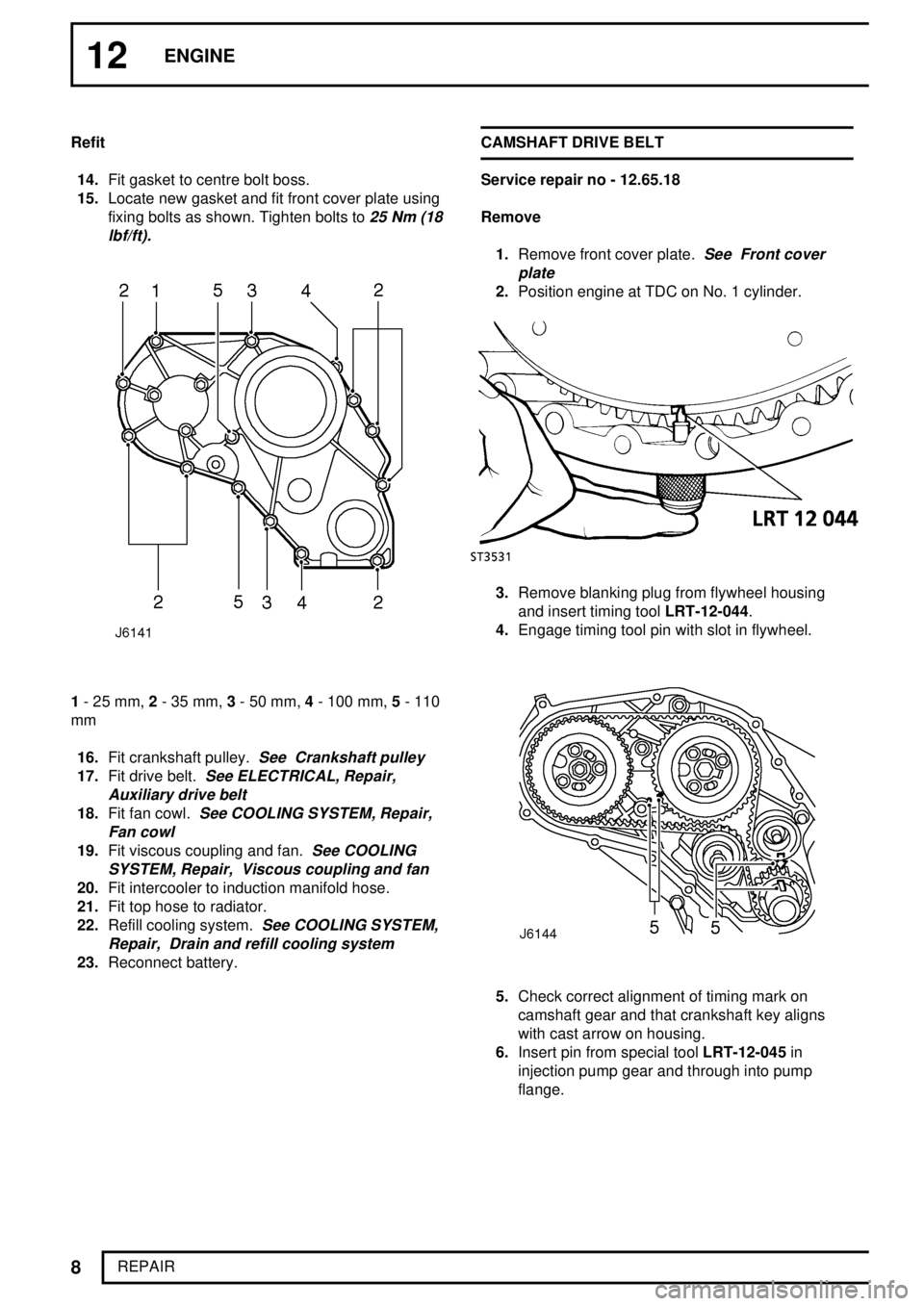
12ENGINE
8
REPAIR Refit
14.Fit gasket to centre bolt boss.
15.Locate new gasket and fit front cover plate using
fixing bolts as shown. Tighten bolts to
25 Nm (18
lbf/ft).
1- 25 mm,2- 35 mm,3- 50 mm,4- 100 mm,5- 110
mm
16.Fit crankshaft pulley.
See Crankshaft pulley
17.Fit drive belt.See ELECTRICAL, Repair,
Auxiliary drive belt
18.Fit fan cowl.See COOLING SYSTEM, Repair,
Fan cowl
19.Fit viscous coupling and fan.See COOLING
SYSTEM, Repair, Viscous coupling and fan
20.Fit intercooler to induction manifold hose.
21.Fit top hose to radiator.
22.Refill cooling system.
See COOLING SYSTEM,
Repair, Drain and refill cooling system
23.Reconnect battery.CAMSHAFT DRIVE BELT
Service repair no - 12.65.18
Remove
1.Remove front cover plate.
See Front cover
plate
2.Position engine at TDC on No. 1 cylinder.
3.Remove blanking plug from flywheel housing
and insert timing toolLRT-12-044.
4.Engage timing tool pin with slot in flywheel.
5.Check correct alignment of timing mark on
camshaft gear and that crankshaft key aligns
with cast arrow on housing.
6.Insert pin from special toolLRT-12-045in
injection pump gear and through into pump
flange.
Page 69 of 455
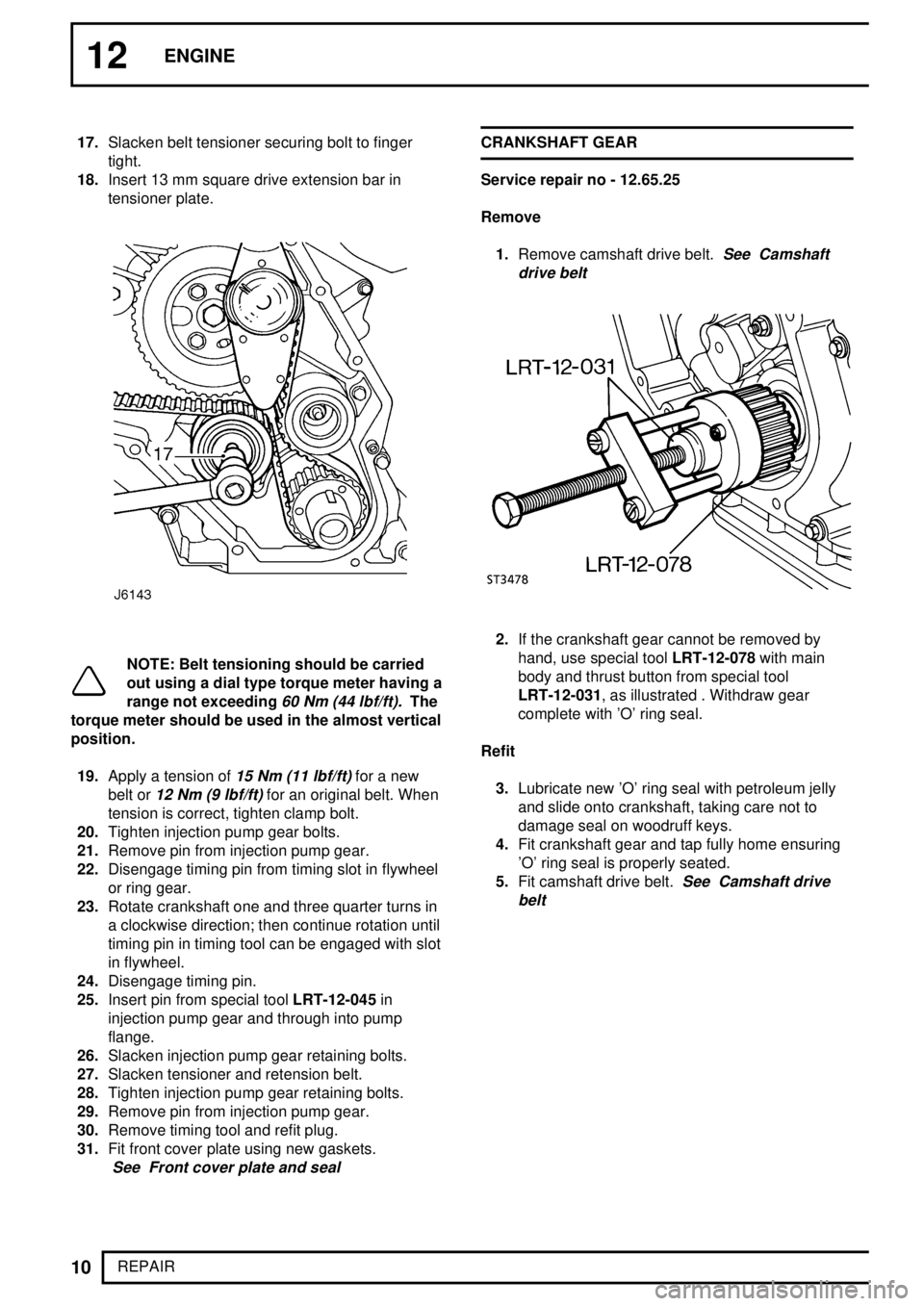
12ENGINE
10
REPAIR 17.Slacken belt tensioner securing bolt to finger
tight.
18.Insert 13 mm square drive extension bar in
tensioner plate.
NOTE: Belt tensioning should be carried
out using a dial type torque meter having a
range not exceeding
60 Nm (44 lbf/ft).The
torque meter should be used in the almost vertical
position.
19.Apply a tension of
15 Nm (11 lbf/ft)for a new
belt or
12 Nm (9 lbf/ft)for an original belt. When
tension is correct, tighten clamp bolt.
20.Tighten injection pump gear bolts.
21.Remove pin from injection pump gear.
22.Disengage timing pin from timing slot in flywheel
or ring gear.
23.Rotate crankshaft one and three quarter turns in
a clockwise direction; then continue rotation until
timing pin in timing tool can be engaged with slot
in flywheel.
24.Disengage timing pin.
25.Insert pin from special toolLRT-12-045in
injection pump gear and through into pump
flange.
26.Slacken injection pump gear retaining bolts.
27.Slacken tensioner and retension belt.
28.Tighten injection pump gear retaining bolts.
29.Remove pin from injection pump gear.
30.Remove timing tool and refit plug.
31.Fit front cover plate using new gaskets.
See Front cover plate and seal
CRANKSHAFT GEAR
Service repair no - 12.65.25
Remove
1.Remove camshaft drive belt.
See Camshaft
drive belt
2.If the crankshaft gear cannot be removed by
hand, use special toolLRT-12-078with main
body and thrust button from special tool
LRT-12-031, as illustrated . Withdraw gear
complete with 'O' ring seal.
Refit
3.Lubricate new 'O' ring seal with petroleum jelly
and slide onto crankshaft, taking care not to
damage seal on woodruff keys.
4.Fit crankshaft gear and tap fully home ensuring
'O' ring seal is properly seated.
5.Fit camshaft drive belt.
See Camshaft drive
belt
Page 150 of 455
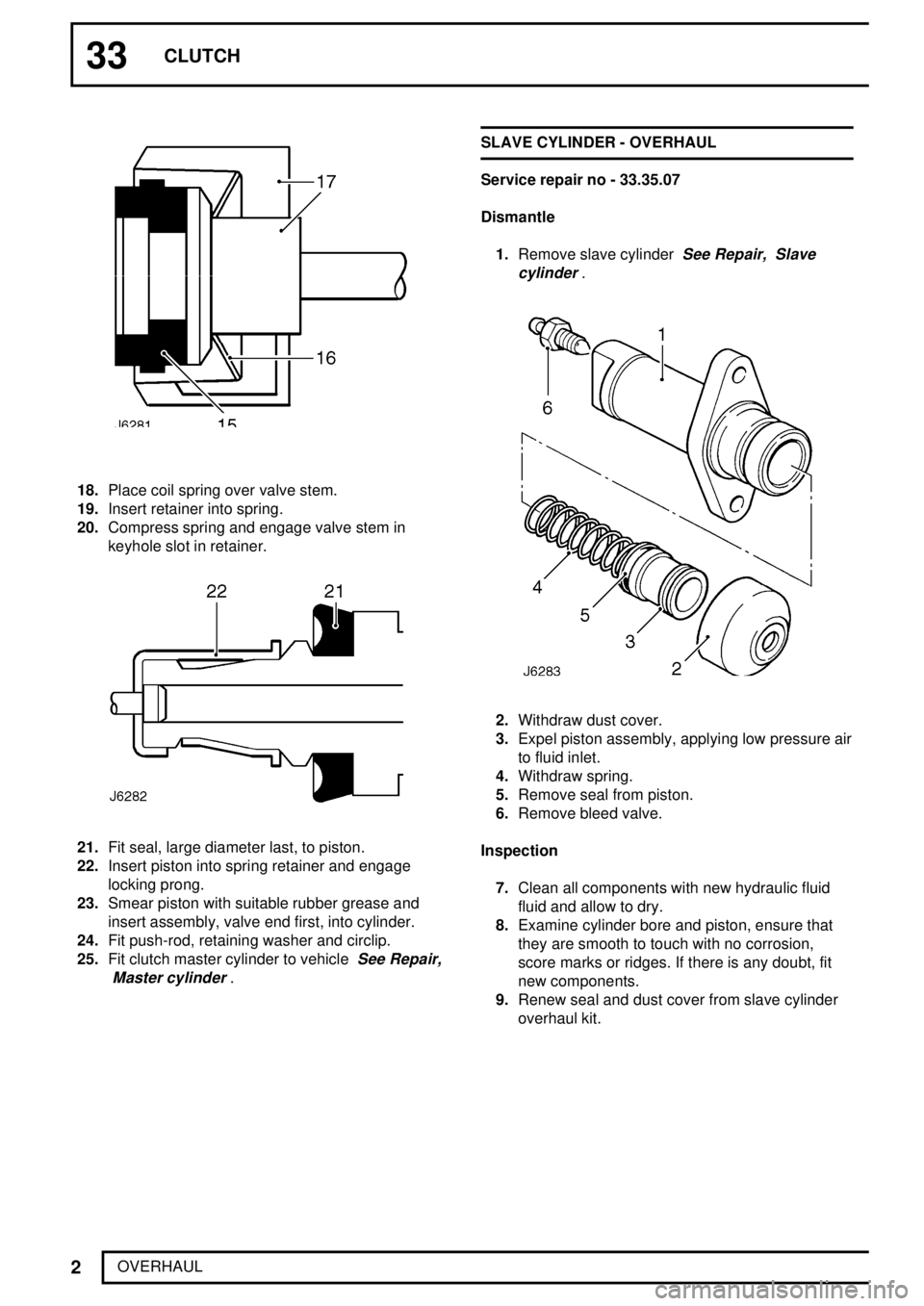
33CLUTCH
2
OVERHAUL
18.Place coil spring over valve stem.
19.Insert retainer into spring.
20.Compress spring and engage valve stem in
keyhole slot in retainer.
21.Fit seal, large diameter last, to piston.
22.Insert piston into spring retainer and engage
locking prong.
23.Smear piston with suitable rubber grease and
insert assembly, valve end first, into cylinder.
24.Fit push-rod, retaining washer and circlip.
25.Fit clutch master cylinder to vehicle
See Repair,
Master cylinder
.SLAVE CYLINDER - OVERHAUL
Service repair no - 33.35.07
Dismantle
1.Remove slave cylinder
See Repair, Slave
cylinder
.
2.Withdraw dust cover.
3.Expel piston assembly, applying low pressure air
to fluid inlet.
4.Withdraw spring.
5.Remove seal from piston.
6.Remove bleed valve.
Inspection
7.Clean all components with new hydraulic fluid
fluid and allow to dry.
8.Examine cylinder bore and piston, ensure that
they are smooth to touch with no corrosion,
score marks or ridges. If there is any doubt, fit
new components.
9.Renew seal and dust cover from slave cylinder
overhaul kit.
Page 290 of 455
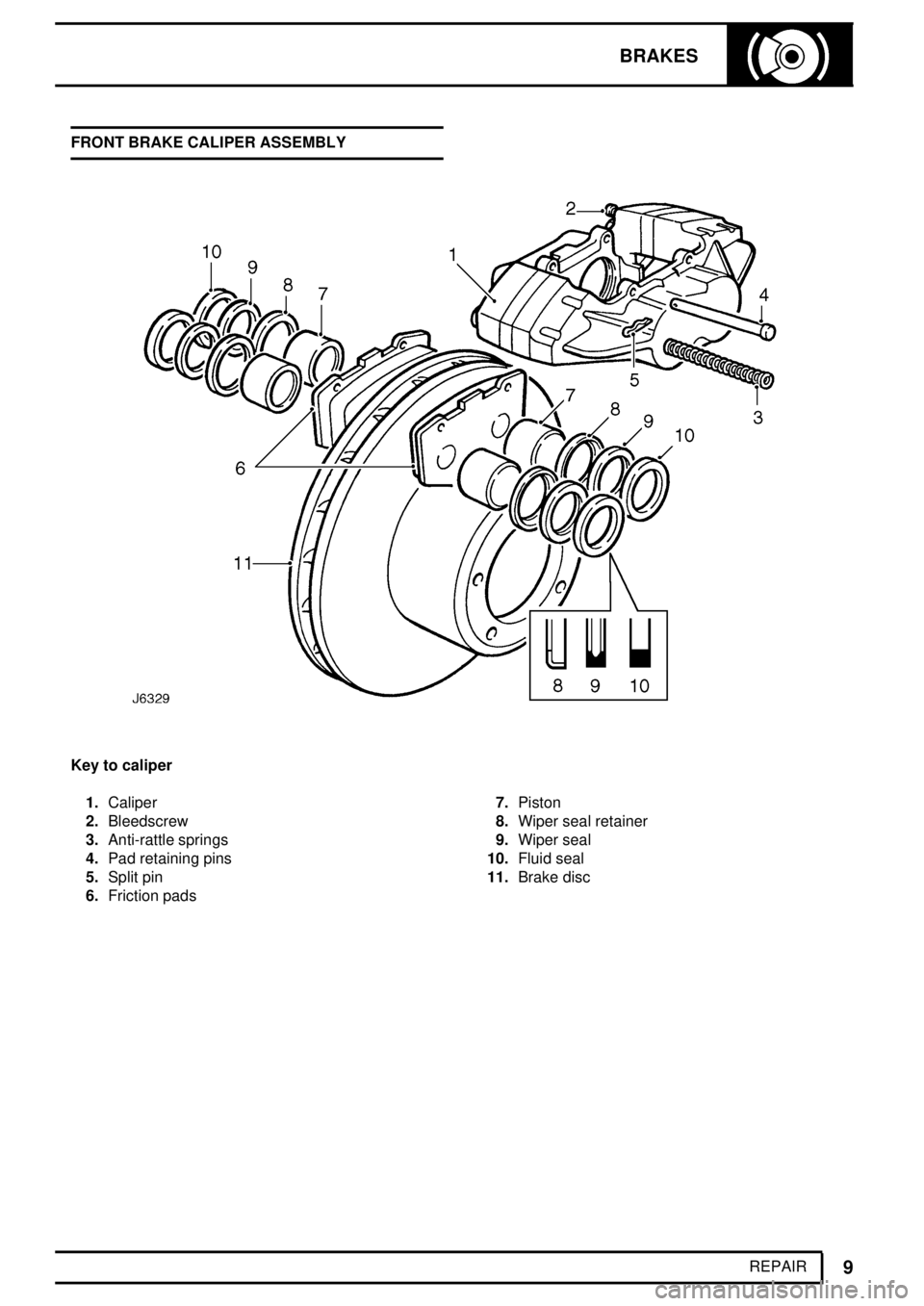
BRAKES
9
REPAIR FRONT BRAKE CALIPER ASSEMBLY
Key to caliper
1.Caliper
2.Bleedscrew
3.Anti-rattle springs
4.Pad retaining pins
5.Split pin
6.Friction pads7.Piston
8.Wiper seal retainer
9.Wiper seal
10.Fluid seal
11.Brake disc
Page 293 of 455
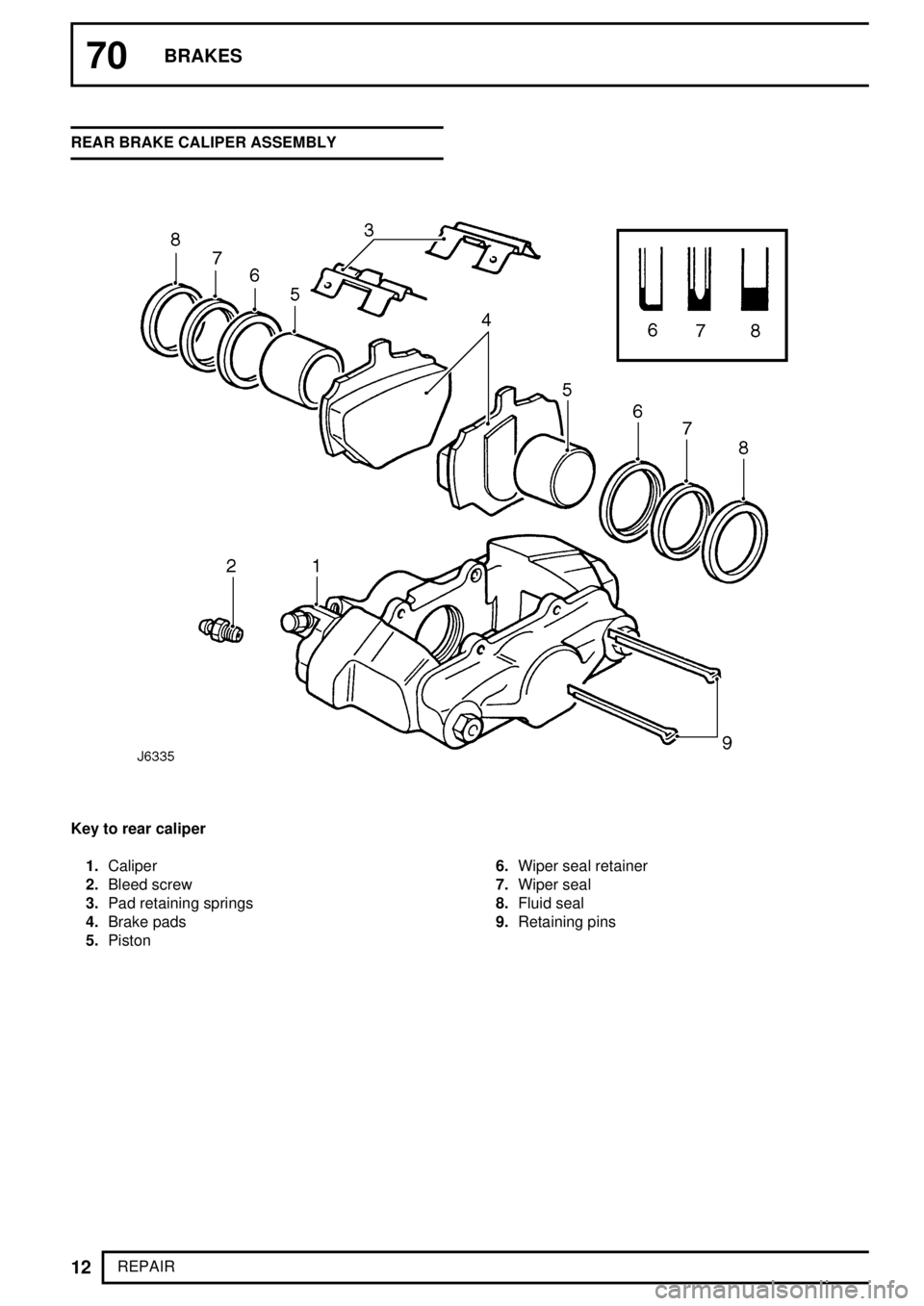
70BRAKES
12
REPAIR REAR BRAKE CALIPER ASSEMBLY
Key to rear caliper
1.Caliper
2.Bleed screw
3.Pad retaining springs
4.Brake pads
5.Piston6.Wiper seal retainer
7.Wiper seal
8.Fluid seal
9.Retaining pins
Page 300 of 455
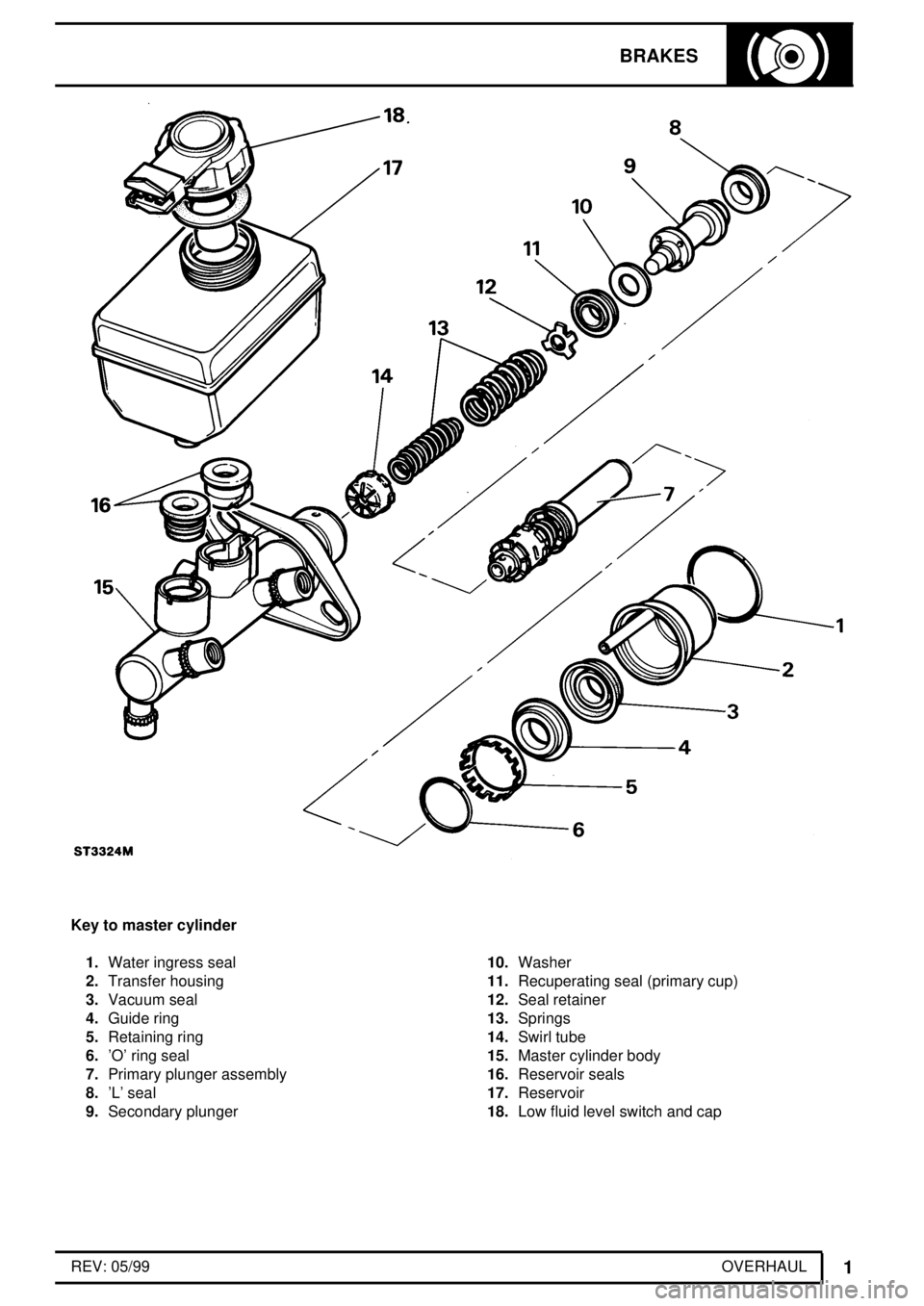
BRAKES
1
OVERHAUL REV: 05/99
Key to master cylinder
1.Water ingress seal
2.Transfer housing
3.Vacuum seal
4.Guide ring
5.Retaining ring
6.'O' ring seal
7.Primary plunger assembly
8.'L' seal
9.Secondary plunger10.Washer
11.Recuperating seal (primary cup)
12.Seal retainer
13.Springs
14.Swirl tube
15.Master cylinder body
16.Reservoir seals
17.Reservoir
18.Low fluid level switch and cap
Page 306 of 455
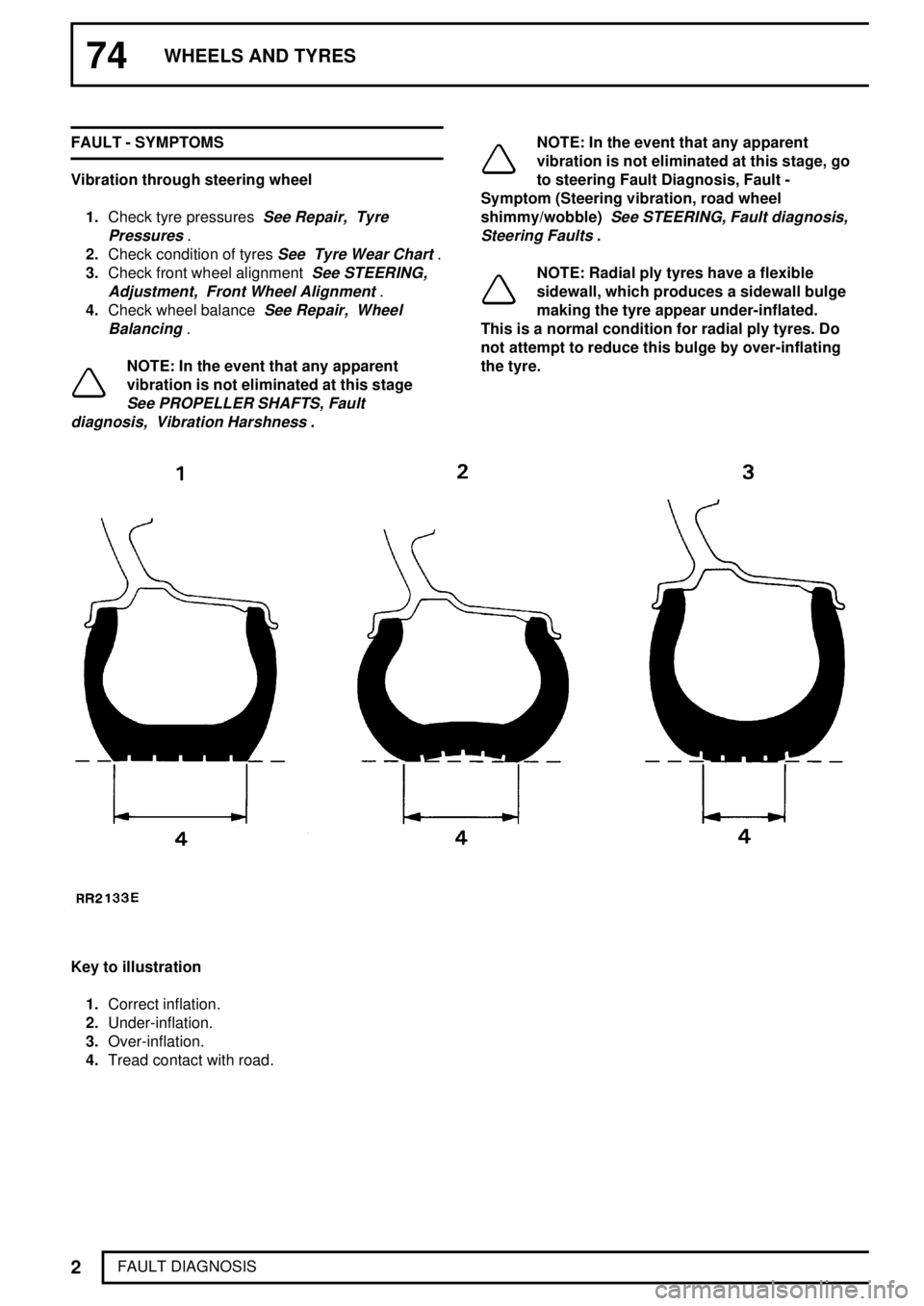
74WHEELS AND TYRES
2
FAULT DIAGNOSIS FAULT - SYMPTOMS
Vibration through steering wheel
1.Check tyre pressures
See Repair, Tyre
Pressures
.
2.Check condition of tyres
See Tyre Wear Chart.
3.Check front wheel alignment
See STEERING,
Adjustment, Front Wheel Alignment
.
4.Check wheel balance
See Repair, Wheel
Balancing
.
NOTE: In the event that any apparent
vibration is not eliminated at this stage
See PROPELLER SHAFTS, Fault
diagnosis, Vibration Harshness
.
NOTE: In the event that any apparent
vibration is not eliminated at this stage, go
to steering Fault Diagnosis, Fault -
Symptom (Steering vibration, road wheel
shimmy/wobble)
See STEERING, Fault diagnosis,
Steering Faults
.
NOTE: Radial ply tyres have a flexible
sidewall, which produces a sidewall bulge
making the tyre appear under-inflated.
This is a normal condition for radial ply tyres. Do
not attempt to reduce this bulge by over-inflating
the tyre.
Key to illustration
1.Correct inflation.
2.Under-inflation.
3.Over-inflation.
4.Tread contact with road.
Page 321 of 455
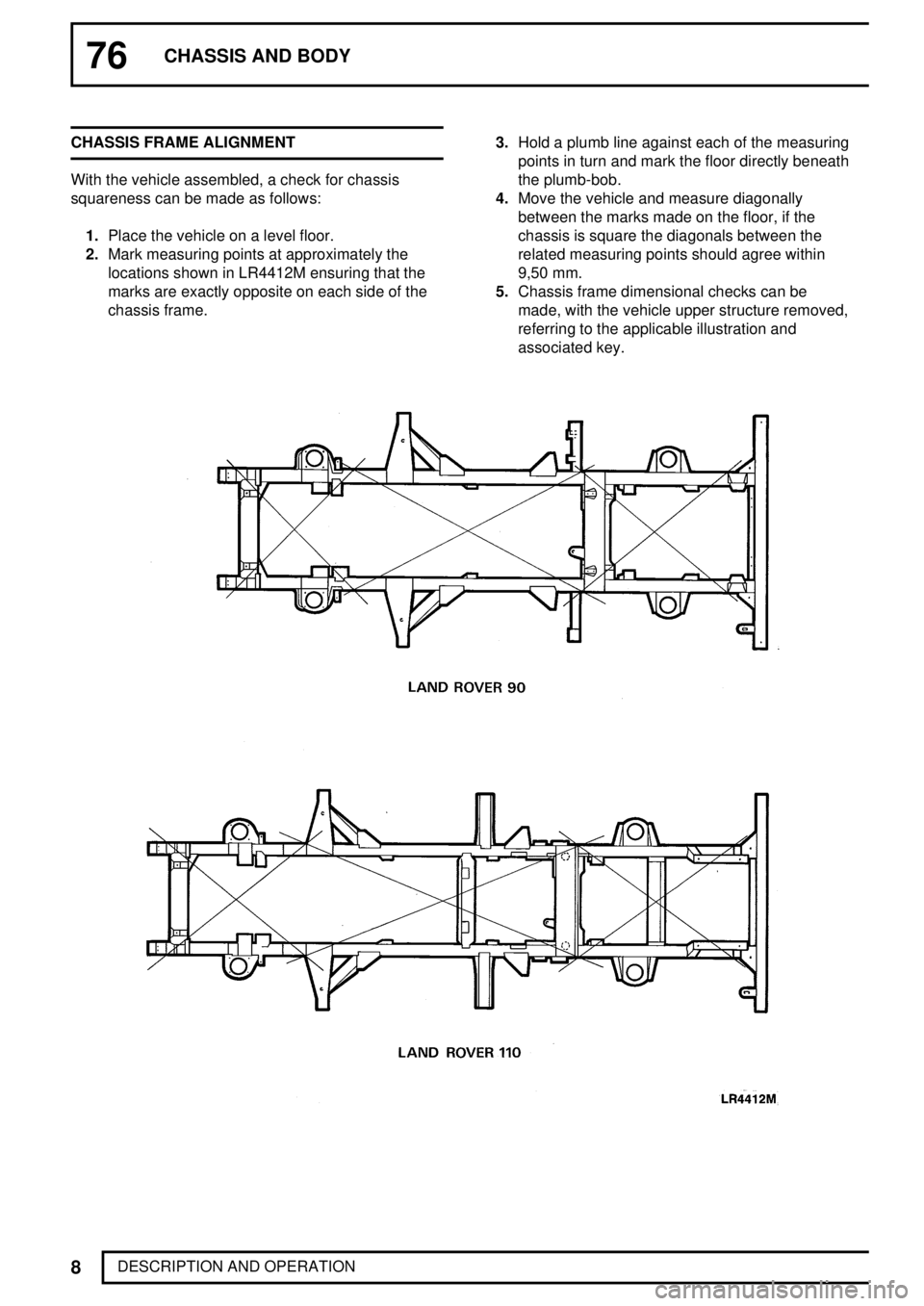
76CHASSIS AND BODY
8
DESCRIPTION AND OPERATION CHASSIS FRAME ALIGNMENT
With the vehicle assembled, a check for chassis
squareness can be made as follows:
1.Place the vehicle on a level floor.
2.Mark measuring points at approximately the
locations shown in LR4412M ensuring that the
marks are exactly opposite on each side of the
chassis frame.3.Hold a plumb line against each of the measuring
points in turn and mark the floor directly beneath
the plumb-bob.
4.Move the vehicle and measure diagonally
between the marks made on the floor, if the
chassis is square the diagonals between the
related measuring points should agree within
9,50 mm.
5.Chassis frame dimensional checks can be
made, with the vehicle upper structure removed,
referring to the applicable illustration and
associated key.