engine LAND ROVER DEFENDER 1996 User Guide
[x] Cancel search | Manufacturer: LAND ROVER, Model Year: 1996, Model line: DEFENDER, Model: LAND ROVER DEFENDER 1996Pages: 455, PDF Size: 6.44 MB
Page 16 of 455
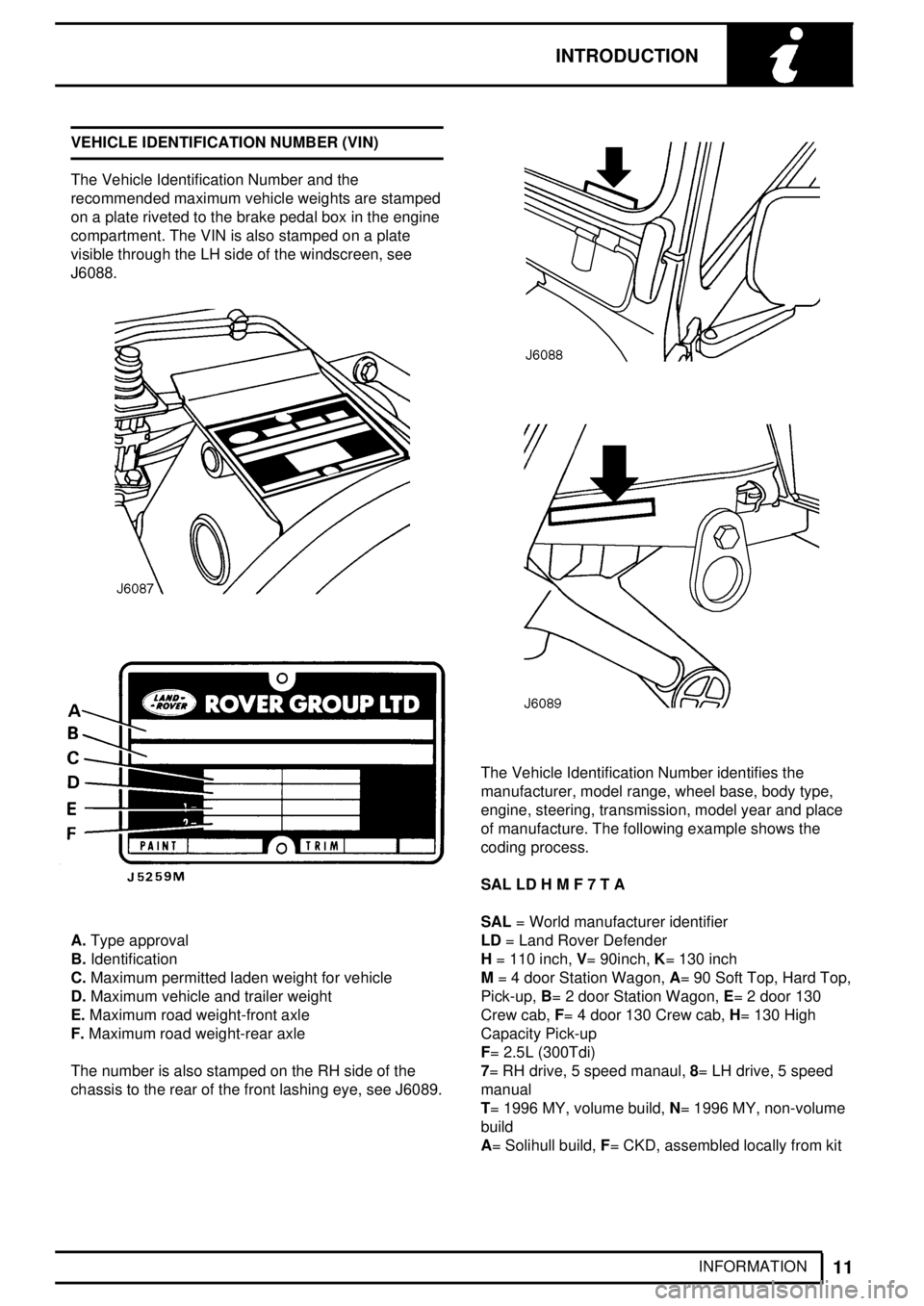
INTRODUCTION
11
INFORMATION VEHICLE IDENTIFICATION NUMBER (VIN)
The Vehicle Identification Number and the
recommended maximum vehicle weights are stamped
on a plate riveted to the brake pedal box in the engine
compartment. The VIN is also stamped on a plate
visible through the LH side of the windscreen, see
J6088.
A.Type approval
B.Identification
C.Maximum permitted laden weight for vehicle
D.Maximum vehicle and trailer weight
E.Maximum road weight-front axle
F.Maximum road weight-rear axle
The number is also stamped on the RH side of the
chassis to the rear of the front lashing eye, see J6089.
The Vehicle Identification Number identifies the
manufacturer, model range, wheel base, body type,
engine, steering, transmission, model year and place
of manufacture. The following example shows the
coding process.
SALLDHMF7TA
SAL= World manufacturer identifier
LD= Land Rover Defender
H= 110 inch,V= 90inch,K= 130 inch
M= 4 door Station Wagon,A= 90 Soft Top, Hard Top,
Pick-up,B= 2 door Station Wagon,E= 2 door 130
Crew cab,F= 4 door 130 Crew cab,H= 130 High
Capacity Pick-up
F= 2.5L (300Tdi)
7= RH drive, 5 speed manaul,8= LH drive, 5 speed
manual
T= 1996 MY, volume build,N= 1996 MY, non-volume
build
A= Solihull build,F= CKD, assembled locally from kit
Page 17 of 455
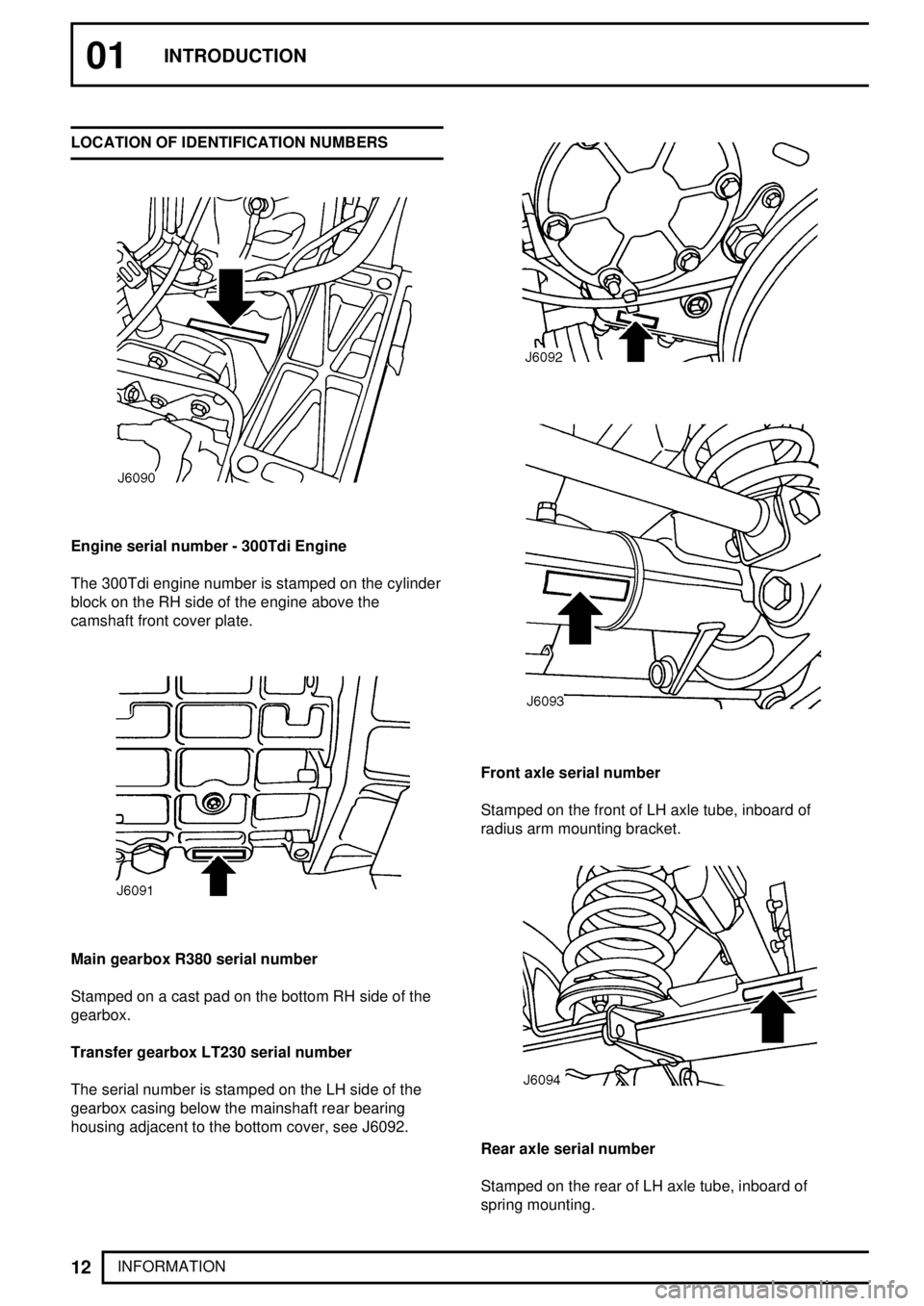
01INTRODUCTION
12
INFORMATION LOCATION OF IDENTIFICATION NUMBERS
Engine serial number - 300Tdi Engine
The 300Tdi engine number is stamped on the cylinder
block on the RH side of the engine above the
camshaft front cover plate.
Main gearbox R380 serial number
Stamped on a cast pad on the bottom RH side of the
gearbox.
Transfer gearbox LT230 serial number
The serial number is stamped on the LH side of the
gearbox casing below the mainshaft rear bearing
housing adjacent to the bottom cover, see J6092.
Front axle serial number
Stamped on the front of LH axle tube, inboard of
radius arm mounting bracket.
Rear axle serial number
Stamped on the rear of LH axle tube, inboard of
spring mounting.
Page 18 of 455
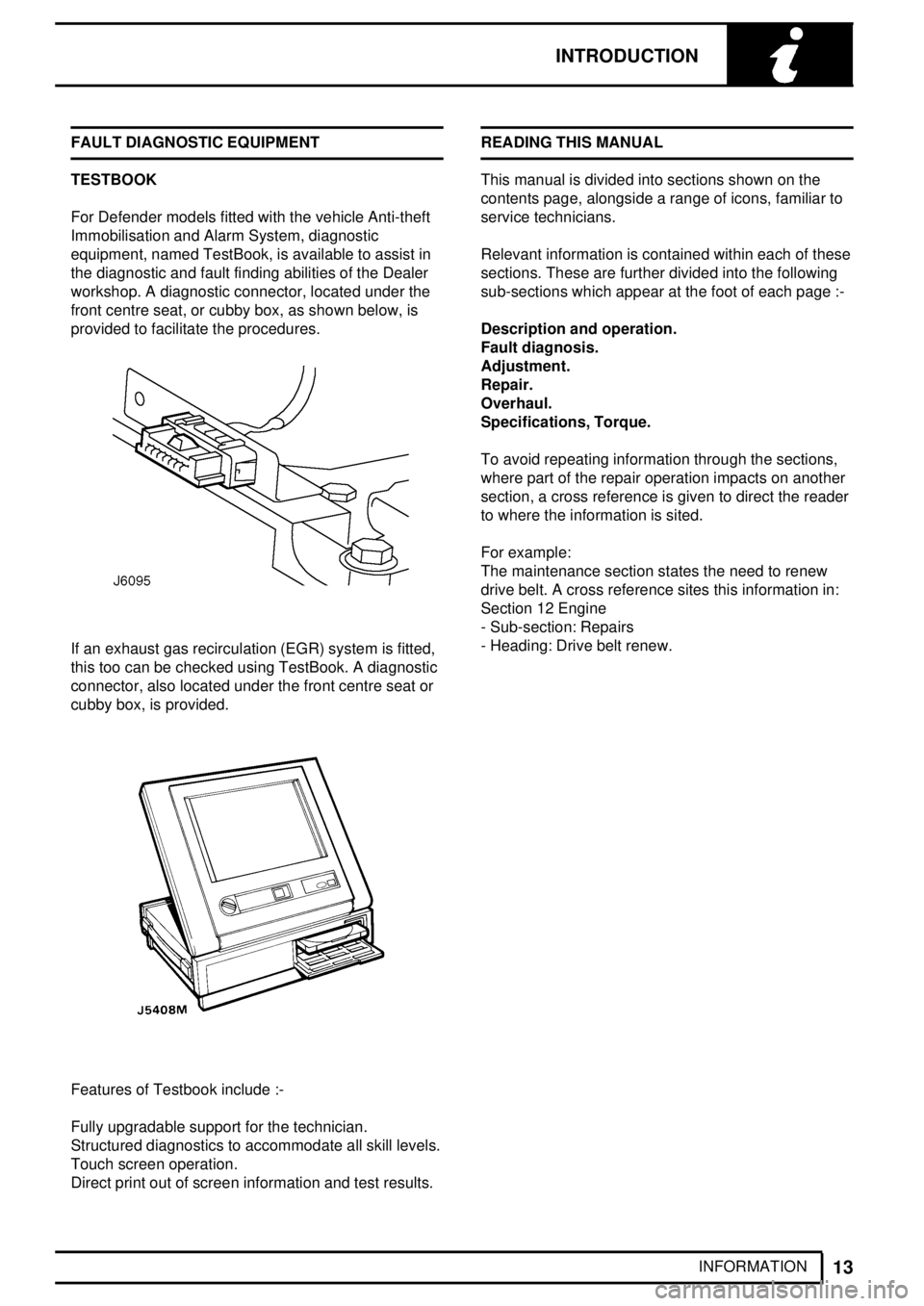
INTRODUCTION
13
INFORMATION FAULT DIAGNOSTIC EQUIPMENT
TESTBOOK
For Defender models fitted with the vehicle Anti-theft
Immobilisation and Alarm System, diagnostic
equipment, named TestBook, is available to assist in
the diagnostic and fault finding abilities of the Dealer
workshop. A diagnostic connector, located under the
front centre seat, or cubby box, as shown below, is
provided to facilitate the procedures.
If an exhaust gas recirculation (EGR) system is fitted,
this too can be checked using TestBook. A diagnostic
connector, also located under the front centre seat or
cubby box, is provided.
Features of Testbook include :-
Fully upgradable support for the technician.
Structured diagnostics to accommodate all skill levels.
Touch screen operation.
Direct print out of screen information and test results.READING THIS MANUAL
This manual is divided into sections shown on the
contents page, alongside a range of icons, familiar to
service technicians.
Relevant information is contained within each of these
sections. These are further divided into the following
sub-sections which appear at the foot of each page :-
Description and operation.
Fault diagnosis.
Adjustment.
Repair.
Overhaul.
Specifications, Torque.
To avoid repeating information through the sections,
where part of the repair operation impacts on another
section, a cross reference is given to direct the reader
to where the information is sited.
For example:
The maintenance section states the need to renew
drive belt. A cross reference sites this information in:
Section 12 Engine
- Sub-section: Repairs
- Heading: Drive belt renew.
Page 19 of 455
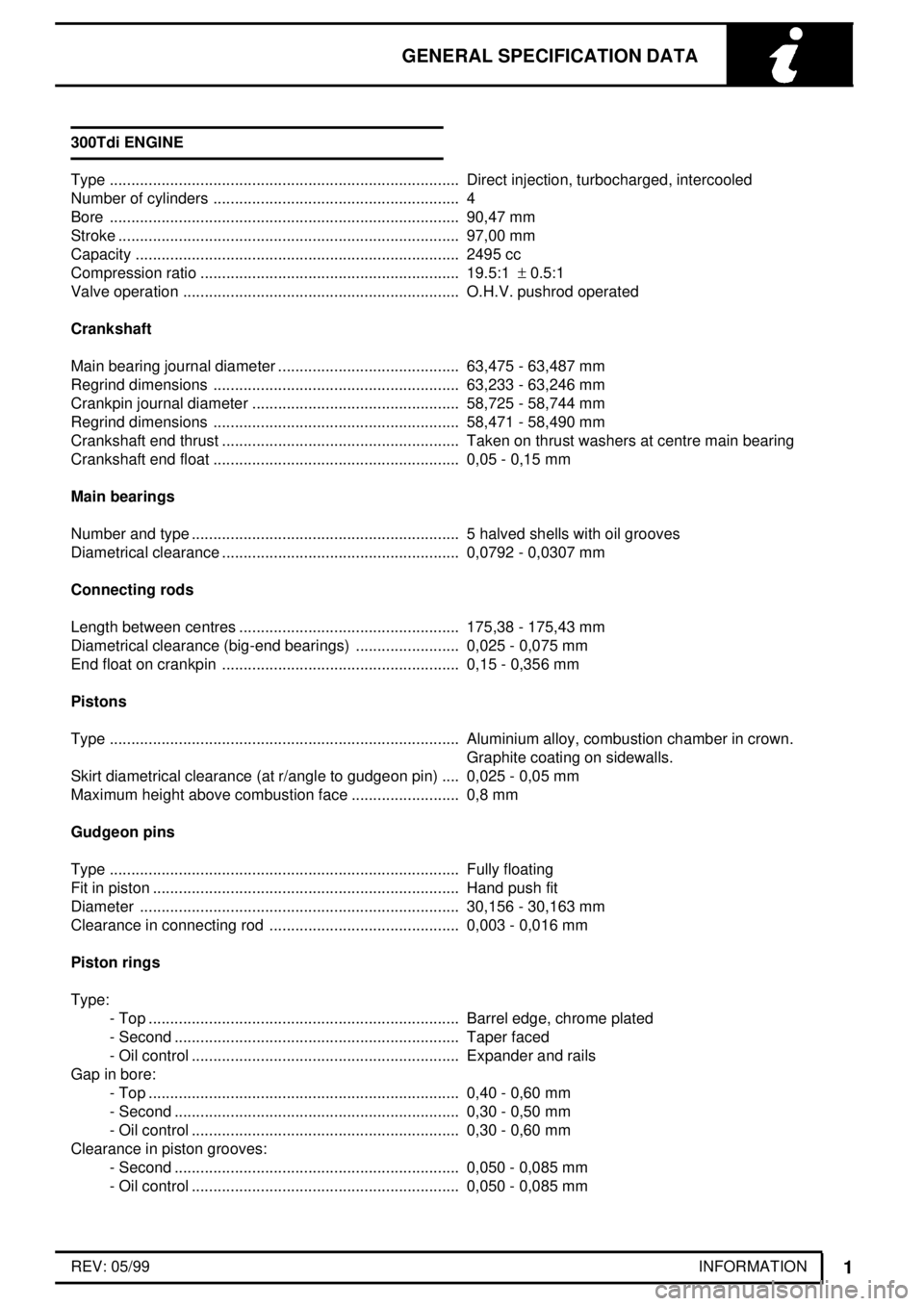
GENERAL SPECIFICATION DATA
1
INFORMATION REV: 05/99 300Tdi ENGINE
Type Direct injection, turbocharged, intercooled.................................................................................
Number of cylinders 4.........................................................
Bore 90,47 mm.................................................................................
Stroke 97,00 mm...............................................................................
Capacity 2495 cc...........................................................................
Compression ratio 19.5:1±0.5:1 ............................................................
Valve operation O.H.V. pushrod operated................................................................
Crankshaft
Main bearing journal diameter 63,475 - 63,487 mm..........................................
Regrind dimensions 63,233 - 63,246 mm.........................................................
Crankpin journal diameter 58,725 - 58,744 mm................................................
Regrind dimensions 58,471 - 58,490 mm.........................................................
Crankshaft end thrust Taken on thrust washers at centre main bearing.......................................................
Crankshaft end float 0,05 - 0,15 mm.........................................................
Main bearings
Number and type 5 halved shells with oil grooves..............................................................
Diametrical clearance 0,0792 - 0,0307 mm.......................................................
Connecting rods
Length between centres 175,38 - 175,43 mm...................................................
Diametrical clearance (big-end bearings) 0,025 - 0,075 mm........................
End float on crankpin 0,15 - 0,356 mm.......................................................
Pistons
Type Aluminium alloy, combustion chamber in crown..................................................................................
Graphite coating on sidewalls.
Skirt diametrical clearance (at r/angle to gudgeon pin) 0,025 - 0,05 mm....
Maximum height above combustion face 0,8 mm.........................
Gudgeon pins
Type Fully floating.................................................................................
Fit in piston Hand push fit.......................................................................
Diameter 30,156 - 30,163 mm..........................................................................
Clearance in connecting rod 0,003 - 0,016 mm............................................
Piston rings
Type:
- Top Barrel edge, chrome plated........................................................................
- Second Taper faced..................................................................
- Oil control Expander and rails..............................................................
Gap in bore:
- Top 0,40 - 0,60 mm........................................................................
- Second 0,30 - 0,50 mm..................................................................
- Oil control 0,30 - 0,60 mm..............................................................
Clearance in piston grooves:
- Second 0,050 - 0,085 mm..................................................................
- Oil control 0,050 - 0,085 mm..............................................................
Page 20 of 455
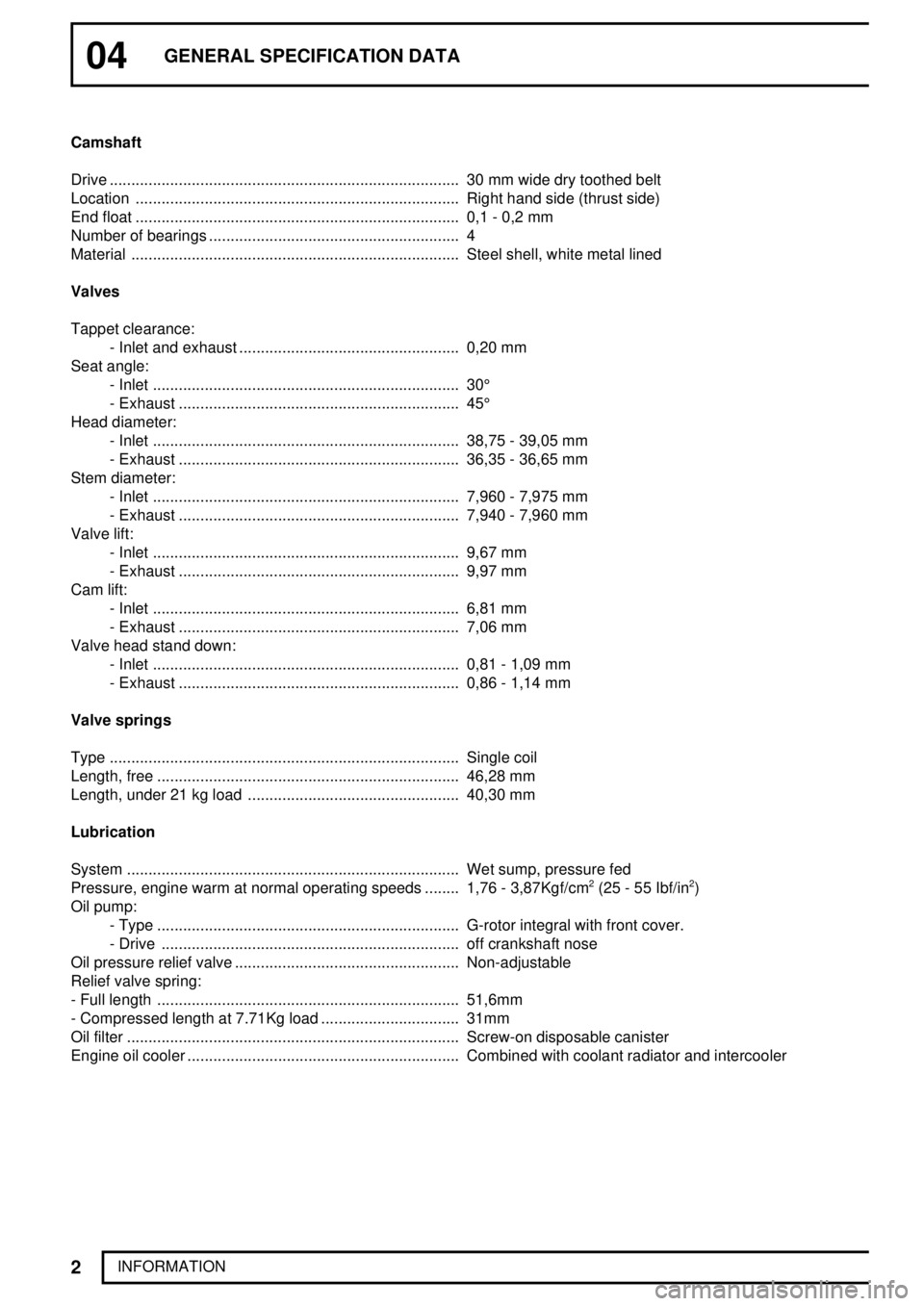
04GENERAL SPECIFICATION DATA
2
INFORMATION Camshaft
Drive 30 mm wide dry toothed belt.................................................................................
Location Right hand side (thrust side)...........................................................................
End float 0,1 - 0,2 mm...........................................................................
Number of bearings 4..........................................................
Material Steel shell, white metal lined............................................................................
Valves
Tappet clearance:
- Inlet and exhaust 0,20 mm...................................................
Seat angle:
- Inlet 30° .......................................................................
- Exhaust 45° .................................................................
Head diameter:
- Inlet 38,75 - 39,05 mm.......................................................................
- Exhaust 36,35 - 36,65 mm.................................................................
Stem diameter:
- Inlet 7,960 - 7,975 mm.......................................................................
- Exhaust 7,940 - 7,960 mm.................................................................
Valve lift:
- Inlet 9,67 mm.......................................................................
- Exhaust 9,97 mm.................................................................
Cam lift:
- Inlet 6,81 mm.......................................................................
- Exhaust 7,06 mm.................................................................
Valve head stand down:
- Inlet 0,81 - 1,09 mm.......................................................................
- Exhaust 0,86 - 1,14 mm.................................................................
Valve springs
Type Single coil.................................................................................
Length, free 46,28 mm......................................................................
Length, under 21 kg load 40,30 mm.................................................
Lubrication
System Wet sump, pressure fed.............................................................................
Pressure, engine warm at normal operating speeds 1,76 - 3,87Kgf/cm
2(25 - 55 Ibf/in2) ........
Oil pump:
- Type G-rotor integral with front cover.......................................................................
- Drive off crankshaft nose.....................................................................
Oil pressure relief valve Non-adjustable....................................................
Relief valve spring:
- Full length 51,6mm......................................................................
- Compressed length at 7.71Kg load 31mm................................
Oil filter Screw-on disposable canister.............................................................................
Engine oil cooler Combined with coolant radiator and intercooler...............................................................
Page 31 of 455
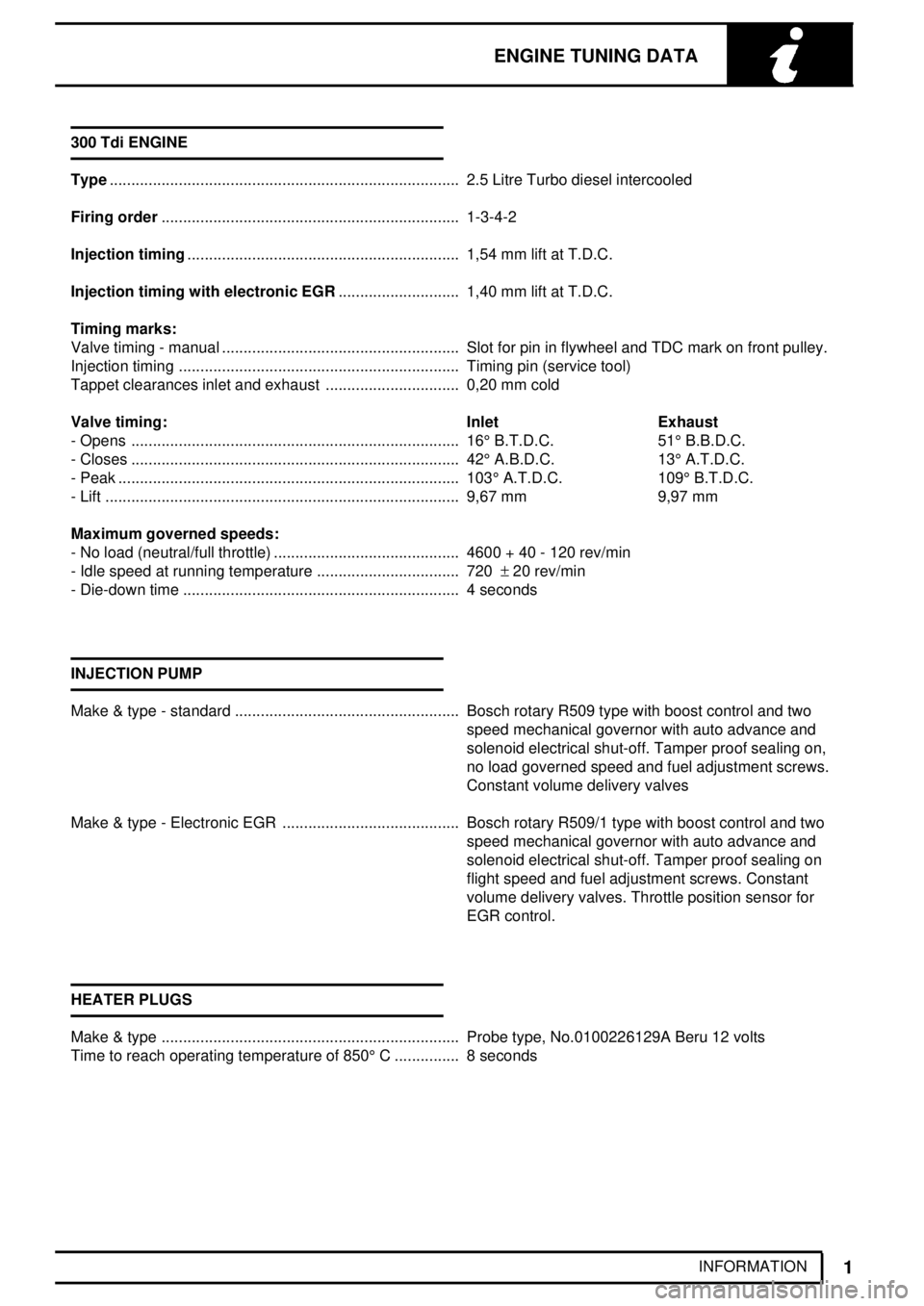
ENGINE TUNING DATA
1
INFORMATION 300 Tdi ENGINE
Type2.5 Litre Turbo diesel intercooled .................................................................................
Firing order1-3-4-2 .....................................................................
Injection timing1,54 mm lift at T.D.C. ...............................................................
Injection timing with electronic EGR1,40 mm lift at T.D.C. ............................
Timing marks:
Valve timing - manual Slot for pin in flywheel and TDC mark on front pulley........................................................
Injection timing Timing pin (service tool).................................................................
Tappet clearances inlet and exhaust 0,20 mm cold...............................
Valve timing: Inlet Exhaust
- Opens 16°B.T.D.C. ............................................................................ 51°B.B.D.C.
- Closes 42°A.B.D.C. ............................................................................ 13°A.T.D.C.
- Peak 103°A.T.D.C. ............................................................................... 109°B.T.D.C.
- Lift 9,67 mm.................................................................................. 9,97 mm
Maximum governed speeds:
- No load (neutral/full throttle) 4600 + 40 - 120 rev/min...........................................
- Idle speed at running temperature 720±20 rev/min .................................
- Die-down time 4 seconds................................................................
INJECTION PUMP
Make & type - standard Bosch rotary R509 type with boost control and two....................................................
speed mechanical governor with auto advance and
solenoid electrical shut-off. Tamper proof sealing on,
no load governed speed and fuel adjustment screws.
Constant volume delivery valves
Make & type - Electronic EGR Bosch rotary R509/1 type with boost control and two.........................................
speed mechanical governor with auto advance and
solenoid electrical shut-off. Tamper proof sealing on
flight speed and fuel adjustment screws. Constant
volume delivery valves. Throttle position sensor for
EGR control.
HEATER PLUGS
Make & type Probe type, No.0100226129A Beru 12 volts.....................................................................
Time to reach operating temperature of 850°C 8 seconds...............
Page 32 of 455
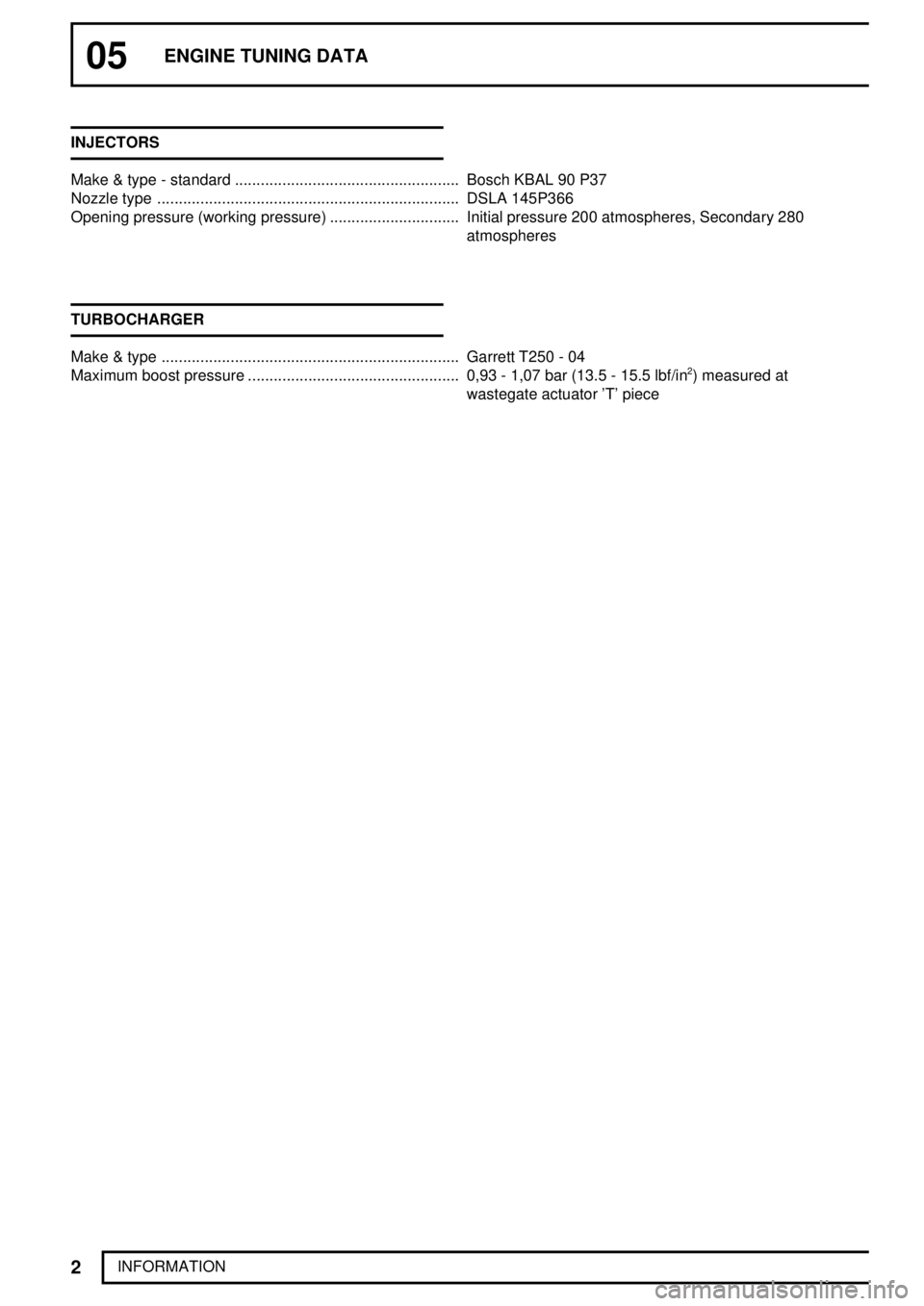
05ENGINE TUNING DATA
2
INFORMATION INJECTORS
Make & type - standard Bosch KBAL 90 P37....................................................
Nozzle type DSLA 145P366......................................................................
Opening pressure (working pressure) Initial pressure 200 atmospheres, Secondary 280..............................
atmospheres
TURBOCHARGER
Make & type Garrett T250 - 04.....................................................................
Maximum boost pressure 0,93 - 1,07 bar (13.5 - 15.5 lbf/in
2) measured at .................................................
wastegate actuator 'T' piece
Page 33 of 455
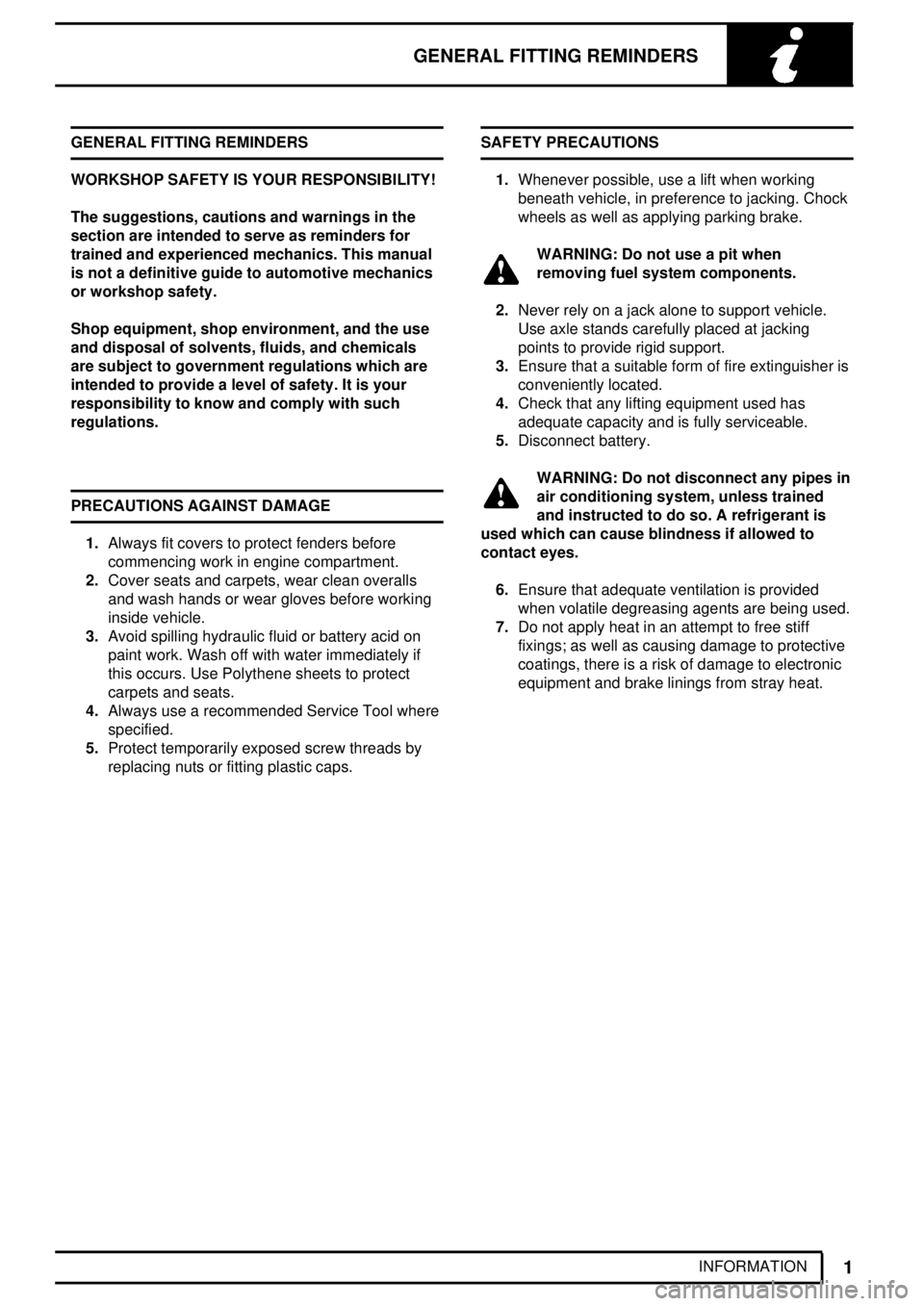
GENERAL FITTING REMINDERS
1
INFORMATION GENERAL FITTING REMINDERS
WORKSHOP SAFETY IS YOUR RESPONSIBILITY!
The suggestions, cautions and warnings in the
section are intended to serve as reminders for
trained and experienced mechanics. This manual
is not a definitive guide to automotive mechanics
or workshop safety.
Shop equipment, shop environment, and the use
and disposal of solvents, fluids, and chemicals
are subject to government regulations which are
intended to provide a level of safety. It is your
responsibility to know and comply with such
regulations.
PRECAUTIONS AGAINST DAMAGE
1.Always fit covers to protect fenders before
commencing work in engine compartment.
2.Cover seats and carpets, wear clean overalls
and wash hands or wear gloves before working
inside vehicle.
3.Avoid spilling hydraulic fluid or battery acid on
paint work. Wash off with water immediately if
this occurs. Use Polythene sheets to protect
carpets and seats.
4.Always use a recommended Service Tool where
specified.
5.Protect temporarily exposed screw threads by
replacing nuts or fitting plastic caps.SAFETY PRECAUTIONS
1.Whenever possible, use a lift when working
beneath vehicle, in preference to jacking. Chock
wheels as well as applying parking brake.
WARNING: Do not use a pit when
removing fuel system components.
2.Never rely on a jack alone to support vehicle.
Use axle stands carefully placed at jacking
points to provide rigid support.
3.Ensure that a suitable form of fire extinguisher is
conveniently located.
4.Check that any lifting equipment used has
adequate capacity and is fully serviceable.
5.Disconnect battery.
WARNING: Do not disconnect any pipes in
air conditioning system, unless trained
and instructed to do so. A refrigerant is
used which can cause blindness if allowed to
contact eyes.
6.Ensure that adequate ventilation is provided
when volatile degreasing agents are being used.
7.Do not apply heat in an attempt to free stiff
fixings; as well as causing damage to protective
coatings, there is a risk of damage to electronic
equipment and brake linings from stray heat.
Page 37 of 455
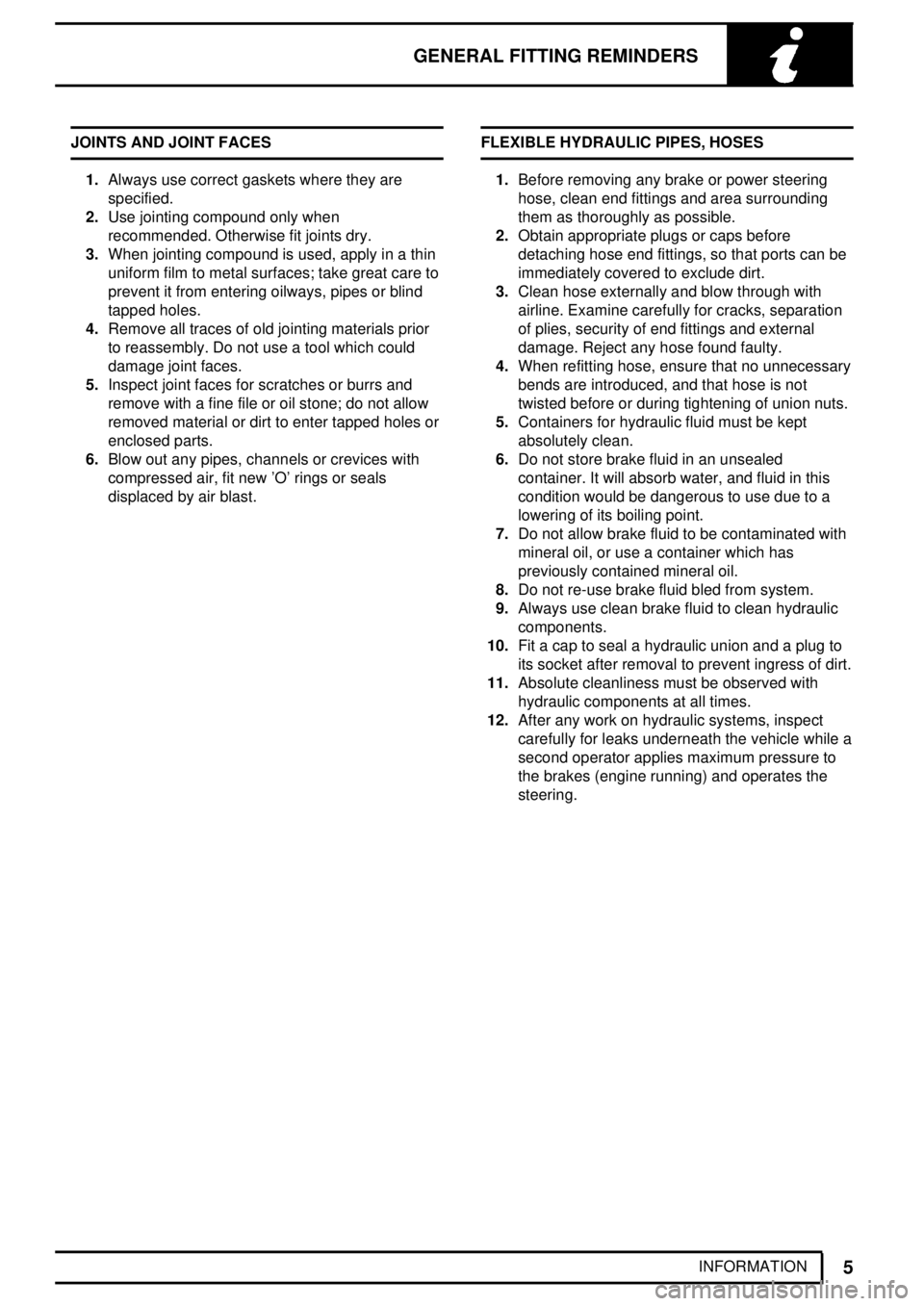
GENERAL FITTING REMINDERS
5
INFORMATION JOINTS AND JOINT FACES
1.Always use correct gaskets where they are
specified.
2.Use jointing compound only when
recommended. Otherwise fit joints dry.
3.When jointing compound is used, apply in a thin
uniform film to metal surfaces; take great care to
prevent it from entering oilways, pipes or blind
tapped holes.
4.Remove all traces of old jointing materials prior
to reassembly. Do not use a tool which could
damage joint faces.
5.Inspect joint faces for scratches or burrs and
remove with a fine file or oil stone; do not allow
removed material or dirt to enter tapped holes or
enclosed parts.
6.Blow out any pipes, channels or crevices with
compressed air, fit new 'O' rings or seals
displaced by air blast.FLEXIBLE HYDRAULIC PIPES, HOSES
1.Before removing any brake or power steering
hose, clean end fittings and area surrounding
them as thoroughly as possible.
2.Obtain appropriate plugs or caps before
detaching hose end fittings, so that ports can be
immediately covered to exclude dirt.
3.Clean hose externally and blow through with
airline. Examine carefully for cracks, separation
of plies, security of end fittings and external
damage. Reject any hose found faulty.
4.When refitting hose, ensure that no unnecessary
bends are introduced, and that hose is not
twisted before or during tightening of union nuts.
5.Containers for hydraulic fluid must be kept
absolutely clean.
6.Do not store brake fluid in an unsealed
container. It will absorb water, and fluid in this
condition would be dangerous to use due to a
lowering of its boiling point.
7.Do not allow brake fluid to be contaminated with
mineral oil, or use a container which has
previously contained mineral oil.
8.Do not re-use brake fluid bled from system.
9.Always use clean brake fluid to clean hydraulic
components.
10.Fit a cap to seal a hydraulic union and a plug to
its socket after removal to prevent ingress of dirt.
11.Absolute cleanliness must be observed with
hydraulic components at all times.
12.After any work on hydraulic systems, inspect
carefully for leaks underneath the vehicle while a
second operator applies maximum pressure to
the brakes (engine running) and operates the
steering.
Page 40 of 455
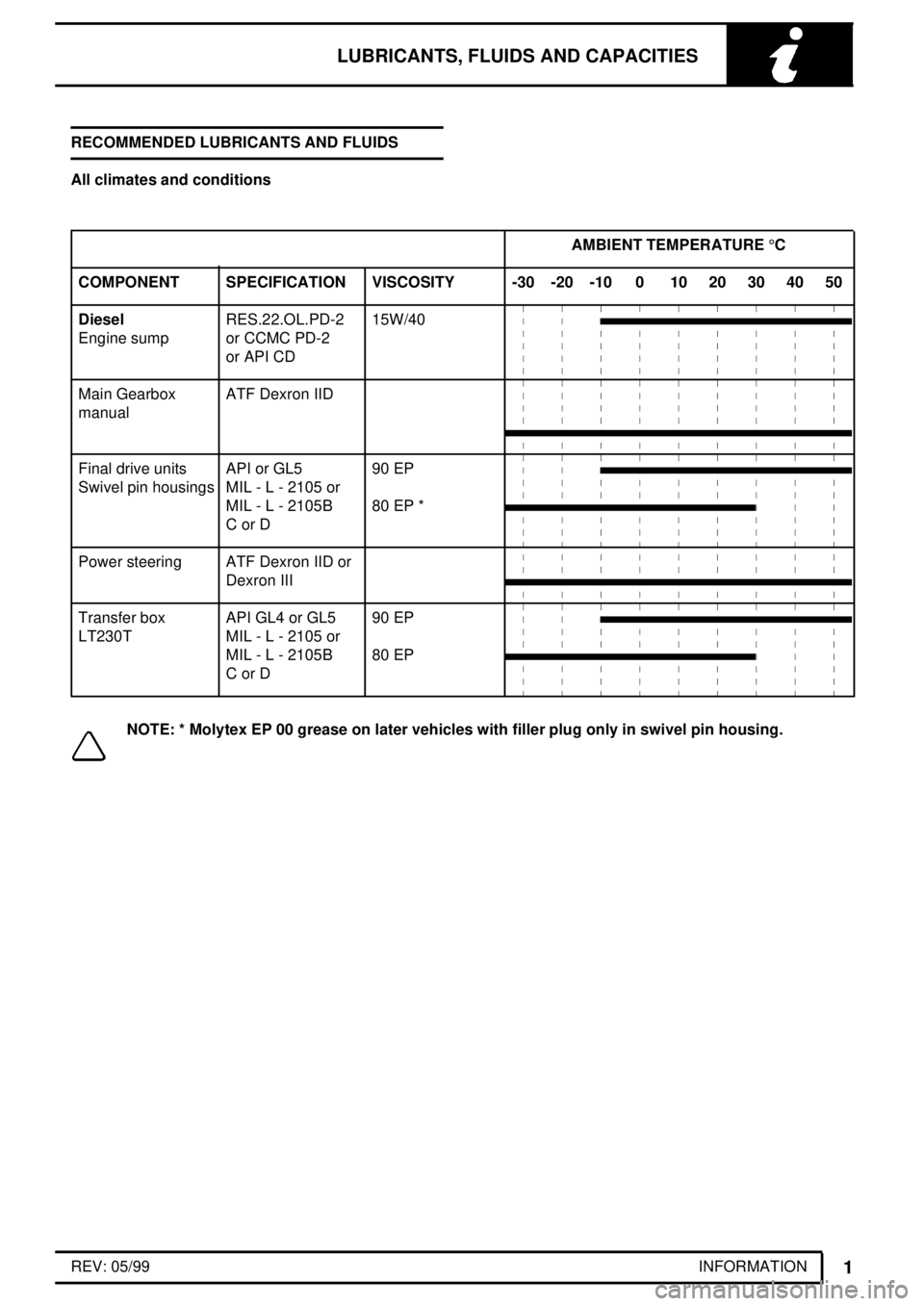
LUBRICANTS, FLUIDS AND CAPACITIES
1
INFORMATION REV: 05/99 RECOMMENDED LUBRICANTS AND FLUIDS
All climates and conditions
AMBIENT TEMPERATURE°C
COMPONENT SPECIFICATION VISCOSITY -30 -20 -10 0 10 20 30 40 50
DieselRES.22.OL.PD-2 15W/40
Engine sump or CCMC PD-2
or API CD
Main Gearbox
manualATF Dexron IID
Final drive units API or GL5 90 EP
Swivel pin housings MIL - L - 2105 or
MIL - L - 2105B 80 EP *
CorD
Power steering ATF Dexron IID or
Dexron III
Transfer box API GL4 or GL5 90 EP
LT230T MIL - L - 2105 or
MIL - L - 2105B 80 EP
CorD
NOTE: * Molytex EP 00 grease on later vehicles with filler plug only in swivel pin housing.