check engine light LAND ROVER DEFENDER 1996 Workshop Manual
[x] Cancel search | Manufacturer: LAND ROVER, Model Year: 1996, Model line: DEFENDER, Model: LAND ROVER DEFENDER 1996Pages: 455, PDF Size: 6.44 MB
Page 280 of 455
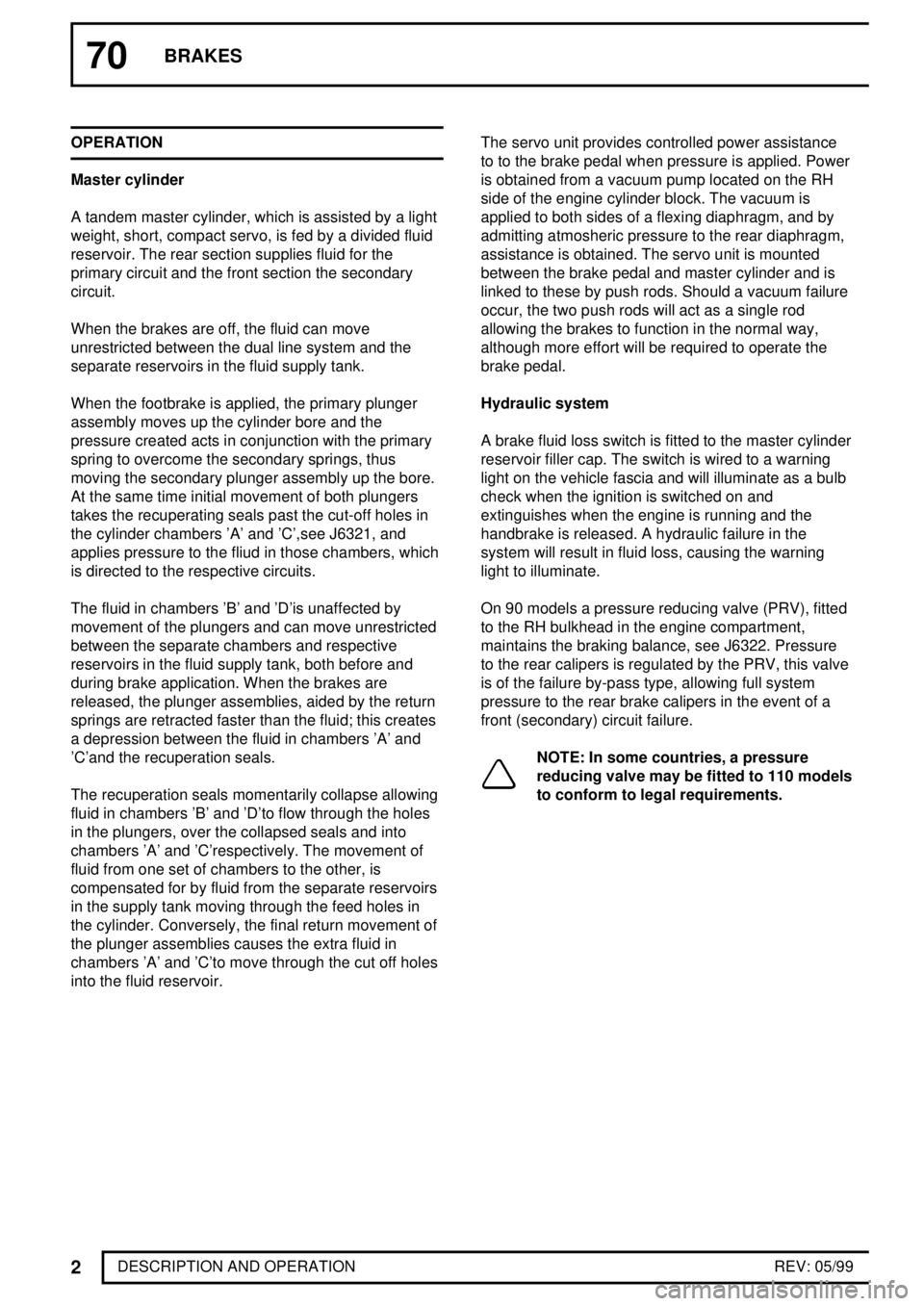
70BRAKES
2
DESCRIPTION AND OPERATION REV: 05/99 OPERATION
Master cylinder
A tandem master cylinder, which is assisted by a light
weight, short, compact servo, is fed by a divided fluid
reservoir. The rear section supplies fluid for the
primary circuit and the front section the secondary
circuit.
When the brakes are off, the fluid can move
unrestricted between the dual line system and the
separate reservoirs in the fluid supply tank.
When the footbrake is applied, the primary plunger
assembly moves up the cylinder bore and the
pressure created acts in conjunction with the primary
spring to overcome the secondary springs, thus
moving the secondary plunger assembly up the bore.
At the same time initial movement of both plungers
takes the recuperating seals past the cut-off holes in
the cylinder chambers 'A' and 'C',see J6321, and
applies pressure to the fliud in those chambers, which
is directed to the respective circuits.
The fluid in chambers 'B' and 'D'is unaffected by
movement of the plungers and can move unrestricted
between the separate chambers and respective
reservoirs in the fluid supply tank, both before and
during brake application. When the brakes are
released, the plunger assemblies, aided by the return
springs are retracted faster than the fluid; this creates
a depression between the fluid in chambers 'A' and
'C'and the recuperation seals.
The recuperation seals momentarily collapse allowing
fluid in chambers 'B' and 'D'to flow through the holes
in the plungers, over the collapsed seals and into
chambers 'A' and 'C'respectively. The movement of
fluid from one set of chambers to the other, is
compensated for by fluid from the separate reservoirs
in the supply tank moving through the feed holes in
the cylinder. Conversely, the final return movement of
the plunger assemblies causes the extra fluid in
chambers 'A' and 'C'to move through the cut off holes
into the fluid reservoir.The servo unit provides controlled power assistance
to to the brake pedal when pressure is applied. Power
is obtained from a vacuum pump located on the RH
side of the engine cylinder block. The vacuum is
applied to both sides of a flexing diaphragm, and by
admitting atmosheric pressure to the rear diaphragm,
assistance is obtained. The servo unit is mounted
between the brake pedal and master cylinder and is
linked to these by push rods. Should a vacuum failure
occur, the two push rods will act as a single rod
allowing the brakes to function in the normal way,
although more effort will be required to operate the
brake pedal.
Hydraulic system
A brake fluid loss switch is fitted to the master cylinder
reservoir filler cap. The switch is wired to a warning
light on the vehicle fascia and will illuminate as a bulb
check when the ignition is switched on and
extinguishes when the engine is running and the
handbrake is released. A hydraulic failure in the
system will result in fluid loss, causing the warning
light to illuminate.
On 90 models a pressure reducing valve (PRV), fitted
to the RH bulkhead in the engine compartment,
maintains the braking balance, see J6322. Pressure
to the rear calipers is regulated by the PRV, this valve
is of the failure by-pass type, allowing full system
pressure to the rear brake calipers in the event of a
front (secondary) circuit failure.
NOTE: In some countries, a pressure
reducing valve may be fitted to 110 models
to conform to legal requirements.
Page 413 of 455
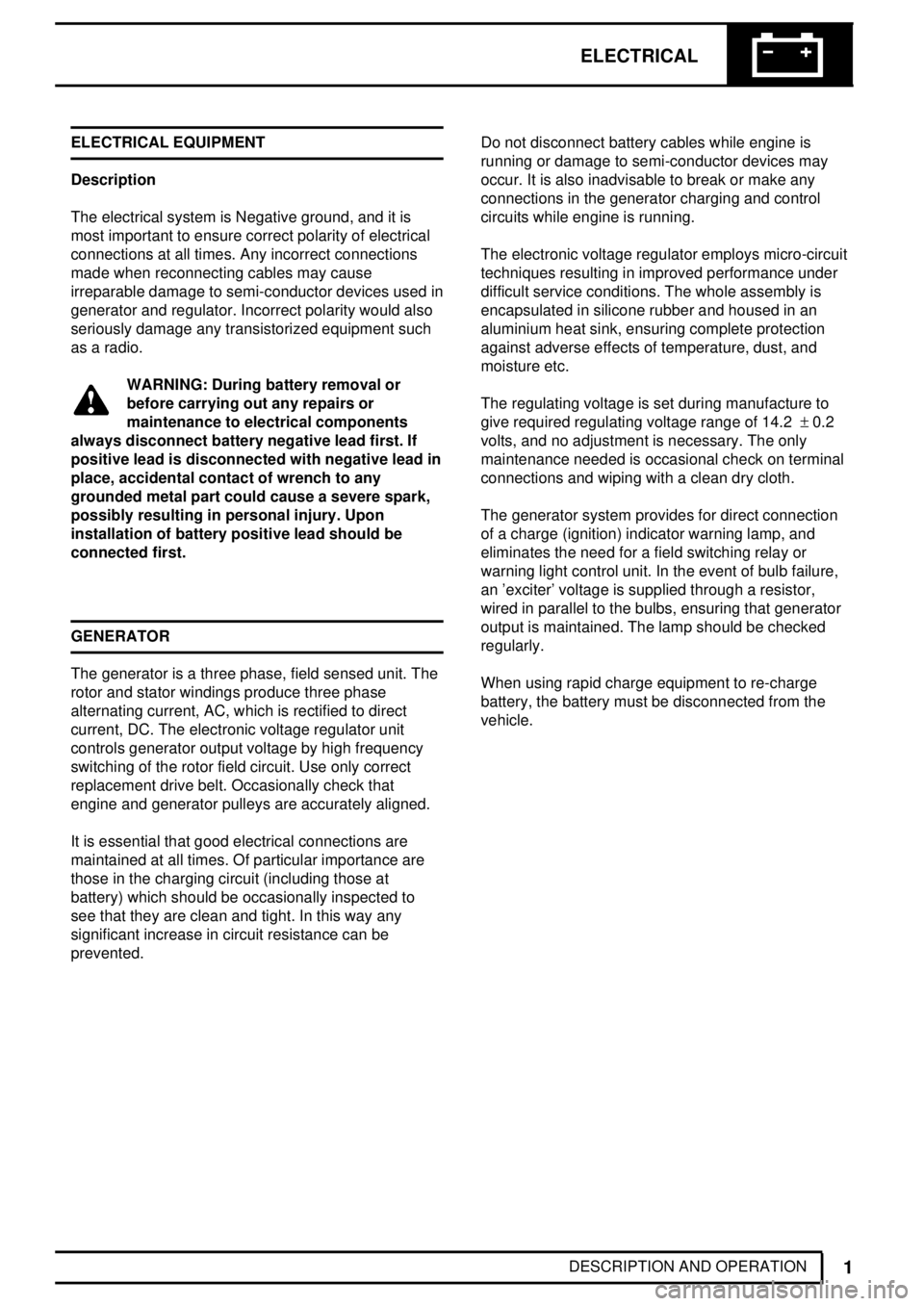
ELECTRICAL
1
DESCRIPTION AND OPERATION ELECTRICAL EQUIPMENT
Description
The electrical system is Negative ground, and it is
most important to ensure correct polarity of electrical
connections at all times. Any incorrect connections
made when reconnecting cables may cause
irreparable damage to semi-conductor devices used in
generator and regulator. Incorrect polarity would also
seriously damage any transistorized equipment such
as a radio.
WARNING: During battery removal or
before carrying out any repairs or
maintenance to electrical components
always disconnect battery negative lead first. If
positive lead is disconnected with negative lead in
place, accidental contact of wrench to any
grounded metal part could cause a severe spark,
possibly resulting in personal injury. Upon
installation of battery positive lead should be
connected first.
GENERATOR
The generator is a three phase, field sensed unit. The
rotor and stator windings produce three phase
alternating current, AC, which is rectified to direct
current, DC. The electronic voltage regulator unit
controls generator output voltage by high frequency
switching of the rotor field circuit. Use only correct
replacement drive belt. Occasionally check that
engine and generator pulleys are accurately aligned.
It is essential that good electrical connections are
maintained at all times. Of particular importance are
those in the charging circuit (including those at
battery) which should be occasionally inspected to
see that they are clean and tight. In this way any
significant increase in circuit resistance can be
prevented.Do not disconnect battery cables while engine is
running or damage to semi-conductor devices may
occur. It is also inadvisable to break or make any
connections in the generator charging and control
circuits while engine is running.
The electronic voltage regulator employs micro-circuit
techniques resulting in improved performance under
difficult service conditions. The whole assembly is
encapsulated in silicone rubber and housed in an
aluminium heat sink, ensuring complete protection
against adverse effects of temperature, dust, and
moisture etc.
The regulating voltage is set during manufacture to
give required regulating voltage range of 14.2±0.2
volts, and no adjustment is necessary. The only
maintenance needed is occasional check on terminal
connections and wiping with a clean dry cloth.
The generator system provides for direct connection
of a charge (ignition) indicator warning lamp, and
eliminates the need for a field switching relay or
warning light control unit. In the event of bulb failure,
an 'exciter' voltage is supplied through a resistor,
wired in parallel to the bulbs, ensuring that generator
output is maintained. The lamp should be checked
regularly.
When using rapid charge equipment to re-charge
battery, the battery must be disconnected from the
vehicle.
Page 429 of 455
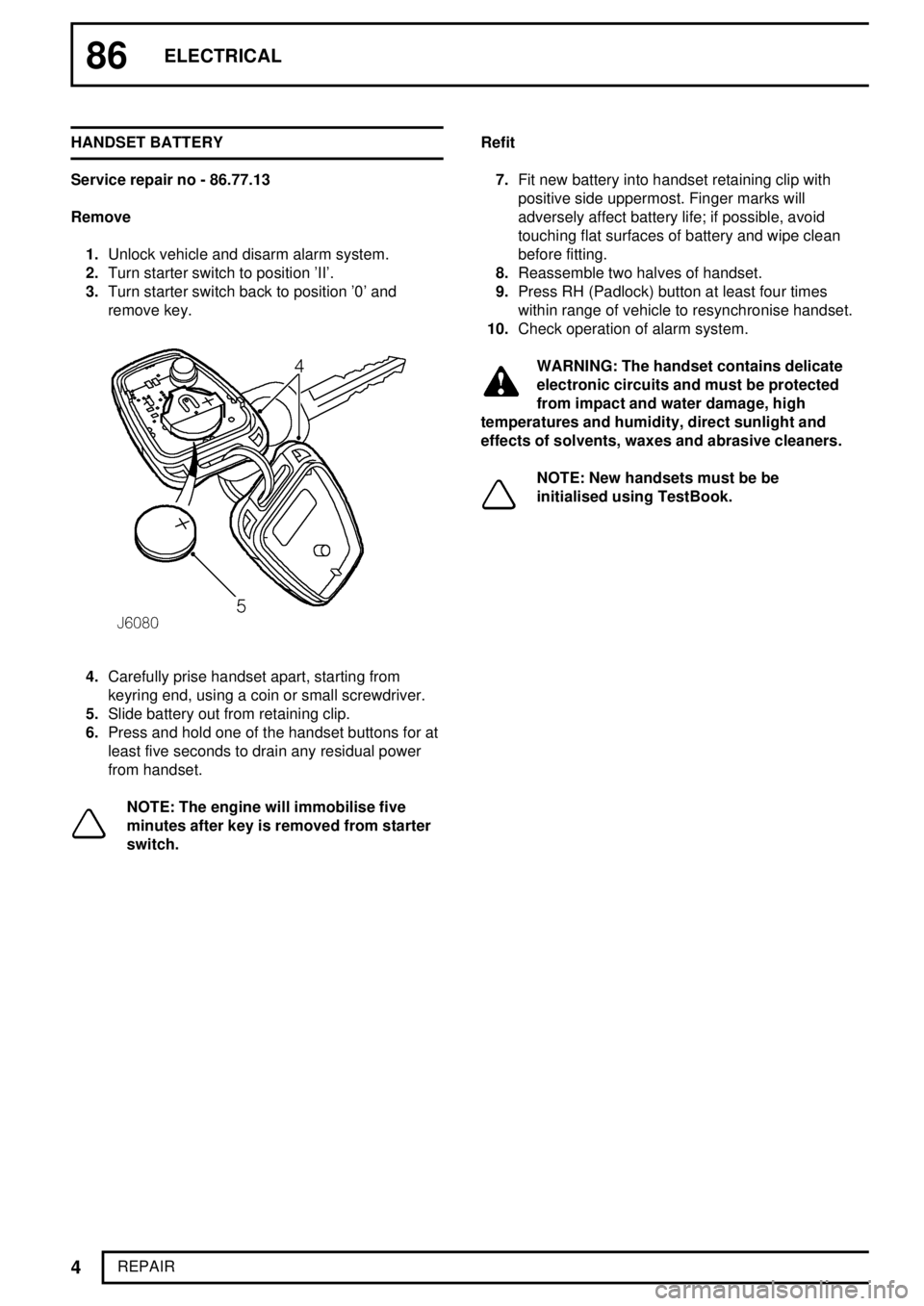
86ELECTRICAL
4
REPAIR HANDSET BATTERY
Service repair no - 86.77.13
Remove
1.Unlock vehicle and disarm alarm system.
2.Turn starter switch to position 'II'.
3.Turn starter switch back to position '0' and
remove key.
4.Carefully prise handset apart, starting from
keyring end, using a coin or small screwdriver.
5.Slide battery out from retaining clip.
6.Press and hold one of the handset buttons for at
least five seconds to drain any residual power
from handset.
NOTE: The engine will immobilise five
minutes after key is removed from starter
switch.Refit
7.Fit new battery into handset retaining clip with
positive side uppermost. Finger marks will
adversely affect battery life; if possible, avoid
touching flat surfaces of battery and wipe clean
before fitting.
8.Reassemble two halves of handset.
9.Press RH (Padlock) button at least four times
within range of vehicle to resynchronise handset.
10.Check operation of alarm system.
WARNING: The handset contains delicate
electronic circuits and must be protected
from impact and water damage, high
temperatures and humidity, direct sunlight and
effects of solvents, waxes and abrasive cleaners.
NOTE: New handsets must be be
initialised using TestBook.