stop start LAND ROVER DEFENDER 1996 Workshop Manual
[x] Cancel search | Manufacturer: LAND ROVER, Model Year: 1996, Model line: DEFENDER, Model: LAND ROVER DEFENDER 1996Pages: 455, PDF Size: 6.44 MB
Page 50 of 455
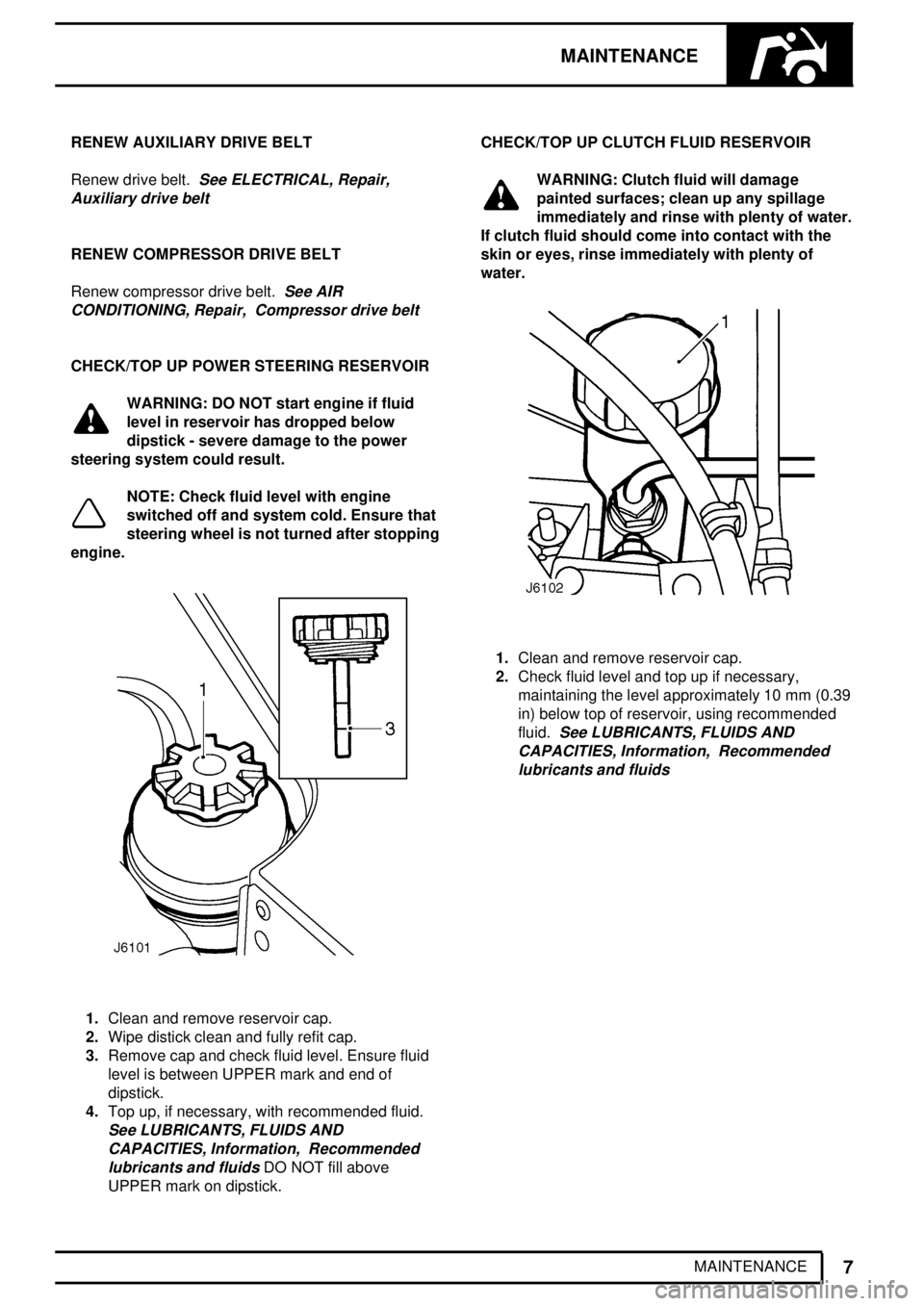
MAINTENANCE
7
MAINTENANCE RENEW AUXILIARY DRIVE BELT
Renew drive belt.
See ELECTRICAL, Repair,
Auxiliary drive belt
RENEW COMPRESSOR DRIVE BELT
Renew compressor drive belt.
See AIR
CONDITIONING, Repair, Compressor drive belt
CHECK/TOP UP POWER STEERING RESERVOIR
WARNING: DO NOT start engine if fluid
level in reservoir has dropped below
dipstick - severe damage to the power
steering system could result.
NOTE: Check fluid level with engine
switched off and system cold. Ensure that
steering wheel is not turned after stopping
engine.
1.Clean and remove reservoir cap.
2.Wipe distick clean and fully refit cap.
3.Remove cap and check fluid level. Ensure fluid
level is between UPPER mark and end of
dipstick.
4.Top up, if necessary, with recommended fluid.
See LUBRICANTS, FLUIDS AND
CAPACITIES, Information, Recommended
lubricants and fluids
DO NOT fill above
UPPER mark on dipstick.CHECK/TOP UP CLUTCH FLUID RESERVOIR
WARNING: Clutch fluid will damage
painted surfaces; clean up any spillage
immediately and rinse with plenty of water.
If clutch fluid should come into contact with the
skin or eyes, rinse immediately with plenty of
water.
1.Clean and remove reservoir cap.
2.Check fluid level and top up if necessary,
maintaining the level approximately 10 mm (0.39
in) below top of reservoir, using recommended
fluid.
See LUBRICANTS, FLUIDS AND
CAPACITIES, Information, Recommended
lubricants and fluids
Page 99 of 455
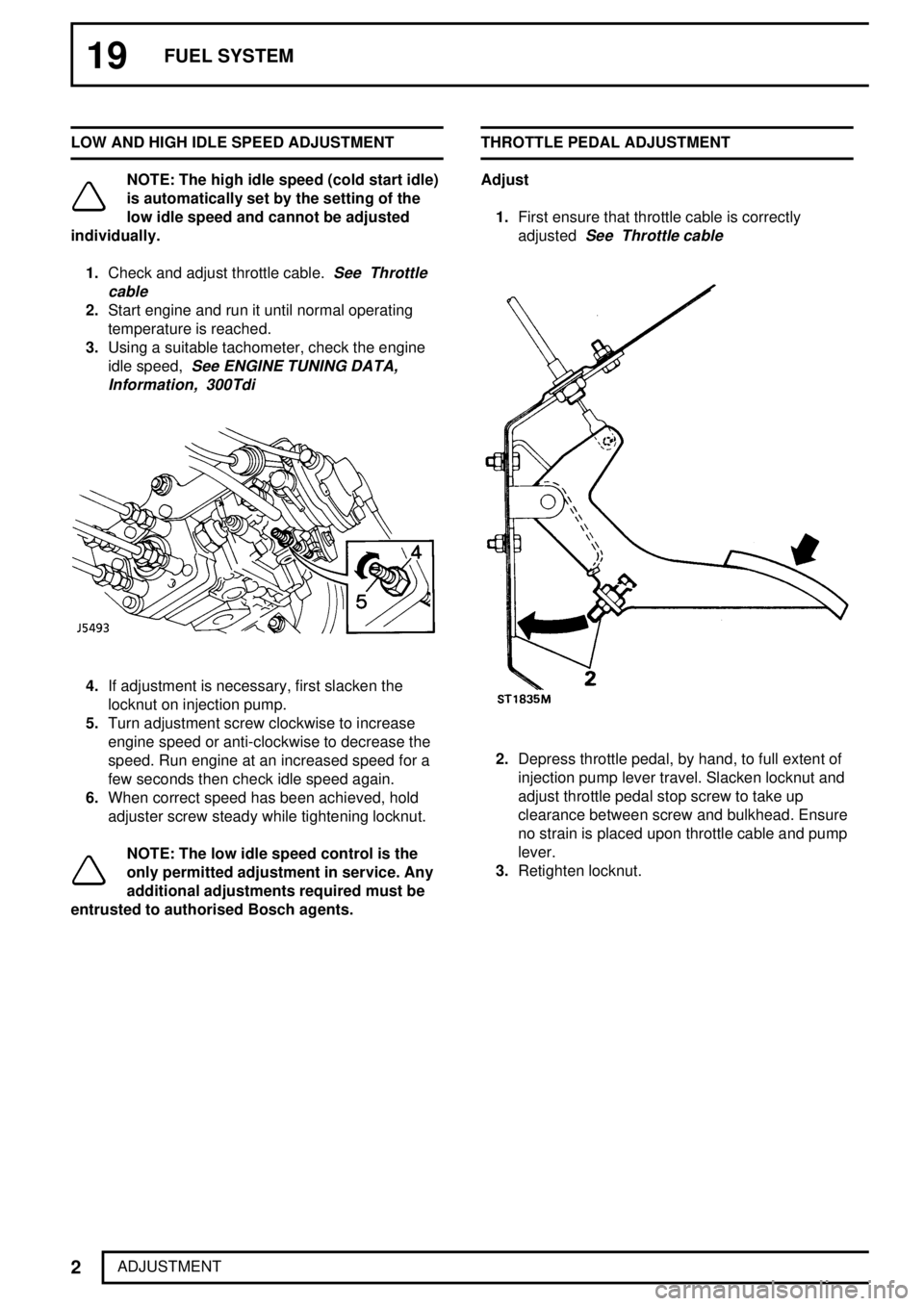
19FUEL SYSTEM
2
ADJUSTMENT LOW AND HIGH IDLE SPEED ADJUSTMENT
NOTE: The high idle speed (cold start idle)
is automatically set by the setting of the
low idle speed and cannot be adjusted
individually.
1.Check and adjust throttle cable.
See Throttle
cable
2.Start engine and run it until normal operating
temperature is reached.
3.Using a suitable tachometer, check the engine
idle speed,
See ENGINE TUNING DATA,
Information, 300Tdi
4.If adjustment is necessary, first slacken the
locknut on injection pump.
5.Turn adjustment screw clockwise to increase
engine speed or anti-clockwise to decrease the
speed. Run engine at an increased speed for a
few seconds then check idle speed again.
6.When correct speed has been achieved, hold
adjuster screw steady while tightening locknut.
NOTE: The low idle speed control is the
only permitted adjustment in service. Any
additional adjustments required must be
entrusted to authorised Bosch agents.THROTTLE PEDAL ADJUSTMENT
Adjust
1.First ensure that throttle cable is correctly
adjusted
See Throttle cable
2.Depress throttle pedal, by hand, to full extent of
injection pump lever travel. Slacken locknut and
adjust throttle pedal stop screw to take up
clearance between screw and bulkhead. Ensure
no strain is placed upon throttle cable and pump
lever.
3.Retighten locknut.
Page 380 of 455
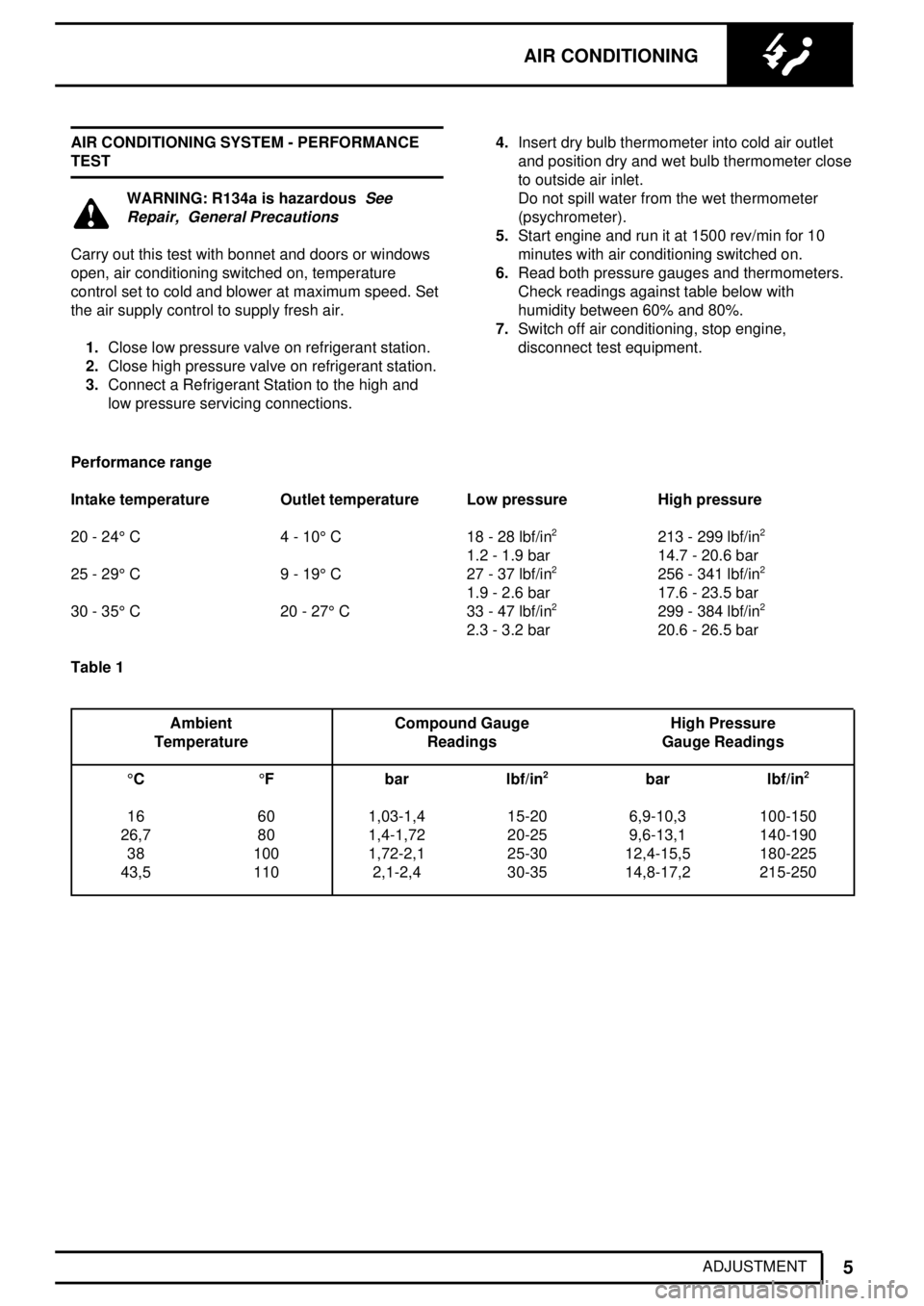
AIR CONDITIONING
5
ADJUSTMENT AIR CONDITIONING SYSTEM - PERFORMANCE
TEST
WARNING: R134a is hazardousSee
Repair, General Precautions
Carry out this test with bonnet and doors or windows
open, air conditioning switched on, temperature
control set to cold and blower at maximum speed. Set
the air supply control to supply fresh air.
1.Close low pressure valve on refrigerant station.
2.Close high pressure valve on refrigerant station.
3.Connect a Refrigerant Station to the high and
low pressure servicing connections.4.Insert dry bulb thermometer into cold air outlet
and position dry and wet bulb thermometer close
to outside air inlet.
Do not spill water from the wet thermometer
(psychrometer).
5.Start engine and run it at 1500 rev/min for 10
minutes with air conditioning switched on.
6.Read both pressure gauges and thermometers.
Check readings against table below with
humidity between 60% and 80%.
7.Switch off air conditioning, stop engine,
disconnect test equipment.
Performance range
Intake temperature Outlet temperature Low pressure High pressure
20 - 24°C4-10°C 18 - 28 lbf/in
2213 - 299 lbf/in2
1.2 - 1.9 bar 14.7 - 20.6 bar
25 - 29°C9-19°C 27 - 37 lbf/in2256 - 341 lbf/in2
1.9 - 2.6 bar 17.6 - 23.5 bar
30 - 35°C20-27°C 33 - 47 lbf/in2299 - 384 lbf/in2
2.3 - 3.2 bar 20.6 - 26.5 bar
Table 1
Ambient Compound Gauge High Pressure
Temperature Readings Gauge Readings
°C°F bar lbf/in
2bar lbf/in2
16 60 1,03-1,4 15-20 6,9-10,3 100-150
26,7 80 1,4-1,72 20-25 9,6-13,1 140-190
38 100 1,72-2,1 25-30 12,4-15,5 180-225
43,5 110 2,1-2,4 30-35 14,8-17,2 215-250
Page 381 of 455
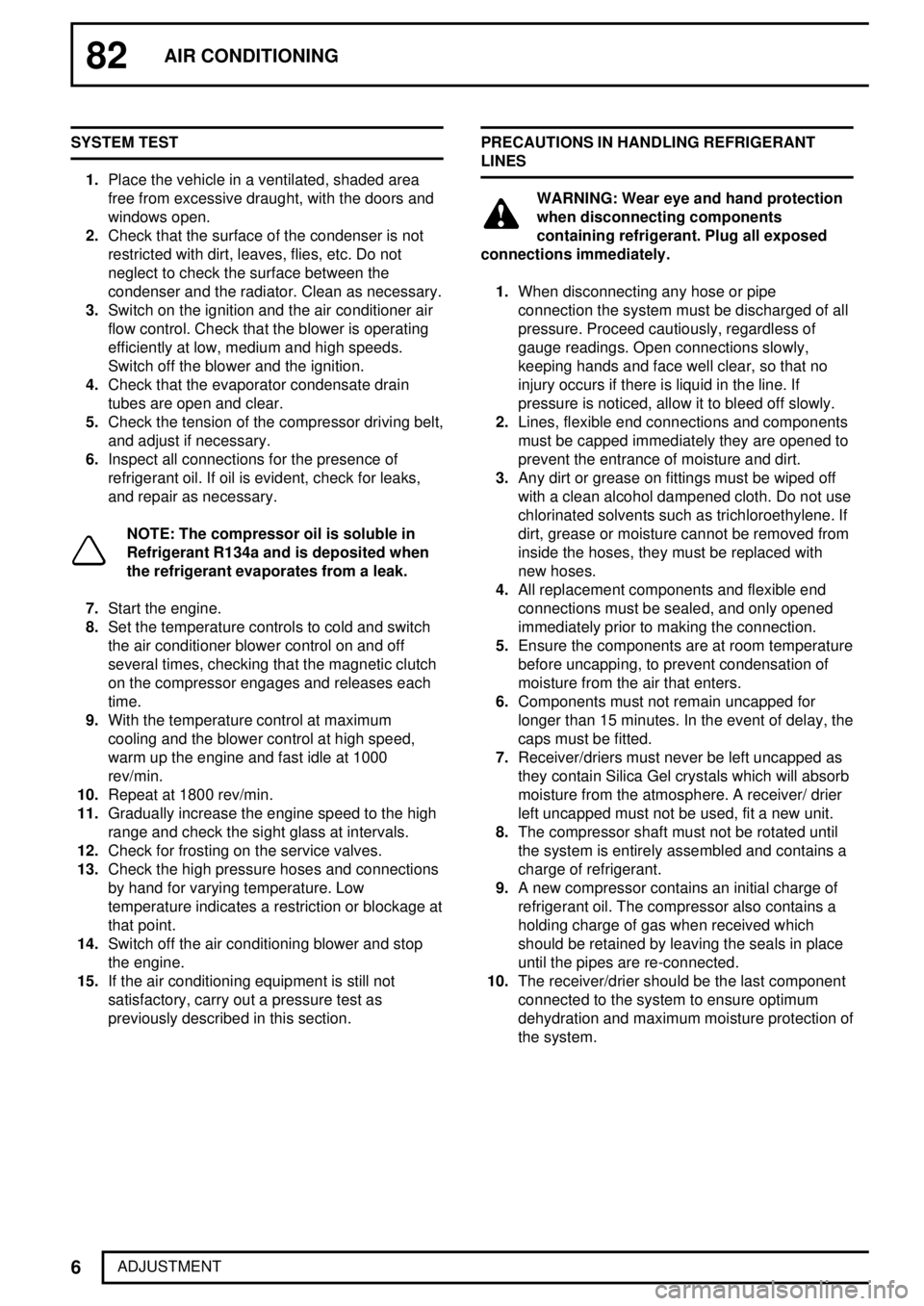
82AIR CONDITIONING
6
ADJUSTMENT SYSTEM TEST
1.Place the vehicle in a ventilated, shaded area
free from excessive draught, with the doors and
windows open.
2.Check that the surface of the condenser is not
restricted with dirt, leaves, flies, etc. Do not
neglect to check the surface between the
condenser and the radiator. Clean as necessary.
3.Switch on the ignition and the air conditioner air
flow control. Check that the blower is operating
efficiently at low, medium and high speeds.
Switch off the blower and the ignition.
4.Check that the evaporator condensate drain
tubes are open and clear.
5.Check the tension of the compressor driving belt,
and adjust if necessary.
6.Inspect all connections for the presence of
refrigerant oil. If oil is evident, check for leaks,
and repair as necessary.
NOTE: The compressor oil is soluble in
Refrigerant R134a and is deposited when
the refrigerant evaporates from a leak.
7.Start the engine.
8.Set the temperature controls to cold and switch
the air conditioner blower control on and off
several times, checking that the magnetic clutch
on the compressor engages and releases each
time.
9.With the temperature control at maximum
cooling and the blower control at high speed,
warm up the engine and fast idle at 1000
rev/min.
10.Repeat at 1800 rev/min.
11.Gradually increase the engine speed to the high
range and check the sight glass at intervals.
12.Check for frosting on the service valves.
13.Check the high pressure hoses and connections
by hand for varying temperature. Low
temperature indicates a restriction or blockage at
that point.
14.Switch off the air conditioning blower and stop
the engine.
15.If the air conditioning equipment is still not
satisfactory, carry out a pressure test as
previously described in this section.PRECAUTIONS IN HANDLING REFRIGERANT
LINES
WARNING: Wear eye and hand protection
when disconnecting components
containing refrigerant. Plug all exposed
connections immediately.
1.When disconnecting any hose or pipe
connection the system must be discharged of all
pressure. Proceed cautiously, regardless of
gauge readings. Open connections slowly,
keeping hands and face well clear, so that no
injury occurs if there is liquid in the line. If
pressure is noticed, allow it to bleed off slowly.
2.Lines, flexible end connections and components
must be capped immediately they are opened to
prevent the entrance of moisture and dirt.
3.Any dirt or grease on fittings must be wiped off
with a clean alcohol dampened cloth. Do not use
chlorinated solvents such as trichloroethylene. If
dirt, grease or moisture cannot be removed from
inside the hoses, they must be replaced with
new hoses.
4.All replacement components and flexible end
connections must be sealed, and only opened
immediately prior to making the connection.
5.Ensure the components are at room temperature
before uncapping, to prevent condensation of
moisture from the air that enters.
6.Components must not remain uncapped for
longer than 15 minutes. In the event of delay, the
caps must be fitted.
7.Receiver/driers must never be left uncapped as
they contain Silica Gel crystals which will absorb
moisture from the atmosphere. A receiver/ drier
left uncapped must not be used, fit a new unit.
8.The compressor shaft must not be rotated until
the system is entirely assembled and contains a
charge of refrigerant.
9.A new compressor contains an initial charge of
refrigerant oil. The compressor also contains a
holding charge of gas when received which
should be retained by leaving the seals in place
until the pipes are re-connected.
10.The receiver/drier should be the last component
connected to the system to ensure optimum
dehydration and maximum moisture protection of
the system.