headlamp LAND ROVER DEFENDER 1996 Workshop Manual
[x] Cancel search | Manufacturer: LAND ROVER, Model Year: 1996, Model line: DEFENDER, Model: LAND ROVER DEFENDER 1996Pages: 455, PDF Size: 6.44 MB
Page 26 of 455
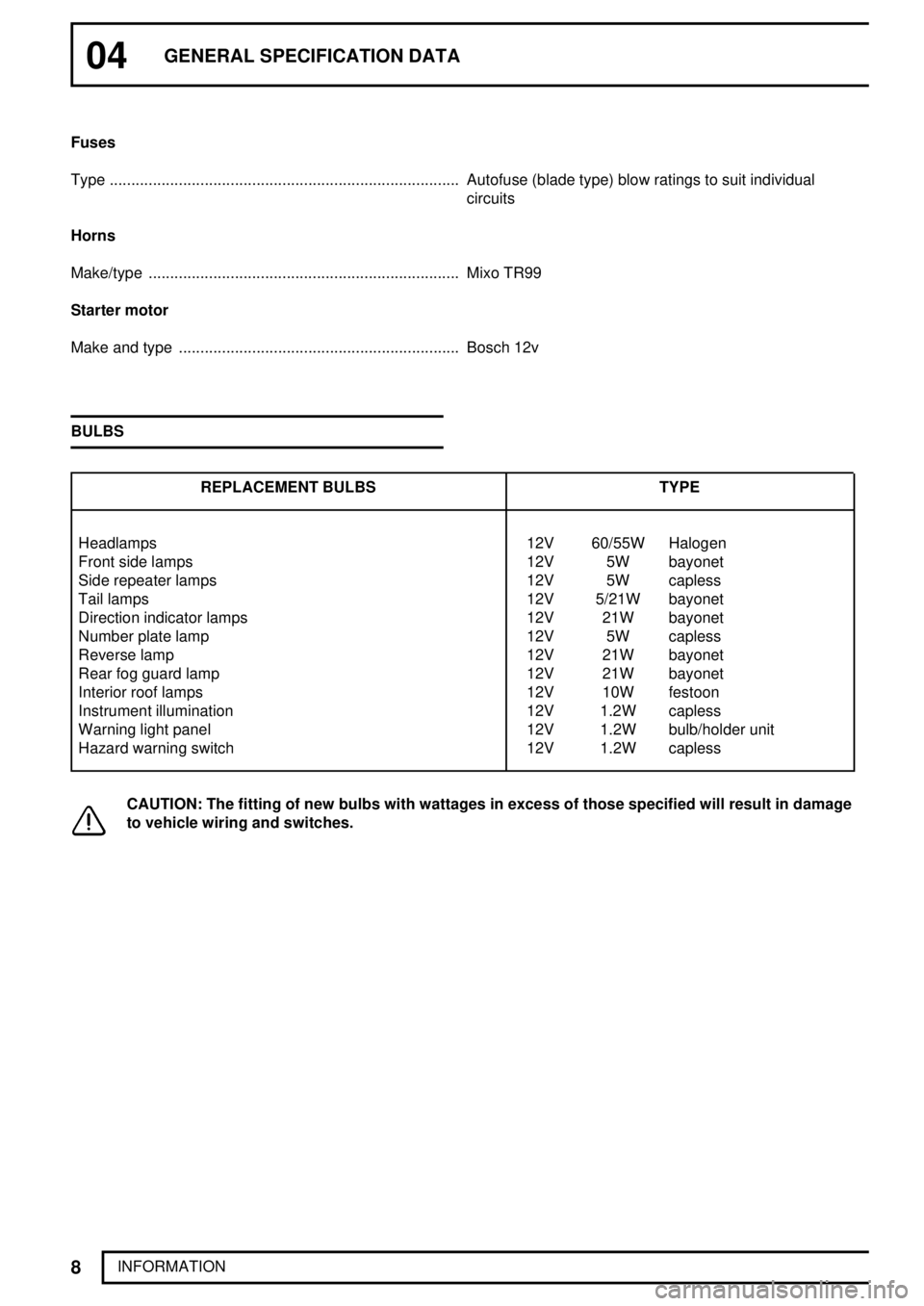
04GENERAL SPECIFICATION DATA
8
INFORMATION Fuses
Type Autofuse (blade type) blow ratings to suit individual.................................................................................
circuits
Horns
Make/type Mixo TR99........................................................................
Starter motor
Make and type Bosch 12v.................................................................
BULBS
REPLACEMENT BULBS TYPE
Headlamps 12V 60/55W Halogen
Front side lamps 12V 5W bayonet
Side repeater lamps 12V 5W capless
Tail lamps 12V 5/21W bayonet
Direction indicator lamps 12V 21W bayonet
Number plate lamp 12V 5W capless
Reverse lamp 12V 21W bayonet
Rear fog guard lamp 12V 21W bayonet
Interior roof lamps 12V 10W festoon
Instrument illumination 12V 1.2W capless
Warning light panel 12V 1.2W bulb/holder unit
Hazard warning switch 12V 1.2W capless
CAUTION: The fitting of new bulbs with wattages in excess of those specified will result in damage
to vehicle wiring and switches.
Page 45 of 455
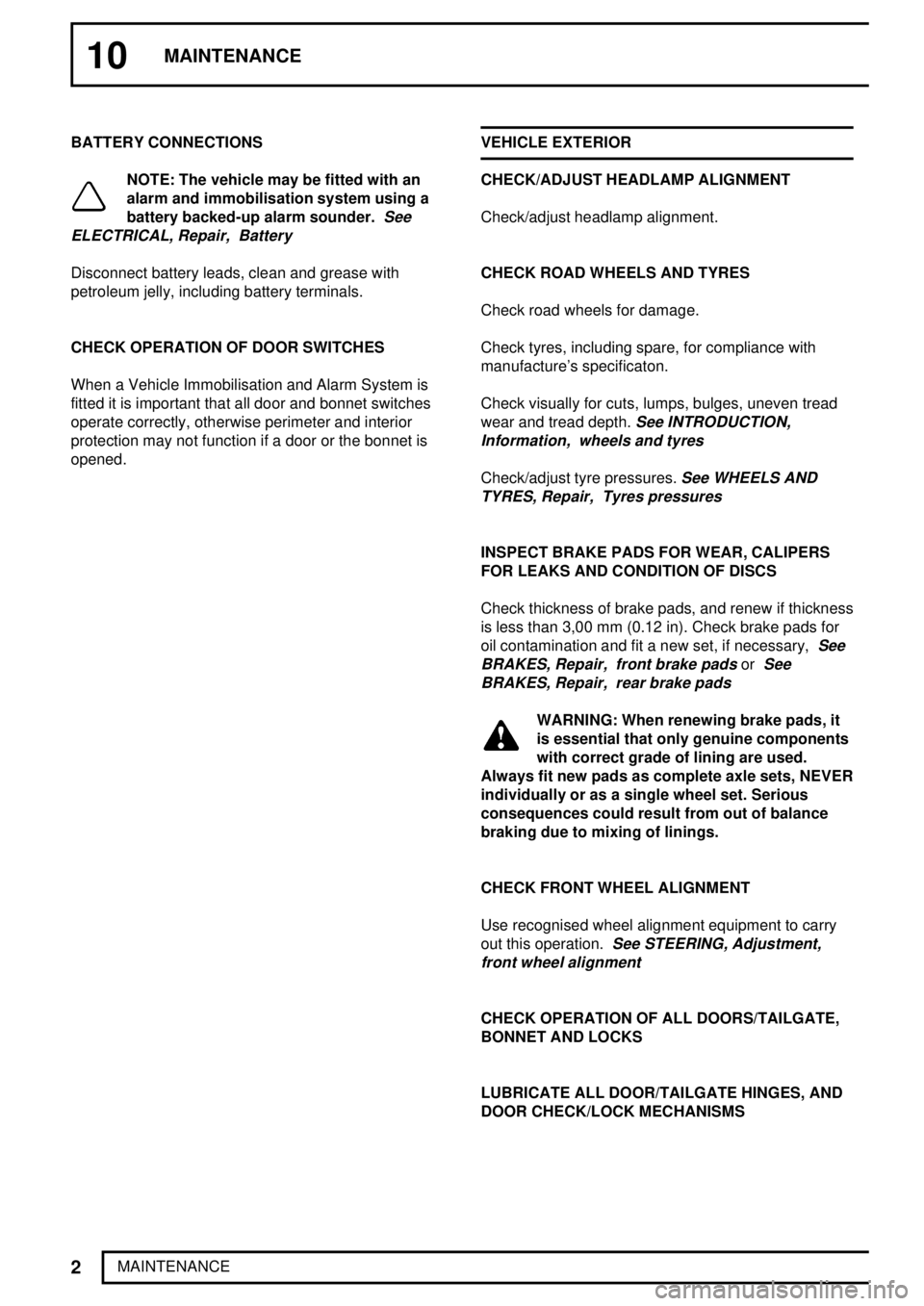
10MAINTENANCE
2
MAINTENANCE BATTERY CONNECTIONS
NOTE: The vehicle may be fitted with an
alarm and immobilisation system using a
battery backed-up alarm sounder.
See
ELECTRICAL, Repair, Battery
Disconnect battery leads, clean and grease with
petroleum jelly, including battery terminals.
CHECK OPERATION OF DOOR SWITCHES
When a Vehicle Immobilisation and Alarm System is
fitted it is important that all door and bonnet switches
operate correctly, otherwise perimeter and interior
protection may not function if a door or the bonnet is
opened.VEHICLE EXTERIOR
CHECK/ADJUST HEADLAMP ALIGNMENT
Check/adjust headlamp alignment.
CHECK ROAD WHEELS AND TYRES
Check road wheels for damage.
Check tyres, including spare, for compliance with
manufacture's specificaton.
Check visually for cuts, lumps, bulges, uneven tread
wear and tread depth.
See INTRODUCTION,
Information, wheels and tyres
Check/adjust tyre pressures.See WHEELS AND
TYRES, Repair, Tyres pressures
INSPECT BRAKE PADS FOR WEAR, CALIPERS
FOR LEAKS AND CONDITION OF DISCS
Check thickness of brake pads, and renew if thickness
is less than 3,00 mm (0.12 in). Check brake pads for
oil contamination and fit a new set, if necessary,
See
BRAKES, Repair, front brake pads
orSee
BRAKES, Repair, rear brake pads
WARNING: When renewing brake pads, it
is essential that only genuine components
with correct grade of lining are used.
Always fit new pads as complete axle sets, NEVER
individually or as a single wheel set. Serious
consequences could result from out of balance
braking due to mixing of linings.
CHECK FRONT WHEEL ALIGNMENT
Use recognised wheel alignment equipment to carry
out this operation.
See STEERING, Adjustment,
front wheel alignment
CHECK OPERATION OF ALL DOORS/TAILGATE,
BONNET AND LOCKS
LUBRICATE ALL DOOR/TAILGATE HINGES, AND
DOOR CHECK/LOCK MECHANISMS
Page 419 of 455
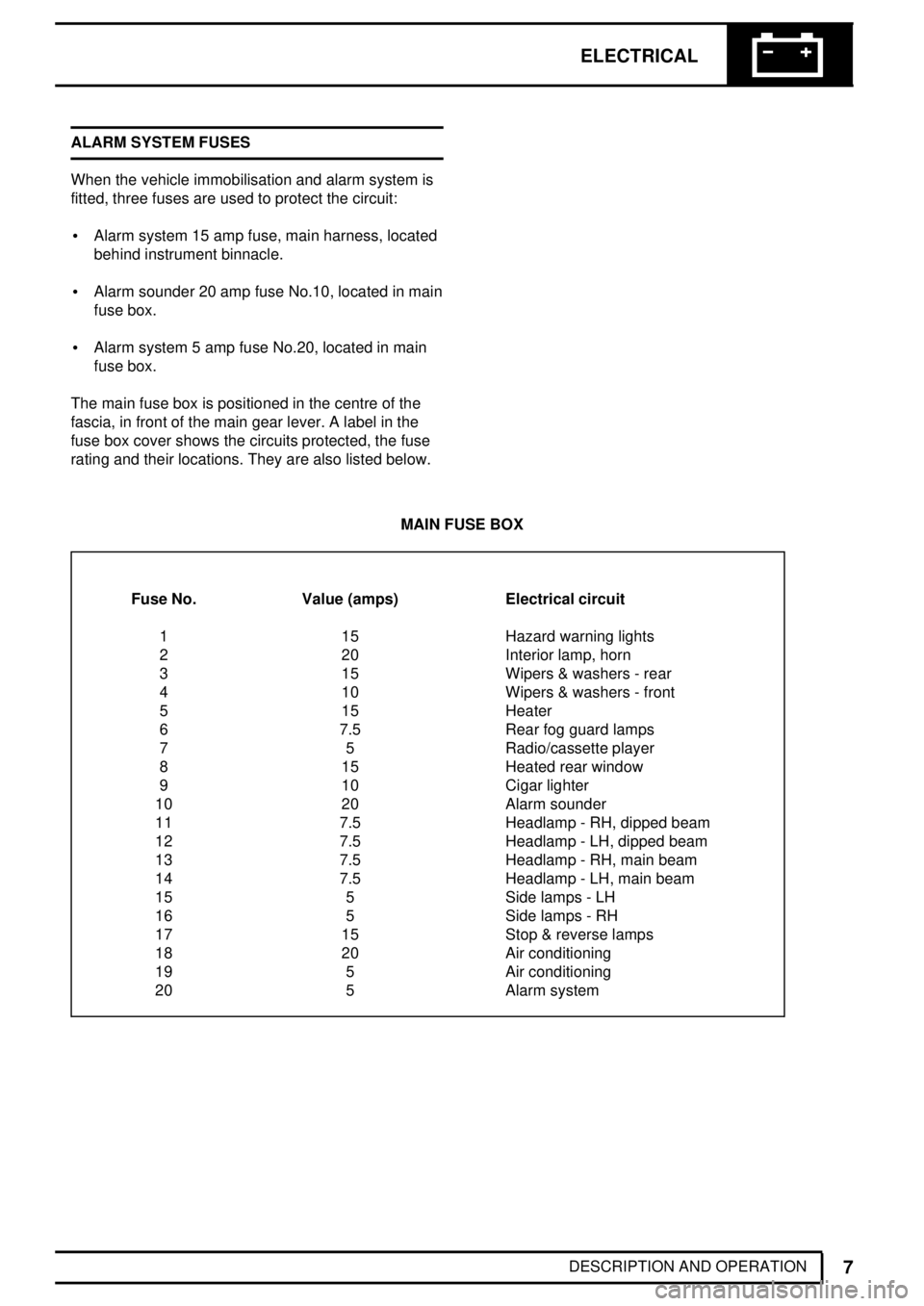
ELECTRICAL
7
DESCRIPTION AND OPERATION ALARM SYSTEM FUSES
When the vehicle immobilisation and alarm system is
fitted, three fuses are used to protect the circuit:
·Alarm system 15 amp fuse, main harness, located
behind instrument binnacle.
·Alarm sounder 20 amp fuse No.10, located in main
fuse box.
·Alarm system 5 amp fuse No.20, located in main
fuse box.
The main fuse box is positioned in the centre of the
fascia, in front of the main gear lever. A label in the
fuse box cover shows the circuits protected, the fuse
rating and their locations. They are also listed below.
MAIN FUSE BOX
Fuse No. Value (amps) Electrical circuit
1 15 Hazard warning lights
2 20 Interior lamp, horn
3 15 Wipers & washers - rear
4 10 Wipers & washers - front
5 15 Heater
6 7.5 Rear fog guard lamps
7 5 Radio/cassette player
8 15 Heated rear window
9 10 Cigar lighter
10 20 Alarm sounder
11 7.5 Headlamp - RH, dipped beam
12 7.5 Headlamp - LH, dipped beam
13 7.5 Headlamp - RH, main beam
14 7.5 Headlamp - LH, main beam
15 5 Side lamps - LH
16 5 Side lamps - RH
17 15 Stop & reverse lamps
18 20 Air conditioning
19 5 Air conditioning
20 5 Alarm system
Page 425 of 455
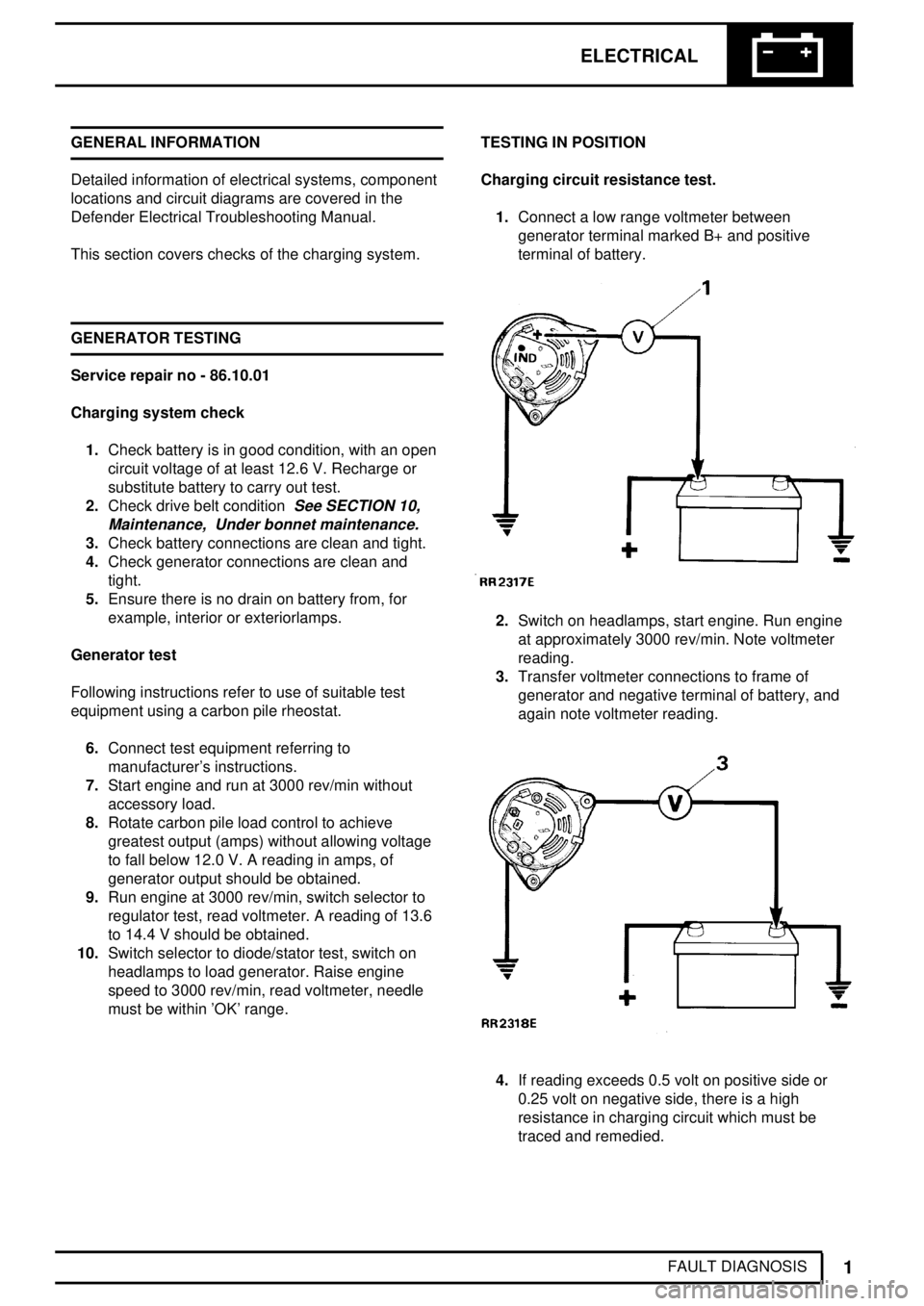
ELECTRICAL
1
FAULT DIAGNOSIS GENERAL INFORMATION
Detailed information of electrical systems, component
locations and circuit diagrams are covered in the
Defender Electrical Troubleshooting Manual.
This section covers checks of the charging system.
GENERATOR TESTING
Service repair no - 86.10.01
Charging system check
1.Check battery is in good condition, with an open
circuit voltage of at least 12.6 V. Recharge or
substitute battery to carry out test.
2.Check drive belt condition
See SECTION 10,
Maintenance, Under bonnet maintenance.
3.Check battery connections are clean and tight.
4.Check generator connections are clean and
tight.
5.Ensure there is no drain on battery from, for
example, interior or exteriorlamps.
Generator test
Following instructions refer to use of suitable test
equipment using a carbon pile rheostat.
6.Connect test equipment referring to
manufacturer's instructions.
7.Start engine and run at 3000 rev/min without
accessory load.
8.Rotate carbon pile load control to achieve
greatest output (amps) without allowing voltage
to fall below 12.0 V. A reading in amps, of
generator output should be obtained.
9.Run engine at 3000 rev/min, switch selector to
regulator test, read voltmeter. A reading of 13.6
to 14.4 V should be obtained.
10.Switch selector to diode/stator test, switch on
headlamps to load generator. Raise engine
speed to 3000 rev/min, read voltmeter, needle
must be within 'OK' range.TESTING IN POSITION
Charging circuit resistance test.
1.Connect a low range voltmeter between
generator terminal marked B+ and positive
terminal of battery.
2.Switch on headlamps, start engine. Run engine
at approximately 3000 rev/min. Note voltmeter
reading.
3.Transfer voltmeter connections to frame of
generator and negative terminal of battery, and
again note voltmeter reading.
4.If reading exceeds 0.5 volt on positive side or
0.25 volt on negative side, there is a high
resistance in charging circuit which must be
traced and remedied.
Page 438 of 455
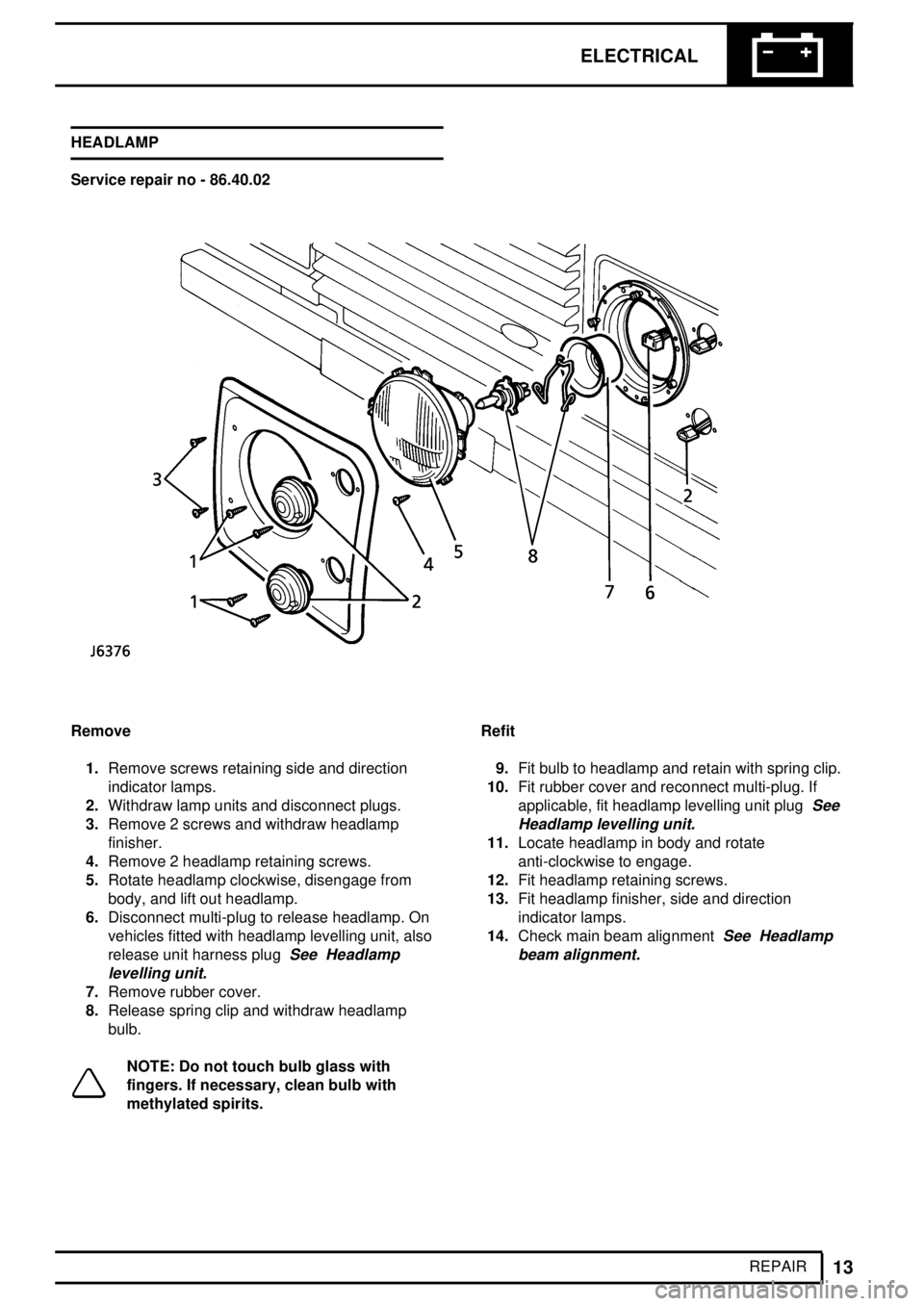
ELECTRICAL
13
REPAIR HEADLAMP
Service repair no - 86.40.02
Remove
1.Remove screws retaining side and direction
indicator lamps.
2.Withdraw lamp units and disconnect plugs.
3.Remove 2 screws and withdraw headlamp
finisher.
4.Remove 2 headlamp retaining screws.
5.Rotate headlamp clockwise, disengage from
body, and lift out headlamp.
6.Disconnect multi-plug to release headlamp. On
vehicles fitted with headlamp levelling unit, also
release unit harness plug
See Headlamp
levelling unit.
7.Remove rubber cover.
8.Release spring clip and withdraw headlamp
bulb.
NOTE: Do not touch bulb glass with
fingers. If necessary, clean bulb with
methylated spirits.Refit
9.Fit bulb to headlamp and retain with spring clip.
10.Fit rubber cover and reconnect multi-plug. If
applicable, fit headlamp levelling unit plug
See
Headlamp levelling unit.
11.Locate headlamp in body and rotate
anti-clockwise to engage.
12.Fit headlamp retaining screws.
13.Fit headlamp finisher, side and direction
indicator lamps.
14.Check main beam alignment
See Headlamp
beam alignment.
Page 445 of 455
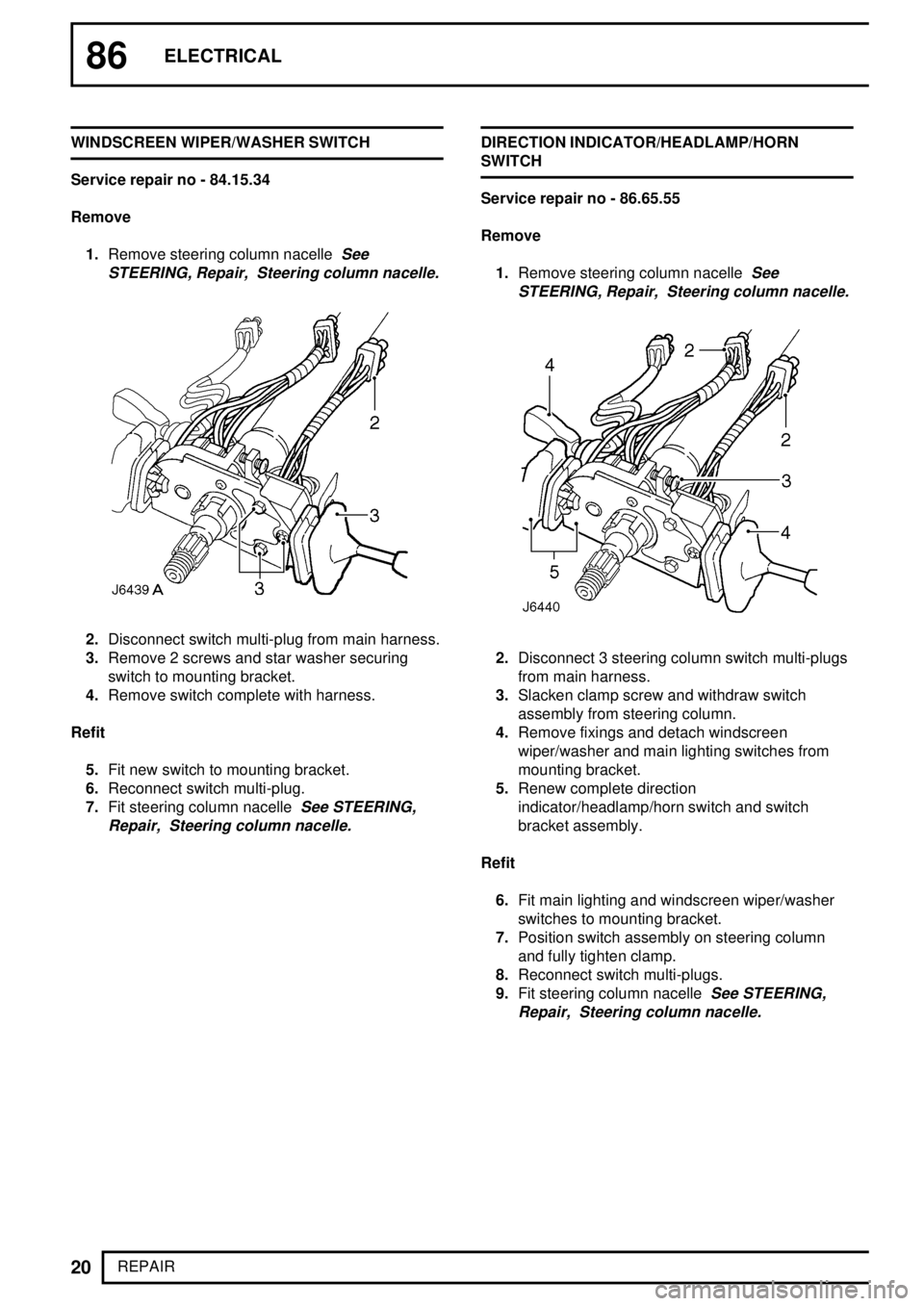
86ELECTRICAL
20
REPAIR WINDSCREEN WIPER/WASHER SWITCH
Service repair no - 84.15.34
Remove
1.Remove steering column nacelle
See
STEERING, Repair, Steering column nacelle.
2.Disconnect switch multi-plug from main harness.
3.Remove 2 screws and star washer securing
switch to mounting bracket.
4.Remove switch complete with harness.
Refit
5.Fit new switch to mounting bracket.
6.Reconnect switch multi-plug.
7.Fit steering column nacelle
See STEERING,
Repair, Steering column nacelle.
DIRECTION INDICATOR/HEADLAMP/HORN
SWITCH
Service repair no - 86.65.55
Remove
1.Remove steering column nacelle
See
STEERING, Repair, Steering column nacelle.
2.Disconnect 3 steering column switch multi-plugs
from main harness.
3.Slacken clamp screw and withdraw switch
assembly from steering column.
4.Remove fixings and detach windscreen
wiper/washer and main lighting switches from
mounting bracket.
5.Renew complete direction
indicator/headlamp/horn switch and switch
bracket assembly.
Refit
6.Fit main lighting and windscreen wiper/washer
switches to mounting bracket.
7.Position switch assembly on steering column
and fully tighten clamp.
8.Reconnect switch multi-plugs.
9.Fit steering column nacelle
See STEERING,
Repair, Steering column nacelle.
Page 448 of 455
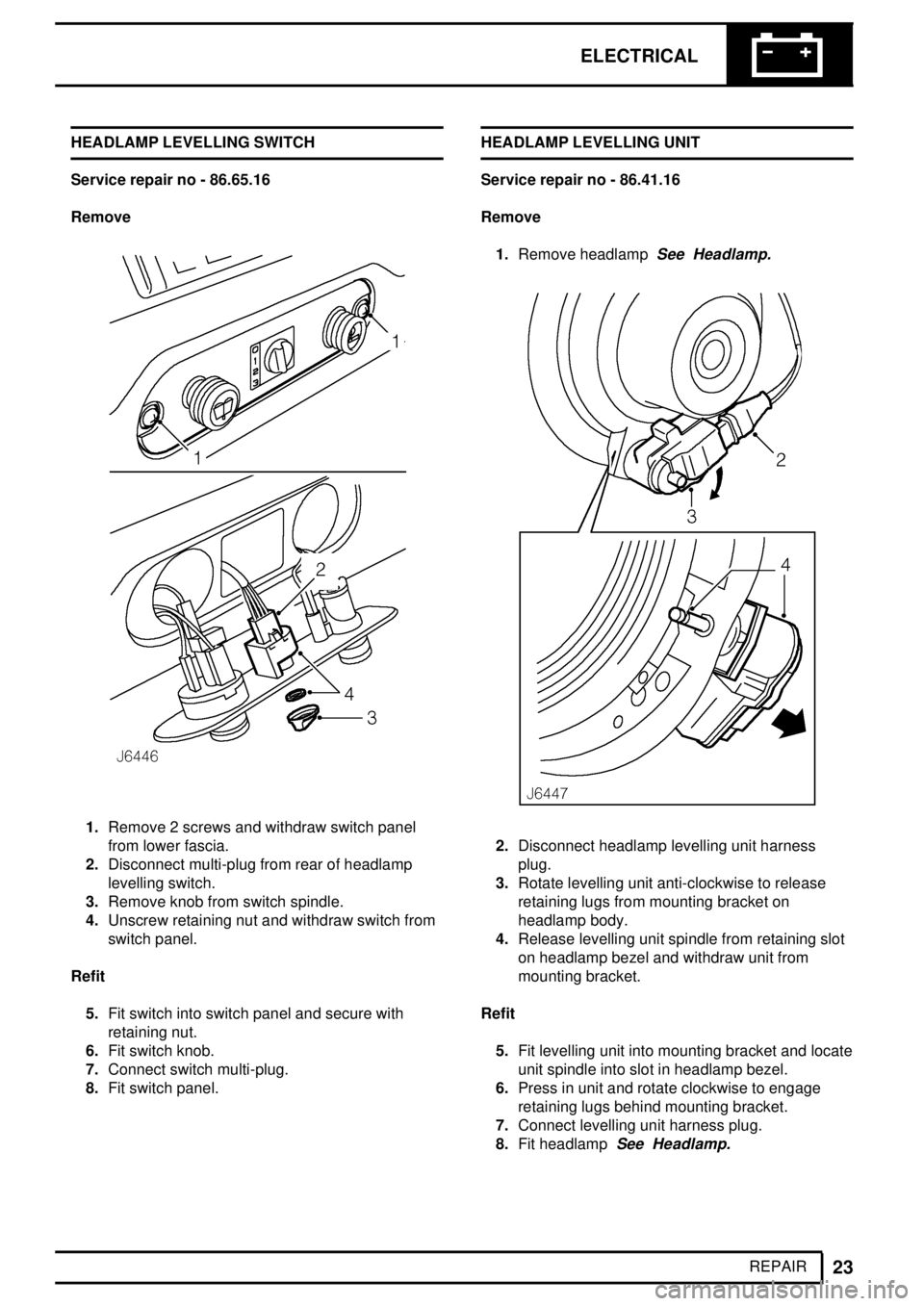
ELECTRICAL
23
REPAIR HEADLAMP LEVELLING SWITCH
Service repair no - 86.65.16
Remove
1.Remove 2 screws and withdraw switch panel
from lower fascia.
2.Disconnect multi-plug from rear of headlamp
levelling switch.
3.Remove knob from switch spindle.
4.Unscrew retaining nut and withdraw switch from
switch panel.
Refit
5.Fit switch into switch panel and secure with
retaining nut.
6.Fit switch knob.
7.Connect switch multi-plug.
8.Fit switch panel.HEADLAMP LEVELLING UNIT
Service repair no - 86.41.16
Remove
1.Remove headlamp
See Headlamp.
2.Disconnect headlamp levelling unit harness
plug.
3.Rotate levelling unit anti-clockwise to release
retaining lugs from mounting bracket on
headlamp body.
4.Release levelling unit spindle from retaining slot
on headlamp bezel and withdraw unit from
mounting bracket.
Refit
5.Fit levelling unit into mounting bracket and locate
unit spindle into slot in headlamp bezel.
6.Press in unit and rotate clockwise to engage
retaining lugs behind mounting bracket.
7.Connect levelling unit harness plug.
8.Fit headlamp
See Headlamp.
Page 449 of 455
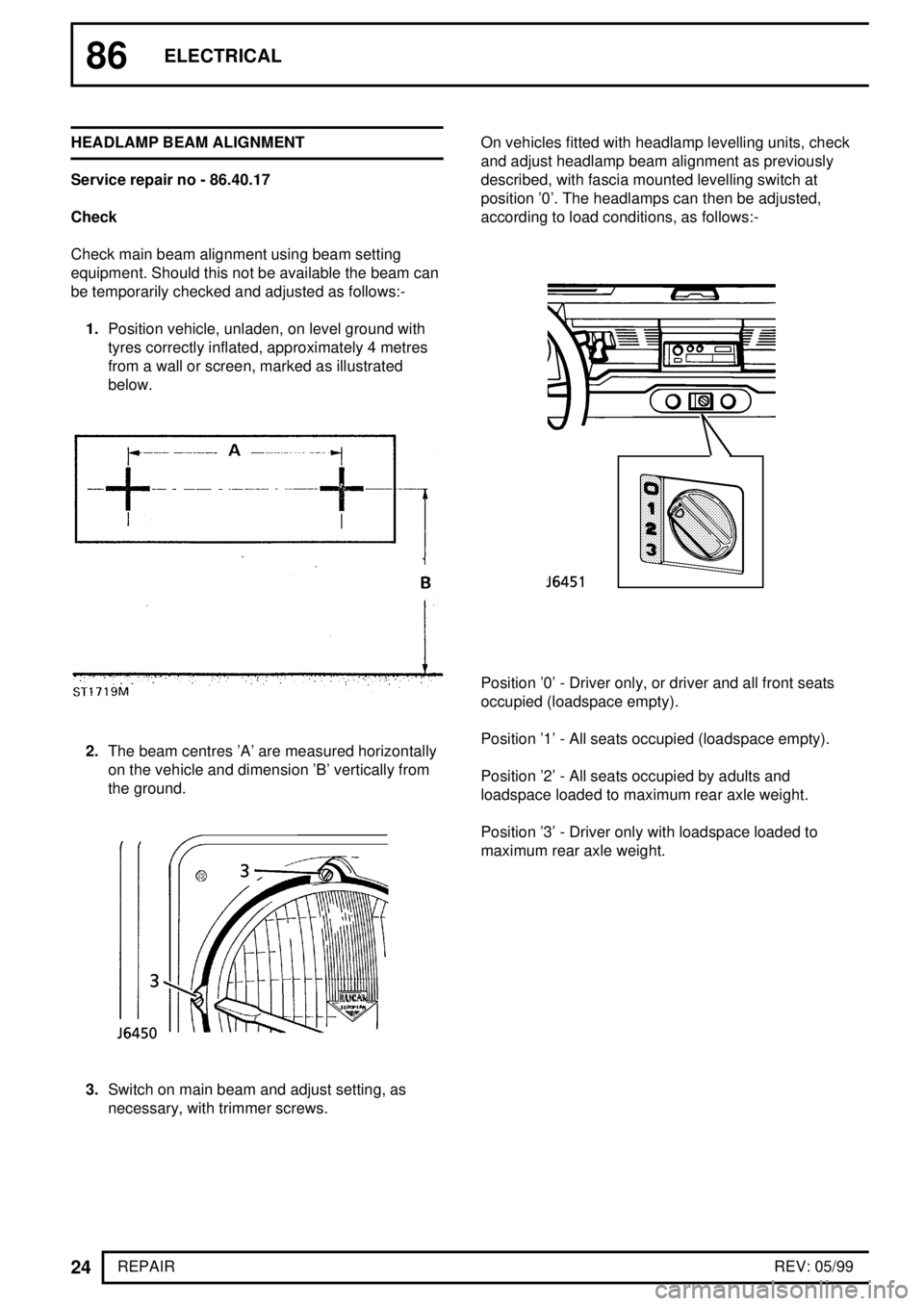
86ELECTRICAL
24
REPAIRREV: 05/99 HEADLAMP BEAM ALIGNMENT
Service repair no - 86.40.17
Check
Check main beam alignment using beam setting
equipment. Should this not be available the beam can
be temporarily checked and adjusted as follows:-
1.Position vehicle, unladen, on level ground with
tyres correctly inflated, approximately 4 metres
from a wall or screen, marked as illustrated
below.
2.The beam centres 'A' are measured horizontally
on the vehicle and dimension 'B' vertically from
the ground.
3.Switch on main beam and adjust setting, as
necessary, with trimmer screws.On vehicles fitted with headlamp levelling units, check
and adjust headlamp beam alignment as previously
described, with fascia mounted levelling switch at
position '0'. The headlamps can then be adjusted,
according to load conditions, as follows:-
Position '0' - Driver only, or driver and all front seats
occupied (loadspace empty).
Position '1' - All seats occupied (loadspace empty).
Position '2' - All seats occupied by adults and
loadspace loaded to maximum rear axle weight.
Position '3' - Driver only with loadspace loaded to
maximum rear axle weight.