relay LAND ROVER DEFENDER 1999 User Guide
[x] Cancel search | Manufacturer: LAND ROVER, Model Year: 1999, Model line: DEFENDER, Model: LAND ROVER DEFENDER 1999Pages: 667, PDF Size: 8.76 MB
Page 259 of 667
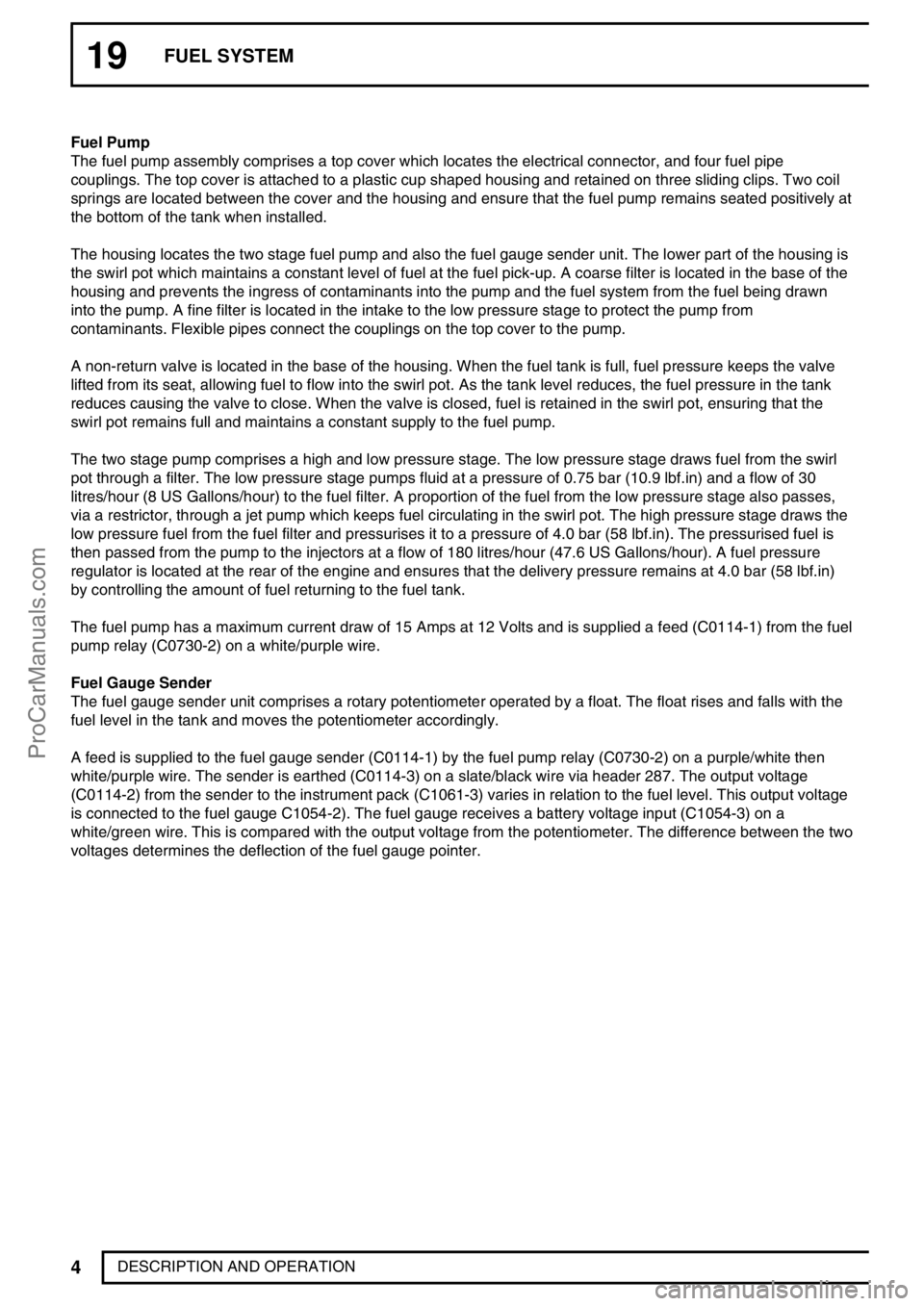
19FUEL SYSTEM
4
DESCRIPTION AND OPERATION Fuel Pump
The fuel pump assembly comprises a top cover which locates the electrical connector, and four fuel pipe
couplings. The top cover is attached to a plastic cup shaped housing and retained on three sliding clips. Two coil
springs are located between the cover and the housing and ensure that the fuel pump remains seated positively at
the bottom of the tank when installed.
The housing locates the two stage fuel pump and also the fuel gauge sender unit. The lower part of the housing is
the swirl pot which maintains a constant level of fuel at the fuel pick-up. A coarse filter is located in the base of the
housing and prevents the ingress of contaminants into the pump and the fuel system from the fuel being drawn
into the pump. A fine filter is located in the intake to the low pressure stage to protect the pump from
contaminants. Flexible pipes connect the couplings on the top cover to the pump.
A non-return valve is located in the base of the housing. When the fuel tank is full, fuel pressure keeps the valve
lifted from its seat, allowing fuel to flow into the swirl pot. As the tank level reduces, the fuel pressure in the tank
reduces causing the valve to close. When the valve is closed, fuel is retained in the swirl pot, ensuring that the
swirl pot remains full and maintains a constant supply to the fuel pump.
The two stage pump comprises a high and low pressure stage. The low pressure stage draws fuel from the swirl
pot through a filter. The low pressure stage pumps fluid at a pressure of 0.75 bar (10.9 lbf.in) and a flow of 30
litres/hour (8 US Gallons/hour) to the fuel filter. A proportion of the fuel from the low pressure stage also passes,
via a restrictor, through a jet pump which keeps fuel circulating in the swirl pot. The high pressure stage draws the
low pressure fuel from the fuel filter and pressurises it to a pressure of 4.0 bar (58 lbf.in). The pressurised fuel is
then passed from the pump to the injectors at a flow of 180 litres/hour (47.6 US Gallons/hour). A fuel pressure
regulator is located at the rear of the engine and ensures that the delivery pressure remains at 4.0 bar (58 lbf.in)
by controlling the amount of fuel returning to the fuel tank.
The fuel pump has a maximum current draw of 15 Amps at 12 Volts and is supplied a feed (C0114-1) from the fuel
pump relay (C0730-2) on a white/purple wire.
Fuel Gauge Sender
The fuel gauge sender unit comprises a rotary potentiometer operated by a float. The float rises and falls with the
fuel level in the tank and moves the potentiometer accordingly.
A feed is supplied to the fuel gauge sender (C0114-1) by the fuel pump relay (C0730-2) on a purple/white then
white/purple wire. The sender is earthed (C0114-3) on a slate/black wire via header 287. The output voltage
(C0114-2) from the sender to the instrument pack (C1061-3) varies in relation to the fuel level. This output voltage
is connected to the fuel gauge C1054-2). The fuel gauge receives a battery voltage input (C1054-3) on a
white/green wire. This is compared with the output voltage from the potentiometer. The difference between the two
voltages determines the deflection of the fuel gauge pointer.
ProCarManuals.com
Page 349 of 667
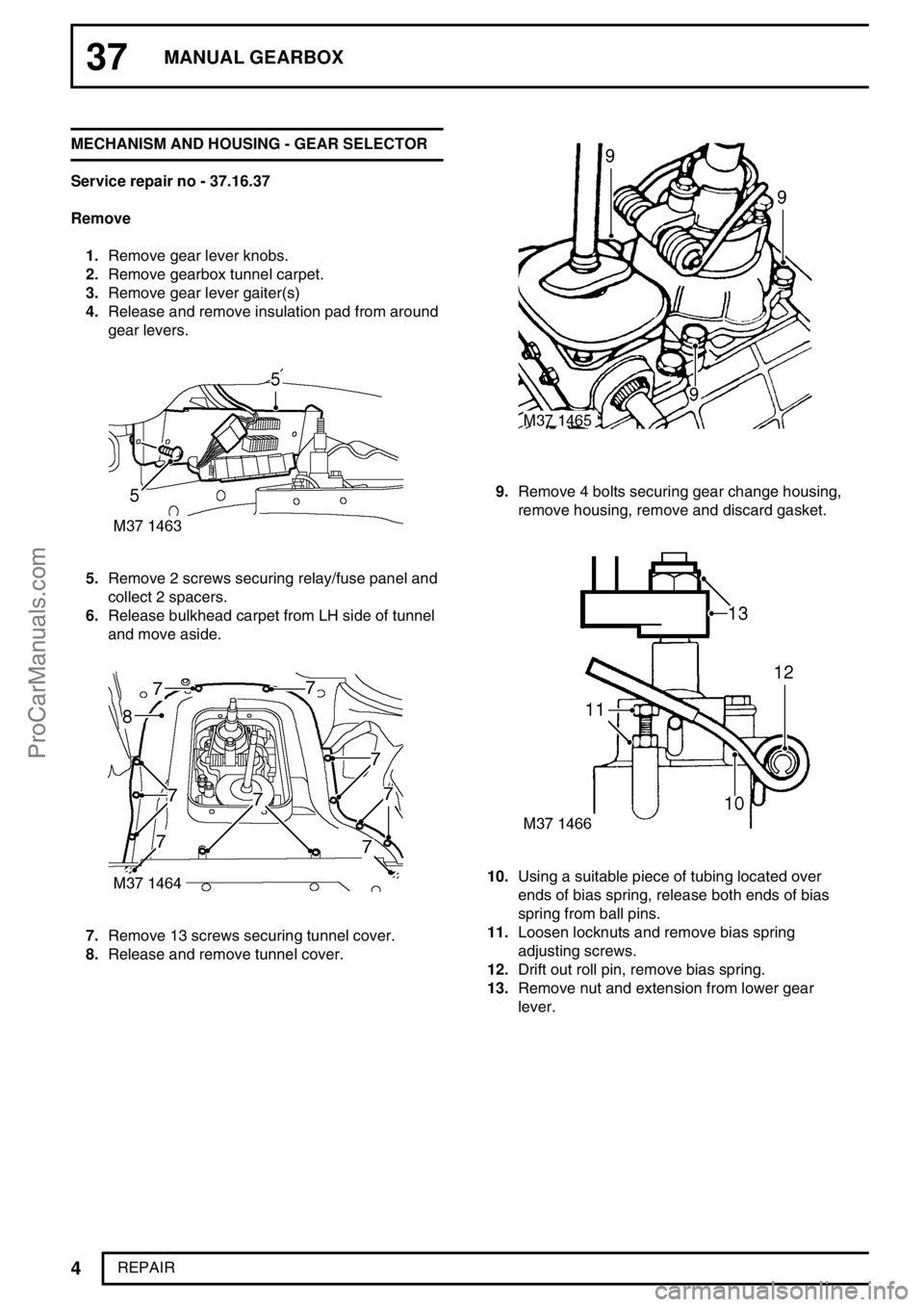
37MANUAL GEARBOX
4
REPAIR MECHANISM AND HOUSING - GEAR SELECTOR
Service repair no - 37.16.37
Remove
1.Remove gear lever knobs.
2.Remove gearbox tunnel carpet.
3.Remove gear lever gaiter(s)
4.Release and remove insulation pad from around
gear levers.
5.Remove 2 screws securing relay/fuse panel and
collect 2 spacers.
6.Release bulkhead carpet from LH side of tunnel
and move aside.
7.Remove 13 screws securing tunnel cover.
8.Release and remove tunnel cover.
9.Remove 4 bolts securing gear change housing,
remove housing, remove and discard gasket.
10.Using a suitable piece of tubing located over
ends of bias spring, release both ends of bias
spring from ball pins.
11.Loosen locknuts and remove bias spring
adjusting screws.
12.Drift out roll pin, remove bias spring.
13.Remove nut and extension from lower gear
lever.
ProCarManuals.com
Page 350 of 667
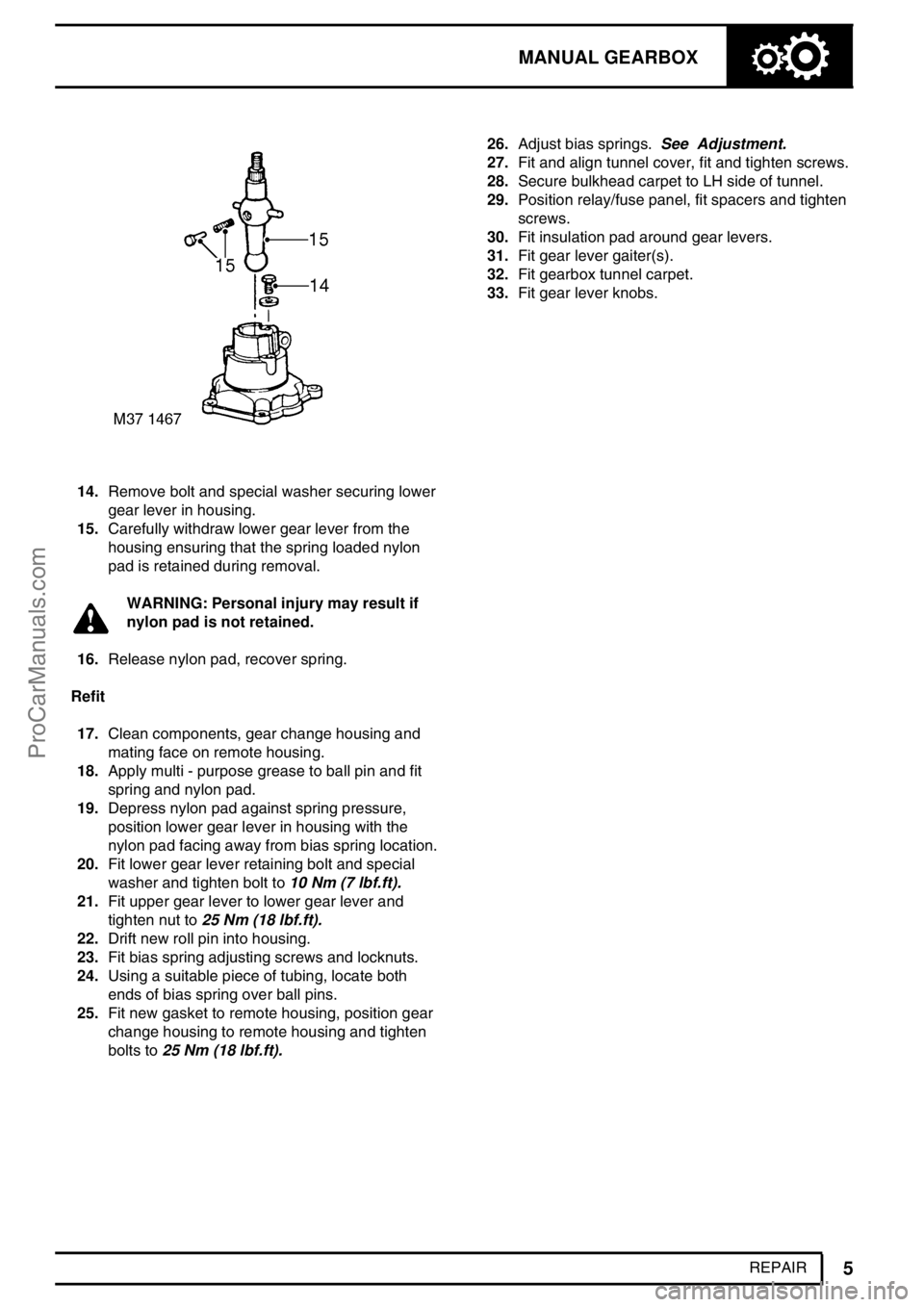
MANUAL GEARBOX
5
REPAIR
14.Remove bolt and special washer securing lower
gear lever in housing.
15.Carefully withdraw lower gear lever from the
housing ensuring that the spring loaded nylon
pad is retained during removal.
WARNING: Personal injury may result if
nylon pad is not retained.
16.Release nylon pad, recover spring.
Refit
17.Clean components, gear change housing and
mating face on remote housing.
18.Apply multi - purpose grease to ball pin and fit
spring and nylon pad.
19.Depress nylon pad against spring pressure,
position lower gear lever in housing with the
nylon pad facing away from bias spring location.
20.Fit lower gear lever retaining bolt and special
washer and tighten bolt to10 Nm (7 lbf.ft).
21.Fit upper gear lever to lower gear lever and
tighten nut to25 Nm (18 lbf.ft).
22.Drift new roll pin into housing.
23.Fit bias spring adjusting screws and locknuts.
24.Using a suitable piece of tubing, locate both
ends of bias spring over ball pins.
25.Fit new gasket to remote housing, position gear
change housing to remote housing and tighten
bolts to25 Nm (18 lbf.ft).26.Adjust bias springs.See Adjustment.
27.Fit and align tunnel cover, fit and tighten screws.
28.Secure bulkhead carpet to LH side of tunnel.
29.Position relay/fuse panel, fit spacers and tighten
screws.
30.Fit insulation pad around gear levers.
31.Fit gear lever gaiter(s).
32.Fit gearbox tunnel carpet.
33.Fit gear lever knobs.
ProCarManuals.com
Page 351 of 667
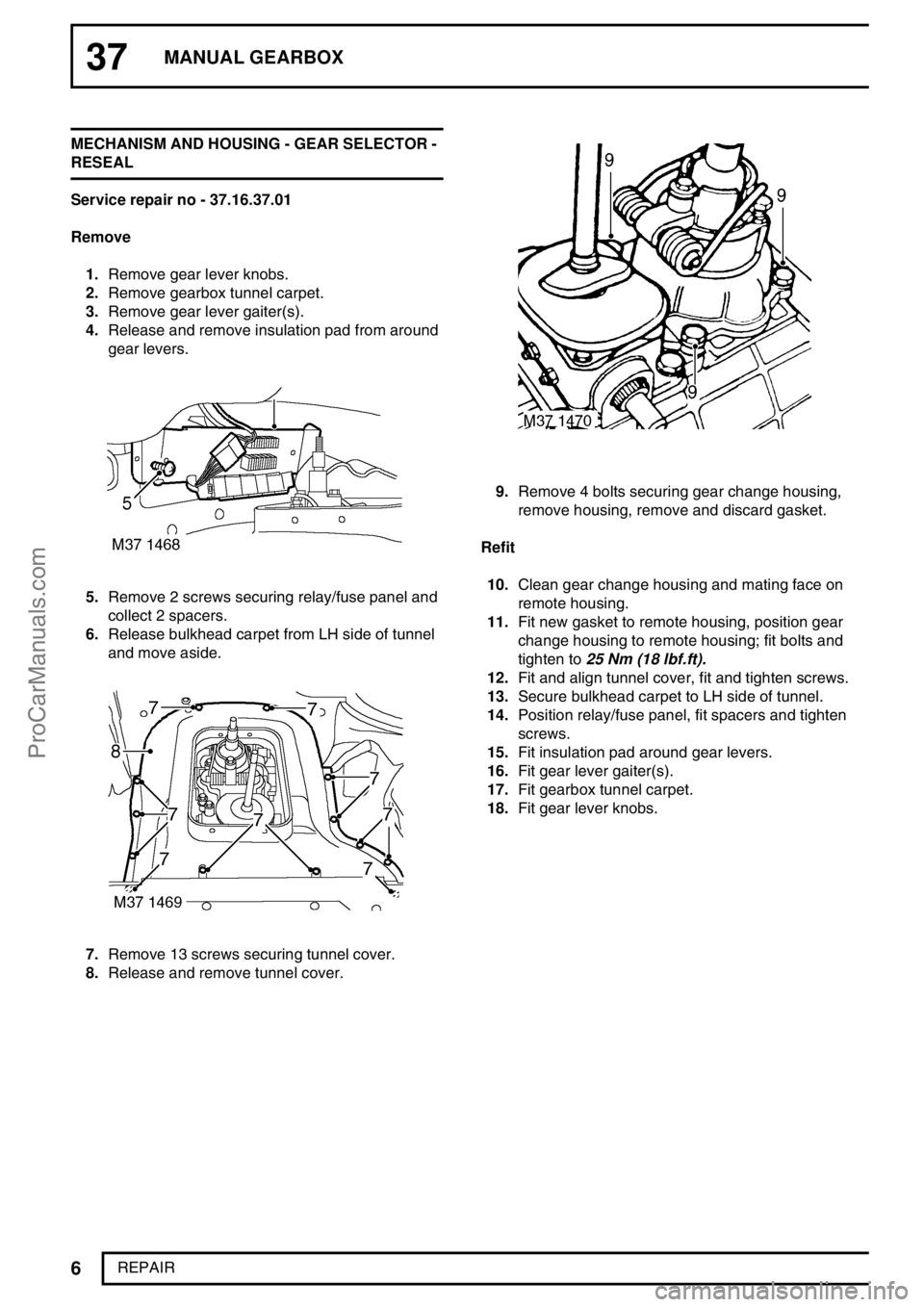
37MANUAL GEARBOX
6
REPAIR MECHANISM AND HOUSING - GEAR SELECTOR -
RESEAL
Service repair no - 37.16.37.01
Remove
1.Remove gear lever knobs.
2.Remove gearbox tunnel carpet.
3.Remove gear lever gaiter(s).
4.Release and remove insulation pad from around
gear levers.
5.Remove 2 screws securing relay/fuse panel and
collect 2 spacers.
6.Release bulkhead carpet from LH side of tunnel
and move aside.
7.Remove 13 screws securing tunnel cover.
8.Release and remove tunnel cover.
9.Remove 4 bolts securing gear change housing,
remove housing, remove and discard gasket.
Refit
10.Clean gear change housing and mating face on
remote housing.
11.Fit new gasket to remote housing, position gear
change housing to remote housing; fit bolts and
tighten to25 Nm (18 lbf.ft).
12.Fit and align tunnel cover, fit and tighten screws.
13.Secure bulkhead carpet to LH side of tunnel.
14.Position relay/fuse panel, fit spacers and tighten
screws.
15.Fit insulation pad around gear levers.
16.Fit gear lever gaiter(s).
17.Fit gearbox tunnel carpet.
18.Fit gear lever knobs.
ProCarManuals.com
Page 352 of 667
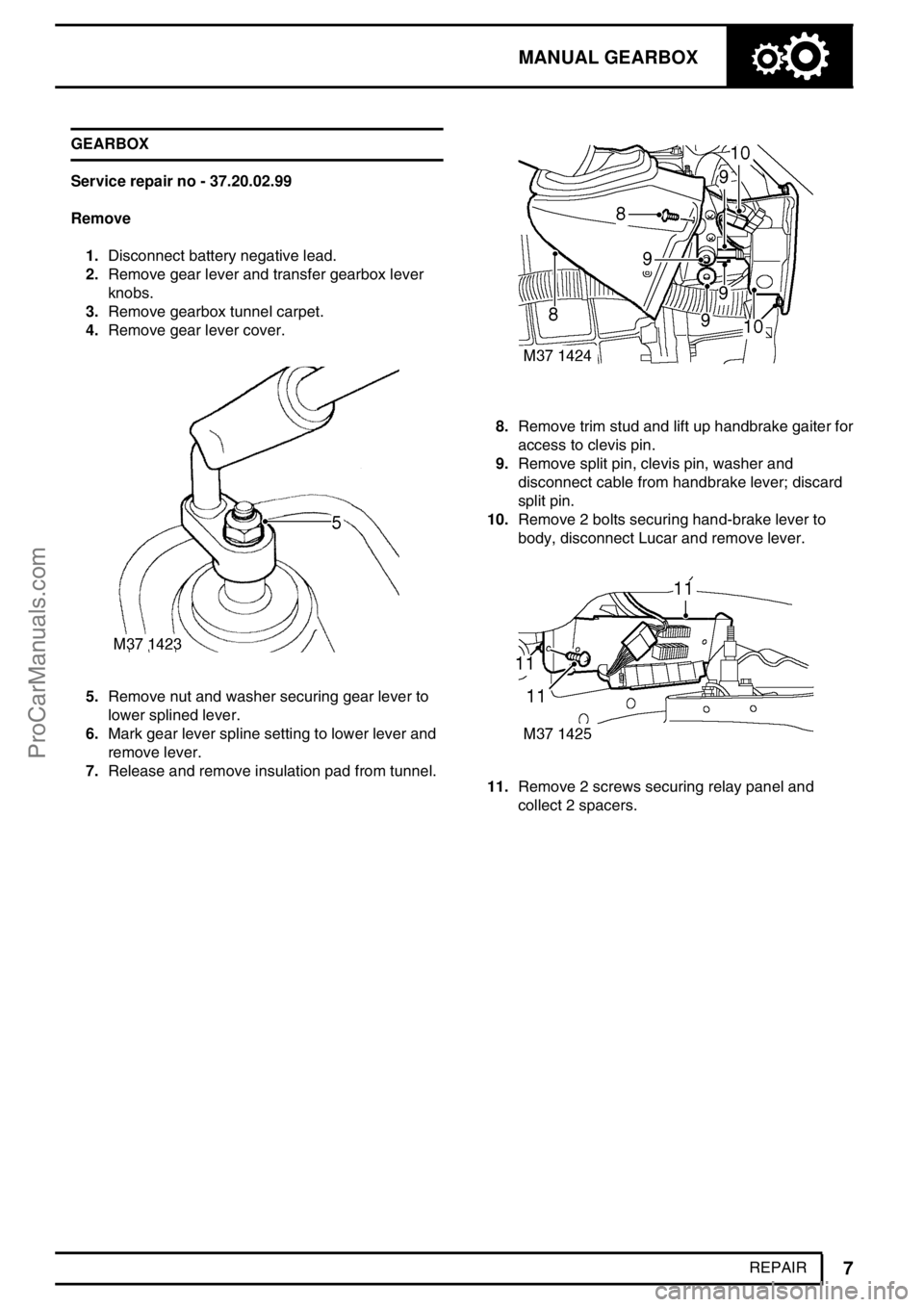
MANUAL GEARBOX
7
REPAIR GEARBOX
Service repair no - 37.20.02.99
Remove
1.Disconnect battery negative lead.
2.Remove gear lever and transfer gearbox lever
knobs.
3.Remove gearbox tunnel carpet.
4.Remove gear lever cover.
5.Remove nut and washer securing gear lever to
lower splined lever.
6.Mark gear lever spline setting to lower lever and
remove lever.
7.Release and remove insulation pad from tunnel.
8.Remove trim stud and lift up handbrake gaiter for
access to clevis pin.
9.Remove split pin, clevis pin, washer and
disconnect cable from handbrake lever; discard
split pin.
10.Remove 2 bolts securing hand-brake lever to
body, disconnect Lucar and remove lever.
11.Remove 2 screws securing relay panel and
collect 2 spacers.
ProCarManuals.com
Page 356 of 667
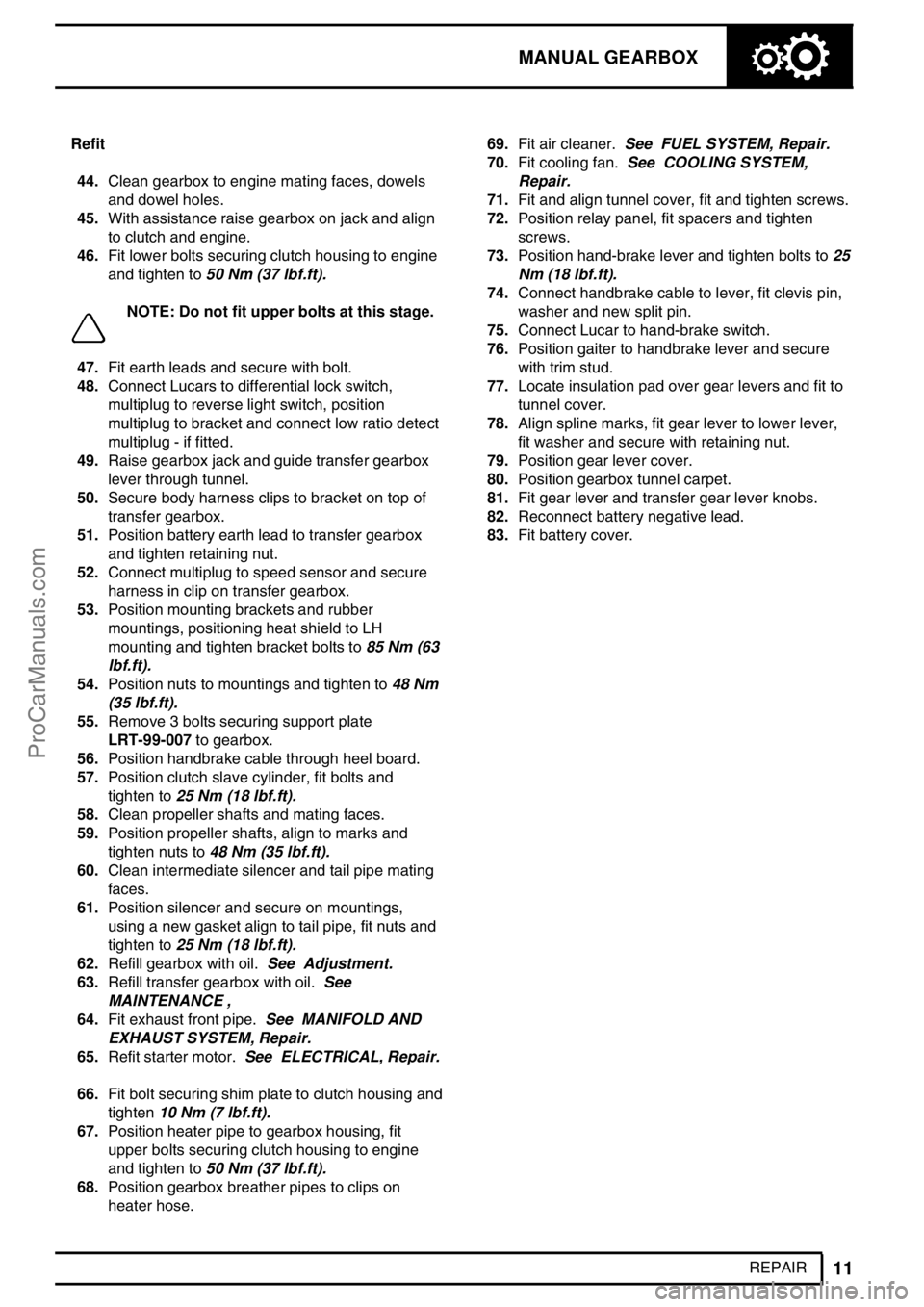
MANUAL GEARBOX
11
REPAIR Refit
44.Clean gearbox to engine mating faces, dowels
and dowel holes.
45.With assistance raise gearbox on jack and align
to clutch and engine.
46.Fit lower bolts securing clutch housing to engine
and tighten to50 Nm (37 lbf.ft).
NOTE: Do not fit upper bolts at this stage.
47.Fit earth leads and secure with bolt.
48.Connect Lucars to differential lock switch,
multiplug to reverse light switch, position
multiplug to bracket and connect low ratio detect
multiplug - if fitted.
49.Raise gearbox jack and guide transfer gearbox
lever through tunnel.
50.Secure body harness clips to bracket on top of
transfer gearbox.
51.Position battery earth lead to transfer gearbox
and tighten retaining nut.
52.Connect multiplug to speed sensor and secure
harness in clip on transfer gearbox.
53.Position mounting brackets and rubber
mountings, positioning heat shield to LH
mounting and tighten bracket bolts to85 Nm (63
lbf.ft).
54.Position nuts to mountings and tighten to48 Nm
(35 lbf.ft).
55.Remove 3 bolts securing support plate
LRT-99-007to gearbox.
56.Position handbrake cable through heel board.
57.Position clutch slave cylinder, fit bolts and
tighten to25 Nm (18 lbf.ft).
58.Clean propeller shafts and mating faces.
59.Position propeller shafts, align to marks and
tighten nuts to48 Nm (35 lbf.ft).
60.Clean intermediate silencer and tail pipe mating
faces.
61.Position silencer and secure on mountings,
using a new gasket align to tail pipe, fit nuts and
tighten to25 Nm (18 lbf.ft).
62.Refill gearbox with oil.See Adjustment.
63.Refill transfer gearbox with oil.See
MAINTENANCE ,
64.Fit exhaust front pipe.See MANIFOLD AND
EXHAUST SYSTEM, Repair.
65.Refit starter motor.See ELECTRICAL, Repair.
66.Fit bolt securing shim plate to clutch housing and
tighten10 Nm (7 lbf.ft).
67.Position heater pipe to gearbox housing, fit
upper bolts securing clutch housing to engine
and tighten to50 Nm (37 lbf.ft).
68.Position gearbox breather pipes to clips on
heater hose.69.Fit air cleaner.See FUEL SYSTEM, Repair.
70.Fit cooling fan.See COOLING SYSTEM,
Repair.
71.Fit and align tunnel cover, fit and tighten screws.
72.Position relay panel, fit spacers and tighten
screws.
73.Position hand-brake lever and tighten bolts to25
Nm (18 lbf.ft).
74.Connect handbrake cable to lever, fit clevis pin,
washer and new split pin.
75.Connect Lucar to hand-brake switch.
76.Position gaiter to handbrake lever and secure
with trim stud.
77.Locate insulation pad over gear levers and fit to
tunnel cover.
78.Align spline marks, fit gear lever to lower lever,
fit washer and secure with retaining nut.
79.Position gear lever cover.
80.Position gearbox tunnel carpet.
81.Fit gear lever and transfer gear lever knobs.
82.Reconnect battery negative lead.
83.Fit battery cover.
ProCarManuals.com
Page 357 of 667
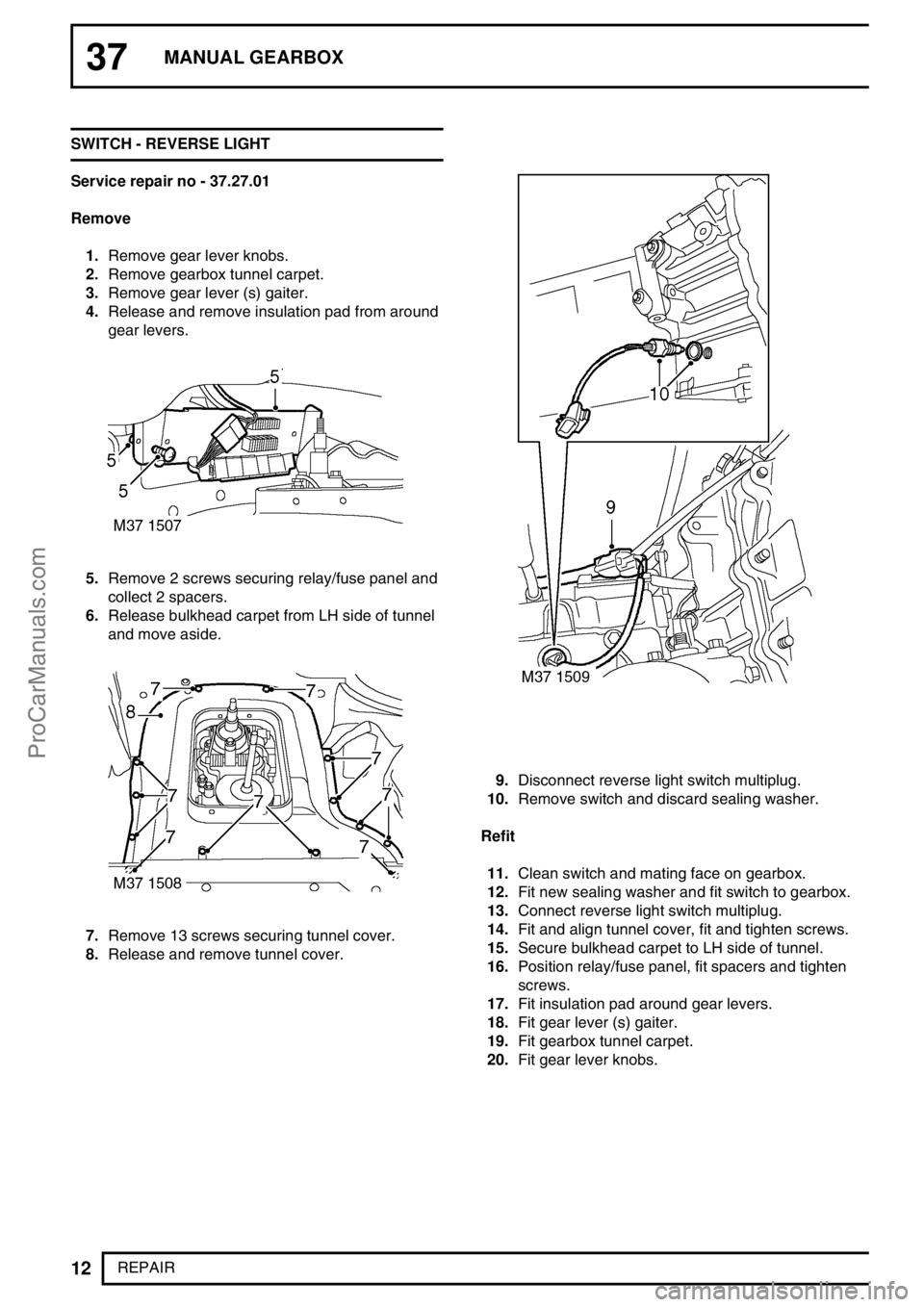
37MANUAL GEARBOX
12
REPAIR SWITCH - REVERSE LIGHT
Service repair no - 37.27.01
Remove
1.Remove gear lever knobs.
2.Remove gearbox tunnel carpet.
3.Remove gear lever (s) gaiter.
4.Release and remove insulation pad from around
gear levers.
5.Remove 2 screws securing relay/fuse panel and
collect 2 spacers.
6.Release bulkhead carpet from LH side of tunnel
and move aside.
7.Remove 13 screws securing tunnel cover.
8.Release and remove tunnel cover.
9.Disconnect reverse light switch multiplug.
10.Remove switch and discard sealing washer.
Refit
11.Clean switch and mating face on gearbox.
12.Fit new sealing washer and fit switch to gearbox.
13.Connect reverse light switch multiplug.
14.Fit and align tunnel cover, fit and tighten screws.
15.Secure bulkhead carpet to LH side of tunnel.
16.Position relay/fuse panel, fit spacers and tighten
screws.
17.Fit insulation pad around gear levers.
18.Fit gear lever (s) gaiter.
19.Fit gearbox tunnel carpet.
20.Fit gear lever knobs.
ProCarManuals.com
Page 360 of 667
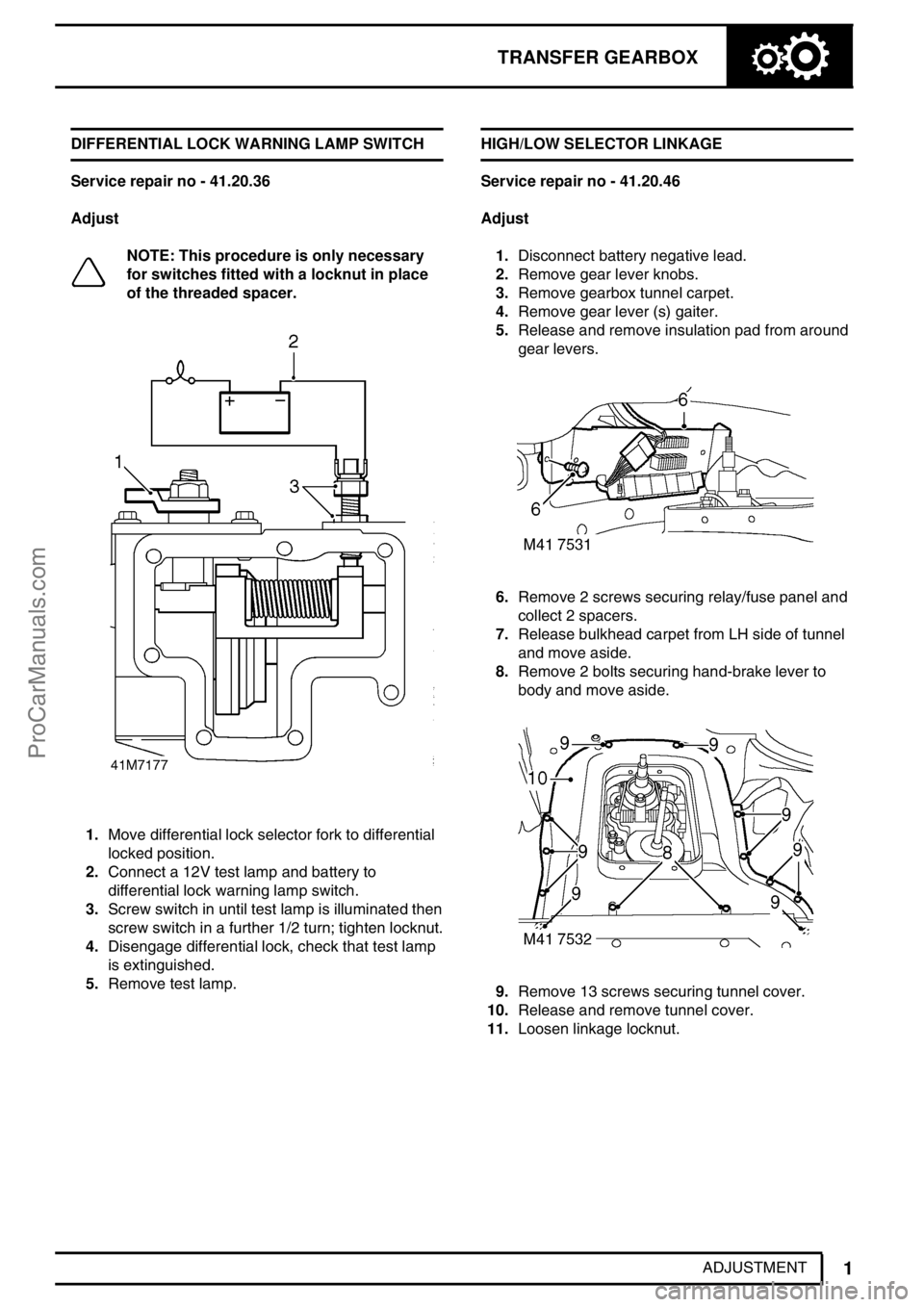
TRANSFER GEARBOX
1
ADJUSTMENT DIFFERENTIAL LOCK WARNING LAMP SWITCH
Service repair no - 41.20.36
Adjust
NOTE: This procedure is only necessary
for switches fitted with a locknut in place
of the threaded spacer.
1.Move differential lock selector fork to differential
locked position.
2.Connect a 12V test lamp and battery to
differential lock warning lamp switch.
3.Screw switch in until test lamp is illuminated then
screw switch in a further 1/2 turn; tighten locknut.
4.Disengage differential lock, check that test lamp
is extinguished.
5.Remove test lamp.HIGH/LOW SELECTOR LINKAGE
Service repair no - 41.20.46
Adjust
1.Disconnect battery negative lead.
2.Remove gear lever knobs.
3.Remove gearbox tunnel carpet.
4.Remove gear lever (s) gaiter.
5.Release and remove insulation pad from around
gear levers.
6.Remove 2 screws securing relay/fuse panel and
collect 2 spacers.
7.Release bulkhead carpet from LH side of tunnel
and move aside.
8.Remove 2 bolts securing hand-brake lever to
body and move aside.
9.Remove 13 screws securing tunnel cover.
10.Release and remove tunnel cover.
11.Loosen linkage locknut.
ProCarManuals.com
Page 361 of 667
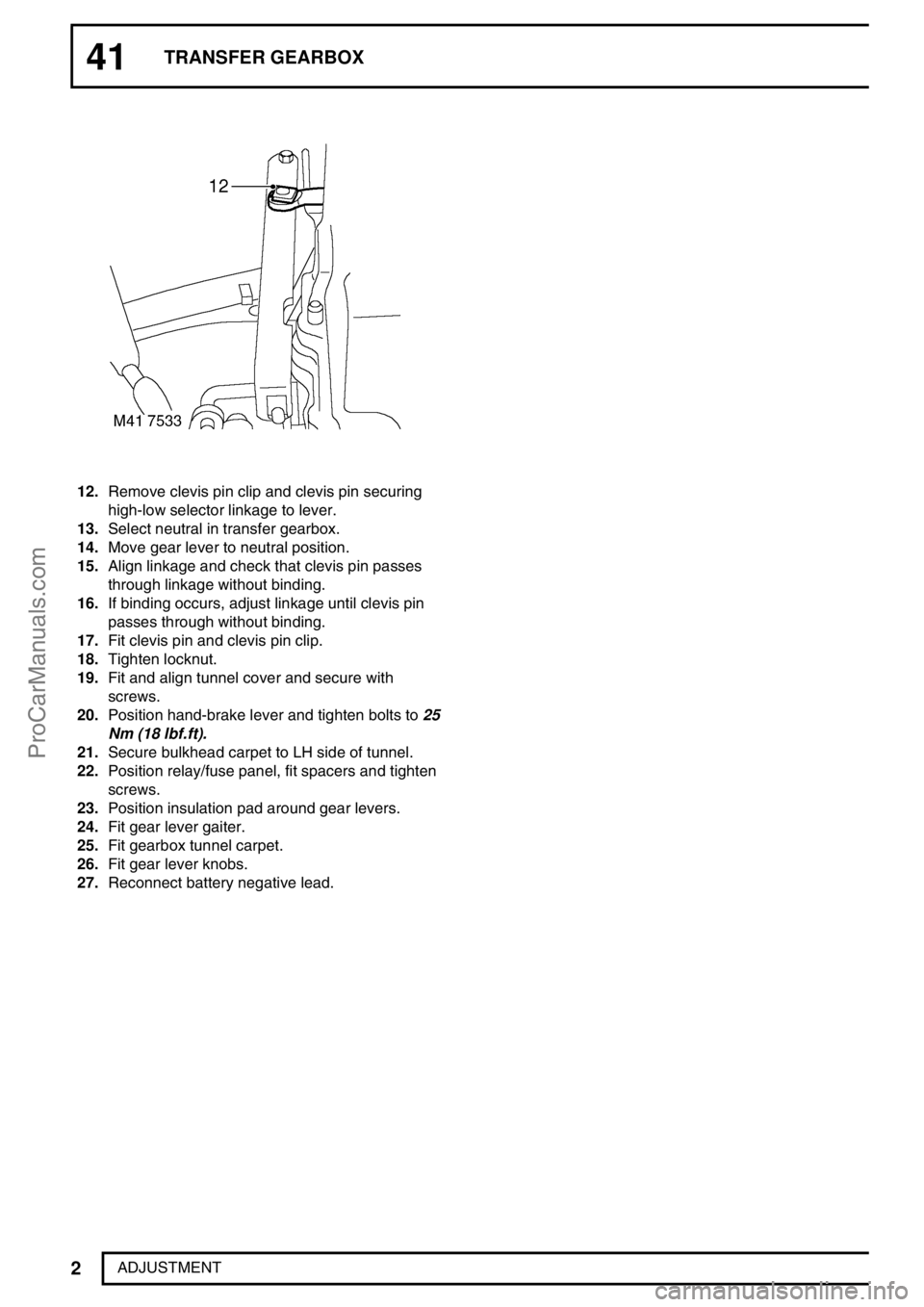
41TRANSFER GEARBOX
2
ADJUSTMENT
12.Remove clevis pin clip and clevis pin securing
high-low selector linkage to lever.
13.Select neutral in transfer gearbox.
14.Move gear lever to neutral position.
15.Align linkage and check that clevis pin passes
through linkage without binding.
16.If binding occurs, adjust linkage until clevis pin
passes through without binding.
17.Fit clevis pin and clevis pin clip.
18.Tighten locknut.
19.Fit and align tunnel cover and secure with
screws.
20.Position hand-brake lever and tighten bolts to25
Nm (18 lbf.ft).
21.Secure bulkhead carpet to LH side of tunnel.
22.Position relay/fuse panel, fit spacers and tighten
screws.
23.Position insulation pad around gear levers.
24.Fit gear lever gaiter.
25.Fit gearbox tunnel carpet.
26.Fit gear lever knobs.
27.Reconnect battery negative lead.
ProCarManuals.com
Page 368 of 667
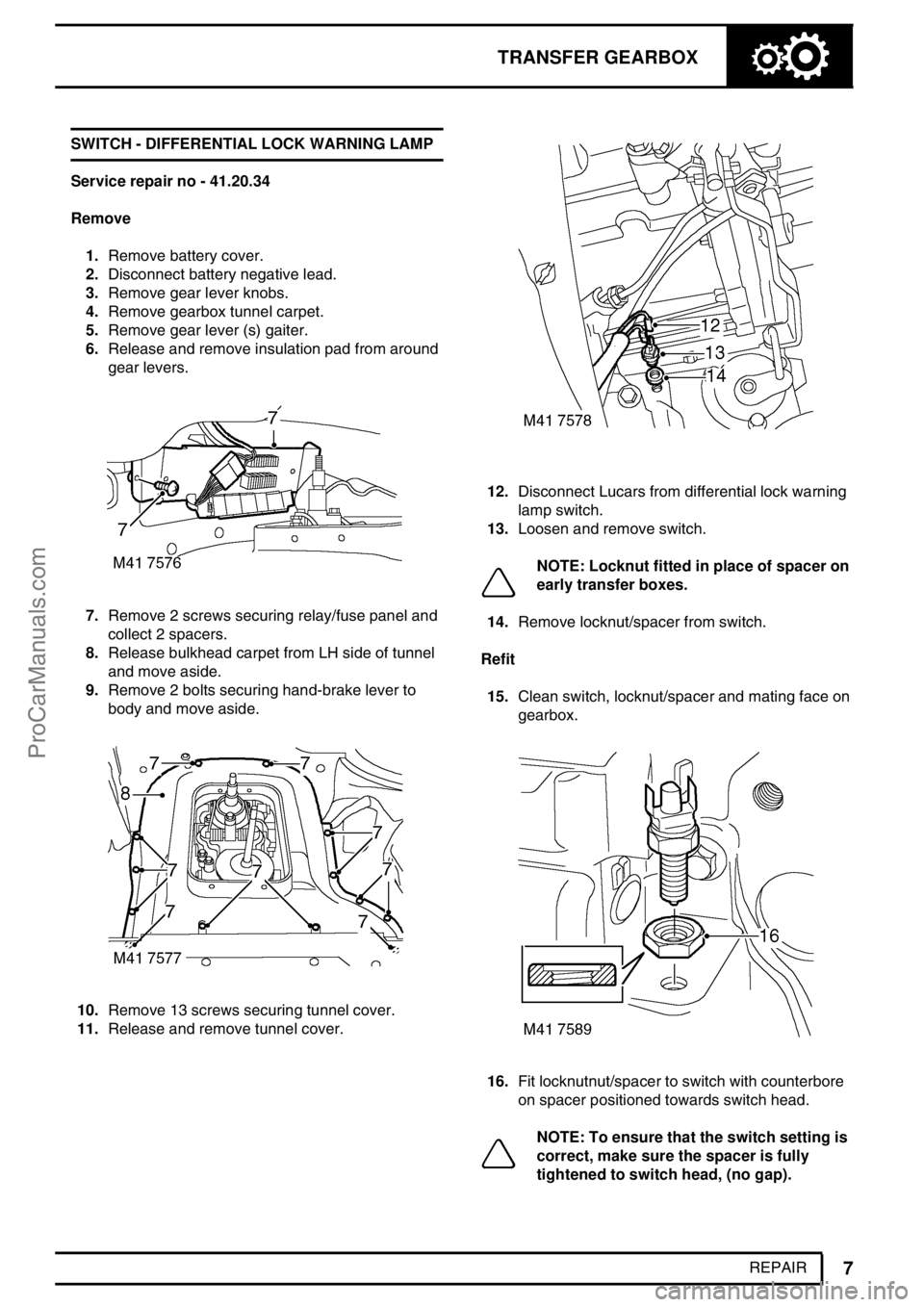
TRANSFER GEARBOX
7
REPAIR SWITCH - DIFFERENTIAL LOCK WARNING LAMP
Service repair no - 41.20.34
Remove
1.Remove battery cover.
2.Disconnect battery negative lead.
3.Remove gear lever knobs.
4.Remove gearbox tunnel carpet.
5.Remove gear lever (s) gaiter.
6.Release and remove insulation pad from around
gear levers.
7.Remove 2 screws securing relay/fuse panel and
collect 2 spacers.
8.Release bulkhead carpet from LH side of tunnel
and move aside.
9.Remove 2 bolts securing hand-brake lever to
body and move aside.
10.Remove 13 screws securing tunnel cover.
11.Release and remove tunnel cover.
12.Disconnect Lucars from differential lock warning
lamp switch.
13.Loosen and remove switch.
NOTE: Locknut fitted in place of spacer on
early transfer boxes.
14.Remove locknut/spacer from switch.
Refit
15.Clean switch, locknut/spacer and mating face on
gearbox.
16.Fit locknutnut/spacer to switch with counterbore
on spacer positioned towards switch head.
NOTE: To ensure that the switch setting is
correct, make sure the spacer is fully
tightened to switch head, (no gap).
ProCarManuals.com