engine LAND ROVER DEFENDER 1999 Workshop Manual
[x] Cancel search | Manufacturer: LAND ROVER, Model Year: 1999, Model line: DEFENDER, Model: LAND ROVER DEFENDER 1999Pages: 667, PDF Size: 8.76 MB
Page 527 of 667
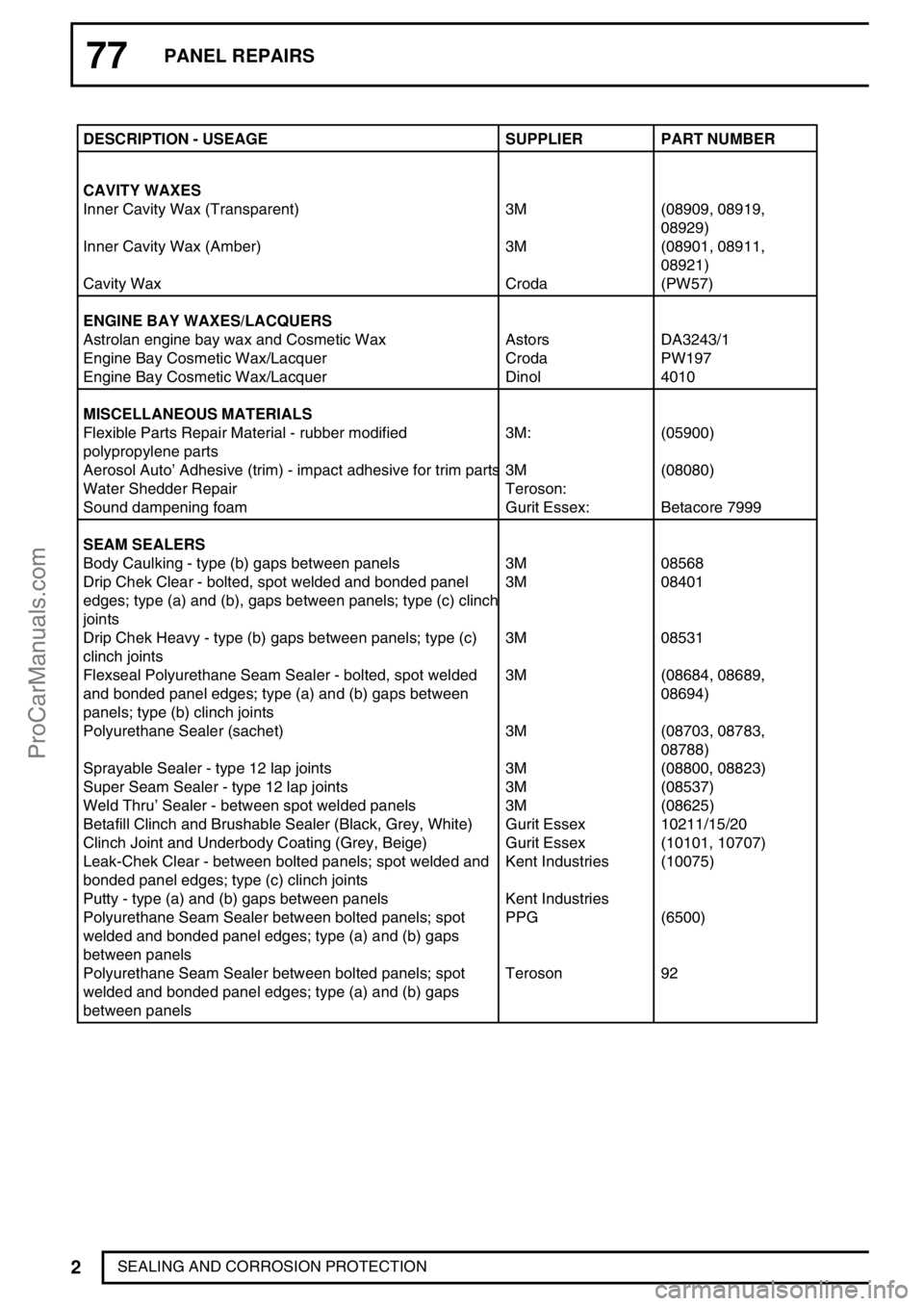
77PANEL REPAIRS
2
SEALING AND CORROSION PROTECTION DESCRIPTION - USEAGE SUPPLIER PART NUMBER
CAVITY WAXES
Inner Cavity Wax (Transparent) 3M (08909, 08919,
08929)
Inner Cavity Wax (Amber) 3M (08901, 08911,
08921)
Cavity Wax Croda (PW57)
ENGINE BAY WAXES/LACQUERS
Astrolan engine bay wax and Cosmetic Wax Astors DA3243/1
Engine Bay Cosmetic Wax/Lacquer Croda PW197
Engine Bay Cosmetic Wax/Lacquer Dinol 4010
MISCELLANEOUS MATERIALS
Flexible Parts Repair Material - rubber modified
polypropylene parts3M: (05900)
Aerosol Auto’Adhesive (trim) - impact adhesive for trim parts 3M (08080)
Water Shedder Repair Teroson:
Sound dampening foam Gurit Essex: Betacore 7999
SEAM SEALERS
Body Caulking - type (b) gaps between panels 3M 08568
Drip Chek Clear - bolted, spot welded and bonded panel
edges; type (a) and (b), gaps between panels; type (c) clinch
joints3M 08401
Drip Chek Heavy - type (b) gaps between panels; type (c)
clinch joints3M 08531
Flexseal Polyurethane Seam Sealer - bolted, spot welded
and bonded panel edges; type (a) and (b) gaps between
panels; type (b) clinch joints3M (08684, 08689,
08694)
Polyurethane Sealer (sachet) 3M (08703, 08783,
08788)
Sprayable Sealer - type 12 lap joints 3M (08800, 08823)
Super Seam Sealer - type 12 lap joints 3M (08537)
Weld Thru’Sealer - between spot welded panels 3M (08625)
Betafill Clinch and Brushable Sealer (Black, Grey, White) Gurit Essex 10211/15/20
Clinch Joint and Underbody Coating (Grey, Beige) Gurit Essex (10101, 10707)
Leak-Chek Clear - between bolted panels; spot welded and
bonded panel edges; type (c) clinch jointsKent Industries (10075)
Putty - type (a) and (b) gaps between panels Kent Industries
Polyurethane Seam Sealer between bolted panels; spot
welded and bonded panel edges; type (a) and (b) gaps
between panelsPPG (6500)
Polyurethane Seam Sealer between bolted panels; spot
welded and bonded panel edges; type (a) and (b) gaps
between panelsTeroson 92
ProCarManuals.com
Page 533 of 667
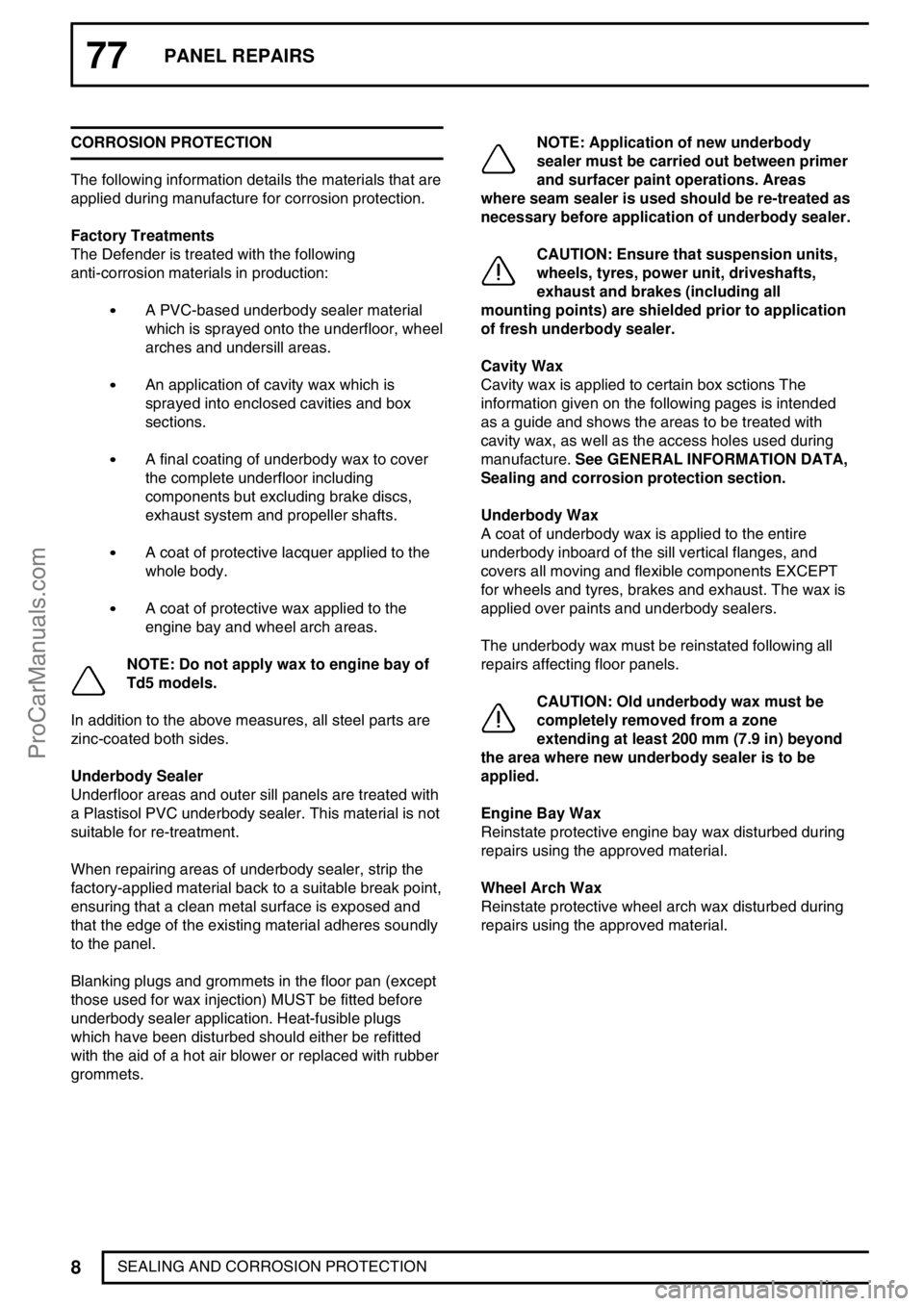
77PANEL REPAIRS
8
SEALING AND CORROSION PROTECTION CORROSION PROTECTION
The following information details the materials that are
applied during manufacture for corrosion protection.
Factory Treatments
The Defender is treated with the following
anti-corrosion materials in production:
A PVC-based underbody sealer material
which is sprayed onto the underfloor, wheel
arches and undersill areas.
An application of cavity wax which is
sprayed into enclosed cavities and box
sections.
A final coating of underbody wax to cover
the complete underfloor including
components but excluding brake discs,
exhaust system and propeller shafts.
A coat of protective lacquer applied to the
whole body.
A coat of protective wax applied to the
engine bay and wheel arch areas.
NOTE: Do not apply wax to engine bay of
Td5 models.
In addition to the above measures, all steel parts are
zinc-coated both sides.
Underbody Sealer
Underfloor areas and outer sill panels are treated with
a Plastisol PVC underbody sealer. This material is not
suitable for re-treatment.
When repairing areas of underbody sealer, strip the
factory-applied material back to a suitable break point,
ensuring that a clean metal surface is exposed and
that the edge of the existing material adheres soundly
to the panel.
Blanking plugs and grommets in the floor pan (except
those used for wax injection) MUST be fitted before
underbody sealer application. Heat-fusible plugs
which have been disturbed should either be refitted
with the aid of a hot air blower or replaced with rubber
grommets.
NOTE: Application of new underbody
sealer must be carried out between primer
and surfacer paint operations. Areas
where seam sealer is used should be re-treated as
necessary before application of underbody sealer.
CAUTION: Ensure that suspension units,
wheels, tyres, power unit, driveshafts,
exhaust and brakes (including all
mounting points) are shielded prior to application
of fresh underbody sealer.
Cavity Wax
Cavity wax is applied to certain box sctions The
information given on the following pages is intended
as a guide and shows the areas to be treated with
cavity wax, as well as the access holes used during
manufacture.See GENERAL INFORMATION DATA,
Sealing and corrosion protection section.
Underbody Wax
A coat of underbody wax is applied to the entire
underbody inboard of the sill vertical flanges, and
covers all moving and flexible components EXCEPT
for wheels and tyres, brakes and exhaust. The wax is
applied over paints and underbody sealers.
The underbody wax must be reinstated following all
repairs affecting floor panels.
CAUTION: Old underbody wax must be
completely removed from a zone
extending at least 200 mm (7.9 in) beyond
the area where new underbody sealer is to be
applied.
Engine Bay Wax
Reinstate protective engine bay wax disturbed during
repairs using the approved material.
Wheel Arch Wax
Reinstate protective wheel arch wax disturbed during
repairs using the approved material.
ProCarManuals.com
Page 534 of 667
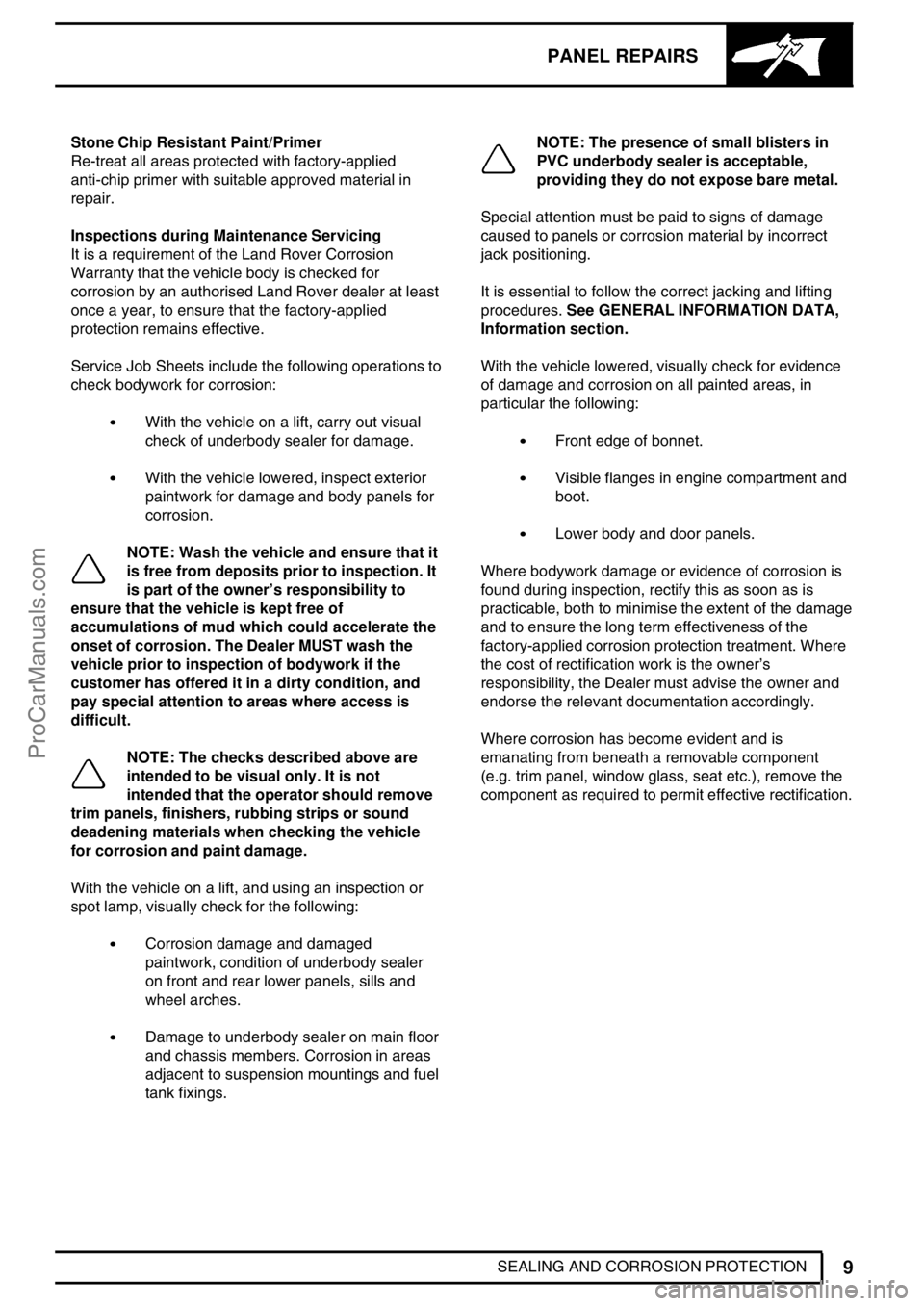
PANEL REPAIRS
9
SEALING AND CORROSION PROTECTION Stone Chip Resistant Paint/Primer
Re-treat all areas protected with factory-applied
anti-chip primer with suitable approved material in
repair.
Inspections during Maintenance Servicing
It is a requirement of the Land Rover Corrosion
Warranty that the vehicle body is checked for
corrosion by an authorised Land Rover dealer at least
once a year, to ensure that the factory-applied
protection remains effective.
Service Job Sheets include the following operations to
check bodywork for corrosion:
With the vehicle on a lift, carry out visual
check of underbody sealer for damage.
With the vehicle lowered, inspect exterior
paintwork for damage and body panels for
corrosion.
NOTE: Wash the vehicle and ensure that it
is free from deposits prior to inspection. It
is part of the owner’s responsibility to
ensure that the vehicle is kept free of
accumulations of mud which could accelerate the
onset of corrosion. The Dealer MUST wash the
vehicle prior to inspection of bodywork if the
customer has offered it in a dirty condition, and
pay special attention to areas where access is
difficult.
NOTE: The checks described above are
intended to be visual only. It is not
intended that the operator should remove
trim panels, finishers, rubbing strips or sound
deadening materials when checking the vehicle
for corrosion and paint damage.
With the vehicle on a lift, and using an inspection or
spot lamp, visually check for the following:
Corrosion damage and damaged
paintwork, condition of underbody sealer
on front and rear lower panels, sills and
wheel arches.
Damage to underbody sealer on main floor
and chassis members. Corrosion in areas
adjacent to suspension mountings and fuel
tank fixings.
NOTE: The presence of small blisters in
PVC underbody sealer is acceptable,
providing they do not expose bare metal.
Special attention must be paid to signs of damage
caused to panels or corrosion material by incorrect
jack positioning.
It is essential to follow the correct jacking and lifting
procedures.See GENERAL INFORMATION DATA,
Information section.
With the vehicle lowered, visually check for evidence
of damage and corrosion on all painted areas, in
particular the following:
Front edge of bonnet.
Visible flanges in engine compartment and
boot.
Lower body and door panels.
Where bodywork damage or evidence of corrosion is
found during inspection, rectify this as soon as is
practicable, both to minimise the extent of the damage
and to ensure the long term effectiveness of the
factory-applied corrosion protection treatment. Where
the cost of rectification work is the owner’s
responsibility, the Dealer must advise the owner and
endorse the relevant documentation accordingly.
Where corrosion has become evident and is
emanating from beneath a removable component
(e.g. trim panel, window glass, seat etc.), remove the
component as required to permit effective rectification.
ProCarManuals.com
Page 535 of 667
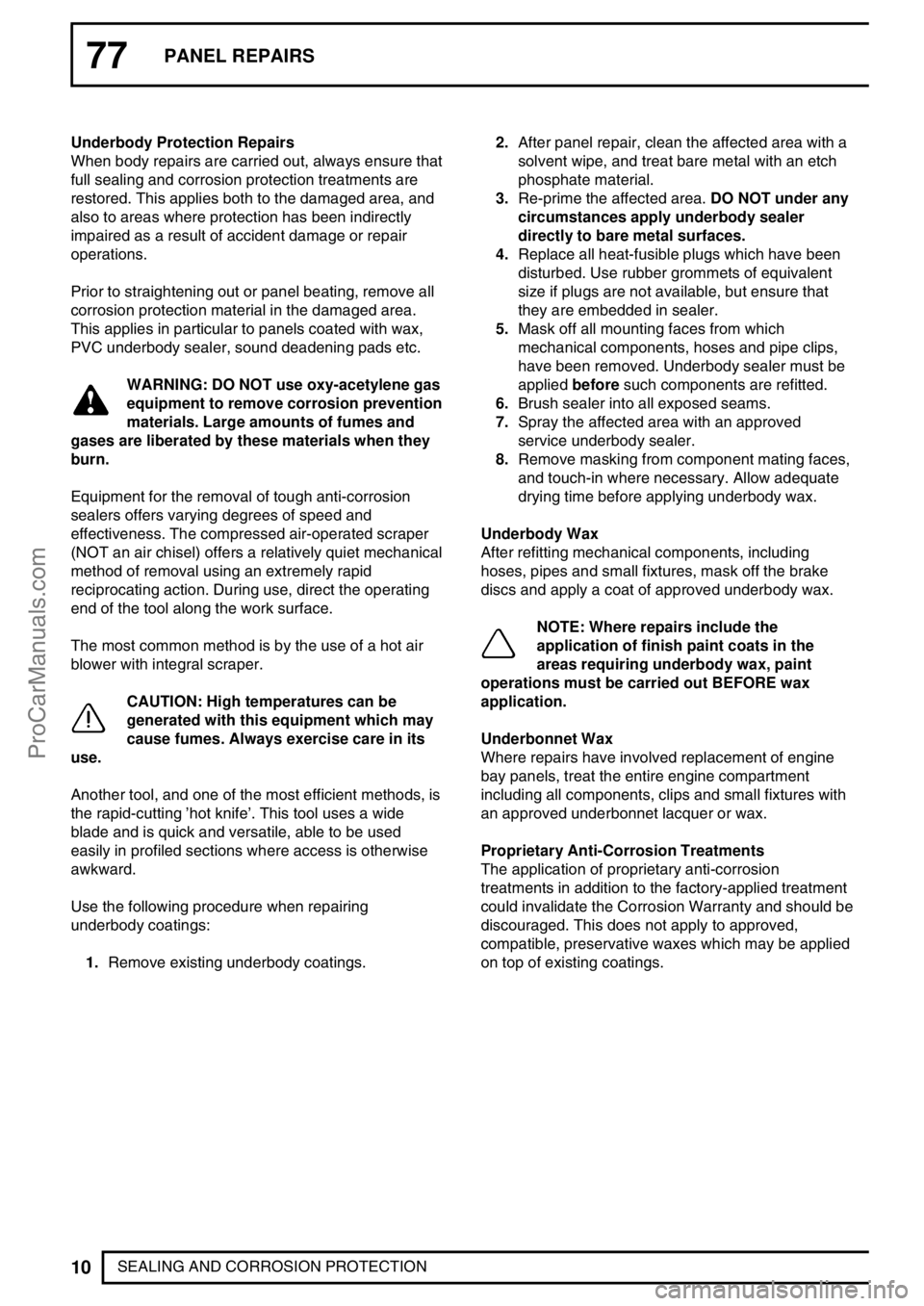
77PANEL REPAIRS
10
SEALING AND CORROSION PROTECTION Underbody Protection Repairs
When body repairs are carried out, always ensure that
full sealing and corrosion protection treatments are
restored. This applies both to the damaged area, and
also to areas where protection has been indirectly
impaired as a result of accident damage or repair
operations.
Prior to straightening out or panel beating, remove all
corrosion protection material in the damaged area.
This applies in particular to panels coated with wax,
PVC underbody sealer, sound deadening pads etc.
WARNING: DO NOT use oxy-acetylene gas
equipment to remove corrosion prevention
materials. Large amounts of fumes and
gases are liberated by these materials when they
burn.
Equipment for the removal of tough anti-corrosion
sealers offers varying degrees of speed and
effectiveness. The compressed air-operated scraper
(NOT an air chisel) offers a relatively quiet mechanical
method of removal using an extremely rapid
reciprocating action. During use, direct the operating
end of the tool along the work surface.
The most common method is by the use of a hot air
blower with integral scraper.
CAUTION: High temperatures can be
generated with this equipment which may
cause fumes. Always exercise care in its
use.
Another tool, and one of the most efficient methods, is
the rapid-cutting’hot knife’. This tool uses a wide
blade and is quick and versatile, able to be used
easily in profiled sections where access is otherwise
awkward.
Use the following procedure when repairing
underbody coatings:
1.Remove existing underbody coatings.2.After panel repair, clean the affected area with a
solvent wipe, and treat bare metal with an etch
phosphate material.
3.Re-prime the affected area.DO NOT under any
circumstances apply underbody sealer
directly to bare metal surfaces.
4.Replace all heat-fusible plugs which have been
disturbed. Use rubber grommets of equivalent
size if plugs are not available, but ensure that
they are embedded in sealer.
5.Mask off all mounting faces from which
mechanical components, hoses and pipe clips,
have been removed. Underbody sealer must be
appliedbeforesuch components are refitted.
6.Brush sealer into all exposed seams.
7.Spray the affected area with an approved
service underbody sealer.
8.Remove masking from component mating faces,
and touch-in where necessary. Allow adequate
drying time before applying underbody wax.
Underbody Wax
After refitting mechanical components, including
hoses, pipes and small fixtures, mask off the brake
discs and apply a coat of approved underbody wax.
NOTE: Where repairs include the
application of finish paint coats in the
areas requiring underbody wax, paint
operations must be carried out BEFORE wax
application.
Underbonnet Wax
Where repairs have involved replacement of engine
bay panels, treat the entire engine compartment
including all components, clips and small fixtures with
an approved underbonnet lacquer or wax.
Proprietary Anti-Corrosion Treatments
The application of proprietary anti-corrosion
treatments in addition to the factory-applied treatment
could invalidate the Corrosion Warranty and should be
discouraged. This does not apply to approved,
compatible, preservative waxes which may be applied
on top of existing coatings.
ProCarManuals.com
Page 585 of 667
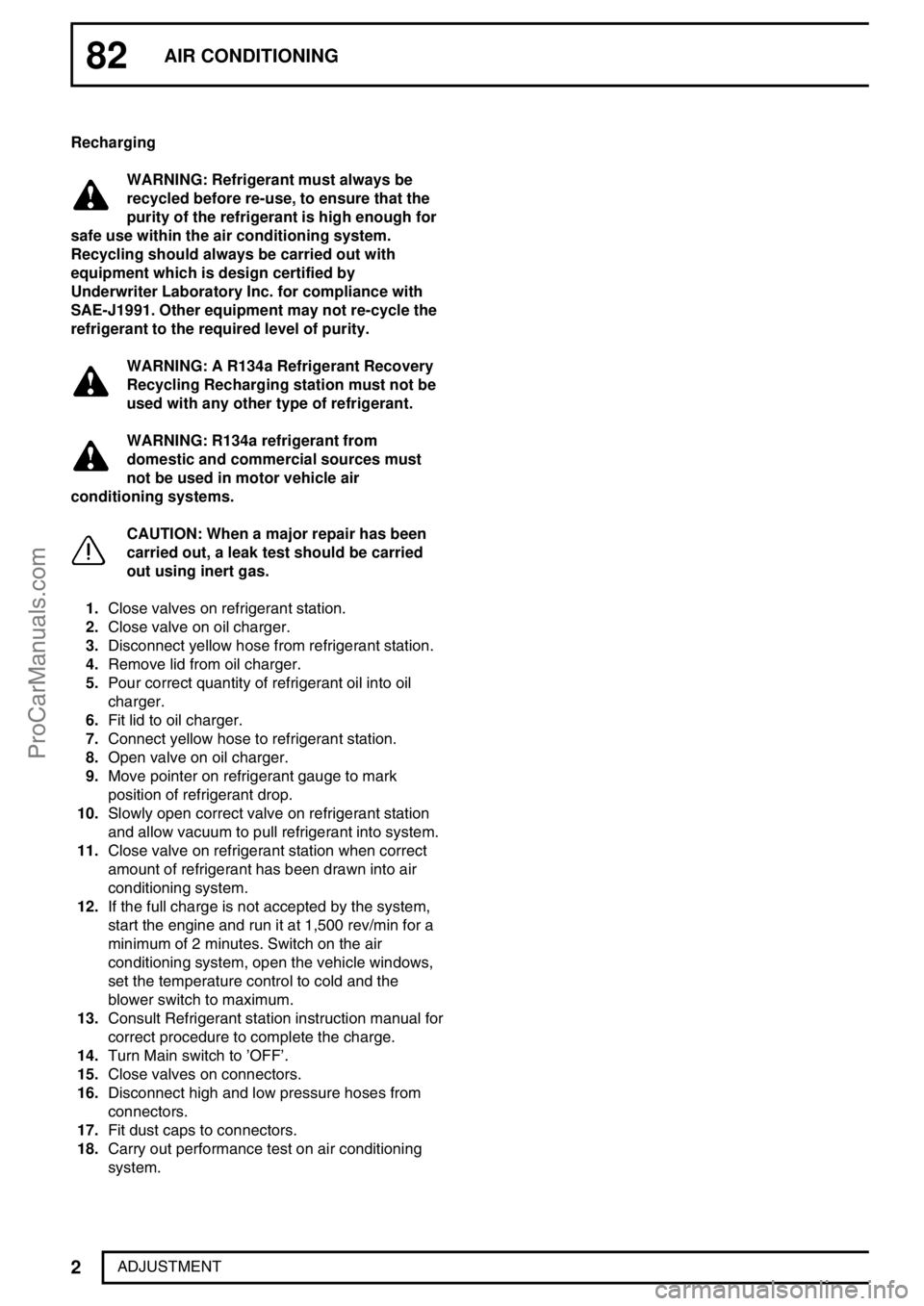
82AIR CONDITIONING
2
ADJUSTMENT Recharging
WARNING: Refrigerant must always be
recycled before re-use, to ensure that the
purity of the refrigerant is high enough for
safe use within the air conditioning system.
Recycling should always be carried out with
equipment which is design certified by
Underwriter Laboratory Inc. for compliance with
SAE-J1991. Other equipment may not re-cycle the
refrigerant to the required level of purity.
WARNING: A R134a Refrigerant Recovery
Recycling Recharging station must not be
used with any other type of refrigerant.
WARNING: R134a refrigerant from
domestic and commercial sources must
not be used in motor vehicle air
conditioning systems.
CAUTION: When a major repair has been
carried out, a leak test should be carried
out using inert gas.
1.Close valves on refrigerant station.
2.Close valve on oil charger.
3.Disconnect yellow hose from refrigerant station.
4.Remove lid from oil charger.
5.Pour correct quantity of refrigerant oil into oil
charger.
6.Fit lid to oil charger.
7.Connect yellow hose to refrigerant station.
8.Open valve on oil charger.
9.Move pointer on refrigerant gauge to mark
position of refrigerant drop.
10.Slowly open correct valve on refrigerant station
and allow vacuum to pull refrigerant into system.
11.Close valve on refrigerant station when correct
amount of refrigerant has been drawn into air
conditioning system.
12.If the full charge is not accepted by the system,
start the engine and run it at 1,500 rev/min for a
minimum of 2 minutes. Switch on the air
conditioning system, open the vehicle windows,
set the temperature control to cold and the
blower switch to maximum.
13.Consult Refrigerant station instruction manual for
correct procedure to complete the charge.
14.Turn Main switch to’OFF’.
15.Close valves on connectors.
16.Disconnect high and low pressure hoses from
connectors.
17.Fit dust caps to connectors.
18.Carry out performance test on air conditioning
system.
ProCarManuals.com
Page 586 of 667
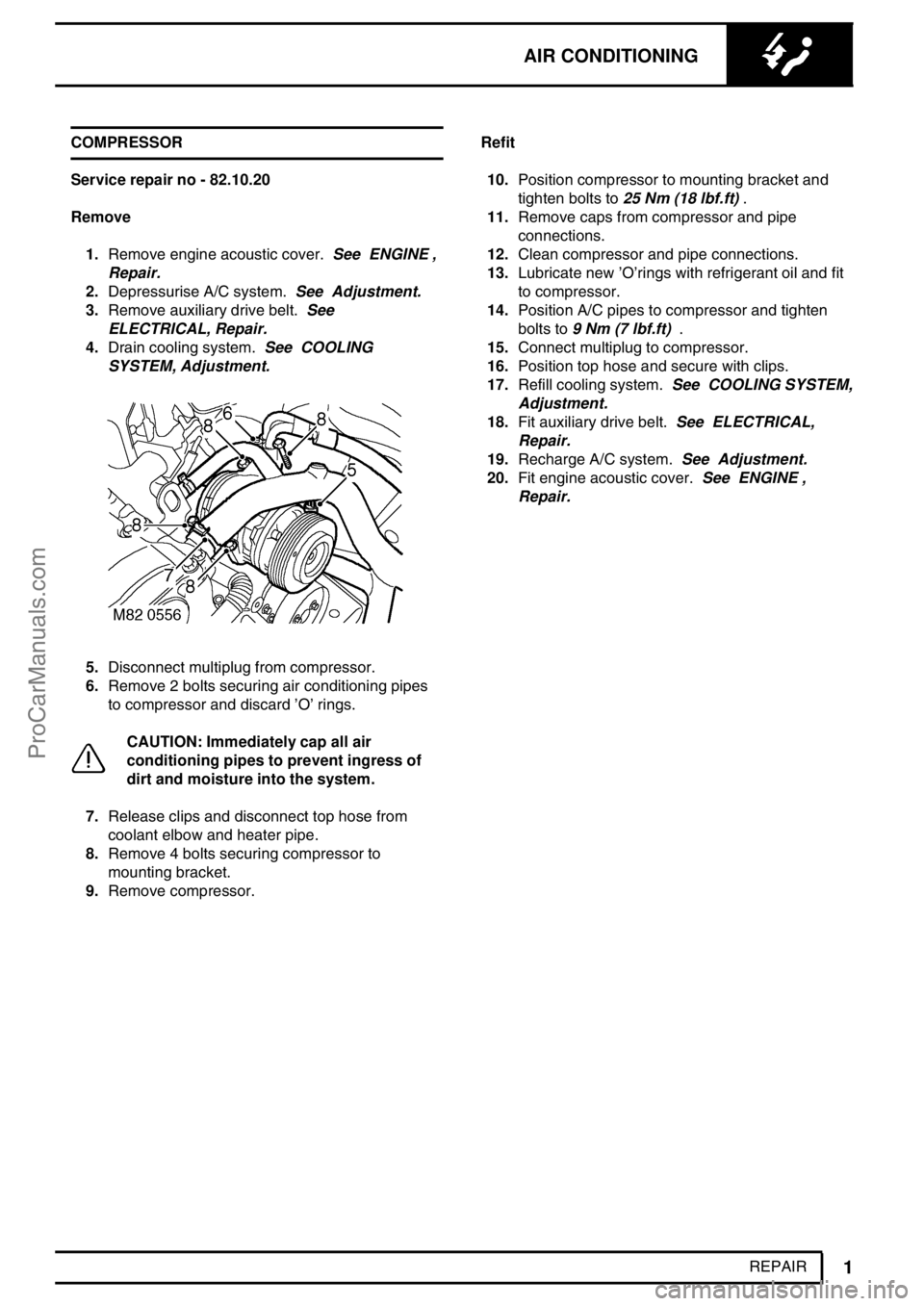
AIR CONDITIONING
1
REPAIR COMPRESSOR
Service repair no - 82.10.20
Remove
1.Remove engine acoustic cover.See ENGINE ,
Repair.
2.Depressurise A/C system.See Adjustment.
3.Remove auxiliary drive belt.See
ELECTRICAL, Repair.
4.Drain cooling system.See COOLING
SYSTEM, Adjustment.
5.Disconnect multiplug from compressor.
6.Remove 2 bolts securing air conditioning pipes
to compressor and discard’O’rings.
CAUTION: Immediately cap all air
conditioning pipes to prevent ingress of
dirt and moisture into the system.
7.Release clips and disconnect top hose from
coolant elbow and heater pipe.
8.Remove 4 bolts securing compressor to
mounting bracket.
9.Remove compressor.Refit
10.Position compressor to mounting bracket and
tighten bolts to25 Nm (18 lbf.ft).
11.Remove caps from compressor and pipe
connections.
12.Clean compressor and pipe connections.
13.Lubricate new’O’rings with refrigerant oil and fit
to compressor.
14.Position A/C pipes to compressor and tighten
bolts to9 Nm (7 lbf.ft).
15.Connect multiplug to compressor.
16.Position top hose and secure with clips.
17.Refill cooling system.See COOLING SYSTEM,
Adjustment.
18.Fit auxiliary drive belt.See ELECTRICAL,
Repair.
19.Recharge A/C system.See Adjustment.
20.Fit engine acoustic cover.See ENGINE ,
Repair.
ProCarManuals.com
Page 610 of 667
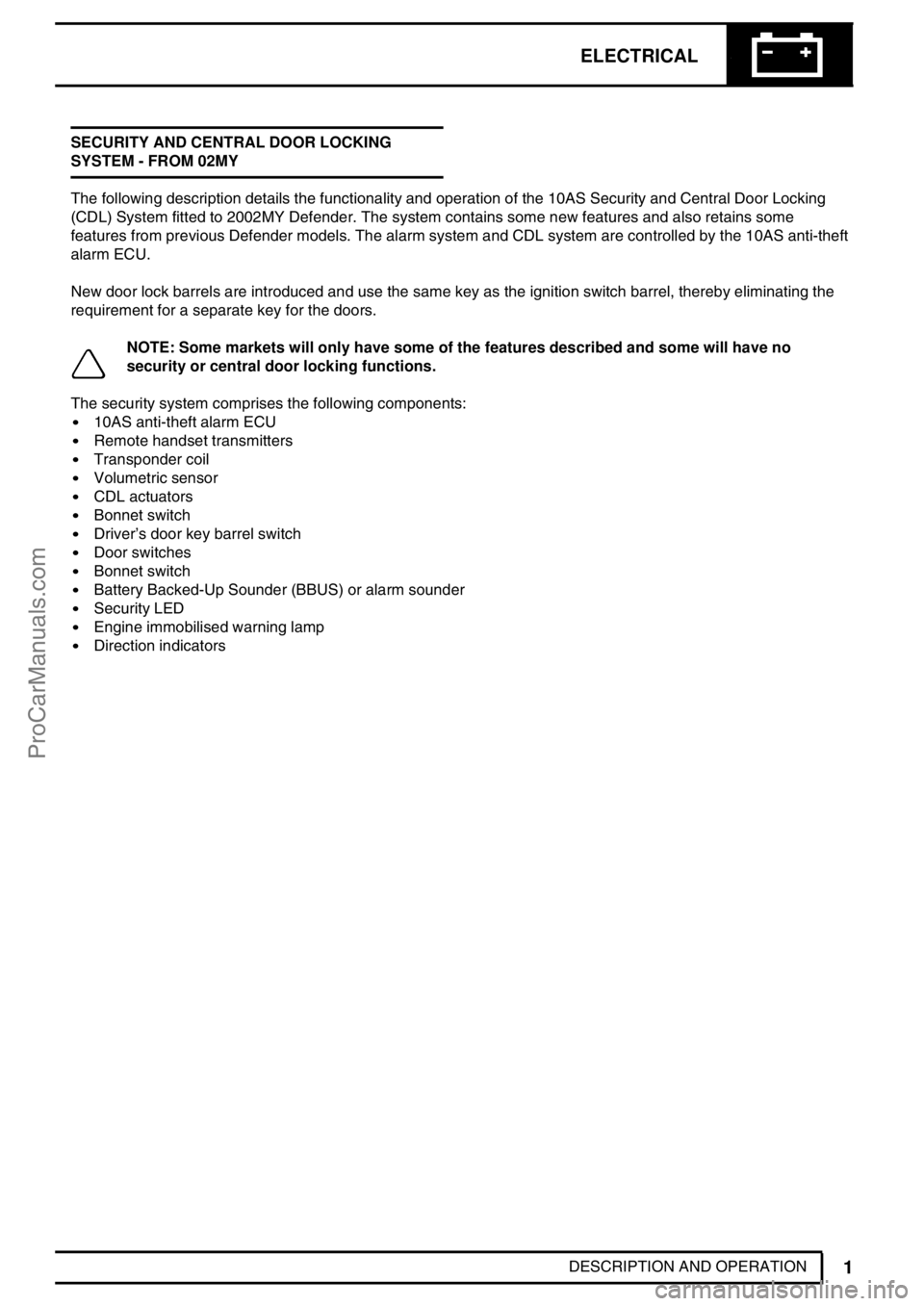
ELECTRICAL
1
DESCRIPTION AND OPERATION SECURITY AND CENTRAL DOOR LOCKING
SYSTEM - FROM 02MY
The following description details the functionality and operation of the 10AS Security and Central Door Locking
(CDL) System fitted to 2002MY Defender. The system contains some new features and also retains some
features from previous Defender models. The alarm system and CDL system are controlled by the 10AS anti-theft
alarm ECU.
New door lock barrels are introduced and use the same key as the ignition switch barrel, thereby eliminating the
requirement for a separate key for the doors.
NOTE: Some markets will only have some of the features described and some will have no
security or central door locking functions.
The security system comprises the following components:
10AS anti-theft alarm ECU
Remote handset transmitters
Transponder coil
Volumetric sensor
CDL actuators
Bonnet switch
Driver’s door key barrel switch
Door switches
Bonnet switch
Battery Backed-Up Sounder (BBUS) or alarm sounder
Security LED
Engine immobilised warning lamp
Direction indicators
ProCarManuals.com
Page 611 of 667
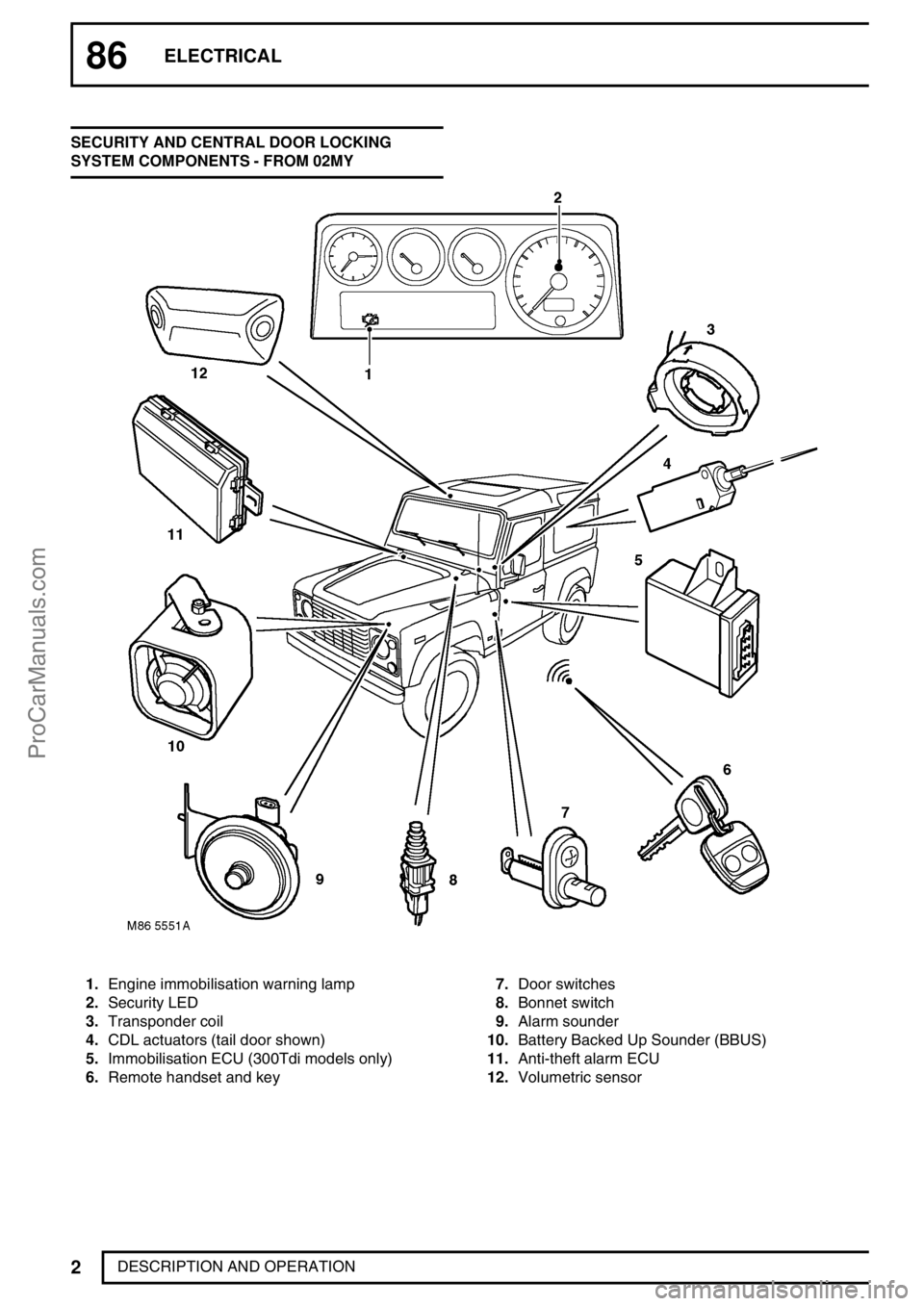
86ELECTRICAL
2
DESCRIPTION AND OPERATION SECURITY AND CENTRAL DOOR LOCKING
SYSTEM COMPONENTS - FROM 02MY
1.Engine immobilisation warning lamp
2.Security LED
3.Transponder coil
4.CDL actuators (tail door shown)
5.Immobilisation ECU (300Tdi models only)
6.Remote handset and key7.Door switches
8.Bonnet switch
9.Alarm sounder
10.Battery Backed Up Sounder (BBUS)
11.Anti-theft alarm ECU
12.Volumetric sensor
ProCarManuals.com
Page 612 of 667
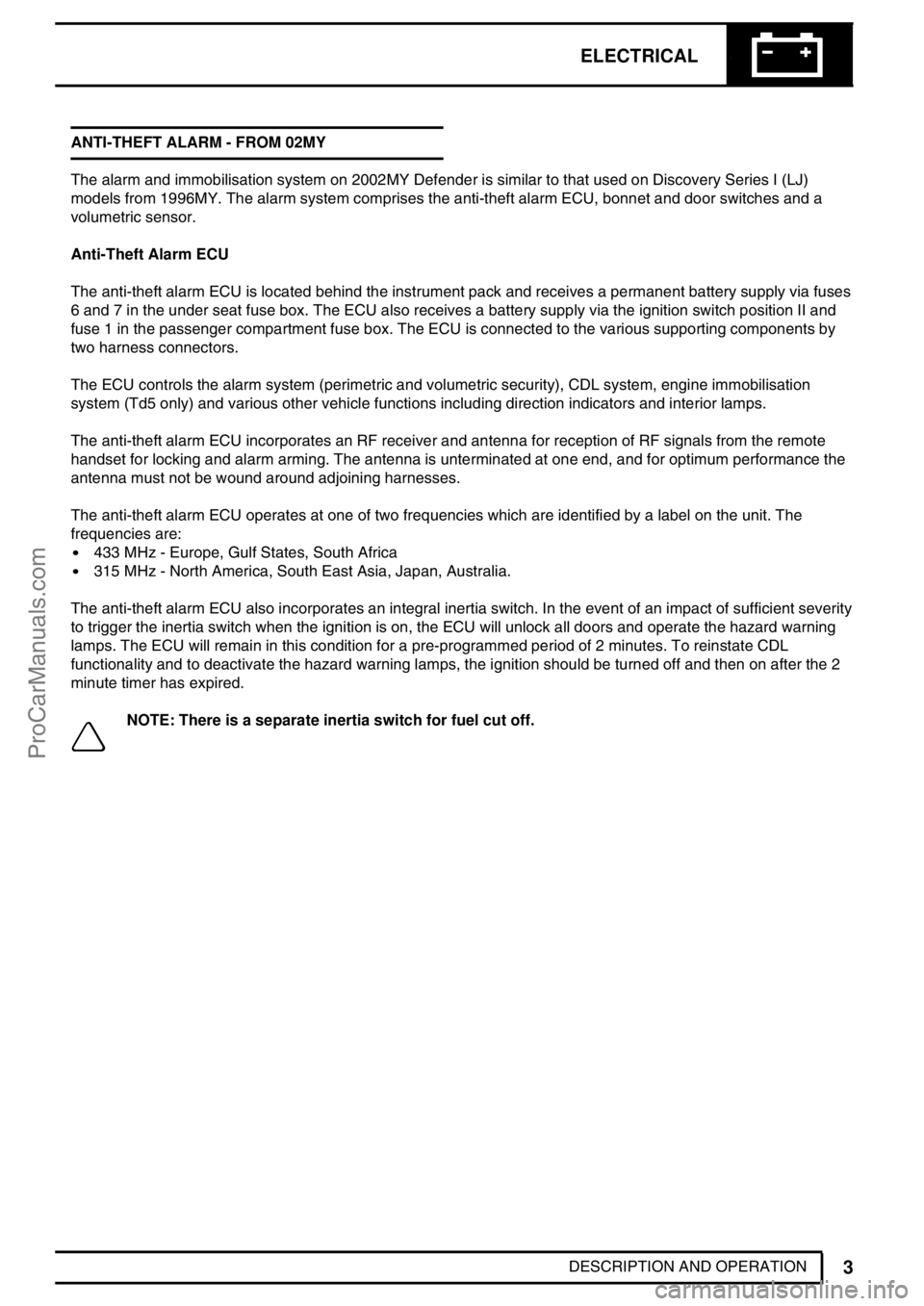
ELECTRICAL
3
DESCRIPTION AND OPERATION ANTI-THEFT ALARM - FROM 02MY
The alarm and immobilisation system on 2002MY Defender is similar to that used on Discovery Series I (LJ)
models from 1996MY. The alarm system comprises the anti-theft alarm ECU, bonnet and door switches and a
volumetric sensor.
Anti-Theft Alarm ECU
The anti-theft alarm ECU is located behind the instrument pack and receives a permanent battery supply via fuses
6 and 7 in the under seat fuse box. The ECU also receives a battery supply via the ignition switch position II and
fuse 1 in the passenger compartment fuse box. The ECU is connected to the various supporting components by
two harness connectors.
The ECU controls the alarm system (perimetric and volumetric security), CDL system, engine immobilisation
system (Td5 only) and various other vehicle functions including direction indicators and interior lamps.
The anti-theft alarm ECU incorporates an RF receiver and antenna for reception of RF signals from the remote
handset for locking and alarm arming. The antenna is unterminated at one end, and for optimum performance the
antenna must not be wound around adjoining harnesses.
The anti-theft alarm ECU operates at one of two frequencies which are identified by a label on the unit. The
frequencies are:
433 MHz - Europe, Gulf States, South Africa
315 MHz - North America, South East Asia, Japan, Australia.
The anti-theft alarm ECU also incorporates an integral inertia switch. In the event of an impact of sufficient severity
to trigger the inertia switch when the ignition is on, the ECU will unlock all doors and operate the hazard warning
lamps. The ECU will remain in this condition for a pre-programmed period of 2 minutes. To reinstate CDL
functionality and to deactivate the hazard warning lamps, the ignition should be turned off and then on after the 2
minute timer has expired.
NOTE: There is a separate inertia switch for fuel cut off.
ProCarManuals.com
Page 621 of 667
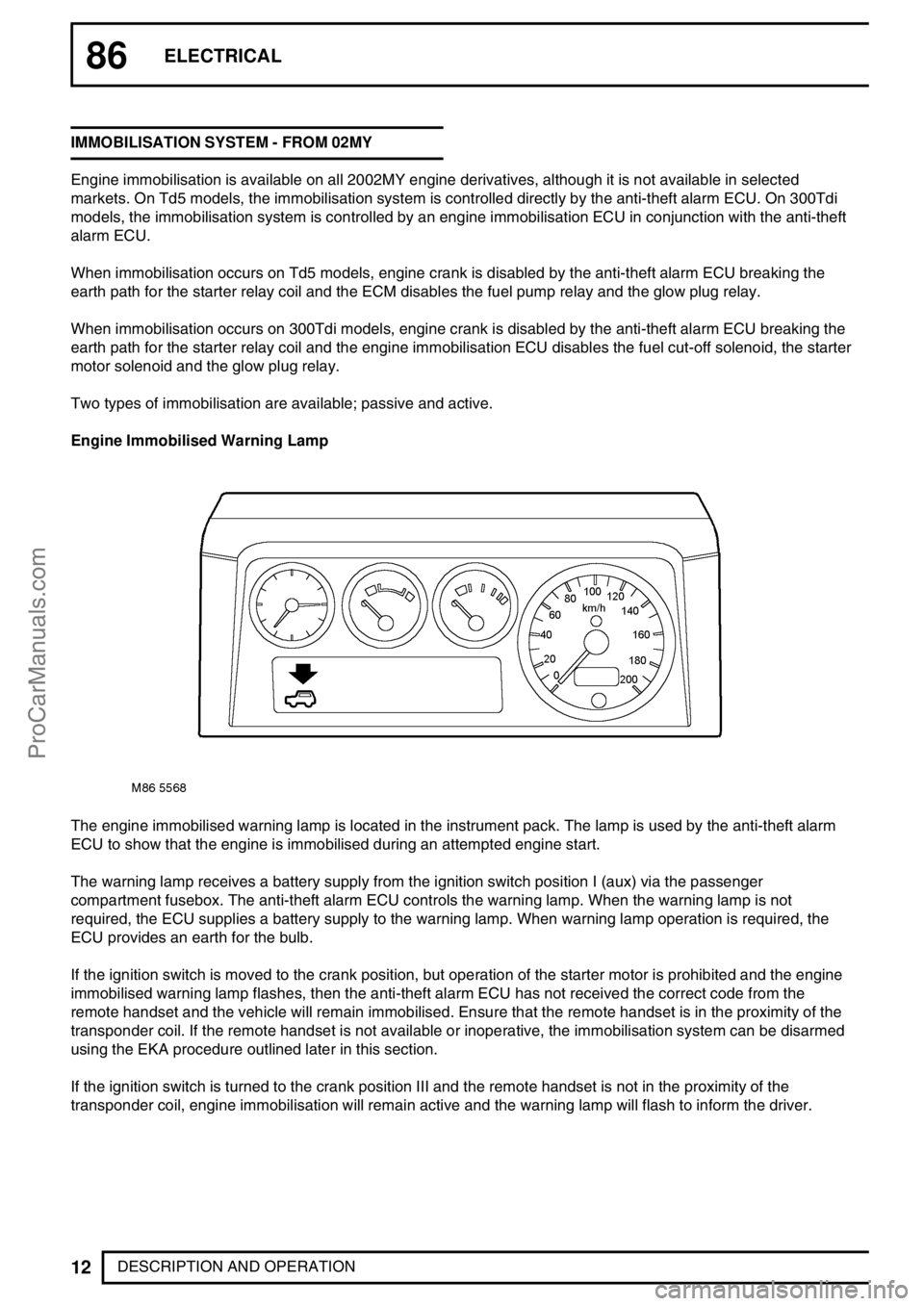
86ELECTRICAL
12
DESCRIPTION AND OPERATION IMMOBILISATION SYSTEM - FROM 02MY
Engine immobilisation is available on all 2002MY engine derivatives, although it is not available in selected
markets. On Td5 models, the immobilisation system is controlled directly by the anti-theft alarm ECU. On 300Tdi
models, the immobilisation system is controlled by an engine immobilisation ECU in conjunction with the anti-theft
alarm ECU.
When immobilisation occurs on Td5 models, engine crank is disabled by the anti-theft alarm ECU breaking the
earth path for the starter relay coil and the ECM disables the fuel pump relay and the glow plug relay.
When immobilisation occurs on 300Tdi models, engine crank is disabled by the anti-theft alarm ECU breaking the
earth path for the starter relay coil and the engine immobilisation ECU disables the fuel cut-off solenoid, the starter
motor solenoid and the glow plug relay.
Two types of immobilisation are available; passive and active.
Engine Immobilised Warning Lamp
The engine immobilised warning lamp is located in the instrument pack. The lamp is used by the anti-theft alarm
ECU to show that the engine is immobilised during an attempted engine start.
The warning lamp receives a battery supply from the ignition switch position I (aux) via the passenger
compartment fusebox. The anti-theft alarm ECU controls the warning lamp. When the warning lamp is not
required, the ECU supplies a battery supply to the warning lamp. When warning lamp operation is required, the
ECU provides an earth for the bulb.
If the ignition switch is moved to the crank position, but operation of the starter motor is prohibited and the engine
immobilised warning lamp flashes, then the anti-theft alarm ECU has not received the correct code from the
remote handset and the vehicle will remain immobilised. Ensure that the remote handset is in the proximity of the
transponder coil. If the remote handset is not available or inoperative, the immobilisation system can be disarmed
using the EKA procedure outlined later in this section.
If the ignition switch is turned to the crank position III and the remote handset is not in the proximity of the
transponder coil, engine immobilisation will remain active and the warning lamp will flash to inform the driver.
ProCarManuals.com