fuel type LAND ROVER DEFENDER 1999 Workshop Manual
[x] Cancel search | Manufacturer: LAND ROVER, Model Year: 1999, Model line: DEFENDER, Model: LAND ROVER DEFENDER 1999Pages: 667, PDF Size: 8.76 MB
Page 26 of 667
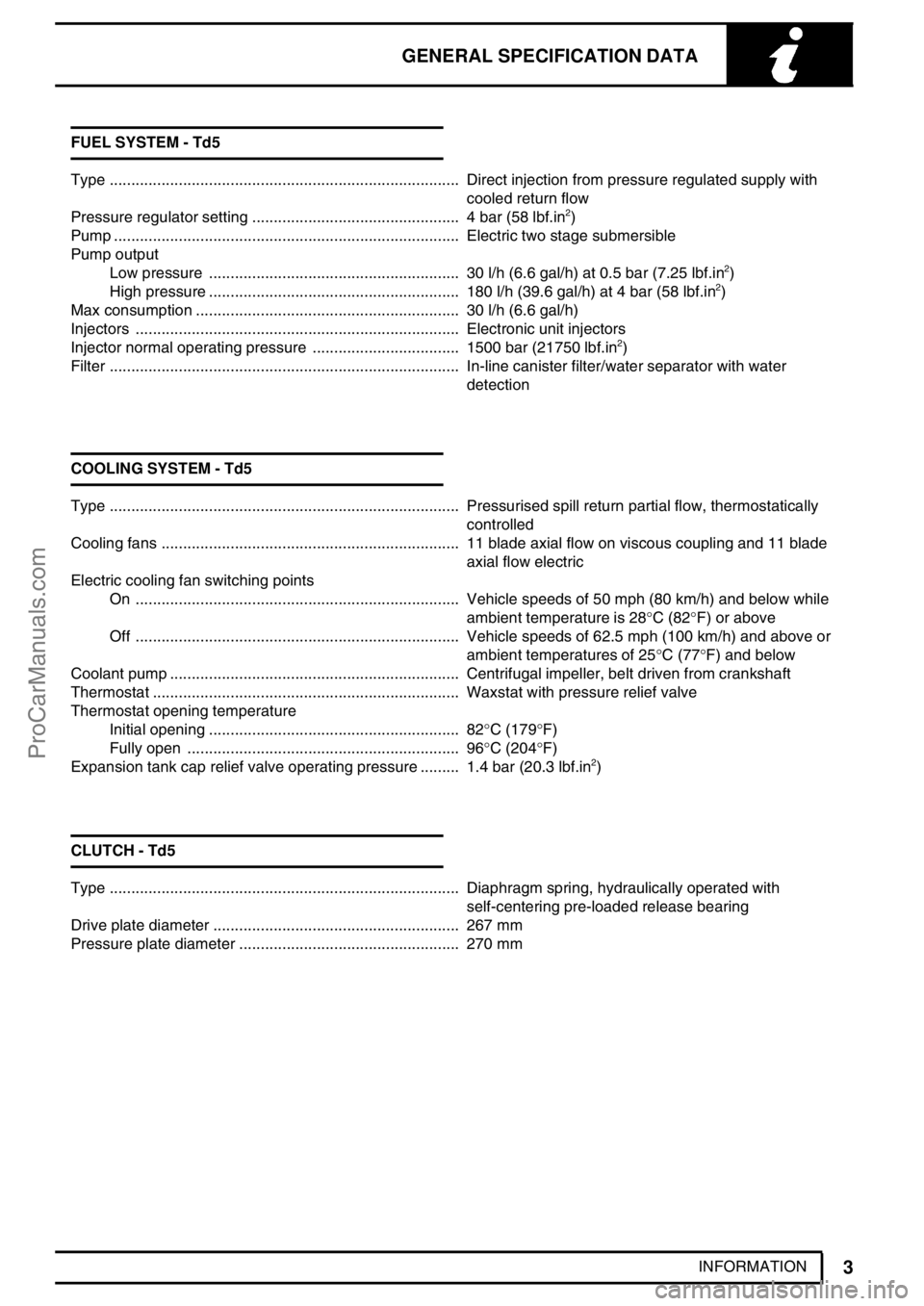
GENERAL SPECIFICATION DATA
3
INFORMATION FUEL SYSTEM - Td5
Type Direct injection from pressure regulated supply with.................................................................................
cooled return flow
Pressure regulator setting 4 bar (58 lbf.in
2) ................................................
Pump Electric two stage submersible................................................................................
Pump output
Low pressure 30 l/h (6.6 gal/h) at 0.5 bar (7.25 lbf.in
2) ..........................................................
High pressure 180 l/h (39.6 gal/h) at 4 bar (58 lbf.in2) ..........................................................
Max consumption 30 l/h (6.6 gal/h).............................................................
Injectors Electronic unit injectors...........................................................................
Injector normal operating pressure 1500 bar (21750 lbf.in
2) ..................................
Filter In-line canister filter/water separator with water.................................................................................
detection
COOLING SYSTEM - Td5
Type Pressurised spill return partial flow, thermostatically.................................................................................
controlled
Cooling fans 11 blade axial flow on viscous coupling and 11 blade.....................................................................
axial flow electric
Electric cooling fan switching points
On Vehicle speeds of 50 mph (80 km/h) and below while...........................................................................
ambient temperature is 28°C (82°F) or above
Off Vehicle speeds of 62.5 mph (100 km/h) and above or...........................................................................
ambient temperatures of 25°C (77°F) and below
Coolant pump Centrifugal impeller, belt driven from crankshaft...................................................................
Thermostat Waxstat with pressure relief valve.......................................................................
Thermostat opening temperature
Initial opening 82°C (179°F) ..........................................................
Fully open 96°C (204°F) ...............................................................
Expansion tank cap relief valve operating pressure 1.4 bar (20.3 lbf.in
2) .........
CLUTCH - Td5
Type Diaphragm spring, hydraulically operated with.................................................................................
self-centering pre-loaded release bearing
Drive plate diameter 267 mm.........................................................
Pressure plate diameter 270 mm...................................................
ProCarManuals.com
Page 28 of 667
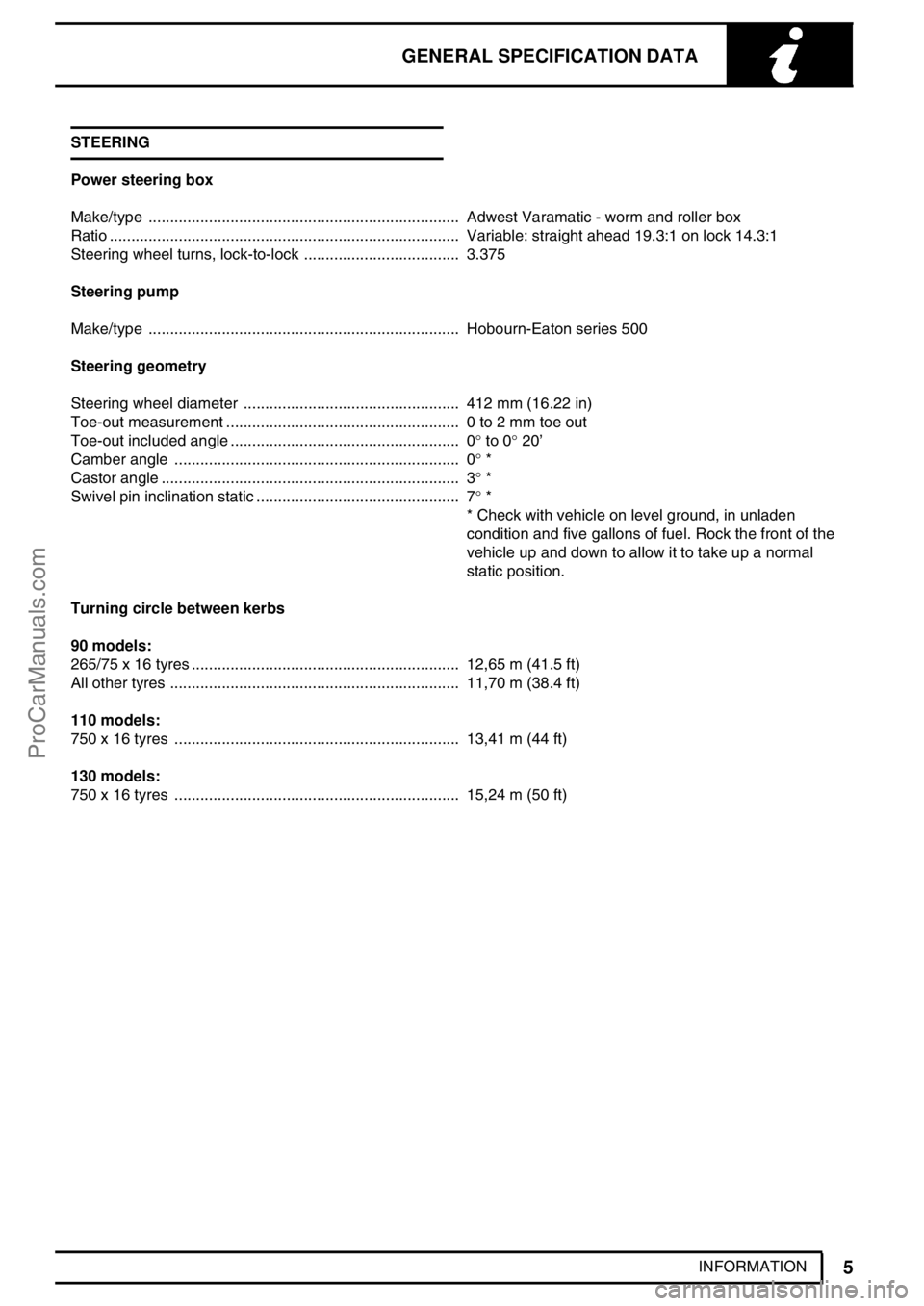
GENERAL SPECIFICATION DATA
5
INFORMATION STEERING
Power steering box
Make/type Adwest Varamatic - worm and roller box........................................................................
Ratio Variable: straight ahead 19.3:1 on lock 14.3:1.................................................................................
Steering wheel turns, lock-to-lock 3.375....................................
Steering pump
Make/type Hobourn-Eaton series 500........................................................................
Steering geometry
Steering wheel diameter 412 mm (16.22 in)..................................................
Toe-out measurement 0 to 2 mm toe out......................................................
Toe-out included angle 0°to 0°20’ .....................................................
Camber angle 0°* ..................................................................
Castor angle 3°* .....................................................................
Swivel pin inclination static 7°* ...............................................
* Check with vehicle on level ground, in unladen
condition and five gallons of fuel. Rock the front of the
vehicle up and down to allow it to take up a normal
static position.
Turning circle between kerbs
90 models:
265/75 x 16 tyres 12,65 m (41.5 ft)..............................................................
All other tyres 11,70 m (38.4 ft)...................................................................
110 models:
750 x 16 tyres 13,41 m (44 ft)..................................................................
130 models:
750 x 16 tyres 15,24 m (50 ft)..................................................................
ProCarManuals.com
Page 45 of 667
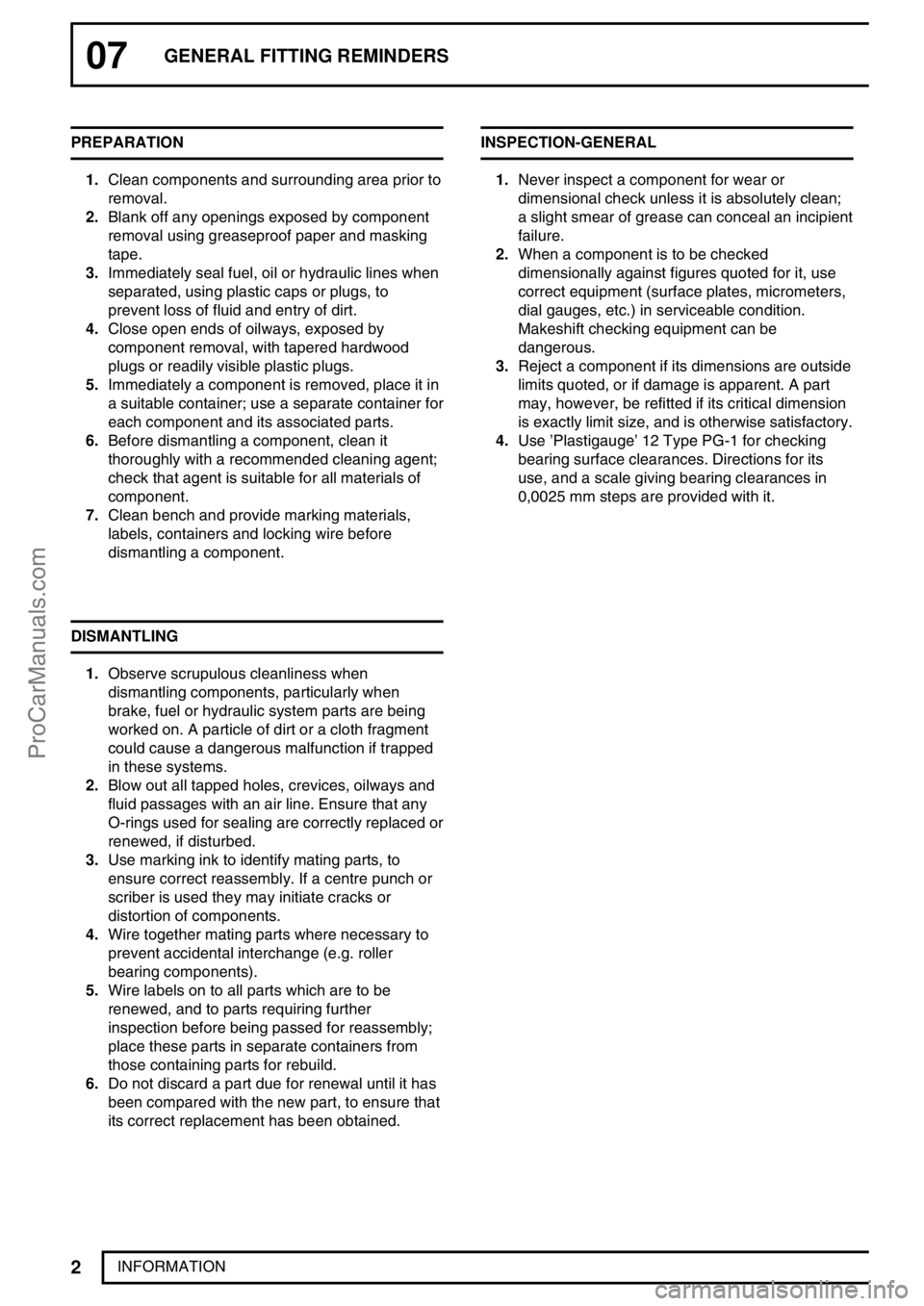
07GENERAL FITTING REMINDERS
2
INFORMATION PREPARATION
1.Clean components and surrounding area prior to
removal.
2.Blank off any openings exposed by component
removal using greaseproof paper and masking
tape.
3.Immediately seal fuel, oil or hydraulic lines when
separated, using plastic caps or plugs, to
prevent loss of fluid and entry of dirt.
4.Close open ends of oilways, exposed by
component removal, with tapered hardwood
plugs or readily visible plastic plugs.
5.Immediately a component is removed, place it in
a suitable container; use a separate container for
each component and its associated parts.
6.Before dismantling a component, clean it
thoroughly with a recommended cleaning agent;
check that agent is suitable for all materials of
component.
7.Clean bench and provide marking materials,
labels, containers and locking wire before
dismantling a component.
DISMANTLING
1.Observe scrupulous cleanliness when
dismantling components, particularly when
brake, fuel or hydraulic system parts are being
worked on. A particle of dirt or a cloth fragment
could cause a dangerous malfunction if trapped
in these systems.
2.Blow out all tapped holes, crevices, oilways and
fluid passages with an air line. Ensure that any
O-rings used for sealing are correctly replaced or
renewed, if disturbed.
3.Use marking ink to identify mating parts, to
ensure correct reassembly. If a centre punch or
scriber is used they may initiate cracks or
distortion of components.
4.Wire together mating parts where necessary to
prevent accidental interchange (e.g. roller
bearing components).
5.Wire labels on to all parts which are to be
renewed, and to parts requiring further
inspection before being passed for reassembly;
place these parts in separate containers from
those containing parts for rebuild.
6.Do not discard a part due for renewal until it has
been compared with the new part, to ensure that
its correct replacement has been obtained.INSPECTION-GENERAL
1.Never inspect a component for wear or
dimensional check unless it is absolutely clean;
a slight smear of grease can conceal an incipient
failure.
2.When a component is to be checked
dimensionally against figures quoted for it, use
correct equipment (surface plates, micrometers,
dial gauges, etc.) in serviceable condition.
Makeshift checking equipment can be
dangerous.
3.Reject a component if its dimensions are outside
limits quoted, or if damage is apparent. A part
may, however, be refitted if its critical dimension
is exactly limit size, and is otherwise satisfactory.
4.Use’Plastigauge’12 Type PG-1 for checking
bearing surface clearances. Directions for its
use, and a scale giving bearing clearances in
0,0025 mm steps are provided with it.
ProCarManuals.com
Page 111 of 667
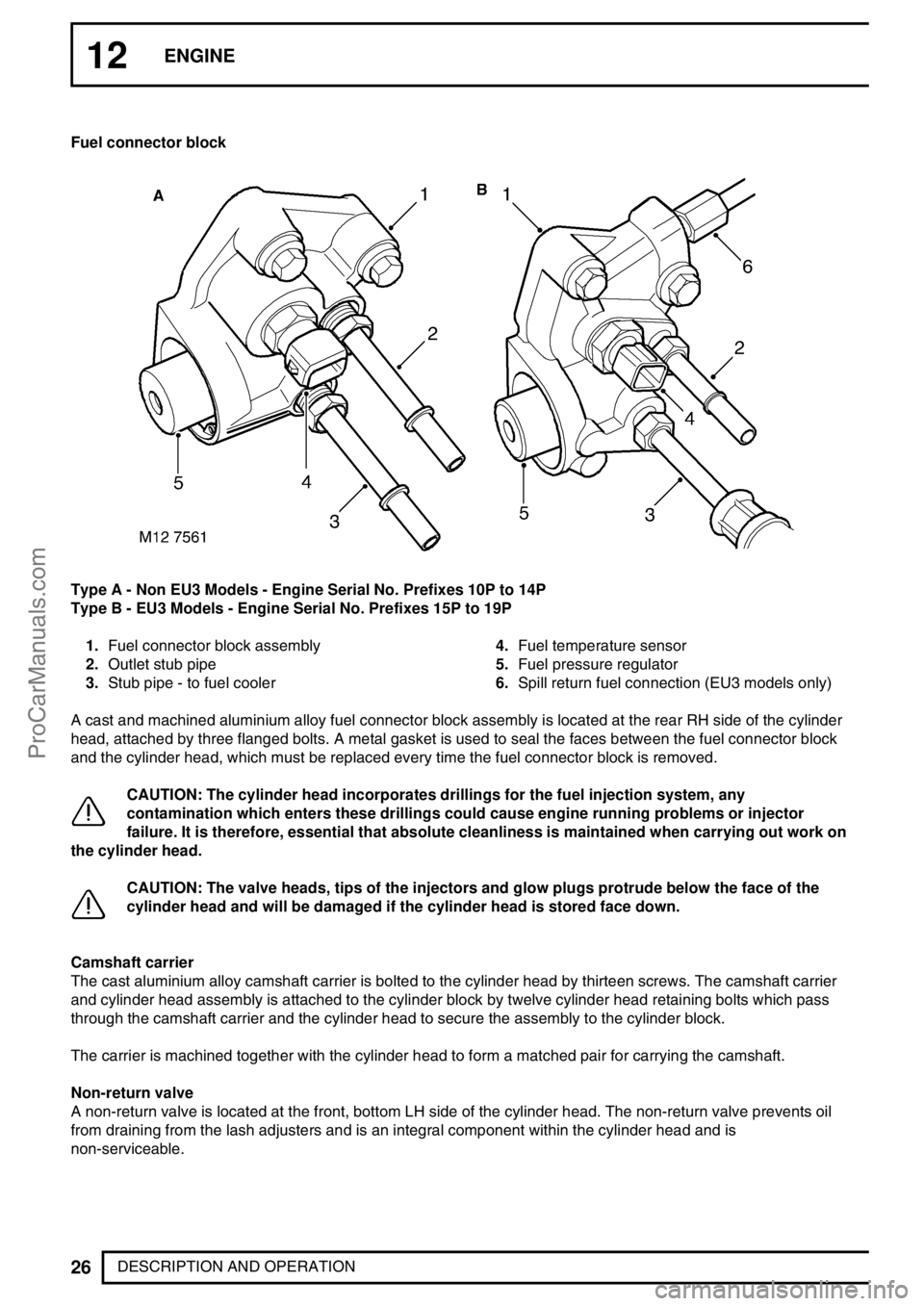
12ENGINE
26
DESCRIPTION AND OPERATION Fuel connector block
Type A - Non EU3 Models - Engine Serial No. Prefixes 10P to 14P
Type B - EU3 Models - Engine Serial No. Prefixes 15P to 19P
1.Fuel connector block assembly
2.Outlet stub pipe
3.Stub pipe - to fuel cooler4.Fuel temperature sensor
5.Fuel pressure regulator
6.Spill return fuel connection (EU3 models only)
A cast and machined aluminium alloy fuel connector block assembly is located at the rear RH side of the cylinder
head, attached by three flanged bolts. A metal gasket is used to seal the faces between the fuel connector block
and the cylinder head, which must be replaced every time the fuel connector block is removed.
CAUTION: The cylinder head incorporates drillings for the fuel injection system, any
contamination which enters these drillings could cause engine running problems or injector
failure. It is therefore, essential that absolute cleanliness is maintained when carrying out work on
the cylinder head.
CAUTION: The valve heads, tips of the injectors and glow plugs protrude below the face of the
cylinder head and will be damaged if the cylinder head is stored face down.
Camshaft carrier
The cast aluminium alloy camshaft carrier is bolted to the cylinder head by thirteen screws. The camshaft carrier
and cylinder head assembly is attached to the cylinder block by twelve cylinder head retaining bolts which pass
through the camshaft carrier and the cylinder head to secure the assembly to the cylinder block.
The carrier is machined together with the cylinder head to form a matched pair for carrying the camshaft.
Non-return valve
A non-return valve is located at the front, bottom LH side of the cylinder head. The non-return valve prevents oil
from draining from the lash adjusters and is an integral component within the cylinder head and is
non-serviceable.
ProCarManuals.com
Page 112 of 667
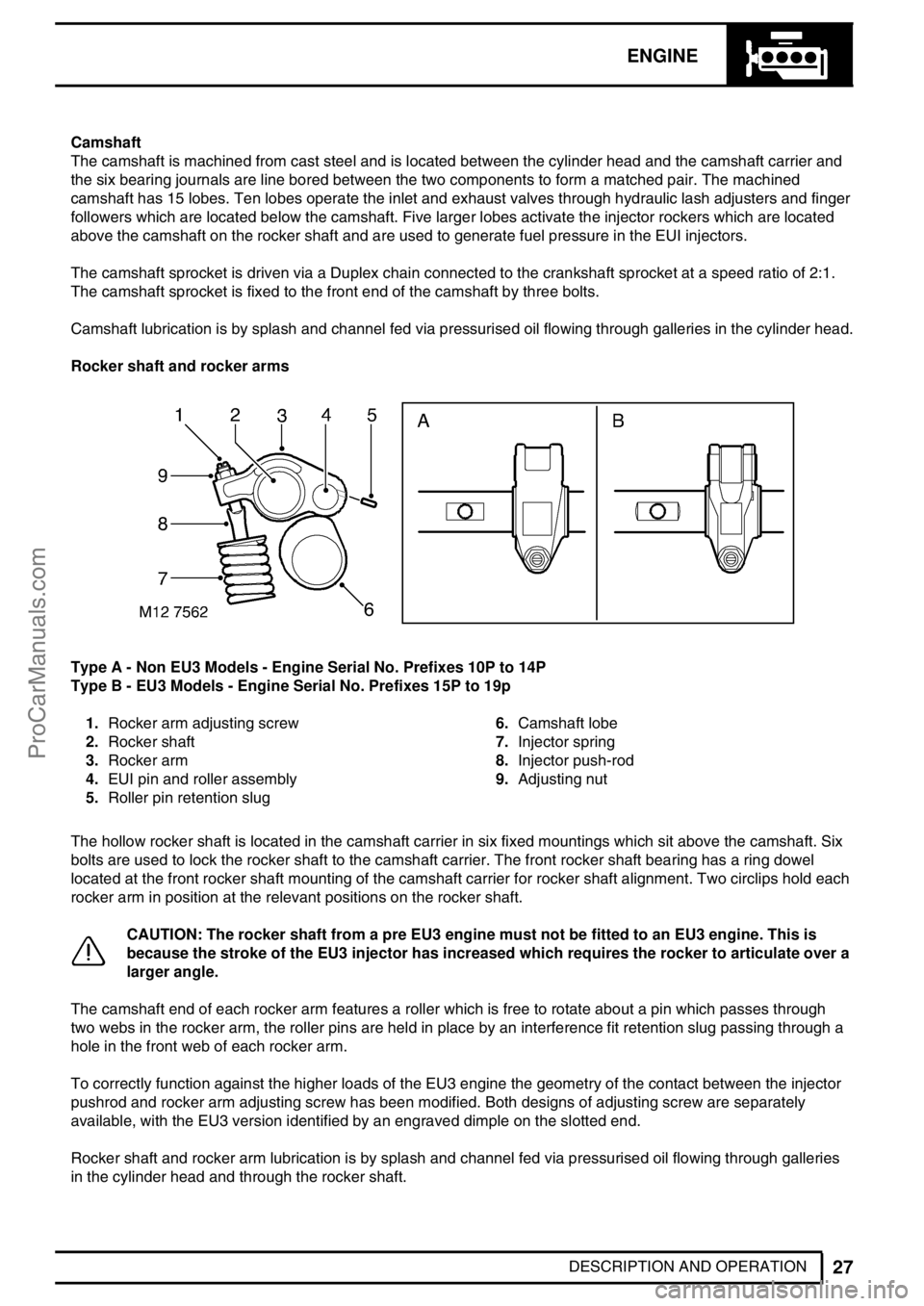
ENGINE
27
DESCRIPTION AND OPERATION Camshaft
The camshaft is machined from cast steel and is located between the cylinder head and the camshaft carrier and
the six bearing journals are line bored between the two components to form a matched pair. The machined
camshaft has 15 lobes. Ten lobes operate the inlet and exhaust valves through hydraulic lash adjusters and finger
followers which are located below the camshaft. Five larger lobes activate the injector rockers which are located
above the camshaft on the rocker shaft and are used to generate fuel pressure in the EUI injectors.
The camshaft sprocket is driven via a Duplex chain connected to the crankshaft sprocket at a speed ratio of 2:1.
The camshaft sprocket is fixed to the front end of the camshaft by three bolts.
Camshaft lubrication is by splash and channel fed via pressurised oil flowing through galleries in the cylinder head.
Rocker shaft and rocker arms
Type A - Non EU3 Models - Engine Serial No. Prefixes 10P to 14P
Type B - EU3 Models - Engine Serial No. Prefixes 15P to 19p
1.Rocker arm adjusting screw
2.Rocker shaft
3.Rocker arm
4.EUI pin and roller assembly
5.Roller pin retention slug6.Camshaft lobe
7.Injector spring
8.Injector push-rod
9.Adjusting nut
The hollow rocker shaft is located in the camshaft carrier in six fixed mountings which sit above the camshaft. Six
bolts are used to lock the rocker shaft to the camshaft carrier. The front rocker shaft bearing has a ring dowel
located at the front rocker shaft mounting of the camshaft carrier for rocker shaft alignment. Two circlips hold each
rocker arm in position at the relevant positions on the rocker shaft.
CAUTION: The rocker shaft from a pre EU3 engine must not be fitted to an EU3 engine. This is
because the stroke of the EU3 injector has increased which requires the rocker to articulate over a
larger angle.
The camshaft end of each rocker arm features a roller which is free to rotate about a pin which passes through
two webs in the rocker arm, the roller pins are held in place by an interference fit retention slug passing through a
hole in the front web of each rocker arm.
To correctly function against the higher loads of the EU3 engine the geometry of the contact between the injector
pushrod and rocker arm adjusting screw has been modified. Both designs of adjusting screw are separately
available, with the EU3 version identified by an engraved dimple on the slotted end.
Rocker shaft and rocker arm lubrication is by splash and channel fed via pressurised oil flowing through galleries
in the cylinder head and through the rocker shaft.
ProCarManuals.com
Page 238 of 667
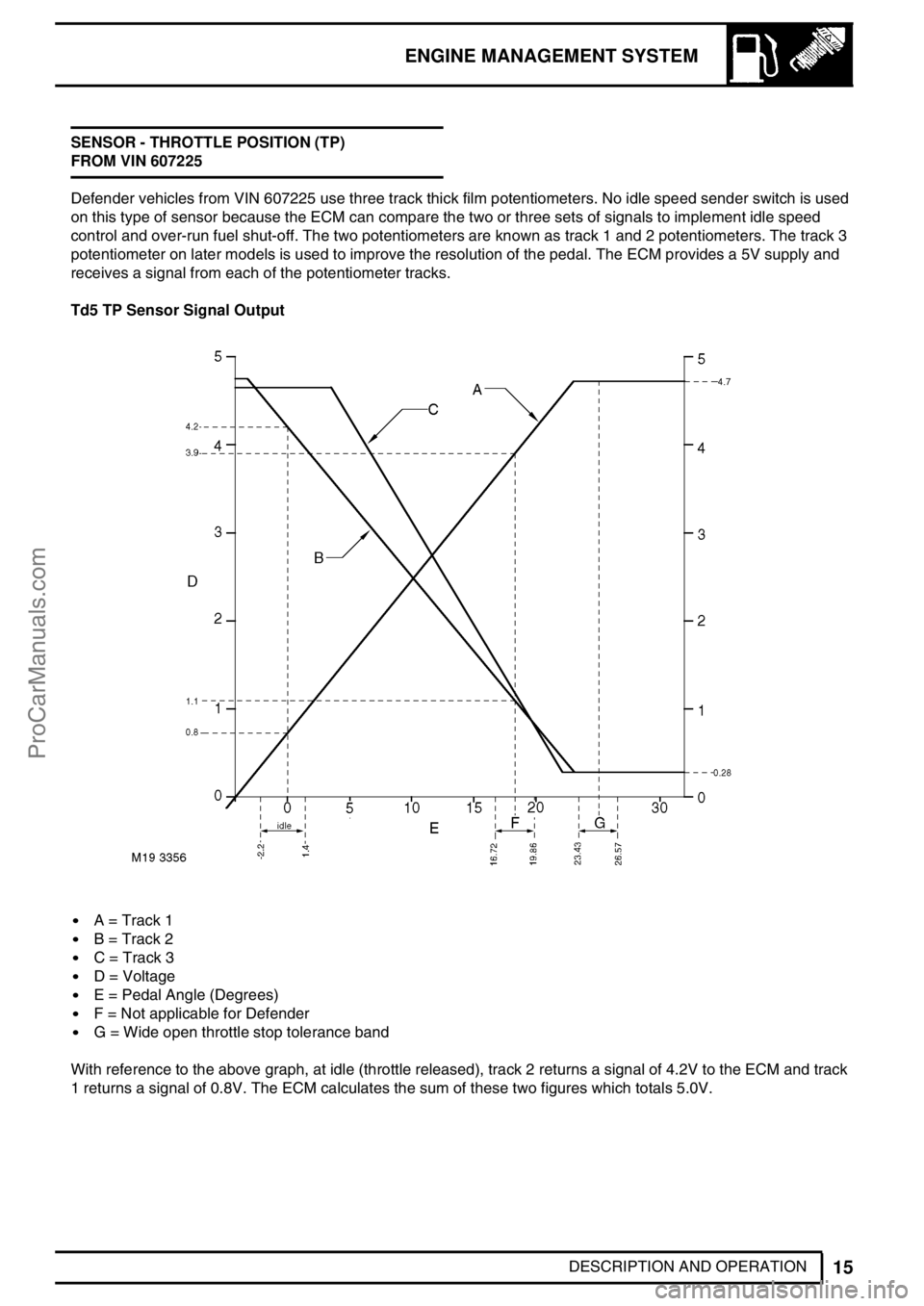
ENGINE MANAGEMENT SYSTEM
15
DESCRIPTION AND OPERATION SENSOR - THROTTLE POSITION (TP)
FROM VIN 607225
Defender vehicles from VIN 607225 use three track thick film potentiometers. No idle speed sender switch is used
on this type of sensor because the ECM can compare the two or three sets of signals to implement idle speed
control and over-run fuel shut-off. The two potentiometers are known as track 1 and 2 potentiometers. The track 3
potentiometer on later models is used to improve the resolution of the pedal. The ECM provides a 5V supply and
receives a signal from each of the potentiometer tracks.
Td5 TP Sensor Signal Output
A = Track 1
B = Track 2
C = Track 3
D = Voltage
E = Pedal Angle (Degrees)
F = Not applicable for Defender
G = Wide open throttle stop tolerance band
With reference to the above graph, at idle (throttle released), track 2 returns a signal of 4.2V to the ECM and track
1 returns a signal of 0.8V. The ECM calculates the sum of these two figures which totals 5.0V.
ProCarManuals.com
Page 258 of 667
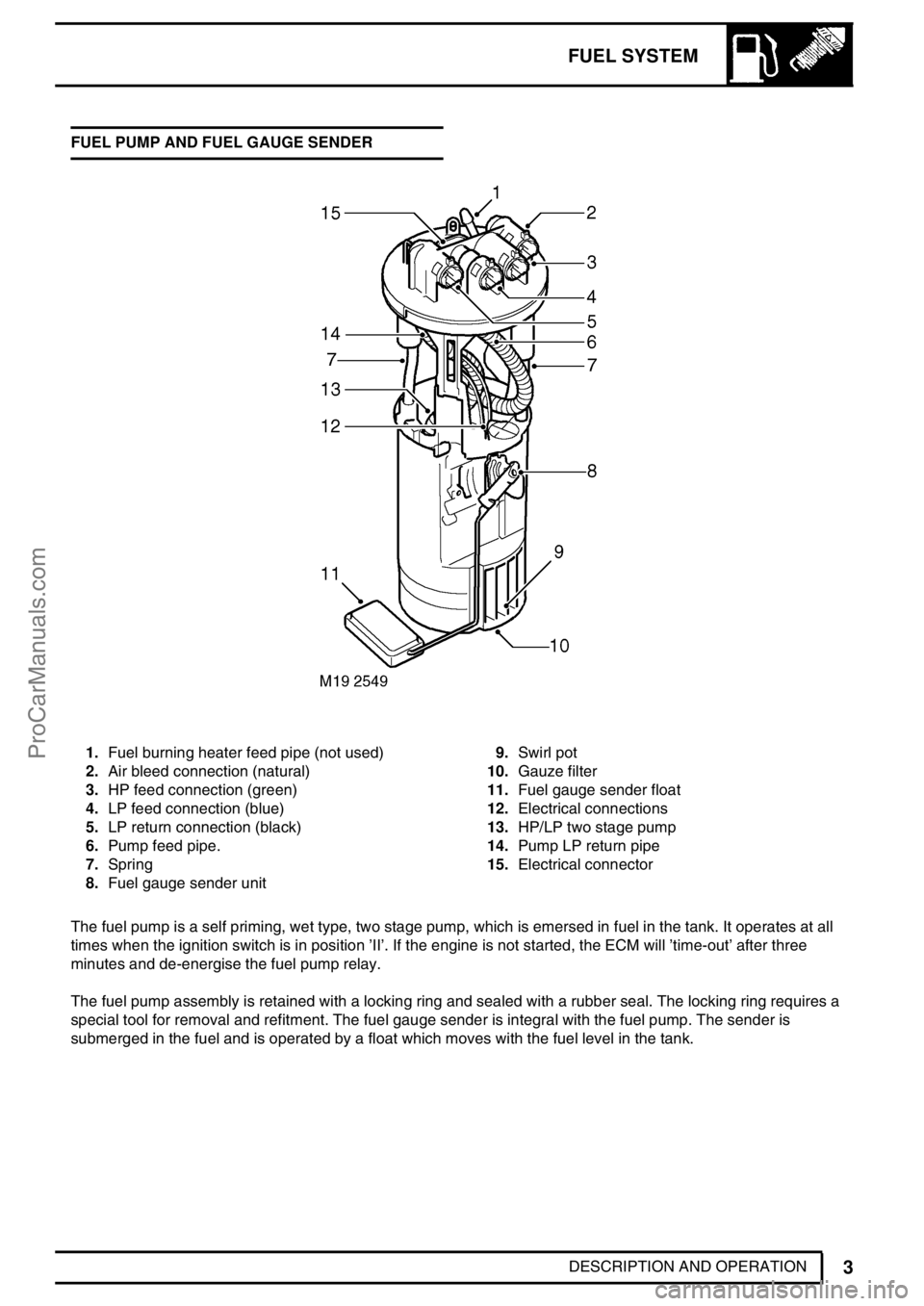
FUEL SYSTEM
3
DESCRIPTION AND OPERATION FUEL PUMP AND FUEL GAUGE SENDER
1.Fuel burning heater feed pipe (not used)
2.Air bleed connection (natural)
3.HP feed connection (green)
4.LP feed connection (blue)
5.LP return connection (black)
6.Pump feed pipe.
7.Spring
8.Fuel gauge sender unit9.Swirl pot
10.Gauze filter
11.Fuel gauge sender float
12.Electrical connections
13.HP/LP two stage pump
14.Pump LP return pipe
15.Electrical connector
The fuel pump is a self priming, wet type, two stage pump, which is emersed in fuel in the tank. It operates at all
times when the ignition switch is in position’II’. If the engine is not started, the ECM will’time-out’after three
minutes and de-energise the fuel pump relay.
The fuel pump assembly is retained with a locking ring and sealed with a rubber seal. The locking ring requires a
special tool for removal and refitment. The fuel gauge sender is integral with the fuel pump. The sender is
submerged in the fuel and is operated by a float which moves with the fuel level in the tank.
ProCarManuals.com
Page 264 of 667
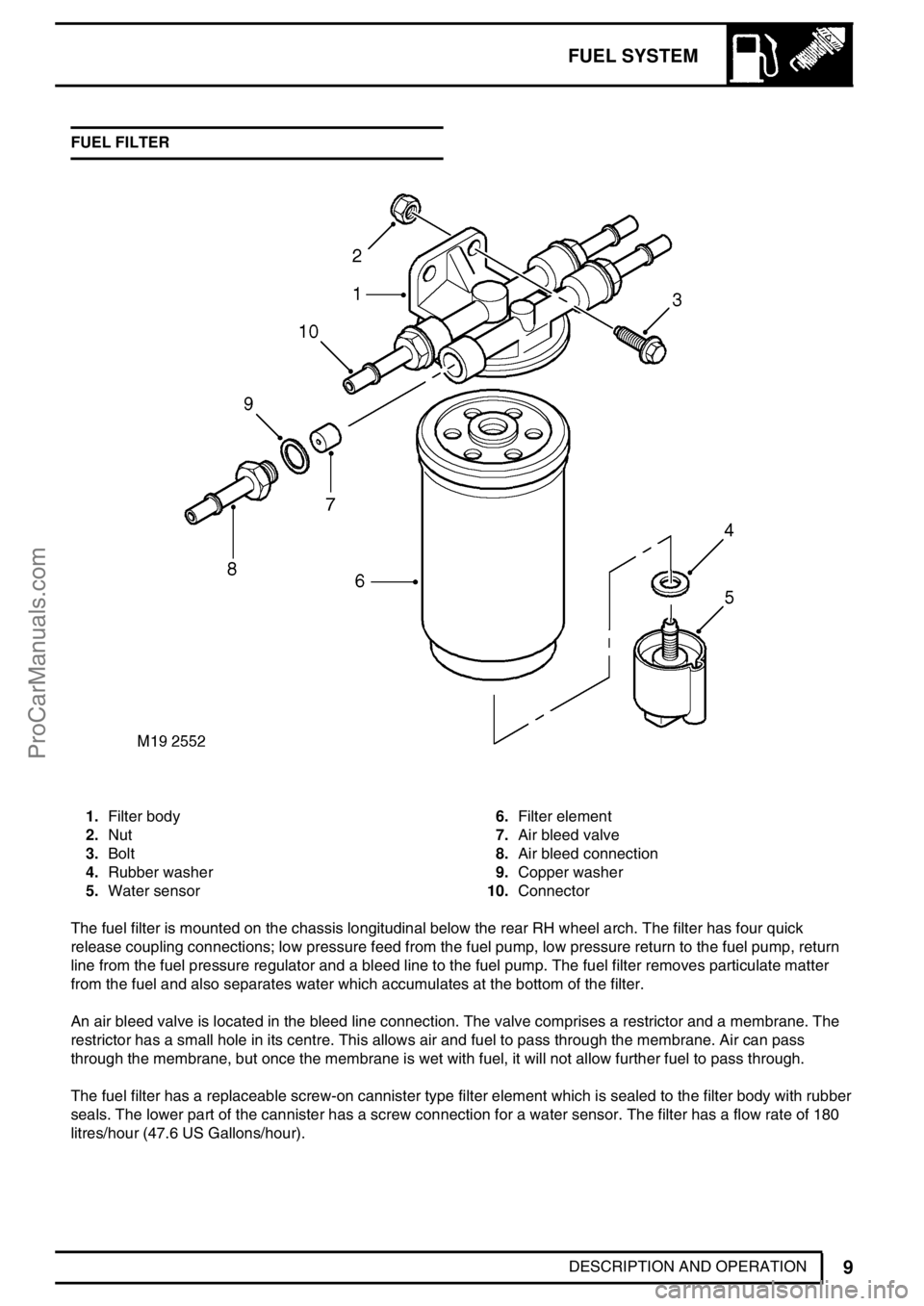
FUEL SYSTEM
9
DESCRIPTION AND OPERATION FUEL FILTER
1.Filter body
2.Nut
3.Bolt
4.Rubber washer
5.Water sensor6.Filter element
7.Air bleed valve
8.Air bleed connection
9.Copper washer
10.Connector
The fuel filter is mounted on the chassis longitudinal below the rear RH wheel arch. The filter has four quick
release coupling connections; low pressure feed from the fuel pump, low pressure return to the fuel pump, return
line from the fuel pressure regulator and a bleed line to the fuel pump. The fuel filter removes particulate matter
from the fuel and also separates water which accumulates at the bottom of the filter.
An air bleed valve is located in the bleed line connection. The valve comprises a restrictor and a membrane. The
restrictor has a small hole in its centre. This allows air and fuel to pass through the membrane. Air can pass
through the membrane, but once the membrane is wet with fuel, it will not allow further fuel to pass through.
The fuel filter has a replaceable screw-on cannister type filter element which is sealed to the filter body with rubber
seals. The lower part of the cannister has a screw connection for a water sensor. The filter has a flow rate of 180
litres/hour (47.6 US Gallons/hour).
ProCarManuals.com
Page 294 of 667
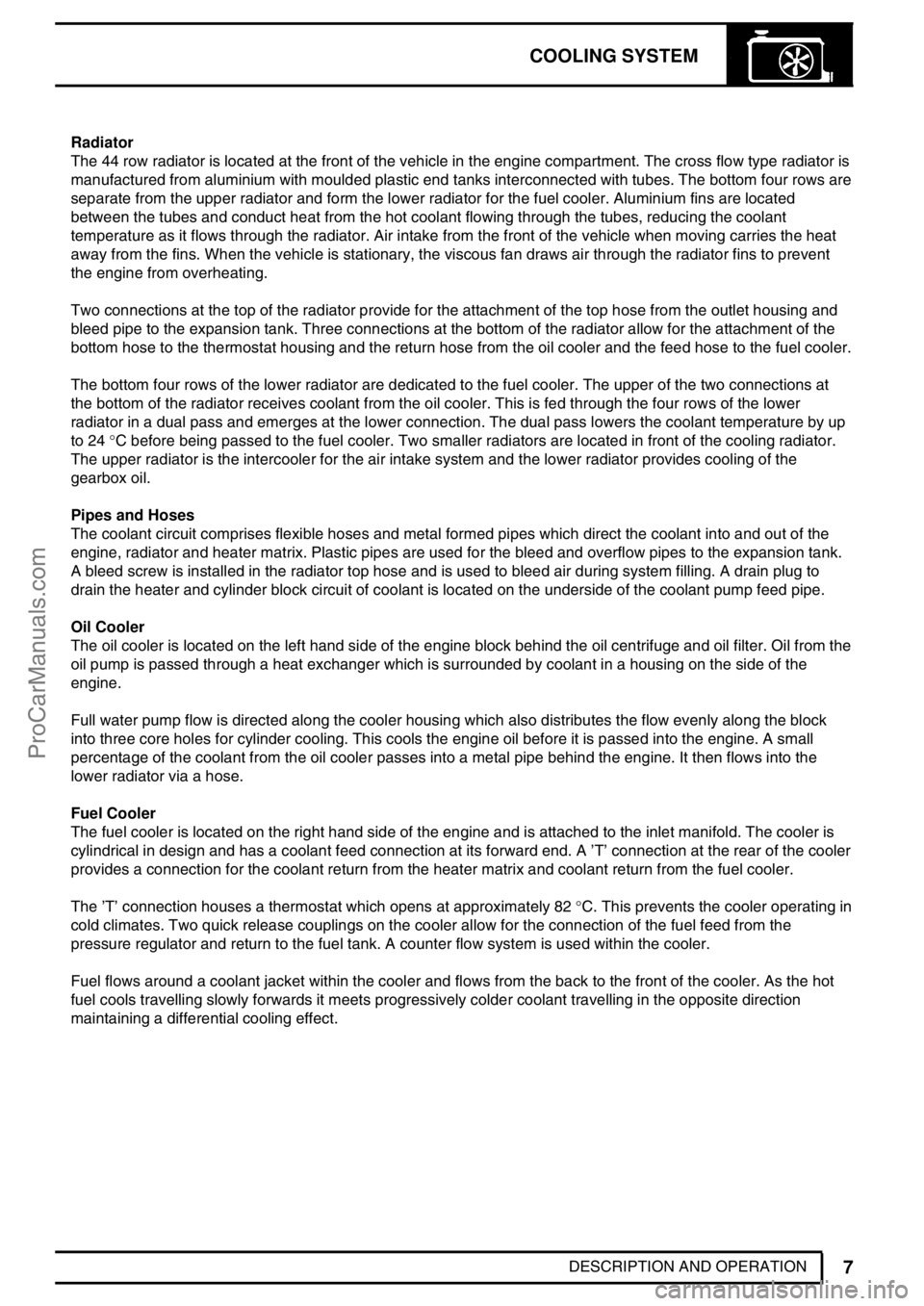
COOLING SYSTEM
7
DESCRIPTION AND OPERATION Radiator
The 44 row radiator is located at the front of the vehicle in the engine compartment. The cross flow type radiator is
manufactured from aluminium with moulded plastic end tanks interconnected with tubes. The bottom four rows are
separate from the upper radiator and form the lower radiator for the fuel cooler. Aluminium fins are located
between the tubes and conduct heat from the hot coolant flowing through the tubes, reducing the coolant
temperature as it flows through the radiator. Air intake from the front of the vehicle when moving carries the heat
away from the fins. When the vehicle is stationary, the viscous fan draws air through the radiator fins to prevent
the engine from overheating.
Two connections at the top of the radiator provide for the attachment of the top hose from the outlet housing and
bleed pipe to the expansion tank. Three connections at the bottom of the radiator allow for the attachment of the
bottom hose to the thermostat housing and the return hose from the oil cooler and the feed hose to the fuel cooler.
The bottom four rows of the lower radiator are dedicated to the fuel cooler. The upper of the two connections at
the bottom of the radiator receives coolant from the oil cooler. This is fed through the four rows of the lower
radiator in a dual pass and emerges at the lower connection. The dual pass lowers the coolant temperature by up
to 24°C before being passed to the fuel cooler. Two smaller radiators are located in front of the cooling radiator.
The upper radiator is the intercooler for the air intake system and the lower radiator provides cooling of the
gearbox oil.
Pipes and Hoses
The coolant circuit comprises flexible hoses and metal formed pipes which direct the coolant into and out of the
engine, radiator and heater matrix. Plastic pipes are used for the bleed and overflow pipes to the expansion tank.
A bleed screw is installed in the radiator top hose and is used to bleed air during system filling. A drain plug to
drain the heater and cylinder block circuit of coolant is located on the underside of the coolant pump feed pipe.
Oil Cooler
The oil cooler is located on the left hand side of the engine block behind the oil centrifuge and oil filter. Oil from the
oil pump is passed through a heat exchanger which is surrounded by coolant in a housing on the side of the
engine.
Full water pump flow is directed along the cooler housing which also distributes the flow evenly along the block
into three core holes for cylinder cooling. This cools the engine oil before it is passed into the engine. A small
percentage of the coolant from the oil cooler passes into a metal pipe behind the engine. It then flows into the
lower radiator via a hose.
Fuel Cooler
The fuel cooler is located on the right hand side of the engine and is attached to the inlet manifold. The cooler is
cylindrical in design and has a coolant feed connection at its forward end. A’T’connection at the rear of the cooler
provides a connection for the coolant return from the heater matrix and coolant return from the fuel cooler.
The’T’connection houses a thermostat which opens at approximately 82°C. This prevents the cooler operating in
cold climates. Two quick release couplings on the cooler allow for the connection of the fuel feed from the
pressure regulator and return to the fuel tank. A counter flow system is used within the cooler.
Fuel flows around a coolant jacket within the cooler and flows from the back to the front of the cooler. As the hot
fuel cools travelling slowly forwards it meets progressively colder coolant travelling in the opposite direction
maintaining a differential cooling effect.
ProCarManuals.com
Page 621 of 667
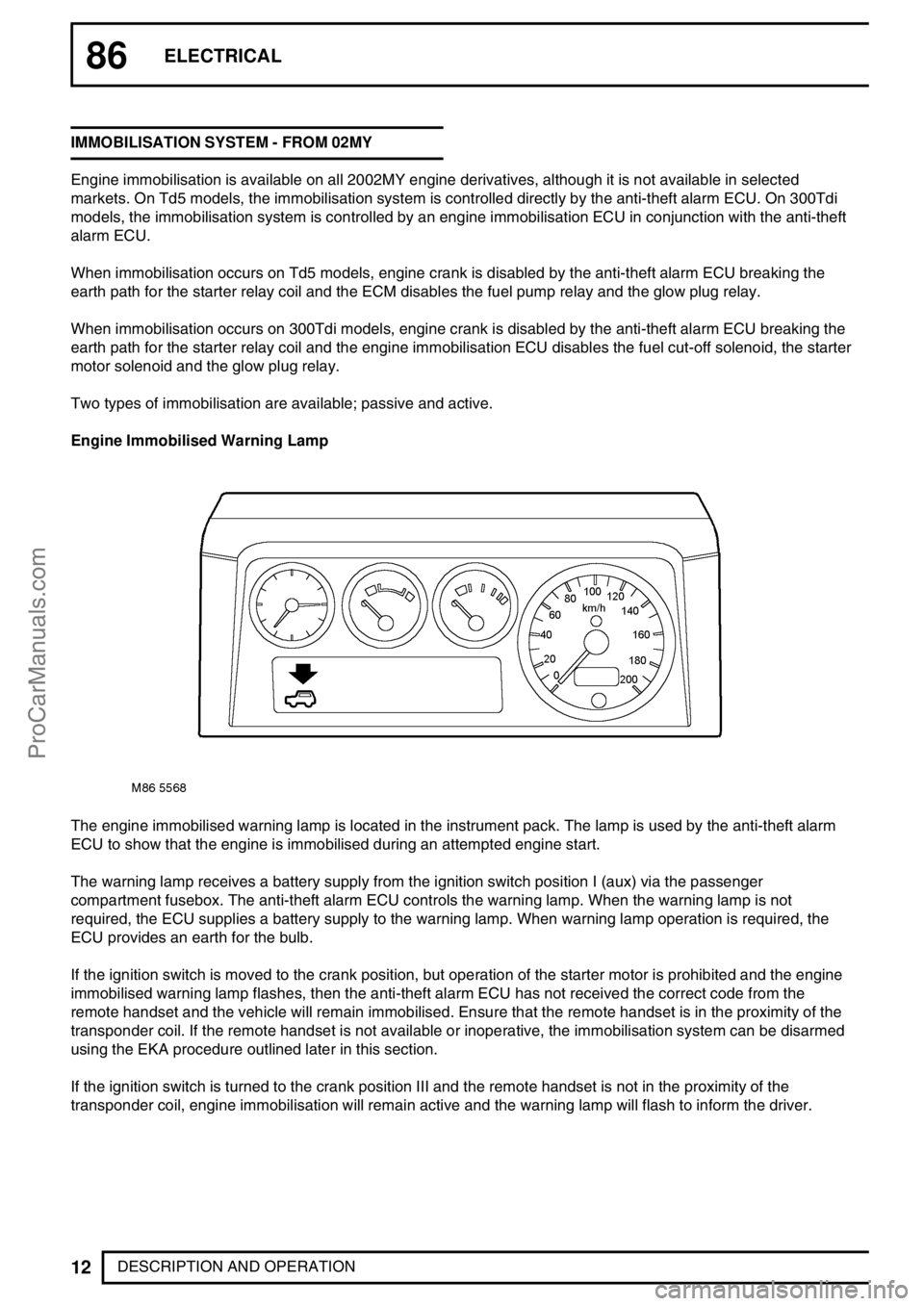
86ELECTRICAL
12
DESCRIPTION AND OPERATION IMMOBILISATION SYSTEM - FROM 02MY
Engine immobilisation is available on all 2002MY engine derivatives, although it is not available in selected
markets. On Td5 models, the immobilisation system is controlled directly by the anti-theft alarm ECU. On 300Tdi
models, the immobilisation system is controlled by an engine immobilisation ECU in conjunction with the anti-theft
alarm ECU.
When immobilisation occurs on Td5 models, engine crank is disabled by the anti-theft alarm ECU breaking the
earth path for the starter relay coil and the ECM disables the fuel pump relay and the glow plug relay.
When immobilisation occurs on 300Tdi models, engine crank is disabled by the anti-theft alarm ECU breaking the
earth path for the starter relay coil and the engine immobilisation ECU disables the fuel cut-off solenoid, the starter
motor solenoid and the glow plug relay.
Two types of immobilisation are available; passive and active.
Engine Immobilised Warning Lamp
The engine immobilised warning lamp is located in the instrument pack. The lamp is used by the anti-theft alarm
ECU to show that the engine is immobilised during an attempted engine start.
The warning lamp receives a battery supply from the ignition switch position I (aux) via the passenger
compartment fusebox. The anti-theft alarm ECU controls the warning lamp. When the warning lamp is not
required, the ECU supplies a battery supply to the warning lamp. When warning lamp operation is required, the
ECU provides an earth for the bulb.
If the ignition switch is moved to the crank position, but operation of the starter motor is prohibited and the engine
immobilised warning lamp flashes, then the anti-theft alarm ECU has not received the correct code from the
remote handset and the vehicle will remain immobilised. Ensure that the remote handset is in the proximity of the
transponder coil. If the remote handset is not available or inoperative, the immobilisation system can be disarmed
using the EKA procedure outlined later in this section.
If the ignition switch is turned to the crank position III and the remote handset is not in the proximity of the
transponder coil, engine immobilisation will remain active and the warning lamp will flash to inform the driver.
ProCarManuals.com