jacking LAND ROVER DEFENDER 1999 Workshop Manual
[x] Cancel search | Manufacturer: LAND ROVER, Model Year: 1999, Model line: DEFENDER, Model: LAND ROVER DEFENDER 1999Pages: 667, PDF Size: 8.76 MB
Page 6 of 667
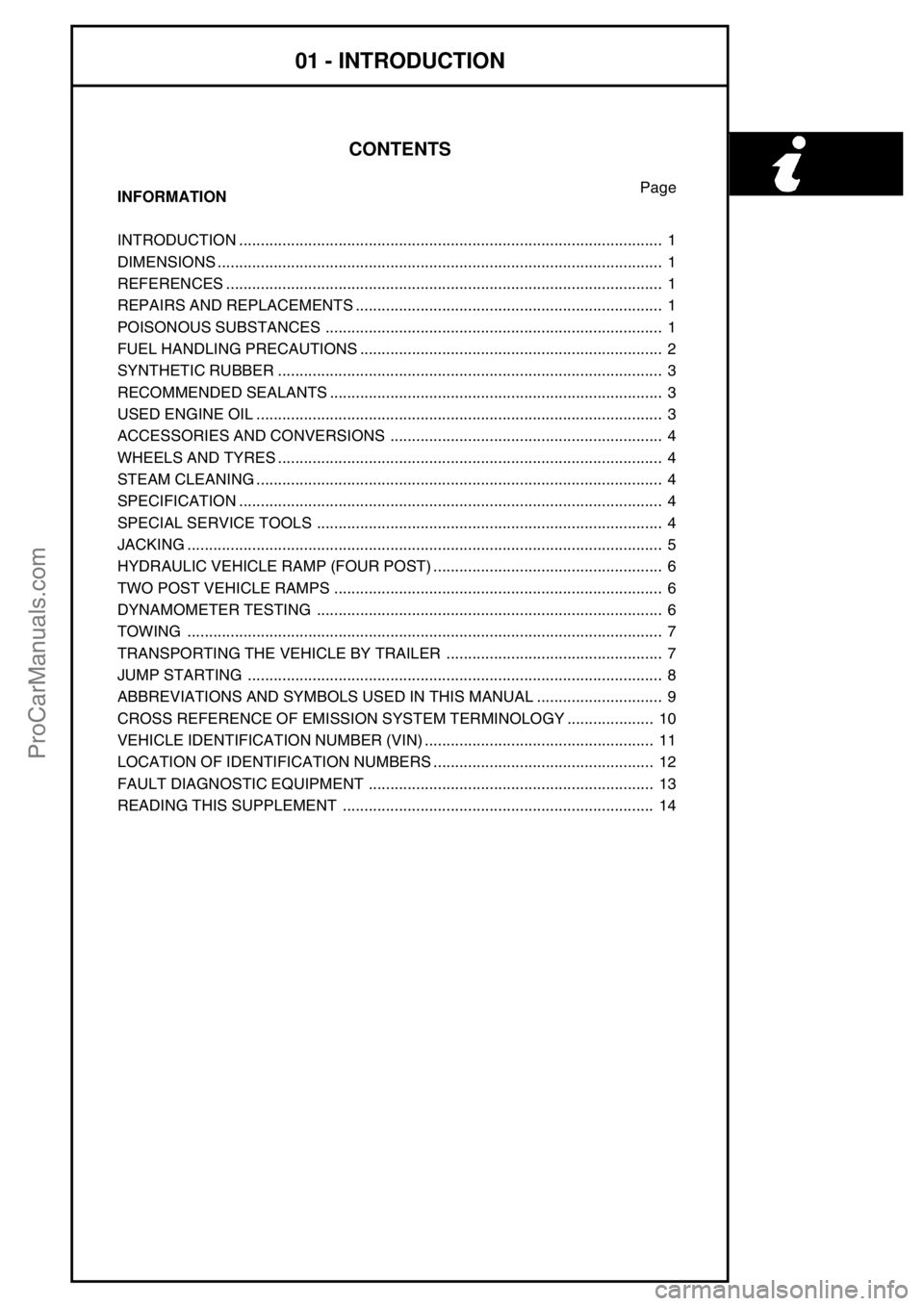
01 - INTRODUCTION
CONTENTS
Page
INFORMATION
INTRODUCTION 1..................................................................................................
DIMENSIONS 1.......................................................................................................
REFERENCES 1.....................................................................................................
REPAIRS AND REPLACEMENTS 1.......................................................................
POISONOUS SUBSTANCES 1..............................................................................
FUEL HANDLING PRECAUTIONS 2......................................................................
SYNTHETIC RUBBER 3.........................................................................................
RECOMMENDED SEALANTS 3.............................................................................
USED ENGINE OIL 3..............................................................................................
ACCESSORIES AND CONVERSIONS 4...............................................................
WHEELS AND TYRES 4.........................................................................................
STEAM CLEANING 4..............................................................................................
SPECIFICATION 4..................................................................................................
SPECIAL SERVICE TOOLS 4................................................................................
JACKING 5..............................................................................................................
HYDRAULIC VEHICLE RAMP (FOUR POST) 6.....................................................
TWO POST VEHICLE RAMPS 6............................................................................
DYNAMOMETER TESTING 6................................................................................
TOWING 7..............................................................................................................
TRANSPORTING THE VEHICLE BY TRAILER 7..................................................
JUMP STARTING 8................................................................................................
ABBREVIATIONS AND SYMBOLS USED IN THIS MANUAL 9.............................
CROSS REFERENCE OF EMISSION SYSTEM TERMINOLOGY 10....................
VEHICLE IDENTIFICATION NUMBER (VIN) 11.....................................................
LOCATION OF IDENTIFICATION NUMBERS 12...................................................
FAULT DIAGNOSTIC EQUIPMENT 13..................................................................
READING THIS SUPPLEMENT 14........................................................................
ProCarManuals.com
Page 12 of 667
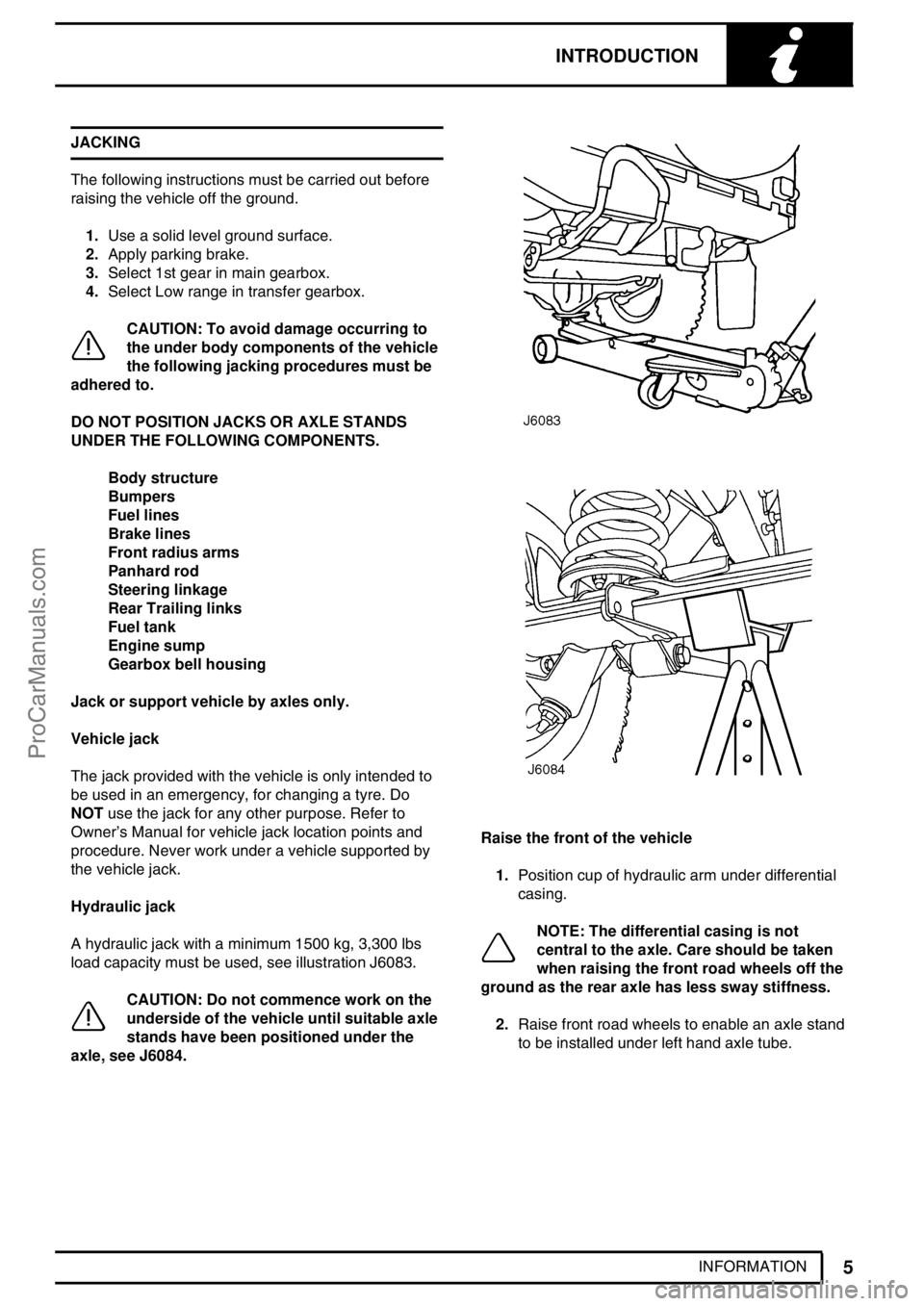
INTRODUCTION
5
INFORMATION JACKING
The following instructions must be carried out before
raising the vehicle off the ground.
1.Use a solid level ground surface.
2.Apply parking brake.
3.Select 1st gear in main gearbox.
4.Select Low range in transfer gearbox.
CAUTION: To avoid damage occurring to
the under body components of the vehicle
the following jacking procedures must be
adhered to.
DO NOT POSITION JACKS OR AXLE STANDS
UNDER THE FOLLOWING COMPONENTS.
Body structure
Bumpers
Fuel lines
Brake lines
Front radius arms
Panhard rod
Steering linkage
Rear Trailing links
Fuel tank
Engine sump
Gearbox bell housing
Jack or support vehicle by axles only.
Vehicle jack
The jack provided with the vehicle is only intended to
be used in an emergency, for changing a tyre. Do
NOTuse the jack for any other purpose. Refer to
Owner’s Manual for vehicle jack location points and
procedure. Never work under a vehicle supported by
the vehicle jack.
Hydraulic jack
A hydraulic jack with a minimum 1500 kg, 3,300 lbs
load capacity must be used, see illustration J6083.
CAUTION: Do not commence work on the
underside of the vehicle until suitable axle
stands have been positioned under the
axle, see J6084.
Raise the front of the vehicle
1.Position cup of hydraulic arm under differential
casing.
NOTE: The differential casing is not
central to the axle. Care should be taken
when raising the front road wheels off the
ground as the rear axle has less sway stiffness.
2.Raise front road wheels to enable an axle stand
to be installed under left hand axle tube.
ProCarManuals.com
Page 44 of 667
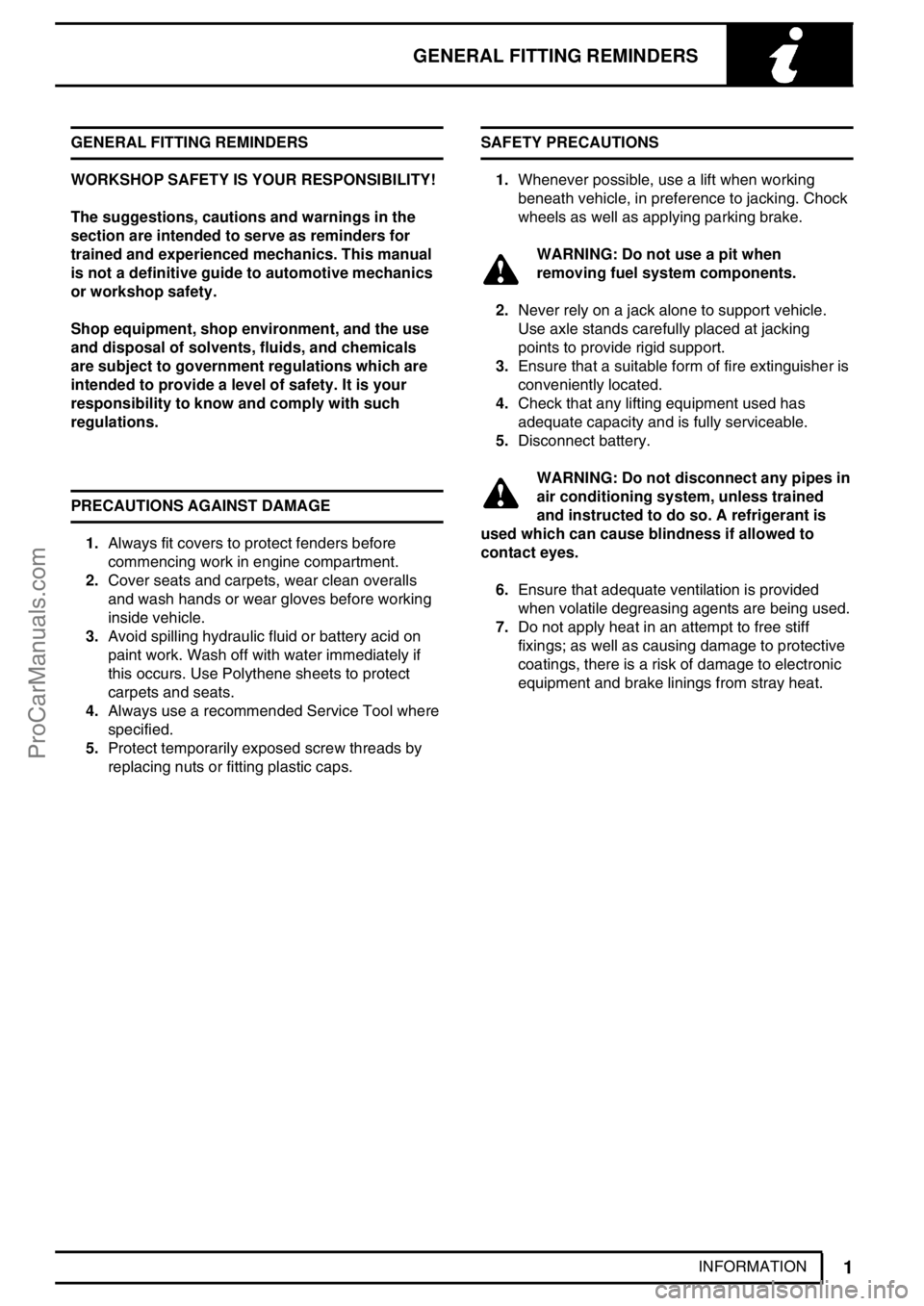
GENERAL FITTING REMINDERS
1
INFORMATION GENERAL FITTING REMINDERS
WORKSHOP SAFETY IS YOUR RESPONSIBILITY!
The suggestions, cautions and warnings in the
section are intended to serve as reminders for
trained and experienced mechanics. This manual
is not a definitive guide to automotive mechanics
or workshop safety.
Shop equipment, shop environment, and the use
and disposal of solvents, fluids, and chemicals
are subject to government regulations which are
intended to provide a level of safety. It is your
responsibility to know and comply with such
regulations.
PRECAUTIONS AGAINST DAMAGE
1.Always fit covers to protect fenders before
commencing work in engine compartment.
2.Cover seats and carpets, wear clean overalls
and wash hands or wear gloves before working
inside vehicle.
3.Avoid spilling hydraulic fluid or battery acid on
paint work. Wash off with water immediately if
this occurs. Use Polythene sheets to protect
carpets and seats.
4.Always use a recommended Service Tool where
specified.
5.Protect temporarily exposed screw threads by
replacing nuts or fitting plastic caps.SAFETY PRECAUTIONS
1.Whenever possible, use a lift when working
beneath vehicle, in preference to jacking. Chock
wheels as well as applying parking brake.
WARNING: Do not use a pit when
removing fuel system components.
2.Never rely on a jack alone to support vehicle.
Use axle stands carefully placed at jacking
points to provide rigid support.
3.Ensure that a suitable form of fire extinguisher is
conveniently located.
4.Check that any lifting equipment used has
adequate capacity and is fully serviceable.
5.Disconnect battery.
WARNING: Do not disconnect any pipes in
air conditioning system, unless trained
and instructed to do so. A refrigerant is
used which can cause blindness if allowed to
contact eyes.
6.Ensure that adequate ventilation is provided
when volatile degreasing agents are being used.
7.Do not apply heat in an attempt to free stiff
fixings; as well as causing damage to protective
coatings, there is a risk of damage to electronic
equipment and brake linings from stray heat.
ProCarManuals.com
Page 532 of 667
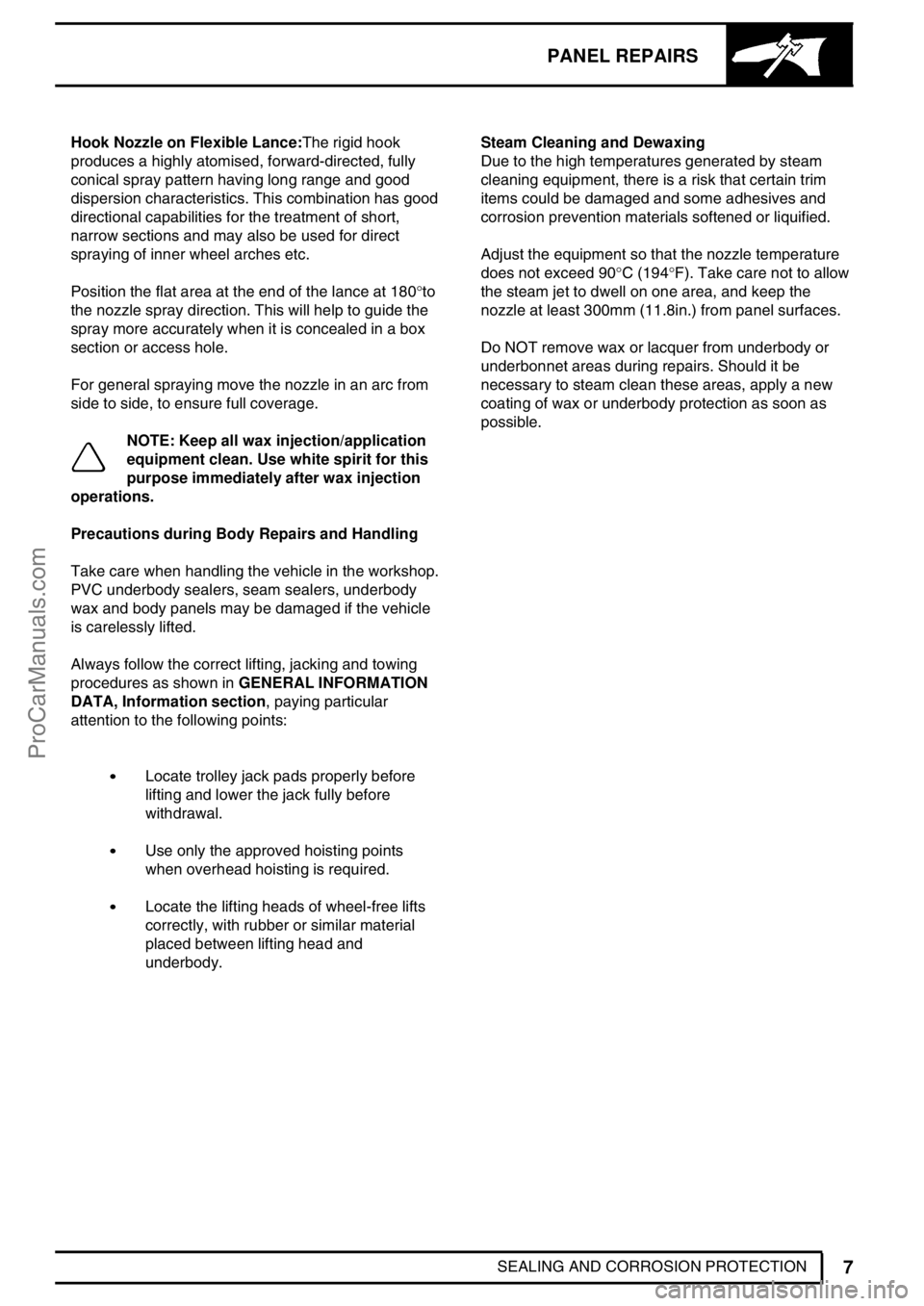
PANEL REPAIRS
7
SEALING AND CORROSION PROTECTION Hook Nozzle on Flexible Lance:The rigid hook
produces a highly atomised, forward-directed, fully
conical spray pattern having long range and good
dispersion characteristics. This combination has good
directional capabilities for the treatment of short,
narrow sections and may also be used for direct
spraying of inner wheel arches etc.
Position the flat area at the end of the lance at 180°to
the nozzle spray direction. This will help to guide the
spray more accurately when it is concealed in a box
section or access hole.
For general spraying move the nozzle in an arc from
side to side, to ensure full coverage.
NOTE: Keep all wax injection/application
equipment clean. Use white spirit for this
purpose immediately after wax injection
operations.
Precautions during Body Repairs and Handling
Take care when handling the vehicle in the workshop.
PVC underbody sealers, seam sealers, underbody
wax and body panels may be damaged if the vehicle
is carelessly lifted.
Always follow the correct lifting, jacking and towing
procedures as shown inGENERAL INFORMATION
DATA, Information section, paying particular
attention to the following points:
Locate trolley jack pads properly before
lifting and lower the jack fully before
withdrawal.
Use only the approved hoisting points
when overhead hoisting is required.
Locate the lifting heads of wheel-free lifts
correctly, with rubber or similar material
placed between lifting head and
underbody.Steam Cleaning and Dewaxing
Due to the high temperatures generated by steam
cleaning equipment, there is a risk that certain trim
items could be damaged and some adhesives and
corrosion prevention materials softened or liquified.
Adjust the equipment so that the nozzle temperature
does not exceed 90°C (194°F). Take care not to allow
the steam jet to dwell on one area, and keep the
nozzle at least 300mm (11.8in.) from panel surfaces.
Do NOT remove wax or lacquer from underbody or
underbonnet areas during repairs. Should it be
necessary to steam clean these areas, apply a new
coating of wax or underbody protection as soon as
possible.
ProCarManuals.com
Page 534 of 667
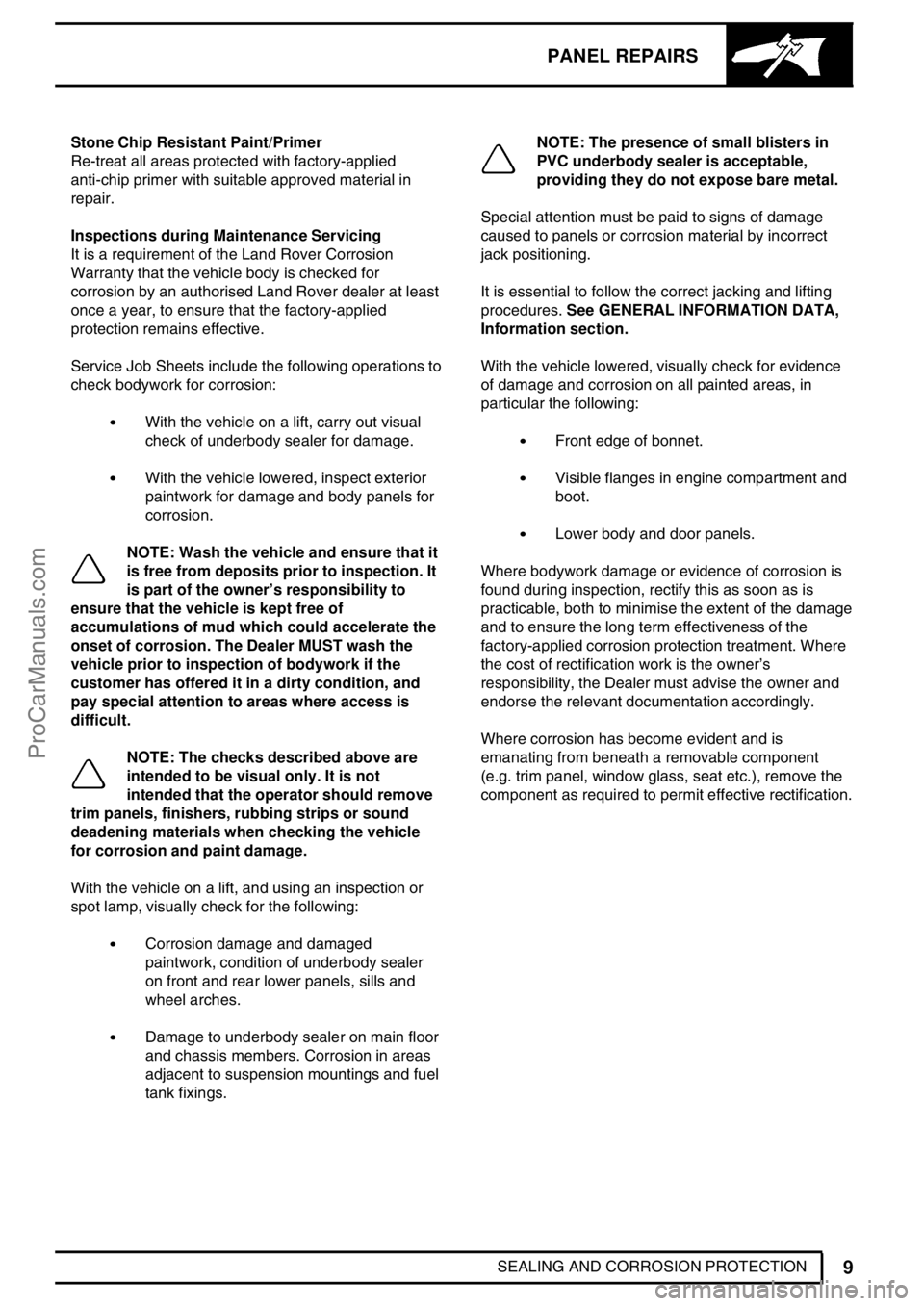
PANEL REPAIRS
9
SEALING AND CORROSION PROTECTION Stone Chip Resistant Paint/Primer
Re-treat all areas protected with factory-applied
anti-chip primer with suitable approved material in
repair.
Inspections during Maintenance Servicing
It is a requirement of the Land Rover Corrosion
Warranty that the vehicle body is checked for
corrosion by an authorised Land Rover dealer at least
once a year, to ensure that the factory-applied
protection remains effective.
Service Job Sheets include the following operations to
check bodywork for corrosion:
With the vehicle on a lift, carry out visual
check of underbody sealer for damage.
With the vehicle lowered, inspect exterior
paintwork for damage and body panels for
corrosion.
NOTE: Wash the vehicle and ensure that it
is free from deposits prior to inspection. It
is part of the owner’s responsibility to
ensure that the vehicle is kept free of
accumulations of mud which could accelerate the
onset of corrosion. The Dealer MUST wash the
vehicle prior to inspection of bodywork if the
customer has offered it in a dirty condition, and
pay special attention to areas where access is
difficult.
NOTE: The checks described above are
intended to be visual only. It is not
intended that the operator should remove
trim panels, finishers, rubbing strips or sound
deadening materials when checking the vehicle
for corrosion and paint damage.
With the vehicle on a lift, and using an inspection or
spot lamp, visually check for the following:
Corrosion damage and damaged
paintwork, condition of underbody sealer
on front and rear lower panels, sills and
wheel arches.
Damage to underbody sealer on main floor
and chassis members. Corrosion in areas
adjacent to suspension mountings and fuel
tank fixings.
NOTE: The presence of small blisters in
PVC underbody sealer is acceptable,
providing they do not expose bare metal.
Special attention must be paid to signs of damage
caused to panels or corrosion material by incorrect
jack positioning.
It is essential to follow the correct jacking and lifting
procedures.See GENERAL INFORMATION DATA,
Information section.
With the vehicle lowered, visually check for evidence
of damage and corrosion on all painted areas, in
particular the following:
Front edge of bonnet.
Visible flanges in engine compartment and
boot.
Lower body and door panels.
Where bodywork damage or evidence of corrosion is
found during inspection, rectify this as soon as is
practicable, both to minimise the extent of the damage
and to ensure the long term effectiveness of the
factory-applied corrosion protection treatment. Where
the cost of rectification work is the owner’s
responsibility, the Dealer must advise the owner and
endorse the relevant documentation accordingly.
Where corrosion has become evident and is
emanating from beneath a removable component
(e.g. trim panel, window glass, seat etc.), remove the
component as required to permit effective rectification.
ProCarManuals.com