LAND ROVER DISCOVERY 1995 Service Repair Manual
Manufacturer: LAND ROVER, Model Year: 1995, Model line: DISCOVERY, Model: LAND ROVER DISCOVERY 1995Pages: 976, PDF Size: 14.57 MB
Page 961 of 976
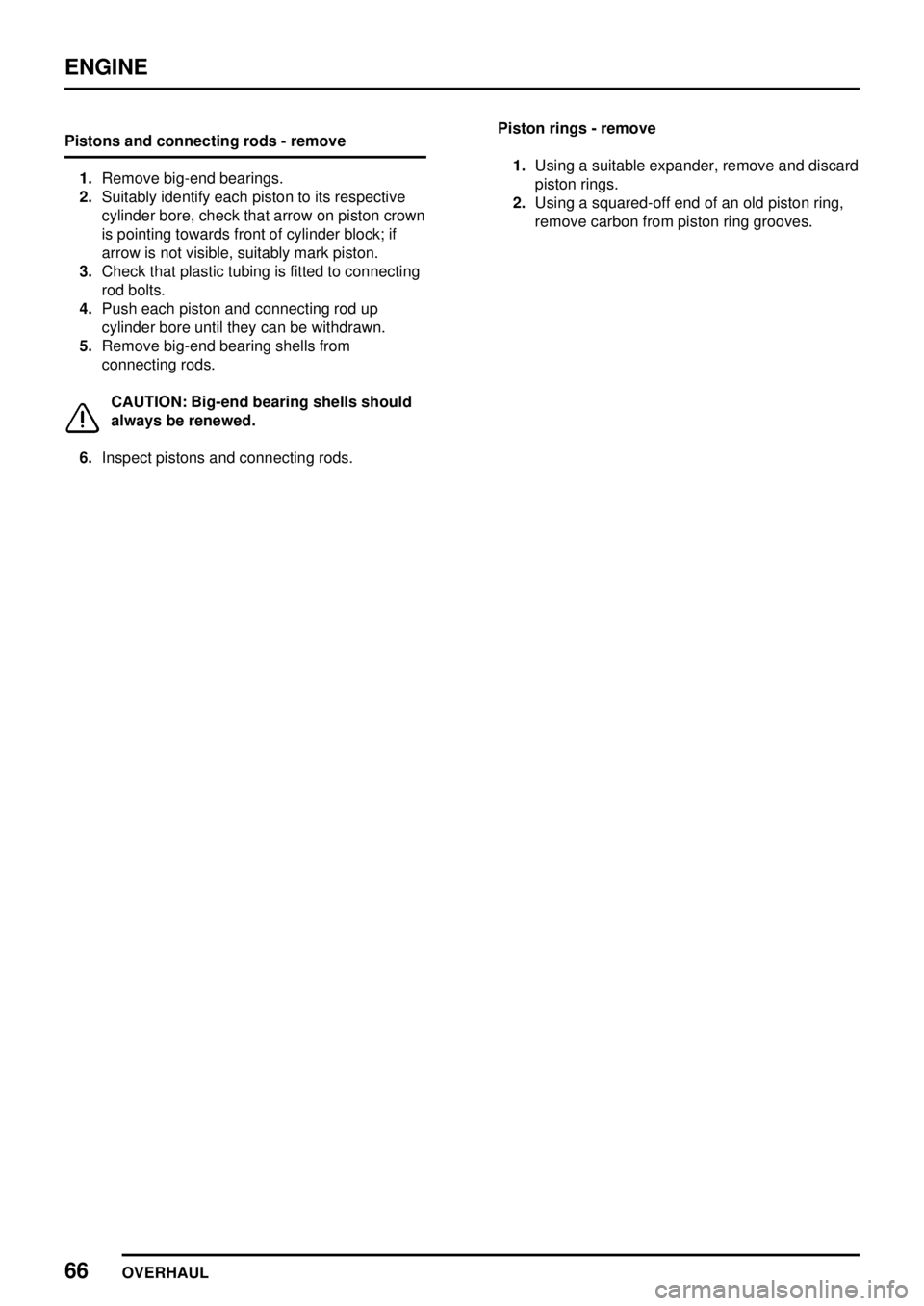
ENGINE
66
OVERHAUL Pistons and connecting rods - remove
1.Remove big-end bearings.
2.Suitably identify each piston to its respective
cylinder bore, check that arrow on piston crown
is pointing towards front of cylinder block; if
arrow is not visible, suitably mark piston.
3.Check that plastic tubing is fitted to connecting
rod bolts.
4.Push each piston and connecting rod up
cylinder bore until they can be withdrawn.
5.Remove big-end bearing shells from
connecting rods.
CAUTION: Big-end bearing shells should
always be renewed.
6.Inspect pistons and connecting rods.Piston rings - remove
1.Using a suitable expander, remove and discard
piston rings.
2.Using a squared-off end of an old piston ring,
remove carbon from piston ring grooves.
Page 962 of 976
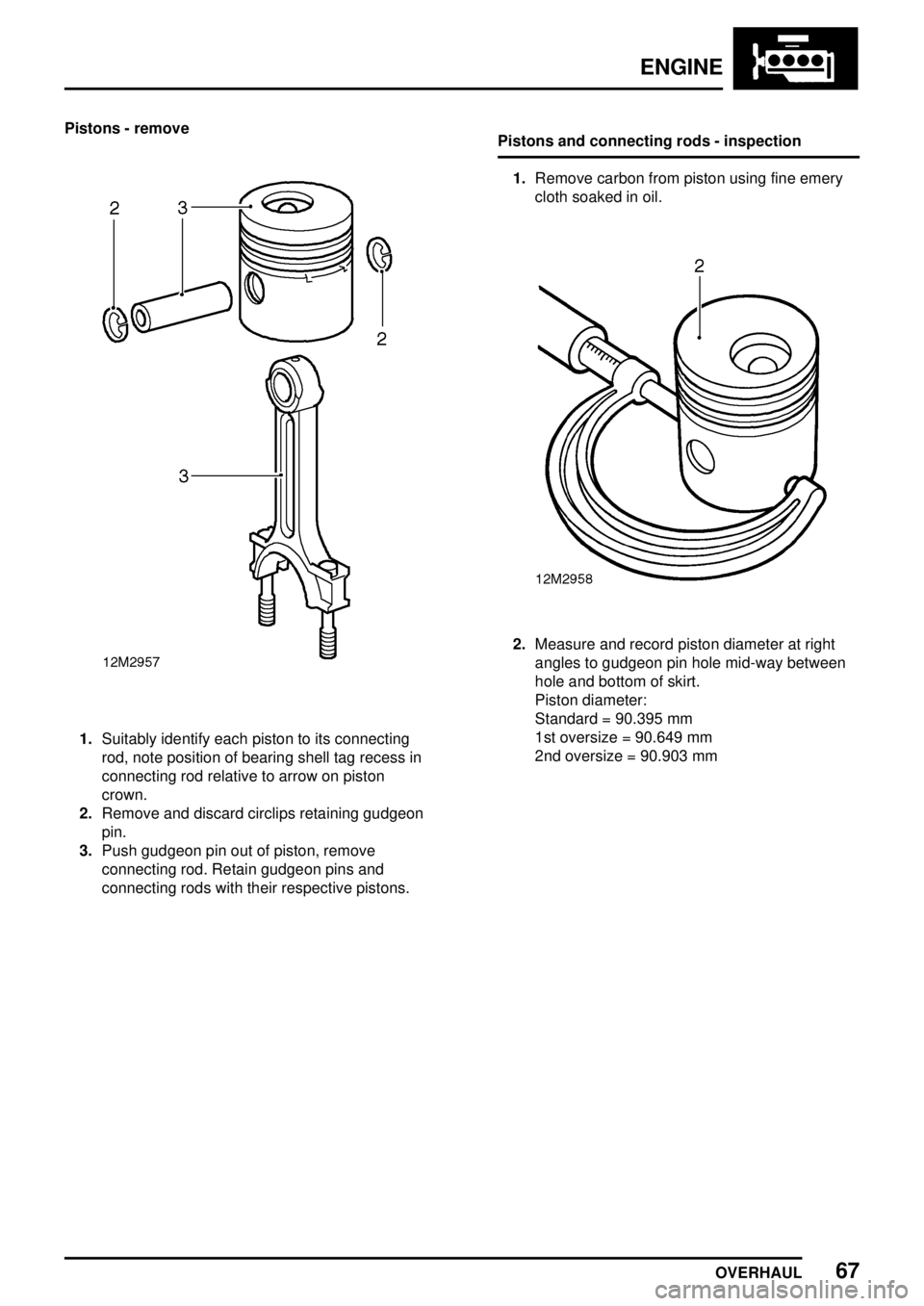
ENGINE
OVERHAUL67
Pistons - remove
1.Suitably identify each piston to its connecting
rod, note position of bearing shell tag recess in
connecting rod relative to arrow on piston
crown.
2.Remove and discard circlips retaining gudgeon
pin.
3.Push gudgeon pin out of piston, remove
connecting rod. Retain gudgeon pins and
connecting rods with their respective pistons.Pistons and connecting rods - inspection
1.Remove carbon from piston using fine emery
cloth soaked in oil.
2.Measure and record piston diameter at right
angles to gudgeon pin hole mid-way between
hole and bottom of skirt.
Piston diameter:
Standard = 90.395 mm
1st oversize = 90.649 mm
2nd oversize = 90.903 mm
Page 963 of 976
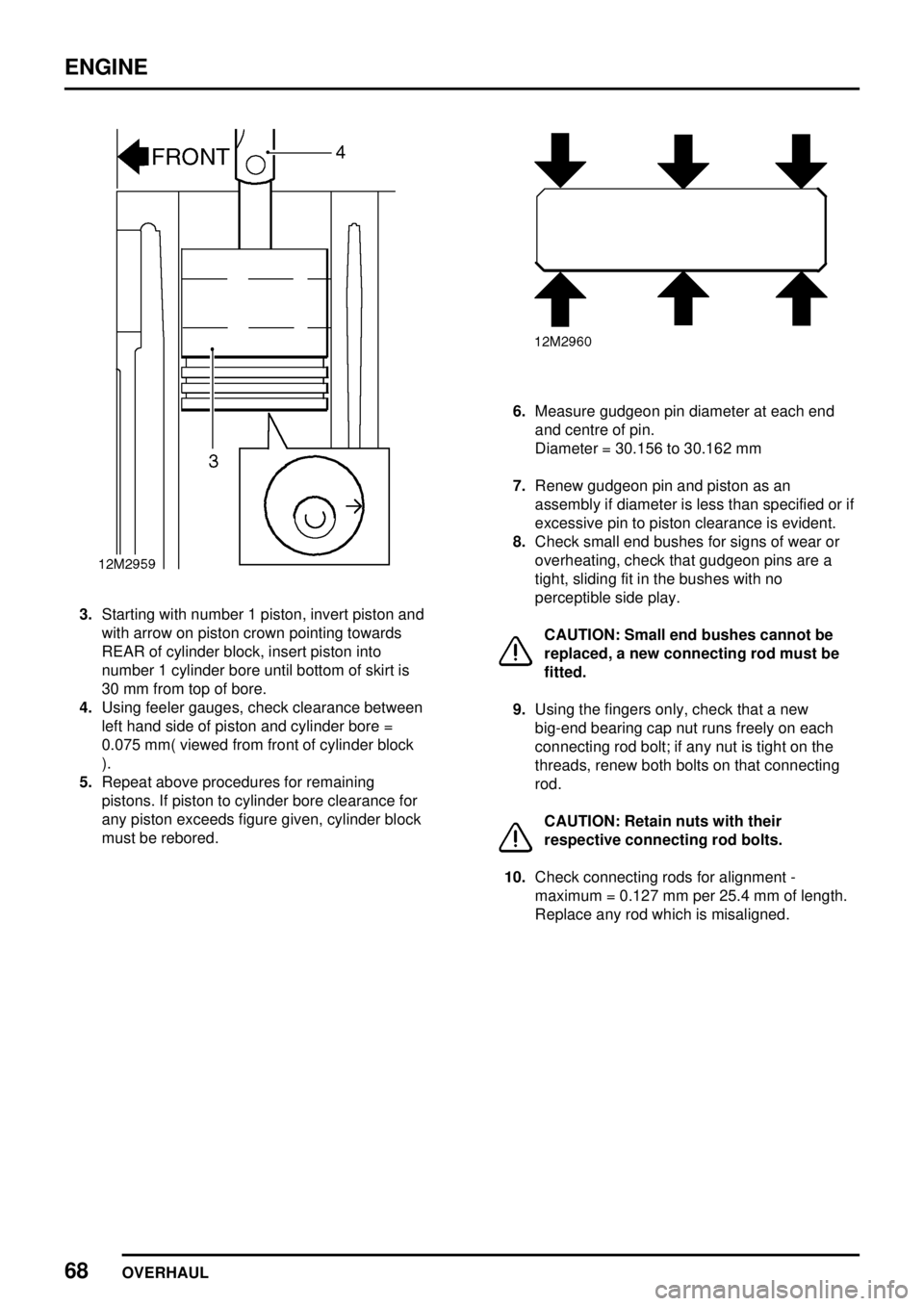
ENGINE
68
OVERHAUL
3.Starting with number 1 piston, invert piston and
with arrow on piston crown pointing towards
REAR of cylinder block, insert piston into
number 1 cylinder bore until bottom of skirt is
30 mm from top of bore.
4.Using feeler gauges, check clearance between
left hand side of piston and cylinder bore =
0.075 mm( viewed from front of cylinder block
).
5.Repeat above procedures for remaining
pistons. If piston to cylinder bore clearance for
any piston exceeds figure given, cylinder block
must be rebored.
6.Measure gudgeon pin diameter at each end
and centre of pin.
Diameter = 30.156 to 30.162 mm
7.Renew gudgeon pin and piston as an
assembly if diameter is less than specified or if
excessive pin to piston clearance is evident.
8.Check small end bushes for signs of wear or
overheating, check that gudgeon pins are a
tight, sliding fit in the bushes with no
perceptible side play.
CAUTION: Small end bushes cannot be
replaced, a new connecting rod must be
fitted.
9.Using the fingers only, check that a new
big-end bearing cap nut runs freely on each
connecting rod bolt; if any nut is tight on the
threads, renew both bolts on that connecting
rod.
CAUTION: Retain nuts with their
respective connecting rod bolts.
10.Check connecting rods for alignment -
maximum = 0.127 mm per 25.4 mm of length.
Replace any rod which is misaligned.
Page 964 of 976
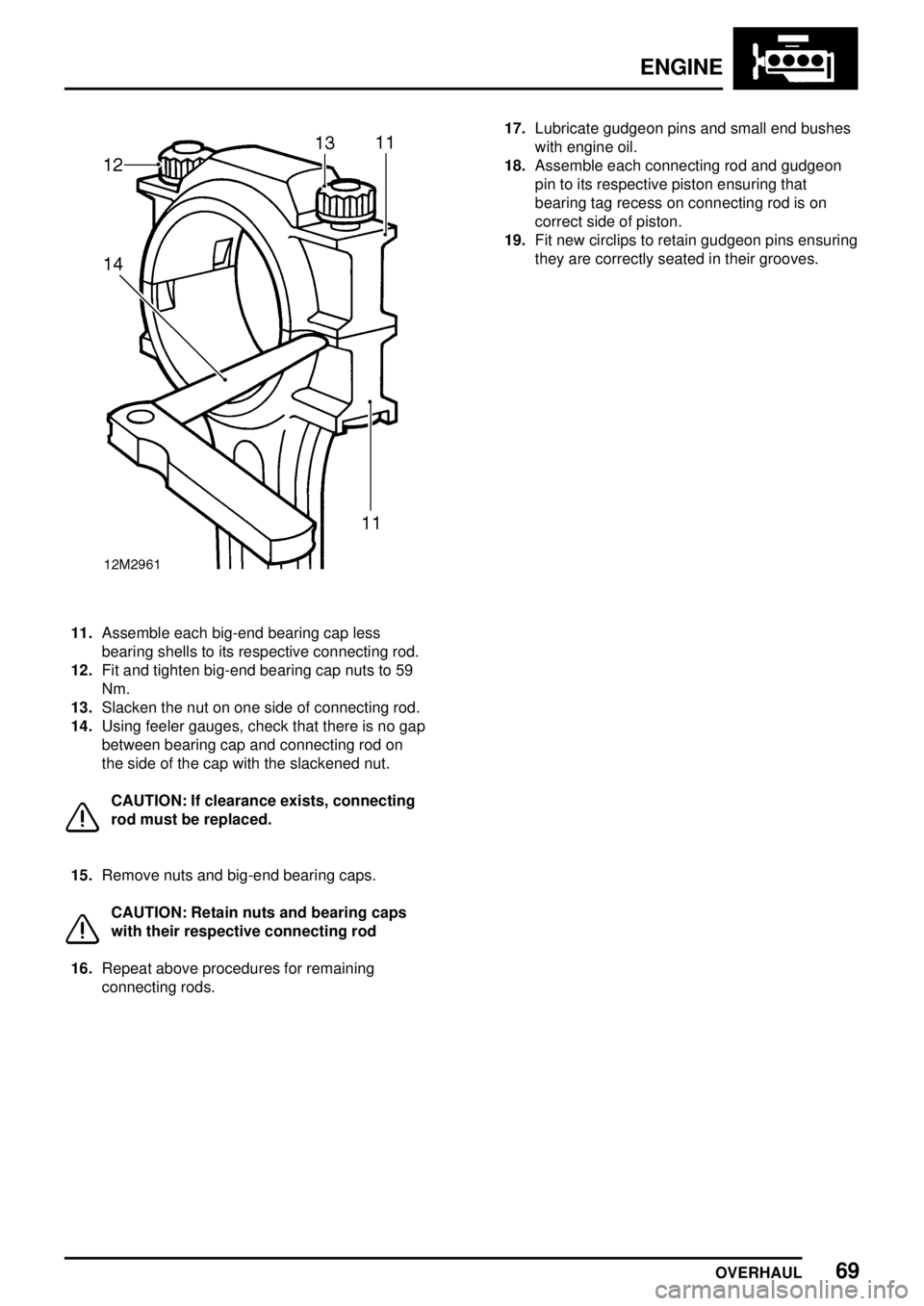
ENGINE
OVERHAUL69
11.Assemble each big-end bearing cap less
bearing shells to its respective connecting rod.
12.Fit and tighten big-end bearing cap nuts to 59
Nm.
13.Slacken the nut on one side of connecting rod.
14.Using feeler gauges, check that there is no gap
between bearing cap and connecting rod on
the side of the cap with the slackened nut.
CAUTION: If clearance exists, connecting
rod must be replaced.
15.Remove nuts and big-end bearing caps.
CAUTION: Retain nuts and bearing caps
with their respective connecting rod
16.Repeat above procedures for remaining
connecting rods.17.Lubricate gudgeon pins and small end bushes
with engine oil.
18.Assemble each connecting rod and gudgeon
pin to its respective piston ensuring that
bearing tag recess on connecting rod is on
correct side of piston.
19.Fit new circlips to retain gudgeon pins ensuring
they are correctly seated in their grooves.
Page 965 of 976
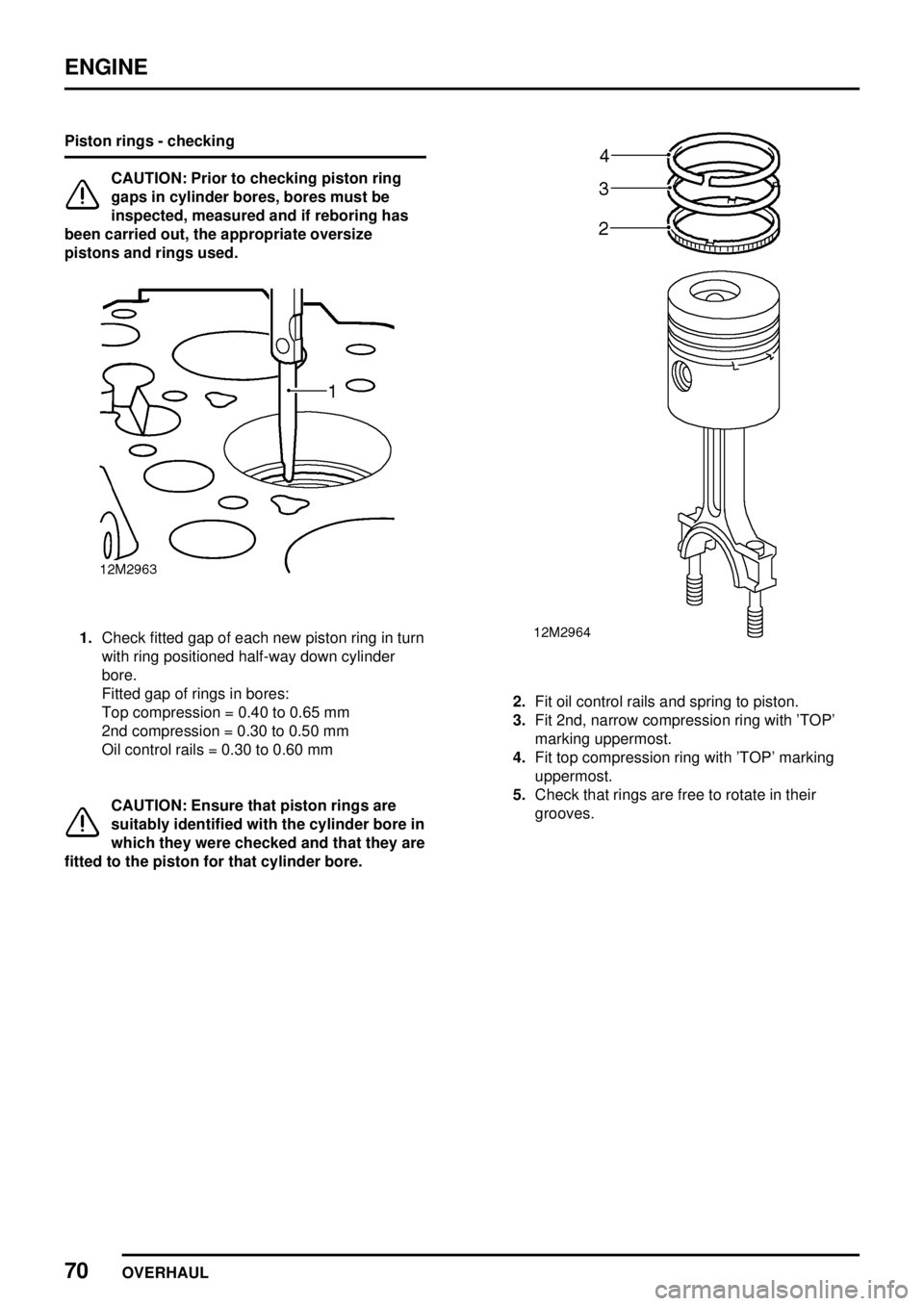
ENGINE
70
OVERHAUL Piston rings - checking
CAUTION: Prior to checking piston ring
gaps in cylinder bores, bores must be
inspected, measured and if reboring has
been carried out, the appropriate oversize
pistons and rings used.
1.Check fitted gap of each new piston ring in turn
with ring positioned half-way down cylinder
bore.
Fitted gap of rings in bores:
Top compression = 0.40 to 0.65 mm
2nd compression = 0.30 to 0.50 mm
Oil control rails = 0.30 to 0.60 mm
CAUTION: Ensure that piston rings are
suitably identified with the cylinder bore in
which they were checked and that they are
fitted to the piston for that cylinder bore.
2.Fit oil control rails and spring to piston.
3.Fit 2nd, narrow compression ring with 'TOP'
marking uppermost.
4.Fit top compression ring with 'TOP' marking
uppermost.
5.Check that rings are free to rotate in their
grooves.
Page 966 of 976
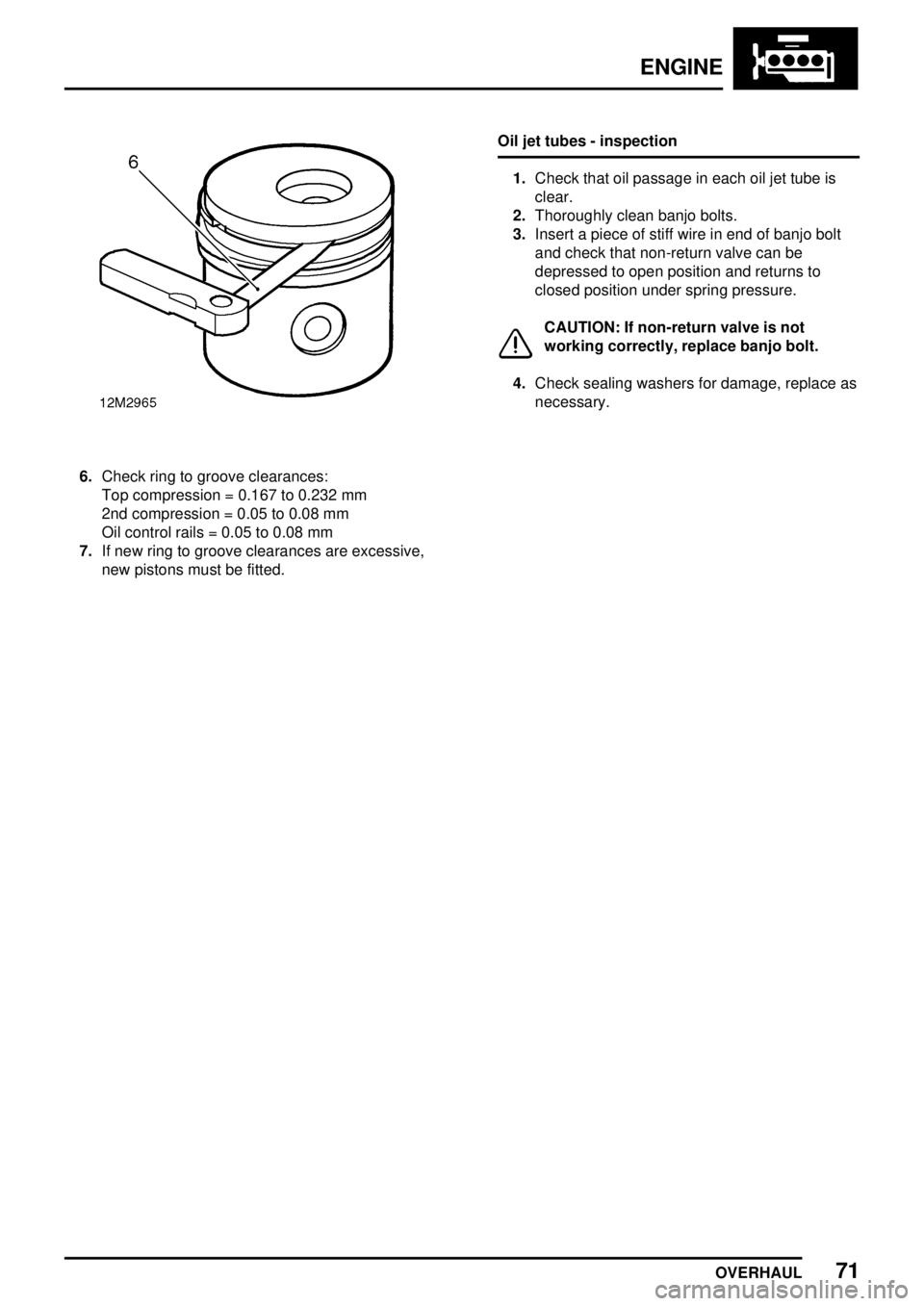
ENGINE
OVERHAUL71
6.Check ring to groove clearances:
Top compression = 0.167 to 0.232 mm
2nd compression = 0.05 to 0.08 mm
Oil control rails = 0.05 to 0.08 mm
7.If new ring to groove clearances are excessive,
new pistons must be fitted.Oil jet tubes - inspection
1.Check that oil passage in each oil jet tube is
clear.
2.Thoroughly clean banjo bolts.
3.Insert a piece of stiff wire in end of banjo bolt
and check that non-return valve can be
depressed to open position and returns to
closed position under spring pressure.
CAUTION: If non-return valve is not
working correctly, replace banjo bolt.
4.Check sealing washers for damage, replace as
necessary.
Page 967 of 976
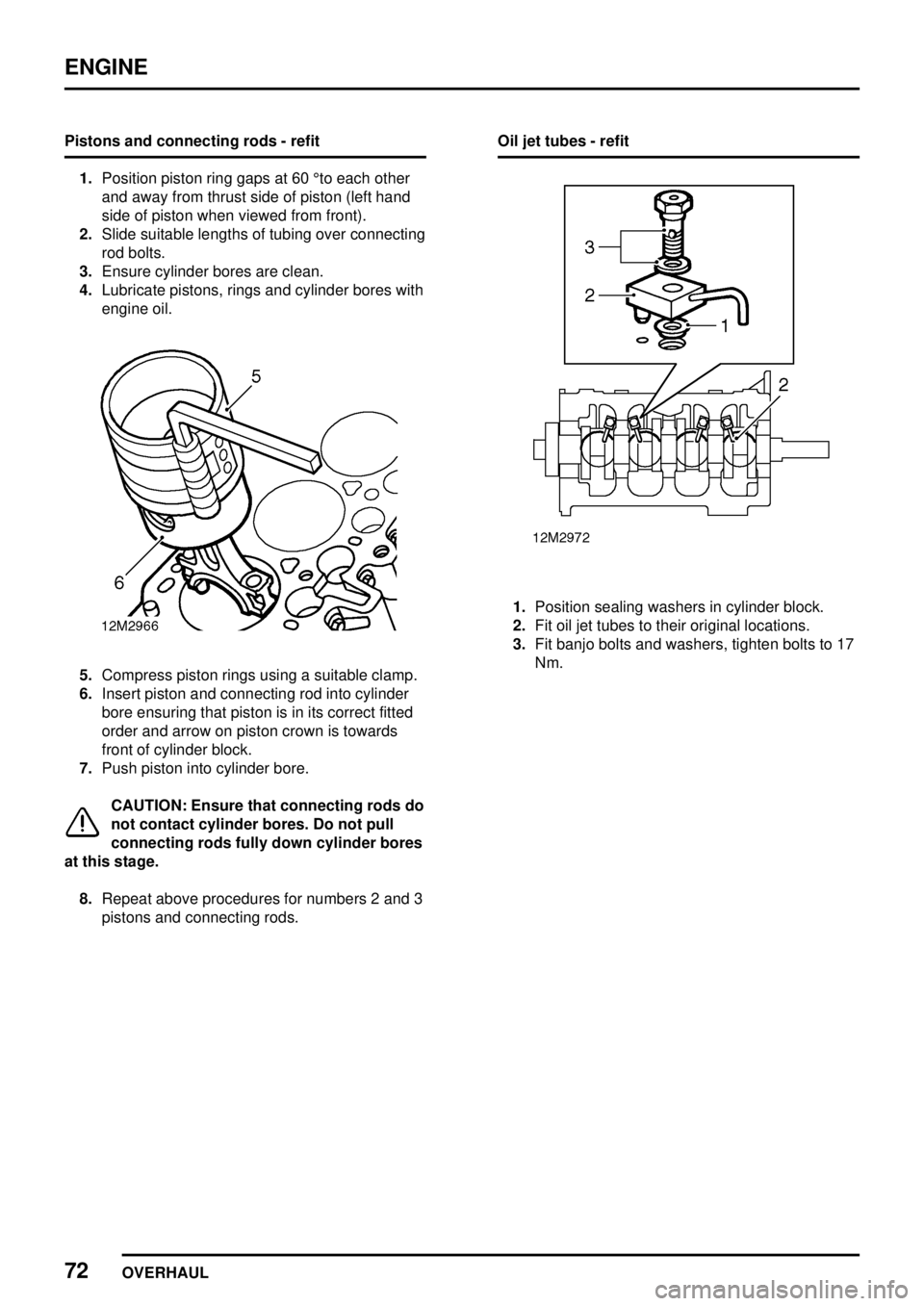
ENGINE
72
OVERHAUL Pistons and connecting rods - refit
1.Position piston ring gaps at 60°to each other
and away from thrust side of piston (left hand
side of piston when viewed from front).
2.Slide suitable lengths of tubing over connecting
rod bolts.
3.Ensure cylinder bores are clean.
4.Lubricate pistons, rings and cylinder bores with
engine oil.
5.Compress piston rings using a suitable clamp.
6.Insert piston and connecting rod into cylinder
bore ensuring that piston is in its correct fitted
order and arrow on piston crown is towards
front of cylinder block.
7.Push piston into cylinder bore.
CAUTION: Ensure that connecting rods do
not contact cylinder bores. Do not pull
connecting rods fully down cylinder bores
at this stage.
8.Repeat above procedures for numbers 2 and 3
pistons and connecting rods.Oil jet tubes - refit
1.Position sealing washers in cylinder block.
2.Fit oil jet tubes to their original locations.
3.Fit banjo bolts and washers, tighten bolts to 17
Nm.
Page 968 of 976
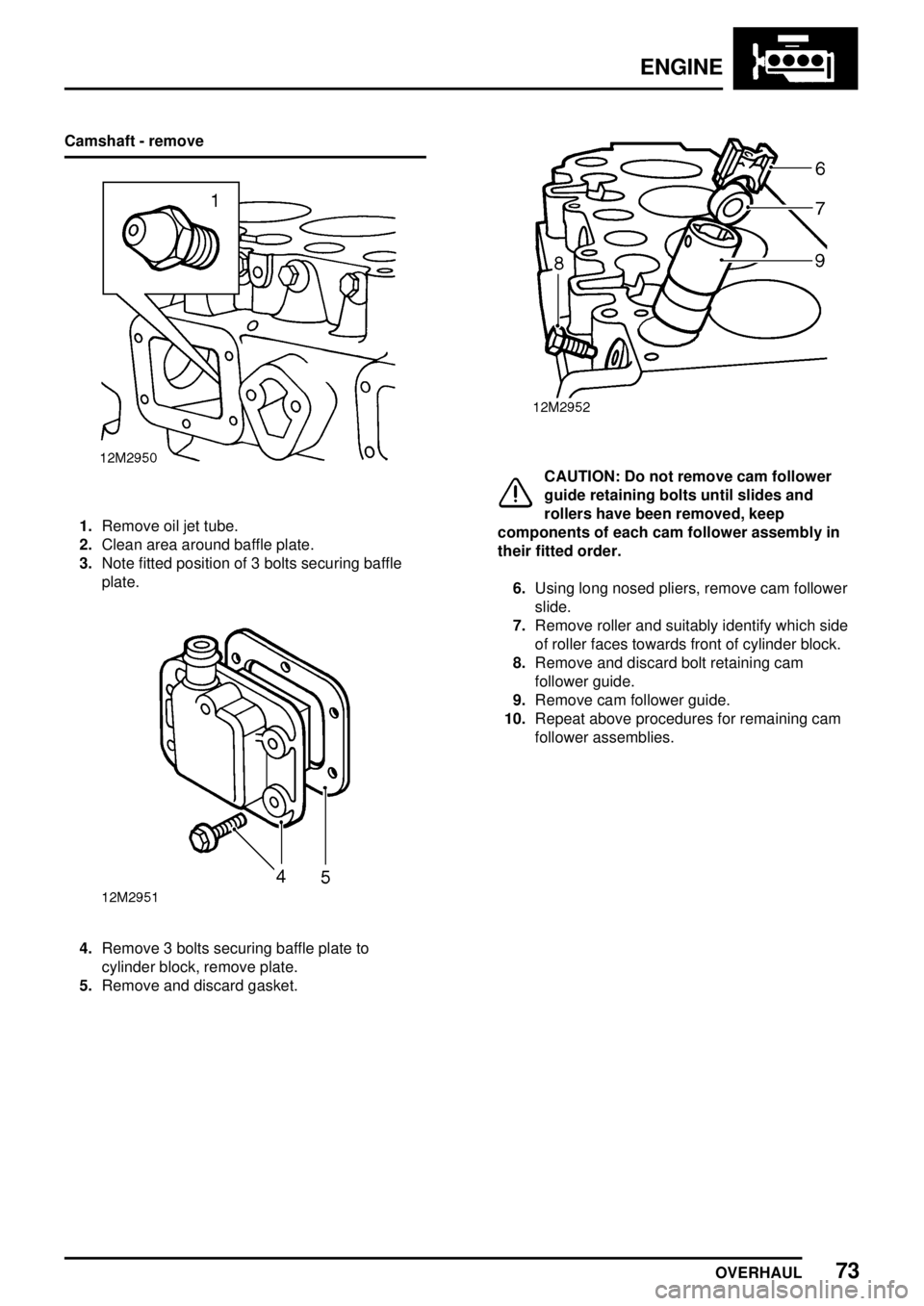
ENGINE
OVERHAUL73
Camshaft - remove
1.Remove oil jet tube.
2.Clean area around baffle plate.
3.Note fitted position of 3 bolts securing baffle
plate.
4.Remove 3 bolts securing baffle plate to
cylinder block, remove plate.
5.Remove and discard gasket.
CAUTION: Do not remove cam follower
guide retaining bolts until slides and
rollers have been removed, keep
components of each cam follower assembly in
their fitted order.
6.Using long nosed pliers, remove cam follower
slide.
7.Remove roller and suitably identify which side
of roller faces towards front of cylinder block.
8.Remove and discard bolt retaining cam
follower guide.
9.Remove cam follower guide.
10.Repeat above procedures for remaining cam
follower assemblies.
Page 969 of 976
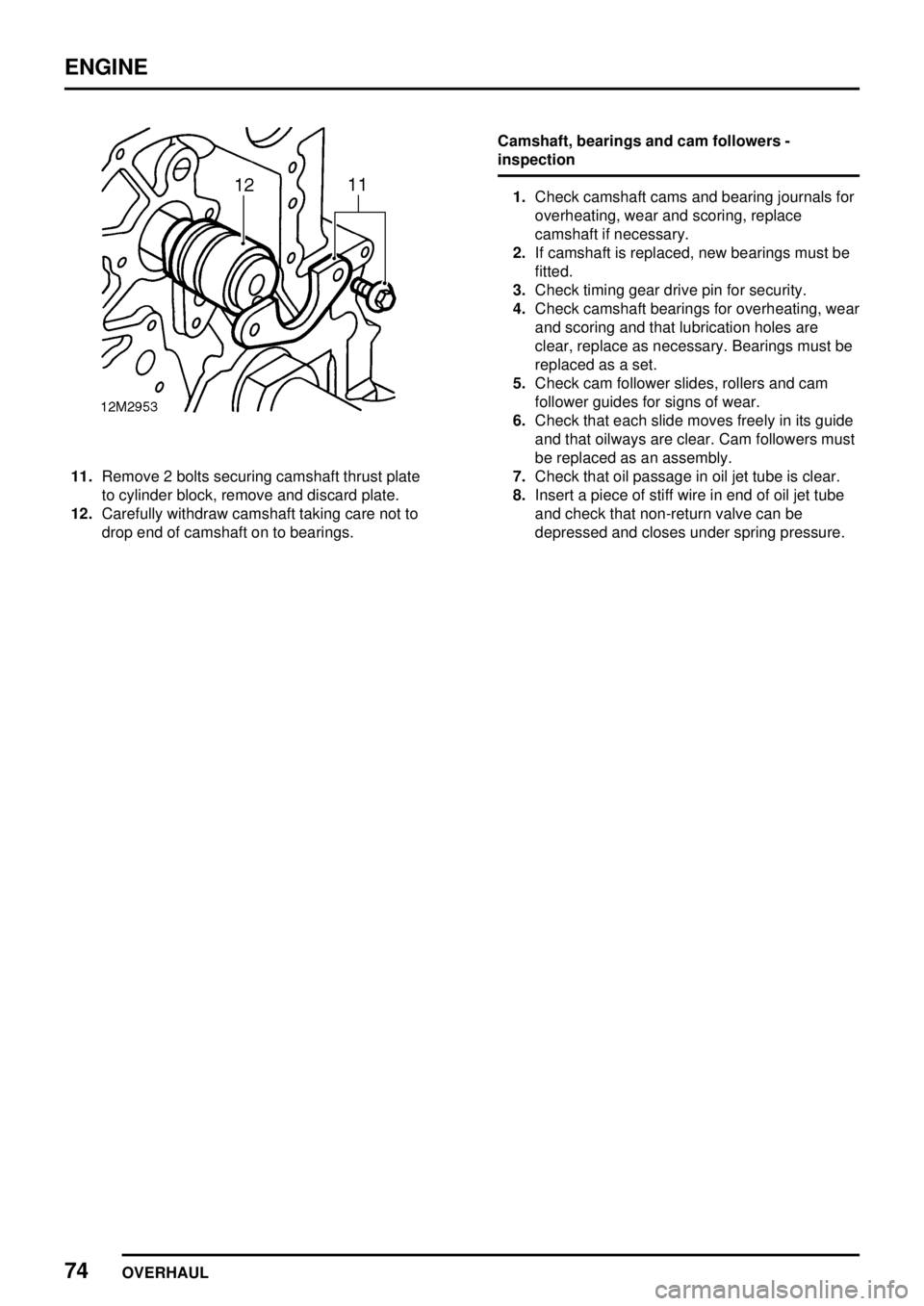
ENGINE
74
OVERHAUL
11.Remove 2 bolts securing camshaft thrust plate
to cylinder block, remove and discard plate.
12.Carefully withdraw camshaft taking care not to
drop end of camshaft on to bearings.Camshaft, bearings and cam followers -
inspection
1.Check camshaft cams and bearing journals for
overheating, wear and scoring, replace
camshaft if necessary.
2.If camshaft is replaced, new bearings must be
fitted.
3.Check timing gear drive pin for security.
4.Check camshaft bearings for overheating, wear
and scoring and that lubrication holes are
clear, replace as necessary. Bearings must be
replaced as a set.
5.Check cam follower slides, rollers and cam
follower guides for signs of wear.
6.Check that each slide moves freely in its guide
and that oilways are clear. Cam followers must
be replaced as an assembly.
7.Check that oil passage in oil jet tube is clear.
8.Insert a piece of stiff wire in end of oil jet tube
and check that non-return valve can be
depressed and closes under spring pressure.
Page 970 of 976
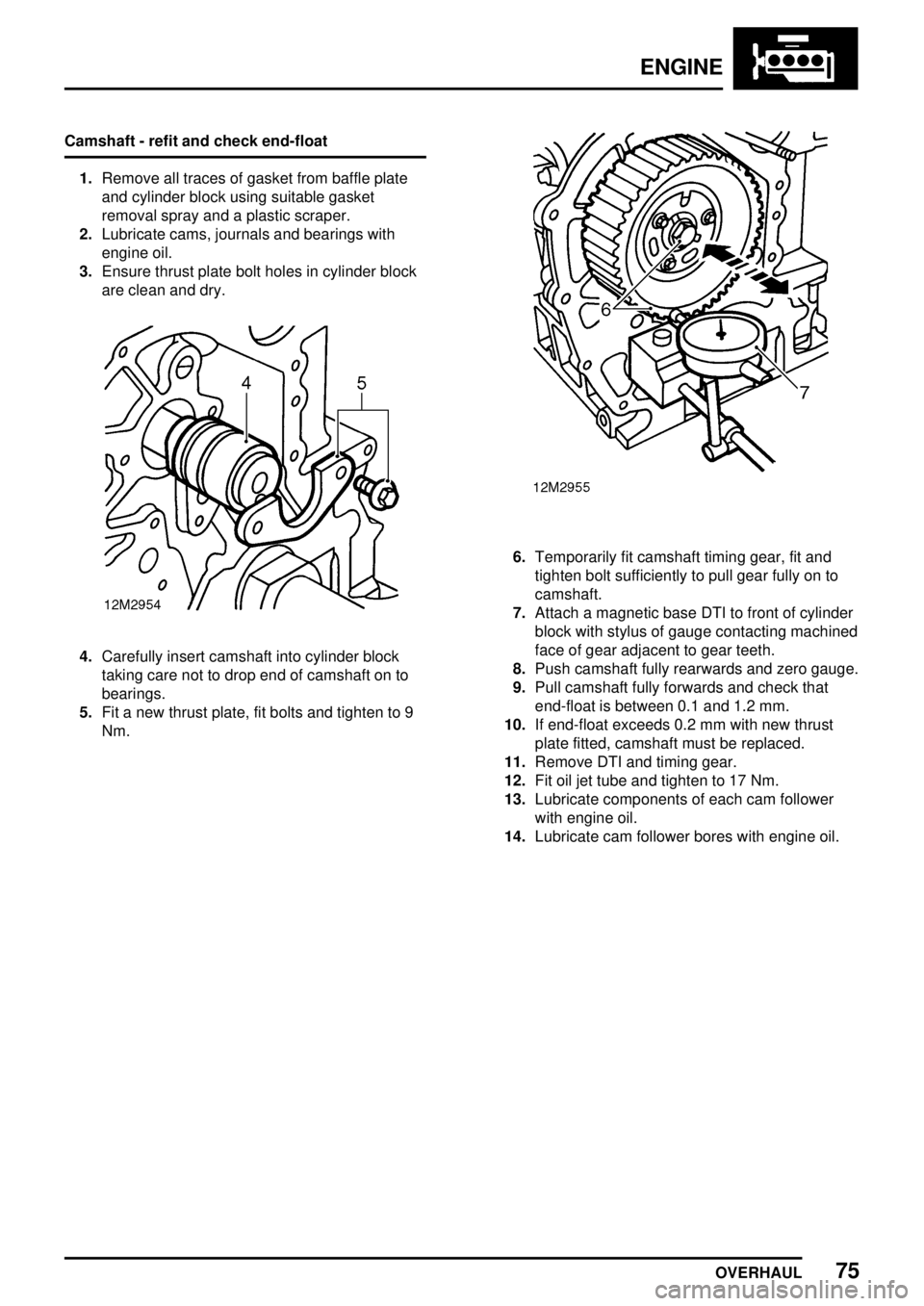
ENGINE
OVERHAUL75
Camshaft - refit and check end-float
1.Remove all traces of gasket from baffle plate
and cylinder block using suitable gasket
removal spray and a plastic scraper.
2.Lubricate cams, journals and bearings with
engine oil.
3.Ensure thrust plate bolt holes in cylinder block
are clean and dry.
4.Carefully insert camshaft into cylinder block
taking care not to drop end of camshaft on to
bearings.
5.Fit a new thrust plate, fit bolts and tighten to 9
Nm.
6.Temporarily fit camshaft timing gear, fit and
tighten bolt sufficiently to pull gear fully on to
camshaft.
7.Attach a magnetic base DTI to front of cylinder
block with stylus of gauge contacting machined
face of gear adjacent to gear teeth.
8.Push camshaft fully rearwards and zero gauge.
9.Pull camshaft fully forwards and check that
end-float is between 0.1 and 1.2 mm.
10.If end-float exceeds 0.2 mm with new thrust
plate fitted, camshaft must be replaced.
11.Remove DTI and timing gear.
12.Fit oil jet tube and tighten to 17 Nm.
13.Lubricate components of each cam follower
with engine oil.
14.Lubricate cam follower bores with engine oil.