compression ratio LAND ROVER DISCOVERY 1995 User Guide
[x] Cancel search | Manufacturer: LAND ROVER, Model Year: 1995, Model line: DISCOVERY, Model: LAND ROVER DISCOVERY 1995Pages: 873, PDF Size: 12.89 MB
Page 117 of 873
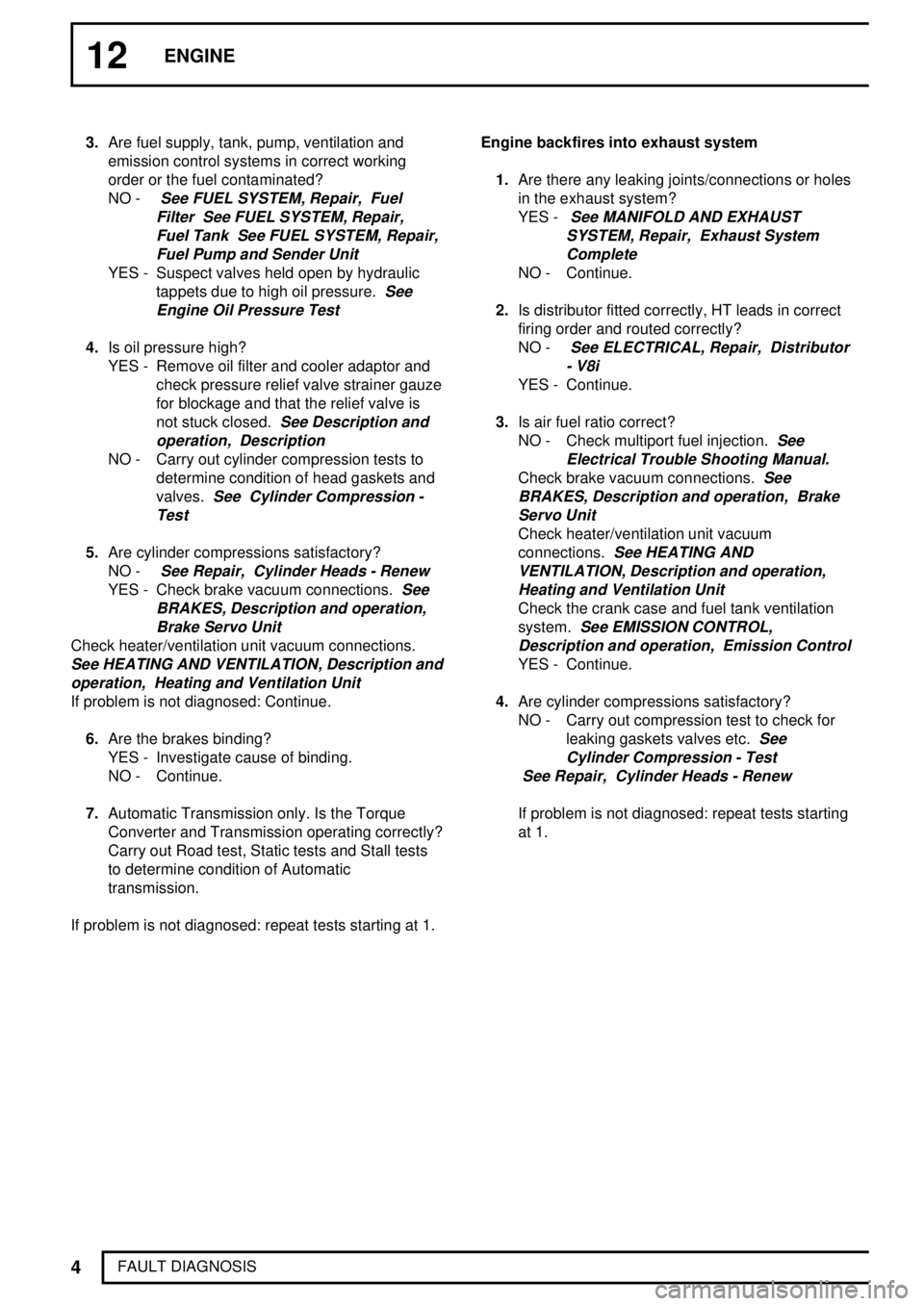
12ENGINE
4
FAULT DIAGNOSIS 3.Are fuel supply, tank, pump, ventilation and
emission control systems in correct working
order or the fuel contaminated?
NO -
See FUEL SYSTEM, Repair, Fuel
Filter See FUEL SYSTEM, Repair,
Fuel Tank See FUEL SYSTEM, Repair,
Fuel Pump and Sender Unit
YES - Suspect valves held open by hydraulic
tappets due to high oil pressure.
See
Engine Oil Pressure Test
4.Is oil pressure high?
YES - Remove oil filter and cooler adaptor and
check pressure relief valve strainer gauze
for blockage and that the relief valve is
not stuck closed.
See Description and
operation, Description
NO - Carry out cylinder compression tests to
determine condition of head gaskets and
valves.
See Cylinder Compression -
Test
5.Are cylinder compressions satisfactory?
NO -
See Repair, Cylinder Heads - Renew
YES - Check brake vacuum connections.See
BRAKES, Description and operation,
Brake Servo Unit
Check heater/ventilation unit vacuum connections.
See HEATING AND VENTILATION, Description and
operation, Heating and Ventilation Unit
If problem is not diagnosed: Continue.
6.Are the brakes binding?
YES - Investigate cause of binding.
NO - Continue.
7.Automatic Transmission only. Is the Torque
Converter and Transmission operating correctly?
Carry out Road test, Static tests and Stall tests
to determine condition of Automatic
transmission.
If problem is not diagnosed: repeat tests starting at 1.Engine backfires into exhaust system
1.Are there any leaking joints/connections or holes
in the exhaust system?
YES -
See MANIFOLD AND EXHAUST
SYSTEM, Repair, Exhaust System
Complete
NO - Continue.
2.Is distributor fitted correctly, HT leads in correct
firing order and routed correctly?
NO -
See ELECTRICAL, Repair, Distributor
- V8i
YES - Continue.
3.Is air fuel ratio correct?
NO - Check multiport fuel injection.
See
Electrical Trouble Shooting Manual.
Check brake vacuum connections.See
BRAKES, Description and operation, Brake
Servo Unit
Check heater/ventilation unit vacuum
connections.
See HEATING AND
VENTILATION, Description and operation,
Heating and Ventilation Unit
Check the crank case and fuel tank ventilation
system.
See EMISSION CONTROL,
Description and operation, Emission Control
YES - Continue.
4.Are cylinder compressions satisfactory?
NO - Carry out compression test to check for
leaking gaskets valves etc.
See
Cylinder Compression - Test
See Repair, Cylinder Heads - Renew
If problem is not diagnosed: repeat tests starting
at 1.
Page 118 of 873
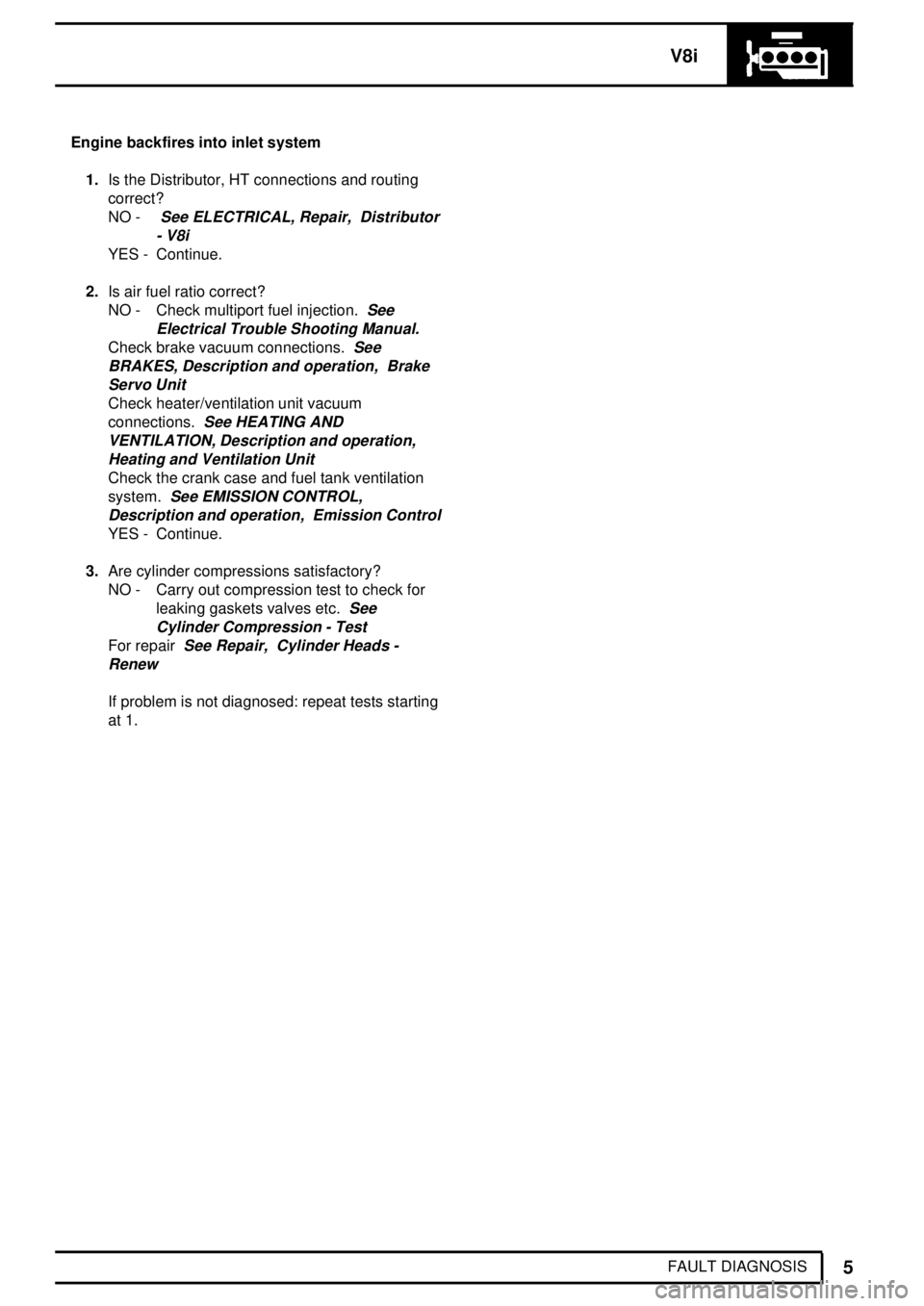
V8i
5
FAULT DIAGNOSIS Engine backfires into inlet system
1.Is the Distributor, HT connections and routing
correct?
NO -
See ELECTRICAL, Repair, Distributor
- V8i
YES - Continue.
2.Is air fuel ratio correct?
NO - Check multiport fuel injection.
See
Electrical Trouble Shooting Manual.
Check brake vacuum connections.See
BRAKES, Description and operation, Brake
Servo Unit
Check heater/ventilation unit vacuum
connections.
See HEATING AND
VENTILATION, Description and operation,
Heating and Ventilation Unit
Check the crank case and fuel tank ventilation
system.
See EMISSION CONTROL,
Description and operation, Emission Control
YES - Continue.
3.Are cylinder compressions satisfactory?
NO - Carry out compression test to check for
leaking gaskets valves etc.
See
Cylinder Compression - Test
For repairSee Repair, Cylinder Heads -
Renew
If problem is not diagnosed: repeat tests starting
at 1.
Page 130 of 873
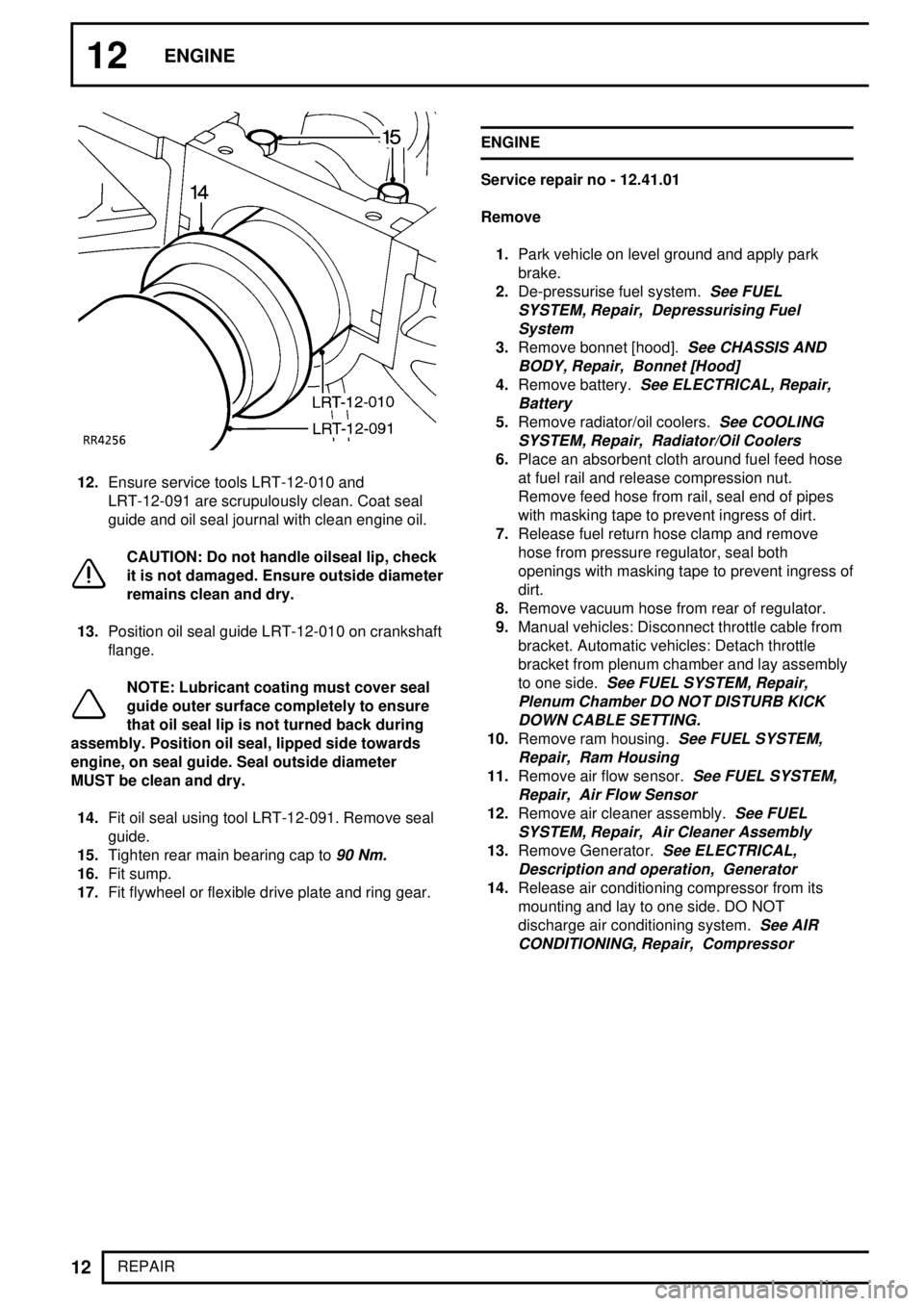
12ENGINE
12
REPAIR
12.Ensure service tools LRT-12-010 and
LRT-12-091 are scrupulously clean. Coat seal
guide and oil seal journal with clean engine oil.
CAUTION: Do not handle oilseal lip, check
it is not damaged. Ensure outside diameter
remains clean and dry.
13.Position oil seal guide LRT-12-010 on crankshaft
flange.
NOTE: Lubricant coating must cover seal
guide outer surface completely to ensure
that oil seal lip is not turned back during
assembly. Position oil seal, lipped side towards
engine, on seal guide. Seal outside diameter
MUST be clean and dry.
14.Fit oil seal using tool LRT-12-091. Remove seal
guide.
15.Tighten rear main bearing cap to
90 Nm.
16.Fit sump.
17.Fit flywheel or flexible drive plate and ring gear.ENGINE
Service repair no - 12.41.01
Remove
1.Park vehicle on level ground and apply park
brake.
2.De-pressurise fuel system.
See FUEL
SYSTEM, Repair, Depressurising Fuel
System
3.Remove bonnet [hood].See CHASSIS AND
BODY, Repair, Bonnet [Hood]
4.Remove battery.See ELECTRICAL, Repair,
Battery
5.Remove radiator/oil coolers.See COOLING
SYSTEM, Repair, Radiator/Oil Coolers
6.Place an absorbent cloth around fuel feed hose
at fuel rail and release compression nut.
Remove feed hose from rail, seal end of pipes
with masking tape to prevent ingress of dirt.
7.Release fuel return hose clamp and remove
hose from pressure regulator, seal both
openings with masking tape to prevent ingress of
dirt.
8.Remove vacuum hose from rear of regulator.
9.Manual vehicles: Disconnect throttle cable from
bracket. Automatic vehicles: Detach throttle
bracket from plenum chamber and lay assembly
to one side.
See FUEL SYSTEM, Repair,
Plenum Chamber DO NOT DISTURB KICK
DOWN CABLE SETTING.
10.Remove ram housing.See FUEL SYSTEM,
Repair, Ram Housing
11.Remove air flow sensor.See FUEL SYSTEM,
Repair, Air Flow Sensor
12.Remove air cleaner assembly.See FUEL
SYSTEM, Repair, Air Cleaner Assembly
13.Remove Generator.See ELECTRICAL,
Description and operation, Generator
14.Release air conditioning compressor from its
mounting and lay to one side. DO NOT
discharge air conditioning system.
See AIR
CONDITIONING, Repair, Compressor
Page 152 of 873
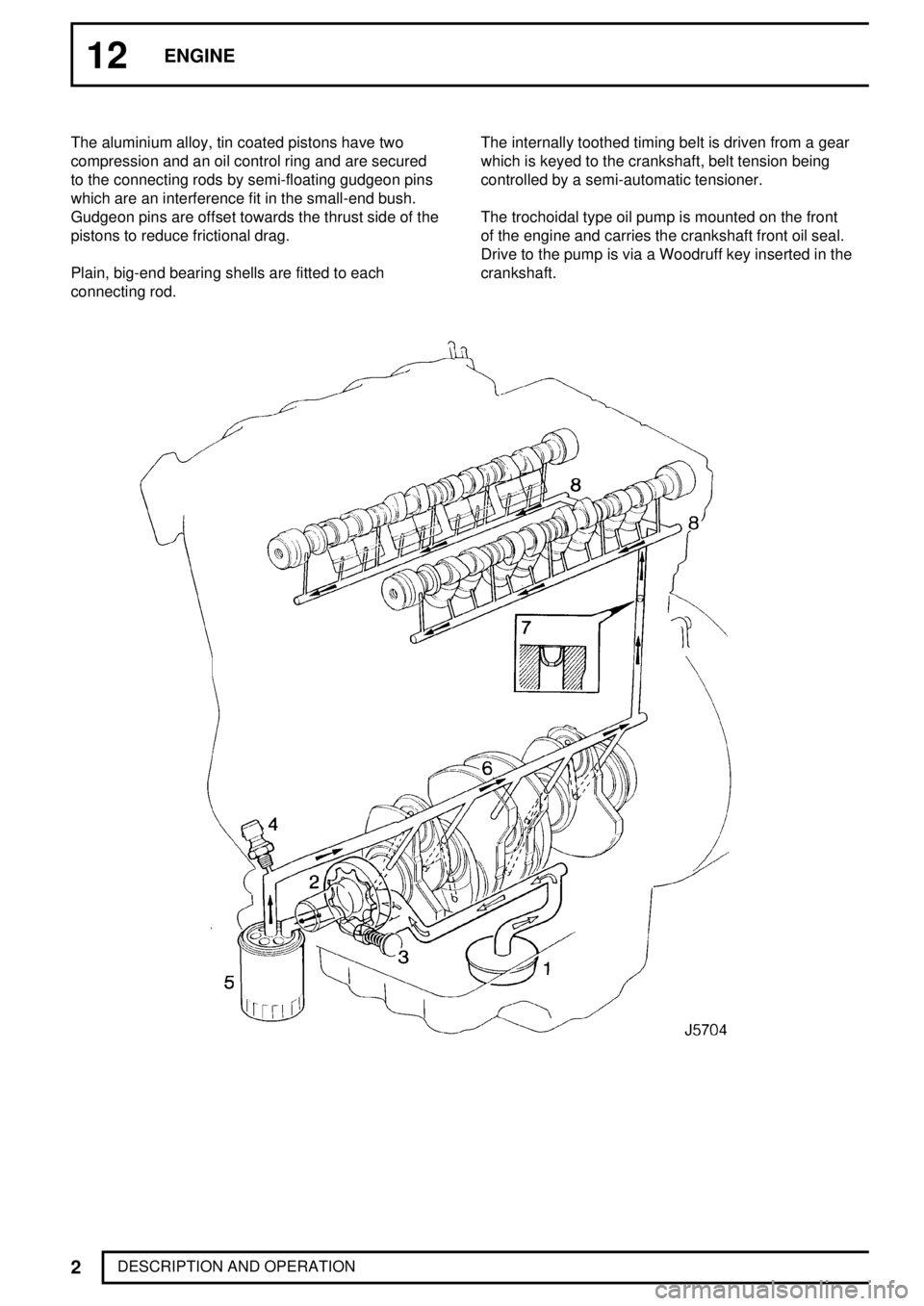
12ENGINE
2
DESCRIPTION AND OPERATION The aluminium alloy, tin coated pistons have two
compression and an oil control ring and are secured
to the connecting rods by semi-floating gudgeon pins
which are an interference fit in the small-end bush.
Gudgeon pins are offset towards the thrust side of the
pistons to reduce frictional drag.
Plain, big-end bearing shells are fitted to each
connecting rod.The internally toothed timing belt is driven from a gear
which is keyed to the crankshaft, belt tension being
controlled by a semi-automatic tensioner.
The trochoidal type oil pump is mounted on the front
of the engine and carries the crankshaft front oil seal.
Drive to the pump is via a Woodruff key inserted in the
crankshaft.
Page 154 of 873
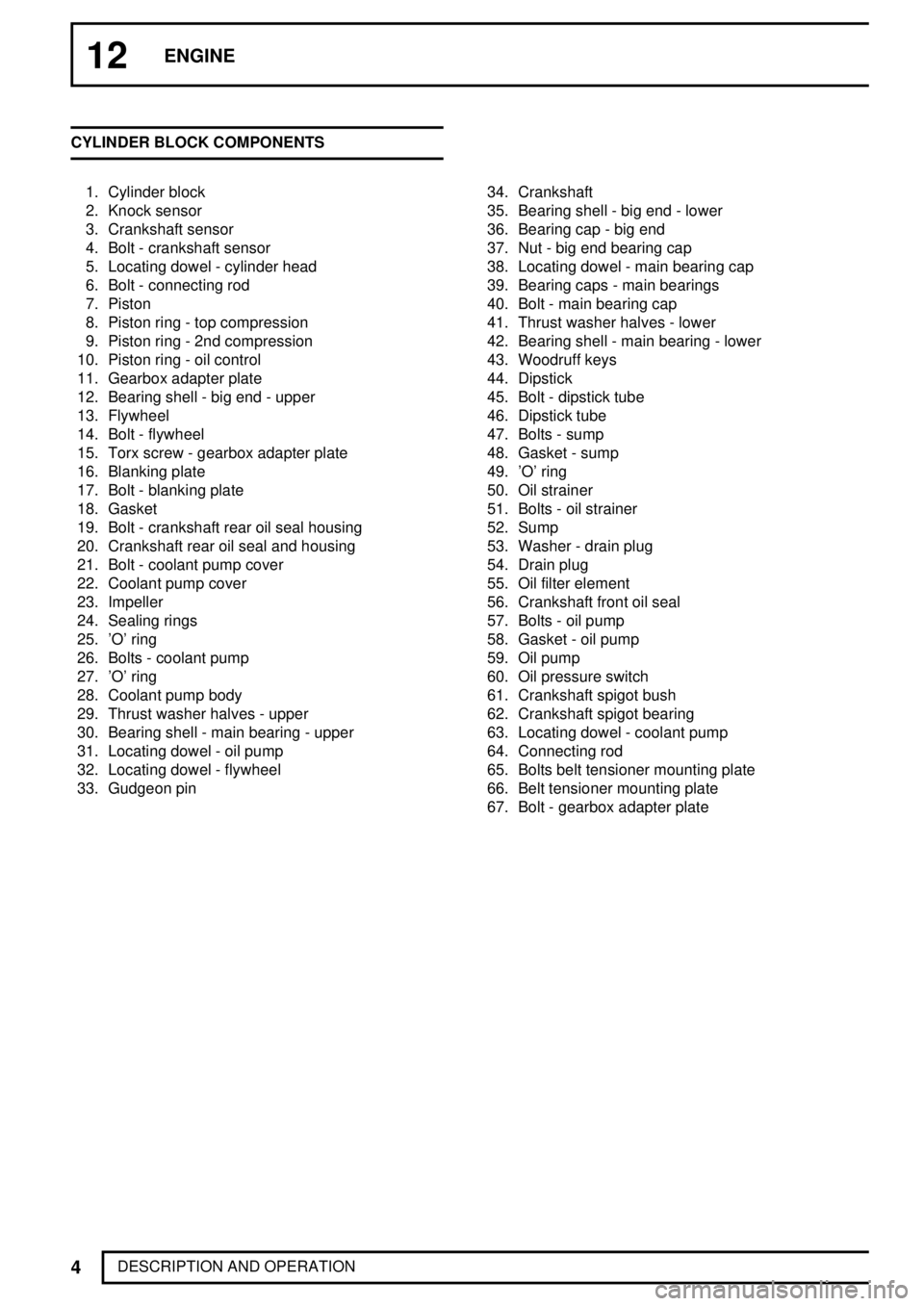
12ENGINE
4
DESCRIPTION AND OPERATION CYLINDER BLOCK COMPONENTS
1. Cylinder block
2. Knock sensor
3. Crankshaft sensor
4. Bolt - crankshaft sensor
5. Locating dowel - cylinder head
6. Bolt - connecting rod
7. Piston
8. Piston ring - top compression
9. Piston ring - 2nd compression
10. Piston ring - oil control
11. Gearbox adapter plate
12. Bearing shell - big end - upper
13. Flywheel
14. Bolt - flywheel
15. Torx screw - gearbox adapter plate
16. Blanking plate
17. Bolt - blanking plate
18. Gasket
19. Bolt - crankshaft rear oil seal housing
20. Crankshaft rear oil seal and housing
21. Bolt - coolant pump cover
22. Coolant pump cover
23. Impeller
24. Sealing rings
25. 'O' ring
26. Bolts - coolant pump
27. 'O' ring
28. Coolant pump body
29. Thrust washer halves - upper
30. Bearing shell - main bearing - upper
31. Locating dowel - oil pump
32. Locating dowel - flywheel
33. Gudgeon pin34. Crankshaft
35. Bearing shell - big end - lower
36. Bearing cap - big end
37. Nut - big end bearing cap
38. Locating dowel - main bearing cap
39. Bearing caps - main bearings
40. Bolt - main bearing cap
41. Thrust washer halves - lower
42. Bearing shell - main bearing - lower
43. Woodruff keys
44. Dipstick
45. Bolt - dipstick tube
46. Dipstick tube
47. Bolts - sump
48. Gasket - sump
49. 'O' ring
50. Oil strainer
51. Bolts - oil strainer
52. Sump
53. Washer - drain plug
54. Drain plug
55. Oil filter element
56. Crankshaft front oil seal
57. Bolts - oil pump
58. Gasket - oil pump
59. Oil pump
60. Oil pressure switch
61. Crankshaft spigot bush
62. Crankshaft spigot bearing
63. Locating dowel - coolant pump
64. Connecting rod
65. Bolts belt tensioner mounting plate
66. Belt tensioner mounting plate
67. Bolt - gearbox adapter plate
Page 209 of 873
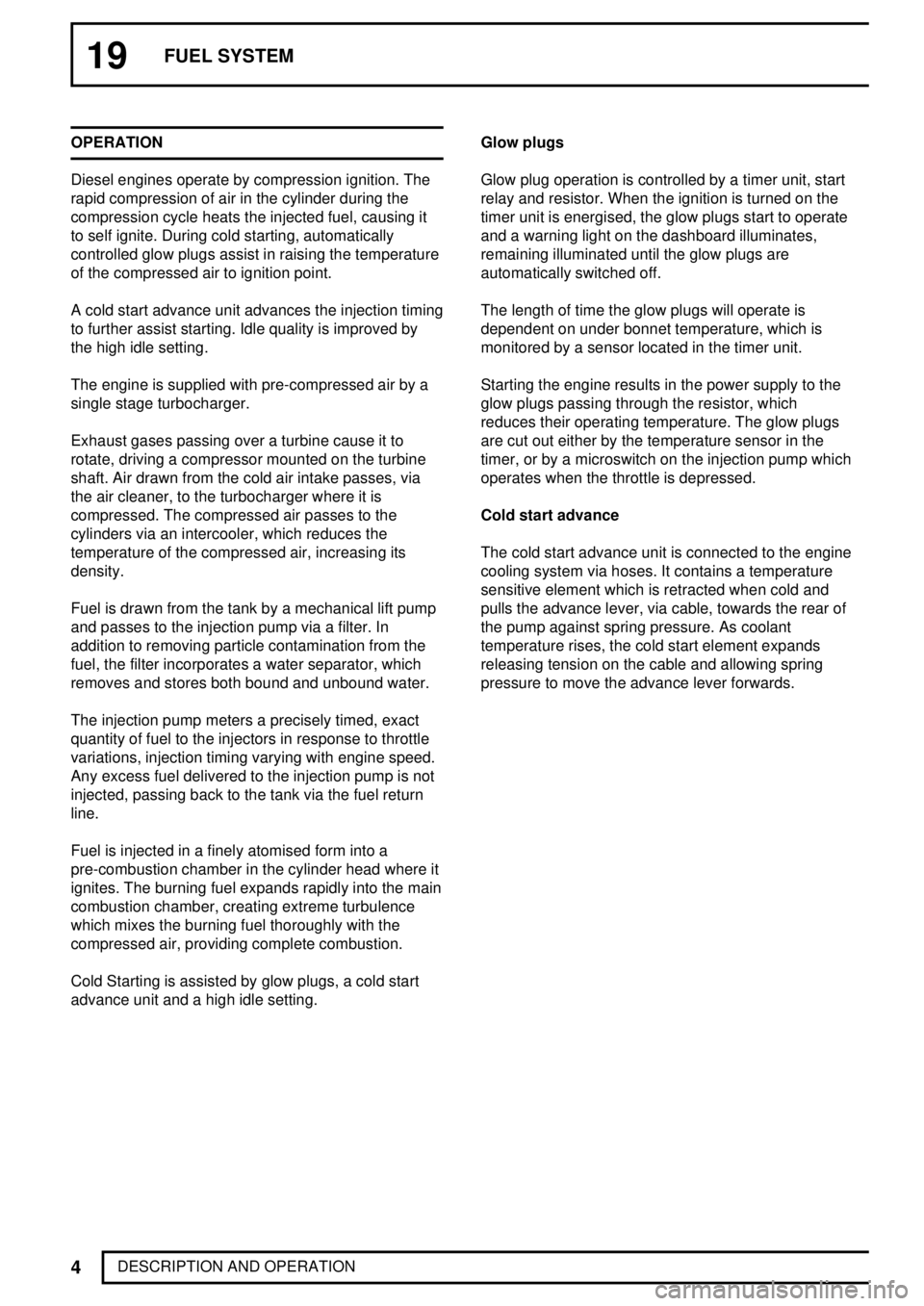
19FUEL SYSTEM
4
DESCRIPTION AND OPERATION OPERATION
Diesel engines operate by compression ignition. The
rapid compression of air in the cylinder during the
compression cycle heats the injected fuel, causing it
to self ignite. During cold starting, automatically
controlled glow plugs assist in raising the temperature
of the compressed air to ignition point.
A cold start advance unit advances the injection timing
to further assist starting. Idle quality is improved by
the high idle setting.
The engine is supplied with pre-compressed air by a
single stage turbocharger.
Exhaust gases passing over a turbine cause it to
rotate, driving a compressor mounted on the turbine
shaft. Air drawn from the cold air intake passes, via
the air cleaner, to the turbocharger where it is
compressed. The compressed air passes to the
cylinders via an intercooler, which reduces the
temperature of the compressed air, increasing its
density.
Fuel is drawn from the tank by a mechanical lift pump
and passes to the injection pump via a filter. In
addition to removing particle contamination from the
fuel, the filter incorporates a water separator, which
removes and stores both bound and unbound water.
The injection pump meters a precisely timed, exact
quantity of fuel to the injectors in response to throttle
variations, injection timing varying with engine speed.
Any excess fuel delivered to the injection pump is not
injected, passing back to the tank via the fuel return
line.
Fuel is injected in a finely atomised form into a
pre-combustion chamber in the cylinder head where it
ignites. The burning fuel expands rapidly into the main
combustion chamber, creating extreme turbulence
which mixes the burning fuel thoroughly with the
compressed air, providing complete combustion.
Cold Starting is assisted by glow plugs, a cold start
advance unit and a high idle setting.Glow plugs
Glow plug operation is controlled by a timer unit, start
relay and resistor. When the ignition is turned on the
timer unit is energised, the glow plugs start to operate
and a warning light on the dashboard illuminates,
remaining illuminated until the glow plugs are
automatically switched off.
The length of time the glow plugs will operate is
dependent on under bonnet temperature, which is
monitored by a sensor located in the timer unit.
Starting the engine results in the power supply to the
glow plugs passing through the resistor, which
reduces their operating temperature. The glow plugs
are cut out either by the temperature sensor in the
timer, or by a microswitch on the injection pump which
operates when the throttle is depressed.
Cold start advance
The cold start advance unit is connected to the engine
cooling system via hoses. It contains a temperature
sensitive element which is retracted when cold and
pulls the advance lever, via cable, towards the rear of
the pump against spring pressure. As coolant
temperature rises, the cold start element expands
releasing tension on the cable and allowing spring
pressure to move the advance lever forwards.
Page 276 of 873
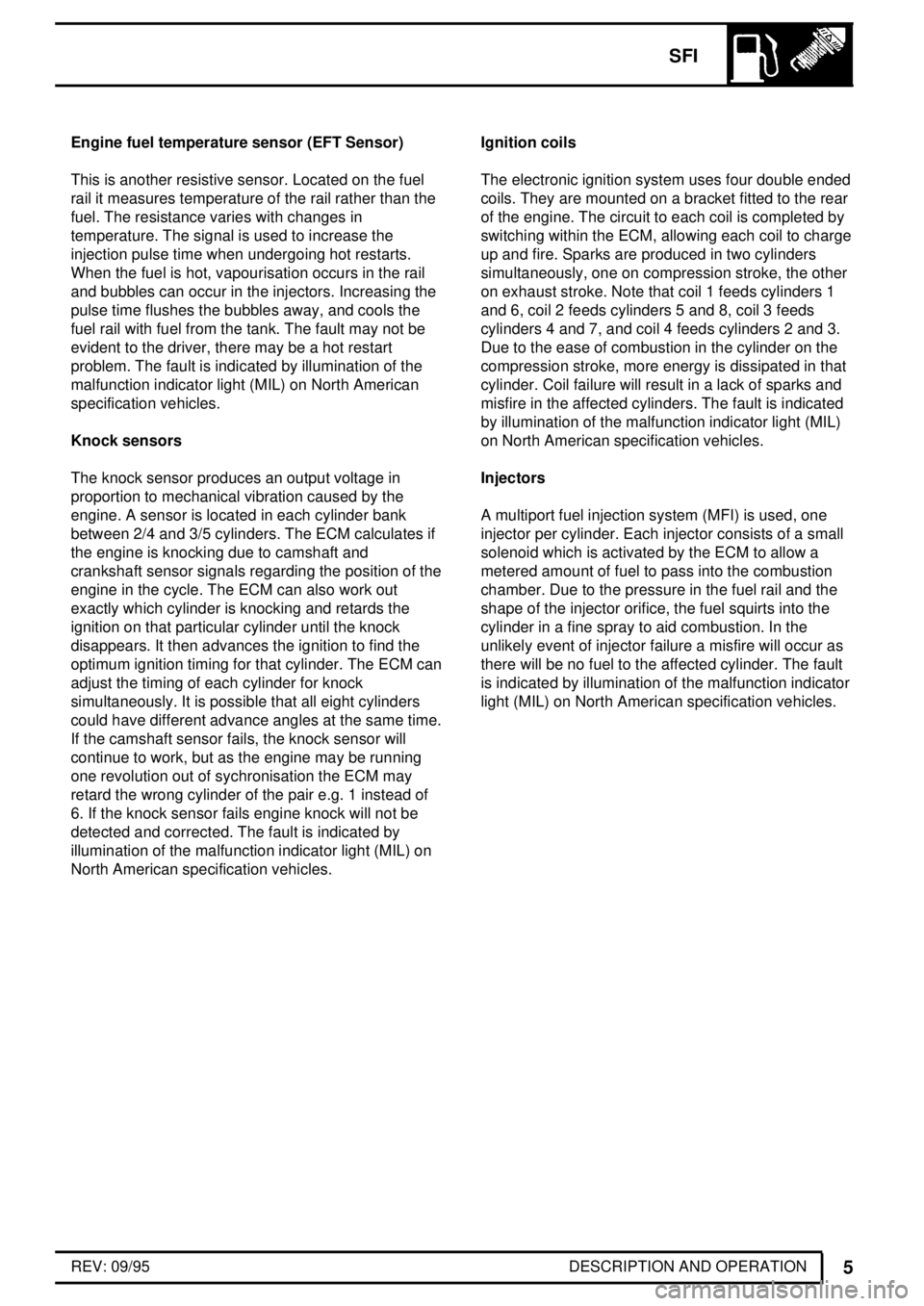
SFI
5
DESCRIPTION AND OPERATION REV: 09/95 Engine fuel temperature sensor (EFT Sensor)
This is another resistive sensor. Located on the fuel
rail it measures temperature of the rail rather than the
fuel. The resistance varies with changes in
temperature. The signal is used to increase the
injection pulse time when undergoing hot restarts.
When the fuel is hot, vapourisation occurs in the rail
and bubbles can occur in the injectors. Increasing the
pulse time flushes the bubbles away, and cools the
fuel rail with fuel from the tank. The fault may not be
evident to the driver, there may be a hot restart
problem. The fault is indicated by illumination of the
malfunction indicator light (MIL) on North American
specification vehicles.
Knock sensors
The knock sensor produces an output voltage in
proportion to mechanical vibration caused by the
engine. A sensor is located in each cylinder bank
between 2/4 and 3/5 cylinders. The ECM calculates if
the engine is knocking due to camshaft and
crankshaft sensor signals regarding the position of the
engine in the cycle. The ECM can also work out
exactly which cylinder is knocking and retards the
ignition on that particular cylinder until the knock
disappears. It then advances the ignition to find the
optimum ignition timing for that cylinder. The ECM can
adjust the timing of each cylinder for knock
simultaneously. It is possible that all eight cylinders
could have different advance angles at the same time.
If the camshaft sensor fails, the knock sensor will
continue to work, but as the engine may be running
one revolution out of sychronisation the ECM may
retard the wrong cylinder of the pair e.g. 1 instead of
6. If the knock sensor fails engine knock will not be
detected and corrected. The fault is indicated by
illumination of the malfunction indicator light (MIL) on
North American specification vehicles.Ignition coils
The electronic ignition system uses four double ended
coils. They are mounted on a bracket fitted to the rear
of the engine. The circuit to each coil is completed by
switching within the ECM, allowing each coil to charge
up and fire. Sparks are produced in two cylinders
simultaneously, one on compression stroke, the other
on exhaust stroke. Note that coil 1 feeds cylinders 1
and 6, coil 2 feeds cylinders 5 and 8, coil 3 feeds
cylinders 4 and 7, and coil 4 feeds cylinders 2 and 3.
Due to the ease of combustion in the cylinder on the
compression stroke, more energy is dissipated in that
cylinder. Coil failure will result in a lack of sparks and
misfire in the affected cylinders. The fault is indicated
by illumination of the malfunction indicator light (MIL)
on North American specification vehicles.
Injectors
A multiport fuel injection system (MFI) is used, one
injector per cylinder. Each injector consists of a small
solenoid which is activated by the ECM to allow a
metered amount of fuel to pass into the combustion
chamber. Due to the pressure in the fuel rail and the
shape of the injector orifice, the fuel squirts into the
cylinder in a fine spray to aid combustion. In the
unlikely event of injector failure a misfire will occur as
there will be no fuel to the affected cylinder. The fault
is indicated by illumination of the malfunction indicator
light (MIL) on North American specification vehicles.
Page 520 of 873
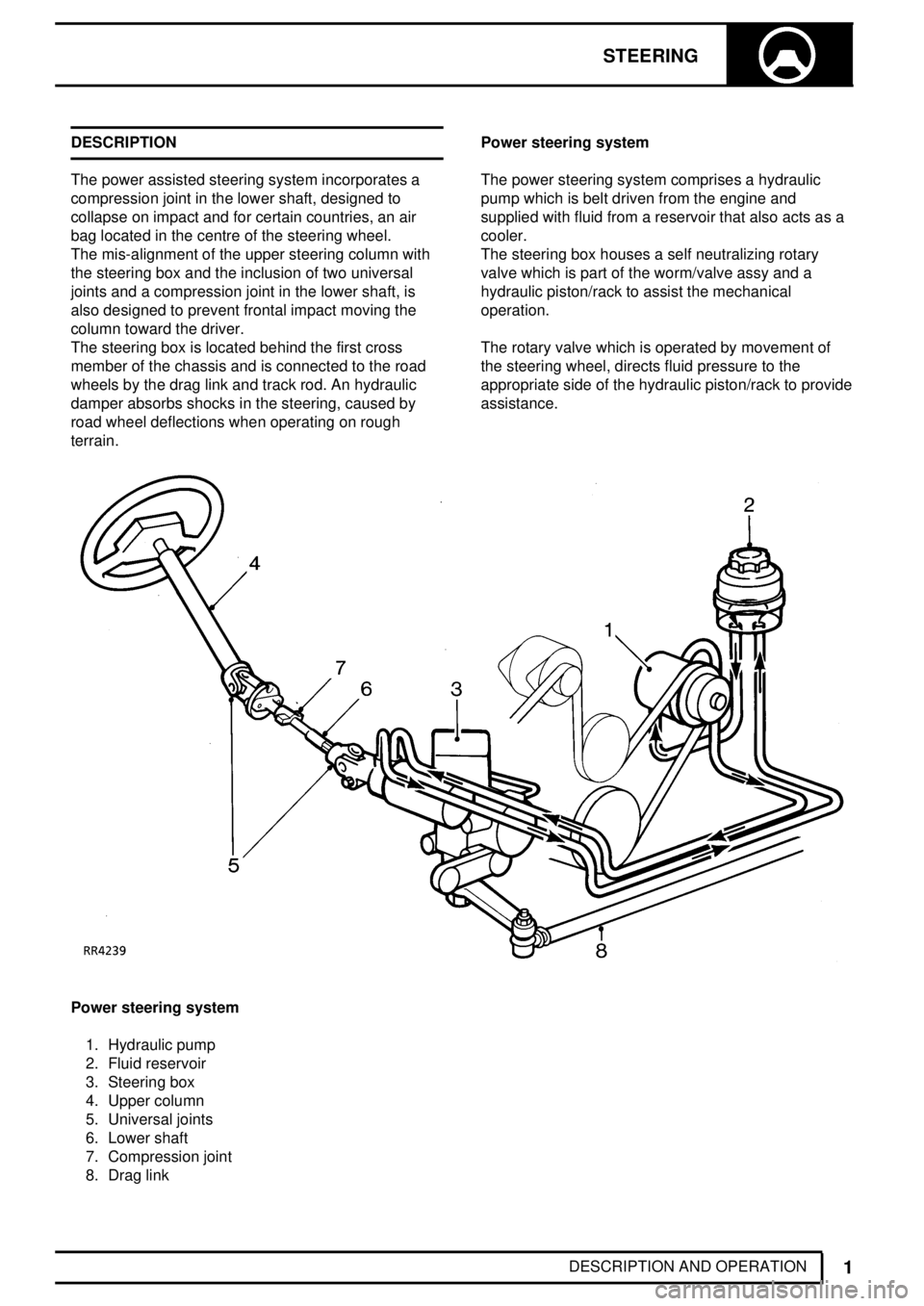
STEERING
1
DESCRIPTION AND OPERATION DESCRIPTION
The power assisted steering system incorporates a
compression joint in the lower shaft, designed to
collapse on impact and for certain countries, an air
bag located in the centre of the steering wheel.
The mis-alignment of the upper steering column with
the steering box and the inclusion of two universal
joints and a compression joint in the lower shaft, is
also designed to prevent frontal impact moving the
column toward the driver.
The steering box is located behind the first cross
member of the chassis and is connected to the road
wheels by the drag link and track rod. An hydraulic
damper absorbs shocks in the steering, caused by
road wheel deflections when operating on rough
terrain.Power steering system
The power steering system comprises a hydraulic
pump which is belt driven from the engine and
supplied with fluid from a reservoir that also acts as a
cooler.
The steering box houses a self neutralizing rotary
valve which is part of the worm/valve assy and a
hydraulic piston/rack to assist the mechanical
operation.
The rotary valve which is operated by movement of
the steering wheel, directs fluid pressure to the
appropriate side of the hydraulic piston/rack to provide
assistance.
Power steering system
1. Hydraulic pump
2. Fluid reservoir
3. Steering box
4. Upper column
5. Universal joints
6. Lower shaft
7. Compression joint
8. Drag link
Page 522 of 873

STEERING
3
DESCRIPTION AND OPERATION Steering column components
1. Upper shroud
2. Column harness
3. Cruise control switch (if fitted)
4. Steering wheel and nut
5. Rotary coupler
6. Column switch
7. Shear bolts
8. Switch saddle
9. Upper steering column
10. Universal joint
11. Universal joint bolt
12. Steering column lock assembly13. Lower shroud
14. Column lock/ignition
15. Air bag mounting bracket (if fitted)
16. Air bag module
17. Steering pad (non-airbag)
18. Lower shaft
19. Rubber coupling
20. Compression joint
21. Universal joint
22. Universal joint bolt
Page 529 of 873
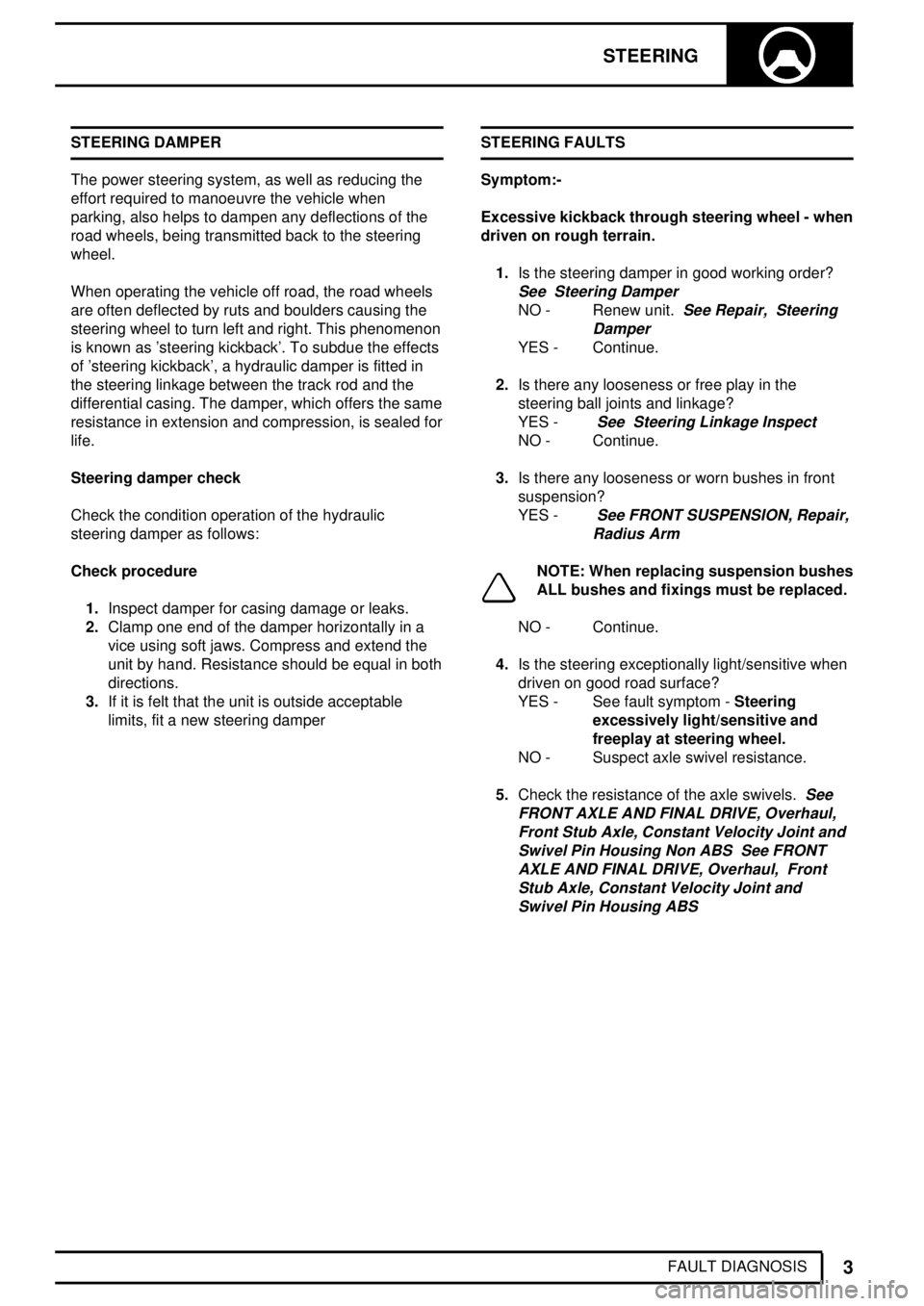
STEERING
3
FAULT DIAGNOSIS STEERING DAMPER
The power steering system, as well as reducing the
effort required to manoeuvre the vehicle when
parking, also helps to dampen any deflections of the
road wheels, being transmitted back to the steering
wheel.
When operating the vehicle off road, the road wheels
are often deflected by ruts and boulders causing the
steering wheel to turn left and right. This phenomenon
is known as 'steering kickback'. To subdue the effects
of 'steering kickback', a hydraulic damper is fitted in
the steering linkage between the track rod and the
differential casing. The damper, which offers the same
resistance in extension and compression, is sealed for
life.
Steering damper check
Check the condition operation of the hydraulic
steering damper as follows:
Check procedure
1.Inspect damper for casing damage or leaks.
2.Clamp one end of the damper horizontally in a
vice using soft jaws. Compress and extend the
unit by hand. Resistance should be equal in both
directions.
3.If it is felt that the unit is outside acceptable
limits, fit a new steering damperSTEERING FAULTS
Symptom:-
Excessive kickback through steering wheel - when
driven on rough terrain.
1.Is the steering damper in good working order?
See Steering Damper
NO - Renew unit.See Repair, Steering
Damper
YES - Continue.
2.Is there any looseness or free play in the
steering ball joints and linkage?
YES -
See Steering Linkage Inspect
NO - Continue.
3.Is there any looseness or worn bushes in front
suspension?
YES -
See FRONT SUSPENSION, Repair,
Radius Arm
NOTE: When replacing suspension bushes
ALL bushes and fixings must be replaced.
NO - Continue.
4.Is the steering exceptionally light/sensitive when
driven on good road surface?
YES - See fault symptom -Steering
excessively light/sensitive and
freeplay at steering wheel.
NO - Suspect axle swivel resistance.
5.Check the resistance of the axle swivels.
See
FRONT AXLE AND FINAL DRIVE, Overhaul,
Front Stub Axle, Constant Velocity Joint and
Swivel Pin Housing Non ABS See FRONT
AXLE AND FINAL DRIVE, Overhaul, Front
Stub Axle, Constant Velocity Joint and
Swivel Pin Housing ABS