headlamp LAND ROVER DISCOVERY 1995 Workshop Manual
[x] Cancel search | Manufacturer: LAND ROVER, Model Year: 1995, Model line: DISCOVERY, Model: LAND ROVER DISCOVERY 1995Pages: 873, PDF Size: 12.89 MB
Page 33 of 873
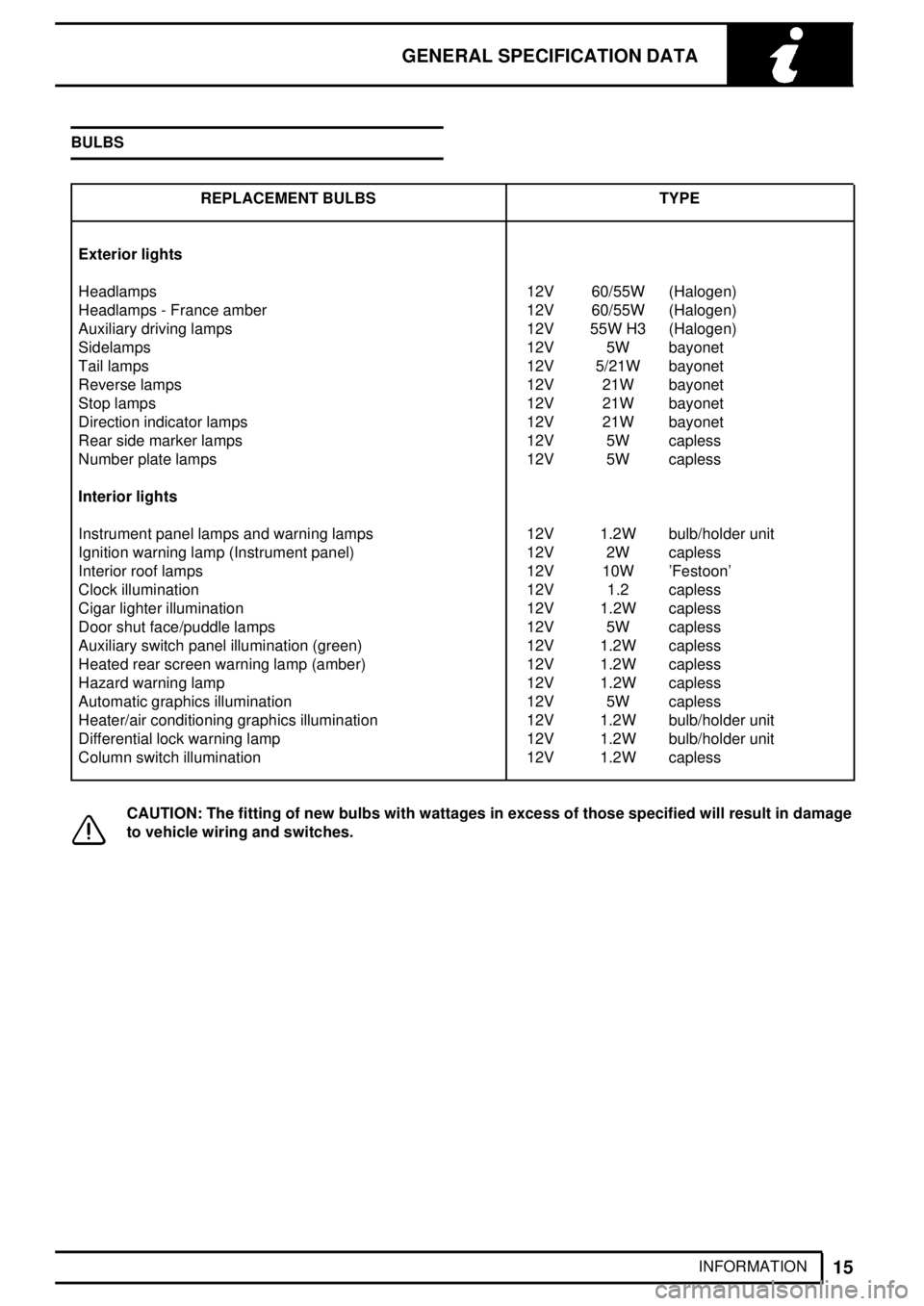
GENERAL SPECIFICATION DATA
15
INFORMATION BULBS
REPLACEMENT BULBS TYPE
Exterior lights
Headlamps 12V 60/55W (Halogen)
Headlamps - France amber 12V 60/55W (Halogen)
Auxiliary driving lamps 12V 55W H3 (Halogen)
Sidelamps 12V 5W bayonet
Tail lamps 12V 5/21W bayonet
Reverse lamps 12V 21W bayonet
Stop lamps 12V 21W bayonet
Direction indicator lamps 12V 21W bayonet
Rear side marker lamps 12V 5W capless
Number plate lamps 12V 5W capless
Interior lights
Instrument panel lamps and warning lamps 12V 1.2W bulb/holder unit
Ignition warning lamp (Instrument panel) 12V 2W capless
Interior roof lamps 12V 10W 'Festoon'
Clock illumination 12V 1.2 capless
Cigar lighter illumination 12V 1.2W capless
Door shut face/puddle lamps 12V 5W capless
Auxiliary switch panel illumination (green) 12V 1.2W capless
Heated rear screen warning lamp (amber) 12V 1.2W capless
Hazard warning lamp 12V 1.2W capless
Automatic graphics illumination 12V 5W capless
Heater/air conditioning graphics illumination 12V 1.2W bulb/holder unit
Differential lock warning lamp 12V 1.2W bulb/holder unit
Column switch illumination 12V 1.2W capless
CAUTION: The fitting of new bulbs with wattages in excess of those specified will result in damage
to vehicle wiring and switches.
Page 65 of 873
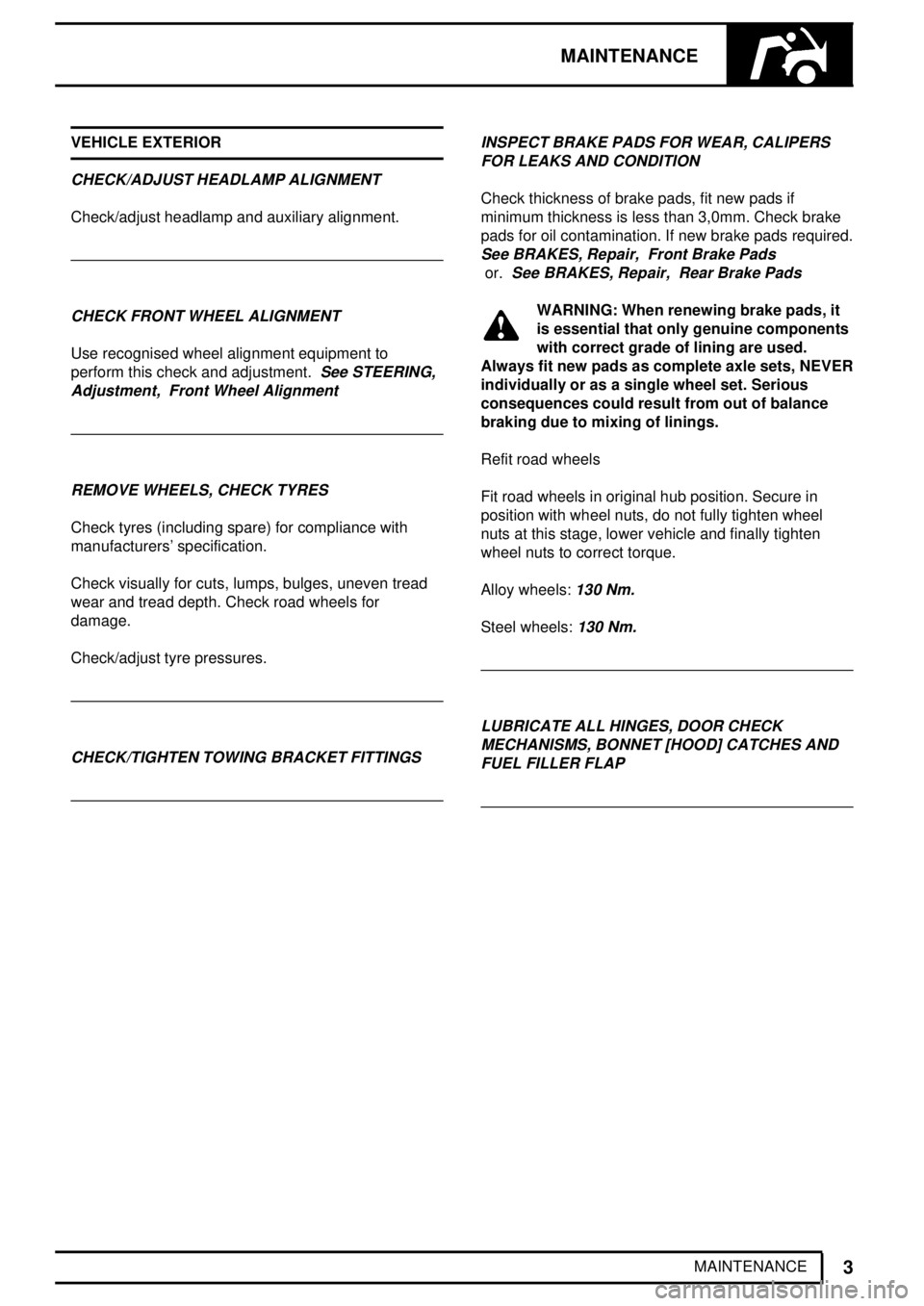
MAINTENANCE
3
MAINTENANCE VEHICLE EXTERIOR
CHECK/ADJUST HEADLAMP ALIGNMENT
Check/adjust headlamp and auxiliary alignment.
CHECK FRONT WHEEL ALIGNMENT
Use recognised wheel alignment equipment to
perform this check and adjustment.
See STEERING,
Adjustment, Front Wheel Alignment
REMOVE WHEELS, CHECK TYRES
Check tyres (including spare) for compliance with
manufacturers' specification.
Check visually for cuts, lumps, bulges, uneven tread
wear and tread depth. Check road wheels for
damage.
Check/adjust tyre pressures.
CHECK/TIGHTEN TOWING BRACKET FITTINGSINSPECT BRAKE PADS FOR WEAR, CALIPERS
FOR LEAKS AND CONDITION
Check thickness of brake pads, fit new pads if
minimum thickness is less than 3,0mm. Check brake
pads for oil contamination. If new brake pads required.
See BRAKES, Repair, Front Brake Pads
or.See BRAKES, Repair, Rear Brake Pads
WARNING: When renewing brake pads, it
is essential that only genuine components
with correct grade of lining are used.
Always fit new pads as complete axle sets, NEVER
individually or as a single wheel set. Serious
consequences could result from out of balance
braking due to mixing of linings.
Refit road wheels
Fit road wheels in original hub position. Secure in
position with wheel nuts, do not fully tighten wheel
nuts at this stage, lower vehicle and finally tighten
wheel nuts to correct torque.
Alloy wheels:
130 Nm.
Steel wheels:130 Nm.
LUBRICATE ALL HINGES, DOOR CHECK
MECHANISMS, BONNET [HOOD] CATCHES AND
FUEL FILLER FLAP
Page 700 of 873
![LAND ROVER DISCOVERY 1995 Workshop Manual CHASSIS AND BODY
33
REPAIR WINGS [FENDERS]
Service repair no - 76.10.24
Remove
1.Disconnect battery negative lead.
2.Remove the headlamp surround.
3.Remove the front bumper assembly.
4.Remove the indi LAND ROVER DISCOVERY 1995 Workshop Manual CHASSIS AND BODY
33
REPAIR WINGS [FENDERS]
Service repair no - 76.10.24
Remove
1.Disconnect battery negative lead.
2.Remove the headlamp surround.
3.Remove the front bumper assembly.
4.Remove the indi](/img/64/57248/w960_57248-699.png)
CHASSIS AND BODY
33
REPAIR WINGS [FENDERS]
Service repair no - 76.10.24
Remove
1.Disconnect battery negative lead.
2.Remove the headlamp surround.
3.Remove the front bumper assembly.
4.Remove the indicator repeater light.
5.Remove the four screws securing the wing
[fender] at the 'A' post.
6.Remove the bolts securing the bottom of the
wing [fender] at the bumper retaining bracket
and at the sill finisher.
7.If removing the RH wing [fender] loosen the
radio aerial securing nut.
8.Remove the seven bolts from the drain channel
in the top of the wing [fender].
9.Break the sealed joints at the valance and 'A'
post; then complete the removal of the wing
[fender]. If removing a RH wing withdraw the
wing [fender] sufficiently to allow removal of the
aerial before completing the removal.Cleaning/painting
10.Thoroughly clean all traces of existing sealant
from the sealing faces of the valance and 'A'
post.
11.Paint the cleaned surfaces with etch primer.
12.If the existing wing [fender] is to be refitted
repeat the cleaning and painting procedure on
the wing [fender] sealing surfaces.
Refit
13.Apply 3M 8572 Bolted Panel Sealer to the joint
faces on the valance and 'A' post and to the
bracket face.
14.Refit the wing [fender], on RH wings [fenders] fit
the radio aerial, and secure with the bolts and
screws ensuring that the wing [fender] correctly
aligns with the bonnet [hood].
Page 794 of 873

WIPERS AND WASHERS
1
DESCRIPTION AND OPERATION WINDSCREEN WIPER AND WASHER OPERATION
The illustration below locates and identifies the main
components of the windscreen and washer system
which is operated by a multi-switch on the right hand
side of the steering column.
All functions of the system are described in the
following paragraphs.
1. Multi-switch
2. Wiper motor
3. Wiper arm/blade
4. Washer reservoir
5. Windscreen washer motor/pump
6. Non return valve
7. Washer jet
8. Rear window washer motor pump
9. Non return valve10. Headlamp power wash motor/pump
11. Headlamp power washer jet
12. Non return valve
13. Rear window wiper switch
14. Rear window washer switch
15. Rear window wiper motor, arm and blade
16. Washer jet
Page 795 of 873
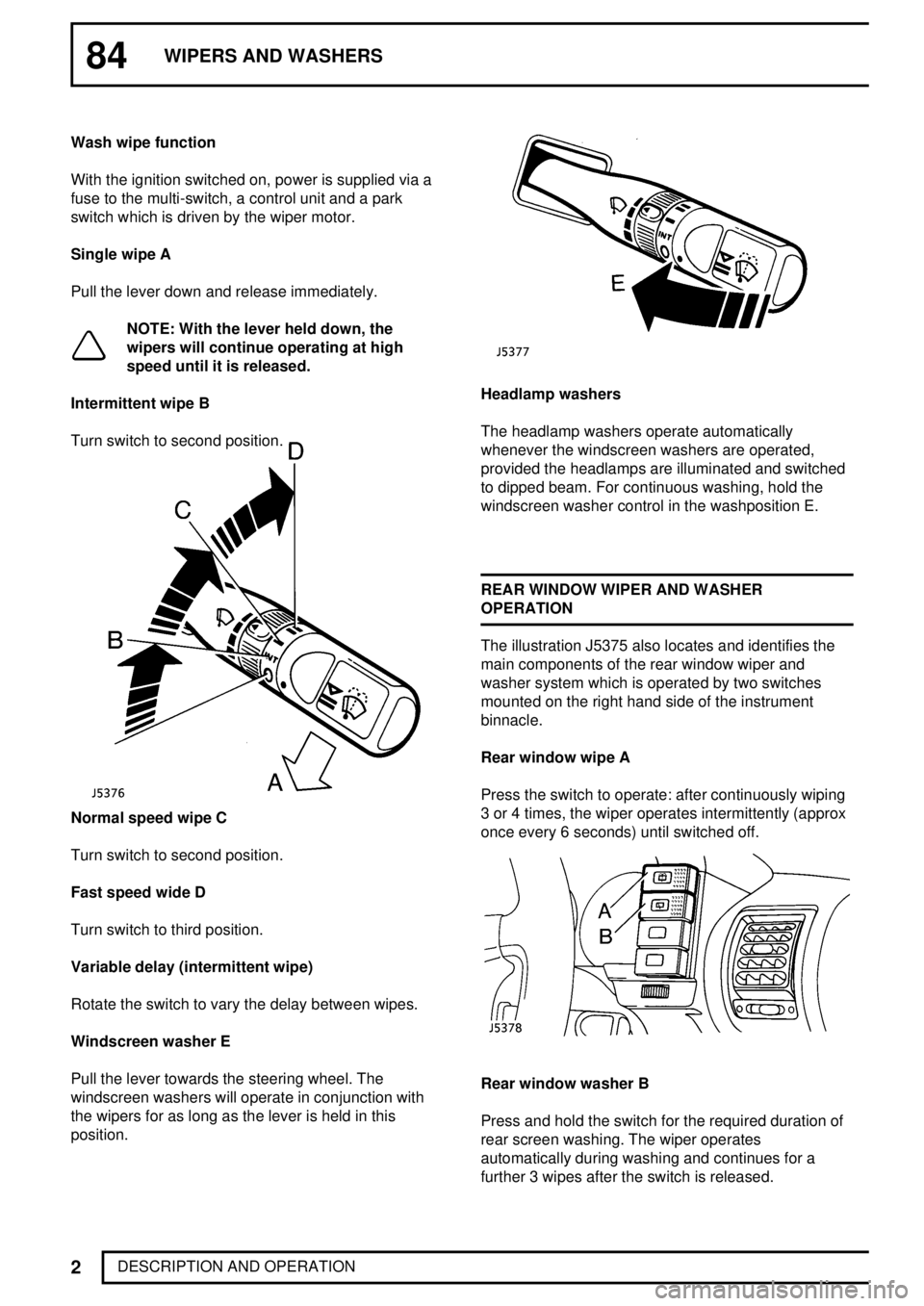
84WIPERS AND WASHERS
2
DESCRIPTION AND OPERATION Wash wipe function
With the ignition switched on, power is supplied via a
fuse to the multi-switch, a control unit and a park
switch which is driven by the wiper motor.
Single wipe A
Pull the lever down and release immediately.
NOTE: With the lever held down, the
wipers will continue operating at high
speed until it is released.
Intermittent wipe B
Turn switch to second position.
Normal speed wipe C
Turn switch to second position.
Fast speed wide D
Turn switch to third position.
Variable delay (intermittent wipe)
Rotate the switch to vary the delay between wipes.
Windscreen washer E
Pull the lever towards the steering wheel. The
windscreen washers will operate in conjunction with
the wipers for as long as the lever is held in this
position.
Headlamp washers
The headlamp washers operate automatically
whenever the windscreen washers are operated,
provided the headlamps are illuminated and switched
to dipped beam. For continuous washing, hold the
windscreen washer control in the washposition E.
REAR WINDOW WIPER AND WASHER
OPERATION
The illustration J5375 also locates and identifies the
main components of the rear window wiper and
washer system which is operated by two switches
mounted on the right hand side of the instrument
binnacle.
Rear window wipe A
Press the switch to operate: after continuously wiping
3 or 4 times, the wiper operates intermittently (approx
once every 6 seconds) until switched off.
Rear window washer B
Press and hold the switch for the required duration of
rear screen washing. The wiper operates
automatically during washing and continues for a
further 3 wipes after the switch is released.
Page 803 of 873

WIPERS AND WASHERS
7
REPAIR HEADLAMP POWER WASH JET
Service repair no - 84.20.08
Remove
1.Disconnect hose from power wash jet.
2.Remove nut securing jet to bumper.
3.Remove power wash jet.
Refit
4.Reverse removal procedure. 1 to 3.POWER WASH HOSE
Service repair no - 84.20.14
Remove
1.Disconnect power wash hoses from jets and
washer pump.
2.Release clamps securing hose.
3.Remove power wash hose.
Refit
4.Reverse removal procedure. 1 to 3, locating
hose in original position.
Page 815 of 873

ELECTRICAL
1
FAULT DIAGNOSIS GENERAL INFORMATION
The electrical fault diagnostic tool on Discovery
vehicles is Testbook. Detailed information of electrical
systems, component locations and circuit diagrams
are covered in the Discovery Electrical
Troubleshooting Manual.
See INTRODUCTION,
Information, Fault Diagnostic Equipment
This section covers checks of the charging and
ignition system.
GENERATOR TESTING
Service repair no - 86.10.01
Charging system check
1.Check battery is in good condition, with an open
circuit voltage of at least 12.6 V. Recharge or
substitute battery to carry out test.
2.Check drive belt condition.
See SECTION 10,
Maintenance, Under Bonnet [Hood]
Maintenance
3.Check battery connections are clean and tight.
4.Check generator connections are clean and
tight.
5.Ensure there is no drain on battery from, for
example, interior, under bonnet [hood] or door
edge lamps.
Generator test
Following instructions refer to use of suitable test
equipment using a carbon pile rheostat.
6.Connect test equipment referring to
manufacturer's instructions.
7.Start engine and run at 3000 rev/min without
accessory load.
8.Rotate carbon pile load control to achieve
greatest output (amps) without allowing voltage
to fall below 12.0 V. A reading in amps, of
generator output, minus 10% to allow for EFI
and Ignition loss, should be obtained.
9.Run engine at 3000 rev/min, switch selector to
regulator test, read voltmeter. A reading of 13.6
to 14.4 V should be obtained.
10.Switch selector to diode/stator test, switch on
headlamps to load generator. Raise engine
speed to 3000 rev/min, read voltmeter, needle
must be within 'OK' range.TESTING IN POSITION
Charging circuit resistance test.
1.Connect a low range voltmeter between
generator terminal marked B+ and positive
terminal of battery.2.Switch on headlamps, start engine. Run engine
at approximately 3000 rev/min. Note voltmeter
reading.
3.Transfer voltmeter connections to frame of
generator and negative terminal of battery, and
again note voltmeter reading.
4.If reading exceeds 0.5 volt on positive side or
0.25 volt on negative side, there is a high
resistance in charging circuit which must be
traced and remedied.
Page 854 of 873
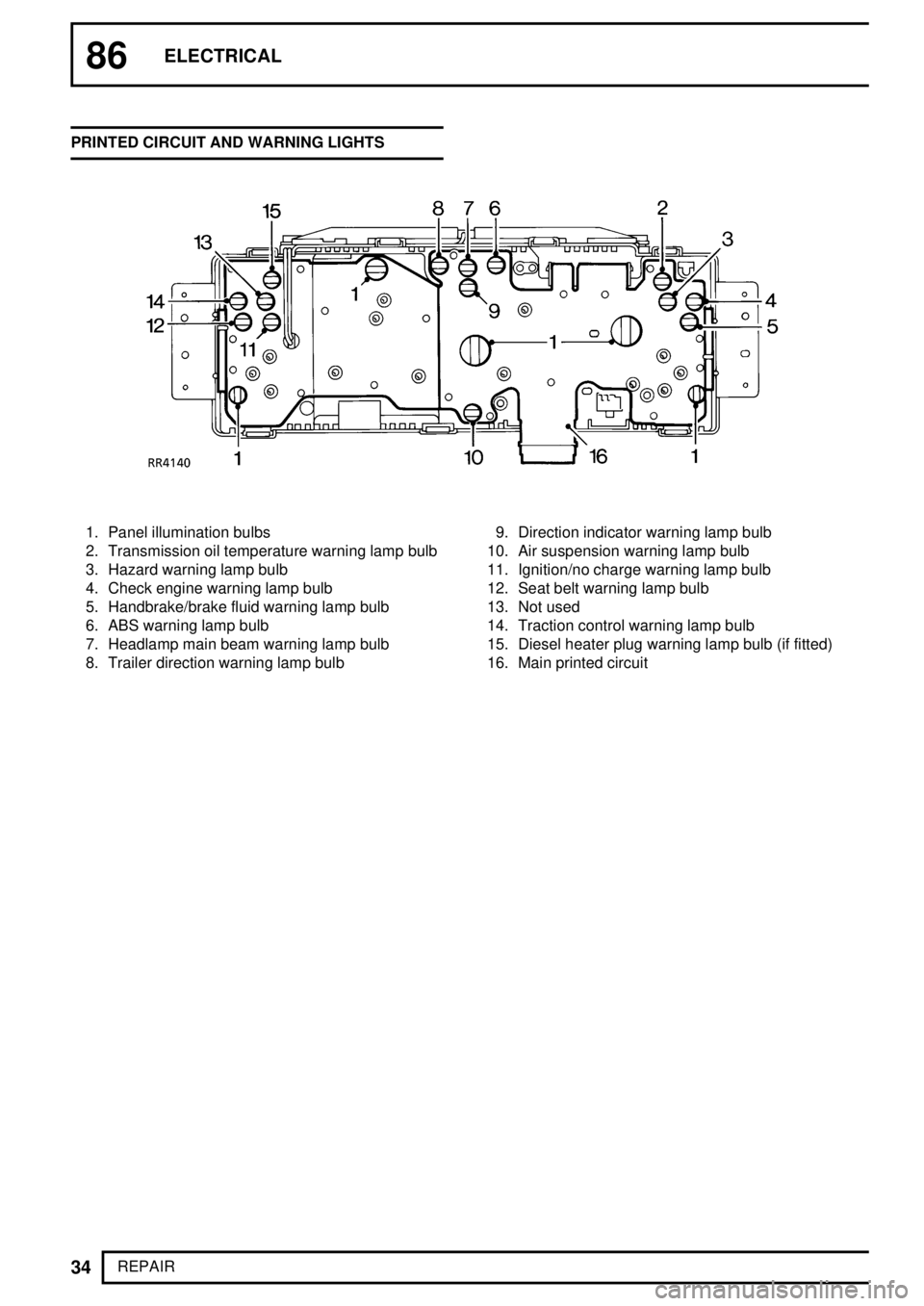
86ELECTRICAL
34
REPAIR PRINTED CIRCUIT AND WARNING LIGHTS
1. Panel illumination bulbs
2. Transmission oil temperature warning lamp bulb
3. Hazard warning lamp bulb
4. Check engine warning lamp bulb
5. Handbrake/brake fluid warning lamp bulb
6. ABS warning lamp bulb
7. Headlamp main beam warning lamp bulb
8. Trailer direction warning lamp bulb9. Direction indicator warning lamp bulb
10. Air suspension warning lamp bulb
11. Ignition/no charge warning lamp bulb
12. Seat belt warning lamp bulb
13. Not used
14. Traction control warning lamp bulb
15. Diesel heater plug warning lamp bulb (if fitted)
16. Main printed circuit
Page 862 of 873

86ELECTRICAL
42
REPAIR FOG LAMP - FRONT
Service repair no - 86.40.96
Remove
1.Locate and release lamp harness multiplug from
clip behind headlamp.
2.Disconnect multiplug.
3.Attach a draw string to harness.
4.Remove 2 nuts securing lamp bracket to bumper
studs.
5.Remove 2 screws securing lamp bracket to
spoiler.
6.Release lamp assembly and pull lamp harness
through front panel.
7.Detach draw string from harness.
8.Remove lamp/bracket assembly.
9.Remove 2 spire nuts from lamp bracket.
Refit
10.Reverse removal procedure.