service indicator LAND ROVER DISCOVERY 1995 Workshop Manual
[x] Cancel search | Manufacturer: LAND ROVER, Model Year: 1995, Model line: DISCOVERY, Model: LAND ROVER DISCOVERY 1995Pages: 873, PDF Size: 12.89 MB
Page 13 of 873
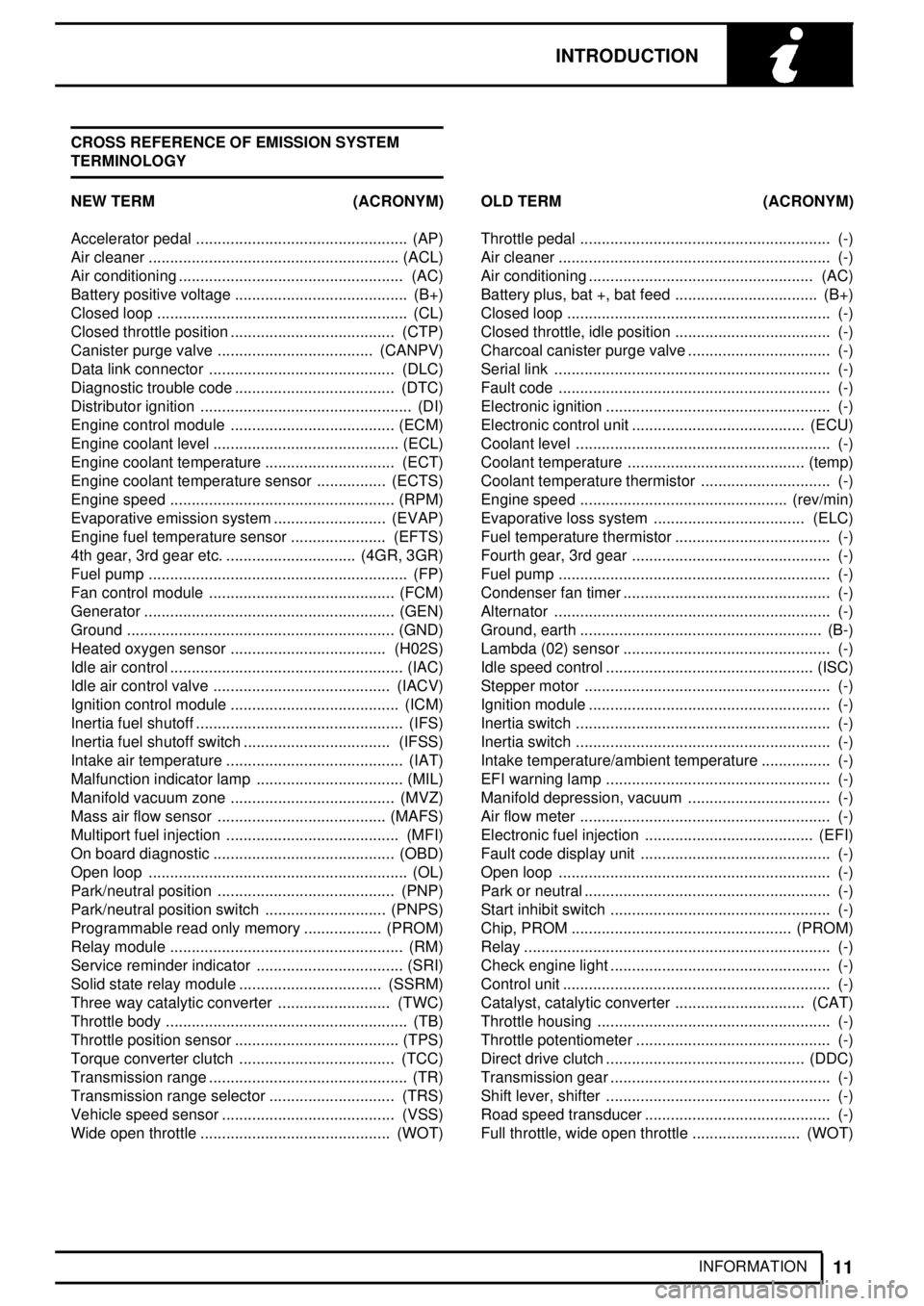
INTRODUCTION
11
INFORMATION CROSS REFERENCE OF EMISSION SYSTEM
TERMINOLOGY
NEW TERM (ACRONYM)
Accelerator pedal (AP).................................................
Air cleaner (ACL)..........................................................
Air conditioning (AC)....................................................
Battery positive voltage (B+)........................................
Closed loop (CL)..........................................................
Closed throttle position (CTP)......................................
Canister purge valve (CANPV)....................................
Data link connector (DLC)...........................................
Diagnostic trouble code (DTC).....................................
Distributor ignition (DI).................................................
Engine control module (ECM)......................................
Engine coolant level (ECL)...........................................
Engine coolant temperature (ECT)..............................
Engine coolant temperature sensor (ECTS)................
Engine speed (RPM)....................................................
Evaporative emission system (EVAP)..........................
Engine fuel temperature sensor (EFTS)......................
4th gear, 3rd gear etc. (4GR, 3GR)..............................
Fuel pump (FP)............................................................
Fan control module (FCM)...........................................
Generator (GEN)..........................................................
Ground (GND)..............................................................
Heated oxygen sensor (H02S)....................................
Idle air control (IAC)......................................................
Idle air control valve (IACV).........................................
Ignition control module (ICM).......................................
Inertia fuel shutoff (IFS)................................................
Inertia fuel shutoff switch (IFSS)..................................
Intake air temperature (IAT).........................................
Malfunction indicator lamp (MIL)..................................
Manifold vacuum zone (MVZ)......................................
Mass air flow sensor (MAFS).......................................
Multiport fuel injection (MFI)........................................
On board diagnostic (OBD)..........................................
Open loop (OL)............................................................
Park/neutral position (PNP).........................................
Park/neutral position switch (PNPS)............................
Programmable read only memory (PROM)..................
Relay module (RM)......................................................
Service reminder indicator (SRI)..................................
Solid state relay module (SSRM).................................
Three way catalytic converter (TWC)..........................
Throttle body (TB)........................................................
Throttle position sensor (TPS)......................................
Torque converter clutch (TCC)....................................
Transmission range (TR)..............................................
Transmission range selector (TRS).............................
Vehicle speed sensor (VSS)........................................
Wide open throttle (WOT)............................................OLD TERM (ACRONYM)
Throttle pedal (-)..........................................................
Air cleaner (-)...............................................................
Air conditioning (AC)....................................................
Battery plus, bat +, bat feed (B+).................................
Closed loop (-).............................................................
Closed throttle, idle position (-)....................................
Charcoal canister purge valve (-).................................
Serial link (-)................................................................
Fault code (-)...............................................................
Electronic ignition (-)....................................................
Electronic control unit (ECU)........................................
Coolant level (-)...........................................................
Coolant temperature (temp).........................................
Coolant temperature thermistor (-)..............................
Engine speed (rev/min)................................................
Evaporative loss system (ELC)...................................
Fuel temperature thermistor (-)....................................
Fourth gear, 3rd gear (-)..............................................
Fuel pump (-)...............................................................
Condenser fan timer (-)................................................
Alternator (-)................................................................
Ground, earth (B-)........................................................
Lambda (02) sensor (-)................................................
Idle speed control (ISC)................................................
Stepper motor (-).........................................................
Ignition module (-)........................................................
Inertia switch (-)...........................................................
Inertia switch (-)...........................................................
Intake temperature/ambient temperature (-)................
EFI warning lamp (-)....................................................
Manifold depression, vacuum (-).................................
Air flow meter (-)..........................................................
Electronic fuel injection (EFI).......................................
Fault code display unit (-)............................................
Open loop (-)...............................................................
Park or neutral (-).........................................................
Start inhibit switch (-)...................................................
Chip, PROM (PROM)...................................................
Relay (-).......................................................................
Check engine light (-)...................................................
Control unit (-)..............................................................
Catalyst, catalytic converter (CAT)..............................
Throttle housing (-)......................................................
Throttle potentiometer (-).............................................
Direct drive clutch (DDC)..............................................
Transmission gear (-)...................................................
Shift lever, shifter (-)....................................................
Road speed transducer (-)...........................................
Full throttle, wide open throttle (WOT).........................
Page 63 of 873
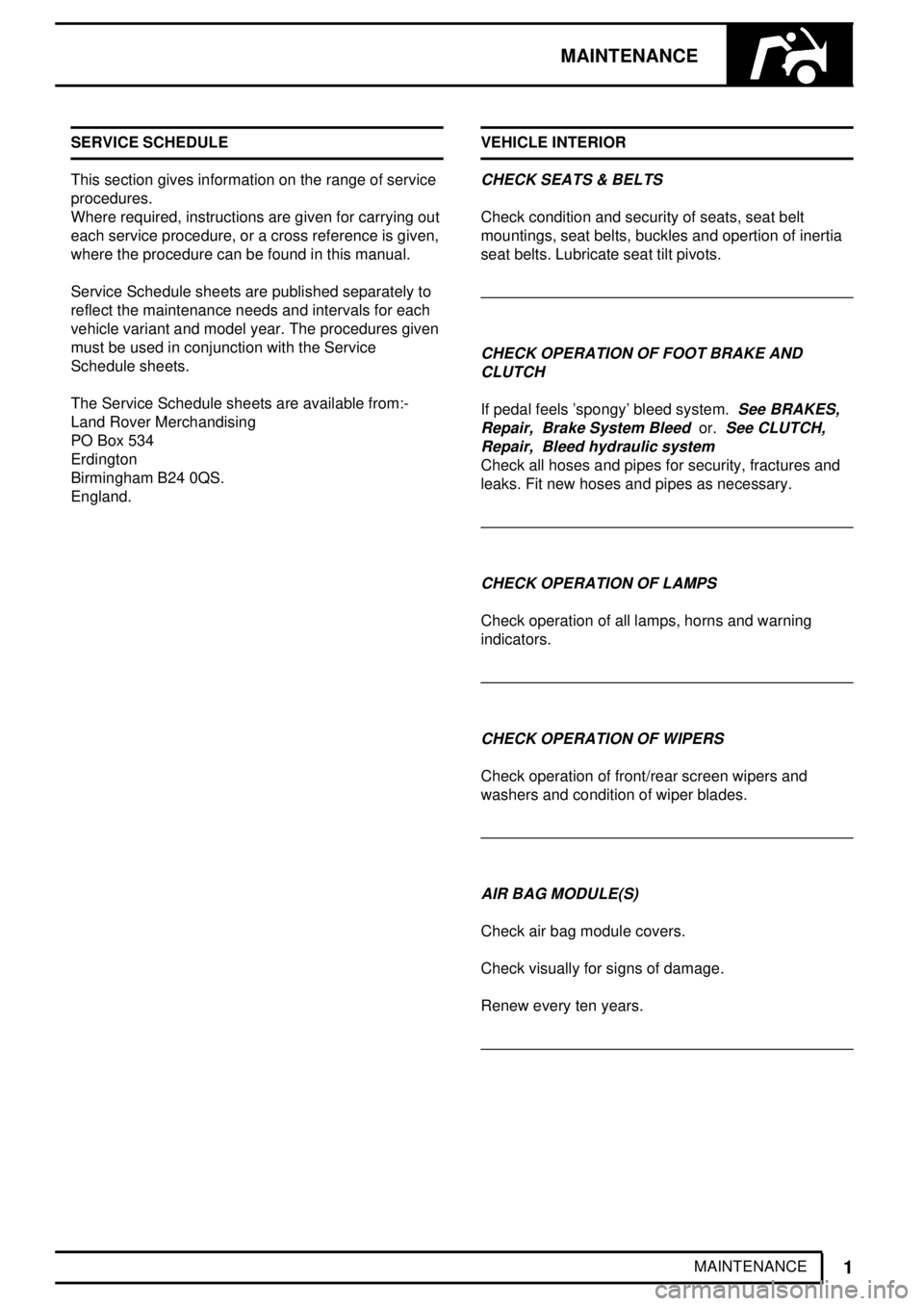
MAINTENANCE
1
MAINTENANCE SERVICE SCHEDULE
This section gives information on the range of service
procedures.
Where required, instructions are given for carrying out
each service procedure, or a cross reference is given,
where the procedure can be found in this manual.
Service Schedule sheets are published separately to
reflect the maintenance needs and intervals for each
vehicle variant and model year. The procedures given
must be used in conjunction with the Service
Schedule sheets.
The Service Schedule sheets are available from:-
Land Rover Merchandising
PO Box 534
Erdington
Birmingham B24 0QS.
England.VEHICLE INTERIOR
CHECK SEATS & BELTS
Check condition and security of seats, seat belt
mountings, seat belts, buckles and opertion of inertia
seat belts. Lubricate seat tilt pivots.
CHECK OPERATION OF FOOT BRAKE AND
CLUTCH
If pedal feels 'spongy' bleed system.See BRAKES,
Repair, Brake System Bleed
or.See CLUTCH,
Repair, Bleed hydraulic system
Check all hoses and pipes for security, fractures and
leaks. Fit new hoses and pipes as necessary.
CHECK OPERATION OF LAMPS
Check operation of all lamps, horns and warning
indicators.
CHECK OPERATION OF WIPERS
Check operation of front/rear screen wipers and
washers and condition of wiper blades.
AIR BAG MODULE(S)
Check air bag module covers.
Check visually for signs of damage.
Renew every ten years.
Page 80 of 873
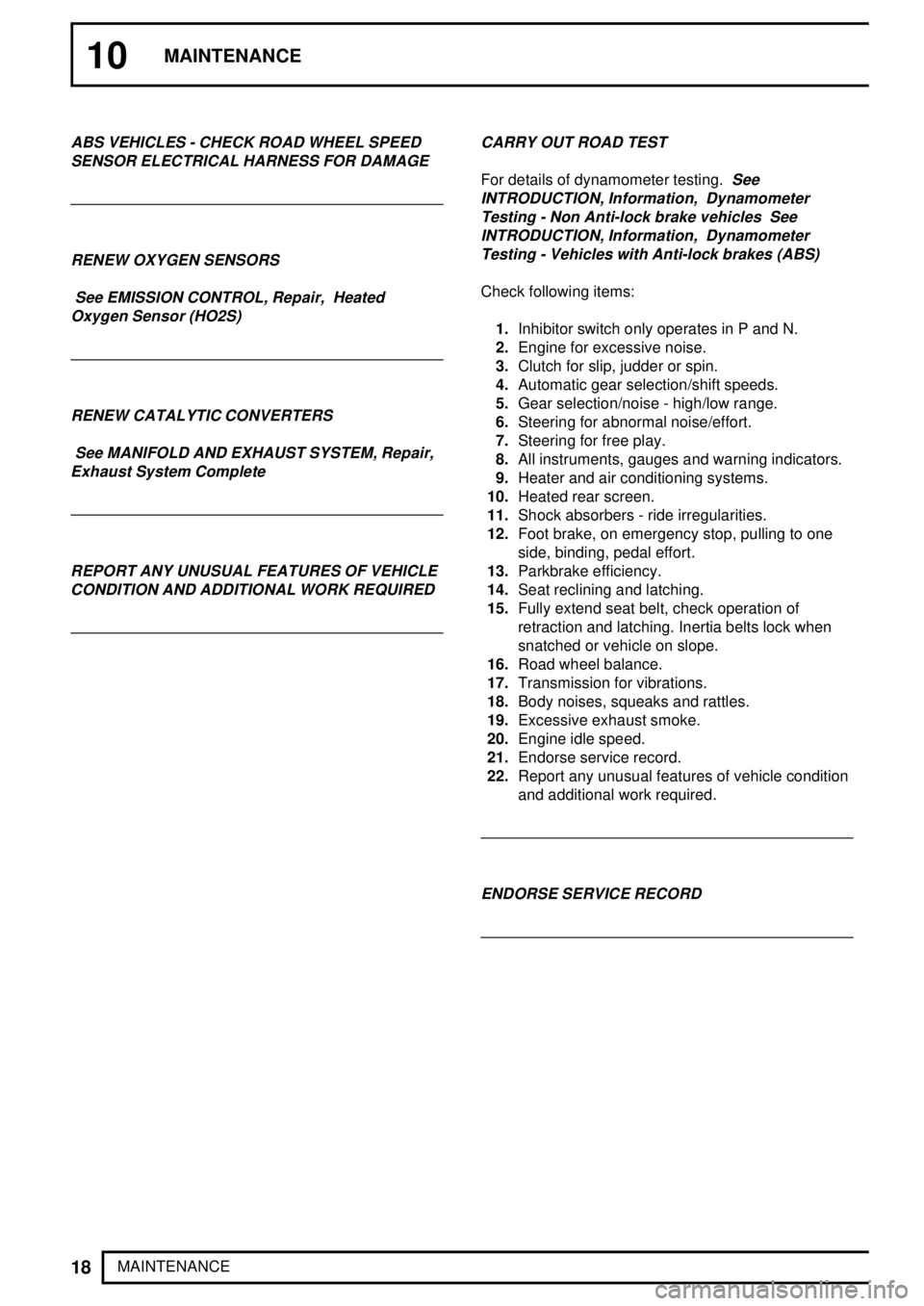
10MAINTENANCE
18
MAINTENANCE
ABS VEHICLES - CHECK ROAD WHEEL SPEED
SENSOR ELECTRICAL HARNESS FOR DAMAGE
RENEW OXYGEN SENSORS
See EMISSION CONTROL, Repair, Heated
Oxygen Sensor (HO2S)
RENEW CATALYTIC CONVERTERS
See MANIFOLD AND EXHAUST SYSTEM, Repair,
Exhaust System Complete
REPORT ANY UNUSUAL FEATURES OF VEHICLE
CONDITION AND ADDITIONAL WORK REQUIREDCARRY OUT ROAD TEST
For details of dynamometer testing.See
INTRODUCTION, Information, Dynamometer
Testing - Non Anti-lock brake vehicles See
INTRODUCTION, Information, Dynamometer
Testing - Vehicles with Anti-lock brakes (ABS)
Check following items:
1.Inhibitor switch only operates in P and N.
2.Engine for excessive noise.
3.Clutch for slip, judder or spin.
4.Automatic gear selection/shift speeds.
5.Gear selection/noise - high/low range.
6.Steering for abnormal noise/effort.
7.Steering for free play.
8.All instruments, gauges and warning indicators.
9.Heater and air conditioning systems.
10.Heated rear screen.
11.Shock absorbers - ride irregularities.
12.Foot brake, on emergency stop, pulling to one
side, binding, pedal effort.
13.Parkbrake efficiency.
14.Seat reclining and latching.
15.Fully extend seat belt, check operation of
retraction and latching. Inertia belts lock when
snatched or vehicle on slope.
16.Road wheel balance.
17.Transmission for vibrations.
18.Body noises, squeaks and rattles.
19.Excessive exhaust smoke.
20.Engine idle speed.
21.Endorse service record.
22.Report any unusual features of vehicle condition
and additional work required.
ENDORSE SERVICE RECORD
Page 95 of 873
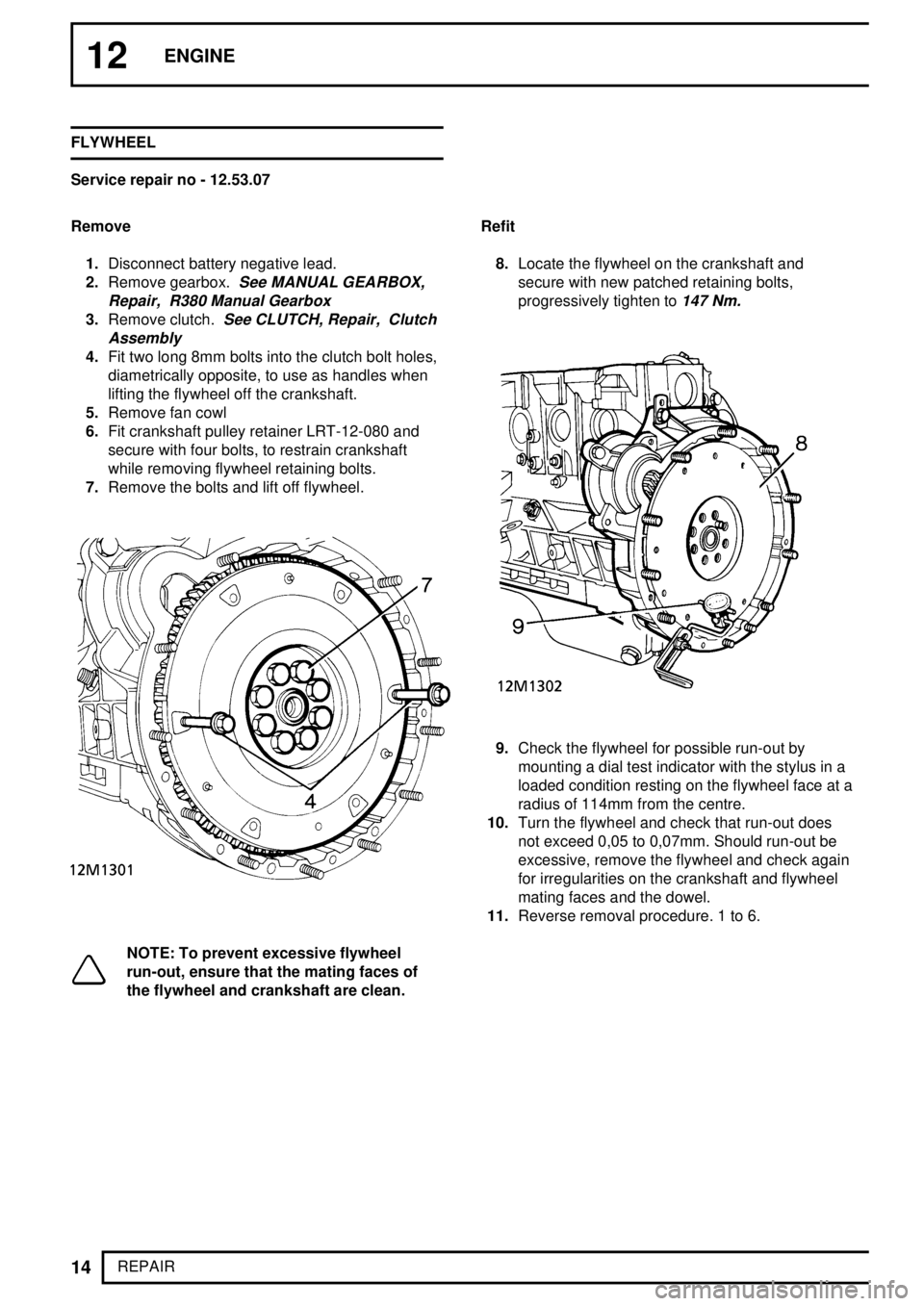
12ENGINE
14
REPAIR FLYWHEEL
Service repair no - 12.53.07
Remove
1.Disconnect battery negative lead.
2.Remove gearbox.
See MANUAL GEARBOX,
Repair, R380 Manual Gearbox
3.Remove clutch.See CLUTCH, Repair, Clutch
Assembly
4.Fit two long 8mm bolts into the clutch bolt holes,
diametrically opposite, to use as handles when
lifting the flywheel off the crankshaft.
5.Remove fan cowl
6.Fit crankshaft pulley retainer LRT-12-080 and
secure with four bolts, to restrain crankshaft
while removing flywheel retaining bolts.
7.Remove the bolts and lift off flywheel.
NOTE: To prevent excessive flywheel
run-out, ensure that the mating faces of
the flywheel and crankshaft are clean.Refit
8.Locate the flywheel on the crankshaft and
secure with new patched retaining bolts,
progressively tighten to
147 Nm.
9.Check the flywheel for possible run-out by
mounting a dial test indicator with the stylus in a
loaded condition resting on the flywheel face at a
radius of 114mm from the centre.
10.Turn the flywheel and check that run-out does
not exceed 0,05 to 0,07mm. Should run-out be
excessive, remove the flywheel and check again
for irregularities on the crankshaft and flywheel
mating faces and the dowel.
11.Reverse removal procedure. 1 to 6.
Page 352 of 873
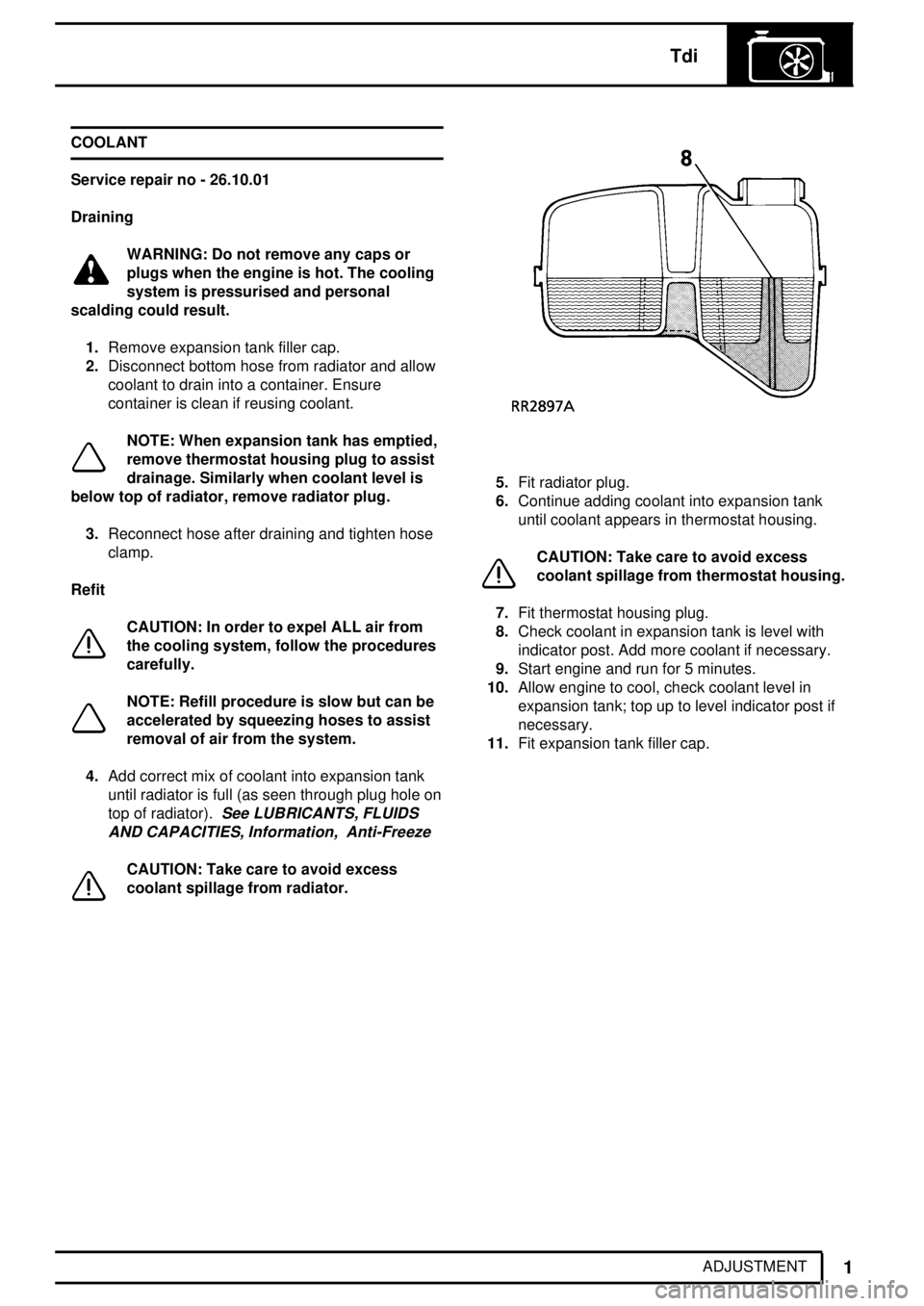
Tdi
1
ADJUSTMENT COOLANT
Service repair no - 26.10.01
Draining
WARNING: Do not remove any caps or
plugs when the engine is hot. The cooling
system is pressurised and personal
scalding could result.
1.Remove expansion tank filler cap.
2.Disconnect bottom hose from radiator and allow
coolant to drain into a container. Ensure
container is clean if reusing coolant.
NOTE: When expansion tank has emptied,
remove thermostat housing plug to assist
drainage. Similarly when coolant level is
below top of radiator, remove radiator plug.
3.Reconnect hose after draining and tighten hose
clamp.
Refit
CAUTION: In order to expel ALL air from
the cooling system, follow the procedures
carefully.
NOTE: Refill procedure is slow but can be
accelerated by squeezing hoses to assist
removal of air from the system.
4.Add correct mix of coolant into expansion tank
until radiator is full (as seen through plug hole on
top of radiator).
See LUBRICANTS, FLUIDS
AND CAPACITIES, Information, Anti-Freeze
CAUTION: Take care to avoid excess
coolant spillage from radiator.
5.Fit radiator plug.
6.Continue adding coolant into expansion tank
until coolant appears in thermostat housing.
CAUTION: Take care to avoid excess
coolant spillage from thermostat housing.
7.Fit thermostat housing plug.
8.Check coolant in expansion tank is level with
indicator post. Add more coolant if necessary.
9.Start engine and run for 5 minutes.
10.Allow engine to cool, check coolant level in
expansion tank; top up to level indicator post if
necessary.
11.Fit expansion tank filler cap.
Page 494 of 873
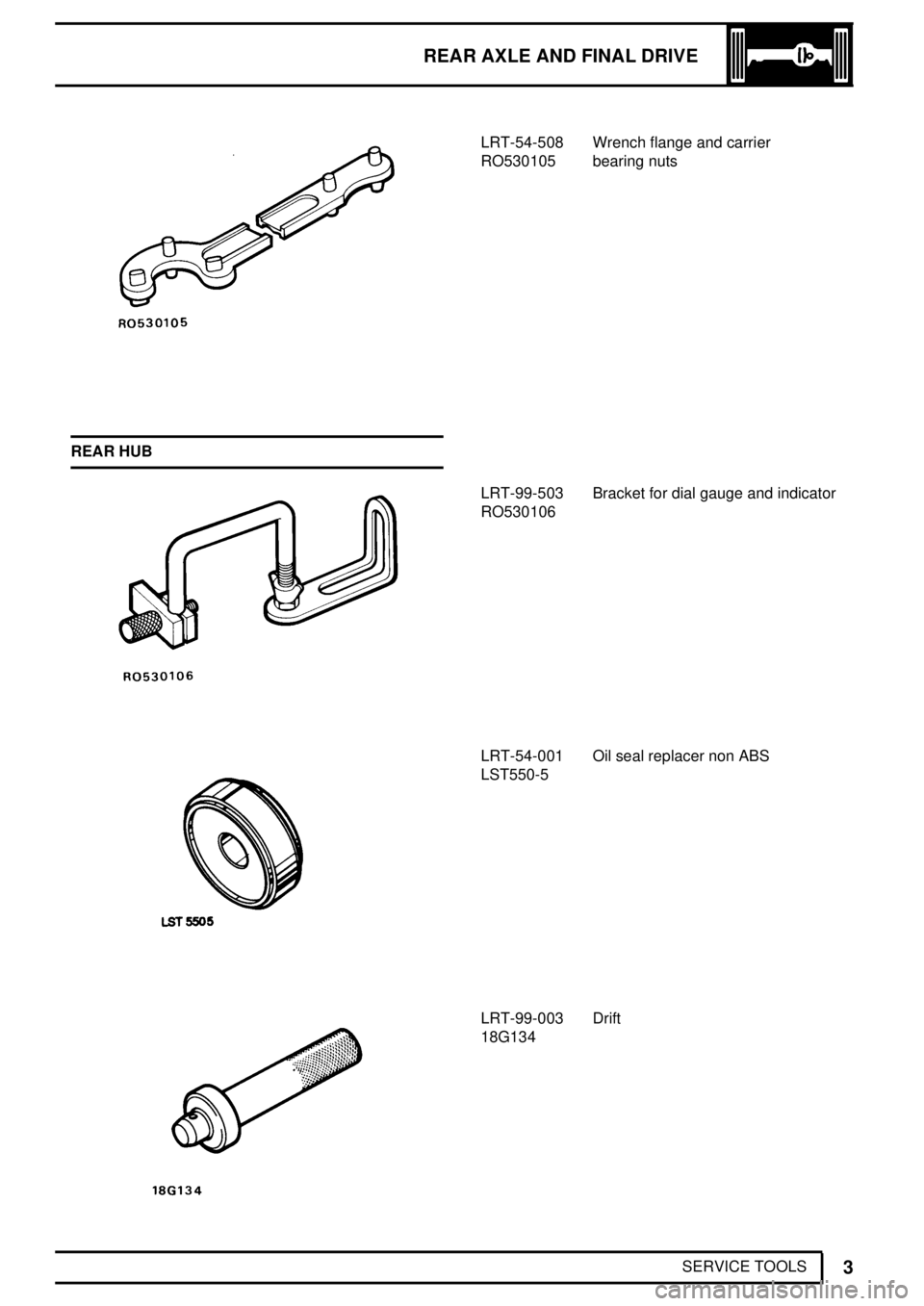
REAR AXLE AND FINAL DRIVE
3
SERVICE TOOLS
LRT-54-508 Wrench flange and carrier
RO530105 bearing nuts
REAR HUB
LRT-99-503 Bracket for dial gauge and indicator
RO530106
LRT-54-001 Oil seal replacer non ABS
LST550-5
LRT-99-003 Drift
18G134
Page 500 of 873
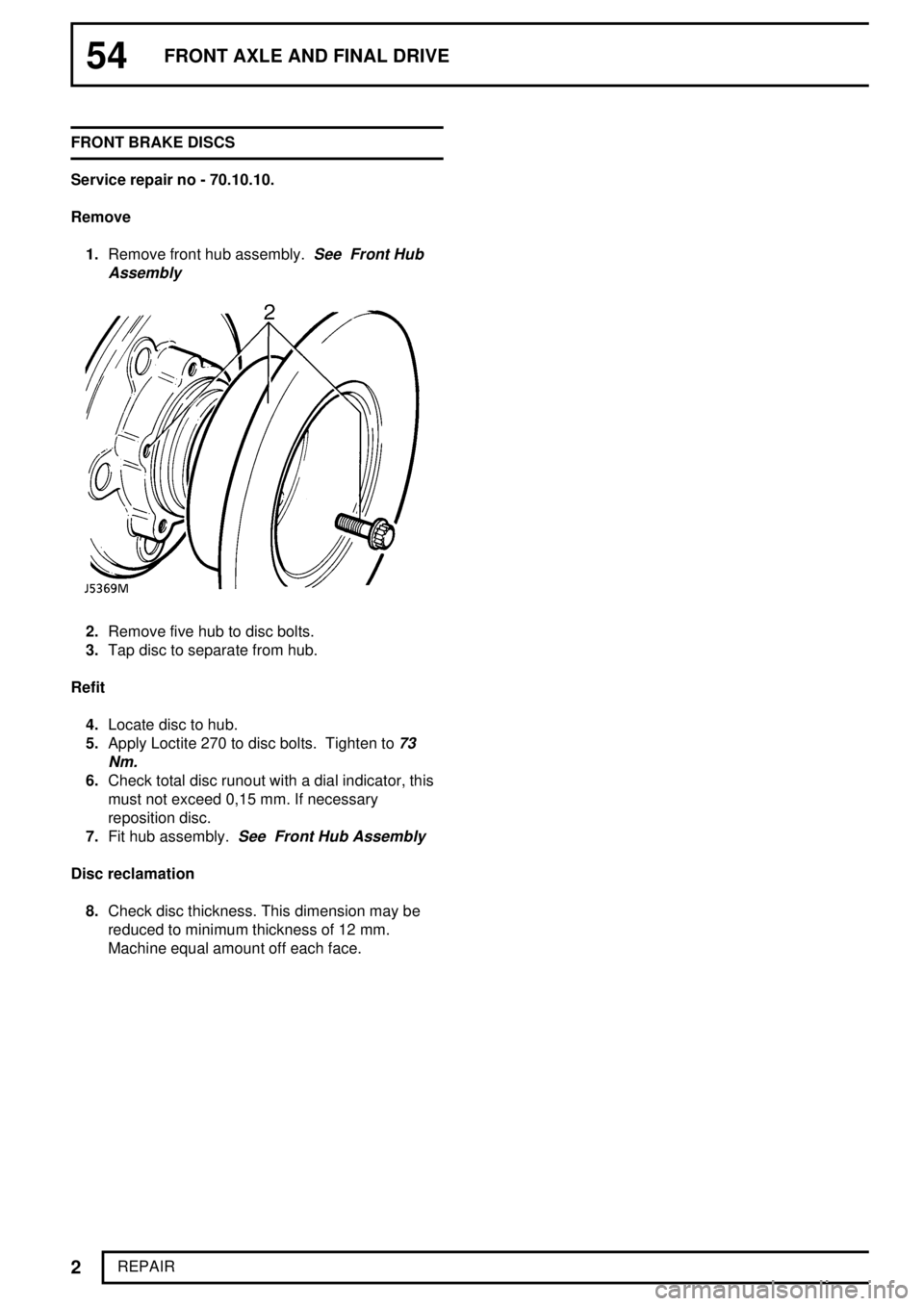
54FRONT AXLE AND FINAL DRIVE
2
REPAIR FRONT BRAKE DISCS
Service repair no - 70.10.10.
Remove
1.Remove front hub assembly.
See Front Hub
Assembly
2.Remove five hub to disc bolts.
3.Tap disc to separate from hub.
Refit
4.Locate disc to hub.
5.Apply Loctite 270 to disc bolts. Tighten to
73
Nm.
6.Check total disc runout with a dial indicator, this
must not exceed 0,15 mm. If necessary
reposition disc.
7.Fit hub assembly.
See Front Hub Assembly
Disc reclamation
8.Check disc thickness. This dimension may be
reduced to minimum thickness of 12 mm.
Machine equal amount off each face.
Page 551 of 873
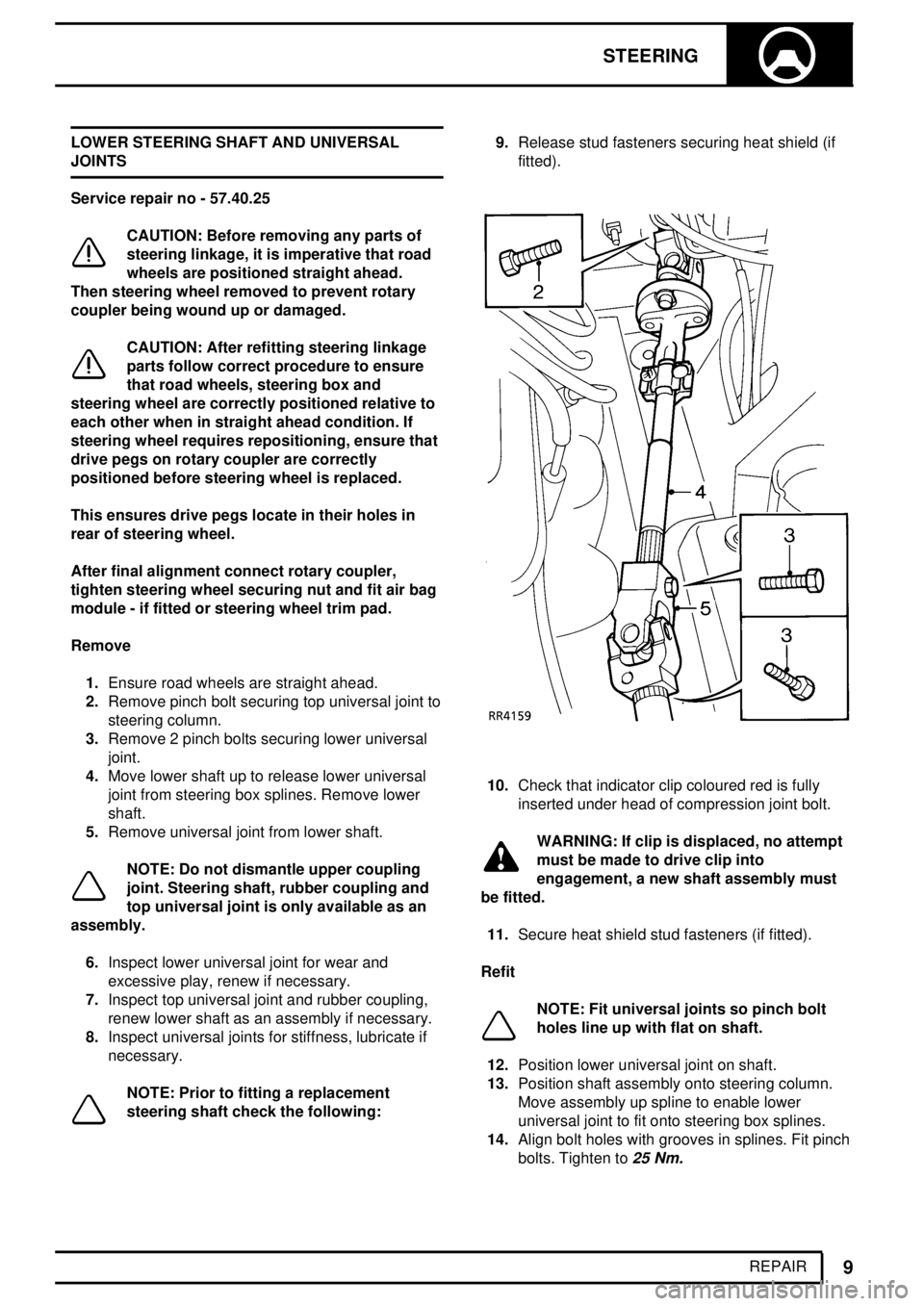
STEERING
9
REPAIR LOWER STEERING SHAFT AND UNIVERSAL
JOINTS
Service repair no - 57.40.25
CAUTION: Before removing any parts of
steering linkage, it is imperative that road
wheels are positioned straight ahead.
Then steering wheel removed to prevent rotary
coupler being wound up or damaged.
CAUTION: After refitting steering linkage
parts follow correct procedure to ensure
that road wheels, steering box and
steering wheel are correctly positioned relative to
each other when in straight ahead condition. If
steering wheel requires repositioning, ensure that
drive pegs on rotary coupler are correctly
positioned before steering wheel is replaced.
This ensures drive pegs locate in their holes in
rear of steering wheel.
After final alignment connect rotary coupler,
tighten steering wheel securing nut and fit air bag
module - if fitted or steering wheel trim pad.
Remove
1.Ensure road wheels are straight ahead.
2.Remove pinch bolt securing top universal joint to
steering column.
3.Remove 2 pinch bolts securing lower universal
joint.
4.Move lower shaft up to release lower universal
joint from steering box splines. Remove lower
shaft.
5.Remove universal joint from lower shaft.
NOTE: Do not dismantle upper coupling
joint. Steering shaft, rubber coupling and
top universal joint is only available as an
assembly.
6.Inspect lower universal joint for wear and
excessive play, renew if necessary.
7.Inspect top universal joint and rubber coupling,
renew lower shaft as an assembly if necessary.
8.Inspect universal joints for stiffness, lubricate if
necessary.
NOTE: Prior to fitting a replacement
steering shaft check the following:9.Release stud fasteners securing heat shield (if
fitted).
10.Check that indicator clip coloured red is fully
inserted under head of compression joint bolt.
WARNING: If clip is displaced, no attempt
must be made to drive clip into
engagement, a new shaft assembly must
be fitted.
11.Secure heat shield stud fasteners (if fitted).
Refit
NOTE: Fit universal joints so pinch bolt
holes line up with flat on shaft.
12.Position lower universal joint on shaft.
13.Position shaft assembly onto steering column.
Move assembly up spline to enable lower
universal joint to fit onto steering box splines.
14.Align bolt holes with grooves in splines. Fit pinch
bolts. Tighten to
25 Nm.
Page 634 of 873
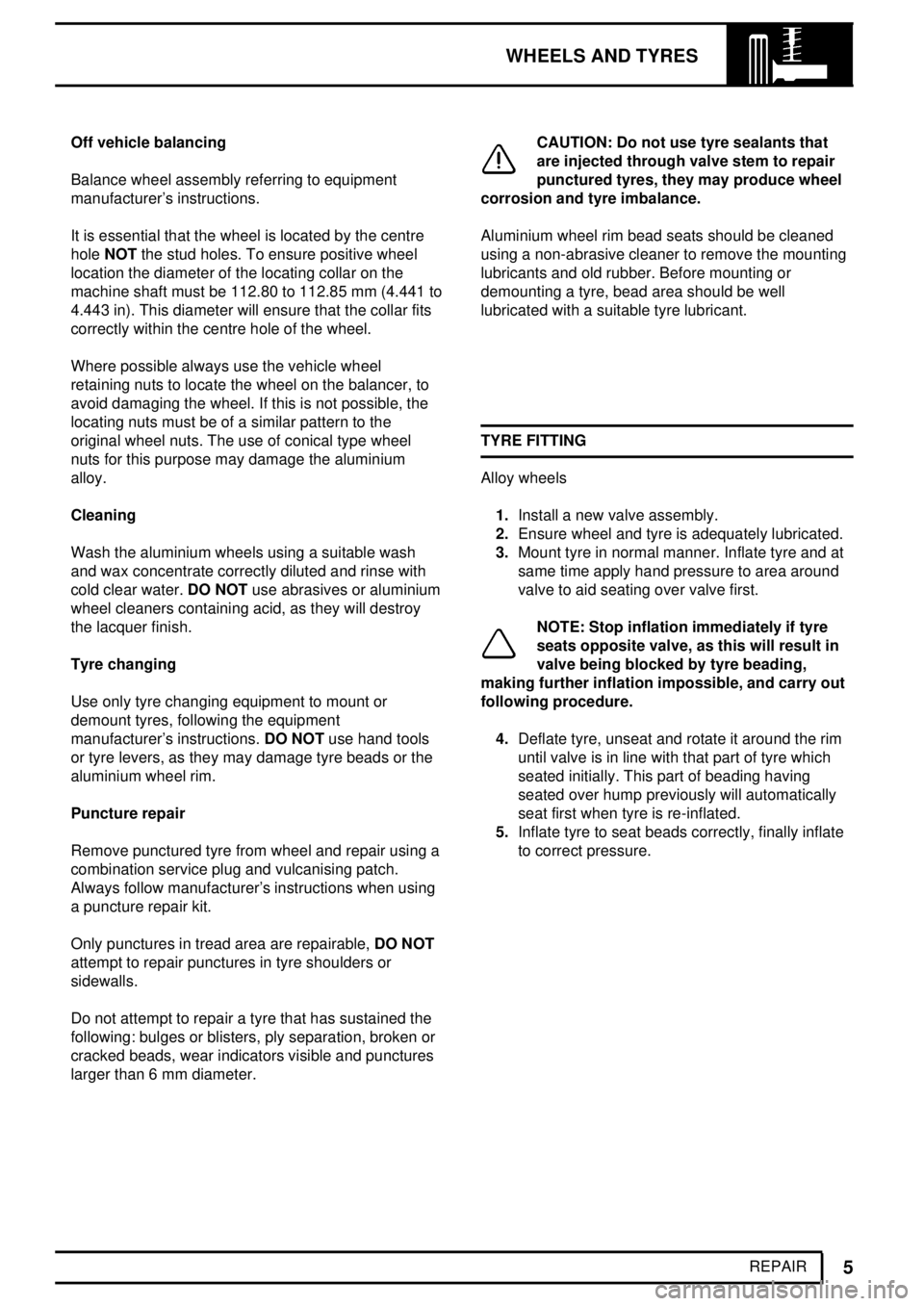
WHEELS AND TYRES
5
REPAIR Off vehicle balancing
Balance wheel assembly referring to equipment
manufacturer's instructions.
It is essential that the wheel is located by the centre
holeNOTthe stud holes. To ensure positive wheel
location the diameter of the locating collar on the
machine shaft must be 112.80 to 112.85 mm (4.441 to
4.443 in). This diameter will ensure that the collar fits
correctly within the centre hole of the wheel.
Where possible always use the vehicle wheel
retaining nuts to locate the wheel on the balancer, to
avoid damaging the wheel. If this is not possible, the
locating nuts must be of a similar pattern to the
original wheel nuts. The use of conical type wheel
nuts for this purpose may damage the aluminium
alloy.
Cleaning
Wash the aluminium wheels using a suitable wash
and wax concentrate correctly diluted and rinse with
cold clear water.DO NOTuse abrasives or aluminium
wheel cleaners containing acid, as they will destroy
the lacquer finish.
Tyre changing
Use only tyre changing equipment to mount or
demount tyres, following the equipment
manufacturer's instructions.DO NOTuse hand tools
or tyre levers, as they may damage tyre beads or the
aluminium wheel rim.
Puncture repair
Remove punctured tyre from wheel and repair using a
combination service plug and vulcanising patch.
Always follow manufacturer's instructions when using
a puncture repair kit.
Only punctures in tread area are repairable,DO NOT
attempt to repair punctures in tyre shoulders or
sidewalls.
Do not attempt to repair a tyre that has sustained the
following: bulges or blisters, ply separation, broken or
cracked beads, wear indicators visible and punctures
larger than 6 mm diameter.
CAUTION: Do not use tyre sealants that
are injected through valve stem to repair
punctured tyres, they may produce wheel
corrosion and tyre imbalance.
Aluminium wheel rim bead seats should be cleaned
using a non-abrasive cleaner to remove the mounting
lubricants and old rubber. Before mounting or
demounting a tyre, bead area should be well
lubricated with a suitable tyre lubricant.
TYRE FITTING
Alloy wheels
1.Install a new valve assembly.
2.Ensure wheel and tyre is adequately lubricated.
3.Mount tyre in normal manner. Inflate tyre and at
same time apply hand pressure to area around
valve to aid seating over valve first.
NOTE: Stop inflation immediately if tyre
seats opposite valve, as this will result in
valve being blocked by tyre beading,
making further inflation impossible, and carry out
following procedure.
4.Deflate tyre, unseat and rotate it around the rim
until valve is in line with that part of tyre which
seated initially. This part of beading having
seated over hump previously will automatically
seat first when tyre is re-inflated.
5.Inflate tyre to seat beads correctly, finally inflate
to correct pressure.
Page 652 of 873
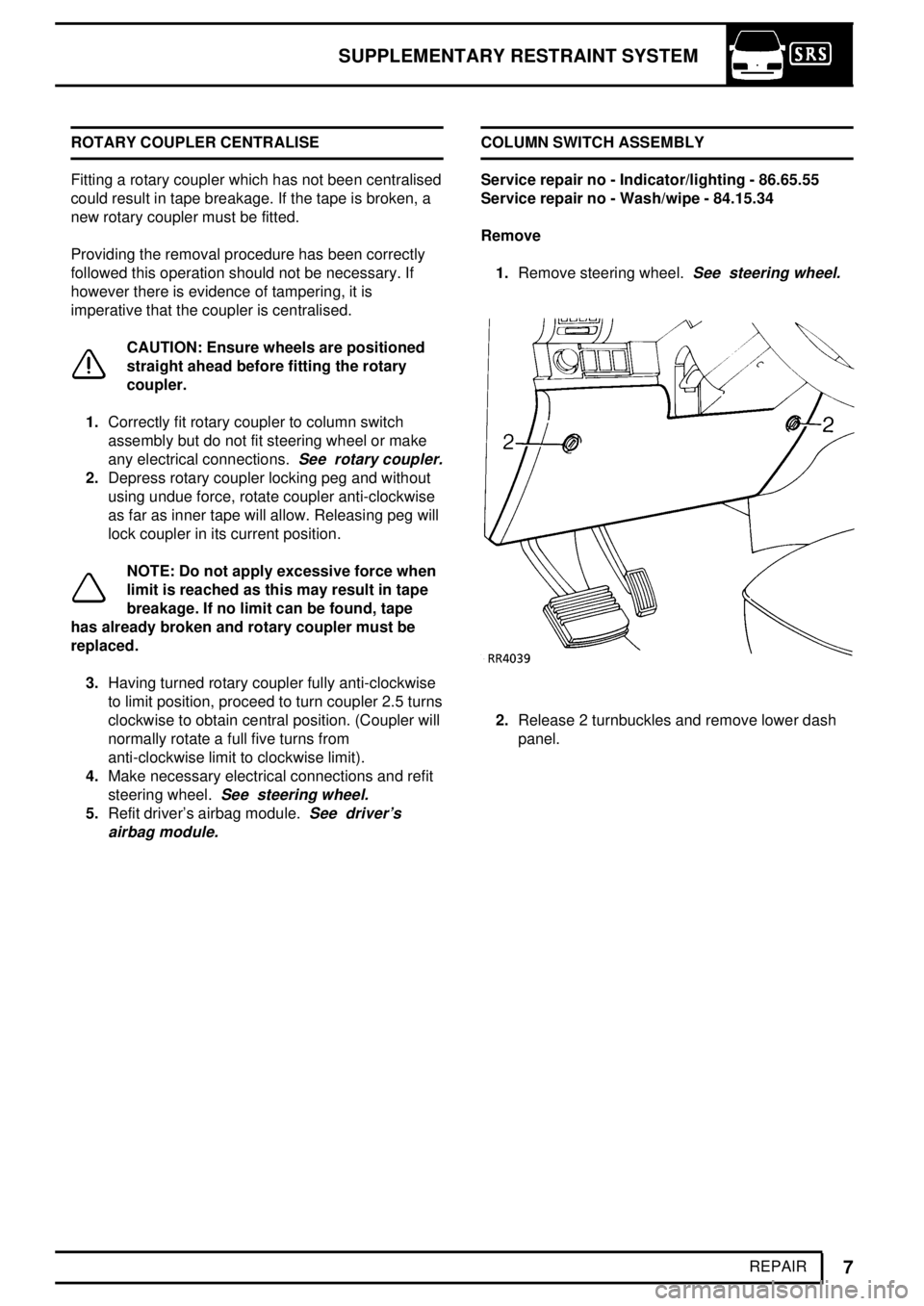
SUPPLEMENTARY RESTRAINT SYSTEM
7
REPAIR ROTARY COUPLER CENTRALISE
Fitting a rotary coupler which has not been centralised
could result in tape breakage. If the tape is broken, a
new rotary coupler must be fitted.
Providing the removal procedure has been correctly
followed this operation should not be necessary. If
however there is evidence of tampering, it is
imperative that the coupler is centralised.
CAUTION: Ensure wheels are positioned
straight ahead before fitting the rotary
coupler.
1.Correctly fit rotary coupler to column switch
assembly but do not fit steering wheel or make
any electrical connections.
See rotary coupler.
2.Depress rotary coupler locking peg and without
using undue force, rotate coupler anti-clockwise
as far as inner tape will allow. Releasing peg will
lock coupler in its current position.
NOTE: Do not apply excessive force when
limit is reached as this may result in tape
breakage. If no limit can be found, tape
has already broken and rotary coupler must be
replaced.
3.Having turned rotary coupler fully anti-clockwise
to limit position, proceed to turn coupler 2.5 turns
clockwise to obtain central position. (Coupler will
normally rotate a full five turns from
anti-clockwise limit to clockwise limit).
4.Make necessary electrical connections and refit
steering wheel.
See steering wheel.
5.Refit driver's airbag module.See driver's
airbag module.
COLUMN SWITCH ASSEMBLY
Service repair no - Indicator/lighting - 86.65.55
Service repair no - Wash/wipe - 84.15.34
Remove
1.Remove steering wheel.
See steering wheel.
2.Release 2 turnbuckles and remove lower dash
panel.